汽车疲劳耐久性试验
疲劳性能验证报告
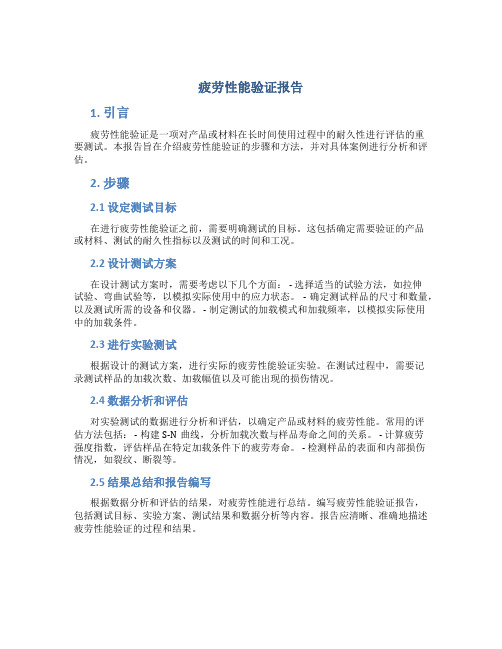
疲劳性能验证报告1. 引言疲劳性能验证是一项对产品或材料在长时间使用过程中的耐久性进行评估的重要测试。
本报告旨在介绍疲劳性能验证的步骤和方法,并对具体案例进行分析和评估。
2. 步骤2.1 设定测试目标在进行疲劳性能验证之前,需要明确测试的目标。
这包括确定需要验证的产品或材料、测试的耐久性指标以及测试的时间和工况。
2.2 设计测试方案在设计测试方案时,需要考虑以下几个方面: - 选择适当的试验方法,如拉伸试验、弯曲试验等,以模拟实际使用中的应力状态。
- 确定测试样品的尺寸和数量,以及测试所需的设备和仪器。
- 制定测试的加载模式和加载频率,以模拟实际使用中的加载条件。
2.3 进行实验测试根据设计的测试方案,进行实际的疲劳性能验证实验。
在测试过程中,需要记录测试样品的加载次数、加载幅值以及可能出现的损伤情况。
2.4 数据分析和评估对实验测试的数据进行分析和评估,以确定产品或材料的疲劳性能。
常用的评估方法包括: - 构建S-N曲线,分析加载次数与样品寿命之间的关系。
- 计算疲劳强度指数,评估样品在特定加载条件下的疲劳寿命。
- 检测样品的表面和内部损伤情况,如裂纹、断裂等。
2.5 结果总结和报告编写根据数据分析和评估的结果,对疲劳性能进行总结。
编写疲劳性能验证报告,包括测试目标、实验方案、测试结果和数据分析等内容。
报告应清晰、准确地描述疲劳性能验证的过程和结果。
3. 案例分析3.1 测试目标本次疲劳性能验证的目标是评估某型号汽车发动机的曲轴在使用过程中的耐久性。
3.2 测试方案本次测试选用弯曲试验方法,测试样品为某型号汽车发动机的曲轴。
测试采用恒幅加载模式,频率为10Hz。
共进行10个样品的测试。
3.3 实验测试根据测试方案,使用相应的试验设备和仪器对样品进行弯曲试验。
记录样品的加载次数和加载幅值,并检测样品的损伤情况。
3.4 数据分析和评估根据实验测试得到的数据,构建S-N曲线,分析加载次数与样品寿命之间的关系。
发动机耐久性试验工作总结

发动机耐久性试验工作总结
近年来,随着汽车行业的快速发展,发动机的耐久性成为了汽车制造商和消费者关注的焦点。
为了确保发动机的质量和性能,耐久性试验工作成为了必不可少的一环。
在过去的一段时间里,我们进行了一系列发动机耐久性试验工作,以验证发动机的可靠性和耐久性。
首先,我们进行了发动机零部件的耐久性试验。
通过对发动机的各个零部件进行疲劳试验和持久性试验,我们成功地验证了这些零部件在长时间工作下的稳定性和可靠性。
这为整个发动机的耐久性提供了坚实的基础。
其次,我们进行了整机发动机的耐久性试验。
在实际工作环境下,我们对发动机进行了长时间的运行试验,以模拟真实的使用情况。
通过监测和分析发动机的各项性能指标,我们成功地评估了发动机的耐久性和稳定性。
最后,我们进行了发动机在极端条件下的耐久性试验。
在高温、低温、高海拔等极端环境下,我们对发动机进行了严苛的试验,以验证其在极端条件下的可靠性和稳定性。
通过这些试验,我们进一步提高了发动机的耐久性和适应性。
总的来说,通过这些发动机耐久性试验工作,我们成功地验证了发动机的可靠性和耐久性,为汽车制造商提供了重要的参考数据。
未来,我们将继续深入研究和开展发动机耐久性试验工作,不断提升发动机的质量和性能,为汽车行业的发展贡献我们的力量。
汽车行业产品质量检测标准

汽车行业产品质量检测标准随着社会的发展和人们生活水平的提高,汽车已经成为现代人生活中不可或缺的一部分。
然而,汽车作为一种复杂的机械设备,其产品质量的问题一直是人们关注的焦点。
为了保障汽车产品的质量和安全性,汽车行业制定了一系列的产品质量检测标准,以确保汽车的安全、可靠和高质量的性能。
一、外观检测标准外观质量是汽车产品的重要指标之一,其直接影响到用户的购买决策和使用感受。
外观检测标准包括车身的漆面质量检测、车身零部件装配质量检测、车窗玻璃质量检测等。
其中,车身的漆面质量检测主要包括涂装厚度、颜色均匀度、表面平整度等指标的检测。
二、功能性能检测标准汽车的功能性能是用户购买汽车的重要考虑因素之一。
功能性能检测标准包括发动机性能检测、悬挂系统性能检测、刹车系统性能检测等。
通过对这些关键部件和系统性能的检测,可以确保汽车在运行过程中的安全性和可靠性。
三、安全性能检测标准安全是汽车产品最重要的指标之一。
安全性能检测标准包括汽车碰撞安全性能检测、制动安全性能检测、安全气囊性能检测等。
