8000T浮吊船体建造原则工艺
8000T浮吊船体建造原则工艺

1总则1.1本文件为8000T浮吊船船体建造施工原则指导性工艺文件。
1.2本文依据《8000T浮吊合同—详细技术规范—[驳船部分]》的要求编写。
1.3本船入韩国船级社(KR),KRS1—起重机驳船.IWS。
1.4在船体建造中,除遵守本文件的要求外,还应同时满足KR规范要求、CSQS(2005)《中国造船质量标准》和CB/T3136—95《船体建造精度标准》、建造合同和设计图样中的有关规定和要求。
2概述本船为非自航非旋转起重驳,线型为方艏方艉,舷侧底部为圆舭,艏艉船底呈雪撬型,无梁拱,无艏艉舷弧。
艏部设有起重机支架,艉部为上层建筑,艉机舱。
本船设有部分双层底,部分平台,两侧为箱形,主结构采用纵骨架式,由横向强框架支撑,主甲板为强力甲板。
主甲板下设有7道水密横舱壁和4道前后贯穿连续纵舱壁将船体分割为多个水密舱室,压载水舱、淡水舱、饮水舱、污水舱、机舱、副机舱、锚链舱、液压泵站,燃油舱等,,详见总布置图。
上层建筑甲板室采用横骨架式结构。
2.1 主尺度总长:172.0 m垂线间长:170.0 m型宽:67.0 m型深:11.0 m满载吃水: 6.8 m2.2 甲板层高(中心线处)主甲板—A甲板 3.0 mA甲板—B甲板 3.0 mB甲板—C甲板 3.0 mC甲板—D甲板 3.0 m2.3 肋距、梁拱、脊弧肋距与纵骨间距:全船肋骨间距2500.0 m 纵骨间距0.8、0.78m梁拱:主甲板—D甲板` 0.0 m 脊弧:本船无脊弧3船体材料及技术要求3.1船体结构选用钢板、型材和铸锻件应满足KR规范要求并附有质量保证书。
3.2主船体结构的板材、零件缺陷需在CSQS(2005)标准之内,超差缺陷的修补须应满足中国船舶行业标准(CB),或经船东和KR 船级社同意。
3.3本船材料的使用应符合规格书(或有关图纸要求)。
当规格书(或有关图纸)中规定的任何一种材料无法及时获得,应征KR、船东和船厂互相同意的情况下使用适当的替代材料。
船体施工工艺

本船将主船体划为5个立体分段,分别为101、102、103、104、105分段;主甲板室划分为2个立体分段,分别为201、202分段。
上甲板室划分为1个立体分段,301分段。
2.3分段建造简介胎架采取反造甲板胎架(模板每2~3肋位设置)主船体分段以主甲板为基准面进行反造;上层建筑分段分别以各层甲板为基准面进行反造。
各分段采取各构件按铺板贴胎、板缝焊接、划线、结构安装、验收、焊接的工艺顺序进行制作全船板材采用数控切割下料,型材采用手工下料。
2.4分段合拢根据本船分段划分特点,本船将按下列合拢顺序进行本船的船台合拢:分段组装先后顺序序分段名备注号1 102分段定位分段上船台2 101、103分段分别与102分段合拢3 104分段与103分段合拢4 105分段与104分段合拢悉有关的工艺和技术文件,按要求施工。
4.3工艺要求4.3.1小组立4.3.1.1小组立工艺流程4.3.1.2小组立作业标准a) 构件对划线(理论线)<1.5mm~2.0mmb) 平整度<4mm~6mmc) 小零件对大零件垂直度<2 mmd) 平面板架:L<±4mm B<±4mme) 对角线差值:L1-L2<4mm4.3.2中组立4.3.2.1 中组立工艺流程4.3.2.2 中组立作业标准a) 构件对合线(理论线或对合线)偏移<1.5mmb) 主要平面不平度<4mmc) 小零件对大零件垂直度<2mmd) 框架四角水平<±4mme) 纵骨端面平面度<±4mmf) 两对角线中点间距≤2mm4.3.3大组立4.3.3.1 客船双层底大组立4.3.3.1.1工艺流程4.3.3.1.2装配作业标准a) 分段长:L <±4mmb) 分段宽:B <±4mmc) 分段高:H <±3mmd) 分段方正度:<4mm (内、外底板对角线差值)e) 分段扭曲度:<±8mm (内底板四角水平)f) 纵骨端平面度:<±4mmg) 内、外底板中心线偏差<±3mmh) 内、外底板肋位线偏差<±3mm4.3.3.2机舱大组立4.3.3.2.1机舱工艺流程4.3.3.2.2装配作业标准a) 分段长L <±4mmb) 分段宽B <±4mmc) 分段高H <±4mmd) 分段方正度(内底板四角水平)<±8mm4.3.3.3其它立体分段大组立4.3.3.3.1分段工艺流程4.3.3.3.2装配作业标准a) 分段长<±4mmb) 分段宽<±4mmc) 分段高<±4mmd) 纵横舱壁垂直度<0.1%h,且小于10mme) 分段两端平面<±4mm4.3.3.4艉部分段大组立4.3.3.4.1艉部分段工艺流程4.3.3.4.2装配作业标准a) 前后尾轴管偏心<3mm (施工中焊接变形进行监控)b) 尾尖舱壁水平<±4mmc) 和铸钢件相焊焊缝铸钢件和钢板预热。
浮船施工方案(3篇)

第1篇一、项目背景随着我国基础设施建设的不断发展,桥梁、码头、水利工程等工程对浮船施工的需求日益增加。
浮船施工具有施工速度快、适应性强、不受地面条件限制等优点,已成为水利工程、港口建设等领域的重要施工方式。
本方案旨在为浮船施工提供一套科学、合理、安全的施工方案。
二、工程概况1. 工程名称:某水利工程浮船施工2. 工程地点:某市某区某河段3. 工程规模:全长1000米,河宽80米,水深5米4. 施工内容:河床清淤、河道拓宽、护岸建设、桥梁建设等三、施工组织1. 施工队伍:由具有丰富浮船施工经验的施工队伍组成,包括项目经理、技术负责人、施工人员、安全员等。
2. 施工设备:浮船、吊车、挖掘机、推土机、混凝土搅拌车、装载机等。
3. 施工材料:混凝土、钢筋、石料、木材、水泥、沙子等。
四、施工工艺1. 浮船准备- 浮船选用符合设计要求的浮船,确保浮船稳定性。
- 浮船内部设置操作平台,方便施工人员进行操作。
- 浮船外部涂刷防腐蚀涂料,延长使用寿命。
2. 浮船定位- 根据工程图纸,确定浮船的定位位置。
- 使用GPS定位系统,精确测量浮船位置。
- 利用锚绳将浮船固定在预定位置。
3. 河床清淤- 使用挖掘机将河床内的淤泥挖出,运至指定地点堆放。
- 清淤过程中,注意保护河床生态环境。
4. 河道拓宽- 使用挖掘机将河床两侧的土方挖出,拓宽河道。
- 拓宽后的河床进行平整,确保河床表面平整。
5. 护岸建设- 根据设计要求,选择合适的护岸材料。
- 使用吊车将护岸材料运至施工现场。
- 护岸材料按照设计要求进行安装,确保护岸稳固。
6. 桥梁建设- 根据设计图纸,进行桥梁基础施工。
- 使用浮船作为施工平台,进行桥梁主体结构施工。
