VRDS渣油加氢装置工艺原理
RHT系列渣油加氢催化剂在齐鲁VRDS装置上的工业应用
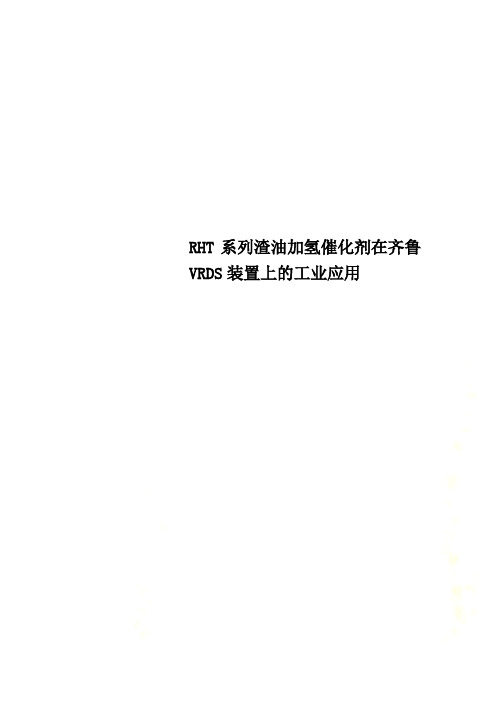
RHT系列渣油加氢催化剂在齐鲁VRDS装置上的工业应用RHT系列渣油加氢催化剂在齐鲁VRDS装置上的工业应用穆海涛孙振光齐鲁石化公司胜利炼油厂(山东淄博255434)摘要介绍了由北京石油化工研究院研制、开发、用于渣油加氢装置固定床反应器的RHT系列催化剂在胜利炼油厂VRDS装置的首次工业应用情况。
该催化剂采用自行开发的级配路线,较好地结合了脱金属剂、脱硫剂、脱氮剂的性能特点,使整个运行周期的催化剂活性和稳定性达到较好地匹配,已达到同类进口催化剂的水平。
关键词渣油加氢催化剂活性稳定性1 前言随着环保法规的日益严格,对炼油企业生产清洁油品并做到清洁生产的要求越来越高,也越来越严格。
渣油加氢装置因为具有液体产品收率高、环境友好等诸多优点,使渣油加氢成为炼厂清洁加工高硫、高金属渣油的重要技术。
将经过渣油加氢脱除硫、金属、氮等杂质的加氢产品送往催化裂化装置作原料,不但可以生产出低硫、低氮高质量的轻质油品,而且大大降低对环境的污染。
因此渣油加氢工艺在炼厂的地位和作用也越来越重要。
胜利炼油厂渣油加氢脱硫(VRDS)装置是国内第一套渣油加氢处理装置,1992年5月26日首次开工,在渣油加氢生产、技术方面积累了丰富的经验。
1999年底,该装置加工能力从0.84 Mt/a扩能为1.50 Mt/a,改造中又首次引进了美国雪弗隆(Chevron)公司的上流式反应器专利技术(UFR),建设成为目前世界上唯一一套采用上流式反应器与固定床反应器组合床工艺技术的渣油加氢处理装置,装置生产的主要目的就是为催化裂化装置提供优质渣油进料。
该装置技术先进,工艺程度复杂,改造后投入运行表明:该装置对提高全厂轻油收率,增加经济效益具有非常重要的作用。
石油化工科学院(RIPP)在对渣油加氢机理进行深入研究的基础上,成功开发了渣油加氢RHT系列催化剂,并在2001年12月份通过了中石化股份公司的技术鉴定,2002年10月利用胜利炼油厂UFR/VRDS装置秋季检修换剂机会更换了固定床一个系列的催化剂为石科院RHT系列催化剂,开始进行工业应用,该项目同时被列入2002年中国石油化工股份公司的科技开发项目。
VRDS渣油加氢装置技术特点

VRDS渣油加氢装置技术特点1.1 装置特点①UFR/VRDS加工的是高硫、高残炭的常减压减四线和减低渣油,通过加氢脱硫、加氢脱残炭、加氢脱金属等反应,生产适合催化裂化的原料。
②UFR是有三个催化剂床层的上流式反应器,其主要的工艺目的是在稳定状态下操作UFR,大幅度地降低进料中的金属含量,以防止固定床反应器内催化剂过早失活。
加热后的UFR进料(油氢混合物)进入反应器底部,向上流动通过球型催化剂颗粒填充床层。
因为是上流方向,所以UFR 催化剂床层轻微悬浮。
③优化的换热网络系统,设置原料、常渣、柴油、反应产物等的换热器,利用系统热能加热原料、反应进料、轻烃等,提高了热利用率。
加热炉采用余热回收,空气与烟气进行换热,回收烟气中的热量,提高加热炉热效率。
④重油加氢装置的DCS控制系统于2009年由原来的ABB公司的Advance 500更新为Honeywell公司PKS R310系统,先进控制系统的平台更新为EAS NODE,先进控制软件最近升级为技术更为先进的Profit suite R320控制器软件。
VRDS装置使用了先进控制应用的意义在于,希望通过先进控制的应用可以帮助操作人员实现最大的高附加值产品产率、最小的产品指标富裕量、最小的能量消耗从而获得最大的经济效益。
⑤UFR/VRDS装置反应器和循环气体系统分为A、B 两列。
2007年停工后,通过新加流程,使VRDS装置具备单列停开工能力,依靠单系列流程,VRDS装置已经成功实现4次单系列停开工。
充分利用催化剂活性,实现渣油处理最大效益。
1.2 技术改造1.2.1 烟气余热回收系统1、项目实施的背景进入21世纪后,为了适应节能降耗的大趋势,重油加氢装置进行了多项重大节能改造项目,其中就包括加热炉余热回收系统改造。
重油加氢装置原有一套加热炉余热回收系统,加热炉高温烟气排入到集合烟道去往废锅做热源产0.8MPa蒸汽,由于燃料中的硫含量较高,废锅的省煤器段难以避免烟气低温露点腐蚀,所以废锅投用很短时间就因省煤器段破坏而停用,5台加热炉的烟气直接排放大气,排烟平均温度340℃,能量损失严重。
惠州石化VRDS装置渣油深度脱金属的工业应用

惠州石化VRDS装置渣油深度脱金属的工业应用作者:姜龙雨吴海波来源:《当代化工》2019年第02期摘 ;;;;;要:论述了CLG公司固定床渣油加氢处理技术在中海油惠州石化有限公司400万t/aVRDS装置的工业应用。
该装置原料设计镍+钒含量102 wppm,经深度加氢脱金属,加氢重油产品镍+钒含量可以达到10 wppm以下。
该装置第一周期运行结果表明,深度加氢脱金属同时能够实现装置长周期运行。
