(完整版)飞机制造工艺基础2
(完整版)飞机制造工艺基础3
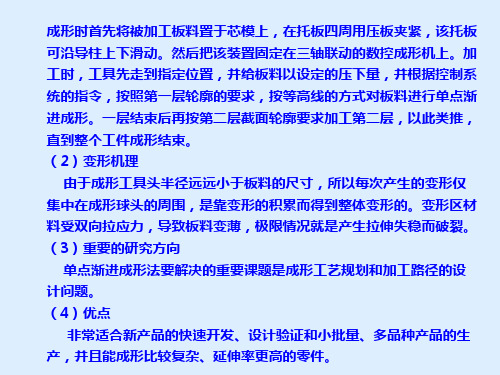
一.整体壁板毛坯 主要为铝合金,另有钛合金、镁合金。整体壁板毛坯的主要制造方法: 热摸锻、挤压、自由锻板坯、热轧平板毛坯和特种铸造。
1.大吨位液压机和锻模生产壁板毛坯 优点:生产率高、锻件纤维组织连续,晶粒致密,强度高,可制造复杂 形状筋肋和对接接头。
热模锻毛坯接近于成品尺寸,厚度和桁 条间距误差小于0.6mm,锻造斜度小锻需要吨位极大的机床,铝合金壁 板每平方米投影面积约需3万吨压力, 精锻时要5~6万吨。且锻模制造困难、 周期长、劳动量大。如某飞机整体壁板 的锻模重量达50~60吨。 这些问题限制了热模锻方法的广泛应用。
Most authors used in their experimental study on incremental forming regular 3 axis milling machine. Figure 7 presents the incremental forming process.
characteristics of the incremental forming process are pointed out:
- the sheet is formed according to a given locus - the deformation of the sheet is point-by-point - the deformation of every step is small.
Figure 8 The control system of Dieless NC Forming machine.
Figure 9 Equipment for Dieless NC Forming process
The blank sheet is attached to a blank holder. The blank holder moves in vertical direction according to descending of Ztool and along X- and Y-planes.
飞机制造技术基础

传统飞机结构研制过程(模拟量传递):样件,模具 数字量传递飞机结构研制过程:三维数模 钣金件数字化制造过程:以橡皮囊液压成形为例 弯边角度线定义方法:弯边角度线 工艺耳片:1、钣金件在成形过程中定位;
2、钣金件在切边过程中定位; 3、钣金件在装配过程中定位 工艺耳片的表示方法:1、用点和轴线(法矢)表示;
2,用点、轴线(法矢) 、孔轮廓和耳片轮廓表示; 3、用实体和轴线表示
航空产品数控加工的特点:(1)产品类型复杂,具有小批量、多样化特点 (2)结构趋于复杂化和整体化,工艺难度大,过程复杂; (3)薄壁化、大型化特点突出,变形控制极为关键; (4)材料去除量大,切削加工效率问题突出 (5)质量控制要求高 (6)产品材料多样 (7)大型结构件毛料价值高,质量风险大
2、降低造型材料的发气量;严格控制铸型中的水分,清除冷铁、型芯撑表面的锈蚀、油污, 并保持干燥等。
3、增加铸型的排气能力;控制型砂的干湿程度和紧实度,降低浇注速度等。
第二节 铸造的类型和概念 离心铸造,陶瓷模铸造,压铸,熔模铸造: 熔模铸造的特性:
尺寸精度高;表面粗糙度小;可浇 注形状复杂的薄壁铸件,铸型预热后浇注冷却速度 慢 ,铸件的力学性能较低。最适于铸造几克到十几千克;型壳用耐高温材料制成,故能适用于 各种铸造合金,特别是形状复杂的高熔点合金和难机械加工合金。熔模铸造的铸型属一次性铸 型。 失模铸造 近净成型铸造是指把金属铸造成非常接近最终成形件的形状,铸造出的工件只需少量的机加工, 由此它被称作近净成型 硬模铸造,石膏模铸造,壳型铸造,砂模铸造
第五节 铸造在航空航天中的应用
铸造在航空航天工业中的应用特点 1、铸造材料以轻质铝合金、高温钛合金等为主。钛合金精密铸造方向上,以熔模精密铸造和石 墨型铸造为主。 2、铸造成形采用当前最先进的技术完成精密铸造 3、铸造基本属于近净成型铸造
飞机制造工艺导论
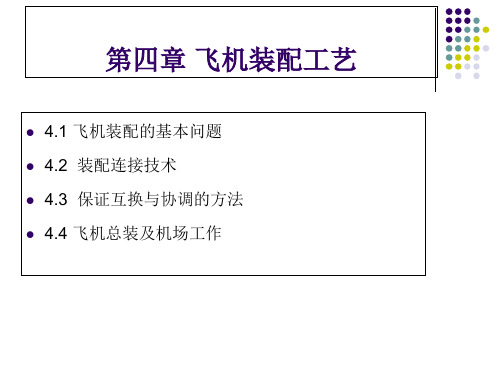
部件或段件可分为板件。板件是由部件或段件的一部分 蒙皮以及内部纵向、横向骨架元件(如长桁、翼肋或隔框的 一部分)所组成,有时还包括安装在其上的导管、电缆及设 备。如机翼中段的上下板件(壁板),机身的上下左右板件。
(1)、工艺性审查;
(2)、取决于综合的技术经济分析结果。即工艺分离面划分的原则 (装配原则)
3、工艺分离面划分的原则(装配原则)
分散装配原则:
一个部件的装配工作在较多的工作地点和工艺装备 上进行。
(1)、增加平行工作地、装配分散进行、扩大工作面、
