孔类零件的编程与加工
数控加工程序编制铣削编程4孔类零件的程序编制
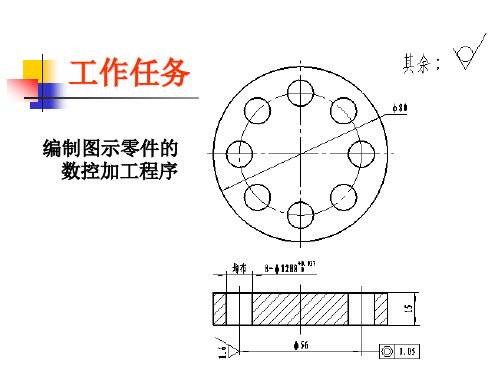
二、相关知识
(四)孔加工循环指令
举例:如图所示,用此程序加 工xy平面上在z轴方向排列的螺 纹孔M12x1。在此,出发点定 为x30y20,第一个孔与此参考 点的距离为20mm,其他的钻 孔相互间的距离也是20mm。 首先执行循环LCYC83加工孔, 然后运行循环LCYC84进行螺 纹切削。钻孔深度为80mm, 攻70mm。
LCYC60循环指令应用
二、相关知识
(四)孔加工循环指令
N10 G0 G54 G71 G17 G90 Tl Dl ;确定工艺参数 N20 S500 M3 y30 x20 z110 ;回到出发点(任意的) N30 R10l=75 R102=2 R103=72 R104=22 ;定义钻孔循环参数 N40 R105=l R107=82 R108=20 R109=10 ;定义钻孔循环参数 N50 R110=30 R111=10 R127=1 ;定义钻孔循环参数 N60 Rl15=83 R116=30 R117=20 R118=20 Rl19=5 R120=90 R121=20 N70 LCYC60 ;调用线性孔循环 N71 M05;
刀具,从而保孔的尺寸精度和表面粗糙度值。
二、相关知识
(三)孔加工刀具的选用
3)钻削速度V、进给量F的选择 F(mm/min)=S(r/min)×f(mm/r) S(r/min)=1000×V/(π×D) (r/min)
钻削进给量F参考值
加工材料
深 径 切削用
刀具直径do(mm)
比
量
灰铸铁
可锻铁、锰铸 铁
l/do
8 10 12 16 20 25 30 35 40
163~229HB (HT100、
HT150)
可锻铸铁 (≤229HB)
加工中心29个孔打孔编程格式

加工中心29个孔打孔编程格式摘要:1.加工中心29个孔的基本信息2.打孔编程的步骤与方法3.编程格式的规范与应用4.实际操作中的注意事项正文:加工中心29个孔打孔编程格式是在制造业中广泛应用的一种工艺方法。
在进行打孔编程时,需要遵循一定的步骤与方法,以确保孔位的精确度和加工效率。
本文将详细介绍加工中心29个孔的打孔编程格式,并提供实用的操作指南。
一、加工中心29个孔的基本信息加工中心29个孔是指在加工过程中,需要在工件上打29个孔。
这些孔的位置、直径、深度和分布应根据零件图纸和加工要求来确定。
在实际操作中,加工中心29个孔可分为两类:一类是通孔,另一类是盲孔。
通孔是指孔底与孔口在同一平面上,而盲孔则是指孔底与孔口不在同一平面上。
二、打孔编程的步骤与方法1.读取零件图纸,了解孔的位置、直径、深度等信息,为编程做好准备。
2.选择合适的编程软件,如CAM软件、UG软件等,根据零件图纸和加工要求进行编程。
3.编写程序,包括以下内容:(1)设定加工中心的工作坐标系,使编程坐标系与工件坐标系一致。
(2)编写孔的加工循环,包括孔的直径、深度、进给速度、切削速度等参数。
(3)编写移位指令,使加工中心在打孔过程中能够自动移位。
(4)编写刀具补偿指令,以保证孔径的精度。
(5)编写安全区域指令,避免加工过程中发生碰撞。
4.模拟加工,检查程序的正确性,调整参数以优化加工过程。
5.实现在线加工,监控加工过程,确保孔的加工质量。
三、编程格式的规范与应用1.编程格式应遵循加工中心的编程规范,如ISO代码、G代码等。
2.编程格式应清晰、简洁,便于阅读和理解。
3.编程格式中的指令应准确无误,确保加工中心能够按照要求进行加工。
4.编程格式中的参数应合理设置,以提高加工效率和加工质量。
四、实际操作中的注意事项1.严格按照零件图纸和加工要求进行编程,确保孔位的精确度。
2.合理选择刀具,根据孔的直径、深度和材料特性选择合适的切削参数。
3.加工过程中注意监控刀具的磨损情况,及时更换刀具以保证孔的加工质量。
数控车孔类零件的加工教案
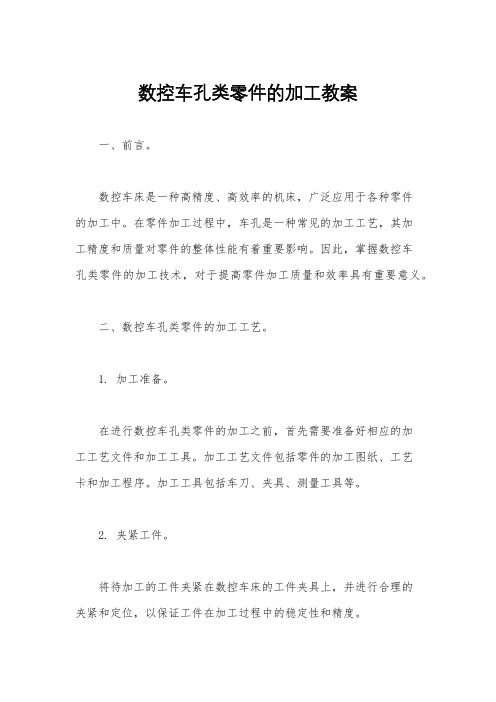
数控车孔类零件的加工教案一、前言。