关 ;键 ;词:VRDS;渣油加氢处理;脱金属;工业应用中图分类号:TE624 ;;;;;;文献标识码: A ;;;;;;文章编号:1671-0460(2019)02-0337-04Abstract: The industrial application of CLG fixed bed residue hydrotreating technology in 4 Mt/a VRDS unit of CNOOC Huizhou petrochemical company was discussed. The raw material of the unit contains 102 wppm of nickel and vanadium, and the content of nickel and vanadium in the hydrotreated heavy oil product can be less than 10 wppm after deep hydrodemetallization. The running results in No.1 operation period show that the long-term operation of the unit can be achieved with deep hydrodemetallization process.Key words: VRDS; Residue hydrotreating; Hydrodemetallization; Industrial application為了合理利用石油资源,满足不断增长的轻质油品需求以及适应日趋严格的环保要求,各国炼油工业都非常重视渣油转化[1]。
渣油加氢工艺及工程技术探讨

渣油加氢工艺及工程技术探讨摘要:随着石油资源的日益减少和原油重质化、劣质化趋势的加剧,渣油加氢工艺逐渐成为渣油加工的重要手段之一。
介绍了渣油加氢工艺的反应原理,分析了渣油加氢技术的应用,最后提出了渣油加氢装置高效运行的保障措施。
关键词:炼油;渣油加氢;工艺技术介绍渣油是原油经蒸馏处理后,由非理想组分或杂质组成的残余油。
由于二次加工的困难,炼油厂通常将其作为锅炉燃料燃烧。
由于渣油中原油含量高,燃烧处理不仅浪费有限的资源,而且对周围环境造成威胁和污染。
采用加氢工艺处理残渣。
该工艺方案不仅可以增加企业的经济收入,减少环境污染,而且可以提高资源利用率,真正把有限的资源吃掉、晒干、炒熟。
这是一种在中国主要炼油厂广泛推广和实施的残渣处理工艺。
1.渣油加氢工艺反应原理1.1脱硫反应脱硫反应是渣油加氢处理过程中最重要的化学反应。
由于残渣硫化物的类型和结构复杂多变,实际反应过程中涉及的脱硫反应也更加复杂。
一般来说,硫化物的脱硫反应可以近似地看作是在催化剂作用下残渣中硫化物的碳硫断裂的氢解反应,并释放出硫化氢气体和无硫饱和烃,该反应强烈且不可逆。
催化剂颗粒的总体尺寸、孔径分布和工艺条件是影响加氢脱硫反应程度的两个主要因素。
1.2脱金属反应加氢脱金属反应的主要目的是去除镍、铁等金属杂质,这些杂质对渣油的二次反应性能有很大影响。
与脱硫反应类似,脱金属反应是渣油加氢处理的另一个重要化学反应。
整个反应过程通常通过一个或多个可逆反应完成。
反应的第一步是氢化生成中间产物。
中间产物进一步氢解,最终形成固体金属硫化物,附着或沉积在催化剂表面或孔口附近。
催化剂颗粒的总体尺寸、孔径分布和反应物分子的扩散速率是影响加氢脱金属反应程度的两个主要因素。
1.3反硝化反应残渣中的氮元素以氮杂环化合物的形式存在。
加氢反应通常需要先经过杂环饱和,然后碳氮断裂形成气相产物。
因此,渣油脱氮反应过程非常复杂多变。
产物中硫化氢的含量、各种氮化物之间的竞争吸附以及反应物分子的扩散速率是影响反硝化反应程度的主要因素。
关于渣油加氢处理催化剂及工艺技术

关于渣油加氢处理催化剂及工艺技术一、渣油加氢处理技术概况当今世界,石油资源逐渐变劣、变重,使轻质油品收率下降,而世界经济的快速发展对轻质油品的需求却日益增长。
如何合理利用和深度加工劣质或重质原油,是炼油工业面临的一个迫切需要解决的难题。
在国内,原油资源满足不了我国国民经济快速发展的需要,进口中东原油以增加我国的能源供给势在必行。
中东原油加工的主要技术难点是高硫原油的合理利用,从当今炼油技术水平来看, 渣油固定床加氢处理是合理利用含硫渣油的最为有效的手段之一二、渣油加氢处理过程的化学反应及催化剂1、渣油加氢处理过程的化学反应在重油加氢处理过程中,主要的化学反应有:加氢脱金属(HDM);加氢脱硫(HDS);加氢脱氮(HDN);加氢裂化(HC);不饱和键的加氢(如芳烃饱和—HDA)等。
针对这些反应,渣油加氢处理催化剂主要包括渣油加氢保护剂,脱金属催化剂,脱硫催化剂和脱氮催化剂四大类。
2、减压渣油加氢处理系列催化剂(FZC —XX系列)该系列催化剂自1986年开始研制以来,现已研究开发成功四大类共十六个牌号的催化剂。
研究开发过程中共申请国内外专利六十余项,有效地保护了我国自力更生开发的渣油固定床加氢处理技术(简称S-RHT技术)。
3、常压渣油加氢处理系列催化剂(FZC-XXX系列)1995年我国开始针对进口高硫原油开展了常压渣油加氢处理系列催化剂的研究开发工作。
本项目包括三大类(加氢脱硫,加氢脱金属和保护)催化剂的开发,1998年底完成全部实验室研制和工业放大工作,先后申请专利12项。
试验结果表明,FZC-XXX系列催化剂达到国际先进水平,填补了国内空白。
三、S-RHT渣油固定床加氢处理技术的工业应用1、减压渣油加氢处理S-RHT工业装置所用主要催化剂物化性质S-RHT工业装置有效地脱除了渣油中的硫、氮、金属等杂质,除生产少量石脑油和部分优质低硫轻柴油外,收率90%左右的加氢常渣是合格的RFCC进料,有效地实现了含硫渣油的全转化。
渣油加氢工艺的研究与应用
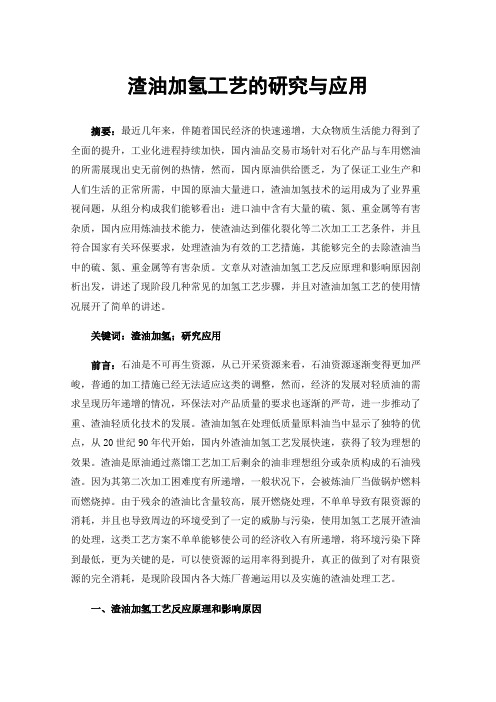
