VAVE价值工程价值分析报告
vave价值工程详解

vave与生产计划
生产计划
VAVE方法在生产计划中的应用,能 够更好地协调和平衡生产能力、交货 期和库存等要素,实现更优的生产计 划。
资源优化
VAVE方法可以优化资源利用,降低生 产成本和提高生产效率。例如,通过 对生产流程的优化,可以减少生产过 程中的浪费,提高资源利用效率。
生产灵活性
VAVE方法可以提高生产灵活性,更好 地应对市场变化和客户需求。例如, 通过采用模块化设计和生产,可以快 速调整和转换生产模式,满足不同客 户的需求。
vave与生产控制
生产控制
VAVE方法在生产控制中的应用,可以更好地协调和平衡生产进度和质量等要素,实现更 优的生产控制。
质量控制
VAVE方法可以优化质量控制,提高产品质量和客户满意度。例如,通过采用先进的质量 检测技术和设备,可以实现产品质量的有效控制和持续改进。
生产协调
VAVE方法可以加强生产协调,提高生产效率和生产管理水平。例如,通过采用先进的生 产管理系统和技术,可以实现各生产部门之间的有效协调和沟通,提高生产效率和生产管 理水平。
通过对产品或系统进行分析,找 到能够提高性能的关键因素,实 现产品或系统的优化设计。
增强可靠性
通过研究产品或系统的可靠性, 采取有效的措施提高产品或系统 的可靠性,降低维修和更换成本 。
价值分析的原理
以功能分析为核心
通过对产品或系统进行功能分析,了解产品或系统所能实现的功能及其重要性。
生命周期成本分析
对产品或系统进行功能分 析,了解各功能的重要性 。
制定替代方案
根据功能分析的结果,制 定替代方案,并对各方案 进行比较和分析。
进行成本分析 和比较
对各替代方案进行成本分 析和比较,找出最优方案 。
建筑工程项目价值分析
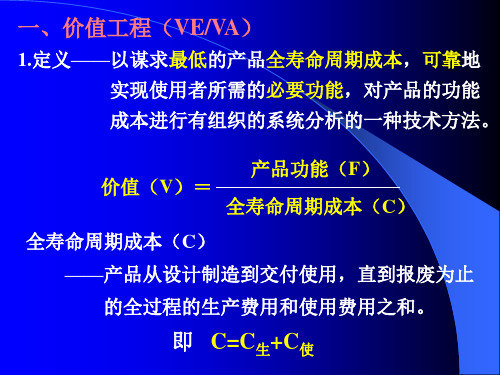
平均得分 功能评价系数 F=
平均得分总和
第二步,求成本系数 零部件成本
成本系数(ci)= 总成本 第三步,求价值系数
价值系数 ( vi )=
功能系数( fi ) 成本系数( ci )
最后按以下原则进行选择(3种情况):
F V=1
V>1
V<1 C
V<1,成本偏高,应作为分析对象 V>1,较理想,但若V很大可能存在质量隐患,则要
曲线所包络的阴影部分为最合适区域
曲线的确定:
即曲线上任意一点Q(前图)价值系数坐标图(Xi , Yi )至标准线V=1的垂线QP即Q点到标准线的距离R与OP 即P点到坐标中心 O的长度L, R与L的乘积是一个给定的
常数S, 见下图。
R×L= R1×L1 = R2×L2 = S
L大则R小 S一定
L小则R大
现举自来水笔作例子来说明这一方法。
把自来水笔分为墨水、笔尖、笔圈、吸墨水管、 押黄、笔杆、杆帽、气孔、笔套九个零件。根据功能 分析求出各零件的功能评价系数、成本系数,并已求 得各零件的价值系数 (见下表)。
通过试验取S=50,在价值系数坐标图上作出的两 条曲线,并把表中的数值画在价值系数坐标图上 (见下 图)。
总
代号 A B C D E F G
计
费 用(元) 29113.01 41909.53 75149.86 10446.04 20571.49 33777.31 5390.59
216357.83
% 13.46 19.37 34.73 4.83 9.51 15.61 2.49 100
按费用(或其百分比)大小排序:
末位功能1 并列 末位功能2 关系
目
手段
价值分析与价值工程VAVE
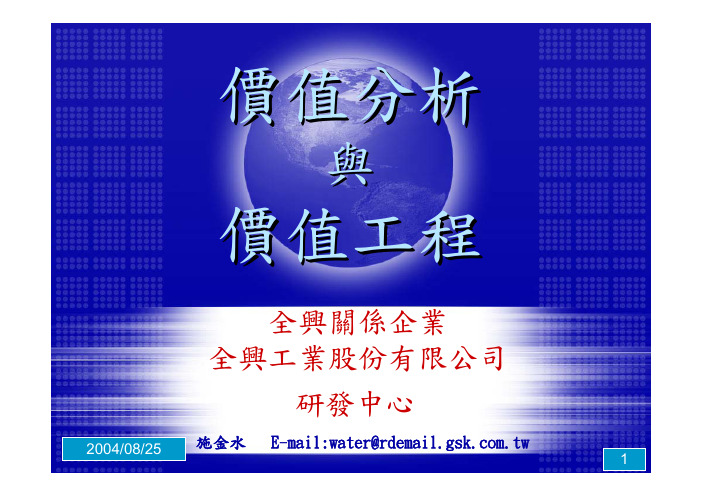
產品製造階段:(VA)
產品製作依排定加工過程逐一完成該程序。
產品行銷階段:(VA)
接觸顧客,回饋顧客聲音,販賣顧客所需之產品。
2009/10/9 WATER
7
價值工程
產品設計階流程
產品概念(客戶心聲-V.O.C.) 產品企劃(設計目標) 企劃審查(可行性評估) 產品設計(產品關鍵特性) 設計審查(D-FMEA) 設計驗證(MOCKUP製作) 產品開發(產品展開工程)
價值分析
與
價值工程
全興關係企業 全興工業股份有限公司
研發中心
2004/08/25 施金水 E-mail:water@
1
課程內容
壹.導言(環境競爭區相) 貳. 價值分析與價值工程(VA/VE的定義及意義表述) 參.價值工程(產品設計概念及價值來源) 肆.核心能力(市場發展的專業能力) 伍.價值分析(產品規劃、成本分析及改善精神及步驟) 陸.結論(價值、機能與成本關係) 柒.Q & A(交流)
2009/10/9 WATER
•產品系統設計審 查 •分系統或分項設 計審查 •組件設計審查 •零件設計審查 •原料設計審查
41
柒.產品設計理念
產品設計審查效果
•可告性保證
避免失敗重演,選擇適當材料.加工製程.安全係數.考慮人體工學,維修 容易
•製造成本降低
適切另件,材料,使用庫存,共用件,易製化
產品創造與創新
什麼是創造?
產生新穎、有價值的知識 必須要有
豐富的創意與創造力
什麼是創新?
