液压轴向柱塞泵马达工艺的设计与生产线规划
轴向柱塞液压马达的设计(有cad图+三维图)

摘要液压马达是液压系统的一种执行元件,它将液压泵提供的液体压力能转变为其输出轴的机械能。
其主要应用于注塑机械、船舶、卷扬机、工程机械、建筑机械、煤矿机械、矿山机械、冶金机械、船舶机械、石油化工、港口机械等。
液压马达和液压泵从工作原理上来说,都是通过密封工作腔的容积变化来实现能量转换的,只不过液压马达的密封工作腔容积由小变大时输入的是压力油,密封工作腔容积由大变小时排出的是低压油。
液压马达在输入的压力油作用下,直接或间接对转动部件施加压力并产生扭矩,以克服负载实现转动;同时液压马达的回液腔向油箱(开式系统)或泵的吸液口(闭式系统)回液,并降低压力。
不同结构类型的液压马达,其主要的差别是扭矩产生的方式不一样。
本课题的目的是了解斜盘式轴向柱塞液压马达的工作原理,在此基础上,设计一款小型液压马达。
本课题研究的斜盘式轴向柱塞马达属于可逆的液压元件。
同一元件既可作油马达使用,又可作油泵使用。
这种马达具有结构紧凑、体积小、重量轻、工作压力高、效率高等优点。
它同其它元件(阀、液压缸等)可组成闭式或开式液压系统。
对斜盘式轴向柱塞马达的研究,对于液压系统的能耗、提高系统的效率、降低噪音、改善工作性能和保证系统的可靠工作都十分重要。
因此对斜盘式轴向柱塞马达的研究具有重大的价值和意义。
关键词:液压马达;斜盘;液压;柱塞AbstractHydraulic motor is a kind of actuators of hydraulic system, it can convert the fluid pressure provided by hydraulic pump into mechanical energy (turning moment and rotating speed). Hydraulic motor is also called oil motor, and it is mostly applied to Plastic Injection Machinery, shipping, winch, engineering machinery, building machinery, coal mine machinery, mining machinery, metallurgical machinery, marine machinery, petrochemical engineering, harbour machinery and so on. The working principles of hydraulic motor and hydraulic pump are both achieving energy conversion by changing volume of the annular seal space. But the volume of the annular seal space of hydraulic motor becomes bigger and bigger when high pressure oil enters, and the volume of the annular seal space of hydraulic motor becomes smaller and smaller when low pressure oil gets out. Hydraulic motor directly or indirectly puts pressure on rotatable parts and generates torsion under the pressure of high pressure oil, in order to overcome the load to achieve rotation. At the same time, the liquid cavity of hydraulic motor returns oil to oil tank ( open-type system ) or oil suction ( close-type system ), in order to reduce pressure. The main differences among different kinds of hydraulic motors are the ways of generating torque. The purpose of this task is understanding the working principle of axial piston hydraulic motor, and designing a small hydraulic motor on this basis. The axial piston hydraulic motor is reversible hydraulic component. The same element can be used both as hydraulic motor and hydraulic pump. This kind of hydraulic motor has the advantages of compact structure, small