滚刀工作原理分析
滚刀工作原理分析

滚刀工作原理分析摘要:滚刀是一种常见的切削工具,常用于金属加工和木材加工等行业。
本文将对滚刀的工作原理进行分析,重点介绍滚刀的结构和切削原理,并对其优点和应用进行讨论。
通过对滚刀工作原理的深入了解,可以更好地理解和应用滚刀,提高工作效率和加工质量。
一、滚刀的结构滚刀由刀杆、刀盘和切削刃组成。
其中,刀杆是滚刀的支撑结构,可以连接到加工设备上;刀盘是滚刀的主体部分,上面装有切削刃;切削刃是滚刀切削工件的部分,通常由硬质合金制成。
二、滚刀的切削原理滚刀的切削原理与传统的刀具不同。
传统的刀具通过切削刃与工件接触并沿切削方向切削,而滚刀则是通过滚刀切削刃与工件接触并沿切削方向滚动切削。
滚刀的切削过程具有以下几个特点:1. 切削力分布均匀:由于滚刀的切削刃是沿切削方向滚动,切削力在切削区域分布均匀。
与传统刀具相比,可以减少工件受力集中的问题,提高加工精度和工件表面质量。
2. 减小切削力:滚刀的切削刃与工件接触并滚动切削,摩擦力相对较小,因此切削力也相对较小。
这有利于减小加工设备的负荷,延长设备的使用寿命。
3. 降低切削温度:滚刀的滚动切削过程中,切削刃与工件接触时间较短,切削温度相对较低。
这有利于减少工件热变形和刀具磨损,提高加工质量和刀具寿命。
三、滚刀的优点滚刀相对于传统刀具具有一些明显的优点,主要包括以下几个方面:1. 提高加工效率:由于滚刀切削力小,加工时可采用较大的切削深度和进给量,提高了加工效率。
2. 改善工件表面质量:滚刀的切削刃滚动切削过程中,可以减小切削力和切削温度,提高工件的表面粗糙度和平整度。
3. 延长刀具寿命:滚刀的切削刃滚动切削,切削力相对较小,减少了刀具的磨损与损伤,延长了刀具的使用寿命。
四、滚刀的应用滚刀广泛应用于金属加工和木材加工等行业。
在金属加工中,滚刀主要用于车削、镗削、铣削等工艺;在木材加工中,滚刀主要用于刨削和铣削等工艺。
滚刀的应用可以提高加工效率、改善加工质量,并减少刀具的消耗和设备的维修成本。
泥水盾构机滚刀使用分析
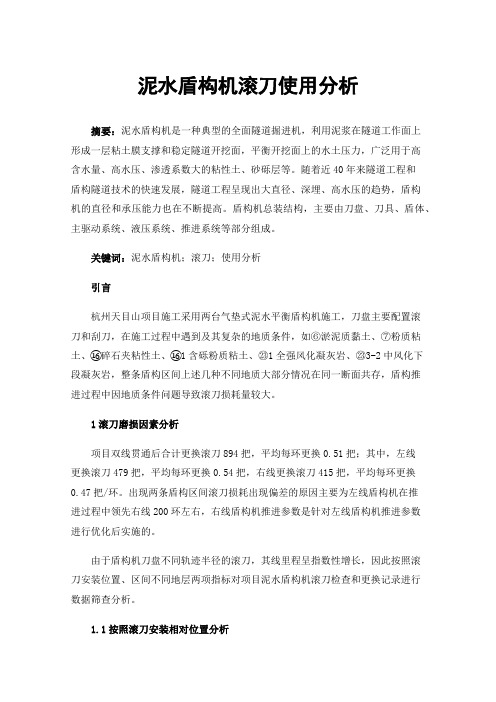
泥水盾构机滚刀使用分析摘要:泥水盾构机是一种典型的全面隧道掘进机,利用泥浆在隧道工作面上形成一层粘土膜支撑和稳定隧道开挖面,平衡开挖面上的水土压力,广泛用于高含水量、高水压、渗透系数大的粘性土、砂砾层等。
随着近40年来隧道工程和盾构隧道技术的快速发展,隧道工程呈现出大直径、深埋、高水压的趋势,盾构机的直径和承压能力也在不断提高。
盾构机总装结构,主要由刀盘、刀具、盾体、主驱动系统、液压系统、推进系统等部分组成。
关键词:泥水盾构机;滚刀;使用分析引言杭州天目山项目施工采用两台气垫式泥水平衡盾构机施工,刀盘主要配置滚刀和刮刀,在施工过程中遇到及其复杂的地质条件,如⑥淤泥质黏土、⑦粉质粘土、⑯碎石夹粘性土、⑯1含砾粉质粘土、㉓1全强风化凝灰岩、㉓3-2中风化下段凝灰岩,整条盾构区间上述几种不同地质大部分情况在同一断面共存,盾构推进过程中因地质条件问题导致滚刀损耗量较大。
1滚刀磨损因素分析项目双线贯通后合计更换滚刀894把,平均每环更换0.51把;其中,左线更换滚刀479把,平均每环更换0.54把,右线更换滚刀415把,平均每环更换0.47把/环。
出现两条盾构区间滚刀损耗出现偏差的原因主要为左线盾构机在推进过程中领先右线200环左右,右线盾构机推进参数是针对左线盾构机推进参数进行优化后实施的。
由于盾构机刀盘不同轨迹半径的滚刀,其线里程呈指数性增长,因此按照滚刀安装位置、区间不同地层两项指标对项目泥水盾构机滚刀检查和更换记录进行数据筛查分析。
1.1按照滚刀安装相对位置分析滚刀不同安装位置更换频次依次从刀盘中心(13#)向外侧逐渐增大(81#,同轨迹三把滚刀),从下图可看出趋势线逐步增高。
刀盘中心滚刀运行轨迹半径从中心向外侧陆续增加,不同滚刀轨迹运行圆周长度(线里程)呈线性变长,相同地层中滚刀磨损程度也是逐渐变大,符合物理规律。
1.2按照区间断面不同地层分析由于整个区间多种不同地质条件长距离共存,根据开仓检查情况发现对两两相距较远的滚刀磨损情况差异较大。
滚刀工作原理分析

滚刀工作原理分析滚刀是一种常用的工业制刀设备,常用于食品、医药、化工等行业的制刀工作。
滚刀工作原理是通过旋转刀片切割材料,具有高效、精准、环保等特点。
本文将就滚刀工作原理进行详细分析。
一、滚刀的结构滚刀主要由电机、轴承、刀架等部件组成。
其中电机提供动力,驱动滚刀旋转;轴承既支撑滚刀的旋转又保证稳定性;刀架是安装刀片的部位,可分成正交式和斜式两种。
正交式刀架主要是用于切割硬材料,具有切口整齐、刀尖稳固等优点;斜式刀架可以根据需要调整切角,常用于切割软材料。
二、滚刀的切割原理滚刀采用滚刀切割原理。
滚刀上安装的刀片不是像一般的刀片一样,是以“刀尖”形式出现的,而是采用细小的齿轮,所以滚刀就像一只带牙的圆柱体。
当滚刀旋转时,齿轮螺旋式排开材料,在齿轮间空隙处,材料受到齿轮带牙的切割作用,从而切割成精准的指定尺寸。
在一定角度下材料随着刀片的带动会离开母材并且成为一个整体,继续沿着滚刀移动。
从而实现批量、大量、高效的切割操作。