数控车床是一种高精度、高效率的机床,广泛应用于各种零件的加工中。
在零件加工过程中,车孔是一种常见的加工工艺,其加工精度和质量对零件的整体性能有着重要影响。
因此,掌握数控车孔类零件的加工技术,对于提高零件加工质量和效率具有重要意义。
二、数控车孔类零件的加工工艺。
1. 加工准备。
在进行数控车孔类零件的加工之前,首先需要准备好相应的加工工艺文件和加工工具。
加工工艺文件包括零件的加工图纸、工艺卡和加工程序。
加工工具包括车刀、夹具、测量工具等。
2. 夹紧工件。
将待加工的工件夹紧在数控车床的工件夹具上,并进行合理的夹紧和定位,以保证工件在加工过程中的稳定性和精度。
3. 加工参数设置。
根据零件的加工要求和数控车床的性能特点,设置加工参数,包括主轴转速、进给速度、切削深度、切削速度等。
合理的加工参数设置对于保证零件加工质量和提高加工效率至关重要。
4. 车刀选择和装夹。
根据零件的加工要求和加工特点,选择合适的车刀,并将车刀装夹在数控车床的刀架上。
在装夹过程中,需要保证车刀的正确位置和角度,以保证切削的精度和质量。
5. 加工操作。
根据加工程序和加工要求,进行数控车孔类零件的加工操作。
在加工过程中,需要密切关注加工状态,及时调整加工参数和刀具位置,以保证加工的精度和质量。
6. 质量检验。
在加工完成后,进行零件质量的检验。
主要包括尺寸精度、表面粗糙度和孔的圆度等方面。
对于不合格的零件,需要及时调整加工参数和工艺,以保证零件的质量和性能。
三、数控车孔类零件的加工注意事项。
1. 加工前的准备工作要充分,包括加工工艺文件的准备、加工工具的选择和加工参数的设置等。
2. 在夹紧工件时,需要保证夹紧力的均匀和稳定,以避免在加工过程中出现工件的变形和位移。
3. 在车刀选择和装夹时,需要保证车刀的刃口尖锐和刀具的稳定性,以保证切削的精度和表面质量。
4. 在加工过程中,需要密切关注加工状态,及时调整加工参数和刀具位置,以保证加工的精度和质量。
模块五(项目四)孔类零件.
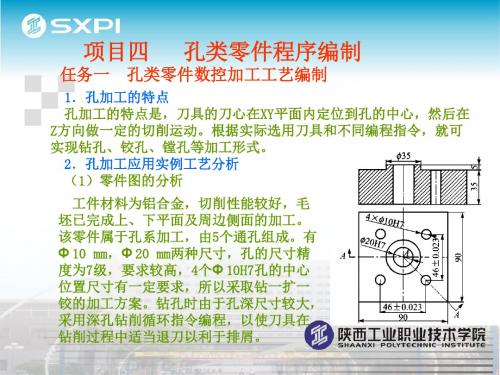
③用Φ 10mm的机用铰刀精铰 4 ×Φ 10 mm的孔至尺寸要求;
④用Φ 13mm的麻花钻将Φ 20mm的孔粗钻至Φ 13mm; ⑤用Φ 19.8mm的麻花钻将Φ 20mm的孔粗钻至Φ 19.8mm;
⑥用Φ 20H7的机用铰刀精铰Φ 20mm的孔至尺寸要求。4个Φ 20 mm孔加工 于XY平面的进给路线,如图所示。
(2)刀具及切削用量的确定 刀具选择:T2:Φ 3 mm的高速钢中心钻,T3:Φ 9.8 mm的高速钢 麻花钻,T4:Φ 10H7的机用铰刀,T5:Φ 13mm高速钢麻花钻,T6: Φ 19.8mm麻花钻,T7:Φ 20H7机用铰刀 (3)工件装夹 选择毛坯底面和两侧面为定位平面,其中底面为主定位面,采用 等高垫铁在平口虎钳口上装夹定位或直接将工件毛坯放在工作台上, 用等高垫铁将工件托起,再用百分表找正工件两侧面进行安装定位, 最后用压板螺母、螺栓、垫圈等元件将工件夹紧。
3.编写加工程序 用 FANUC 0i-MB数控系统的指令及规则编写的加工程序如下:
O3001; N0010 G21; N0020 G17 G40 G49 G69 G80 G90 ; N0030 G54; N0040 T2M6; N0050 S1400 M03; N0060 G00 XO YO ; N0070 G43 G00 Z50 H02; N0080 G00 Z10; N0090 G99 G81 X0 YO Y0 Z-5 R5 F50; N0100 X23 Y23 Z-10 R2; N0110 X-23;N0120 Y-23; N0130 G98 X23; N0140 G80; N0150 GO0 Z50;
N0160 N0170 N0180 N0190 N0200 N0210 N0220 N0230 N0240 N0250 N0260 N0270 N0280 N0290 N0300 N0310 N0320 N0330 N0340 N0350
项目9.3 孔类零件的加工.
