螺旋挤压机
挤压机螺杆几何参数设计
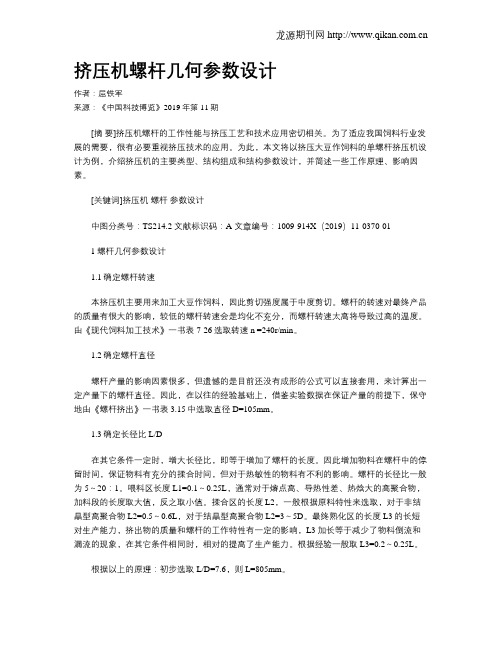
挤压机螺杆几何参数设计作者:屈铁军来源:《中国科技博览》2019年第11期[摘要]挤压机螺杆的工作性能与挤压工艺和技术应用密切相关。
为了适应我国饲料行业发展的需要,很有必要重视挤压技术的应用。
为此,本文将以挤压大豆作饲料的单螺杆挤压机设计为例,介绍挤压机的主要类型、结构组成和结构参数设计,并简述一些工作原理、影响因素。
[关键词]挤压机螺杆参数设计中图分类号:TS214.2 文献标识码:A 文章编号:1009-914X(2019)11-0370-011螺杆几何参数设计1.1确定螺杆转速本挤压机主要用来加工大豆作饲料,因此剪切强度属于中度剪切。
螺杆的转速对最终产品的质量有很大的影响,较低的螺杆转速会是均化不充分,而螺杆转速太高将导致过高的温度。
由《现代饲料加工技术》一书表7-26选取转速n =240r/min。
1.2确定螺杆直径螺杆产量的影响因素很多,但遗憾的是目前还没有成形的公式可以直接套用,来计算出一定产量下的螺杆直径。
因此,在以往的经验基础上,借鉴实验数据在保证产量的前提下,保守地由《螺杆挤出》一书表3.15中选取直径D=105mm。
1.3确定长径比L/D在其它条件一定时,增大长径比,即等于增加了螺杆的长度。
因此增加物料在螺杆中的停留时间,保证物料有充分的揉合时间,但对于热敏性的物料有不利的影响。
螺杆的长径比一般为5~20:1。
喂料区长度L1=0.1~0.25L,通常对于熔点高、导热性差、热焓大的高聚合物,加料段的长度取大值,反之取小值。
揉合区的长度L2,一般根据原料特性来选取,对于非结晶型高聚合物L2=0.5~0.6L,对于结晶型高聚合物L2=3~5D。
最终熟化区的长度L3的长短对生产能力,挤出物的质量和螺杆的工作特性有一定的影响,L3加长等于减少了物料倒流和漏流的现象,在其它条件相同时,相对的提高了生产能力。
根据经验一般取L3=0.2~0.25L。
根据以上的原理:初步选取L/D=7.6,则L=805mm。
螺旋式栅渣压窄机
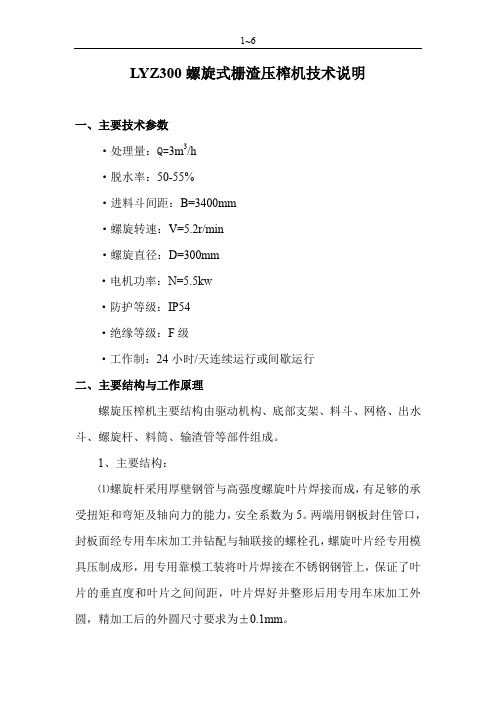
LYZ300螺旋式栅渣压榨机技术说明一、主要技术参数·处理量:Q=3m3/h·脱水率:50-55%·进料斗间距:B=3400mm·螺旋转速:V=5.2r/min·螺旋直径:D=300mm·电机功率:N=5.5kw·防护等级:IP54·绝缘等级:F级·工作制:24小时/天连续运行或间歇运行二、主要结构与工作原理螺旋压榨机主要结构由驱动机构、底部支架、料斗、网格、出水斗、螺旋杆、料筒、输渣管等部件组成。
1、主要结构:⑴螺旋杆采用厚壁钢管与高强度螺旋叶片焊接而成,有足够的承受扭矩和弯矩及轴向力的能力,安全系数为5。
两端用钢板封住管口,封板面经专用车床加工并钻配与轴联接的螺栓孔,螺旋叶片经专用模具压制成形,用专用靠模工装将叶片焊接在不锈钢钢管上,保证了叶片的垂直度和叶片之间间距,叶片焊好并整形后用专用车床加工外圆,精加工后的外圆尺寸要求为±0.1mm。
