最新丁二烯装置历年事故汇编
丁二烯装置危害因素分析及安全控制措施王岩
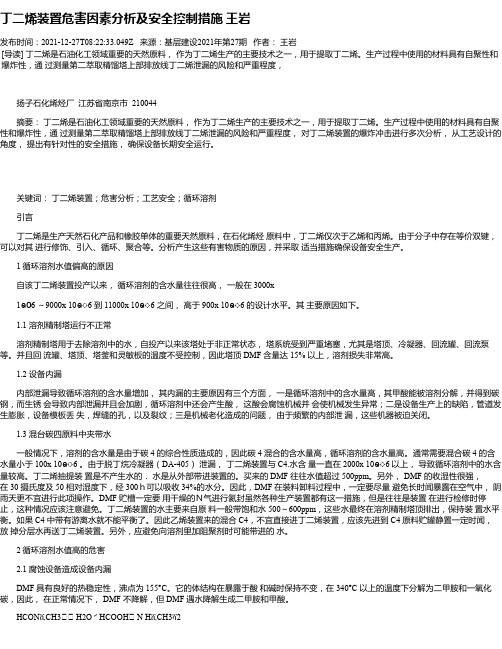
丁二烯装置危害因素分析及安全控制措施王岩发布时间:2021-12-27T08:22:33.049Z 来源:基层建设2021年第27期作者:王岩[导读] 丁二烯是石油化工领域重要的天然原料,作为丁二烯生产的主要技术之一,用于提取丁二烯。
生产过程中使用的材料具有自聚性和爆炸性,通过测量第二萃取精馏塔上部排放线丁二烯泄漏的风险和严重程度,扬子石化烯烃厂江苏省南京市 210044摘要:丁二烯是石油化工领域重要的天然原料,作为丁二烯生产的主要技术之一,用于提取丁二烯。
生产过程中使用的材料具有自聚性和爆炸性,通过测量第二萃取精馏塔上部排放线丁二烯泄漏的风险和严重程度,对丁二烯装置的爆炸冲击进行多次分析,从工艺设计的角度,提出有针对性的安全措施,确保设备长期安全运行。
关键词:丁二烯装置;危害分析;工艺安全;循环溶剂引言丁二烯是生产天然石化产品和橡胶单体的重要天然原料,在石化烯烃原料中,丁二烯仅次于乙烯和丙烯。
由于分子中存在等价双键,可以对其进行修饰、引入、循环、聚合等。
分析产生这些有害物质的原因,并采取适当措施确保设备安全生产。
1 循环溶剂水值偏高的原因自该丁二烯装置投产以来,循环溶剂的含水量往往很高,一般在 3000x 1െ06 ~9000x 10െ◌6 到 11000x 10െ◌6 之间,高于 900x 10െ◌6 的设计水平。
其主要原因如下。
1.1 溶剂精制塔运行不正常溶剂精制塔用于去除溶剂中的水,自投产以来该塔处于非正常状态,塔系统受到严重堵塞,尤其是塔顶、冷凝器、回流罐、回流泵等。
并且回流罐、塔顶、塔釜和灵敏板的温度不受控制,因此塔顶 DMF 含量达 15% 以上,溶剂损失非常高。
1.2 设备内漏内部泄漏导致循环溶剂的含水量增加,其内漏的主要原因有三个方面,一是循环溶剂中的含水量高,其甲酸能被溶剂分解,并得到碳钢,而生锈会导致内部泄漏并且会加剧,循环溶剂中还会产生酸,这酸会腐蚀机械并会使机械发生异常;二是设备生产上的缺陷,管道发生膨胀,设备模板丢失,焊缝的孔,以及裂纹;三是机械老化造成的问题,由于频繁的内部泄漏,这些机器被迫关闭。
丁二烯残液装车管线燃爆事故分析

【 关 键 词 】丁 二 烯 残 液 ; 管线 ; 燃爆; 聚合 ; 乙烯 基 乙炔
2 01 3 年1 2 月1 5日5 时5 0 分许 , 储 运 车 间北 烯 残 液持 续 受热 , 在 泄压 回流 管 阻塞 的情 况 下 , 罐 区传来 爆 炸声 , 当班班 长 立 即到 室外 查 看 , 发 管线 内乙烯基 乙炔 发生爆 炸 , 物料 外泄 引发 二次
P 一 0 8 0 3 A/ B出 口回 流 阀 ( 4 #) , 同时 关 闭 装 车 管 线 向 阀处 有 9 5 %聚 合 物 和 5 %的 冰 , 导致 回流管线堵
伴 热 线 总 阀 并 拨 打 火 警 电话 。 5 时5 5 分, 分 公 司 调 塞 , 出 入 口关 闭 的 情 况 下 , 因伴热 温度过 高 , 造 成 度 室 当 班 调 度 员接 到 报 告 后 , 迅 速 按 照 公 司 事 故 管 线 中 物 料 温 度 持 续 升 高 , 压 力上 升 , 乙 烯 基 乙
状 态进行检查 。 ( 2) 操作 规程 存 在错 误 。 在 公 司 储 运 车 间 的 残 液装车 步骤 中 , 其 中 有 两 条 都 要 求 打 开 回流 阀
的 发生 , 应 负 次 要责 任 。
3 结 论 与建 议
通过 以上分析 , 发 现 管 线 伴 热 的 工 艺 存 在 较
这 样温 度 为2 6 5 ℃的 中压 蒸汽 伴 热使 管 线 能温 升 有可 能达 到 起爆 温 近 只有 中压 蒸汽 可 以采 用 ,
度 从 而 引起 爆 炸 。 中压蒸 汽 被错 误 用于伴 热 。 车 间应 负主 要 责任 , 设计 院应负次要责任 。 操作规 程存 在的错 误 , 导 致 操 作 人 员使 回 流
丁二烯管线设备爆裂致灾危害

请注意丁二烯管线、设备爆裂致灾危害一、前言101年4月6日凌晨03:30分,XX某石化厂之丁二烯工场管线爆破,引发火灾(如图1),在附近居民强烈反应及新闻媒体持续追踪报导下,引发民众再度对工安问题的疑虑与关注,特别是石化制程,由于其流体多具有可燃、爆炸或毒性特质,稍一不慎,制程发生工安意外,不但设备毁坏,生产停止,甚至引起附近居民抗议,企业形象受损,如造成员工生命损伤,更是一个家庭永远的痛,工安问题一定要审慎面对防护!二、事故经过本工安事故发生于XX某石化厂之丁二烯工场,其连接再沸器与安全阀之10吋管线,平常处于滞留状态,因管内丁二烯与氧发生反应,产生丁二烯过氧化物,该丁二烯过氧化物再与丁二烯单体聚合,生成爆米花状(popcorn)丁二烯聚合物(如图2),该爆米花状丁二烯聚合物又快速聚合反应,体积迅速膨胀,致管线充压而撑破,导致管内丁二烯聚合物、丁二烯暴露于空气中,产生过氧化物,进而与大气中氧急速反应,导致管线爆裂(如*图3),引发大火。
图2 丁二烯聚合生成爆米花状、海绵状聚合物图3 丁二烯管线爆裂三、丁二烯相关事故丁二烯制程设备、管路发生爆炸、火灾事故时有所闻(如表1)。
丁二烯火灾、爆炸工安事故大致可分两大类型:一类是物理性因素所造成,主因是丁二烯端聚物的生成和迅速增大,胀破设备、管道,导致爆炸、火灾物料大量泄漏,遇火源即发生火灾爆炸;另一类是化学因素所造成,主因是丁二烯过氧化物在一定的条件下爆炸分解,其爆炸威力强大,如果可燃物量多,则可能发生二次爆炸、着火,其危害更大。
表1 丁二烯设备、管路工安事故案例2012丁二烯工场制程,因连接再沸器与安全阀之管线爆破造成丁二烯与空气接触,引发火灾。
2000 法国丁二烯工场制程,因连接再沸器与安全阀之管线爆破,造成7吨丁二烯外泄,被气体侦测器侦测到,紧急应变得宜,未酿成事故。
2000 中国40吨丁二烯球槽发生爆炸火灾。
1994 日本一500 kg 丁二烯钢瓶在使用时,因内含微量爆米花状丁二烯聚合物,且该钢瓶储放在直接日晒下,造成丁二烯聚合物迅速增长,堵住安全阀,钢瓶因过压而爆炸。
连续重整装置事故汇编
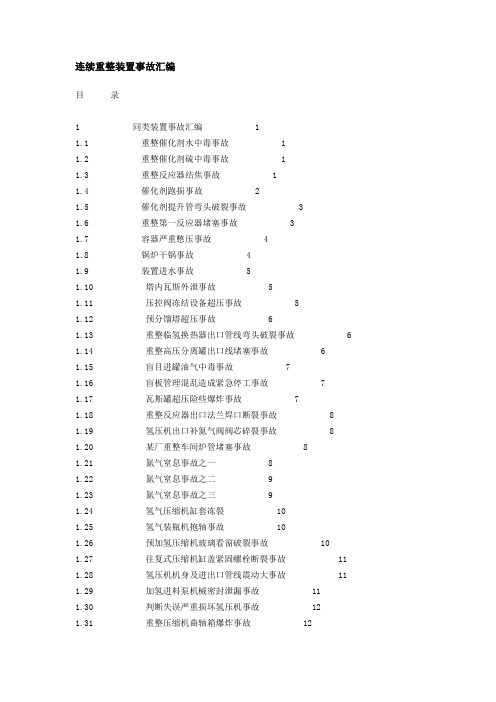