- 桥梁施工过程中,注意安全防护。
五、施工进度1. 施工准备阶段:1个月2. 河床清淤阶段:2个月3. 河道拓宽阶段:1个月4. 护岸建设阶段:1个月5. 桥梁建设阶段:3个月6. 验收阶段:1个月六、施工安全1. 人员安全:加强对施工人员的安全教育,提高安全意识。
3000_t超大超高型浮吊船起重机安装工艺
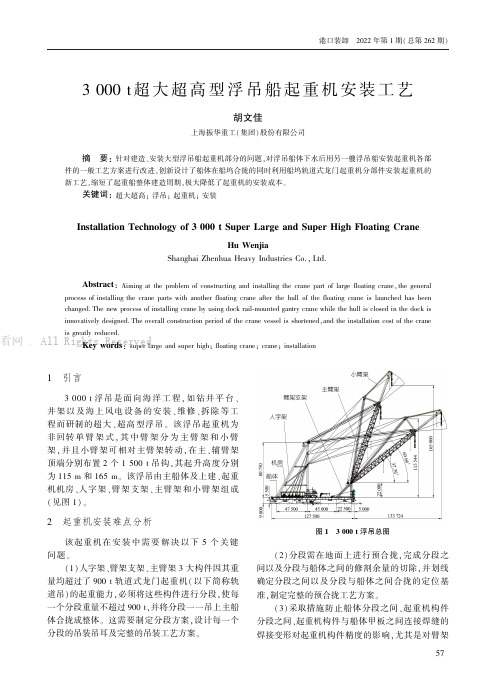
3000t超大超高型浮吊船起重机安装工艺胡文佳上海振华重工(集团)股份有限公司㊀㊀摘㊀要:针对建造㊁安装大型浮吊船起重机部分的问题,对浮吊船体下水后用另一艘浮吊船安装起重机各部件的一般工艺方案进行改进,创新设计了船体在船坞合拢的同时利用船坞轨道式龙门起重机分部件安装起重机的新工艺,缩短了起重船整体建造周期,极大降低了起重机的安装成本㊂㊀㊀关键词:超大超高;浮吊;起重机;安装Installation Technology of3000t Super Large and Super High Floating CraneHu WenjiaShanghai Zhenhua Heavy Industries Co.,Ltd.㊀㊀Abstract:Aiming at the problem of constructing and installing the crane part of large floating crane,the general process of installing the crane parts with another floating crane after the hull of the floating crane is launched has been changed.The new process of installing crane by using dock rail-mounted gantry crane while the hull is closed in the dock is innovatively designed.The overall construction period of the crane vessel is shortened,and the installation cost of the crane is greatly reduced.㊀㊀Key words:super large and super high;floating crane;crane;installation1㊀引言3000t浮吊是面向海洋工程,如钻井平台㊁井架以及海上风电设备的安装㊁维修㊁拆除等工程而研制的超大㊁超高型浮吊㊂该浮吊起重机为非回转单臂架式,其中臂架分为主臂架和小臂架,并且小臂架可相对主臂架转动,在主㊁辅臂架顶端分别布置2个1500t吊钩,其起升高度分别为115m和165m㊂该浮吊由主船体及上建㊁起重机机房㊁人字架㊁臂架支架㊁主臂架和小臂架组成(见图1)㊂2㊀起重机安装难点分析该起重机在安装中需要解决以下5个关键问题㊂(1)人字架㊁臂架支架㊁主臂架3大构件因其重量均超过了900t轨道式龙门起重机(以下简称轨道吊)的起重能力,必须将这些构件进行分段,使每一个分段重量不超过900t,并将分段一一吊上主船体合拢成整体㊂这需要制定分段方案,设计每一个分段的吊装吊耳及完整的吊装工艺方案㊂图1㊀3000t浮吊总图(2)分段需在地面上进行预合拢,完成分段之间以及分段与船体之间的修割余量的切除,并划线确定分段之间以及分段与船体之间合拢的定位基准,制定完整的预合拢工艺方案㊂(3)采取措施防止船体分段之间㊁起重机构件分段之间㊁起重机构件与船体甲板之间连接焊缝的焊接变形对起重机构件精度的影响,尤其是对臂架75博看网 . All Rights Reserved.支架和臂架铰点孔同轴度的影响㊂(4)由于臂架从0ʎ扳起,此工况不在起重机设计工况内,需计算此工况电机功率是否满足;变幅钢丝绳㊁变幅机构所有零件是否安全;人字架㊁臂架支架㊁主臂架结构是否安全㊂(5)计算人字架㊁臂架支架船体约束反力,并由此校核船体结构的安全,并设计臂架扳起过程中船体吃水和压载舱加载方案㊂3㊀安装工艺设计3.1㊀项目场地布局当坞内进行主船体合拢的同时,在坞北端900t轨道吊覆盖的的场地内同时进行人字架㊁臂架支架㊁主臂架㊁小臂架的整体合拢或预合拢,并在人字架和臂架支架完成在主船体上的搭载后,完成主臂架分段的吊装合拢及小臂架的吊装(见图2)㊂图2㊀起重机构件预拼装及在船体上搭载场地分布图3.2㊀船体安装的顺序船体分段的搭载合拢应从中间分段向前后两段的顺序展开,应尽量先完成起重机机器房所在部位的船体分段的合拢,以便于尽早开展各机构的搭载㊁电气控制部分的安装以及电缆走线工作的完成㊂随后进行机器房安装,人字架各分段的吊装㊁焊接,臂架支架的吊装定位㊁焊接,臂架铰点孔的加工㊁头部调整(小臂架变幅)机构㊁稳货机构的安装㊂以上安装完成后进行主臂架的吊装,穿主铰点轴;小臂架的吊装,穿小臂架轴;穿引主变幅㊁小臂变幅㊁起升㊁索具钩㊁稳货钩钢丝绳㊂在此基础上,用主变幅机构将主臂架和小臂架从0ʎ扳至50ʎ仰角后,浮吊就可以下水,进入调试阶段㊂4㊀安装工艺方案实施4.1㊀人字架安装工艺人字架高度高㊁质量重㊁结构复杂,吊装难度大㊂在吊装搭载前,人字架在地面进行了预拼装㊂在预拼装完成后用激光经纬仪划出压杆片体㊁拉杆片体㊁上部横梁的安装定位基准(纵向㊁横向中心线以及水平等高线),并用全站仪实测船甲板上表面拉杆和压杆与船体连接的4个部位的水平高度值,依据实测值复算出拉杆㊁压杆圆管端部的余量修割线位置线,并修割余量㊂完成机房的组装后进行人字架吊装,各机构的排装㊁电缆的铺设及接线可在人字架安装过程中同步进行㊂人字架安装顺序为压杆片体-两侧面的横撑㊁斜撑-拉杆片体-上部横梁-2个变幅滑轮架(见图3)㊂图3㊀人字架搭载吊装图4.2㊀臂架支架安装工艺臂架支架分为上部横梁和左右2个片体3个分段,并在地面按以下2个步骤进行预拼装:①臂架铰点结构以下部分组合成左右2个片体,并与臂架铰点结构预拼装,并划出左右片体在船体结85博看网 . All Rights Reserved.