轧制工艺参数
角钢轧制工艺技术规程最新
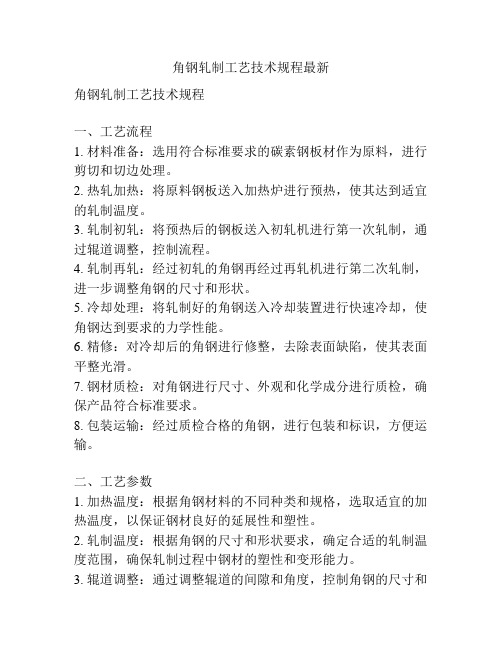
角钢轧制工艺技术规程最新角钢轧制工艺技术规程一、工艺流程1. 材料准备:选用符合标准要求的碳素钢板材作为原料,进行剪切和切边处理。
2. 热轧加热:将原料钢板送入加热炉进行预热,使其达到适宜的轧制温度。
3. 轧制初轧:将预热后的钢板送入初轧机进行第一次轧制,通过辊道调整,控制流程。
4. 轧制再轧:经过初轧的角钢再经过再轧机进行第二次轧制,进一步调整角钢的尺寸和形状。
5. 冷却处理:将轧制好的角钢送入冷却装置进行快速冷却,使角钢达到要求的力学性能。
6. 精修:对冷却后的角钢进行修整,去除表面缺陷,使其表面平整光滑。
7. 钢材质检:对角钢进行尺寸、外观和化学成分进行质检,确保产品符合标准要求。
8. 包装运输:经过质检合格的角钢,进行包装和标识,方便运输。
二、工艺参数1. 加热温度:根据角钢材料的不同种类和规格,选取适宜的加热温度,以保证钢材良好的延展性和塑性。
2. 轧制温度:根据角钢的尺寸和形状要求,确定合适的轧制温度范围,确保轧制过程中钢材的塑性和变形能力。
3. 辊道调整:通过调整辊道的间隙和角度,控制角钢的尺寸和形状,以满足产品的要求。
4. 冷却速率:根据角钢的不同材质和尺寸,控制冷却速率,使得角钢获得合适的强度和韧性。
5. 精修要求:对角钢的表面进行打磨和修整,使其表面平整光滑,不得有明显的锈蚀、气泡和裂纹等缺陷。
6. 质检标准:根据相关国家标准和技术要求,对角钢进行尺寸、外观和化学成分的质检,保证产品符合标准要求。
7. 包装要求:将质检合格的角钢进行包装,采用适当的包装材料和方式,以防止角钢在运输过程中受到损坏。
三、安全措施1. 操作人员必须熟知工艺流程和操作规程,严禁违规操作和擅自调整设备参数。
2. 加热炉和冷却装置必须经过定期维护和检修,确保正常运行。
3. 操作人员必须穿戴好安全防护用具,避免发生工伤事故。
4. 严禁在工作区域内吸烟、玩耍和乱扔废料,保持工作环境整洁有序。
5. 定期进行设备的维修和保养,确保设备的正常运行和安全使用。
dp780热轧带钢生产工艺参数

DP780热轧带钢是一种高强度、高延展性的汽车板材,具有良好的成形性能和焊接性能,在汽车制造领域得到广泛应用。
为了生产出符合要求的DP780热轧带钢,生产工艺参数的选择至关重要。
本文将从热轧带钢的工艺参数选择、控制和调整等方面进行讨论。
一、热轧带钢的工艺参数选择1、轧制温度的选择热轧带钢的轧制温度对其组织和性能有着至关重要的影响。
一般而言,DP780热轧带钢的轧制温度一般在800~1100摄氏度之间。
过低的轧制温度会使钢材的塑性降低,难以形成均匀的组织;而过高的轧制温度会导致晶粒长大,影响其强度和塑性。
在选择热轧带钢的轧制温度时,需要考虑其成分、厚度、宽度等因素,综合考虑找到最适宜的温度范围。
2、轧制力的控制在热轧带钢的生产过程中,轧制力的控制对最终产品的性能有着重要的影响。
适当的轧制力可以有效地改变钢材的组织结构,提高其强度和延展性。
但是,过大的轧制力可能会导致过度的塑性变形,影响产品的表面质量,甚至导致裂纹的产生。
在热轧带钢的生产中,需要根据钢材的特性和成型要求,合理控制轧制力的大小和分布。
3、冷却方式的选择热轧带钢在轧制后需要进行冷却,以使其组织结构得到稳定和均匀的改善。
冷却方式的选择对最终产品的组织和性能有着直接的影响。
常见的冷却方式包括空气冷却、水冷却、油冷却等。
不同的冷却方式会对热轧带钢的强度、塑性和表面质量产生不同的影响。
在选择冷却方式时,需要考虑产品的具体要求,合理选择适宜的冷却方式。
二、热轧带钢的工艺参数控制1、轧制温度的控制在热轧带钢的生产中,轧制温度的控制是一个复杂而关键的问题。
轧制温度受到许多因素的影响,如进料温度、轧制速度、轧辊温度等。
为了确保热轧带钢的组织和性能达到要求,需要对轧制温度进行精确而有效的控制。
采用先进的温度控制系统和实时监测手段,能够及时调整轧制温度,保证产品的质量稳定和一致性。
2、轧制力的监测与调整轧制力是影响热轧带钢成形过程的重要因素之一。
通过对轧制力的监测和分析,可以了解产品在轧制过程中的变形状态,及时发现异常情况并进行调整。
轧机工艺参数

轧机工艺参数轧机工艺参数是指在金属轧制过程中,对轧机进行调整和控制的一些关键参数。
这些参数的选择和调整直接影响到轧机的工作效果和产品质量。
本文将从轧机速度、轧制压力、轧辊直径和材料温度等方面介绍轧机工艺参数的重要性及其对轧制过程的影响。