渣油加氢工艺的研究与应用摘要:最近几年来,伴随着国民经济的快速递增,大众物质生活能力得到了全面的提升,工业化进程持续加快,国内油品交易市场针对石化产品与车用燃油的所需展现出史无前例的热情,然而,国内原油供给匮乏,为了保证工业生产和人们生活的正常所需,中国的原油大量进口,渣油加氢技术的运用成为了业界重视问题,从组分构成我们能够看出:进口油中含有大量的硫、氮、重金属等有害杂质,国内应用炼油技术能力,使渣油达到催化裂化等二次加工工艺条件,并且符合国家有关环保要求,处理渣油为有效的工艺措施,其能够完全的去除渣油当中的硫、氮、重金属等有害杂质。
文章从对渣油加氢工艺反应原理和影响原因剖析出发,讲述了现阶段几种常见的加氢工艺步骤,并且对渣油加氢工艺的使用情况展开了简单的讲述。
关键词:渣油加氢;研究应用前言:石油是不可再生资源,从已开采资源来看,石油资源逐渐变得更加严峻,普通的加工措施已经无法适应这类的调整,然而,经济的发展对轻质油的需求呈现历年递增的情况,环保法对产品质量的要求也逐渐的严苛,进一步推动了重、渣油轻质化技术的发展。
渣油加氢在处理低质量原料油当中显示了独特的优点,从20世纪90年代开始,国内外渣油加氢工艺发展快速,获得了较为理想的效果。
渣油是原油通过蒸馏工艺加工后剩余的油非理想组分或杂质构成的石油残渣。
因为其第二次加工困难度有所递增,一般状况下,会被炼油厂当做锅炉燃料而燃烧掉。
由于残余的渣油比含量较高,展开燃烧处理,不单单导致有限资源的消耗,并且也导致周边的环境受到了一定的威胁与污染,使用加氢工艺展开渣油的处理,这类工艺方案不单单能够使公司的经济收入有所递增,将环境污染下降到最低,更为关键的是,可以使资源的运用率得到提升,真正的做到了对有限资源的完全消耗,是现阶段国内各大炼厂普遍运用以及实施的渣油处理工艺。
一、渣油加氢工艺反应原理和影响原因在渣油加氢的过程当中,时常会同时出现精制和裂化两种反应,其主要的反应方式有以下几个方面:1.脱硫反应渣油加氢处理工艺当中最为关键的化学反应则是脱硫反应,因为渣油硫化物的类别以及结构繁琐多样,因此,在实际的反应过程当中,所囊括的脱硫反应也较为繁琐。
170万吨、年渣油加氢装置操作法
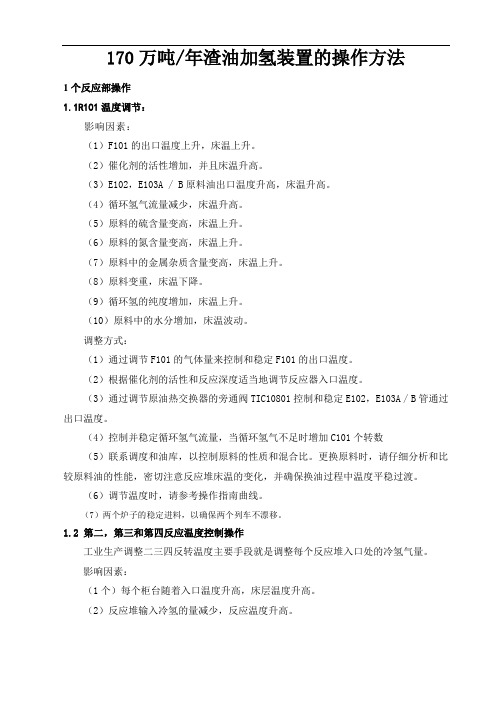
170万吨/年渣油加氢装置的操作方法1个反应部操作1.1R101温度调节:影响因素:(1)F101的出口温度上升,床温上升。
(2)催化剂的活性增加,并且床温升高。
(3)E102,E103A / B原料油出口温度升高,床温升高。
(4)循环氢气流量减少,床温升高。
(5)原料的硫含量变高,床温上升。
(6)原料的氮含量变高,床温上升。
(7)原料中的金属杂质含量变高,床温上升。
(8)原料变重,床温下降。
(9)循环氢的纯度增加,床温上升。
(10)原料中的水分增加,床温波动。
调整方式:(1)通过调节F101的气体量来控制和稳定F101的出口温度。
(2)根据催化剂的活性和反应深度适当地调节反应器入口温度。
(3)通过调节原油热交换器的旁通阀TIC10801控制和稳定E102,E103A / B管通过出口温度。
(4)控制并稳定循环氢气流量,当循环氢气不足时增加C101个转数(5)联系调度和油库,以控制原料的性质和混合比。
更换原料时,请仔细分析和比较原料油的性能,密切注意反应堆床温的变化,并确保换油过程中温度平稳过渡。
(6)调节温度时,请参考操作指南曲线。
(7)两个炉子的稳定进料,以确保两个列车不漂移。
1.2 第二,第三和第四反应温度控制操作工业生产调整二三四反转温度主要手段就是调整每个反应堆入口处的冷氢气量。
影响因素:(1个)每个柜台随着入口温度升高,床层温度升高。
(2)反应堆输入冷氢的量减少,反应温度升高。
(3)反应深度增加并且反应温度升高。
(4)原材料油性质对反应温度的影响与R101相同。
(5)催化剂的活性增加并且床温升高。
(6)循环氢的纯度增加,反应温度升高。
调整方式:(1个)通过监管每个柜台进口冷氢量调整输入口腔温度和床地板温度保持每张床的温度上升≯28℃。
(2)为了防止温度过度波动,温度调节范围应在0.5℃关于。
(3)将转换深度控制在设计范围内。
(4)原材料油当性质改变时,调节反应温度的方法与R101相同。
渣油加氢技术

(第十章第四、五节)
渣油加氢工艺反应器类型
固定床 渣油+H2
移动床
生成油+H2 催化剂
沸腾床
浆液床
生成油+H2
生成油+H2油 催化剂 +H2
渣油 催化剂 +H2
渣油+H2+催化剂
几种渣油加氢工艺技术特点
工艺类型
可加工原料油: Ni+V, ppm 残炭值,%
反应压力, MPa 反应温度, ℃ 体积空速, h-1 主要反应类别 渣油转化率, %
H HH
H2(+H2S) NixSy
Ni-X
催化剂使用寿命(t)与MOC的关系
催化剂使用寿命(t) ≈催化剂容金属能力(MOC)
催化剂级配的作用
渣油Ni+V含量与催化剂耗量的关系
14.00 7.00 3.50 m3原料油/kg催化剂 1.75
0.35 脱硫率/%
催化剂活性与寿命的平衡
催化剂级配
Ⅰ
最高温度
1
25 10 13 10 14 100
装置套数
12 5
1
16 5 7 5
7
58
沸腾床
500 600 1230 125 0 0 0 145 2600
所占比例,% 19 23 47
500
0
6 100
装置套数
44
6
100
0
1
16
占世界渣油加氢总能力:固定床=82%;沸腾床=18%
固定床渣油加氢在炼厂中的作用
复杂 成熟
较复杂 开发中
中等
较高
中等
不同渣油加氢工艺产品性质比较
VRDS渣油加氢装置工艺指标调整
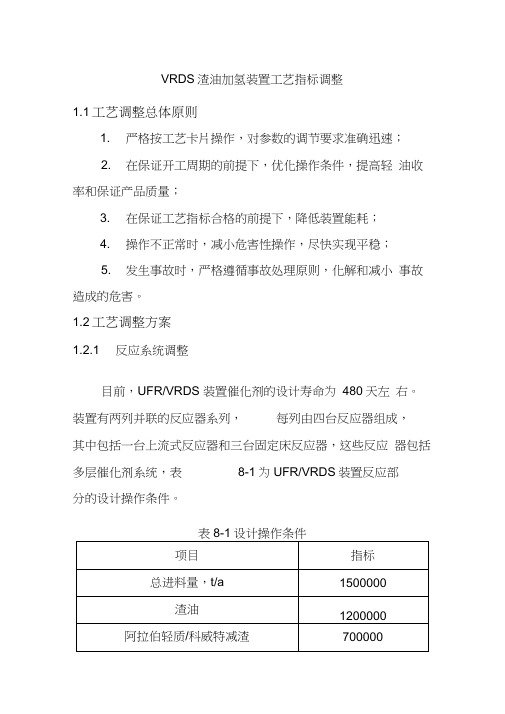
