03 蜡油加氢裂化装置学生版xch
蜡油加氢裂化装置氢耗的影响因素分析及措施

蜡油加氢裂化装置氢耗的影响因素分析及措施摘要:在炼油企业降耗增效的大形势下,降低氢耗对于降低加工成本尤为重要。
蜡油加氢处理装置的氢耗在加工成本中占很大比例。
为了降低蜡油加氢处理装置的氢耗,有必要分析其影响因素并提出改进建议,为车间节能生产提供参考。
基于此,对蜡油加氢裂化装置氢耗的影响因素分析及措施进行研究,以供参考。
关键词:新氢;反应温度;原料组分;溶解损失;转化率引言加热炉的燃料气消耗在炼油装置能耗中占有相当大的比例,少则20%~30%,多则80%~90%,加热炉技术水平及操作性能极大地影响着炼油装置的能源消耗水平。
因此,提高加热炉热效率,降低燃料气消耗,对降低能耗具有十分重要的意义。
1氢耗的影响因素1.1溶解损失在氢气循环过程中,一部分氢气会溶解在热高压分离器(简称热高压分离器)和冷高压分离器(简称冷高压分离器)的液相中,称为溶解损失。
相关研究文献指出,180℃和240℃的高温是两个拐点。
在80℃左右,循环氢的体积分数最低。
当温度高于180℃时,循环氢的体积分数随着温度的升高而逐渐增加。
当温度超过240℃时,循环氢体积分数的增加趋势减缓。
考虑到循环氢浓度和设备的承受能力,装置的高温应为240℃~260℃。
对于高冷含量,降低操作温度有利于提高氢气纯度,但温度过低和高压空冷器、高压换热器负荷过重会导致能耗过高。
综合考虑,冷高分操作温度应控制在45℃~55℃。
1.2压力控制装置的压力控制采用循氢机入口的压力控制器控制新氢返回量和循氢机入口分液罐顶排放循环氢来控制,这样可以有效控制系统压力,又可以对临氢系统的氢分压进行调节,这种方式避免了循环氢连续排放造成的氢气浪费。
1.3浓度一般钢材在水溶液中,浓度越高,越容易产生硫化物应力腐蚀开裂。
有日本资料报导:当水溶液中的浓度低于50~60ppm时,应力腐蚀开裂的可能性很低。
对任何一种钢,都存在一个浓度的门限值,超过此门限值都可发生应力腐蚀开裂。
Troiano曾对16Mn钢试样进行研究,考察常温下浓度对裂纹扩展的影响,试验结果表明,常温条件下,钢材内部裂纹扩展非常缓慢。
蜡油加氢裂化装置柴油转化、减油增化方向研究

蜡油加氢裂化装置柴油转化、减油增化方向研究摘要:本文先是对蜡油加氢裂化装置概况及现状进行分析,其次蜡油加氢裂化装置柴油转化、减油增化的影响因素,最后提出蜡油加氢裂化装置柴油转化、减油增化的对策,促进企业可持续发展。
关键词:蜡油加氢;裂化装置;柴油转化;减油增化当前,为了促进企业可持续发展,很有必要探讨蜡油加氢裂化装置柴油转化、减油增化的措施,降低成本,提高企业发展效益。
1蜡油加氢裂化装置概况及现状某石化千万吨炼油项目的主体装置为蜡油加氢裂化装置,其将美国UOP企业的加氢裂化专利技术与工艺包引进。
通过分析,加氢裂化设计规模为每年210万吨,一年操作时间为8400h,装置操作弹性为60%~110%。
这一装置的主要反应部分在于合理利用炉前婚氢、单段全循环、热高分工艺流程,且还设置了循环氢脱硫塔,分馏系统主要使用的是四塔分离流程出柴油方案,即分馏塔、硫化氢脱硫塔、柴油汽提塔、航煤汽提塔[1]。
该装置使用的操作方法为单段全循环方法,最大程度地完成中间馏分忧的生产,将其当做整个企业的调和组分,将少量加氢裂化还未转化的油去重油催化裂化当做主要的原料,冷低分气脱硫之后可以去PSA装置完成氢气提纯,含硫干气到轻烃回收装置中。
当前,企业原始设计方案采用低硫原油为主要原料,完成最大量生产中间馏分柴油方案。
2016年企业为了降低生产加工总成本,将其换成加工高硫原料油,生产的是高效的石脑油,让装置柴汽比方案明显降低。
2018年之前,基本维持装置重石脑油在0.5~1.2ppm。
从2018年开始,维持硫含量在2.0~4.0ppm之间。
为了给下游重整更优的原料,被迫将加裂装置的石脑油通过石脑油加氢装置脱硫之后将其送到重整装置,最终导致企业加工总成本明显提高。
2蜡油加氢裂化装置柴油转化、减油增化的影响因素2.1反应器后精制剂超负荷运行最初的蜡油加氢裂化装置设计原材料为轻蜡油,反应器之内的催化剂装填级配更多以原始方案为基础,主要设计在于生产中间馏分油。
蜡油加氢裂化装置反应器飞温问题研究
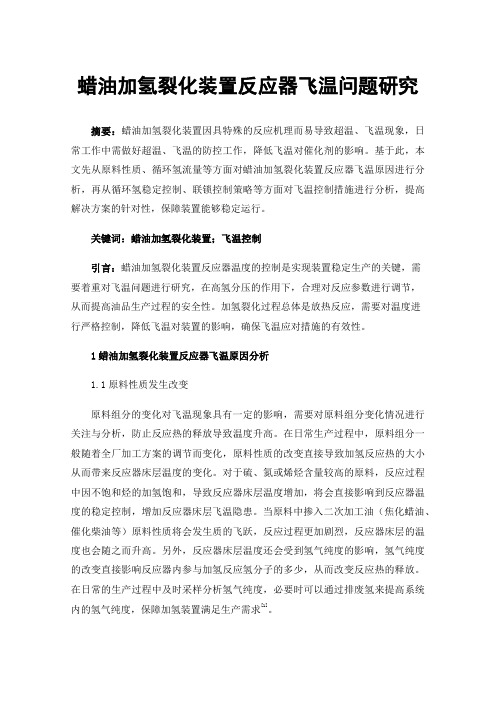
蜡油加氢裂化装置反应器飞温问题研究摘要:蜡油加氢裂化装置因具特殊的反应机理而易导致超温、飞温现象,日常工作中需做好超温、飞温的防控工作,降低飞温对催化剂的影响。
基于此,本文先从原料性质、循环氢流量等方面对蜡油加氢裂化装置反应器飞温原因进行分析,再从循环氢稳定控制、联锁控制策略等方面对飞温控制措施进行分析,提高解决方案的针对性,保障装置能够稳定运行。
关键词:蜡油加氢裂化装置;飞温控制引言:蜡油加氢裂化装置反应器温度的控制是实现装置稳定生产的关键,需要着重对飞温问题进行研究,在高氢分压的作用下,合理对反应参数进行调节,从而提高油品生产过程的安全性。
加氢裂化过程总体是放热反应,需要对温度进行严格控制,降低飞温对装置的影响,确保飞温应对措施的有效性。
1蜡油加氢裂化装置反应器飞温原因分析1.1原料性质发生改变原料组分的变化对飞温现象具有一定的影响,需要对原料组分变化情况进行关注与分析,防止反应热的释放导致温度升高。
在日常生产过程中,原料组分一般随着全厂加工方案的调节而变化,原料性质的改变直接导致加氢反应热的大小从而带来反应器床层温度的变化。