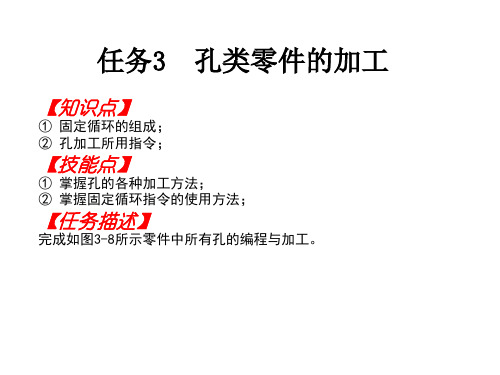
①直径在M6以下的螺纹不适合在立式数控铣床上加工,因为自动攻螺纹不能随机控 制加工状态,且小直径丝锥易折断。 ②攻丝时要求排屑效果好,因此一般应加注切削液。 ③丝锥用钝后应及时更换,不得强行攻制,以免加工时发生折断。 ④立式数控铣床上采用固定循环指令编写攻丝程序,它的6个基本动作类同于孔加工 循环。加工前首先根据图纸要求计算出螺纹底孔的直径,并选择麻花钻加工出底 孔;攻丝加工的进给速度与主轴转速及内螺纹的螺距有关,编程中有的直接给定 螺距,机床可自动计算其进给速度;有的则需将计算出的进给速度()写入程序 中。 表3-9 数控铣床上孔的加工方法
快速移动 快速移动 手动移动 切削进给
2 孔加工固定循环概述
图3-9 固定循环动作及图形符号 (1)孔加工固定循环动作 固定循环通常由六个基本动作构成。(见图3-9) 动作1——X、Y轴定位。刀具快速定位到孔加工的位置(初始点)。 动作2——快进到R点平面。刀具自初始点快速进给到R点平面(准备切削的位 置),在多孔加工时,为了刀具移动的安全,应注意R点平面Z值的选取。 动作3——孔加工。以切削进给方式执行孔加工的动作。 动作4——在孔底的动作。包括暂停、主轴定向停止、刀具移位等动作。 动作5——返回到R点平面。 动作6——快速返回到初始点。 (2)孔加工固定循环的基本格式
粗镗→半精镗→精镗(如仍达不到精度还可进一步采用精细镗)
关于表3-8的说明如下: ①在加工直径小于30mm且没有预孔的毛坯孔时,为了保证钻孔加工的 定位精度,可选择在钻孔前先将孔口端面铣平或采用打中心孔的加工 方法。 ②对于表5-1中的扩孔及粗镗加工,也可采用立铣刀铣孔的加工方法。 ③在加工螺纹孔时,先加工出螺纹底孔,对于直径在M6下的螺纹,通常 不在数控铣床上加工;对于直径在M6~M20的螺纹,通常采用攻螺 纹的加工方法;而对于直径在M20以上的螺纹,可采用螺纹铣刀铣削 加工。
数控车床的孔加工编程方法举例
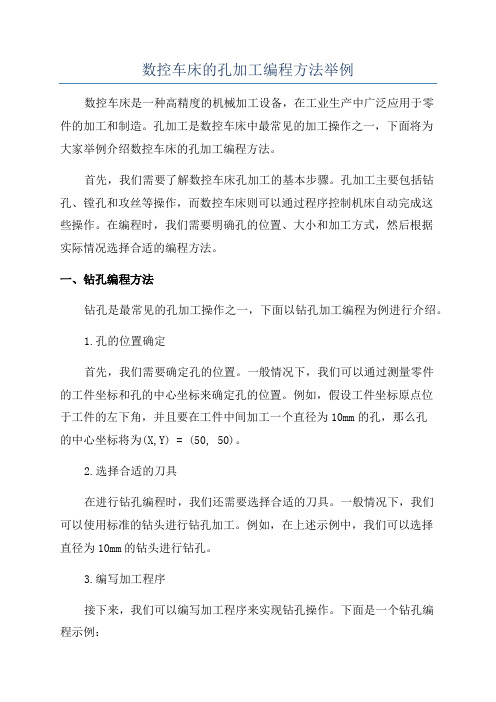
数控车床的孔加工编程方法举例数控车床是一种高精度的机械加工设备,在工业生产中广泛应用于零件的加工和制造。
孔加工是数控车床中最常见的加工操作之一,下面将为大家举例介绍数控车床的孔加工编程方法。
首先,我们需要了解数控车床孔加工的基本步骤。
孔加工主要包括钻孔、镗孔和攻丝等操作,而数控车床则可以通过程序控制机床自动完成这些操作。
在编程时,我们需要明确孔的位置、大小和加工方式,然后根据实际情况选择合适的编程方法。
一、钻孔编程方法钻孔是最常见的孔加工操作之一,下面以钻孔加工编程为例进行介绍。
1.孔的位置确定首先,我们需要确定孔的位置。
一般情况下,我们可以通过测量零件的工件坐标和孔的中心坐标来确定孔的位置。
例如,假设工件坐标原点位于工件的左下角,并且要在工件中间加工一个直径为10mm的孔,那么孔的中心坐标将为(X,Y) = (50, 50)。
2.选择合适的刀具在进行钻孔编程时,我们还需要选择合适的刀具。
一般情况下,我们可以使用标准的钻头进行钻孔加工。
例如,在上述示例中,我们可以选择直径为10mm的钻头进行钻孔。
3.编写加工程序接下来,我们可以编写加工程序来实现钻孔操作。
下面是一个钻孔编程示例:O0001(程序号)N1G90G54G64G80(绝对坐标系,工件坐标系,等距插补模式,取消固定循环)N2S500M3(设置主轴转速为500转/分钟,开启主轴)N3G0X50Y50(快速定位到孔的中心坐标)N4 G81 Z-10 R2 F100 (启动钻孔循环,Z轴下降10mm,每次进刀2mm,进给速度为100mm/分钟)N5G80(取消固定循环)N6M5(关闭主轴)N7M30(程序结束)在上述示例中,首先通过G90指令设置绝对坐标系和工件坐标系。
