AspenPlus在常减压蒸馏装置中的应用
Aspen+plus精馏模拟

Aspen plus 在精馏中的应用实例教程 /teacherf/
第 3 页共 37 页
3. 精馏塔的简捷计算
·设计任务 确定理论塔板数 确定合适的回流比
·DSTWU 精馏模型简介
本例选择 DSTWU 简捷精馏计算模型. DSTWU 可对一个带有分凝器或全凝器一股进料和两种产品的蒸馏塔进行简捷精馏 计算. DSTWU 假设恒定的摩尔溢流量和恒定的相对挥发度
1)创建精馏塔模块 在模型库中选择塔设备 column 标签,如图 3.1-1.
图 3.1-1
点击该 DSTWU 模型的下拉箭头,弹出三个等效的模块,任选其一如图 3.1-2 所示.
Aspen plus 在精馏中的应用实例教程 /teacherf/
第 4 页共 37 页
·定义每个组分流量或分率(Composition) Mass-frac(质量分率):WATER: 0.632; CH3OH: 0.368.
输入数据后的窗口如图 3.5 所示.
3.6 定义单元模型
图 3.5
Aspen plus 在精馏中的应用实例教程 /teacherf/
输入回流比的实际值; 定义回流比与最小回流比的比值. 输入负号后再入数值. 在这里我们取最小回流比的 2 倍, 故输入-2.
·定义轻重关键组分的回收率(Key component recoveries) Dstwu 要求定义组分的份的回收率. 计算得到两种组分的回收率为:
轻关键组分的回收率为 0.9983 重关键组分的回收率为 0.0029
第 12 页共 37 页
3.7 模拟计算与结果查看
点击工具栏中的蓝色 N-> 图标,即可进行计算,同时进入“Control Panel”页显示运行信息, 如图 3.7-1. 该图标的作用是执行下一步操作,若数据未输入完毕自动转到待输入数据的窗口; 若数据输入完毕,则进行计算. 上面操作也可点击 Run 菜单中的 run 命令来直接
基于AspenPlus和AspenDynamics的常减压装置流程模拟
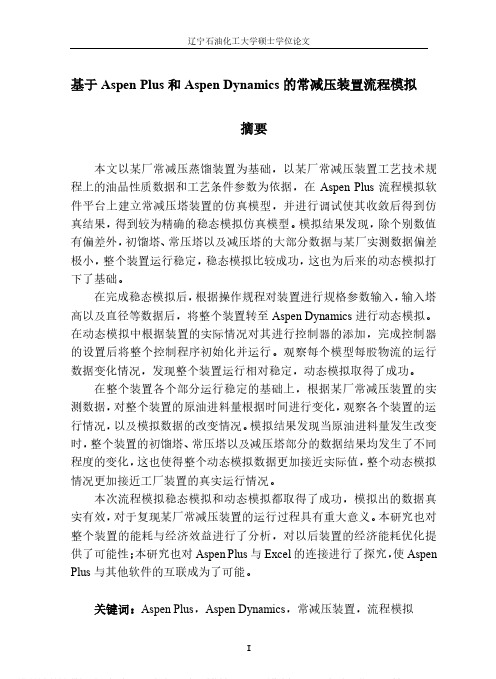
基于Aspen Plus和Aspen Dynamics的常减压装置流程模拟摘要本文以某厂常减压蒸馏装置为基础,以某厂常减压装置工艺技术规程上的油品性质数据和工艺条件参数为依据,在Aspen Plus流程模拟软件平台上建立常减压塔装置的仿真模型,并进行调试使其收敛后得到仿真结果,得到较为精确的稳态模拟仿真模型。
模拟结果发现,除个别数值有偏差外,初馏塔、常压塔以及减压塔的大部分数据与某厂实测数据偏差极小,整个装置运行稳定,稳态模拟比较成功,这也为后来的动态模拟打下了基础。
在完成稳态模拟后,根据操作规程对装置进行规格参数输入,输入塔高以及直径等数据后,将整个装置转至Aspen Dynamics进行动态模拟。
在动态模拟中根据装置的实际情况对其进行控制器的添加,完成控制器的设置后将整个控制程序初始化并运行。
观察每个模型每股物流的运行数据变化情况,发现整个装置运行相对稳定,动态模拟取得了成功。
在整个装置各个部分运行稳定的基础上,根据某厂常减压装置的实测数据,对整个装置的原油进料量根据时间进行变化,观察各个装置的运行情况,以及模拟数据的改变情况。
模拟结果发现当原油进料量发生改变时,整个装置的初馏塔、常压塔以及减压塔部分的数据结果均发生了不同程度的变化,这也使得整个动态模拟数据更加接近实际值,整个动态模拟情况更加接近工厂装置的真实运行情况。
本次流程模拟稳态模拟和动态模拟都取得了成功,模拟出的数据真实有效,对于复现某厂常减压装置的运行过程具有重大意义。
本研究也对整个装置的能耗与经济效益进行了分析,对以后装置的经济能耗优化提供了可能性;本研究也对Aspen Plus与Excel的连接进行了探究,使Aspen Plus与其他软件的互联成为了可能。
关键词:Aspen Plus,Aspen Dynamics,常减压装置,流程模拟Process simulation of atmospheric and vacuum distillation unit based on Aspen Plus and Aspen DynamicsABSTRACTIn this thesis, based on the atmospheric and vacuum distillation unit in a plant, the oil property data and process condition parameters in the process specification of atmospheric and vacuum unit in a plant are used as the basis, and the simulation model of atmospheric and vacuum tower unit is established on Aspen Plus process simulation software platform. After debugging, the simulation results are obtained after convergence, and a more accurate steady-state simulation model is obtained. The simulation results show that most of the data of the primary distillation tower, atmospheric pressure tower and pressure reducing tower have little deviation from the measured data of a certain plant, the whole unit runs stably and the steady-state simulation is relatively successful, which also lays a foundation for the later dynamic simulation.After the completion of the steady-state simulation, the specification parameters of the device are input according to the operation procedures, and the tower height and diameter data are input, the whole device is transferred to Aspen Dynamics for dynamic simulation. In the dynamic simulation, the controller is added according to the actual situation of the device. After the controller is set, the whole control program is initialized and run. By observing the operation data of each model, it is found that the operation of the whole device is relatively stable and the dynamic simulation is successful.On the basis of stable operation of each part of the whole unit, according to the measured data of atmospheric and vacuum unit in a certain plant, the crude oil feeding amount of the whole unit changes according to time, and the operation of each unit is observed, as well as the change of simulation data. Thesimulation results show that when the crude oil feed quantity changes, the data results of the primary distillation tower, atmospheric pressure tower and pressure reducing tower of the whole unit have changed in varying degrees, which also makes the whole dynamic simulation data closer to the actual value and the whole dynamic simulation situation closer to the real operation of the plant.The steady-state simulation and dynamic simulation of this process have been successful, and the simulated data are real and effective, which is of great significance for the recurrence of the operation process of atmospheric and vacuum distillation unit in a plant. This study also analyzes the energy consumption and economic benefits of the whole device, and provides the possibility for the optimization of the economic energy consumption of the device in the future; this study also explores the connection between Aspen Plus and excel, making the interconnection between Aspen Plus and other software possible.KEYWORDS: Aspen Plus, Aspen Dynamics, Atmospheric and