连续重整装置事故汇编目录1 同类装置事故汇编 11.1 重整催化剂水中毒事故 11.2 重整催化剂硫中毒事故 11.3 重整反应器结焦事故 11.4 催化剂跑损事故 21.5 催化剂提升管弯头破裂事故 31.6 重整第一反应器堵塞事故 31.7 容器严重憋压事故 41.8 锅炉干锅事故 41.9 装置进水事故 51.10 塔内瓦斯外泄事故 51.11 压控阀冻结设备超压事故 51.12 预分馏塔超压事故 61.13 重整临氢换热器出口管线弯头破裂事故 6 1.14 重整高压分离罐出口线堵塞事故 61.15 盲目进罐油气中毒事故 71.16 盲板管理混乱造成紧急停工事故 71.17 瓦斯罐超压险些爆炸事故 71.18 重整反应器出口法兰焊口断裂事故 81.19 氢压机出口补氮气阀阀芯碎裂事故 81.20 某厂重整车间炉管堵塞事故 81.21 氮气窒息事故之一 81.22 氮气窒息事故之二 91.23 氮气窒息事故之三 91.24 氢气压缩机缸套冻裂 101.25 氢气装瓶机抱轴事故 101.26 预加氢压缩机玻璃看窗破裂事故 101.27 往复式压缩机缸盖紧固螺栓断裂事故 11 1.28 氢压机机身及进出口管线震动大事故 11 1.29 加氢进料泵机械密封泄漏事故 111.30 判断失误严重损坏氢压机事故 121.31 重整压缩机曲轴箱爆炸事故 121.32 九江石化铂重整装置F101闪爆事故之一 131.33 九江石化铂重整装置F101闪爆事故之二 131.34 九江石化铂重整装置F101闪爆事故之三 141.35 九江石化铂重整装置F101闪爆事故之四 141.36 加热炉回火伤人事故之一 151.37 加热炉回火伤人事故之二 151.38 加热炉回火伤人事故之三 151.39 加热炉回火事故之四 161.40 加热炉回火伤人事故之五 161.41 重整炉出口法兰着火事故 161.42 处理堵塞管线引起人烧伤事故 171.43 预加氢催化剂自燃事故 171.44 炉膛气体未分析点火爆炸伤人事故 171.45 加热炉炉膛爆炸事故 171.46 扫线动火互不联系造成爆塔事故 181.47 违章操作造成氢气爆炸着火烧伤人员事故 181.48 装置吹扫中着火致使2人被烧死事故 181.49 高温汽油烫伤人事故 191.50 1993年金陵石化铂重整车间氢贮瓶爆炸事故报告 192 镇海炼化公司部分事故汇编 212.1 1980年11月6日炼油厂成品油码头冒罐跑油事故 212.2 1981年3月7日炼油厂热电站重大停电事故 212.3 1981年4月7日炼油厂热电站锅炉严重缺水造成炉管胀接口泄漏事故 212.4 1982年7月23日炼油厂油品车间油罐爆炸事故 222.5 1982年8月14日炼油厂催化车间跑润滑油事故 222.6 1983年9月17日化肥厂合成车间2#渣油贮罐冒罐事故 23 2.7 1984年6月18日炼油厂油品车间油罐抽瘪事故 232.8 1985年1月11日化肥厂火炬倾斜事故 232.9 1987年6月30日化肥厂4118-K1T烧瓦事故 242.10 1988年1月30日炼油厂油品车间碱液严重烧伤事故 24 2.11 1988年11月5日化肥厂仪表工误操作造成全厂停车事故 24 2.12 1989年9月5日炼油厂排水车间重伤事故 252.13 1990年1月5日化肥厂合成车间现场着火伤人事故 252.14 1990年5月22日炼油厂油品车间氢氟酸灼伤事故 252.15 1991年1月21日机修厂铆焊车间检修工硫化氢中毒事故 262.16 1991年4月25日化肥厂合成车间现场着火伤人事故 26 2.17 1992年10月16日化肥厂常明火炬管线水击落架事故 26 2.18 1993年 7月16日炼油厂丙烷压缩机开关带负荷合闸事故 272.19 1994年4月1日炼油厂一套常减压串跑油事故 272.20 1994年10月6日炼油厂催化车间着火烧伤检修工事故 27 2.21 1995年3月31日炼油厂Ⅰ套常减压着火事故 282.22 1995年5月28日化肥厂合成车间误操作引起停车事故 28 2.23 1995年6月22日仓储公司贮运车间串油事故 282.24 1995年9月10日化肥厂0101-V1-3渣油罐憋压损坏事故 29 2.25 1995年9月19日炼油厂焦化行车工违章作业致人重伤事故 292.26 1996年1月23日炼油厂加氢装置润滑油泵轴瓦损坏事故 30 2.27 1997年1月10日化肥厂合成车间1#气化炉闪爆伤人事故 30 2.28 1997年3月13日炼油厂聚丙烯车间三名职工违章抽烟引起闪燃事故 302.29 1997年6月22日仓储公司贮运车间跑油事故 312.30 1997年7月10日炼油厂加氢裂化F-304爆炸事故 312.31 1998年1月22日炼油厂焦化车间火灾伤人事故 312.32 1998年2月13日炼油厂一车间着火伤人事故 322.33 1999年1月29日仓储公司贮运车间串油事故 322.34 1999年3月21日炼油厂油品车间泵房火灾事故 332.35 1999年11月22日炼油厂重油催化检修现场跑油事故 33 2.36 1999年11月26日炼油厂油品车间丙烯栈台火灾事故 33 2.37 1999年12月15日炼油厂重油催化检修现场瓦斯外泄事故 332.38 2000年3月30日炼油厂一车间火灾事故 342.39 2000年4月20日炼油厂二电站CFB锅炉设备损坏的事故 35 2.40 2000年9月29日炼油厂油品车间重伤事故 352.41 2001年3月15日一车间“3.15”火灾事故 352.42 2001年3月31日重一F-501闪爆 362.43 2001年7月24日炼油厂化验职工李一平死亡事故 363 重整装置长期稳定运转中常见问题与相关事故 383.1 重整装置预处理单元腐蚀问题及相关事故 383.2 重整装置的积碳问题与相关事故 413.3 重整催化剂氮中毒问题 443.4 重整原料油的切割与保护问题 453.5 原料中硫的控制问题与催化剂硫中毒事故 463.6 重整反应系统水环境控制问题与相关事故 473.7 催化剂氯失调问题与相关事故 483.8 对突发事故的处理原则和方法 501 同类装置事故汇编1.1 重整催化剂水中毒事故1.1.1 原料带水现象91年12月14日下午,九江石化铂重整装置预分馏塔操作出现异常,塔顶回流罐液面上升,拔头油量增大,随后出现重整产氢量逐渐下降,由4500Nm3/h下降到2000Nm3/h,循环氢纯度由83%上升到96%。
同类丁二烯装置事故案例汇编

国内外同类装置事故汇编1兰州石化分公司“1•7”爆炸火灾事故1.1 事故企业概况兰州石化分公司现有总资产约340亿,员工2.74万人,下属9个生产分厂,90套炼化生产装置,原油加工能力1050万吨/年,乙烯生产能力70万吨/年。
这次事故涉及的合成橡胶厂有10套生产装置,主要包括10万吨/年和5.5万吨/年丁苯橡胶装置、5万吨/年和1.5万吨/年丁腈橡胶装置等;石油化工厂有6套生产装置,主要包括25万吨/年乙烯装置、6万吨/年线性低密度聚乙烯装置、14万吨/年高密度聚乙烯装置等。
发生事故的316号罐区始建于1969年,共有29个中间物料储罐,分属于兰州石化分公司石油化工厂和合成橡胶厂。
合成橡胶厂负责管理4个裂解碳四球罐和3个丁二烯球罐,7个球罐容积均为120M3。
石油化工厂负责管理的22个储罐中,有10个为立式储罐(属压力容器),储存拔头油、丙烯、丙烷和1-丁烯;另外12个为常压立式罐,分别储存碳九、抽余油、加氢汽油等重组分。
1.2 事故简要经过1月7日17时16分左右,合成橡胶厂316罐区操作工在巡检中发现裂解碳四球罐(R202)出口管路弯头处泄漏,立即报告当班班长。
17时18分,当班班长打电话向合成橡胶厂生产调度室报告现场发生泄漏,并要求派消防队现场监护。
17时20分,位于泄漏点北面约50米的丙烯腈装置焚烧炉操作工向石油化工厂生产调度室报告R202所在罐区产生白雾,接着又报告白雾迅速扩大。
