压铸模具设计基本参数
压铸模具设计方案
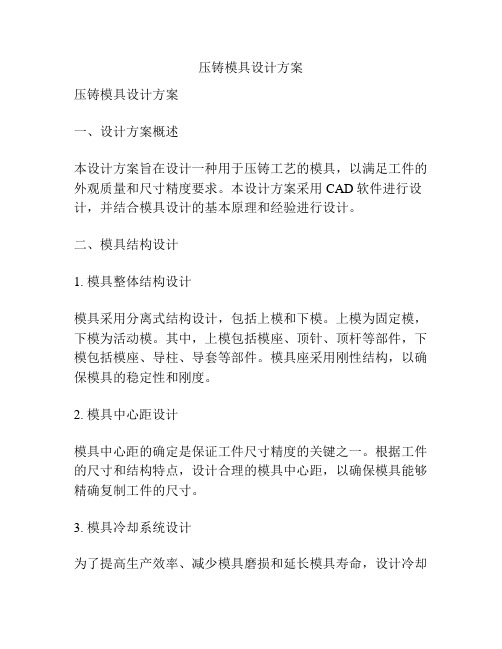
压铸模具设计方案压铸模具设计方案一、设计方案概述本设计方案旨在设计一种用于压铸工艺的模具,以满足工件的外观质量和尺寸精度要求。
本设计方案采用CAD软件进行设计,并结合模具设计的基本原理和经验进行设计。
二、模具结构设计1. 模具整体结构设计模具采用分离式结构设计,包括上模和下模。
上模为固定模,下模为活动模。
其中,上模包括模座、顶针、顶杆等部件,下模包括模座、导柱、导套等部件。
模具座采用刚性结构,以确保模具的稳定性和刚度。
2. 模具中心距设计模具中心距的确定是保证工件尺寸精度的关键之一。
根据工件的尺寸和结构特点,设计合理的模具中心距,以确保模具能够精确复制工件的尺寸。
3. 模具冷却系统设计为了提高生产效率、减少模具磨损和延长模具寿命,设计冷却系统对模具进行冷却。
冷却系统包括冷却孔和进水口,通过冷却水的流动,迅速冷却模具,以提高生产效率和模具寿命。
4. 模具材料选择模具的材料选择是保证模具寿命和使用效果的重要因素。
根据工件的材料和要求,选择适当的模具材料,保证模具具有良好的硬度和耐磨性。
三、模具生产工艺1. 加工工艺规程模具的加工工艺包括数控加工、外圆磨削等。
根据模具的具体结构和工艺要求,制定合理的加工工艺规程,以确保模具的加工质量。
2. 检测工艺模具加工完成后,进行检测以验证模具的质量。
检测工艺包括模具尺寸检测、表面质量检测等,通过合适的检测工艺,确保模具符合设计要求。
四、模具的维护、维修和更换为了保证模具的正常使用和延长其寿命,进行模具的定期维护、维修和更换。
维护工作包括清洁模具、添加润滑剂等,维修工作包括修复模具损伤、更换模具部件等,更换工作包括根据模具磨损程度,定期更换模具部件。
五、结论本设计方案是一种用于压铸工艺的模具设计方案,通过合理的结构设计、材料选择和加工工艺,可以满足工件的外观质量和尺寸精度要求。
同时,通过模具的定期维护、维修和更换,可以保证模具的正常使用和延长其寿命。
压铸工艺参数公式
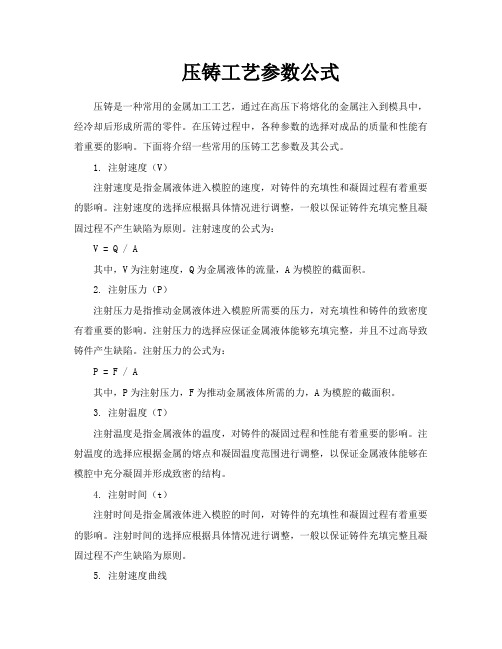
压铸工艺参数公式压铸是一种常用的金属加工工艺,通过在高压下将熔化的金属注入到模具中,经冷却后形成所需的零件。
在压铸过程中,各种参数的选择对成品的质量和性能有着重要的影响。
下面将介绍一些常用的压铸工艺参数及其公式。
1. 注射速度(V)注射速度是指金属液体进入模腔的速度,对铸件的充填性和凝固过程有着重要的影响。
注射速度的选择应根据具体情况进行调整,一般以保证铸件充填完整且凝固过程不产生缺陷为原则。
注射速度的公式为:V = Q / A其中,V为注射速度,Q为金属液体的流量,A为模腔的截面积。
2. 注射压力(P)注射压力是指推动金属液体进入模腔所需要的压力,对充填性和铸件的致密度有着重要的影响。
注射压力的选择应保证金属液体能够充填完整,并且不过高导致铸件产生缺陷。
注射压力的公式为:P = F / A其中,P为注射压力,F为推动金属液体所需的力,A为模腔的截面积。
3. 注射温度(T)注射温度是指金属液体的温度,对铸件的凝固过程和性能有着重要的影响。
注射温度的选择应根据金属的熔点和凝固温度范围进行调整,以保证金属液体能够在模腔中充分凝固并形成致密的结构。
4. 注射时间(t)注射时间是指金属液体进入模腔的时间,对铸件的充填性和凝固过程有着重要的影响。
注射时间的选择应根据具体情况进行调整,一般以保证铸件充填完整且凝固过程不产生缺陷为原则。
5. 注射速度曲线注射速度曲线是指注射过程中注射速度随时间的变化规律。
注射速度曲线的选择应根据具体情况进行调整,一般以保证铸件充填完整且凝固过程不产生缺陷为原则。
6. 注射压力曲线注射压力曲线是指注射过程中注射压力随时间的变化规律。
注射压力曲线的选择应根据具体情况进行调整,一般以保证铸件充填完整且凝固过程不产生缺陷为原则。
以上所述的压铸工艺参数及其公式只是一些常用的参考,实际应用中还需要根据具体情况进行调整和优化。
压铸工艺的优化是一个综合性的问题,需要考虑材料的性质、模具的设计、设备的性能等多个方面因素的综合影响。
压铸件设计规范详解

压铸件设计规范详解压铸件是指利用压铸工艺将熔融金属注入模具中,经过凝固和冷却后得到的零件。
由于该工艺具有生产效率高、成本低、制造精度高等优点,被广泛应用于汽车、航空航天、电子等领域。
为了保证压铸件质量和安全性,需要遵循一系列的设计规范。
下面将详细介绍压铸件设计规范。
一、材料选择1.铝合金:常用的有A380、A383、A360等。
根据使用条件和要求,选择合适的铝合金材料,确保压铸件具有良好的强度和塑性。
2.压铸型腔材料:常用的有铜合金、热处理工具钢等。
要选择适当的材料,以耐高温和磨损。
二、模具设计1.模具设计必须满足压铸件的要求,保证铸件的尺寸精度和表面质量。
