TBM盘形滚刀磨损速率研究_谭青
TBM盘形滚刀磨损机理及其数值模拟的开题报告

TBM盘形滚刀磨损机理及其数值模拟的开题报告一、课题背景及研究意义:盾构机是一个大型工程机械设备,通常用于地下隧道建设中。
其中,TBM(盾构机)是一种先进的技术,其主要应用于市政道路、铁路、地铁、水利工程等领域。
然而,在TBM的使用过程中,由于各种原因,滚刀的磨损问题逐渐显现出来。
而且在大型准直掘进的时候,盘形滚刀的磨损速度尤其快。
因此,对于盘形滚刀的磨损机理和数值模拟研究具有重要的现实意义和深远的理论价值。
本文旨在深入探讨TBM盘形滚刀的磨损机理,并利用数值模拟技术进行验证,以期为实际工程提供一定的参考价值与指导意义。
二、主要研究内容:1. 盘形滚刀的结构及性能特点分析:包括盘形滚刀的工作原理、结构特点、功能以及材料特性等方面内容的分析。
2. 盘形滚刀的磨损机理的研究:基于轮廓针形理论,从宏观微观两个层面进行分析和研究。
在宏观层面,分析和研究与盘形滚刀磨损有关的主要因素,如盘形滚刀与地质环境、盘形滚刀与导向头、盘形滚刀表面材料等相互作用的机理,并结合实际工程中的磨损情况进行分析;在微观层面,采用嵌入式原子方法对盘形滚刀表面进行模拟计算,分析盘形滚刀在磨损过程中的表面能量变化等。
3. 盘形滚刀的磨损机理数值模拟:基于轱轴轮轮廓变化、盘形滚刀与岩土地质力学性质与磨损机理、非线性弹性数学模型等,设计盘形滚刀表面的数值模拟程序,利用计算机模拟出盘形滚刀的磨损过程和变化规律。
三、研究目标和意义1. 在实际工程中,对于TBM盘形滚刀的磨损机理进行深入研究和分析,能够为盾构机工程的可靠、节能、环保、高效运行提供技术支持。
2. 通过深入分析盘形滚刀磨损机理,并利用数值模拟技术,对盘形滚刀进行模拟预测,实现对设备运行维修的优化有效,提高其工作效率和使用寿命。
四、研究方法与技术路线1. 盘形滚刀的结构及性能特点分析:采用文献资料法,结合盾构机设备生产制造的相关技术和知识,深入挖掘和分析相关的研究进展和发展趋势。
2. 盘形滚刀的磨损机理的研究:采用界面互动机理的分析方法和原子嵌入式势场的计算技术,建立了盘形滚刀表面磨损机理的数学模型。
不同围压与节理特征下盘形滚刀破岩数值研究
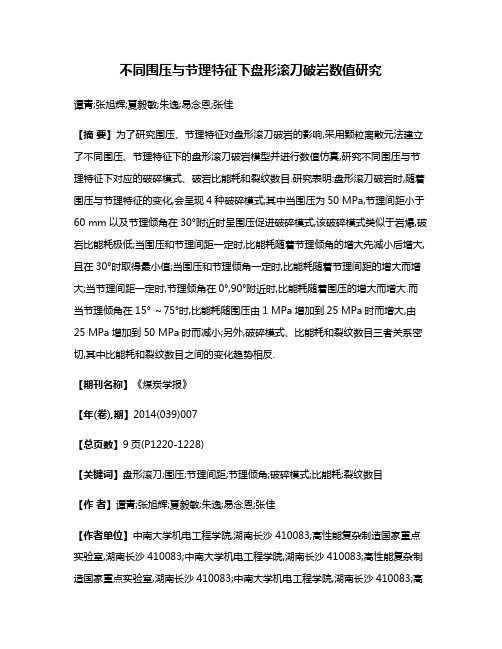
不同围压与节理特征下盘形滚刀破岩数值研究谭青;张旭辉;夏毅敏;朱逸;易念恩;张佳【摘要】为了研究围压、节理特征对盘形滚刀破岩的影响,采用颗粒离散元法建立了不同围压、节理特征下的盘形滚刀破岩模型并进行数值仿真,研究不同围压与节理特征下对应的破碎模式、破岩比能耗和裂纹数目.研究表明:盘形滚刀破岩时,随着围压与节理特征的变化,会呈现4种破碎模式;其中当围压为50 MPa,节理间距小于60 mm以及节理倾角在30°附近时呈围压促进破碎模式,该破碎模式类似于岩爆,破岩比能耗极低;当围压和节理间距一定时,比能耗随着节理倾角的增大先减小后增大,且在30°时取得最小值;当围压和节理倾角一定时,比能耗随着节理间距的增大而增大;当节理间距一定时,节理倾角在0°,90°附近时,比能耗随着围压的增大而增大.而当节理倾角在15° ~75°时,比能耗随围压由1 MPa增加到25 MPa时而增大,由25 MPa增加到50 MPa时而减小;另外,破碎模式、比能耗和裂纹数目三者关系密切,其中比能耗和裂纹数目之间的变化趋势相反.【期刊名称】《煤炭学报》【年(卷),期】2014(039)007【总页数】9页(P1220-1228)【关键词】盘形滚刀;围压;节理间距;节理倾角;破碎模式;比能耗;裂纹数目【作者】谭青;张旭辉;夏毅敏;朱逸;易念恩;张佳【作者单位】中南大学机电工程学院,湖南长沙410083;高性能复杂制造国家重点实验室,湖南长沙410083;中南大学机电工程学院,湖南长沙410083;高性能复杂制造国家重点实验室,湖南长沙410083;中南大学机电工程学院,湖南长沙410083;高性能复杂制造国家重点实验室,湖南长沙410083;中南大学机电工程学院,湖南长沙410083;高性能复杂制造国家重点实验室,湖南长沙410083;中南大学机电工程学院,湖南长沙410083;高性能复杂制造国家重点实验室,湖南长沙410083;湘潭大学机械工程学院,湖南湘潭411105【正文语种】中文【中图分类】TP391.9;U455.3全断面隧道掘进机(TBM)已经广泛使用于地下空间的隧道掘进工程中,而TBM盘形滚刀破岩又是掘进过程中的核心内容,因此对盘形滚刀破岩的研究显得极为重要。
滚刀滚动切削岩石的数值及试验研究

滚刀滚动切削岩石的数值及试验研究谭青;杨秧;夏毅敏;易念恩;张旭辉【摘要】为了研究滚刀滚动切削岩石的性能,合理简化盘形滚刀滚压破岩过程,采用颗粒离散元法分别建立了考虑摩擦力的滚刀滚动切削有、无节理岩体模型,分析了滚动切削模拟过程中切削力、裂纹发育、岩石破碎形态的变化规律.利用滚刀回转切削试验台进行了破岩试验,得到切削力随工况变化的规律,验证了仿真模型的准确性.研究结果表明:对无节理岩体,提高贯入度会增加主干裂纹深度和破碎面积,提高切削速度会增加法向力,而对滚动力影响不大;对含节理岩体,岩体节理强度越强则主干裂纹越深,比能耗越高;岩体的节理倾向会对破岩比能耗产生一定的影响,正向倾角切削效率高于逆向倾角约12%;节理倾角越小,正、逆向节理倾角破岩比能耗差值越大;合理安排刀盘正反转可提高破岩效率.【期刊名称】《湖南大学学报(自然科学版)》【年(卷),期】2018(045)008【总页数】10页(P69-78)【关键词】盘形滚刀;岩石力学;裂纹;节理;比能耗【作者】谭青;杨秧;夏毅敏;易念恩;张旭辉【作者单位】中南大学高性能复杂制造国家重点实验室,湖南长沙410083;中南大学机电工程学院,湖南长沙410083;中南大学高性能复杂制造国家重点实验室,湖南长沙410083;中南大学机电工程学院,湖南长沙410083;中南大学高性能复杂制造国家重点实验室,湖南长沙410083;中南大学机电工程学院,湖南长沙410083;中南大学高性能复杂制造国家重点实验室,湖南长沙410083;中南大学机电工程学院,湖南长沙410083;中南大学高性能复杂制造国家重点实验室,湖南长沙410083;中南大学机电工程学院,湖南长沙410083【正文语种】中文【中图分类】TP391.9;U455.39随着我国隧道工程建设的展开,全断面岩石掘进机(Full face rock tunnel boring machine,TBM)以其施工效率高、掘进安全、噪声小等诸多优点,在隧道施工中使用日益广泛.岩石的破坏和剥落通过刀盘上的盘形滚刀滚动切削来实现,然而在实际切削过程中,地质情况是复杂多变的,如岩石种类、节理等[1-2].国内外学者针对TBM不同工况下破岩效率进行了相应的滚刀切削试验.刘红岩等人[3]通过物理实验研究了节理对岩石的破坏模式、单轴抗压强度、弹性模量的影响.Howarth[4]通过线性切割试验研究了刀间距对破岩效果的影响.龚秋明等人[5]研究了岩石节理间距对破岩效果的作用,发现节理面对破岩过程中滚刀的力有很大影响.以上研究探讨了不同地质条件下掘进参数对滚刀滚动破岩效果的作用.近年来也有学者通过数值仿真研究滚刀切削岩石的工况并取得了一些成果.Bejari 等人[6-7]采用UDEC研究了节理对刀具破岩的影响,研究表明节理间距增大会减小刀具的切入率.Sun等人[8]采用有限元法对盘形滚刀的最优刀间距进行分析,并解决了平面刀盘的布置问题.Labra等人[9]采用混合离散元/有限元法建立滚刀切削岩石模型并分析掘进参数下滚刀破岩过程.马洪素等人[10]通过两组试验对不同节理倾向下裂纹走向进行研究,并通过FLAC分析了裂纹走向与应力场分布的关系.孔晓璇等人[11]及孙金山等人[12]通过PFC2D研究双滚刀侵入不同节理间距及节理倾角的岩体时裂纹的走向,得到了节理特征对裂纹扩展的影响.张桂菊等人[13]采用二维颗粒离散元研究岩石温度对破岩的影响.Liu等人[14-16]采用PFC2D研究单、多滚刀垂直侵入岩石的效率与岩石裂纹扩展形态.Choi等[17]采用PFC2D研究节理间距与节理倾角对滚刀受力的影响.谭青等[18]采用PFC2D研究滚刀侵入不同围压与节理条件岩石时破碎模式与破岩比能耗的规律.上述模拟研究多将滚刀滚动切削过程简化为滚刀垂直贯入岩体的过程,忽略滚刀水平滚动以及岩石摩擦因素.易于观察到滚刀垂直贯入岩石过程中裂纹发育规律,难以得到滚刀滚动破岩过程中岩石裂纹发育规律.此外,以上建立的岩石节理模型仅关注节理倾角或者节理间距,尚未考虑含节理岩体强度和节理倾向对破岩的影响.本文采用离散元数值方法建立了无节理滚动切削与含节理滚动切削模型,通过改变滚刀工作参数及岩石参数,对贯入度、切削速度、节理倾向、含节理岩体强度等参数进行模拟.通过观察仿真结果,得到破岩时滚刀受力、岩石裂纹数量变化、岩石裂纹生长过程,最后以回转试验对仿真得到的切削力进行验证.本文的创新之处在于:建立了考虑摩擦力的滚刀滚动切削数值模型,该模型与实际工程应用中滚刀破岩过程拟合度更高;分析不同工况下滚刀受力与岩石破碎模式的关联规律;建立了不同节理倾向、倾角与节理面强度的岩石模型,其结论适用地质范围更广.1 数值模型的建立1.1 简化滚刀模型TBM在掘进时,滚刀布置在刀盘上并伴随刀盘的运动而做垂直贯入和水平滚动(视掌子面为水平面),滚刀与岩石相互作用时产生指向掌子面的法向力FN、与掌子面平行而指向滚刀平移方向的滚动力FR和受到回转切削影响生成的侧向力FL三种滚刀切削力,如图1所示.法向力主要由刀盘推力提供,滚动力主要由刀盘扭矩提供,侧向力主要由回转运行中滚刀对岩石的挤压力产生.考虑本文主要研究滚刀水平滚动破岩,忽视侧向力影响,因此将三维的滚刀运动简化为二维滚动过程.文献[14-18]研究证明,将滚刀三维破岩简化为二维破岩是可行的.本文以工程实践中的常用滚刀进行1∶2缩尺所得的小滚刀作为研究对象,其参数见表1.基于表1中参数,简化滚刀模型为二维模型.1.2 模型宏、细观参数的标定由于试验条件限制,假定切削对象为泥岩、砂岩等软岩,由于天然岩石内部初始损伤缺陷难以统计,为了增加试验的可重复性,降低试样物理力学性能分布的随机性,本文采用混凝土代替岩石进行研究.混凝土的制作和养护参照GB/T 50081-2002《普通混凝土力学性能试验方法标准》[19].在力学测试中心测得混凝土试样的物理力学性能参数如表2所示,由表2可知,混凝土强度等级为C20,其抗压强度等物理力学特性近似自然界的泥岩、砂岩等软岩[20].为建立颗粒流模型细观参数与材料宏观物理力学参数之间的联系,需要确定颗粒的基本尺寸等参数(表3).以单轴压缩、巴西劈裂和直剪试验对模型进行标定(图2):单轴压缩试验见图2(a);巴西劈裂试验见图2(b);剪切试验见图2(c).通常采用试凑法按照一定规律反复调整细观参数,直到仿真输出曲线接近物理标定的曲线即可.标定得到的颗粒流模型细观力学参数见表4.图1 滚刀切削力示意图Fig.1 Cutter forces of the disc cutter表1 滚刀基本参数Tab.1 The basic parameters of the disc cutter直径/cm刀刃宽度/mm过渡圆弧半径/mm刀刃角/(°)2110420表2 软岩材料宏观参数Tab.2 Macro-parameters of soft rock material参数名单位数值密度kg/m32 360弹性模量GPa1.82抗压强度MPa21.88抗拉强度MPa1.47内聚力MPa4.12内摩擦角(°)35表3 颗粒流模型基本参数Tab.3 Basic parameters of PFC2DmodelRmin/mmRmax/Rminkn/ks0.31.22.5图2 颗粒流模型细观参数的确定Fig.2 Meso-parameters determination in PFC2D表4 细观力学参数Tab.4 Meso-mechanical parameters参数名单位数值颗粒密度kg/m32 950法向强度MPa15切向强度MPa15法向刚度N/m9.5×108切向刚度N/m3.8×108摩擦因数0.31.3 建立滚刀滚动切削数值模型为了研究滚动切削对破岩的影响,根据标定得到的细观力学参数分别建立无节理、含节理两种滚刀侵入岩体的切削模型.试样被安置在一个三面墙皆被固定的方槽中,模型尺寸为400 mm×200 mm.节理模型中节理特征通过JSET命令设置,由于滚刀的刚度远远大于软岩的刚度,所以将滚刀简化为刚体并赋予属性wall类型.滚刀在破岩过程中因摩擦力而被动转动,滚刀与岩石的接触摩擦因数取0.3.通过FISH语句可以提取滚刀受力等信息.仿真中材料的破坏过程可视为颗粒间连接键在载荷作用下断裂的过程.键连接有两种形式:接触键和平行键.通过设定键与颗粒的大小、强度,对不同的本构进行表述,当载荷超过预设键的强度时,便会使颗粒脱离接触而产生破坏,通过观察、统计仿真所得的微观裂纹可以了解岩体内部破碎情况.2 滚刀切削无节理岩石模型分析2.1 滚刀切削过程分析图3为滚刀滚动切削破岩过程,根据工程实践应用,设定滚刀贯入度为8 mm,切削速度为0.6 m/s.随着滚刀向前推进,岩体上层的岩石不断被破碎,滚刀前方产生较大的破碎块(图3(a)),同时岩体内部产生大量微裂纹,部分微裂纹汇聚成主干裂纹并向岩体深处扩展.图3 滚刀滚动切削岩石动态过程Fig.3 Dynamic process of rock cutting图4为滚刀切削力及滚刀角速度动态变化图.由图4可知,滚刀破岩过程中滚刀力曲线波动较大,且法向力的波动远大于滚动力.