17时21分,合成橡胶厂316罐区当班班长再次向生产调度室报告现场泄漏严重。
17时24分,现场即发生爆炸。
之后又接连发生数次爆炸,爆炸导致316号罐区四个区域引发大火。
事故发生后,企业和地方消防部门调集460余名消防官兵、86台各类消防车辆迅速赶到现场,展开扑救。
鉴于着火物料多为轻质烃类,扑救十分困难,现场抢险灭火指挥部决定,对4个着火区实行控制燃烧,同时对周边罐采取隔离冷却保护措施。
大火直到9日19时才基本扑灭。
丁二烯险兆事故报道

及时发现重大设备隐患防止事故发生化工分厂在生产过程中把安全生产放在第一位,认真进行安全检查,强化设备管理,及时发现发现重大设备隐患,避免了一起重大事故发生,为装置的安全生产提供了保证。
7月下旬,按照分公司的生产部署,化工分厂丁二烯装置进行开车准备,7月21日在对丁二烯产品冷凝器进行检查时,工段长发现冷凝器外壳有一处凸起变形,马上向分厂和有关部门报告,经过分析认定是丁二烯产生聚合物形成爆聚,对设备产生的巨大压力致使设备变形。
丁二烯聚合物,俗称“爆米花”是丁二烯生产过程中容易出现的一种异常现象。
通常是由于系统内带入残留的氧和铁锈,造成丁二烯自身聚合,轻的造成堵塞设备和管道,严重的会使设备变形和爆炸。
所以这是威胁丁二烯装置安全运行的主要隐患。
我们厂丁二烯装置开车几年来,还是第一次发生这种问题,并且是非常严重的。
万幸的是我们在装置开车前发现了事故隐患,将事故消灭在萌芽状态。
否则,一旦进料开车,聚合物继续扩大,很有可能将冷凝器爆裂,物料大量泄漏局面很难控制,后果不堪设想。
分析起来,造成我们厂丁二烯装置出现“爆米花”的主要原因,是由于丁二烯装置冷凝器频发出现泄漏,被迫停车检修不计其数。
所以造成循环水漏进物料系统,水中的氧积存在设备里导致聚合物的发生。
目前,经过有关部门鉴定该设备不能继续使用已经报废,等待更换新的设备。
之所以能够及时发现如此重大的设备隐患,就是在于杜连杰同志具有很高的安全意识、过硬的业务水平和高度的工作责任心。
应该说为我们企业的安全生产做出了贡献。
这种敬业精神值得我们每一个职工学习。
年化工事故案例文字说明
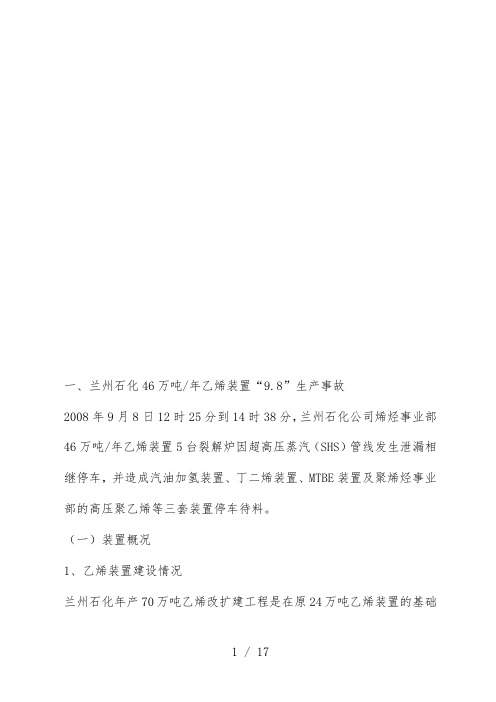
一、兰州石化46万吨/年乙烯装置“9.8”生产事故2008年9月8日12时25分到14时38分,兰州石化公司烯烃事业部46万吨/年乙烯装置5台裂解炉因超高压蒸汽(SHS)管线发生泄漏相继停车,并造成汽油加氢装置、丁二烯装置、MTBE装置及聚烯烃事业部的高压聚乙烯等三套装置停车待料。
(一)装置概况1、乙烯装置建设情况兰州石化年产70万吨乙烯改扩建工程是在原24万吨乙烯装置的基础上,新建了年产46万吨的乙烯装置。
新建的乙烯装置采纳美国KBR 公司的专利技术,北京寰球工程公司完成详细设计,上海惠生工程公司为PC承包商,中油一建、中油六建、吉林化建等负责施工建设。
2、工艺流程(1)乙烯装置要紧流程乙烯装置原料经预处理后进入裂解炉,裂解炉产生超高压蒸汽作为裂解气压缩机驱动动力。
裂解气依次进入急冷油和急冷水塔。
急冷水塔出口裂解气进入裂解气压缩机1~3段,经加压后进入碱洗塔,碱洗后的裂解气进入高低压脱丙烷塔,塔釜的废碱液进入废碱处理单元,碳四以上的重组分进入脱丁烷塔。
裂解气进入压缩机四段后,经加压进行脱砷及加氢反应器后,裂解气进入冷区分离出甲烷、乙烷、乙烯、丙烯、丙烷等组分。
具体见附件1-1:乙烯装置要紧流程简图。
(2)裂解炉脱盐水及高压蒸汽流程由总管来的锅炉给水压力为0.5~0.6 MPa,常温下经中间凝液换热器后,温度升高到70℃左右进入脱氧槽。
经低压蒸汽气提脱氧,加入中和胺和脱氧剂后,脱氧水温度达到116℃, 压力为0.1MPa,脱氧水经汽包给水泵701J加压到11.0MPa后进入锅炉给水预热盘管预热到120~140℃后,进入高压汽包。
高压汽包出来的饱和蒸汽温度为319℃进入裂解炉冷蒸汽过热盘管过热后,由蒸汽减温器注入锅炉给水,再经热蒸汽过热盘管加热到515℃后进入超高压蒸汽总管。
具体见附件1-2:裂解炉脱盐水及高压蒸汽流程示意图。
(3)碱液线流程乙烯装置碱洗塔塔釜排出含有冷凝烃类的废碱液进入废碱分离罐,脱除废碱中的烃类物质后进入废碱液储罐,然后由废碱氧化气提泵抽出,进入废碱氧化汽提塔进行氧化反应,氧化后的废碱液进入中和系统,和硫酸进行中和反应,到达要求的PH值后,污水排入化污系统。
储罐事故案例
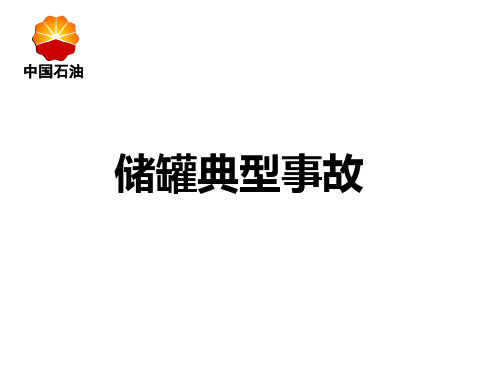
该球罐自投用后两年零两个月使用期间,球罐经 常处于较低容量,只有三次达到额定容量,第三次封装后 四天,即在18日破裂。
该球罐投用后,一直没有进行过检查,破裂前, 安全阀正常,排污阀正常关闭。球罐的主体材质为15MnVR, 内径9200毫米,壁厚25毫米,容积400立方米,用于贮存 液化石油气。
事故原因: 1.根据断口特征和断裂力学的估算,该球罐的 破裂是属于低应力的脆性断裂,主断裂源在上环焊缝的内 壁焊趾上,长约65毫米。 2.经宏观及无损检验,上、下环焊缝焊接质量很差, 焊缝表面及内部存在很多咬边、错边、裂纹、熔合不良、 夹渣及气孔等缺陷。 3.事故发生前在上下环焊缝内壁焊趾的一些部位 已存在纵向裂纹,这些裂纹与焊接缺陷(如咬边)有关。 4.球罐投入使用后,从未进行检验,制造、安装中 的先天性缺陷未及时发现和消除,使裂纹扩展、当球罐内 压力稍有波动便造成低应力脆性断裂。
间接原因之一:压力管道管理缺失,专业 管理人员工作失职。
2007年3月,橡胶厂对316#罐区R203 -R207五具储罐所属管线进行了检测,检测结果五具储罐 底部管线存在“管线弯头处壁厚不合格,且腐蚀较严重” 的现象,均判为四级,并将R201 --R204罐底部管线更换 计划列入2007年6月份的检维修计划,但是具体实施中只 对R201罐底部管线进行了更换。
改进与启示: 国家出台了《锅炉压力容器安全监察暂行条
例》 (Q:哪一年?)。
垫片老化引发的泄漏爆炸
西安市液化气罐“3.05”爆炸事故
事故经过: 1998年3月5日15:45分,西安煤气公司液化石油 气管理所的一容积为400立方、储存170吨液化气的11号球 罐根部发生泄漏。6分钟后,西安市消防队赶到现场,用 水枪驱散泄漏的液化气。由于液化气的气化温度很低,以 致喷出的消防水变成了水雾,与此同时,现场采取了切断 电源、清除一切火源、禁止在现场附近行驶车辆等措施。 在用去80条棉被对泄漏部位封堵,并对泄漏的储罐进行了 注水后,18:40,堵漏取得了明显效果。18:45,泄漏的液 化气发生了闪爆。7名消防战士和5名液化气站工作人员牺 牲,伤32人。社会影响极大。
丁二烯聚合类型及部分事故案例

在丁二烯生产装置中,丁二烯聚合物种类主要有:1.1 丁二烯二聚物丁二烯受热会发生二聚反应,生成4一乙烯基环己烯。
其反应速度取决于温度,且为放热反应。
反应方程式如下。
该化学反应在萃取精馏系统及普通精馏系统均可发生。