特点
(2)、结构开敞可达性好,改善劳动条件
(3)、有利于机械化和自动化,提高劳动生产率,缩短
部件装配周期,提高装配质量。
成批生产阶段
集中装配原则:
少数工作地点、少量工艺装备。
(1)、装配工艺装备较少,减少了工艺装备的制造费用
特点
(2)、协调关系较简单,
(3)、生产准备周期较短
研制、试制生产阶段
4.1.2 装配准确度
一、飞机装配准确度要求 二、制造准确度和协调准确度的基本概念 三、提高装配准确度的补偿方法
一、飞机装配准确度要求
装配准确度
装配后飞机机体及部件的几何形状、尺寸等实际数 值与设计所规定的理论数值的误差。对于不同类型的飞 机和飞机上不同的部位,装配准确度的要求不同。
飞机的空气动力性能 飞机的操纵性能
部件气动力外形准确度 部件内部组合件和零件的位置准确度
部件间相对位置的准确度
1、部件气动力外形准确度
第四章 飞机装配工艺
4.1 飞机装配的基本问题 4.2 装配连接技术 4.3 保证互换与协调的方法 4.4 飞机总装及机场工作
飞机研制过程与制造技术

02 在浅筋条小曲率壁板的研制生产中,
采用先进的喷丸成形技术。波音的数 控喷丸系统,不仅可控制成形参数, 而且可预测和控制喷丸强化与抛光工 序对壁板外形的影响,并研发了叶轮 式数控抛丸设备。
03 在高筋网格式整体壁板研制生产中,
开发压弯与喷丸复合成形技术,发展
了带自适应系统的数控压弯机。
04 在成形设备方面,除扩大规格外,弯
A
在总体设计基础上,进行飞 机各部件结构的初步设计(或 称结构打样设计);
B
对全机结构进行强度计算;
C
完成零构件的详细设计和细 节设计,完成结构的全部零 构件图纸和部件、组件安装 图。
一 航空器研制过程
3.飞机制造过程
试制
飞机制造工厂根据 飞机设计单位提供 的设计图纸和技术 资料进行试制。
装设备、发动机
在传统制造技术基础上发展起来的先进制造技术已成为支撑现代制造业的 骨架和核心,以信息化带动传统制造业,企业信息化工程得到长足发展。
二 航空器制造技术特点
飞机装配是整个飞机制造过程的龙头,飞机装配技术是中 国飞机制造过程中最薄弱的环节,这项复杂的系统工程, 涉及飞机设计、工艺计划、零件生产、部件装配和全机对 接总装的全部过程,有4个关键技术:简易型架装配技术、 自动化铆接技术、先进定位装配技术和装配过程的数字化 仿真技术。
01
为选择满意的外形须做 大量的风洞试验;
02
对用新材料(如复合材 料)制作的结构性能进 行某些专题研究和试验 ;
03
对某些关键的结构件或 结构设计方案进行必要 的疲劳或损伤容限的设 计研制试验,为详细设 计提供数据或进行早期 验证等。
04
二 航空器制造技术特点
航空器制造涉及多个学科,包括空气动力学、材料学、航 空电子学等;飞机整体结构制造技术有:高效数控加工、 大型壁板的形成技术和大型壁板精确加工技术。集成的整 体结构、复材构件和数字化技术,构筑了新一代飞机先进 制造技术的主体框架。
飞机装配工艺课件-2

三种尺寸传递原则的应用 • 形状复杂的零件采用相互联系制造原则。在制
造过程中,将那些技术难度大、制造准确度不
可能达到很高的环节,作为尺寸传递的公共环
节,这样就能显著地提高零件之间的协调准确
度。由于飞机构造上的特点,采用这种原则保
证协调具有特别重要的现实意义。而独立制造
原则仅适用于那些形状比较简单的零件,如起
次反复移形过程。在制订产品的装配和协调
方案时,要注意选择合理的、能保证各类工
艺装备协调的尺寸传递体系(协调路线)。
工艺装备的协调路线是:根据所采用的尺
寸传递体系说明,由产品图纸通过实物模拟量
(模线、样板、标准工艺装备)或数字信息
(产品几何数学模型),将机体上某一配合或 对接部位中一个或一组协调的尺寸和形状,传 递到有关工艺装备上去的传递环节、传递关系 和传递流程图。
模线样 板-标 准样件 协调系 统
~~适于 成批生产 小型飞机
10
模线样板-局部标准样件协调系统~~广泛应用
以飞机外形的数学模型为基础的协调系统 --数字量传递体系
建立飞机外形、内部结构的几何模型 数控绘图机
几何数据库
理论模线 结构模线 飞机生产图纸
工艺装备、整体结构件的数控加工、数控测量
协调要求。
互换性的分类
使用互换性
按性质分类
分 类 按互换部位
生产互换性 外部互换性 内部互பைடு நூலகம்性 完全互换
按互换级别
不完全互换 (替换)
使用互换性:为了保证飞机的正常使用,对
在使用中可能损坏的机体部件、组合件(如机
翼、尾翼、活动面、各种舱门、口盖)或成品 件(如发动机、特种设备、仪表、油箱等), 要求具有不经挑选和补充加工就能更换,并在 更换后不影响飞机使用性能的要求。
飞机制造的技术和工艺

飞机制造的技术和工艺随着科技的不断进步,飞机的制造技术和工艺也在不断变化和提升。