滚刀的能力在于,可以在一定的尺寸范围内调整齿轮的规格,从而达到不同的切割尺寸和形状。
三、滚刀的优势1、高效:滚刀切割线速度可以达到10-60米/秒,因此对于生产效率有很大提升。
2、精准:滚刀切割尺寸精度高,一般达到±0.01毫米。
可进行高精度、高质量的切割加工。
3、环保:滚刀切割不会产生任何毒害物质,也不会产生噪声和振动,可以满足绿色环保要求。
4、适应性强:滚刀切割可以处理多种材质的材料,如纸张、塑料、金属、橡胶等材料,可以在不同领域中应用。
四、滚刀的应用滚刀广泛应用于食品、医药、化工、电子等行业中的制刀工作。
特别是饼干、巧克力、药品、橡胶等行业的生产加工中,滚刀的应用是必不可少的。
在制刀过程中,滚刀的应用可以提高效率,缩短生产周期,保证产品的质量和稳定性。
同时,滚刀的应用还可以降低生产成本,提升企业的利润。
五、总结滚刀的工作原理是通过旋转刀片切割材料。
滚刀采用滚刀切割原理,具有高效、精准、环保等特点。
滚刀工作原理分析
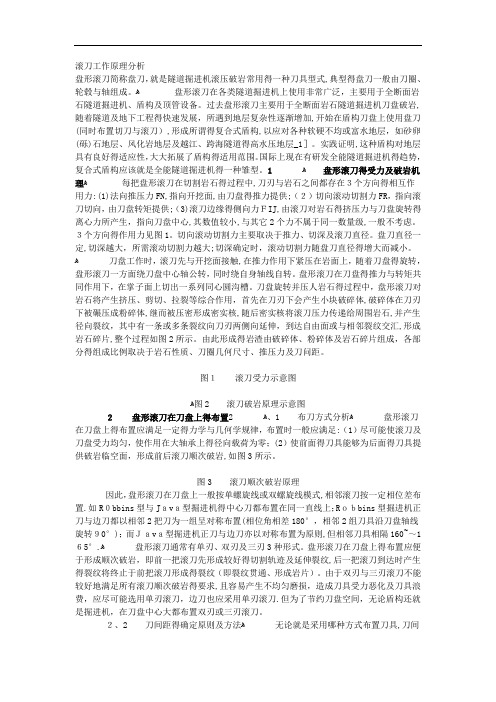
滚刀工作原理分析盘形滚刀简称盘刀,就是隧道掘进机滚压破岩常用得一种刀具型式,典型得盘刀一般由刀圈、轮毂与轴组成。
ﻫ盘形滚刀在各类隧道掘进机上使用非常广泛,主要用于全断面岩石隧道掘进机、盾构及顶管设备。
过去盘形滚刀主要用于全断面岩石隧道掘进机刀盘破岩,随着隧道及地下工程得快速发展,所遇到地层复杂性逐渐增加,开始在盾构刀盘上使用盘刀(同时布置切刀与滚刀),形成所谓得复合式盾构,以应对各种软硬不均或富水地层,如砂卵(砾)石地层、风化岩地层及越江、跨海隧道得高水压地层_1]。
实践证明,这种盾构对地层具有良好得适应性,大大拓展了盾构得适用范围。
国际上现在有研发全能隧道掘进机得趋势,1盘形滚刀得受力及破岩机复合式盾构应该就是全能隧道掘进机得一种雏型。
ﻫ理ﻫ每把盘形滚刀在切割岩石得过程中,刀刃与岩石之间都存在3个方向得相互作用力:(1)法向推压力FN,指向开挖面,由刀盘得推力提供;(2)切向滚动切割力FR,指向滚刀切向,由刀盘转矩提供;(3)滚刀边缘得侧向力FIJ,由滚刀对岩石得挤压力与刀盘旋转得离心力所产生,指向刀盘中心,其数值较小,与其它2个力不属于同一数量级,一般不考虑。
3个方向得作用力见图1。
切向滚动切割力主要取决于推力、切深及滚刀直径。
盘刀直径一定,切深越大,所需滚动切割力越大;切深确定时,滚动切割力随盘刀直径得增大而减小。
ﻫ刀盘工作时,滚刀先与开挖面接触,在推力作用下紧压在岩面上,随着刀盘得旋转,盘形滚刀一方面绕刀盘中心轴公转,同时绕自身轴线自转。
盘形滚刀在刀盘得推力与转矩共同作用下,在掌子面上切出一系列同心圆沟槽。
刀盘旋转并压人岩石得过程中,盘形滚刀对岩石将产生挤压、剪切、拉裂等综合作用,首先在刀刃下会产生小块破碎体,破碎体在刀刃下被碾压成粉碎体,继而被压密形成密实核,随后密实核将滚刀压力传递给周围岩石,并产生径向裂纹,其中有一条或多条裂纹向刀刃两侧向延伸,到达自由面或与相邻裂纹交汇,形成岩石碎片,整个过程如图2所示。
滚刀工作原理分析

滚刀工作原理分析(共6页) -本页仅作为预览文档封面,使用时请删除本页-滚刀工作原理分析盘形滚刀简称盘刀,是隧道掘进机滚压破岩常用的一种刀具型式,典型的盘刀一般由刀圈、轮毂和轴组成。
盘形滚刀在各类隧道掘进机上使用非常广泛,主要用于全断面岩石隧道掘进机、盾构及顶管设备。
过去盘形滚刀主要用于全断面岩石隧道掘进机刀盘破岩,随着隧道及地下工程的快速发展,所遇到地层复杂性逐渐增加,开始在盾构刀盘上使用盘刀(同时布置切刀和滚刀),形成所谓的复合式盾构,以应对各种软硬不均或富水地层,如砂卵(砾)石地层、风化岩地层及越江、跨海隧道的高水压地层_1]。
实践证明,这种盾构对地层具有良好的适应性,大大拓展了盾构的适用范围。
国际上现在有研发全能隧道掘进机的趋势,复合式盾构应该是全能隧道掘进机的一种雏型。
1 盘形滚刀的受力及破岩机理每把盘形滚刀在切割岩石的过程中,刀刃与岩石之间都存在3个方向的相互作用力:(1)法向推压力FN,指向开挖面,由刀盘的推力提供;(2)切向滚动切割力FR,指向滚刀切向,由刀盘转矩提供;(3)滚刀边缘的侧向力FIJ,由滚刀对岩石的挤压力和刀盘旋转的离心力所产生,指向刀盘中心,其数值较小,与其它2个力不属于同一数量级,一般不考虑。
3个方向的作用力见图1。
切向滚动切割力主要取决于推力、切深及滚刀直径。
盘刀直径一定,切深越大,所需滚动切割力越大;切深确定时,滚动切割力随盘刀直径的增大而减小。
刀盘工作时,滚刀先与开挖面接触,在推力作用下紧压在岩面上,随着刀盘的旋转,盘形滚刀一方面绕刀盘中心轴公转,同时绕自身轴线自转。
盘形滚刀在刀盘的推力和转矩共同作用下,在掌子面上切出一系列同心圆沟槽。
刀盘旋转并压人岩石的过程中,盘形滚刀对岩石将产生挤压、剪切、拉裂等综合作用,首先在刀刃下会产生小块破碎体,破碎体在刀刃下被碾压成粉碎体,继而被压密形成密实核,随后密实核将滚刀压力传递给周围岩石,并产生径向裂纹,其中有一条或多条裂纹向刀刃两侧向延伸,到达自由面或与相邻裂纹交汇,形成岩石碎片,整个过程如图2所示。
滚齿机加工原理及误差分析