这说明岩石内部裂纹扩展主要由法向力主导,滚刀与岩石接触而转动,角速度均值约为5 rad/s,这说明滚刀的旋转瞬心在刀刃下方附近.图5为FISH函数记录的裂纹数目变化.随着切削行程的增加裂纹数目线性增加,张拉裂纹数目始终大于剪切裂纹数目,说明滚刀破岩过程中岩石的破碎以张拉破坏为主.切削行程/mm图4 滚刀力与角速度变化图Fig.4 Variation diagram of cutting force and angular velocity2.2 贯入度对滚刀切削的影响贯入度及切削速度的变化会改变滚刀与岩石的接触情况,同时受力、岩石破碎形态以及裂纹发育都会受到影响.图6反映了滚刀切削行程为300 mm,切削速度为0.6 m/s时不同贯入度下的切削状态.从图6可知,岩石破碎面积与主干裂纹深度均随贯入度的增加而增大.切削行程/mm图5 微裂纹个数随切削行程变化图Fig.5 Variation diagram of crack number with cutting length图6 不同贯入度下滚刀滚动破岩状态Fig.6 Rock breaking state under different cutting depths如图7所示,贯入度的增加使得主干裂纹平均深度大幅度增长.然而,随着贯入度的增加,主干裂纹平均长度与贯入度的比值在下降,说明随着贯入度增加,主干裂纹平均长度增速下降,单纯增加贯入度并不能有效增加主干裂纹长度.主干裂纹的扩张虽然消耗了大量能量,但并未直接将岩体剥落下来.较深的主干裂纹说明滚刀做功主要引起裂纹纵深发展,而用于表面破岩的做功较少,所以主干裂纹越长则破岩效率越低.此外,统计仿真结果可知,随着贯入度的增加,微裂纹数量线性增长.当贯入度较小时,剪切微裂纹占多数,在较大贯入度下,张拉微裂纹则占多数.这说明增加贯入度有利于张拉微裂纹的发育.通常岩石破碎效率以破碎比功[13]来衡量.本文为了简化模型,不考虑破碎块度大小,以掘进机常用的比能耗SE来衡量破岩效率.由于本文开展二维数值模拟,故将其定义为刀具切削单位面积岩石所需消耗的能量,表示为:(1)式中:SE为破岩比能耗(MJ/m2);WN为滚刀法向力做功;WR为滚刀滚动力做功;FN为法向力(N);FR为滚动力(N);p为贯入度(mm);J为滚刀的切削行程(mm);S为岩石破碎的面积(mm2).一般情况下法向力做功为滚动力做功的5%[18],故实际计算中只考虑滚动力做功.贯入度/mm图7 贯入度与裂纹深度关联规律Fig.7 Variation of cutting depth with crack depth随着贯入度的增加,滚刀滚动力和法向力都呈递增趋势(表5).其中,滚刀滚动力增长率远大于法向力的增长率,这说明滚动力对贯入度更加敏感.在工程中,一般控制滚刀的贯入度不超过10 mm以避免贯入度过大而增加滚刀的受力负荷,造成滚刀过早失效.由表5可知,随着滚刀贯入度的增加,破碎面积的增长速率下降,而比能耗迅速上升,最大增加量约为96%.说明增大贯入度虽然提高破岩速度,但是切削效率下降,且加剧了滚刀磨损,缩短了轴承寿命,导致提早换刀.因此,在施工中,不可盲目增加贯入度以提高掘进效率.表5 不同贯入度下滚刀滚动破岩参数统计表Tab.5 Simulation results with different cutting depth贯入度/mm滚动力/kN法向力/kN破碎面积/cm2比能耗/(J·cm-2)41.439.88110.503.8862.1912.23141.174.6584.0214.44176.926.82104.5815. 69180.177.632.3 速度对滚刀切削的影响图8为滚刀切削行程为300 mm,贯入度为6 mm时的破岩状态图.由图8可知,在不同切削速度下,岩体破坏状况相近,裂纹扩展情况及破碎块的形成亦相似.这说明切削速度对岩石破坏以及裂纹扩展的影响不大.此外,统计仿真结果可知,裂纹总数随切削速度变化波动较小,这说明切削速度不是影响微裂纹数目的主要参数.剪裂纹数目所占总裂纹数目的比例随切削速度的增加而上升.图8 不同切削速度下滚刀滚动破岩状态图Fig.8 Rock breaking state diagram with different cutting speed表6为不同切削速度下滚刀破岩的参数统计表.可知加大切削速度对滚动力、破碎面积和比能耗的影响并不大.滚刀法向力对切削速度较为敏感,随着切削速度的提升,法向力显著增加,当切削速度从0.4 m/s提高到1 m/s时,滚刀法向力增加约50%.因此,施工中在确保滚刀承受的法向冲击力不超过刀圈承载额的前提下,可提高切削速度增加破岩速度.表6 不同切削速度下滚刀滚动破岩参数统计表Tab.6 Simulation results with different cutting speed速度/(m·s-1)滚动力/kN法向力/kN破碎面积/cm2比能耗/(J·cm-2)0.42.128.9132.254.810.62.5210.6134.675.610.82.6111.6139.005.631.02.71 12.23131.176.203 滚刀切削含节理岩石模型分析3.1 滚刀切削过程分析已有研究表明[6,7,11],节理特性对滚刀切削岩石有较大的影响.自然界中岩石的节理分布一般都比较复杂,同时滚刀与节理的相对位置也不断变化,因此,本文对此进行必要的简化.假定数值模型中只存在一组等间距节理(设节理间距恒为10 mm),综合考虑节理倾向、倾角和含节理岩体强度对滚刀破岩的影响,规定节理倾向与滚刀掘进方向一致为正向,相反为逆向.图9和图10分别为水平0°和垂直90°,正、逆向倾角分别为20°、40°、60°和80°的节理岩体.含节理的岩体强度由节理面的颗粒细观参数(摩擦因数、法向强度、切向强度)间接决定.通过改变节理面的颗粒细观参数,可以得到不同强度的节理岩体(也有文献简称为节理强度),即节理岩体具有不同的内聚力和内摩擦角.不同强度节理岩体的物理数值可通过直剪试验得到(图2(c)).研究发现,当摩擦因数一定时(本文设置摩擦因数为0.3),法向强度与切向强度越大,得到含节理的岩体强度也会较大.本文用2种节理面颗粒连接强度(法向与切向强度分别取8 kPa和200 kPa)来描述低强度和高强度含节理岩体.图9和图10是切削距离为250 mm,贯入度为8 mm,削速度为0.6 m/s时的破岩状态图.其中,图9对应的节理面粘接强度为8 kPa,摩擦因数为0.3,节理强度较低.从图9可知,主干裂纹很少向纵深扩展,这是由于低强度节理面很容易起裂和断裂,阻碍了滚刀力向岩体深处传递,所以岩体深处很少有主干裂纹.此外,还可以观察到有大量碎块从岩体表面崩落,起裂方向大多垂直于节理面.图10对应的节理面粘接强度为200 kPa,摩擦因数为0.3,节理强度高.当节理倾向为正,倾角分别为60°与80°时可以观察到主干裂纹扩展方向有垂直于节理面的倾向,有的主干裂纹可以跨越几组节理面到达岩体深处.这说明较高的节理强度对于裂纹扩张的阻碍效应小于低节理强度.当节理倾向为逆向时,倾角分别为60°和80°时,主干裂纹扩展方向有平行于节理面的倾向,与无节理破岩比较(图6(c)),二者裂纹扩展形态非常近似,节理的存在对于主干裂纹扩展深度影响很小.图9 低强度含节理岩体(连接强度为8 kPa)Fig.9 Low strength for jointed rock masses(joint bond strength 8 kPa)图10 高强度含节理岩体(连接强度为200 kPa)Fig.10 High strength for jointed rock masses(joint bond strength 200 kPa)3.2 节理特征对微裂纹数量的影响微裂纹与节理关联规律如图11所示.由图11可知,高强度节理岩体含张拉裂纹数量多于低强度岩体,低强度节理岩体含剪切裂纹数量多于高强度岩体.考虑到岩石抗压不抗拉的特性,滚刀入侵高强度节理岩体时主要发生了张拉破坏.对低强度节理岩体而言,节理间连接强度较低,节理层容易断裂,因而剪切裂纹较高强度节理岩体多.岩体节理强度高时,正向节理倾角下含有更多的微裂纹数量.此外,节理倾角分别为20°、60°时,裂纹发育受到阻碍.节理角度/(°)(a)拉张裂纹数节理角度/(°)(b)剪切裂纹数图11 微裂纹与节理特征关系图Fig.11 Relation diagram of micro-crack numbers with joint characteristics3.3 节理特征对裂纹深度的影响节理倾角与节理强度对主干裂纹的扩展深度有着明显的控制作用:应力场不均分布导致低强度节理面容易产生张拉微裂纹起裂[10],节理面对主干裂纹扩展起阻隔作用[5],而且节理倾角能影响主干裂纹扩展方向.因此,在相同的主干裂纹长度下,裂纹深度会由于扩展方向的改变而改变.主干裂纹深度整体趋势规律如图12所示. 相较低强度节理面,高强度节理面中主干裂纹更容易扩展到岩体深处,这是由于低强度节理面对裂纹继续扩展起到阻隔作用.基于上文讨论,主干裂纹深度过大对于提高破岩效率并无直接益处,所以低节理强度更有利于提高破岩效率.由图12可看出,水平和垂直节理倾角下主干裂纹相对较长.在高强度节理面中,倾角分别为20°、60°时,主干裂纹较浅,且逆向节理倾角产生的裂纹较正向倾角更深,这反映了正向节理倾角下破岩更加高效.在低强度节理面中,正、逆向倾角则对裂纹深度无明显影响.节理角度/(°)图12 主干裂纹深度与节理特征关系图Fig.12 Relation diagram main crack depth with joint characteristics3.4 节理特征对破岩面积的影响在相同贯入度下,更大的破碎面积意味着更快的掘进速度.通过测量,可以得到破岩面积受节理特征影响的规律,如图13所示.正向倾角破岩面积更大,高强度节理面下该现象更显著.高强度节理倾角分别为80°与0°时,破碎面积相比其他倾角更大,该结论与谭青等[18]的结论一致.低强度节理倾角分别为20°、60°和90°时,破碎面积相对较小.节理角度/(°)图13 破岩面积与节理特征关系图Fig.13 Variation of breakingarea with joint characteristics3.5 节理特征对比能耗的影响通过仿真计算,得出滚刀力、破碎面积及比能耗等参数如表7所示.由于仿真条件限制,破碎块无法排出(图9(d)),导致在后续滚刀切削中已经崩落的岩石会进一步被滚刀破碎,造成滚动力增加.为了贴近实际施工状态,对仿真所得滚动力乘以系数φ(φ取值为0~1).根据表7中数据可以得到比能耗趋势如图14所示.表7 比能耗统计表Tab.7 Specific energy statistics table连接强度/kPa节理倾向节理倾角/(°)滚动力/kN破碎面积/cm2比能耗/(J·cm-2)8逆正03.48114.17.63203.81105.29.05404.13126.38.17604.31124.18.68804.42125.78.79904.10117.68.72203.31107.47.70403.54120.37.36603.74117.87.94804. 26126.98.39200逆正05.37137.79.74204.78126.59.45405.38133.710.06604.66124.09.40804.96133 .29.31904.70130.59.00204.27131.18.14404.79135.58.84604.27125.98.48804. 58133.88.56由图14可知,在相同掘进参数下,正向节理倾角比能耗均低于逆向倾角比能耗.这是由于在逆向倾角下,滚刀运动方向与节理夹角大多呈钝角,主干裂纹将沿节理面向深处扩展.在正向倾角下,夹角多为锐角,滚刀挤压节理面产生破碎块,因而阻断主干裂纹的扩展.该结论与文献[17]中结论一致.在垂直90°倾角时,滚刀力一部分与节理面相互作用使岩石破碎,一部分沿节理面向岩石内部传递.90°节理倾角比能耗介于正向和逆向倾角比能耗之间.由表7中切削比能耗计算可知,正向倾角下节理岩体切削效率高于逆向倾角约12%.对低强度节理岩体,当节理倾角分别为20°、40°、60°和80°时,比能耗减少比例分别为18%、11%、9%和5%;对高强度节理岩体,减少比例分别为16%、14%、11%和9%,这是由岩体的连接强度所决定的.在低节理强度下,岩体连接强度小,使岩体容易破碎,所以低强度节理岩体受节理倾角影响较大;反之,高强度节理岩体强度受倾角影响较小.低节理强度岩体比能耗普遍低于高节理强度岩体,这说明低强度节理面阻隔了主干裂纹向岩体深处扩展,减少了滚刀做功的无效耗散,提高了破岩效率.相反,高强度节理面不易阻隔主干裂纹向岩体深处扩展,破岩效率不如低强度节理岩体高.整体上,正向倾角为20°对提高滚动切削高强度节理岩体的效率有利,正向倾角为40°时对提高滚动切削低强度节理岩体效率有利.节理角度/(°)(a)低强度节理岩体倾向对比节理角度/(°)(b)高强度节理岩体倾向对比节理角度/(°)(c)逆向倾角高、低强度岩体对比节理角度/(°)(d)正向倾角高、低强度岩体对比图14 比能耗与节理特征关系图Fig.14 Variation of specific energy with joint characteristics4 试验验证4.1 试验系统组成试验在盘形滚刀回转破岩试验台上进行.如图15(a)和图15(b)所示,试验台由回转机械主机、液压系统、控制系统和测试系统构成.测试系统由三向力传感器、低通滤波器、USB采集卡、工控机、高速摄像系统、LabVIEW系统组成.高速摄像系统可以捕捉到岩体表面起撬直到崩落的全过程(图15(c)和图15(d)).