vacuum unit, Process simulation目录摘要 (I)ABSTRACT (III)1绪论 (1)1.1课题的研究背景及意义 (1)1.2化工流程模拟技术 (1)1.3流程模拟的应用 (2)1.4流程模拟在常减压装置中的应用 (3)1.5本文结构介绍 (3)2常减压装置的工艺流程 (5)2.1常减压装置在原油加工中的地位 (5)2.2常减压装置的原理 (5)2.3流程模拟软件算法原理 (6)2.3.1稳态模拟 (6)2.3.2动态模拟 (9)2.4常减压装置的工艺流程 (10)2.5小结 (11)3常减压装置的稳态模拟 (13)3.1建立整个装置模型 (13)3.1.1原油虚拟组分切割 (13)3.1.2装置模型选型 (15)3.2物料连接 (23)3.2.1 物流连接说明 (23)3.2.2 模型组态 (24)3.3数据输入与选项设置 (35)3.3.1初馏塔数据 (35)3.3.2常压塔数据 (37)3.3.3减压塔数据 (42)3.3.4原油进料数据 (49)3.3.5加热器、冷凝器与空冷器数据 (49)3.3.6泵数据 (50)3.3.7调节阀数据 (51)3.3.8分离罐数据 (51)3.3.9分离器数据 (52)3.4装置收敛调试 (53)3.4.1选择收敛方法 (55)3.4.2调节塔本身迭代次数与公差 (55)3.4.3调节整个装置迭代次数 (56)3.4.4设置撕裂物流 (56)3.4.5调节蒸汽汽提量 (58)3.4.6调节中段回流量 (58)VI3.5稳态模拟的模拟结果与数据分析 (59)3.5.1初馏塔部分 (59)3.5.2常压塔部分 (59)3.5.3减压塔部分 (60)3.6小结 (61)4常减压装置的动态模拟 (63)4.1Aspen Plus动态参数设置 (63)4.1.1初馏塔规格输入 (63)4.1.2常压塔规格输入 (65)4.1.3减压塔规格输入 (67)4.1.4其他模型规格修改 (69)4.2Aspen Dynamics控制器设置 (71)4.2.1转至Aspen Dynamics (71)4.2.2初馏塔控制器设置与调试 (73)4.2.3常压塔控制器设置与调试 (79)4.2.4减压塔控制器设置与调试 (82)4.3动态模拟的收敛调试 (84)4.4动态模拟结果与数据分析 (90)4.4.1初馏塔部分 (90)4.4.2常压塔部分 (95)4.4.3减压塔部分 (100)VII4.5小结 (109)5流程模拟的应用与扩展 (111)5.1稳态模拟结果与Excel的连接 (111)5.2稳态模拟结果经济能耗分析 (115)5.3小结 (118)6总结 (119)参考文献 (121)致谢 (126)VIII1绪论1.1课题的研究背景及意义石油炼制工程是需要消耗高能源的工程,它所消耗的能量占全国工业总能耗中的绝大部分比例。
应用ASPENPLUS建立常减压装置的模拟系统(2)
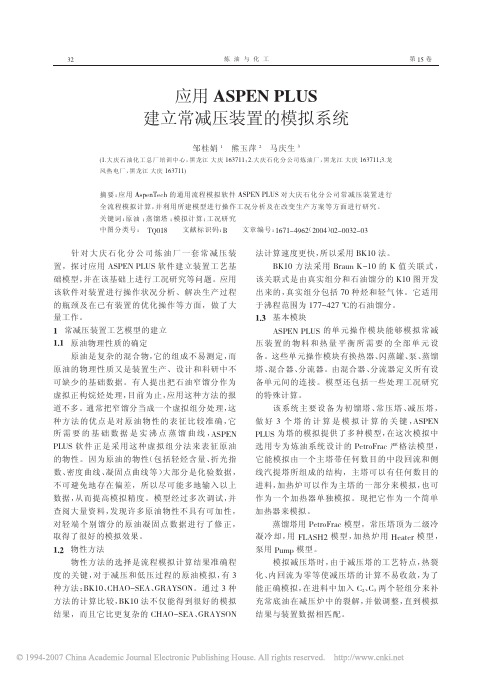
常一线航煤 常二线柴油
"6)$ 5*
#’6) *"/
5%*
从表 ! , /, #, % 看出, ! 计算的塔的回流比为
#6),与实际的回流比 #6$ 相近; " 计算的产品航
煤、 柴油的馏程分布与标定值基本一致, 常顶油稍 低, 航煤密度为 "6))$ , 不小于 "6))%8 见表 *9; 闪点 为 #’6) 2 , 不小于 /$ 2 ; 冰点 5%* 2 ; 常二线柴油 凝固点为 5* 2 , 介于 "75) 2 之间; 闪点为 *"/ 2 , 不小于 ’) 2。 从以上数据分析看, 侧线产品指标均 能满足要求。 航煤抽出量为 !) /%" +3 - > , 标定值为 相对误差 *6# & , 抽出 /1 ")" +3 - >, 标 !) )’’ +3 - >, 定量 /) )!#+3 - > , 相对误差 "6$ & ; # ?@<AB <CD@ 还可以做出塔内汽液负荷分布、塔板温度分布图 等, 为生产提供指导 =见图 !、 /。
图 # 常压塔板温度分布
" 生产方案改变的模拟计算
随着市场需求或季节的变化,大庆石化分公 司炼油厂一套常减压装置从航煤生产切换到生产 高煤方案, 生产相应地需要进行调整, 如降一中量 等。利用这套模型, 根据高煤生产方案的产品质量 要求,调整模型中产品规定的范围及相关的独立 变量, 可以很快得出高煤生产方案下的工艺参数,
)/ $" *"" **/ *!) *#)
*’% *)1 *$" !"# !!* !#"
AspenPlus蒸馏中的作用
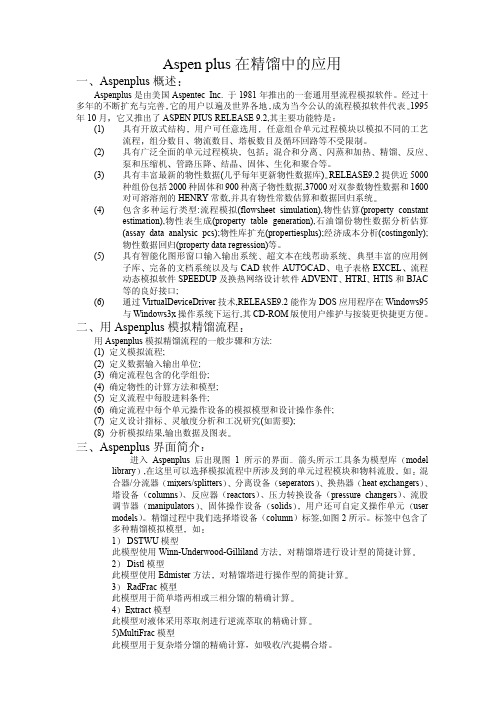
Aspen plus 在精馏中的应用 一Aspenplus 概述Aspenplus 是由美国Aspentec Inc. 于1981年推出的一套通用型流程模拟软件经过十多年的不断扩充与完善它的用户以遍及世界各地成为当今公认的流程模拟软件代表1995年10月它又推出了ASPEN PIUS RELEASE 9.2,其主要功能特是(1)具有开放式结构用户可任意选用任意组合单元过程模块以模拟不同的工艺流程组分数目物流数目塔板数目及循环回路等不受限制(2) 具有广泛全面的单元过程模块包括混合和分离闪蒸和加热精馏反应泵和压缩机管路压降结晶固体生化和聚合等(3) 具有丰富最新的物性数据(几乎每年更新物性数据库)RELEASE9.2提供近5000种组份包括2000种固体和900种离子物性数据,37000对双参数物性数据和1600对可溶溶剂的HENRY 常数,并具有物性常数估算和数据回归系统(4) 包含多种运行类型:流程模拟(flowsheet simulation),物性估算(property constantestimation),物性表生成(property table generation),石油馏份物性数据分析估算(assay data analysic pcs);物性库扩充(propertiesplus);经济成本分析(costingonly);物性数据回归(property data regression)等(5) 具有智能化图形窗口输入输出系统典型丰富的应用例子库完备的文档系统以及与CAD AUTOCAD 电子表格EXCEL 流程动态模拟软件SPEEDUP HTRI HTIS 和BJAC等的良好接口;(6) 通过VirtualDeviceDriver 技术,RELEASE9.2能作为DOS 应用程序在Windows95与Windows3x 操作系统下运行,其CD-ROM 版使用户维护与按装更快捷更方便二用Aspenplus 模拟精馏流程用Aspenplus 模拟精馏流程的一般步骤和方法:(1) 定义模拟流程; (2) 定义数据输入输出单位; (3) 确定流程包含的化学组份; (4) 确定物性的计算方法和模型;(5) 定义流程中每股进料条件;(6) 确定流程中每个单元操作设备的模拟模型和设计操作条件; (7) 定义设计指标灵敏度分析和工况研究(如需要);(8) 分析模拟结果,输出数据及图表 三Aspenplus 界面简介进入Aspenplus 后出现图1所示的界面箭头所示工具条为模型库modellibrary ,在这里可以选择模拟流程中所涉及到的单元过程模块和物料流股如混合器/分流器mixers/splitters分离设备seperators换热器heat exchangers塔设备columns 反应器reactors 压力转换设备pressure changers 流股调节器manipulators 固体操作设备solids 用户还可自定义操作单元user models 精馏过程中我们选择塔设备column 标签,如图2所示标签中包含了多种精馏模拟模型如1 DSTWU 模型此模型使用Winn-Underwood-Gilliland 方法对精馏塔进行设计型的简捷计算 2 Distl 模型此模型使用Edmister 方法对精馏塔进行操作型的简捷计算3 RadFrac 模型此模型用于简单塔两相或三相分馏的精确计算4Extract 模型此模型对液体采用萃取剂进行逆流萃取的精确计算5)MultiFrac 模型此模型用于复杂塔分馏的精确计算如吸收/汽提耦合塔欢迎访问/forum-405-1.html,流程模拟根据地图1 图26SCFrac 模型 复杂塔的精馏简捷计算如常减压蒸馏塔和真空蒸馏塔 7PetroFrac 模型 此模型用于石油精炼中的分馏精确计算如预闪蒸塔8RateFrac 模型 此模型用于基于非平衡模型的操作型分馏精确计算 9BatchFrac 模型 此模型用于两相或三相间歇式精馏的精确计算 操作单元模块左侧为流股单元从中可选择物流热流和功 流股单元上侧的小箭头可用来选择流程图中的对象 模型库上方的空白页面为流程图其上可使用模型库中的操作单元和流股单元绘制工艺流程图下面结合一个精馏设计型算例来具体介绍Aspenplus 模拟流程的过程 四设计型计算设计任务在常压连续筛板精馏塔中精馏分离含苯41%的苯甲苯混合液要求塔顶馏出液中含甲苯量不大于4塔底釜液中含甲苯量不低于96以上均为质量分率已知参数 苯甲苯混合液处理量4t/h 进料热状态自选回流比自选塔顶压强4kPa 表压热源低压饱和水蒸汽单板压降不大于0.7kPa 计算中所用物性数据由Aspenplus 自己提供或计算 1定义模拟流程;1 在模型库中选择塔设备column 标签如图3所示2 选择DSTWU 模型进行设计型简捷计算点击该模型的向下箭头弹出三个等效的模块任选其一如图4所示图3 3在空白流程图上单击即可绘出一个精馏塔模型如图5所示该模型可用三种方法进行放大 a 可双击流股单元上侧的小箭头在流程图上单击鼠标右键选择zoom in 放大或选择zoom out 缩小整个图面b) 可双击流股单元上侧的小箭头进入选取对象模式单击精馏塔图标将其选中将鼠标移至对角线的端部直接拖拽即可放大或缩小直到满意的图形大小为止图4图5c) 点击view 菜单栏中的zoom 子菜单选择zoom in 或zoom out 进行放大或缩小放大后的流程图如图6所示4图63我们在图6的基础上绘制流股单击流股单元向下箭头选择流股类型在这里我们选择material类型选择后得到图7所示图7在箭头提示下我们可以根据需要来绘制流股其中红色箭头表示必须定义的流股蓝色箭头表示可选定义的流股不同的模型我们根据设计任务绘制一股进料塔顶和塔底两股出料得到图8图8为了便于后续操作我们可以改变流股和模块的名称方法如下单击流股或模块点击鼠标右键在弹出的菜单中选择rename stream或rename block即可改变名称在对话框中输入改后的名称在这里我们将入料改为FEED塔顶出料改为D塔底出料改为L改变名称后的流程图如图9所示(2)定义数据输入输出单位;点击data 菜单中的setup,出现初始化设置窗口如图10系统自身有一套默认的设置同时用户也可以根据要求来自己修改或定义包括单位及其他全局设置在这里我们使用系统默认的设置图10 