构上的定位基准线以及下端的余量修割线,同时基准中心线引申至臂架铰点结构;②取下2个铰点头部结构与中间横梁拼装组合成1个构件(见图4)㊂图4㊀臂架支架安装示意图在臂架支架安装定位并完成连接部的第一道焊接后,即可进行头部调整机构和稳货机构的吊装定位焊接,吊装前应根据船体整体纵向和横向中心线划出臂架横梁的中心线及6个机构的定位基准线㊂臂架铰点孔位于上部横梁两端,左右2个铰点孔有同轴度要求㊂为防止焊接变形对铰点孔同轴度的影响,镗孔前必须完成臂架支架分段之间㊁臂架支架与船体之间以及与臂架支架下部的船体分段之间的连接焊缝的施焊㊂采用2台镗床同时镗孔,用全站仪配合多棱镜校对2根镗排的同轴度,且校对都安排在凌晨太阳出来以前进行㊂实际镗排的同轴度控制在30~50μm 之间㊂4.3㊀主臂架和小臂架安装工艺主臂架质量为1921t,将其分为3个分段(见图5)㊂后段断面布置在离中间连接横梁2470mm处,这样能使后段与中段的焊接变形因横梁处较强的刚性而降到最低程度,从而最大限度的保证两侧铰点孔的同轴度不因焊接变形而降低㊂图5㊀主臂架分段装示意图㊀㊀主臂架在地面完成3个分段的预拼装,用激光经纬仪划出分段之间的定位基准(水平㊁横向㊁纵向中心线),并划出主臂架和小臂架铰点孔中心线后镗孔,镗孔的过程中按臂架支架铰点孔精度控制方法调校两侧镗排以保证两侧孔的同轴度㊂在此工位完成主臂架附件(滑轮㊁吊钩定滑轮组㊁舾装件㊁电气附件等)的组装,同时完成小臂架的镗孔和组装㊂按图6所示,先吊装主臂架后段并完成铰点轴的安装,随后吊装中段㊁前段,定位后进行各分段连接焊缝的施焊,施焊时应注意两侧对称施焊;在焊接的同时完成小臂架的吊装以及所有钢丝绳的穿引㊂4.4㊀臂架扳起时起重机安全性验算臂架在0ʎ拉起为非正常工况,经计算,此工况下的变幅钢丝绳拉力为23MN,大于正常工况最大计算拉力17MN,有必要对此工况下的起重机相关机构及结构的强度进行安全性验算㊂计算采用AN-SYS 有限元分析软件,臂架位于水平位置建立模型㊂对变幅机构进行钢丝绳㊁电机静功率㊁卷筒扭矩及机构零件的安全性验算㊂经计算,钢丝绳的安全系数为2.3,电机的过载系数为1.1,而卷筒在此工况时的扭矩小于变幅机构计算书中的最大计算扭矩(此时钢丝绳在卷筒最底层,力臂最小),因此可以判定变幅机构所有传动零件是安全的㊂对主臂架(主弦杆和腹杆的4个单元)㊁人字架的压杆和拉杆㊁臂架支架㊁变幅滑轮架等危险结构及危险单元进行验算,除进行最大应力验算外,还对受压杆件进行了稳定性计算㊂经计算,所有结构均安全㊂95博看网 . All Rights Reserved.图6㊀主臂架安装示意图4.5㊀船体结构安全性验算在进行上述验算的同时,计算出臂架0ʎ扳起时人字架和臂架支架与船体连接部位处船体的约束反力,将此数据输入船体结构有限元分析模型,发现以下3处危险部位:人字架压杆处船体结构的最大应力达282.3MPa;船艉部最大形变较大为282.26mm;臂架支架部位部分坞墩受力超载,最大达36MN㊂为此经过计算,在臂架从0ʎ扳起至50ʎ的过程中,在坞内放水用浮力减轻坞墩受力,在压载舱加水降低尾部形变和船体结构的应力,并在臂架扳起的过程中不断地调整坞内的水位高度和舱室压载高度,可保证船体结构及坞墩受力在安全范围内,且船体未浮起㊂5㊀结语本项目已顺利完成建造和试验并投入使用,证明该工艺方案可行,可节约建造时间,降低建造成本,对大型船厂在建造同类型大型浮吊时具有借鉴意义㊂胡文佳:200125,上海市浦东新区东方路3261号收稿日期:2021-07-06DOI:10.3963/j.issn.1000-8969.2022.01.022皮带输送机钢丝胶带硫化工艺方案优化温晓磊河北港口集团有限公司㊀㊀摘㊀要:皮带输送机是矿山㊁港口等干散货运输的重要设备㊂在皮带输送机钢丝胶带热硫化接头过程中,根据环境㊁温度等因素变化,对硫化工艺进行优化㊂经实践证明,优化后可改善硫化效果,提高硫化效率,节约停机成本,具备推广价值㊂㊀㊀关键词:胶带;硫化;工艺优化Optimization of Vulcanization Process Plan for Steel Wire Belt of Belt ConveyorWen XiaoleiHebei Port Group Co.,Ltd.㊀㊀Abstract :Belt conveyor is an important equipment for dry bulk transportation such as mines and ports.In theprocess of hot vulcanization joint of steel wire belt of belt conveyor,the vulcanization process is optimized according to thechanges of environment,temperature and other factors.The practice shows that the optimization can improve the vulcaniza-tion effect,improve the vulcanization efficiency,save the shutdown cost,and has popularization value.㊀㊀Key words :belt;vulcanization;process optimization6博看网 . All Rights Reserved.。
浮吊船整体架设钢桁梁施工技术

浮吊船整体架设钢桁梁施工技术发表时间:2017-08-11T10:42:26.280Z 来源:《基层建设》2017年第11期作者:杨旭东施逸楠[导读] 摘要:伴随着我国南北经济的不断增长,全国范围内各大运河的顺利运营运输离不开各个船只的流动运行。
南通振华重型装备制造有限公司南通分公司江苏省南通市 226001摘要:伴随着我国南北经济的不断增长,全国范围内各大运河的顺利运营运输离不开各个船只的流动运行。
多数都采用了浮吊船的架设钢桁梁整体结构,这一结构中,不仅船只的资本投资金额较小,而且还具有安全性能高、封航时间较短的优点。
本文就运河上浮吊船整体架设钢桁梁施工技术进行了一系列的分析与探讨,希望能为运河浮吊船的工程施工技术提升提供一些有效的参考意见。
关键词:浮吊船;架设钢桁梁;工程施工技术;建筑工程前言伴随着水路运输的作用越来越大,范围越来越广,国内运河的利用率也随之达到最高,运河当中最主要的运输工具浮吊船的使用也就随之更加广泛。
那么,如何将运河上浮吊船整体架设钢桁工程施工的场地与支架设计以及工程施工工艺进行有效优化,从而将运河上浮吊船整体架设钢桁工程顺利施工完成,是十分值得广大运河浮吊船整体架设钢桁工程的施工作业者值得思考的问题。
一、施工方案概述(一)进行施工方案类比选择在我国的当前河道上,想要将如此重量的钢桁梁架设起来,一般都会采用浮托的施工方案进行工程施工。