2.模腔设计要考虑到铸件收缩率、冷却速度等因素,以避免产生缺陷和变形。
3.合理安排模具冷却系统,保证压铸件内部和表面的冷却均匀。
三、尺寸设计1.压铸件的尺寸设计应符合产品技术要求和工艺要求,确保功能和安装的需要。
2.避免设计尺寸太小或太薄,以免产生破裂和变形。
3.设计保证良好的表面质量,避免设计中出现接触不良、挤压不足等问题。
四、壁厚设计1.壁厚不应过薄,以免影响产品的强度和刚性。
2.避免壁厚过大,以减少成本和缩短冷却时间。
3.边缘和角部应注意壁厚过渡,避免产生应力集中。
五、设计角度和半径1.设计时应根据铝合金的流动性选择合适的角度和半径。
2.避免设计尖锐角度和太小的半径,以免产生气孔和挤压不足。
3.设计角度和半径应保持一定的一致性,避免因设计不当导致铸件变形和收缩不均匀。
六、设计放射状构件1.当压铸件具有放射状构件时,要合理设计放射状梁的位置和数量,以充分利用材料,并减少成本。
2.注意放射状构件的设计不应影响整体结构的强度。
七、设计排气系统1.设计时要考虑到铸件内部的气孔、气泡等气体排出问题。
2.合理安排和设计排气道,以保证良好的注模效果和铸件质量。
八、设计孔和螺纹1.设计孔和螺纹时应遵循标准规范,确保质量和安装的可靠性。
2.孔和螺纹的位置和尺寸应符合产品要求,保证压铸件的功能和使用要求。
压铸件结构设计

h2≥0.8mm
a≤3°
压铸件加强筋的运用
3,作为散热加强;
4,作为装饰作用。
2,引导料流流向;
1,加强结构强度;
压铸件结构工艺性分析一
不好的案例
好的案例
说明
于型模中加工凹入文字较之加工凸出文字为困难﹒且模具寿命难以保证,使用后续刻加工﹐则与此相反。
1.5
0.014~0.020
6
0.056~0.084
2
0.018~0.026
7
0.066~0.100
2.5
0.022~0.032
8
0.076~0.116
3
0.028~0.040
9
0.088~0.138
3.5
0.034~0.050
10
0.100~0.160
4
0.040~0.060
合金浇注温度高时,填充时间可选长些。 模具温度高时,填充时间可选长些。 铸件厚壁部分离内浇口远时,填充时间可选长些。 熔化潜热和比热高的合金,填充时间可选长些。
好的案例
说明
陈学民
2021
2023
内容大纲
O1
产品的壁厚(模具成型的基础)
O2
产品的拔模(模具脱模的保障)
O3
产品的圆角(模具寿命的关键)
O4
加强筋的设计(结构优化的手段)
压铸件壁厚的设计
3.5
2.5
3.5
2.5
2.5
2.0
>500
3.0
1.8
3.0
1.8
2.2
1.5
>100~500
2.5
压铸工艺流程中的模具设计要点

压铸工艺流程中的模具设计要点压铸是一种常用的金属加工工艺,通过将熔融金属注入模具中,并在固化后取出成型件。
模具设计是整个压铸工艺中的关键环节,决定了成型件的质量和生产效率。
本文将从模具结构设计、材料选择和加工工艺三个方面讨论压铸工艺流程中的模具设计要点。
一、模具结构设计要点1. 合理选择模具结构模具结构的设计应根据产品的形状、尺寸和压铸工艺要求进行合理选择。
一般常见的模具结构包括单腔、多腔、合模和分模等。
对于形状复杂的产品,可以采用多腔结构来提高生产效率。
对于尺寸较大的产品,可以考虑采用合模结构来减少模具成本。
2. 考虑产品的冷却和顶针装置在模具设计中,需要考虑产品的冷却和顶针装置。
冷却系统的设计应能够有效地排除熔融金属的热量,以确保成型件的质量。
顶针装置的设计应满足产品的要求,并保证顶针在压铸过程中的精确位置。
3. 设计合理的浇口和溢流槽浇口和溢流槽是模具设计中的重要组成部分。
设计浇口时应考虑熔融金属的流动性和冷却速度,并确保浇口与产品的结合处处于合适的位置。
溢流槽的设计应考虑金属液体的顺利流动,以避免产生气体和杂质。
二、材料选择要点1. 选择耐磨耐热的材料模具在压铸过程中需要承受高温和高压的作用,因此材料的选择至关重要。
一般采用耐磨耐热的工具钢或合金钢作为模具材料,以保证模具的使用寿命和成型件的质量。
此外,还应考虑材料的加工性能和可靠性。
2. 考虑材料的强度和刚性模具的结构设计需要兼顾材料的强度和刚性。
材料的强度直接影响到模具的承载能力,而刚性则影响到模具的稳定性和精度。
因此,在模具设计中应根据产品的要求选择合适的材料,并进行合理的加工和热处理,以提高模具的性能。
三、加工工艺要点1. 精确计算和控制成型参数在压铸工艺中,成型参数的精确计算和控制是保证成型件质量和加工效率的关键。
成型参数包括注射速度、压力、温度和冷却时间等。
合理选择和控制这些参数,可以避免产生缺陷和变形,提高成型件的精度和表面质量。
压铸铝技术参数范文

压铸铝技术参数范文
1.压铸铝材料:
常用的铝合金材料有ADC12、A380、A383等,它们具有良好的流动性、耐腐蚀性和机械性能。
选择合适的铝合金材料可以根据零件的具体要求,
如强度、耐磨性、外观等。