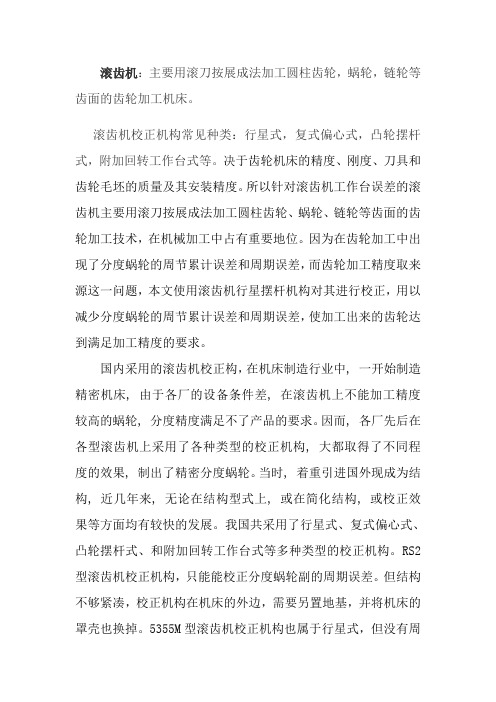
滚齿机:主要用滚刀按展成法加工圆柱齿轮,蜗轮,链轮等齿面的齿轮加工机床。
滚齿机校正机构常见种类:行星式,复式偏心式,凸轮摆杆式,附加回转工作台式等。
决于齿轮机床的精度、刚度、刀具和齿轮毛坯的质量及其安装精度。
所以针对滚齿机工作台误差的滚齿机主要用滚刀按展成法加工圆柱齿轮、蜗轮、链轮等齿面的齿轮加工技术,在机械加工中占有重要地位。
因为在齿轮加工中出现了分度蜗轮的周节累计误差和周期误差,而齿轮加工精度取来源这一问题,本文使用滚齿机行星摆杆机构对其进行校正,用以减少分度蜗轮的周节累计误差和周期误差,使加工出来的齿轮达到满足加工精度的要求。
国内采用的滚齿机校正构,在机床制造行业中, 一开始制造精密机床, 由于各厂的设备条件差, 在滚齿机上不能加工精度较高的蜗轮, 分度精度满足不了产品的要求。
因而, 各厂先后在各型滚齿机上采用了各种类型的校正机构, 大都取得了不同程度的效果, 制出了精密分度蜗轮。
当时, 着重引进国外现成为结构, 近几年来, 无论在结构型式上, 或在简化结构, 或校正效果等方面均有较快的发展。
我国共采用了行星式、复式偏心式、凸轮摆杆式、和附加回转工作台式等多种类型的校正机构。
RS2 型滚齿机校正机构,只能能校正分度蜗轮副的周期误差。
但结构不够紧凑,校正机构在机床的外边,需要另置地基,并将机床的罩壳也换掉。
5355M型滚齿机校正机构也属于行星式,但没有周期误差校正凸轮, 机构是封闭的。
其结构复杂, 构件将近85 种, 使用不方便, 需将机床的双蜗杆传动改成单蜗杆传动, 此时, 必需拆除一根蜗杆。
由于校正机构安装位置不够妥当,使得一部分齿轮外露。
这种结构不太适用于大型滚齿机。
FO-10滚齿机行星式校正机构,该机构有一定的简化, 它省去了四根摆杆和一根长套筒, 结构就比较紧凑一些。
它装在机床分度挂轮箱处, 不需另置地基, 但其构件的种数仍然较多, 达45种, 放大比为0.182毫米每秒。
这种机构的轮廓尺寸较大。
TBM11刀具试制报告

TB880E型TBM11刀具试制报告1.进口正滚刀的结构测绘及材料分析进口正滚刀的结构见图1,滚刀主要由刀圈、旋转及密封、安装、润滑几个部分组成。
1.1正滚刀的刀圈正滚刀的刀圈是刀具的主要易损件(祥见刀圈国产化试制报告),刀圈采用过盈配合热装在刀体上,实现刀圈的径向固定,利用刀体一端的轴肩和另一端的挡圈结合过盈配合实现刀圈的轴向固定,保证刀圈在正常工作时不会发生刀圈的径向转动和轴向移动。
1.2正滚刀的旋转及密封正滚刀在使用中平均每把要承受25吨的推力,其设计为端盖与刀轴固定在一起,通过轴承和浮动环实现刀具的旋转和密封。
一对圆锥滚子轴承采用TIMKEN公司成品,其型号为HH224334-HH224310,承受力为,轴承內圈过渡配合装在刀轴上,外圈装在刀体内;滚刀的密封是在刀体的两端和对应的刀盖上放置浮动金属密封环,其尺寸为φ227x15,O型橡胶圈为φ9.5。
1.3刀具的安装正滚刀的安装是采用端盖上的螺栓孔。
端盖一方面用螺栓与刀轴连接,组成刀具总成,保证刀具的转动力矩50NM,另一方面通过其上的螺栓孔与刀盘连接,把刀具固定在刀盘上,其安装尺寸见图1。
1.4正滚刀的润滑正滚刀的润滑采用机油润滑,润滑油除了润滑和冷却作用外,还加入了特殊气味的添加剂,起到预报漏油的作用。
1.5正滚刀主要零件的材料分析1.5.1材料成分见表12. 进口中心刀的结构测绘及材料分析进口中心刀的结构见图1,由图与图比较可以看出中心刀与正滚刀的主要差别有如下几点。
2.1 安装方式正滚刀是单个安装在刀盘上,其刀座是固定在刀盘上的;中心刀是安装在刀架上,刀架是活动的,六个刀架并排装在刀盘上,靠两端楔块轴向压紧中心刀.2.2 密封形式中心刀在设计时受到空间限制(硬岩时刀间距不能太宽),刀体上留不出单独安放金属浮动密封环的位置,故设计成在刀体两端直接作成密封带,与两端端盖上安置的金属浮动密封环配合实现密封.2.3 刀轴形式中心刀刀轴与一端端盖制造成一体,另一端端盖通过定位凸台保证径向定位,并保证刀圈工作时承受径向力,用M30的螺栓把两个端盖连接成一体.刀轴与端盖制成一体,虽然制造加工困难,但能够减少装配误差,是可取的结构形式.2.4 中心刀与支架的连接装配好的中心刀靠端盖上的斜面与支架上的斜面接触保证中心刀高度,用四块压板把中心刀压装在支架上.2.5 中心刀主要零件的材料成分和性能见表3 表4中心刀主要零件的材料成分表32.6 中心刀制造的工艺难点中心刀所有零件尺寸精度和表面光洁度普遍要求高,零件的调质硬度也普遍高,刀体端面直接作成密封带,对材料,热处理工艺和加工工艺都有很高的要求。
盾构刀具大解析

构刀具。
陶瓷材料
具有极高的硬度和耐磨 性,适用于高速切削和 干切削,但脆性较大。
超硬材料
如金刚石和立方氮化硼 ,具有极高的硬度和耐 磨性,适用于加工极硬
岩石。
制造工艺与流程
01
02
03
04Βιβλιοθήκη 锻造工艺通过高温加热、锻打和冷却等 工序,使钢材达到所需形状和
06
盾构刀具未来发展趋势与挑战
Chapter
技术创新方向预测
新型材料应用
