涤纶染色温度精编版
实验十八热熔法染涤棉混纺织物染色技术

实验十八热熔法染涤/棉混纺织物染色技术【实验目的】通过本实验使学生了解分散染料常用的热熔染色方法,并学会分散染料热熔法染涤纶的工艺条件和操作要领。
【实验原理】分散染料是一类分子结构较简单、几乎不溶于水的非离子型染料,染色时依靠分散剂的作用以微小颗粒的形式均匀分散在染液中。
它是涤纶及其混纺织物染色的主要染料。
涤/棉混纺织物的染色,根据染色制品的色泽及要求不同,可用多种的染色方法,其一是用一种染料同时染两种纤维获得匀一色,浅色染色制品多用此方法;其二是用一种染料只染一种纤维获得深色,另一种纤维留白;其三是用两种染料同时染两种纤维,这种染色过程比较繁锁,可以用高温高压法先染涤纶,再用棉的染料套染棉纤维。
或者两种染料同浴轧染。
【实验过程】本实验采用分散染料上染涤纶。
一、实验准备1、仪器:染杯(500ml)、烧杯(250ml)、量筒(10ml、100ml)、刻度吸管(2ml-10ml)、水浴锅、分析天平、玻璃棒2、药品:分散红S-R、分散黄、冰醋酸、海藻酸钠、渗透剂JFC、碳酸钠、肥皂3、实验材料:涤纶织物(每块80mm×150mm)4、溶液配制:5%NaAlg溶液:称取5g海藻酸钠溶于100ml蒸馏水中。
二、实验处方1、按处方配好染液,备用。
2、二浸二轧,轧余率60~70%,浸轧温度20~40℃,30秒。
3、用电炉烘干。
将织物一分为二,一半热熔固色,另一半不热熔。
4、热熔,温度170℃,5分钟。
5、染后水洗后,皂煮(95℃,5-10分钟)。
6、水洗,晾干。
四、注意事项1、浸轧染液及烘干应均匀,烘干温度以不超过80℃为宜。
2、织物烘干后应立即热熔,避免遇到水滴而产生水渍疵布。
五、实验报告1、贴样,比较热熔前后织物颜色的变化。
分散染料涤纶染色工艺
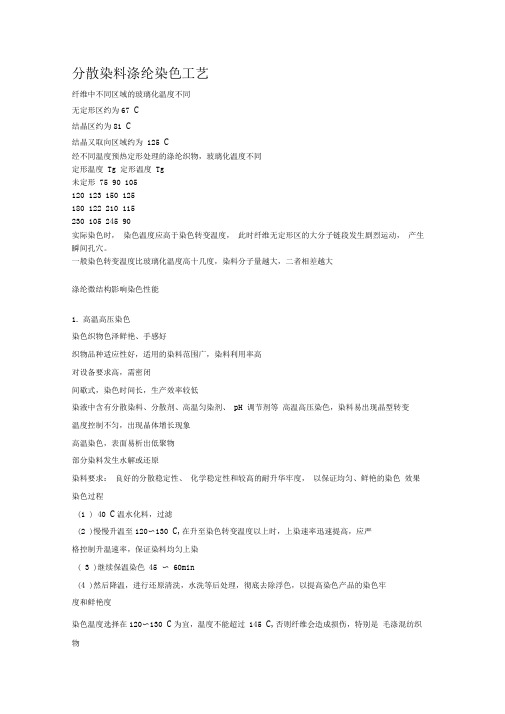
分散染料涤纶染色工艺纤维中不同区域的玻璃化温度不同无定形区约为67 C结晶区约为81 C结晶又取向区域约为125 C经不同温度预热定形处理的涤纶织物,玻璃化温度不同定形温度Tg 定形温度Tg未定形75 90 105120 123 150 125180 122 210 115230 105 245 90实际染色时,染色温度应高于染色转变温度,此时纤维无定形区的大分子链段发生剧烈运动,产生瞬间孔穴。
一般染色转变温度比玻璃化温度高十几度,染料分子量越大,二者相差越大涤纶微结构影响染色性能1.高温高压染色染色织物色泽鲜艳、手感好织物品种适应性好,适用的染料范围广,染料利用率高对设备要求高,需密闭间歇式,染色时间长,生产效率较低染液中含有分散染料、分散剂、高温匀染剂、pH 调节剂等高温高压染色,染料易出现晶型转变温度控制不匀,出现晶体增长现象高温染色,表面易析出低聚物部分染料发生水解或还原染料要求:良好的分散稳定性、化学稳定性和较高的耐升华牢度,以保证均匀、鲜艳的染色效果染色过程(1 ) 40 C温水化料,过滤(2 )慢慢升温至120〜130 C,在升至染色转变温度以上时,上染速率迅速提高,应严格控制升温速率,保证染料均匀上染( 3 )继续保温染色45 〜60min(4 )然后降温,进行还原清洗,水洗等后处理,彻底去除浮色,以提高染色产品的染色牢度和鲜艳度染色温度选择在120〜130 C为宜,温度不能超过145 C,否则纤维会造成损伤,特别是毛涤混纺织物染色温度控制分三个阶段:(1 )染色升温阶段:在70〜110 C温度区间,染料上染速率很快,要严格控制1〜2 C /min , 保证染料均匀吸附(2 )染色保温阶段染料向纤维内部扩散,并增进染料移染,染匀染透(3 )降温阶段在玻璃化温度以上,降温速率应适当慢些,其后快速降温,避免引起织物产生折皱和手感粗糙pH值控制在5〜6之间,色光纯正、色泽鲜艳,上染百分率高;高温碱性,染料水解,碱性太强,织物损伤大,手感差但酸性染色,齐聚物容易沉积在织物表面浴比:小,节能节水,但易使织物产生折皱、擦伤、染色不匀大,耗能耗水匹染:10 : 1〜30 : 1分散剂影响匀染剂(载体、非离子型活性剂)(1 )缓染剂通过助剂对染料或纤维亲和力,延缓染料上染,使染料能均匀地吸附在纤维的各个部分,从而染色均匀,但会导致上染百分率下降(2)移染匀染剂一般为载体、非离子型聚氧乙烯类表面活性剂载体有毒非离子表面活性剂在染色温度高于浊点,会产生沉淀,一般需与阴离子表面活性剂复配2.