从最早的飞机制造到现代高科技飞机制造,专业人员在技术方面做出了令人瞩目的进步和贡献。
一、制造流程飞机制造是一项极其复杂的工作。
其制造流程包括设计、制造、装配和测试这几个环节。
其中,设计过程是非常重要的环节,设计师必须能够将飞机的设计理念、材料和性能相结合,才能保证飞机的飞行安全和性能达成预期效果。
制造飞机的主要材料包括金属材料、复合材料等。
与传统的金属材料相比,复合材料具有高强度、高刚度、轻重量等特点,能够有效地减轻飞机的重量。
随着复合材料的广泛应用,使得飞机的性能得到大大提高。
装配是飞机制造过程中的关键环节。
由于飞机部件的要求比较高,装配前必须要进行多次精细的加工和检验。
其中,金属件通常采用机加工和冷成形等方式加工,而复合材料则采用顶尖技术加工和成型,以保证飞机的性能。
测试环节也是飞机制造中最重要的环节之一。
测试过程中,必须进行全面的性能检测,包括飞机静态测试、飞行测试、负载测试等。
测试结果将直接影响到飞机的飞行性能和安全性。
二、新技术随着科技的不断进步,飞机制造的新技术也在不断涌现。
例如,3D打印技术、机器学习技术、大数据处理技术等,这些新技术的应用将大大提高飞机制造的效率和质量。
3D打印技术可以将数字模型直接转化为实体零件,使得飞机零部件的制造更加精确和快速。
机器学习技术可以通过对飞机数据进行分析,提高飞机的使用寿命和性能。
大数据处理技术可以直接对飞机数据进行监控和分析,提高飞机的运行效率和安全性。
三、展望未来的飞机制造将更加注重智能化、无人化和可持续性,这也是飞机制造技术和工艺发展的方向和目标。
未来的飞机将具备更高的自动化和智能化水平,具有更强的飞行能力和安全性。
同时,未来飞机制造将更加注重生态环保和可持续性。
随着社会对环境保护意识的日益加强,飞机制造将更加注重环保和节能,减少对环境造成的负面影响。
总之,飞机制造的技术和工艺是一个不断进步的过程,随着技术的发展和进步,未来的飞机将变得更加智能、高效和环保。
飞机工艺学

【飞机制造过程】:工艺准备、毛坯的制备、零件加工、飞机装配和总装、试验和试飞【飞机产品特点】:1、零件数量大、品种多2、选用的材料多3、外形复杂、精度要求高4、外形尺寸大,刚度小5、结构不断改进、产量变化范围大【飞机制造工艺的特点】:1、必须采用特殊的保证互换协调的方法2、生产准备量大、生产准备周期长3、装配工作量大,装配周期长4、生产方法要有较大机动性5、协作生产6、要不断引进各种新材料、新工艺【互换性】:独立制造的零件(组合件、部件)装配时不需要补充加工就能满足使用要求【协调性】:两个或两个以上相装配的零件(组合件、部件),其装配部位几何形状和尺寸相符合的程度。
【互换性要求】:除几何尺寸和形状互换之外,还包括1、气动外形2、对接分离面3、强度互换4、重心互换【制造准确度】:产品实际尺寸与设计尺寸相符合的程度【协调准确度】:两个相互配合的零件(组合件、部件)相互配合部位尺寸相符合的程度重在提高协调准确度【飞机生产协调原则】联系系数k=2m\(n1+n2) m为尺寸传递种公共环节数n1、n2 各个零件尺寸传递中各自环节数1、独立制造原则,m=1,k最小(保证互换性,工作面大,尺寸精度要求高,适合刚度大的零件)2、相互联系原则,m=n1或m=n2,k趋于1(有一定公共环节,需各种工艺装备,成本高,准备周期长,但使用广泛)3、相互修配原则,k处于0与1 之间(协调准确度最高,仅一个非公共环节,工作分散性最差,不具有互换性)【硬铝合金LY12、超硬铝LC4】钣金零件制造的基本原理:体积不变。
屈服极限以上“收”--收缩变形,板料纤维缩短,厚度增加;“放”--拉伸变形,板料纤维伸长,厚度减少。
【铝合金、镁合金、合金钢、钛合金】【热处理】:退火是将工件加热到适当温度,根据材料和工件尺寸采用不同的保温时间,然后进行缓慢冷却,目的是使金属内部组织达到或接近平衡状态,获得良好的工艺性能和使用性能,或者为进一步淬火作组织准备。
(完整版)飞机制造工艺基础4
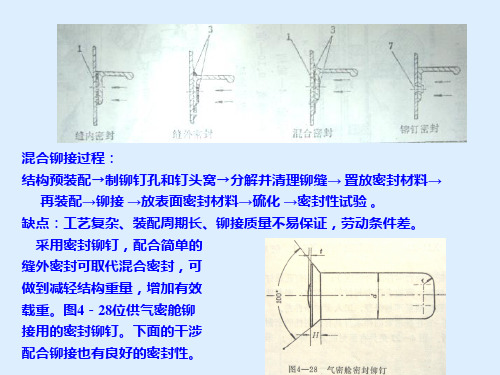
※用等距样板配合检验量规进行: 图4-88,将样板按基准面(前、后梁)固定在部件受检验剖面上,
然后再用千分垫测量贴合程度。对接接头尺寸是用量规和检验销检查 (见图4-89)。 缺点:操作麻烦。
较完善的方法:用检验型架,构造与装配型架大致相同,但检验型架刚度 要更大,其卡板按部件的理论外形放大一个等距间隙,图4-90.测量准 确度可达±0.2毫米。
混合铆接过程: 结构预装配→制铆钉孔和钉头窝→分解并清理铆缝→ 置放密封材料→
再装配→铆接 →放表面密封材料→硫化 →密封性试验 。 缺点:工艺复杂、装配周期长、铆接质量不易保证,劳动条件差。
采用密封铆钉,配合简单的 缝外密封可取代混合密封,可 做到减轻结构重量,增加有效 载重。图4-28位供气密舱铆 接用的密封铆钉。下面的干涉 配合铆接也有良好的密封性。