⑵料筒壁厚4mm,内径305mm。
⑶驱动机构采用立式减速机,该机传动扭矩大,噪音低,使用寿命长等特点。
2、工作原理:栅渣进入位于料筒上方的入料口内,当驱动装置驱动螺旋杆转动时,栅渣被螺旋推动着前进,并被压紧推入输渣管内排至下道工序。
压出的水份由料筒下部泄水孔排出由接水槽导出。
三、主要零部件材料·底部支架:304不锈钢·料斗:304不锈钢·网格:304不锈钢·出水斗:304不锈钢·螺旋杆:304不锈钢·料筒:304不锈钢·输渣管:304不锈钢·紧固件:1Cr18Ni9Ti不锈钢四、电器控制系统设有就地控制箱进行现场控制,并设有PLC接口,同时设有起停控制按钮、起停指示灯、转换开关、紧急停车按钮、故障报警指示灯。
五、设备设计、制造、检验所遵循的标准目录该产品在设计、制造、检验、包装运输及安装过程中所遵循的标准均为国标(GB)或部标(JB)这些通用标准目录省略,只提供专用标准目录如下:JB2932-86 水处理设备制造技术条件JB/ZQ4000.2-86 切削加工件通用技术条件JB/ZQ4000.3-86 焊接件通用技术条件JB/ZQ4000.5-86 铸件通用技术条件JB/ZQ4000.7-86 锻件通用技术条件JB/T5000.5-98 有色金属铸件通用技术条件JB/ZQ4000.9-86 装配技术条件JB/ZQ4000.10-86 涂装通用技术条件JB/ZQ4286-86 包装技术通用技术条件GB1176 铸造铜合金技术条件GB1220 不锈钢棒GB6414 铸件尺寸公差GB9439 灰铸铁件GB3797-89 装有电子器件电控箱技术条件GB4720-84 低压电器电控箱GB/T4942.2-93 低压电器外壳防护等级GB8923-85 涂装前钢材表面锈蚀等级和除锈等级GB4879-99 防锈包装YJ010 抛丸喷砂技术条件及检验方法JB/ZQ4000.1-86 产品检验通用技术要求适用于本产品的“产品出厂前的检验规则和方法”适用于本产品的“产品安装手册”及“产品安装检验规则和方法”适用于本产品的“产品型式试验规则”“产品的试验方法”六、设备的可靠性及耐久性1、设备无故障时间不少于10000小时。
螺旋挤压分离机设计和力学分析
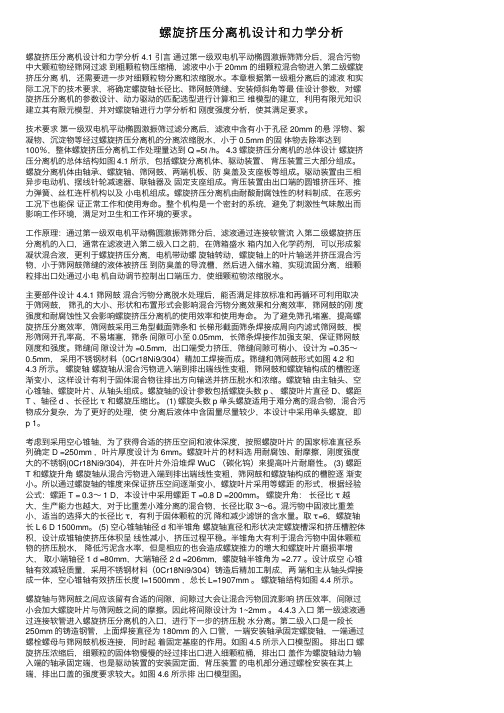
螺旋挤压分离机设计和⼒学分析螺旋挤压分离机设计和⼒学分析 4.1 引⾔通过第⼀级双电机平动椭圆激振筛筛分后,混合污物中⼤颗粒物经筛⽹过滤到粗颗粒物压缩桶,滤液中⼩于 20mm 的细颗粒混合物进⼊第⼆级螺旋挤压分离机,还需要进⼀步对细颗粒物分离和浓缩脱⽔。
本章根据第⼀级粗分离后的滤液和实际⼯况下的技术要求,将确定螺旋轴长径⽐、筛⽹⿎筛缝、安装倾斜⾓等最佳设计参数,对螺旋挤压分离机的参数设计、动⼒驱动的匹配选型进⾏计算和三维模型的建⽴,利⽤有限元知识建⽴其有限元模型,并对螺旋轴进⾏⼒学分析和刚度强度分析,使其满⾜要求。