3确定流程包含的化学组份在窗口左侧的目录树结构中选择components 文件夹进行化学组分定义点击其下的specification 出现图11所示窗口在此窗口中我们可以定义流程中所涉及的化学组分定义方法如下a) 可以在component ID或component name中直接输入组分的英文名称b) 可以使用Aspenplus提供的find工具单击find按钮出现如图12所示的窗口图12在出现的对话框中可以输入组分的英文名称或分子式也可以输入其部分字符串这里我们输入分子式c6h6按回车键或点击find now按钮出现窗口如图13图12再选择所需组分点击窗口下侧的add按钮该组分就被添加到组分列表中关闭对话框后的窗口如图14所示图14其中Component ID是该组分的代号用户可以进行修改用同样方法输入甲苯组分结果如图15所示图15(4) 确定物性的计算方法和模型在窗口左侧的目录树结构中选择properties文件夹进行物性设置点击其下的specification出现图16所示窗口图16在该窗口中我们可以定义流程类型物性计算方法等根据不同的物系选择不同的物性计算方法对于理想物系可以选择Ideal方法非理想物系可选择典型的Wiston或Uniquac等方法电解质溶液也有其相应的计算方法在这里苯和甲苯体系可近似看成理想系我们选择Ideal方法其他设置由系统默认确定5定义流程中每股进料条件在窗口左侧的目录树结构中选择streams文件夹将可看到我们先前在流程图中定义的三股物料D FEED L其中FEED流股为已知流股D L流股为待定流股故我们仅定义FEED流股的状态参数选择FEED文件夹中的Input后出现如图17所示窗口进料热状态在state variables中定义若为过冷液体或过热气体可通过指定压力和温度定义若为气液混合进料可通过指定气相分率和温度或压力之一来定义在这里我们选取进料热状态为饱和液体在Vapor fraction中输入0在pressure中输入1atm 下来可以定义物料的流量根据不同需要可以定义摩尔体积质量或标准体积流量在这里我们用质量流量输入4000kg/hr下面定义组分流量或组分分率我们在这里选用质量分率在相应组分后输入其质量分率输入数据后的窗口如图18所示图186确定流程中每个单元操作设备的模拟模型和设计操作条件在此流程中只有column这一个Dstwu模型下面定义这个模型在窗口左侧的目录树结构中选择Blocks文件夹将可看到我们先前在流程图中定义的column模型选择column文件夹中的Input后出现如图19所示窗口此模型既可以定义塔板数进行操作型计算又可以定义回流比进行设计型计算由于我们进行的是设计型计算在这里定义回流比定义回流比时有两种定义方法定义回流比的实际值或定义回流比与最小回流比的比值前者直接输入数值即可后者输入负号后再入数值在这里我们取最小回流比的2倍故输入-2接下来定义轻重关键组分的回收率来确定分离要求经过计算可得轻关键组分的回收率为0.9859重关键组分的回收率为0.0285接下来定义再沸器和冷凝器的压力在一般的精馏设计中再沸器和冷凝器的压力比较接近大气压力且再沸器压力高于冷凝器压力这里我们分别取为110kPa 和105kPa 冷凝器使用全凝器其余设置由系统默认确定输入数据后的窗口如图20所示到此数据输入完毕可以进行计算点击工具栏中的蓝色N->图标即可进行计算该图标的作用是进行下一步操作若数据未输入完毕自动转到待输入数据的窗口若数据输入完毕则进行计算计算完毕后窗口如图21所示也可点击Run 菜单中的run 命令来直接进行计算图20结果生成后即可查看点击箭头所指文件夹出现如图22所示窗口图22点击左侧的Streams文件夹或Blocks文件夹即可查看物流或模块模型的计算结果点击Blocks文件夹点击子文件夹Column中的Results可看到塔的设计参数包括最小回流比实际回流比最小理论板数实际理论板数冷凝器和再沸器的热负荷等如图23所示其计算出的塔板数与最小回流比同图解法的结果相近比较如下计算数据图解法计算数据*物理量 Aspenplus理论塔板数12.775 13.5 最小回流比 1.3665 1.38 *计算数据及过程参见<<化工原理课程设计>> 柴诚敬等编天津科学技术出版社出版 P97同理点击相应文件夹可以查看物流Feed D L 的参数为了进一步熟悉DSTWU 模型我们依据上面的设计型计算结果进行操作型计算检验其结果的可靠性 五操作型计算精馏塔塔板数为上述计算的结果13其它已知条件与设计型计算基本相同计算实际操作时的回流比 在操作型计算中流程模拟的前5步与设计型计算相同在第6步中设计型计算定义精馏塔的回流比而操作型计算定义塔板数这里我们定义塔板数为13其它条件不变输入数据后的窗口如图24所示点击N->计算结果窗口如图25所示图24在设计型计算中回流比为 2.73塔板数为12.78而在操作型计算中我们将塔板数取为13得到的回流比为2.66由两次计算结果可以看出结论比较可靠到此为止我们针对一个具体的算例对精馏流程作了设计型和操作型分析由于在实际问题中我们比较关心一个变量随另一个变量变化的趋势既所谓的灵敏度分析这一方法可用来进行流程的优化下来我们结合具体的实例来介绍在Aspen plus 中如何进行灵敏度分析 六灵敏度分析 1设计型计算中回流比对塔板数的影响在图26中把窗口切换至input 输入窗口所得结果如图27所示:在图27中点击左侧Model Aalysis Tools 文件夹中的子文件夹sensitivity 得到如图28所示的窗口:点击窗口中的new 按钮建立一个新的灵敏度分析任务在弹出的对话框中输入该任务的名称N-R 确定后得到窗口如图29所示在这个界面中我们定义该灵敏度分析过程中所涉及的变量,包括理论塔板数和回流比点击New 按钮输入新变量名称N 确定后出现如图30所示窗口在该窗口中定义变量N 的属性即具体含义该窗口左侧可以定义变量所属的类型这样可以缩小我们的参考范围其中All 包括所有类型的变量Blocks 包括所有模块变量Streams 包括所有物流变量Property 包括所有物性变量Costing 包括所有与经济指标相关的变量N 代表理论塔板数是精馏塔的参数因此选择Block 在type 中选择Block Var 说明N 是一个模块变量在Block 中选择Column 模块表明N 是模型Column 的变量在Variable 中选择Act Stages塔板数定义后的窗口如图31所示点击N->按钮完成定义用类似的方法定义回流比变量R 定义后窗口如图32所示得到的最终变量列表如图33所示定义完变量后说明灵敏度分析中的操作变量回流比及其变化范围选中Vary 标签进行定义类似于变量定义的方法定义操作变量选择所属类型模块及其意义选择Overall range 定义其变化范围这里我们将上限Upper 和下限lower 分别定义为4和1.37应注意下限应大于其最小回流比否则系统提示计算出错在point 中可以输入运算的点数点数越多则拟合出的曲线越光滑但运算量越大在这里我们取50个点数据输入完毕后的窗口如图34所示选择Tabulate 标签定义因变量N 在Column No.中输入1在tabulate variable 中输入N 完成后的窗口如图35所示到此该灵敏度分析的数据输入部分已完成点击N->图标进行计算计算结果如图36所示我们可以用计算出来的数据作图观察N 随R 的变化趋势选中Vary1一列在Plot 菜单中选择X Axis Variable 定义RR 为x 轴变量选中N 一列在Plot 菜单中选择Y Axis Variable 定义N 为y 轴变量在Plot 菜单中选择Display Plot 即可作出图表得到的图表如图37所示在图表空白处双击得到如图38所示窗口在该窗口中可以设定图表的属性及一些参数由于Aspenplus 可能将先前输入的回流比2实际意义为最小回流比的2倍作为一个数据点因此该图表的起点为2在-21.37区间上的曲线没有意义在分析过程中不予考虑由得到的图表可知接近最小回流比处塔板数随回流比的增大而急剧减小且随着其继续增大变化趋于平缓且在回流比大于3时塔板数基本不变可以结合根据具体情况选择比较经济的操作回流比值得一提的是尽管Aspenplus 对数据处理的能力不强仅能由数据点做出曲线但是其数据可以通过Copy 命令复制并使用Paste 命令粘贴到其他功能强大的数据处理软件中例如Excel Origin 等为了进一步熟悉灵敏度分析这一重要的方法我们再做一个设计型计算中轻关键组分回收率对理论塔板数影响的灵敏度分析 2轻关键组分回收率对理论塔板数影响 点击灵敏度分析创建窗口图28中的new 按钮建立一个新的灵敏度分析任务在弹出的对话框中输入该任务的名称N Recovl 确定后得到窗口如图39所示在该窗口中如前述方法定义两个变量Recovl N 其中Recovl 是表示轻关键组分的回收率定义完后窗口如图40所示N 同前得到的最终变量列表如图41所示计算点数同前输入完毕后如图42所示在Tabulate 标签栏中设置不变图42到此该灵敏度分析的数据输入部分已完成点击N->图标进行计算计算结果如图43所示下面我们用所得的结果作图分析得到的图的方法与上相同选中Vary1一列在Plot菜单中选择X Axis Variable定义Recovl为x轴变量选中N一列在Plot菜单中选择Y Axis Variable定义N为y轴变量在Plot菜单中选择Display Plot即可作出图表得到的图表如图44所示图44由图可以看出轻组分的回收率在0.9500.999之间变动时随着它的的增大塔板数随之增大特别指出的是从回收率大于0.990以后随着回收率的增大理论塔板数急剧增大在实际生产过程中应该结合分离要求和经济因素选择一个合理回收率由以上可以看出通过进行灵敏度分析选取适当的操作变量值不仅可以达到分离要求而且可以降低经济投入因此灵敏度分析是一个十分重要的方法应该熟练掌握下面再介绍一些Aspenplus使用过程中值得注意的一些技巧和方法七Aspenplus使用技巧Aspenplus是一套比较智能化的系统对于同一操作可有不同的操作方法而且对于用户应该做什么和如何做都有比较详细的指示和说明下面就举几例方便大家的操作1比较细心的同学可能注意到在输入窗口左侧的文件夹上有不同的标志和等其中红色标志表示该项目的数据输入未完成蓝色则表示已完成根据不同的标志我们可以确定该输入哪些数据并确定数据是否输入完毕在结果窗口中也有相应的标志代表结果正确或计算有误这些标志大大方便了我们的数据输入和结果判断工作2Aspenplus软件的窗口右下角是状态栏它表示当前工作所处的阶段和状态在数据输入未完成时显示Required input incomplete在数据输入完毕已可进行计算时显示Input