volume, light-weight, high working pressure and high workpiece ratio. It can compose closed type hydraulic system and open type hydraulic system with other hydraulic component. The research on axial piston hydraulic motor is very important to reducing energy consumption of hydraulic system, increasing the efficiency of hydraulic system, reducing noise of hydraulic system, improving the working performance of hydraulic system and ensuring the reliability of hydraulic system. So the research on axial piston hydraulic motor has the important value and significance.Key words: hydraulic motor; swash plate; hydraumatic; plunger目录概述 (4)第1章设计方案选定 (13)1.1 液压马达排量计算 (15)1.2确定斜盘倾角α、柱塞直径d、柱塞分布圆直径D和柱塞数z (16)1.3 柱塞的详细设计 (17)1.4 滑靴尺寸的确定 (19)1.5 压盘及斜盘尺寸的确定 (20)1.6 主要零件的材料与技术要求 (22)1.7 缸体的强度计算 (23)1.8 主要零件的材料与技术要求 (24)第2章主要零部件的设计 (27)2.1 花键设计 (27)2.2 弹簧的设计 (28)2.3 导向平键的设计 (29)2.4 中心传动轴的强度校核 (29)2.5 滚动轴承的强度校核 (29)第3章结论 (31)谢辞 (33)参考文献 (34)概述液压马达和液压泵在结构形式上的分类完全一样,都有齿轮式、叶片式、柱塞式、螺杆式等类型。
多排式轴向柱塞液压马达(或液压泵)设计指导书
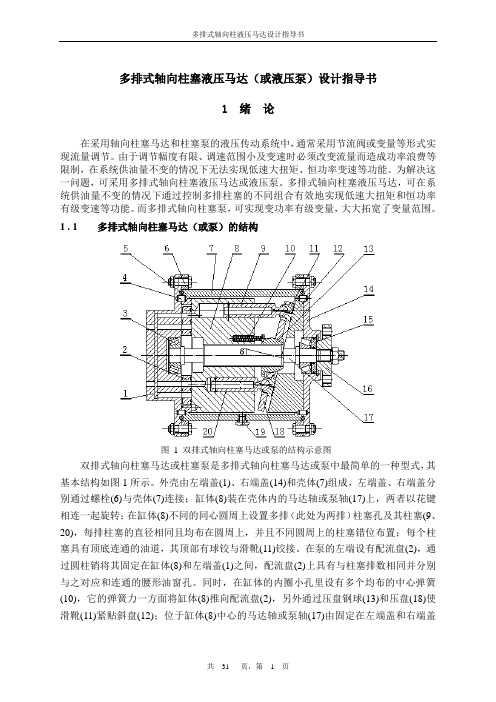
多排式轴向柱塞液压马达(或液压泵)设计指导书1 绪论在采用轴向柱塞马达和柱塞泵的液压传动系统中,通常采用节流阀或变量等形式实现流量调节。
由于调节幅度有限、调速范围小及变速时必须改变流量而造成功率浪费等限制,在系统供油量不变的情况下无法实现低速大扭矩、恒功率变速等功能。
为解决这一问题,可采用多排式轴向柱塞液压马达或液压泵。
多排式轴向柱塞液压马达,可在系统供油量不变的情况下通过控制多排柱塞的不同组合有效地实现低速大扭矩和恒功率有级变速等功能。
而多排式轴向柱塞泵,可实现变功率有级变量,大大拓宽了变量范围。
1 . 1 多排式轴向柱塞马达(或泵)的结构图 1 双排式轴向柱塞马达或泵的结构示意图双排式轴向柱塞马达或柱塞泵是多排式轴向柱塞马达或泵中最简单的一种型式,其基本结构如图1所示。
外壳由左端盖(1)、右端盖(14)和壳体(7)组成,左端盖、右端盖分别通过螺栓(6)与壳体(7)连接;缸体(8)装在壳体内的马达轴或泵轴(17)上,两者以花键相连一起旋转;在缸体(8)不同的同心圆周上设置多排(此处为两排)柱塞孔及其柱塞(9、20),每排柱塞的直径相同且均布在圆周上,并且不同圆周上的柱塞错位布置;每个柱塞具有顶底连通的油道,其顶部有球铰与滑靴(11)铰接。
在泵的左端设有配流盘(2),通过圆柱销将其固定在缸体(8)和左端盖(1)之间,配流盘(2)上具有与柱塞排数相同并分别与之对应和连通的腰形油窗孔。
同时,在缸体的内圈小孔里设有多个均布的中心弹簧(10),它的弹簧力一方面将缸体(8)推向配流盘(2),另外通过压盘钢球(13)和压盘(18)使滑靴(11)紧贴斜盘(12);位于缸体(8)中心的马达轴或泵轴(17)由固定在左端盖和右端盖的圆锥滚子轴承(3)支撑,并在右端与半联轴器(16)相联;缸体与左端盖和右端盖连接处以及右端圆锥滚子轴承外设有密封圈(5、15),并在缸体下部设有出油孔和油塞(19)。
多排式轴向柱塞马达或泵与单排式轴向柱塞马达或泵在结构上相似,可以简单地看成是多个单排式轴向柱塞马达或泵的叠加。
轴向柱塞泵泵体加工工艺规程设计及工装夹具设计
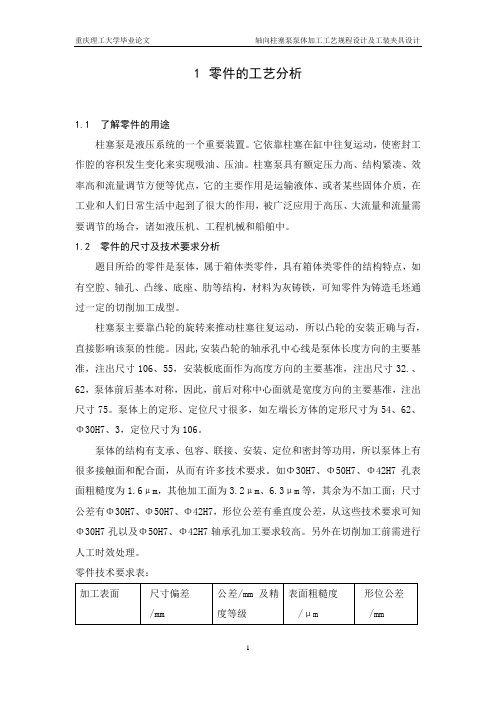
1零件的工艺分析1.1 了解零件的用途柱塞泵是液压系统的一个重要装置。
它依靠柱塞在缸中往复运动,使密封工作腔的容积发生变化来实现吸油、压油。
柱塞泵具有额定压力高、结构紧凑、效率高和流量调节方便等优点,它的主要作用是运输液体、或者某些固体介质,在工业和人们日常生活中起到了很大的作用,被广泛应用于高压、大流量和流量需要调节的场合,诸如液压机、工程机械和船舶中。
1.2 零件的尺寸及技术要求分析题目所给的零件是泵体,属于箱体类零件,具有箱体类零件的结构特点,如有空腔、轴孔、凸缘、底座、肋等结构,材料为灰铸铁,可知零件为铸造毛坯通过一定的切削加工成型。
柱塞泵主要靠凸轮的旋转来推动柱塞往复运动,所以凸轮的安装正确与否,直接影响该泵的性能。