產生新穎、有價值的事與物
2009/10/9 WATER
14
參.產品創意設計
產品創新方式
价值分析VA价值工程VE
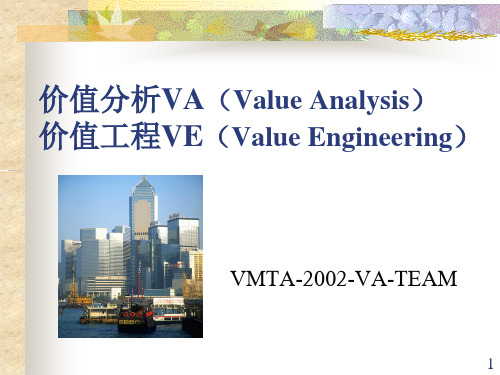
32
⑨ ⑩ ⑪ ⑫ ⑬ ⑭ ⑮ ⑯
检讨能否增加生产量 检讨能否改变生产方法 检讨能否减低不必要的作业程序 检讨能否将作业简化 检讨能否将作业综合起来操作? 检讨能否停止作业的检查? 检讨间接费用与利益是否适当? 检讨供应者是否适当?
33
降低成本的注意事项
降低成本的注意事项 (1)设 计 ① 注意是否有机能不明的零件 ② 注意是否能够减少螺丝钉 ③ 是否多做必要作业以上的工作量? ④ 零件的尺寸是否能够缩小 ⑤ 一个零件是否能够兼具双重机能? ⑥ 公差是否符合
基本步骤 工作计划 技术的应用
1.决定功能 1. 决定方针 1. 消除一般性论调
2. 搜集情报 2. 从可靠的情报来源取得解答
6.消除障碍
2.功能评价 2.搜集情报 1.消除一般性论调
2.了解成本
3.从可靠的情报来源取得解答
6.消除障碍
8.对主要的公差作成本的评价
9.利用业者可用的功能制品
11.使用专门的生产程序
CPM法)
26
箭头图例
0
0
1
A
5
B 3
5 5 2
8
11
E
3
4
D 10
1
51
5G
5
5
2 02 60
1
C
41
F
9
45
4
要径(CP): 1
2
5
6
27
八、结语:
VA、VE是一种组织方式的活动,其目的是借
此手法达成降低成本,达到最高利润的目的, 其对象原仅是产品,服务也是其对象之一。
故有组织的VA/VE變形蟲組織‘扁平組織
价值分析VA(Value Analysis) 价值工程VE(Value Engineering)
VAVE价值分析

VA/VE价值工程/价值分析一、发展史:1.1947年美国GE 公司麦尔斯发表VA/VE至今已有50年.2.1955年日本开始研究VA/VE并在企业界,学术界不断使用训练,并成立日本VE 协会.3.1980年日本设立了麦尔斯奖,松下幸之助曾表示“经营=VE”,稻盛和夫也主张“决定价格就是经营”.4.1967年中国生产力中心邀请日本产业能率大学学者开办 VA/VE课程.二、VA/VE 的概念与原则:1.概念:透过组织的努力,针对产品或服和的机能加以研究,以最低的寿命周期成本(life cycle cost)成本,确实达到必要的机能.V=F/CV:Value价值 F:Function 机能 C: Cost 成本2.VA/VE的五大特点:(1)组织的努力(2)机能的研究(3)对象为产品或服务(4)最低的寿命周期成本(5)确实达成必要的机能3.VA/VE活动中必须遵守的七个原则:(1)顾客优先原则(2)价值提升原则(3)机能思考原则(4)经济性思考原则(5)创造性思考原则(6)情报活用原则(7)团队设计(Team Design)原则三、提高价值的基本途径:1.F不变,降低成本,提高V. F /C =V2.C不变,F提高,增加V. F /C=V3.F增加,C增加,增加V. F /C =V4.F下降(降低次要功能),C下降,V增加 F /C =V5.运用新技术,改革产品,提高F ,降低C. F /C =V四、VA/VE的实施步骤:1.对象的选择2.情报的收集3.功能分析4.提改进方案5.方案评价与选择6.试验7.提案审批和实施对象的选择功能分析提改进方案试验提案,审批,实施五、VA/VE对象的选择:1.原则:以能否收到较大的经济效果为基本原则.2.对象:(1)产品:a.需求量大的产品b.正在研制即将投入市场的新产品c.竞争激烈的产品d.用户意见大,急需改进的产品e.成本高,利润少的产品f.结构复杂,技术落后,工序繁多,工艺落后,原材料品种多,紧缺资源耗用量大的产品.(2)零部件:a.数量多的零部件.b.制造费用高的零部件.c.结构复杂的零部件.d.体积重量大的零部件.e.用料多,耗缺稀资源的零部件.f.坏品率高的产品六、VA/VE的十大思考方向:1.一个恒久不变的真理:最终目的为“顾客满意”.2.由两大领域下手:目的与手段.3.除三呆、灭三K,以三大技术、三个基本步骤,达到三化(3S)(1)三呆:不节省、不合理、不均一(2)三K:脏乱、危险、吃力.(3)三大技术:成本分析、机能分析、创造力技术(4)三个基本步骤:机能分析、机能评价、提出改善方案(5)三化:标准化、专业化、简单化.4.应用改善四原则、改善四方向于管理四循环.(1)改善四原则:消除、合并、重排、简化(2)改善四方向:解决问题、改善现状、创造新机、突破现状(3)管理四循环:计划、实施、确认、处置5.五五问法~5W2H与5Why(1)5W2H:What,Who,When,Where,Why,How to do,How much(2)5Why:丰田5个为什么a.为何要这么做?b.为何要使用现行的机械?c.为何要在此处进行这项工作?d.为何要依现行的顺序去做?e.为何要做成这个样子?6.六大目标~PQCDSM产量(Production)、品质(Quality)、成本(Cost) 、交期(Delivery) 、安全(Safety)士气(Morale) 7.思考七个问题来消除七大浪费:(1)七个问题:a.它是什么?b.它的机能是什么?c.它的成本是多少?d.它的价值是多少?e.有哪些方法可以达到对象的机能?f.新方案的成本是多少?g.新方案能满足要求吗?(2)七大浪费:a.制造不良的浪费b.制造过多的浪费c.加工的浪费d.搬运的浪费e.库存的浪费f.动作的浪费g.等待的浪费8.八个改善着眼点:材料、加工、模治检具、能源、物流、品质、规格、采购9.九点查检表(Osborne查检表)(1)替代(Substitute)(2)组合(Combine)(3)能否从其它类似的东西借取构想(Adopt)(4)修正(Modify)(5)扩大(Magnify)(6)缩小( Minify)(7)有无其它的使用方法(Put to other use)(8)重排(Rearrange)(9)相反(Reverse)10.