热熔染色在185〜215 C干热条件下使染料在纤维上发生固着的连续轧染的染色方法连续化生产,生产效率高,用水量少,污水少,使用的染料要求耐升华牢度较高染色时织物所受张力较大,织物手感及色泽鲜艳度不及高温高压染色法一般多用于涤棉混纺织物中涤纶染色浸轧液含有分散染料、分散剂、渗透剂、防泳移剂等染料颗粒要特别匀细,渗透性及分散稳定性要好二浸二轧,室温,涤棉织物轧余率一般为50〜60 %焙烘固色(热熔)温度根据染料升华牢度来选择,一般为180〜220 C,时间2〜1min染色工艺条件(1 )润湿剂或渗透剂润湿剂可以排除织物中的空气,有利于染料渗透到织物内部织物前处理充分,可不加(2 )泳移现象及防止因染料对涤纶缺乏亲和力,容易发生烘干现象合理烘干方式提高浸轧效果,减少带液率,涤棉带液率降低到20 %〜30 %后,不会发生明显泳移加入适量防泳移剂热熔染色时间和时间选择织物烘干后,染料停留在纤维表面,没有与纤维发生固着,通过高温热焙烘,染料向纤维内部扩散,把纤维染透,完成固色一一热熔固色温度高一一染料升华较多拼色时,染料耐升华性应相近3.载体染色利用载体助剂对涤纶的增塑膨化性能,在常压100 C条件下染色设备简单,适合毛涤织物染色另外,载体对染料具有亲和性,对染料溶解能力高,提高染料浓度,提高吸附和扩散;过高, 也不好但载体有毒性,存在环境污染,残留载体不易洗净,影响染色牢度分散染料染色原理及工艺分散染料是一类水溶性较低的非离子型染料。
染色工艺基础知识
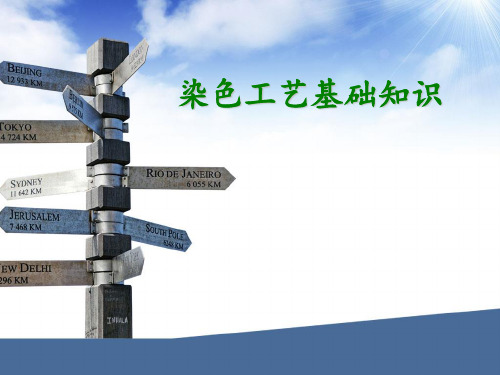
中),匀染性差。
阳离子蓝 FGL B、共轭型 :
CH3 C C - CH = CH + N CH3 N CH3 CH3 C2H4Cl Cl-
特点:色泽鲜艳, 匀染性好,染料敏 感(对PH、热等 )
阳离子桃红FG
阳离子染料染色机理
腈纶上的酸性基团电离,使纤维带负电荷: 腈纶—COOH 腈纶—SO3H 腈纶—COO-+H+ 腈纶—SO3-+H+
染色工艺基础知识
目录
1
涤纶染色工艺原理 锦纶染色工艺原理 腈纶染色工艺原理 纤维素纤维染色工艺原理
2
3
4
一、涤纶染色工艺原理
涤纶(PET):
大分子两端各含有一个-OH,不含亲水 基团 熔点约为267℃ 结晶度可达40%-60%,分子排列紧密 玻璃化温度Tg为125℃ 涤纶在碱性条件下易发生水解
H OCH2CH2 O O C O C n O CH2CH2OH
分 散 染 料 高 温 匀 染 剂 分 散 剂 H A C 调 节 P H = 5 6
1.温度:涤纶染色的温度为135℃,此温度称为染色转变温度(TD)。在常
温下,涤纶无定形区大分子间排列紧密,常温下染料分子难以进入纤维 内部,当纤维加热到玻璃化温度(Tg,125℃)以上时,无定形区部分分子链 运动加剧,分子间的空隙增大,染料分子可以进入纤维内部进行上染。 一般TD较Tg高十几度,根据扩散系数来决定的。
CN COOCH3 CH2SO3Na
阳离子染料:阳离子染料的阳电荷是通过氮原子季铵化后引入 到染料分子中的。绝大部分阳离子染料可分为隔离型和共轭型 。 O NHCH
A、隔离型:
3
特点:给色量稍低,色光不 十分鲜艳,但耐热、耐晒,耐酸 碱的稳定性好。上染率高(电荷集
分散染料涤纶染色工艺
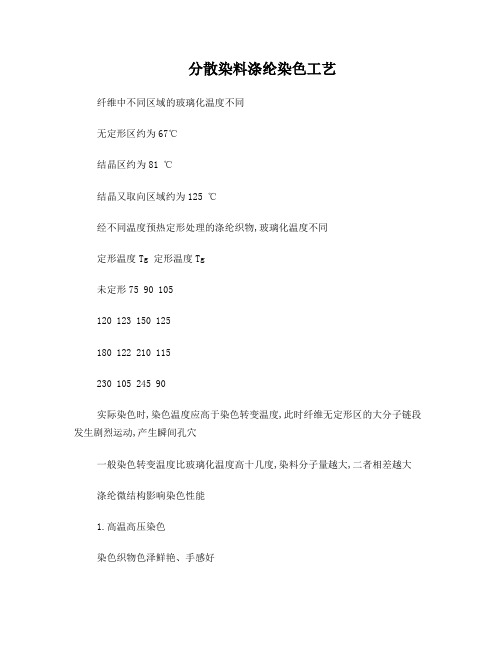
分散染料涤纶染色工艺纤维中不同区域的玻璃化温度不同无定形区约为67℃结晶区约为81 ℃结晶又取向区域约为125 ℃经不同温度预热定形处理的涤纶织物,玻璃化温度不同定形温度Tg 定形温度Tg未定形75 90 105120 123 150 125180 122 210 115230 105 245 90实际染色时,染色温度应高于染色转变温度,此时纤维无定形区的大分子链段发生剧烈运动,产生瞬间孔穴一般染色转变温度比玻璃化温度高十几度,染料分子量越大,二者相差越大涤纶微结构影响染色性能1.高温高压染色染色织物色泽鲜艳、手感好织物品种适应性好,适用的染料范围广,染料利用率高对设备要求高,需密闭间歇式,染色时间长,生产效率较低染液中含有分散染料、分散剂、高温匀染剂、pH调节剂等高温高压染色,染料易出现晶型转变温度控制不匀,出现晶体增长现象高温染色,表面易析出低聚物部分染料发生水解或还原染料要求:良好的分散稳定性、化学稳定性和较高的耐升华牢度,以保证均匀、鲜艳的染色效果染色过程(1)40 ℃温水化料,过滤(2)慢慢升温至120~130 ℃,在升至染色转变温度以上时,上染速率迅速提高,应严格控制升温速率,保证染料均匀上染(3)继续保温染色45~60min(4)然后降温,进行还原清洗,水洗等后处理,彻底去除浮色,以提高染色产品的染色牢度和鲜艳度染色温度选择在120~130℃为宜,温度不能超过145℃,否则纤维会造成损伤,特别是毛涤混纺织物染色温度控制分三个阶段:(1)染色升温阶段:在70~110℃温度区间,染料上染速率很快,要严格控制1~2℃/min,保证染料均匀吸附(2)染色保温阶段染料向纤维内部扩散,并增进染料移染,染匀染透(3)降温阶段在玻璃化温度以上,降温速率应适当慢些,其后快速降温,避免引起织物产生折皱和手感粗糙pH值控制在5~6之间,色光纯正、色泽鲜艳,上染百分率高;高温碱性,染料水解,碱性太强,织物损伤大,手感差但酸性染色,齐聚物容易沉积在织物表面浴比:小,节能节水,但易使织物产生折皱、擦伤、染色不匀大,耗能耗水匹染:10:1~30:1分散剂影响匀染剂(载体、非离子型活性剂)(1)缓染剂通过助剂对染料或纤维亲和力,延缓染料上染,使染料能均匀地吸附在纤维的各个部分,从而染色均匀,但会导致上染百分率下降(2)移染匀染剂一般为载体、非离子型聚氧乙烯类表面活性剂载体有毒非离子表面活性剂在染色温度高于浊点,会产生沉淀,一般需与阴离子表面活性剂复配2.热熔染色在185~215℃干热条件下使染料在纤维上发生固着的连续轧染的染色方法连续化生产,生产效率高,用水量少,污水少,使用的染料要求耐升华牢度较高染色时织物所受张力较大,织物手感及色泽鲜艳度不及高温高压染色法一般多用于涤棉混纺织物中涤纶染色浸轧液含有分散染料、分散剂、渗透剂、防泳移剂等染料颗粒要特别匀细,渗透性及分散稳定性要好二浸二轧,室温,涤棉织物轧余率一般为50~60%焙烘固色(热熔)温度根据染料升华牢度来选择,一般为180~220℃,时间2~1min 染色工艺条件(1)润湿剂或渗透剂润湿剂可以排除织物中的空气,有利于染料渗透到织物内部织物前处理充分,可不加(2)泳移现象及防止因染料对涤纶缺乏亲和力,容易发生烘干现象合理烘干方式提高浸轧效果,减少带液率,涤棉带液率降低到20%~30%后,不会发生明显泳移加入适量防泳移剂热熔染色时间和时间选择织物烘干后,染料停留在纤维表面,没有与纤维发生固着,通过高温热焙烘,染料向纤维内部扩散,把纤维染透,完成固色——热熔固色温度高——染料升华较多拼色时,染料耐升华性应相近3.载体染色利用载体助剂对涤纶的增塑膨化性能,在常压100℃条件下染色设备简单,适合毛涤织物染色另外,载体对染料具有亲和性,对染料溶解能力高,提高染料浓度,提高吸附和扩散;过高,也不好但载体有毒性,存在环境污染,残留载体不易洗净,影响染色牢度。
染色工艺基础知识

剂,染深色也仅需加少量助染剂。
Nylonthrene B染料主要用于卷染。
2021/6/16
N N C C CH3 CN
HO N Cl
Cl SO3Na
弱酸性黄3GS
11
酸性染料染色机理
酸性染料的主要结构:
D–SO3–Na+ → D–SO3– + Na+
N H 3+ H +
H N
O H -
C O O -
因此一般选用弱酸性染料染锦纶。其键结主要是靠纤维分子在酸性条件下末端带正电 的氨基与染料的磺酸基团的离子结合以及分子彼此间形成的范德华力和氢键结合。
2021/6/16
12
染色工艺过程
染物于50~60℃入染,以1℃/1.5min的速率升温至70℃ ,再以 1℃/2~4min的速率升温至沸,再沸染45~75min,然后水洗烘干。
冷水洗、热水洗、 皂洗、热水洗、冷水洗
K型 60 85
2021/6/16
26
2.轧染(pad) 一浴法
浸轧染液 → 烘干 → 汽蒸 → 后处理
室温
染料 NaHCO3 防泳移剂 尿素
预+烘
100-104℃ 1-5min
二浴法 浸轧染液 → 烘干 → 轧碱 → 汽蒸 → 后处理
染料 防泳移剂 尿素
(K)NaOH (时间短)
反应性弱,适于高温(90℃以 上)染色,可在碱性较强的条 件下与纤维反应,又称热固型 活性染料,染料不易水解,贮 存稳定性较好,“染料-纤 维”共价键的水解稳定性比X 型染料好。
(1)反应性:X型>KN型>K 型,染色温度50~70℃,在弱 碱性条件下固色; (2)“染料-纤维”共价键的 耐酸稳定性较好,耐碱的水解稳 定性差; (3)染料溶解性好,色泽鲜 艳。
(工艺技术)分散染料涤纶染色工艺

分散染料涤纶染色工艺纤维中不同区域的玻璃化温度不同无定形区约为67℃结晶区约为81 ℃结晶又取向区域约为125 ℃经不同温度预热定形处理的涤纶织物,玻璃化温度不同定形温度Tg 定形温度Tg未定形75 90 105120 123 150 125180 122 210 115230 105 245 90实际染色时,染色温度应高于染色转变温度,此时纤维无定形区的大分子链段发生剧烈运动,产生瞬间孔穴。