因此,安装凸轮的轴承孔中心线是泵体长度方向的主要基准,注出尺寸106、55,安装板底面作为高度方向的主要基准,注出尺寸32.、62,泵体前后基本对称,因此,前后对称中心面就是宽度方向的主要基准,注出尺寸75。
泵体上的定形、定位尺寸很多,如左端长方体的定形尺寸为54、62、Φ30H7、3,定位尺寸为106。
泵体的结构有支承、包容、联接、安装、定位和密封等功用,所以泵体上有很多接触面和配合面,从而有许多技术要求。
如Φ30H7、Φ50H7、Φ42H7孔表面粗糙度为1.6μm,其他加工面为3.2μm、6.3μm等,其余为不加工面;尺寸公差有Φ30H7、Φ50H7、Φ42H7,形位公差有垂直度公差,从这些技术要求可知Φ30H7孔以及Φ50H7、Φ42H7轴承孔加工要求较高。
另外在切削加工前需进行人工时效处理。
零件技术要求表:经分析,该零件视图、尺寸公差和技术要求正确,完整统一。
结构工艺完整,有利于机加工、装配。
2零件的生产类型本零件属中批量生产,由题目知Q=5000件,则N=Qn(1+α+β)=5500,取α=β=5%。
3拟定工艺路线3.1 定位基准的选择3.1.1 设计基准分析C面是高度方向的设计基准,A面是宽度方向的设计基准,并且C面是Φ50H7和Φ42H7两孔的轴线的设计基准,3.1.2 定位基准的选择基准选择是工艺规程设计中的重要工作之一。
一种新型液压轴向柱塞泵的设计

接 头组件 , 便可 使其 处 于最佳 连接 位置 。
3 )回油管 接座
而 回油管接座 的设计 也 比较独 特 , 其结构 图见 图 3 ,
凸 K 向
图 3 回油 管 接 座 结 构
为锻件结构 , 它一方面起到垂 直通道 的转弯 作用 , 又是单 向阀阀体 , 同时还可用其来旋转 管接 头 , 调整管接 头的方
3 结 论
通 过 以上 分 析 , 经过 实 际装机 使用 后证 明 , 种 并 该 回油 单 向 阀管 接 头设 计 合 理 , 构 紧 凑 , 装 灵 活 方 结 安
便 , 用 安全 可靠 , 全满 足 了主 机 各项性 能 与技术 要 使 完
求, 不失 为一 种优 良的设计 方案 , 已经产 生 了 良好 的经 济 与社 会效 益 , 得推 广 。 值 口
、 e
、 s
席、 — 鼍
赤 、 — 鼍
虑
辟
—舒
虽 然简单 , 却新 颖别 致 , 中回油 螺管 既是 其与泵 体 的 其
结合 件 , 是 回油通 道 , 又 同时 也 是 管 接 头 的旋 转 轴 , 当 接 口与主 机对 接不 上时 , 可拧 松上 端螺母 , 平旋 转管 水
维普资讯
20 06年 第 4期
液 压 与 气动
测定 为 1 ~1 。 0 2级
轴向柱塞泵泵体加工生产线专机及主辅助设备(车基准机床及双头镗床液压系统设计)
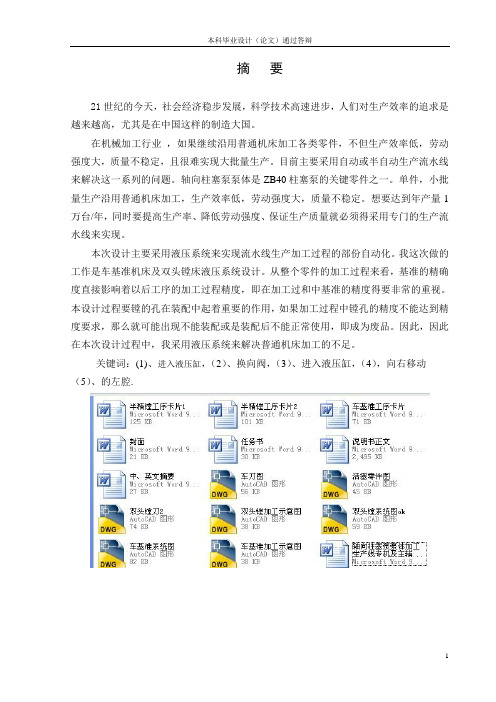
摘要21世纪的今天,社会经济稳步发展,科学技术高速进步,人们对生产效率的追求是越来越高,尤其是在中国这样的制造大国。
在机械加工行业,如果继续沿用普通机床加工各类零件,不但生产效率低,劳动强度大,质量不稳定,且很难实现大批量生产。
目前主要采用自动或半自动生产流水线来解决这一系列的问题。
轴向柱塞泵泵体是ZB40柱塞泵的关键零件之一。
单件,小批量生产沿用普通机床加工,生产效率低,劳动强度大,质量不稳定。
想要达到年产量1万台/年,同时要提高生产率、降低劳动强度、保证生产质量就必须得采用专门的生产流水线来实现。
本次设计主要采用液压系统来实现流水线生产加工过程的部份自动化。
我这次做的工作是车基准机床及双头镗床液压系统设计。
从整个零件的加工过程来看,基准的精确度直接影响着以后工序的加工过程精度,即在加工过和中基准的精度得要非常的重视。
本设计过程要镗的孔在装配中起着重要的作用,如果加工过程中镗孔的精度不能达到精度要求,那么就可能出现不能装配或是装配后不能正常使用,即成为废品。
因此,因此在本次设计过程中,我采用液压系统来解决普通机床加工的不足。
关键词:(1)、进入液压缸,(2)、换向阀,(3)、进入液压缸,(4),向右移动(5)、的左腔.AbstractIn the 21st century, with the steady development of our socio-economy and rapid advance of scientific and technological, people pursuit of efficiency of production become more and more urgent, especially in China, which is a big manufacturing country.In the mechanical processing industry, if we continue to use ordinary machine tool to process various components, it will results in low production efficiency, labor intensity and unsteady quality, which is very difficult to achieve mass production. At present, we mainly use the automatic or semi-automatic