然后通过G64指令设置等距插补模式,取消固定循环。
接着,通过G0指令进行快速定位,将刀具移动到孔的中心坐标处。
然后通过G81指令启动钻孔循环,设置Z轴下降10mm,每次进刀2mm,进给速度为100mm/分钟。
数控加工程序编制-加工中心-孔类零件程序编制全解

G88循环
二、相关知识
(二)固定循环功能
(5)精镗循环(G76) 指令格式: G76 X_ Y_ Z_ R_ Q_ F_
精镗时,主轴在孔底定向停止后,向刀尖反方向移 动,然后快速退刀。
这种带有让刀的退刀不会划伤已加工平面,保证了 镗孔精度。
程序格式中,Q 表示刀尖的偏移量,一般为正数, 移动方向由机床参数设定。
1
钻中心孔
2
钻φ5mm通孔
3
攻丝
螺纹孔加工工序卡
刀具规格
类型
材料
A4中心钻
高速钢
Φ4.2mm麻花钻 高速钢
M5mm细牙丝锥 高速钢
主轴转速 (r/min)
1200 600 80
进给速度 (mm/min)
20 30 64
(6)编制零件螺纹孔钻中心孔加工程序
四、拓展知识
用西门子802D孔及螺纹加工循环指令加工图零件。
(二)固定循环功能
(2)带停顿的钻孔循环(G82) 指令格式:
G82 X_Y_Z_P_R_F_
G82循环
该指令除了要在孔底暂停外,其它动作与G81相同。暂 停时间由地址P给出。此指令主要用于加工盲孔,以提 高孔深精度。
二、相关知识
(二)固定循环功能
(3)断屑式深孔加工循环(G73)
指令格式: G73 X_Y_Z_Q_R_F_
三、工作任务的完成
(一)数控加工工艺的制订
4.刀具准备,填写刀具卡
序号
1 2 3
4
5 6 7
刀具号
T05 T06 T07
名称 麻花钻 麻花钻 镗刀
T08 镗刀
T09 中心钻 T10 机用铰刀 T11 麻花钻
刀具规格 直径
数控车床编程与操作项目四 套类零件加工任务二阶梯孔盲孔类零件加工
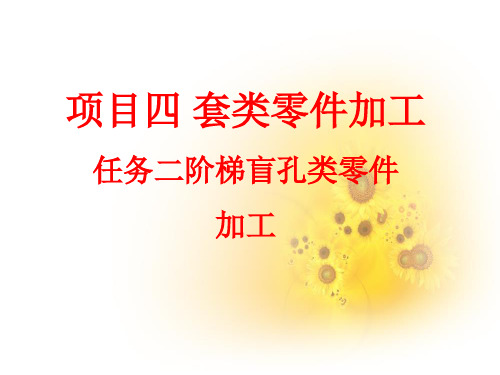
【实施训练】
一、加工准备
1.检查毛坯尺寸; 2.开机、回参考点; 3.装夹刀具与工件。 4.程序输入。把编写好的程序通过数控面板输入到数控机床。
二、对刀操作
内沟槽车刀采用试切对刀,其对刀方法如下: 1.X向对刀 用内沟槽车刀试车一内孔,长度为3~5mm,然后沿+Z方向退出刀具, 停车测量内孔直径,将其值输入到相应刀具长度补偿中。 2.Z向对刀 移动内沟槽车刀使刀尖与工件右端面平齐,可借助金属直尺确定,然后 将位置数据输入到相应刀具长度补偿中。
Z-25. X45. Z-46. G00 X100.Z100.
动作说明 选择01号刀,取消刀补,指定主轴恒转速,每转进给,进给速 度0.2mm/r 刀具快速移到加工起点 设置外圆复合循环粗加工循环参数
外轮廓精加工轨迹
退刀准备换刀
N110 N120 N130 N140 N150 N160 N170 N180 N190 N200 N210 N220 N230 N240 N250 N260 N270 N280 N290 N300 N310 N320 N330 N340 N350
N360 N370 N380 N390 N400 N410 N420 N430
G00 X18. Z2. G01 Z-15.05
X29. G04 U1. X18. F0.2
Z2. G00 X100. Z100.