2.模具设计:
模具设计是压铸铝技术中的重要环节,直接影响到零件的质量和生产
效率。
合理的模具设计应该考虑到以下几个方面:
-零件的形状和尺寸
-壁厚的均匀性
-腔壁的表面光洁度
-浇口和放气口的位置和数量
-零件的铸造方向
3.工艺参数:
压铸铝的工艺参数包括注射压力、铸造温度、冷却时间等。
以下是一
些常用的工艺参数:
-注射压力:一般在50-200MPa之间,根据零件的尺寸和形状来确定。
-铸造温度:常用的铸造温度为650-750℃,具体温度可以根据铝合
金的特性进行调整。
-冷却时间:冷却时间对于铝合金零件的组织和性能有重要影响,一
般为20-30秒。
过长或过短的冷却时间都会影响零件的质量。
4.设备要求:
压铸铝需要使用专门的压铸机进行生产,压铸机的选择应该考虑到以
下几个因素:
-注射压力和注射容量:根据铝合金零件的要求来确定。
-注射系统的稳定性和可调性:可以根据具体的工艺要求来选择合适
的注射系统。
-液压系统的稳定性和动力输出能力:确保能够提供足够的注射压力。
综上所述,压铸铝技术参数包括铝合金材料的选择、模具设计、工艺
参数的确定以及设备要求等方面。
合理的技术参数的选择可以提高生产效
率和零件的质量,满足不同零件的使用要求。
标准铝压铸工艺参数表

标准铝压铸工艺参数表1. 压铸温度。
铝合金的压铸温度是影响产品质量的重要参数之一。
通常情况下,铝合金的压铸温度在650°C至750°C之间。
过高的温度会导致产品熔融不均匀,而过低的温度则会造成产品表面粗糙。
因此,在实际生产中,需要根据具体的铝合金材料选择合适的压铸温度。
2. 压射速度。
压射速度是指铝合金液态金属进入模腔的速度。
适当的压射速度可以确保产品充填充分,避免气孔和夹杂物的产生。
一般来说,压射速度应根据产品的形状和尺寸进行调整,以保证产品的成型质量。
3. 模具温度。
模具温度对铝合金压铸产品的表面质量和尺寸精度有着重要影响。
过高或过低的模具温度都会导致产品的缺陷,因此需要根据具体的铝合金材料和产品要求来确定合适的模具温度。
4. 注射压力。
注射压力是指压铸机对铝合金液态金属施加的压力。
适当的注射压力可以确保产品充填充分,避免产品内部产生气孔和夹杂物。
在实际生产中,需要根据产品的形状和尺寸来确定合适的注射压力。
5. 冷却时间。
冷却时间是指产品在模具中冷却的时间。
适当的冷却时间可以确保产品的尺寸精度和表面质量。
通常情况下,冷却时间需要根据产品的厚度和材料来确定,以确保产品达到理想的硬度和强度。
6. 顶杆力。
顶杆力是指顶出铝合金产品的力量。
适当的顶杆力可以确保产品顺利脱模,避免产品变形和损坏。
在实际生产中,需要根据产品的形状和尺寸来确定合适的顶杆力。
7. 模具开合力。
模具开合力是指模具在开合过程中所受的力量。
适当的模具开合力可以确保模具的正常运行,避免模具损坏和产品缺陷。
在实际生产中,需要根据模具的结构和尺寸来确定合适的模具开合力。
总结:以上是标准铝压铸工艺参数表的相关内容,希望能对大家在铝合金压铸加工过程中有所帮助。
在实际生产中,需要根据具体的产品要求和铝合金材料来确定合适的工艺参数,以确保产品质量和生产效率。
同时,也需要不断优化和调整工艺参数,以适应市场和客户需求的变化。
希望大家能够加强学习和实践,不断提升铝合金压铸加工的技术水平和质量管理水平。
压铸模具的技术要求文档

压铸模具的技术要求文档压铸模具是现代工业生产中常用的一种模具,用于制造各种金属制品。
压铸模具的技术要求非常高,对模具的设计、制造、使用等方面都有相应的要求。
本文将从几个方面详细介绍压铸模具的技术要求。
一、设计要求1.模具结构设计要合理,要考虑到产品的结构特点、工艺要求等因素,并保证在模具使用中有较高的稳定性和精度。
2.模腔的设计要充分考虑充型性、冷却性、顶出性等要素,确保产品成型质量稳定。
3.模具的开口方式、进料方式等设计要符合产品要求,并能保证模具的安全操作。
二、材料要求1.模具材料应具有良好的刚性、韧性和耐磨性,能够承受较大的冲击负荷和高温环境,如工具钢、合金钢等。
2.模具的热处理要求良好,能够使模具硬度均匀、稳定,延长使用寿命。
三、制造要求1.模具加工要求高精度、高质量,要保证模具的尺寸精度和表面质量。
2.维修和保养要定期进行,及时处理模具的磨损、损伤等问题,确保模具的正常使用和寿命。
四、使用要求1.模具的操作人员要具备一定的技能和经验,严格按照操作规程进行操作,保证操作的安全和准确性。
2.模具的使用环境要保持清洁、干燥,避免灰尘、水汽等对模具的损坏。
3.模具的顶出装置、冷却装置等要保持良好的工作状态,及时进行维修和更换。
五、质量控制要求1.模具的尺寸精度、表面质量等要进行严格的检测和控制,保证产品的准确性和一致性。
2.定期对模具进行检测和维修,及时发现并解决模具的问题,防止因模具问题引起的产品质量问题。
总结:压铸模具的技术要求非常高,对模具的设计、制造、使用等方面都有严格要求。