complete计算完毕后结果是否正确可靠也有相应的提示通过这些提示我们可以确定结果的可信度3正如前面提及的Aspenplus提供一个下一步按钮N->在设计过程的任意时刻点击它系统都会自动跳转到当前应当进行的工作并弹出一个窗口对此操作进行详尽的说明这为我们输入数据提供了极大的方便4同大家所熟悉的常用软件一样Aspenplus也提供右键快捷菜单在该菜单中包括了当前状态下可以进行的大部分操作适当的使用右键菜单可以加速我们的设计过程从而缩短设计时间八结束语Aspenplus 是一个功能十分强大的流程模拟软件在化工系统设计及优化过程中得到了广泛的应用上述仅讨论了如何用其来设计精馏塔及一些影响精馏塔设计因素的灵敏度分析实际上使用该软件的其他塔模型如RadFrac可进一步进行部分塔板参数的设计计算因此如何选择一个适当的模型来满足我们的设计需求也相当重要由于Aspenplus我们提供了很多不同功能的模型这就要求我们在平时多练习多积累一些模型的用法到实际使用时不至于不知如何下手总之希望大家能够多摸索多练习多总结熟练掌握Aspenlus软件目前我们使用的Aspenplus是英文版本的大家在使用过程中难免遇到一些不常见或不清楚意思的英文单词为此我们编制了叙词表方便大家查阅叙词表atm 1atm为一个标准大气压Bar 巴压力单位BaseMethod 基本方法包含了一系列物性方程Batch 批量处理BatchFrac 用于两相或三相间歇式精馏的精确计算Benzene 苯Blocks 模型所涉及的塔设备的各个参数Block-Var 模块变量ChemVar 化学变量Columns 塔Columnspecifications 塔规格CompattrVar 组分变量Components 输入模型的各个组成ComponentsId 组分代号Componentsname 组分名称Composition 组成Condenser 冷凝器Condenserspecifications 冷凝器规格Constraint 约束条件Conventional 常规的Convergence 模型计算收敛时所涉及到的参数设置Databrowser 数据浏览窗口Displayplot 显示所做的图Distl 使用Edmister方法对精馏塔进行操作型的简捷计算DSTWU 使用Winn-Underwood-Gilliland方法对精馏塔进行设计型的简捷计算 DV:D 精馏物气相摩尔分率ELECNRTL 物性方程适用于中压下任意电解质溶液体系Extract 对液体采用萃取剂进行逆流萃取的精确计算Find 根据用户提供的信息查找到所要的物质Flowsheetingoptions 流程模拟选项Formula 分子式Gasproc 气化Heat Duty 热负荷HeatExchangers 热交换器Heavy key 重关键组分IDEAL 物性方程适用于理想体系Input summary 输入梗概Key component recoveries 关键组分回收率kg/sqcm 千克每平方厘米Lightkey 轻关键组分Manipulated variable 操作变量Manipulators 流股调节器Mass 质量流量Mass-Conc 质量浓度Mass-Flow 质量流量Mass-Frac 质量分率Materialstreams 绘制流程图时的流股包括work(功)heat热和material物料mbar 毫巴Mixers/splitters 混合器/分流器Mmhg 毫米汞柱mmwater 毫米水柱Model analysis tools 模型分析工具Model library 模型库Mole 摩尔流量Mole-Conc 摩尔浓度Mole-Flow 摩尔流量Mole-Frac 摩尔分率MultiFrac 用于复杂塔分馏的精确计算如吸收/汽提耦合塔N/sqm 牛顿每平方米NSTAGE 塔板数Number of stages 塔板数Oil Gas 油气化Optimization 最优化Overallrange 灵敏度分析时变量变化范围Pa 国际标准压力单位PACKHEIGHT 填料高度Partial condenser with all vapor distillate 产品全部是气相的部分冷凝器Partial condenser with vapor and liquid distillate 有气液两相产品的部分冷凝器PBOT 塔底压力PENG-ROB 物性方程适用于所有温度及压力下的非极性或极性较弱的混合物体系 Petchem 聚酯化合物PetroFrac 用于石油精炼中的分馏精确计算如预闪蒸塔Plot 图表PR-BM 物性方程适用于所有温度及压力下非极性或者极性较弱的体系 Pressure 压力PressureChangers 压力转换设备PRMHV2 物性方程适用于较高温度及压力下极性或非极性的化合物混合体系 Process type 处理类型Properties 输入各物质的物性Property methods & models 物性方法和模型psi 英制压力单位psig 磅/平方英寸(表压)PSRK 物性方程适用于较高温度及压力下极性或非极性的轻组分气体化合物体系 PTOP 塔顶压力RadFrac 用于简单塔两相或三相分馏的精确计算RateFrac 用于基于非平衡模型的操作型分馏精确计算Reactions 模型中各种设备所涉及的反应Reactors 反应器ReactVar 反应变量Reboiler 再沸器RECOVH 重关键组分回收率RECOVL 轻关键组分回收率Refinery 精炼Reflux ratio 回流比Reinitialize 重新初始化Result summary 结果梗概Retrieve parameter results 结果参数检索RKS-BM 物性方程适用于所有温度及压力下非极性或者极性较弱的体系 RKSMHV2 物性方程适用于较高温度及压力下极性或非极性的轻组分气体化合物体系 RK-SOA VE 物性方程适用于所有温度及压力下的非极性或极性较弱的混合物体系 RKSWS 物性方程适用于较高温度及压力下极性或非极性的轻组分气体化合物体系 RR 回流比Run status 运行状态SCFrac 复杂塔的精馏简捷计算如常减压蒸馏塔和真空蒸馏塔Sensitivity 灵敏度Separators 分离器Solids 固体操作设备SR-POLAR 物性方程适用于较高温度及压力下极性或非极性的轻组分气体化合物体系 State variables 状态变量Stdvol 标准体积流量Stdvol-Flow 标准体积流量Stdvol-Frac 标准体积分率Stream 各个输入输出组分的流股StreamVar 流股变量Substream name 分流股类型Temperature 温度Toluene 甲苯Torr 托真空度单位Total condenser 全凝器Total flow 总流量UNIQUAC 物性方程适用于极性和非极性强非理想体系UtilityVar 公用工程变量Vaiable number 变量数Vaporfraction 汽相分率V olume 体积流量X Axisvariable 作图时的横坐标变量Y Axisvariable 作图时的纵坐标变量。
基于AspenPlus的常压蒸馏装置流程优化

第36卷增刊2009年北京化工大学学报(自然科学版)Jour nal of Beijing U niversity of Chemical T echnolog y (N atural Science)V ol.36,Sup.2009基于Aspen Plus 的常压蒸馏装置流程优化张 哲 卢 涛*(北京化工大学机电工程学院,北京 100029)摘 要:为增加年综合收益,应用流程模拟软件Aspen Plus 对某厂一套常压蒸馏装置进行流程优化。
在流程模拟的基础上,给定约束条件,优化决策变量,建立了以年综合收益最大为目标函数的优化模型,并在Aspen Plus 平台上进行二次开发,对优化模型进行了求解,获得了良好的优化结果,详细分析了产品收益与泵动力消耗、加热和冷却负荷以及蒸汽消耗等成本对年综合收益的贡献率及影响。
最终得到了年综合收益最大化下的各工艺参数。
关键词:Aspen Plus;流程优化;常压蒸馏;年收益中图分类号:T K 065收稿日期:2008 10 06第一作者:男,1983年生,硕士生*通讯联系人E mail:likesurg e@引 言随着市场竞争日益激烈和原油价格的上浮,如何采用信息化技术实现常减压蒸馏装置的全流程模拟与优化,以提高经济效益,越来越受到人们的关注[1 2]。
目前Aspen Plus 是广泛应用于化工流程开发和设计的大型流程模拟与优化软件[3 4],采用这项信息化技术可以有效的实现化工工艺全流程的模拟与优化。
魏忠[5]主要采用PRO/ 模拟软件对常减压蒸馏装置的热力学模型进行讨论及对精馏塔进行物料及热量的衡算,但缺乏操作参数对于整个系统影响的分析,邹桂娟[6]用Aspen Plus 建立了常减压装置的模拟系统,但没有在流程模拟的基础上进行二次开发来满足进一步的工艺要求。
本文以某炼油厂一套常压装置为研究对象,在Aspen Plus 11 1平台上编写计算年综合收益的Fortran 程序,选用常压塔汽提蒸汽流量为优化变量,以常压塔各产品的恩氏蒸馏温度为约束条件,使得常压蒸馏装置的年综合收益最大。
化工设计中流程模拟软件Aspen Plus的使用

4结 语
市场的热 需促使 L N G 车 用市场快速 发展 , 但我 们也应该 明 积极 推广 L N G汽车 优势 , 切 实解决 油改 L N G技 术难 题 , 形成 一 确 L N G产业 不能滥 发展 , 要 适时 适宜 , 逐步 形成加 气站 网络 覆 定 的改 装验 收标 准 , 才能 惠及 大众 , 切 实促进 L N G车用 市场 长
以, L N G在这 个范 围内的发 展 前景 是十 分看 好 的 。同时 , L N G
【 2 ] 王华北. 我国L N G工业发展及应用研 究[ D 】 , 2 0 0 9 . [ 3 】 霍 自成. 青藏两省 区L N G应用的市场分析及发展策略研
D 1 , 2 0 1 2 . 储运 装备也 正在朝 着多样化 的方 向发 展 , 加快L N G产业在 天然 究【 『 4 ] 廖 子夏. 四川省天 然气 车用市场 发展现 状及 前景分析 [ J ] . 气应用市场 新技 术的融 合 , 在天然 气应用 中还有一 些新技 术是 2 0 1 3 ( 2 0 ) . 可以与 L i N G产业共 同发展的 , 例如 C N G 储存 与运输方 面的一些 技术 与市场 , [ 5 】 渐入佳 境 的L N G商用汽 车[ J ] . 交通世界 , 2 0 1 2 ( 1 2 ) . 新 装备 与新 方法 , N G r I ( 天然 气水合物) 的生 产与运送 技术 , A N G
型重 载运输 车 等可 采用 L N G作为燃 料 。而对 于各 类船舶 更是
参考文献 :
[ 1 】 中国车用 L N G市场发 展 与加气 站建设 趋 势[ J 1 .
