常压蒸馏塔的温度控制
化学工艺石油常压蒸馏

不致过高,或保证塔内有尽可能高
的真空度
4.中段循环回流
优点:
设计塔:可以减小塔径 正在生产的塔:可以提高 处理量
使塔内汽、液相负荷分布均匀 可以更加合理地利用回流热量 不足: 是原油换热 的主要热源
打入冷回流,需增加换热板
循环回流段以上内回流减少了,塔板效率降低 投资高,制造工艺复杂
二、回流方式
采用各种回流的目的
保证精馏塔具有精馏的作用
取走塔内剩余热量
控制和调节塔内各点温度
保证塔内汽液相负荷分布均匀 保证各产品质量
1、塔顶冷回流
部分过冷液体从塔顶返回塔内,用于控制塔顶 温度,提供塔内精馏所需回流,并从塔顶取走 剩余热量; 当只采用塔顶冷回流时,冷回流的取热量应等 于全塔总剩余热量; 当回流热量一定时,冷回流的温度越低,冷回 流的流量就越低; 一般常压塔的汽油冷回流温度为30~40℃
循环回流:是从塔内某个位置抽出部分液体,经换 热冷却到一定温度后再返回塔内,物流 在整个过程中处于液相,只是在塔内外 循环流动,借助于换热器取走部分剩余 热量
3.塔顶循环回流
塔顶循环回流主要应用于以下情况:
塔顶回流热量大,考虑回收这部分 热量,以降低装置能耗 塔顶馏出物中含有较多的不凝气, 使搭顶冷凝冷却器的传热系数降低 要求尽量降低塔顶馏出线及冷却系 统的流动压力降,以保证塔顶压力
3.汽提蒸汽用量
汽提蒸汽一般都是用温度为400~450℃的过热水蒸气 目的 ★ 侧线汽提:驱除低沸点组分,提高产品闪点,改善分 馏精确度; ★ 常压塔底汽提:降低塔底重油中<350℃的馏分含量,
以提高轻质油收率,同时也减轻了塔的负荷;
★ 减压塔底汽提:降低汽化段的油气分压,尽量提高减 压塔的拔出率 用量 汽提蒸汽一般要占汽提油品重量的2~4%
常压塔温度控制系统

⑷ 注意工艺操作的合理性、经济性。
简单控制系统由四个基本环节做成,被控对象、测量变送装置、控制器、 执行器四个部分的传递函数分别为Go(S),Gm(S),Gc(S),Gv(S)。简单控制 系统是最基本的控制系统。约占工业控制系统的80%以上。只有在简单 控制系统不能满足生产更高要求的情况下,才用复杂控制系统。 单回路控制系统是最基本的控制系统,由于其结构简单,投资少,易于 调整,操作维护比较方便,又能满足此系统的控制要求。所以本套系统 可采用简单的单回路控制。系统的流程图如下:
在串级控制系统中,由于引入了一个副回路,不仅能及早克 服进入副回路的扰动,而且又能改善过程特性。副调节器具有 “粗调”的作用,主调节器具有“细调”的作用,从而使其控 制品质得到进一步提高。当以塔顶采出液为主要产品时,往往 以精馏段的温度为衡量质量的间接指标,这时可选精馏段某点 温度作为被控参数(间接反应塔顶采出液的纯度),以回流量 QL作为被控变量做成单回路控制系统,亦可以组成串级控制系 统。
(2)当干扰首先进入精馏段时,例如进料产生的干扰首先引起精 馏段和塔顶参数的变化,故用精馏段温度控制比较及时,动态响应 比较迅速。
(3)串级控制系统的流量回路岁回流罐液位与压力、精馏塔内压 力等于干扰对回流量的影响有较强的抑制,可实现被控参数的高精 度控制。
一线温度控制系统设计