VRDS渣油加氢装置工艺指标调整1.1工艺调整总体原则1. 严格按工艺卡片操作,对参数的调节要求准确迅速;2. 在保证开工周期的前提下,优化操作条件,提高轻油收率和保证产品质量;3. 在保证工艺指标合格的前提下,降低装置能耗;4. 操作不正常时,减小危害性操作,尽快实现平稳;5. 发生事故时,严格遵循事故处理原则,化解和减小事故造成的危害。
1.2工艺调整方案1.2.1 反应系统调整目前,UFR/VRDS 装置催化剂的设计寿命为480天左右。
装置有两列并联的反应器系列,每列由四台反应器组成,其中包括一台上流式反应器和三台固定床反应器,这些反应器包括多层催化剂系统,表8-1为UFR/VRDS装置反应部分的设计操作条件。
表8-1设计操作条件注:1.仅以活性催化剂为基础(不考虑制成催化剂和级配催化剂)。
2•仅以减渣为基础3. 开工初期定义为首次进渣油后30 天。
4. 新氢加上循环氢进入第一台反应器。
5. 所述排放速度和泄漏量为纯氢气。
1.2.1.1 反应温度温度是加氢反应的重要控制参数,提高反应温度可以极大地提高加氢反应的速度,从而使原料油中硫、氮、金属等杂质的脱除率提高,原料油的裂化程度提高,轻油收率提高。
在具体的工艺过程中,其它工艺参数(如原料性质、进料量、反应催化剂活性等)对加氢反应的影响可以通过反应温度的调整加以补偿。
通常所说的反应温度为整个催化剂床层温度的加权平均值(CAT )。
上流式反应器(R-1305/R1306 )和固定床一反(R-1310 /R1311 )所装的是脱金属催化剂,提高温度有利于提高金属杂质的脱除率。
但过高的脱金属温度,会使得金属杂质较快地沉积在催化剂的表面,造成差压上升和催化剂的迅速失活从而缩短开工周期;太低的脱金属温度又会造成金属脱除率降低,使金属沉积到后部活性较高的转化催化剂上引起催化剂失活,同样会影响开工周期。
所以合适的脱金属温度的选择是至关重要的。
固定床二反和三反装的是脱S 和脱N 转化催化剂,提高该温度可提高S、N 的脱除率和转化深度,但温度提高到一定程度,渣油热裂化反应的速度大于加氢反应的速度,产品中不饱和烃增加,并且伴随热裂化反应的进行,缩合生焦反应加剧,将很快造成催化剂的生焦失活。
VRDS渣油加氢装置概况

VRDS渣油加氢装置概况1.1 装置简介为适应原油逐年重质化、劣质化的趋势,提高轻油收率和减少环境污染,胜利炼油厂于1989年10月份从美国雪弗隆(Chevron)公司引进了设计能力为84×104t/a的固定床减压渣油加氢脱硫装置(简称VRDS)。
该装置由华鲁工程公司设计,中石化十化建承建,1992年5月21日建成投产。
1998年,根据中石化公司整体原油加工方案的安排,胜利炼油厂需要掺炼75%(6.0 Mt/a)的进口中东高硫原油,胜利炼油厂原有以加工胜利原油为主的加工流程难以适应劣质高硫原油的加工,为此,1999年10月份装置进行了扩能改造,增加了Chevron公司的最新专利—上流式反应器(Up Flow Reactor,简称UFR),因此,装置又简称为UFR/VRDS。
2000年1月7日完成并投产。
装置改造后的设计处理能力150×104t/a(其中包括120×104t/a减压渣油及30×104t/a减压蜡油),主要对中东减压渣油进行脱硫、脱氮、脱金属并部分裂解为石脑油、柴油和蜡油。
设计运转初期,349℃产品馏份的MCR为<8.5%,S<0.5%,末期MCR<9.2%、S<0.8%,生产的石脑油可作为乙烯原料,柴油是优质的低硫轻柴油产品,常压渣油是优质的催化裂化原料。
2005年,随着VRDS—FCC组合工艺的投用,常压和减压渣油混合做为催化原料,催化回炼油改进本装置处理,优化了FCC装置原料性质,提高了FCC装置轻油收率。
2006年10月份,利用第五周期停工检修时机,进行了装置节能改造,主要改造内容是停开减压塔,对原料/产品换热网络进行优化和流程动改,及对加热炉烟气余热回收系统进行改造。
2006年11月14日装置开工正常。
目前随着催化剂级配及操作的不断优化,装置运行周期已延长到480天。
图3-1 渣油加氢装置方块流程图1.2 工艺原理1.2.1 工艺过程渣油加氢作为重油加工的重要手段,在整个炼厂的加工工艺中有着十分重要的地位。
渣油加氢装置工艺参数及产品质量控制方法

渣油加氢装置工艺参数及产品质量控制方法10.3.1加氢反应器R-l01入口温度反应温度是反应部分的最主要工艺参数,是脱硫,脱氮效果的主要变量,是加氢精制的重要调节参数。
反应温度主要根据原料油的性质、反应进料量、催化剂活性和产品的质量要求等因素进行选择。
操作的最佳温度是满足产品质量的最低温度。
控制目标:指令值的±1℃控制范围:375~390℃相关参数:反应炉两路出口温度TIC10501A 、TIC10501B;燃料气压控PIC10506A、PIC10506B;热高分入口温度TIC10801;反应进料量FIC10303;循环氢流量FI10901及纯度等。
控制方式:R-l01入口温度是由TIC10501A 、TIC10501B分别串级F101燃料气压控PIC10506A、PIC10506B通过控制燃料气量来实现的,如图所示。
设置的温控TIC10801是通过调整进出换热器的物料量来控制热高分入口温度。
当满足热高分温度时,应尽量关小TIC10801提高F101入口温度,减少瓦斯消耗。
反应炉负荷过小时,为了反应炉正常的燃烧,保证反应器入口温度稳定,可以适当调节TIC10801的开度,给F101以一定的调节余量,以便于反应入口温度的灵活调节。
提降温度和进料量应遵循先提量后提温,先降温后降量的原则。
影响因素:(1)F101的出口温度升高,床层温度上升。
(2)催化剂的活性提高,床层温度上升。
(3)E102、E103A/B的原料油出口温度提高,床层温度上升。