成功的十大关键因素(KSF)(1)高阶主管必须真心投入与支持.(2)负责执行的人必须得到上级的授权.(3)执行的人要尽量专职,而且日后要成为这方面的专家.(4)推动VA/VE活动必须由上而下(Top Down),而提出VA/VE改善必须是由下而上(Bottom Up)(5)推动小集团活动培养自动自发的精神(6)建立模范团队,以便让其它人员观摩与效法.(7)与其它推动VA/VE有成效的公司作交流.(8)采跨机能(Cross-function)的组织.(9)各单位良好的互动人际关系.(10)强调并落实VA/VE教育训练.七、VA/VE未来展望:1.提升竞争力的有效途径:竞争力=f(价值/成本)2.提高效率的最佳技巧:最小投入最大产出之原则来设计整个进行过程以达到降低成本的目标.3.导入VA/VE的产业逐渐扩大.制造、营建、物流、服务、医疗业.4.促进经营中的核心管理技术成长.5.以附加价值链协助企业流程改造.顾客价值分析竟争策略产品/服务制程价值采购/供货商价值工程分析价值分析6.融合改善与创新的手法为达成顾客满意.7.符合环境保护的世界趋势.8.价值管理将成为企业体质改善经营活动.9.VA/VE与IE,QC之融合.(参照表一)10.VA/VE是企业永续经营的有效途径.表一IE、QC、VE三大管理技术的比较表二企业永续经营的四个方向八、价值工程活动成果评价:1.全年凈节约额.全年凈节约额=改进前单件成本-改进后单件成本) X年产量-VE/VA活动费用.2.成本降低率= 改进前成本-改进后成本改进前成本 X 100%3.投资效率:投资效率= 全年凈节约额价值工程活动费用。
VEVA相知介价值工程ValueEngineeringVE,又称价值分析
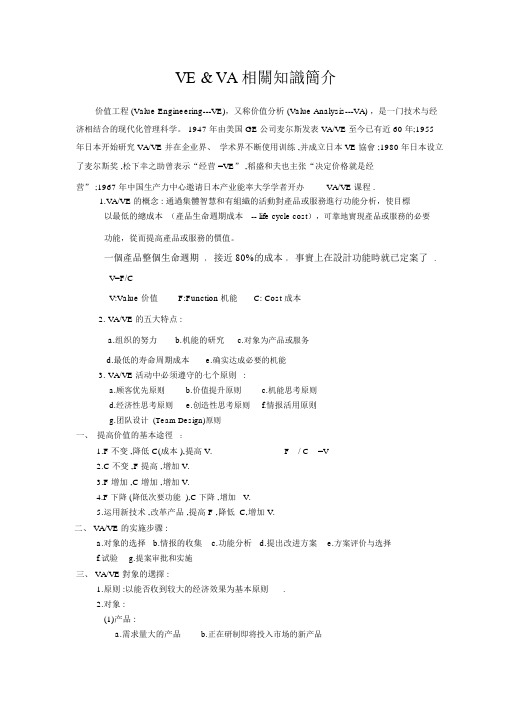
VE & VA 相關知識簡介价值工程 (Value Engineering---VE),又称价值分析 (Value Analysis---VA) ,是一门技术与经济相结合的现代化管理科学。
1947 年由美国 GE 公司麦尔斯发表 VA/VE 至今已有近 60 年;1955年日本开始研究 VA/VE 并在企业界、学术界不断使用训练 ,并成立日本 VE 協會 ;1980 年日本设立了麦尔斯奖 ,松下幸之助曾表示“经营 =VE” ,稻盛和夫也主张“决定价格就是经营” ;1967 年中国生产力中心邀请日本产业能率大学学者开办VA/VE 课程 .1.VA/VE 的概念 : 通過集體智慧和有組織的活動對產品或服務進行功能分析,使目標以最低的總成本(產品生命週期成本-- life cycle cost),可靠地實現產品或服務的必要功能,從而提高產品或服務的價值。
一個產品整個生命週期,接近 80%的成本,事實上在設計功能時就已定案了.V=F/CV:Value 价值F:Function 机能C: Cost 成本2. VA/VE 的五大特点 :a.组织的努力b.机能的研究c.对象为产品或服务d.最低的寿命周期成本e.确实达成必要的机能3.VA/VE 活动中必须遵守的七个原则 :a.顾客优先原则b.价值提升原则c.机能思考原则d.经济性思考原则e.创造性思考原则f.情报活用原则g.团队设计(Team Design)原则一、提高价值的基本途徑:F / C=V1.F 不变 ,降低 C(成本 ),提高 V.2.C 不变 ,F 提高 ,增加 V.3.F 增加 ,C 增加 ,增加 V.4.F 下降 (降低次要功能 ),C 下降 ,增加V.5.运用新技术 ,改革产品 ,提高 F ,降低 C,增加 V.二、 VA/VE 的实施步骤 :a.对象的选择b.情报的收集c.功能分析d.提出改进方案e.方案评价与选择f.试验g.提案审批和实施三、 VA/VE 對象的選擇 :1.原则 :以能否收到较大的经济效果为基本原则.2.对象 :(1)产品 :a.需求量大的产品b.正在研制即将投入市场的新产品c.竞争激烈的产品d.用户意见大 ,急需改进的产品e.成本高 ,利润少的产品f.结构复杂、技术落后、工序繁多、工艺落后、原材料品种多、紧缺资源耗用量大的产品(2)零部件 :a.数量多的零部件b.制造费用高的零部件.c.结构复杂的零部件d.体积重量大的零部件.e.用料多,耗缺稀资源的零部件f.坏品率高的产品四、四、VA/VE 的十大思考方向 :1.一个恒久不变的真理:最终目的为“顾客满意”.2.由两大领域下手 :目的与手段 .3.除三呆、灭三K,以三大技术、三个基本步骤,达到三化 (3S)(1)三呆 :不节省、不合理、不均一(2)三 K: 脏乱、危险、吃力.(3)三大技术 :成本分析、机能分析、创造力技术(4)三个基本步骤 :机能分析、机能评价、提出改善方案(5)三化 :标准化、专业化、简单化.4.应用改善四原则、改善四方向于管理四循环.(1)改善四原则 :消除、合并、重排、简化(2)改善四方向 :解决问题、改善现状、创造新机、突破现状(3)管理四循环 :计划、实施、确认、处置5.五五问法 ~5W2H 与 5Why(1)5W2H:What,Who,When,Where,Why,How to do,How much(2)5Why:丰田 5 个为什么a.为何要这么做 ?b.为何要使用现行的机械 ?c.为何要在此处进行这项工作 ?d.为何要依现行的顺序去做 ? e.为何要做成这个样子 ?6.六大目标 ~PQCDSM产量 (Production)、品质 (Quality)、成本 (Cost) 、交期 (Delivery) 、安全 (Safety)士气 (Morale) 7.思考七个问题来消除七大浪费:(1)七个问题 :a.它是什么 ?b.它的机能是什么 ?c.它的成本是多少 ?d.它的价值是多少 ?e.有哪些方法可以达到对象的机能?f. 新方案的成本是多少?g.新方案能满足要求吗?(2)七大浪费 :a.制造不良的浪费b.制造过多的浪费c.加工的浪费d.搬运的浪费e.库存的浪费f.动作的浪费g.