技术要求第⼀级双电机平动椭圆激振筛过滤分离后,滤液中含有⼩于孔径 20mm 的悬浮物、絮凝物、沉淀物等经过螺旋挤压分离机的分离浓缩脱⽔,⼩于 0.5mm 的固体物去除率达到100%,整体螺旋挤压分离机⼯作处理量达到 Q =5t /h。
4.3 螺旋挤压分离机的总体设计螺旋挤压分离机的总体结构如图 4.1 所⽰,包括螺旋分离机体、驱动装置、背压装置三⼤部分组成。
螺旋分离机体由轴承、螺旋轴、筛⽹⿎、两端机板、防臭盖及⽀座板等组成。
驱动装置由三相异步电动机、摆线针轮减速器、联轴器及固定⽀座组成。
背压装置由出⼝端的圆锥挤压环、推⼒弹簧、丝杠连杆机构以及⼩电机组成。
螺旋挤压分离机由耐酸耐腐蚀性的材料制成,在恶劣⼯况下也能保证正常⼯作和使⽤寿命。
整个机构是⼀个密封的系统,避免了刺激性⽓味散出⽽影响⼯作环境,满⾜对卫⽣和⼯作环境的要求。
⼯作原理:通过第⼀级双电机平动椭圆激振筛筛分后,滤液通过连接软管流⼊第⼆级螺旋挤压分离机的⼊⼝,通常在滤液进⼊第⼆级⼊⼝之前,在筛箱盛⽔箱内加⼊化学药剂,可以形成絮凝状混合液,更利于螺旋挤压分离,电机带动螺旋轴转动,螺旋轴上的叶⽚输送并挤压混合污物,⼩于筛⽹⿎筛缝的液体被挤压到防臭盖的导流槽,然后进⼊储⽔箱,实现流固分离,细颗粒排出⼝处通过⼩电机⾃动调节控制出⼝端压⼒,使细颗粒物浓缩脱⽔。
双螺杆挤压机

1.2.2 挤压型膨化设备分类
1)按照挤压过程剪切力 2)按照挤压机受热方式 3)按照螺杆根数 4)按照物料水分 5)其他类型
(一)按挤压过程剪切力的高低分类
(1)高剪切力挤压机: 1)挤压过程中能够产生较高剪切力的挤压机; 2)螺杆上常带有反向螺杆; 3)作业性较好,可方便地生产出多种挤压产品。 4)常具有较高转速和较高挤压温度。 5)适于简单形状产品的生产。
双螺杆挤压机:两对相互连续啮合的反 向或同向旋转的螺杆靠正位移原理强制 输送物料,使物料在机内分布均匀
多螺杆挤压机
(四)按螺杆转速进行分类
(1)普通挤压机 (2)高速挤压机 (3)超高速挤压机
1.螺杆挤压原理:
1)螺杆上的螺旋推挤可塑性物料向前运 动;
2)物料在出口模具的背后受阻形成压力;
1.2.1 挤压型膨化过程
1)是一个高温高压的过程;
2)可较方便地调节挤压过程的压力剪切力,作 用和时间;
3)可将挤压过程应用于某些需高温高压的生化 反映过程;
大多数的食品挤压机是将加热、蒸煮与挤 压成型两种作用有机地结合起来,使原料经挤压 机后,成为具有一定形状和质构的熟化或半熟化 的产品。
3)螺杆的旋转和摩擦生热及外部加热, 使物料在机筒内受到高温高压剪切力的 作用,最后从摸孔中挤出。
2.单螺杆挤压机 图中所示为典型的单螺杆挤压 机主要元件工作原理图。单螺杆挤压机由圆筒 形腔体和在其中旋转的螺杆组成。为了实现不 同的使用目的,螺杆和腔体都可以设计成为逐 渐变细的形状;然而,大多数单螺杆挤压机的 几何形状为圆柱形。物料的流动是在螺杆和腔 体之间的通道中沿着腔体的轴向作螺旋运动。
为了使物ቤተ መጻሕፍቲ ባይዱ在机筒内承受逐渐增大的压缩力,常 将螺杆与机筒配合为如下三种型式 :