随着新材料的不断涌现,盾构刀 具将采用更高强度、耐磨性和耐 热性的材料,如高性能陶瓷、超 硬合金等,以提高刀具的使用寿
命和切削效率。
智能化技术融合
结合人工智能、大数据等技术, 实现盾构刀具的智能化设计、制 造和管理,提高生产效率和降低
推进和导向
盾构机的推进系统提供前 进动力,导向系统控制盾 构机的掘进方向。
关键技术与创新
刀具材料和制造工艺
高性能的硬质合金、陶瓷和超硬 材料等被应用于刀具制造,提高 了刀具的耐磨性和切削效率。
智能控制系统
引入先进的传感器和控制系统, 实现盾构机的自动化和智能化控 制,提高施工效率和安全性。
01 02 03 04
盾构刀具大解析
汇报人:XX
目录
• 盾构刀具概述 • 盾构刀具结构与工作原理 • 盾构刀具材料选择与制造工艺 • 盾构刀具性能评价与试验方法 • 盾构刀具应用实例分析 • 盾构刀具未来发展趋势与挑战
01
盾构刀具概述
Chapter
定义与分类
定义
盾构刀具是盾构机上的重要部件 ,用于在地下开挖过程中破碎岩 石和土壤。
第三章 滚齿机的传动原理图
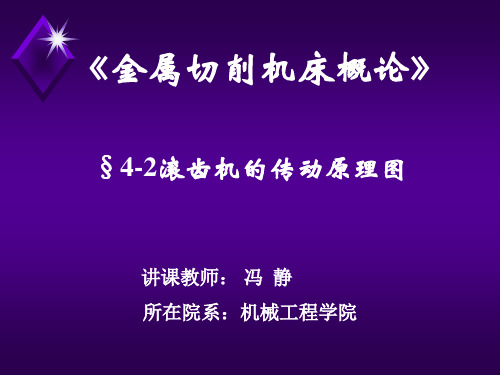
五、本章重点难点
1、加工直齿轮时所需的两个成形运动
2、加工斜齿轮时增加一条附加转动链(难点)
3、滚刀安装角的确定(难点)
谢
谢
成形法加工
展成法加工
滚刀加工直齿圆柱齿轮的运动分析
[母线]: 由展成法形成,
B11和B12
[导线]:
由相切法形成,
B11和A2
产生螺旋线的内链——差动链: 丝杠——工作台
if
iY
加上差动链后的原理图
B22 iv
B11
B12 A21 ix iS iY
正确的滚切斜齿原理图——加入合成机构
1 2
iv
3 4 9
5
合成
B11 B12 B22 A21
12
6
7 ix 8
10 iS 11 14 iY 13
15
[问题1]:滚齿机设计制造时应按以下哪种
表面——运动——传动
1、表面
直齿圆柱齿轮:母线是渐开线,导线是直线。
2、运动
滚刀加工直齿圆柱齿轮的运动分析
二、滚切直齿时的传动原理图
1、传动链分析
1)形成母线的展成复合运动
内链:滚刀B11——工件B12 外链:电机——滚刀
2)刀移动的简单成形运动
外链:电机——丝杠
2、原理图-1
1)主运动链 电机——滚刀
原理图设计?
1 2
iv
iv
3 4 9 7 ix 8
B11 B12 B22 A21
12
10 iS 11 14 iY 13
ix
if
四、滚刀的安装
1、加工直齿时
δ=ω
2、加工斜齿时
[问题2]:左旋滚刀能否加工右旋齿轮?
滚刀工作原理分析
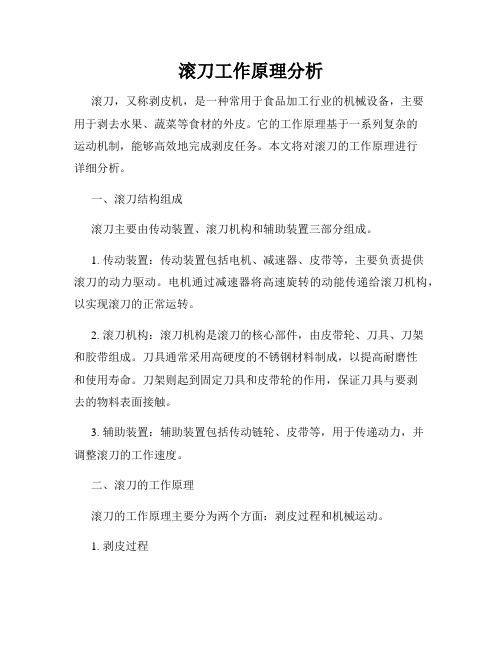
滚刀工作原理分析滚刀,又称剥皮机,是一种常用于食品加工行业的机械设备,主要用于剥去水果、蔬菜等食材的外皮。
它的工作原理基于一系列复杂的运动机制,能够高效地完成剥皮任务。
本文将对滚刀的工作原理进行详细分析。
一、滚刀结构组成滚刀主要由传动装置、滚刀机构和辅助装置三部分组成。
1. 传动装置:传动装置包括电机、减速器、皮带等,主要负责提供滚刀的动力驱动。
电机通过减速器将高速旋转的动能传递给滚刀机构,以实现滚刀的正常运转。
2. 滚刀机构:滚刀机构是滚刀的核心部件,由皮带轮、刀具、刀架和胶带组成。
刀具通常采用高硬度的不锈钢材料制成,以提高耐磨性和使用寿命。
刀架则起到固定刀具和皮带轮的作用,保证刀具与要剥去的物料表面接触。
3. 辅助装置:辅助装置包括传动链轮、皮带等,用于传递动力,并调整滚刀的工作速度。
二、滚刀的工作原理滚刀的工作原理主要分为两个方面:剥皮过程和机械运动。
1. 剥皮过程滚刀的剥皮过程依赖于刀具的尖端对食材的压力和切割。
当滚刀开始运转时,刀具的尖端会与食材的表面接触,并施加一定的压力。
同时,刀具以一定的速度绕食材表面旋转,通过切割作用将外皮逐渐剥离。
2. 机械运动滚刀的机械运动包括旋转和传递动力两个方面。
滚刀的旋转是通过传动装置提供动力,并传递给刀具。
电机通过减速器将高速旋转的动能传递给滚刀机构,滚刀机构中的皮带轮通过皮带将动力传递给刀具,使其绕食材表面快速旋转。
传递动力则是通过传动链轮、皮带等辅助装置实现的。
传动链轮的作用是使电机旋转传递给其他部件,确保滚刀正常工作。
皮带则起到调整滚刀的工作速度的作用,通过改变皮带的松紧程度来控制滚刀的转速。
三、工作原理分析滚刀的工作原理基于剥皮过程和机械运动,具有以下特点:1. 高效剥皮:滚刀通过刀具的旋转和切割作用,能够快速剥离食材的外皮,提高剥皮效率。
2. 刀具材质硬度高:为了保证刀具的耐磨性和使用寿命,滚刀通常采用高硬度的不锈钢材料制成,能够有效应对高强度的使用环境。
隧道掘进机盘形滚刀的工作原理分析
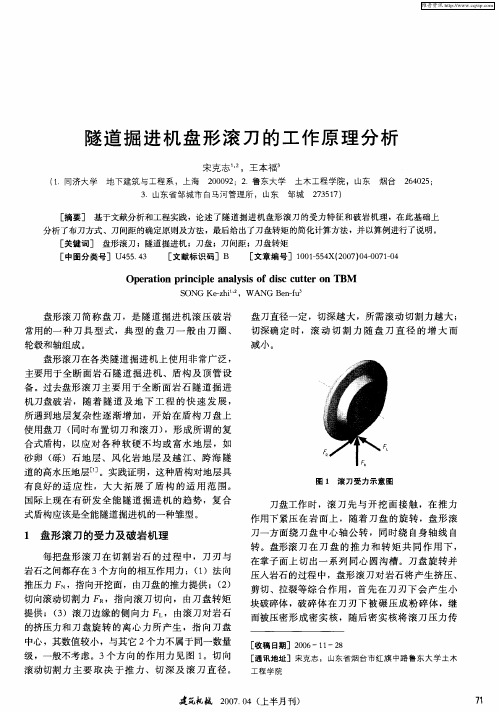
隧 道 掘 进 机 盘 形 滚 刀 的 工 作 原 理 分 析
宋克 志1 ,王 本福 I
(.同济 大学 1 地 下建筑 与工程 系 ,上海 209 ;2 鲁东 大学 0 02 . 土木 工程学 院 ,山东 邹城 23 1 ) 7 57 烟台 2 42 60 5 3 山东省 邹城 市 白马河管理 所 ,山东 .