切削对象为混凝土(仿软岩),混凝土的物理力学指标见表2,滚刀参数见表1.图15 TBM滚刀物理切削试验Fig.15 Experiment of rock breaking by TBM disc cutter4.2 滚刀受力分析试验试验通过改变切削速度及贯入度来观察滚刀的受力状况,进行2组试验分别记录滚刀滚压过程中所受的三向力和滚刀行程.第1组试验为恒定速度:贯入度分别采用4 mm和10 mm,切削速度为0.6 m/s.第2组试验为恒定贯入度:切削速度分别采用0.4 m/s和1.0 m/s,贯入度为6 mm.不同贯入度与切削速度下切削力变化情况如图16所示.4.3 切削力误差分析PFC2D基本结构是一个三维的圆柱体(圆柱体有厚度,但是不能在Z轴上移动,只能在X和Y轴移动、转动),厚度定义为滚刀刀刃宽,仿真得到的滚刀力与物理试验测试的滚刀力之差别在于是否考虑滚刀两侧摩擦力.本文研究滚刀在较小贯入度下的切削,此时摩擦力影响较小.根据仿真与试验滚刀力的数据做出误差分析,如表8所示.可见贯入度较大时,因摩擦力引入的误差会增大,平均误差为16.44%.这说明仿真得到的滚动力较为贴近工程实际情况.同时证明数值模型与试验试样的宏观物理参数一致性较高.图16 不同贯入度与切削速度下切削力变化曲线Fig.16 Cutting force with different cutting depth and speeds表8 不同掘进参数下的误差分析Tab.8 Error analysis under different cutting parameters贯入度/mm速度/(m·s-1)滚动力/kN仿真值试验值误差/%法向力/kN仿真值试验值误差/%40.61.431.5910.06 9.889.940.60 100.64.583.4632.3715.6913.8213.53 60.42.521.7444.83 10.68.5823.54 61.02.712.813.5612.2312.613.015 结论1)无节理切削组中,贯入度从4 mm 提高到10 mm会增加主干裂纹深度和破碎面积,但裂纹深度和破碎面积的增长速率会逐渐降低,且比能耗相应增加96%.相对法向力,滚刀的滚动力对贯入度更加敏感.施工中不能盲目增加贯入度,以免损坏刀架.2)无节理切削组中,当切削速度从0.4 m/s 提高到1.0 m/s时,滚刀法向力增加。
TBM滚刀刀圈材料合金成分对组织和耐磨性能的影响
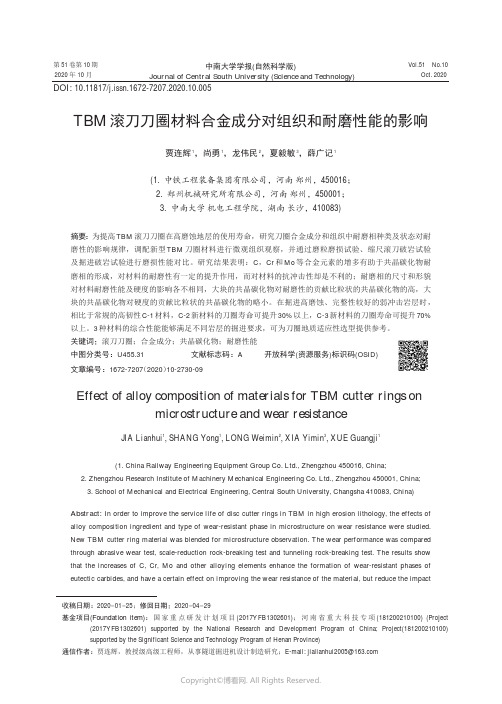
第51卷第10期2020年10月中南大学学报(自然科学版)Journal of Central South University (Science and Technology)V ol.51No.10Oct.2020TBM 滚刀刀圈材料合金成分对组织和耐磨性能的影响贾连辉1,尚勇1,龙伟民2,夏毅敏3,薛广记1(1.中铁工程装备集团有限公司,河南郑州,450016;2.郑州机械研究所有限公司,河南郑州,450001;3.中南大学机电工程学院,湖南长沙,410083)摘要:为提高TBM 滚刀刀圈在高磨蚀地层的使用寿命,研究刀圈合金成分和组织中耐磨相种类及状态对耐磨性的影响规律,调配新型TBM 刀圈材料进行微观组织观察,并通过磨粒磨损试验、缩尺滚刀破岩试验及掘进破岩试验进行磨损性能对比。
研究结果表明:C ,Cr 和Mo 等合金元素的增多有助于共晶碳化物耐磨相的形成,对材料的耐磨性有一定的提升作用,而对材料的抗冲击性却是不利的;耐磨相的尺寸和形貌对材料耐磨性能及硬度的影响各不相同,大块的共晶碳化物对耐磨性的贡献比粒状的共晶碳化物的高,大块的共晶碳化物对硬度的贡献比粒状的共晶碳化物的略小。
在掘进高磨蚀、完整性较好的弱冲击岩层时,相比于常规的高韧性C-1材料,C-2新材料的刀圈寿命可提升30%以上,C-3新材料的刀圈寿命可提升70%以上。
3种材料的综合性能能够满足不同岩层的掘进要求,可为刀圈地质适应性选型提供参考。
关键词:滚刀刀圈;合金成分;共晶碳化物;耐磨性能中图分类号:U455.31文献标志码:A开放科学(资源服务)标识码(OSID)文章编号:1672-7207(2020)10-2730-09Effect of alloy composition of materials for TBM cutter rings onmicrostructure and wear resistanceJIA Lianhui 1,SHANG Yong 1,LONG Weimin 2,XIA Yimin 3,XUE Guangji 1(1.China Railway Engineering Equipment Group Co.Ltd.,Zhengzhou 450016,China;2.Zhengzhou Research Institute of Machinery Mechanical Engineering Co.Ltd.,Zhengzhou 450001,China;3.School of Mechanical and Electrical Engineering,Central South University,Changsha 410083,China)Abstract:In order to improve the service life of disc cutter rings in TBM in high erosion lithology,the effects of alloy composition ingredient and type of wear-resistant phase in microstructure on wear resistance were studied.New TBM cutter ring material was blended for microstructure observation.The wear performance was compared through abrasive wear test,scale-reduction rock-breaking test and tunneling rock-breaking test.The results show that the increases of C,Cr,Mo and other alloying elements enhance the formation of wear-resistant phases of eutectic carbides,and have a certain effect on improving the wear resistance of the material,but reduce the impactDOI:10.11817/j.issn.1672-7207.2020.10.005收稿日期:2020−01−25;修回日期:2020−04−29基金项目(Foundation item):国家重点研发计划项目(2017YFB1302601);河南省重大科技专项(181200210100)(Project(2017YFB1302601)supported by the National Research and Development Program of China;Project(181200210100)supported by the Significant Science and Technology Program of Henan Province)通信作者:贾连辉,教授级高级工程师,从事隧道掘进机设计制造研究;E-mail:**********************第10期贾连辉,等:TBM滚刀刀圈材料合金成分对组织和耐磨性能的影响resistance of the material.The effect of the size and morphology of the wear-resistant phase on the wear resistance and hardness of the material is also rge eutectic carbides contribute more to wear resistance than the granular eutectic carbides,and large eutectic carbides contribute slightly less to the hardness than the granular eutectic carbides.In driving high abrasion and weak integrity rock formations,compared with the conventional high toughness C-1material,the life of the cutter ring of the new C-2material can be increased by more than30%, and C-3new material ring life can be increased by more than70%.The comprehensive performance of the three materials can meet the requirements of different rock formations,which provides reference for the geological adaptability selection of cutter ring.Key words:disc cutter ring;alloy composition;eutectic carbide;wear-resisting performance岩石隧道掘进机(tunnel boring machine,TBM)掘进过程中伴随刀盘转动,刀盘上安装的盘形滚刀刀圈直接与岩体相互作用,滚刀贯入岩体滚动挤压,岩石表面产生局部变形并出现微观裂纹,随着挤压力增大,微观裂纹发展成为主裂纹并贯通,形成岩片破碎[1−2]。
TBM滚刀磨损研究现状及展望
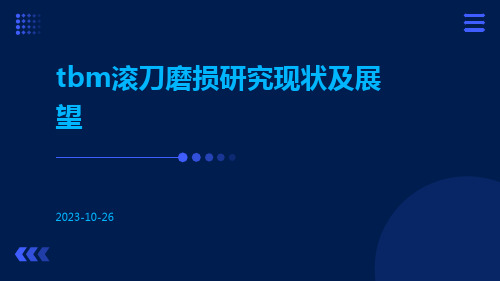
03
随着隧道施工向高速度、高效率、高精度方向发展,对TBM滚刀磨损的研究显得尤为重要。
通过对TBM滚刀磨损的研究,可以深入了解滚刀磨损的机理和规律,为优化滚刀设计和提高隧道施工效率提供理论支持。
对于隧道施工单位而言,通过研究滚刀磨损规律,可以制定更为合理的维护和更换滚刀的策略,提高施工经济效益。
改进滚刀结构设计
利用传感器和监测系统,实时监测滚刀的磨损状态和地下岩层的分布情况,为调整施工参数和预防性维护提供依据。
发展智能监测技术
THANKS
感谢观看
tbm滚刀磨损研究现状及展望
2023-10-26
目录
contents
研究背景和意义tbm滚刀磨损研究现状滚刀磨损对tbm性能的影响展望与挑战结论与建议
01
研究背景和意义
01
TBM(Tunnel Boring Machine)是一种先进的隧道施工设备,广泛应用于全球各地的隧道建设中。
研究背景
02
开发了基于图像识别、振动分析、声发射等技术的在线监测系统,用于实时监测滚刀的磨损状态。
滚刀磨损监测技术
建立了滚刀磨损数据共享平台,汇集了不同地质条件下的滚刀磨损数据,为工程实践提供参考。
滚刀磨损数据库建设
滚刀磨损研究起步较晚
工程应用与理论研究结合
创新性研究成果
国的影响
研究结论
滚刀磨损的主要原因是岩石的硬度、裂隙发育程度、地下水等因素,这些因素在不同地层条件下是不断变化的。
滚刀磨损的后果包括刀具损坏、更换频繁、施工周期延长和成本增加等,对隧道施工和工程安全造成不利影响。
目前,针对滚刀磨损的研究主要集中在材料、热处理和结构设计等方面,虽然取得了一定的成果,但仍存在许多亟待解决的问题。
岩石温度对盘形滚刀掘进参数破岩特性的影响
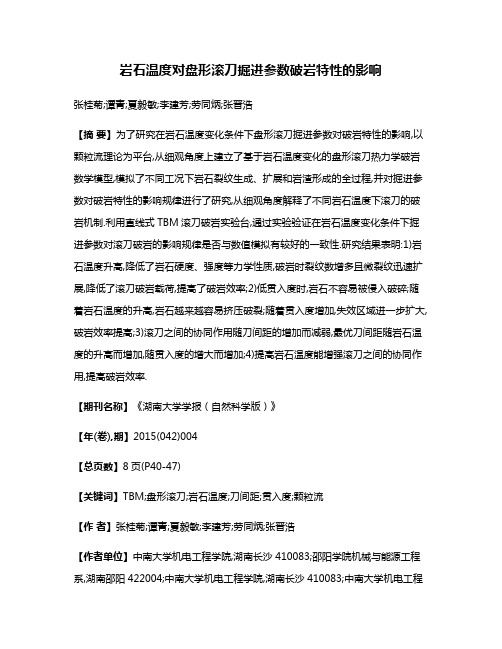
