关于汽车转向节的铸造问题
有关铸造式汽车转向节加工工艺分析
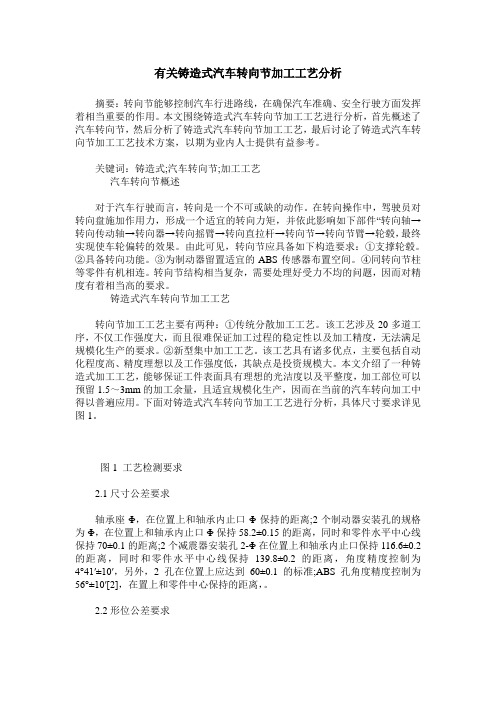
有关铸造式汽车转向节加工工艺分析摘要:转向节能够控制汽车行进路线,在确保汽车准确、安全行驶方面发挥着相当重要的作用。
本文围绕铸造式汽车转向节加工工艺进行分析,首先概述了汽车转向节,然后分析了铸造式汽车转向节加工工艺,最后讨论了铸造式汽车转向节加工工艺技术方案,以期为业内人士提供有益参考。
关键词:铸造式;汽车转向节;加工工艺汽车转向节概述对于汽车行驶而言,转向是一个不可或缺的动作。
在转向操作中,驾驶员对转向盘施加作用力,形成一个适宜的转向力矩,并依此影响如下部件“转向轴→转向传动轴→转向器→转向摇臂→转向直拉杆→转向节→转向节臂→轮毂,最终实现使车轮偏转的效果。
由此可见,转向节应具备如下构造要求:①支撑轮毂。
②具备转向功能。
③为制动器留置适宜的ABS传感器布置空间。
④同转向节柱等零件有机相连。
转向节结构相当复杂,需要处理好受力不均的问题,因而对精度有着相当高的要求。
铸造式汽车转向节加工工艺转向节加工工艺主要有两种:①传统分散加工工艺。
该工艺涉及20多道工序,不仅工作强度大,而且很难保证加工过程的稳定性以及加工精度,无法满足规模化生产的要求。
②新型集中加工工艺。
该工艺具有诸多优点,主要包括自动化程度高、精度理想以及工作强度低,其缺点是投资规模大。
本文介绍了一种铸造式加工工艺,能够保证工件表面具有理想的光洁度以及平整度,加工部位可以预留1.5~3mm的加工余量,且适宜规模化生产,因而在当前的汽车转向加工中得以普遍应用。
下面对铸造式汽车转向节加工工艺进行分析,具体尺寸要求详见图1。
图1 工艺检测要求2.1尺寸公差要求轴承座Φ,在位置上和轴承内止口Φ保持的距离;2个制动器安装孔的规格为Φ,在位置上和轴承内止口Φ保持58.2±0.15的距离,同时和零件水平中心线保持70±0.1的距离;2个减震器安装孔2-Φ在位置上和轴承内止口保持116.6±0.2的距离,同时和零件水平中心线保持139.8±0.2的距离,角度精度控制为4°41′±10′,另外,2孔在位置上应达到60±0.1的标准;ABS孔角度精度控制为56°±10′[2],在置上和零件中心保持的距离,。
铝合金转向节挤压铸造技术研究与应用

铝合金转向节挤压铸造技术研究与应用摘要:近年来,随着能源紧缺及对环境保护的需要,各国对汽车燃油消耗效率及温室气体排放量制定了更加严格的法规与标准。
而汽车轻量化则是降低燃油消耗的重要途径之一,也是汽车生产商研发的主要目标。
因此,以铝为代表的轻质合金材料得到了越来越广泛的应用。
本文对挤压铸造生产铝合金转向节工艺进行研究,在不同的机型上用挤压铸造工艺开发的铝合金转向节各项性能指标可完全达到技术要求。
关键词:铝合金;转向节;挤压铸造引言采用有色轻金属材料代替黑色金属材料是当前国际上汽车轻量化的主要途径,为使汽车减轻自重,便要求汽车零部件必须轻量化、薄壁化、精确化、强韧化。
所以,汽车的钢铁材质零部件不断被质量轻的铝合金件所取代,在成形工艺上以挤压铸造替代普通铸造及锻造,以达到提高毛坯的精度、减少加工余量、减少原材料消耗,从而实现减重、降低成本的目的。
本文对挤压铸造机生产铝合金转向节的特点进行分析论述,供同行参考。
1再生铝概念再生铝是由废旧废铝合金材料或者含铝的废料,经重新熔化提炼而得到的铝合金或铝金属,是金属铝的一个重要来源,再生铝主要是以铝合金的形式出现的。
再生铝以废铝作为主要原料,经预处理、熔炼、精炼、铸锭等生产工序后得到铝合金。
铝的抗腐蚀性强,在使用过程中损耗程度极低,且在多次重复循环利用后不会丧失其基本特性,具有极高的再生利用价值。
2压铸工艺一体化压铸实为真空压铸工艺加入高真空控制系统,需要高精度传感器控制抽真空过程。
工艺流程为合模、浇注、真空开启、型腔抽真空排气、压射、开模、取件、喷涂、再次合模等。
在压铸过程中,由高精度真空传感器控制真空罐、浇注排气阀和型腔排气阀,并通过参数设定来触发四个接触点:浇注真空开始、浇注真空结束、型腔真空开始和型腔真空结束。
压铸的高速充型易导致压室或型腔中的气体无法完全排出,气体卷入金属液会以气孔的形式存在于铸件中,无法焊接,降低力学性能,所以一体压铸必须配置型腔抽真空系统。
汽车转向节的铸造问题

技术创新方法(TRIZ)学习报告作品名称:汽车转向节的铸造问题院级名称:机电工程技术学院班级名称:应用电子103姓名:陈伟2011-2012学年第2学期(START)一、应用背景及意义:汽车转向节是连接汽车方向盘与前轮轮轴的部件,并与减震器相连。
二、主要功能:1:与前轮轴相连接,承担轴传来的力和力矩。
2:汽车转向的转动部件。
3吸收汽车行进过程中的震荡。
它是汽车中应力最为集中、最为复杂的零件,直接关系到汽车的安全性能,因此它的设计标准十分严格,制造过程和产品测试都要求符合规范。
三、矛盾定义及创新原理目前转向节是由球墨铸铁为主要原料铸造而成,并加入碳、硅等元素,在微观结构上在铁原子之间形成碳或硅小颗粒以加强合金钢的延展性(韧性),宏观上提高零件的抗拉强度和疲劳强度。
而且碳、硅元素的含量要求适当,过多会使合金变脆而导致强度下降。
2001年大众汽车(墨西哥)公司引进一套转向节铸造生产线,主要步骤是在感应电炉中在1400℃高温下熔化铸铁,以镁作催化剂混合适量沙粒(硅)产生反应形成熔液浇注入砂型中,冷却后打破砂型对铸件进行检测,进一步机械加工最终成品。
生产线将型砂经传送带回收处理循环利用,熔渣与不合格铸件同样用升降机回收作为原料再次放入电炉。
生产初期,应用此生产线使生产效率得以大幅提高,但同时也产生了铸件废品率(主要为缩型)也大幅提高的问题,经研究发现是由于熔液中沙粒含量超标(使熔液流动性差)造成的。
导致生产成本升高以及效率下降。
图4 生产线示意图有何经济效益和社会效益:应用TRIZ理论对问题进行分析和创新后,在对生产线稍加改造后,问题得以有效解决,产品不合格率由大于10%降到低于3%,同时不增加任何额外投入,在生产成本不变的情况下,简化了生产线,缩短了生产周期。
