生产线平衡的秘笈.pptx
合集下载
怎样保持生产线平衡PPT课件
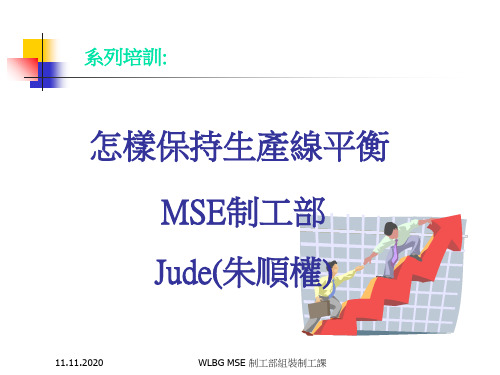
11.11.2020
(直通流程 1 )
(直通流程 2 )
WLBG MSE 制工部組裝制工課
相關的概念
概念8:高效率 1. 通常認為高效率就是:快速,簡單&大規模 2. 我們認為沒有浪費的時候才是高效率的
操作效率=實際產量/設定產能*100% 整體工廠效率(OPE)=平衡率*稼動率*操作效率
11.11.2020
WLBG MSE 制工部組裝制工課
相關的概念
概念9:改善 I. 同樣的投入更大的輸出; II. 不增值(無效)增值(有效)
?不增值?
等待 不良
庫存 移動
……
11.11.2020
WLBG MSE 制工部組裝制工課
例1: 減少移動與庫存提高效率
11.11.2020
WLBG MSE 制工部組裝制工課
T1
T3 T4 T5
S1 S2 S3 S4 S5 工站
單件標准時間 = T1+T2+T3+T4+T5 (流程中各工站所有動作標准時間之和)
11.11.2020
WLBG MSE 制工部組裝制工課
相關的概念
概念2:可供工時
可供工時=可供時間 *人數-借出工時 可供時間:上班時間內,為某產品生產而投入 的所有時間
上例中,若換線時間是15分鍾,則計劃停線工時為20人 *15min=300min=5H,則投入工時和稼動率為
60H-5H=55H 稼動率=55H/60H=92%
11.11.2020
WLBG MSE 制工部組裝制工課
相關的概念
概念4:設定產能 設定產能(H) =3600(S)/瓶頸時間(S) 設定產能(班)=投入時間/瓶頸時間(S)
系列培訓:
(直通流程 1 )
(直通流程 2 )
WLBG MSE 制工部組裝制工課
相關的概念
概念8:高效率 1. 通常認為高效率就是:快速,簡單&大規模 2. 我們認為沒有浪費的時候才是高效率的
操作效率=實際產量/設定產能*100% 整體工廠效率(OPE)=平衡率*稼動率*操作效率
11.11.2020
WLBG MSE 制工部組裝制工課
相關的概念
概念9:改善 I. 同樣的投入更大的輸出; II. 不增值(無效)增值(有效)
?不增值?