LSY260螺旋输送压榨机技术说明

技术附件1.螺旋输送压榨机(LSY260x4.0x3-Z)1.1适用范围LSY型螺旋输送压榨机主要用于输送格栅并压榨脱水。
1.2供货范围卖方提供的无轴螺旋输送机为倾斜布置形式,用于输送和压榨经挠起来的栅渣。
螺旋输送压榨机的接口与相应的格栅的卸料口相配合。
1.3 技术参数输送能力:2~3m3/h长度:4.0m倾斜角度:3°螺旋体直径:φ220 mm电机功率:1.1Kw额定转速:24rpm电机防护等级:IP55绝缘等级:F级数量:1台1.4 结构特点1.无轴螺旋输送机有合适的叶片直径,在最大输送长度下具有足够的强度与刚度。
输送具有合适的旋转速度,既能输送栅渣或污泥又不造成阻塞。
2.传动形式采用电机减速机与螺旋体驱动轴直连。
3.驱动装置适用于户外使用,电机减速装置采用轴装式减速机的结构形式,是传动效率高、低噪音、使用寿命长、运行平稳可靠的产品。
4.无轴螺旋片具有足够的强度和刚度,螺旋叶片厚度16mm,螺旋片宽度50mm。
5.无轴螺旋输送机有型钢支撑固定在混凝土的土建基础上。
6.螺旋输送槽厚度2.5mm,制成U型断面,除进料口敞开外,其余部分沿螺旋槽加平盖封闭。
7.输送机能每日24小时连续运行。
8.输送机的出口设置卸料漏斗,与后序处理设备的进料口相衔接。
输送机槽内的耐磨衬板能方便地更换,使用寿命2年以上。
1.5引用和执行标准GB1220—84 不锈钢GB3280—84 不锈钢热轧钢板GB4227—84 不锈钢热轧等边角钢GB2270—80 不锈钢无缝钢管GB983—85 不锈钢焊条GB4942.1—85 电机外壳防护Q/ZB75—86 机械加工通用技术条件1.6 主要材料及产品材质螺旋叶片不锈钢304输送机壳体、盖板不锈钢304筛管不锈钢304耐磨衬条(或衬板)耐磨HDPE紧固件不锈钢304支架、传动轴碳钢热镀锌减速电机 SEW3. 螺旋输送压榨一体机参数表。
双螺杆挤压膨化机在水产饲料应用上的优势

双螺杆挤压膨化机在水产饲料应用上的优势据有关资料统计,我国目前每年水产饲料的需求量约为3000万t,但仅有1/3使用工业配合水产饲料,而其中绝大部分为传统的制粒工艺所生产的硬颗粒水产饲料。
随着水产养殖业向规模化、集约化、专业化方向的发展,对水产饲料的要求也越来越高,传统制粒机生产的配合水产饲料存在着水中稳定性差、沉降速度快、易造成饲料散失和水质污染等弊端,已越来越不适应现代水产养殖业发展的需要。
采用挤压膨化技术加工的水产饲料能较好地解决这些问题,可以生产浮性料、慢沉料和沉性料等适合现代水产养殖业发展的理想饲料形态,具有极大的发展空间。
在我国有着较好的市场前景。
目前,我国水产饲料生产厂家由于受到原有生产工艺条件和设备等方面的限制,挤压膨化水产饲料只占很小一部分,而且以单螺杆挤压膨化机为主,主要是由于进口双螺杆挤压膨化机投资成本太高,而国产双螺杆挤压膨化机技术性能和质量等方面尚有差距、也缺乏针对饲料工业特点应用的大产量机型,尽管从单螺杆和双螺杆的挤压膨化原理及机体结构分析就可看出双螺杆挤压膨化机具有明显的优势并具有更好的性价比,但相对于食品加工业的应用仍要逊色得多。