该种方法主要就是将钢桁梁运用支架法将其沿着桥梁的纵向进行拼装,将支撑点设置为航道上的诸多付拖船,从而利用牵引力将钢桁梁的整体移动到墩柱上完成就位[1]。
该种施工方案的缺点主要是临时支架的利用时间过长,封航的时间过多,而且大面积的占用了引桥的施工现场,对引桥的施工造成了负面影响。
该种项目施工方案的施工期间不长,还受到引桥施工周边的诸多房屋拆迁工程影响,根本不能够提供足够钢桁梁拼装所需要的施工场地。
在这一前提下,大部分的钢桁梁架设施工都会采用工期较长、施工成本较少的浮吊船整体架设钢桁梁施工方案。
大型海洋船舶起重机的吊装工艺

大型海洋船舶起重机的吊装工艺大型海洋船舶起重机是一种用于装卸货物的重型机械设备,可以承载数百吨的重量,因此在进行吊装时需要非常谨慎。
以下是大型海洋船舶起重机的吊装工艺。
1.准备工作在进行吊装前,需要进行一系列准备工作。
首先需要确定吊装地点,确定好吊装地点后需要对吊装区域进行清理,排除任何障碍物确保吊装时不会受到任何干扰。
其次需要检查起重机的各项部件是否正常工作并进行最后一次确认。
2.选择合适的吊装设备一般来说,大型海洋船舶起重机的吊装需要使用大型吊车或吊机等设备。
在选择合适的吊装设备时,需要注意设备的承载能力和使用限制。
3.吊装起重机的组成部分在吊装起重机之前,需要拆卸起重机的一些组成部分,如吊臂、钩吊等部件。
需要根据起重机的型号、各部件之间的连接方式、材料等,进行安全拆卸并分类存放。
4.吊装起重机主机开始吊装起重机主机时,需要确认吊装点是否合适,并进行绳索的正确架设。
在吊装时,需要根据吊装点的位置,配合吊车或吊机操作人员进行协同作业。
在吊起起重机主机后,需要进行调整,以确保主机与地面平齐。
5.吊装起重机组成部分并进行安装在吊装吊臂、钩吊等组成部分时,需要先将这些部分进行拼装,并进行必要的检查,确保各部分连接正常。
在进行吊装时,需要根据各部分的叠放顺序,进行正确拆装并注意安全。
6.现场安装为确保新安装的起重机符合使用要求,需要进行现场安装,并进行调整,以确保起重机整体与场地平齐。
同时进行最后一次检查,确保整个过程安全可靠。
以上是大型海洋船舶起重机的吊装工艺。
在进行吊装时需要严格按照规定操作,并注意安全。
如有不确定的地方,应及时咨询专业技术人员。
船舶建造工艺策划方案

船舶建造工艺策划方案一、前言船舶建造工艺是指在船舶设计的基础上,通过一系列的工艺流程和制造手段,将设计图纸转化为实际的船体结构。
船舶建造工艺策划方案是指为了顺利完成船舶建造工艺流程,保证船舶质量和建造进度,制定的详细工艺流程和实施方案。
本文主要讲述船舶建造工艺策划方案的编制内容和要求,以期为读者提供一份全面和详细的指导。
二、编制内容和要求1. 工艺流程船舶建造工艺策划方案的主要内容是工艺流程,该流程应该包含以下几个方面:1.材料清单:列举船体建造中需要用到的主要材料,并注明该材料的性质、品牌、规格和供应商等信息。
2.加工计划:依据设计图纸,制定具体的材料加工计划,包括材料预处理、切割、焊接、钻孔、砂光和喷漆等加工环节。
3.装配计划:依据设计图纸和加工计划,制定具体的船体装配计划,包括船壳、船底、船甲板、救生艇和船舱等主要部件的安装顺序和方法等。
4.检验计划:依据国家标准和船级社要求,制定详细的检验计划,保证船舶建造过程中的质量和安全。
5.试验计划:制定船舶建造完成后的各项试验计划,确保船体结构和各项设备能够正常运转并满足设计要求。
2. 实施方案除工艺流程外,船舶建造工艺策划方案中还需要包含具体的实施方案,该方案应该包含以下几个方面:1.人员配备:制定人员配备方案,指明需要配备的专业人员和工人数量,确保人员数量和质量满足工艺流程的要求。
2.设备采购:指明需要采购的专业设备和材料,包括焊接机、起重机、喷漆设备和脚手架等,并确定采购渠道和规格品牌等。
3.安全措施:制定安全措施方案,确保船舶建造过程中的人身安全和设备安全,并指明风险评估和应急措施。
4.质量控制:制定质量控制方案,确保船体结构和设备的质量和安全,并确保检查流程的合理性和有效性。
3. 相关文件船舶建造工艺策划方案还需要包含以下相关文件:1.设计图纸:明确船体结构和各项设备的设计方案。
2.国家标准和船级社要求:确保船体结构和各项设备满足国家标准和船级社要求。
大型海洋船舶起重机的吊装工艺-精品文档

大型海洋船舶起重机的吊装工艺随着海域资源的大力开发和利用,相应海洋工程装备的制造业也越来越繁荣。
海洋船舶起重机也向着大起重量和大下降深度发展。
我公司大型海洋船舶起重机项目也越来越多。
大型海洋船舶起重机整机重量一般在380t〜610t左右,并且体积庞大长33.8m〜52.6m、宽8.7m〜11.1m、高14.6 〜16.0m,现有的吊装设备和吊装工具、吊耳布置等情况给车间和外场的吊装工作带来极大的困难。
此大型海洋船舶起重机吊装工艺,详细论述了大型海洋船舶起重机(以下简称海工吊)吊装操作的整个过程。
1 大型海洋船舶起重机吊装工艺内容1.1 塔身钢结构吊装大型海洋船舶起重机塔身钢结构重量约在80t〜110t,外形尺寸长5.3m〜8.1m *宽4.1m〜7.6m *高5.2m〜10.5m的筒体式结构。
利用单台行车吊运塔身至支撑架上与回转支撑进行安装。
由于塔身的吊耳布置和塔身重心位置不在与塔身轴线平行的同一条直线上,直接吊运塔身顶部吊耳塔身会倾斜,所以采取用手拉葫芦配合调整塔身平衡进行吊装。
在起吊前不断调整手拉葫芦长度来调整塔身的平衡,并注意铰点上的吊带和手拉葫芦受力要均匀。
待塔身调整平衡后,行车缓缓起吊塔身至回转支撑上方并慢慢下降。
完成塔身与回转支撑的安装。
此时第一步吊装已完成,手拉葫芦的使用和调整塔身平衡是此步骤的要点。
1.2 吊运塔身至发运工装塔身与回转支撑安装完毕后总重量在loot〜155t,外形尺寸长5.3m〜8.1m *宽4.1m〜7.6m *高5.3m〜11.0m。
此部吊装利用两台行车配合进行抬吊,并利用吊梁把塔身的自重分配到两台行车上,以满足行车起升能力。
此吊梁可以综合大型海洋船舶起重机重量来进行设计,以考虑到使用的通用性。
这里设计的是250t “十”字吊梁。
为了保证塔身在吊运过程中的平衡,吊梁设计时应增加吊耳,此吊耳用于吊塔身上的铰点孔。
吊梁设计是此部吊装的关键,并且要考虑到吊梁的通用性,吊梁上吊耳布置要根据塔身上吊耳布置情况和行车抬吊最小间距进行设计,适当多布置些吊耳。
大吨位钢桁架桥浮吊整体吊装架设施工工法