总装是桨叶前段和后段件的装配。工件装配和固化都在夹具中进 行,用机械加压方法保证大梁和后段件胶粘面与弦平面垂直。
上述装配工作完成后,还要对翼尖、调整片等做架外安装和铆接, 并对表面作密封,测量扭角等。 (5)桨叶称重和平衡
旋翼各桨叶应是静平衡的,它是动平衡的必要条件。所以制造过程中一定 作好重量控制。
飞机水平测量原理: 在部件表面规定的位置,按照型架
中的专用装置标出点的记号,这些点为 水平测量点,实际上是将飞机理论轴线 转换到部件外表面,作为测量基准。测 量时,只要检查这些点相互位置的数据, 就可以确定部件相对位置的几何参数是 否符合技术条件。图4-92中,1-10各测 量点都在部件装配时定出,用水平仪将 1、2和1‘调到同一水平面内,再用经纬 仪把7、8调到一个垂直面内,然后用水 平仪、经纬仪分别测3 、 4 、 9 、 10 就可判断机身各段的同轴度、机翼安装 角、下反角等。
(完整版)飞机制造工艺基础1
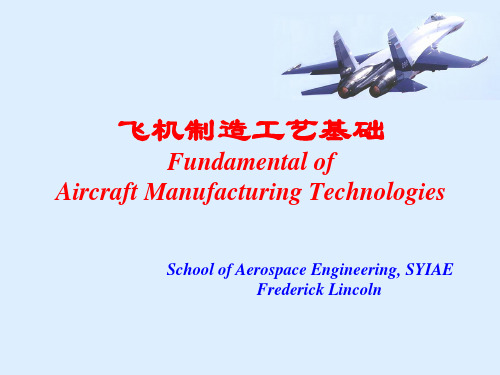
一般互换零(构、部)件的特性是:能与另外一个同样零(构、部) 件互相代替,完成一样准确的特定任务。互换性是产品相互配合部分的结 构属性,它指同名零、组、部件在几何尺寸、形位参数和物理、机械性能 各方面都能相互取代而具有的一致性。
二.互换性的分类
•按性质分类
•按互换部位
分类
•按互换级别 •按制造分工
无论是采用一般及其制造中的公差配合制度,还是采用模线样板方 法作为飞机制造中保证互换性的方法,产品互换性的基础都是保证制造 准确度与协调准确度。
•保证协调准确度的基本方法
显然,要使两个相互配合的零
件的同名尺寸相互协调,它们的 尺寸传递过程之间就必然存在一 定的联系。
如图所示,零件A和零件B是要 相互协调的。假定LA和LB是协调 尺寸,则它们的形成经过了许多 次尺寸传递,其中有的是两个尺 寸公共的环节,有的尺寸是两个 尺寸各自的环节,后者将产生两 个尺寸的协调误差ΔAB。
•若n1=n2=1,K值最大,相当于修配原则制造,协调性最佳。
原则:
要想提高协调准确度,除了努力提高零件制造准确度之外,减少制
造环节或增加两个零件尺寸传递过程中的公共环节以缩短尺寸的协调过
程都是非常必要的。
有三种不同的原则取得尺寸协调的过程: (a)协调过程称零件按独立制造的原则形成的协调过程; (b)按相互联系制造原则形成的协调过程; (c)按补偿原则制造所形成的协调过程。 3.1按独立制造原则进行协调
•使用互换性 •生产互换性
•外部互换性 •内部互换性
•完全互换 •不完全互换
(替换)
•厂内互换 •厂际互换 •国际互换
1.使用互换性: 为了保证飞机的正常使用,对在使用中可能损坏的机体部件、组合件
飞机结构件制造工艺2讲课文档
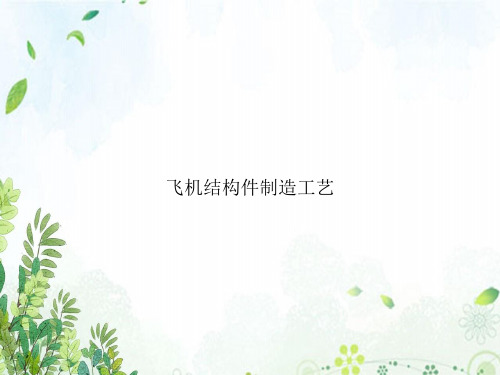
轰六整体壁板在飞机上的位置
ARJ21飞机机翼下中壁板零件
ARJ21飞机机翼下中壁板零件。壁板由21个口框 、口框加强区、肋加强 区、长桁加强区、双向削斜变厚度蒙皮等构成,各加强区形成纵横交错的 网状结构,加强区厚度和口框面积占整个壁板面积的46%,壁板最厚处达 11.8mm,而最薄处仅2mm。
架一批,每批的制造工时达10万小时,制造周期需10~12个月。
整体壁板 壁板的外形尺寸大,壁板变厚度、非等
截面,成型后底面壁薄、筋条高、结构网 络化,加工完成后材料去除率大,易发生 变形。
梁、框、肋零件的腹板、筋和外形缘条最小厚度仅有1~2mm,不易装夹, 铣切加工时,零件易振动,如是锻件毛坯,加工后变形量大,若加工的工步和 切削参数选用不当,板面的翘曲可达几十mm。
整体壁板的切削加工
数控加工变形的控制 产生原因
毛坯 =〉成形、热处理 ==〉残余应力 数控加工
表层被切削掉时,其残留内应力平衡状态被破坏
从夹具上卸下 ==〉残余应力释放 工件往往会产生很大的翘曲变形
整体壁板的切削加工
解决方法:
毛坯 ==〉减少残余应力 ==〉预拉伸板。选用经预拉伸 (预压缩、以及锤打处理)的铝合金厚板作壁板的材料。 在固溶热处理以后进行拉伸(约2%~4%)。 工艺方法上:采用正反面多次反复加工的工艺方法进行壁 板大平面的加工;先进行粗加工并留出较小余量(然后可 以进行热处理并矫正变形),再进行精加工,这时由于切 削余量已经很小即可以达到减少变形的目的;铣切筋条时, 采用自外向内对称加工的方法,可减少加工变形。 工艺参数上,选取合理的进给速度和切削深度。 矫形:压力机、喷丸、滚弯等对变形反方向加力矫正
化学铣切的机理是晶界和 晶粒的溶解――化学切削。 它的加工质量取决于前道 机械加工的表面质量和形 状。
飞机制作知识点总结

飞机制作知识点总结飞机是人类工程技术的杰作,它的制造需要各种专业知识和技能。