(4)循环氢流量减小,床层温度上升。
(5)原料含硫量变高,床层温度上升。
(6)原料含氮量变高,床层温度上升。
(7)原料中金属杂质含量变高,床层温度上升。
(8)原料变重,床层温度下降。
(9)循环氢纯度提高,床层温度上升。
(10)原料含水增加,床层温度波动。
调节方法:(1)通过调节F101的瓦斯量来控稳F101的出口温度。
(2)根据催化剂表现的活性和反应深度适当调整反应器入口温度。
170万渣油加氢装置培训资料装置操作法

170万渣油加氢装置培训资料装置操作法渣油加氢装置(Residue Hydrocracking Unit)是炼油厂中的一种重要设备,主要用于转化高温渣油中的重油组分,将其转化为高质量的轻质产品,以提高产品质量和增加产能。
以下是关于渣油加氢装置操作法的一些培训资料,共计1200字以上。
一、渣油加氢装置的工作原理和主要设备渣油加氢装置主要通过催化剂的作用,在高温高压的条件下将渣油中的重油组分进行裂解和重整,得到较为轻质的产品。
主要包括以下工艺流程和设备:1.进料处理:将渣油经过预热和脱盐等处理后进入催化剂床层。
2.加氢反应:在催化剂床层中,将渣油与氢气混合后,在高温高压的条件下进行化学反应,催化剂起到催化作用。
3.催化剂再生:催化剂在反应过程中逐渐失活,需要进行再生,去除积聚在催化剂上的杂质和炭质。
4.产品分离和净化:经过反应后的物料通过分离装置进行产品分离,得到不同质量级别的轻质产品。
二、装置操作注意事项1.操作前准备:操作人员应在操作前检查催化剂床层情况、催化剂再生设备等操作部位的状态。
2.安全操作:操作人员应穿戴个人防护装备,并熟悉工艺流程和装置设备的安全操作规程。
3.温度和压力控制:操作人员应控制好加氢反应的温度和压力,确保在正常工作范围内。
4.操作流程控制:按照工艺操作规程,控制好物料的进料速度、催化剂再生周期、产品分离装置的操作等,确保装置的正常运行。
5.催化剂管理:操作人员应监测催化剂的性能和活性,及时更换并处理废催化剂。
6.灾害防范:操作人员应时刻注意装置的安全状况,避免发生火灾、爆炸等意外事故,并及时响应紧急情况。
三、装置操作技巧1.合理调整操作参数:根据渣油的性质和产品要求,合理调整加氢反应的温度、压力和催化剂用量等操作参数,以达到最佳反应效果。
2.善于处理异常情况:操作人员应具备处理异常情况的能力,如催化剂塌陷、过压、过热等情况,及时采取相应的措施。
3.及时维护设备:对于装置设备的维护保养工作,应及时进行,保证装置的正常运行和使用寿命。
VRDS渣油加氢装置工艺原理

VFIDS 渣油加氢装置工艺原理1.1工艺过程渣油加氢作为重油加工的重要手段,在整个炼厂的加工工艺中有着格外重要的地位oUFR/VRDS 工艺作为现代炼油厂重油加工的重要工艺,在优化原油加工流程,提高整个企业的效益,推动炼油行业的技术进步有着格外重要的意义。
其一,做为重油深度转化的工艺,它不仅本身可转化为轻油,还可与催化裂化工艺组合,使全部渣油轻质化,从而使炼厂获得最高的轻油收率。
其二,做为一种加氢工艺,它在提高产品质量,削减污染,改善环境方面具有其它加工工艺不行替代的优势,并且可生产优质的催化裂化原料,也为催化裂化生产清洁汽油创造了条件。
UFR/VRDS 装置釆用Chevron 公司专利技术,其工艺特点:原料选择范围宽,可加工多种原油的减渣。
在原油中, 经该过程验证的有:阿拉伯中、重质原油,科威特原油,加利福尼亚原油,北坡原油,美国中部大陆原油及孤岛原油等。
UFR/VRDS 工艺最初釆用了Chevron 公司的“ICR系”列催化剂,现在催化剂己全部国产化,石油化工科学争论院开发的UFR 和固定床渣油加氢RHT 系列催化剂,抚顺石油化工争论院开发的UFR 和固定床渣油加氢FZC 系列催化剂。
催化剂以多孔氧化铝为担体,浸渍银、钻、铜等金属,具有较高的金属容纳量和较高的脱硫、脱氮活性,其HDM 率达80%, HDN 率为50%产品名称石脑油、柴油、常压渣油原加工设计力量84 [(Tt/a 减压渣油120104t/a减压渣油及3010恤减压现加工设计力量装置建设时间投产日期蜡油1988 年10 月6 日1992 年5 月第一次装置改造日期1999 年10 月20 日第一次改造投产日期2023 年1 月7 日其次次装置改造日期2023 年10 月16 日70%。
釆用多种催化剂组合的催化剂级配方案,实现渣油高转化率的同时又进展深度脱硫、脱氮、脱金属。
由于催化剂按尺寸、外形和活性进展合理级配, 从而使HDM 段达最长使用周期,同时延缓或尽可能避开了主要由铁、钙沉积引起的反响器床层压降上升的问题。
VRDS渣油加氢装置主要原料及辅助材料性质

VRDS渣油加氢装置主要原料及辅助材料性质1.1 主要原料性质URF/VRDS装置原料为阿拉伯轻质油与科威特原油(1:1)减压渣油(占渣油量的58%~66%)和孤岛减压渣油(占渣油量的42%~34%),常减压装置的减三线和焦化装置的焦化蜡油及催化装置的回炼油作为外部稀释油,进料来自常减压装置和重油原料罐区。
URF/VRDS装置的设计原料(减压渣油)性质见表6-1。
表6-1 VRDS装置设计原料性质表Fe μg.g-1 6Ca μg.g-1 5Na μg.g-1 3滤后机杂μg.g-1 40(1). 稀释油:第三、第四常减压装置的减三线蜡油,延迟焦化装置的焦化蜡油,第一和第二催化裂化装置的回炼油。
(2). 封油:第三、第四常减压装置的减三线蜡油,SSOT装置原料,罐区880#和881#蜡油。
(3). 急冷油:第三、第四常减压装置的减三线蜡油。
(4). 正常生产期间(也包括开工和停工),原料的界区条件、流量见表6-2。