首先是轧机速度。
轧机速度是指轧机轧制工作时金属材料的进给速度。
轧机速度的选择要根据金属材料的性质、厚度和轧制要求等因素进行调整。
过高的轧机速度会导致轧制过程中产生过大的热量,可能引起材料内部结构的改变,从而影响产品的力学性能。
而过低的轧机速度则会导致生产效率低下。
因此,合理选择适当的轧机速度是保证轧机工艺顺利进行的重要因素之一。
其次是轧制压力。
轧制压力是指轧机在轧制过程中对金属材料施加的压力。
轧制压力的大小决定了金属材料的变形程度和轧制效果。
过大的轧制压力会导致轧制过程中金属材料的塑性变形过大,可能引起内部裂纹和变形不均匀等问题。
而过小的轧制压力则会导致轧制效果不理想,产品表面质量不达标。
因此,合理选择适当的轧制压力对保证产品质量和工艺效果至关重要。
轧辊直径也是轧机工艺参数中的重要因素。
轧辊直径的选择与轧制材料的厚度和硬度密切相关。
较小直径的轧辊适用于轧制较薄的材料,能够提供更高的轧制压力,但对轧辊的耐用性要求较高。
而较大直径的轧辊适用于轧制较厚的材料,能够提供较大的轧制力,但对轧机的承载能力要求较高。
因此,在轧机工艺中,合理选择适当的轧辊直径能够提高轧制效果,保证产品质量。
最后是材料温度。
材料温度是指轧制过程中金属材料的温度。
材料温度的控制对轧制过程中的变形能力、力学性能和表面质量等方面都有重要影响。
过高的材料温度会导致材料塑性变形能力增加,但容易引起材料表面氧化和热裂纹等问题。
而过低的材料温度会导致材料的塑性变形能力降低,轧制效果不理想。
因此,在轧机工艺中,合理控制金属材料的温度对保证轧制过程的顺利进行和产品质量的提高至关重要。
轧机工艺参数是保证金属轧制过程顺利进行和产品质量的关键因素。
BJ001-铸轧工艺参数计算

读书笔记
铸轧工艺参数计算
铸轧的主要工艺参数
铸轧区长度 铸轧速度 浇注温度 冷却强度 凝固瞬间铝熔体供给所需的静压力
在轧辊直径、铸轧板厚度一定的正常铸轧情况下,上述工艺参数之一有变化,其它工艺参数将随之变 化才可能保持铸轧工艺的稳定性。生产实践表明,在调整各工艺参数之间的关系时,应使凝固区与变形区 的高与长有一定的比例关系,以保证绝对压下量△h 恒定,才能确保铸轧过程的连续性和稳定性,使铸轧 带坯具有优良的组织。
1 铸轧区长度
双辊式铸轧机的铸轧区的建立与铸轧辊的冷却强度、铸轧速度、带坯厚度有直接关系。图 1 为双辊式 连续铸轧机铸轧区示意图,由图可知,铸轧区由铝熔体冷却到结晶温度的冷却区(Z1),铸轧区(Z2)和轧 制变形区(Z3)组成。根据铸轧工艺的不同,各区长度存在一定比例关系。铸轧区长度可按下式计算,其 计算结果与实际情况比较接近。
Z
∆ 2
√∆
式中: Z——铸轧区长度,cm; H——前箱熔体水平面与氧化膜之间的高度差,cm; ρ——熔体密度,kg/—铸轧速度,m/min; v2——平均凝固速度,cm/min; h——带坯厚度,cm; σ——表面张力系数,N·cm-1; Δh——绝对压下量,cm; R——铸轧辊半径,cm。
对于双辊倾斜式连续铸轧机,生产实践表明,铸轧角在 8°~9°范围内变化,铸轧区长度可用式 2 计 算。生产实践证明,双辊倾斜式φ650mm 铸轧机和φ980mm 铸轧机铸轧区最大长度分别为 50mm 和 70mm 左右。
Z Rsinθ
式中: Z——铸轧区长度,mm;
读书笔记
θ——铸轧角,°(度); R——轧辊半径,mm。 2 铸轧力计算公式 p K应宽外 p——铸轧坯对铸轧辊的平均单位压力,MPa; 应——应力状态系数,用来考虑外摩擦和张力对单位压力的影响; 外——外端影响系数,由于轧制外区对轧制区有影响而引入的系数; 宽——宽展系数,轧制时带坯宽展时而引入的对平均单位压力的影响系数; K——铝带坯在铸轧温度时的真实变形抗力,MPa;
薄带铸轧工艺技术规范
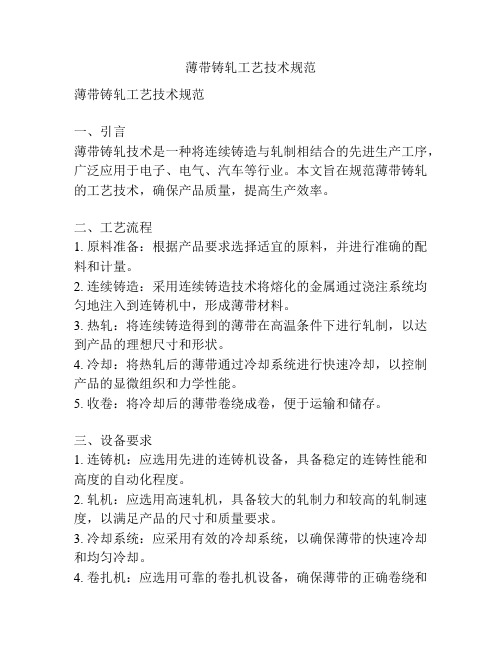
薄带铸轧工艺技术规范薄带铸轧工艺技术规范一、引言薄带铸轧技术是一种将连续铸造与轧制相结合的先进生产工序,广泛应用于电子、电气、汽车等行业。
本文旨在规范薄带铸轧的工艺技术,确保产品质量,提高生产效率。
二、工艺流程1. 原料准备:根据产品要求选择适宜的原料,并进行准确的配料和计量。
2. 连续铸造:采用连续铸造技术将熔化的金属通过浇注系统均匀地注入到连铸机中,形成薄带材料。
3. 热轧:将连续铸造得到的薄带在高温条件下进行轧制,以达到产品的理想尺寸和形状。