只有合理的设计,良好的材料和制造工艺,正确的使用和维护,才能保证模具的高质量和长寿命,从而保证产品的质量和生产效率。
因此,在实际应用中,需要充分重视压铸模具的技术要求,综合考虑各方面因素,确保模具的高效稳定运行。
压铸工艺参数

压铸工艺参数
一、压铸机参数
1.锁模力:压铸机锁模力是指压铸机在关闭模具时施加在模具上的力量,这个参数的选取要根据铸件的大小和形状来确定。
2.注射压力:指压铸机在注入合金液态金属时向模腔施加的压力,需
要根据合金的液态流动性来设定。
3.注射速度:指合金液态金属进入模腔的速度,需要控制在合适的范
围内,既要保证充模完全,又要避免过快造成气孔和模具损坏。
二、模具参数
1.冷却系统:合理的冷却系统可以提高铸件的质量和生产效率,可以
通过冷却水的流量、温度和冷却通道的设计来控制。
2.喷油系统:喷油系统用于在压铸之前,在模具表面形成一层润滑膜,减少金属与模具的摩擦,需要控制喷油量和喷油位置。
3.模具温度:模具温度会影响合金凝固速度和铸件表面质量,可以通
过加热、降温等方式来控制。
三、材料参数
1.合金成分:合金成分是对压铸件的力学性能和化学性能有很大影响
的因素,需要根据产品的要求选择合适的合金成分。
2.熔化温度:合金的熔化温度会影响注入流动性和凝固速度,需要根
据合金的熔化温度范围进行控制。
3.熔金温度:熔金温度是指合金进入模腔前的温度,需要根据合金的熔点和凝固温度来确定。
除了以上介绍的参数,还有一些其他的因素也会影响压铸工艺,比如模具的设计、铸件的几何形状以及工艺操作等。
这些参数和因素都需要通过实践和不断探索来确定和优化,以提高压铸的质量和效率。
对于不同的产品和工艺需求,压铸工艺参数也会有所差别,因此需要根据具体情况进行调整和优化。
压铸模具设计理论参数表1

图标注:1,需要填写项目2,自动计算项目3,压室充满度(%)的范围:35%~45%4,一般来说(高速长度+增压长度)<(定模厚度-分流锥凸出长度)5,从内浇口的速度和填充时间上估算出内浇口的面积。
6,压铸机的压射比压根据产品的复杂程度和铸件的质量要求取30~70Mpa(mm)(s)(s)(s)(m/s)(mm³/s)后压室100%充满后铝液到达内浇口位置(%(m/s)(ms)(实际值(ms))(m/s)7,从需要的锁模力取得压铸机的大小。
LDL L L H L P L BFs适用机型800T\850T 压射中心-250拉杆螺纹M24模具结构1模2腔压室有效长度(mm)420定模厚度(mm)205分流锥凸出长度(mm)50冲头直径(mm)80止口尺寸Φ×L(mm)Ø200X25压射比压(Mpa)50锁模力Fd(KN)8342.54056.74041.2016.48125663713784115低速速度(m/sec)0.17低速长度(mm)416高速速度(m/sec) 2.5高速长度(mm)139开始时间(s) 2.504结束时间(s)模流。
20模流。
2.4480.056增压长度(mm)保压时间(s)高低速转换时间(s)高速时间(s)口实际平均速度(m/s)和内浇口面积的倍数浇口平均流量(mm³/s)压铸工艺表L1(mm)后压室100%充满L4(mm)后铝液到达内浇口位置换时铝液进入型腔的百分比(%)头设计的速度(m/s)设计的填充时间(ms)这两项尽量保持一致,可通过改变射头速度或射头直径来实现填充时间(实际值(ms))浇口设计的速度(m/s)这两项尽量保持一致,可通过改变射头速度、直径或浇口面积来实现压铸模具设计参数图表。
铝合金箱体压铸模具设计说明书

毕业设计(论文)任务书 2015 届机械工程及自动化专业题目:铝合金箱体压铸模具的设计子题:学生姓名:班级学号:指导教师:职称:所在系(教研室):机电与信息工程系下达日期:2014年7月4日完成日期:2015年5月8日摘要压铸模具是铸造液态模锻的一种方法,一种在专用的压铸模锻机上完成的工艺。
它的基本工艺过程是:金属液先低速或高速铸造充型进模具的型腔内,模具有活动的型腔面,它随着金属液的冷却过程加压锻造,既消除毛坯的缩孔缩松缺陷,也使毛坯的内部组织达到锻态的破碎晶粒。
毛坯的综合机械性能得到显著的提高。
本文运用大学所学的知识,了解压铸模具的工作原理,在此基础上,设计一款铝合金箱体压铸模具。
通过查找相关资料,了解铝合金箱体压铸模具的内部结构和工作原理,构建了铝合金箱体压铸模具组成结构的总的指导思想,从而得出了该铝合金箱体压铸模具的优点是高效,经济,并且运行效果好,运行平稳的结论。