等待 不良
庫存 移動
……
11.11.2020
WLBG MSE 制工部組裝制工課
例1: 減少移動與庫存提高效率
11.11.2020
WLBG MSE 制工部組裝制工課
T1
T3 T4 T5
S1 S2 S3 S4 S5 工站
單件標准時間 = T1+T2+T3+T4+T5 (流程中各工站所有動作標准時間之和)
11.11.2020
WLBG MSE 制工部組裝制工課
相關的概念
概念2:可供工時
可供工時=可供時間 *人數-借出工時 可供時間:上班時間內,為某產品生產而投入 的所有時間
上例中,若換線時間是15分鍾,則計劃停線工時為20人 *15min=300min=5H,則投入工時和稼動率為
60H-5H=55H 稼動率=55H/60H=92%
11.11.2020
WLBG MSE 制工部組裝制工課
相關的概念
概念4:設定產能 設定產能(H) =3600(S)/瓶頸時間(S) 設定產能(班)=投入時間/瓶頸時間(S)
系列培訓:
生产线平衡分析与改善(最全面的IE分析,生产线平衡)ppt课件

0.1
0.2 0.5 1.0 2.0 5.0 ≥10
<1.0 100 50 20 10 5 2 1
1.0~2.0 50 20 20 10 5 2 1
2.0~5.0 20 20 10 5 2 2 1
5.0~10 10 10 5 2 2 1 1
13
三、流水生产线平衡的设计方法
3、 单品种流水线平衡方法 ● 案例:生产线平衡分析案例(直流式流程序为例)
10 A
工序1
工序2 11 B
工序3 12 E
C5
4 D
工序4 3
F
11 H
7
工序6
G
3 I
工序5 34
五、生产线平衡的其它案例
装配流水线平衡的方法很多,这里介绍一种简便而又能取得 满意效果的方法——阶位法。 阶位法的工作步骤如下
① 作图表示装配工艺过程中各作业元素的先后关系,并标 明每项作业元素的时间。 ② 从作业元素先后关系图找出每项作业元素的后续作业 元素,计算它们的时间总和,即每项作业元素的阶位值。 ③ 按阶位值的大小,由大到小,将作业元素排队,制成 作业元素阶位表。 ④ 从阶位值最高的作业元素开始,向工作地分配作业要 素。每分配一项作业元素,计算一次在节拍时间内的剩余 时间。若剩余时间足够安排另一项作业元素,从阶位表中 找出阶位值次高的作业元素分给该工作地。若剩余时间不 够安排其它作业元素,就向下一个工作地分配,直到全部 作业要素都被安排入工作地为止。
比较B、C两个工作站,将可发现B工作站的产能为C工作站的 2.69倍,B、C两个工作站将积压大量的半成品。若以传统追求 各工作站提升效率的方式进行管理,B工作站的效率提升,只会 恶化B、C站的半成品积压的浪费,而无助于整体产量的提高 (假设B工作站经训练生产效率达100%,则B工作站每小时产量 将达702.35个,产量为C工作站的3.36倍)。
生产线平衡的秘籍

必要重新安排。 (三)虽然使用批量生产,因生产量增加,有必
要改用生产线化。 (四)现在实施生产线生产,由于产品一部分变
更,修正工程分析必要。 (五)工序间的负荷不平衡,要改善生产线,其
工程分析的顺序或重点会改变其编排。
16
3、生产线工程分析及编排要点
(A)装配顺序的考量。 (B)时间的分析。 (C)主生产线和副生产线串联。 (D)必要条件的分析:
9
SDCA 与 PDCA
PD AC
現有 水準
PD AC
SD AC
SD AC
具體落實的方法:QC Story
SD AC
期望 水準
S:標準化程序,SOP (P:Plan計劃)
D:Do執行 C:Check檢查 A:Action行動
‧維持:(Standardization)DCA 依標準SOP而DCA
‧改善:I(Improvement)DCA 依改善之計劃而DCA
步骤4 准备改善作业的进行 步骤5 藉着5S及目视管理不断改善“个别作业准备”的目 8
維持/改善/創新 三階段
高階主管 中階主管 基層員工
維持
創新 改善
維持(Maintenance): ‧遵守作業標準
改善(Improvement): ‧改良改善
創新(Innovation,Break-Through): ‧結構性改善 ‧滿足客戶潛在需求
搬运设备选定
生产线布置设计
工厂 布置原则
稼动时间 预测不良率等
输送带上 的产品间隔 生产线速度