4. 冷却:将热轧后的薄带通过冷却系统进行快速冷却,以控制产品的显微组织和力学性能。
5. 收卷:将冷却后的薄带卷绕成卷,便于运输和储存。
三、设备要求1. 连铸机:应选用先进的连铸机设备,具备稳定的连铸性能和高度的自动化程度。
2. 轧机:应选用高速轧机,具备较大的轧制力和较高的轧制速度,以满足产品的尺寸和质量要求。
3. 冷却系统:应采用有效的冷却系统,以确保薄带的快速冷却和均匀冷却。
4. 卷扎机:应选用可靠的卷扎机设备,确保薄带的正确卷绕和稳定性。
四、工艺参数1. 连铸工艺参数:包括浇注温度、冷却方式、浇注速度等,应根据具体材料和产品要求进行合理的设定。
2. 轧制工艺参数:包括轧制温度、轧制力、轧制速度等,应根据材料的热变形特性和产品的尺寸要求进行合理的设定。
3. 冷却工艺参数:包括冷却速度、冷却介质等,应根据材料的热处理要求和产品的显微组织控制要求进行合理的设定。
五、质量控制1. 原料检验:对原材料进行化学成分、物理性能等方面的检验,确保原材料符合产品要求。
2. 在线检测:对连续铸造、热轧、冷却等过程进行在线检测,及时发现并纠正问题,确保产品质量。
3. 产品检验:对成品薄带进行外观质量、尺寸精度、机械性能、化学成分等方面的检验,确保产品达到标准要求。
六、安全环保1. 设备安全:保证设备的安全运行,提供必要的防护设施和安全培训。
2. 废水处理:配备有效的废水处理设施,确保废水符合环保要求。
3铝板冷轧工艺计算及校核

3铝板冷轧工艺计算及校核铝板冷轧工艺是铝板加工的一种常见方法,通过冷轧可以改变铝板的形状和厚度,并提高铝板的机械性能。
下面我们将介绍冷轧铝板的工艺计算及校核。
1.工艺计算铝板冷轧的工艺计算包括轧制力计算、轧辊布置计算和冷轧工艺参数计算等。
(1)轧制力计算铝板冷轧的轧制力是冷轧工艺中最为重要的计算参数,它不仅影响轧辊的尺寸设计和轧制机的选型,还对冷轧后的铝板质量有着重要的影响。
常用的轧制力计算公式为:F=(Ys+Yd)×b×h×μ×K×Ln其中,F为轧制力,Ys为切变模量,Yd为弯曲模量,b为工件宽度,h为工件厚度,μ为摩擦系数,K为轧制系数,Ln为冷轧变形速率。
(2)轧辊布置计算轧辊的布置对铝板冷轧的效果和质量有着重要的影响。
一般来说,轧辊的布置应满足以下要求:轧辊尽可能多,轧制力均匀分布,轧辊布置的均匀性。
轧辊布置计算主要包括轧机参数的选择、轧辊直径的确定、轧辊布置的设计等。
(3)冷轧工艺参数计算冷轧工艺参数是冷轧铝板的重要工艺控制要素,主要包括冷轧温度、轧制厚度、轧制速度、轧制压力等。
这些参数的选择要根据铝板的材料性能、工件形状和加工要求等来确定。
通过合理的参数选择,可以保证冷轧铝板的加工质量。
2.校核计算冷轧铝板的校核计算主要是为了验证冷轧过程中工艺参数的合理性和加工质量的可靠性。
常见的校核计算包括轧制力的校核、轧辊强度的校核和轧辊挠度计算等。
(1)轧制力的校核根据轧制力的计算结果,可以对轧制力进行校核,判断轧制力是否过大或过小。
如果轧制力过大,可能会导致轧辊变形或破裂,严重影响冷轧质量;如果轧制力过小,则可能导致轧制厚度偏大或变形不均匀,也会影响冷轧质量。
(2)轧辊强度的校核轧辊的强度是冷轧铝板加工过程中的重要考虑因素,轧辊的强度不能低于冷轧过程中所产生的最大应力。
通过对轧辊的强度进行校核,可以保证冷轧过程中的工艺参数可靠。
(3)轧辊挠度计算轧辊挠度是冷轧铝板工艺中需要考虑的一个关键参数。
1450轧机轧制工艺规程
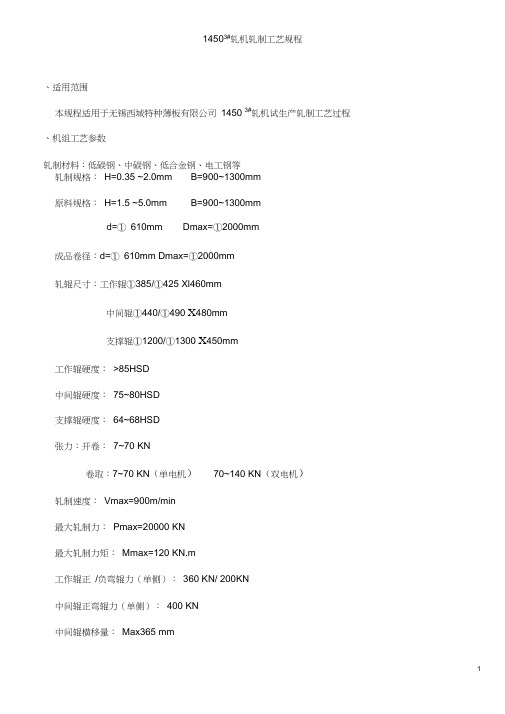
14503#轧机轧制工艺规程、适用范围本规程适用于无锡西城特种薄板有限公司1450 3#轧机试生产轧制工艺过程、机组工艺参数轧制材料:低碳钢、中碳钢、低合金钢、电工钢等轧制规格:H=0.35 ~2.0mm B=900~1300mm原料规格:H=1.5 ~5.0mm B=900~1300mmd=① 610mm Dmax=①2000mm成品卷径:d=① 610mm Dmax=①2000mm轧辊尺寸:工作辊①385/①425 Xl460mm中间辊①440/①490 X480mm支撑辊①1200/①1300 X450mm工作辊硬度:>85HSD中间辊硬度:75~80HSD支撑辊硬度:64~68HSD张力:开卷:7~70 KN卷取:7~70 KN(单电机)70~140 KN(双电机)轧制速度:Vmax=900m/min最大轧制力:Pmax=20000 KN最大轧制力矩:Mmax=120 KN.m工作辊正/负弯辊力(单侧):360 KN/ 200KN中间辊正弯辊力(单侧):400 KN中间辊横移量:Max365 mm主电机功率:Nmax=1197*4 KW= 4788 KW主电机转速:350/800 r/mi n 减速比:1.0588传动方式:双电机上、下工作辊单独传动三、轧制工艺规程3.1原料制度3.1.1化学成分低碳钢化学成分应符合下表规定其余化学元素:N2切.005% , Cu 0.15% , Cr0.08% , Ni 0.10%,也可供应符合上表规定的其他牌号钢种。