表6-2 原料界区条件物流来源温度℃压力MPa流量t/h1.减压渣油常减压装置/罐区150 0.5 151.22.外来稀释油常减压、催化、焦化装置90 0.5~1.5 20~503.蜡油(开停工用VGO)罐区100 0.5 42~85VRDS的新氢是由补充氢压缩机组K-1010/1020/1030提供的。
氢气来源有一、二制氢装置产氢、乙烯电解氢、普里森氢提浓装置(PRISM)回收的高纯度氢气。
设计新氢纯度99.5%,CO+CO2最大≯50μg.g-1,氮气≯1000μg.g-1。
新氢和PRISM氢气的组成见表6-3。
表6-3 氢气组成分析注:1.* 物料平衡中不包括。
2.“-”意指低于0.04%。
1.2 主要辅助材料性质1.2.2 液体三剂1.2.2.1 渣油阻垢剂QSFH-C渣油阻垢剂具有以下性能:1、清净分散性,阻垢剂能够阻止油料中的腐蚀产物、盐类和杂质颗粒聚集沉积,减少无机垢的生成;2、抗氧化性,与被氧化的烃自由基形成惰性分子,使链反应中止,不能形成大分子聚合物;3、阻聚合性,阻止烃分子的聚合,减少有机垢的生成,4、钝化金属表面性,使设备和管道的材质在高温下不能对脱氢生焦起催化作用。
制氢装置的大概工艺原理说明
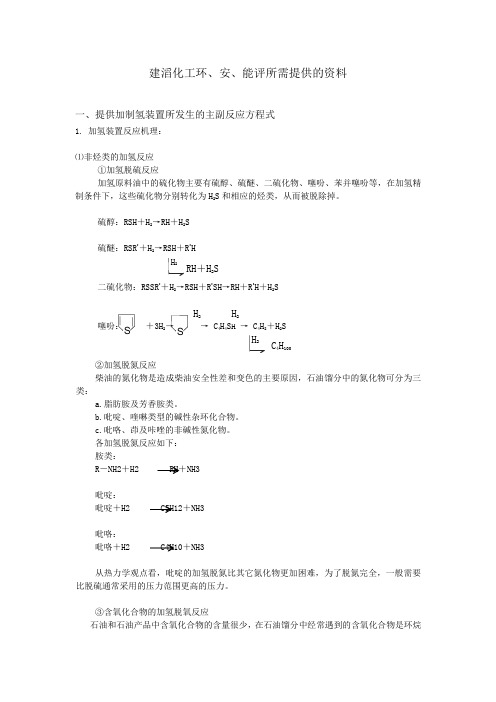
建滔化工环、安、能评所需提供的资料一、提供加制氢装置所发生的主副反应方程式1. 加氢装置反应机理:⑴非烃类的加氢反应①加氢脱硫反应加氢原料油中的硫化物主要有硫醇、硫醚、二硫化物、噻吩、苯并噻吩等,在加氢精制条件下,这些硫化物分别转化为H 2S 和相应的烃类,从而被脱除掉。
硫醇:RSH +H 2→RH +H 2S硫醚:RSR ’+H 2→RSH +R ’H二硫化物:RSSR ’+H 2→RSH +R ’SH →RH +R ’H +H 2S+3H 2→ C 4H 4SH→H 2S②加氢脱氮反应柴油的氮化物是造成柴油安全性差和变色的主要原因,石油馏分中的氮化物可分为三类:a.脂肪胺及芳香胺类。
b.吡啶、喹啉类型的碱性杂环化合物。
c.吡咯、茚及咔唑的非碱性氮化物。
各加氢脱氮反应如下: 胺类:R -NH2+H2 RH +NH3吡啶:吡啶+H2 C5H12+NH3吡咯:吡咯+H2 C4H10+NH3从热力学观点看,吡啶的加氢脱氮比其它氮化物更加困难,为了脱氮完全,一般需要比脱硫通常采用的压力范围更高的压力。
③含氧化合物的加氢脱氧反应石油和石油产品中含氧化合物的含量很少,在石油馏分中经常遇到的含氧化合物是环烷H 2H 2 C 4H 100酸。
各种含氧化合物的加氢反应:RO+H2RH+H2O⑵烃类的加氢反应在加氢精制条件下,烃类的加氢反应主要是不饱和烃和芳烃的加氢饱和。
这些反应对改善油品的质量和性能具有重要意义。
例如烯烃,特别是二烯烃的加氢可以提高油品的安定性,芳烃的加氢可以提高柴油的十六烷值。
①不饱和烃的加氢反应直馏馏分中一般不含有不饱和烃,但二次加工产品催化柴油、焦化柴油中则含有大量的不饱和烃。
这些不饱和烃在加氢精制条件下很容易饱和。
代表性反应如下:a H2→R-CH23b+H2c H2②芳烃的加氢饱和反应加氢原料油中的芳烃加氢,主要是指稠环芳烃(菲系、萘系)的加氢。
加氢活性:环烯烃>烯烃》芳烃多环>双环》单环提高反应温度,芳烃加氢转化率下降,提高反应压力,芳烃加氢转化率增大。
国内渣油加氢工艺发展概述

国内渣油加氢工艺发展概述摘要:渣油加氢处理技术是重油深加工,产品清洁化重要技术之一。
掌握固定床渣油加氢技术、移动床渣油加氢工艺、沸腾床加氢工艺、悬浮床渣油加氢裂化工艺,利用其优缺点科学规划炼化布局,对重油进行高效深度转化是炼油企业提升竞争力的关键。
关键词:渣油、加氢、悬浮床、沸腾床、移动床引言炼油企业正面临着石油重质化、劣质化而且高硫原油逐渐增多的问题。
与此同时,市场对轻质油品的需求逐渐增多,环保法规对产品质量的要求也日趋严格。
渣油加氢技术作为重油轻质化、优质化的有利手段,越来越受到重视。
渣油是原油中组分最复杂的部分,其中含有较多的金属、硫、氮及其它非理想组分。
在加氢处理的过程中,仅仅使用一种催化剂难以有效的脱除渣油中的各类杂质,国内外的渣油处理催化剂多种多样,适应不同的原料状况和产品要求。
1渣油加氢技术概述渣油加工技术由脱碳技术和加氢技术,其中脱碳技术包括热加工、溶剂脱沥青和重油催化裂化;加氢技术则包括渣油加氢处理、加氢精制和加氢裂化。
渣油脱碳工艺要减小一部分原料的H/C比,不可避免的要产生一部分气体烃和H/C比较小的缩合产物焦炭,从而使脱碳过程的轻质油收率不会很高。
而渣油加氢工艺可以很好地利用渣油中所含的碳来提高液体产品收率,使产品质量有所提高,并且可以处理高硫、相对中等金属含量和残炭含量的渣油,其操作压力和操作温度高,转化率通常为30%~50%。
渣油加氢的主要目的:一是经脱硫后制得低硫燃料油;二是经预处理后为催化裂化和加氢裂化等后续工艺提供原料。
按反应器分类有固定床、移动床、沸腾床(膨胀床)和悬浮床(浆液床)加氢工艺。
2渣油加氢工艺2.1固定床渣油加氢该工艺是在馏分油加氢技术上发展来的,原料油自上而下流入反应器,催化剂采用分级装填技术可以有效延长催化剂使用寿命和提高产品质量。
精制深度高,脱硫率一般可达90%以上。
其操作压力较高,一般为10~18MPa,温度为340~450℃,体积空速为0.1~1.0h-1,化学氢耗为80~240Nm3/m3,大于538℃渣油转化率一般为10~50%。
渣油加氢技术工艺原理