一般染色转变温度比玻璃化温度高十几度,染料分子量越大,二者相差越大涤纶微结构影响染色性能1.高温高压染色染色织物色泽鲜艳、手感好织物品种适应性好,适用的染料范围广,染料利用率高对设备要求高,需密闭间歇式,染色时间长,生产效率较低染液中含有分散染料、分散剂、高温匀染剂、pH调节剂等高温高压染色,染料易出现晶型转变温度控制不匀,出现晶体增长现象高温染色,表面易析出低聚物部分染料发生水解或还原染料要求:良好的分散稳定性、化学稳定性和较高的耐升华牢度,以保证均匀、鲜艳的染色效果染色过程(1)40 ℃温水化料,过滤(2)慢慢升温至120~130 ℃,在升至染色转变温度以上时,上染速率迅速提高,应严格控制升温速率,保证染料均匀上染(3)继续保温染色45~60min(4)然后降温,进行还原清洗,水洗等后处理,彻底去除浮色,以提高染色产品的染色牢度和鲜艳度染色温度选择在120~130℃为宜,温度不能超过145℃,否则纤维会造成损伤,特别是毛涤混纺织物染色温度控制分三个阶段:(1)染色升温阶段:在70~110℃温度区间,染料上染速率很快,要严格控制1~2℃/min,保证染料均匀吸附(2)染色保温阶段染料向纤维内部扩散,并增进染料移染,染匀染透(3)降温阶段在玻璃化温度以上,降温速率应适当慢些,其后快速降温,避免引起织物产生折皱和手感粗糙pH值控制在5~6之间,色光纯正、色泽鲜艳,上染百分率高;高温碱性,染料水解,碱性太强,织物损伤大,手感差但酸性染色,齐聚物容易沉积在织物表面浴比:小,节能节水,但易使织物产生折皱、擦伤、染色不匀大,耗能耗水匹染:10:1~30:1分散剂影响匀染剂(载体、非离子型活性剂)(1)缓染剂通过助剂对染料或纤维亲和力,延缓染料上染,使染料能均匀地吸附在纤维的各个部分,从而染色均匀,但会导致上染百分率下降(2)移染匀染剂一般为载体、非离子型聚氧乙烯类表面活性剂载体有毒非离子表面活性剂在染色温度高于浊点,会产生沉淀,一般需与阴离子表面活性剂复配2.热熔染色在185~215℃干热条件下使染料在纤维上发生固着的连续轧染的染色方法连续化生产,生产效率高,用水量少,污水少,使用的染料要求耐升华牢度较高染色时织物所受张力较大,织物手感及色泽鲜艳度不及高温高压染色法一般多用于涤棉混纺织物中涤纶染色浸轧液含有分散染料、分散剂、渗透剂、防泳移剂等染料颗粒要特别匀细,渗透性及分散稳定性要好二浸二轧,室温,涤棉织物轧余率一般为50~60%焙烘固色(热熔)温度根据染料升华牢度来选择,一般为180~220℃,时间2~1min染色工艺条件(1)润湿剂或渗透剂润湿剂可以排除织物中的空气,有利于染料渗透到织物内部织物前处理充分,可不加(2)泳移现象及防止因染料对涤纶缺乏亲和力,容易发生烘干现象合理烘干方式提高浸轧效果,减少带液率,涤棉带液率降低到20%~30%后,不会发生明显泳移加入适量防泳移剂热熔染色时间和时间选择织物烘干后,染料停留在纤维表面,没有与纤维发生固着,通过高温热焙烘,染料向纤维内部扩散,把纤维染透,完成固色——热熔固色温度高——染料升华较多拼色时,染料耐升华性应相近3.载体染色利用载体助剂对涤纶的增塑膨化性能,在常压100℃条件下染色设备简单,适合毛涤织物染色另外,载体对染料具有亲和性,对染料溶解能力高,提高染料浓度,提高吸附和扩散;过高,也不好但载体有毒性,存在环境污染,残留载体不易洗净,影响染色牢度分散染料染色原理及工艺分散染料是一类水溶性较低的非离子型染料。
分散染料涤纶染色工艺

分散染料涤纶染色工艺纤维中不同区域的玻璃化温度不同无定形区约为67℃结晶区约为81 ℃结晶又取向区域约为125 ℃经不同温度预热定形处理的涤纶织物,玻璃化温度不同定形温度Tg 定形温度Tg未定形75 90 105120 123 150 125180 122 210 115230 105 245 90实际染色时,染色温度应高于染色转变温度,现在纤维无定形区的大分子链段发生剧烈运动,产生瞬时孔穴。
一样染色转变温度比玻璃化温度高十几度,染料分子量越大,二者相差越大涤纶微结构阻碍染色性能1.高温高压染色染色织物色泽鲜艳、手感好织物品种适应性好,适用的染料范畴广,染料利用率高对设备要求高,需密闭间歇式,染色时刻长,生产效率较低染液中含有分散染料、分散剂、高温匀染剂、pH调剂剂等高温高压染色,染料易显现晶型转变温度操纵不匀,显现晶体增长现象高温染色,表面易析出低聚物部分染料发生水解或还原染料要求:良好的分散稳固性、化学稳固性和较高的耐升华牢度,以保证平均、鲜艳的染色成效染色过程(1)40 ℃温水化料,过滤(2)慢慢升温至120~130 ℃,在升至染色转变温度以上时,上染速率迅速提高,应严格操纵升温速率,保证染料平均上染(3)连续保温染色45~60min(4)然后降温,进行还原清洗,水洗等后处理,完全去除浮色,以提高染色产品的染色牢度和鲜艳度染色温度选择在120~130℃为宜,温度不能超过145℃,否则纤维会造成损害,专门是毛涤混纺织物染色温度操纵分三个时期:(1)染色升温时期:在70~110℃温度区间,染料上染速率专门快,要严格操纵1~2℃/min,保证染料平均吸附(2)染色保温时期染料向纤维内部扩散,并增进染料移染,染匀染透(3)降温时期在玻璃化温度以上,降温速率应适当慢些,其后快速降温,幸免引起织物产生折皱和手感粗糙pH值操纵在5~6之间,色光纯正、色泽鲜艳,上染百分率高;高温碱性,染料水解,碱性太强,织物损害大,手感差但酸性染色,齐聚物容易沉积在织物表面浴比:小,节能节水,但易使织物产生折皱、擦伤、染色不匀大,耗能耗水匹染:10:1~30:1分散剂阻碍匀染剂(载体、非离子型活性剂)(1)缓染剂通过助剂对染料或纤维亲和力,延缓染料上染,使染料能平均地吸附在纤维的各个部分,从而染色平均,但会导致上染百分率下降(2)移染匀染剂一样为载体、非离子型聚氧乙烯类表面活性剂载体有毒非离子表面活性剂在染色温度高于浊点,会产生沉淀,一样需与阴离子表面活性剂复配2.