1.2 丁二烯热聚物1,3-丁二烯的分子具有共轭双健结构,化学性质较为活泼,然而它的分子空间结构是对称的,较难激化成活性聚合基,但在高温环境中,只要有足够热能,1,3-丁二烯的分子的双健是能够打开成为双自由基,从而引发聚合。
该化学反应主要发生在萃取精馏系统及一二汽提系统。
1.3 丁二烯端基聚合物如上所述,1,3-丁二烯的分子具有共轭双健结构,化学性质较为活泼,然而它的分子空间结构是对称的,较难激化成活性聚合基,在较低的温度和没有引发剂的作用,聚合的速度极慢,且聚合产物大多是分子量较小的丁二烯二聚物。
图2为聚合速率与温度关系图,图3为聚合速率与引发剂关系图。
在引发剂作用下,操作温度足够高,就能激活1,3-丁二烯取代基,使其按自由基聚合的方式形成端基聚合物。
聚合过程分三个步骤进行:1.3.1 丁二烯过氧化自聚物形成 1,3-丁二烯与系统中的氧作用,发生氧化反应,生成过氧化自聚物。
这种过氧化自聚物是一种淡黄色油状物质,密度大,易沉积于设备、管线死角上。
2.3.2 自由基的形成丁二烯过氧化自聚物极不稳定,在加热的情况下可断裂成活性自由基。
1.3.3丁二烯游离基链增长活性自由基与丁二烯分子作用,按线性方向形成爆米花状端基聚合物这过程为放热反应,反应速度快;自由基不断转移,使链不断增长,聚合物分子快速增大,体积急剧膨胀。
由于为放热反应,造成局部温度急剧上升,形成恶性循环,严重时产生爆炸。
端基聚合特点是反应速度快、生成物体积大,破坏力极强,是堵塞设备、造成设备损毁、酿成安全事故的重要原因,也是丁二烯聚合在丁二烯装置主要形式。
2. 影响丁二烯聚合聚的因素分析2.1 氧的影响氧是形成过氧化物的必要条件,因此,控制丁二烯气相氧含量可达到防止过氧化物产生的目的。
储罐事故案例汇编

储罐事故案例汇编质量安全环保科整理2016年6月一、突遇局部强对流天气,量油口突然冒烟(一)事故经过2010年4月19日18时37分,西北销售公司王家沟石油商业储备库计量员胡某与西部管道乌鲁木齐输油气分公司计量员代某在TG105油罐进行计量交接。
18时51分王家沟地区天气骤变,冰雹猛降。
此时,西部管道乌鲁木齐输油气分公司计量员代某继续进行计量作业,18时54分,量油口突然冒烟,作业人员胡某紧急关闭量油口,与代某在撤离过程中报警。
接警后,新疆服务中心警消队、新疆油田公司消防六大队、市消防局相继赶到现场,利用固定消防设施和移动消防车进行喷淋降温,1小时后,冒烟现象消失。
在确认隐患消除后,4月20日0时,油库恢复正常运行。
(二)事故原因作业人员在大罐上计量交接时,突遇局部强对流天气(强风伴随冰雹),瞬间在油罐顶部积聚大量的静电负荷,适逢计量交接作业,油罐量油孔敞开,大量的静电荷载量油孔内发生瞬间能量释放,引爆了浮盘上部的气体混合物,导致闪爆事故发生。
(三)事故教训及采取措施要加强罐区库区的监控、巡检工作,检查测试防静电设施的完好情况,尤其要做好物料输送装卸过程中、以及异常气候条件下作业时的防静电工作,严格执行《液体石油产品静电安全规程》(GB13348-2009)的相关规定,控制好物料的流速,杜绝因静电引发事故。
同时,风力大于5级时,操作人员不得从事相关作业;雷暴天气下操作人员不得靠近罐体作业。
二、硫化亚铁自燃,引起石脑油罐发生闪爆(一)事故经过2010年5月9日0:45分,中国石油化工股份有限公司上海高桥分公司炼油部2号联合罐区按照调度安排,1613号罐(重整原料罐,5000立方米,内浮顶罐结构,直径21米,高度16.5米,储存介质为石脑油)开始收3号蒸馏装置生产的石脑油。
10:00左右,在继续收油的同时,开始自1615号罐向1613号罐转油,此时液位为5.09米,到11:20,1613号罐(此时温度为27℃)发生闪爆,罐顶撕开,并起火燃烧。
国内外同类装置事故案例汇编
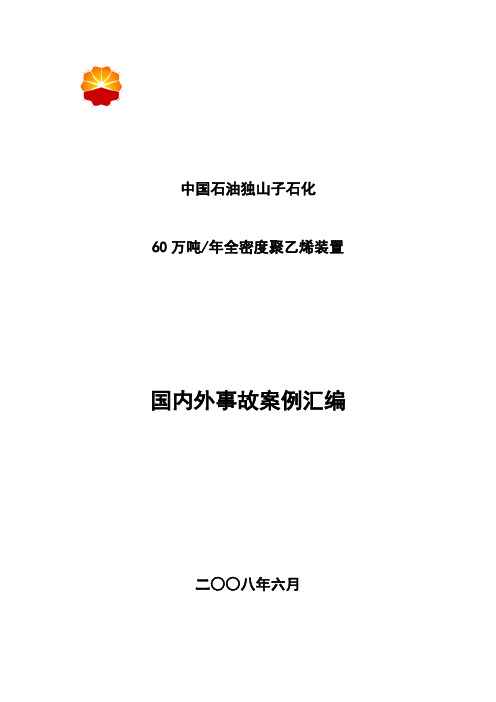
中国石油独山子石化60万吨/年全密度聚乙烯装置国内外事故案例汇编二○○八年六月前言本书汇集了一些国内外同类装置事故案例,希望通过此书,使大家能够对全密度聚乙烯装置的在生产过程中的各种风险有所认识,提高员工的风险意识,保证装置的安全生产。
在资料编写过程中,可能存在疏漏之处,在使用过程中如发现有不妥之处,敬请提出宝贵意见。
目录(一)火灾爆炸事故 (1)一、某石化塑料厂聚乙烯装置T2系统火灾事故 (1)二、XX石化塑料厂装置聚合系统聚合火灾事故 (2)三、置换方案不合理排出三乙基铝自燃着火 (3)四、TEA钢瓶更换着火事故 (4)五、作业环境存在隐患三乙基铝泄漏着火 (5)六、工具使用不当泄漏着火 (6)七、阀门内漏积聚静电引起闪爆 (6)八、无票动火割错管线泄漏着火 (7)九、措施不当静电起火 (8)十、操作不当引起着火 (8)十一、违章操作倒淋冻融泄漏静电起火 (9)十二、麻痹大意引起着火 (10)十三、经验不足冒然作业引起泄漏着火 (10)十四、橡胶塑化模头堵塞引起着火 (11)十五、罐体清洗不干净静电引发着火 (12)十六、电线短路引起闪爆着火 (12)十七、违章指挥违章操作塔体被火烧坏 (13)十八、违章作业风筒着火 (14)十九、违规设计违章操作引燃通风柜 (14)二十、低标准老毛病引燃可燃物 (15)二十一、机械故障泄漏爆燃 (16)二十二、压力表质量问题泄漏着火 (17)二十三、违章使用非防爆工具碰撞着火 (17)二十四、2000年乙烯厂着火事故 (18)二十五、密封失效泄漏着火 (19)二十六、施工留下隐患引发泄漏着火 (20)二十七、作业环境存在隐患三乙基铝泄漏着火 (21)二十八、现场疏忽检查电线腐蚀短路引起着火 (22)二十九、中心化验室“7.24”着火事故 (23)三十、2002年乙烯厂着火事故 (25)(二)人身伤害事故 (26)一、22F420D堵手孔伤人事故 (26)二、造粒F848水箱烫伤人 (27)三、消防栓水阀飞出伤人 (28)四、无证操作叉车翻造成人员受伤 (28)五、下直梯踩空坠落受伤 (28)六、硫酸喷出灼伤 (29)七、劳保穿戴不合格肩及右臂被碾伤 (29)八、缺乏经验眼被灼伤 (30)九、违章作业手指被截 (30)十、巡检跌倒,造成胸骨骨裂 (30)十一、盘车电机叶片飞出伤人 (31)十二、盲目作业手指被切断 (32)十三、未戴防护面具TBC灼伤眼睛 (32)十四、巡检不慎坠落腰、胸多处骨折 (33)十五、无证驾驶叉车保管员被撞受伤 (33)十六、违章用火闪爆作业人腿部骨折 (33)十七、麻痹大意习惯性违章手指骨折 (34)十八、巡检不慎踩空腰部受伤 (34)十九、个人防护不当带压操作受伤 (35)二十、麻痹大意高处摔下右腿骨折 (35)二十一、麻痹大意手臂骨折 (36)二十二、产品质量有问题操作人员无辜遇难 (36)二十三、为取一餐证钢板倒下砸断腿 (37)二十四、未交底检修作业人受伤 (37)二十五、活塞杆断裂碰撞曲轴箱闪爆 (38)二十六、消防演练阀体飞出打伤人 (38)二十七、台阶冰雪未清理滑跌骨折 (39)二十八、违章检修机泵眼睛被油伤 (39)二十九、现场未交底钳工人员被烫伤 (41)三十、误操作左手食指指端挤断 (42)三十一、绝缘降低母线短路灼伤作业人 (42)三十二、配合不当踝骨骨折 (43)三十三、违章操作手被挤伤 (43)三十四、电缆接头燃爆伤人 (44)三十五、工具接地电弧伤人 (45)三十六、违章作业电弧伤人 (46)三十七、未戴防护面具眼睛被氨灼伤 (47)三十八、2004年人身伤害事故 (47)三十九、乙烯6.29事故 (49)四十、2005年人身伤害事故 (49)四十一、销售车间“1.12”人身伤害事故 (51)四十二、巡检不慎滑倒尾骨骨折 (52)四十三、忽视安全麻痹大意焊工腿被挤断 (52)四十四、阀门内漏积聚静电引起闪爆 (53)四十五、作业不慎脚部骨折 (53)四十六、阀体回摆作业人站位不当手臂被挤伤 (54)四十七、作业不慎腰部受伤 (54)四十八、作业不慎,高处坠落 (55)(三)中毒窒息事故 (56)一、氮气窒息事故 (56)二、21S412窒息事故 (56)三、20F061氮气窒息事故 (57)四、2006年中毒事故 (58)(四)泄漏事故 (59)一、设备排气阀泄露烃类气体 (59)二、设备法兰大量泄露流化气 (59)三、设备法兰大量泄露流化气 (60)四、火炬燃料气管线积水 (61)五、阀门内漏积聚静电引起闪爆 (62)六、碳四泄漏事故 (63)(五)重大隐患抢险 (64)(一)火灾爆炸事故一、某石化塑料厂聚乙烯装置T2系统火灾事故1、事故经过2002年11月15日上午8:50,某石化塑料厂聚乙烯装置中控室显示T2钢瓶已经用空,于是当班操作人员通知催化剂操作员刘XX到现场进行钢瓶切换。
丁二烯生产装置爆炸事故发生的原因及防范措施

丁二烯生产装置爆炸事故发生的原因及防范措施发布时间:2021-09-13T01:10:05.057Z 来源:《基层建设》2021年第17期作者:单宝忠[导读] 摘要:随着丁二烯抽提装置规模的扩大,年产10kt以上装置不断出现,丁二烯生产装置的安全生产与长期运行已成为一个亟待解决的问题。
身份证号码:6402211989****XXXX摘要:随着丁二烯抽提装置规模的扩大,年产10kt以上装置不断出现,丁二烯生产装置的安全生产与长期运行已成为一个亟待解决的问题。
基于此,本文首先阐述了丁二烯的相关概述,并详细探讨了丁二烯生产装置爆炸事故原因及其防范措施。
关键词:丁二烯;生产装置;爆炸事故;措施近年来,我国丁二烯装置在生产、储运中发生了多起安全事故,造成人员伤亡及财产损失。
此外,下游橡胶、甲基叔丁装置等整个乙烯装置上下游生产波动,甚至导致装置非计划停产,严重影响了装置的整体经济效益。
这些事故表明,丁二烯装置尤其是乙腈法丁二烯装置的生产技术及安全管理有待进一步提高。
一、丁二烯简介丁二烯是一种有机化合物,化学式C4H6,无色气体,有轻微芳香气味。
熔点-108.9℃,沸点-4.4℃,相对密度0.6211(20/4℃);不溶于水,易溶于乙醇、甲醇、丙酮、乙醚、氯仿等性质。
它是合成橡胶、树脂、尼龙等的原料,主要工艺是丁烷和丁烯脱氢或碳四馏分分离,具有麻醉、刺激粘膜、易液化等特点,临界温度161.8,临界压力4.26MPa,与空气形成爆炸性混合物,爆炸极限为2.16~11.47%(体积)。
丁二烯是合成橡胶(丁苯橡胶、顺丁橡胶、丁腈橡胶、氯丁橡胶)的主要原料。
随着苯乙烯塑料的发展,苯乙烯与丁二烯的共聚已被用于生产多功能树脂(如ABS树脂、SBS树脂、BS树脂、MBS树脂),因此,丁二烯在树脂生产中占有重要地位。
此外,丁二烯还用于生产乙烯降冰片烯(乙丙橡胶的第三单体)、1,4-丁二醇(工程塑料)、己二腈(尼龙66单体)、环丁砜、蒽醌、四氢呋喃等,是重要的基础化工原料。
国内外芳烃事故

国内外芳烃同类装置事故汇编1、德国法兰克福格里斯海姆的赫司特公司的芳烃中间厂化学品泄漏事故概况及经过(中毒和窒息)1993年2月22日,德国法兰克福格里斯海姆的赫司特公司的芳烃中间厂,大约有十吨化学品,主要是中间体邻硝基苯甲醚因压力升高(从9巴升至16巴)从防爆安全阀中释放出来。
但赫司特公司说,没有明显的高毒性二恶类化合物存在。
粘性的不溶水的邻硝基苯甲醚,损坏了车辆、屋顶、污染了土壤和植物。
清除工作包括用一种醇水混合物分散化学品,除去污染的蔬菜,土壤和冷却残留物一并除去,清理工作将花费1000万马克。
大约有200公斤化学品渗入到莱茵河,对莱茵河实施警戒。
释放引起一系列有关硝基苯甲醚毒性的争论。
环境组织认为温度不可能生成高毒性的二恶类化合物的母体。
事故发生后工厂已关闭,至3月5日尚未清理完。
事物原因分析:人为失误。
2、洛阳石化芳烃装置吸附剂中毒事故洛阳石化总厂芳烃装置吸附分离单元采用美国UOP公司的ADS-27吸附剂,2002年6月28日,洛阳石化芳烃联合装置发生乙二醇误入装置导致吸附剂中毒事故,造成装置停车。
装置停工后,洛阳石化立即与UOP公司联系,一方面进行失活剂的评价,一方面寻求再生方法。
失活吸附剂再生工作,属世界首例,没有任何经验可以借鉴,难度大,风险大。
石化集团公司在对方认为几乎没有再生可能的情况下,经过研究,决定依靠自己的技术力量进行攻关,实现失活吸附剂的再生。
在中石化集团公司直接领导下,石科院对吸附剂中毒抢救进行了多次试验,并确定了科学、合理的抢救方案。
之后,由石科院、天津石化、扬子石化等单位专家组成的集团公司专家组和洛阳石化的技术人员,坚持“安全第一、稳步推进”的原则,依靠集体的智慧,在最短的时间内完成了再生工艺研究、再生方案编制和再生流程的改造,通过洗脱、液相干燥、气相干燥等工艺,至10月8日,仅用66天就完成了技术难度极大的吸附剂再生工作。
3、美国一节含有芳烃浓缩物在尼马吉河上的桥上脱轨事故一、事故概况及经过1992年6月30日,一列火车在液的槽车翻入河中,槽车中的26000加仑物质中大部分泄漏出来,由于蒸气包围该地区,迫使两个州数万人疏散,大约有12人因接触有毒蒸气感到头昏、头痛、灼伤眼睛、皮肤而住院。
北京化工学院丁二烯钢瓶爆炸

北京化工学院丁二烯钢瓶爆炸一、事故概况及经过1990年4月10日4时05分,北京化工学院有机实验楼南侧钢瓶房内发出嘶嘶响声,并冒出白色烟雾,紧接着变为黄色烟雾,几分钟后,丁二烯钢瓶即爆炸。
爆炸后的钢瓶沿筒体纵向裂开,裂开后扩展至底部环向焊缝熔合线处撕开,顶部封头和筒体仍连在一起,筒体裂开部分几乎展成平板。
与之一起放置的丙烯钢瓶被炸变形,但未破裂。
钢瓶房及与之毗邻的围墙部分倒塌,有机实验楼南侧窗玻璃大部分被震碎,无机试验楼北侧窗玻璃部分被震碎。
由于钢瓶房周围当时无人,因而未造成人员伤亡。
二、事故原因分析爆炸钢瓶内的丁二烯是于1989年4月27日在北京燕化公司橡胶厂研究所中试罐区灌装的,到该瓶爆炸时,瓶内丁二烯已灌装近一年时间。
瓶内残留有少量丁二烯低聚物吸收部分或微量氧,可形成过氧化物或过氧化氢。
这些低聚物的过氧化物或过氧化氢即使在常温下,由于时间过长会逐渐分解形成自由基,自由基积累到一定浓度后引起丁二烯自聚。
聚合时伴随放热(17千卡/摩尔),可使钢瓶内温度升高,温度的上升又导致聚合加速,形成恶性循环,短时间内温度可升至300~500℃。
温度升高同时还造成丁二烯大量汽化,瓶内压力可达到140~150公斤/厘米2,远远超过钢瓶设计的工作压力,造成了钢瓶爆炸。
这起事故是由于丁二烯钢瓶储存期过长,瓶内丁二烯自聚引起的爆炸。