产品特性 作业特性
7
缩短准备时间方法
步骤1 对准备作业分析,把内部作业准备和外部作业准备 区分开来。
步骤2 分开外部作业准备,尽可能进行外部作业准备,缩 短机械停待的时间。
要改用生产线化。 (四)现在实施生产线生产,由于产品一部分变
更,修正工程分析必要。 (五)工序间的负荷不平衡,要改善生产线,其
工程分析的顺序或重点会改变其编排。
16
3、生产线工程分析及编排要点
(A)装配顺序的考量。 (B)时间的分析。 (C)主生产线和副生产线串联。 (D)必要条件的分析:
9
SDCA 与 PDCA
PD AC
現有 水準
PD AC
SD AC
SD AC
具體落實的方法:QC Story
SD AC
期望 水準
S:標準化程序,SOP (P:Plan計劃)
D:Do執行 C:Check檢查 A:Action行動
‧維持:(Standardization)DCA 依標準SOP而DCA
‧改善:I(Improvement)DCA 依改善之計劃而DCA
步骤4 准备改善作业的进行 步骤5 藉着5S及目视管理不断改善“个别作业准备”的目 8
維持/改善/創新 三階段
高階主管 中階主管 基層員工
維持
創新 改善
維持(Maintenance): ‧遵守作業標準
改善(Improvement): ‧改良改善
創新(Innovation,Break-Through): ‧結構性改善 ‧滿足客戶潛在需求
搬运设备选定
生产线布置设计
工厂 布置原则
稼动时间 预测不良率等
输送带上 的产品间隔 生产线速度
产品特性 作业特性
7
缩短准备时间方法
步骤1 对准备作业分析,把内部作业准备和外部作业准备 区分开来。
步骤2 分开外部作业准备,尽可能进行外部作业准备,缩 短机械停待的时间。
生产线平衡管理培训讲义(PPT 40页).ppt
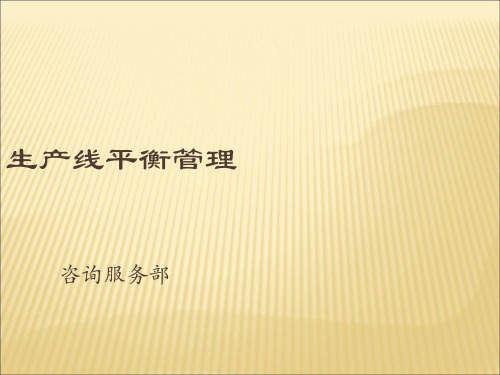
44.1 2.0 22.1
53.5 3.0 17.8
51.0 3.0 17.0
8
9 10 11
圆挑下脚
合计
瓶颈 平衡 工序 率
39.0 2.0 19.5
345 18 22.1 87%
生产工序平衡图
节拍时 间:19.11
25.0
秒
20.0
15.0
10.0
人均时间
5.0
0.0
1
2
3
4
5
6
7
8
生产线平衡调节(1/3)
步骤二:初拟人员分配(举例)
标准工时/人员初拟分配表
款号:
序号
o0011
工序
款式: 男士圆领衫
工序等级 机器类型
班组总人数:
18
标准工时(秒/件)
节拍时间:
19.11
理论人员 建议安排人员
备注说明
1
拼接罗纹领
2
拼肩缝
3
翻上罗纹领
4
拉后领滚条
5
盖后领滚条连放唛
6
单针缉前领圈明线
7
上袖(短袖)
8
拷摆缝夹洗唛(短袖)
三线及 作业员1 四线及 作业员
单针 电脑平
作业员
三线及骨 作业员2 四线及骨 作业员
单针 电脑平车
作业员
拼接罗纹领/拼肩缝
翻上罗纹领
盖后领滚条连放唛/ 单针缉前领圈明线
盖后领滚条连放唛/ 单针缉前领圈明线
上袖(短袖) 拷摆缝夹洗唛(短袖) 拷摆缝夹洗唛(短袖)
圆挑袖口(短袖)
圆挑下脚
单针 电脑平
作业员
10‘
10‘
生产线平衡方法.pptx

OEE所涵盖的其 他时间损失
传统效率衡量方 式只计算了部分
时间损失
总时间损失
六种重大OEE损失类型 OEE时间损失分为6大类
质量缺陷
计划外停 机
机器故障
速度下降
换线
损坏
OEE计算 – 模型
六种重大损失降低机器效能说明
设备时间
设备损失
设备最大可用工时
可使用总工时
时间稼动
SD损失
性能稼动 速度损失 价值稼动
• 14、Thank you very much for taking me with you on that splendid outing to London. It was the first time that I had seen the Tower or any of the other fam ous sights. If I'd gone alone, I couldn't have seen nearly as much, because I wouldn't have known my way about.