T R uc K &L 0 G I s r r I c s , 2 0 1 2  ̄ ) .
AspenPlus应用技术介绍ZZ

建立流程图 组分数据 物性方法 物流数据 单元操作模型数据 其它数据
热力学 方程
单元操作 方程
数学 方程
如何能学习好Aspen Plus??
1、在不断使用中学习 2、利用好各种中英文培训和使用手册 3、Aspen Plus自带的帮助文档 4、利用好Aspen Plus软件附带的实例 5、参加Aspen Plus软件相关的高级培训
钮
后一个 表页按
钮
菜单树
提示域
状态指示符号
符号
意义 该表输入未完成 该表输入完成 该表中没有输入,是可选项 对于该表有计算结果 对于该表有计算结果,但有计算错误 对于该表有计算结果,但有计算警告 对于该表有计算结果,但生成结果后输入发生改变
建立模拟模型的基本步骤
1. 启动User Interface 2. 选用Template 3. 选用单元操作模块:Model Blocks 4. 连结流股:Streams 5. 设定全局特性:Setup Global Specification 6. 输入化学组分信息 Components 7. 选用物性计算方法和模 8. Property Methods & Models
从数据浏览器的Pump对象下选择Results查看结果
Pump的示例
一水泵将压强为 1.5 bar 的水加压到 6 bar,水的温度为 25 C,流量为 100 m3/h。 泵的效率为 0.68,驱动电机的效率为 0.95。
求:泵提供给流体的功率、泵所需要的 轴功率、以及电机消耗的电功率各是多少?
简称Aspen,意为“过程工程的先进系统”。 1976年由美国能源部资助,麻省理工学院
主持、55个高校和公司参与开发。1982年为了 将其商品化,成立了AspenTech公司,并称之 为Aspen Plus。
Aspen Plus在精馏操作分析中的应用

Aspen Plus在精馏操作分析中的应用精馏是化工行业中应用很广的一种工艺操作。
影响精馏效果的因素很多,往往一个因素发生变化时,会牵扯到一些其他因素发生变化。
这使得精馏过程变得颇为灵活和复杂。
如何有效的对精馏操作进行全面详细的分析一直是技术人员的研究难点和重点。
本文简要介绍了Aspen Plus软件,并详细探讨了它在精馏操作分析中的实际应用,供大家学习交流。
标签:Aspen Plus;精馏操作;分析;应用前言精馏是化工行业中应用很广的一种工艺操作。
影响精馏效果的因素的是多方面的,主要包括分离物的组成和性质、操作过程和设备的物理参数等等。
往往一个因素发生变化时,会牵扯到一些其他因素发生变化。
由于这些影响因素多呈非线性变化,使精馏过程变得颇为灵活和复杂,如何有效的对精馏操作进行全面详细的分析一直是技术人员的研究难点和重点。
1 精馏塔的分类和原理简介精馏塔又名蒸馏塔,是一种进行蒸馏的气液塔式接触装置,主要有填料塔和板式塔两种类型,根据操作方式的不同又可以分为间隙精馏塔和连续精馏塔。
整个物料变化过程就是气相物质和液相物质相互作用的过程,首先气相从塔底进入塔内,与塔内下降的液相接触,气相中难挥发的物质源源不断的向液相转化,与此同时,液相中容易挥发的物质也会转化到气相中去,随着工序的继续,重组分在塔底积聚,轻组分流向塔顶,逐步实现轻重组分的分离。
分离出的气相进入冷凝器,液相组分一部分作为蒸馏的液体取出,另一部分继续返回塔顶进入蒸馏塔中。
塔底流出的液体,部分送入再沸器加热蒸发成气相,其它的液体作为釜残液取出。
2 Aspen Plus软件简介Aspen是由美国麻省理工学院(MIT)主持、多个部门共同参与联合开发的。
它是一款用于模拟化工生产工艺的模拟软件。
Aspen Plus拥有最完善的物性数据库,包含六千多种纯组分的物性数据。
其次,它还具有超强的热力学计算系统,以及各种单元操作模块。
Aspen Plu在整个化工工艺装置的研发、设计和安置中都发挥着巨大的作用。
石化厂气体分馏装置工艺的模拟优化

某炼厂20kt/a气体分馏装置工艺设计摘要针对某石化厂气体分馏装置工艺流程进行了模拟计算, 分析并提出了减少各塔热负荷旳优化方案, 进行了优化计算, 并与优化前进行了比较, 成果表明, 优化方案可行并有效, 减少了热负荷, 提高了经济效益。
关键词气体分馏丙烯优化方案热负荷提高效益一.序言近20数年来, 受两次能源危机旳影响和经济全球化旳制约, 我国炼油企业旳节能工作逐渐向广度和深度发展, 获得了很大旳成绩, 重要工艺装置旳能耗大大减少, 如常减压蒸馏、焦化等, 国内先进装置旳能耗基本靠近世界先进水平, 但从炼油厂旳整体来看, 加工单位原油旳能耗还比国外高出不少, 详细表目前全厂旳蒸汽动力系统、原料和产品储运系统及其他系统(包括厂区采暖、空调等等)能耗高, 重要原因是全厂各工艺装置间及装置与这些系统间缺乏热联合, 缺乏对大系统能源旳总体优化运用旳考虑。
丙烯是重要旳化工原料, 近年来伴随聚丙烯工业旳发展和车用液化气旳不停推广应用, 市场对高纯度丙烯、丙烷旳需求日趋扩大。
优化操作并合理回收丙烯, 得到高纯度丙烯可带来可观旳经济效益。
充足运用已经有设施, 通过方案优化, 在不变化主产品丙烯纯度旳条件下, 减少各塔热负荷用量, 从而减少共用工程用量, 提高生产过程旳经济效益, 具有较大旳意义。
本模拟优化设计是应用Aspen Plus化工模拟软件针对广州某石化厂实际气体分馏旳工艺装置而进行旳模拟优化工作。
二. 流程描述本流程是某石化厂气体分馏装置工艺流程, 1985年设计投入使用, 原料是来自催化裂化妆置旳液化气(气体构成如表2.1所示), 液化气由蒸气加热器B1预热到87℃, 由泵打入脱丙烷塔B2, 操作压力20KG/cm2, 温度48℃, 塔顶产物为乙烷、丙烷和丙烯旳混合物(构成见表2.2), 塔底产物碳四、碳五组分, 构成见表2.3 。
B2塔顶馏出物进入脱乙烷塔B3, 在压力为30Kg/cm2、温度59℃下操作, 塔顶主产物为乙烷, 构成见表2.4, 塔底产物重要为丙烷和丙烯, 构成见表2.5。
Aspen Plus 7.2 在精馏设计中的应用

Aspen Plus 7.2 在精馏设计中的应用作者:王济阳来源:《卷宗》2016年第07期摘要:精馏是化工行业中应用很广泛的一种工艺操作。
本文主要以Aspen Plus 7.2在精馏设计中的应用为例,介绍了Aspen Plus 7.2在化工设计中的步骤和方法。
关键词:Aspen Plus 7.2;精馏;化工设计精馏是化工行业中应用非常广泛的一种工艺操作,影响精馏效果的因素的方面很多。
往往一个因素发生变化时,会引起一些其他因素随之变化。
由于化工模拟软件Aspen Plus的存在,使得化工技术人员工作量减轻很多。
1 Aspen Plus的简介Aspen Plus是大型通用流程模拟系统,源于美国能源部七十年代后期在麻省理工学院(MIT)组织的会战,开发新型第三代流程模拟软件。
该项目称为“过程工程的先进系统”(Advanced System for Process Engineering,简称ASPEN),并于1981年底完成。
1982年为了将其商品化,成立了AspenTech公司,并称之为Aspen Plus。
该软件经过20多年来不断地改进、扩充和提高,已先后推出了十多个版本,成为举世公认的标准大型流程模拟软件,应用案例数以百万计。
全球各大化工、石化、炼油等过程工业制造企业及著名的工程公司都是Aspen Plus的用户。
2 Aspen Plus 7.2对甲醇精馏的模拟通过严格计算RadFrac精馏塔来分离甲醇和水的混合物。
进料组成为水63.2%(质量分数),甲醇36.2%,流率为120000 lb/hr,压力为18 psi (1 psi=6894.76 Pa),饱和液体进料(进料的汽相分率为0),精馏塔有38块塔板,进料在第23块板上。
塔顶压力为16.1 psi,每板的压力降为0.1 psi,塔顶为全凝器,蒸出流率为39885 lb/hr,回流比为1.3。
选用NRTL-RK 物性方法。
计算:1)绘制Aspen Plus的过程流程图;2)再沸器和冷凝器的热负荷。
基于Aspen Plus对常减压技术的优化探讨
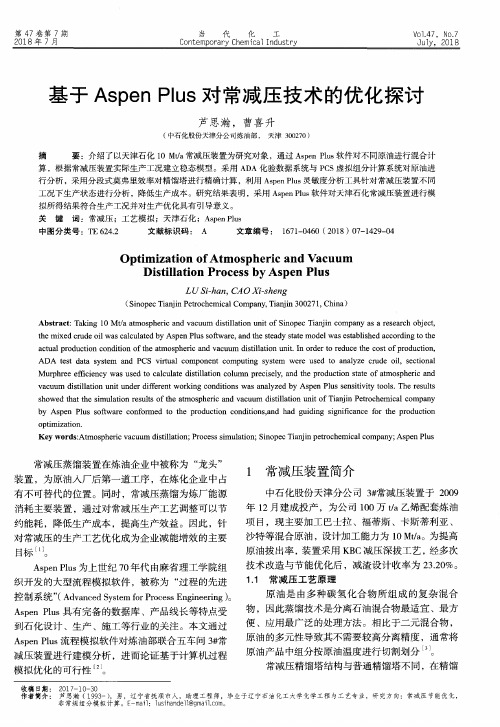
原油是 由多种碳 氢化合物所组成 的复 杂混合
Aspen Plus具 有 完备 的数 据 库 、产 品线长 等特 点 受 物 ,因此蒸馏技术是分离石油混合物最适宜 、最方
到石 化设 计 、生 产 、施工 等行 业 的关 注 。本文 通 过 便 、应 用 最广 泛 的处理 方法 。相 比于二元 混 合物 ,
第 47卷 第 7期 2018年 7月
当 代 化 工
Contemporary Chemical Industry
Vo].47. N0.7 July, 2018
基 于 Aspen Plus对 常减 压 技 术 的优 化 探讨
芦思瀚 ,曹喜升
(中石 化股 份 天津分 公 司炼 油部 , 天 津 300270)
showed that the simulation results of the atm ospheric and vacuum distillation unit of Tianjin Petrochemical company
by A spen Plus softw are conform ed to the production conditions,and had guiding signif icance for the production optim ization.