大吨位钢桁架桥浮吊整体吊装架设施工工法钢桁架桥是一种具有较大吨位的桥梁结构,其浮吊整体吊装架设是建造钢桁架桥的重要工法之一。
本文将针对大吨位钢桁架桥浮吊整体吊装架设工法进行详细阐述。
一、工法概述大吨位钢桁架桥浮吊整体吊装架设工法是指将整个钢桁架桥构件作为整体进行吊装架设的一种工法。
它相对于分段吊装架设工法,具有操作简便、施工效率高等优点。
二、前期准备在进行大吨位钢桁架桥浮吊整体吊装架设工法之前,需要进行充分的前期准备工作。
包括测量宽度、确认吊装位置、评估承重能力、制定安全措施等。
三、浮吊器具的选择在整体吊装桥梁时,浮吊器具的选择至关重要。
一般情况下,我们可以选择专业的浮吊设备,如浮吊平台、起重机等。
浮吊平台能够满足钢桁架桥的重量要求,并提供稳定的平台给起重机使用。
四、吊装架设工序1. 预先安装浮吊平台:将浮吊平台搭设在需要吊装的位置上,确保平台横向稳定。
在安装过程中,要确保护栏的牢固性和平台底部的平整度。
2. 安装起重机:将起重机吊装到浮吊平台上,并进行稳固固定。
起重机的选择要根据桥梁的重量和吊装高度来确定。
3. 调整平台水平度:调整浮吊平台的水平度,以确保后续的吊装过程顺利进行。
可以使用水平仪等工具进行测量和调整。
4. 吊装桥梁:将钢桁架桥构件整体吊装到合适的位置,可以采用起重机配合人工指挥的方式进行。
5. 定位和固定桥梁:将吊装好的钢桁架桥构件进行定位并固定。
在这一步骤中,需要根据设计要求进行精确调整,以确保桥梁的位置正确、稳定。
五、施工注意事项1. 安全第一:施工过程中,必须重视安全,严格执行安全操作规程,提前预防和消除隐患。
2. 严格控制浮吊平台的承重:浮吊平台的承重能力必须能够满足钢桁架桥的重量要求,且要经过专业计算和评估确认。
3. 防止桥梁变形:在吊装桥梁的过程中,要特别注意防止桥梁变形,避免不必要的损坏。
4. 平稳下降:在桥梁吊装过程中,需要控制起重机的速度和方向,确保桥梁平稳下降到位。
80000t级整体式浮船坞的拖航工程设计

52卷第1期(总第194期)中国造船V ol.52 No.1 (Serial No. 194)2011年3 月SHIPBUILDING OF CHINA Mar. 2011文章编号:1000-4882(2011)01-0165-0880000t级整体式浮船坞的拖航工程设计蒋志岩1,林华2,王文正1,吕洋1(1. 大连中远船务工程有限公司,大连 116113;2. 中远船务工程集团有限公司物资管理中心,大连 116600)摘要该文以一艘80000t级整体式浮船坞拖航为例,从被拖物的角度对拖航工程设计的步骤及工作内容做了系统阐述;在此基础上,针对浮船坞的特点对浮船坞拖航的技术难点做了进一步的探讨。
由于浮船坞的拖航阻力较大,拖力点的选取和拖力眼板的设计便成为浮船坞拖航设计的一项重要工作;鉴于浮船坞的强度校核关乎整个拖航工程的安全,该文利用有限元方法对浮船坞进行了整船有限元分析,既校核了拖航状态下的扭转强度、横向强度和局部强度,也对按规范进行的总纵强度校核做了进一步的验证。
坞墙既高又窄的结构特点使得对坞吊进行就地有效封固成为一项特别困难的工作,为了节约将坞吊拆卸再安装的高额成本,对其进行了专门的绑扎设计。
关键词:浮船坞;拖航;有限元方法;总纵强度;绑扎系固中图分类号:U661.43 文献标识码:A0 引言作为大型的修造船设施,浮船坞的建造港与使用港经常位于不同地域;由于买卖、转让、租借等原因,也可能使浮船坞的使用港在其服役期内发生变化。
鉴于浮船坞没有自航能力,因此必须借助拖船对其进行拖航作业,以达到变换使用港的目的。
由于浮船坞的造价上亿元,并且拖航时坞上一般都有相关人员随行;所以,一旦发生危险,后果将不堪设想。
与普通驳船或常规海损船相比,浮船坞有着自身的结构特点和船型特性;另外,相对于一般船舶而言,可供参考的浮船坞拖航实例也比较少。
由此可见,将浮船坞的拖航作为一个工程问题进行全面、深入的研究是十分必要的。
浮船设计与施工建设方案

浮船设计与施工建设方案浮船设计与施工建设方案1.概述1.1 工程概况及编制目的构皮滩水电站通航建筑物下游引航道位于大坝下游约800m处,右岸地形陡峻,施工道路布置困难。
为解决右岸机械、物资、渣石运至左岸施工的交通问题,特编制本方案,指导浮船项目施工,使其设计、安装和运行处于受控状态,满足质量、安全和运行要求。
1.2 地质特征下游引航道沿线地表有少量厚度不大的第四系残坡积层及冲积层分布,出露地层为寒武系中上统娄山关群(∈2+3ls)。
岩性主要为中厚层、薄层灰质白云岩、厚层白云质灰岩,顶部含燧石结核和白云质条带。
1.3 风向风力乌江流域全年地面盛行偏北风,夏季偏南风略占优。
工程所在地余庆县历年各月最大XXX速见下表。
余庆县历年各月最大SE风速表(单位:m/s)月份 1 2 3 4 5 6 7 8 9 10 11 12 全年风速 6.0 7.0 14.0 7.0 8.0 6.0 10.0 8.0 6.0 6.0 6.0 7.0 14.01.4 设计洪水构皮滩水电站为峡谷型水库,每年5月至10月为汛期(其中6月至7月为主汛期),11月至次年4月为枯水期。
江界河水文站多年平均流量为716m³/s,实测最大流量m³/s,最小流量86m³/s,调查历史最大流量m³/s。
构皮滩坝址天然水位流量关系见下表。
构皮滩坝址天然水位流量关系表D尺水位(m、黄海)F尺水位(m、黄海)流量(m³/s)429 427.2 83429.3 427.5 105429.5 427.7 117430 428.4 165431 429.4 261432 430.5 382433 431.6 517434 432.7 662435 433.8 827436 434.9 1010438 437 1396440 439.1 1808442 441.1 2269444 443.1 2778446 445.1 3359448 447.1 3991450 449.1 4676452 451.1 5426454 453.1 6260456 455 7115458 457 8029以上是浮船设计与施工建设方案的概述。
大型海洋船舶起重机的吊装工艺

优化吊装方案:根据实际情况选择合适的吊装方式,降低成本和时间消耗
强化设备维护:定期对起重设备进行检查和维护,确保设备处于良好状态
提高操作技能:加强操作人员的技能培训,提高吊装操作的准确性和稳定性
引入智能化技术:利用现代科技手段,如智能化控制系统,提高吊装效率
加强安全管理的建议与对策
制定严格的安全管理制度和操作规程,确保员工遵守。