问题描述:使用生产线后,整个铸造过程的操作性提高了,但相应的也产生了铸件废品率增加了。
研究发现,问题的产生是由于感应电炉中的熔液的沙粒含量超标,导致熔液流动性差造成的。
铝合金汽车转向节精密铸造工艺研究

第16卷第3期精密成形工程2024年3月JOURNAL OF NETSHAPE FORMING ENGINEERING181铝合金汽车转向节精密铸造工艺研究赵海涛1,甘万兵1,晏洋1,席小龙1,姚会婷1,陈毅1,丁华锋1,2*(1.湖北三环锻造有限公司,湖北襄阳 441700;2.湖北文理学院汽车与交通工程学院,湖北襄阳 441053)摘要:目的对某铝合金汽车转向节的精密铸造工艺进行设计与优化研究,以得到合格的铝合金汽车转向节的精密铸造工艺方案。
方法结合铝合金转向节铸件的结构特征、铸件材料特性和铸造经验,在转向节铸件主体部和鹅颈部各开设一个内浇口,设计了铝合金转向节初始浇注方案;通过在初始工艺方案中铸件缺陷较严重的区域设置补缩冒口、在铸件顶部增设排气道等措施给出了铝合金汽车转向节的优化浇注方案,基于ProCAST软件建立了铝合金转向节精密铸造2种浇注方案的有限元模型,对铝合金转向节精密铸造的充型过程、凝固过程及缩孔缩松特性进行了数值模拟与分析。
结果铝合金转向节铸件初始浇注方案的充型过程相对稳定流畅,铸件在凝固过程中有孤立液相区的形成,完全凝固后铸件中间部位存在大面积缩松缩孔缺陷;优化浇注方案能够控制金属液的流动、充型顺序及凝固特性,铸件的整个凝固过程基本呈中间对称分布,最后凝固区域位于补缩冒口内部,最大缩孔缩松率控制在2%以下。
结论优化浇注方案的设计合理且有效,能够有效地消除铝合金转向节铸件的缺陷。
关键词:铝合金;转向节;精密铸造;铸造缺陷;工艺设计;数值模拟DOI:10.3969/j.issn.1674-6457.2024.03.020中图分类号:TG249.5 文献标志码:A 文章编号:1674-6457(2024)03-0181-07Precision Casting Process of Aluminum Alloy Automobile Steering KnuckleZHAO Haitao1, GAN Wanbing1, YAN Yang1, XI Xiaolong1, YAO Huiting1, CHEN Yi1, DING Huafeng1,2*(1. Hubei Tri-Ring Forging Co., Ltd., Hubei Xiangyang 441700, China; 2. School of Automotive and Traffic Engineering,Hubei University of Arts and Sciences, Hubei Xiangyang 441053, China)ABSTRACT: The work aims to design and optimize the precision casting process of a certain type of aluminum alloy automo-bile steering knuckles to obtain a qualified precision casting process scheme of aluminum alloy automobile steering knuckles.Based on the structural characteristics, material properties and casting experience of aluminum alloy steering knuckle castings, an ingate was opened in the main body and the goose neck of the steering knuckle casting respectively, and an initial pouring scheme of aluminum alloy steering knuckles was designed. The optimized pouring scheme of aluminum alloy automobile steer-ing knuckles was given by setting feeding risers in the area with serious casting defects in the initial process scheme and adding exhaust ducts at the top of the casting. Based on ProCAST software, the finite element models of two pouring schemes for pre-cision casting of aluminum alloy steering knuckles were established, and the filling process, solidification process and shrinkage porosity characteristics of precision casting of aluminum alloy steering knuckles were numerically simulated and analyzed. The filling process of the initial pouring scheme of the aluminum alloy steering knuckle casting was relatively stable and smooth,收稿日期:2024-01-12Received:2024-01-12引文格式:赵海涛, 甘万兵, 晏洋, 等. 铝合金汽车转向节精密铸造工艺研究[J]. 