production lines to solve those issues. Axial piston pump Body Pump is ZB40 one of the key components. Single pieces and small batch production by using ordinary machine processing result in low productivity, labor intensity and quality instability. Try to achieve annual output of 10,000 units/ year, we should increase productivity, reduce labor intensity and assure quality in a new producing line.This design focuses on hydraulic pipeline systems, which is used to achieve the production process of automation. My work on this design is to design the standard of lathing and the headed benchmark boring machine hydraulic system. From the entire parts of the machining process, the benchmark precision direct impact on the future operations of the processing accuracy, so the accuracy of the benchmarks needs to be very seriously. The design process should be boring holes in the assembly plays an important role. If processing Boring not achieve the accuracy and precision, it is possible that no assembly or assembly after normal use, that is to say the products will become as scrap. Therefore, in this design, I mainly use hydraulic system to solve those deficiencies of ordinary Machining.Keys: (1) Directional Valve), (2) Check Valve, (3) Directional Valve (4) Work Table (5) Cylinder.目录中文摘要 (I)英文摘要 (II)第1章车基准机床液压系统设计 (1)1.1 编制车基准端面和车基准外圆的加工工序过程卡片 (5)1.1.1 分析零件图 (5)1.1.2 确定毛坯尺寸 (6)1.1.3 拟定加工工艺路线 (7)1.1.4 确定工序尺寸及工差 (8)1.1.5 确定切削用量及工时 (9)1.1.6 填写加工工序卡片 (13)1.2 后刀架纵向液压缸设计 (13)1.2.1 负载分析 (13)1.2.2 负载图和速度图的绘制 (14)1.2.3 液压缸主要参数的确定 (15)1.2.4 液压缸的强度校核 (16)1.2.5 稳定性校核 (18)1.2.6 液压缸在不同阶段的压力、流量、功率计算 (19)1.3 后刀架横向液压缸设计 (20)1.3.1 负载分析 (21)1.3.2 负载图和速度图的绘制 (22)1.3.3 液压缸主要参数的确定 (22)1.3.4 液压缸的强度校核 (23)1.3.5 稳定性校核 (25)1.3.6 液压缸在不同阶段的压力、流量、功率计算 (27)1.4 前刀架横向液压缸和纵向液压缸设计 (28)1.5 夹紧液压缸设计 (28)1.5.1 夹紧液压缸负载分析 (28)1.5.2 夹紧液压缸负载图和速度图的绘制 (29)1.5.3 夹紧液压缸主要参数的确定 (30)1.5.4 夹紧液压缸的强度校核 (31)1.5.5 夹紧液压缸稳定性校核 (32)1.5.6 夹紧液压缸在不同阶段的压力、流量、功率计算 (33)1.6 顶尖液压缸设计 (34)1.7 液压系统图的拟定 (34)1.7.1 液压回路的选择 (35)1.7.2 液压回路的综合 (37)1.8 液压元件的选择 (38)1.8.1 液压泵和电动机 (38)1.8.2 阀类元件及辅助元件 (39)1.8.3 油管和油箱 (40)1.9 液压系统的性能验算 (41)第2章双头镗床液压系统设计 (42)2.1 编制双头半精镗加工工序过程卡片 (42)2.1.1 分析零件图 (42)2.1.2 确定毛坯尺寸 (43)2.1.3 拟定加工工艺路线 (44)2.1.4 确定工序尺寸及公差 (44)2.1.5 确定切削用量及工时 (44)2.1.6 填写加工工序卡片 (45)2.2 双头镗床左右动力头液压缸设计 (45)2.2.1 液压缸负载分析 (46)2.2.2 液压缸负载图和速度图的绘制 (47)2.2.3 