定期进行安全培训和演练,提高员工的安全意识和应急处理能力。
配备齐全的安全设施和设备,确保在紧急情况下能够及时有效地应对。
加强现场监督和管理,及时发现和纠正不安全行为和状态。
THANK YOU
汇报人:
分类:根据吊装能力和应用场景,大型海洋船舶起重机可分为轻型、中型和重型三种类型。
特点:大型海洋船舶起重机具有吊装能力强、适用范围广、稳定性好、可靠性高等特点,能够满足大型海洋工程建设的需要。
吊装工艺流程
PART 02
吊装前准备
确定吊装方案
添加标题
吊装机械选择与调试
添加标题
吊装人员培训与安全教育
添加标题
吊装精度控制
吊装操作:由经验丰富的吊装操作人员执行,确保吊装过程中各项参数的准确性
测量定位:使用高精度测量仪器对吊点进行精确测量和定位
吊装方案:制定详细的吊装方案,包括吊装顺序、吊装路径等
监控与调整:在吊装过程中,实时监控吊装状态并进行必要的调整,确保吊装精度符合要求
吊装工艺的应用和发展
PART 04
大型海洋船舶起重机的吊装工艺
汇报人:
目录
01
大型海洋船舶起重机概述
02
吊装工艺流程
03
吊装工艺要点
浮船施工方案百度文库

浮船施工方案1. 引言浮船施工方案是指在水上进行船舶修建、维护和改造的施工方案。
本文档将详细介绍浮船施工方案的要点和操作步骤,以便工程人员能够按照规范进行施工。
2. 项目概述浮船施工项目是一项重要的船舶工程项目,它包括以下主要内容: - 船舶设计方案 - 施工材料准备 - 船体结构施工 - 船舶设备安装 - 船厂测试和调整3. 浮船施工步骤3.1 船舶设计方案在进行浮船施工前,需要根据船舶的类型和功能设计出相应的设计方案。
设计方案包括船舶的尺寸、结构、材料等。
设计方案需要经过船级社或相关部门的审查和批准。
3.2 施工材料准备在施工前,需要准备好所需的施工材料。
施工材料包括船板、船舶设备、管道、电气设备等。
施工材料的选择应符合相关标准和规定。
3.3 船体结构施工船体结构施工是浮船施工的核心环节,包括船体分段、焊接、打磨等工序。
在船体结构施工中,需要按照设计方案和施工图纸进行操作,确保船体结构的牢固和安全。
3.4 船舶设备安装在船体结构施工完成后,需要进行船舶设备的安装工作。
船舶设备包括通风系统、水电系统、舱室设备等。
船舶设备的安装需要按照相关规范和要求进行,确保船舶设备的正常运行。
3.5 船厂测试和调整在浮船施工完成后,需要进行船厂测试和调整工作,以确保船舶的各项性能指标满足设计要求。
船厂测试包括船舶的浮力测试、航行试验等。
在测试和调整过程中,需要记录和分析相关数据,及时调整和修正。
4. 安全措施在进行浮船施工时,需要严格遵守相关的安全措施,以确保工作人员的人身安全和施工质量。
安全措施包括: - 工作人员需要佩戴相关防护设备,如安全帽、防护服等。
- 施工现场应设置警示标志,清晰标识危险区域。
- 施工设备和工具应符合安全要求,经过合格检测。
- 施工人员需要接受相关的安全培训。
5. 施工质量控制在进行浮船施工时,需要严格控制施工质量,确保船舶的结构牢固、设备正常运行。
施工质量控制包括: - 施工过程中要定期进行检测和验收,以确保施工质量符合要求。
船体建造流程船台(船坞)总装和船舶下水

船体建造流程(6 )船台(船坞)总装和船舶下水6 船台(船坞)总装。
船舶总装主要指的是船体总装,即在船体结构经过预装配形成的分段或总段之后在船台(船坞)完成整个船体装配(也有下水之后再吊装上建的)的工艺阶段。
船台(船坞)总装也可称之为大合拢、搭载,它对保证船舶建造质量,缩短船舶建造周期有着很大的影响。
一般而言,由于军舰的设备较多,其船台(船坞)周期相比民船会长很多。
一个船厂的船台(船坞)数量是有限的,船台(船坞)周期越短,船厂造出的船就越多,因此船台(船坞)周期是表明一个船厂先进性的很重要的指标。
一个很明显的例子就是印度的国产航母蓝天卫士号,目前已经两次下水,而且第二次下水的船舶完整性还是很差,这表明船台(船坞)周期拖期太长了(否则不会给别的船腾地方),说明印度的船舶制造业距离世界先进水平还是有较大差距的。
目前日韩的船台船坞)周期较短,相对而言,我国的产品船台周期会较长一些。
船台(船坞)应具有坚实的地基,并设置靠近水域的地方,以便于船舶下水。
常见的船台(船坞)类型有:纵向倾斜船台。
纵向倾斜船台是一种船台平面与水平面呈一定角度,倾斜度通常取1/24-1/14. 纵向倾斜船台的地基由钢筋混凝土结构构成,沿船台两侧设置平行的起重机轨道,配备起重能力较大的龙门吊。
这种船台的优点是投资小;占地面积小,利用率高;维护费用低,船舶建造与下水在同一位置,建造场地比较紧凑,一般不需移船,因而不设专门的移船装置。
缺点是装配、检验不便(有斜度);起重高度要求高;劳动条件差;下水对水域宽度有一定要求。
纵向倾斜船台通常与纵向涂油、钢珠滑道结合使用。
沪东的8万吨纵向倾斜船台(沪东有拥有360米X 92米干船坞一座,配备二台700 吨龙门吊;12 万吨级和8 万吨级船台各1 座,2 万吨级船台2 座)水平船台。
水平船台就是船台基面与水平面平行的船台,地基上铺设供船台小车移动的钢轨。
水平船台可以分为室内和室外两种。
优点是装配、检验方便;下水安全;分(总)段可利用船台小车移位;能并列多个船位,可以双向使用,能下水也能上排。
船舶建造的工艺流程
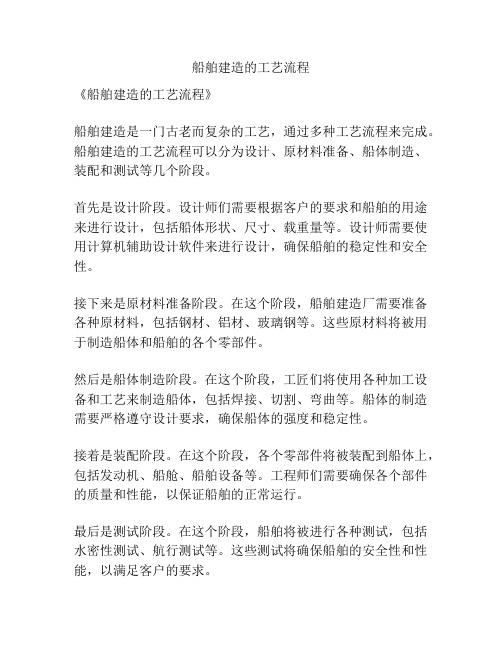
船舶建造的工艺流程
《船舶建造的工艺流程》
船舶建造是一门古老而复杂的工艺,通过多种工艺流程来完成。
船舶建造的工艺流程可以分为设计、原材料准备、船体制造、装配和测试等几个阶段。
首先是设计阶段。
设计师们需要根据客户的要求和船舶的用途来进行设计,包括船体形状、尺寸、载重量等。
设计师需要使用计算机辅助设计软件来进行设计,确保船舶的稳定性和安全性。
接下来是原材料准备阶段。
在这个阶段,船舶建造厂需要准备各种原材料,包括钢材、铝材、玻璃钢等。
这些原材料将被用于制造船体和船舶的各个零部件。
然后是船体制造阶段。
在这个阶段,工匠们将使用各种加工设备和工艺来制造船体,包括焊接、切割、弯曲等。
船体的制造需要严格遵守设计要求,确保船体的强度和稳定性。
接着是装配阶段。
在这个阶段,各个零部件将被装配到船体上,包括发动机、船舱、船舶设备等。
工程师们需要确保各个部件的质量和性能,以保证船舶的正常运行。
最后是测试阶段。
在这个阶段,船舶将被进行各种测试,包括水密性测试、航行测试等。