Station 2: G:11.3-11.3=0 Total time=11.3
Station 5: N:11.3-10.7=0.6 Total time=10.7
Station 3: C:11.3-2.1=9.2 D:9.2-2.5=6.7 E:6.7-1.8=4.9 F:4.9-1.8=3.1 H:3.1-2.1=1 Total time=10.3
6. 设定产能 标准产能
实际产能
1:TT & CT
1.Tact time=Cycle time的计算:
B
①A
传统效率衡量方 式只计算了部分
时间损失
总时间损失
六种重大OEE损失类型 OEE时间损失分为6大类
质量缺陷
计划外停 机
机器故障
速度下降
换线
损坏
OEE计算 – 模型
六种重大损失降低机器效能说明
设备时间
设备损失
设备最大可用工时
可使用总工时
时间稼动
SD损失
性能稼动 速度损失 价值稼动
• 14、Thank you very much for taking me with you on that splendid outing to London. It was the first time that I had seen the Tower or any of the other fam ous sights. If I'd gone alone, I couldn't have seen nearly as much, because I wouldn't have known my way about.
Station 2: G:11.3-11.3=0 Total time=11.3
Station 5: N:11.3-10.7=0.6 Total time=10.7
Station 3: C:11.3-2.1=9.2 D:9.2-2.5=6.7 E:6.7-1.8=4.9 F:4.9-1.8=3.1 H:3.1-2.1=1 Total time=10.3
6. 设定产能 标准产能
实际产能
1:TT & CT
1.Tact time=Cycle time的计算:
B
①A
生产线平衡培训课程PPT课件

第13页/共48页
二. 生产线平衡分析方法
• 案例计算
第14页/共48页
二. 生产线平衡分析方法
• 案例
第15页/共48页
二. 生产线平衡分析方法
6. 生产线平衡分析方法
第16页/共48页
二. 生产线平衡分析方法
7. 改善瓶颈岗位
第17页/共48页
二. 生产线平衡分析方法
• 改善四大原则
• 较少动作次数
改善前生产线平衡率=(18+16+24+37+45+16)/(37*7)*100%=60.2%
• 改善前生产线各工位平衡图
第42页/共48页
四. 线平衡经典案例分享
2. 改善前分析
第43页/共48页
四. 线平衡经典案例分享
பைடு நூலகம்3. 改善前后对比
第44页/共48页
四. 线平衡经典案例分享
3. 改善前后对比
B值得最优值为“1”
第29页/共48页
三. B值、F值的定义和计算
2. 一个流成产 One world、One dream One piece、One flow
• One piece flow是指单件进行生产,即人工每次只加工一件产品或部件,理想状态下,任何操作工位 间和工作内的多余的WIP为零。
• 例1:缩短生产节拍 • 提升生产速度,维持人手不变。
第20页/共48页
二. 生产线平衡分析方法
• 例2:减少人手(1) • 减少人员,维持生产速度不变
第21页/共48页
二. 生产线平衡分析方法
• 例3:减少人手(2) • 降低线体速度,减少生产产量
第22页/共48页
二. 生产线平衡分析方法
二. 生产线平衡分析方法
• 案例计算
第14页/共48页
二. 生产线平衡分析方法
• 案例
第15页/共48页
二. 生产线平衡分析方法
6. 生产线平衡分析方法
第16页/共48页
二. 生产线平衡分析方法
7. 改善瓶颈岗位
第17页/共48页
二. 生产线平衡分析方法
• 改善四大原则
• 较少动作次数
改善前生产线平衡率=(18+16+24+37+45+16)/(37*7)*100%=60.2%
• 改善前生产线各工位平衡图
第42页/共48页
四. 线平衡经典案例分享
2. 改善前分析
第43页/共48页
四. 线平衡经典案例分享
பைடு நூலகம்3. 改善前后对比
第44页/共48页
四. 线平衡经典案例分享
3. 改善前后对比
B值得最优值为“1”
第29页/共48页
三. B值、F值的定义和计算
2. 一个流成产 One world、One dream One piece、One flow
• One piece flow是指单件进行生产,即人工每次只加工一件产品或部件,理想状态下,任何操作工位 间和工作内的多余的WIP为零。
• 例1:缩短生产节拍 • 提升生产速度,维持人手不变。
第20页/共48页
二. 生产线平衡分析方法
• 例2:减少人手(1) • 减少人员,维持生产速度不变
第21页/共48页
二. 生产线平衡分析方法
• 例3:减少人手(2) • 降低线体速度,减少生产产量
第22页/共48页
二. 生产线平衡分析方法
生产线平衡(实例版)PPT课件
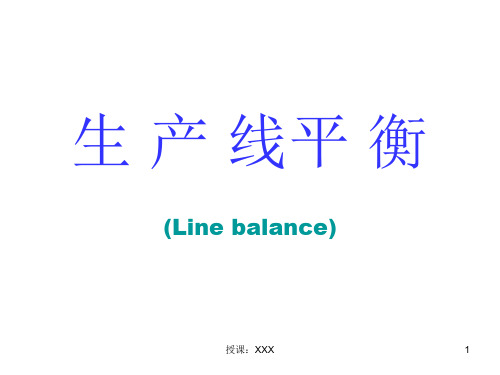
产能力﹑生产速度和效率.