3.1.2尺寸精确性和均匀性3.1.3坯料表面质量钢带表面不得有气泡、结疤、裂纹、夹杂和其他对使用有害的缺陷,钢带卷不得有分层3.1.4工艺性能冷轧用坯料力学性能应符合下表规定321压下制度主要是依据设备能力、轧制要求,充分利用带钢塑性,并考虑加工硬化程度,用最少的道次,最大的压下量,分配道次加工量,以尽可能减少中间退火次数,轧出质量合格的产品,达到优质、高产、低成本,操作方便、可靠。
冷轧带钢的轧制工艺制度

冷轧带钢的轧制工艺制度冷轧带钢是指将钢坯经过冷轧工艺加工而成的带状钢材。
冷轧带钢具有优良的表面质量、尺寸精度和机械性能,广泛应用于汽车制造、电气设备、建筑结构等领域。
下面是冷轧带钢的轧制工艺制度,详细介绍了冷轧带钢的轧制流程、设备要求、工艺参数等内容。
一、工艺流程1.原材料准备:选择合适的钢坯进行切割,并进行清洗去除表面污染物。
2.加热处理:将钢坯进行加热处理,提高其塑性和可塑性,便于后续的轧制加工。
3.轧制:采用冷轧机将加热处理的钢坯进行轧制,初轧得到初始带钢,经过多次轧制得到所需的规格和尺寸。
4.退火处理:对轧制后的带钢进行退火处理,消除内部应力,提高带钢的硬度、韧性和尺寸精度。
5.表面处理:对退火处理后的带钢进行除锈、清洗等处理,使其具有良好的表面质量。
6.成品制备:切割、卷取或剪切带钢,制备成所需的成品形式,如卷材、板材等。
二、设备要求1.冷轧机:冷轧机是冷轧带钢的主要设备,具有较大的轧制压力和辊系数量,能够实现多次轧制和调节带钢的厚度。
2.加热炉:加热炉用于对钢坯进行加热处理,通过控制加热温度和时间,提高钢材的塑性和可塑性。
3.退火炉:退火炉用于对轧制后的带钢进行退火处理,消除内部应力,改善带钢的硬度、韧性和尺寸精度。
4.表面处理设备:包括除锈机、清洗机等,用于清除带钢表面的污垢和氧化物,保证带钢表面的质量。
5.切割、卷取或剪切设备:用于将带钢制备成所需的成品形式,如卷材、板材等。
三、工艺参数1.加热温度:加热处理时的温度应根据不同的钢种和规格进行调节,一般在800℃到1200℃之间。
2.轧制温度:冷轧带钢的轧制温度一般在室温到300℃之间,根据不同的钢种和规格进行调节。
3.轧制压力:冷轧机的轧制压力应根据带钢的规格和厚度进行调整,以确保轧制质量和尺寸精度。
4.退火温度:退火处理时的温度应根据不同的钢种和规格进行调节,一般在500℃到800℃之间。
5.表面处理参数:包括除锈机的清理能力、清洗机的清洗时间和温度等,具体参数根据带钢表面的质量要求进行调节。
轧钢工艺标准

编号:C(C)-04-501 A/2
轧钢工艺标准
编制:张进京
审核:
批准:
发布日期:2016年4月29 日生效日期:2016年5月5 日.
.
说明
一、生产工艺路线:原料检查-加热-除鳞-轧制-冷床-剪切-收集-包装-堆垛冷却
二、轧钢工艺主要由加热制度、轧制制度、冷却制度三大部分组成。
三、钢种生产工艺依照轧钢工艺标准执行;客户有特别需求的出具该客户控制要点。
四、每年度对轧钢工艺标准进行修订。
五、轧钢工艺标准,作为轧钢工艺技术规程的补充,标准中未作规定的常规要求,以轧钢工艺技术规程为准。
.
一、轧钢各工序控制规范
.
二、轧钢加热制度
.
钢种加热分类预览表
.
三、轧制制度
1、根据各规格对应的孔型,使用符合要求的轧机和导卫进行轧制。
2、生产各规格时,按对应的《轧钢生产工艺卡》设定各道次料型尺寸和参数。
轧制过程中,检查轧槽和导卫,磨损严重要及时更换;轧机替换辊道和输送辊道表面要保持光滑,磨损严重的及时进行3、
修磨或更换。
4、成品外形和表面质量要符合对应产品的技术标准的相关要求;中间道次轧件不得有耳子、折叠等缺陷。
5、对需要进行精整处理的产品,尺寸需要按尽量符合正偏差要求进行控制,留出精整余量。
6、锚链钢轧制精度按照Q/CJS298-2015A/0内控标准执行
7、终轧温度控制在900-1050℃。
8、轧制降速原则
.
.
.