这些测试将确保船舶的安全性和性能,以满足客户的要求。
总之,船舶建造的工艺流程是一个复杂而精细的过程,需要设计师、工匠和工程师们的共同努力。
只有严格遵守工艺流程,才能保证船舶的质量和性能。
大型钢结构水上浮吊吊装工法

大型钢结构水上浮吊吊装工法1.前言随着工业技术的快速发展,大型的重工业厂房、超大的钢结构构件已不再鲜见。
后金融危机时代,随着经济的逐渐回暖,大型的桥梁、码头、船坞、港池等的开工建设,更给重型钢结构的水、陆吊装带来更多新的课题。
南通联合重工科技有限公司900T桥式起重机栈桥钢结构工程经过比照水上浮式起重船(包括“全回转式”及“固定拨杆式”)和普通履带吊的作业特点,通过一系列周密的技术措施,圆满完成了该工程的全部吊装工作,工程建设质量达到交通部行业规范规定的“优良”标准,在此基础上形成本工法。
2.工法特点2.1浮吊使用不同于陆域吊装机械,不能单独作业,浮吊在作业时必需伴有系列的专业船泊配套使用;2.2作业面在水域,构件从驳船上直接起吊,空中翻身、就位;2.3对比全回转式浮式起重船和固定拨杆起重船,前者能提高工效,比后者更灵活、而且能节省大量租赁台班费用。
2.4大型构件吊装时的钢丝绳以及构件本身的应力应变计算。
确保吊装工作的操作安全和吊装时构件本身的结构安全。
3.适用范围3.1大型构件的水上浮吊吊装工程:譬如横跨船坞、港池等的重型龙门吊、桥式起重机,桥梁,码头工程等。
3.2作业面在陆域的大型构件吊装在计算钢丝绳以及构件本身的应力应变时也可参考本工法。
4. 施工工艺流程及操作要点4.1施工工艺流程施工工艺流程4.2浮吊使用要点4.2.1在租赁浮吊的同时,必须同时租赁锚艇(用于给浮吊抛锚及精确定位),如吊装时间处于台风的多发季节,还得随时联系拖轮(或者是随浮吊带有拖轮),能抢在台风到来之前,第一时间把浮吊拖到指定的安全锚地;4.2.2除了解浮吊的作业工况,吊装能力外,还得充分考虑到浮吊的如下技术数据:①船长;②船宽;③满载吃水深度;④底板材质等;如下图所示,在图示的环境下展开吊装,如船宽超过作业面的宽度,则浮吊无法进入作业区域。
如采用固定拨杆式的浮吊,即使能够进入作业面,由于臂杆无法自由转动,而船身又受两侧承台限制,则根本无法作业。
- 1、下载文档前请自行甄别文档内容的完整性,平台不提供额外的编辑、内容补充、找答案等附加服务。
- 2、"仅部分预览"的文档,不可在线预览部分如存在完整性等问题,可反馈申请退款(可完整预览的文档不适用该条件!)。
- 3、如文档侵犯您的权益,请联系客服反馈,我们会尽快为您处理(人工客服工作时间:9:00-18:30)。
1总则1.1本文件为8000T浮吊船船体建造施工原则指导性工艺文件。
1.2本文依据《8000T浮吊合同—详细技术规范—[驳船部分]》的要求编写。
1.3本船入韩国船级社(KR),KRS1—起重机驳船.IWS。
1.4在船体建造中,除遵守本文件的要求外,还应同时满足KR规范要求、CSQS(2005)《中国造船质量标准》和CB/T3136—95《船体建造精度标准》、建造合同和设计图样中的有关规定和要求。
2概述本船为非自航非旋转起重驳,线型为方艏方艉,舷侧底部为圆舭,艏艉船底呈雪撬型,无梁拱,无艏艉舷弧。
艏部设有起重机支架,艉部为上层建筑,艉机舱。
本船设有部分双层底,部分平台,两侧为箱形,主结构采用纵骨架式,由横向强框架支撑,主甲板为强力甲板。
主甲板下设有7道水密横舱壁和4道前后贯穿连续纵舱壁将船体分割为多个水密舱室,压载水舱、淡水舱、饮水舱、污水舱、机舱、副机舱、锚链舱、液压泵站,燃油舱等,,详见总布置图。
上层建筑甲板室采用横骨架式结构。
2.1 主尺度总长:172.0 m垂线间长:170.0 m型宽:67.0 m型深:11.0 m满载吃水: 6.8 m2.2 甲板层高(中心线处)主甲板—A甲板 3.0 mA甲板—B甲板 3.0 mB甲板—C甲板 3.0 mC甲板—D甲板 3.0 m2.3 肋距、梁拱、脊弧肋距与纵骨间距:全船肋骨间距2500.0 m 纵骨间距0.8、0.78m梁拱:主甲板—D甲板` 0.0 m 脊弧:本船无脊弧3船体材料及技术要求3.1船体结构选用钢板、型材和铸锻件应满足KR规范要求并附有质量保证书。
3.2主船体结构的板材、零件缺陷需在CSQS(2005)标准之内,超差缺陷的修补须应满足中国船舶行业标准(CB),或经船东和KR 船级社同意。
3.3本船材料的使用应符合规格书(或有关图纸要求)。
当规格书(或有关图纸)中规定的任何一种材料无法及时获得,应征KR、船东和船厂互相同意的情况下使用适当的替代材料。
3.4本船采用普通船用KR-A及KR-AH32、KR-DH32等高强度钢和不锈钢等。
所用焊条、焊丝、焊剂及保护气体等焊接材料不仅应符合KR有关规定和经KR认可产品(并通过相应的试验验收),而且应与板材相匹配。
起重机基座及周边结构、吊耳及周边结构等高强度钢应采用低氢型高强度焊接材料,其余部分按常规船舶要求进行。
3.5钢板预处理表面预处理前,应先用溶剂或中性清洁剂擦净表面的油和油脂,如有需要应用清水洗表面,以期水溶性盐(氯化钠)残余含量达到≤50mg/m2的要求。
板厚≥6mm的钢板和型材均应进行喷丸预处理。
钢板粗糙度达到Sa2.5的标准,型材达到Sa2~2.5 标准。
如果喷丸不能实行,则可用喷砂除锈达到SIS Sa2.5标准。
处理后应立即喷一层大约15μm厚的无机硅酸锌车间底漆,底漆应适合下道漆的喷涂。
板厚<6mm不进行喷丸处理,在喷涂底漆前可喷砂处理并达到St2~ St3标准或酸洗。
3.6工艺孔及其它3.6.1在建造过程中为了方便施工人员的进出,联络和通风等的需要可以开些临时性的工艺孔,这些工艺孔需经船东的认可,完工后补焊、磨平,并不应减弱结构强度和密性要求。
3.6.2脚手架,吊耳以及它们的加强结构在不会给船舶正常作业带来不便的情况下可以根据所在位置和船东需求决定是否保留。
3.6.3所有钢材、型钢的切口必须打磨光滑,避免锐边;焊接咬口、熔渣等须进行修补、打磨,所有钢构件自由边应光滑或平滑至圆角R0.5mm。
所有开口和开孔应圆滑过渡。
4船体建造4.1建造方案与制造要求根据本船结构特点,主船体分为左、右两舷侧及中左、中右四大块,左右两舷侧呈完整箱型结构并带一部分甲板,中间二大块呈“工”字形与“T”字形,机舱区域又有内底分段(分左右两个)。
吊机机座及机座加强分在几个分段里制造。
上层建筑;横向分成左右两个,纵向按板规分,分层吊装。
4.1.1 主甲板、外板大合拢板缝设置见分段划分图。