近年来,随着国内企业引进、消化吸收国外先进技术使国产双螺杆挤压膨化机生产技术水平不断提高,特别是针对水产饲料生产推出了双螺杆挤压膨化专用机型,使用单螺杆挤压膨化机的投资同样可以选用双螺杆机型,从而改变了人们以往以投资成本高阻碍使用双螺杆机型的观念。
为了适应我国饲料工业发展的需要和提高产品质量,很有必要重视和推广双螺杆挤压膨化技术在饲料加工中的应用,发挥出双螺杆挤压膨化机的原料适应性更宽、产品适应性更广、产品内在和外观质量更好、同等动力下产量更高、熟化均质效果更好、工艺操作更简便、易损件磨损更轻、生产成本更低的诸多优势,让饲料加工企业在新建、扩建水产饲料及宠物食品等特种饲料生产线时,有更充分的理由选择使用双螺杆挤压膨化机。
1挤压膨化原理挤压膨化加工定义为这样一种工艺过程,即:迫使饲料/食品原料在一种或几种工艺条件下(如搅拌、加热、剪切)流动通过压模,令物料成形和/或喷发汽化(RossenandMiller,1973)。
第四章-螺杆挤出机-1(新)

三、分类
按螺杆数目分
单、双、多 (前两种用得最多)
按喂料方式分
冷喂、热喂(要预热>50℃)
按螺杆安装位置分
卧式、立式
按螺杆转速分
常规(100~300r/min)、高速(300~900r/min)、 超高速(900~1500r/min)
四、规格表示及技术特征
挤出成型过程可分为如下三个阶段:
1、塑化阶段 在挤出机上进行塑料的加热和混炼, 使固态原料变为均匀的粘性流体。
2、成型阶段 在挤出机螺杆的作用下,熔融塑料 以一定的压力和速度连续通过装在挤出机上的成型 机头,获得一定的断面形状。
3、定形阶段 通过冷却等方法使熔融塑料已获取 的形状固定下来,成为固态制件。
2. 摩擦系数 f
在螺杆结构参数确定,以及工艺参 数设定后,移动角只与摩擦因数 有关。
a. 提高螺杆光洁度;涂F4
b. 在料筒上开设纵向槽沟,提高 物料与机筒之间的摩擦因数;
c. 降低螺杆温度,通冷却水;
d. 根据摩擦因数与温度的关系, 适当提高加工温度。
总结:为获得最大的固体输送速率
从挤出机结构来考虑:
一台挤出机的生产率、塑化质量、填加物的 分散性、熔体温度、动力消耗等,主要决定 于螺杆的性能。
(一)常规螺杆 一、评价螺杆的标准及设计时应考虑的因素 1、评价螺杆质量的标准有: ①塑化质量 一根螺杆必须能生产出合乎质量要
求的制品。即制品:
A、具有合乎要求的各种性能。具有合乎规定的物 理、化学、力学、电学性能;
a.增加螺槽深度是有利的,但会受到螺杆
扭矩的限制。其次,降低塑料与螺杆的摩擦系数 也是有利的。再者,增大塑料与料筒的摩擦系数, 也可以提高固体输送速率,但要注意会引起物料 停滞甚至分解,因此料筒内表面还是要尽量光洁。
双螺杆挤压机使用说明