五、附表:钢种工艺制度明细预览表。
棒材轧制过程数学模型
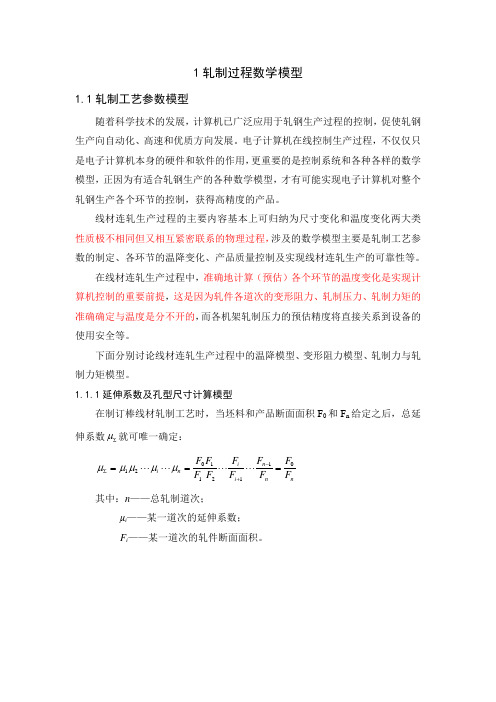
0.2220
-0.1697
0.3792
1.384
30CrSiMo
159.9
-2.833
3.670
0.1627
-0.0945
0.3454
1.337
12Mn
160.9
-2.744
3.493
0.2270
-0.1865
0.4433
1.543
12MnNb①
164.5
-2.682
3.414
0.1216
当静力变形时(102s-1)为0.9%~2.6%;
当动力变形时(102s-1)为19%~21%;
σb——强度极限,MPa;
ty0——钢材的熔点温度,K。
取钢材的密度γ=7.8,则得:
(1.10)
由于传导和对流引起的温降很小,甚至可以忽略不计。此时可以采用А.И.采利柯夫方法计算在孔型中轧制和移送到下一孔型时间内,轧件温度得变化:
Sf=V1/VR-1(1.1)
其中:
V1,VR——轧件出口速度及孔型槽底处的轧辊线速度。
在孔型中轧制时,前滑值取平均值 ,其计算式为
式中 ——变形区中性角的平均值;
——咬入角的平均值;
——摩擦角,一般为21~27度;
——轧辊工作直径的平均值;
——轧件轧前、轧后高度的平均值;
1.1.3轧件温降模型
轧件在轧制过程中的温度变化,是由辐射、传导、对流引起的温降和金属变形所产生的温升合成的,可用下式表示:
=ln
=
(1.19)
其中:
F0,FH——轧件入口断面面积和轧件被孔型压掉部分的断面面积;
F——轧辊平均工作半径;
N——轧辊转数,r/min;
轧制工艺技术

轧制工艺技术轧制工艺技术,是指通过机械力将金属坯料进行连续轧制、变形和压制,使其从粗糙的坯料变成平整、有形状的金属条、板、管等材料的过程。
轧制工艺技术是金属加工中常用的一种工艺方法,广泛应用于冶金、机械制造、船舶、汽车等领域。
轧制工艺技术主要包括轧制方法、轧制设备和工艺参数三个方面。
轧制方法主要有热轧和冷轧两种。
热轧是将金属加热到一定温度后进行轧制,适用于低碳钢、合金钢等材料的加工。
热轧工艺具有高产量、易控制等优点,但也会引起材料强度下降、变形度不定等缺点。
冷轧是将金属在室温下进行轧制,适用于不锈钢、铝合金等材料的加工。
冷轧工艺具有制品质量好、表面光洁等优点,但也会引起轧制力大、设备损坏等缺点。
轧制设备主要包括轧机和辅助设备。
轧机是轧制过程中最重要的设备之一,它主要由辊子、辊架、传动装置等组成。
根据轧机的结构和原理的不同,可以分为压下式轧机、抓下式轧机和压痕式轧机三种。
辅助设备主要包括卷板机、脱碳炉、退火炉等,它们的作用是为轧机提供原料和对轧制过程进行辅助处理。
工艺参数是指在轧制过程中需要控制的各项参数。
工艺参数的选择直接影响到轧制产品的质量和性能。
常见的工艺参数有轧制温度、轧制力、轧制速度等。
轧制温度是指轧制过程中金属的温度,不同的材料对轧制温度有不同的要求,过高或过低的温度都会影响到轧制产品的质量。
轧制力是指轧制时作用在轧辊上的力,它的大小直接影响到轧制产品的变形度和机械性能。
轧制速度是指轧制辊的线速度,不同的产品对轧制速度有不同的要求,过快或过慢的速度都会影响到轧制产品的表面质量。
轧制工艺技术的应用可以使金属材料获得更好的性能和表面质量,有助于提高产品的竞争力和降低成本。
同时,轧制工艺技术也对轧制设备和工艺参数的要求提出了挑战。
为了更好地应对这些挑战,需要不断改进和创新轧制工艺技术,提高轧制产品的质量和生产效率。
镁合金轧制板材工艺的主要热轧工艺参数是什么(精)

镁合金轧制板材工艺的主要热轧工艺参数是什么
镁合金热轧制变形时, 都会具有较好的轧制性能。
热轧制变形时多采用二辊轧机, 大批量生产时常采用三辊或者四辊轧机。
轧制时道次压下量通常控制在 10%-25%, 加热一次后可进行多道次轧制。
为了降低轧制力并改善板材性能,轧制时通常使用润滑剂,可将含 2%的调水油均匀地喷涂于加热的轧辊表面。
在粗轧时为了防止粘辊,可用猪油、石蜡、硼氮化合物等作为润滑剂。
镁合金的冷轧变形不易进行, 不能像铝合金那样可以达到 98%以上的总加工率与 60%左右的道次加工率。
镁合金的冷轧能力取决于合金成分以及热轧工艺和组织。
通常 AZ31的冷轧总变形量可达 16%,大部分镁合金对冷加工硬化很敏感,对冷轧镁合金板材进行不同程度的中间退火或成品退火, 可改善其冷变形能力, 并获得不同状态和性能的制品。