液压缸主要参数的确定 (47)2.2.4 液压缸的强度校核 (48)2.2.5 液压缸稳定性校核 (50)2.2.6 液压缸在不同阶段的压力、流量、功率计算 (51)2.3 双头镗床夹紧液压缸设计 (51)2.4 双头镗床液压系统图的拟定 (52)2.4.1 双头镗床液压回路的选择 (52)2.4.2 双头镗床液压回路的综合拟定 (54)2.5 双头镗床液压系统元件的选择 (55)2.5.1 双头镗床液压系统液压泵和电动机 (55)2.5.2 双头镗床液压系统阀类元件及辅助元件 (56)2.5.3 双头镗床液压系统油管和油箱 (57)2.6 双头镗床液压系统的性能验算 (58)设计总结 (59)参考文献 (60)致谢 (61)附表 (58)第1章车基准机床液压系统设计车基准加工示意图如下:后刀架工 件顶尖夹具前刀架图1-1 车基准加工示意图上图由五个部分组成,在加工过程中共须要设计六个液压缸实现。
【完整版毕业设计】轴向柱塞泵设计

(此文档为word格式,下载后您可任意编辑修改!)1 绪论1.1 国内CY系列轴向柱塞泵发展概况就市场发展需求来看,我国目前大量使用的CY系列轴向柱塞泵,2003年全国的总产量达到了20万台[1-2]。
这类泵的最大特点是采用大轴承支承缸体,具有压力高、工艺性好、成本低、维修方便等优点,比较适合国情,因此,市场需求量大,也成为当今我国应用最广的开式油路轴向柱塞泵。
CY型轴向泵从1966年开始设计以来,前人总结经验摸索,经过CY14-I,CYI4-lA,CYI4-IB几个发展阶段,每一个发展时期泵的性能、寿命都得到提高,品种也不断丰富。
但是,从1982年CY14-1B轴向泵定型以来,已经过去20余年的时间,该泵的结构发展依旧停滞、变化不大。
由于近年来,世界上各家公司的柱塞泵技术已有长足进步,加上国内市场经济的蓬勃发展,对使用CY14-1B泵的更高要求,迫切需要符合市场经济的轴向柱塞泵,因此对CY14-1B轴向泵进行更新,开发一种噪声更低、自吸性能更好、节能、省料、使用更可靠的轴回柱塞泵就显得迫在眉睫,这就是CY14-1BK轴向柱塞泵[3-7]。
早期的斜盘式轴向泵的压力都只有7MPa,但现代液压传动系统注重效率和经济,均要求更高的压力。
目前市场上的定量斜盘式轴向柱塞泵的压力均已达21--48 MPa,这是因为我们在各自的发展过程中,工业在进步,突破了一些关键技术[8-10]。
2003年产量估计有近20万台,各行各业中应用非常广泛,特别是应用于CY14-1B斜盘型开式轴向柱塞泵。
从1972年开始设计研制,到1982年定型,但是从此之后的20多年的时间里,泵的结构基本是没有什么变化,甚至出现有些厂家生产20余年,没有任何改进。
但是世界上的柱塞泵发展不会因为国内的不进步发展而停止不前的,柱塞泵的各个方面有了长足的进步,然而CY14-1 B轴向泵的使用中也依然发现不少的问题,柱塞在工作是压排油液终了之余,柱塞底腔仍有一些油液未排除,当柱塞进入吸入行程时,这样便导致损失了一部分吸入容积,降低了容积效率。
轴向柱塞泵泵体加工工艺规程设计及工装夹具设计
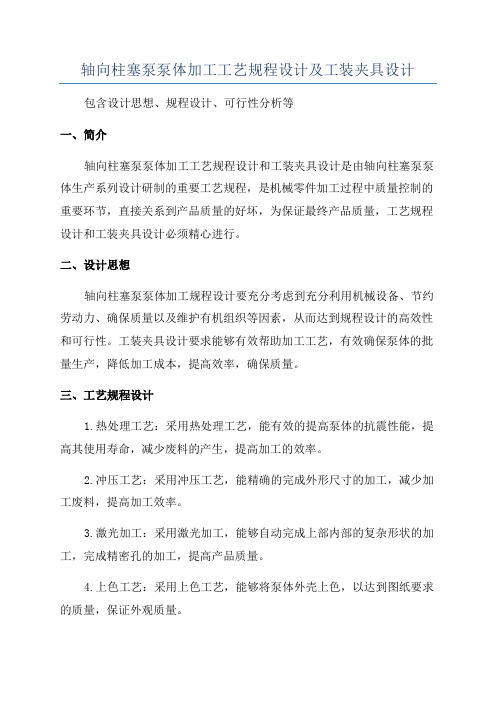
轴向柱塞泵泵体加工工艺规程设计及工装夹具设计
包含设计思想、规程设计、可行性分析等
一、简介
轴向柱塞泵泵体加工工艺规程设计和工装夹具设计是由轴向柱塞泵泵体生产系列设计研制的重要工艺规程,是机械零件加工过程中质量控制的重要环节,直接关系到产品质量的好坏,为保证最终产品质量,工艺规程设计和工装夹具设计必须精心进行。
二、设计思想
轴向柱塞泵泵体加工规程设计要充分考虑到充分利用机械设备、节约劳动力、确保质量以及维护有机组织等因素,从而达到规程设计的高效性和可行性。
工装夹具设计要求能够有效帮助加工工艺,有效确保泵体的批量生产,降低加工成本,提高效率,确保质量。
三、工艺规程设计
1.热处理工艺:采用热处理工艺,能有效的提高泵体的抗震性能,提高其使用寿命,减少废料的产生,提高加工的效率。
2.冲压工艺:采用冲压工艺,能精确的完成外形尺寸的加工,减少加工废料,提高加工效率。
3.激光加工:采用激光加工,能够自动完成上部内部的复杂形状的加工,完成精密孔的加工,提高产品质量。
4.上色工艺:采用上色工艺,能够将泵体外壳上色,以达到图纸要求的质量,保证外观质量。
液压轴向柱塞泵马达工艺设计及生产线规划概述
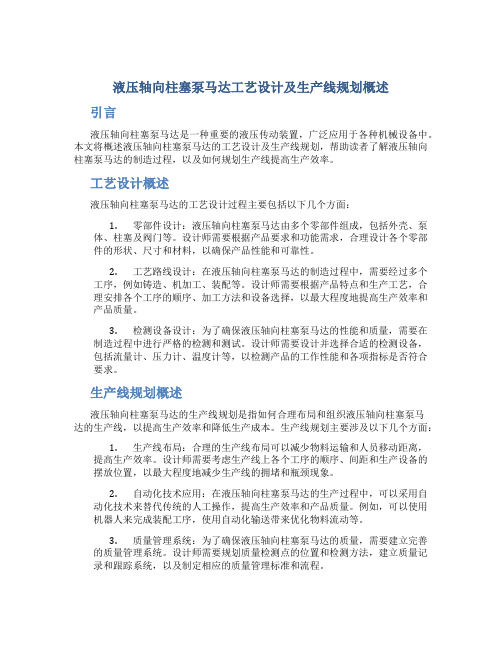
液压轴向柱塞泵马达工艺设计及生产线规划概述引言液压轴向柱塞泵马达是一种重要的液压传动装置,广泛应用于各种机械设备中。
本文将概述液压轴向柱塞泵马达的工艺设计及生产线规划,帮助读者了解液压轴向柱塞泵马达的制造过程,以及如何规划生产线提高生产效率。
工艺设计概述液压轴向柱塞泵马达的工艺设计过程主要包括以下几个方面:1.零部件设计:液压轴向柱塞泵马达由多个零部件组成,包括外壳、泵体、柱塞及阀门等。
设计师需要根据产品要求和功能需求,合理设计各个零部件的形状、尺寸和材料,以确保产品性能和可靠性。
2.工艺路线设计:在液压轴向柱塞泵马达的制造过程中,需要经过多个工序,例如铸造、机加工、装配等。
设计师需要根据产品特点和生产工艺,合理安排各个工序的顺序、加工方法和设备选择,以最大程度地提高生产效率和产品质量。
3.检测设备设计:为了确保液压轴向柱塞泵马达的性能和质量,需要在制造过程中进行严格的检测和测试。