其计算公式:
计划期内有效工作时间
节拍r= 计划期内计划产量
[时间/件]
授课:XXX
11
1﹑生产线平衡的相关概念
例﹕节拍计算
某制品流水线计划年销售量为500000件﹐另 需生产备件10000件﹐良率98%﹐两班制工作 ﹐每班8小时﹐每周6天工作时间﹐时间有效 利用系数95%﹐求流水线的节拍。
按A 键 按 B 键归零
23
2﹑生产线平衡的实施
2.1.3时间记录表
授课:XXX
9.23
24
2﹑生产线平衡的实施
2.1.4工时测量的作用
➢ 获取各工站的实际操作时间﹐为山积表 制作﹐时间平衡作准备﹔
➢ 通过时间观测﹐分析作业价值﹐发现问 题和改善空间﹔
➢ 形成标准﹐比较实际差异﹐找出问题.
授课:XXX
时间
瓶颈时间
T1 T2
T5
T3 T4
S1 S2 S3 S4 工站
S1 S2 S3 S4 S5 工站
授课:XXX
29
2﹑生产线平衡的实施
2.3.3提高作业者技能
--或调换高技能作业者
1.优化工站物料﹐
时
工具摆放
间
2.改善操作员的
操作方法
3.提高操作员动作
效率
授课:XXX
山积表 重合简取排并化消
工 站
时间
T2
T1
T3 T4 T5
工站 S1 S2 S3 S4 S5
单件标准时间= T1+T2+T3+T4+T5
(流程中各工站所有动作标准时间之和)
授课:XXX
13
1﹑生产线平衡的相关概念
其计算公式:
计划期内有效工作时间
节拍r= 计划期内计划产量
[时间/件]
授课:XXX
11
1﹑生产线平衡的相关概念
例﹕节拍计算
某制品流水线计划年销售量为500000件﹐另 需生产备件10000件﹐良率98%﹐两班制工作 ﹐每班8小时﹐每周6天工作时间﹐时间有效 利用系数95%﹐求流水线的节拍。
按A 键 按 B 键归零
23
2﹑生产线平衡的实施
2.1.3时间记录表
授课:XXX
9.23
24
2﹑生产线平衡的实施
2.1.4工时测量的作用
➢ 获取各工站的实际操作时间﹐为山积表 制作﹐时间平衡作准备﹔
➢ 通过时间观测﹐分析作业价值﹐发现问 题和改善空间﹔
➢ 形成标准﹐比较实际差异﹐找出问题.