精密成形工程, 2024, 16(3): 181-187. ZHAO Haitao, GAN Wanbing, YAN Yang, et al. Precision Casting Process of Aluminum Alloy Automobile Steering Knuckle[J]. Journal of Netshape Forming Engineering, 2024, 16(3): 181-187.*通信作者(Corresponding author)182精密成形工程 2024年3月and the isolated liquid phase zone was formed during the solidification process of the casting. After solidification, there was a large area of shrinkage defects in the middle of the casting. The optimized pouring scheme could control the flow, filling se-quence and solidification characteristics of the molten metal. The whole solidification process of the casting basically presenteda symmetrical distribution in the middle. The final solidification area was located inside the feeding riser, and the maximumshrinkage porosity was controlled below 2%. The design of optimized pouring scheme is reasonable and effective, which can effectively eliminate the defects of aluminum alloy steering knuckle castings.KEY WORDS: aluminum alloy; steering knuckle; precision casting; casting defects; process design; numerical simulation随着全球环保要求的不断提高,对车辆排放标准和燃油效率的要求也更为严格[1]。
高端商务车铝合金转向节精密铸锻复合成形工艺优化
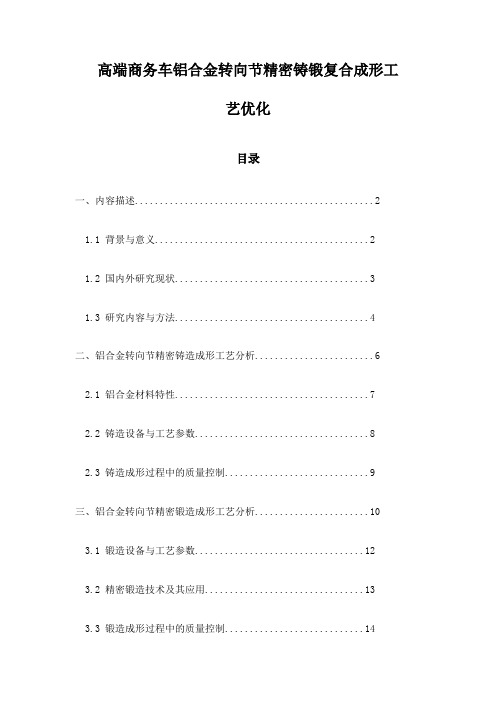
高端商务车铝合金转向节精密铸锻复合成形工艺优化目录一、内容描述 (2)1.1 背景与意义 (2)1.2 国内外研究现状 (3)1.3 研究内容与方法 (4)二、铝合金转向节精密铸造成形工艺分析 (6)2.1 铝合金材料特性 (7)2.2 铸造设备与工艺参数 (8)2.3 铸造成形过程中的质量控制 (9)三、铝合金转向节精密锻造成形工艺分析 (10)3.1 锻造设备与工艺参数 (12)3.2 精密锻造技术及其应用 (13)3.3 锻造成形过程中的质量控制 (14)四、铝合金转向节精密铸锻复合成形工艺优化 (15)4.1 复合成形工艺设计 (16)4.2 材料选择与性能预测 (18)4.3 工艺参数优化与仿真验证 (19)4.4 工艺实施与效果评估 (20)五、实验设计与结果分析 (21)5.1 实验材料与设备 (22)5.2 实验方案设计 (23)5.3 实验结果与分析 (25)5.4 成果总结与讨论 (27)六、结论与展望 (28)6.1 研究成果总结 (29)6.2 存在问题与不足 (30)6.3 后续研究方向与应用前景展望 (31)一、内容描述本文档主要研究高端商务车铝合金转向节精密铸锻复合成形工艺的优化。
随着汽车行业的发展,对汽车零部件的性能要求越来越高,尤其是在安全性、舒适性和节能性方面。
铝合金转向节作为汽车转向系统的关键部件,其性能直接影响到整车的安全和操控性能。
对铝合金转向节的制造工艺进行优化具有重要的实际意义。
本文首先介绍了高端商务车铝合金转向节的市场需求和发展趋势,分析了现有铸造和锻造工艺在生产过程中存在的问题,如成本高、效率低、产品性能不稳定等。
针对这些问题,本文提出了一种精密铸锻复合成形工艺,通过将铸造和锻造工艺相结合,实现铝合金转向节的高效、精密制造。
本文从以下几个方面对精密铸锻复合成形工艺进行了优化:优化铸造工艺参数,提高铝合金转向节的致密度和力学性能;改进锻造工艺流程,提高铝合金转向节的成型精度和表面质量;引入先进的热处理工艺,改善铝合金转向节的组织和性能;采用智能化设备和自动化生产线,提高生产效率和产品质量稳定性。
铸态高强度高韧性QT550-10汽车转向节铸件开发
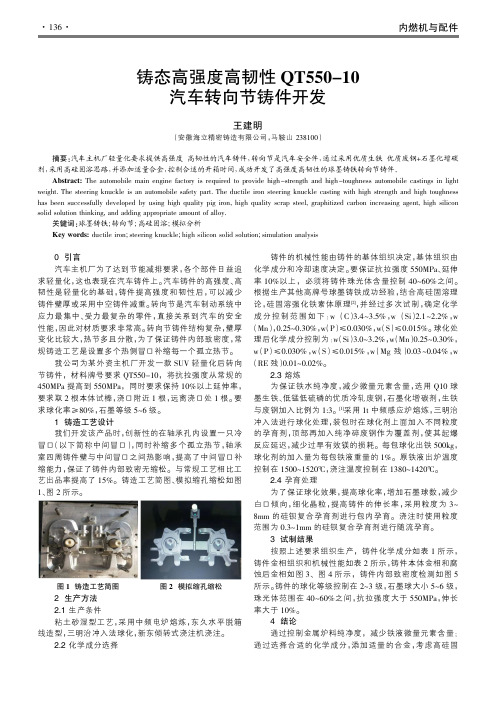
1、图2所示。
图1铸造工艺简图图2模拟缩孔缩松2生产方法2.1生产条件粘土砂湿型工艺,采用中频电炉熔炼,东久水平脱箱线造型,三明治冲入法球化,新东倾转式浇注机浇注。
2.2化学成分选择编号w (C )w (Si )w (Mn )w (S )P )w (Cu )w (Mg )1234563.403.453.483.463.503.443.183.153.123.163.113.140.300.280.270.290.280.270.0110.0120.0100.0120.0110.0100.0260.0250.0240.0250.0260.0220.560.580.550.570.580.570.0410.0400.0450.0430.0420.043表1试制化学成分汇总%)表本体试样的金相和机械性能编号球化级别(级)石墨大小(级)珠光体(体积分数%)渗碳体(%)抗拉强度(MPa )冲击韧度(/J ·cm -2)伸长率(%)硬度(HBS )12345622232265665655505555605500000062063561558561060550586562556311.812.410.813.212.010.6202212208213216206溶,通过硅固溶强化铁素体;并且自动造型线故障率低,保证了开箱时间,从而保证了铸件的冷却速度;通过这些措施,保证了粘土砂湿型工艺稳定生产铸态QT550-10球墨铸铁转向节铸件。