关键词:铝合金箱体压铸模具;型腔;效率;模具AbstractThe environment of global economic development, China industries affected by other countries advanced technology at the same time, foreign enterprises and brand spread to more and more Chinese has become an opportunity. Cap pressing machine in industry through a variety of ways have been working with the relevant technology, and constantly improve their own strength and core competitiveness, and narrow the gap with developed countries.In the new market demand, update the sleeve pressing machine is a pressing matter of the moment. The production of pipe pressing machine equipment manufacturing enterprises to fully tap the potential of the market, vigorously develop the sleeves of large low cost pressing special machinery and equipment, plays a positive role in the evolution of automatic assembly, the assembly of mechanical equipment. There is a large pipe equipment on equipment safety index has strict requirements of production. In the production equipment of enterprises, give full consideration to the possible problems in the operation of the equipment, so as to reduce the noise pollution caused by vibration or improper operation of equipment phenomenon and manufacturing of domestic pipe pressing equipment with global appeal, economic, security and stability of the theme consistent. Increase and production pipe pressing equipment of new energy saving.Key word:pneumatic manipulator;cylinder;pneumatic loop;Fout degrees of freedom.目录摘要 (1)Abstract (2)第一章绪论 (3)1.1 模具介绍 (4)1.2 模具在加工工业中的地位................... 错误!未定义书签。
压铸模具标准
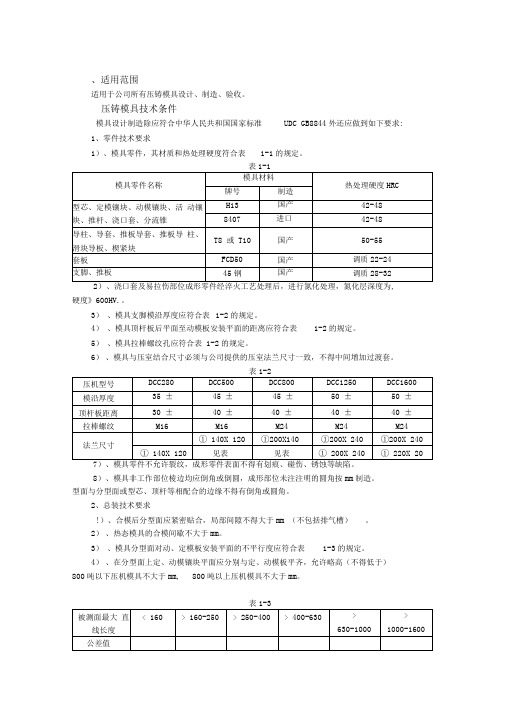
、适用范围适用于公司所有压铸模具设计、制造、验收。
压铸模具技术条件模具设计制造除应符合中华人民共和国国家标准UDC GB8844外还应做到如下要求:1、零件技术要求1)、模具零件,其材质和热处理硬度符合表1-1的规定。
表2)、浇口套及易拉伤部位成形零件经淬火工艺处理后,进行氮化处理,氮化层深度为, 硬度》600HV.。
3)、模具支脚模沿厚度应符合表1-2的规定。
4)、模具顶杆板后平面至动模板安装平面的距离应符合表1-2的规定。
5)、模具拉棒螺纹孔应符合表1-2的规定。
6)、模具与压室结合尺寸必须与公司提供的压室法兰尺寸一致,不得中间增加过渡套。
表1-27)、模具零件不允许裂纹,成形零件表面不得有划痕、碰伤、锈蚀等缺陷。
8)、模具非工作部位棱边均应倒角或倒圆,成形部位未注注明的圆角按mm制造。
型面与分型面或型芯、顶杆等相配合的边缘不得有倒角或圆角。
2、总装技术要求!)、合模后分型面应紧密贴合,局部间隙不得大于mm (不包括排气槽)。
2)、热态模具的合模间歇不大于mm。
3)、模具分型面对动、定模板安装平面的不平行度应符合表1-3的规定。
4)、在分型面上定、动模镶块平面应分别与定、动模板平齐,允许略高(不得低于)800吨以下压机模具不大于mm, 800吨以上压机模具不大于mm。
表5)套板和各镶块的配合面,在分型面上100 mm内,允许有两处小于mm的缝隙,但其长度应小于15 mm。
6)滑块运行应平稳,合模后滑块与楔紧块应压紧,接触面积不小于四分之三,开模后定位应准确、可靠。