飞机制作是一项复杂的工程,它需要大量的机械设计、材料科学、航空航天工程、电子技术等各个领域的知识。
飞机的制造包括机身、机翼、发动机、座舱、起落架等各个部分,每个部分都是由专门设计和制造的。
在飞机制造过程中,需要通过CAD绘图、结构分析、模拟实验等技术手段来完成飞机的设计和验证。
以下是飞机制作的一些知识点总结:1.飞机结构设计飞机的结构设计是飞机制造的重要部分,它关乎着飞机的安全和性能。
飞机的结构设计主要包括机身设计、机翼设计、尾翼设计等。
在飞机结构设计中,需要考虑飞机的强度、刚度、稳定性、重量等因素,并且需要满足飞行的要求。
2.飞机材料飞机的材料一般是由金属材料、复合材料、塑料等多种材料组合而成。
在飞机制造中,需要选择合适的材料来保证飞机的性能和安全。
飞机制造中通常使用的材料有铝合金、钛合金、碳纤维复合材料等。
3.飞机动力系统飞机的动力系统是飞机制造的另一个重要部分,它包括发动机、螺旋桨、燃料系统等。
飞机的动力系统需要满足飞机的推力、燃料消耗、重量等要求,并且需要具有高可靠性和高效率。
4.飞机航电系统飞机的航电系统是飞机制造中的另一个重要部分,它包括飞机的导航系统、通信系统、飞行控制系统等。
飞机航电系统需要满足飞行的安全和精准性要求,并且需要具有稳定性和高可靠性。
5.飞机制造工艺飞机的制造工艺是飞机制造的重要环节,它包括零部件的制造、组装、调试等各个环节。
在飞机制造工艺中,需要使用各种机械设备、焊接、切割、铆接等工艺手段来完成飞机的制造。
同时也需要严格控制工艺参数,以保证飞机的质量和性能。
飞机的制作是一个综合性的工程,它需要各个专业领域的知识和技能。
飞机制作的知识点总结中,包括了飞机的结构设计、材料、动力系统、航电系统及制造工艺等各个方面,这些知识点是飞机制造的基础和关键。
只有系统掌握这些知识点,才能保证飞机的制造质量和飞行性能。
飞机如何制作?

飞机如何制作?
飞机的制造是一个高度复杂而精密的过程,涉及多个学科领域,包括航空工程、材料科学、机械工程等。
以
下是通常的飞机制造过程的基本步骤:
设计:飞机的制造过程始于设计阶段。
航空工程师和设计师使用计算机辅助设计(CAD)软件,制定飞机的
外形、结构、机翼形状、动力系统等各个方面。
材料选择:根据设计要求,选择合适的材料,包括
轻量且高强度的金属合金、复合材料、塑料等。
制造结构:利用机械加工、焊接、精密铸造等工艺
制造飞机的各个结构部分,包括机翼、机身、尾翼等。
动力系统:安装和调试发动机及相关的动力系统。
这可能包括涡轮喷气发动机、螺旋桨引擎或其他推进系统。
电气系统:安装电气系统,包括飞机的仪表、导航
系统、通信设备等。
组装:将所有制造好的部件组装到一起。
这通常包
括对飞机结构的焊接、螺栓连接等工作。
测试:在飞机首次组装完成后,进行多个层面的测试,包括地面测试、发动机启动测试、滑行测试等。
飞行测试:飞机完成地面测试后,进行首次飞行测试。
这是确保飞机性能和安全性的关键步骤。
认证:飞机制造商需要取得适航认证,这是由相关
的航空管理机构进行的,以确保飞机符合安全和性能标准。
生产:一旦飞机通过测试并获得适航认证,制造商
可以进行批量生产,生产多架相同或类似型号的飞机。
整个过程需要高度专业化的团队,包括工程师、设计师、技术人员和飞行测试员。
这也是一个周期较长、资
金密集、技术要求极高的制造过程。
飞机的零件制造工艺

飞机的零件制造工艺飞机的零件制造工艺是指将设计好的零件图纸通过一系列的工艺流程和加工工艺,将原材料加工成具有设计要求的零件的过程。
随着飞机工艺的发展和进步,飞机零件的制造工艺也在不断改进和创新。
飞机的零件制造工艺主要包括以下几个方面:1. 零件的设计与工艺规划:在零件的设计阶段,需要考虑到零件的材料、结构、形状等因素,制定出相应的工艺规划和工艺流程。
这一阶段的目标是确定最佳的加工方式和工艺参数,确保零件具有良好的质量和性能。
2. 材料的选择与准备:在零件制造之前,需要选择合适的材料,并进行相应的材料准备工作。
材料的选择要考虑到零件的设计要求、质量要求和使用环境等因素,以确保零件具有足够的强度和耐用性。
3. 加工工艺的选择与优化:根据零件的形状和材料特性,选择合适的加工工艺进行加工。
飞机零件加工的常见方法包括铣削、车削、钻削、锻造、拉伸等。
同时,还需要优化加工工艺参数,如切削速度、进给量和切削深度等,以提高零件的加工效率和质量。
4. 检验与调整:在零件加工过程中,需要进行不同的检验控制来确保零件的质量。
常见的检验方法包括外观检查、尺寸检测、力学性能测试等。
如果发现零件不合格,需要及时调整加工工艺和参数,进行二次加工或修正,以确保零件满足设计要求。
5. 表面处理与防腐蚀:在零件制造完成后,需要对零件进行表面处理和防腐蚀措施,以提高零件的耐腐蚀性和外观质量。