岩石温度对盘形滚刀掘进参数破岩特性的影响张桂菊;谭青;夏毅敏;李建芳;劳同炳;张晋浩【摘要】为了研究在岩石温度变化条件下盘形滚刀掘进参数对破岩特性的影响,以颗粒流理论为平台,从细观角度上建立了基于岩石温度变化的盘形滚刀热力学破岩数学模型,模拟了不同工况下岩石裂纹生成、扩展和岩渣形成的全过程,并对掘进参数对破岩特性的影响规律进行了研究,从细观角度解释了不同岩石温度下滚刀的破岩机制.利用直线式TBM滚刀破岩实验台,通过实验验证在岩石温度变化条件下掘进参数对滚刀破岩的影响规律是否与数值模拟有较好的一致性.研究结果表明:1)岩石温度升高,降低了岩石硬度、强度等力学性质,破岩时裂纹数增多且微裂纹迅速扩展,降低了滚刀破岩载荷,提高了破岩效率;2)低贯入度时,岩石不容易被侵入破碎;随着岩石温度的升高,岩石越来越容易挤压破裂;随着贯入度增加,失效区域进一步扩大,破岩效率提高;3)滚刀之间的协同作用随刀间距的增加而减弱,最优刀间距随岩石温度的升高而增加,随贯入度的增大而增加;4)提高岩石温度能增强滚刀之间的协同作用,提高破岩效率.【期刊名称】《湖南大学学报(自然科学版)》【年(卷),期】2015(042)004【总页数】8页(P40-47)【关键词】TBM;盘形滚刀;岩石温度;刀间距;贯入度;颗粒流【作者】张桂菊;谭青;夏毅敏;李建芳;劳同炳;张晋浩【作者单位】中南大学机电工程学院,湖南长沙410083;邵阳学院机械与能源工程系,湖南邵阳422004;中南大学机电工程学院,湖南长沙410083;中南大学机电工程学院,湖南长沙410083;高性能复杂制造国家重点实验室,湖南长沙 410083;中南大学机电工程学院,湖南长沙410083;中南大学机电工程学院,湖南长沙410083;中南大学机电工程学院,湖南长沙410083【正文语种】中文【中图分类】TP391.9;U455.39全断面岩石隧道掘进机(full face hard rock tunnel boring machine, 简称TBM)集大型化、自动化、高速化、流程化、精密化等特性于一体,广泛应用于铁路建设、南水北调、西气东输等隧道工程中.[1]盘形滚刀是TBM破碎岩石的主要刀具,其破岩效率直接影响隧道工程的开挖进度.在大埋深、长距离硬岩掘进环境中,TBM通常会受到复杂地质条件如高温、节理、岩溶、高地应力、掘进地层的自重应力、温度引起的热应力等因素的影响,使岩石表现出与浅部截然不同的物理力学特性,进而造成滚刀的损耗量大、破岩效率低、稳定性差等施工问题.[2]因此,在考虑这些掘进中的地质因素耦合作用下,提高滚刀的破岩效率,延长滚刀的使用寿命已经成为国内外专家学者研究的重要课题.针对不同温度条件下岩石的力学性能变化,国内外许多专家学者做了大量的研究工作:Vander Molen[3]就1980年以前的温度对岩石特性影响的主要研究成果做了系统的总结;Alm[4]等研究了花岗岩在不同温度条件下的力学性能及其微破裂性能;Chen等 [5]研究了在单轴压缩和疲劳载荷条件下温度对花岗岩力学性能的影响;Smithies等[6]探讨了不同温度下花岗岩岩石和岩浆的力学性质,如泊松比、弹性模量、断裂韧性、抗压强度以及岩石微破裂,获得了岩石力学性能随温度和时间的破坏机理;张志镇等[7]通过高温冷却加载以及实时高温加载下的单轴压缩试验,得到了两种加载方式下弹性模量、单轴抗压强度、剪切滑移应变及纵波波速等随温度的变化规律;左建平等[8]研究了不同温度对岩石的破坏规律以及变形的影响,建立了岩石在静载荷下温压耦合的破坏准则.盘形滚刀掘进参数(贯入度和刀间距)的合理设计是提高TBM破岩效率的关键因素,设计掘进参数时需综合考虑地质条件的影响.由于在不同的温度条件下,岩石表现出不同的力学特性以及破裂方式,因而针对岩石温度变化设计滚刀掘进参数具有一定的现实意义.研究掘进过程中刀具与岩石之间相互作用的工作状况与动态行为,揭示破岩机理及破碎特征,可为延长刀具的使用寿命、改善切削效果、提高破岩效率提供理论基础.为此,本文尝试在岩石温度及掘进参数变化的条件下,从岩体细观尺度出发,基于颗粒流离散元方法对盘形滚刀的破岩特性进行分析,研究不同岩石温度下滚刀掘进参数对破岩特性的影响,并进行数值模拟及实验验证,为TBM盘形滚刀的破岩机理研究提供一定的理论依据,同时对提高滚刀的破岩效率、增强滚刀的地质适应性和使用寿命,实现高效率、低能耗、低损耗的隧道掘进具有一定的理论价值和工程意义.1.1 岩石颗粒流方法颗粒流方法是一种离散单元法,其从细观角度的离散单元之间的相互作用,解释岩石的宏观变形等力学性质,对分析大位移、大变形以及非线性等相关的岩石问题具有显著的优势.颗粒离散元法可以解决研究对象在特定条件下的宏观变形与裂纹问题.其将离散单元分为颗粒以及块体两部分,根据单元之间的相互作用以及循环迭代求解整个颗粒集合体的行为.当两颗粒接触时,会产生位移重叠;根据力-位移定律和本构关系可以得到颗粒受到的力,进而获得颗粒的加速度、速度以及新的位移量,如此反复循环[9].式中:mi和Ji分别为颗粒单元的质量和转动惯量;和分别为颗粒单元的中心位置和角矢量;为颗粒单元i的相邻颗粒单元j对它的作用力;为到颗粒单元i的力臂;和分别为颗粒单元i的外力和外力矩;Ni为颗粒单元i的邻居单元数目;N为模型中颗粒单元的总数目.1.2 颗粒流热力学耦合计算模型在颗粒流方法中,采用与颗粒有关的热存储器以及与接触键有关的热管的细观模型来模拟宏观的温度场,热量在激活管道中通过激活的热存储器进行传递.当岩石样本模型中两颗粒的接触有重叠或存在接触键时,热存储器之间的热管被激活;当岩石样本模型在加载过程中不存在接触键或接触键断裂时,将影响活动热管的数量,进而改变材料的宏观热学特性[10].岩石、混凝土等材料的破坏可以看作颗粒之间接触键的断裂过程.1)颗粒流热力学基本方程.对于连续介质,假设物体的应变变化不会引起温度的改变,则热传导方程为:其中:qi为热流通量;qv为单位热功率密度;ρ为材料的密度;Cv为岩石材料的比热容;T为材料温度.依据傅里叶变换,连续介质的热流通量和温度梯度之间的关系为:其中:kij为材料的热传导率张量.对式(3)进行离散化,假设离散后的颗粒总体积为V,单位体积内的热流通量用qi的散度表示,则在颗粒体积V的热存储器上平均散度qi为:假设离散后材料的热量只在N个热管中流动,从而式(4)可以转换为:其中:下标p为与热管p相关的变量;为流经热管p的功率,此处可得离散化后的热传导方程:其中:Qv=Vqv,为离散化后的热源强度;m为离散化后的质量.在颗粒离散元中,假设单个热管的热阻为η,颗粒体中包含N个热管,总体积为V,由于热量只在热管内流通,则材料的平均热流通量为:其中:A(p)为热管的有效横截面积;l(p)为热管的长度.热管的热流通量为:其中ΔT为热管两端的温度差,与温度梯度的关系为:可得颗粒离散元中热传导率的张量kij表达式为:从式(10)可以看出,只要给定单位法向矢量、单个热管的长度、热阻及总热管数目等相关参数就可计算出颗粒离散元材料的热传导率.2)颗粒流热力学耦合方程.颗粒流程序中,主要通过颗粒元素之间接触键的热膨胀来描述颗粒材料的热应变,则宏观温度的变化引起的材料热应变可通过对颗粒半径的改变来实现.当宏观温度改变ΔT,可计算出颗粒半径的改变量ΔR=αRΔT.其中:α是指颗粒的热线性膨胀系数.假设两颗粒元素之间存在接触键且热管已经激活,则接触键的长度随着宏观温度的改变会产生相应的变化,从而影响颗粒的受力情况.当温度变化为ΔT时,随着接触键长度的改变,颗粒受到的法向力为其中为接触键的法向刚度;A为接触键的横截面面积;为颗粒材料的热膨胀系数.在实际数值模拟中,可通过对岩石材料加载不同的温度,来模拟岩石材料宏观热力学特性.1.3 盘形滚刀破岩效率盘形滚刀的破岩效率主要通过比能耗大小来体现,比能耗指滚刀切割单位体积岩石所做的功[11].式中:Es为破岩比能耗;Fv为滚刀所受平均垂直力;Fr为滚刀所受平均滚动力;d为贯入度;S为破碎块面积;l为滚刀的切削轨迹,只考虑滚刀侵入过程时l=0;V为岩屑体积,V=St,t为单位厚度.1.4 盘形滚刀侵入岩体模型本课题研究的岩石材料是从广州某地采购的花岗岩,为了使颗粒流样本能够反映真实岩石材料的宏观力学特性,需匹配岩石材料的细观参数与宏观力学特性,对材料的宏、细观参数进行标定.依据真实试验测得的数据,通过数值试验反复进行调节细观参数,直到试验表现出来的宏观特性与真实材料的宏观特性参数相一致,标定过程才算完成,标定过程参见文献[12-13]. 图1所示为双刀破岩的颗粒流模型,其中参数D为刀间距,d为贯入度.在数值模拟过程中,将盘形滚刀刀圈定义为刚体,刀圈轮廓用刚性墙(wall)模拟,文中采用的是应用较为广泛的近似常截面盘形滚刀,适应软到中硬岩地层,主要几何参数:刀刃顶部宽度10 mm,过渡圆弧半径4 mm,刀刃角20°.岩石试件尺寸为200 mm×400 mm,包含颗粒数目38 662个.利用软件自带fish语言,编制控制滚刀运动的伺服控制程序,通过改变岩石的温度参数及掘进参数,监测盘形滚刀破岩规律的变化.2.1 数值模拟2.1.1 破岩体积分析岩石温度对破岩体积的数值模拟结果进行统计分析,结果如图2所示.可以看出:在同一温度和刀间距条件下,随着贯入度的增加,岩石的破碎体积过度增大,因此破碎体积增加的幅度逐渐减少;在同一温度和贯入度条件下,破岩体积随刀间距的增加而增大,说明刀间距的增大增加了滚刀之间能够破碎的岩石体积,当滚刀之间的岩石裂纹贯通,相应的破岩体积增大,但当刀间距增加到一定程度时,裂纹会互不贯通,出现各自破岩现象;在同一刀间距和贯入度条件下,随着岩石温度的增加,岩石从无法交汇贯通逐渐过渡到贯通、过度破碎,说明岩石温度是影响滚刀破岩体积的一个因素,温度的增加造成了滚刀破岩载荷减少,同时促进岩石裂纹的扩展,相应的破岩体积也随着增大,其增加的幅度逐渐增大,说明温度的增加,引起岩石内部应力的减少,减少的幅度逐渐增大,岩石更加容易破碎,且破岩体积相应增大.2.1.2 破岩载荷分析根据数值结果对滚刀破岩平均载荷进行分析,结果如图3所示.可知,在相同岩石温度、贯入度条件下,滚刀的破岩载荷随着刀间距的增加逐渐增加,这是由于刀间距较小时,滚刀之间存在协同效应,滚刀受到的破岩载荷相对较小;刀间距逐渐增大,协同作用逐渐减弱,滚刀呈现各自破碎的状况,对应的破岩平均载荷也相应增大.在相同贯入度、刀间距条件下,随着温度的逐渐升高,滚刀的破岩平均载荷逐渐降低.这是由于温度的升高,增加了岩石内部的热应力,降低了岩石的断裂韧度以及强度,使得岩石更加容易破裂,并且增大了滚刀之间的协同效应,滚刀平均载荷也逐渐降低.2.1.3 破岩比能耗分析对数值模拟的破碎体积和破岩平均载荷进行统计,计算各工况条件下的破岩比能耗,结果如图4所示.可以看出:在相同贯入度和岩石温度条件下,滚刀破岩比能耗随刀间距的增加呈现先减小后增大的趋势,说明在该工况下存在一个最优刀间距,使得滚刀的破岩比能耗最小.在常温和贯入度d=4 mm时,岩石的破碎模式从裂纹贯通过渡到没有贯通,刀间距的增加,使得破岩体积和破岩载荷增大,但增大的幅度不一样,开始破岩载荷增大的幅度比破岩体积增大的幅度小,滚刀破岩比能耗随刀间距的增大而逐渐减小.随着刀间距进一步增大,岩石裂纹从贯通过渡到不贯通,滚刀之间的协同作用减弱,滚刀的破岩比能耗随之增大,并且破岩体积由于裂纹没有贯通而变得很小,滚刀的破岩比能耗随刀间距的增大而逐渐增大.在同一贯入度以及刀间距下,随着岩石温度的升高,使得岩石更加容易侵入,岩石更加容易破碎,滚刀的破岩比能耗逐渐减小,对应的最小比能耗即最优刀间距则增大到150 ℃时的80 mm,如图4(a)所示.贯入度为8 mm时,由于滚刀贯入度的增大,滚刀之间的协同效应相对增大,破岩比能耗逐步增加,裂纹从不贯通过渡到刚好贯通最终为过度破碎状态,滚刀的破碎体积逐渐增大,同时滚刀的破岩比能耗也增大,增大的幅度比破岩体积大,因此,滚刀的破岩比能耗增大, 如图4(b)所示.2.2 实验验证2.2.1 实验装置采用实验方法可以准确获得特定参数对盘形滚刀破岩特性的影响,更直观地再现不同岩石温度下滚刀掘进参数变化对破岩特性的影响.因此,通过模拟实验对不同岩石温度条件下滚刀破岩过程进行研究,分析相应的破岩特性,与数值模拟结果进行对比以验证其合理性,有助于全面研究盘形滚刀在不同岩石温度下掘进参数变化的破岩特性.为了使实验模拟接近实际施工条件,课题组自主设计了直线式TBM滚刀破岩实验台,如图5所示.实验台主要由油缸、导向机构、导轨、横梁、岩石料仓、液压站、操作台等部分组成.2.2.2 实验方法实验通过直线式TBM滚刀破岩实验台对不同岩石温度下改变掘进参数对破岩过程进行研究,了解滚刀破岩的动态特性.岩石加热装置如图6所示,加热时将其放置于岩石上,使加热板与岩土直接接触,通电后加热棒产生热量通过加热板传递给岩石;铁制上板和铝制下板对加热板的位置固定进行夹紧,阻止热量往铁板传递.依次进行25,50,75,100,125和150 ℃下滚刀的破岩实验;采用三向力传感器记录不同工况条件下滚刀的破岩载荷,转换成电压信号后通过数据采集卡采集数据;实验过程中,观察滚刀破岩现象,记录滚刀破岩载荷、破岩体积、岩石的裂纹扩展规律以及岩渣破碎块度,计算破岩比能耗;最后通过Lab View进行数据分析,分析刀间距及贯入度变化对滚刀破岩特性的影响.2.2.3 实验结果分析1)破岩载荷分析图7所示为当D=4 mm,d=80 mm时,不同岩石温度下滚刀破岩载荷的仿真值与实验值对比曲线.可以看出:随着岩石温度的升高,滚刀的破岩载荷逐渐下降,并呈现一定的阶跃性,这与数值仿真得出的变化规律基本一致.这表明岩石温度是影响盘形滚刀破岩效率的一个关键因素,岩石温度的升高会使岩石内部产生新的微裂纹或使原有微裂纹进一步扩展,改变了岩石的强度及硬度,从而导致破岩载荷的改变.通过图7可以看出仿真值与实验值之间存在一定的误差,这主要是由于数值仿真实验中只对岩石局部进行加热,没有整体加热,且岩石加热后到切削有一定的时间差,使得岩石有一定的热量散失.2)破岩现象分析图8所示为双滚刀共同破岩时,不同工况下岩石破碎情况.可以看出:刀间距为60 mm时,滚刀之间的协同作用较强,滚刀之间的岩石被完全破碎,形成许多小块的岩渣,岩石过度破碎,岩石温度越高,破碎块度越小,如图8(a)和(b)所示;刀间距为80 mm时,滚刀之间的协同作用减弱,刀间岩石裂纹基本贯通,产生大块的岩渣,岩石温度越高,破碎效率越好,如图8(c)和(d)所示;刀间距为100 mm 时,滚刀之间的协同作用较差,温度较低时,滚刀下方出现两条互不交汇的压痕,呈现各自破碎状态,岩石温度越高,压痕越明显,产生大量粉末状岩渣,出现过度破碎现象,能量耗损过大,破岩效率反而降低,如图8(e)和(f)所示.总之岩石温度的升高能增强滚刀之间的协同作用,提高滚刀的破岩效率.根据实验破碎模式的统计结果,可以看出其变化规律与数值模拟所得出的岩石破碎规律基本一致,从而验证了数值仿真的可靠性以及可行性.3)破岩效率分析采用精密电子秤对各工况下滚刀的破岩量进行称量,并进行记录和统计,再根据岩石材料的质量,可以获得滚刀的破岩体积,利用公式(13)计算出各工况下的破岩比能耗.