对于硫、氮或烯烃含量较高的原料,反应过程中因不饱和烃的加氢饱和,导致反应器床层温度增加,将会直接影响到反应器温度的稳定控制,增加反应器床层飞温隐患。
当原料中掺入二次加工油(焦化蜡油、催化柴油等)原料性质将会发生质的飞跃,反应过程更加剧烈,反应器床层的温度也会随之而升高。
另外,反应器床层温度还会受到氢气纯度的影响,氢气纯度的改变直接影响反应器内参与加氢反应氢分子的多少,从而改变反应热的释放。
在日常的生产过程中及时采样分析氢气纯度,必要时可以通过排废氢来提高系统内的氢气纯度,保障加氢装置满足生产需求[1]。
1.2循环氢流量偏低蜡油加氢裂化反应过程中,将会释放出大量的热量,对装置稳定运行具有较大的影响,需要采用循环氢来控制反应器各床层温度,提高内部热量的散发效率,确保温度控制效果的稳定性。
加氢裂化装置正常操作规程
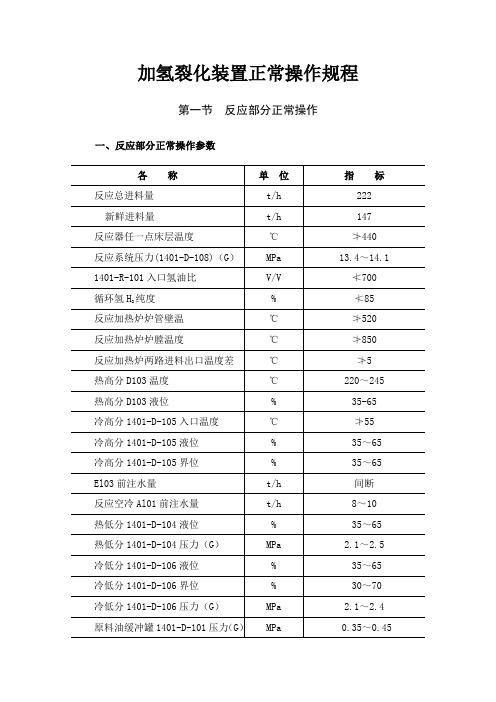
加氢裂化装置正常操作规程第一节反应部分正常操作一、反应部分正常操作参数二、一般规定在开工进程中需要进行升降压、升降温,为了保证装置的安全和长周期运行,需要遵循以下规程:1.反应器升压在下述的任何一项操作中,反应器应按以下推荐的温度和压力限制进行操作。
反应器每一次升压,在反应器所有部件的金属温度达到51℃以前,压力应不超过反应器入口设计压力的四分之一(4.125MPa)。
一旦反应器在高于357℃的温度下操作过,对于以后的所有开工,在反应器各部件的金属温度没有达到93℃以前,反应器压力应不超过入口设计压力的四分之一(4.125MPa)。
2.反应器降压在反应器正常操作压力和温度下,钢材里的氢浓度可达几个ppm,当反应器被冷却和降压时,溶解度降低,导致氢浓度过饱和。
当反应器脱气时(如开停工时)必须小心防止因为过饱和的氢浓度引起钢的氢脆变。
停工时,在任一表面温度降到93℃或更低温度前,反应器应降压到或以下4.125MPa。
降压时另外一个要考虑的问题是由于高流速产生高压降而增加的反应器内部构件的应力,降压速度应控制到任何一个反应器的总压降都不超过0.6MPa。
3.反应器升温在反应器升温期间,升温速度应保持在下列限度以内。
工艺流体限制反应器表面温度<93℃>93℃进料温度变化<8℃/15分钟<14℃/15分钟进料温度比最低表面温度比最低表面温度最多高167 最多高167C4.反应器降温在反应器降温期间,降温速度应保持在下列限度以内:工艺流体限制反应器外壳金属温度<93℃>93℃进料温度变化<8℃/15分钟<14℃/15分钟进料温度比最低表面温度比最低表面温度最多低11l℃最多低11l℃三、操作因素分析1.反应温度反应温度是控制脱硫脱氮率的重要手段。
对于1401-R-101,提高反应温度,提高了脱硫脱氮率,为裂化反应创造条件。
对于1401-R-102,提高反应温度可使裂解反应速度加快,原料的裂化程度加深,生成油中低沸点组分含量增加,气体产率增加。
蜡油加氢装置掺炼催化裂化柴油的工业应用
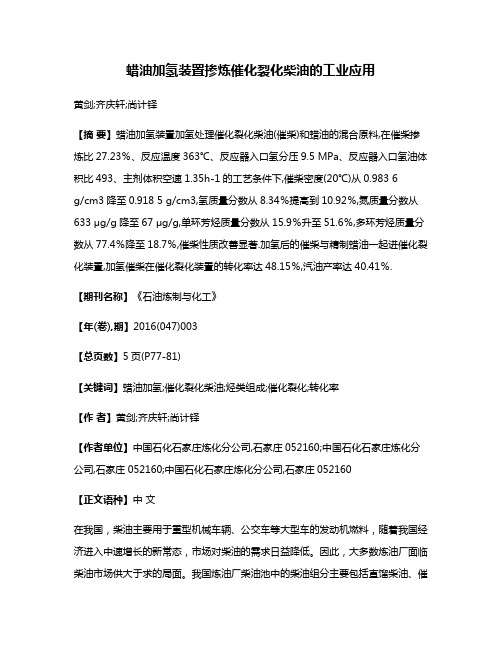
蜡油加氢装置掺炼催化裂化柴油的工业应用黄剑;齐庆轩;尚计铎【摘要】蜡油加氢装置加氢处理催化裂化柴油(催柴)和蜡油的混合原料,在催柴掺炼比27.23%、反应温度363℃、反应器入口氢分压9.5 MPa、反应器入口氢油体积比493、主剂体积空速1.35h-1的工艺条件下,催柴密度(20℃)从0.983 6g/cm3降至0.918 5 g/cm3,氢质量分数从8.34%提高到10.92%,氮质量分数从633 μg/g降至67 μg/g,单环芳烃质量分数从15.9%升至51.6%,多环芳烃质量分数从77.4%降至18.7%,催柴性质改善显著.加氢后的催柴与精制蜡油一起进催化裂化装置,加氢催柴在催化裂化装置的转化率达48.15%,汽油产率达40.41%.【期刊名称】《石油炼制与化工》【年(卷),期】2016(047)003【总页数】5页(P77-81)【关键词】蜡油加氢;催化裂化柴油;烃类组成;催化裂化;转化率【作者】黄剑;齐庆轩;尚计铎【作者单位】中国石化石家庄炼化分公司,石家庄052160;中国石化石家庄炼化分公司,石家庄052160;中国石化石家庄炼化分公司,石家庄052160【正文语种】中文在我国,柴油主要用于重型机械车辆、公交车等大型车的发动机燃料,随着我国经济进入中速增长的新常态,市场对柴油的需求日益降低。
因此,大多数炼油厂面临柴油市场供大于求的局面。
我国炼油厂柴油池中的柴油组分主要包括直馏柴油、催化裂化柴油(简称催柴)、加氢裂化柴油及少量焦化柴油和其它加氢单元副产的少量柴油,其中催柴性质差,严重影响出厂柴油产品质量。
目前,催柴加工工艺技术主要有加氢精制工艺、加氢改质工艺[1]、加氢裂化工艺、加氢处理-催化裂化联合工艺[2-3]。
催柴通过加氢精制和加氢改质工艺,性质得到改善,但柴油十六烷值提高幅度有限,且不能降低柴油总产量;通过加氢裂化工艺,能够将部分催柴转化成高辛烷值汽油,但该工艺存在工艺条件苛刻,催化剂使用寿命短、氢耗高的问题;通过加氢处理-催化裂化联合工艺,能够将部分催柴转化成高辛烷值汽油,且加氢单元操作条件相对缓和,常规的加氢装置即可满足要求。
蜡油加氢裂化装置反应器飞温原因分析及对策
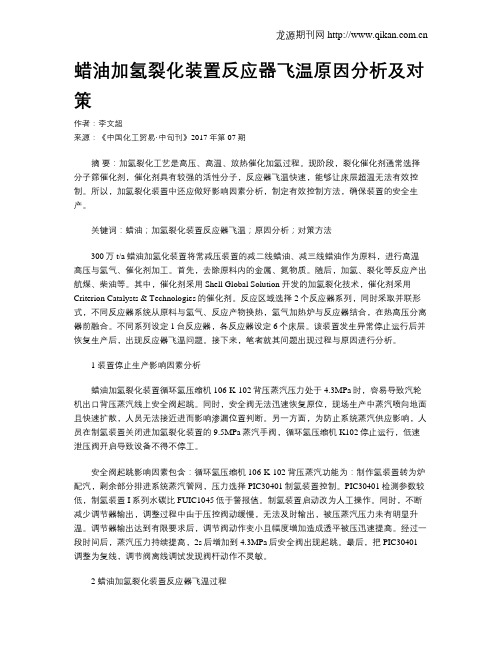
蜡油加氢裂化装置反应器飞温原因分析及对策作者:李文超来源:《中国化工贸易·中旬刊》2017年第07期摘要:加氢裂化工艺是高压、高温、放热催化加氢过程。