三、事故的责任分析和对责任者的处理由于此次爆炸事故是由于丁二烯自聚所致,学校在管理和使用方面也制订了有关规定,因而此次事故不涉及个人责任。
四、防止同类事故的措施1.丁二烯钢瓶内残存的丁二烯低聚物在每次充装前必须清除干净,可用高纯氮气反复吹扫,或采取其他必要方法,以减少瓶内低聚物的残存量。
2.尽量缩短储存时间,储存期一般不应超过半年。
3.由于丁二烯是一种活性很高的聚合单体,为了减缓丁二烯的自聚,在充装丁二烯时可加入阻聚剂。
4.要做好丁二烯钢瓶的定期检验工作。
国内外化工安全事故案例汇总

国内外化工安全事故案例汇总近年来,不幸的化工安全事故在国内外频频发生,给人们的生命财产安全带来了巨大威胁。
下面将对一些近年来发生的重大化工安全事故进行汇总。
国内化工安全事故案例:1.2005年11月,江苏南京爆炸案:江苏南京江宁区化工厂发生爆炸,造成至少7人死亡,上百人受伤。
事故原因是厂内储存的危险品未按规定进行分类、分堆、储存,导致含氯碱性物质溶液发生爆炸。
2.2024年8月,新疆哈密爆炸案:新疆哈密华新化纤公司发生爆炸,2人死亡,6人受伤。
事故原因是操作人员在操作蓄电池时不慎引爆了可燃气体。
3.2024年8月,天津港爆炸事故:天津港发生集装箱化学品仓库爆炸,造成173人死亡,多人失踪,数千人受伤。
事故原因为违法储存大量危险化学品,有的化学品储存超过规定限额,导致爆炸发生。
4.2024年3月,江苏连云港爆炸事故:江苏连云港化工园区发生爆炸,造成78人死亡,94人受伤,82人失联。
事故原因是储存过量化学品的厂房未经审批,同时储存、运输等环节违反安全规定。
国外化工安全事故案例:1.1984年,印度博帕尔毒气泄露事故:印度化工厂泄露大量有毒气体,导致至少2.5万人死亡,千万人受伤。
事故原因是操作失误和设施缺陷。
2.2005年,美国得克萨斯州瑞克温爆炸事故:美国化学品厂发生爆炸,造成15人死亡,180人受伤。
事故原因是操作失误和安全管理不善。
3.2024年,日本福岛核泄漏事故:日本福岛核电站因地震和海啸导致核泄漏,造成数千人死亡,数万人被迫撤离。
事故原因是地震和海啸造成核电站设施破坏,导致核泄漏。
4.2024年,黎巴嫩贝鲁特港爆炸事故:贝鲁特港发生巨大爆炸,造成至少200人死亡,数千人受伤。
事故原因是存放在港口的火药库发生意外爆炸。
以上仅是一部分国内外化工安全事故的案例,这些事故给人们敲响了警钟,提醒我们化工企业和有关部门要高度重视化工安全,加强安全管理,合理规划生产、储存和运输环节,确保人民群众生命财产安全。
同类丁二烯装置事故案例汇编

同类丁二烯装置事故案例汇编目录1. 中国地区案例 (2)1.1 上海某化工厂丁二烯装置发生重大泄漏事故 (2)1.2 内蒙古某企业丁二烯装置爆炸事故 (3)1.3 浙江某公司丁二烯装置火灾事故 (5)2. 国外地区案例 (6)2.1 美国某地区丁二烯装置罐体破裂事故 (7)2.2 韩国某厂丁二烯装置蒸发器泄漏事故 (9)2.3 日本某公司丁二烯装置管道泄漏事故 (10)3. 典型事故成因分析 (11)3.1 操作失误 (12)3.1.1 工艺操作规程执行不到位 (14)3.1.2 操作员缺乏足够的专业知识和经验 (15)3.2 设备缺陷 (16)3.2.1 反应釜泄漏 (17)3.2.2 管道腐蚀 (19)3.2.3 阀门失效 (20)3.3 环境因素 (21)3.4 消防设施不足 (22)4. 安全控制措施 (23)4.1 工艺操作优化 (24)4.1.1 完善工艺操作规程,加强培训和考核 (26)4.1.2 引进先进的工艺控制系统 (27)4.2 设备安全提升 (28)4.2.1 定期对设备进行检测和维修 (30)4.2.2 更换易损件,并采用耐腐蚀材质 (31)4.2.3 加强设备监控,及时发现故障 (32)4.3 安全意识培训 (33)4.3.1 定期开展安全培训,提升员工安全意识 (35)4.3.2 加强宣传教育,提高公司安全管理水平 (36)5. 案例研究 (37)5.1 案例一 (39)5.2 案例二 (39)1. 中国地区案例在一个案例中,一个位于江苏省的石化工厂在操作丁二烯泵时未遵循安全操作规程,导致泵体因超负荷工作而发生故障,随后引发了火灾。
事故发生的原因被认定为泵体温度过高导致的金属疲劳,而这一现象被忽视,最终导致了丁二烯的泄露和火灾。
工厂工作人员虽然在尝试灭火时进行了积极的响应,但由于未使用适当的灭火设施,导致火灾蔓延,造成了严重的财产损失和环境污染。
在另一个案例中,位于中国西部的一家生产企业中的一个丁二烯储罐由于设计上的缺陷和缺乏定期维护,导致压力控制系统失效,引发了爆炸事故。
丁二烯聚合类型及部分事故案例
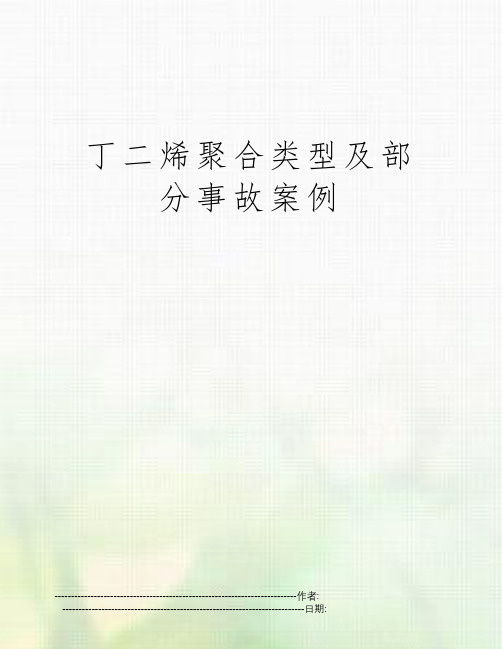
丁二烯聚合类型及部分事故案例--------------------------------------------------------------------------作者: _____________--------------------------------------------------------------------------日期: _____________在丁二烯生产装置中,丁二烯聚合物种类主要有:1.1 丁二烯二聚物丁二烯受热会发生二聚反应,生成4一乙烯基环己烯。
其反应速度取决于温度,且为放热反应。
反应方程式如下。
该化学反应在萃取精馏系统及普通精馏系统均可发生。
1.2 丁二烯热聚物 1,3-丁二烯的分子具有共轭双健结构,化学性质较为活泼,然而它的分子空间结构是对称的,较难激化成活性聚合基,但在高温环境中,只要有足够热能,1,3-丁二烯的分子的双健是能够打开成为双自由基,从而引发聚合。
该化学反应主要发生在萃取精馏系统及一二汽提系统。
1.3 丁二烯端基聚合物如上所述,1,3-丁二烯的分子具有共轭双健结构,化学性质较为活泼,然而它的分子空间结构是对称的,较难激化成活性聚合基,在较低的温度和没有引发剂的作用,聚合的速度极慢,且聚合产物大多是分子量较小的丁二烯二聚物。
图2为聚合速率与温度关系图,图3为聚合速率与引发剂关系图。
在引发剂作用下,操作温度足够高,就能激活1,3-丁二烯取代基,使其按自由基聚合的方式形成端基聚合物。
聚合过程分三个步骤进行:1.3.1 丁二烯过氧化自聚物形成 1,3-丁二烯与系统中的氧作用,发生氧化反应,生成过氧化自聚物。
这种过氧化自聚物是一种淡黄色油状物质,密度大,易沉积于设备、管线死角上。
2.3.2 自由基的形成丁二烯过氧化自聚物极不稳定,在加热的情况下可断裂成活性自由基。
1.3.3丁二烯游离基链增长活性自由基与丁二烯分子作用,按线性方向形成爆米花状端基聚合物这过程为放热反应,反应速度快;自由基不断转移,使链不断增长,聚合物分子快速增大,体积急剧膨胀。
丁二烯生产装置爆炸事故发生的原因及防范措施
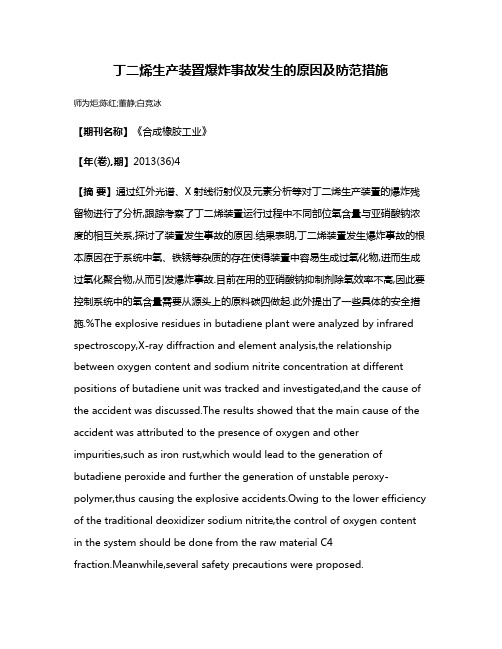