等待的浪费8.八个改善着眼点 :材料、加工、模治检具、能源、物流、品质、规格、采购9.九点查检表 (Osborne查检表 )(1)替代 (Substitute)(2)组合 (Combine)(3)能否从其它类似的东西借取构想(Adopt)(4)修正 (Modify)(5)扩大 (Magnify)(6)缩小 ( Minify)(7)有无其它的使用方法(Put to other use)(8)重排 (Rearrange)(9)相反 (Reverse)10.成功的十大关键因素 (KSF)(1)高阶主管必须真心投入与支持.(2)负责执行的人必须得到上级的授权.(3)执行的人要尽量专职,而且日后要成为这方面的专家.(4)推动 VA/VE 活动必须由上而下(Top Down),而提出 VA/VE 改善必须是由下而上(Bottom Up)(5)推动小集团活动培养自动自发的精神(6)建立模范团队 ,以便让其它人员观摩与效法.(7)与其它推动VA/VE 有成效的公司作交流.(8)采跨机能 (Cross-function)的组织 .(9)各单位良好的互动人际关系.(10)强调并落实VA/VE 教育训练 .四、 VA/VE 未來展望 :1.提升竞争力的有效途徑:竞争力 =F(价值 /成本 )2.提高效率的最佳技巧:以最小投入最大产出之原则来设计整个进行过程以达到降低成本的目标.3.导入 VA/VE 的产业逐渐扩大 .制造业、营建业、物流业、服务业、医疗业.4.促进经营中的核心管理技术成长.5.以附加价值链协助企业流程改造.顾客价值分析竟争策略产品/服务制程价值采购/供货商价值工程分析价值分析6.融合改善与创新的手法为达成顾客满意.7.符合环境保护的世界趋势.8.价值管理将成为企业体质改善经营活动.9.VA/VE 与 IE,QC 之融合 .(参照表一 )10.VA/VE 是企业永续经营的有效途徑.表一 : IE 、QC、 VE 三大管理技术的比较企业的三大管理技术改善方法的名称IE(Industrial QC(Quality Control)VE(Value Engineering)Engineering)分析现有的制程或作为了品质的维持及提各种产品或工作必有其存在目的主要的内容业方法 ,并测定所需时升 ,应用各种的统计方或亦即具有某种机能 ,从机能的角间或工时 ,以改善工作法做分析、量测 ,以设度做分析的方法及时间定品质基准诞生年代1911 年1920年1947年特征现象面原因面目的面原来的目的提高工程与作业的效提升产品与服务的品提升产品与服务的价值率质有效利用人员 ,机械材料方法设计管理等资源最终的目标顾客满意方法研究 (动作研究 )QC 七大手法成本分析主要的技术作业测定 (时间研究 )机能分析新 QC 七大手法创造力技术与降低成本的透过工时的减少或各透过顾客抱怨的减少, 透过具有相同机能的其它方法之种浪费的排除来降低不良的降低等来降低引进来大幅地降低成本相关性成本成本属性归纳归纳发散表二 : 企业永续经营的四个方向因果分析矯正措施解決問題Repair改善現狀腦力激蕩改善對策Refine4R創造新機品質標竿突現創意Renovate突破現狀再造工程流程革命Reinvent五、价值工程活动成果评价:1.全年凈节约额 .全年凈节约额 =(改进前单件成本---改进后单件成本 ) * 年产量 --VE/VA 活动费用 .2.成本降低率 =改进前成本--改进后成本*100%改进前成本3.投资效率 :投资效率 =全年凈节约额价值工程活动费用应用价值工程 (VE)理论,对工程项目进行科学的分析,对设计方案进行优化选择,不仅从技术上,还要从技术与经济相结合的前提下进行充分论证,在满足工程结构及使用功能要求的前提下,依据经济指标和综合效益选择设计方案,显得越来越重要。
采购价值工程与价值分析VAVE
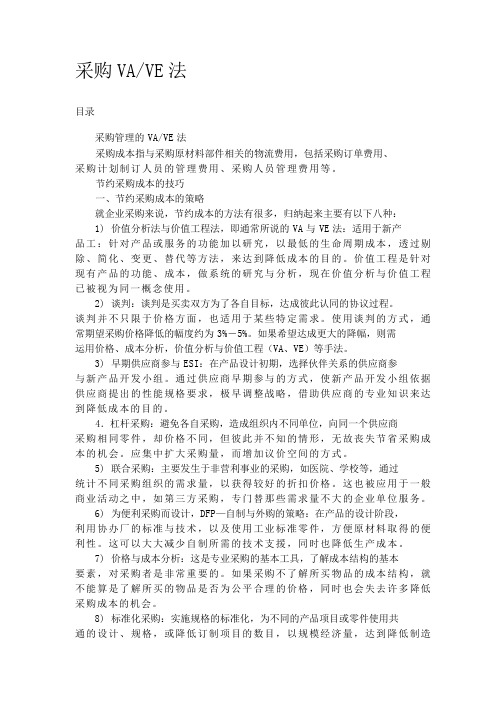
采购VA/VE法目录采购管理的VA/VE法采购成本指与采购原材料部件相关的物流费用,包括采购订单费用、采购计划制订人员的管理费用、采购人员管理费用等。
节约采购成本的技巧一、节约采购成本的策略就企业采购来说,节约成本的方法有很多,归纳起来主要有以下八种:1)价值分析法与价值工程法,即通常所说的VA与VE法:适用于新产品工:针对产品或服务的功能加以研究,以最低的生命周期成本,透过剔除、简化、变更、替代等方法,来达到降低成本的目的。
价值工程是针对现有产品的功能、成本,做系统的研究与分析,现在价值分析与价值工程已被视为同一概念使用。
2)谈判:谈判是买卖双方为了各自目标,达成彼此认同的协议过程。
谈判并不只限于价格方面,也适用于某些特定需求。
使用谈判的方式,通常期望采购价格降低的幅度约为3%-5%。
如果希望达成更大的降幅,则需运用价格、成本分析,价值分析与价值工程(VA、VE)等手法。
3)早期供应商参与ESI:在产品设计初期,选择伙伴关系的供应商参与新产品开发小组。
通过供应商早期参与的方式,使新产品开发小组依据供应商提出的性能规格要求,极早调整战略,借助供应商的专业知识来达到降低成本的目的。
4.杠杆采购:避免各自采购,造成组织内不同单位,向同一个供应商采购相同零件,却价格不同,但彼此并不知的情形,无故丧失节省采购成本的机会。
应集中扩大采购量,而增加议价空间的方式。
5)联合采购:主要发生于非营利事业的采购,如医院、学校等,通过统计不同采购组织的需求量,以获得较好的折扣价格。
这也被应用于一般商业活动之中,如第三方采购,专门替那些需求量不大的企业单位服务。
6)为便利采购而设计,DFP—自制与外购的策略:在产品的设计阶段,利用协办厂的标准与技术,以及使用工业标准零件,方便原材料取得的便利性。
这可以大大减少自制所需的技术支援,同时也降低生产成本。
7)价格与成本分析:这是专业采购的基本工具,了解成本结构的基本要素,对采购者是非常重要的。
VEVA价值工程价值分析