重庆大学的陈绪宏对 AZ31镁合金连续铸轧工艺过程进行了实验研究,并成功生产出了厚度为 1~3mm ,边部齐整,表面质量良好的镁合金薄带。
实验研究表明,要得到较好表面质量和力学性能的薄带需要合理的控制各个工艺参数, 当辊速为
10~15r/min, 浇铸温度为 655~ 665℃,辊缝为 0.9mm 时,获得了质量良好的镁合金薄带。
轧制工艺参数测试技
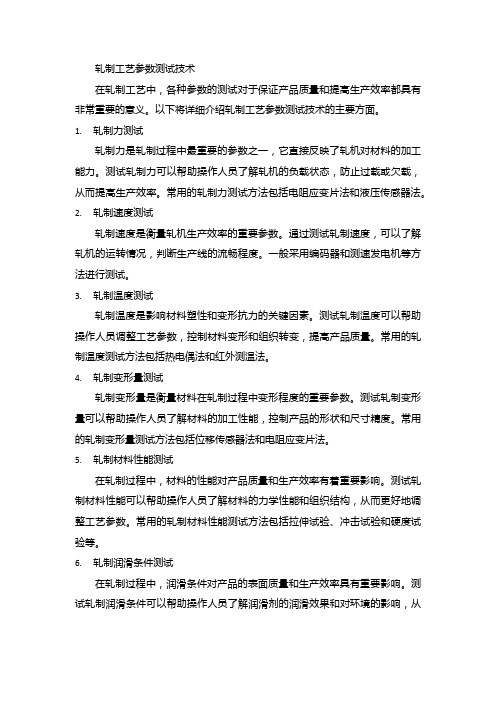
轧制工艺参数测试技术在轧制工艺中,各种参数的测试对于保证产品质量和提高生产效率都具有非常重要的意义。
以下将详细介绍轧制工艺参数测试技术的主要方面。
1.轧制力测试轧制力是轧制过程中最重要的参数之一,它直接反映了轧机对材料的加工能力。
测试轧制力可以帮助操作人员了解轧机的负载状态,防止过载或欠载,从而提高生产效率。
常用的轧制力测试方法包括电阻应变片法和液压传感器法。
2.轧制速度测试轧制速度是衡量轧机生产效率的重要参数。
通过测试轧制速度,可以了解轧机的运转情况,判断生产线的流畅程度。
一般采用编码器和测速发电机等方法进行测试。
3.轧制温度测试轧制温度是影响材料塑性和变形抗力的关键因素。
测试轧制温度可以帮助操作人员调整工艺参数,控制材料变形和组织转变,提高产品质量。
常用的轧制温度测试方法包括热电偶法和红外测温法。
4.轧制变形量测试轧制变形量是衡量材料在轧制过程中变形程度的重要参数。
测试轧制变形量可以帮助操作人员了解材料的加工性能,控制产品的形状和尺寸精度。
常用的轧制变形量测试方法包括位移传感器法和电阻应变片法。
5.轧制材料性能测试在轧制过程中,材料的性能对产品质量和生产效率有着重要影响。
测试轧制材料性能可以帮助操作人员了解材料的力学性能和组织结构,从而更好地调整工艺参数。
常用的轧制材料性能测试方法包括拉伸试验、冲击试验和硬度试验等。
6.轧制润滑条件测试在轧制过程中,润滑条件对产品的表面质量和生产效率具有重要影响。
测试轧制润滑条件可以帮助操作人员了解润滑剂的润滑效果和对环境的影响,从而更好地选择和使用润滑剂。
常用的轧制润滑条件测试方法包括摩擦系数测试和润滑剂性能测试等。
7.轧制坯料尺寸测试在轧制过程中,坯料的尺寸对产品的形状和尺寸精度有着重要影响。
测试坯料尺寸可以帮助操作人员了解坯料的形状和尺寸精度,从而更好地控制产品的加工过程。
常用的坯料尺寸测试方法包括卡尺测量法和磨床测量法等。
总之,对轧制工艺参数进行测试是保证产品质量和提高生产效率的关键手段。
轧制工艺参数设计

7 轧制工艺参数设计7.1 压下规程设计冷轧板带压下规程的设计一般包括原料规格的选择、轧制方案的确定、各道次压下量的分配与计算以及轧制速度的确定等。
7.1.1 坯料厚度选择在选择原料厚度时主要考虑冷轧总变形程度对性能及结构的影响。
由于对一定钢种、规格的产品,必须有一定的冷轧总变形程度,才能通过热处理获得所需要的一定的晶粒组织和性能。
坯料最大厚度受咬入能力和设备条件的限制;坯料最小厚度应考虑热轧带钢的供应情况,成品厚度和组织性能。
此外,选择原料厚度时,还要考虑生产能力的提高,故应根据具体情况做出选择。
本设计的代表产品是920×0.49 1020×0.95 1120×1.35 1220×1.75 1320×2.15 本设计选用厚度2.1 mm的带钢生产厚度为0.49mm成品板带钢,4.0 mm生产厚度为0.95mm的成品带钢,5.5mm生产厚度为1.35mm的成品带钢,4.0 mm生产厚度为1.75 mm的成品带钢,4.5mm生产厚度为2.15mm的成品带钢[4]。
7.1.2 轧制方案冷轧轧程是冷轧过程中每次中间退火所完成的冷轧工作。
冷轧轧程的确定主要取决于所轧钢种的软硬特性,坯料与成品的厚度,所采用的冷轧工艺和冷轧制度以及轧机的能力等因素,并随着工艺和设备的改进,轧制方案也在不断的变化。
例如选用润滑性能更好的工艺润滑剂或采用直径更小的高硬度工作辊都能减少所需要的轧程数。
因此,在确定冷轧轧程方案时,需要考虑已有的设备与工艺条件,还应充分研究各种提高冷轧效率的措施。
7.1.3 压下量的分配与计算在选择压下制度时,第一、二机架为利用金属的塑性,可以给予较大压下量,但往往受到咬入条件的限制,在有良好润滑研磨的轧辊允许咬入角3°到4°,而表面比较粗糙的轧辊为5°到8°,第一机架考虑到热轧来料的厚度偏差不宜采用过大压下量。
钢材轧制比8-概述说明以及解释
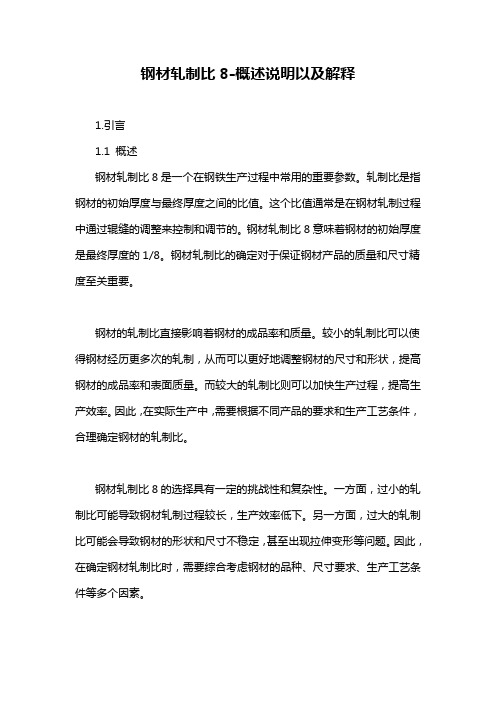