M30
快速移至起刀点 至切内沟槽处 切内沟槽 暂停 X向退刀 Z向退刀 快速移至换刀点 程序结束
暂停,主轴停,测量 设置转速与进给速度 刀具快速移到循环起点,建立刀补 精加工外轮廓 退刀准备换刀并取消刀补 暂停,主轴停,测量 换内轮廓粗加工刀 设置主轴转速 快速移至循环起点
设置内轮廓复合循环粗加工循环参数
加工中心的孔加工编程及技巧

《加工中心的孔加工编程及技巧》2005年5月25日加工中心的孔加工编程及技巧摘要:孔加工在数控加工中一直占有重要的地位,如何在加工过程中按照合理的工艺编制出正确的加工程序是非常关键的因素。
关键词:孔加工固定循环子程序极坐标一、引言孔加工在数控加工中一直占有重要的地位。
在合理的加工工艺编制好以后如何编制出正确的程序将直接影响到工件是否加工合格。
复杂的孔加工将用到数控系统中的许多功能。
诸如:孔加工固定循环、子程序、极坐标、坐标旋转等。
因此,如何将这些指令灵活应用在加工的程序中将直接关系到程序的合理性。
二、应用实例下面就以一个定位连接板(图1)作为实例,介绍该类程序的编制及技巧。
1、技术要求:1)零件材料:灰铸铁HT2002)加工部位:加粗部分(φ110,2-φ70H7),8-M12深15,18-φ13深20。
3)加工说明:φ70H7预孔为铸造,余量5mm。
基准面A、B、C、D前工序已完成。
夹具形式不用考虑,φ110孔用铣削方式。
4)数控机床:立式加工中心VMC800;数控系统:FANUC 0iM5)按数控工序卡片编制加工中心程序。
6)程序编制方法:固定循环、子程序、坐标系旋转、极坐标指令等图1 定位连接板2、加工工艺3、加工程序主程序O0001;第0001号程序,加工主程序;建立工件坐标系,并运动到φ70H7孔的中心位置N10T02M6;调用02号刀具(粗镗φ);刀具长度正补偿,并运动到安全高度M03S380;主轴正转M08;打开冷却液;调用粗加工固定循环加工φ70H7孔至φ;在位置继续加工G80;取消固定循环N20T03M6;调用03号刀具(φ40立铣刀铣φ110孔);快速定位到φ110孔的中心位置;刀具长度正补偿,并运动到安全高度M3S420;主轴正转;下刀至第一次的深度位置(粗加工)M98P0501;调用0501号子程序S560;下刀至第二次的深度位置(半精加工)M98P0501;调用0501号子程序M01;检查尺寸。
数控铣床加工中心加工工艺编程与操作孔槽类工件加工
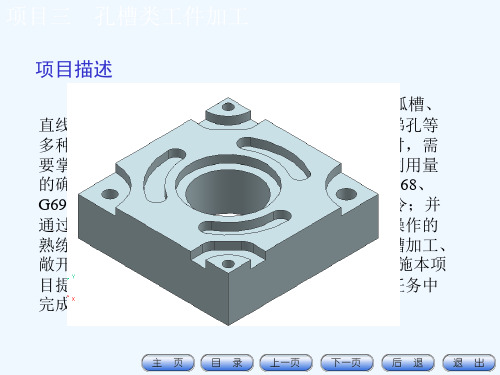
任务1 钻孔加工
4)固定循环的两种返回方式
注意: G98返回初始平面。 G99返回安全平面。
任务1 钻孔加工
固定循环的两种返回方式动画演示
任务1 钻孔加工
G98、G99两种返回方式的应用区别
任务1 钻孔加工
(2)G81、G82钻孔循环指令详解 1)G81、G82指令格式: G81 X Y Z R F K ; G82 X Y Z R P F K ;
任务1 钻孔加工
2、孔加工路线及余量的确定
(3)孔加工时各工序间余量确定
加工工序
加工直径 (毫米)
工序特点
扩孔
10~20 20~50
钻孔后扩孔 粗扩后精扩 钻孔后扩孔 粗扩后精扩
10~20
铰孔
20~30 30~50
50~80
80~100
半精镗
20~80 80~150
精镗
<30 30~130
>130
任务1 钻孔加工 相关知识:
1、孔加工方法选择及常见孔加工刀具 2、孔加工路线及余量的确定 3、钻孔加工固定循环指令
任务1 钻孔加工
1、孔加工方法选择及常见孔加工刀具
序号 1 2 3 4 5 6 7
8
9
加工方案
钻 钻—铰 钻—粗铰(扩)—精铰
钻—扩 钻—扩—铰 钻—扩—粗铰—精铰
粗镗(扩孔) 粗镗(扩孔) —半精镗
暂停、主轴正转 主轴准停 — — 暂停 —
暂停、主轴正转 —
主轴停 主轴正转 暂停、主轴停
暂停
退刀动作 快速进给 快速进给 快速进给
— 快速进给 快速进给 快速进给 切削进给 切削进给 快速进给 快速进给 手动进给 切削进给
用途 高速深孔加工 攻左旋螺纹
数控车(铣)床编程与操作课题1 通孔类零件加工
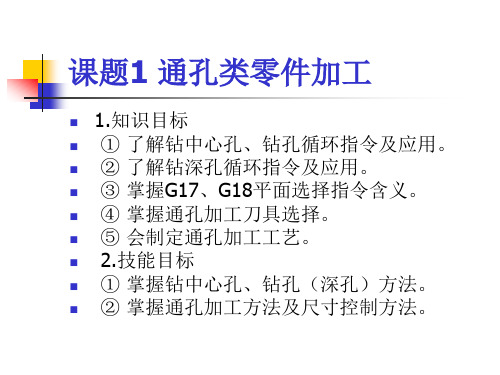
两种方案加工路线差不多。具体步骤见加工工 艺(表3-5)。
3.选择合理切削用量
工步号
1 2 3 4 5 6
7 8