8)、模具套板应有足够的刚性和强度,在承受压铸机锁模力和金属液压力下,不发生影响使用的变形。
9)、型腔的反压力中心尽可能接近压铸机合模中心,以免压铸机受力不均,造成合模不严。
10)、导柱伸出长度不得低于型腔最高点。
11)模具所有活动部分,应保证位置准确、动作可靠,不得有歪斜和卡滞现象。
滑块滑座等易磨易损部件、导柱和导套、推板导柱和导套、顶杆等易磨易损件应考虑摩擦副,同时均应采用刚性好、强度高的耐磨、耐热材料。
压铸件设计的基本参数

压铸件设计的基本参数1.材料选择:压铸件的材料选择是非常重要的,它直接影响到产品的质量和性能。
常见的压铸件材料有铝合金、锌合金、镁合金等。
在选择材料时需要考虑产品的使用环境、耐腐蚀性能、强度要求等因素。
2.壁厚:压铸件的壁厚是指铸件的各个部位的厚度。
在设计压铸件时,需要根据产品的使用要求和材料的性能来确定壁厚。
壁厚太薄会导致铸件变形、开裂等缺陷,壁厚太厚则会增加材料的使用量和加工难度。
3.溢出量:溢出量是指铸件外形与模具铸型之间的间隙量。
溢出量的大小会直接影响到产品的尺寸精度和表面质量。
一般情况下,溢出量约为1-2%,但具体数值需要根据产品的形状、尺寸和模具的特点进行调整。
4.弯曲角度:5.翘曲和扭曲:在设计压铸件时,需要避免翘曲和扭曲现象的发生。
翘曲是指铸件在冷却过程中由于不均匀收缩而产生的变形,扭曲是指在铸造过程中产生的不均匀应力所致的变形。
为了避免这些问题,可以通过增加冷却时间、合理设置冷却通道等方式来改善。
6.排气:在设计压铸件时,需要考虑到铸件内部的气体排出。
铸件内部的气体会产生气孔、夹杂等缺陷,影响产品的质量。
因此,在设计模具时需要预留适当的排气孔或避免部位。
7.表面质量:压铸件的表面质量对产品的外观和性能有着重要影响。
因此,在设计时要考虑到产品表面的处理方式,如喷砂、抛光等。
此外,在设计模具时需要避免出现划痕、气泡等缺陷。
8.模具设计:压铸件的模具设计是整个工艺的关键环节。
模具的设计必须满足产品的形状、尺寸精度和表面质量的要求。
在模具设计过程中,需要考虑到模具的结构强度、冷却方式、开合力等因素。
综上所述,压铸件的设计需要考虑到材料选择、壁厚、溢出量、弯曲角度、翘曲和扭曲问题、排气、表面质量和模具设计等多个方面。
只有在综合考虑各种参数的情况下,才能设计出满足产品要求的优质压铸件。
压铸机基本参数教案(精)

职业教育材料成型与控制技术专业教学资源库《铝合金铸件铸造技术》课程教案压力铸造—压铸机基本参数制作人:刘洋陕西工业职业技术学院压力铸造—压铸机基本参数一、压铸型(模)厚度压铸型(模)厚度是压铸型(模)合紧时的厚度,即压铸型合紧时压铸机动型座板与定型座板之间的距离,用H表示。
由于调型(模)机构的作用,H大小可以在一定范围内调整,卧式冷室压铸机用“模薄(H min)”、“模厚(H max)”表示H的最小和最大值,如图1所示。
图1 压铸模具厚度范围二、动型座板行程动型座板行程是动型座板的最大移动距离,如图2所示。
动型座板行程实际上就是压铸机开型(模)后型(模)具分型面之间的最大距离,用L 表示。
在设计时,开型(模)行程应满足下列条件:L≥L取式中L取—开型(模)后分型面之间能取出铸件的最小距离(mm)。
图2 开合模行程示意图三、大杠之间的内尺寸压铸机大杠(又称哥林柱)间在水平和垂直方向的内尺寸(又称哥林柱内距),如图所示。
压铸型(模)在装入型面空间内时,一般要求压铸型(模)的长或宽尺寸应小于相应大杠之间的内尺寸如图3所示。
大杠之间的内尺寸用(水平×垂直)(mm)表示。
图3大杆之间的内尺寸四、大杠直径大杠直径表明大杠的粗细,大杠的直径可能影响大杠的刚性,关心大杠直径主要是考虑机器的结构稳固性,尤其是开合模机构,单位为mm。
五、顶出力压铸机顶出铸件时,推杆板受到顶出机构所施加的静压力。
顶出运动是通过顶出液压缸内液压油的压力推动活塞,再由活塞杆传递给推杆板来实现。
顶出力理论计算公式为:F顶=πD12P1/4式中P1--顶出液压缸工作液的压力(MPa);D1--顶出液压缸内径(mm);F顶--顶出力(N)。
六、顶出行程顶出行程是顶出机构可以将压铸件顶出的最大距离。
液压顶出时与顶出液压缸本身行程有关,机械式顶出与后推杆长度有关。
顶出机构应该保证将压铸件从型腔中顶出一定距离,使其与压铸模具脱离,方便取出,用S 表示,单位为mm。
不同吨位压铸机模具长宽高参数参考
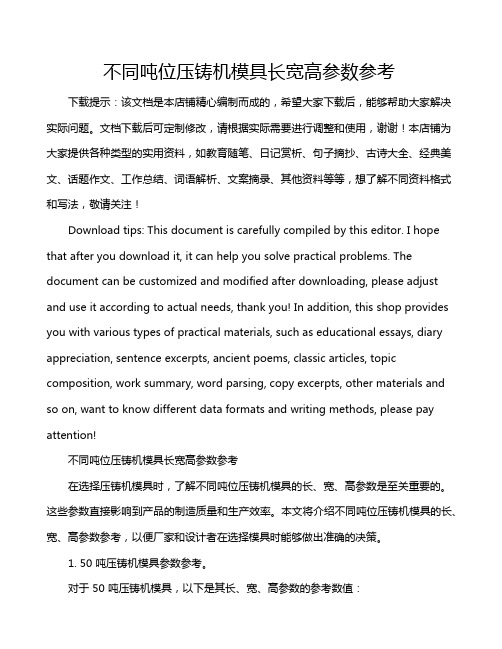
不同吨位压铸机模具长宽高参数参考下载提示:该文档是本店铺精心编制而成的,希望大家下载后,能够帮助大家解决实际问题。