授课:XXX
时间
瓶颈时间
T1 T2
T5
T3 T4
S1 S2 S3 S4 工站
S1 S2 S3 S4 S5 工站
授课:XXX
29
2﹑生产线平衡的实施
2.3.3提高作业者技能
--或调换高技能作业者
1.优化工站物料﹐
时
工具摆放
间
2.改善操作员的
操作方法
3.提高操作员动作
效率
授课:XXX
山积表 重合简取排并化消
工 站
时间
T2
T1
T3 T4 T5
工站 S1 S2 S3 S4 S5
单件标准时间= T1+T2+T3+T4+T5
(流程中各工站所有动作标准时间之和)
授课:XXX
13
1﹑生产线平衡的相关概念
《生产线平衡》课件

瓶颈工序
生产节拍
生产线上的瓶颈工序是指生产能力不足的 工作站,应通过优化生产流程和调整工作 量来消除瓶颈。
生产节拍是指生产线上的一个工作站完成 一个产品所需的时间,应保持生产节拍的 一致性以提高生产效率。
02
生产线平衡的优化方法
工艺流程分析
总结词
通过对生产工艺流程的详细分析,识别流程中的瓶颈和浪费,为后续优化提供基 础。
工作研究
总结词
通过系统的方法对工作过程进行研究 ,以提高工作效率和工作质量。
详细描述
工作研究是对整个工作过程进行系统 化研究的学科,通过工作研究可以发 现工作中存在的问题和瓶颈,提出改 进方案,提高工作效率和工作质量。
动作分析
总结词
对操作过程中的动作进行分解、分析和 优化,以提高工作效率和减轻工人负担 。
优化工艺流程
总结词
通过优化工艺流程,可以减少生产瓶颈,提高生产线的平衡率。
详细描述
对工艺流程进行分析,找出瓶颈环节,通过改进工艺、调整设备参数等方式,提高各环节的生产能力 ,使整个生产线更加平衡。
提高设备利用率
总结词
通过提高设备利用率,可以降低生产成本, 提高产能。
详细描述
合理安排生产计划,确保设备得到充分利用 。同时,加强设备维护保养,延长设备使用 寿命,降低故障率,进一步提高设备利用率 。
生产线平衡的目标与原则
目标
实现工作站间的平衡,提高生产效率,降低生产成本。
原则
合理分配工作量、保持生产线的连续性和稳定性、优化生产流程。
生产线平衡的评估指标
平衡率
空闲时间
衡量生产线平衡程度的指标,计算公式为 (各工作站所需时间总和)/(最长工作站 所需时间)×100%。
生产线平衡详解26页PPT
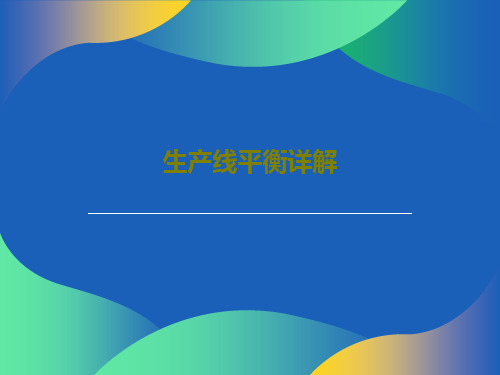
45、法律的制定是为了保证每一个人 自由发 挥自己 的才能 ,而不 是为了 束缚他 的才能 。—— 罗伯斯 庇尔
61、奢侈是舒适的,否则就不是奢侈 。——CocoCha nel 62、少而好学,如日出之阳;壮而好学 ,如日 中之光 ;志而 好学, 如炳烛 之光。 ——刘 向 63、三军可夺帅也,匹夫不可夺志也。 ——孔 丘 64、人生就是学校。在那里,与其说好 的教师 是幸福 ,不如 说好的 教师是 不幸。 ——海 贝尔 65、接受挑战,就可以享受胜利的喜悦 。——杰纳勒 尔·乔治·S·巴顿
生产线平衡详解
41、实际上,我们想要的不是针对犯 罪的法 律,而 是针对 疯狂的 法律。 ——马 克·吐温 42、法律的力量应当跟随着公民,就 像影子 跟随着 身体一 样。— —贝卡 利亚 43、法律和制度必须跟上人类思想进 步。— —杰弗 逊 44、人类受制于法律,法律受制于情 理。— —托·富 勒
谢谢!