VEVA价值工程价值分析VE(Value Engineering)是一种系统化、创造性的方法,它通过对产品、工程或业务流程进行分析和评估,寻找新的解决方案,从而提供更高的性能、更低的成本或更好的价值。
VE最早由美国建筑师劳伦斯·米尔斯创立于1947年,其目的是在完全满足使用要求的前提下,尽可能减少成本。
VE强调在完全满足用户需求的前提下,通过优化设计、材料和流程等方面来降低成本。
VE将多种技术、方法和工具相结合,以提高效率和提供更高的客户满意度。
在实践过程中,VE通常以以下步骤进行:1.识别目标和制定计划:明确项目目标,加强项目计划和团队组织,确定VE活动的范围和时间表。
2.建立工作组:组建VE工作组,包括来自不同领域的专家,以保证综合性和多角度的分析。
3.收集和分析信息:收集和整理与项目相关的信息,包括技术规范、用户需求、工艺流程等,以便分析和评估现有方案。
4.创造性的想法与方法:根据收集的信息,工作组成员进行创造性的思考,提出新的想法和方法,以改进现有方案。
5.剔除无效方案:根据分析和评估结果,剔除不可行或不经济的方案,留下具有较高性能和较低成本的方案。
6.实施和监控:选择最佳方案后,制定实施计划,并在执行过程中进行监控和控制,以确保项目效果达到预期。
VA(Value Analysis)是VE的一项重要技术,它主要用于评估和改进现有产品、服务或流程的价值。
VA通过对产品或服务进行分解、分析和评估,找出其中的价值和浪费,从而优化设计和提高价值。
价值工程和价值分析可以在各个行业和领域中应用。
在制造业中,价值工程可以用于改善产品设计和制造流程,降低成本和提高质量。
在建筑行业中,价值工程可以用于优化设计、节约材料和改善施工流程。
在服务行业中,价值工程可以用于评估和改进服务流程,提高服务质量和客户满意度。
总之,VE和VA作为一种系统化的方法和工具,可以帮助组织和企业提供更具竞争力的产品和服务,通过降低成本、提高质量和创新等方式来提高综合竞争力。
价值分析VAVE

價值分析之發展沿革
誕生 1947 發展 1954~1963 導於日本 1960~1965 由於 Asbestos事件(GE公司) VA終於被 開發 (L.D. Miles) 被國防部船舶局採用,改稱為VE被加 入於國防部減低成本計畫中,因此企業 爭相採用 由於S.F. 哈因立滋之介紹在採購部門獲 得成果
授課大綱源自 基本概念 顧客價值與評估
價值分析的沿革與技術
機能定義與評價
替代方案製作與執行
問題與討論
基本概念
利潤與管理技術 企業擴大利益之考量
價值分析與其他管理技術之關係
利潤與管理技術
企業為了貢獻於社會並持續發展,必需擴大利基來 增加利潤,而增加利潤的方法有三種:
以較低成 本獲得較 佳機能之 東西
以相同成 本獲得較 佳機能之 東西
(A)
以稍高成 本獲得更 佳機能之 東西
【VE與減低成本】 減低成本 減低成本 ≠VE=價值提昇 非減低成本
(B) (C) 機能提昇 成本增加
(D)
價值分析技術的特徵
顧客本位之想法 機能中心的手法
團隊設計(Team Design)
顧客希望從交易中獲取價值 價值就是低價格
顧客價值
稀少價值 交換價值
成本價值
貴重價值(魅力價值)
顧客價值之評估
V(Value)
: 價值之尺度。
F(Function) :製品或服務之機能價值
C(Cost) 。
: 完成該機能所需要之總成本
顧客價值管理原則
VAVE价值工程价值分析定稿版
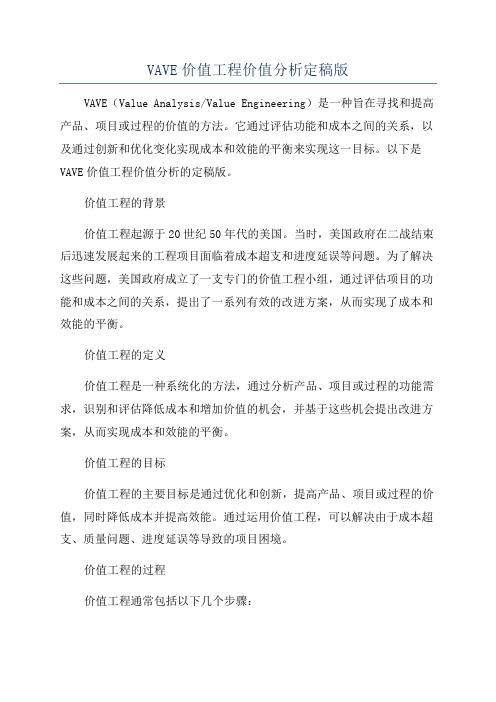
VAVE价值工程价值分析定稿版VAVE(Value Analysis/Value Engineering)是一种旨在寻找和提高产品、项目或过程的价值的方法。
它通过评估功能和成本之间的关系,以及通过创新和优化变化实现成本和效能的平衡来实现这一目标。
以下是VAVE价值工程价值分析的定稿版。
价值工程的背景价值工程起源于20世纪50年代的美国。
当时,美国政府在二战结束后迅速发展起来的工程项目面临着成本超支和进度延误等问题。
为了解决这些问题,美国政府成立了一支专门的价值工程小组,通过评估项目的功能和成本之间的关系,提出了一系列有效的改进方案,从而实现了成本和效能的平衡。
价值工程的定义价值工程是一种系统化的方法,通过分析产品、项目或过程的功能需求,识别和评估降低成本和增加价值的机会,并基于这些机会提出改进方案,从而实现成本和效能的平衡。
价值工程的目标价值工程的主要目标是通过优化和创新,提高产品、项目或过程的价值,同时降低成本并提高效能。
通过运用价值工程,可以解决由于成本超支、质量问题、进度延误等导致的项目困境。
价值工程的过程价值工程通常包括以下几个步骤:1.项目定义阶段:明确项目目标、范围和约束条件,确定召集和组织价值工程小组的方式。
2.信息收集阶段:收集和整理与项目相关的信息,包括功能需求、成本数据、设计图纸等。
3.功能分析阶段:识别和分析项目的功能需求,确定各种功能的重要性和优先级。
4.价值评估阶段:基于功能需求和成本数据,评估现有方案的成本效益,确定优化和创新机会。
5.改进方案阶段:针对已识别的改进机会,提出具体的改进方案,并分析其成本效益。
6.方案选择阶段:比较和评估各种改进方案,选择最具成本效益的方案。
7.方案实施阶段:根据选择的方案,实施相应的改进措施,并监控其效果和成本。
价值工程的应用价值工程可以应用于各种不同的领域和项目,包括产品开发、工程项目、生产过程等。
通过应用价值工程,可以实现成本的降低、质量的提高、进度的加快等目标。
(整理)VE、VA价值工程、价值分析

VE、V A价值工程、价值分析价值分析V A(Value Analysis )价值工程VE(Value Engineering)一、前言V A是美国奇异公司麦尔斯于1947年所创立的一种手法,其主要功用是在保持产品的性能、质量及可靠性条件下,籍有系统、有条理研究步骤,改良设计,变更材料种类或主,变更制造程序或方法,或变更来源,其各项研究期以最低成本获得产品必要的功能和质量。