热熔染色在185~215℃干热条件下使染料在纤维上发生固着的连续轧染的染色方法连续化生产,生产效率高,用水量少,污水少,使用的染料要求耐升华牢度较高染色时织物所受张力较大,织物手感及色泽鲜艳度不及高温高压染色法一样多用于涤棉混纺织物中涤纶染色浸轧液含有分散染料、分散剂、渗透剂、防泳移剂等染料颗粒要专门匀细,渗透性及分散稳固性要好二浸二轧,室温,涤棉织物轧余率一样为50~60%焙烘固色(热熔)温度依照染料升华牢度来选择,一样为180~220℃,时刻2~1min染色工艺条件(1)润湿剂或渗透剂润湿剂能够排除织物中的空气,有利于染料渗透到织物内部织物前处理充分,可不加(2)泳移现象及防止因染料对涤纶缺乏亲和力,容易发生烘干现象合理烘干方式提高浸轧成效,减少带液率,涤棉带液率降低到20%~30%后,可不能发生明显泳移加入适量防泳移剂热熔染色时刻和时刻选择织物烘干后,染料停留在纤维表面,没有与纤维发生固着,通过高温热焙烘,染料向纤维内部扩散,把纤维染透,完成固色——热熔固色温度高——染料升华较多拼色时,染料耐升华性应相近3.载体染色利用载体助剂对涤纶的增塑膨化性能,在常压100℃条件下染色设备简单,适合毛涤织物染色另外,载体对染料具有亲和性,对染料溶解能力高,提高染料浓度,提高吸附和扩散;过高,也不行但载体有毒性,存在环境污染,残留载体不易洗净,阻碍染色牢度分散染料染色原理及工艺分散染料是一类水溶性较低的非离子型染料。
涤纶的染色原理
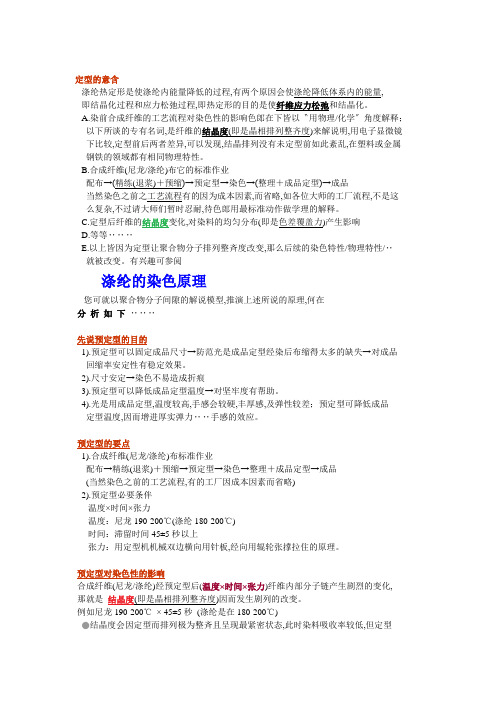
定型的意含涤纶热定形是使涤纶内能量降低的过程,有两个原因会使涤纶降低体系内的能量,即结晶化过程和应力松弛过程,即热定形的目的是使纤维应力松弛和结晶化。
A.染前合成纤维的工艺流程对染色性的影响色郎在下皆以〝用物理/化学〞角度解释;以下所谈的专有名词,是纤维的结晶度(即是晶相排列整齐度)来解说明,用电子显微镜下比较,定型前后两者差异,可以发现,结晶排列没有未定型前如此紊乱,在塑料或金属钢铁的领域都有相同物理特性。
B.合成纤维(尼龙/涤纶)布它的标准作业配布→(精练(退浆)+预缩)→预定型→染色→(整理+成品定型)→成品当然染色之前之工艺流程有的因为成本因素,而省略,如各位大师的工厂流程,不是这么复杂,不过请大师们暂时忍耐,待色郎用最标准动作做学理的解释。
C.定型后纤维的结晶度变化,对染料的均匀分布(即是色差覆盖力)产生影响D.等等‥‥‥E.以上皆因为定型让聚合物分子排列整斉度改变,那么后续的染色特性/物理特性/‥就被改变。
有兴趣可参阅涤纶的染色原理您可就以聚合物分子间隙的解说模型,推演上述所说的原理,何在分析如下‥‥‥先说预定型的目的1).预定型可以固定成品尺寸→防范光是成品定型经染后布缩得太多的缺失→对成品回缩率安定性有稳定效果。
2).尺寸安定→染色不易造成折痕3).预定型可以降低成品定型温度→对坚牢度有帮助。
4).光是用成品定型,温度较高,手感会较硬,丰厚感,及弹性较差;预定型可降低成品定型温度,因而增进厚实弹力‥‥手感的效应。
预定型的要点1).合成纤维(尼龙/涤纶)布标准作业配布→精练(退浆)+预缩→预定型→染色→整理+成品定型→成品(当然染色之前的工艺流程,有的工厂因成本因素而省略)2).预定型必要条伴温度×时间×张力温度:尼龙190-200℃(涤纶180-200℃)时间:滞留时间45±5秒以上张力:用定型机机械双边横向用针板,经向用辊轮张撑拉住的原理。
预定型对染色性的影响合成纤维(尼龙/涤纶)经预定型后(温度×时间×张力)纤维内部分子链产生剧烈的变化,那就是结晶度(即是晶相排列整齐度)因而发生剧列的改变。
涤纶的染色性能
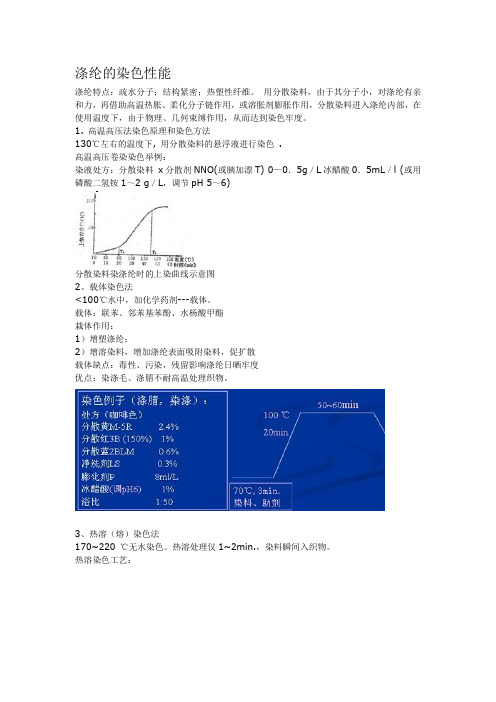
涤纶的染色性能
涤纶特点:疏水分子;结构紧密;热塑性纤维。
用分散染料,由于其分子小,对涤纶有亲和力,再借助高温热胀、柔化分子链作用,或溶胀剂膨胀作用,分散染料进入涤纶内部,在使用温度下,由于物理、几何束缚作用,从而达到染色牢度。
1. 高温高压法染色原理和染色方法
130℃左右的温度下, 用分散染料的悬浮液进行染色 .