参考文献:[1]李蒙.铸铁QT600-10球铁的试制[A].2009中国铸造活动周论文集[C].沈阳:全国铸造学会,2009.[2]张伯明,王机祥.高Si 球墨铸铁的新发展QT600-10[J].现代铸铁,2013(5):49-58.[3]郑康,周建明,崔十达.铸态珠光体球墨铸铁活塞环毛坯的研制[J].内燃机配件,1987(03):1-9.图3本体球化率图4腐蚀后金相图5铸件解剖着色检测。
汽车制动器铸件生产中的质量问题与对策
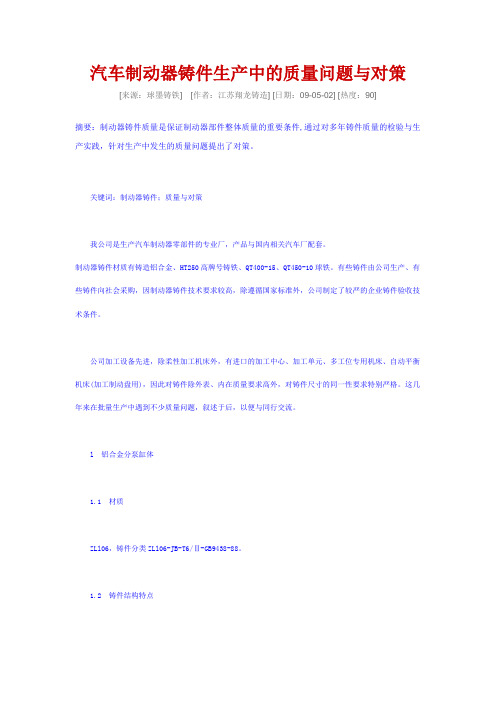
汽车制动器铸件生产中的质量问题与对策[来源:球墨铸铁][作者:江苏翔龙铸造] [日期:09-05-02] [热度:90]摘要:制动器铸件质量是保证制动器部件整体质量的重要条件,通过对多年铸件质量的检验与生产实践,针对生产中发生的质量问题提出了对策。
关键词:制动器铸件;质量与对策我公司是生产汽车制动器零部件的专业厂,产品与国内相关汽车厂配套。
制动器铸件材质有铸造铝合金、HT250高牌号铸铁、QT400-15、QT450-10球铁。
有些铸件由公司生产、有些铸件向社会采购,因制动器铸件技术要求较高,除遵循国家标准外,公司制定了较严的企业铸件验收技术条件。
公司加工设备先进,除柔性加工机床外,有进口的加工中心、加工单元、多工位专用机床、自动平衡机床(加工制动盘用),因此对铸件除外表、内在质量要求高外,对铸件尺寸的同一性要求特别严格。
这几年来在批量生产中遇到不少质量问题,叙述于后,以便与同行交流。
l 铝合金分泵缸体1.1 材质ZLl06,铸件分类ZLl06-JB-T6/Ⅱ-GB9438-88。
1.2 铸件结构特点分泵缸体有多种尺寸,重量0.1-0.2kg,前泵为盲孔缸体、后泵为通孔缸体,缸孔加工粗糙度Ra0.4,压力试验12.7MPa。
1.3 曾发生的质量问题1.3.1 缸孔出现氧化夹渣(1)成因:属二次氧化夹渣,主要是由于浇注系统设计不当,铝液充填型腔发生喷射、飞溅。
(2)对策:采用蛇形浇注系统,内浇口改为底注。
1.3.2 缸孔出现硬质点(1)成因:铝液被Al2O3夹杂严重污染,Al2O3硬脆,HV=682~1354,是铝基体的10~20倍,加工中刀锋与Al2O3相遇产生崩刀,使缸孔粗糙度达不到.Ra0.4而报废。
(2)对策:①提高炉料清洁度,生锈的原料、被机油污染的浇冒口回炉料禁用。
②控制炉料中的回炉料比例,尤其是含Fe量大于0.5%者慎用。
③严格按熔化工艺规程要求熔炼,精炼除气,保温合金。
④严禁铝液超出浇注温度上限、长时间存放。
汽车转向节差压铸造及淬火过程应力应变场数值模拟
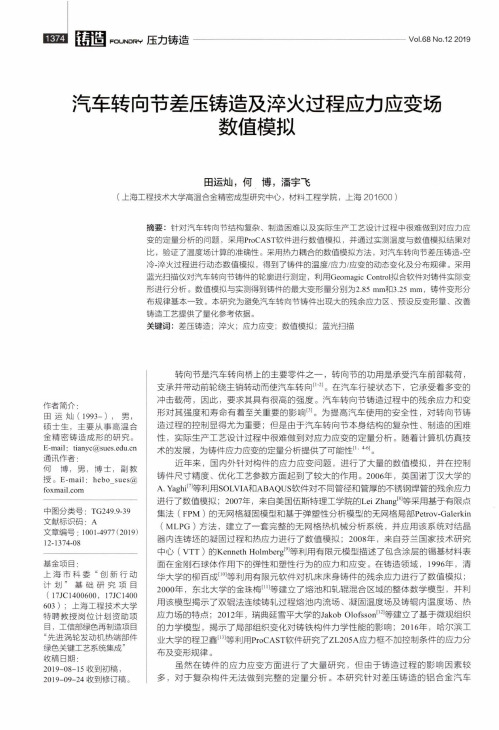
转 向 节 是 汽 车 转 向 桥 上 的 主 要 零 件 之 一 ,转 向 节 的 功 用 是 承 受 汽 车 前 部 载 荷 , 支 承 并 带 动 前 轮 绕 主 销 转 动 而 使 汽 车 转 向 在 汽 车 行 驶 状 态 下 ,它承受着多变的 冲 击 载 荷 ,因 此 ,要 求 其 具 有 很 高 的 强 度 。汽 车 转 向 节铸造过程中的残余应力和变 形 对 其 强 度 和 寿 命 有 着 至 关 重 要 的 影 响 [3]。为 提 高 汽 车 使 用 的 安 全 性 ,对转向节铸 造 过 程 的 控 制 显 得 尤 为 重 要 ;但 是 由 于 汽 车 转 向 节 本 身 结 构 的 复 杂 性 、制造的困难 性 ,实 际 生 产 工 艺 设 计 过 程 中 很 难 做 到 对 应 力 应 变 的 定 量 分 析 。随着计算机仿真技 术 的 发 展 ,为 铸 件 应 力 应 变 的 定 量 分 析 提 供 了 可 能 性 。
转 向 节 残 余 应 力 大 、产 生 的 变 形 大 等 问 题 ,尝试采用 ProCAST铸 造 仿 真 软 件 ,对 铸 件 铸 造 过 程 的 应 力 应 变 场 进 行 了 数 值 模 拟 ,得 到 了 其 冷 却 过 程 中 温 度 /应 力 / 应 变 的 动 态 变 化 及 分 布 规 律 。同时采用热电偶测温的 方 法 测 定 了 模 具 特 征 位 置 的 温 度 变 化 ,采用蓝光扫描 仪 对 汽 车 转 向 节 ■ 铸 件 的 轮 廓 进 行 测 定 ,利 用 G e o m a g ic Control拟 合 软 件 对 铸 件 实 际 变 形 进 行 分 析 ,从而验证 数 值 模 拟 结 果 ,为 避 免 汽 车 转 向 节 铸 件 出 现 大 的 残 余 应 力 区 、改善铸造工艺提供了量化参考依据。
汽车转向节锻造说明书
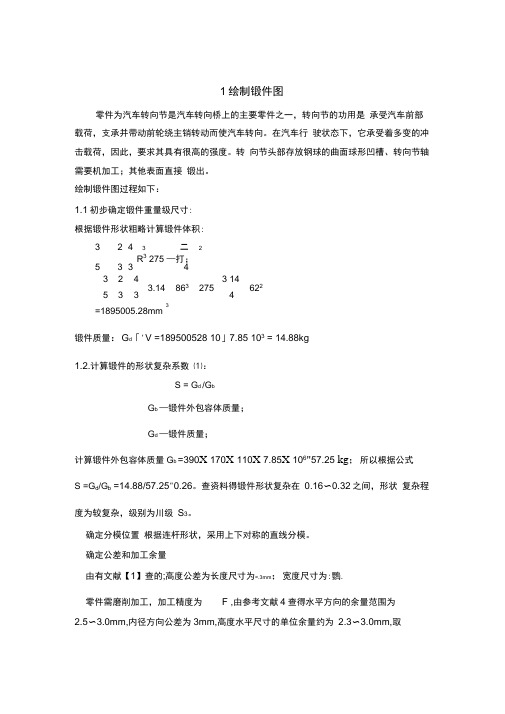
1绘制锻件图零件为汽车转向节是汽车转向桥上的主要零件之一,转向节的功用是承受汽车前部载荷,支承并带动前轮绕主销转动而使汽车转向。
在汽车行驶状态下,它承受着多变的冲击载荷,因此,要求其具有很高的强度。
转向节头部存放钢球的曲面球形凹槽、转向节轴需要机加工;其他表面直接锻出。
绘制锻件图过程如下:1.1初步确定锻件重量级尺寸:根据锻件形状粗略计算锻件体积:3 24 3二2R3 275 —打;5 3 3 43 24 3 143.14 863275 6225 3 3 43=1895005.28mm锻件质量:G d「'V =189500528 10」7.85 103= 14.88kg1.2.计算锻件的形状复杂系数⑴:S = G d /G bG b —锻件外包容体质量;G d —锻件质量;计算锻件外包容体质量G b =390X 170X 110X 7.85X 106"57.25 kg;所以根据公式S =G d/G b=14.88/57.25"0.26。