常见的表面处理方法包括喷涂、阳极氧化、电镀等,防腐蚀措施包括防锈涂层、防腐蚀涂层等。
6. 组装与测试:对于复杂的飞机零件,需要进行组装和测试。
组装阶段需要根据零件图纸进行精确的组装,确保各个部件的焊接、螺栓连接等都符合要求。
测试阶段需要进行功能测试、负载测试、密封测试等,以确保组装的飞机零件在使用过程中能够正常工作。
总之,飞机的零件制造工艺是一个复杂而关键的过程,要求制造人员具备丰富的专业知识和技术能力。
通过不断的工艺改进和创新,可以提高零件的加工精度和质量,提高飞机整体性能和安全性。
飞机结构及加工工艺全

A380、B7771机体结构机头系统组成包含零件图片备注鼻锥?Radome雷达罩雷击保护条(lightning strikeprotectionstrips黄色为雷击保护条,材料铜Cockpit驾驶员座舱驾驶员座舱结构图Noselandinggear bay前起落架舱下部有电子舱和前轮舱,包括电子舱的接近门等开口和对前轮舱的各种支撑./可以看到飞机的顶升点。
装在FR8上.FWDpressurebulkhead前压力隔框前压力隔框FR1,厚度为1.6mm,可以看到前部有水平的加强筋.在隔框有垂直的加强筋.为防鸟击在压力隔框前装有6mm厚的AFRP芳纶纤维蜂窝复合材料机身弯曲链接部位1.客舱压力;2.鸟击;3.着陆时的冲击;4.碰撞时的冲击和快速卸压;5.空气动力;6.飞机顶撑;7.机身的抗弯曲能力。
图片起落架机翼:2×4刹车装置、承力支柱、减震器(常用承力支柱作为减震器外筒)、收放机构、前轮减摆器和转弯操纵机构等。
sooopsl 的高压液压源机身:2×6机头:1×22动力系统发动机核心机左栏第一张图片是安装发动机的装置;第二张图片是发动机;涡轮组件附件及齿轮箱其它燃油系统(航空汽油用于活塞发动机;航空煤油用于燃气涡轮发动机.)飞机燃油系统飞机的燃油系统由油箱、供油系统、通气系统、加油放油系统和指示系统组成。
第一张为飞机结构燃油箱;第二张图片为飞机系统供油图.辅助动力装置(APU )其作用是向飞机独立地提供电力和压缩空气,也有少量的APU 可以向飞机提供附加推力。
(A320)动力部分:单级钛合金压缩比为6:l 的离心压气机,环形回流燃烧室,单级径向内流式涡轮。
下图所示为APU 动力装置在尾椎上的排气口,进气口则在垂直尾翼上。
(A380)(A320)附加齿轮箱:附件齿轮箱安装在离心压气机外包的末端并由动力部分驱动。
它由驱动垫来驱动:一个AC 发电机,二个起动机马达,一个发电机滑油回油泵,一个燃油控制和润滑泵,一个冷却风扇。
机型制造基础知识培训内容

机型制造基础知识培训内容一、引言飞机制造是航空工业的核心,它涉及到设计、材料选择、制造工艺、组装和测试等多个环节。
本培训旨在为参与者提供飞机制造的基础知识,以确保他们能够理解并参与到飞机制造的各个阶段。
二、飞机设计原理- 2.1 设计理念:介绍飞机设计的基本原则,包括性能要求、安全性、经济性和环保性。
- 2.2 空气动力学基础:讲解飞机的升力、阻力、推力和稳定性等基本概念。
- 2.3 结构设计:阐述飞机结构设计的要点,包括翼型、机身、尾翼等部件的设计。
三、材料科学- 3.1 材料分类:介绍飞机制造中常用的材料,如铝合金、钛合金、复合材料等。
- 3.2 材料特性:分析不同材料的物理、化学和机械特性,以及它们在飞机制造中的应用。
- 3.3 材料选择:讨论在特定飞机部件制造中材料选择的依据和标准。
四、制造工艺- 4.1 传统制造技术:介绍锻造、铸造、焊接等传统制造工艺。
- 4.2 高级制造技术:讲解数控加工、3D打印、激光切割等现代制造技术。
- 4.3 制造流程:阐述飞机部件从原材料到成品的整个制造流程。
五、飞机组装技术- 5.1 组装流程:介绍飞机组装的基本步骤,包括部件的定位、连接和调整。
- 5.2 组装工具与设备:讲解飞机组装过程中使用的专用工具和设备。
- 5.3 质量控制:强调组装过程中的质量控制要点,确保飞机的安全性和可靠性。
六、飞机测试与验证- 6.1 地面测试:介绍飞机在地面进行的测试,如静态测试、动态测试等。
- 6.2 飞行测试:讲解飞机在实际飞行中的测试项目和方法。
- 6.3 测试数据分析:分析测试数据,确保飞机性能符合设计要求。
七、飞机制造的未来趋势- 7.1 技术创新:探讨航空工业中的新技术,如电动飞机、无人驾驶飞机等。
- 7.2 制造自动化:分析自动化技术在飞机制造中的应用和影响。
- 7.3 可持续发展:讨论飞机制造过程中的环保问题和可持续发展策略。
八、结语通过本次培训,参与者应能够对飞机制造的基础知识有一个全面的了解。
- 1、下载文档前请自行甄别文档内容的完整性,平台不提供额外的编辑、内容补充、找答案等附加服务。
- 2、"仅部分预览"的文档,不可在线预览部分如存在完整性等问题,可反馈申请退款(可完整预览的文档不适用该条件!)。