渣油加氢技术工艺原理由于石油资源有限、原油变重变劣、中间馏分油的需求量增加及环保法规越来越严格等因素,渣油轻质化技术不断发展,通过渣油加氢处理后的渣油,送到催化裂化装置处理,生产出大量的合格轻质油。
减压渣油是原油经过加工后密度最大、杂质组分含量最高的油品,含有相当多的金属、硫、氮、及残炭等物质,杂质金属、氮会使下游装置催化剂失去活性,严重影响下游装置的生产周期;硫化物会腐蚀生产装置的设备及管线;残炭在下游装置催化裂化装置深加工过程中,极不稳定,很容易结焦,影响催化裂化装置的长周期运行;在装置原料中掺入减压重蜡油与焦化蜡油,有效降低渣油进料的粘度与杂质含量,利于催化加氢反应的进行,利于装置的操作与长周期运行。
本装置采用固定床加氢工艺,在适当的温度、压力、氢油比和空速条件下,原料油和氢气在催化剂的作用下进行反应,使油品中的杂质,即硫、氮、氧化物转化成为相应的易于除去的H2S、NH3和H2O而脱除,重金属杂质与H2S反应生成金属硫化物沉积在催化剂上,稠环芳烃及一部分不饱和烃得到加氢饱和,为下游装置生产出合格的原料油,同时副产出部分柴油及石脑油。
在渣油加氢处理过程中,所发生的化学反应很多,也非常复杂,但主要有以下几种反应发生:1)加氢脱硫反应2)加氢脱金属反应3)加氢脱氮反应4)加氢脱残碳反应5)加氢脱氧反应6)芳烃饱和反应7)烯烃饱和反应8)加氢裂化反应9)缩合生焦反应2.1加氢脱硫反应(HDS)渣油加氢脱硫反应是渣油加氢处理过程中所发生的最主要的化学反应,在催化剂和氢气的作用下,通过加氢脱硫反应,各种含硫化合物转化为不含硫的烃类和H 2S 。
烃类留在产品中,而H 2S 从反应物中脱除。
原油中大部分的硫存在于渣油中,渣油中的硫主要分布在芳烃、胶质和沥青质中,其中绝大部分的硫以噻吩和噻吩衍生物的形式存在。
通过氢解反应将这种大分子的C -S 键断开,使S 转化为H 2S 。
以噻吩和苯并噻吩为例,加氢脱硫反应式为:存在于非沥青质中的硫,在加氢条件下较容易脱除,可达到较高的转化深度,但存在于沥青质中的硫,由于沥青质的大分子结构,则很难脱除,因此,渣油加氢脱硫过程的脱硫率是有一定限度的。
LH_04重油加氢脱铁催化剂在炼油厂VRDS装置上的工业应用
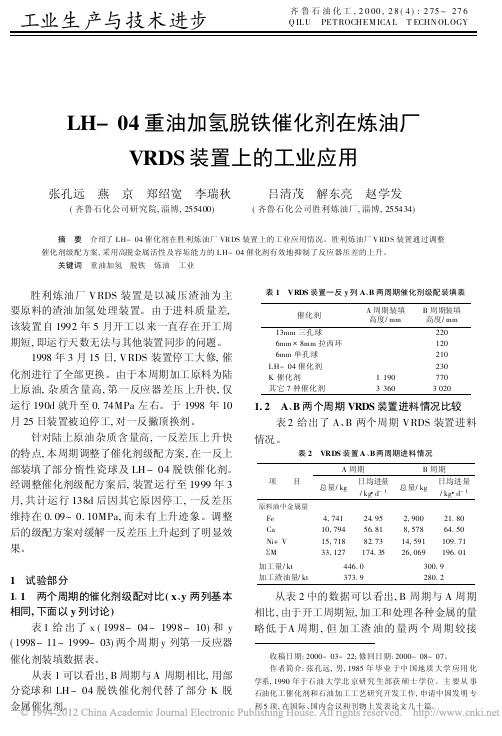
LH-04重油加氢脱铁催化剂在炼油厂VRDS装置上的工业应用张孔远燕京郑绍宽李瑞秋吕清茂解东亮赵学发(齐鲁石化公司研究院,淄博,255400)(齐鲁石化公司胜利炼油厂,淄博,255434)摘要介绍了LH-04催化剂在胜利炼油厂VRDS装置上的工业应用情况。
胜利炼油厂VRDS装置通过调整催化剂级配方案,采用高脱金属活性及容垢能力的LH-04催化剂有效地抑制了反应器压差的上升。
关键词重油加氢脱铁炼油工业胜利炼油厂VRDS装置是以减压渣油为主要原料的渣油加氢处理装置。
由于进料质量差,该装置自1992年5月开工以来一直存在开工周期短,即运行天数无法与其他装置同步的问题。
1998年3月15日,VRDS装置停工大修,催化剂进行了全部更换。
由于本周期加工原料为陆上原油,杂质含量高,第一反应器差压上升快,仅运行190d就升至0.74MPa左右。
于1998年10月25日装置被迫停工,对一反撇顶换剂。
针对陆上原油杂质含量高,一反差压上升快的特点,本周期调整了催化剂级配方案,在一反上部装填了部分惰性瓷球及LH-04脱铁催化剂。
经调整催化剂级配方案后,装置运行至1999年3月,共计运行138d后因其它原因停工,一反差压维持在0.09~0.10MPa,而未有上升迹象。
调整后的级配方案对缓解一反差压上升起到了明显效果。
1试验部分111两个周期的催化剂级配对比(x、y两列基本相同,下面以y列讨论)表1给出了x(1998-04~1998-10)和y (1998-11~1999-03)两个周期y列第一反应器催化剂装填数据表。
从表1可以看出,B周期与A周期相比,用部分瓷球和LH-04脱铁催化剂代替了部分K脱金属催化剂。
表1VRDS装置一反y列A、B两周期催化剂级配装填表催化剂A周期装填高度/mmB周期装填高度/mm 13mm三孔球2206mm@8mm拉西环1206mm单孔球210LH-04催化剂230K催化剂1190770其它7种催化剂336030201.2A、B两个周期VRDS装置进料情况比较表2给出了A、B两个周期VRDS装置进料情况。
渣油加氢工艺技术PPT课件

26
前 言--加氢技术发展历程
• 国内加氢技术发展历程和概况
– 重油加氢处理领域技术开发 • 2002年上流式渣油加氢催化剂工业应用; • 2006年,自主技术建成海南310万吨/年RDS 装置 ; • 2008年,国产渣油加氢催化剂在印尼国家石油公 司ARDS应用; • RIPP开发渣油加氢—催化裂化双向组合技术; • FRIPP开发了渣油加氢—催化裂化深度耦合技术 ,即将在石家庄应用;
- 1、下载文档前请自行甄别文档内容的完整性,平台不提供额外的编辑、内容补充、找答案等附加服务。
- 2、"仅部分预览"的文档,不可在线预览部分如存在完整性等问题,可反馈申请退款(可完整预览的文档不适用该条件!)。
- 3、如文档侵犯您的权益,请联系客服反馈,我们会尽快为您处理(人工客服工作时间:9:00-18:30)。
加氢反应举例如下:
硫醇氢气催化剂烷烃硫化氢
噻吩氢气催化剂烷烃硫化氢
1.2.2加氢脱氮反应(HDN)
原料中的含氮化合物经加氢后生成氨和烃类,但氮仅部分脱除。随后氨从反应产物中脱除,仅留下烃类在产品中。脱氮的反应热大约为2730KJ/m3耗氢。原料的含氮量为0.8%,脱除率为60%~73%,因此它对反应热的贡献只有脱硫反应的70%左右。由于积垢以及芳烃的逆平衡转换都会降低脱氮率,因此脱氮率从运转初期(SOR)的73%下降到运转末期的60%左右。