高温高压卷染染色举例:
染液处方:分散染料x分散剂NNO(或胰加漂T) 0—0.5g/L冰醋酸0.5mL/l (或用磷酸二氢铵1~2 g/L,调节pH 5~6)
分散染料染涤纶时的上染曲线示意图
2、载体染色法
<100℃水中,加化学药剂---载体。
载体:联苯、邻苯基苯酚、水杨酸甲酯
栽体作用:
1)增塑涤纶;
2)增溶染料,增加涤纶表面吸附染料,促扩散
载体缺点:毒性、污染,残留影响涤纶日晒牢度
优点:染涤毛、涤腈不耐高温处理织物。
3、热溶(熔)染色法
170~220 ℃无水染色。
热溶处理仅1~2min.,染料瞬间入织物。
热溶染色工艺:
纯涤纶连续化加工,大批量生产。
手感、鲜艳度差。
6涤纶织物的染色工
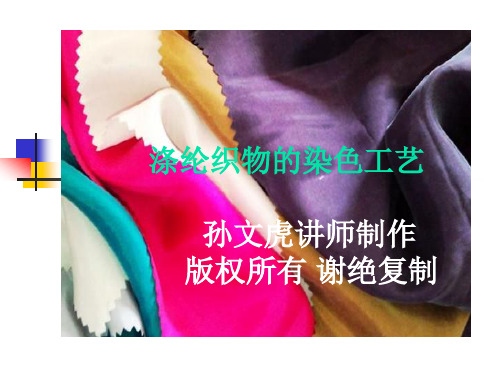
4、分散染料在什么样的条件下进行洗缸清洁。
深色急转浅色时清洗缸;染一种颜色时间过
长,转染另一种颜色时需要清洗缸。洗缸时应注 意以下问题。A:染缸要分深、中、浅专用染缸 机台,并每周清洗一次。B:为有利于机台清洁, 实行机内经常清洗。C:热交换器过滤网应每班 清理一次。D:洗缸时要开染机及喷淋管进行洗 淋喷将水放至尺位看不见为止。E:洗缸水位采用 满缸水进行还原清洗。F:洗完后,降温至80℃ 以下,排液后,将机内清缸水放入化料桶,并清 洗化料桶及输料管道。G:冷水冲洗染机及料桶
涤纶织物的能:染料分子不含有水溶性基 团,溶解度很低,染色时必须借助于分散剂使染 料均匀地分散在染液中,耐酸不耐碱,在高温碱 性条件下,分散染料分子中某些基团会水解或被 还原,使染料结构发生变化,造成色浅或萎暗。 拼色时尽量选择升华牢度相近的染料。
至干净。H:清缸参考工艺如下。
助
剂
浅色 中色 深色 特深
保险粉(kg/缸) Na2S2O4
5
8 10 12
碱(kg/缸)NaOH 8 10 15 15
或采用清缸剂8~15g/缸,主要工艺条件: 130℃X30~60min
5、分散染料出现色花后应如何去解决
煮练不良造成色花,可经再煮练一次在高温 染色机内复色。煮练按常规工艺;复色按常规工 艺130℃X30min,染色处方为:染料5~10% (占原来染料的总量)匀染剂100~200%(占 原来匀染剂总量),修补剂0.5~2ml/L,PH值
80℃以下再采取边加水加排液水洗。B、①、对
松驰煮练后的半成品,水洗一定要充分干净,布 幅中PH值控制在7~7.5,必要时,清洗水后,用 1%冰醋酸中和残碱后再水洗,要做到当班煮练, 当班染色。②、分散染料应先用1:10的冷水打 浆,再用水的温度<50℃的温水充分搅拌均匀, 稀释过滤后,方可加入染缸使用;加料顺序应是 先加稀释后的冰醋酸,再加溶解好的助剂(匀染 剂和分散剂),最后加入分散染料;③、严格按 工艺曲线做好升温与保温。④、染色容布量是否 适当,应根据不同机型和织物的厚薄不同而定, 一般容布量控制在原设计量的80%左右,染色布 长一般控制在每圈布长不超过3min。按照布的厚 薄不同及时调整喷嘴直径的大小,以便织物顺畅 运转防止喷嘴过大,织物堆置混乱而造成染色时 打结。C、染液中可加入防皱匀染剂0.5g/L促使 织物沉降润滑,减小鸡爪痕,同时使
涤纶详解

谢谢
细度(dpf)
超细 0.01 细旦 1以下 常规 1.5 2.0等等
20D/96f 84D/384f
涤纶的变化
化学共混
阻燃 超仿棉 阳离子 低熔点
原液共混
着色 消光 抗菌 竹碳 凉感 发热
纺丝共混
复合纺丝 并列纺丝
纤维共混
纱线 织物
阻燃
卤系阻燃
因为不环保,基本不用了
导电纤维
金属 不锈钢丝 镀银 涤纶或尼龙镀银
碳纤维嵌入
抗静电 用于行业服务
电阻率(Ω/cm)106~107 涤纶基长丝: 20D 涤纶基毛条:3D*76mm 可染尼纶基短纤(白色):2.5D*38mm 可染涤纶基短纤(白色):2.5D*38mm
纤维变化
高收缩 沸水收缩率大于8~9%
铜系抗菌 高浓度
锌系+铜系抗菌 对白色念珠菌强(真菌)
检测报告 甲壳素抗菌
吸湿排汗
吸湿与排汗
超细纤维吸湿 可以是自身重量的2.5倍 但不易干 就是不排汗
实现方式
改变截面 “十” “W” “米” “C”等
50D/48f 75d/72f
赋予涤纶亲水特性 50D/72f 75D/72f
0.052~ 0.05
腈纶
尼龙+粘胶
5 0.05~
140d+75d 用于床品 蚕丝