双螺杆挤压机使用说明江南大学机械工程学院指导教师:目录目录一、设计任务 (4)二、双螺杆挤压机的组成及应用 (5)1.主机 (5)2.辅机 (5)3.控制系统 (5)三、硬件设计 (6)1. ISA 芯片 (6)2. 或非门电路 (6)3.CD4067芯片 (6)4. AD转换器A D574 (6)5.数模转换器 (7)6.交流型固态继电器 (7)7.开关量输出 (8)8.译码器 (8)9.模拟量的采集 (9)10.电机的控制 (9)11. 温控设计 (10)12.报警设计 (11)四、软件界面设计 (12)1. 主界面 (12)2. 温度参数设置 (12)3.P I D参数设置 (13)4. 报警参数设置 (14)5. 电机操作控制 (14)6风机开启温度设定 (14)五、软件设计 (15)1. 程序流程图 (15)2.软件中用到变量 (15)3. 系统启动 (16)4. 报警参数采集及控制模块 (16)(1)电流报警 (16)(2)电流报警子程序 (16)(3)电流报警流程 (17)(4)融压融温报警与显示 (17)(5)融压/融温报警子程序 (18)(6)容温/容压报警流程 (19)(7)报警子程序 (19)5. 温度及电流采集(A/D采集) (19)(1)所需运行的程序 (19)(2)采集流程 (19)6. 温度控制 (20)(1)PID控制子程序 (20)(2)温度PID控制 (20)(3)PID控制流程图 (21)(4)降温风机控制 (21)7. 显示 (22)8. 权限设置 (22)9.电机转速调节设计 (22)(1)转速、转向设置系统 (22)(2)传递控制结构:电机转速转向控制 (22)(3)传递控制流程(D/A转换控制转速) (23)10. 数据组输入程序 (24)六、总结 (25)七、参考资料 (25)双螺杆挤压机设计说明一、设计任务1.设计硬件原理图一张。
此硬件可以插入PC机的ISA插槽,用于实PC机和塑料挤压机的连接,其中包含有计算机测控系统的前向通道和后向通道部分。
螺旋挤压式固液分离机及其应用

1999年第2期螺旋挤压式固液分离机及其应用苏海泉一、国内养猪业的发展状况自改革开放以来,随着我国城乡人民生活水平的提高,人们对禽、畜、肉、蛋、奶的需求与日俱增,年人均占有量已逐渐达到或接近世界平均水平,这给国内畜禽养殖业的发展带来了机遇。
以往小家小户的散户养殖业已不再适应大规模肉蛋奶市场的需求,代之而起的是日益发展的规模化养殖业。
目前国内的养猪养鸡规模已经发展到上万只、几万只乃至几十万只规模的养猪场;几万只、几十万只乃至上百万只的养鸡场,正如雨后春笋般地发展起来。
当人们品尝着美味的畜禽制品时,不容忽略另一个严峻的现实,那就是规模化养殖给环境带来的污染。
就大型养猪场而言,一只猪平均每天要消耗1公斤~2公斤精饲料,与此同时一天内要消耗10公斤~20公斤的水,这些污水与猪的粪尿掺和在一起排出猪场,一个上万头的猪场,每天将产生上百吨的粪水,常温下这些废水要发酵、发臭,要污染土地、水源和空气。
日积月累这些粪污将占去几十亩甚至上百亩的土地,长时间的破坏环境,以至变得非治理不行的程度。
至于大规模的养鸡场,其粪便的恶臭更让人无法忍耐。