常用 的一 种 刀 具 型 式 ,典 型 的盘 刀 一 般 由刀 圈 、
盘 刀直径 一定 ,切 深 越 大 ,所 需 滚 动 切 割力 越 大 ; 切深 确 定 时 ,滚 动 切 割 力 随 盘 刀 直 径 的 增 大 而
减小 。
轮 毂和轴 组成 。 盘形 滚刀 在各 类 隧 道 掘进 机 上 使 用 非 常 广泛 , 主要用 于 全 断 面 岩 石 隧 道 掘 进 机 、盾 构 及 顶 管设 备 。过 去盘形 滚 刀 主 要 用 于全 断 面 岩 石 隧道 掘 进 机 刀盘破 岩 ,随 着 隧 道 及 地 下 工 程 的 快 速 发 展 , 所遇 到地 层 复 杂 性 逐 渐 增 加 ,开 始 在 盾 构 刀 盘 上 使用 盘 刀 ( 同时 布置 切 刀 和 滚 刀 ) ,形 成 所 谓 的 复
滚刀 。
2 2 刀 间距 的确 定原 则及 方法 .
无 论是 采 用 哪 种 方 式 布 置 刀 具 ,刀 间 距 都 是 首 要考 虑 的技 术 问 题 之 一 。 刀 间距 的考 虑 有 两 种 方 式 : ( )在 同一 台 机 器上 刀 间距 不 变 ,以改 变 1
Ope a i n prn i l na y i f d s u tr o r to i c p e a l sso ic c te n TBM
S ONG -h 。 W ANG n f 。 Kez i Be -u
小型顶管机刀盘设计与有限元分析

小型顶管机刀盘设计与有限元分析李冲;李静;谢禹钧【摘要】顶管工程被认为是非开挖工程施工的一种工艺,顶管机刀盘作为油气管道穿越顶管机的关键工作部件,主要用来完成对掌子面岩土的破碎剥离,对掘进性能有重要影响。
针对穿河地区特殊地质概况,拟定刀盘结构设计方案,给出扭矩和推力计算方法,利用有限元分析软件 ANSYS 建立刀盘有限元模型,并在实际工况载荷下对刀盘整体进行静力分析,得到应力、应变分布和强度分布。
分析结果表明,危险截面出现在牛腿与传动轴交界处,最大应力为37.6 MPa,最大变形为0.06 mm。
%Pipe jacking project is regarded as a technology of non-excavation pipe jacking construction project,which has the most prominent feature of adaptability.The cutter head is one of the key components of the jacking machine crossing oil-gas pipelines,which major function is to accomplish crushing and peeling of rock soil of tunnel face,and takes a key role in digging function.Because of the difficulty of changing cutters and the complexity of the work environment,there is a high demand for the intensity of the cutter head.A corresponding cutter design program is established based on the special geology of the construction domain,and the torque and thrust calculation methods are given.Besides,the finite element model is established under the help of the ANSYS(finite element analysis software),so that the stress,strain,and strength reserve distribution are obtained.The analysis results show that the greatest equivalent stress appears at the interface between corbel and transmission shaft.The greatest stress is 37.6 MPa and the largest distortion is 0.06 mm.The resultof this research provides effective theory evidence for optimal structural design of the cutter head.【期刊名称】《石油化工高等学校学报》【年(卷),期】2016(029)004【总页数】5页(P87-91)【关键词】刀盘;设计;有限元分析【作者】李冲;李静;谢禹钧【作者单位】辽宁石油化工大学机械工程学院,辽宁抚顺 113001;辽宁石油化工大学机械工程学院,辽宁抚顺 113001;辽宁石油化工大学机械工程学院,辽宁抚顺 113001【正文语种】中文【中图分类】TH122;TH391.9非开挖技术,这一术语近年来被频繁提及,其特点是施工过程中无需开挖土体,在工作井下完成管道铺设。
张学强-上软下硬地层下滚刀失效及应对措施

刀刃与岩石接触区域任 意点压强如图3所示,设 滚刀在初始状态刚好与滚 压弧区接触,在刀盘开始 转动的瞬间,由于滚刀上 任意点均按摆线轨迹运动 ,在一定的滚刀转角增量 条件下,A点沿摆线方向 的位移量依次大于B点的 位移量,在岩石弹性范围 内,A点的压强依次大于 B点的压强,在A点的岩 石达到破坏瞬间,弧区各 点的