设计师需要设计并选择合适的检测设备,包括流量计、压力计、温度计等,以检测产品的工作性能和各项指标是否符合要求。
生产线规划概述液压轴向柱塞泵马达的生产线规划是指如何合理布局和组织液压轴向柱塞泵马达的生产线,以提高生产效率和降低生产成本。
生产线规划主要涉及以下几个方面:1.生产线布局:合理的生产线布局可以减少物料运输和人员移动距离,提高生产效率。
设计师需要考虑生产线上各个工序的顺序、间距和生产设备的摆放位置,以最大程度地减少生产线的拥堵和瓶颈现象。
2.自动化技术应用:在液压轴向柱塞泵马达的生产过程中,可以采用自动化技术来替代传统的人工操作,提高生产效率和产品质量。
例如,可以使用机器人来完成装配工序,使用自动化输送带来优化物料流动等。
3.质量管理系统:为了确保液压轴向柱塞泵马达的质量,需要建立完善的质量管理系统。
设计师需要规划质量检测点的位置和检测方法,建立质量记录和跟踪系统,以及制定相应的质量管理标准和流程。
结论液压轴向柱塞泵马达的工艺设计和生产线规划对于产品的性能和质量有着重要影响。
液压轴向柱塞泵马达工艺设计及生产线规划
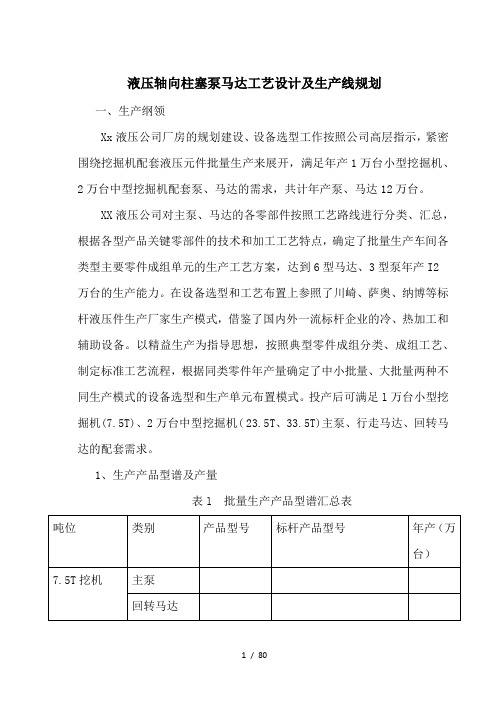
液压轴向柱塞泵马达工艺设计及生产线规划一、生产纲领Xx液压公司厂房的规划建设、设备选型工作按照公司高层指示,紧密围绕挖掘机配套液压元件批量生产来展开,满足年产1万台小型挖掘机、2万台中型挖掘机配套泵、马达的需求,共计年产泵、马达12万台。
XX液压公司对主泵、马达的各零部件按照工艺路线进行分类、汇总,根据各型产品关键零部件的技术和加工工艺特点,确定了批量生产车间各类型主要零件成组单元的生产工艺方案,达到6型马达、3型泵年产I2万台的生产能力。
在设备选型和工艺布置上参照了川崎、萨奥、纳博等标杆液压件生产厂家生产模式,借鉴了国内外一流标杆企业的冷、热加工和辅助设备。
以精益生产为指导思想,按照典型零件成组分类、成组工艺、制定标准工艺流程,根据同类零件年产量确定了中小批量、大批量两种不同生产模式的设备选型和生产单元布置模式。
投产后可满足l万台小型挖掘机(7.5T)、2万台中型挖掘机( 23.5T、33.5T)主泵、行走马达、回转马达的配套需求。
1、生产产品型谱及产量表l 批量生产产品型谱汇总表2、生产单元零件类型及产量3、工作时间及设备利用率核算原则按设备全年有效工作时间300天,每天3班制,有效工作时间20小时计算,全年有效工作时间6000小时。
4、外协、外购零件类型锻、铸件毛坯热处理、粗加工工序、弹簧、冲压件、简单零件外协;标准件、轴承、密封件外购。
二、厂房工艺布置简述1、批量生产车间制造流程如图l厂房设计、施工时,结合液压件精密制造的工艺要求,各生产单元、辅助间、功能区域等均按其实际使用需求进行设计。
设备基础、防振、恒温、恒湿、防爆、抽风等工艺要求尚需要及厂房的设计部门作充分沟通。
困尚未最终确定设备型号和台数,厂房水电气用量及管网布置暂无法确定。
2.工艺布置原则工艺布置原则简述如下:2. I 成组技术原则:对零件的结构、加工工艺进行分析,对相似的零件和工艺流程进行统计,并布置在同一加工单元,采用同类型生产设备集中生产,减少物流、装夹、换刀等待时间,提高生产效率和设备利用率。
柱塞式液压马达项目计划书
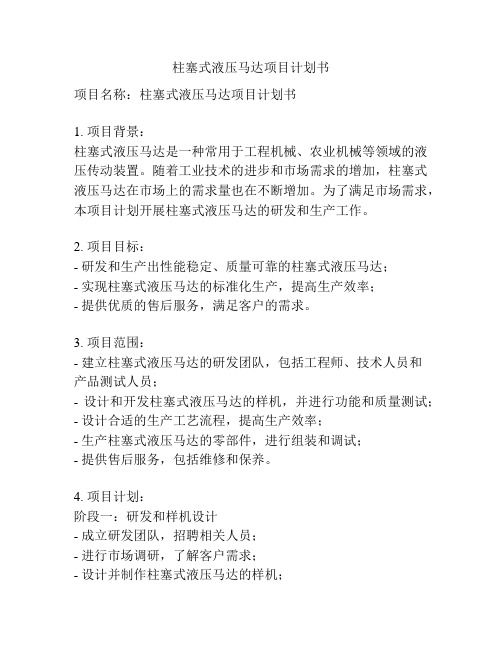
柱塞式液压马达项目计划书项目名称:柱塞式液压马达项目计划书1. 项目背景:柱塞式液压马达是一种常用于工程机械、农业机械等领域的液压传动装置。
随着工业技术的进步和市场需求的增加,柱塞式液压马达在市场上的需求量也在不断增加。
为了满足市场需求,本项目计划开展柱塞式液压马达的研发和生产工作。
2. 项目目标:- 研发和生产出性能稳定、质量可靠的柱塞式液压马达;- 实现柱塞式液压马达的标准化生产,提高生产效率;- 提供优质的售后服务,满足客户的需求。
3. 项目范围:- 建立柱塞式液压马达的研发团队,包括工程师、技术人员和产品测试人员;- 设计和开发柱塞式液压马达的样机,并进行功能和质量测试;- 设计合适的生产工艺流程,提高生产效率;- 生产柱塞式液压马达的零部件,进行组装和调试;- 提供售后服务,包括维修和保养。
4. 项目计划:阶段一:研发和样机设计- 成立研发团队,招聘相关人员;- 进行市场调研,了解客户需求;- 设计并制作柱塞式液压马达的样机;- 进行功能和质量测试。
阶段二:生产工艺设计- 分析样机测试结果,优化设计;- 设计合适的生产工艺流程,提高生产效率;- 确定生产设备和材料的采购计划;- 建立质量控制体系,确保产品质量。
阶段三:批量生产和售后服务- 进行柱塞式液压马达的零部件生产;- 进行组装和调试;- 提供售后服务,包括维修和保养;- 监控产品质量,并对生产过程进行改进。
5. 项目资源:- 人力资源:研发团队成员、生产工人、售后服务人员;- 物力资源:办公设备、生产设备、原材料;- 财务资源:项目资金、投资者支持。
6. 风险管理:- 技术风险:研发过程中可能出现技术难题,需要及时解决;- 市场风险:市场需求可能发生变化,需要及时调整产品设计;- 生产风险:生产过程中可能出现质量问题,需要加强质量控制。
- 1、下载文档前请自行甄别文档内容的完整性,平台不提供额外的编辑、内容补充、找答案等附加服务。
- 2、"仅部分预览"的文档,不可在线预览部分如存在完整性等问题,可反馈申请退款(可完整预览的文档不适用该条件!)。