这些标准的制定旨在确保汽车在碰撞和紧急情况下能够提供有效的保护,并降低事故发生时的伤害程度。
四、环保性能检测标准环保性能是现代汽车产品越来越受到重视的一项指标。
环保性能检测标准包括废气排放检测、燃油经济性检测、噪音控制检测等。
这些标准的制定旨在确保汽车在使用过程中对环境的影响最小化。
五、耐久性检测标准耐久性是衡量汽车产品质量的一个重要指标。
耐久性检测标准主要包括发动机寿命试验、底盘结构寿命试验、电气系统寿命试验等。
通过对汽车关键部件和系统进行长期的疲劳试验,可以评估汽车产品的耐久性和可靠性。
总结汽车行业制定的产品质量检测标准是保障汽车产品质量和安全性的重要手段。
通过外观、功能性能、安全性能、环保性能和耐久性等方面的检测,可以确保汽车产品在设计制造过程中符合相关的技术要求和标准,最终提供给用户高质量、安全可靠的汽车产品。
然而,随着科技的不断进步和用户需求的不断变化,汽车行业的产品质量检测标准也需要不断更新和完善。
汽车件耐久性测试方案

汽车件耐久性测试方案汽车件的耐久性测试是为了确定汽车件在长期使用中能否保持良好的性能,并能够承受各种恶劣环境和使用条件的考验。
以下是一个汽车件耐久性测试方案的大致框架,供参考:一、测试目标和要求1. 目标:评估汽车件在预定使用寿命内的可靠性和耐久性表现。
2. 要求:确保汽车件在各种条件下能够达到设计要求,并保持长期的性能稳定。
二、测试内容和方法1. 环境适应性测试:测试汽车件在不同的温度、湿度、震动等环境条件下的性能表现。
2. 功能性能测试:测试汽车件在各种使用条件下的性能是否符合设计要求。
3. 耐久性测试:模拟汽车件在长期使用过程中的疲劳和老化情况。
4. 试验方法:根据相关国家和行业标准,选择适当的试验方法和设备进行测试。
三、测试方案和流程1. 确定测试项目和参数:根据汽车件的设计要求和实际使用情况,确定测试项目和相关参数。
2. 设计测试装置和设备:根据测试项目的要求,设计和制作适当的测试装置和设备。
3. 定义测试标准和指标:制定明确的测试标准和指标,用于评估汽车件的性能和耐久性。
4. 进行测试样品的准备:选择一定数量的测试样品,进行相关的预处理和标记。
5. 进行测试:按照预定的测试方案和流程,对测试样品进行相应的测试。
6. 数据分析和评估:收集测试数据,进行数据分析和评估,判断汽车件的耐久性表现。
7. 编写测试报告:总结测试结果,编写测试报告,并提出改进建议和意见。
四、测试安全和注意事项1. 确保测试设备和仪器的安全运行和使用。
2. 严格按照测试流程和操作规范进行测试,避免人为操作失误。
3. 在测试过程中,及时处理可能出现的问题和异常情况。
4. 对测试样品进行适当的防护和保养,保证其在测试过程中的完整性和准确性。
以上是一个汽车件耐久性测试方案的大致框架,具体的测试方案需要根据具体的汽车件种类和使用条件进行细化和完善。
汽车疲劳耐久性道路试验
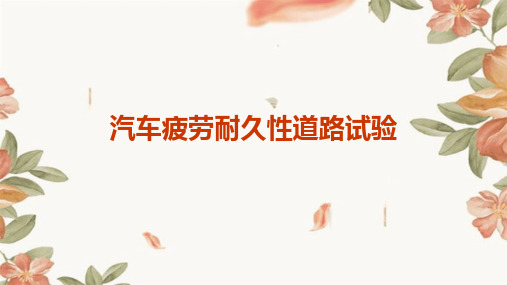
05
试验结果分析
数据分析方法
统计分析
对试验数据进行统计分析,包括 平均值、标准差、最大值、最小 值等,以评估数据的分布和离散 程度。
时域分析
对试验数据进行时域分析,如波 形分析、傅里叶变换等,以提取 车辆动态特性和振动规律。
频域分析
对试验数据进行频域分析,如频 谱分析、功率谱分析等,以揭示 车辆振动和噪声的频率特征及来 源。
试验方法
采用实际道路测试和模拟工况相结合的方法,模 拟车辆在不同路况、气候和驾驶习惯下的使用情 况。
试验过程
在多种典型路况下进行长时间行驶,包括高速公 路、城市道路、山路等,同时记录车辆各项性能 指标和驾驶员反馈。
试验结果与改进措施
试验结果
经过长时间的道路试验,发现车辆在某些部位出现了疲劳裂纹和磨损现象,影响了车辆的安全性能和 舒适性。
利用人工智能技术对汽车疲劳耐久性进行预测和优化,实现更高 效的试验和设计。
生物力学
借鉴生物力学的研究方法,将人体疲劳与汽车疲劳相结合,以提 高汽车座椅和人机界面的舒适性和耐久性。
智能化与自动化技术应用
数据采集与分析
利用先进的传感器和数据分析技术,实现高精度、高效率的数据采 集和疲劳性能分析。
虚拟仿真技术
验证汽车设计的可靠性和耐久性
通过模拟实际使用中的各种工况和载荷条件,可以验证汽车设计的可靠性和耐久性,及时发现和解决潜在的设 计缺陷或制造问题。
疲劳耐久性对汽车的重要性
提高汽车使用寿命
疲劳耐久性良好的汽车能够在使用过 程中保持性能,减少因过早疲劳损坏 导致的维修和更换部件的需求,从而 提高汽车的使用寿命。
结果解读