丁二烯生产装置爆炸事故发生的原因及防范措施师为炬;陈红;董静;白竞冰【期刊名称】《合成橡胶工业》【年(卷),期】2013(36)4【摘要】通过红外光谱、X射线衍射仪及元素分析等对丁二烯生产装置的爆炸残留物进行了分析,跟踪考察了丁二烯装置运行过程中不同部位氧含量与亚硝酸钠浓度的相互关系,探讨了装置发生事故的原因.结果表明,丁二烯装置发生爆炸事故的根本原因在于系统中氧、铁锈等杂质的存在使得装置中容易生成过氧化物,进而生成过氧化聚合物,从而引发爆炸事故.目前在用的亚硝酸钠抑制剂除氧效率不高,因此要控制系统中的氧含量需要从源头上的原料碳四做起.此外提出了一些具体的安全措施.%The explosive residues in butadiene plant were analyzed by infrared spectroscopy,X-ray diffraction and element analysis,the relationship between oxygen content and sodium nitrite concentration at different positions of butadiene unit was tracked and investigated,and the cause of the accident was discussed.The results showed that the main cause of the accident was attributed to the presence of oxygen and other impurities,such as iron rust,which would lead to the generation of butadiene peroxide and further the generation of unstable peroxy-polymer,thus causing the explosive accidents.Owing to the lower efficiency of the traditional deoxidizer sodium nitrite,the control of oxygen content in the system should be done from the raw material C4fraction.Meanwhile,several safety precautions were proposed.【总页数】3页(P252-254)【作者】师为炬;陈红;董静;白竞冰【作者单位】中国石油大庆化工研究中心,黑龙江大庆163000;中国石油兰州化工研究中心,兰州730060;中国石油兰州化工研究中心,兰州730060;中国石油兰州化工研究中心,兰州730060【正文语种】中文【中图分类】TQ221.22+3【相关文献】1.燃气火灾爆炸事故原因与防范措施 [J], 袁杰荣2.丁二烯缓冲罐自聚物的生成原因及防范措施 [J], 赵瑞军;代杨;谢洪涛;王娜;唐仲赟;孙宏岩3.液化气球罐爆炸事故原因分析及防范措施 [J], 朱伟4.一起乙腈生产装置熔盐系统爆炸事故直接原因技术分析 [J], 赵素娟5.一起静电除焦器爆炸事故原因分析及防范措施 [J], 刘亮因版权原因,仅展示原文概要,查看原文内容请购买。
- 1、下载文档前请自行甄别文档内容的完整性,平台不提供额外的编辑、内容补充、找答案等附加服务。
- 2、"仅部分预览"的文档,不可在线预览部分如存在完整性等问题,可反馈申请退款(可完整预览的文档不适用该条件!)。
- 3、如文档侵犯您的权益,请联系客服反馈,我们会尽快为您处理(人工客服工作时间:9:00-18:30)。
丁二烯装置历年事故汇编丁二烯装置历年事故汇编(草案)案例1时间:1999年6月22日一、事故经过:6月22日上午8:50,室内PICA-109、FRCA-118调节阀首先动作,然后所有处于自动状态的调节阀相继动作,控制室仪表盘报警声响,报警灯亮,室内按紧急停车按钮PB-1、PB-2、PB-3作紧急停车处理。
二、原因分析:由于仪表风突然中断,造成处于自动状态的调节阀相继动作:气开调节阀阀位全关,气开调节阀则阀位全开。
装置操作系统处于失控状态,无法正常调节控制,被迫进行紧急停车。
三、应急措施:1、按紧急停车按钮PB-1、PB-2、PB-3。
2、开B-GB101压缩机四只小油槽液面控制阀旁路。
3、按紧急停车步骤做好后处理工作。
四、经验及整改措施:1、外管网在切换仪表风管线时没有通知车间,并且在切换过程中程序出错。
2、仪表风管线整改:仪表风总线与N2总管加一3/4″管线,当仪表风中断或压力不足需要提高压力时,由N2替代或补充。
案例2时间:1999年12月8日一、事故经过:12月8日下午12:30,第二萃取精馏塔系统停车,CM出口接临时管线到B-DA106进料,B-DA107塔丁二烯自身循环,B-DA106物料通过不合格管线返回FB-1314,9日二萃部分开始检修,10日下午,二萃部分开车,11日凌晨5:00产品合格。
二、原因分析:1、丁二烯的性质丁二烯-1.3因双键存在,化学性质较为活泼,在第二萃取系统会有高分子的胶状直链聚合物生成。
2、运转周期长负荷高:丁二烯装置由于连续高负荷运转,运行连续时间已达10个多月,系统结焦(胶)情况较严重,尤以B-DA103、104、105二萃系统最为严重,从操作波动情况来看,已严重影响正常生产,威胁到丁二烯产品质量及生产负荷的提高。
3、阻聚剂:萃取系统阻隔聚剂糠醛(化A)在循环溶剂中的含量偏低。
4、系统氧含量的控制:丁二烯热聚物三要素:一定的丁二烯-1.3浓度+湿度+氧气,在过滤器切换过程中因没有进行N2置换,氧气通过过滤器切换过程带入系统,是正常生产过程中氧气带入系统的主要途径之一。
三、应急措施:1、CM出口接临时管线至B-DA106塔,回收粗丁二烯(避免放至火炬),减少丁二烯损失。
2、B-DA107塔自身循环,节约和缩短开车时间。
3、二萃系统检修清洗(包括塔内件系统、再沸器等)。
四、经验及整改措施:1、调整阻聚剂糠醛(化A)添加量,确保在循环溶剂中含量0.7~1.0%(m/m)。
2、过滤器切换过程中进行N2置换,避免因过滤器的切换氧气带入系统。
3、适当调整操作参数:在正常生产过程中适当降低塔压和塔釜温度,严禁釜温大幅波动或飞温。
4、认真总结高负荷长周期运行对装置的影响程度,确认最佳的运行周期和操作负荷。
案例3时间:2000年6月9日一、事故经过6月9日15:00,丁二烯装置B-DA101B塔塔釜压力逐渐上升,引起压缩机二段出口压力上升,15:30打开HC-101,16:20发现FB-101溶剂贮罐室内显示液面计失真(现场玻璃板液面显示6%左右),降负荷至10.0t/h,17:00丁二烯产品切不合格,后经过数次提负荷,均不能维持正常操作,负荷维持在10.0t/h,10日10:00产品合格进球罐。
二、原因分析:B-DA101B塔系统由于较多氧气的富集,在较短时间内生成的较多的丁二烯热聚物吸附在塔上和降液管内,造成浮阀不能正常开启和因降液管出口堰堵塞造成液流的不平衡,(特别是B-DA101塔釜113、114、115塔塔板),又因B-FB101溶剂罐室内显示失准,造成大量溶剂富积于B-DA101B塔内,造成塔内局部变相液泛,萃取效果严重下降,导致产品不合格。