约能耗 ,降低 生 产成 本 ,提高 生产 效 益 。因此 ,针 项 目 ,现 主要加 工 巴士拉 、福蒂 斯 、卡斯 蒂利 亚 、
对 常减 压 的生 产 工艺 优化 成 为企业 减 能增 效 的主要 沙 特等 混合 原油 ,设计 加 工能 力为 10 Mt/a。为 提 高
目标 …。
原 油拔 出率 ,装 置采 用 KBC减 压 深拔 工艺 ,经 多 次
基于Aspen Plus的原油常减压蒸馏装置的模拟

候 会 峰 叶 枫 叶 绍 宁。 王 中博 , , ,
(. 疆 大 学 化 工 学 院 , 疆 乌 鲁 木 齐 1新 新 8 0 ቤተ መጻሕፍቲ ባይዱ }. 国石 油 乌 鲁 木 齐 石 化 分 公 司 , 疆 乌 鲁 木 齐 3062中 新 801) 3 0 9
摘 要 : Ase ls 件 平 台 上 , 在 pnPu 软 以标 定 数 据 为 主要 输 入 数 据 , 以产 品 控 制 指 标 为 主 要 约 束 条 件 ,
2 .CNPC Ur mq t o h mia o a y u i Per c e c lC mp n ,Ur mq 3 0 9 u i 0 1 ,Ch n ) 8 i a Ab t a t sr c :Th ta y s a e smu a i n fo o r d i a mo p e i a d v c u d s i a i n u i f r a f c o s e t b ih d e s e d — t t i l t l w fc u e o l t s h rc n a u m it lt n t o a t r i sa l e o l o s u e h a i r t n d t st e man i p td t n h r d c o to a g t s t eman c n t an so h p n P u l t s d t ec l a i a a a h i n u a a a d t e p o u tc n r l r e sa h i o s r i t n t e As e l s p a — b o t
Aspen+Plus在精馏操作分析中的应用

Aspen Plus的使用方法一般可分为4部分。 1.1定义模拟流程
模拟流程的定义就是选择合适的单元过程模块并用物料 流和能流进行连接,但与实际工艺流程并非完全相同,其实 质是对实际生产情况建立数学模型的过程。 1.2设置流程模拟参数
该部分包括模拟化学组分、热力学方法、流股信息、模块 参数以及计算方法的设置,其操作可在软件Next导航按钮提 示下完成。但选择适宜的物性方法是模拟成功与否的关键。
图5进料位置对热负荷的影响 和质量。
参考文献 [1]潘文群,孙德松.计算机在精馏操作性计算中的应用[J].化工时刊,2000(5):33—35 [2]赵毅,吴雪梅,潘艳秋,等.精馏操作型问题的讨论[J].化工高等教育,2008(5):92-97 [3]李伟,朱家文,徐心如,等.现代化工模拟软件在分离工程课程教学中的应用[J].化工高等教育,2007(2):66—67 [4]刘保柱,于风文,朱菊香.Aspen Plus应用于化工原理课程设计的实践[J].化工高等教育,2007,(2):23-25
2)进料位置。在回流比RR=3,塔顶产品量D=36 kmol/h的操作条件下,仅改变进料位置,模拟结果如图
4、图5所示。进料位置过高或过低均降低产品的分离程
度,并且增加加热蒸汽用量。
3结束语
在讲述化工原理生对精馏的基本
原理和概念产生更加深刻的理解,极大提高教学效率
■技术在线
张治山高军李敏:Asp。n P1u。在精馏操作分析中的应用
95
10.3969/j.i ssn.1671—489X.2010.15.095
As pen P I U S在精馏操作分析中的应用木
张治山高军李敏 山东科技大学化学与环境工程学院 山东青岛266510
简单蒸馏于AspenPlus上之操作
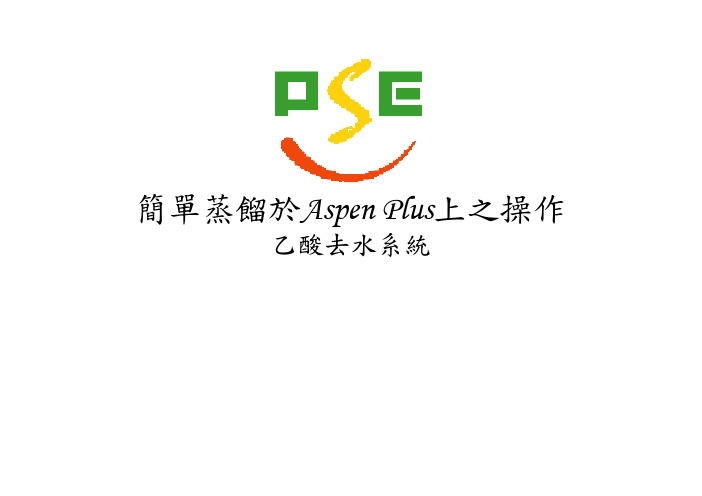
簡單蒸餾於Aspen Plus上之操作乙酸去水系統Introduction•Interface introduction•AspenPlus basic operation•Start with a steady‐state simulation –A simple distillation of Water and Acetic acid •Set up column length and diameter –Tray sizing and tray rating •Optimization for the design specification O i i i f h d i ifi i–Use “Design SPEC/VARY” functionInterface UserAcid Water 輸入物質–Acetic &可自行改名稱選擇物性的模式UniQUACWilsonUniQ‐HOC….建立蒸餾塔的模組與各股物流StreamBlock進料組成點擊兩次進料股設定點兩次蒸餾塔進行設定Column Settings餾(cont’d) Column Settings (cont d)Column Sizing新增一個“Tray Sizing” 功能Column SizingThe typical distance between trays(tray spacing) is 0.61m (2 ft)(tray spacing)is061m2ftColumn Rating一開始先給一個合理的塔徑(起始值)新增一個“Tray Rating” 功能Column Rating計算壓力降(可以固定塔頂壓力或是塔底壓力)執行當輸入完畢後按此當右下角出現兩個鈕執行藍色表示有結果,出現黃色表示到達Decanter 不分相或Design到邊界Results available Results with warningsspec 到邊界,出現紅色表示無法收斂。
流程模拟软件AspenPlus在精馏塔设计中的应用_李峰

3.4 进料位置的优化 精馏塔塔板数设置为 90 块,泡点进料 ,物性
方法使用 PR,冷凝器为全凝器,回流比 4.36,蒸流 液占进料物料的分率为 0.97816, 选择 SULZER- CY 型填料。 使用 Aspen Plus 中的灵敏度分析功 能 “Sensitivity” 功 能 , 设 置 采 集 变 量 为 塔 顶 产 品 摩 尔 纯 度 , 设 置 操 作 变 量 为 “FEED-STAGE”, 得 到 如图 4 所示的塔顶产品摩尔纯度与进料板关系 图。
压力 /MPa 1.2 1.0 0.0 0.6 0.4 0.2
塔顶产品纯度 /mol% 99.9 99.9 99.9 99.9 99.9 99.9
表 5 操作压力对精馏塔各参数的影响
回流比 Reflux Ratio
4.67 4.56 4.07 3.81 3.54 3.28
塔径 /mm 382 380 382 385 395 423
- 48 -
化工L INDUSTRY
Vol.45 No.9(2014)
流程模拟软件 Aspen Plus 在精馏塔设计中的应用
李 峰, 赵新堂, 万宝锋 (中化近代环保化工(西安)有限公司, 陕西 西安 710201)
摘 要: 以 Aspen Plus 流程模拟软件对精馏塔进行了简捷设计和严格核算, 对精馏塔设 计的影响因素进行了分析,并对精馏塔的经济核算进行了初步说明。
434 141850 141884
400 120816 120850
387 112889 112923
380 108868 108902
377 107397 107431
374 105482 105516
馏塔,用于工业生产后创造良好的经济效益。 3.3 操作压力的优化
基于Aspen+Plus的原油蒸馏装置流程模拟及优化

明显,当汽提蒸汽量继续提高时,常底重油350℃馏 出量的变化幅度降低。
因此,根据模拟计算结果,建议装置在该加工
负荷下,将常压炉的出口温度控制在360~364℃之 间,将塔底汽提蒸汽量控制在3~4t/h之间,以保证 在尽可能提高装置常压拔出率的情况下,实现装置 的节能降耗。
万方数据
增刊1
水春贵.基于Aspen
因:一是目前装置加工的原油性质与建模时的原油
性质不一样;二是实际加工量偏小;三是受各中段 回流换热器换热面积的影响,其流量调整受到限