文档下载后可定制修改,请根据实际需要进行调整和使用,谢谢!本店铺为大家提供各种类型的实用资料,如教育随笔、日记赏析、句子摘抄、古诗大全、经典美文、话题作文、工作总结、词语解析、文案摘录、其他资料等等,想了解不同资料格式和写法,敬请关注!Download tips: This document is carefully compiled by this editor. I hope that after you download it, it can help you solve practical problems. The document can be customized and modified after downloading, please adjust and use it according to actual needs, thank you! In addition, this shop provides you with various types of practical materials, such as educational essays, diary appreciation, sentence excerpts, ancient poems, classic articles, topic composition, work summary, word parsing, copy excerpts, other materials and so on, want to know different data formats and writing methods, please pay attention!不同吨位压铸机模具长宽高参数参考在选择压铸机模具时,了解不同吨位压铸机模具的长、宽、高参数是至关重要的。
欧洲压铸模具设计标准是什么

欧洲压铸模具设计标准是什么
欧洲压铸模具设计标准主要参考以下两个标准:EN 12844:2000 和
EN 12845:2018。
EN 12844:2000 标准是针对压铸模具设计和制造的一般要求。
该标准涵盖了各个方面的设计要求,包括模具材料的选择、构造和安装、尺寸和公差、模型设计和制造等。
在模具材料选择方面,标准要求使用高质量的材料,如工具钢、合金钢或特殊材料,以提供足够的刚度和耐用性。
同时还需要考虑材料的热膨胀系数,以避免在制造过程中出现尺寸变化问题。
构造和安装方面,标准要求模具结构必须稳固且易于安装和拆卸。
它还指导了模具的冷却系统设计,以确保在铸造过程中能够有效地控制温度。
尺寸和公差方面,标准规定了模具中各个部件的尺寸公差。
这有助于确保模具制造的精度和准确性。
模型设计和制造方面,标准要求模型必须符合铸件设计的要求,并能够满足铸造过程中的流动和凝固特性。
此外,标准还规定了模具表面处理的要求,以提高铸件的质量和外观。
EN 12845:2018 标准则是针对铸造模具的材料选择和铸造参
数进行指导的。
该标准包含了模具材料的分类和性能要求,根
据铸造材料的种类和特性,指导了合适的模具材料选择和使用。
此外,该标准还着重强调了模具的制造过程控制要求,包括温度控制、浇注和冷却过程的参数控制等。
这些要求旨在保证铸造过程中的质量和稳定性。
总结起来,欧洲压铸模具设计标准主要关注模具的材料选择、构造和安装、尺寸和公差、模型设计和制造,以及铸造模具的材料选择和铸造参数控制。
这些标准的遵循有助于确保模具制造的质量和稳定性,并最终提高铸件的质量和生产效率。
压铸模具简明设计手册
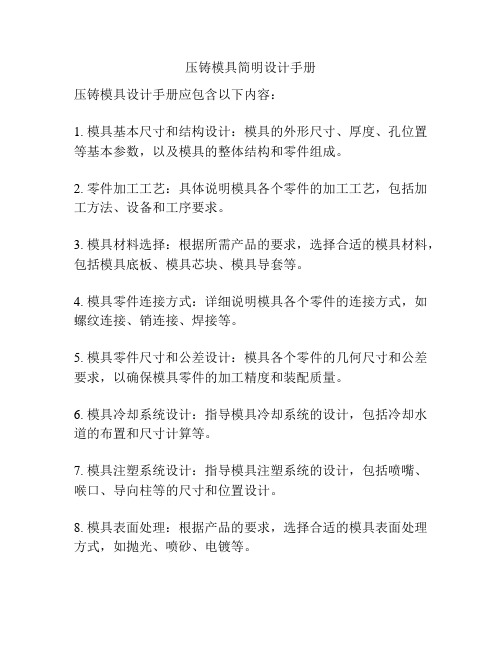
压铸模具简明设计手册
压铸模具设计手册应包含以下内容:
1. 模具基本尺寸和结构设计:模具的外形尺寸、厚度、孔位置等基本参数,以及模具的整体结构和零件组成。
2. 零件加工工艺:具体说明模具各个零件的加工工艺,包括加工方法、设备和工序要求。
3. 模具材料选择:根据所需产品的要求,选择合适的模具材料,包括模具底板、模具芯块、模具导套等。
4. 模具零件连接方式:详细说明模具各个零件的连接方式,如螺纹连接、销连接、焊接等。
5. 模具零件尺寸和公差设计:模具各个零件的几何尺寸和公差要求,以确保模具零件的加工精度和装配质量。
6. 模具冷却系统设计:指导模具冷却系统的设计,包括冷却水道的布置和尺寸计算等。
7. 模具注塑系统设计:指导模具注塑系统的设计,包括喷嘴、喉口、导向柱等的尺寸和位置设计。
8. 模具表面处理:根据产品的要求,选择合适的模具表面处理方式,如抛光、喷砂、电镀等。
9. 模具试模和调试方法:详细说明模具的试模和调试方法,包括模具组装、调试参数和注意事项等。
10. 模具维护和保养:指导模具的维护和保养工作,包括清洁、润滑、更换易损件等。
11. 模具设计注意事项:总结模具设计过程中需要注意的一些
常见问题和注意事项,如回缩量、顶出方式、模具分型等。
压铸模具设计手册应该简明扼要地介绍上述内容,方便模具设计人员参考和应用。
关于压铸模具设计制作技术标准要求