二、何谓V A、VE(一)定义:“价值分析为研讨分析制品的“功能”和“成本”如何配合,作有计划、有系统、有组织的变更设计、变更材料在及形态,变更制造方法、变更供应来源……,期以真正最低本而猁必要的功能和适当质量的一种专门学问。
(二)成本与价值:1、价值的函义极为广泛,大约可分为下列四种:(1)使用的价值:工具……(2)贵重的价值:珠宝……(3)成本的价值:工资、材料…….(4)交换的价值:货币……2、成本的降低与价值的关系(1)降低成本产生的利益与增加产出的意义是相同的。
(2)成本的降低不应牺牲方为上策(3)成本的降低是消除不必要的费用3、不必要的成本的形成可分为下列种:(1)缺乏资料情报(2)缺乏构想(3)临时性的情况(4)习惯与态度4、价值分析的目标:价值是“为了猁可资信赖的工作或服务所需支付的最低价格”或“制造产品或服务所必备的功能,所城要的最低成本”。
F(功能或质量)V(价值)=C(成本或价格)三、“价值”的重要:良好的价值(Best Value)须考虑二大因素即“性能”与“能本。
”(一)产品的生命周期与价值工程的关系:1.第一阶段为研究发展期:创新功能、完善功能2.第二阶段为成长时期:降低成本3.第三阶段为成熟时期:延长产品寿命或增加更多新功能(二)企业中V A/VE工程运用的状况:1.1947年GE公司2.1954年美国海军6人小组3.1964年美国通用汽车、美国西屋公司4.1965年日本企业全面实施推动5.1999年中国大陆北京成立价值工程协会四、值分析的推行方法:*价值分析的七大基本步骤:1.选择价值分析的对象明确评定功能2.收集资料3.研究替代品与改造方案4.成本的分析5.试验可行性6.建议及实施(一)、选择价值分析的对象1.选择制品中销售金额较大或产量了多者2.制品之构造较为复杂者3.制品在严格的要求条件下,设计完成者4.与价值标准比较并检讨有降低之可能者5.制品研究开发时间较急促者6.价格在长时间固定不变者(二)、明确评定功能:任何产品均有主要功能及次要功能,在价值分析时应将制品的各种功能一一分析,按其构造及无价值零件,对功能重要性之比例是否平衡再行评定,何者可减除,何者必须保留或改进。
VAVE价值工程方案

VAVE价值工程方案一、VAVE价值工程方案的理念VAVE价值工程方案的核心理念是通过对产品设计、生产工艺、材料成本等方面进行综合优化,最大程度地实现性能和成本的平衡,从而提升产品的市场竞争力。
它主要包括以下几个方面的内容:1. 价值分析:对产品的功能和性能进行综合分析,找出设计中存在的不必要的成本,同时保持或者提升产品的功能和性能。
2. 降低成本:通过设计、材料选择、生产工艺等方面的优化,实现产品成本的降低,同时保证产品的性能和质量。
3. 提升质量:通过优化产品设计和生产工艺,保证产品的质量和可靠性,从而提升用户满意度和品牌形象。
4. 提高效率:通过优化生产工艺和流程,实现生产效率和资源利用的最大化,降低生产成本。
VAVE价值工程方案的实施可以为企业带来显著的经济效益和市场竞争优势,同时也能够促进行业的可持续发展。
二、VAVE价值工程方案在汽车行业的应用汽车行业是VAVE价值工程方案的典型应用领域。
汽车制造复杂,产品更新换代迅速,成本高、周期短等特点使得汽车制造企业对VAVE价值工程方案的需求迫切。
VAVE价值工程方案在汽车行业的应用主要集中在以下几个方面:1. 车身设计:通过优化车身结构设计、材料选择以及生产工艺,实现车身重量的减轻,从而提升汽车的燃油经济性和行驶性能。
2. 发动机设计:通过优化发动机结构、燃烧系统和冷却系统等,实现发动机功率的提升、燃油消耗的降低,从而提升汽车的动力性能和燃油经济性。
3. 零部件设计:通过优化零部件结构设计、材料选择以及生产工艺,实现零部件成本的降低、使用寿命的提升,从而降低汽车的制造成本和维护成本。
VAVE价值工程方案在汽车行业的应用可以为企业带来巨大的经济效益和市场竞争力,并且能够推动汽车行业的技术创新和可持续发展。
三、VAVE价值工程方案在电子产品领域的应用电子产品是VAVE价值工程方案的另一个重要应用领域。
电子产品更新换代快,市场竞争激烈,成本控制至关重要,因此企业对VAVE价值工程方案的需求迫切。
价值分析VAValueAnalysis概述
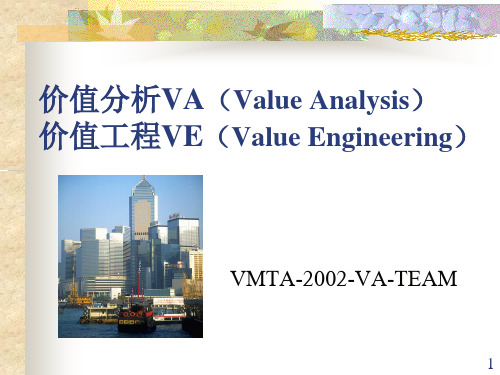
作相互评价,求出零件之加重系数。 3. 最后组合起来,功能系数与零件系
数相乘后,再相加即可求出个别组件之 价值系数。 4. 比较此价值系数就可对各零件的功 能判断其优劣性。
14
(三)收集资料: 资料收集为价值分析重要工作,内容应包括; 1. 各种材料的规格与价格 2. 各种加工方法的费用 3. 各种代用品的资料 4. 与制品有关的各种资料 5. 设计上的各种规格 6. 产品的演化资料 7. 同业间产品的状况、资讯 8. 零配件外协厂方面的资料
15
(四)研究替代品与改进方案: 1. 集体脑力风暴法 2. 比较分析法 3. 查检表(调查表)法
16
1`/一、头脑风暴法(BS法) BS是Brain Storming的缩写,是指自由奔放、 打破常规、创造性的思考问题。我国的“诸葛 亮会”与此类似。一般由5-13个参与为宜,主 持人要熟悉价值工程研究对象、善于引导,参 加人员要有企业内外部的专业人员。 BS法有四条规则:①不互相指责;②鼓励自由 的提出想法;③欢迎提出大量方案;④欢迎完 善别人提出的方案。 在会议上对表达的设想,不必追求全面系统, 但记录工作一定要认真。 国外经验证明,采用头脑风暴法提出方案比同 样的人单独提方案的效果要大65%-93%。
11
(一)选择价值分析的对象 1.选择制品中销售金额较大或产量最多者 2.制品之构造较为复杂者 3.制品在严格的要求条件下,设计完成者 〈汽車.飛機.計算機.手機…..〉 4.与价值标准比较并检讨有降低之可能者 5. 制品研究开发时间较急促者〈競爭激烈〉 6. 价格在长时间固定不变者〈3-5年者〉
1. 2. 3. 4. 5. 6. 7. 8.