表1所示为各工况下的破岩比能耗实验值与仿真值.可以看出:1)在同一岩石温度下,随着滚刀之间岩石裂纹从没有贯通到刚好贯通,比能耗逐渐减小;随着岩石裂纹从刚好贯通到过渡破碎,比能耗增加,即存在一个最优刀间距破岩比能耗最小,其数值大概在80 mm左右;在相同刀间距和岩石温度下,贯入度越大,破岩效率越高.2)在同一刀间距下,随着温度的升高,岩石裂纹从无贯通到交汇贯通,再到过度破碎,比能耗先减小后上升,说明岩石温度是影响比能耗的一个因素,随着温度的升高,最优刀间距逐渐升高.由于仿真过程中所用的离散元颗粒模型是二维的,被设置为刚体的滚刀不可破坏和磨损,滚刀切削条件是在理想工况条件下进行的,没有受到来自外部无关条件的干扰,而在破岩实验过程中,滚刀会存在磨损,且实验条件如滚刀的加载、岩石的加热以及测试条件等受外界条件干扰的影响,因此仿真值与实验值存在一定的误差,但在允许范围内.1)滚刀的破岩载荷随贯入度的增加呈跃进破碎特性;随着岩石温度的升高,破岩载荷逐渐降低,岩石破碎体积增加.2)滚刀间距的增加,抑制了滚刀之间的协同作用,岩石裂纹不易交汇贯通,滚刀破岩呈现各自破碎模式;随着贯入度的增加,岩石裂纹从不交汇到刚好交汇贯通,最后到形成过度破碎的破碎模式,使得滚刀下方应力之间出现相互作用,减弱了滚刀之间岩石的强度,致使侧向裂纹扩展速度向两侧自由面增加.3)随着岩石温度的升高,岩石的强度以及破裂方式发生改变,岩石更加容易破碎,相同刀间距、贯入度条件下,相对于温度较低时岩石裂纹没有出现贯通,温度较高时已经出现贯通甚至过度贯通状态,滚刀的最优刀间距随岩石温度的升高而升高,随贯入度的增大而变大.总的来说,岩石温度的升高能增强滚刀之间的协同作用,使滚刀的破岩效率增高.这表明岩石温度是影响滚刀破岩特性的重要因素之一,基于岩石温度的滚刀掘进参数对破岩特性影响的研究具有一定工程实践价值.†通讯联系人,E-mail:**********************【相关文献】[1] 王梦恕. 中国铁路、隧道与地下空间发展概况[J]. 隧道建设, 2010, 30(4):351-364.WANG Meng-shu. An overview of development of railways, tunnels and underground works in China[J]. Tunnel Construction, 2010, 30(4):351-364. (In Chinese)[2] WANG L, KANG Y, CAI Z, et al. The energy method to predict disc cutter wear extent for hard rock TBMs [J]. Tunneling and Underground Space Technology, 2012, 28(4): 183-191.[3] VANDER MOLEN I. The shift of the α-β transition of associ ation with the thermal expression granite at high pressure [J]. Tectonophsics, 1981,73: 323-342.[4] ALM O, JAKTLUND L L. The influence of micro crack density on the elastic and fracture mechanical properties of Stripa granite [J]. Physics of the Earth and Planetary Interiors, 1985, 40:17-61.[5] CHEN Y L, NI J, SHAO W, et al. Experimental study on the influence of temperature on the mechanical properties of granite under uni-axial compression and fatigue loading [J].International Journal of Rock Mechanics and Mining Sciences, 2012, 56 (2): 62-69. [6] SMITHIES R H, HOWARD P M, KIRKLAND C L, et al. High-temperature granite magmatism [J]. Journal of Petrology, 2011,52(5):931-958.[7] 张志镇, 高峰, 徐小丽. 花岗岩力学特性的温度效应试验研究[J]. 岩土力学, 2011, 32(8):2346-2352.ZHANG Zhi-zhen, GAO Feng, XU Xiao-li. Experimental study of temperature effect of mechanical properties of granite[J]. Rock and Soil Mechanics, 2011, 32(8): 2346-2352. (In Chinese)[8] 左建平, 谢和平, 刘瑜杰, 等. 不同温度热处理后砂岩三点弯曲的断裂特性[J]. 固体力学学报, 2010,31(2):119-126.ZUO Jian-ping, XIE He-ping, LIU Yu-jie, et al. Investigation on fracture characteristics of sandstone after thermal effects through three bending point experiments[J]. Chinese Journal of Solid Mechanics, 2010,31(2):119-126. (In Chinese)[9] CHO N, MARTIN C D, SEGO D C. A clumped particle model for rock[J]. International Journal of Rock Mechanics and Mining Sciences, 2007, 44(7): 997-1010.[10]李建芳. 岩石温度对盘形滚刀破岩特性影响的研究[D]. 长沙:中南大学机电工程学院, 2014.LI Jian-fang. The research on influence of rock breaking mechanism by disc cutters under the temperature of rock[D]. Changsha: College of Mechanical and Electrical Engineering, Central South University, 2014. (In Chinese)[11]LIU H Y, KOU S Q, LINDQVIST P A. Numerical studies on bit-rock fragmentation mechanisms[J]. International Journal of Geomechanics, 2008, 8(1): 45-67.[12]徐孜军. 盾构刀具破岩特性的数值模拟及实验研究[D]. 长沙:中南大学, 2012: 43-46.XU Zi-jun. Numerical simulation and experimental study of rock breaking mechanism by shield machine cutters[D]. Changsha: Central South University, 2012: 43-46. (In Chinese) [13]赵衡, 曹文贵, 李翔. 考虑应变率影响的单轴受压岩石动态变形过程模拟[J]. 湖南大学学报:自然科学版, 2008, 35(8):14-18.ZHAO Heng, CAO Wen-gui, LI Xiang. Study on the simulation of the dynamic deformation process of uniaxial compressed rock with consideration of strain rate [J]. Journal of Hunan University: Natural Sciences, 2008, 35(8):14-18. (In Chinese)。
TBM滚刀磨损和转速在线监测系统的研究的开题报告
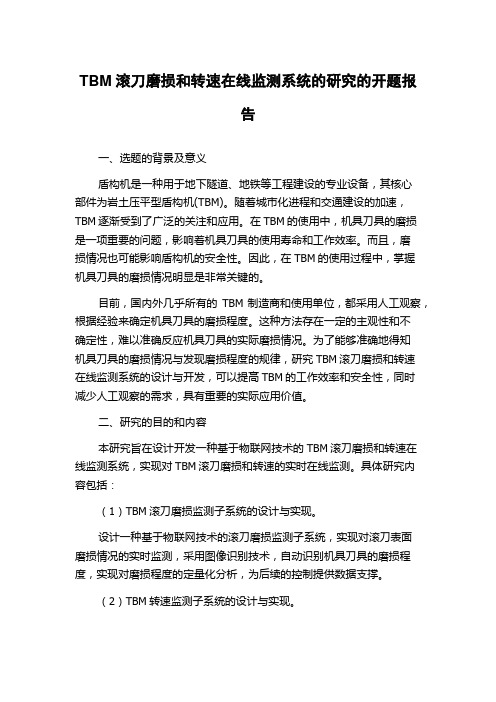
TBM滚刀磨损和转速在线监测系统的研究的开题报告一、选题的背景及意义盾构机是一种用于地下隧道、地铁等工程建设的专业设备,其核心部件为岩土压平型盾构机(TBM)。
随着城市化进程和交通建设的加速,TBM逐渐受到了广泛的关注和应用。
在TBM的使用中,机具刀具的磨损是一项重要的问题,影响着机具刀具的使用寿命和工作效率。
而且,磨损情况也可能影响盾构机的安全性。
因此,在TBM的使用过程中,掌握机具刀具的磨损情况明显是非常关键的。
目前,国内外几乎所有的TBM制造商和使用单位,都采用人工观察,根据经验来确定机具刀具的磨损程度。
这种方法存在一定的主观性和不确定性,难以准确反应机具刀具的实际磨损情况。
为了能够准确地得知机具刀具的磨损情况与发现磨损程度的规律,研究TBM滚刀磨损和转速在线监测系统的设计与开发,可以提高TBM的工作效率和安全性,同时减少人工观察的需求,具有重要的实际应用价值。
二、研究的目的和内容本研究旨在设计开发一种基于物联网技术的TBM滚刀磨损和转速在线监测系统,实现对TBM滚刀磨损和转速的实时在线监测。
具体研究内容包括:(1)TBM滚刀磨损监测子系统的设计与实现。
设计一种基于物联网技术的滚刀磨损监测子系统,实现对滚刀表面磨损情况的实时监测,采用图像识别技术,自动识别机具刀具的磨损程度,实现对磨损程度的定量化分析,为后续的控制提供数据支撑。
(2)TBM转速监测子系统的设计与实现。
设计一种基于物联网技术的滚刀转速监测子系统,实现对TBM滚刀的转速实时监测,采用非接触式传感器,实现对滚刀转速的高精度监测,提高对系统监测结果的准确性和可靠性。
(3)TBM滚刀磨损与转速在控制策略中的应用。
采用模糊神经网络算法,将实时监测的TBM滚刀磨损和转速信息作为输入参数,建立基于前馈控制与反馈控制的TBM控制模型,预测机具刀具的磨损趋势,调整工作模式,减少机具刀具的损耗,延长其使用寿命。
三、研究的方法本研究采用基于物联网技术的TBM滚刀磨损和转速在线监测系统,结合图像识别技术、非接触式传感器技术和模糊神经网络等算法,建立滚刀磨损和转速监测子系统,实现对滚刀表面磨损和转速的实时监测,并将数据作为输入参数,建立基于前馈控制与反馈控制的TBM控制模型,实现对机具刀具的优化控制。
TBM多刀不同切削顺序破岩过程的数值研究

械 的使用 [ . 1 刀具 是 TB 隧道 掘进 机 ) ] M( 的关键 破岩
部件, 而作 为 主要 掘进刀具 的滚刀 , 其破 岩效率 直接
1 模 型 的建 立 及 参 数 的 选 取
TB 在施 工 中常遇 到各种 复杂 的地 质条件 , M 建
立 全 因素模型 是不 现 实 的 , 因此 须 对 实 际 问题 进 行 必 要 的简化. 文 对 破 岩 过 程进 行 适 当简 化 , 定 本 假 TB 在 特定单 一 的地 层 下 掘进 , 略 地 下 水 、 度 M 忽 温
第2 1卷 第 3 期
2 1 年 9月 01
湖 南 工 程 学 院 学 报
V 1 2 . . o . 1 No 3
S p. 0 1 e t 2 1
J u n l fHu a n tt t fEn ie rn o r a n nI siu eo gn e ig o
TBM 多 刀 不 同 切 削 顺 序 破 岩 过 程 的 数 值 研 究
软 件 建 立 了无 围压条 件 下三把 T M 刀具 按 不 同次序 截割 节理不发 育岩石 的仿 真模 型. 此基 础 上设 B 在 计 了一组 数值 试 验 , 功 地模 拟 出 了 TB 刀具在 切割 岩石 时 , 石裂 纹 生成 、 成 M 岩 扩展 和岩 石 破碎 块 形成
的全过 程. 真 结果表 明 : 同时加栽 时所 需的 刀具 临界 应 力 更 大; 仿 不 同时加 栽和 顺 次加 栽 时存 在 两种 不 同的破碎 模 式 , 虽然破碎 区都 由侧 向裂纹 交汇而成 , 但破碎 块 的形状 有所 不 同; 三种加 载方 式下 , 力 的 应
面时必 定存在 着某 一 先 后顺 序 , 同的 滚压 次 序 对 不
TBM盘形滚刀破岩最优贯入度的数值模拟