模块,每个塔内的关键参数设定见表l。表4【l】。利 用以上基础数据,建立装置稳态模型,各塔参数以 万方数据
E—mail:shuicg.jmh@sin叩ec.cⅢ
中外能源
・10・ SIN0一GLOBAL ENERGY
2011年第16卷
0.2l%;而在塔底汽提蒸汽量为8.0t/h情况下,常压 炉出口温度每升高2cC,常底重油350℃馏出量仅 降低0.05%。同理,在常压炉出口温度保持不变情
2 5 2 13 27 35 43
汽提塔l 减压塔 汽提塔2 汽提塔3
表5初馏塔操作数据与计算值对比
项目 初馏塔顶温度/℃ 初馏塔顶回流温度,℃ 初馏塔底温度,℃ 标定值
123 40 197 201 50
计算值
124-8 40 198 200 50 Nhomakorabea3
进料温度,℃
8
初馏塔顶压力,kPa
22 30
从图2还可以看出,塔底汽提蒸汽量控制在 2—4t/h之间,对常底重油350℃馏出量的影响较为
项目 初馏塔 常压塔 减压塔 塔板数
21 49
表4常压塔和减压塔汽提塔
再沸器选型
Aspen Plus 流程模拟应用7精馏 萃取 吸收塔单元模拟
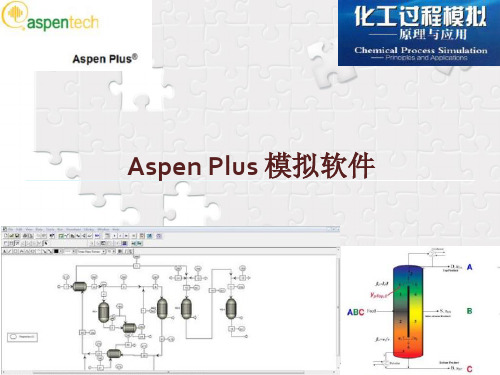
挥发度
蒸馏基础知识
表示物质挥发能力的大小
对纯组分: v Po
对混合液体: vA PA xA
vB PB xB
对理想溶液: PA PAo xA
PB PBo xB
vA PAo
vB PBo
v f T
蒸馏基础知识
相对挥发度α
定义: ➢ 混合物中两组分挥发度之比,用来表示挥发能
力的差异
➢ 对二元物系,通常用轻组分的挥发度比上重组 分的挥发度
低压: vA PA / xA 理想物系 PA0
vB PB / xB
PB0
高压: K A
KB
同样适用于 低压理想物系
蒸馏基础知识
相对挥发度表示的相平衡关系
二元物系:
KA KB
yA / xA yB / xB
yA / yB xA / xB
y /1 y x /1 x
y x 1 ( 1) x ─以α表示的相平衡方程
再沸器的作用:
提供高温低浓的汽相作为精馏介 质,保证精馏的正常进行
蒸馏基础知识——理论板数计算
精馏段操作线方程
总物料衡算: Vn1 Ln D
轻组分物料衡算:
Vn1 yn1 Ln xn DxD
yn1
Ln Vn1
xn
D Vn1
xD
恒摩尔流假定成立,令回流比为
V, y1
L, xD 1 2 3
Ln, xn n
Aspen Plus 模拟软件
分离塔单元模拟 -精馏、萃取、吸收
蒸馏基础知识
蒸馏依据 蒸馏过程利用均相液体混合物中 各组分饱和蒸汽压(或沸点或挥 发性)的差异而使各组分得以分 离
蒸馏基础知识
蒸馏过程的分类
MTBE装置AspenPlus流程模拟应用效果
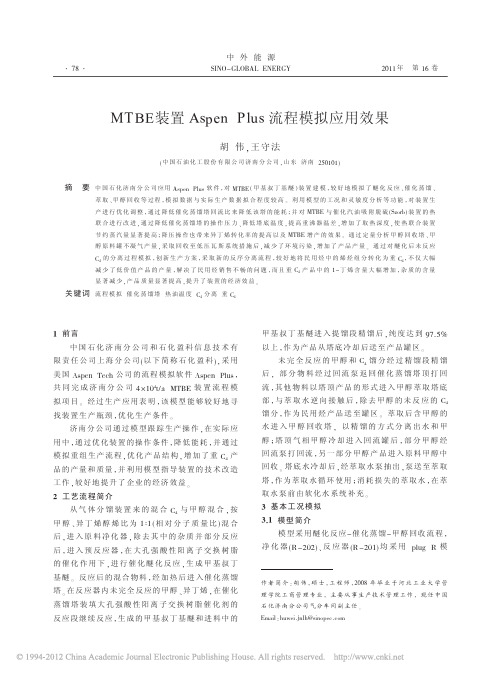
48.5 0.54 50.7 0.55 127.8 0.65 8.3 5.0
48.9 0.52 51.6 0.55 128.1 0.64 8.0 5.05 63.2 0.003 100 0.022 2.4 2.0 63.4 0.004 100.7 0.02 2.5 2.0
进 料 压 力 /MPa( 表 ) 出 口 温 度 /℃ 出 口 压 力 /MPa( 表 )
表 1 C4 、 甲 醇 进 料 组 成 表
组 分 ID 组分名称 进 料 组 成 , %( 质 量 分 数 ) 组 分 ID 组分名称 反 -2- 丁 烯 顺 -2- 丁 烯 丁二烯 甲 醇 甲 醇 水 进 料 组 成 , %( 质 量 分 数 )
C4 IC4= 1-BUT-01 C3 ISOBU-01 N-BUT-01
5 模型分析 5.1 进 料 醇 烯 比 对 全 装 置 异 丁 烯 总 转 化 率 的 影 响
3 基本工况模拟 3.1 模 型 简 介
模型采 用 醚 化 反 应-催 化 蒸 馏-甲 醇 回 收 流 程 , 净 化 器 (R -202) 、 反 应 器 (R -201) 均 采 用 plug R 模
作 者 简 介 : 胡 伟 , 硕 士 , 工 程 师 , 2008 年 毕 业 于 河 北 工 业 大 学 管 理学院工商管理专业, 主要从事生产技术管理工作, 现任中国 石化济南分公司气分车间副主任。
异丁烯 正丁烯 丙 烷 异丁烷 正丁烷
TRANS-01 21 14 0.01 40.99 8 MEOH H2O CIS-2-01 1 , 3-B-01
5 6 5 99.95 0.05
4 模拟结果对比
在压力给定条件下,测量点温度、各物 流 流 量 组 成 对 比 结 果 见 表 2,产 品 组 成 对 比 结 果 见 表 3。 从
AspenPlus在常减压蒸馏装置中的应用
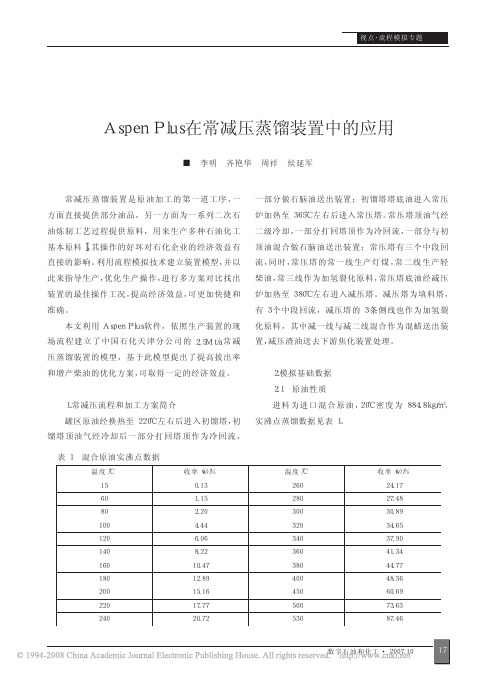
2.2 过程参数 在进行装置过程参数收集时, 按照先采集操作 数据, 再进行现场取油样的顺序进行。装置的实际操 作是动态的, 过程参数会在一定范围内波动, 因此, 在收集过程参数时, 不仅采集了即时数据, 对重要的 过程参数还收集了一段时间内的数据, 根据数据变 化趋势可以判断即时数据的合理性, 同时在合理范
Aspen Plus 在常减压蒸馏装置中的应用
■ 李明 齐艳华 周祥 侯延军
常减压蒸馏装置是原油加工的第一道工序, 一 方面直接提供部分油品, 另一方面为一系列二次石 油炼制工艺过程提供原料, 用来生产多种石油化工 基本原料[], 其操作的好坏对石化企业的经济效益有 直接的影响。利用流程模拟技术建立装置模型, 并以 此来指导生产, 优化生产操作, 进行多方案对比找出 装置的最佳操作工况, 提高经济效益, 可更加快捷和 准确。
5.2 增产柴油 为提高柴汽比以缓解国内消费柴汽比大于生产 柴汽比的局面, 增加柴油产量也是优化常减压装置 操作目标之一。其优化问题可表述为: 目标: Max flow( 常二线) 约束: 常一线干点≯240℃, 常二线 95%点≯365℃ 自变量: 塔顶温度, 常一线抽出量, 常三线抽出 量, 常塔底汽提蒸汽量
减压系统直接模拟的结果与产品实际馏程偏差 较大, 失去指导意义。初步分析主要有两个原因: 一 个重要的是, 530℃以前的原油实沸点蒸馏数据由实 验得到, 较为准确, 而 530℃以后的蒸馏数据由软件 自动外推, 有一定的误差; 另一个是, 常压塔底的渣 油在减压炉中发生部分高温裂解也是导致减压塔模 拟失真的一个主要原因。目前已有文献报道, 在常减 炉入口通过人为的加入一定组成的轻端组分后较好 的模拟了包括减压塔在内的常减压蒸馏流程。为此, 该模型在减压系统前加入模拟裂解气, 具体裂解气 组分见表 4。
- 1、下载文档前请自行甄别文档内容的完整性,平台不提供额外的编辑、内容补充、找答案等附加服务。
- 2、"仅部分预览"的文档,不可在线预览部分如存在完整性等问题,可反馈申请退款(可完整预览的文档不适用该条件!)。
- 3、如文档侵犯您的权益,请联系客服反馈,我们会尽快为您处理(人工客服工作时间:9:00-18:30)。
1.常减压流程和加工方案简介 罐区原油经换热至 220℃左右后进入初馏塔, 初 馏塔顶油气经冷却后一部分打回塔顶作为冷回流,
数字石油和化工 · 2007.10
19
视 点!·流 程 模 拟 专 题
表 4 模拟裂解气组分
组分名称 C3H8
C4H10- 1 C5H12- 1 C5H12- 2 C5H12- 3 C6H14- 1
含量( W) /% 10 10 10 15 25 30
综合以上分析, 在进行常减压蒸馏装置模拟时, 准确的原油性质数据对模拟结果有很大的影响。其 中, 缺乏轻端组分分析是模拟中遇到的普遍问题, 软 件外推的原油高沸程馏程数据的准确性对模拟结 果, 特别是对减压塔的模拟结果有重要的影响, 减压 系统的模拟通过人为的加入一定量模拟裂解气可得 到具有指导意义的模型。
5.2 增产柴油 为提高柴汽比以缓解国内消费柴汽比大于生产 柴汽比的局面, 增加柴油产量也是优化常减压装置 操作目标之一。其优化问题可表述为: 目标: Max flow( 常二线) 约束: 常一线干点≯240℃, 常二线 95%点≯365℃ 自变量: 塔顶温度, 常一线抽出量, 常三线抽出 量, 常塔底汽提蒸汽量
计 算 值 /% 100.00