该产品用途为何? 工作精密度如何? 是否满足功能上需求? 是否达到品质上要求? 是否符合可靠度条件? 安全性如何? 大量生产有否困难? 保养修理是否容易?
VAVE价值分析及价值工程课件

5.五五问法~5W2H与5Why
(1)5W2H:What,Who,When,Where,Why,How to do,How much
(2)5Why:丰田5个为什么
a.为何要这么做?
b.为何要使用现行的机械?
c.为何要在此处进行这项工作?
d.为何要依现行的顺序去做?
e.为何要做成这个样子?
6.大目标~PQCDSM 产量(Production)、品质(Quality)、成本(Cost) 、交期(Delivery) 、
事業部推動人
24 of 40
VA/VE活動流程
事業部推動 人立案追蹤.
專案負責人 結案後提出 <VA/VE結案 報告>
提案簽核OK後交本事業部推動 納入專案追蹤.同時提案人需對所 提專案作持續追蹤及時更新回報.
1.專案負責人在所提專案試得驗證 成功功,且正式導入開始效益創造 時需及時功,且正式導入開始效益 創造時需及時 2. 提案經驗證無法推行時提案人仍 需提出<結案報告>作為個人年度績 效考核;專案獎勵------視情況由干 事推出經委員
更接近人们日常生活常用的“合算不合算”、“值得不值 得”的意思,是指事物的有益程度。
价值工程中关于价值的概念是个科学的概念,它正确反映 了功能和成本的关系,为分析与评价产品的价值提供了一个 科学的标准。树立这样一种价值观念就能在企业的生产经营 中正确处理质量和成本的关系,生产适销对路产品,不断提 高产品的价值,使企业和消费者都获得好处。
例如,将技术与经济价值结合起来研究生产和管理的其他问题, 这就是早期的价值工程。1955年这一方法传入日本后与全面质量管理 相结合,得到进一步发扬光大,成为一套更加成熟的价值分析方法。
麦尔斯发表的专著《价值分析的方法》使价值工程很快在世界范围 内产生巨大影响。
价值的工程案例分析报告
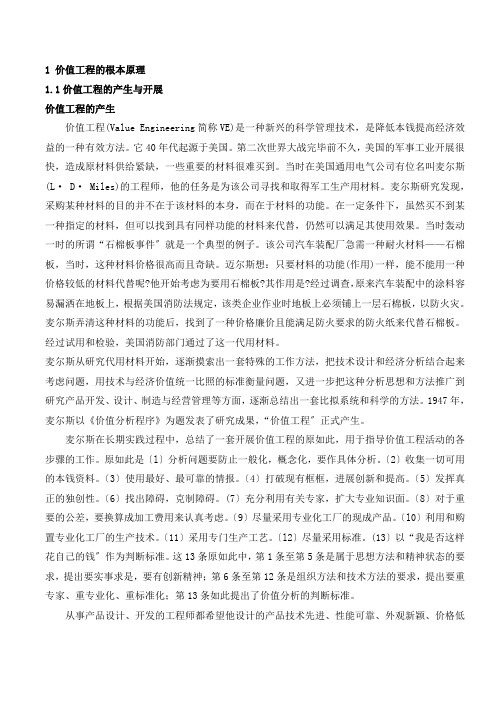
1 价值工程的根本原理1.1价值工程的产生与开展价值工程的产生价值工程(Value Engineering简称VE)是一种新兴的科学管理技术,是降低本钱提高经济效益的一种有效方法。
它40年代起源于美国。
第二次世界大战完毕前不久,美国的军事工业开展很快,造成原材料供给紧缺,一些重要的材料很难买到。
当时在美国通用电气公司有位名叫麦尔斯(L· D· M iles)的工程师,他的任务是为该公司寻找和取得军工生产用材料。
麦尔斯研究发现,采购某种材料的目的并不在于该材料的本身,而在于材料的功能。
在一定条件下,虽然买不到某一种指定的材料,但可以找到具有同样功能的材料来代替,仍然可以满足其使用效果。
当时轰动一时的所谓“石棉板事件〞就是一个典型的例子。
该公司汽车装配厂急需一种耐火材料——石棉板,当时,这种材料价格很高而且奇缺。
迈尔斯想:只要材料的功能(作用)一样,能不能用一种价格较低的材料代替呢?他开始考虑为要用石棉板?其作用是?经过调查,原来汽车装配中的涂料容易漏洒在地板上,根据美国消防法规定,该类企业作业时地板上必须铺上一层石棉板,以防火灾。
麦尔斯弄清这种材料的功能后,找到了一种价格廉价且能满足防火要求的防火纸来代替石棉板。
经过试用和检验,美国消防部门通过了这一代用材料。
麦尔斯从研究代用材料开始,逐渐摸索出一套特殊的工作方法,把技术设计和经济分析结合起来考虑问题,用技术与经济价值统一比照的标准衡量问题,又进一步把这种分析思想和方法推广到研究产品开发、设计、制造与经营管理等方面,逐渐总结出一套比拟系统和科学的方法。
1947年,麦尔斯以《价值分析程序》为题发表了研究成果,“价值工程〞正式产生。
麦尔斯在长期实践过程中,总结了一套开展价值工程的原如此,用于指导价值工程活动的各步骤的工作。
原如此是〔l〕分析问题要防止一般化,概念化,要作具体分析。
〔2〕收集一切可用的本钱资料。
〔3〕使用最好、最可靠的情报。
- 1、下载文档前请自行甄别文档内容的完整性,平台不提供额外的编辑、内容补充、找答案等附加服务。
- 2、"仅部分预览"的文档,不可在线预览部分如存在完整性等问题,可反馈申请退款(可完整预览的文档不适用该条件!)。
- 3、如文档侵犯您的权益,请联系客服反馈,我们会尽快为您处理(人工客服工作时间:9:00-18:30)。
VA/VE价值工程/价值分析
一、发展史:
1.1947年美国GE 公司麦尔斯发表VA/VE至今已有50年.