据了解,目前北京周边大型猪场已达到100多个,大型鸡场也有几十个,由此产生的废水占用了很大面积的土地,这些粪水既不易流动又不便运输,是个老大难的问题。
从国内外养猪业的现状来看,几乎没有什么好的办法,在诸多解决粪水污染的方案中,选用螺旋挤压式固液分离机对猪场粪水进行固液分离,仍是一种投入不高、经济效益明显的方案。
二、在处理猪场粪水中的应用进入90年代,国内外的畜禽养殖业都有所发展,特别是养猪规模迅速增大,畜禽养殖业要走大规模生产的路子,规模大了才能提高效益,但同时要解决效益与污染的防治问题。
近年来我国农业的发展依靠的是科学种田,主要采用措施有两个,一是良种,二是化肥。
使用化肥的确能达到大面积的增产,但是过长时间、过量使用的结果也是不容忽视的,其副作用使土壤板结、地力下降。
实践证明,土壤需要有机肥,特别是需要有机复合肥。
牛粪污螺旋挤压式固液分离机优化设计与试验

牛粪污螺旋挤压式固液分离机优化设计与试验关正军;王新志;张旭;王伟东【摘要】为优化螺旋挤压式固液分离机工作参数,研究了牛粪尿TS质量分数为10%时,变径螺旋轴分离段锥度、分离筛笼栅条间隙、螺旋轴转速、出料端部压力对机器分离效率、原料的固体去除率和机器能耗的影响.经参数优化和试验验证,在螺旋轴分离段锥度2.68°、分离筛笼栅条间隙1 mm、螺旋轴转速60 r/min、出料端部初始压力3 250 N时,分离效率可达746.18 kg/h,固体去除率可达49.84%,分离后固体的含水率为61%,分离效果较好.【期刊名称】《农业机械学报》【年(卷),期】2016(047)011【总页数】7页(P192-197,149)【关键词】牛粪;固液分离;螺旋挤压;参数优化【作者】关正军;王新志;张旭;王伟东【作者单位】东北农业大学工程学院,哈尔滨150030;东北农业大学工程学院,哈尔滨150030;东北农业大学工程学院,哈尔滨150030;黑龙江八一农垦大学生命科学技术学院,大庆163319【正文语种】中文【中图分类】S216.4第一次全国污染源普查公报[1]数据显示,畜禽养殖业粪便年产生量2.43亿t,尿液年产生量1.63亿t。
利用固液分离技术对畜禽粪便进行处理,能够有效提高有机成分的利用率,是实现畜禽养殖粪污资源化利用和无害化处理的重要环节。
KAPARAJU等[2]通过研究牛粪固液分离后的产气效果,发现固液分离后的牛粪颗粒明显细化,对厌氧发酵产气率有明显的正向促进作用;关正军等[3]对牛粪固液分离后进行了分离液厌氧发酵技术研究,结果表明与原牛粪相比,用牛粪分离液发酵甲烷产率有明显提高,水力停留时间明显缩短。
畜禽养殖粪便的固液分离方法主要有:筛分分离、带式压滤分离、高速离心分离、螺旋挤压分离等[4],其中螺旋挤压式分离的分离效果最好、效率最高,适合规模化养殖场使用[5]。
由于缺少统一的标准和理论依据,当前市场上的螺旋挤压式固液分离机结构多采用等轴径等螺距设计,少数变轴径变螺距结构也是凭经验加工,没有具体设计依据。
螺旋挤压式固液分离机