TBM盘形滚刀破岩最优贯入度的数值模拟程永亮【摘要】In order to study the rock fragmentation efficiency of TBM disc cutters and its optimal penetration, the finite elements theory was used and the extended Drucker-Prager nonlinear constitutive model was adopted as the rock constitutive model. Considering the damage failure criteria which includes deleting function unit, the process of double disc cutters' rock fragmentation was simulated in three-dimensional dynamic way to study the interaction between rocks and cutters. And the rotary cutting test bench was used to perform the experiment of double disc cutters' rock fragmentation to verify the rationality of the simulation results. The results show that at the penetration of 2.0 mm, the cutting forces of two disc cutters are almost the same. At the penetration of 10.0 mm, the cutting force of the first disc cutter is larger than that of the second disc cutter. Under certain stratum, there is an optimal penetration to make the specific energy consumption the lowest. At the penetration of 4.3 mm, rock cracks can interact with each other and complete fragments can be formed. At the same time, the specific energy consumption is the least. When the penetration is less than 4.3 mm, the cracks cannot intersect through the rocks and rock ridge is formed. When the penetration is larger than 4.3 mm, the rock is broken excessively.%为了研究TBM盘形滚刀的破岩效率及其最优贯入度,运用有限元单元理论,采用扩展的Drucker-Prager非线性弹塑性本构模型作为岩石的本构模型,考虑包括单元删除功能的损伤失效准则,对双滚刀切削岩石的过程进行三维动态模拟,研究岩石与刀具相互作用特性.利用回转式切削实验台进行双滚刀破岩实验,验证结果的合理性.研究结果表明:当贯入度为2.0 mm时,2把滚刀的切削力基本相同;当贯入度为10.0 mm 时,前把滚刀的切削力大于后把滚刀的切削力;在特定地层下,存在1个最优贯入度,使得滚刀切削比能耗最低;当贯入度为4.3 mm时,岩石裂纹能相互交汇,形成完整的碎片,切削比能耗最小;当贯入度小于4.3 mm时,岩石不能产生贯穿裂纹,形成岩脊;当贯入度大于4.3 mm时,岩石过度破碎.【期刊名称】《中南大学学报(自然科学版)》【年(卷),期】2017(048)004【总页数】8页(P936-943)【关键词】TBM;盘形滚刀;扩展的Drucker-Prager非线性弹塑性本构模型;贯入度【作者】程永亮【作者单位】中南大学机电工程学院,湖南长沙,410083;中国铁建重工集团有限公司,湖南长沙,410100【正文语种】中文【中图分类】TU45;TP391.9全断面岩石掘进机(tunnel boring machine, TBM)是目前性能最好的隧道掘进专业工程机械,广泛应用于地铁、轨道交通、市政、水利水电、隧道等地下工程建设[1−3]。
TBM掘进机盘型滚刀的研制
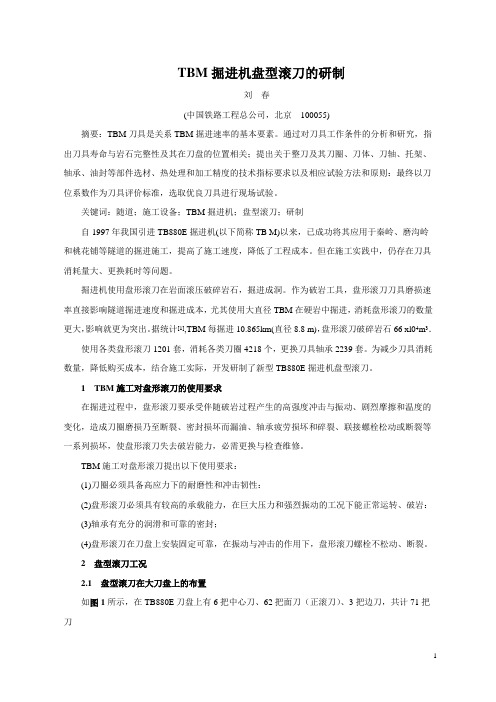
TBM掘进机盘型滚刀的研制刘春(中国铁路工程总公司,北京100055)摘要:TBM刀具是关系TBM掘进速率的基本要素。
通过对刀具工作条件的分析和研究,指出刀具寿命与岩石完整性及其在刀盘的位置相关;提出关于整刀及其刀圈、刀体、刀轴、托架、轴承、油封等部件选材、热处理和加工精度的技术指标要求以及相应试验方法和原则:最终以刀位系数作为刀具评价标准,选取优良刀具进行现场试验。
关键词:随道;施工设备;TBM掘进机;盘型滚刀;研制自1997年我国引进TB880E掘进机(以下简称TB M)以来,已成功将其应用于秦岭、磨沟岭和桃花铺等隧道的掘进施工,提高了施工速度,降低了工程成本。
但在施工实践中,仍存在刀具消耗量大、更换耗时等问题。
掘进机使用盘形滚刀在岩面滚压破碎岩石,掘进成洞。
作为破岩工具,盘形滚刀刀具磨损速率直接影响隧道掘进速度和掘进成本,尤其使用大直径TBM在硬岩中掘进,消耗盘形滚刀的数量更大,影响就更为突出。
据统计[1],TBM每掘进10.865km(直径8.8 m),盘形滚刀破碎岩石66 xl04m3.使用各类盘形滚刀1201套,消耗各类刀圈4218个,更换刀具轴承2239套。
为减少刀具消耗数量,降低购买成本,结合施工实际,开发研制了新型TB880E掘进机盘型滚刀。
1 TBM施工对盘形滚刀的使用要求在掘进过程中,盘形滚刀要承受伴随破岩过程产生的高强度冲击与振动、剧烈摩擦和温度的变化,造成刀圈磨损乃至断裂、密封损坏而漏油、轴承疲劳损坏和碎裂、联接螺栓松动或断裂等一系列损坏,使盘形滚刀失去破岩能力,必需更换与检查维修。
TBM施工对盘形滚刀提出以下使用要求:(1)刀圈必须具备高应力下的耐磨性和冲击韧性:(2)盘形滚刀必须具有较高的承载能力,在巨大压力和强烈振动的工况下能正常运转、破岩:(3)轴承有充分的润滑和可靠的密封;(4)盘形滚刀在刀盘上安装固定可靠,在振动与冲击的作用下,盘形滚刀螺栓不松动、断裂。
2 盘型滚刀工况2.1 盘型滚刀在大刀盘上的布置如图1所示,在TB880E刀盘上有6把中心刀、62把面刀(正滚刀)、3把边刀,共计71把刀进行掘进,另外还有2把扩孔刀,作为更换边刀时扩孔之用。
TBM盘形滚刀磨损预测模型
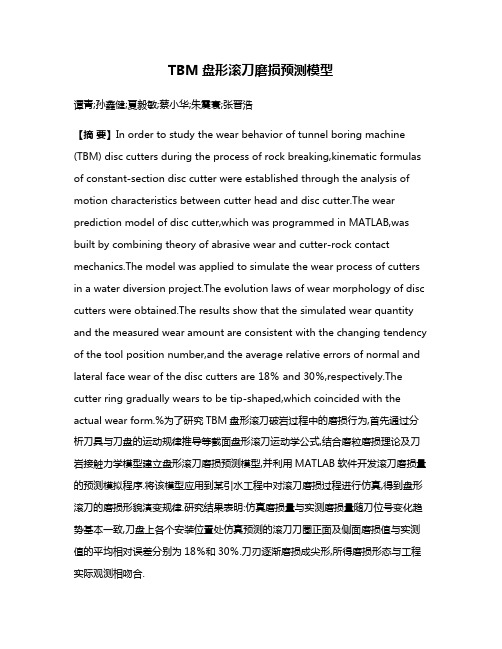
TBM盘形滚刀磨损预测模型谭青;孙鑫健;夏毅敏;蔡小华;朱震寰;张晋浩【摘要】In order to study the wear behavior of tunnel boring machine (TBM) disc cutters during the process of rock breaking,kinematic formulas of constant-section disc cutter were established through the analysis of motion characteristics between cutter head and disc cutter.The wear prediction model of disc cutter,which was programmed in MATLAB,was built by combining theory of abrasive wear and cutter-rock contact mechanics.The model was applied to simulate the wear process of cutters in a water diversion project.The evolution laws of wear morphology of disc cutters were obtained.The results show that the simulated wear quantity and the measured wear amount are consistent with the changing tendency of the tool position number,and the average relative errors of normal and lateral face wear of the disc cutters are 18% and 30%,respectively.The cutter ring gradually wears to be tip-shaped,which coincided with the actual wear form.%为了研究TBM盘形滚刀破岩过程中的磨损行为,首先通过分析刀具与刀盘的运动规律推导等截面盘形滚刀运动学公式,结合磨粒磨损理论及刀岩接触力学模型建立盘形滚刀磨损预测模型,并利用MATLAB软件开发滚刀磨损量的预测模拟程序.将该模型应用到某引水工程中对滚刀磨损过程进行仿真,得到盘形滚刀的磨损形貌演变规律.研究结果表明:仿真磨损量与实测磨损量随刀位号变化趋势基本一致,刀盘上各个安装位置处仿真预测的滚刀刀圈正面及侧面磨损值与实测值的平均相对误差分别为18%和30%.刀刃逐渐磨损成尖形,所得磨损形态与工程实际观测相吻合.【期刊名称】《中南大学学报(自然科学版)》【年(卷),期】2017(048)001【总页数】7页(P54-60)【关键词】TBM;盘形滚刀;磨损预测;数值仿真【作者】谭青;孙鑫健;夏毅敏;蔡小华;朱震寰;张晋浩【作者单位】中南大学高性能复杂制造国家重点实验室,湖南长沙,410083;中南大学机电工程学院,湖南长沙,410083;中南大学高性能复杂制造国家重点实验室,湖南长沙,410083;中南大学机电工程学院,湖南长沙,410083;中南大学高性能复杂制造国家重点实验室,湖南长沙,410083;中南大学机电工程学院,湖南长沙,410083;中南大学高性能复杂制造国家重点实验室,湖南长沙,410083;中南大学机电工程学院,湖南长沙,410083;中南大学高性能复杂制造国家重点实验室,湖南长沙,410083;中南大学高性能复杂制造国家重点实验室,湖南长沙,410083【正文语种】中文【中图分类】TH117.1全断面岩石隧道掘进机(TBM)目前广泛应用于岩石地层的隧道开挖,盘形滚刀作为TBM破岩的核心部件,在开挖过程中需要承受极大的推进力以及与岩石之间的摩擦力,极易产生严重磨损[1]。
斜井TBM新型与普通刀具的磨损效果对比研究
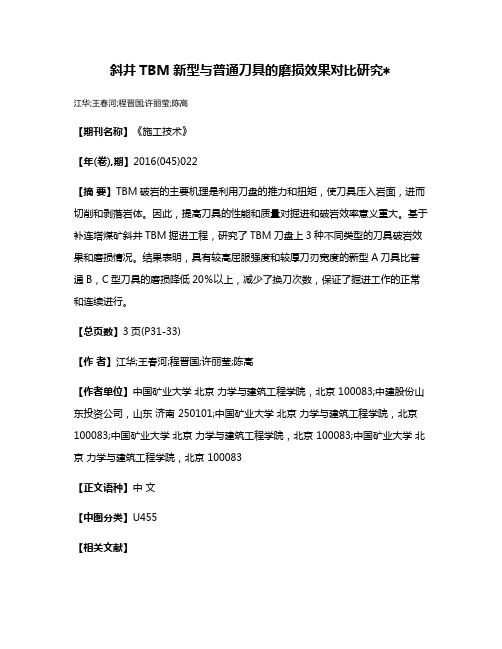
斜井TBM新型与普通刀具的磨损效果对比研究∗
江华;王春河;程晋国;许丽莹;陈高
【期刊名称】《施工技术》
【年(卷),期】2016(045)022
【摘要】TBM破岩的主要机理是利用刀盘的推力和扭矩,使刀具压入岩面,进而切削和剥落岩体。
因此,提高刀具的性能和质量对掘进和破岩效率意义重大。
基于补连塔煤矿斜井TBM掘进工程,研究了TBM刀盘上3种不同类型的刀具破岩效果和磨损情况。
结果表明,具有较高屈服强度和较厚刀刃宽度的新型A刀具比普通B,C型刀具的磨损降低20%以上,减少了换刀次数,保证了掘进工作的正常和连续进行。
【总页数】3页(P31-33)
【作者】江华;王春河;程晋国;许丽莹;陈高
【作者单位】中国矿业大学北京力学与建筑工程学院,北京 100083;中建股份山东投资公司,山东济南 250101;中国矿业大学北京力学与建筑工程学院,北京100083;中国矿业大学北京力学与建筑工程学院,北京 100083;中国矿业大学北京力学与建筑工程学院,北京 100083
【正文语种】中文
【中图分类】U455
【相关文献】
1.一种新型TBM刀具磨损检测技术 [J], 李宏波;孙振川;周建军;张宏伟;韩雪峰;喻伟
2.滚刀直径对引汉济渭秦岭隧洞TBM刀具磨损影响实验研究 [J], 蔡昱;祝和意
3.TBM隧道围岩力学参数对凿碎比功及刀具磨损值影响分析 [J], 王亚暐; 吴光
4.大型输水通道硬岩地层双护盾TBM掘进模式与刀具磨损分析 [J], 王付利
5.斜井TBM刀具磨损更换预测方法研究 [J], 刘颖超;江玉生;程晋国;嵇长民
因版权原因,仅展示原文概要,查看原文内容请购买。
TBM掘进刀具磨损实时监测技术及刀盘振动监测分析
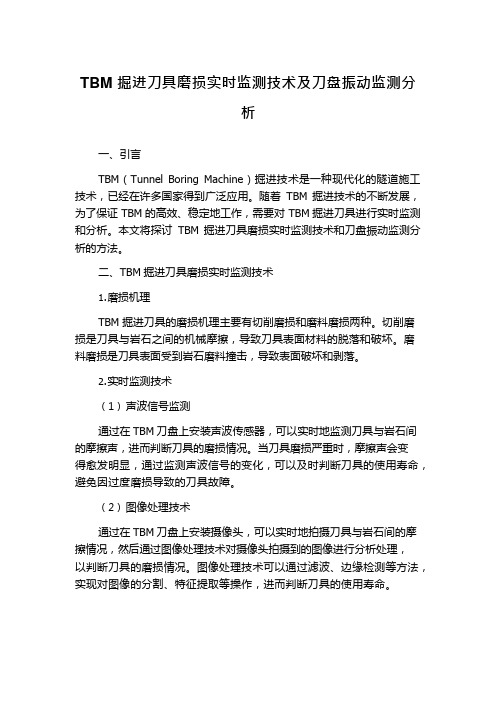
TBM 掘进刀具磨损实时监测技术及刀盘振动监测分析一、引言TBM(Tunnel Boring Machine)掘进技术是一种现代化的隧道施工技术,已经在许多国家得到广泛应用。
随着TBM 掘进技术的不断发展,为了保证TBM 的高效、稳定地工作,需要对TBM 掘进刀具进行实时监测和分析。
本文将探讨TBM 掘进刀具磨损实时监测技术和刀盘振动监测分析的方法。
二、TBM 掘进刀具磨损实时监测技术1.磨损机理TBM 掘进刀具的磨损机理主要有切削磨损和磨料磨损两种。
切削磨损是刀具与岩石之间的机械摩擦,导致刀具表面材料的脱落和破坏。
磨料磨损是刀具表面受到岩石磨料撞击,导致表面破坏和剥落。
2.实时监测技术(1)声波信号监测通过在TBM 刀盘上安装声波传感器,可以实时地监测刀具与岩石间的摩擦声,进而判断刀具的磨损情况。
当刀具磨损严重时,摩擦声会变得愈发明显,通过监测声波信号的变化,可以及时判断刀具的使用寿命,避免因过度磨损导致的刀具故障。
(2)图像处理技术通过在TBM 刀盘上安装摄像头,可以实时地拍摄刀具与岩石间的摩擦情况,然后通过图像处理技术对摄像头拍摄到的图像进行分析处理,以判断刀具的磨损情况。
图像处理技术可以通过滤波、边缘检测等方法,实现对图像的分割、特征提取等操作,进而判断刀具的使用寿命。