表3-5通孔零件加工工艺
工步内容
刀具号
车右端面
T01
粗、精车φ34、φ30外圆至尺寸
程序段号
程序内容 (法那克系统)
N10 G40 G99 G80 G18
N20 T0505
N30 M3 S600
N40 G00 X17.6 Z3
N50 G01 Z-43 F0.15
N60 X17
N70 G00 Z3
程序内容 (西门子系统) G40 G90 G95 G18 T05 D1 M3 S600 G00 X17.6 Z3 G01 Z-43 F0.15 X17 G00 Z3
3.钻深孔循环指令
(1)指令功能 通过分步钻入直至达到给定的钻削深度, 在每步钻削时通过刀具退回且停顿一定 时间达到断屑或排屑目的,最后刀具以 快速移动速度退回。
(2)指令格式 法那克系统与西门子系统深孔钻削循环 指令见表3-3。
(3)指令使用说明
1)调用钻孔循环G83(LCYC83)前应先指定主轴转速和方向。 2)调用西门子钻孔循环(LCYC83)前,刀具应处于钻孔位置;
刀具沿-X方向进刀,转速为 800r/min 精车φ30外圆 精车台阶面 精车φ34外圆 刀具沿+X方向退出 刀具退回至换刀点 程序停、主轴停、测量 换中心钻 设置钻中心孔转速 刀具移动至循环起点
设置循环参数,调用钻孔循环钻 中心孔
刀具退回至换刀点 换麻花钻 设置钻孔速度 钻头移动至循环起点
孔加工编程与仿真加工介绍课件
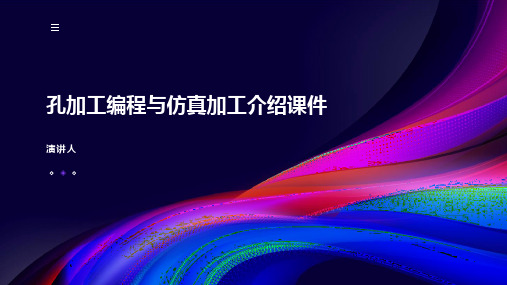
提高加工质量:通过编程和仿真, 提高加工质量,减少质量问题
降低加工成本
01 02 03 04
01
优化加工工艺:通过仿真加工,优 化加工工艺,提高加工效率
02
减少废品率:通过仿真加工,提前 发现并解决加工问题,减少废品率
03
降低设备损耗:通过仿真加工,优 化设备参数,降低设备损耗
自动编程:利用自动编程系统进行孔加工编程, 如FANUC、SIEMENS等 混合编程:结合手工编程和CAM编程,提高编 程效率和精度
编程实例
01
编程步骤:选择孔 加工类型、设定加 工参数、生成加工
程序
02
实例一:钻孔加工, 设定钻头直径、进 给速度、切削深度
等参数
03
实例二:镗孔加工, 设定镗刀直径、进 给速度、切削深度
谢谢
04
提高生产效率:通过仿真加工,缩 短生产周期,提高生产效率
优化加工工艺
1
提高加工效率:通过优化加工工艺, 提高生产效率,降低生产成本。
2
减少废品率:优化加工工艺,减少 废品率,提高产品质量。
3
提高加工精度:优化加工工艺,提 高加工精度,满足产品精度要求。
4
降低能耗:优化加工工艺,降低能 耗,实现绿色生产。
计算机辅助工程(CAE): 利用计算机技术进行工程分
析和优化
4
仿真加工:利用计算机技术 进行加工过程的模拟和优化, 以提高生产效率和产品质量
仿真软件介绍
Mastercam:功能强大, 支持多种数控系统,操作简
单,适合初学者
Cimatron:集成 CAD/CAM/CAE功能,支 持多种数控系统,适合复杂
阶梯孔类零件的工艺分析及数控编程举例(附数控加工工序卡)
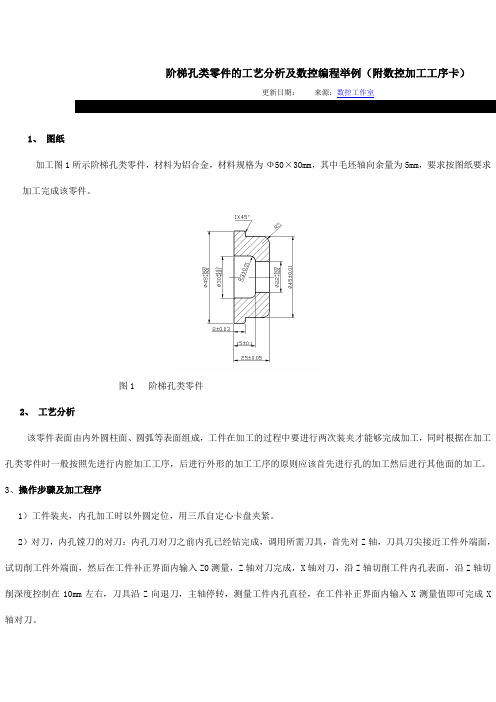
阶梯孔类零件的工艺分析及数控编程举例(附数控加工工序卡)更新日期:来源:数控工作室1、图纸加工图1所示阶梯孔类零件,材料为铝合金,材料规格为Ф50×30mm,其中毛坯轴向余量为5mm,要求按图纸要求加工完成该零件。
图1 阶梯孔类零件2、工艺分析该零件表面由内外圆柱面、圆弧等表面组成,工件在加工的过程中要进行两次装夹才能够完成加工,同时根据在加工孔类零件时一般按照先进行内腔加工工序,后进行外形的加工工序的原则应该首先进行孔的加工然后进行其他面的加工。
3、操作步骤及加工程序1)工件装夹,内孔加工时以外圆定位,用三爪自定心卡盘夹紧。
2)对刀,内孔镗刀的对刀:内孔刀对刀之前内孔已经钻完成,调用所需刀具,首先对Z轴,刀具刀尖接近工件外端面,试切削工件外端面,然后在工件补正界面内输入Z0测量,Z轴对刀完成,X轴对刀,沿Z轴切削工件内孔表面,沿Z轴切削深度控制在10mm左右,刀具沿Z向退刀,主轴停转,测量工件内孔直径,在工件补正界面内输入X测量值即可完成X 轴对刀。