硬岩复合地层下滚刀的磨损失效原因分析硬岩复合地层下针对滚刀的失效形式分析状态描述原因分析改进措施修复方法正常磨损仅刀圈磨损且磨损均匀一刀圈出现局部崩碎原因主要原因是刀圈硬度偏高韧性偏低刀圈热处理工艺改进刀圈材料选择一般情况下只需更换刀多边磨一般为刀圈局部崩碎造成偏磨随地层变化刀体内部未破坏受力后转动刀圈热处理工艺改进刀圈材料选择大部分只需更换刀圈少数刀体有磨损的需更原因很多过载轴承与密封装配问题施工参数选择尽可能大载荷的轴承轴承游隙密封压力整体结构施工参数等方面调整一般较轻磨损的只需换刀圈较大部分的刀体轴承密封置换刀圈断裂刀圈硬度过高韧性差刀圈热处理工艺改进刀圈材料选择一般磨损较严重刀体必须更换整刀掉落螺栓松脱螺纹部分淬火处理标准螺纹制作更换安装部件山东天工内部资料案例分析轴承损坏
硬岩复合地层下针对滚刀的失效形式分析
状态描述 Ⅰ Ⅱ Ⅲ
正常磨损 刀圈崩牙
原因分析
仅刀圈磨损且磨损均匀一 致 刀圈出现局部崩碎原因主 要原因是刀圈硬度偏高, 韧性偏低 一般为刀圈局部崩碎造成 偏磨,随地层变化,刀体 内部未破坏,受力后转动 再偏磨 原因很多,过载、轴承与 密封、装配问题施工参数 等
1、刀圈材料选择。刀圈选用一种新型 合金热作模具钢,其合金含量高达 15%,含碳量达0.8%,原材料冶炼 过程采用电炉冶炼、真空除气、电 渣从熔、高压锻造等先进冶炼工艺 ,从原材料源头就有效控制钢材的 纯度及性能。
盾构刀具类型及刀具磨损分析张正银

盾构刀具类型及刀具磨损分析张正银发布时间:2023-07-02T07:02:30.721Z 来源:《建筑实践》2023年8期作者:张正银[导读] 盾构刀具是盾构机掘进的关键部件,盾构机的推进速度直接受到盾构刀具类型、质量等的影响,进而影响到整个施工进度及工程的效益。
本文通过对盾构刀具的分类,介绍了不同盾构刀具的磨损的原因,通过分析表明刀具的磨损不仅与刀具的质量有关,还与地质条件、掘进参数设置、刀具的配置等等有关。
最后分析了不同刀具的破坏形式,并给出了几点相关减少盾构刀具磨损的建议。
重庆交通大学重庆市 400074摘要:盾构刀具是盾构机掘进的关键部件,盾构机的推进速度直接受到盾构刀具类型、质量等的影响,进而影响到整个施工进度及工程的效益。
本文通过对盾构刀具的分类,介绍了不同盾构刀具的磨损的原因,通过分析表明刀具的磨损不仅与刀具的质量有关,还与地质条件、掘进参数设置、刀具的配置等等有关。
最后分析了不同刀具的破坏形式,并给出了几点相关减少盾构刀具磨损的建议。
关键词:盾构刀具;刀具分类;磨损一、引言伴随着我国经济的快速发展,城市的地表土地资源捉襟见肘,未来城市发展将往城市地下空间转移,而在城市地下空间的开发过程中,会经常遇到各种复杂的地质条件,需要大量相关的技术设备。
近年来盾构技术得到了广泛的采用,但同时也受到了各方面严峻的挑战。
在整个掘进过程中,由于复杂的地质条件会导致刀具出现磨损,刀具的磨损受到多方面因素的影响,包括刀具结构和材料自身、掘进参数设置、地质条件、刀具与地质条件的适应程度等等,其中刀具与地质条件的适应程度是重要的影响因素,不同的刀具应与不同的地质条件相适应才能使加快盾构机的掘进进度,相反如果刀具和前方地质条件不相适应,那么这将会使得盾构机掘进效降低,严重的还会导致刀具磨损,将直接影响到掘进的工作效率、工程的进展及工程的经济效益。
本论文通过介绍了盾构刀具的分类并分析了这些刀具的功能作用和在不同地质条件下的适应性,从目前存在的刀具磨损的问题,给出了几点减少刀具磨损的措施。
滚齿机工作原理 功能分析 介绍
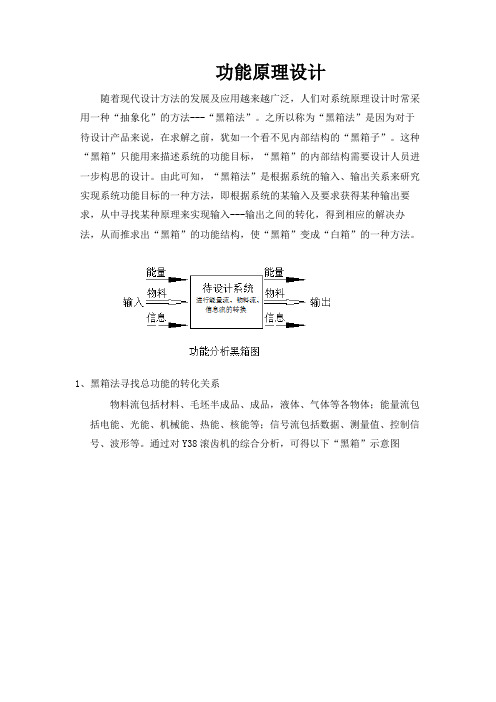
功能原理设计随着现代设计方法的发展及应用越来越广泛,人们对系统原理设计时常采用一种“抽象化”的方法---“黑箱法”。
之所以称为“黑箱法”是因为对于待设计产品来说,在求解之前,犹如一个看不见内部结构的“黑箱子”。
这种“黑箱”只能用来描述系统的功能目标,“黑箱”的内部结构需要设计人员进一步构思的设计。
由此可知,“黑箱法”是根据系统的输入、输出关系来研究实现系统功能目标的一种方法,即根据系统的某输入及要求获得某种输出要求,从中寻找某种原理来实现输入---输出之间的转化,得到相应的解决办法,从而推求出“黑箱”的功能结构,使“黑箱”变成“白箱”的一种方法。
1、黑箱法寻找总功能的转化关系物料流包括材料、毛坯半成品、成品,液体、气体等各物体;能量流包括电能、光能、机械能、热能、核能等;信号流包括数据、测量值、控制信号、波形等。
通过对Y38滚齿机的综合分析,可得以下“黑箱”示意图通过黑箱法分析,滚齿机是将轮坯通过一定的加工过程,最终得到所需产品—齿轮的机器。
该过程有各种能量的交换、损失,同时还与外界的环境密切相关。
2、滚齿加工原理齿轮是现代机械传动中的重要组成部分。
从国防机械到民用机械,从重工业机械到轻工业机械,无不广泛的采用齿轮传动。
随着汽车、机械、航天等工业领域的高速发展,对齿轮的需求量日益增加,对齿轮加工的效率、质量及加工成本的要求愈来愈高,滚齿机是齿轮加工加床中的一种,由于滚齿机既适合高效率的齿形粗加工,又适合中等精度齿轮的精加工,因此受到广泛的应用。
为此滚齿机的研究仍是大家努力的方向齿轮加工机床的种类繁多,构造各异,加工方法也不相同,齿形加工可按在加工中有无切屑而区分为无屑加工和切削加工两大类。
无屑加工包括热轧、冷轧、压铸和粉末冶金等,无屑加工生产率高,材料消耗少,故成本低,但加工精度不高。
(1)冷轧冷轧是能在圆柱形零件上生产出齿轮的齿、花键、细齿、油槽或螺纹的一种很简单的方法。
生产率很高,用此方法扎制一个齿轮仅需3~5秒钟,但它受轧制形状和材料的限制较大。
解析滚刀式皮辊轧花机结构原理、间隙调整及常见故障排除
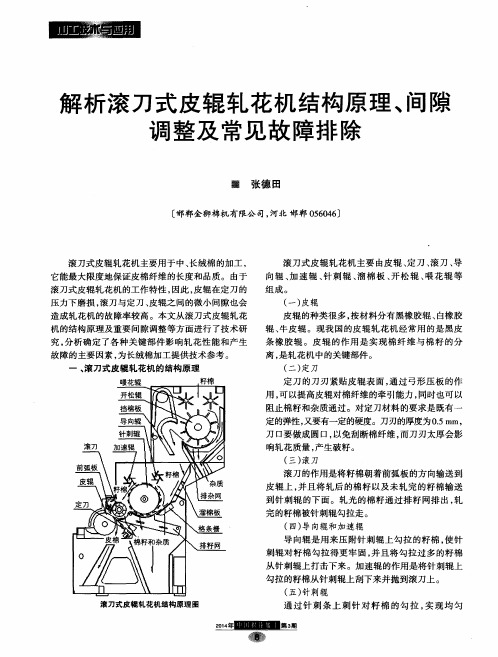
其结 构和 清花刺 钉辊一 样 , 对喂料 辊 喂人 的 籽棉 进行 开 松 、 清理 , 给 下 面 的 针 刺 辊 输 送 松 散
的籽 棉 。 ( 八) 喂花辊
定 刀刃太厚或太薄——打磨或更换新 的定刀 ,
刀刃 控制 在 0 . 5 mm左右 。
由两 个 叶 片 式 辊 对 转 , 实 现 对 籽 棉 的 向 下 输