0.05 5
丙纶
铜氨长丝+尼龙
0.055~
50D+75D 用于T恤 粘胶纤维
0.07 1
氯纶
维纶包涤纶
醋脂
0.05
空气
75d 用于衬衣和T恤 锦纶
0.244~
0.33
水
7
λ/w/m·℃
一种涤纶丝高温高压染色工艺

本发明公开了一种涤纶丝高温高压染色工艺,包括以下步骤:松筒、装笼、染前处理、配置染液、同浴染色、一次水洗、还原清洗、二次水洗、脱水和烘干,所述染液配置步骤中的染料配方包括分散染料、阻燃剂、分散均染剂和醋酸,其中分散染料用量为1.8-2%(o.w.f),阻燃剂用量为15-20%(o.w.f),分散均染剂的用量为0.5~1g/L,染液的浴比为15:1,醋酸为染液的pH值调节剂,使用醋酸将染液的pH值控制在5~6之间;本发明的染液中添加有阻燃剂,阻燃剂的添加,使得涤纶丝在染色的过程中同时获得阻燃效果,提高了涤纶丝的阻燃性。
1、一种涤纶丝高温高压染色工艺,其特征在于:包括以下步骤:松筒、装笼、染前处理、配置染液、同浴染色、一次水洗、还原清洗、二次水洗、脱水和烘干,所述染液配置步骤中的染料配方包括分散染料、阻燃剂、分散均染剂和醋酸,其中分散染料用量为1.8-2%(o.w.f),阻燃剂用量为15-20%(o.w.f),分散均染剂的用量为0.5~1g/L,染液的浴比为15:1,醋酸为染液的pH值调节剂,使用醋酸将染液的pH值控制在5~6之间。
2、根据权利要求1所述的一种涤纶丝高温高压染色工艺,其特征在于:所述阻燃剂选用型号为TF-6142Y的阻燃剂,所述分散均染剂选用阴离子型的苯乙烯苯酚聚氧乙烯醚硫酸铵盐高温均染剂。
3、根据权利要求2所述的一种涤纶丝高温高压染色工艺,其特征在于:配置染液时使用40℃温水化开分散染料,充分搅拌至完全分散后加入盛有中性软水的高温高压染机的染缸内,然后加入阻燃剂、分散匀染剂和醋酸,并搅拌均匀。
4、根据权利要求1-3任意一项所述的一种涤纶丝高温高压染色工艺,其特征在于:所述松筒步骤使用不锈钢弹簧管进行,松筒后涤纶丝的缠绕密度为0.33-0.39g/cm3,松筒后的涤纶丝装笼处理。
5、根据权利要求4所述的一种涤纶丝高温高压染色工艺,其特征在于:所述染前处理步骤为将装笼的涤纶丝浸入淡碱溶液中,在100-120℃条件下处理10-20min,并加入皂洗剂1g/L去油处理,然后使用70-80℃的清水进行冲洗,冲洗时间为5-10min。
分散染料涤纶染色

偶氮型分散染料
1. 苯-N=N-苯
大部分偶氮型分散染料属于此类。
R2
R4
R1
NN
R6 N
R7
R3
R5
R1:-NO2; R2、R3:H或吸电子基(-Cl、-Br、-CN、-NO2、
-COOCH3等); R4、R5:-CH3、-OCH3、-NHCOCH3等; R6、R7:-C2H5、-C2H4OH、-C2H2CN、
分散染料
1. 特点 • 染料分子结构简单。 • 不含水溶性基团,含有极性基团(-NH2、-OH、-NO2、
-CN等),染料微溶于水;染料的溶解度随染液温度的提 高而提高。 • 染色时染液中染料以分散状态存在;染料以单分子状态上 染纤维。 • 染色方法有高温高压染色法、热熔染色法、载体染色法。 • 主要用于涤纶纤维染色,染色牢度好,但部分染料的耐升 华牢度差。也可用于醋酯纤维、锦纶、腈纶纤维染色。
杂环部分可以是重氮组分或偶合组分。
O2N
N
NN
S
C2H5OCOCH3 N
C2H5OCOCH3
C.I.分散CH3蓝295
蒽醌型分散染料
• 色谱全,主要有红、紫、蓝色,颜色鲜艳,性质 稳定(化学稳定性、光化学稳定性、热稳定性 好) ,即耐晒、耐热、耐还原性能好;
• 成本比偶氮染料高; • 着色力不及偶氮染料。
2、工艺处方
• 分散染料
x%(对织物重)
• 分散剂NNO(或胰加漂T)
0~0.5g/L
• 冰HAC
0.5ml/L(调节PH=5~6)
二、热溶染色法工艺
• 1、工艺流程及主要条件
浸轧染液(二浸二轧,轧余率65%,20~40℃)→预烘 (80~120℃) →热溶(180~210℃,1~2min)→后处理(或 套染棉)
染色涤纶经编绒布申报要素
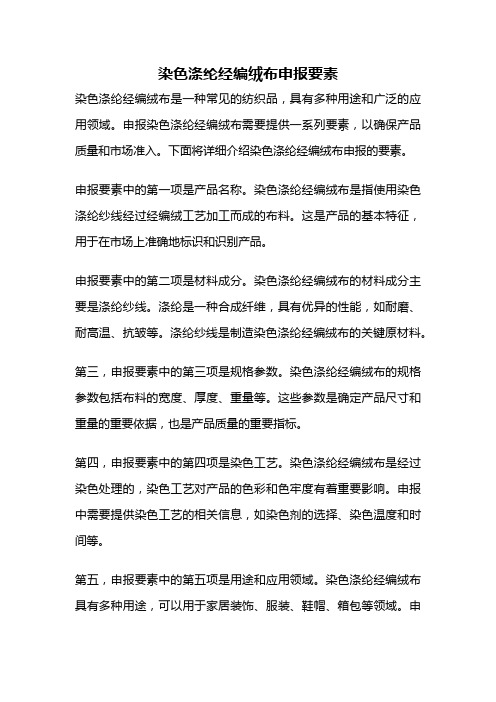
染色涤纶经编绒布申报要素染色涤纶经编绒布是一种常见的纺织品,具有多种用途和广泛的应用领域。
申报染色涤纶经编绒布需要提供一系列要素,以确保产品质量和市场准入。