关于压铸模具设计制作技术标准要求ADC-03-版本A0 实施日期2020-1-1编制人更改记录标记处数更改依据更改人更改日期审核人批准人1、目的标准化压铸模具,达到提高模具寿命,减少装拆模浪费,提高产品质量,降低产品制造成本。
2、适用范围公司所用压铸模具。
3、内容3.1 产品孔由压铸模具保证,切边冲孔后无后处理工序的要求:对不需要后续加工直接压铸成型,经过切边冲孔就直接交货的产品,压铸模具设计时,孔内销子孔分型面尽量选择在孔的中间段,两边销子在分型面留隔皮间隙0.1-0.2mm。
目的是防止单边销子,隔皮在孔口,切边毛刺不净或蹦口,需要后续补充加工来保证,增加了制造成本。
如下图示例。
3.2 模芯材料:模芯材料用国际知名品牌材料的优质模具钢,保证量产过程中模具质量稳定,减少反复修模造成浪费。
3.3模具浇注系统设计:合适的浇注口大小影响模具型腔注满的时间和压射力大小、速度高低、填充时间。
A、流道设计应符合流体力学原理,尽量各分流道做到铝液能同时到达各内浇口。
B、流道截面积从料柄分出到内浇口应逐步收紧变小,不可突然变大,造成喷射卷气。
C、流道不能小90°突然转急弯。
如因条件限制必须急弯,应采用大圆弧过渡,以减低压铸铸造压力和速度,避免压力速度过大产生飞边、涨模。
D、料筒选择:填充率30-50%.3.4 模具冷却系统:A、模具冷却主要是控制模具温度高低,同时使模具温度均匀,不均匀的模具温度将影响:产品有严重的缺陷,如开裂、冷隔、变形、压铸气孔、缩孔等。
温度过低,铸件冷隔,温度过高,铸件缩孔。
B、模具冷却水管要做成拔插式快换接头。
C、模具冷却水管理进水、出水管要有颜色区分,进水管蓝色,出水管红色。
D、模具定模侧上方集水器高度必须小于250mm,以避免与喷雾机干涉。
E、从模具内部接出来的水管要与图纸一致的编号标识,以利于根据模具温度要求调整冷却水的流量大小(开关开度)。
3.5 模具顶出系统:A、顶杆位置布置应使顶出力量均匀、平衡,防止因顶出力量不平衡,造成顶出变形。
- 1、下载文档前请自行甄别文档内容的完整性,平台不提供额外的编辑、内容补充、找答案等附加服务。
- 2、"仅部分预览"的文档,不可在线预览部分如存在完整性等问题,可反馈申请退款(可完整预览的文档不适用该条件!)。
- 3、如文档侵犯您的权益,请联系客服反馈,我们会尽快为您处理(人工客服工作时间:9:00-18:30)。
项目负责人:
1、产品信息
产品外形尺寸 (mm)
产品平均壁厚 (mm)
其他要求:
231×207×48
2、设计分析
分型投影面积 (cm2)
铸件总重量(g)
1287 10878
冲头直径(mm)
130
理论: 399 二速起始点
(mm)
实际:
周期/时间:
模穴数量 产品材料
1 ADC12
产品重量 (g)
2087 46% 1250 理论: 0.3 实际: 理论: 37.7 实际: 理论: 60 实际: 理论: 95.2 实际: 理论: 5.5
产品面积
(cm2)
323
溢块排气面积
(cm2)
498
浇道面积
(cm2)
466
产品重量(g)
5957
溢块排气重量 (g)
浇道料炳重量 (g)
2087 2834
冲头截面积 13273.22896
三快起动点 (浇道比例)%
100%
压机参数:
压射力KN (ton)
活塞行程 (mm)
冲头跟踪距离 (mm)
模框顶面至分 流锥顶面距离
1075 880 320 180
比压(Mpa) 793.702876
压机比压参数 表(刻度参考)
4.53570235
锁模力(不带溢 块投影面积)T
483.0612245
锁模力(带溢块 投影面积)T
787.9591837
实际: 167
油缸
滑块抽拔力 (KG)
0
周长(mm)
深度(mm)
出模斜度(度)
880
排气方式
真空
抽芯力(T)
3T/3T
其他要求:
3、问题
设计问题:
增压速度 (m/s)
实际:
主浇道截面 积(mm2)
模具需要温 度(℃)
抽芯距离 (mm)
424 40/31
收缩率 (‰)
排气口截面 积(mm2) 留模时间
(s)
抽芯方式
制造问题:
4、总结
设计总结:
制造总结:
试模总结: 改进总结:
5957 2
料管长度 (mm)
料柄厚度 (mm)
5957 740 30
理论: 442 三速起始点
(mm) 实际:
编号:
产品重量 (g)
滑块数量 (个)
溢块流道总 重量(g) 料管利用率
(%) 压机规格
(T)
冲头一速 (m/s)
理论: 0.8 冲头二速(m/s)
实际:
理论: 2.5 冲头三速 (m/s)
实际:
ห้องสมุดไป่ตู้
内浇口速度 (m/s)
理论: 充填时间(s)
实际:
0.1010
理论: 660 金属液温度
(℃) 实际:
产品需要比 压(Mpa)
理论: 8.3 压射力(T)
实际:
压射力 (%)
理论: 7.56% 实际:
锁模力最大 承受比压 (Mpa)
理论: 增压力(T)
理论: 增压速度 (m/s)
收缩率 (‰)
增压力(T) 实际:
内浇口截面积 (mm2)