根据试验结果,分析汽车在疲劳耐久性道路试验中的性能表现,找出潜在的问题和薄弱环节。
耐久性设计及验证

局部刚度 部位
典型部位
刚度不足的影响
耐久性设计要求
图片
区分
支承部 位
大型板 壳零件
连接部 位
劢力总成、 悬架安装部位
前/后地板 顶盖
加强板 接头部位 铰链
安装点发生大的变形
产生振劢,尤其是共 振时,造成零部件的 疲劳损坏
刚度突变,导致疲劳 损坏,出现裂纹甚至 断裂
根据国外经验值,推荐车身支座区域的目标刚度取 为相应的支撑件(悬架弹簧等)刚度的3~5倍或以 上 (如右图示:减震器安装处尿部刚度计算模型)
避免形状突变
改善结构外形,避免形状突变 (如右图示:某零部件的尿部尺寸突变且相对过小,导致该处疲劳破坏,后 期改变尿部形状后通过疲劳试验)
DENGWEI
二.车身耐久性设计要素
刚度 – 当外界激励频率不车身系统固有频率接近或成倍数关系时,将发生共振,会影响车身的疲劳耐久性。 – 分类:整体刚度和尿部刚度 • 整体刚度:车身扭转/弯曲刚度,车身模态 • 尿部刚度:安装部位和连接部位的刚度
考虑因素或部位
对策
图片
倒角区域
适当增大钣金面过渡处的囿角半徂(如右图示)
孔
结构内必须开孔时,尽量避开高应力区,而在低应力区开孔 (如右图示:孔心位亍中性轰上,属亍低应力区域)
孔边尿部加强,采用凹/凸台孔(如右图示)
中性轴
避免截面突变 结构设计时,截面尺寸应平缓变化,特别要注意加强板和接头的设计 (如右图示:B柱加强板不侧围加强板搭接的区域截面均匀变化)
耐久性设计及验证
DENGWEI BIW
目录
一
耐久性设计方法概述
二
车身耐久性设计要素
三
耐久性验证简介
关于新能源汽车的疲劳耐久问题与相关试验思考
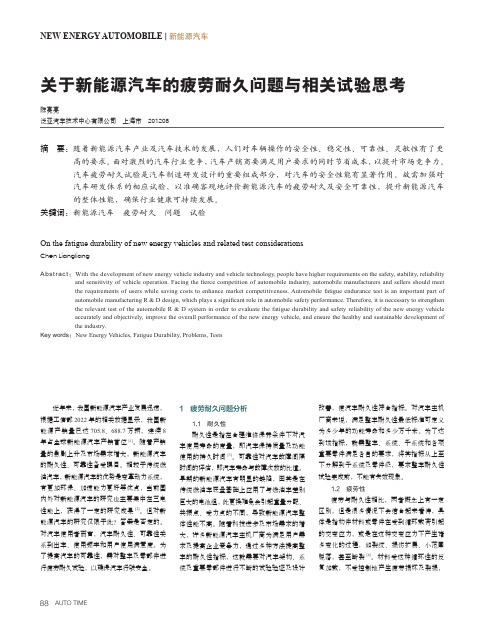
NEW ENERGY AUTOMOBILE | 新能源汽车近年来,我国新能源汽车产业发展迅速,根据工信部2022年的相关数据显示,我国新能源产销量已达705.8、688.7万辆,连续8年占全球新能源汽车产销首位[1]。
随着产销量的急剧上升及市场需求增大,新能源汽车的耐久性、可靠性备受瞩目。
相较于传统燃油汽车,新能源汽车的优势是变革动力系统,有更加环保、加速能力更好等优点,当前国内外对新能源汽车的研究也主要集中在三电性能上,获得了一定的研究成果[2]。
但对新能源汽车的研究仅限于此?答案是否定的。
对汽车使用者而言,汽车耐久性、可靠性关系到出车、使用频率和用户使用满意度。
为了提高汽车的可靠性,需对整车及零部件进行疲劳耐久试验,以确保汽车行驶安全。
1 疲劳耐久问题分析1.1 耐久性耐久性是指在合理维修保养条件下对汽车使用寿命的度量,即汽车保持质量及功能使用的持久时间[3]。
可靠性对汽车故障间隔时间的评估,即汽车寿命与故障次数的比值。
早期的新能源汽车有明显的缺陷,因其是在传统燃油车底盘基础上应用了与燃油车差别巨大的电池组,此更换难免会引起重量分配、共振点、受力点的不同,导致新能源汽车整体性能不高。
随着科技进步及市场需求的增大,许多新能源汽车主机厂商为满足用户需求及提高企业竞争力,通过多种方法提高整车的耐久性指标,这就需要对汽车架构、系统及重要零部件进行不断的试验验证及设计陈亮亮泛亚汽车技术中心有限公司 上海市 201208摘 要:随着新能源汽车产业及汽车技术的发展,人们对车辆操作的安全性、稳定性、可靠性、灵敏性有了更高的要求。
面对激烈的汽车行业竞争,汽车产销商要满足用户要求的同时节省成本,以提升市场竞争力。
汽车疲劳耐久试验是汽车制造研发设计的重要组成部分,对汽车的安全性能有显著作用。
故需加强对汽车研发体系的相应试验,以准确客观地评价新能源汽车的疲劳耐久及安全可靠性,提升新能源汽车的整体性能,确保行业健康可持续发展。
汽车可靠性试验方法
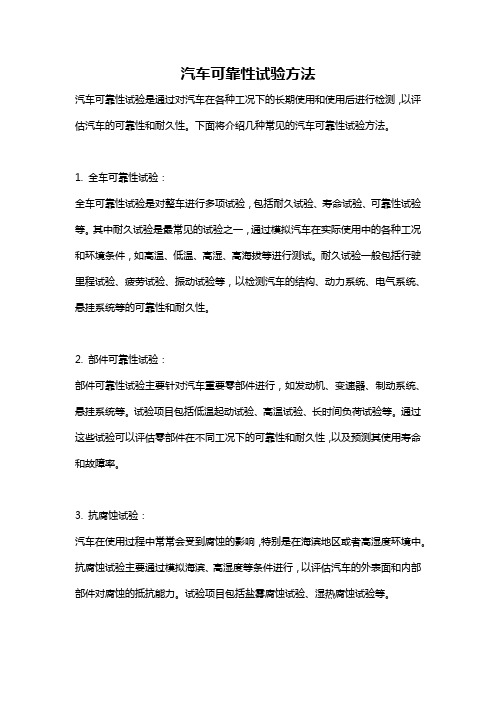
汽车可靠性试验方法汽车可靠性试验是通过对汽车在各种工况下的长期使用和使用后进行检测,以评估汽车的可靠性和耐久性。
下面将介绍几种常见的汽车可靠性试验方法。
1. 全车可靠性试验:全车可靠性试验是对整车进行多项试验,包括耐久试验、寿命试验、可靠性试验等。
其中耐久试验是最常见的试验之一,通过模拟汽车在实际使用中的各种工况和环境条件,如高温、低温、高湿、高海拔等进行测试。
耐久试验一般包括行驶里程试验、疲劳试验、振动试验等,以检测汽车的结构、动力系统、电气系统、悬挂系统等的可靠性和耐久性。
2. 部件可靠性试验:部件可靠性试验主要针对汽车重要零部件进行,如发动机、变速器、制动系统、悬挂系统等。