解 析 滚 刀 式皮 辊 轧 花 机 结构 原 理 间 隙 调 整 及 常见 故 障排 除
张德 田
[ 邯郸 金狮 棉机 有机主要用于中、 长绒棉 的加工 ,
它能 最 大限 度地保 证 皮棉 纤维 的长度 和 品质 。 由于 滚刀 式皮 辊 轧花 机 的工作 特性 , 因此 , 皮辊 在 定刀 的 压 力下磨 损 , 滚 刀与 定 刀 、 皮辊 之 间 的微 小 间隙也 会 造成 轧 花机 的故 障率 较 高 。本 文从滚 刀 式皮 辊轧 花 机 的结构 原 理及 重要 间隙调 整 等方 面进 行 了技术 研 究, 分 析 确 定 了 各种 关 键 部 件影 响轧 花 性 能 和产 生
定 刀 高低 , 使 定 刀 刀 刃处 于皮 辊 与滚 刀 两 中心连 线 以下 6 a r m左 右 的工 作位 置 。
工作 间隙太大——调整滚刀和皮辊 、 滚刀和定
刀之 间 的 间隙 。
( 二) 调整皮辊与定刀间的压力
通 过 调 整皮 辊 的位 置来 改 变 压 力 的大 小 ; 通 过
弧板和滚刀、 皮辊的间隙调整为 0 . 5 2 m m为宜 。 滚刀刀刃太锋利 , 毛刺太多——进行打磨 。
排 籽 网 的位 置不对 —— 重 新调 整底 网与滚 刀 的 间隙为 1 2 l n m, 底 网前 端 与 定 刀 之 间 的 间 隙要 控 制
盾构机滚刀磨损原因分析及改进方法

盾构机滚刀磨损原因分析及改进方法作者:雷霆来源:《世界家苑·学术》2018年第07期摘要:介绍了盾构机滚刀的工作原理,详细的介绍了滚刀的磨损和破坏形式并进行了原因分析。
在此基础上结合实际盾构施工过程提出了一系列施工注意措施以及滚刀的改进方法。
最后,展望了盾构机滚刀磨损研究的发展方向和前景。
关键词:盾构机滚刀;正常磨损;轴承破坏;热处理滚刀的切削原理主要是依靠刀具挤压破岩,一般用于岩石隧道掘进。
工作时,滚刀在推进力的作用下,排列在刀盘上的盘形滚刀紧压岩面,随着刀盘的旋转,岩面被碾出一系列同心圆,利用滚刀的楔块作用,当超过岩石受力极限时,两个同心圆之间的岩石中间裂缝贯通,岩片被剥落,从而达到破岩挖掘的作用。
然而由于山体岩石的高强度、高硬度与地质条件的复杂性等原因,使掘进机刀具成为掘进过程中最易损坏的零部件。
因此,自主开发集高强度、高硬度、高耐磨性与耐热疲劳性能好和优良的韧性于一身的刀具是加快工程进度、降低盾构施工成本的决定性因素。
用于盾构隧道掘进的刀具按照形状、作用方式的不同,可分为滚刀和切削刀具两种不同的类型。
在硬岩地层中采用滚刀,软土地层常用切削刀具,本文主要介绍滚刀磨损的原因以及改进方法。
一、滚刀磨损形式及原因分析①正常磨损。
滚刀进行破岩时,破岩效率与其刀口宽度有关。
随着滚刀刀圈磨损量的增加,刀口宽度增加,达到一定范围时会影响掘进速度,由于受到刀圈加工工艺的限制,而且新装刀圈与齿刀之间的高差为35mm,所以确定正滚刀与中心刀最大磨损量为30mm;而边缘滚刀则因隧道直径以及所处位置的要求,其磨损极限一般为15mm。
正常磨损是刀具失效的主要形式,另正常磨损又称为均匀磨损,其磨损形状为在刀口宽度范围内磨损较均匀。
②滚刀刀圈断裂。
在掘进过程中由于岩石情况发生变化或刀盘其他部件(如齿刀等)脱落卡在刀刀与岩壁之间,会导致刀圈局部过载而使刀圈应力集中、发生断裂,同时刀圈与刀体配合过盈量未达到要求也会造成刀圈断裂。
- 1、下载文档前请自行甄别文档内容的完整性,平台不提供额外的编辑、内容补充、找答案等附加服务。
- 2、"仅部分预览"的文档,不可在线预览部分如存在完整性等问题,可反馈申请退款(可完整预览的文档不适用该条件!)。
- 3、如文档侵犯您的权益,请联系客服反馈,我们会尽快为您处理(人工客服工作时间:9:00-18:30)。
滚刀工作原理分析
盘形滚刀简称盘刀,是隧道掘进机滚压破岩常用的一种刀具型式,典型的盘刀一般由刀圈、轮毂和轴组成。
盘形滚刀在各类隧道掘进机上使用非常广泛,主要用于全断面岩石隧道掘进机、盾构及顶管设备。
过去盘形滚刀主要用于全断面岩石隧道掘进机刀盘破岩,随着隧道及地下工程的快速发展,所遇到地层复杂性逐渐增加,开始在盾构刀盘上使用盘刀(同时布置切刀和滚刀),形成所谓的复合式盾构,以应对各种软硬不均或富水地层,如砂卵(砾)石地层、风化岩地层及越江、跨海隧道的高水压地层_1]。
实践证明,这种盾构对地层具有良好的适应性,大大拓展了盾构的适用范围。
国际上现在有研发全能隧道掘进机的趋势,复合式盾构应该是全能隧道掘进机的一种雏型。
1 盘形滚刀的受力及破岩机理
每把盘形滚刀在切割岩石的过程中,刀刃与岩石之间都存在3个方向的相互作用力:(1)法向推压力FN,指向开挖面,由刀盘的推力提供;(2)切向滚动切割力FR,指向滚刀切向,由刀盘转矩提供;(3)滚刀边缘的侧向力FIJ,由滚刀对岩石的挤压力和刀盘旋转的离心力所产生,指向刀盘中心,其数值较小,与其它2个力不属于同一数量级,一般不考虑。
3个方向的作用力见图1。
切向滚动切割力主要取决于推力、切深及滚刀直径。
盘刀直径一定,切深越大,所需滚动切割力越大;切深确定时,滚动切割力随盘刀直径的增大而减小。
刀盘工作时,滚刀先与开挖面接触,在推力作用下紧压在岩面上,随着刀盘的旋转,盘形滚刀一方面绕刀盘中心轴公转,同时绕自身轴线自转。
盘形滚刀在刀盘的推力和转矩共同作用下,在掌子面上切出一系列同心圆沟槽。
刀盘旋转并压人岩石的过程中,盘形滚刀对岩石将产生挤压、剪切、拉裂等综合作用,首先在刀刃下会产生小块破碎体,破碎体在刀刃下被碾压成粉碎体,继而被压密形成密实核,随后密实核将滚刀压力传递给周围岩石,并产生径向裂纹,其中有一条或多条裂纹向刀刃两侧向延伸,到达自由面或与相邻裂纹交汇,形成岩石碎片,整个过程如图2所示。
由此形成的岩渣由破碎体、粉碎体及岩石碎片组成,各部分的组成比例取决于岩石性质、刀圈几何尺寸、推压力及刀问距。
图1 滚刀受力示意图
图2 滚刀破岩原理示意图
2 盘形滚刀在刀盘上的布置
2.1 布刀方式分析