- 3、如文档侵犯您的权益,请联系客服反馈,我们会尽快为您处理(人工客服工作时间:9:00-18:30)。
液压轴向柱塞泵马达工艺设计及生产线规划一、生产纲领Xx液压公司厂房的规划建设、设备选型工作按照公司高层指示,紧密围绕挖掘机配套液压元件批量生产来展开,满足年产1万台小型挖掘机、2万台中型挖掘机配套泵、马达的需求,共计年产泵、马达12万台。
XX液压公司对主泵、马达的各零部件按照工艺路线进行分类、汇总,根据各型产品关键零部件的技术和加工工艺特点,确定了批量生产车间各类型主要零件成组单元的生产工艺方案,达到6型马达、3型泵年产I2万台的生产能力。
在设备选型和工艺布置上参照了川崎、萨奥、纳博等标杆液压件生产厂家生产模式,借鉴了国内外一流标杆企业的冷、热加工和辅助设备。
以精益生产为指导思想,按照典型零件成组分类、成组工艺、制定标准工艺流程,根据同类零件年产量确定了中小批量、大批量两种不同生产模式的设备选型和生产单元布置模式。
投产后可满足l万台小型挖掘机(7.5T)、2万台中型挖掘机( 23.5T、33.5T)主泵、行走马达、回转马达的配套需求。
1、生产产品型谱及产量表l 批量生产产品型谱汇总表2、生产单元零件类型及产量3、工作时间及设备利用率核算原则按设备全年有效工作时间300天,每天3班制,有效工作时间20小时计算,全年有效工作时间6000小时。
4、外协、外购零件类型锻、铸件毛坯热处理、粗加工工序、弹簧、冲压件、简单零件外协;标准件、轴承、密封件外购。
二、厂房工艺布置简述1、批量生产车间制造流程如图l厂房设计、施工时,结合液压件精密制造的工艺要求,各生产单元、辅助间、功能区域等均按其实际使用需求进行设计。
设备基础、防振、恒温、恒湿、防爆、抽风等工艺要求尚需要与厂房的设计部门作充分沟通。
困尚未最终确定设备型号和台数,厂房水电气用量及管网布置暂无法确定。
2.工艺布置原则工艺布置原则简述如下:2. I 成组技术原则:对零件的结构、加工工艺进行分析,对相似的零件和工艺流程进行统计,并布置在同一加工单元,采用同类型生产设备集中生产,减少物流、装夹、换刀等待时间,提高生产效率和设备利用率。
可实现同类机床多品种批量柔性制造。
2 .2 根据批量大小决定是否采自动上下料机构:根据每种零件的年产量大小、零件重量、装夹定位复杂程度、单件加工时间等决定上下料方式。
年产量小于5万件的零部件属于中小批量生产,年产量大于5万件小于10万问的属于中批量生产,中小批量生产零件选用手工上下料方式。
年产量大干10万件的零件生产属于大批量生产,采用自动上下料方式。
2.3 单机、多机实现柔性制造:对零件重量重、装夹定位复杂、工序如工时间长的零件,采用工序集中原则来减少装夹次数和时间。
同类型零件在一种机床或两种类型机床上全部加工完成。
选用的卧式加工中心、立式车削中心均具备“多工作台+中央刀库+刀具管理+在线尺寸检测+中央生产管理系统”等功能,根据机床工作台数量的多少,可同时加工几种类型品种的零件,采用手工上下料,不需更换夹具,可实现24小时无间断加工2.4 对滚齿、插齿、珩磨、研磨、去毛刺等非杯设备,由于加工零件种类繁多,年生产量均属于中小批量生产,装夹定位方式复杂,采用手动上下料方式。
2. 5 精密磨削单元:采用恒温、无尘、封闭作业。
对于大批量生产的零件采用自动上下料方式,配置自动检测功能,可实现8 -24小时无人化加工。
对于中小批量的零件采用手工上下料方式。
2 .6 各生产单元加工的所有零件的位置尺寸精度采用线后检测。
2 .7 生产单元布置原则:对壳体、端盖类零件采用“一个流”布置原则。
对于中小批量的精密零件生产采用U型布置,实现物流最短、一人多机,采用手动上下料方式,工序和机床之间采用滑道传输。
对大批量牛产的零件实现自动上下料,根据不同零件的加工材料、单件加工成本、一次投资大小等因素综合考虑,决定单元自动化程度。
实现8-16小时无人加工。
2 8 热处理生产线采用同类热处理方法、设备集中组线,实现自动上下料方式。
热处理封闭作业,不影响其它生产单元。
2 9 建立泵、马达装配生产线,采用恒温、无尘、封闭作业。
具备在线尺寸、扭矩、气密性、装配防错、漏装检测等功能,可以实现年装配20万台泵、马达的生产能力。
2.10出厂试验单元建立泵、行走马达、回转马达3条试验线,测试数据计算机自动采集,实现快速装卸,试验台对称布置实现一人两机操作。
2 .11 喷漆单元具备清洗功能,采用机器人自动喷漆,喷漆线采用封闭式作业,采用天然气加热烘干,人工上下料方式,具备年产15万台的生产能力。
三、关键生产单元典型工艺及布置示意图批量车间内各机加单元(壳体、端盖、斜盘(包括制动油缸)、控制阀体、主轴、缸体和球铰、柱塞滑靴、配流盘和回程盘、阀芯阀套等机加单元)、热处理单元、装配单元、试验单元、喷漆和包装单元为批量生产的核心单元。
3.1端盖加工单元3.1.1、端盖类零件年需求量统计主机配套主机数量端盖品种年需求量3.1.2、单元描述根据端盖单元各品种年需求量统计,共计有X种,年需求量共计XX万件。
属于多品种中、小批量,根据组线思路的不同,有两种加工模式:3.1.2.1.单机FMS柔性制造模式:设备为单机多托盘形式,殴各与设备间托盘不互相流通,每台设各可以同时装夹几型产品,同类型端盖零件所有加工工序可在一台设备上完成,实现单机柔性制造。
根据端盖类零件的加工特征(单工序加工时间超过30分钟),所以采用手动上下料方式,工装、刀具准备不占用加工时间,可实现24小时不间断加工。