数控加工工序卡3)编写程序1、应用G71内外径粗车复合循环指令进行编程:O0013;G90;(绝对坐标编程)G95;(转化为每转进给)M03S400;(主轴正转400r/min)T0101;(调用一号刀具90°外圆车刀粗加工用)G00X52;Z2;(刀具定位)G71U1R1X0.5Z0.1P10Q11F0.3;(外圆粗车复合循环指令,单边切深为2mm,退刀量为1mm,轴向留量为0.5mm,径向留量为0.1mm)M00;(程序停止)M05;(主轴停转)T0202;(调用二号刀具90°外圆车刀精加工用)G95;(转化为每转进给)G00X50;Z2;(刀具定位)P10G00X35;(刀具快速进给至精加工位置,精加工开始行)G01G42Z0F0.1;(刀具精进给至Z0位置进给量为0.1mm/r)G03X45Z-5R5F0.1;(精加工R5圆弧)G01Z-17;(精加工Ф45尺寸)G00G40X50;(取消刀补)Z100;(刀具退刀至安全位置)M05;(主轴停转)G95;(转化为每转进给)M03S400;(主轴正转400r/min)T0303;(调用三号刀具通孔镗刀粗加工内孔用)G00X18;Z2;(刀具定位)G71U1R1X-0.5Z0.1P12Q13F0.3;(内孔粗车复合循环指令,单边切深为2mm,退刀量为1mm,轴向留量为0.5mm,径向留量为0.1mm)M00;(程序停止)M05;(主轴停转)M03S800;(主轴正转800r/min)T0404;(调用四号刀具通孔镗刀精加工内孔用)G95;(转化为每转进给)G00X18;Z2;(刀具定位)N12G00X30;(刀具快速进给至加工位置)G01G41Z-12F0.1;(精加工Ф30建立刀补进给量为0.1mm/r)G01X22;N13Z-27;(精加工Ф22内孔进给量为0.1mm/r)G00G40X18;(取消刀补)Z100;(刀具退刀至安全位置)M05;(主轴停转)G95;(转化为每转进给)M03S400;(主轴正转400r/min)T0101;(调用一号刀具90°外圆车刀粗加工外圆用)G00X52;Z2;(刀具定位)G71U1R1X0.5Z0.1P14Q15F0.3;(外圆粗车复合循环指令,单边切深为2mm,退刀量为1mm,轴向留量为0.5mm,径向留量为0.1mm)M00;(程序停止)M05;(主轴停转)M03S800;(主轴正转800r/min)G95;(转化为每转进给)T0202;(调用二号刀具90°外圆车刀精加工外圆用)G00X52;Z2;(刀具定位)P14G00X48;(刀具快速进给至加工位置)P15G01G42Z-10F0.1;(精加工Ф48外圆进给量为0.1mm/r)Z100;(刀具退刀至安全位置)M05;(主轴停转)M30;(程序结束返回至程序头)4)试运行5)切削加工。
- 1、下载文档前请自行甄别文档内容的完整性,平台不提供额外的编辑、内容补充、找答案等附加服务。
- 2、"仅部分预览"的文档,不可在线预览部分如存在完整性等问题,可反馈申请退款(可完整预览的文档不适用该条件!)。
- 3、如文档侵犯您的权益,请联系客服反馈,我们会尽快为您处理(人工客服工作时间:9:00-18:30)。
上一页 下一页 返回
任务14孔类零件的编程与加工
次加工的深度,F为进给速度,K为重复次数 • 该循环执行高速深孔钻。它执行间歇进给直到孔的底部,同时从孔
中排除切屑。
上一页 下一页 返回
任务14ห้องสมุดไป่ตู้类零件的编程与加工
• 孔加工动作如图6. 5所示,通过Z轴方向的间断进给可以较容易地实 现断屑与排屑。用U写入第一次的加工深度(增量值且用正值表示), 退刀量d用参数设定
上一页 下一页 返回
任务14孔类零件的编程与加工
• 任务实施 • 一、工艺与编程 • 1.工艺分析 • 分析零件图,根据图6. 1示各孔尺寸精度及表面粗糙度要求,孔1、
孔2加工方法为:钻中心孔一钻孔一扩孔;孔3、孔4加工方法为:钻中心 孔一钻孔一扩孔一铰孔;孔5、孔6加工方法为:钻孔一扩孔一粗锁一精 锁加工。在数控铣床上进行加工,平口钳装夹工件,选取工件上表面 中心O点作为工件原点。 • 2.刀具选择 • 加工方法与刀具选择如表6. 3所示,各刀具切削参数及长度补偿如 表6. 4所示。
上一页 下一页 返回
任务14孔类零件的编程与加工
• 2)返回点平面选择指令G98 , G99 • 由G98 , G99指令决定刀具在返回时达到的平面,G98指令返回到