对于炼油厂常压塔温度控制系统中一线温度的检测,可以用简单 控制系统实现,生产过程是按质量指标进行控制,按理应该以直接 反应产品质量的变量作为被控参数,但有时由于缺乏检测直接反应 产品质量参数的有效手段,无所岁产品质量作为直接检测;所以对 炼油厂精馏塔出口产品的检测就转化为对一线温度的检测,蒸馏塔 的一线出口温度是被控参数,从而间接检测产品质量。温度变送器 TT将采集到的出口温度的信号送入温度控制器TC,控制器通过控制调 节阀的开度,进而调节了进入精馏塔的冷凝水的量,从而控制了温 度,使之保持在被控参数上。
常减压蒸馏原理

常减压蒸馏原理摘要:常压蒸馏是石油加工的“龙头装置”,后续二次加工装置的原料,及产品都是由常减压蒸馏装置提供。
常减压蒸馏主要是通过精馏过程,在常压和减压的条件下,根据各组分相对挥发度的不同,在塔盘上汽液两相进行逆向接触、传质传热,经过多次汽化和多次冷凝,将原油中的汽、煤、柴馏分切割出来,生产合格的汽油、煤油、柴油及蜡油及渣油等。
(1)由此掌握常减压蒸馏原理对于从事相关工作的人员来说显得尤其重要。
本文先从蒸馏的基本概念和原理说起,然后分别对常压蒸馏、减压蒸馏的原理做一个简要介绍。
关键词:蒸馏、基本概念和原理、常压蒸馏、减压蒸馏一、蒸馏的基本概念和原理1、基本概念1.1饱和蒸汽压任何物质(气态、液态和固态)的分子都在不停的运动,都具有向周围挥发逃逸的本领,液体表面的分子由于挥发,由液态变为气态的现象,我们称之为蒸发。
挥发到周围空间的气相分子由于分子间的作用力以及分子与容器壁之间的作用,使一部分气体分子又返回到液体中,这种现象称之为冷凝。
在某一温度下,当液体的挥发量与它的蒸气冷凝量在同一时间内相等时,那么液体与它液面上的蒸气就建立了一种动态平衡,这种动态平衡称为气液相平衡。
当气液相达到平衡时,液面上的蒸气称为饱和蒸汽,而由此蒸气所产生的压力称为饱和蒸汽压,简称为蒸汽压。
蒸气压的高低表明了液体中的分子离开液面气化或蒸发的能力,蒸气压越高,就说明液体越容易气化。
在炼油工艺中,根据油品的蒸气压数据,可以用来计算平衡状态下烃类气相和液相组成,也可以根据蒸气压进行烃类及其混合物在不同压力下的沸点换算、计算烃类液化条件等。
1.2气液相平衡处于密闭容器中的液体,在一定温度和压力下,当从液面挥发到空间的分子数目与同一时间内从空间返回液体的分子数目相等时,就与液面上的蒸气建立了一种动态平衡,称为气液平衡。
气液平衡是两相传质的极限状态。
气液两相不平衡到平衡的原理,是气化和冷凝、吸收和解吸过程的基础。
例如,蒸馏的最基本过程,就是气液两相充分接触,通过两相组分浓度差和温度差进行传质传热,使系统趋近于动平衡,这样,经过塔板多级接触,就能达到混合物组分的最大限度分离。
常压蒸馏操作

200万吨/年常减压装置1、工艺流程说明装置流程简述约40℃的原油由设在罐区的原油泵(P-101/1.2)送入装置,原油进入装置后进入换热网络I 段,I段换热网络分为两路,在第一路原油经原油—减一及减顶循换热器(E-101/1.2)、原油—常一线换热器(E-102)、原油—常一中(二)换热器(E-103/1.2)、原油-减一中换热器(E-128)、原油加热器(原减五原油换热器E-110)、原油—减二线换热器(E-104)换热到134℃,在第二路原油经原油—常顶循换热器(E-105/1.2)、原油—常二线换热器(E-106)、原油—常三线(二)换热器(E-107)、原油—减三线(二)换热器(E-108)、原油加热器(E-114)、原油-减渣(五)换热器(E-109)换热到135℃,原油出换热网络I段后合并成一路进入电脱盐脱水系统,原油脱盐脱水系统采用二级交直流电脱盐工艺进行深度脱盐脱水。