查资料得锻件形状复杂在0.16〜0.32之间,形状复杂程度为较复杂,级别为川级S3。
确定分模位置根据连杆形状,采用上下对称的直线分模。
确定公差和加工余量由有文献【1】查的;高度公差为长度尺寸为=.3mm;宽度尺寸为:鸚.零件需磨削加工,加工精度为 F ,由参考文献4查得水平方向的余量范围为2.5〜3.0mm,内径方向公差为3mm,高度水平尺寸的单位余量约为2.3〜3.0mm,取3mm。
1.3模锻斜度零件图上的技术条件已注明模锻斜度为5。
1.4圆角半径无零件圆角处取3mm,零件内圆角取R=(2〜3)r,其余圆角取3〜5mm。
1.5技术要求a图上未标注的模锻斜度为5 ;b图上未标注的圆角半径为R=3〜5mm;c允许的错移量为1.4mm;d允许的残留毛边量为1.4mm;e允许的表面缺陷深度为0.5mm;f锻件热处理:正火;g锻件表面清理:为便于检查淬火裂纹,采用喷砂或喷丸。
汽车转向节的锻造工艺付翔

20 世纪 90 年代初期,济南汽车制造总厂和北 京机电所、中国重机公司合作开发了立式锻造转向 节挤压生产工艺,使锻造转向节工艺向前迈进了一 大步。
汽车转向节的锻造工艺
付翔 (中国重汽锻造厂,山东 济南 250116)
摘要:以斯太尔转向节为例介绍了立式锻造转向节工艺;以沃尔沃转向节为例介绍了卧式锻造转向节工 艺;以某轻型汽车转向节为例介绍了锻造带转向臂转向节工艺。叙述了锻造转向节的设备、生产中出现的质 量问题及对热处理要求,最后对锻造生产转向节的经济效益进行了分析。
沃尔沃锻造厂锻造转向节使用美国克林宁公司 生产的 40000kN 热模锻压力机。加热后坯料由滑道 传到指定位置后,人工夹起坯料放到闭式预锻模中, 压力机压下完成预锻工序,然后人工翻转放入终锻 型槽,压力机最后锻造成形。终锻型槽水平分模,人 工把成形的转向节送出压力机,锻件通过输送带送 到切边工位进行切边。每分钟生产三件,生产速度 快,整个锻造生产人工操作,过程简单。
3 锻造设备 锻造转向节使用什么设备要根据生产批量而
定,目前有三类设备可以选择。一类是模锻锤,这一 类设备只适用于小批量生产,而且工艺落后,产品质 量也较低,不适于现代化的需要,但投资较少。第二 类是螺旋压力机或液压机,这一类设备也只能用于 中、小批量生产。第三类就是热模锻压力机,大批量 生产转向节使用热模锻压力机最为适宜,目前,世界 上大多数锻造厂都在使用热模锻压力机锻造转向 节。热模锻压力机可设置多个型槽,设备有下死点, 可提高模具寿命,热模锻压力机一个行程完成一个 工序,工作可靠、生产效率高、易于实现自动化生产、 受其他因素影响小、锻件质量稳定,缺点是设备投资 较大。各种车型转向节锻造使用热模锻压力机顿位 各异:依维柯面包车、全顺面包车等使用 20000kN~ 25000kN 级。中型汽车使用 40000kN 级。沃尔沃、斯 太尔载重车和北方奔驰使用 63000kN 级。
汽车转向节的锻模设计

汽车转向节的锻模设计摘要一辆汽车由多个部分组成,其中的汽车转向节是汽车上的关键零件,它既要承载车体重量,又需要承受前轮刹车的制动力矩并传递转向力矩,所以需要对其外形结构和机械性能有严格要求。
随着汽车行业的快速发展,汽车的需求量增大,对汽车转向节的需求量也同时增加。
由于其外形结构非常特殊,以传统的加工工艺方式已不能满足其强度和精度要求,因此锻造加工成为了制造汽车转向节的最优加工方式。
关键词:转向节预锻终锻1绪论1.1目的及意义汽车转向节是汽车转向控制系统的重要零部件,它承担着传递转向力矩的重要作用,作为汽车的主要安保部件之一,它既承担着车辆的制动力矩,同时还支撑着汽车的总体重量。
在汽车正常行驶途中,汽车转向节时常承担着重复的冲击载荷,所以它必须在满足高强度的机械性能和高标准的配置要求的同时,还要求有强大的抗疲劳能力[1]。
作为车辆的主要驱动元件,汽车转向节能保证车辆在复杂多变的情况下能够保持行驶稳定性,但由于其造型复杂,在生产过程中不易成型,而且对零部件的品质要求也相当高,因此过去的传统生产方式和制造方法已不能满足如今汽车现代化和大批量生产的要求。
不同的汽车型号它们的转向节也会稍有差异,因此现今市场上的转向节型号繁多,实现汽车转向节生产方式的优化是解决汽车批量生产的重要课题[2]。
以锻造加工为主的汽车转向节生产方式,满足了优化转向节锻造技术、降低材料的损耗率、节约工时以及减少成本的要求,同时对汽车转向节的合理锻造方法进行探索研究以及对锻造新工艺的开发具有重要意义,因此对锻模进行高端的技术设计和研究是非常关键的。
现今机器工业中生产毛坯的主要途径之一便是锻造,其优势就是它可以改变各种金属材质原有的组合,使其力学性能与物理性能获得了较大的改善,同时锻造还可以增加各种金属资源使用率以节省各种金属资源,并且锻造还可以直接获得金属零部件的外形,对于部分零部件来说锻造完成后甚至能进行使用。
锻造工艺能挤压锻件中的气孔并其疏松组织,粉碎粗大的颗粒使之变成细小颗粒,并形成沿着零件轮廓合理分布的纤维组织。
解析差压铸造铝合金转向节的热处理工艺

2019年第48卷第4期Vol.48No .42019INDUSTRIAL HEATINGDOI:10.3969/j.issn.1002-1639.2019.04.006解析差压铸造铝合金转向节的热处理工艺李莎(陕西工业职业技术学院材料工程学院热处理教研室,陕西咸阳712000)摘要:在汽车零部件中,转向节占有着相当重要的地位,因为它性能的安全与否直接关系到整个汽车能否安全行驶。
鉴于此以某种铝合金为研究对象(型号A356),探讨了在这种铝合金转向节的差压铸造过程中的生产工艺,特别是对热处理工艺的技术要点做了分析,并结合台架疲劳试验对其性能进行了验证,旨在通过研究为相关领域的探索提供一些可具参考的资料。