关键尺寸公差可以实现线内自动检测,位置尺寸公差线外手动检测。
3.1.2.2、多机FMS柔性制造模式:设备为多机多托盘形式,所有设备配置双托盘,采用手动上下料方式。
其余托盘都集中在托盘库中,通过多任务管理系统可以将任意一个托盘通过自动输送的方式调配到单元中任何一台设备上进行加工,因此多机多托盘形式的制造单元具备更大的柔性,可实现24小时连续加工。
两种加工模式优劣对比见表3。
3.1. 3、加工零件类型(共计XXX类)图二零件示意3.1.4、工艺流程图图三端盖各零件典型工艺流程3.1.5、端盖加工单元设备示意图 单机FMS 柔性制造模式多工作台卧加多工作台卧加多工作台卧加多工作台卧加多工作台卧加多工作台卧加多工作台卧加多工作台卧加多工作台卧加多工作台卧加多工作台卧加多工作台卧加多工作台卧加多工作台卧加清理压力清洗清理热能去毛刺除锈清洗立式珩磨精细清洗周转区图四端盖单机柔性单元平面布置示意图多机FMS 柔性制造模式双工作台卧加双工作台卧加双工作台卧加双工作台卧加双工作台卧加双工作台卧加双工作台卧加双工作台卧加双工作台卧加双工作台卧加清理压力清洗清理热能去毛刺除锈清洗立式珩磨精细清洗周转区托盘库带托盘转运机械人上料上料下料下料图五端盖多机柔性单元平面布置示意图3.2 壳体加工单元主机配套主机数量端盖品种年需求量3.2.2 单元描述根据壳体单元壳体品种年产量统计,共计有X种,年产量共计XXX万件。
壳体单元属于多品种中、小批量生产模式,壳体零件单序加工时间较长(介于15--40分钟),所以采用手动上下料、起重设备辅助的方式。
所有设备选用双工作台或多工作台形式,装夹、上下料不占用加工时间,从而实现连续不间断加工。
根据零件结构和产量,本单元预布置3条生产线(见图9或图10)。
卧式加工中心的选型有单机多工作台和多机多工作台两种形式,具体分析参照端盖单元。
清洗等设备与端盖单元共用,设备与设备之间采用滑道传输。
壳体单元的立车造型具有两种模式,根据零件重量选用不同立式车削中心。
(1)对零件加上装夹夹具较重(中挖行走壳体、回转壳体、中挖主泵中间体及斜盘座超过50KG)的选用单机多工作台立式车削中心;(2)对零件加上装夹夹具较轻(中挖回转端盖、小挖行走、回转壳体、小挖主泵壳体、端盖)的选用双主轴双工作台立车。
并在设备选型的时候注重单机多工作台立式车削中心和双主轴双工作台立车的通用性,这两类设备都能覆盖9种零件,保证设备的通用性,批量生产中如单机设备发生故障,生产任务可及时调配。
立车具加工模式优劣对比见表5。
3.2.3 壳体单元加工零件图3.2.4 壳体典型工艺流程图图7 中挖壳体类工艺流程3.2.6 立车方案优劣对比主机配套主机数量端盖品种年需求量3.3.2 单元描述斜盘单元零件共计种,最大单品种零件年需求量为万件,其余单件品种零件产量为万件。
属于多品种、中、小批量生产模式,采用手动上下料方式。
为提高设备对多品种生产的适应性,本单元选用设备类型为数控车床、立式加工中心、外圆磨床、平面磨床、平面研磨机等,为了减少装夹占用时间,选用双工作台+四轴立加。
上下工序、不同设备间的物流传输采用滑道。
3.3.3 斜盘加工单元零件图11 斜盘加工单元加工零件示意图3.3.4 斜盘加工单元典型工艺流程图清洗中检氮化研平面清洗检验入库研平面清洗检验软氮化清洗检验入库磨平面去毛刺铣平面(双工作台立加,2序)清理毛坯表8 斜盘单元加工设备清单4超声波清洗机35 CTG\DURR\MAFAC工序间清洗,用于去除零件表面油脂、杂质5 平面研磨机 5.5 莱玛特研磨大平面6 平面磨床16 斯图特磨平面7 数控外圆磨60 斯图特磨斜盘跑道8 精细清洗机80 CTG\DURR\MAFAC零件终清洗,去除工作表面的油脂、杂质主机配套主机数量端盖品种年需求量控制阀体单品种产量小于万件,属于多品种小批量生产模式,要求生产设备具备柔性制造能力。
本单元采用多工作台卧式加工中心,采用手工上下料方式,上下料不占用设备加工时间。
阀体在一台设备上两序加工完成,减少物流量。
珩磨、清洗等特种加工设备与端盖加工单元台用,设备与设备之间采用滑道传输。
3.4.3 阀体加工单元典型零件图15 典型阀体类零件示意图3.4.4典型工艺流程图图16 阀体典型工艺流程图图17 阀体加工单元设备布置示意图3.4.6 阀体加工单元设备清单3.5 主轴加工单元主机配套主机数量端盖品种年需求量3.5.2 单元描述根据主轴单元年产量统计,主轴有两种加工模式:(1)工序相对分散,采用手动上、下料,选用数控车床加工(见工艺流程图19);(2)工序相对集中,车削加工采用自动上、下料方式,选用双主轴、取刀塔车削中心(见工艺流程图20),所有车削工序一次加工完毕。
滚(插)齿、去毛刺、清洗等工序所需设备均为非标特种设备,优先采用国产数控高速加工设备。
非标特种设备采用手动上、下料,设备之间采用滑道输送,实现一人多机生产。
3.5.3主轴加工单元单元典型零件下料调质铣端面钻中心孔车外形滚花键车内孔滚花键/插花键去毛刺中间检验清洗氮化精磨外圆端面清洗最终检验油封入库行走马达/中挖主泵主轴两种布置模式优劣对比见表103.6 缸体加工单元主机配套主机数量端盖品种年需求量3.6.2 单元描述3.6.2.1 缸体加工单元根据零件材料的不同布置为两条生产线:铸铁材料缸体生产线(含小挖泵马达、中挖回转)和双台金材料缸体生产线(含中挖泵、行走),详细流程见工艺流程图2。