现阶段,裂化催化剂通常选择分子筛催化剂,催化剂具有较强的活性分子,反应器飞温快速,能够让床层超温无法有效控制。
所以,加氢裂化装置中还应做好影响因素分析,制定有效控制方法,确保装置的安全生产。
关键词:蜡油;加氢裂化装置反应器飞温;原因分析;对策方法300万t/a蜡油加氢化装置将常减压装置的减二线蜡油、减三线蜡油作为原料,进行高温高压与氢气、催化剂加工。
首先,去除原料内的金属、氮物质。
随后,加氢、裂化等反应产出航煤、柴油等。
其中,催化剂采用Shell Global Solution 开发的加氢裂化技术,催化剂采用Criterion Catalysts & Technologies的催化剂。
反应区域选择2个反应器系列,同时采取并联形式,不同反应器系统从原料与氢气、反应产物换热,氢气加热炉与反应器结合,在热高压分离器前融合。
不同系列设定1台反应器,各反应器设定6个床层。
该装置发生异常停止运行后并恢复生产后,出现反应器飞温问题。
接下来,笔者就其问题出现过程与原因进行分析。
1 装置停止生产影响因素分析蜡油加氢裂化装置循环氢压缩机106-K-102背压蒸汽压力处于4.3MPa时,容易导致汽轮机出口背压蒸汽线上安全阀起跳。
同时,安全阀无法迅速恢复原位,现场生产中蒸汽喷向地面且快速扩散,人员无法接近进而影响渗漏位置判断。
另一方面,为防止系统蒸汽供应影响,人员在制氢装置关闭进加氢裂化装置的9.5MPa蒸汽手阀,循环氢压缩机K102停止运行,低速泄压阀开启导致设备不得不停工。
安全阀起跳影响因素包含:循环氢压缩机106-K-102背压蒸汽功能为:制作氢装置转为炉配汽,剩余部分排进系统蒸汽管网,压力选择PIC30401制氢装置控制。
PIC30401检测参数较低,制氢装置I系列水碳比FUIC1045低于警报值。
蜡油加氢裂化装置

180万吨/年蜡油加氢裂化装置一、工艺流程选择1、反应部分流程选择A. 反应部分采用单段双剂串联全循环的加氢裂化工艺。
B. 反应部分流程选择:本装置采用部分炉前混氢的方案,即部分混合氢和原料油混合进入高压换热器后进入反应进料加热炉,另一部分混合氢和反应产物换热后与加热炉出口的混氢油一起进入反应器。
C. 本装置采用热高分流程,低分气送至渣油加氢脱硫后进PSA部分,回收此部分溶解氢。
同时采用热高分油液力透平回收能量。
因本装置处理的原料油流含量很高,氮含量较高,故设循环氢脱硫设施。
2、分馏部分流程选择A. 本项目分馏部分采用脱硫化氢塔-吸收稳定-常压塔出航煤和柴油的流程,分馏塔进料加热炉,优化分流部分换热流程。
采用的流程比传统的流程具有燃料消耗低、投资省、能耗低等特点。
B. 液化气的回收流程选用石脑油吸收,此法是借鉴催化裂化装置中吸收稳定的经验,吸收方法正确可靠,回收率搞。
具有投资少、能耗低、回收率可达95%以上等特点。
3、催化剂的硫化、钝化和再生A、本项目催化剂硫化拟采用干法硫化B、催化剂的钝化方案采用低氮油注氨的钝化方案C、催化剂的再生采用器外再生。
二、工艺流程简介1、反应部分原料油从原料预处理装置和渣油加氢裂化装置进入混合器混合后进入原料缓冲罐(D-101),经升压泵(P-101)升压后,再经过过滤(SR-101),进入滤后原料油缓冲罐(D-102)。
原料油经反应进料泵(P-102)升压后与部分混合氢混合,混氢原料油与反应产物换热(E-101),然后进入反应进料加热炉(F-101)加热,加热炉出口混氢原料和另一部分经换热后的混合氢混合,达到反应温度后进入加氢精制反应器(R-101),然后进入加氢裂化反应器(R-102),在催化剂的作用下,进行加氢反应。
催化剂床层间设有控制反应温度的急冷氢。
反应产物先与部分混合氢换热后再与混氢原料油换热后,进入热高压分离器(D-103)。
装置外来的补充氢由新氢压缩机(K-101)升压后与循环氢混合。
PHC-03型加氢裂化催化剂在1.2Mt·a-1加氢裂化装置的工业应用

2015年8月第23卷第8期 工业催化INDUSTRIALCATALYSIS Aug.2015Vol.23 No.8石油化工与催化收稿日期:2015-04-20;修回日期:2015-08-05作者简介:王文清,1964年生,男,黑龙江省大庆市人,工程师,主要从事炼油生产技术管理工作。
PHC-03型加氢裂化催化剂在1.2Mt·a-1加氢裂化装置的工业应用王文清(中国石油大庆石化公司炼油厂,黑龙江大庆163711)摘 要:对中国石油大庆石化公司炼油厂1.2Mt·a-1加氢裂化装置2012年开始使用的由中国石油石油化工科学研究院开发的PHC-03型加氢裂化催化剂的工业应用进行分析,包括PHC-03型加氢裂化催化剂的装填、硫化、钝化及长周期工业应用。
结果表明,PHC-03型加氢裂化催化剂在工业装置长周期工业应用过程中具有操作易控制、运行平稳、对不同生产方案和负荷适应能力强、催化剂性能良好、液体收率高和中间馏分油选择性好等特点,性能达到预期要求。