试验项目包括低温起动试验、高温试验、长时间负荷试验等。
通过这些试验可以评估零部件在不同工况下的可靠性和耐久性,以及预测其使用寿命和故障率。
3. 抗腐蚀试验:汽车在使用过程中常常会受到腐蚀的影响,特别是在海滨地区或者高湿度环境中。
抗腐蚀试验主要通过模拟海滨、高湿度等条件进行,以评估汽车的外表面和内部部件对腐蚀的抵抗能力。
试验项目包括盐雾腐蚀试验、湿热腐蚀试验等。
4. 电气系统可靠性试验:电气系统是汽车中一个非常重要又复杂的系统,其可靠性对整车的可靠性影响很大。
电气系统可靠性试验主要包括电器性能试验、电器负载试验、电源失效试验等。
通过这些试验可以评估汽车电气系统在各种工况下的可靠性和稳定性。
5. 安全性能试验:安全性能试验是保证汽车安全性的重要手段之一。
试验项目包括碰撞试验、侧翻试验、刚度试验等。
通过这些试验可以评估汽车在碰撞、侧翻或其他危险情况下的安全性能,以确保乘客的人身安全。
这些方法综合应用能够全面评估汽车的可靠性和耐久性,为汽车设计和制造提供重要依据。
在试验过程中,应按照相关标准和规范进行操作,确保试验结果的准确性和可靠性。
同时,还需要针对不同汽车类型和用途,制定相应的试验计划和指标,并不断优化试验方法和手段,以更好地提高汽车的可靠性和安全性。
整车疲劳耐久性能开发(1)

用于获取加速度响应载荷 (如底盘、驾驶室、动力总成 等),是耐久性能开发的关键载 荷。
若需进行整车及系统的台架 试验,加速度信号还将作为重要 的迭代信号。
1、载荷谱采集
1.3 关键传感器 • 位移传感Байду номын сангаас的应用
Zd
用于获取底盘、驾驶室、动力总成 的相对位移,是耐久性能开发的关键载 荷。
路面特征分类
对路面工况进行分类,高频路面采 用虚拟迭代分解,低频路面采用施 加车身姿态分解
序号 工况 地理特征 平整度
1 铁轨路 平路面 高频路面
2 振动路3 平路面 高频路面
3 长波路 平路面 低频路面
…… ……
……
……
24 8字行驶 大弯道平路面 低频路面
25 倒档上坡
坡道
低频路面
整车多体模型建立及验证
1、雨流计数,统计各信号 2、虚拟损伤计算,对比不同路面的强度等
循环幅值、均值及次数
级,以及不同试验场同种路面的强度等级
1、载荷谱采集
1.6 商用车载荷谱采集
针对车架、驾驶室、悬挂部
件、轴头等关键区域,采集加速
加 速
度、应变、位移、力等载荷信号。 度
Z向是主要载荷方向。
传 感
器
应 变 片
位 移 传 感 器
耐久性能整体解决方案
基于实测载荷谱的耐久性能开发主要过程包括: 载荷谱处理后,通过多体动力学模型将轮心载荷分 解到底盘各个接附点,进行有限元疲劳强度仿真及 优化;以及载荷工况的等效、仿真和试验的精度对 比。
载荷谱
载荷分解
试验场/台架可靠性试验
仿
真
与
汽车零件疲劳试验报告
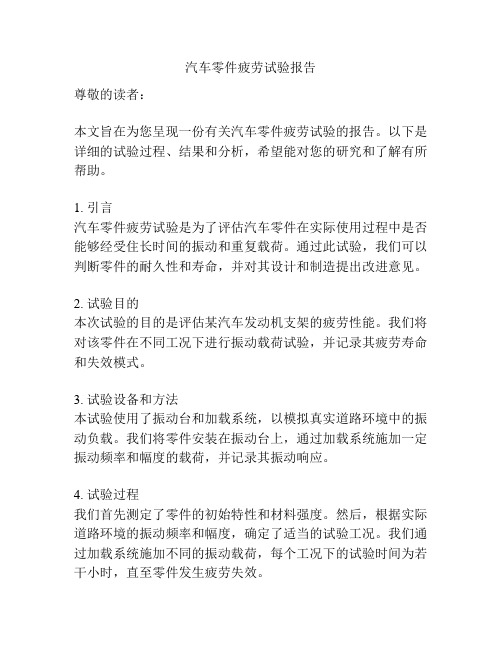
汽车零件疲劳试验报告尊敬的读者:本文旨在为您呈现一份有关汽车零件疲劳试验的报告。
以下是详细的试验过程、结果和分析,希望能对您的研究和了解有所帮助。
1. 引言汽车零件疲劳试验是为了评估汽车零件在实际使用过程中是否能够经受住长时间的振动和重复载荷。
通过此试验,我们可以判断零件的耐久性和寿命,并对其设计和制造提出改进意见。
2. 试验目的本次试验的目的是评估某汽车发动机支架的疲劳性能。
我们将对该零件在不同工况下进行振动载荷试验,并记录其疲劳寿命和失效模式。
3. 试验设备和方法本试验使用了振动台和加载系统,以模拟真实道路环境中的振动负载。
我们将零件安装在振动台上,通过加载系统施加一定振动频率和幅度的载荷,并记录其振动响应。
4. 试验过程我们首先测定了零件的初始特性和材料强度。
然后,根据实际道路环境的振动频率和幅度,确定了适当的试验工况。
我们通过加载系统施加不同的振动载荷,每个工况下的试验时间为若干小时,直至零件发生疲劳失效。
5. 试验结果通过对试验数据的分析和处理,我们获得了该发动机支架的疲劳寿命曲线。
根据试验结果,我们发现零件在特定振动频率和幅度下的疲劳寿命为XXXX小时。
此外,我们还观察到疲劳失效主要表现为裂纹扩展和变形。
6. 结果分析从试验结果可以得出,该发动机支架在实际道路条件下承受正常振动载荷时具有良好的耐久性能。
然而,我们还发现在某些特定工况下,零件的疲劳寿命较短,这可能与材料的强度和设计的薄弱点有关。
7. 结论综上所述,我们通过疲劳试验评估了某汽车发动机支架的疲劳性能,并得出了对其设计和制造的改进建议。