ห้องสมุดไป่ตู้
61、奢侈是舒适的,否则就不是奢侈 。——CocoCha nel 62、少而好学,如日出之阳;壮而好学 ,如日 中之光 ;志而 好学, 如炳烛 之光。 ——刘 向 63、三军可夺帅也,匹夫不可夺志也。 ——孔 丘 64、人生就是学校。在那里,与其说好 的教师 是幸福 ,不如 说好的 教师是 不幸。 ——海 贝尔 65、接受挑战,就可以享受胜利的喜悦 。——杰纳勒 尔·乔治·S·巴顿
生产线平衡详解
41、实际上,我们想要的不是针对犯 罪的法 律,而 是针对 疯狂的 法律。 ——马 克·吐温 42、法律的力量应当跟随着公民,就 像影子 跟随着 身体一 样。— —贝卡 利亚 43、法律和制度必须跟上人类思想进 步。— —杰弗 逊 44、人类受制于法律,法律受制于情 理。— —托·富 勒
谢谢!
ห้องสมุดไป่ตู้
- 1、下载文档前请自行甄别文档内容的完整性,平台不提供额外的编辑、内容补充、找答案等附加服务。
- 2、"仅部分预览"的文档,不可在线预览部分如存在完整性等问题,可反馈申请退款(可完整预览的文档不适用该条件!)。
- 3、如文档侵犯您的权益,请联系客服反馈,我们会尽快为您处理(人工客服工作时间:9:00-18:30)。
基础的改善
运用5S,现 时现地现物管 理,清除浪费
成本降低的整体 实现
通过VA/VE及流
程改善做最佳組
合
3
2. 造成成本高涨的因果图
第一次浪费 ① 设备过剩 ② 库存过剩 ③ 人员过剩
第二次浪费 生产过多浪费
多余折旧费用 多余的保养费用 多余的利息费用 多余的劳务费用
第三次浪费 库存过剩的浪费
第四次浪费 ①多余的仓库 ②多余的搬运人员 ③多余的搬运设备 ④多余的库存管理人员、
生产线平衡的秘笈
1
一. 生產綫平衡概要
没有赚钱的企业是罪恶 ~松下幸之助~
当$1=¥8.26 当$1=¥8.11
当$1=¥7.50
企业有利润吗?
当石油1桶=$30
当石油1桶=$40
贵公司可承受吗?
当石油1桶=$50
当石油1桶=$60
…… 2
1. 正确生产管理工厂改善图
良好生产性保全
保护我们的设备, 实现设备的良好运 行
9
SDCA 与 PDCA
PD AC
現有 水準
PD AC
SD AC
SD AC
具體落實的方法:QC Story
SD AC
期望 水準
S:標準化程序,SOP (P:Plan計劃)
D:Do執行 C:Check檢查 A:Action行動
‧維持:(Standardization)DCA 依標準SOP而DCA
‧改善:I(Improvement)DCA 依改善之計劃而DCA
步骤4 准备改善作业的进行 步骤5 藉着5S及目视管理不断改善“个别作业准备”的目 8
維持/改善/創新 三階段
高階主管 中階主管 基層員工
維持
創新 改善
維持(Maintenance): ‧遵守作業標準
改善(Improvement): ‧改良改善
創新(Innovation,Break-Through): ‧結構性改善 ‧滿足客戶潛在需求
搬运设备选定
生产线布置设计
工厂 布置原则
稼动时间 预测不良率等
输送带上 的产品间隔 生产线速度
产品特性 作业特性
7
缩短准备时间方法
步骤1 对准备作业分析,把内部作业准备和外部作业准备 区分开来。
步骤2 分开外部作业准备,尽可能进行外部作业准备,缩 短机械停待的时间。
步骤3 改善内部作业准备,缩短准备的时间。 工具的改善 确定下一个要加工零部件的摆放位置 确定加工完毕零部件的摆放位置 改善零部件的装卸方法 减少调整作业 对于模具、夹具之高度,可进行标准化
品质管理及保证
改善质量,提供 质量保证
车间之间的协调
以满足顾客为目标, 以“下一道工序是 客户”的认知,推 动车间之间的协调
用“生产管 理”改善和 改变工厂, 完成做强做 大的目标