(3)振动信号监测通过在TBM 刀盘上安装振动传感器,可以实时地监测刀盘的振动情况,进而判断刀具的磨损情况。
当刀具磨损严重时,切削力或岩石磨料对刀具的撞击会导致刀盘的振动增大,通过监测振动信号的变化,可以及时判断刀具的使用寿命。
三、刀盘振动监测分析刀盘振动是TBM 掘进过程中的一个重要问题,它不仅会对TBM 掘进过程产生影响,还会对TBM 设备产生破坏。
因此,对TBM 刀盘的振动进行监测和分析具有重要的意义。
1.振动分析方法(1)时域分析法时域分析法是一种直接观察振动信号波形的方法。
通过对TBM 刀盘上振动传感器采集的振动信号进行时域分析,可以计算出振动信号的振幅、周期等参数,进而判断刀盘的振动状态。
基于流固耦合作用下盘形滚刀优化设计方法初探
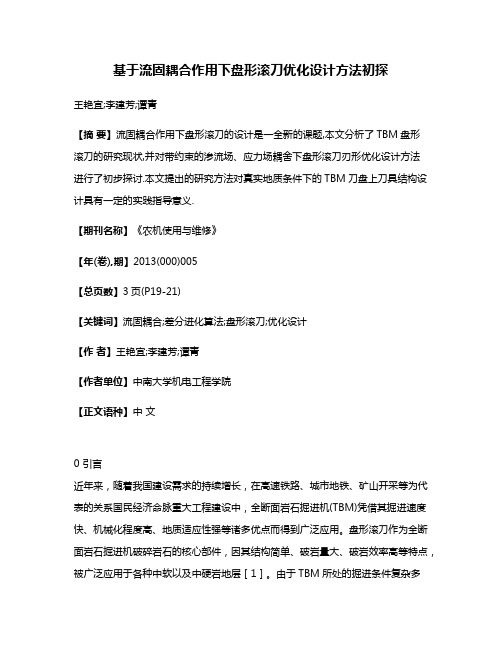
基于流固耦合作用下盘形滚刀优化设计方法初探王艳宜;李建芳;谭青【摘要】流固耦合作用下盘形滚刀的设计是一全新的课题,本文分析了TBM盘形滚刀的研究现状,并对带约束的渗流场、应力场耦舍下盘形滚刀刃形优化设计方法进行了初步探讨.本文提出的研究方法对真实地质条件下的TBM刀盘上刀具结构设计具有一定的实践指导意义.【期刊名称】《农机使用与维修》【年(卷),期】2013(000)005【总页数】3页(P19-21)【关键词】流固耦合;差分进化算法;盘形滚刀;优化设计【作者】王艳宜;李建芳;谭青【作者单位】中南大学机电工程学院【正文语种】中文0 引言近年来,随着我国建设需求的持续增长,在高速铁路、城市地铁、矿山开采等为代表的关系国民经济命脉重大工程建设中,全断面岩石掘进机(TBM)凭借其掘进速度快、机械化程度高、地质适应性强等诸多优点而得到广泛应用。
盘形滚刀作为全断面岩石掘进机破碎岩石的核心部件,因其结构简单、破岩量大、破岩效率高等特点,被广泛应用于各种中软以及中硬岩地层[1]。
由于TBM所处的掘进条件复杂多变,掘进地层受到自重应力、构造应力、岩石遇水后物理化学变化引起的膨胀应力等综合作用,这些因素对盘形滚刀的设计产生很大的影响。
未考虑地质流固耦合效应,设计出来的盘形滚刀表现出很差的地质适应性。
据统计,直径8.8 m的TBM 每掘进10.865 km,使用各类盘形滚刀1201套,消耗量比较大[2]。
因此,研究渗流场、应力场耦合作用下盘形滚刀的优化设计,对减少滚刀的消耗数量乃至提高TBM的掘进效率具有一定的工程实际意义。
1 盘形滚刀设计基础盘形滚刀一般由刀圈、刀体、轴承、轴和密封装置组成。
其中刀圈在破岩过程中直接与岩石接触,刀圈的设计直接影响滚刀破岩性能和滚刀寿命,如图1所示。
图1 盘形滚刀装配图盘形滚刀主要有三种类型的刀圈截面:尖刃楔形截面、弧刃楔形截面和近似常截面,如图2所示,其主要几何参数有:滚刀刀刃宽B、过渡圆弧半径r和刀刃角θ,这些参数对破岩力、破岩效率、能量消耗和滚刀寿命等有较大的影响。
TBM掘进刀具磨损实时监测技术及刀盘振动监测分析
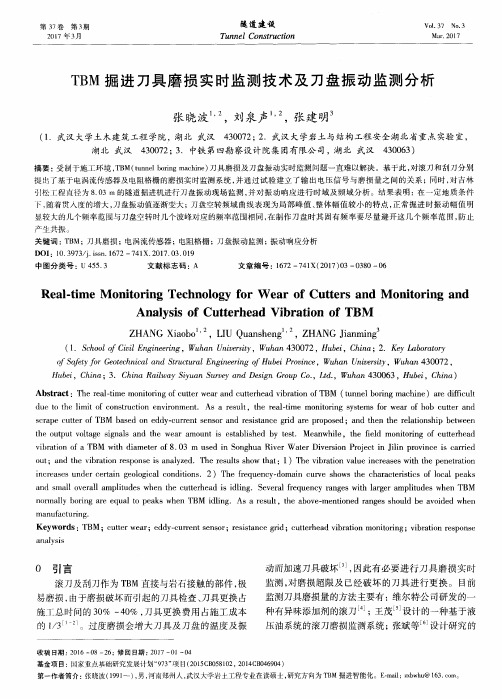
篷 奄建 谨
Tu n ne l Co n s t r u c t i o n
V0 J . 3 7 No . 3 Ma r . 2 01 7
T B M 掘 进 刀具 磨 损 实 时监 测 技 术及 刀 盘 振 动 监 测 分 析
显较 大的几个频率范围与刀盘空转时几个波峰对应 的频率范 围相 同 , 在制作 刀盘 时其 固有频 率要尽量 避开 这几个频 率范 围 , 防止
产 生 共振 。
关键词 : T B M; 刀具磨损 ;电涡流传感 器 ;电阻格栅 ;刀盘振动监测 ; 振动 响应分析
D OI :1 0 . 3 9 7 3 / j . i s s n . 1 6 7 2— 7 4 1 X . 2 0 1 7 . 0 3 . 0 1 9
d u e t o t h e l i mi t o f c o ns t r uc t i o n e n v i r o n me n t .As a r e s u l t ,t h e r e a l — t i me mo n i t o r i n g s y s t e ms f o r we a r o f ho b c u t t e r a n d s c r a p e c u t t e r o f T BM ba s e d o n e d d y - c u r r e n t s e ns o r a n d r e s i s t a n c e g r i d a r e p r o p o s e d;a n d t h e n t h e r e l a t i o ns h i p be t we e n
摘要 : 受制于施工环境 , T B M( t u n n e l b o r i n g m a c h i n e ) 刀具 磨损及刀盘振动实时监测问题一直难 以解决 。基于此 , 对 滚刀和刮刀分别
TBM盘形滚刀的质量控制及其检测维修技术

TBM盘形滚刀的质量控制及其检测维修技术摘要:西康铁路秦岭隧道出口及西南铁路桃花铺1号隧道TBM施工中,在消化引进技术的基础上,对盘形滚刀的损坏规律进行了深入的分析,对如何提高盘形滚刀的寿命、降低刀具消耗进行了深入的研究,并取得了很好的成果,刀具故障率降低,刀具使用寿命得以提高,因而提高了掘进速度,降低了掘进成本,形成了技术经济性能优良的盘形滚刀检测维修技术,可供TBM施工参考。
关键词:隧道掘进机刀具盘形滚刀检测维修TBM(隧道掘进机)作为长大隧道施工最有效的大型机械,掘进时使用在刀盘上安装的盘形滚刀刀刃楔入岩体破碎岩石,刀盘转动带动滚刀在掌子面上滚动进行连续破岩,刀盘被向前推进,滚刀破岩掘进形成洞身。
安装在TBM刀盘上的盘形滚刀是TBM的专有工具,其技术性能的优劣是扩大TBM施工适用范围和降低施工造价的关键技术之一,国外各著名TBM生产厂家对刀具都进行了长期的研究,不断改进TBM 刀具的性能,使产品具有竞争力。
但刀具性能必须在施工中正确使用才能充分发挥。
施工中要对使用的刀具进行严格检测并及时维修,使上机掘进的刀具性能可靠,减少掘进中刀具故障,以提高机器的利用率,从而提高掘进速度;正确使用刀具还必须包括正确更换刀具及其备件,从而降低刀具消耗。
正确使用刀具不仅可提高掘进速度还可从以上两个方面来降低隧道掘进成本。
尤其在硬岩中掘进其重要性更为明显。
西康铁路秦岭隧道出口及西南铁路桃花铺1号隧道TBM施工中,在掌握消化引进技术的基础上,对TBM施工中的刀具技术进行了深入的研究,形成了一套符合我国施工条件、可操作性强的检测维修技术,并取得了很好的技术经济效果。
笔者参加这两条隧道施工的刀具使用与研究,本文是对TB880E型掘进机的17"盘形滚刀检测和维修技术的总结,可供借鉴。
1TBM施工对刀具整备的技术要求TBM施工中的刀盘检查、刀具更换、刀具维修等一系列为使刀盘上的刀具处于良好状态的工作统称为刀具整备,是TBM施工作业的重要组成部分,对隧道施工进度与造价有直接影响,且专业性强,是TBM 施工技术的重点之一。
TBM盘形滚刀切削力学模型分析
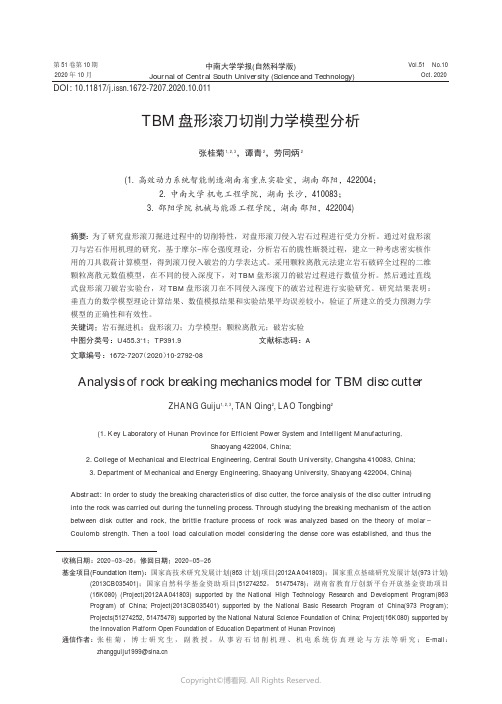
第51卷第10期2020年10月中南大学学报(自然科学版)Journal of Central South University(Science and Technology)V ol.51No.10Oct.2020 TBM盘形滚刀切削力学模型分析张桂菊1,2,3,谭青2,劳同炳2(1.高效动力系统智能制造湖南省重点实验室,湖南邵阳,422004;2.中南大学机电工程学院,湖南长沙,410083;3.邵阳学院机械与能源工程学院,湖南邵阳,422004)摘要:为了研究盘形滚刀掘进过程中的切削特性,对盘形滚刀侵入岩石过程进行受力分析。
通过对盘形滚刀与岩石作用机理的研究,基于摩尔−库仑强度理论,分析岩石的脆性断裂过程,建立一种考虑密实核作用的刀具载荷计算模型,得到滚刀侵入破岩的力学表达式。
采用颗粒离散元法建立岩石破碎全过程的二维颗粒离散元数值模型,在不同的侵入深度下,对TBM盘形滚刀的破岩过程进行数值分析。
然后通过直线式盘形滚刀破岩实验台,对TBM盘形滚刀在不同侵入深度下的破岩过程进行实验研究。
研究结果表明:垂直力的数学模型理论计算结果、数值模拟结果和实验结果平均误差较小,验证了所建立的受力预测力学模型的正确性和有效性。
关键词:岩石掘进机;盘形滚刀;力学模型;颗粒离散元;破岩实验中图分类号:U455.3+1;TP391.9文献标志码:A文章编号:1672-7207(2020)10-2792-08Analysis of rock breaking mechanics model for TBM disc cutterZHANG Guiju1,2,3,TAN Qing2,LAO Tongbing2(1.Key Laboratory of Hunan Province for Efficient Power System and Intelligent Manufacturing,Shaoyang422004,China;2.College of Mechanical and Electrical Engineering,Central South University,Changsha410083,China;3.Department of Mechanical and Energy Engineering,Shaoyang University,Shaoyang422004,China)Abstract:In order to study the breaking characteristics of disc cutter,the force analysis of the disc cutter intruding into the rock was carried out during the tunneling process.Through studying the breaking mechanism of the action between disk cutter and rock,the brittle fracture process of rock was analyzed based on the theory of molar−Coulomb strength.Then a tool load calculation model considering the dense core was established,and thus the DOI:10.11817/j.issn.1672-7207.2020.10.011收稿日期:2020−03−26;修回日期:2020−05−26基金项目(Foundation item):国家高技术研究发展计划(863计划)项目(2012AA041803);国家重点基础研究发展计划(973计划) (2013CB035401);国家自然科学基金资助项目(51274252,51475478);湖南省教育厅创新平台开放基金资助项目(16K080)(Project(2012AA041803)supported by the National High Technology Research and Development Program(863Program)of China;Project(2013CB035401)supported by the National Basic Research Program of China(973Program);Projects(51274252,51475478)supported by the National Natural Science Foundation of China;Project(16K080)supported bythe Innovation Platform Open Foundation of Education Department of Hunan Province)通信作者:张桂菊,博士研究生,副教授,从事岩石切削机理、机电系统仿真理论与方法等研究;E-mail:**********************第10期张桂菊,等:TBM盘形滚刀切削力学模型分析mechanical expression of disc cutter intruding into hard rock was obtained.The two-dimensional numerical model of particle discrete element in the whole process of rock breaking was established by using the particle flow code (PFC)method.At different invasion depths,the process of rock breaking of tunnel boring machine(TBM)disc cutter was numerically analyzed.Then,the rock breaking process of TBM disc cutter at different invasion depths was studied by using the straight-line disc cutter rock breaking experimental platform.The results show that the average errors of vertical force obtained from mathematical models,numerical simulations and experiments are small,which verifies the correctness and validity of the established mechanical model of stress prediction.Key words:tunnel boring machine(TBM);disc cutter;mechanical model;particle flow code(PFC);rock breaking experiment岩石掘进机(tunnel boring machine,TBM)是地下空间隧道掘进的主要工具,在其施工过程中,作为掘进机主要的刀具之一的盘形滚刀,直接参与掘进破岩的工作[1−2]。