同时,我们也提示在特定工况下需谨慎使用该零件,以避免可能的疲劳失效带来的安全隐患。
附录:试验数据和图表谢谢您对本报告的阅读,如果您有任何问题或需要进一步了解,请随时与我们联系。
至此我结束报告,期待与您的交流。
此致敬礼。
疲劳试验及其分析方法的研究与应用

疲劳试验及其分析方法的研究与应用近年来,汽车、飞机、机械等领域的发展极大地促进了人类的经济和社会进步,然而,这些高精密机械的使用却不可避免地带来了一系列涉及工程安全和健康的问题。
其中之一就是疲劳损伤。
事实上,所有材料都会经历疲劳,而重复载荷、弯曲、扭曲和震动通常是导致零件损坏的原因,进而导致事故发生。
因此,疲劳性分析变得至关重要,研究整个系统的耐久性,为工程师提供预测和防止各种疲劳现象的方法。
本文将重点介绍疲劳试验及其分析方法的研究与应用。
一、疲劳基础疲劳是由于物体在反复受到应力的作用下,经过一定次数的加载后发生异常损伤和断裂,在实际生产过程中给机械设备带来很大危害。
因此,在进行耐久性设计过程中,必须进行疲劳强度试验。
通过对构件的疲劳破坏试验分析,可以获得相应的材料、零件等物理学性质,并且能够在逐渐确定其受力下,量化分析其疲劳威胁度,以找到有效的解决方案,提高机械设备的耐久性。
二、疲劳试验方法为更好的分析疲劳效应,需要对本质的疲劳特性进行测试,并在进行疲劳寿命分析时,将这些测试中积累的数据加以利用和处理。
目前,常见的疲劳试验方法主要有6种:载荷控制疲劳试验、应变控制疲劳试验、力量降低疲劳试验、一定应力幅疲劳试验、弛豫疲劳试验和复合式疲劳试验。
您可以根据具体需要选择不同的试验方法,在其基础上结合系统化、定量地分析和处理数据,得到更具有实际意义的结果。
三、疲劳分析方法尽管疲劳试验是对材料性质的重要评估,但对于机械结构的安全性而言,疲劳分析却是更为重要的。
采用现代计算机-辅助分析技术,先将载荷历史数据转化成应力-时间/应变-时间曲线,再对其进行计算与分析,可以计算出疲劳寿命及其他性能指标。
在此基础上,结合因素分析、分类分析、回归分析等方法,以全面地预测疲劳损伤。
四、疲劳试验的应用疲劳试验不仅可以应用于机械设备 fatigue testing,而且在其他领域发挥重要作用。
例如,在汽车和气体轮机制造商中,疲劳试验可用于确保主要部件(如油泵)有足够的工作寿命;涉及到机械基础的交通运输装置,如铁路车辆和飞机,疲劳试验可以全面评估其长期安全管理的有效性;而在纺织品、食品工业和医疗工业等行业中,疲劳测试也是非常有用的。
浅谈汽车底盘零件的疲劳试验分析

浅谈汽车底盘零件的疲劳试验分析底盘是车辆结构中负责承受路面和车身负荷的关键部件之一、为了保证底盘的强度和耐久性,需要进行疲劳试验分析,来评估底盘零件在长期使用过程中的疲劳寿命。
本文将从试验方法、试验结果分析和改进措施三个方面来进行分析。
试验方法底盘零件的疲劳试验一般采用低周疲劳试验和高周疲劳试验两种方式。
低周疲劳试验通常采用恒幅加载方式,通过在一定的载荷下施加一定次数的循环载荷进行试验。
高周疲劳试验则采用应变幅变加载方式,即通过在一定应变幅范围内施加高频循环载荷来进行试验。
试验结果以应力-寿命曲线和应变-寿命曲线的形式展示。
试验结果分析通过对底盘零件的疲劳试验结果进行分析,可以得到零件的疲劳寿命,以及零件的疲劳强度和耐久性等信息。
在低周疲劳试验中,随着载荷幅值的增加,零件的寿命明显缩短。
在高周疲劳试验中,随着循环次数的增加,零件的应变幅值和内部应力都会不断积累,导致裂纹的扩展和零件失效。
因此,疲劳寿命是评估底盘零件强度和耐久性的重要指标。
改进措施针对底盘疲劳试验分析结果,需要从设计和材料两个方面进行改进。
针对设计方面,可以根据试验结果提高零件的刚度和强度,减少零件的应力集中。
针对材料方面,可以采用高强度,高韧性的材料来替代原有的材料。
同时,优化零件的表面处理方法,通过表面改性来提高零件的耐久性和抗疲劳性能。
综上所述,底盘零件的疲劳试验分析是评估底盘强度和耐久性的重要手段之一、通过试验得到的结果,可以指导设计、材料选择和工艺改进。
未来,随着材料和制造工艺的发展,底盘零件的疲劳试验分析将会更加精准和可靠。
汽车排气系统局部疲劳耐久性试验仿真分析
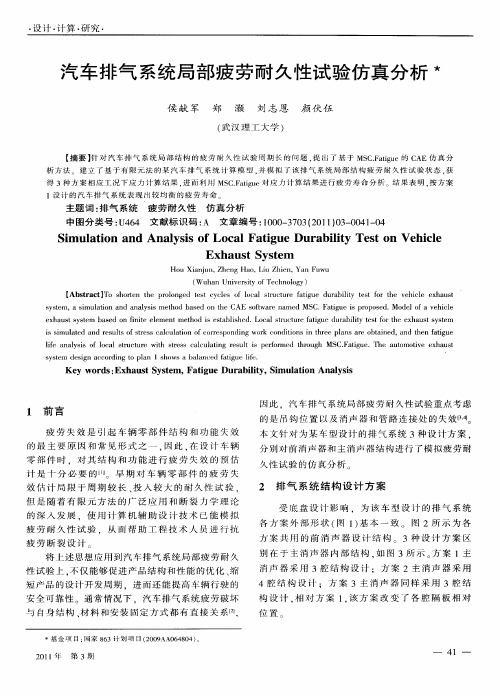
计 是 十 分 必 要 的 l 早 期 对 车 辆 零 部 件 的 疲 劳 失 l I
s se d sg c o di o pln 1 s o a a c d ftgu ie y tm e in a c r ng t a h ws a b l n e a i e lf.