脱盐脱水后原油进入换热网络II段,II段换热网络分为两路,在第一路脱后原油经原油—常二中(二)换热器(E-111/1.2)、原油—减渣(三)换热器(E-112/1.2)、原油—常三线(一)换热器(E-113)换热到213℃,在第二路脱后原油经原油—减四线(二)换热器(E-115)、原油—常一中(一)换热器(E-116/1.2)、原油—减渣(四)换热器(E-117)、原油—常二中(一)换热器(E-118/1.2)、原油—减三线(一)换热器(E-119)换热到213℃,原油出换热网络II段后合并成一路进入初馏塔(C-101)初馏,初馏塔顶油气经初顶油气空冷器(EC-101/1.2)、初顶后冷器(E-141/1.2)冷凝冷却至40℃进入初顶汽油回流罐(D-106)进行油气、油、水三相分离,分离出的初顶汽油由初顶回流泵(P-102/1.2)抽出,一部分作为初顶冷回流打回到初馏塔顶,另一部分作为汽油组分和常顶汽油汇合后进入电精制系统精制;分离出的初顶瓦斯和常顶瓦斯、减顶瓦斯汇合后经压缩机缓冲罐(D-129)分液后进入压缩机(C-136)送至三催化回收,不回收时分离出的初顶瓦斯和常顶瓦斯汇合后经初常顶瓦斯分液罐(D-104)分液后作为常压炉(F-101)的燃料,分离出的含硫污水和常顶分离出的含硫污水汇合进入电脱盐注水罐(D-112)作为电脱盐注水,硫化物与氨氮含量超标的含硫污水送至酸性水汽提装置。
《常压蒸馏操作》课件

应用场景
石油化工
食品工业
常压蒸馏是石油化工领域的重要工艺 流程之一,用于将原油分离成不同沸 点的油品,如汽油、煤油、柴油等。
常压蒸馏在食品工业中用于提取和分 离植物精油、果汁、酒类等,提高产 品的品质和风味。
精细化工
在精细化工领域,常压蒸馏用于分离 和纯化有机溶剂、高纯度气体、香料 等,以满足不同产品的生产需求。
05
常压蒸馏操作案例分析
案例一:某石油加工厂的常压蒸馏操作
总结词
大规模、工业级别
详细描述
该石油加工厂采用常压蒸馏工艺来分离原油 ,通过加热和冷凝的方法将不同沸点的油品 进行分离。该案例重点介绍了大规模工业生 产中的常压蒸馏操作流程、设备配置和维护
要点。
案例二:某化学实验室的常压蒸馏操作
总结词
实验级别、精细控制
冷凝与收集
冷凝器选择
根据溶剂的性质和工艺要求,选择合适的冷凝器,确保冷凝 效果良好。
收集方式
根据需要,可采用分液漏斗、集油器或油水分离器等设备进 行溶剂收集。
残渣与废水处理
残渣处理
对蒸馏后的残渣进行干燥、破碎、压 榨等处理,回收其中的有当处 理,如沉淀、过滤、生化处理等,以 符合环保要求。
历史与发展
历史
常压蒸馏技术起源于古代的炼油和酿酒工艺,随着工业技术的发展,常压蒸馏技 术不断改进和完善,成为现代石油化工和精细化工领域的重要分离技术。
发展
随着环保要求的提高和能源消耗的增加,常压蒸馏技术不断向高效、节能、环保 的方向发展,新型的常压蒸馏设备和工艺不断涌现,提高了分离效率和能源利用 率。
总结词
防爆与安全措施是常压蒸馏操作中的重要环节,直接 关系到人员和设备的安全。
详细描述
常减压冷态开车操作难点解答一---塔顶温度不小于92度.