基于脉冲涡流的tbm盘形滚刀磨损检测方法
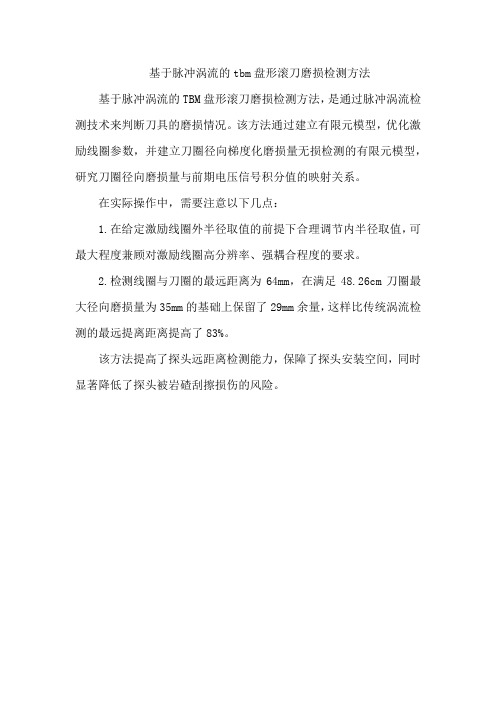
基于脉冲涡流的tbm盘形滚刀磨损检测方法基于脉冲涡流的TBM盘形滚刀磨损检测方法,是通过脉冲涡流检测技术来判断刀具的磨损情况。
该方法通过建立有限元模型,优化激励线圈参数,并建立刀圈径向梯度化磨损量无损检测的有限元模型,研究刀圈径向磨损量与前期电压信号积分值的映射关系。
在实际操作中,需要注意以下几点:
1.在给定激励线圈外半径取值的前提下合理调节内半径取值,可最大程度兼顾对激励线圈高分辨率、强耦合程度的要求。
2.检测线圈与刀圈的最远距离为64mm,在满足48.26cm刀圈最大径向磨损量为35mm的基础上保留了29mm余量,这样比传统涡流检测的最远提离距离提高了83%。
该方法提高了探头远距离检测能力,保障了探头安装空间,同时显著降低了探头被岩碴刮擦损伤的风险。
正、偏楔形盘形滚刀破岩作业载荷对比研究
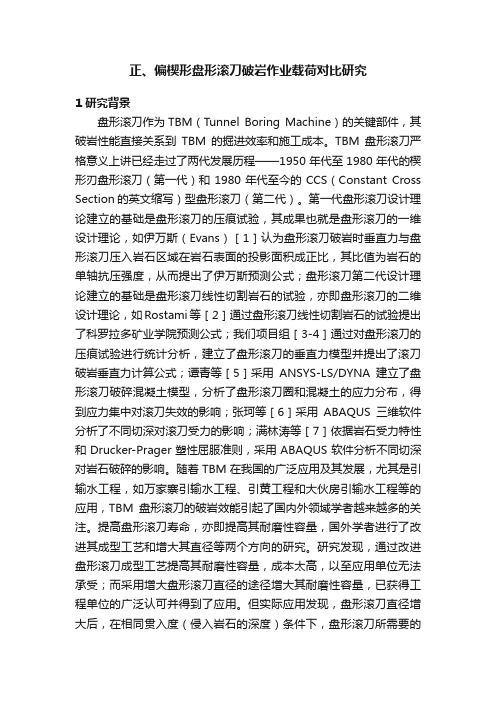
正、偏楔形盘形滚刀破岩作业载荷对比研究1 研究背景盘形滚刀作为TBM(Tunnel Boring Machine)的关键部件,其破岩性能直接关系到TBM的掘进效率和施工成本。
TBM盘形滚刀严格意义上讲已经走过了两代发展历程——1950年代至1980年代的楔形刃盘形滚刀(第一代)和1980年代至今的CCS(Constant Cross Section的英文缩写)型盘形滚刀(第二代)。
第一代盘形滚刀设计理论建立的基础是盘形滚刀的压痕试验,其成果也就是盘形滚刀的一维设计理论,如伊万斯(Evans)[1]认为盘形滚刀破岩时垂直力与盘形滚刀压入岩石区域在岩石表面的投影面积成正比,其比值为岩石的单轴抗压强度,从而提出了伊万斯预测公式;盘形滚刀第二代设计理论建立的基础是盘形滚刀线性切割岩石的试验,亦即盘形滚刀的二维设计理论,如Rostami等[2]通过盘形滚刀线性切割岩石的试验提出了科罗拉多矿业学院预测公式;我们项目组[3-4]通过对盘形滚刀的压痕试验进行统计分析,建立了盘形滚刀的垂直力模型并提出了滚刀破岩垂直力计算公式;谭青等[5]采用ANSYS-LS/DYNA建立了盘形滚刀破碎混凝土模型,分析了盘形滚刀圈和混凝土的应力分布,得到应力集中对滚刀失效的影响;张珂等[6]采用ABAQUS三维软件分析了不同切深对滚刀受力的影响;满林涛等[7]依据岩石受力特性和Drucker-Prager塑性屈服准则,采用ABAQUS软件分析不同切深对岩石破碎的影响。
随着TBM在我国的广泛应用及其发展,尤其是引输水工程,如万家寨引输水工程、引黄工程和大伙房引输水工程等的应用,TBM盘形滚刀的破岩效能引起了国内外领域学者越来越多的关注。
提高盘形滚刀寿命,亦即提高其耐磨性容量,国外学者进行了改进其成型工艺和增大其直径等两个方向的研究。
研究发现,通过改进盘形滚刀成型工艺提高其耐磨性容量,成本太高,以至应用单位无法承受;而采用增大盘形滚刀直径的途径增大其耐磨性容量,已获得工程单位的广泛认可并得到了应用。
- 1、下载文档前请自行甄别文档内容的完整性,平台不提供额外的编辑、内容补充、找答案等附加服务。
- 2、"仅部分预览"的文档,不可在线预览部分如存在完整性等问题,可反馈申请退款(可完整预览的文档不适用该条件!)。
- 3、如文档侵犯您的权益,请联系客服反馈,我们会尽快为您处理(人工客服工作时间:9:00-18:30)。
石表面,与岩石表面之间没有相对滑动作用,而 vdt 与岩石表面相切,因此,滚刀上点 A 与岩石的相对滑 动速度 vdt 为
式中:T 为刀刃宽度。 1.2 盘形滚刀磨损寿命预估 图 2 所示为等截面滚刀刀圈断面。为便于研究, 不考虑过渡圆弧。设刀刃半角为 ,滚刀的初始半径 为 r,初始刀刃宽为 T,以刀圈半径减少 r ( r 为一 极小值 ) 为一磨损步长,则第 i−1 步长时刀圈半径为 ri 1 ,刀刃宽度为 Ti 1 ;第 i 步次时刀圈半径为 ri,刀 刃宽度为 Ti;ri=r−i r ,Ti T 2ir tan 。刀圈磨损 体积 Qi 为
[3] [2]
速度。 由式 (2) 可知磨损速率与载荷和摩擦副之间的相 对滑动速度的乘积成正比,因此,盘形滚刀刀刃上某 点处的磨损速率 (以下称为点磨损速率 )与该点处的接 触力 p 和该点与岩石的相对滑动速度 v 的乘积成正比。 点磨损速率可由下式计算:
d QHale Waihona Puke k pc dt Hc(3)
式中:Qd 为刀刃上某一点的磨损量;p 为接触力;Hc 为滚刀材料表面硬度。科罗拉多矿冶研究院在大量的 岩石切割试验和工程分析基础上提出了考虑岩石力学 性质、滚刀几何参数等的等截面盘形滚刀刀圈连续切 削岩石时接触力 CSM(Colorado school of mincs)模型[17]:
p p 1
其中:
(4)
s 2 c t p C 3 rT r h arccos r
(5)
p 为滚刀正下方的破碎区基本压力; 表示刀刃上某
点以及破岩最大切深点与滚刀中心连线的夹角; 为 滚刀与岩石的接触角; 为刀尖压力分布系数,对于 等截面滚刀, =0~0.2,一般来说,滚刀锋利时取值 较大,一般取 0.1; c 为岩石抗压强度; t 为岩石抗 拉强度;s 为刀尖间距;r 为滚刀半径;T 为滚刀刀刃 宽度;h 为贯入度。设 TBM 掘进时刀盘转速为 0 , 盘形滚刀安装半径为 R,刀径为 r,则盘形滚刀转速 0 R / r 。盘形滚刀的运动实际上是盘形滚刀绕自 身转轴的转动和绕刀盘的旋转轴线旋转的两定轴运动 合成,因此,考虑滚刀运动速度时,一方面,要考虑 滚刀沿切削螺旋线对岩石的滚压运动,另一方面,要 考虑滚刀绕刀盘中心线转动时的侧滑运动,滚压运动 与侧滑运动相互垂直。先考虑对岩石的滚压运动。滚 刀沿切削螺旋线的滚压运动又可分为 2 个运动,如图
Analysis of wear rate of TBM disc cutter
TAN Qing1, 2, XIE Lüjian1, 2, XIA Yimin1, 2, ZHU Zhenhuan1, SUN Xinjian1, WANG Yanyi3
(1. School of Mechanical and Electrical Engineering, Central South University, Changsha 410083, China; 2. State Key Laboratory of High Performance Complex Manufacturing, Central South University, Changsha 410083, China; 3. Department of Engineering, Changde Vocational and Technical College, Changde 415000, China) Abstract: The wear rate of tunnel boring machine (TBM) disc cutter based on contact pressure and relative slide velocity was built. Then the effect of penetration, cutter radius change and installation radius on disc cutter wear rate was researched, and the prediction method of disc cutter’s lifetime was studied. The conclusion was proved by engineering practice. The results show that the point with the maximum wear rate is between the deepest penetration point and breaking forward point. The wear rate of disc cutter increases almost linearly with the installation radius, and it increases with the increase of penetration and the decrease of disc cutter radius, and penetration is the most influential factor of wear rate of disc cutter. Key words: disc cutter; wear rate; penetration; radius of disc cutter; installation radius; lifetime
1 所示。 1) 滚刀在刀盘推动下被动转动。 滚刀在掌子面平
1
盘形滚刀的磨损速率模型
1.1 盘形滚刀磨损速率理论模型 盘形滚刀刀圈正常磨损是刀具消耗的主要形 式[15],而磨粒磨损是滚刀正常磨损的主要形式。影响 磨料磨损的主要因素有作用于接触表面的载荷、相对 滑动距离、被磨损表面的表面性能。磨料磨损量可由 下式求得[16]: Q kWL H (1)
盘形滚刀是隧道掘进机 (tunnel boring machine, TBM)执行开挖工作的核心部件, 由于需要承受很大的
收稿日期:2014−04−10;修回日期:2014−06−22
推进力和与岩石之间的摩擦力, 极易产生严重磨损[1]。 经统计,在秦岭隧道掘进过程中,刀具消耗的成本占
基金项目(Foundation item):国家重点基础研究发展计划 (973 计划)项目(2013CB035401);国家自然科学基金资助项目 (51274252);湖南省战略新 兴 产 业 重 大 科 技 攻 关 项 目 (2012GK4068) (Project(2013CB035401) supported by the National Basic Research Development Program(973 Program) of China; Project(51274252) supported by the National Natural Science Foundation of China; Project(2012GK4068) supported by Strategic Emerging Industries of Science and Technology Key Project of Hunan Province) 通信作者:谭青,博士,教授,从事机械设计方法与理论、机械电子等教学与科研工作;E-mail: jds-share@
图1
滚刀与岩石相对滑动速度
Fig. 1 Relative sliding velocity between rock and disc cutter
2 h 0 2 R sin 2 sin r sin d 2 2π
2
(12)
将式(1)两边对时间 t 求导得
面以最大切深点 P 为速度瞬心滚动[16],滚刀刀刃上点
dQ k Wv dt H
(2)
A 的速度为 vd l
式中:Q 为磨损量; k 为量纲 1 的磨损系数,对于磨 料磨损一般取 10 ~10
−1 −6[16]
其中: 为滚刀转速; l 为 A 点到速度瞬心的距离,
l= AP =2rsin / 2 。将 vd 分解为沿半径 OA 方向的 vdr 和垂直于 OA 方向 vdt 共 2 个速度。其中 vdt 垂直于岩
;W 为作用载荷;L 为磨损
行程; H 为材料表面硬度; v 为摩擦副的相对滑动
第3期
谭青,等:TBM 盘形滚刀磨损速率研究
845
滚刀单位时间内的磨损量即滚刀磨损速率可由点 磨损速率对滚刀与岩石的接触面积分获得:
TBM 盘形滚刀磨损速率研究
谭青 1, 2,谢吕坚 1, 2,夏毅敏 1, 2,朱震寰 1,孙鑫键 1,王艳宜 3 (1. 中南大学 机电工程学院,湖南 长沙,410083; 2. 中南大学 高性能复杂制造国家重点实验室,湖南 长沙,410083; 3. 常德职业技术学院 工程系,湖南 常德,415000)
第 46 卷第 3 期 2015 年 3 月
中南大学学报(自然科学版) Journal of Central South University (Science and Technology)
Vol.46 No.3 Mar. 2015