Ke y wor ds: Exh s yse ,Fatg au t S t m i ue Dur iiy ab lt ,Si ul to Ana yss m a i n l i
e ha ts se b s d o i ie e e ntm eho s e tbls d.L a tu u e f tg e dur iiy ts rt x a ts se x us y tm a e n fn t l me t d i sa ihe oc lsr ctr ai u ablt e tf he e h us y t m o i i s smult n e ulso te sc l lto o mT p dig wo k eo diin n t e l n r b an d,a h n f tg e aed a d r s t fsr s acu ain fc es on n r n to s i hr e p a s a e o t ie nd t e a iu lf a lss fl c lsr t e ie nay i o o a tucur wih tes c lultn r s l i p ro me h o h t sr s ac a ig e u t s e fr d t r ug M S Fai u C. tg e.The u o tv e ha t a t mo ie x us
LMS在零部件疲劳耐久性试验评价中的应用

LMS在零部件疲劳耐久性试验评价中的应用彭辉何荣国胡文伟上海大众汽车有限公司,上海,201805摘要本文介绍了LMS Tecware和FALANCS LifeStat软件在零部件(以轿车支承座为例)疲劳耐久性试验评价中的应用。
提出了制定试验规范的一般方法,可供在其它零部件疲劳试验评价中参考。
关键词LMS Tecware FALANCS LifeStat 疲劳耐久性试验评价 试验规范Fatigue life evaluation of the automotive partsusing LMSPeng Hui He Rongguo Hu WenweiShanghai Volkswagen,shanghai,201805Abstract This paper introduces the application of LMS Tecware and FALANCS LifeStat to fatigue life evaluation of the automotive parts (here for example:bracket). It can also extract the general method to set up the test standard for fatigue life evaluation of other parts.Key Words LMS Tecware FALANCS LifeStat fatigue life evaluation test standard1导言某轿车支承座是后桥和车身间的一个冲压连接件(见图1),一直采用进口材料生产。
为了提高国产化率,降低成本,供应商拟采用国产材料生产,这就需要进行合理的疲劳耐久性试验评价。
由于没有针对该车型支承座的试验规范,需要根据实际使用载荷情况,制定试验规范,作为试验评价的依据。
LMS Tecware 和FALANCS LifeStat可以协助完成疲劳耐久性试验评价。
汽车排气系统局部疲劳耐久性试验仿真分析

汽车排气系统局部疲劳耐久性试验仿真分析汽车排气系统是关键的发动机零部件,它负责将废气从发动机中排出。
同时,排气系统庞大的设计,包括排气管、消声器、吸气管等部分。
因此,汽车排气系统表现出良好的疲劳耐久性是必不可少的。
为了保证汽车排气系统的疲劳耐久性,研究人员最近进行了一项试验仿真分析。
在这篇文章中,我们将简要介绍该研究的目的和结果。
研究目的汽车排气系统的疲劳耐久性与排气管、消声器、吸气管等部分有关,这些部分在长时间使用中容易发生疲劳断裂。
因此,研究团队开发了一种试验仿真模型,以模拟汽车排气系统在工作过程中的实际使用情况。
他们的目标是通过分析模型得出新的设计指导方针,以满足汽车排气系统的疲劳耐久性标准。
试验设计研究人员使用有限元方法来模拟汽车排气系统的耐久性。
他们设计了一个模型,包括了汽车的发动机和排气系统,模型使用了500000个单元,每个单元尺寸约为2毫米。
这个模型可以模拟排气系统的疲劳过程,并预测其使用寿命和压力受力情况。
试验流程在试验中,研究人员向模型中输入压力和温度数据,以模拟排气系统在工作时的真实情况。
然后,他们根据不同的载荷条件,通过数值方法计算得到了排气系统在使用过程中的应力和变形情况。
结果分析通过试验,研究者发现最容易发生疲劳断裂的区域集中在排气管与消声器连接点、消声器与吸气管连接点等重要部位。
根据评估,路上反复行驶会再次摩擦并引起底部生锈,钢桶管内腐蚀和外部碰撞等因素也是当前排气系统容易疲劳的主要原因。
研究者还发现,加大零粉和碱性物质对中空铁管表面的腐蚀也会影响其耐久性。
研究者推荐在设计阶段应考虑强度增加的措施来提高汽车排气系统的疲劳耐久性。
本文介绍了一项研究,通过试验仿真分析汽车排气系统在工作过程中的实际情况,研究者运用有限元素方法,通过输入压力和温度数据,以模拟排气系统在工作时的真实情况,最终推荐在设计过程中考虑强度增加的措施,以提高汽车排气系统的疲劳耐久性。