关键词:铝合金;差压铸造;热处理工艺中图分类号:TG1361文献标志码:A文章编号:1002⁃1639(2019)04⁃0021⁃03Analysis of the Heat Treatment Process of Differential Pressure Casting Aluminum Alloy Knuckle LI Sha(Heat Treatment Department ,School of Material Engineering ,Shanxi Polytechnic Institute ,Xianyang 712000,China )Abstract:The steering knuckle plays an important role in automobile parts.Because the safety of its performance is directly related to the safety of the car.This paper takes in some aluminum alloy as the research object ,(its model is A356),discussed in this kind of differential pressure casting process of aluminum alloy steering knuckle of the production process ,especially made a analysis of the main technical points of the heat treatment process ,and connecting with the bench fatigue test of its performance is verified ,and related areas for the purpose of through re⁃search of this paper research will provide some reference data.Key words:aluminum alloy ;differential pressure casting ;heat treatment process————————————————————————————————————————收稿日期:2019⁃01⁃07作者简介:李莎(1986—),女,硕士,讲师,研究方向为材料改性.在汽车的转向系统中,转向节是不可忽视的构成部分,既可以与汽车悬架、前车轴相连,又是转向系统的制动器相连。
差压铸造铝合金转向节缺陷的分析与工艺改进
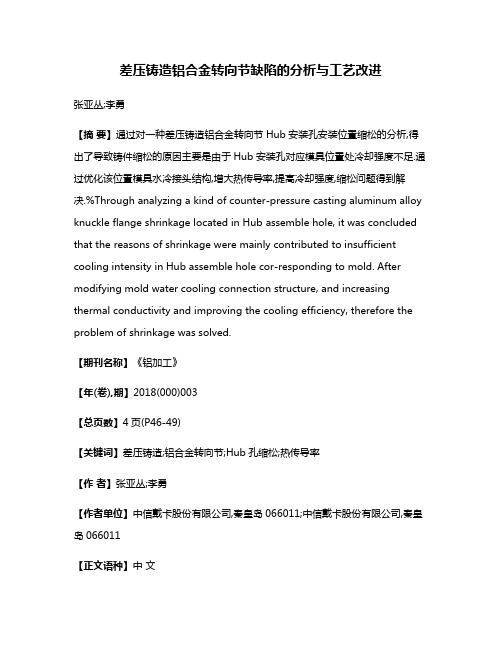
差压铸造铝合金转向节缺陷的分析与工艺改进张亚丛;李勇【摘要】通过对一种差压铸造铝合金转向节Hub安装孔安装位置缩松的分析,得出了导致铸件缩松的原因主要是由于Hub安装孔对应模具位置处冷却强度不足.通过优化该位置模具水冷接头结构,增大热传导率,提高冷却强度,缩松问题得到解决.%Through analyzing a kind of counter-pressure casting aluminum alloy knuckle flange shrinkage located in Hub assemble hole, it was concluded that the reasons of shrinkage were mainly contributed to insufficient cooling intensity in Hub assemble hole cor-responding to mold. After modifying mold water cooling connection structure, and increasing thermal conductivity and improving the cooling efficiency, therefore the problem of shrinkage was solved.【期刊名称】《铝加工》【年(卷),期】2018(000)003【总页数】4页(P46-49)【关键词】差压铸造;铝合金转向节;Hub孔缩松;热传导率【作者】张亚丛;李勇【作者单位】中信戴卡股份有限公司,秦皇岛066011;中信戴卡股份有限公司,秦皇岛066011【正文语种】中文【中图分类】TG2920 前言转向节,是汽车转向桥中的重要零件之一,能够使汽车稳定行驶并灵敏传递行驶方向。
转向节的功能是传递并承受汽车前部载荷,支承并带动前轮绕主销轴线转动而使汽车转向。
汽车转向节锻造方式对加工工艺的影响

汽车转向节锻造方式对加工工艺的影响转向节是汽车转向桥上的主要零件之一,能够使汽车稳定行驶并灵敏传递行驶方向。
一个作用是将方向盘转动的角度值有效地传递到汽车前轮上,适时控制汽车行进中的路线,从而保证汽车安全;另一个作用是承受汽车前部载荷,支承并带动前轮绕主销转动,在汽车行驶状态下,承受着多变的冲击载荷。
因此转向节不仅要求有可靠的强度,而且必须保证其较高的加工精度。
它的几何形状比较复杂,需要加工的几何形体比较多,各几何面之间位置精度要求较高,其加工精度的高低会影响到汽车运行中的转向精度。
本文通过对两种不同锻造工艺生产的锻件的分析,探讨转向节锻件的分模形式、余量分配以及锻造错差等对其加工工艺性的影响,并对在加工过程中夹具设计和定位面的选择等方面提出借鉴。
转向节结构特点转向节形状比较复杂,集中了轴、孔、盘环、叉架等四类零件的结构特点,主要由支承轴、法兰盘、叉架三大部分组成。
支承轴的结构形状为阶梯轴,其结构特点是由同轴的外圆柱面、圆锥面、螺纹面,以及与轴心线垂直的轴肩、过渡圆角和端面组成的回转体;法兰盘部分包括法兰面、联接螺栓通孔和转向限位的螺纹孔;叉架是由转向节的上、下耳和法兰面构成叉架形结构。
从锻造工艺的角度来看,转向节锻件的特点是:支承轴细长,法兰盘较大且有时为异形面,叉架与支撑轴中心线偏转一个角度α且形状复杂,按照《GB12362-2003钢质模锻件公差及机械加工余量》,锻件为典型的复杂叉形件。
转向节加工工艺流程转向节的加工主要工艺流程为:铣轴颈端面,钻两端中心孔→粗车法兰盘端面和支撑轴轴颈→半精车、精车支撑轴颈、圆角,精车法兰,车尾端螺纹→钻、攻法兰面螺纹→粗、精铣上、下耳环内、外端面→粗钻、精镗主销孔→表面淬火(根据需要)→精磨大、小轴承颈及圆角→打刻标识→检验、入库。