下面将详细介绍染色涤纶经编绒布申报的要素。
申报要素中的第一项是产品名称。
染色涤纶经编绒布是指使用染色涤纶纱线经过经编绒工艺加工而成的布料。
这是产品的基本特征,用于在市场上准确地标识和识别产品。
申报要素中的第二项是材料成分。
染色涤纶经编绒布的材料成分主要是涤纶纱线。
涤纶是一种合成纤维,具有优异的性能,如耐磨、耐高温、抗皱等。
涤纶纱线是制造染色涤纶经编绒布的关键原材料。
第三,申报要素中的第三项是规格参数。
染色涤纶经编绒布的规格参数包括布料的宽度、厚度、重量等。
这些参数是确定产品尺寸和重量的重要依据,也是产品质量的重要指标。
第四,申报要素中的第四项是染色工艺。
染色涤纶经编绒布是经过染色处理的,染色工艺对产品的色彩和色牢度有着重要影响。
申报中需要提供染色工艺的相关信息,如染色剂的选择、染色温度和时间等。
第五,申报要素中的第五项是用途和应用领域。
染色涤纶经编绒布具有多种用途,可以用于家居装饰、服装、鞋帽、箱包等领域。
申报中需要明确指出产品的主要应用领域,以便市场和消费者了解和选择产品。
第六,申报要素中的第六项是产品质量标准。
染色涤纶经编绒布的质量标准包括物理性能、化学性能、环境性能等方面。
申报中需要提供相应的标准和测试方法,以确保产品符合相关的质量要求。
申报要素中的最后一项是生产厂家信息。
染色涤纶经编绒布的生产厂家信息是确保产品可追溯性和质量保证的重要依据。
申报中需要提供生产厂家的名称、地址、联系方式等信息。
染色涤纶经编绒布申报要素包括产品名称、材料成分、规格参数、染色工艺、用途和应用领域、产品质量标准和生产厂家信息。
提供这些要素可以确保产品质量和市场准入,为消费者提供优质的染色涤纶经编绒布产品。
- 1、下载文档前请自行甄别文档内容的完整性,平台不提供额外的编辑、内容补充、找答案等附加服务。
- 2、"仅部分预览"的文档,不可在线预览部分如存在完整性等问题,可反馈申请退款(可完整预览的文档不适用该条件!)。
- 3、如文档侵犯您的权益,请联系客服反馈,我们会尽快为您处理(人工客服工作时间:9:00-18:30)。
涤纶染色温度精编版 MQS system office room 【MQS16H-TTMS2A-MQSS8Q8-MQSH16898】
涤纶染色工艺及条件
一.高温高压染色
1化料(40℃温水化料),且过滤;
2染色过程中,染色温度慢慢升至120℃~130℃,在升至染色转变温度以上时,上染速率迅速提高,要严格控制升温速率,保证染料均匀上染;
3继续保温染色45~60MIN
4然后降温,进行还原清洗,水洗等后处理,彻底去除浮色,以提高产品的染色牢度及光泽度;
注:染色温度选择在120℃~130℃为宜,温度不能超过145℃,否则纤维容易造成损伤;染色温度总体控制分为一下三个阶段:
A染色升温阶段:在70~110℃温度区间,染料上染速率较快,要严格控制1~2℃/MIN,以保证染料均匀被吸附;
B染色保温阶段:染料向纤维内部扩散,并增进染料移染,染匀,染透;
C降温阶段:在玻璃化温度以上,降温速率应适当慢些,其后快速降温,避免引起织物产生折皱和手感粗糙等现象;
5PH值的管控
PH值控制在5~6之间,色光纯正,色泽鲜艳,上染百分率高;
注:高温碱性,染料水解,碱性太强,织物损伤打,手感差,但酸性太强,齐聚物容易沉积在织物表面;
6浴比:匹染:10:1~30:1
注:浴比小了,节能节水,但易使织物产生折皱,擦伤,染色不均等;
浴比大了,耗能耗水;
7分散剂的影响:匀染剂(载体,非离子型活性剂)
A缓染剂:通过助剂对染料或纤维亲和力,延缓染料上染,使染料能够均匀的吸附在纤维的各个部位,从而染色均匀,但上染百分率会有所下降;
B移染:匀染剂一般为载体,非离子型聚氧乙烯类表面活性剂;载体有毒,非离子型表面活性剂在染色温度高于浊点时,会产生沉淀,一般需与阴离子表面活性剂复配用;
二.热熔染色
热熔染色工艺,目前在盛泽地区运用还较少,在福建运用较为广泛:
1它是在185℃~215℃干热条件下使染料在纤维上发生固着连续轧染的染色方法,连续化生产,生产率较高,节能节水,对染料的耐升华牢度要求较高,染色时,织物所受的张力较大,织物手感及色泽鲜艳度不及高温高压染色法;
2浸轧液的成分:分散染料,分散剂,渗透剂,防泳移剂等;
3对染料的要求:染料可以要非常匀细,其渗透性及分散稳定性要好。