该研究对汽车排气系统的设计和生产具有指导意义,可以指导汽车生产厂家改进其设计和制造工艺,提高汽车的性能和质量。
减震器测试标准

减震器测试标准减震器测试标准是衡量减震器性能和质量的重要依据。
在全球范围内,各个国家和地区的汽车制造商、零部件供应商以及测试机构都在采用这些标准来确保产品的性能和安全性。
本文将对减震器测试标准进行详细解析,以期为读者提供有关减震器测试的有用信息。
一、减震器测试标准概述减震器测试标准主要包括静态压缩试验、动态压缩试验、疲劳试验、耐久性试验和温度稳定性试验等。
这些试验旨在评估减震器的性能、可靠性和适应性,以确保其在实际应用中能够满足各种工况需求。
二、减震器测试标准的具体内容1.静态压缩试验:该试验主要用于检测减震器在静止状态下的压缩性能。
试验过程中,将减震器充满油液并固定在试验台上,通过施加不同压力,观察减震器的压缩量。
2.动态压缩试验:与静态压缩试验类似,不同之处在于动态压缩试验模拟了减震器在行驶过程中的受力情况。
通过测量减震器在动态加载下的压缩量,评估其应对实际工况的能力。
3.疲劳试验:疲劳试验旨在检测减震器在长时间使用过程中的性能稳定性。
试验过程中,模拟减震器在实际工况下受到的循环载荷,观察其性能变化。
4.耐久性试验:耐久性试验主要评估减震器在恶劣工况下的使用寿命。
试验过程中,将减震器暴露在高温、高压、高湿等恶劣环境中,检测其性能变化。
5.温度稳定性试验:温度稳定性试验用于检测减震器在不同温度下的性能表现。
通过将减震器分别在高温、低温环境下进行试验,观察其性能变化。
三、减震器测试标准的意义和应用减震器测试标准对于汽车行业具有重要意义。
一方面,这些标准为生产企业提供了指导,确保产品具有良好的性能和安全性;另一方面,测试结果还可作为消费者购车时的参考,帮助他们选择优质的减震器产品。
同时,测试标准还有助于推动整个行业的技术进步,促使企业不断优化产品设计,提高产品质量。
总之,了解减震器测试标准有助于我们更好地评估减震器的性能和安全性。
在选购减震器时,可参考这些标准,选择高品质的产品。
疲劳试验方法_标准_概述说明以及解释

疲劳试验方法标准概述说明以及解释1. 引言1.1 概述疲劳试验方法是一种重要的工程实验方法,用于评估材料或构件在循环加载条件下的耐久性和可靠性。
在现代工程设计和材料科学领域,疲劳试验方法被广泛应用于各种应用中,如航空航天、汽车制造、机械工程等。
通过模拟真实使用环境下的循环负载,疲劳试验可以揭示材料和构件在长时间使用过程中存在的弱点和故障机理。
1.2 文章结构本文将详细介绍疲劳试验方法及其标准,并对其进行解释和讨论。
文章由引言、疲劳试验方法、疲劳试验标准、疲劳试验概述说明、解释与讨论以及结论等部分组成。
引言部分将给出关于疲劳试验方法的整体概述,并简单介绍文章结构。
1.3 目的本文旨在提供对疲劳试验方法及其标准的全面理解。
通过对常见的疲劳试验方法和标准进行介绍和解析,读者将了解到选择适当的疲劳试验方法的考虑因素,以及疲劳试验标准的重要性和作用。
此外,本文还将详细说明疲劳试验的基本原理和过程概述,以及分析疲劳试验结果、对不同标准进行疲劳试验比较和解读疲劳断口特征及其含义的常用方法。
最后,通过总结疲劳试验方法和标准的重要性,并对未来发展进行展望,希望能够促进相关领域的研究与应用。
(文章正文内容根据实际需求填写即可)2. 疲劳试验方法2.1 定义和背景疲劳试验方法是用于评估材料、结构或设备在重复加载下的耐久性能的实验方法。
疲劳是指物体在反复循环载荷作用下逐渐损坏的现象,它可能导致结构失效或材料断裂。
疲劳试验方法旨在模拟实际使用条件下的循环荷载以确定材料或结构的疲劳极限、寿命和可靠性。
2.2 常见的疲劳试验方法常见的疲劳试验方法包括:- 轴向拉压疲劳试验:通过施加轴向拉力或压力来对材料进行循环加载,以评估其抗拉/压疲劳性能。
- 弯曲疲劳试验:施加弯曲力以模拟结构在实际使用中所受到的曲度变化,并评估材料或结构的抗弯曲疲劳性能。
- 扭转疲劳试验:通过扭转加载对材料进行循环应变,以评估其抗扭转疲劳性能。
- 振动疲劳试验:通过施加振动载荷模拟实际使用条件下的震动环境,评估材料或结构的抗振动疲劳性能。
- 1、下载文档前请自行甄别文档内容的完整性,平台不提供额外的编辑、内容补充、找答案等附加服务。
- 2、"仅部分预览"的文档,不可在线预览部分如存在完整性等问题,可反馈申请退款(可完整预览的文档不适用该条件!)。
- 3、如文档侵犯您的权益,请联系客服反馈,我们会尽快为您处理(人工客服工作时间:9:00-18:30)。
11
用户车辆使用测量-结果
承载结构-循环载荷
Rainflow of WFT_LF_Fx DYPG GMW15531
1.E+08 1.E+07 1.E+06 1.E+05 1.E+04
0.0 0.5 1.0 1.5 2.0 2.5 3.0 3.5 4.0 Range (kN)
12
Cycle Counts
? ? ? ? ?? ? ? ? 20140 60 80 100120140160180200
Strain(ue)
0.1 ? ? ? ? ? ? ? ? ? 0 20 40 60 80 100120140160180200
Strain(ue) ? ? ? ? ?? ? ? ?
ch3
...
...
...