关键词:石油化学工程;PHC-03催化剂;加氢裂化;中间馏分油doi:10.3969/j.issn.1008 1143.2015.08.013中图分类号:TE624.9;TQ426.95 文献标识码:A 文章编号:1008 1143(2015)08 0645 03CommercialapplicationofPHC 03catalystin1.2Mt·a-1hydrocrackingunitWangWenqing(OilRefineryofPetroChinaDaqingPetrochemicalCompany,Daqing163711,Heilongjiang,China)Abstract:ThecommercialapplicationofPHC 03catalystdevelopedbyPetroChinaPetrochemicalResearchInstitutein1.2Mt·a-1hydrocrackingunitofOilRefineryofPetroChinaDaqingPetrochemicalCompanyin2012wasanalyzed.Thecatalystloading,vulcanization,inactivation,start upandlongperiodoperationwerecomprehensivelyintroduced.TheresultsshowedthatPHC 03catalysthadtheadvantagesofeasycontrol,stableoperation,strongadaptabilitytodifferentproductionplansandloads,goodcatalystperformance,highliquidyield,andgoodselectivitytotheintermediatedistillateduringstart upandlongperiodoperation.Theperformanceofthecatalystachievedtheexpectedrequirements.Keywords:petroleumchemicalengineering;PHC 03catalyst;hydrocracking;intermediatedistillatedoi:10.3969/j.issn.1008 1143.2015.08.013CLCnumber:TE624.9;TQ426.95 Documentcode:A ArticleID:1008 1143(2015)08 0645 03 加氢裂化是生产清洁燃料和化工原料等产品的重要技术。
第八章__加氢裂化装置课件
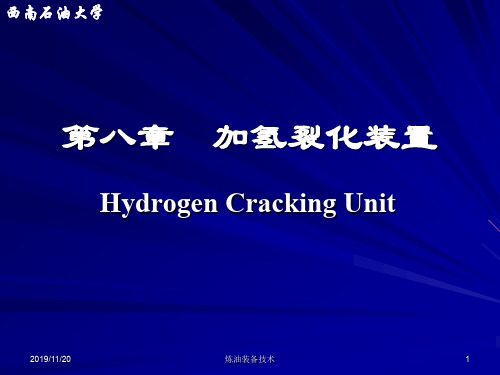
2019/11/20
炼油装备技术
6
西南石油大学
按反应器中催化剂所处的状态不同,可分为固定 床、沸腾床和悬浮床等几种型式。 根据原料和产品目的不同,还可细分出很多种型 式,如:馏分油加氢裂化、渣油加氢裂化以及单 段流程、一段串联流程和两段流程加氢裂化等等。 按尾油循环方式不同可分为一次通过法、部分循 环法和全循环法。
2019/11/20
炼油装备技术
3
西南石油大学
第一节 工作原理、工艺 流程及特点
2019/11/20
炼油装备技术
4
西南石油大学
一、加氢裂化装置的特点
加氢裂化装置是将重质油转化为轻质油的一 种加工手段,其特点是: 1.对原料油的适应性强,可加工直馏重柴油、催化 裂化循环油,焦化馏出油,甚至可用脱沥青重残 油生产汽油、航空煤油和低凝固点柴油; 2.生产方案灵活,可根据不同季节要求来改变生产 方案; 3.产品质量好,轻质油收率高。
2019/11/20
炼油装备技术
27
西南石油大学
3.去垢篮筐
在加氢反应器的顶部催 化剂床层上有时设有去垢篮 筐,与床层上的磁球一起对 进入反应器的介质进行过滤。
去垢篮一般均匀地布置 在床层上表面,篮筐周围充 填适量的大颗粒瓷球,以增 加透气性。
2019/11/20
炼油装备技术
28
西南石油大学
4.催化剂支撑盘
反应器筒体分为冷壁筒 和热壁筒两种。
2019/11/20
炼油装备技术
23
西南石油大学
(二)加氢反应器内件
加氢反应是在高温高压及有腐蚀介质(H2、H2S) 的条件下操作,除了在材质上要注意防止氢腐蚀及其 他介质的腐蚀以外,加氢反应器还应保证: 反应物(油气和氢)在反应器中分布均匀,保证反应物 与催化剂有良好的接触; 及时排除反应热,避免反应温度过高和催化剂过 热.以保证最佳反应条件和延长催化剂寿命; 在反应物均匀分布的前提下,反应器内部的压力降不 致过大,以减少循环压缩机的负荷,节省能源。
蜡油加氢裂化装置设备操作规程
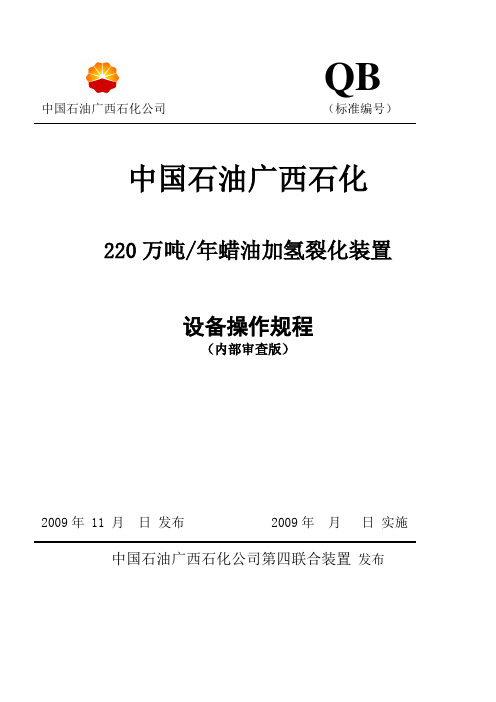
QB 中国石油广西石化公司(标准编号)中国石油广西石化220万吨/年蜡油加氢裂化装置设备操作规程(内部审查版)2009年 11 月日发布 2009年月日实施中国石油广西石化公司第四联合装置发布目录第一章循环氢压缩机K102 (3)1.1压缩机主要技术与性能参数 (4)1.2压缩机结构概述 (7)1.3调节控制系统 (10)1.4润滑油系统介绍 (13)1.5干气密封系统介绍 (25)1.6机组的仪表清单和设定值 (33)1.7常见故障处理 (37)1.8机组试车方案 (43)220万吨/年加氢裂化装置循环机操作规程 (57)第二章新氢压缩机K101 (83)2.1压缩机的基本结构 (83)2.2压缩机机组的基本参数 (90)2.3级间管路及冷却系统 (93)2.4系统流程 (95)2.5机组联锁报警一览表 (95)2.6机组的启动条件 (95)2.7机组联锁停机的条件 (96)2.8日常维护及异常处理 (96)2.9机组试运方案 (105)220万吨/年加氢裂化新氢压缩机操作规程 (115)第三章反应进料泵P101 (133)3.1概述: (133)3.2泵组配置说明 (133)3.3性能参数 (134)3.4泵组本身的联锁配置说明 (135)3.5泵组流程说明: (137)3.6P-101A/B工艺联锁配置说明 (138)3.7日常维护及异常处理 (139)3.8事故处理说明 (141)3.9机泵试车方案 (142)220万吨/年加氢裂化反应进料泵操作规程 (147)第四章高压注水泵P220 (164)4.1注水泵操作参数 (164)4.2注水泵主要组成 (164)4.3注水泵注意事项 (164)220万吨/年加氢裂化注水泵操作规程 (165)第五章贫胺液泵P103 (177)5.1概述 (177)5.2泵组配置说明 (177)5.3性能参数 (179)5.4泵组本身的联锁配置说明 (180)5.5泵组流程说明: (182)5.6P-103A/B工艺联锁配置说明 (182)5.7日常维护及异常处理 (184)5.8事故处理说明 (186)5.9机泵试车方案 (186)220万吨/年加氢裂化贫胺液泵P103操作规程 (192)第六章通用设备操作规程 (209)6.1 隔膜泵开泵 (209)6.2 隔膜泵停泵 (214)6.3 鼓、引风机开机 (218)6.4 鼓、引风机停机 (222)6.5 换热器投用 (225)6.6 换热器停用 (230)6.7 计量泵开泵 (234)6.8 计量泵停泵 (238)6.9 空冷器投用 (241)6.10 空冷器停用 (245)6.11 离心泵开泵 (248)6.12 离心泵停泵 (255)6.13 螺杆泵、齿轮泵开泵 (260)6.14 螺杆泵、齿冷泵停泵 (265)6.15 液下泵开泵 (268)6.16 液下泵停泵 (273)6.17 蒸汽发生器投用 (277)6.18 蒸汽发生器停用 (281)第一章循环氢压缩机K102循环氢压缩机组简介循环氢压缩机组(120-K-102)是广西石化220万吨/年加氢裂化装置的核心设备。
加氢裂化装置加工焦化蜡油操作优化
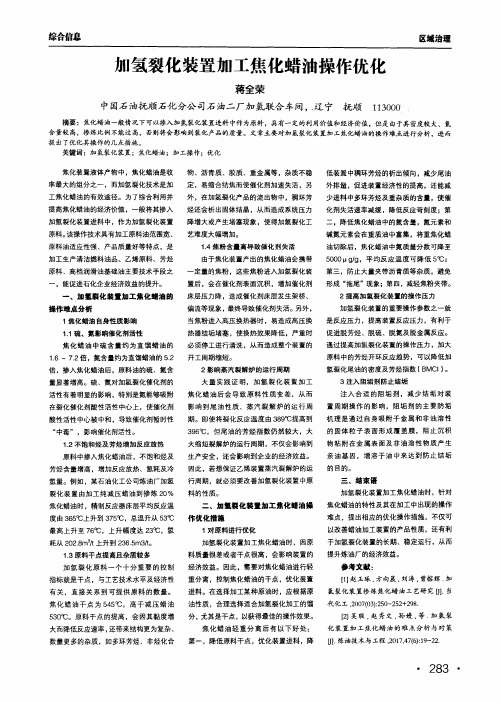
物、沥青质、胶质、重金属等,杂质不稳 定.易缩合结焦而使催化剂加速失活,另 外,在加氢裂化产品的流出物中,稠环芳 烃还会析出固体结晶.从而造成系统压力 降增大或产生堵塞现象,使得加氢裂化工 艺难度大幅增加。
1.4焦粉含量高导致催化剂失活 由于焦化装置产出的焦化蜡油会携带 一定是的焦粉,这些焦粉进入加氢裂化装 置后,会在催化剂表面沉积。增加催化剂 床层压力降,造成催化剂床层发生架桥、 偏流等现象。最终导致催化剂失活。另外, 当焦粉进入高压换热器时,易造成高压换 热器结垢堵塞,使换热效果降低,严重时 必须停工进行清洗。从而造成整个装置的 开工周期缩短。 2影响蒸汽裂解炉的运行周期 大量实践证明,加氢裂化装置加工 焦化蜡油后会导致原料性质变差,从而 影响到尾油性质、蒸汽裂解炉的运行周 期。即使将裂化反应温度由389℃提高到 396℃,但尾油的芳烃指数仍然较大,大 大缩短裂解炉的运行周期.不仅会影响到 生产安全。还会影响到企业的经济效益。 因此。若想保证乙烯装置蒸汽裂解炉的运 行周期,就必须要改善加氢裂化装置中原 料的性质。 二、加氢裂化装置加工焦化蜡油操 作优化措施 1对原料进行优化 加氢裂化装置加工焦化蜡油时。因原 料质量很差或者干点很高,会影响装置的 经济效益。因此,需要对焦化蜡油进行轻 重分离,控制焦化蜡油的干点.优化装置 进料。在选择加工某种原油时,应根据原 油性质,合理选择适合加氢裂化加工的馏 分,尤其是干点,以获得最佳的操作效果。 焦化蜡油轻重分离后有以下好处: 第一,降低原料干点,优化装置进料,降
· 283 ·
低装置中稠环芳烃的析出倾向。减少尾油 外排量,促进装置经济性的提高.还能减 少进料中多环芳烃及重杂质的含量,使催 化剂失活速率减缓,降低反应苛刻度:第 二。降低焦化蜡油中的氮含量,氮元素和 碱氮元素会在重质油中富集,将重焦化蜡 油切除后。焦化蜡油中氮质量分数可降至 5000 u g/g,平均反应温度可降低5℃; 第三,防止大量夹带沥青质等杂质.避免 形成“拖尾”现象;第四.减轻焦粉夹带。
03蜡油加氢裂化装置

3蜡油加氢裂化装置预评价报告3.1装置概况根据总加工流程安排,需建设一套220×104t/a加氢裂化装置。
加工原料为苏丹混合原油的减压蜡油,所用氢气由PSA装置提供。
采用一段全循环流程,最大限度生产中间馏分油,作为全厂产品调合组份。
少量的加氢裂化尾油去重油催化裂化作为原料,冷低分气脱硫后去PSA装置进行氢气提浓,含硫气体和不稳定石脑油至轻烃回收装置。
3.1.1装置名称中国石油天然气股份有限公司广西石化分公司蜡油加氢裂化装置。
3.1.2装置规模及设计能力装置规模为220×104t/a,实际加工量为219.78×104t/a。
年操作时数8400小时。
3.1.3原料及产品3.1.3.1原料来源装置加工原料油为常减压蒸馏装置的减一、减二和减三线蜡油219.78×104t/a。
3.1.3.2产品及去向产品品种及去向见表3.1-1。
装置产品:石脑油、航煤、柴油和尾油。
副产品:冷低分气脱硫后去PSA氢提浓装置,汽提塔顶气至轻烃回收装置。
产品品种及去向见表3.1-1。
3.1.3.3物料平衡装置物料平衡见表3.1-2。
3.1.4公用工程消耗3.1.4.1水用量水用量见表3.1-3。
3.1.4.2电用量电用量见表3.1-4。
3.1.4.3蒸汽用量装置蒸汽用量见表 3.1-5。
3.1.4.4燃料用量燃料用量见表3.1-6。
3.1.4.5压缩空气用量压缩空气用量见表 3.1-7。