2.1955年日本开始研究VA/VE并在企业界,学术界不断使用训练,并成立日本VE 协会.
3.1980年日本设立了麦尔斯奖,松下幸之助曾表示“经营=VE”,稻盛和夫也主“决定价格就是经营”.
4.1967年中国生产力中心邀请日本产业能率大学学者开办 VA/VE课程.
二、VA/VE 的概念与原则:
1.概念:透过组织的努力,针对产品或服和的机能加以研究,以最低的寿命周期成本(life cycle cost)
成本,确实达到必要的机能.
V=F/C
V:Value价值 F:Function 机能 C: Cost 成本
2.VA/VE的五大特点:
(1)组织的努力
(2)机能的研究
(3)对象为产品或服务
(4)最低的寿命周期成本
(5)确实达成必要的机能
3.VA/VE活动中必须遵守的七个原则:
(1)顾客优先原则
(2)价值提升原则
(3)机能思考原则
(4)经济性思考原则
(5)创造性思考原则
(6)情报活用原则
(7)团队设计(Team Design)原则
三、提高价值的基本途径:
1.F不变,降低成本,提高V. F /C =V
2.C不变,F提高,增加V. F /C=V
3.F增加,C增加,增加V. F /C =V
4.F下降(降低次要功能),C下降,V增加 F /C =V
5.运用新技术,改革产品,提高F ,降低C. F /C =V
四、VA/VE的实施步骤:
1.对象的选择
2.情报的收集
3.功能分析
4.提改进方案
5.方案评价与选择
6.试验
7.提案审批和实施
对象的选择
功能分析
提改进方案
试验
提案,审批,实施
五、VA/VE对象的选择:
1.原则:以能否收到较大的经济效果为基本原则.
2.对象:
(1)产品:
a.需求量大的产品
b.正在研制即将投入市场的新产品
c.竞争激烈的产品
d.用户意见大,急需改进的产品
e.成本高,利润少的产品
f.结构复杂,技术落后,工序繁多,工艺落后,原材料品种多,紧缺资源耗
用量大的产品.
(2)零部件:
a.数量多的零部件.
b.制造费用高的零部件.
c.结构复杂的零部件.
d.体积重量大的零部件.
e.用料多,耗缺稀资源的零部件.
f.坏品率高的产品
六、VA/VE的十大思考方向:
1.一个恒久不变的真理:最终目的为“顾客满意”.
2.由两大领域下手:目的与手段.
3.除三呆、灭三K,以三大技术、三个基本步骤,达到三化(3S)
(1)三呆:不节省、不合理、不均一
(2)三K:脏乱、危险、吃力.
(3)三大技术:成本分析、机能分析、创造力技术
(4)三个基本步骤:机能分析、机能评价、提出改善方案
(5)三化:标准化、专业化、简单化.
4.应用改善四原则、改善四方向于管理四循环.
(1)改善四原则:消除、合并、重排、简化
(2)改善四方向:解决问题、改善现状、创造新机、突破现状
(3)管理四循环:计划、实施、确认、处置
5.五五问法~5W2H与5Why
(1)5W2H:What,Who,When,Where,Why,How to do,How much
(2)5Why:丰田5个为什么
a.为何要这么做?
b.为何要使用现行的机械?
c.为何要在此处进行这项工作?
d.为何要依现行的顺序去做?
e.为何要做成这个样子?
6.六大目标~PQCDSM
产量(Production)、品质(Quality)、成本(Cost) 、交期(Delivery) 、安全(Safety)士气(Morale)
7.思考七个问题来消除七大浪费:
(1)七个问题:
a.它是什么?
b.它的机能是什么?
c.它的成本是多少?
d.它的价值是多少?
e.有哪些方法可以达到对象的机能?
f.新方案的成本是多少?
g.新方案能满足要求吗?
(2)七大浪费:
a.制造不良的浪费
b.制造过多的浪费
c.加工的浪费
d.搬运的浪费
e.库存的浪费
f.动作的浪费
g.等待的浪费
8.八个改善着眼点:
材料、加工、模治检具、能源、物流、品质、规格、采购
9.九点查检表(Osborne查检表)
(1)替代(Substitute)
(2)组合(Combine)
(3)能否从其它类似的东西借取构想(Adopt)
(4)修正(Modify)
(5)扩大(Magnify)
(6)缩小( Minify)
(7)有无其它的使用方法(Put to other use)
(8)重排(Rearrange)
(9)相反(Reverse)
10.成功的十大关键因素(KSF)
(1)高阶主管必须真心投入与支持.
(2)负责执行的人必须得到上级的授权.
(3)执行的人要尽量专职,而且日后要成为这方面的专家.
(4)推动VA/VE活动必须由上而下(Top Down),而提出VA/VE改善必须是由下而上(Bottom Up)
(5)推动小集团活动培养自动自发的精神
(6)建立模团队,以便让其它人员观摩与效法.
(7)与其它推动VA/VE有成效的公司作交流.
(8)采跨机能(Cross-function)的组织.
(9)各单位良好的互动人际关系.
(10)强调并落实VA/VE教育训练.
七、VA/VE未来展望:
1.提升竞争力的有效途径:
竞争力=f(价值/成本)
2.提高效率的最佳技巧:
最小投入最大产出之原则来设计整个进行过程以达到降低成本的目标.
3.导入VA/VE的产业逐渐扩大.
制造、营建、物流、服务、医疗业.
4.促进经营中的核心管理技术成长.
5.以附加价值链协助企业流程改造.
顾客价值分析竟争策略产品/服务制程价值采购/供货商
价值工程分析价值分析
6.融合改善与创新的手法为达成顾客满意.
7.符合环境保护的世界趋势.
8.价值管理将成为企业体质改善经营活动.
9.VA/VE与IE,QC之融合.(参照表一)
10.VA/VE是企业永续经营的有效途径.
表一IE、QC、VE三大管理技术的比较
表二企业永续经营的四个方向
八、
价值工程活动成果评价:
1.
全年凈节约额.
全年凈节约额=
改进前单件成本-改进后单件成本) X
年产量-VE/VA 活动费用.
2. 成本降低率
= 改进前成本-改进后成本 改进前成本 X 100% 3.投资效率:
投资效率= 全年凈节约额 价值工程活动费用。