- 3、如文档侵犯您的权益,请联系客服反馈,我们会尽快为您处理(人工客服工作时间:9:00-18:30)。
第六节 飞机蒙皮零件的制造-滚弯和拉形 一.概述 蒙皮是保证飞机气动外形的主要零件,因此它的表面光滑度和外形准
确度直接影响飞机的性能。 尤其是随着飞机蒙皮的加厚,高速飞机部件的装配多以蒙皮为基准,
如图2-63的冲裁。
直线弯边零件是橡皮成形中最简单的一种情况,受力状态见 图2-64。此时只发生弯曲变形,只要圆角半径不太小,就不存在成
形困难。
当橡皮压力不足出现弯边不贴模时,可以适当地增大工艺余量或手 工进行校正。
凹曲线弯边零件见图2-67所示,有封闭和不封闭两种,其成形极限问 题是弯边部分边缘材料受拉伸而过度变薄或开裂。
差一般规定为
,对钛合金为
。
除了普通旋压外,还有一类称为变薄旋压(剪切旋压)。
特点:零件壁厚相对于毛料的原始厚度变薄程度较大,毛料的形状在成
形过程中始终保持不变,即周边不发生收缩或延伸,面积的增加完全靠
毛料的变薄实现。
剪切旋压是在功率高、刚度大的专用机床上,用靠模控制滚轴,按一定
轨迹强力滚挤毛料,从而产生塑性流动取得与芯模一致的形状。
胀形的优点: 工艺过程简单、成本低、表面光滑,可以很容易地成形出凸肚零件。 胀形所用毛坯主要是由板料滚弯焊接而成,或采用有底的拉伸件。
另外还有爆炸胀形:如图2-55 胀形中最大变形区材料的延伸率 从图2-56中可见:
为胀形系数,用来衡量胀形零件的 变形程度。
胀形的最大许可延伸率可查阅手册,它与材料种类、厚度及有无 焊缝等因素有关。 如毛料经过滚弯焊接后,焊缝处塑性最低,它的延伸率比本体材料 降低15~20%,因此:
图2-38为压弯与拉弯成形时应力分布情况对比。
拉弯时,在轴向施加了拉力,改变了剖面上的应力分布,加上拉弯模 预先对回弹量进行了补偿,所以可以明显减小回弹量,保证零件 准确度要求。
航空厂常用的型材拉弯机有: 转台式、张臂式二种。(图2-39、图2-40)
拉弯过程: 预先将型材零件固定在拉伸夹头的气动夹头中,先开动拉伸液压作动筒
为了提高橡皮的单位压力,一般把橡皮装在金属容框里。 采用橡皮容框的 橡皮成形见图2-58所示。
图2-59为一般平面带弯边零件的成形过程。
橡皮成形所需单位压力:35~70MPa。由于需要的单位压力高,而且 容框尺寸又必须足够大,所以对成形压床的吨位要求高。 容框移动式液压机(500~5000吨)
橡皮成形液压机分两类 容框固定式液压机(最大吨位77000吨)
(4)利用橡胶或聚氨脂软凹模代替刚性凸模,调节压入深度 来控制弯曲角度,使卸载回弹后角度符合要求。
Reducing or eliminating Springback
例1. V形件弯曲:见图2-29 采用弯曲模压弯,制模之前要考虑角度
和半径的补偿,再经过试压调整。最后弯曲 成形的压力对回弹也有较大影响。
4)和机加比,材料节省、工时节约、材料组织细化、并且纤维不被切 断。
对某些难成形或常温下塑性较差的材料,可以采用加热强力旋压,见图 2-52
四、胀形 大型旋转体零件,如副油箱外壳等,可以用旋压,但劳动强度大,
因此可用胀形等方法。 胀形是利用分块式刚性模具,或利用液体或弹性体(橡皮)的压力,
把直径较小的筒形或锥形毛坯向外膨胀,成为直径较大的曲母线零件, 见图2-53和图2-54反应两种 不同的施加液压的方法: ①直接将液体通向两端密 封的工件腔内;(结构简单,
对于低塑性材料,如镁合金、钛合 金以及形状复杂的拉深件,为了减少 拉深次数,也可以采用加热拉深的 成形工艺,见图2-48所示。
拉深也可用于成形非圆形的复杂形状零件,如图2-49所示的矩形盒零件, 其四个圆角部位的毛料展开方法比较复杂。
三、旋压 特点: 模具简单,小批量生产成本低,旋压模仅为拉深模的十分之一。 对飞机上的一些大、中型旋转体零件仍延用这种方法。是一种半手
让内部骨架去适应蒙皮,这就对飞机蒙皮零件提出了更高的要求。 单曲度蒙皮:滚弯、压弯
蒙皮零件 双曲度蒙皮:拉形(曲率变化较为平缓) 平板类零件
蒙皮类典型零件见图2-72。 图2-73为用拉形方法制造的双曲度蒙皮典型零件。 二.单曲度蒙皮滚弯成形 板料滚弯零件分类见图2-74。
移动式的构造及传动原理与普通锻压用的液压机相似,只是台面较大, 为了提高生产率常采用多个台面(见图2-58b)。
容框固定式液压机的结构简单、单位压力高、零件成形准确度高、手工 修整量小。见图2-60
图2-60为9600吨容框固定式液压机的外形图,图2-61为 工作原理图
图2-61为筒式橡皮压床。
例2.图2-30复杂剖面钣金型材的多工序 压弯成形,模具与简单V形件弯曲相 似,但工序次序的选择不但影响模具 的数量,有时还决定零件制造的可行 性。
带闭斜角的U形件弯曲成形压弯模具见图2-31。