3.1.4.6氮气用量装置氮气用量见表 3.1-8。
3.1.5装置的平面布置占地面积:180×90=16200 m2。
压缩机厂房分两层布置,房内设置桥式吊车。
装置的所有管桥及构架均采用钢结构。
装置内留有足够的吊装检修用场地,以满足大型吊车接近与回旋。
反应构架上方设置单轨电动吊车与手动葫芦,大型泵的上方设置有检修用手动葫芦或检修吊梁,以方便检修与维护。
管桥成组合式布置,仪表电缆、电气电缆拟以槽盒的形式布置在管桥最上层,便于检修和维护,同时节省地下空间,所有设备与建、构筑物均沿管桥两侧布置;管桥下设置泵房。
蜡油加氢裂化装置掺炼加氢精制柴油的探讨

馏程 ħ ? 初馏点 5% 0% 1 0% 2 0% 5 0% 6 3 0 2 3 3 4 3 4 9 3 6 6 4 0 0 4 2 1 4 5 7 4 7 5 5 2 1 2 9 9 3 3 0 3 4 6 3 6 3 3 9 9 4 1 1 4 5 6 4 7 5 5 2 2 3 3 4 3 4 8 3 5 9 2 6 8 2 1 1 1 7 8
0% 9 5% 9 终馏点
2 0 1 7 0 5 1 6;修改稿收到日期 : 2 0 1 7 0 7 1 6。 收稿日期 : 方友 , 从事加氢裂化工艺管理工作 。 作者简介 : 方友 , : 。 E m a i l f a n o u@c n o o c . c o m . c n 通讯联系人 : g y
1 5] 精制柴油的可行性及其经济效益 [ 。
裂化反应床层 。 蜡 油 加 氢 裂 化 装 置 掺 炼 加 氢 精 制 柴油前以 减 二 线 蜡 油 、 减三线蜡油和焦化蜡油为 原料 , 实际原料加工质量比为 5 掺炼后 0ʒ2 5ʒ2 5, 维持设计的 3 种 蜡 油 间 的 比 例 不 变 。 蜡 油 转 化 率 并尽量维持稳定 。 控制在 8 7%ʃ0 . 5% , 1 1 原料油性质 表 1 为掺炼加氢 精 制 柴 油 前 后 混 合 原 料 油 的 性质对比 。 掺炼前后原料性质基本保持稳定 , 加氢
第1 1期
方 友, 等. 蜡油加氢裂化装置掺炼加氢精制柴油的探讨
5 7
精制柴油硫 、 氮 含 量 很 低, 掺 炼 量 又 较 少, 不影响 氮 含 量, 混 合 进 料 的 硫、 氮含量主 混合进料的 硫 、 要受蜡油进料硫 、 氮含量的变化影响( 主要是原油 。 虽然 加 氢 精 制 柴 油 馏 程 较 轻 , 但因 品种的变化 ) 为掺炼量少 , 并未影 响 混 合 原 料 的 馏 程 , 而且混合 没有出现 原料高压 进 料 泵 的 运 行 也 未 受 到 影 响 , 振动增大的问题 。 通过掺炼硫 、 氮 含 量 很 低 的 加 氢 精 制 柴 油, 有 效降低了 装 置 混 合 进 料 的 硫 含 量 和 密 度 , 硫质量
加氢裂化装置工艺流程
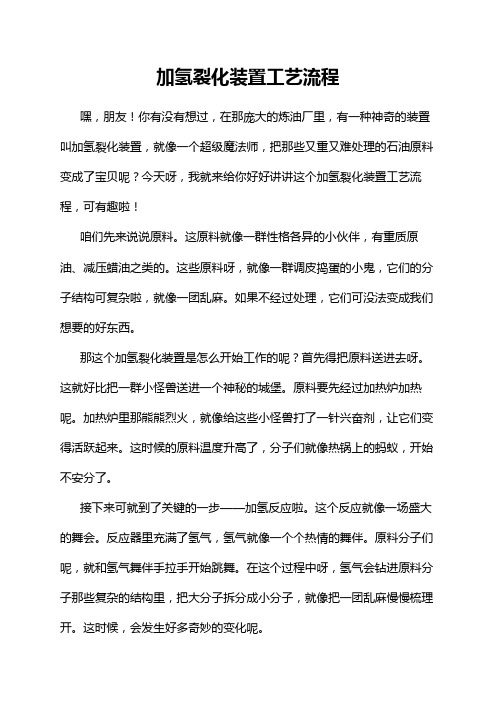
加氢裂化装置工艺流程嘿,朋友!你有没有想过,在那庞大的炼油厂里,有一种神奇的装置叫加氢裂化装置,就像一个超级魔法师,把那些又重又难处理的石油原料变成了宝贝呢?今天呀,我就来给你好好讲讲这个加氢裂化装置工艺流程,可有趣啦!咱们先来说说原料。
这原料就像一群性格各异的小伙伴,有重质原油、减压蜡油之类的。
这些原料呀,就像一群调皮捣蛋的小鬼,它们的分子结构可复杂啦,就像一团乱麻。
如果不经过处理,它们可没法变成我们想要的好东西。
那这个加氢裂化装置是怎么开始工作的呢?首先得把原料送进去呀。
这就好比把一群小怪兽送进一个神秘的城堡。
原料要先经过加热炉加热呢。
加热炉里那熊熊烈火,就像给这些小怪兽打了一针兴奋剂,让它们变得活跃起来。
这时候的原料温度升高了,分子们就像热锅上的蚂蚁,开始不安分了。
接下来可就到了关键的一步——加氢反应啦。
这个反应就像一场盛大的舞会。
反应器里充满了氢气,氢气就像一个个热情的舞伴。
原料分子们呢,就和氢气舞伴手拉手开始跳舞。
在这个过程中呀,氢气会钻进原料分子那些复杂的结构里,把大分子拆分成小分子,就像把一团乱麻慢慢梳理开。
这时候,会发生好多奇妙的变化呢。
我曾经和一个在炼油厂工作的老师傅聊过这个加氢反应。
老师傅满脸自豪地说:“哎呀,你可别小看这个反应,这就像魔法一样。
那些又大又笨的分子,在氢气的作用下,一下子就变得轻巧灵活了。
”我当时就好奇地问:“老师傅,这中间不会出啥岔子吧?”老师傅哈哈一笑说:“当然得小心伺候着啦。
反应的条件可严格了,就像照顾一个娇贵的小婴儿。
温度、压力、氢气的量,哪一个没控制好都不行。
”在加氢反应进行的时候,反应器里就像一个热闹的小世界。
各种分子在那里碰撞、结合、拆分。
就像一群小朋友在游乐场里跑来跑去,一会儿这个和那个凑到一起,一会儿又分开了。
这时候产生的一些产物已经开始有点像我们想要的汽油、柴油之类的东西啦,但还不够纯粹呢。
反应完了之后呀,还得经过分离工序。
这分离工序就像一场大筛选。
270万吨/年蜡油加氢裂化装置开工总结