初始平面,G99指令返回平面R点平面,如图6. 4所示 • 3)孔加工数据 • 3.固定循环指令 • 1)高速深孔钻孔循环指令G73 • 程序格式:G73 X Y Z R Q FK; • 式中,X - Y_为孔的位置,Z为孔底位置,R为参考平面位置,Q为每
的位置)。 • 动作3:孔加工,以切削进给方式执行孔加工的动作。 • 动作4:在孔底的动作,包括暂停、主轴准停、刀具移位等动作 • 动作5:返回到R平面,继续下一步的孔加工 • 动作6:快速返回到初始平面。孔加工完成后,一般应选择初始平面
上一页 下一页 返回
任务14孔类零件的编程与加工
• 固定循环的动作如图6. 2所示。图中用虚线表示的是快速进给,用实 线表示的是切削进给
任务14孔类零件的编程与加工
• 2.评估优化 • 知识拓展 • 1.钻中心孔 • 钻中心孔用于钻孔加工之前,由中心钻来完成。由于麻花钻的横刃
具有一定的长度,引钻时不易定心,加工时钻头旋转轴线不稳定,因 此利用中心钻在平面上先预钻一个凹坑,便于钻头钻入时定心。由于 中心钻的直径较小,加工时主轴转速应不低于1 000 r/min • 2.钻孔 • 钻孔是用钻头在工件实体材料上加工孔的方法。麻花钻是钻孔最常 用的刀具,一般用高速钢制造。
上一页 下一页 返回
孔的加工方法和一般所能达到的精度等级、粗糙度以及合理的加工顺 序见表6. 1
上一页 下一页 返回
任务14孔类零件的编程与加工
• 二、孔加工指令 • 1.固定循环的动作 • 孔加工固定循环通常由以下6个动作组成。 • 动作1: X轴和Y轴定位,刀具快速定位到孔加工的位置上方 • 动作2:快进到R平面,刀具自初始平面快速进给到R平面(准备切削
学习情境6 孔系零件
• 任务14孔类零件的编程与加工 • 任务15螺纹孔类零件的编程与加工 • 任务16孔系零件的编程与加工
任务14孔类零件的编程与加工
• 任务导入 • 对如图6. 1所示零件进行不同要求孔的加工,零件外形尺寸与表面粗
糙度已达到图样要求,材料为45钢 • 知识链接 • 一、孔加工方法 • 孔加工是最常见的零件结构加工之一,应用广泛。在数控铣床(加
上一页 下一页 返回
任务14孔类零件的编程与加工
• 3.加工程序 • 二、技能训练 • ①加工准备。 • ②对刀,设定工件坐标系。 • ③空运行及仿真。 • ④零件自动加工。 • ⑤零件检测。 • ⑥加工结束,清理机床。 • 三、检查与评价 • 1.评分表 • 任务14的评分表见表6.5
上一页 下一页 返回
•
G82 X Y Z R F P K;
• G81指令的加工动作如图6. 6所示。
上一页 下一页 返回
任务14孔类零件的编程与加工
• 4)锁孔循环指令G85 • 程序格式:G85 X Y Z R P F K; • 该循环用于锁孔。孔加工动作如图 6.8所示,X, Y定位,Z轴快速
到R点,以F给定的速度进给到Z点,以F给定速度返回R点,如果在 G98模态下,返回R点后再快速返回初始点。G85一也可用于铰孔。 • 5)精锁孔循环指令G76 • 程序格式:G7 6 X Y Z R Q P FK; • 该循环用于锁削精密孔。孔加工动作如图6. 9所示。 • 4.使用固定循环功能注意事项
• 2.固定循环的指定 • 孔加工固定循环及动作见表6. 2 • 1)数据形式 • 固定循环指令中地址R与地址Z的数据指定与G90或G91的方式选
择有关,图6. 3表示了执行G90或G91指令时的坐标计算方法。选择 G90方式时,R与Z一律取其终点坐标值;选择G91方式时,R是指自初 始点到R点的距离,Z则是指自R点到孔底平面上Z点的距离。
• 2)深孔往复排屑钻孔循环指令G83
• 程序格式:G83 X Y Z R Q F K;
• 该循环用于深孔加工,Q和d与G73循环中的含义相同,与G73略 有不同的是每次刀具间歇进给后,快速退回到R点平面,有的在深孔 加工中排屑。
• 3)钻孔循环指令G81与惚孔循环指令G82
• 程序格式:G81 X Y Z R F K;
• ②形状精度:孔的形状精度,主要是指圆度、圆柱度及孔轴心线的 直线度,一般应控制在孔径公差以内。对于精度要求较高的孔,其形 状精度应控制在孔径公差的1/2一1/3
• ③位置精度:一般有各孔距间误差,各孔的轴心线对端面的垂直度 允差和平行度允差等
• ④表面粗糙度:孔的表面粗糙度要求一般在Ra12. 5一0. 4 um之间 • 实践证明,根据孔的技术要求必须合理选择加工方法和加工步骤。