图2-31
三、型材滚弯 是成形型材零件的经济方法。 变形方式:属于自由弯曲。
可以制造飞机近似圆形的隔框、加强缘条,还可制造变曲率的零件。 型材滚弯典型零件见图2-32。
滚弯时,毛料在滚轴的作用力和摩擦力作用下产生进给和塑性变形,成 形后的曲率半径大小取决于滚轮间的相对位置、毛料厚度及材料的 机械性能。
型材滚弯分类:见图2-33
型材滚弯机分类:
三轴滚弯机
按滚轮所处位置和个数,分 四轴滚弯机 见图2-34
六轴滚弯机
手动
按操作方式,分 机动
滚弯机
液压靠模
滚弯机属于通用设备,不必专门制造模具,尤其适合小批量生产。
∵
当用平板毛料制造锥形件时,t0已经一定,
∴半锥角α越小,零件壁厚t越薄。
对金属材料其变薄量有一定限制,所以α也有一定极限值。见表2-3
旋压与拉深相比,有以下优点:
1)模具简单、经济;
2)零件精度高(
)、均匀、表面光洁( 1.6~0.43);
3)旋压可改善材料的机械性能,其强度极限、硬度和疲劳性能均有明 显提高;
工式加工方法,劳动强度大。 旋压成形机床类似于车床,或用车床改装而成。旋压模用铸铁、钢、
铝或硬木制造,对变形程度较大的零件可采用多次成形及中间退火处理。 旋压过程见图-50。
一般:
锥形件成形最容易→半球形稍难→圆筒形最难(与拉深相反),在
可能情况下尽量把旋压件设计成大曲率光滑曲线形状。
旋压件在成形过程中往往厚度会发生变化,对铝合金零件,厚度容
第五节 框肋类零件的制造-弹性模成形 一、概况
飞机机身隔框和机翼翼肋等零件,虽然可以用刚性模弯边或拉深成 形,但因为零件种类多,每种零件的数量很少,考虑到经济因素,必需 要简化模具。
如图2-57的典型框肋类零件,主要是用橡皮垫代替刚性凹模,即 橡皮成形。
二、橡皮成形机床 橡皮成形属于半模成形,一般只是制造一个凸模,凹模用橡皮代替。
除液压机之外,还有利用炸药爆炸产生的压力来成形零件。见图2-62 炸药的压力是通过水作为介质来传播的。
1.导线 2.筒盖 3.排气管 4.外筒 5.药塞 6.炸药 7.反射罩 8.橡皮 9.零件 10.成形模
三、橡皮成形工艺 直线弯Biblioteka 零件 凸(凹)曲线弯边的平面形零件
可加工的零件: 深度不大的立体形状零件 框肋类零件上的加强梗、减重孔、加强筋等 下料、冲裁、冲孔
二、拉深基本原理及成形工艺 圆筒形零件的拉过程见图2-43。 各部分的应力、应变状态分布图2-44。
为克服拉深过程中凸缘部分毛料的失稳起皱, 模具上一般都要设置压边装置。
如图2-46,拉深成形过程中,在凸模的作用下,把直径为D0的圆形毛料 拉入凹模,形成一个直径为d的圆杯形件,毛坯的外缘压缩量最大,其 应变值为:
进行拉伸加载,达到一定变形量后,在保持拉力不变的情况下,使 型材绕着拉弯模弯曲,直至贴模,然后再补拉,最后取下工件。 拉弯模示意图2-41
拉弯模具一般由:工作部分、垫板、底板组成,用螺栓连接成为整体。 模具设计原则:
工作型面的周长应比零件的切割长度每边加长10mm,两端圆角半径 不小于20 mm,模具侧边通常沿法线方向削平或开缺口,使拉弯终了 时夹头不致于碰到模具侧边。模具的工作面外形按零件的理论外形加 工,不考虑回弹量。模具的剖面形状要与型材的端面内形吻合,垫板 厚度应均匀,比型材腹板厚度大0.2~0.5mm。 材料:精制层板、厚铝板、费旧铝铸造。用于转台式拉弯机上的模具, 因为工作时侧压力较大,多选用厚钢板。 拉弯适用于各种钢材、铝合金、镁合金、钛合金的挤压型材和钣弯型材 零件的成形,制订拉弯工艺的重要内容就是: 选择合理的拉弯变形量、拉弯次数、预拉和补拉量,目的就是在最小的 拉伸量下获得必要的零件准确度。
密封问题难以保证) 毛料8放入凹模9内-夹紧装置吊入 毛料腔内—盖板12紧锁-向作动筒 10内充压缩空气—推动活塞2和杆 6下行—利用密封圈5对毛料下端密 封,同时推顶盖板上行挤压密封圈 密封-充液胀形。
②将液体封闭于橡皮囊内,间接传递成形压力。(密封解决得好,每次成形时 排出和压入的液体少,生产率高)凹模5是用环氧塑脂制造的,凹模的外壳 4要有足够的强度承受张力。橡皮囊3固定于盖板9上,囊内有刚性密闭圆筒 2支撑。工作时,先将毛料8放置于凹模之内,再将橡皮囊凸模放入毛料中, 用锁钩7扣紧于凹模外壳上,从液体导管1注入液体加压成形。
(2)用校正弯曲代替自由弯曲
(3)补偿法:
a.在纯弯曲时,可以根据回弹值得就算结果或经验数据对弯 曲模工作部分形状进行修正,使加载弯曲“过头”一些,卸 载后回弹就能接近或等于图纸规定的尺寸。
b.利用弯曲件回弹方向的特点,使相反方向的回弹变形相互补 偿。
(3)改变模具结构形状,把弯曲凸模做成局部凸起的形状
不利:生产效率低、需要熟练工人,而且对型材厚度、剖面形状有一定
的局限性。
常见问题:型材剖面畸变、腹板失稳、端头局部成形后复直等。见图2-