270万吨/年蜡油加氢裂化装置开工总结罗亮;童军;田亮;武寨虎【期刊名称】《广州化工》【年(卷),期】2014(000)019【摘要】The 2 700 kt/a VGO Hydrocracking Unit of Sichuan Petrochemical Co., Ltd.was handed on the December 28 and it produced on February 28 , 2014 , to achieve successful start -up.The process of original work , such as air, drying catalyst, water transport, dry fractionation of cold and hot oilcatalyst , catalyse presulfurization , switching materials, qualified products were reviewed in detail to assess the operation of the device , the device problems and coping measures.%四川石化公司270万吨/年蜡油加氢裂化装置于2012年12月28日中交,2014年2月28日出合格产品,实现了一次开车成功。
本文对原始开工的过程,如气密、烘炉、催化剂装填、分馏水联运、催化剂干燥、分馏冷热油运、催化剂预硫化、切换原料、出合格产品进行详细的阐述,对装置运行的情况进行评估,提出了装置存在的问题和应对的手段。
【总页数】3页(P152-154)【作者】罗亮;童军;田亮;武寨虎【作者单位】中国石油四川石化有限责任公司,四川彭州 611930;中国石油四川石化有限责任公司,四川彭州 611930;中国石油四川石化有限责任公司,四川彭州 611930;中国石油四川石化有限责任公司,四川彭州 611930【正文语种】中文【中图分类】TE624【相关文献】1.200万吨/年蜡油加氢裂化装置进料泵密封改型 [J], 高仁鹏;李海林;朱狄;纳赛尔·热依木;吴长春2.400万吨/年蜡油加氢裂化装置运行分析 [J], 熊守文3.220万吨/年加氢裂化装置开工技术总结 [J], 张翼;涂银堂;陶峰4.270万吨/年加氢裂化装置开工事故总结 [J], 公为军;高攀;韩杰定5.400万吨/年蜡油加氢裂化装置动态仿真 [J], 郭振刚;邹利妮因版权原因,仅展示原文概要,查看原文内容请购买。
- 1、下载文档前请自行甄别文档内容的完整性,平台不提供额外的编辑、内容补充、找答案等附加服务。
- 2、"仅部分预览"的文档,不可在线预览部分如存在完整性等问题,可反馈申请退款(可完整预览的文档不适用该条件!)。
- 3、如文档侵犯您的权益,请联系客服反馈,我们会尽快为您处理(人工客服工作时间:9:00-18:30)。
920
1
注:*表示间断用量。
1.4.2
电用量见表1-4。
表1-4电用量
序号
电压V
轴功率kW
备注
1
6000V
12750
2
380V
2100
3
220V
150
合计
15000
1.4.3
装置蒸汽用量见表1-5。
表1-5蒸汽用量
蒸汽负荷(t/h)
0.4MPa
1.0MPa
3.5MPa
汽包产汽
用汽
汽包
产汽
背压
产汽
本装置高压空冷器管箱为板焊丝堵式结构。根据操作条件,管箱材料采用碳钢,换热管材料为碳钢。为防止NH3(H2S)的腐蚀,在每根换热管的入口端设置一段不小于600mm长的不锈钢衬管。
(6)压缩机
压缩机是装置中关键机械设备。新氢压缩机选用往复式,开二备一,为保证装置长周期稳定运行,考虑新氢压缩机由国外引进;循环氢压缩机选用背压式蒸汽透平驱动离心式压缩机一台,由国内生产。
表3.2-1主要操作条件
项目
操作条件
精制段
裂化段
后精制段
催化剂
UF-210stars
HC-115
UF-310
体积空速,h-1(对新鲜进料)
工艺流程
单段全循环
工艺条件
混合进料比
1.7
高压分离器压力,MPa
15.2
反应器入口氢油比
713:1
反应温度,℃
精制段:初期375,末期420;
裂化段:初期397,末期428;
分馏塔进料加热炉设计负荷52000 kW,考虑采用立管单排单面辐射管结构型式。
根据炉子的工艺特点,初步选用Φ168管径4管程。
分馏塔进料加热炉采用立管立式炉,循环氢加热炉排出的高温烟气进入分馏塔进料加热炉对流室,回收烟气余热。
(5)冷换设备
本装置高压换热器的管程、壳程均属高压的有10台,管程高压、壳程低压的有4台。根据操作条件,管、壳程壳体的主体材料分别选用2.25Cr-1Mo,换热管材料选用oCr18Ni10Ti。管程采用螺纹锁紧环式结构。
原料油换热系统采用注阻垢剂设施。
航煤出装置线均匀加入抗氧剂。
采用循环氢聚结除液设施。
催化剂采用器外再生。
为确保催化剂、高压设备及操作人员的安全,设置两个压力等级的紧急泄压系统。
2.1.2
(1)反应部分
原料油与柴油换热后通过原料油自动反冲洗过滤器除去大于25μm的固体颗粒,进入原料油缓冲罐,经反应进料泵升压后与反应流出物换热,再与经过换热和加热的循环氢混合,然后进入加氢反应器进行加氢精制、加氢裂化反应。反应流出物与原料油、循环氢换热至适宜温度进入热高压分离器。反应流出物在热高压分离器进行气、液分离,热高分气体与冷低分油换热、冷却后进入冷高压分离器进行油、水、气三相分离。冷高分气经循环氢压缩机入口分液罐去循环氢压缩机升压;冷高分水至酸性水汽提装置统一处理;冷高分油至冷低压分离器进一步闪蒸,冷低分气去脱硫塔;冷低分水与冷高分水一起至酸性水汽提装置统一处理。
冷低分油与热高分气换热后至分馏部分。热高分油至热低压分离器进一步闪蒸,热低压分离器气相与热水换热,并冷却后至冷低压分离器。热低压分离器液体直接至分馏部分。
新氢经新氢压缩机升压后与循环氢压缩机来的循环氢混合,一路用作混合氢气,另一路用作反应器的急冷氢。
参见附图3-1。