2.78 97.21 11.91 5.18 14.51 7.15 58.09 17.02 6.17 33.71
偏 差 /% 0.00 0.00 0.01 - 0.32 0.00 0.00 0.00 0.18 0.00 0.00 0.50
注: 偏差= 计算值- 实际值 偏 差 为 0.00 的 对 应 项 是 建 立 模 型 时 的 已 知 输 入项
视 点·!流 程 模 拟 专 题
Aspen Plus 在常减压蒸馏装置中的应用
■ 李明 齐艳华 周祥 侯延军
常减压蒸馏装置是原油加工的第一道工序, 一 方面直接提供部分油品, 另一方面为一系列二次石 油炼制工艺过程提供原料, 用来生产多种石油化工 基本原料[], 其操作的好坏对石化企业的经济效益有 直接的影响。利用流程模拟技术建立装置模型, 并以 此来指导生产, 优化生产操作, 进行多方案对比找出 装置的最佳操作工况, 提高经济效益, 可更加快捷和 准确。
温 度 /℃ 260 280 300 320 340 360 380 400 450 ห้องสมุดไป่ตู้00 530
收 率 (w)/% 24.17 27.48 30.89 34.65 37.90 41.34 44.77 48.36 60.69 73.63 87.46
数字石油和化工 · 2007.10
17
视 点!·流 程 模 拟 专 题
3.建立模型 初馏塔和常压塔塔内汽液相连续, 模拟时选用 Aspen Plus 的原油蒸馏 PetroFrac 模块。减压塔的侧 线抽出产品全部供给催化裂化或加氢裂化装置, 与 常规精馏塔相比, 有产品质量控制粗犷、产品间无严 格分离要求、塔内气相连续、液相不连续和内回流量 少的特点, 直接使用 PetroFrac 模拟有很大的误差。 针对减压塔的工艺特征, 汪学军等提出把干式减压 塔作为一个闪蒸过程与多个复杂吸收过程的串联, 但基于此方案的计算完全忽略了塔内回流量, 应用 Aspen Plus 建立的模型难以达到物料平衡, 因此本 论文提出了改进的减压塔模型, 将塔顶部分油返回 至塔底渣油, 可解决物料平衡的问题, 建立的常减压 模型见图 1。
定自变量范围: 2000kg/h<塔底汽提蒸汽量<10000kg/ h, Δ塔顶温度≤10℃; 为优化目标函数提供相应的 约束条件, 建立完整的优化模型。通过模型计算可知 常一线抽出量可提高 1t/h, 常二线抽出量可提高 3t/ h, 利用模型可确定塔底气体蒸汽量、Δ塔顶温度分 别在 3.2t/h、3℃的工艺操作下, 可实现优化目标。
减压系统直接模拟的结果与产品实际馏程偏差 较大, 失去指导意义。初步分析主要有两个原因: 一 个重要的是, 530℃以前的原油实沸点蒸馏数据由实 验得到, 较为准确, 而 530℃以后的蒸馏数据由软件 自动外推, 有一定的误差; 另一个是, 常压塔底的渣 油在减压炉中发生部分高温裂解也是导致减压塔模 拟失真的一个主要原因。目前已有文献报道, 在常减 炉入口通过人为的加入一定组成的轻端组分后较好 的模拟了包括减压塔在内的常减压蒸馏流程。为此, 该模型在减压系统前加入模拟裂解气, 具体裂解气 组分见表 4。
2.2 过程参数 在进行装置过程参数收集时, 按照先采集操作 数据, 再进行现场取油样的顺序进行。装置的实际操 作是动态的, 过程参数会在一定范围内波动, 因此, 在收集过程参数时, 不仅采集了即时数据, 对重要的 过程参数还收集了一段时间内的数据, 根据数据变 化趋势可以判断即时数据的合理性, 同时在合理范
图 1 改进后的常减压蒸馏模型
18 2007.10 · 数字石油和化工
视 点·!流 程 模 拟 专 题
4.计算结果及分析 在建立的常减压蒸馏模型中输入过程参数, 模 型计算时按流程物流方向的顺序逐次进行, 将得出 的结果与实际值进行对比, 在合理范围内调整部分
过程参数, 直至计算结果达到预期的目标值。 物料平衡的实际值与计算值的对比结果见表 3,
围内调整重要的过程参数可加快模型的收敛速度, 提高模拟计算的准确性。
根据相关文献, 实际塔板效率选用 60%, 汽提塔 为 2 ̄4 块理论板, 减压塔将填料高度换算为相同分 离效果的理论板数。其他如进料板位置、中段回流位 置和抽出板位置按塔板效率做相应的调整, 由此确 定各塔的过程参数。具体配置参数见表 2。
一部分做石脑油送出装置; 初馏塔塔底油进入常压 炉加热至 365℃左右后进入常压塔。常压塔顶油气经 二级冷却, 一部分打回塔顶作为冷回流, 一部分与初 顶油混合做石脑油送出装置; 常压塔有三个中段回 流, 同时, 常压塔的常一线生产灯煤, 常二线生产轻 柴油, 常三线作为加氢裂化原料, 常压塔底油经减压 炉加热至 380℃左右进入减压塔。减压塔为填料塔, 有 3 个中段回流, 减压塔的 3 条侧线也作为加氢裂 化原料, 其中减一线与减二线混合作为混蜡送出装 置, 减压渣油送去下游焦化装置处理。
( 作者李明, 齐艳华, 周祥单位系石油化工科学 研究院; 侯延军单位系中国石化天津分公司炼油部)
数字石油和化工 · 2007.10
21
图 3 塔顶温度对拔出率影响
图 4 塔底汽提蒸汽量对拔出率影响 确定主要影响因素后, 在保证产品质量合格的前
20 2007.10 · 数字石油和化工
视 点·!流 程 模 拟 专 题
提下, 提高常一线和常二线收率, 优化目标可表述为: 目标: Max flow( 常一线+常二线) 约束: 常一线干点≯240℃, 常二线 95%点≯365℃ 自变量: 塔底汽提蒸汽量, 塔顶温度 运用 Aspen Plus 的优化工具定义 目 标 函 数 ; 给
2.模拟基础数据 2.1 原油性质 进 料 为 进 口 混 合 原 油 , 20℃密 度 为 884.8kg/m3, 实沸点蒸馏数据见表 1。
表 1 混合原油实沸点数据
温 度 /℃ 15 60 80 100 120 140 160 180 200 220 240
收 率 (w)/% 0.13 1.15 2.20 4.44 6.06 8.22 10.47 12.89 15.16 17.77 20.72
表 2 塔的配置参数
塔名称 初馏塔
常压塔
项目 主塔塔板数 进料板 主塔塔板数 进料板 侧线汽提塔塔板数 常一线汽提塔液相采出/返回 常二线汽提塔液相采出/返回 常三线汽提塔液相采出/返回 常顶循液相采出/返回 常一中液相采出/返回 常二中液相采出/返回
塔板数 18 18 29 29 2 9/8 16/15 20/19 3/2 11/10 18/17
利用建立的模型分别考虑塔顶温度, 汽提蒸汽 量因素, 由图 3, 图 4 可以看出这两个因素对拔出率 有较明显的影响。
5.灵敏度分析 优化方案 运用 Aspen Plus 模拟软件的灵敏度分析工具可 以研究过程参数对常减压产品分布的影响程度, 通 过工况分析, 可以在装置的约束条件范围内确定不 同操作条件下的最优化生产方案。 5.1 提高拔出率 拔出率是指初馏塔、常压塔和减压塔的塔顶以 及侧线产品量的总和占处理原油量的比例。原油一 次拔出率是考核常减压蒸馏装置的重要指标之一, 拔出率提高可以提高原油的利用率, 降低下游装置 的负荷及整个炼油厂对油品的再加工及再运输的 能耗。 本论文对如何提高常压塔的拔出率进行了优 化, 主要考虑对经济效益影响大的常一线和常二线 的拔出率。从操作条件上讲, 需要考虑的几个主要因 素有: 塔顶温度、塔底汽提蒸汽量、塔顶压力和进料 温度, 其中, 塔顶压力和进料温度较为稳定, 主要考 虑前二个因素。提高塔顶温度, 加大汽提蒸汽量有利 于塔内汽液相负荷增加, 有利于提高侧线抽出量。
同样, 在满足约束条件的前提下, 利用 AspenPlus 提供的 优 化 工 具 可 以 很 快 得 到 常 二 线 抽 出量可增加 5t/h 的结果。
6.结论 ( 1) 用 Aspen Plus 模拟软件对中国石化天津分 公 司2.5Mt/a 常 减 压 装 置 的 流 程 模 拟 得 到 了 与 实 际 生产流程较为一致的结果, 其中减压系统的模拟需 要补充模拟裂解气。 ( 2) 利用灵敏度分析, 最优化工具结合约束模 块, 选取合适的自变量, 基于 Aspen Plus 常减压蒸馏 模型可以较方便快速的得到最优化解决方案, 供企 业生产者参考。在一定约束条件下提出了提高拔出 率和增产柴油的优化方案, 可为企业带来经济效益。 ( 3) 过程参数数据的收集, 要充分考虑到装置的动 态操作, 根据操作记录区线, 判断数据的合理性。