锻造方式对加工工艺的影响1.锻造方式转向节锻件的生产有两种锻造成形工艺:水平分模(平面分模)和垂直分模(立式分模)。
水平分模是以锻件中心平面为分模面的锻造方式,因支撑轴部分与法兰和叉架部分的截面相差较大,锻造过程中为合理分配坯料致使制坯非常复杂。
转向节铸件外观检验标准
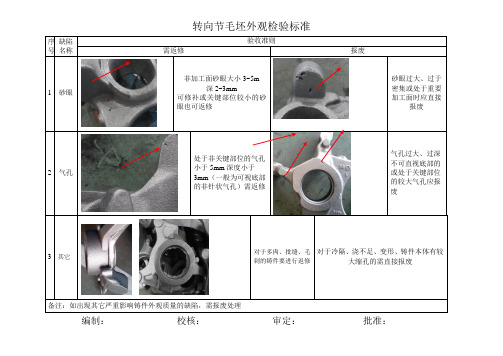
转向节毛坯外观检验标准
序号缺陷
名称
验收准则
需返修报废
1 砂眼
非加工面砂眼大小3~5m
深2~3mm
可修补或关键部位较小的砂
眼也可返修
砂眼过大、过于
密集或处于重要
加工面时应直接
报废
2 气孔处于非关键部位的气孔
小于5mm深度小于
3mm(一般为可视底部
的非针状气孔)需返修
气孔过大、过深
不可直视底部的
或处于关键部位
的较大气孔应报
废
3其它对于多肉、批缝、毛
刺的铸件要进行返修
对于冷隔、浇不足、变形、铸件本体有较
大缩孔的需直接报废
备注:如出现其它严重影响铸件外观质量的缺陷,需报废处理
编制:校核:审定:批准:。
- 1、下载文档前请自行甄别文档内容的完整性,平台不提供额外的编辑、内容补充、找答案等附加服务。
- 2、"仅部分预览"的文档,不可在线预览部分如存在完整性等问题,可反馈申请退款(可完整预览的文档不适用该条件!)。
- 3、如文档侵犯您的权益,请联系客服反馈,我们会尽快为您处理(人工客服工作时间:9:00-18:30)。
关于汽车转向节的铸造问题设计的背景:汽车转向节是连接汽车方向盘与前轮轮轴的部件,并与减震器相连。
它主要有三部分功能:1与前轮轴相连接,承担轴传来的力和力矩,2汽车转向的转动部件,3吸收汽车行进过程中的震荡。
它是汽车中应力最为集中、最为复杂的零件,直接关系到汽车的安全性能,因此它的设计标准十分严格,制造过程和产品测试都要求符合规范。
目前转向节是由球墨铸铁为主要原料铸造而成,并加入碳、硅等元素,在微观结构上在铁原子之间形成碳或硅小颗粒以加强合金钢的延展性(韧性),宏观上提高零件的抗拉强度和疲劳强度。
而且碳、硅元素的含量要求适当,过多会使合金变脆而导致强度下降。
确定待设计系统的主要功能: 2001年大众汽车(墨西哥)公司引进一套转向节铸造生产线,主要步骤是在感应电炉中在1400℃高温下熔化铸铁,以镁作催化剂混合适量沙粒(硅)产生反应形成熔液浇注入砂型中,冷却后打破砂型对铸件进行检测,进一步机械加工最终成品。
生产线将型砂经传送带回收处理循环利用,熔渣与不合格铸件同样用升降机回收作为原料再次放入电炉。
生产初期,应用此生产线使生产效率得以大幅提高,但同时也产生了铸件废品率(主要为缩型)也大幅提高的问题,经研究发现是由于熔液中沙粒含量超标(使熔液流动性差)造成的。
导致生产成本升高以及效率下降。
有何经济效益和社会效益:应用TRIZ理论对问题进行分析和创新后,在对生产线稍加改造后,问题得以有效解决,产品不合格率由大于10%降到低于3%,同时不增加任何额外投入,在生产成本不变的情况下,简化了生产线,缩短了生产周期。
第一步:设计的最终目的:汽车转向节是连接汽车方向盘与前轮轮轴的部件,并与减震器相连。
它主要有三部分功能:1与前轮轴相连接,承担轴传来的力和力矩,2汽车转向的转动部件,3吸收汽车行进过程中的震荡。
能够更好的对汽车进行减震,转向节处的铸造运用更好的材料加强其转向节的强度。
第二步:理想解是什么:转向节是汽车转向桥上的主要零件之一,能够使汽车稳定行驶并灵敏传递行驶方向,转向节的功用是承受汽车前部载荷,支承并带动前轮绕主销转动而使汽车转向。
在汽车行驶状态下,它承受着多变的冲击载荷,因此,要求其具有很高的强度。
能够减少生产浪费,提高生产效率,从转向节的改变从而提高汽车的整体质量,提高汽车承受多变冲击载荷的能力。
第三步:达到理想解得障碍是什么:转向节通过三个衬套和两个螺栓与车身相连,并通过法兰盘的制动器安装孔与制动系统相连。
在车辆高速行驶时,路面通过轮胎传递到转向节上的振动,是我们分析时考虑的主要因素。
计算时利用已有的整车模型,对整车施加4G的重力加速度,算出转向节三个衬套中心点和两个螺栓安装孔中心点的支反力作为施加载荷,并约束法兰盘连接制动系统端面上所有结点的123456自由度。
要限制好自由度以及螺栓与车身相连的契合度,这些都需要慢慢平衡。
第四步:它为什么成为障碍:从机加工艺来讲,转向节分为杆部、法兰盘和叉部等3个部分加工。
(1)杆部加工以中心孔定位,车和磨为主,加工关键是磨削。
(2)法兰盘加工主要是制动器安装孔的加工,要保证其位置度,同时要兼顾加工效率。
并且,利用其中1孔作为加工叉部定位用。
(3)叉部加工是转向节加工的难点,采用两销一面定位,其加工主要是保证主销孔的同轴度,以及主销孔与内端面的垂直度,是整个加工工艺的投资重点和设备选型的关键。
大部分转向节在此部位还有横拉杆装配用的锥孔,这更增加了叉部加工难度,锥孔加工是许多厂家难以100%合格的项目,应予重视,否则,转向节的早期失效就从这里开始。
第五步:如何使障碍消失:杆部的强化处理以提高转向节的疲劳寿命,对大多数类型的转向节都有这方面的技术要求,一般为滚压和中频淬火,以在表面形成残余压应力,提高产品疲劳强度。
国内加工对滚压要求不高,难点在中频淬火,主要是感应器的设计和制造,不过,在这方面国内有专业厂家给与解决。
主销孔压装衬套后的加工,有的压装后不要求加工,有的压装后要求加工。
从装配角度讲,压装后加工更有利于装配,否则影响转向的灵活性。
第六步:什么资源可以帮助你:研究发现,过量沙粒是由于回收熔渣和废件过程中,混入了大量的沙粒(来自打破的砂型),再利用时,这些附着在表面的沙粒溶入了铸液中。
如果在熔渣、不合格铸件的回收过程中去除沙粒,不使其进入再次生产,就可以避开熔液的升高温度问题。
第七步:在其他领域或其他工具可以解决这个问题么:铸铁件经常会发生各种不同的铸造缺陷,如何防止这些缺陷发生,一直是铸件生产厂关注的问题。