三、应急措施:1、负荷降至适当量。
2、增加除氧剂(NaNO2)和阻聚剂(糠醛)添加量。
3、适当降低PICA-105塔压和塔釜TICA-103温度。
四、经验及整改措施:1、检修质量差:塔板清洗不到位,特别是DA-101B、113、114、115塔塔板。
2、系统氧含量过高:a、开车前期N2置换不彻底,尚有死角等。
b、冷运、热运及开车过程中过滤器切换、泵切换时氧气带入系统。
3、开车准备中NaNO2加入量太少,系统中大量氧气没有清除。
4、阻聚剂糠醛(化A)含量过低只有0.2%(m/m)。
案例4时间:2000年9月1日一、事故经过:9月1日8:20左右,由于GA-1011B跳电引起压缩机停车(联锁),同时萃取系统7台泵跳电,造成全线停车。
在组织开停车过程中S-137取样旁路没关,不合格产品外送时,污染球罐进料管道,最终导致球罐产品污染。
二、原因分析:1、油泵跳电,备用泵没及时起跳,油压低于0.28Mpa,造成压缩机停车联锁。
2、由于操作人员对装置流程熟悉程度的缺乏及处理事故能力不够,S-137取样旁路阀没关,造成球罐产品污染。
三、应急措施:1、按事故停车程序处理。
2、精馏系统自身循环。
3、开启GA-1011A油泵。
四、经验及整改措施:1、检查油压联锁、起跳设定值、起跳时间等。
2、加强职工技能培训。
案例5时间:2000年12月12日一、事故经过:12月12日21:00,压缩机系统PICA-107压力缓慢上升,此时PICA-109压力无明显变化,但FR-119返回量下降较多,二段吸入压力最高达到0.25Mpa以上。
22:30按PB-2,压缩机作停车处理。
22:50启动压缩机,12月13日凌晨5:00丁二烯产品合格进球罐。
二、原因分析:根据压缩机系统现象分析:一段进口压力PICA-107缓慢上升,二段压力也逐渐上升,但PICA-109二段出口无明显变化,体现出的是FR-119返回量的下降,因此,原因是由于HC-102(压缩机一段返回调节阀)失控造成。
三、应急措施:1、HC-102调节阀现场手轮控制(双向)。
2、对HC-102现场调节阀进行维修。
四、经验及整改措施:1、室内与现场调节阀阀开度要有记录并要及时对照。
2、当调节阀失控时可用手轮调节。
3、发现问题及时处理。
4、加强职工应急事故处理培训和演习。
案例6时间:2001年6月30日一、事故经过:6月30日17:00时,B-DA107塔塔釜压力明显上升,塔顶压力正常,回流罐液面降低,采出量逐渐减少,但塔釜液面LICA-122显示正常,现场玻璃板液面计显示液面同沉筒显示基本相符。
塔顶与塔釜最大压差达0.12Mpa,塔顶产品中丁二烯-1.3纯度不合格,总炔严重超标达150ppm。
二、原因分析:1、沉筒与玻璃板液面计显示同时失真。
由于B-DA107塔釜重组份TBC含量相对较多(TBC溶点又较低:53℃左右),当投用时间较长时,易沉积于沉筒内壁、底部和浮子上,堵塞玻璃板针型阀阀芯。
2、由于液面显示失真,事实上已造成泛塔:a、由于再沸器气相气孔被液体堵塞,影响气液相分离效果。
b、提馏段塔板局部被液体浸没,相对减少了提馏段塔板数,造成精馏效果下降。
三、应急措施:1、降低B-DA107进料量,减少系统负荷。
2、产品切出走不合格线。
3、待压差接近正常值时相对适当提高回流比。
4、清洗和维修LICA-122沉筒和玻璃板液面计。
5、加大FICA-138的塔釜排放量。
四、经验及整改措施:1、加强现场检查,室内、室外液面要记录和校对。
2、B-DA107塔釜沉筒和玻璃板液面计要定期排放、确认。
3、加强对TBC量的控制。
案例7时间:2001年8月18日一、事故经过:8月18日16:00,B-GA103A试泵,当打开泵进口及密封溶剂管线阀门后,B-DA102、105塔釜液面相继上涨,切换兰式过滤器后,B-DA102液面下降控制较平稳,但B-DA105塔釜液面没有下降迹象,现场检查B-GA109A泵不上量,在B泵的切换过程中发现,泵出口倒淋气排不尽,泵无法正常开启,造成B-DA105塔液面持续上升,无法正常运行。
22:30决定二萃系统停车,产品切至不合格管线,返回碳四原料罐。
二、原因分析:1、B-GA103A试泵后,泵密封溶剂管线阀门没关,密封线上的单向阀因内部有垃圾等原因,不能正常工作,导致B-DA101A塔釜富溶剂有机会倒流到密封溶剂系统。
2、B-GA119进口过滤器不畅,导致泵出口压力偏低,PCA-123压力低于设定值。
3、B-GA119出口几根管线中B-GA103同GA109是并联的一股。
4、由于B-DA101A釜液中溶解着大量的烃类,当釜液由B-GA103泵经密封溶剂管线进入B-GA109泵时,压力徒降导致烃类气化,造成B-GA109泵气蚀,无法正常工作。
5、B-DA105塔釜液面长时间高过再沸器气相管线,导致无法正常气液交换,影响塔的汽提效果。
三、经验及整改措施:1、操作工责任心不强,没有严格按操作规程操作。
2、停泵后,密封溶剂阀要及时关闭。
3、原因分析思路不开阔,局限于就事论事。
4、当事人员汇报不清。
案例8时间:2002年7月2日一、事故经过:7月2日,新区丁二烯装置第一、第二萃取系统,因塔系、再沸器丁二烯热聚物结胶严重,影响装置的高负荷生产和产品质量的保证,决定停车抢修。
12:00C进料停,退料、溶剂热运、冷运等,萃取系统作停车检修前的各项准备4工作,精馏系统退料结束后,置换合格氮气保压。
4日8:00检修进场,7日12:00检修结束。
装置进行开车前的准备工作,8日13:00新区丁二烯装置重新投料开车。
二、原因分析:新区丁二烯装置从今年4月19日开车到7月2日停车,仅维持生产2个多月。
从设备打开后检查的情况分析,造成这次新装置停车检修的原因是多方面的。
首先,从萃取系统各塔的塔板看,普遍情况是塔板上生成了热聚物,尤其是B-DA1102塔塔板更加严重;其次,从再沸器如:B-EA1103A/B、1104A、1111情况来看,结垢物中混有许多铁锈状物。
原因分析主要有以下几点:1、压缩机系统因素a、B-FA1103罐顶至压缩机一段吸入口管线长。
b、压缩机吸入主阀为蝶阀,因阀板较厚相应减少了管径的通量。
c、压缩机一段吸入口过滤器B-FD11011过滤网存在堵塞现象。
d、B-GB1101正常工作能力7500NM3高于B-GB101近30%,相对增加了压缩机一段进口管线的流通量。
由于以上原因,相对增大了B-FA1103罐至压缩机一段吸滤器B-FD11011之间压差,间接造成B-DA1102塔釜压力上升,由0.024Mpa(相对于老区)上升到0.034Mpa,超过设计值0.03Mpa(设计温度为163℃)。
由于B-DA1102塔是常压汽提塔,压力、温度偏高,容易加速再沸器堵塞以及塔板热聚物的生成,造成了DA-1102再沸器严重堵塞,塔板结焦严重的现象。
2、塔内件安装从B-DA1103塔检查发现,大部分降液板与塔板之间的底隙距离偏小,最小的为14mm,一般为20mm,标准值为25mm。