如果想调节此参数, 我们必须要明确此参数有 常压塔各个塔板的温 哪些影响因素 条件:常顶温度≮92℃ 度变化与塔进料温度变化 是一一对应的。
承德石油高等专科学校
职业教育应用化工技术专业教学资源库《汽柴油生产操作》课程
承德石油高等专科学校
职业教育应用化工技术专业教学资源库《汽柴油生产操作》课程
所以关键是调节好常 压塔进料温度,也即常压 炉出口温度
承德石油高等专科学校
职业教育应用化工技术专业教学资源库《汽柴油生产操作》课程
那么常压炉出口温度 跟哪些因素有关呢? 第一,跟燃料气用量 变化有关
第三,跟烟气过剩氧 气量变化有关
第二,跟炉管内被加 热介质流量变化有关
承德石油高等专科学校
职业教育应用化工技术专业教学资源库《汽柴油生产操作》课程
所以,调节常顶温度 ≮92℃,转变为调节炉出 口温度靠近356℃即可。
职业教育应用化工技术专业教学资源库《汽柴油生产操作》课程
常减压蒸馏装置冷态开车操作 难点解答
一、常顶温度≮92℃的调节 郑哲奎
承德石油高等专科学校
职业教育应用化工技术专业教学资源库《汽柴油生产操作》课程
在减压蒸馏装置冷态开车操作过程中, 共分为八个大步骤:
一、装油 二、冷循环 三、热循环 四、常压转入正常
承德石油高等专科学校
职业教育应用化工技术专业教学资源库《汽柴油生产操作》课程
第一,可以加大燃料 气用量
第三,可以适量地增 减炉管内介质的流量
第二,随时调节过剩 氧为4%
承德石油高等专科学校
五、减压转入正常 六、投用一脱三注 七、调制平衡 八、质量指标
承德石油高等专科学校
职业教育应用化工技术专业教学资源库《汽柴油生产操作》课程
蒸馏控制参数

蒸馏工艺2.主要安全控制要求3.共性要求3.1塔内存在危险物料(硝基物中的多硝基物、液氧中的烃类、能引起环氧乙烷聚合的催化剂等)富集的重点部位应进行组分检测,如设置组分分析仪器即时或定期分析组分含量,或采取人工定期取样分析等,并应采取定期排放措施。
3.2采用蒸汽或其他高温气体加热的再沸器,蒸汽或高温气管道上设置流量集中显示、控制阀,根据釜温调节汽(气)量;立式再沸器壳程走蒸汽时,也可在冷凝水管道上设置控制阀。
采用液体加热的再沸器,加热液体的管道上设置控制阀,依据加热液体温度和釜温来调节加热液体流量,在控制阀前设置过滤器。
3.3冷凝器冷却水管设置流量集中显示、报警,冷却水流量低低联锁停加热介质。
3.4塔顶设置压力(或真空度)集中显示,顶部最高操作压力大于0.03MPa的蒸馏设备,应设置安全阀或爆破片等防爆泄压系统。
安全阀设在设备顶部或顶部气相馏出管道上。
3.5使用加热炉加热时,应设置蒸馏加热介质的温度显示,设置燃料或空气流量自动控制,并设置加热炉熄火保护装置。
4.个性要求4.1常压蒸馏塔和加压蒸馏塔设置塔釜压力高限报警、高高联锁切断加热物料。
4.2加压蒸馏系统物料侧放空管道设置压力自动调节。