保证及缩短交期 创建-灵活及可 目视管理的工厂
最低库存 确保库存最低量, 没有无用或多余 东西
个别工序的改善
让每个人都成为多 能高手,提高个人 的改善意识和技巧
5、装配生产线安排流程
图面
试作
出勤率其他
支援人员 间接人员
场区空间分析
•作业空间 •保管空间
装配顺序的决定
时间分析
主线、副线区分 编成条件分析
•优先顺位 •作业位置 •设备
生产线平衡 (工程分割结合)
所要工程数
所要作业人员
人员编成
全面工厂 布置计划
生产计划 规制时间推算
产品的尺寸 作业性其他 工程间隔 生产线长度
生产技术的改善
制造工艺的改善
外协批量改善
简化生产的设计
易于生产的设计 设计更改的最优化 工序布局的改善 工具、夹具改善 加工条件最优化 机械设备故障和不良的排除 目视管理 自动化 批次大小最优化 提高作业人员技能 日程计划和进度的管理
5 S 和 减 少 浪 费
5
4. 生产管理的全貌
营销业务 客户讯息往来 确认订单
使各作业员的工 作范围能弹性的
扩大或缩小
「省人化」 减少各制程的作
业人数
连结U型生产线 的机械配置
多功能作业员 工作轮调
修正标准操作 流程
制程的改善
改善作业
机器的改善 (自动化) 13
改善活动的框架图
生产力的提高
作业人员的削减 (省人化)
标准操作 流程表的修正
人性尊重 作业员提高士气
作业标准化
现场改善的活动
作业员在一周期时间 内可操作许多机器
调查故障,或者是 异常的根本原因
仅供给「良品」
人力操作和机器 作业可以分离
「指示灯」点亮
必要的数量或者 是作业完成,机 器会自动停止
故障被发觉之后, 机器会自动停止
自动化=偏差(异常)发觉后机器会自动停止
12
「省人化」的过程
「少人化」 为适应需要品的变动,对各制程作业人数作弹性变化
预测订单情况 销售计划
产品负责人 订单、出货管理
研发设计部门 研发设计 技术资料整理
生产管理部门
大日程计划
材料计划
产能负荷计划
中日程计划
发行作业指示书
制造工程部门 生产技术、安排、作业指导书
采购
外购、外发、计划, 库存管理
制造部门 小日程管理/作业指导 进度/在制/工具/品质管理
质量管理 成本管理
6
维持品质人员
制造成本增加
4
3. 总结降低成本示意图
降 低 变 动 费
降 低 成 本
降低单价
最佳的采购
最佳的规格等级、 原材料配比等
外协价格的降低
提高良品 率材料利
用率
降低不良率 降低损耗
消除库存
压
缩
提高生产效
固
率、速度、 改善设备开工率、
定
灵活性
改变生产方式
费
减少支出
合理的采购战略
批量的改善
VA/VE
小集团活动
人的作业改善 机器的改善(自动化) 材料消耗品使用上的改善 QCC 提案
பைடு நூலகம்制度
改善的动机
看板制度
14
二. 工程分析及编排要点
1、工程分析
所谓的工程分析就是依照工程顺序为 了达成生产效果,把设备和人配置在连续 生产线的作业区域内所安排的设计。
15
2、工程分析的必要性
(一)投入新产品的大量生产。 (二)虽然是生产线生产,但经常更换形式,有
必要重新安排。 (三)虽然使用批量生产,因生产量增加,有必
要改用生产线化。 (四)现在实施生产线生产,由于产品一部分变
更,修正工程分析必要。 (五)工序间的负荷不平衡,要改善生产线,其
工程分析的顺序或重点会改变其编排。
16
3、生产线工程分析及编排要点
(A)装配顺序的考量。 (B)时间的分析。 (C)主生产线和副生产线串联。 (D)必要条件的分析:
‧創新
10
如何判定生产合理化?
设备的自动化程度不是判定的基准 库存品的高低才是判定的基准
库存高,生产合理化程度低 库存低,生产合理化程度高
降低库存才能达到合理化
11
如何达成「自动化」的目的
适应可能的生产
降低成本
品质保证 人性的尊重
及时生产的达成 作业人数的削减
改善活动(更正活动)
仅供给必要的数量