砂眼、渣孔特征:缺陷处内部或表面充塞着型(芯)砂的小孔,称为砂眼。
若缺陷形状呈不规则,内部是渣或夹杂物,则称为渣孔。
1.砂眼防止措施:(1)提高型(芯)砂的强度及砂型紧实度,减少砂芯的毛刺和砂型的锐角,防止冲砂。
(2)合型前要吹干净型腔和砂芯表面的浮砂,合型后要尽快浇注。
使用冷芯砂时,尽可能分散进铁液,避免冲刷造成砂眼。
(3)防止砂芯烘枯及存放时间过长。
(4)合理设计浇注系统,避免铁液对型壁冲刷力太大;浇口杯表面要光滑,不能有浮砂。
2.渣孔防止措施:(1)提高铁液过热温度,球铁、蠕铁、合金铸铁应该增加扒渣次数,温度允许的情况下,浇注前静止一段时间,以利于熔渣上浮。
(2)防止铁液氧化,严格控制球化剂,孕育剂的加入量(特别是随流孕育的量),球铁采用随流孕育一定要慎重。
(3)合理设计浇注系统,放置滤网片提高档渣能力,浇注包上最好安置挡渣系统,浇注时保持不断流。
(4)球铁铸件在浇注以及铁液在型腔内流动过程中,由于铁液氧化,或者铁液所含各种元素与铸型、砂芯材料反应产生的渣,通常称之为“二次渣”(以区别于浇注前已存在的“一次渣”),这种渣形成的夹渣缺陷往往只能在断口上发现,成品铸件加工面上往往要经磁粉探伤才能发现。
这种夹杂物主要是由氧化物(MgO、SiO2、Feo…)和硫化物(MgS、FeS、MnS…)及其它的夹杂物组成的。
3.“二次渣”的防止措施:①严格控制铁液的残余镁量(一般质量分数控制在0.035%~0.055%,壁薄宜控制在下限,壁厚可控制在上限)。
②降低原铁液含硫量,有条件的要采取脱硫处理,并提高处理温度与浇注温度。
脱硫处理可以大幅度降低原铁液含硫量,能有效地减少“二次渣”。
③适当提高球化剂的稀土含量,降低镁含量,有利于降低铁液结皮温度,减少“二次渣”。
四:矛盾定义及确定创新原理1,对技术系统中的问题进行描述:使用生产线后,整个铸造过程的操作性提高了,但相应的也产生了铸件废品率增加了。
研究发现,问题的产生是由于感应电炉中的熔液的沙粒含量超标,导致熔液流动性差造成的。
若提高熔液温度,可以是问题好转,但会给设备和人员带来危害。
由此产生的技术矛盾为:为提高熔液的适应性和由此带来的温度提高之间的矛盾。
2,分析此问题是技术矛盾还是物理矛盾:一、提取技术矛盾:想要提高的技术特性是铸造的操作性,而随之带来的问题是回收物的量增大了。
二、技术矛盾的两方面抽象为软件分析需要的技术特性有利特性: 33 Ease of operation 操作性不利特性: 1 Weight of moving object 运动物体质量三、技术矛盾矩阵中得到相应的创新原理由第33行第1列得到创新原理25、2、13、15。
四、分析得到的创新原理,找到适用于本问题的解决方案,在解决本问题过程中,应用原理25 13 15五:根据创新原理给出可能的几种解决方案:1 分析沙质含量超标问题一、将具体生产中待解决问题的技术矛盾提取出来由于问题的关键是熔液中沙质含量过高,使熔液的流动性变差,浇铸时容易产生缩型,废件率升高。
在这种情况下,若要使熔液的流动性合乎标准,就要再升高熔液的温度,但是,升高温度对设备和人员都会造成损伤,显然这对于生产是很不利的。
因此,想要提高的技术特性是熔液的适应性,而由此带来的问题是温度会升高。
二、将技术矛盾的两方面抽象为软件分析需要的技术特性有利特性:35 Adaptability适应性不利特性:17 Temperature温度三、技术矛盾矩阵中得到相应的创新原理对应第35行第17列得到四个创新原理:2、27、3、35。
四、据提供的创新原理分析问题,找到解决方案,在解决本问题过程中,应用原理3。
原理3 Local quality 部分改变A 将物体的均一构成或外部环境及作用改为不均一;B 让物体的不同部分各具不同功能;C 让物体的各部分处于各自动作的最佳状态。
分析:根据这个原理想到:如果能改变有害物(沙粒)的位置,不让过量的沙粒进入熔炉应该是最好的解决办法。
研究发现,过量沙粒是由于回收熔渣和废件过程中,混入了大量的沙粒(来自打破的砂型),再利用时,这些附着在表面的沙粒溶入了铸液中。
如果在熔渣、不合格铸件的回收过程中去除沙粒,不使其进入再次生产,就可以避开熔液的升高温度问题。
实际该公司也是基于此方法解决问题的。
而由此又引出另外的新问题:由于回收物夹带的沙粒分两类,粘附性和非粘附性,应分别考虑予以解决。
2、分析非粘附性沙粒消除问题分析生产线产生的问题可以发现,未使用此生产线时,对于废件不直接回收放入电炉,没有沙粒含量超标的问题;使用生产线之后,废件随传送带回收不经处理直接再利用,就出现了这样的问题。
生产线的使用使生产过程的操作性提高了,但带来的问题是铸件不合格率提高了。
(回收物的数量增加了。
)一、提取技术矛盾:想要提高的技术特性是铸造的操作性,而随之带来的问题是回收物的量增大了。
二、技术矛盾的两方面抽象为软件分析需要的技术特性有利特性: 33 Ease of operation 操作性不利特性: 1 Weight of moving object 运动物体质量三、技术矛盾矩阵中得到相应的创新原理由第33行第1列得到创新原理25、2、13、15。
六:确定最理想的解决方案分析得到的创新原理,找到适用于本问题的解决方案, 在解决本问题过程中,应用原理25 13 15 原理25 自助机能A 让物体具有自补充、自恢复功能B 灵活运用剩余的材料及能量分析:本原理启发使用生产线本身产生的能量作为除沙装置的动力来源。
在升降机上增加吸尘装置,使升降机具备除砂功能,同时将熔液散发的热能转化为电能,为升降机和洗尘装置提供能源。
原理13 “The other way round” 逆问题A 用相反的动作代替要求指定的动作B 让物体可动部分不动,不动部分可动分析:根据原理提示,可以将“把沙粒从原料中去除”的思路改为“把原料从沙粒中去除”,将回收过程改为:升降机卸载时先将沙粒与回收物分离,再将已去除沙粒的原料卸下,而沙粒被留在升降机里继续传送。
可以通过在回收物上先盖一个带有大量小孔的筛形盖子,筛掉沙粒后,小孔可以自动封闭,翻转回收装置,回收物落下而沙粒被保留在筛子中间。