(注:接缝处的板与结构如横梁、纵骨等为一刀切)4.1.2 余量分布分段纵向对接余量:(1)定位分段两端正作不加放余量;(2)与定位分段相连(相向)一端加放余量,另一端正作不加放.分段横向对接余量:(1)舷侧分段向船中一端加放余量;(2)中间分段向外(左、右)不加放余量;(3)两中间分段之间右舷分段向船中加放余量。
分段垂向对接余量:下面分段上口正作,上面分段下口加放余量。
上层建筑下口加放余量。
4.1.3 外板、肋板、纵桁及横梁等零件实施数控下料切割划线。
4.1.4 曲型壳板加工,采用油压机作业,水火弯板加工(高强度钢板除外)。
4.1.5 拼板边缘坡口及直线加工采用刨边或半自动切割。
4.1.6 合拢区域所有纵向构件和板材对接缝,采用CO2单面衬垫焊,坡口形式参照焊接规格表。
4.1.7分段的肋骨检验线(中间肋位或中间任取一肋位),水平检验线及中心线在分段完工应划出,并做出硬印记号。
4.1.8电焊收缩补偿量:横向每纵骨间距之间加放0.5mm,纵向不加放。
(以放样零件为准)4.1.9 船台定位以106P为基准定位分段。
4.1.10 纵骨、纵桁材在分段的两端处留200~300mm距离暂时不焊,待两分段合拢接顺后再焊。
4.1.11人孔盖在甲板、内底组件制作时装焊完毕。
4.1.12壳板应将钢板炉批号、钢号、移植记录提交船东。
4.1.13定位焊一律使用Φ3.2焊条,高强度钢板定位焊使用Φ3.2的低氢焊条进行焊接。
4.1.14定位焊全部施焊在结构面,尽量减少外壳板表面及纵横壁板光面的马脚。
4.1.15 定位焊长度一般为≥40mm,定位焊间距为250—350mm,焊脚高度不得超过正式焊缝高度。
4.1.16胎架严格按照图纸型值制作,并加放分段反变形,横向按2/1000(从中向左右加放)。
4.1.17 当结构与图纸矛盾时,应及时与技术部门联系,待处理方案确定后方可继续施工。
4.1.18 结构型线不光顺,不得贴外板,必须将结构型线调借光顺后施工。
4.1.19 分段装焊结束后必须对分段的主要尺寸,四角水平进行测量并记录报质管处复查备案,并将最终分段实际主尺度等数据提交船台合拢,同时对分段的基准肋位线,距中对合线号出,并做圆铳记号。
4.1.20 分段翻身吊耳,必须根据分段结构情况进行加强和防止分段与吊钢缆防磨措施,吊耳的安装角度应与起吊钢缆的角度一致,吊耳间距应控制在起吊钢缆夹角大于60度以上。
4.1.21 分段翻身后,四角处必须搁置坚固、要求分段水平将墩位垫实,或用钢性支撑加强牢固后报验认可、移交电焊。
4.1.22 分段吊装合拢之前,要求船体的装焊、火工矫正以及规定的涂装和预舾装工作必须全部结束,待分段验收后方可合拢。
4.1.23 船台散装零件应尽量贴装在分段内并定位焊牢。
4.1.24 上层建筑层高必须保持正公差,保证层高。
4.1.25大合拢时,船体楞木必须敲紧,防止船体下滑及下沉,以保证船体建造精度。
4.2精度管理:4.2.1基准线是放样、安装、精度控制,测量的基准,每个分段完整时必须号出:中心线、中肋位线、水线或直剖线印记。
作为船台合拢和精度控制准线。
4.2.2胎架底脚线(包括角尺线)划好后经自检互检无误后方能竖立胎架,对角线误差±1mm。
4.2.3板材仅量采用等离子切割,减小切割变形,如有变形轧平后送下道工序。
4.2.4分段焊接后,需经过甲板水平度测量,首、尾、中肋位、左、中、右、(共9处)水平误差±4mm。
如超差经过火工校平直至达到标准为止。
测量数据在中合拢时送船东认可。
4.2.5定位分段船台定位:定位分段基准线以内底板下平面为准,包括标杆上的测量线。
定位分段中心线误差<1mm,中肋位误差±1mm,底板前后挠曲误差±2mm。
左右四角水平度±4mm,用拉条将分段左右前后与船台用钢性撑固定。
4.2.6内底分段对接合拢:首先要测量已定位分段的水平度情况来决定分段前后的高度。
长度以中肋位为准量取。
待分段装焊基本结束,重新测量内底平整度,测量数据交质管部门,同时按船台中心线重新开出(内底板上)船体中心线及中肋位线号圆铳标记。
竖标杆标出各大接头水线,作为舷侧分段的定位基准线。
4.2.7其它分段以内底分段为基准搭载建造。
当主甲板长度接到全船长度的>60%时方可修改船体中心线,以便后续分段的吊装。
4.2.8全船余量分布及搭载顺序见分段划分图。
4.2.9 主要尺度建造公差总长± 170mm型宽± 67mm型深± 10mm基线挠度± 25mm横向上翘下垂± 30mm4.2.10 船台装配偏差舱壁垂直度≤ 10mm分段接缝处肋距± 10mm中心偏差≤ 5mm四角水平± 8mm定位高度(主船体)± 5mm定位高度(上建)± 10mm4.3焊接工艺4.3.1焊工必须持有船级社考核认同的等级资格证书方可进行相关的焊接作业,而且至少有六月以上从事相关工作的经验。
4.3.2所选用的焊接材料应符合KR《材料与焊接规范》篇中的有关规定。
4.3.3本船采用的对接逢、角焊逢等焊接方法、坡口形式、根部间隙应按KR认可的“船体焊接基本规程”的规定进行。
4.3.4船体结构角焊缝的焊脚尺寸按KR认可的JH957-190-01《焊接规格表》执行。
4.3.5凡能用高效焊接的焊缝应尽可能采用自动焊、CO2气体保护焊等高效焊接方法。
4.3.6垂直对接缝采用CO2手工焊,单面施焊双面成型,施焊面有缺陷,则另一面要碳刨清根全焊透。
4.3.7大合拢分段外板的剖口开在外板外表面(非构件面),底部、转圆舭部处的剖口开在外板内表面(构件面),应两种不同剖口交汇处不能施焊,故要求转圆舭部上口留200mm不开剖口,外板下口留200mm暂时不施焊,待两分段拉拢焊缝接顺并上下焊好后再按外板剖口形式开出此剖口、磨光、焊接。
4.3.8在胎架上制造的立体分段,铺板的对接缝尽量采用手工CO2焊和自动焊,外表面翻身碳刨清根、封底焊。
4.3.9雨、雾天不得在室外进行焊接工作,除非有一定的防雨设施和烘干措施。
4.3.10所有焊接材料必须经过烘干处理,低氢焊条焊接一律使用保温桶保温。
CO2气体保护焊时必须设置防风措施,焊前坡口及打磨清洁工作需经报验认可。
控制焊脚尺寸,不宜过大或(7)手工焊、CO2焊坡口清洁工作;(8)分段完工主尺度数据测量,作好记录并将数据提交船台合拢,做好基准线、检验线圆铳印记;(9)分段焊接前应将分段搁置水平状态并报验合格;(10)分段完工前必须根据图纸要求仔细检查完整性;(11)贯穿孔、通焊孔、透气孔、流水孔等要有良好的包角焊。
5下料和加工5.1下料5.1.1下料前应严格检查钢材的钢号、炉号、批号,并作好标识和移植,以便必要时进行追溯原始质量数据。