(2)分馏部分
来自反应部分的低分油进汽提塔,塔底通入水蒸汽汽提,脱除H2S。塔顶气相经空冷器、后冷器冷凝冷却后进汽提塔顶回流罐进行油、气、水三相分离,气体去轻烃回收装置进一步回收液化气;含硫污水去酸性水汽提装置统一处理;塔顶油相一部分送回塔顶作为回流,另一部分送至石脑油加氢精制装置。汽提塔底油作为主分馏塔进料。
1.1
蜡油加氢裂化装置。
1.2
装置规模为220×104t/a,实际加工量为219.78×104t/a。年操作时数8400小时。
1.3
1.3.1
装置加工原料油为常减压蒸馏装置的减一、减二和减三线蜡油219.78×104t/a。
1.3.2
产品品种及去向见表1-1。
装置产品:石脑油、航煤、柴油和尾油。
副产品:冷低分气脱硫后去PSA氢提浓装置,汽提塔顶气至轻烃回收装置。
根据炉子的工艺特点,初步选用Φ152管径8管程,最小壁厚16mm。
由于受循环氢压缩机出口压力的限制,要求尽量减少炉管压降,加氢反应进料加热炉均设计为纯辐射立式炉型,其排出的高温烟气进入分馏塔进料加热炉对流室,回收烟气余热。炉膛用一个单排双面辐射辐射室或两个单排双面辐射室。
(4)分馏塔进料加热炉
分馏塔进料加热炉管内介质为含氢量较低,操作出口温度377℃,操作出口压力为0.2MPa,在此工艺条件下,炉管材质采用T9。
原料油进装置后,首先经自动反冲洗过滤处理,除去大于25微米的颗粒状杂质,防止其沉积在催化剂表面,以减缓反应器压力降的增加,延长装置开工周期。
装置内原料油缓冲罐采用惰性气体保护,避免原料油与空气接触,以减轻原料油在换热器、加热炉管及反应器中的结焦程度。
分馏部分采用先汽提后分馏的四塔流程。
装置内设有冷低分气脱硫设施。
1.4
1.4.1
水用量见表1-3。
表1-3装置给排水用量表
用水地点
给水t/h
排水t/h
新鲜水
除氧水
除盐水
净化水
循环水
含油
污水
含盐
污水
含硫污水
循环
热水
生活
污水
水冷却器
900
900
机泵冷却
25
5
20
配制药剂
反应产物注水
11
11
22
1.0MPa蒸汽
48
汽提蒸汽
5
6
生活用水
1*
1
合计
1
48
11
11
925
10
冷高压分离器等高压容器均为锻焊结构,采用常规设计。主体材料选用16Mn(R-HIC)纯净钢。
(2)反应器
本装置反应器采用单系列,分别设有加氢精制反应器、加氢裂化反应器各一台,采用热壁锻焊结构。主体材质根据操作条件和Nelson曲线,确定为2.25Cr-1Mo-0.25V(SA336F22V),内壁堆焊TP.309L+TP.347,以防止高温H2S-H2腐蚀。反应器按应力分析法进行设计,反应器采用国产或进口,应根据项目工期要求及当时国内外市场的供货情况来确定。
装置
注汽
加热
用汽
汽包
产汽
汽机
用汽
装置
注汽
加热
用汽
-17
6
-28
-71
5
71
1.4.4
燃料用量见表1-6。
表3.1-6燃料用量
序号
使用地点
燃料油kg/h
燃料气kg/h
备注
1
循环氢加热炉
1176
(热值41.868MJ/kg)
2
分馏塔进料加热炉
4023
合计
5199
1.4.5
压缩空气用量见表1-7。
表1-7装置压缩空气用量
表3.2-2主要操作条件
名称
塔顶温度,℃
塔顶压力,MPa(G)
汽提塔
159
1.05
分馏塔
131
0.115
航煤汽提塔
204
0.13
柴油汽提塔
320
0.136
低分气脱硫塔
40
0.8
2.2
2.2.1
(1)容器
热高压分离器为热壁锻焊结构,主体材料选用SA336F22(2.25Cr-1Mo),内壁堆焊TP.309L+TP.347,按应力分析法进行设计。
压缩机厂房分两层布置,房内设置桥式吊车。
装置的所有管桥及构架均采用钢结构。
装置内留有足够的吊装检修用场地,以满足大型吊车接近与回旋。
反应构架上方设置单轨电动吊车与手动葫芦,大型泵的上方设置有检修用手动葫芦或检修吊梁,以方便检修与维护。
管桥成组合式布置,仪表电缆、电气电缆拟以槽盒的形式布置在管桥最上层,便于检修和维护,同时节省地下空间,所有设备与建、构筑物均沿管桥两侧布置;管桥下设置泵房。
(7)机泵
原料油泵由于介质包括新鲜进料和循环油,且温度较高、流量大、扬程高,所以应选用双壳体多级离心泵。鉴于国内大泵的制造技术与国外相比还存在一定差距,为保证装置长周期运转,本可研推荐引进反应进料泵。
(8)设备防腐措施
加氢裂化装置中,通常见到的腐蚀现象有氢腐蚀和硫化氢腐蚀,在许多设备及管道中则存在着这两种介质的同时腐蚀。在高温高压下,氢对钢有强烈的脆化作用,腐蚀的程度取决于操作温度、氢分压及合金元素的添加情况;硫化氢的腐蚀程度主要取决于硫化氢的浓度和操作温度。浓度越大腐蚀越厉害。对于温度来说,200~250℃以下不含水的硫化氢气体,对钢铁不产生腐蚀或腐蚀甚微。当温度大于260℃时,腐蚀加快。装置设备设计按API941《临氢作业用钢防止脱碳和开裂的操作极限》曲线(Nelson曲线)选用相应的材料;凡有高温H2S+ H2腐蚀的部位,材料的腐蚀率按照柯珀(Couper)曲线进行估算,采用内壁堆焊309L+347L等相应的防腐措施;在湿硫化氢应力腐蚀和氢致开裂环境下工作的设备,其主体材质采用16MnR(R-HIC)或16Mn(R-HIC)纯净钢。
序号
项目
压力
MPa(g)
连续Nm3/min
间断Nm3/min
正常
最大
正常
最大
1
净化压缩空气
0.6
6
2
非净化压缩空气
0.6
20
合计
6
20
1.4.6
装置氮气用量见表1-8。