4.3减压蒸馏塔设置塔釜真空度低限报警。
因真空度降低致使温度升高而造成物料有爆炸危险的,设置塔釜真空度低低联锁切断加热物料。
4.4连续蒸馏设置塔进料流量集中显示及自动控制阀。
4.5间歇蒸馏应设置馏出物料出料阀一旦关闭时,保证塔内压力处于正常范围的安全措施。
4.6间歇蒸馏应设置蒸馏釜高、低液位报警,设置蒸馏釜低低液位联锁切断加热介质系统。
4.7平衡蒸馏设置进料温度集中显示及报警。
5.其他安全设计要求5.1有爆炸危险的蒸馏装置设置安全联锁停车系统或具有安全联锁停车功能的其他系统,以保证操作人员及设备运行的安全。
5.2应有防止管道被凝固点较高的物质凝结堵塞,使塔内压增高而引起爆炸的措施,如管道伴热,设置双压力表,安全阀前串联爆破片等。
常减压蒸馏装置自动控制解决方案(精)
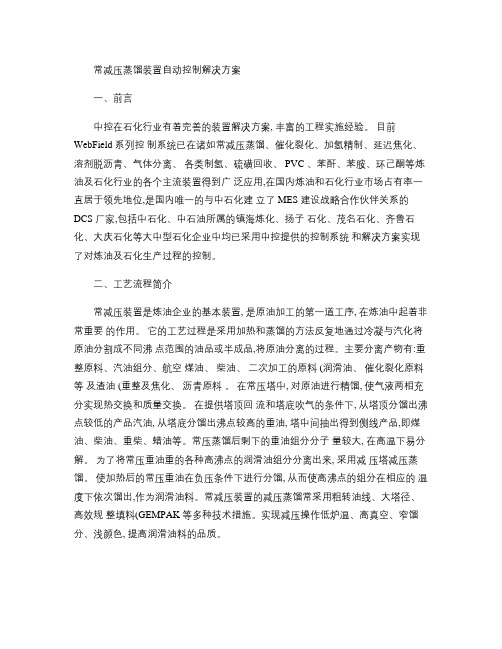
常减压蒸馏装置自动控制解决方案一、前言中控在石化行业有着完善的装置解决方案, 丰富的工程实施经验。
目前WebField 系列控制系统已在诸如常减压蒸馏、催化裂化、加氢精制、延迟焦化、溶剂脱沥青、气体分离、各类制氢、硫磺回收、 PVC 、苯酐、苯胺、环己酮等炼油及石化行业的各个主流装置得到广泛应用,在国内炼油和石化行业市场占有率一直居于领先地位,是国内唯一的与中石化建立了 MES 建设战略合作伙伴关系的DCS 厂家,包括中石化、中石油所属的镇海炼化、扬子石化、茂名石化、齐鲁石化、大庆石化等大中型石化企业中均已采用中控提供的控制系统和解决方案实现了对炼油及石化生产过程的控制。
二、工艺流程简介常减压装置是炼油企业的基本装置, 是原油加工的第一道工序, 在炼油中起着非常重要的作用。
它的工艺过程是采用加热和蒸馏的方法反复地通过冷凝与汽化将原油分割成不同沸点范围的油品或半成品,将原油分离的过程。
主要分离产物有:重整原料、汽油组分、航空煤油、柴油、二次加工的原料 (润滑油、催化裂化原料等及渣油 (重整及焦化、沥青原料。
在常压塔中, 对原油进行精馏, 使气液两相充分实现热交换和质量交换。
在提供塔顶回流和塔底吹气的条件下, 从塔顶分馏出沸点较低的产品汽油, 从塔底分馏出沸点较高的重油, 塔中间抽出得到侧线产品,即煤油、柴油、重柴、蜡油等。
常压蒸馏后剩下的重油组分分子量较大, 在高温下易分解。
为了将常压重油重的各种高沸点的润滑油组分分离出来, 采用减压塔减压蒸馏。
使加热后的常压重油在负压条件下进行分馏, 从而使高沸点的组分在相应的温度下依次馏出,作为润滑油料。
常减压装置的减压蒸馏常采用粗转油线、大塔径、高效规整填料(GEMPAK 等多种技术措施。
实现减压操作低炉温、高真空、窄馏分、浅颜色, 提高润滑油料的品质。
原油图 1 常减压装置工艺流程图三、控制方案3.1 装置关键控制常减压装置通常以常规单回路控制为主,辅以串级、均匀和切换等少量复杂控制。