钢材轧制比8-概述说明以及解释1.引言1.1 概述钢材轧制比8是一个在钢铁生产过程中常用的重要参数。
轧制比是指钢材的初始厚度与最终厚度之间的比值。
这个比值通常是在钢材轧制过程中通过辊缝的调整来控制和调节的。
钢材轧制比8意味着钢材的初始厚度是最终厚度的1/8。
钢材轧制比的确定对于保证钢材产品的质量和尺寸精度至关重要。
钢材的轧制比直接影响着钢材的成品率和质量。
较小的轧制比可以使得钢材经历更多次的轧制,从而可以更好地调整钢材的尺寸和形状,提高钢材的成品率和表面质量。
而较大的轧制比则可以加快生产过程,提高生产效率。
因此,在实际生产中,需要根据不同产品的要求和生产工艺条件,合理确定钢材的轧制比。
钢材轧制比8的选择具有一定的挑战性和复杂性。
一方面,过小的轧制比可能导致钢材轧制过程较长,生产效率低下。
另一方面,过大的轧制比可能会导致钢材的形状和尺寸不稳定,甚至出现拉伸变形等问题。
因此,在确定钢材轧制比时,需要综合考虑钢材的品种、尺寸要求、生产工艺条件等多个因素。
本文将对钢材轧制比8的概念、定义、重要性以及其对钢材生产的影响进行详细的探讨和分析。
通过深入研究和实验验证,可以为钢材生产过程中的轧制比选择提供一定的理论和实践依据。
同时,本文也将对钢材生产工艺的改进和优化提供一些启示,以提高钢材的质量和生产效率。
1.2 文章结构文章结构部分的内容应该包含以下内容:在本文中,我们将按照以下结构来探讨钢材轧制比的重要性。
首先,我们将在引言部分概述本文的主要内容。
然后,在正文部分,我们将给出轧制比的定义,并详细阐述钢材轧制比的重要性。
最后,在结论部分,我们将总结轧制比的影响,并提出对钢材生产的启示。
通过这样的结构,读者可以清晰地了解文章的逻辑顺序,并可以更好地理解钢材轧制比对于钢材生产的重要性。
接下来,我们将从轧制比的定义开始,逐步展开我们的论述。
1.3 目的本文的目的是探讨钢材轧制比对钢材生产的重要性以及其对生产过程的影响。
型材轧钢工艺及参数

型材轧钢工艺及参数从钢坯库100t电动平车开始至成品仓库(短尺钢轨成品库、长尺钢轨成品库、型钢成品库)为止,工程内容主要有原料准备、钢坯加热、轧制作业线、产品冷却、钢轨精整线和型钢精整线等。
产品品种以生产钢轨为主,并兼顾生产H型钢、普通型钢和异型钢。
本设计以生产100m定尺和时速350km/h高速铁路用轨的高档次产品为起点,标志着该钢轨生产工艺及装备具备世界先进水平,其生产工艺特点如下:a)采用5机架万能轧制法生产钢轨,轧制过程为对称变形,对特别重要的轨头和轨底加工良好,产品断面尺寸精度高。
b)采用长尺冷却、长尺矫直、长尺探伤和平直度检测、冷锯定尺生产工艺,从而提高产品质量、成材率和精整能力。
c)采用多级高压水除鳞,清除轧件表面的初生和次生氧化铁皮,利于提高产品表面质量,降低轧辊消耗。
d)万能轧机和轧边机采用CCS紧凑式结构全液压压下、液压位置控制HPC、自动辊缝控制AGC和下水平辊动态轴向调整,轧辊和导卫成组快速更换,轧机刚度好,调整精度高。
e)采用带钢轨预弯装置的步进梁式冷床,可适宜各种产品均匀冷却,弯曲度小,减少钢材表面划伤,降低产品残余应力。
f)钢轨在线检测中心设置钢材表面清理装置、断面尺寸检测、全长平直度检测、表面缺陷涡流探伤、内部缺陷超声波探伤以及缺陷喷标装置等,以确保产品质量等级。
g)钢轨精整采用锯钻加工100m以下各种定尺,满足不同用户需要。
1.2生产规模及产品大纲本工程拟定生产钢轨、H型钢、工字钢等产品。
生产能力为105万t/a,分品种规格的产品大纲见表1。
表1 分品种规格的产品大纲1.3生产工艺流程1.3.1生产工艺流程简述a)钢轨生产经检查合格的连铸坯由原料跨的电动平车及料耙吊车热送到装料台架上,通过装炉辊道,称重、测长后进入步进式加热炉加热。
不能热装的坯料,用吊车吊入原料跨存放。
按生产计划要求,冷坯由吊车吊到上料台架上,通过装炉辊道,经称重、测长后进入加热炉加热。
钢坯加热到1150~1200℃出炉,经高压水除鳞后在第一架开坯机(BD1)上往复轧制5~11道次,在第二架开坯机(BD2)上往复轧制5~7道次,轧出万能轧机所需要的中间坯。
轧制过程工艺参数的测量与分析

估 计工 作 。
轧 制方 法 测 量 前 滑 系 数 和摩 擦 系 数 是 轧 制 工
用实 际轧 制 工 况 下 的采 样 数 据 估 计 变 形 抗 力 和摩 擦系数 的方法 , 称 “K 估 计 ” 北 京 钢 铁 研 究 总 简 。
1 不 同润滑 条件 下的实验数据及
I I 实验及 评价 .