其二,做为一种加氢工艺,它在提高产品质量,减少污染,改善环境方面具有其它加工工艺不可替代的优势,并且可生产优质的催化裂化原料,也为催化裂化生产清洁汽油创造了条件。
UFR/VRDS装置采用Chevron公司专利技术,其工艺特点:原料选择范围宽,可加工多种原油的减渣。在原油中,经该过程验证的有:阿拉伯中、重质原油,科威特原油,加利福尼亚原油,北坡原油,美国中部大陆原油及孤岛原油等。
烯烃加氢反应举例如下:
烯烃氢气催化剂烷烃
1.2.4芳烃饱和反应
原料油中的某些芳烃被加氢后生成环烷烃。芳烃饱和反应占总氢耗和总反应热量的很小但很重要。反应放热量在1470~3150KJ/m3耗氢之间,这取决于芳烃饱和的形式。一般来说,压力越高,温度越低,芳烃饱和程度越高。
芳烃饱和反应举例如下:
芳烃氢气催化剂环烷烃
1.2.1加氢脱硫反应(HDS)
脱硫是原料油中的含硫化合物与氢反应,生成烃类和硫化氢(H2S),从而脱除进料中的硫。反应的副产品硫化氢经过一系列的高、低压分离器从反应产物中分离出来,只剩下烃类产品。硫化氢在高压硫化氢吸收塔(C-1340和C-1341)内基本得以脱除。典型的脱硫反应是将硫醇或噻吩转化为直链或带侧链烷烃和硫化氢。
1.2.6脱金属(HDM)
UFR/VRDS催化剂也能脱除在渣油的环状结构化合物中的金属。含金属的烃分子与硫化氢反应生成金属硫化物,沉积在催化剂表面上。催化剂的活性随着这些金属硫化物覆盖在催化剂(钴、镍、铂)的活性中心而不断下降。金属硫化物沉积在催化剂孔隙的入口附近要比在催化剂颗粒内部更加严重,结果是孔径开度逐渐变小,导致催化剂活性迅速丧失。脱金属(HDM)催化剂一般比脱硫(HDS)催化剂的孔隙大,以防止孔隙的入口堵塞。为了获得所期望的催化剂活性,最好迫使金属沉积在保护反应器的脱金属(HDM)催化剂上,以防止第二个固定床反应器的催化剂过早失去活性。这个反应器床层上的催化剂孔较小,大多数的加氢脱硫反应也发生于此。
该工艺与FCC工艺组合后,大大提高了炼厂轻油收率,增加了经济效益
UFR/VRDS装置概况见表3-1。
表3-1装置概况一览
产品名称
石脑油、柴油、常压渣油
原加工设计能力
84×104t/a减压渣油
现加工设计能力
120×104t/a减压渣油及30×104t/a减压蜡油
装置建设时间
1988年10月6日
量氢气存在的情况下,把大的烃类分子变成小分子的反应。它几乎发生在反应的整个过程中。加氢裂化的反应热大约为1890KJ/m3耗氢,它占总反应热的大部分。胜利炼油厂UFR/VRDS装置的一个主要目的是生产低硫燃料油,侧重在裂解成低沸点的产品上。为此,该装置要在一个比正常运转初期更高的温度下操作,且要维持到末期,导致从运转初期到末期的气体产率增加。然而,由于催化剂积垢的影响,各馏分产品的产率都稍微低于设计预期的运转末期值。还有,高温下的加氢裂化增加了催化剂上的生焦,并且引起了芳烃饱和的逆平衡转移,它们都使脱氮率降低。
VRDS渣油加氢装置工艺原理
1.1工艺过程
渣油加氢作为重油加工的重要手段,在整个炼厂的加工工艺中有着十分重要的地位。UFR/VRDS工艺作为现代炼油厂重油加工的重要工艺,在优化原油加工流程,提高整个企业的效益,推动炼油行业的技术进步有着十分重要的意义。
其一,做为重油深度转化的工艺,它不仅本身可转化为轻油,还可与催化裂化工艺组合,使全部渣油轻质化,从而使炼厂获得最高的轻油收率。
加氢脱氮反应举例如下:
胺氢气催化剂烷烃氨
1.2.3烯烃饱和反应
烯烃饱和是加氢反应中进行得非常快的反应,而且几乎所有的烯烃都被饱和。这些反应的反应热大约为5040KJ/m3耗氢。然而,渣油中烯烃的含量是非常低,因此烯烃饱和对于反应器中总的放热并不多。如果UFR/VRDS原料油中烯烃含量较多(如裂解料),就应注意控制第一床层的温度。
UFR/VRDS工艺最初采用了Chevron公司的“ICR”系列催化剂,现在催化剂已全部国产化,石油化工科学研究院开发的UFR和固定床渣油加氢RHT系列催化剂,抚顺石油化工研究院开发的UFR和固定床渣油加氢FZC系列催化剂。催化剂以多孔氧化铝为担体,浸渍镍、钴、铜等金属,具有较高的金属容纳量和较高的脱硫、脱氮活性,其HDM率达80%,HDN率为50%~70%。采用多种催化剂组合的催化剂级配方案,实现渣油高转化率的同时又进行深度脱硫、脱氮、脱金属。由于催化剂按尺寸、形状和活性进行合理级配,从而使HDM段达最长使用周期,同时延缓或尽可能避免了主要由铁、钙沉积引起的反应器床层压降升高的问题。
加氢处理最基本的反应,按转化率从大到小的顺序为加氢脱硫(HDS),加氢脱金属(HDM),加氢脱氮(HDN),加氢裂化和芳烃饱和。对于VRDS装置来说,脱硫、脱氮、脱残碳和芳烃饱和都是构成氢耗和放热的主要反应。下面将分别对各反应过程进行简要介绍。在反应方程式中,字母“R”代表一个高分子的烃基,而碳原子(C)和氢原子(H)仅代表参与反应的一小部分。
1992年5月
第一次装置改造日期
1999年10月20日
第一次改造投产日期
2000年1月7日
第二次装置改造日期
2006年10月16日
第二次改造投产日期
2006年11月14日
生产厂
胜利炼油厂
建筑面积
1900m2
现有人员
117(2011年5月)
1.2生产原理
加氢处理反应是在高温、高压条件下进行,因此加氢处理单元需要特殊的反应器。在中石化xxUFR/VRDS装置中,冷高分(CHPS)的操作压力为15.11~15.44MPa,从开工初期(SOR)到开工末期(EOR),催化剂的平均温度(CAT)将从390℃升到406℃。