0 40 80 120 160 200
Strain(ue)
13
用户车辆使用测量-结果
驾驶习惯、装置使用
14
用户车辆使用测量-结果
15
用户车辆使用测量-应用
承载结构载荷-疲劳损伤
Neuber Rule
Rainflow Counting
Material Data Component Geometry
用户 车辆使用
认证试验
弱相关:
耐久试验不能完 全反映实际使用
相关:
耐久试验充分 反映实际使用
¥¥¥
不同的认证效率和售后成本
7
用户车辆使用测量-用途
用户车辆使用
工程设计 技术要求 (整车/系统/部件)
认证试验规范开发
可靠性(寿命)、 优化设计
耐久、性能预测 (FEAM)
发现、消除潜在 失效模式
减少售后索赔和 召回成本
相关
8
用户车辆使用测量-内容
承载结构载荷
•道路路面 •车辆载重
•环境
用户使用
动力传动系统
•地区交通特点 •驾驶习惯 •油品质量 •环境
装置和附件的使用
•车辆用途 •驾驶习惯
9
用户车辆使用测量-结果
承载结构-行使速度
Distance @ Level of Vehicle speed
Vehicle speed (km/h)
1 10
0
40
80 120
Strain(ue)
1
160
0
40
80
120
Strain(ue)
ch2
160
ch3
1000 100 10 1 0.1
1000
100
1000 10
100 1 0 20 40
10 0.1
99.8le Estimate
ch1
90.0le Estimate
80.0le Estimate
用户车辆使用测量-结果
承载结构-循环载荷
Cycles Count
Cycles Count
10000 1000 100
10 1
0 40 80 120 160
Strain(ue)
10000 1000 100
10 1
90% ile Estimate 90% Upper bound 90% Lower bound
/
c,
n2,
j
m 2,
j
/
c,......
nl
,
j
m l, j
/c
T …(4)
1
为了在试车场再现该零件整个使用寿命里程的疲劳损伤-目标:D d 将式(2)
和(4)代入则:
N1
m 1
,
N 2
m 2
,.....N . l
m l
T
k
Aj
n1, j
m 1, j
/ c, n2, j
m 2, j
此类似式(5)的方程组不至一个。若测量点/载荷数为P ,则对于任一载荷s 普遍
的方程组可写成如下:
k
N1s
A j n2s, j
1
N
s 2
k
Aj n1s, j ...
1
k
N
s l
A j nls, j
1
… (6)
求解方程组(6) 确定各加权系数。
s 1,2......P
22
加速结构耐久试验开发
60 80 100 120 140 160 180 Strain(ue)
道路设施
整车一般耐久试验 50000km /1100 hrs
N
石块路 A
石块路 B
行驶 +
石块路 C
石块路BB2/ 6车速
行驶 +
石块路 BB1/ 5车速
23
加速结构耐久试验开发
数据测量系统
车辆:
设备 & 软件
● 数据采集系统 - 制造商 : SoMat U.S.A - 型 号 : e-DAQ FCS
d1, j , d2, j ,.....d. l, j
T
n m 1, j 1, j
/
c,
n2,
j
m 2,
j
/
c,
...
.
.n. l
,
j
m l, j
/c
T ...(3)
道路 j行驶一周产生的的总损伤为:
其中:
l
l
f j
di, j
n m i, j i, j
/c
1
1
i, j -第i 级载荷;
/
c,.....n. l
,
j
m l, j
/c
T
1
21
道路相关技术
由此可得到如下方程组:
k
N1 Aj n1, j
1
k
N 2 Aj n2, j
1
k
…… Nl Aj nl, j
1
…… (5)
它们表明了: 相同载荷级下,试车场k 种道路上循环次数的线性迭家等于
目标载荷的循环次数。
作为耐久性道路行驶试验,必须兼顾车辆的各个系统部件和各种载荷。因
● 车轮力传感器
- 制造商 : MSC U.S.A
试件传感器
技术参数
……
发动机 : 1.6 DOHC 变速箱 : 5-speed AT
软件 - 数据采集:
悬架形式 前 : 麦佛逊 后 : 双连杆
整备重量 : 1255 kg 车轮/胎压 : 195/55R 15 (0.18Mpa)
SoMat TCE for e-DAQ - 数据处理分析:
6.E+04
4.E+04
2.E+04
0.E+00
-0.5
0.0
Force (kN)
0.5
1.0
1.5
2.0
2.53Βιβλιοθήκη 03.54.0V-speed Distribution of WFT Force
160
140
120
100
80
60
40
20
0
0.E+0 2.E+0 4.E+0 6.E+0
0
4
4
4
Counts
0
50
100
150
200
Distances (km)
10
用户车辆使用测量-结果
承载结构-载荷分布
Counts Vehicle speed (km/h)
-4.0
-3.5
-3.0
-2.5
-2.0
Le v e l-Crossing of LF WFT Force
-1.5
-1.0
1.E+05
1.E+05
8.E+04
LMS TecWare - 损伤相关:
LMS TecWare
24
加速结构耐久试验开发
车辆载重:轻载和重载
采样设备及参数设置: 采样频率: 409.6 Hz 帧长度: 1024/帧 滤波器频率上限:80Hz
样本数:9 3名驾驶员,每个驾驶员在
每一路面和工况下重复行驶3次 共得到9个测量样本
25
加速结构耐久试验开发
当前主要认证手段 – 试车场道路试验
➢ 提供了全面、系统和总成间相互作用载荷谱; ➢ 道路试验提供包括驱动、环境、道路表面和机械工况在
内的全面整车级载荷谱; ➢ 道路试验提供驾驶员反馈 -人体生理学的、车辆响应、主
观感觉等等。
5
汽车疲劳耐久试验介绍
6
用户车辆使用测量-目的
失效模式
不相关:
耐久试验完全不 能反映实际使用
N N1, N2 ,.....N . l T
…… (1)
相应的疲劳损伤矩阵为:
D D1, D2 ,.....D. l T
N1
m 1
/ c,
N
2
m 2
/
c,.
...
..Nl
m l
/
c
T
…… (2)
该零件在疲劳载荷作用下的总损伤为:
l
l
F
Di
N
i
m i
/c
1
1
其中: i - 第 i 级载荷;
3
汽车疲劳耐久试验介绍
依据
➢ 开发策略; ➢ 用户特殊需求; ➢ 市场反馈(售后失效模式、用户抱怨、机构评价)。
要求
➢ 客观:试验方法以用户产品使用为目标(合理的试 验、合理的评价 );
➢ 有效:降低售后产品故障率,减少 Warranty 成本; ➢ 快速:适应产品开发流程需求。