估计
实验 在  ̄l0 m ×10 b3 m 5 mm 二 辊 轧机 上 进 行 , 实 验 材料 为 0 8沸 , 格 为 0 3 m 规 .4 m×3 5×2 0 m, 8 m 实测
的轧制 压力 和前 滑值 , 到 了提 高数 学 模 型 精 度 的 得 变 形抗 力和摩 擦 系数 值 。 文对 上 述 实 验 得 到 的 数 本 据 进行 了“ ”估计 和 综合 分析 。 K
抗力 值 和 摩 擦 系数 值 与 实 际 轧 制 中 的 值 有 差 异 。 所 以在上 世纪 7 0年 代 , 日本 、 德 和 我 国都提 出 了 西
文章编 号 :6 3— 0 7 2 0 ) 6—0 6 0 17 2 5 (0 7 0 4 1— 5
轧 制 过 程 工 艺 参 数 的测 量 与分 析
张小 平 , 张进 之 张 雪 娜 何 宗 霖 , ,
( . 京航 空航 天 大学 , 1北 北京 10 8 ; . 0 0 3 2 北京钢 铁研 究总 院 , 北京 10 8 ; 0 0 1 3 太原 科技 大学 , . 太原 0 0 2 ) 3 0 4
轧机工艺参数
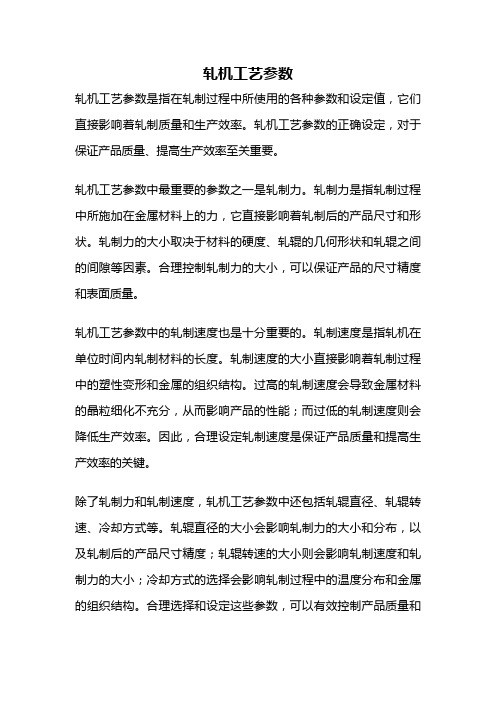
轧机工艺参数轧机工艺参数是指在轧制过程中所使用的各种参数和设定值,它们直接影响着轧制质量和生产效率。
轧机工艺参数的正确设定,对于保证产品质量、提高生产效率至关重要。
轧机工艺参数中最重要的参数之一是轧制力。
轧制力是指轧制过程中所施加在金属材料上的力,它直接影响着轧制后的产品尺寸和形状。
轧制力的大小取决于材料的硬度、轧辊的几何形状和轧辊之间的间隙等因素。
合理控制轧制力的大小,可以保证产品的尺寸精度和表面质量。
轧机工艺参数中的轧制速度也是十分重要的。
轧制速度是指轧机在单位时间内轧制材料的长度。
轧制速度的大小直接影响着轧制过程中的塑性变形和金属的组织结构。
过高的轧制速度会导致金属材料的晶粒细化不充分,从而影响产品的性能;而过低的轧制速度则会降低生产效率。
因此,合理设定轧制速度是保证产品质量和提高生产效率的关键。
除了轧制力和轧制速度,轧机工艺参数中还包括轧辊直径、轧辊转速、冷却方式等。
轧辊直径的大小会影响轧制力的大小和分布,以及轧制后的产品尺寸精度;轧辊转速的大小则会影响轧制速度和轧制力的大小;冷却方式的选择会影响轧制过程中的温度分布和金属的组织结构。
合理选择和设定这些参数,可以有效控制产品质量和生产效率。
轧机工艺参数的设定还要考虑到金属材料的性质和轧制目标。
不同的材料具有不同的塑性和硬度,因此需要根据具体材料的性质来设定轧机工艺参数。
同时,轧制目标也是设定轧机工艺参数的重要参考。
例如,如果要生产高强度的产品,就需要设定较大的轧制力和较低的轧制速度。
轧机工艺参数的正确设定对于保证产品质量和提高生产效率至关重要。
合理设定轧制力、轧制速度、轧辊直径、轧辊转速和冷却方式等参数,可以有效控制产品的尺寸精度、表面质量和金属的组织结构。
因此,在轧机生产中,必须重视轧机工艺参数的设定和调整,以提高产品质量和生产效率。
轧制原理与工艺
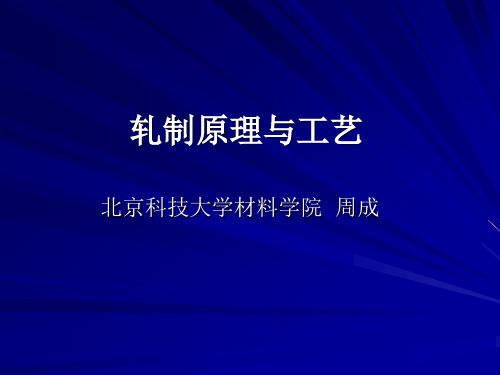
vh vγ
hγ h1
vh h1 vγ hγ
vγ v cos hγ h1 D(1 cos )
vh h cos h1 D (1 cos ) cos v h1 h1
Sh (1 cos )(D cos h1 ) h1
Sh
(1 cos )(D cos h1 ) h1
h 2R1 cos
轧件开始进入轧辊时,轧件与轧辊的最先接触 点和轧辊中心的连线与两轧辊中心连线所构成的 圆心角,称为咬入角。稳定轧制时,咬入角即为 轧件与轧辊相接触的圆弧所对应的圆心角。
1 cos h 2R
sin
O
R
2
sin
2
1 h 2 R
1 (1 cos ) 2
3. 4 平辊轧制时的宽展计算公式
(1)Д.热兹公式
b C h
(2)E. 齐别尔公式
b C
(3)C.И.古布金公式
b (1
h Rh h0
h h h )( f Rh ) h0 2 h0
……
3. 5 侧压后平轧时的宽展
板带轧制中,采用侧压(立辊轧制)调整轧件宽度。侧压 后轧件横断面呈双鼓形,要再经过一道水平轧制消除双鼓 形,然后进入后续轧制道次。 侧压后平轧时轧件的宽展可以认为由两部分组成,一部分 是鼓形的回展Δbb,另一部分是除鼓形回展以外的轧件宽 展Δbs 。
(2)限制宽展
轧制过程中,金属质点横向移动时,除受接触摩擦的 阻碍外,还承受孔型侧壁的限制作用,此时产生的宽展称 为限制宽展。
(3)强制宽展
在轧制过程中,金属质点横向移动时,除受接触摩擦的 阻碍外,还受其它因素的推动,此时产生的宽展称为强制 宽展。由于出现有利于金属质点横向流动的条件,所以强 制宽展大于自由宽展。