盘形滚刀在刀盘上的布置应满足一定的力学和几何学规律,布置时一般应满足:(1)尽可能使滚刀及刀盘受力均匀,使作用在大轴承上的径向载荷为零;(2)使前面的刀具能够为后面的刀具提供破岩临空面,形成前后滚刀顺次破岩,如图3所示。
图3 滚刀顺次破岩原理
因此,盘形滚刀在刀盘上一般按单螺旋线或双螺旋线模式,相邻滚刀按一定相位差布置。
如R0bbins型和Java型掘进机的中心刀都布置在同一直线上;Robbins型掘进机正刀和边刀都以相邻2把刀为一组呈对称布置(相位角相差180°,相邻2组刀具沿刀盘轴线旋转90°);而Java型掘进机正刀和边刀亦以对称布置为原则,但相邻刀具相隔160~~16 5°。
盘形滚刀通常有单刃、双刃及三刃3种形式。
盘形滚刀在刀盘上的布置应便于形成顺次破岩,即前一把滚刀先形成较好的切割轨迹及延伸裂纹,后一把滚刀到达时产生的裂纹将终止于前把滚刀形成的裂纹(即裂纹贯通、形成岩片)。
由于双刃和三刃滚刀不能较好地满足所有滚刀顺次破岩的要求,且容易产生不均匀磨损,造成刀具受力恶化及刀具浪费,应尽可能选用单刃滚刀,边刀也应采用单刃滚刀。
但为了节约刀盘空间,无论盾构还是掘进机,在刀盘中心大都布置双刃或三刃滚刀。
2.2 刀间距的确定原则及方法
无论是采用哪种方式布置刀具,刀间距都是首要考虑的技术问题之一。
刀间距的考虑有两种方式:(1)在同一台机器上刀间距不变,以改变刀盘推力来适应岩石强度的变
化;(2)在同一刀盘上增减刀具数量或改变每把滚刀上的刀圈数来改变刀间距,以适应岩石强度。
第一种考虑方式简单且实用性强,应用较多。
刀间距的确定主要取决于开挖岩层的情况及岩石的种类与强度等,其与岩石强度的关系见图4。
按照剪切破岩理论,破岩模式如图5所示。
由图可知,当刀盘旋转一周,滚刀的切入深度为PR,则按剪切破岩理论,破裂宽度a= PRtanα,要使同一安装半径上的盘形滚刀在刀盘旋转一周的切深相等,切破岩量相同,在相邻滚刀之间就不应存在累积岩脊。
因此为保证岩石切割的条件,刀间距应为:
S≤2a+b=2PR/tanα+b(1)
式中S——刀间距;
PR——切人深度;
α——岩石压裂角,一般在18~30°左右;
a——岩石破裂宽度;
b——刀圈宽度,与刀圈形式及刀圈直径有关。
盘形滚刀布置间距计算举例见表1。
按照上述刀间距计算理论,并考虑刀盘空间,在混合地层中掘进时,刀间距的选择原则一般为:
(1)中心刀较少按最优刀间距布置,它们往往以比较小的刀间距布置,以补偿掘进过程中滚刀可能遇到的困难切割条件。
(2)正刀的刀间距在50~120mm之问,对于软岩层取大值,硬岩层取小值。
(3)隧道以软岩为主并有少量硬岩时,刀间距按软岩选择,掘到硬岩地段时,可以慢速掘进。
(4)隧道以硬岩为主并有中硬岩时,刀间距按二者兼顾原则选择。
如石灰岩地层的刀间距取80mm,花岗岩地层取50mm,在综合布置时刀间距取70mm为宜。
(5)边刀处于刀盘外缘,速度很高,磨损严重,很少按最优刀间距布置。
边刀的刀间距从邻近正刀开始,向外缘逐渐减少,最后2把相邻边刀的刀间距弧长一般为20~25mm,最后一把边刀的刀倾角一般为70°。
边刀的布置采用圆弧过渡,过渡区的曲率半径及边刀数量取决于掘进机直径的大小。
对于小直径掘进机,曲率半径为300~350rnm,边刀数为6~8把;对于大直径掘进机,曲率半径为600~650mm,边刀数为15~18把。
随着滚刀的高强度、耐磨性等技术的综合利用,滚刀的切深得到了很大的提高。
但此时为了达到所需的临界推力,需相应地扩大刀问距,否则会使滚刀处于前最优区工作。
这也可理解为,采用较宽的刀间距后,为使滚刀处于最优间距下工作,必须相应地增加单把滚刀的推压力。
在比切深不变的情况下,增大刀间距能够产生更多的岩石碎片,提高切割效率。
因此,采用较宽的刀间距,减少了刀具的数量,有利于降低单位进尺的刀具消耗,同时,能够减小所需的总转矩和总推力。
但是,滚刀直径从20世纪70年代的280mnl发展到90年代的480mm,刀间距并没有改变。
究其原因,有两个方面:(1)工程实践中总存在保守的观念;(2)采用较宽的刀间距时,将额外地增加预测机一岩相互作用的随机性,特别是在围岩条件较差时更为明显。
Ozd emir和Do1linger(1987)、Hartwing(1993)等的研究都表明了上述观点。
图4 刀间距与岩石强度的关系
图5 盘形滚刀切入岩体示意图
表1 滚刀间距计算举例
3 盘形滚刀的切割力分析
为研究滚刀切割力,设定基本参数如图6、图7所示,其中:
m——滚刀数量;
d——滚刀直径,mm;
PR——每转的滚刀切深,。
mm/r;
Ri——滚刀旋转半径,m;
D——TBM开挖直径,m;
S——滚刀间距,mm;
n——刀盘转速;
Fz——TBM刀盘总推压力,kN;
FN——滚刀法向推压力,kN;
FR——滚刀切向力,kN;
Tz——刀盘转矩,kNm;
Vz——掘进速度,mm/min;
m——滚刀数量,m=D/25。
图6 滚刀切割力计算原理图之一
图7 滚刀切割力计算原理图之二
刀盘刀具设计时,认为总推力在每把滚刀上平均分布,因此有:
单把滚刀的推压力可根据岩石的性质及刀圈几何尺寸来确定。
刀盘转矩为每把滚刀到刀盘旋转中心的力矩之和,即:
式中R为滚刀的平均旋转半径,良可按式(4)近似计算:
滚刀滚动切割阻力为:
式中μN为滚刀滚动切割阻力系数,一般μN≈0.1~0.15,具体与岩石物理力学性质及滚刀切深有关。
需要说明的是,滚动轴承摩擦系数一般取0.002,远小于脚,因此可以忽略滚动轴承的摩擦阻力。
由此可得刀盘转矩:
式(7)中,令,称之为转矩系数。
因此,TBM开挖所需的刀盘转矩为:
Tz=βD2(7)
该式不同于盾构刀盘转矩Tz =αD3。
[算例]已知某TBM,刀盘直径为8.0m,滚刀布置的平均刀间距为70mm。
设计采用1 7”盘形滚刀,其容许推压力为250kN,实际切割时为196kN,μN≈0.12。
所需滚刀数量:
实际设计布设62把滚刀。
按式(6)可得转矩系数:
(按容许推压力250kN计算,β=64.2)
则刀盘转矩为:
Tz=βD2=3225.6kNm
(按容许推压力计算,Tz =4108.8kNm)。