螺旋挤压式固液分离机使用说明书山东鱼台绿华环保节能设备制造有限公司Shandong Yu tai green environmental protection energy saving equipment manufacturing Co., Ltd.Ltd.螺旋挤压式固液分离机使用说明目前,我国大部分养殖户采用直接用水冲洗粪尿。
但这却有用水量大、污染严重,损失大等缺点。
根据新农村建设的要求和人们环保节能意识的加强,现在,养猪场建沼气池和生化池处理粪尿,但是进沼气池的粪类物料都未经固液分离,实际使用证明这样直接的沼气培养效果不是太理想。
因为,未经处理的粪尿水进入沼气池,大大增加了沼气池单位容积的有机负荷量,因此沼气池的容积要增加很多。
由于长期使用沼气池,发酵后留下大量残渣,使沼气池堵塞,容量减小而造成沼气池不能使用,而清洗池既耗力又极不安全,同时增加开支费用。
如果直接销售鲜动物粪便又很难运输。
因此,我们发现应该对动物粪便提前进行固液分离措施,既可解决动物粪便在沼气池的沉淀问题,极大增强沼气池的处理能力,又可大大减小沼气池、生化池的建设面积。
节省环保处理的建设投资和土地使用面积,分离出的粪便干料还可直接作为果树、林木施肥和有机肥的原料。
卖给有机肥厂作为有机肥原料或自做有机肥,做到既有社会效益又有经济效益。
此机可广泛做为鸡、牛、马,鸭及各类集约化养殖场对动物粪便、酒糟、药渣、淀粉渣、酱渣、屠宰厂等高浓度有机污水的渣液分离。
实用性:该系列机渣液分离速度快,经分离后的粪渣含水量在30-40%之间,出渣量及含水量可调整,可适用不同成份的饲料(如草及精饲料),便于运输,其固粒物很适合作为鱼饲料和有机肥的原料等。
先进性:该系列机去污能力强,无堵塞,清洗方便。
经过处理的粪尿水含固率、化学耗氧量、总耗氧量、氮、磷的去除率可在70-95%之间。
耐用性:该系列机的筛网、绞龙等由304不锈钢和耐磨镍合金材质等制成,耐腐蚀、强度高,使用寿命长。
数控电动螺旋压力机简介
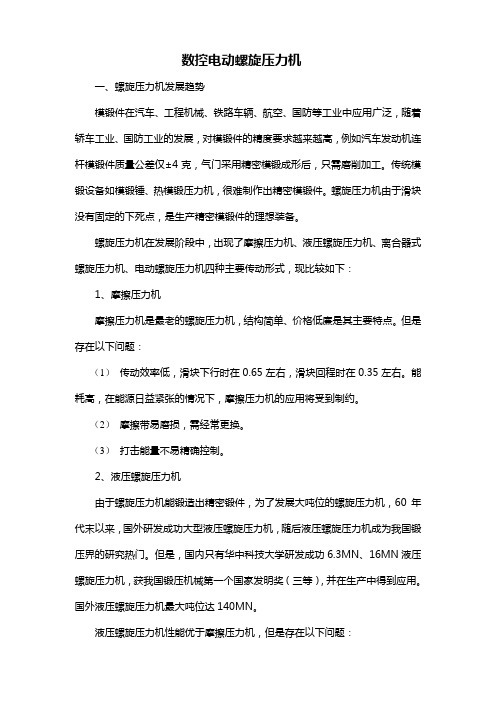
数控电动螺旋压力机一、螺旋压力机发展趋势模锻件在汽车、工程机械、铁路车辆、航空、国防等工业中应用广泛,随着轿车工业、国防工业的发展,对模锻件的精度要求越来越高,例如汽车发动机连杆模锻件质量公差仅±4克,气门采用精密模锻成形后,只需磨削加工。
传统模锻设备如模锻锤、热模锻压力机,很难制作出精密模锻件。
螺旋压力机由于滑块没有固定的下死点,是生产精密模锻件的理想装备。
螺旋压力机在发展阶段中,出现了摩擦压力机、液压螺旋压力机、离合器式螺旋压力机、电动螺旋压力机四种主要传动形式,现比较如下:1、摩擦压力机摩擦压力机是最老的螺旋压力机,结构简单、价格低廉是其主要特点。
但是存在以下问题:(1)传动效率低,滑块下行时在0.65左右,滑块回程时在0.35左右。
能耗高,在能源日益紧张的情况下,摩擦压力机的应用将受到制约。
(2)摩擦带易磨损,需经常更换。
(3)打击能量不易精确控制。
2、液压螺旋压力机由于螺旋压力机能锻造出精密锻件,为了发展大吨位的螺旋压力机,60年代末以来,国外研发成功大型液压螺旋压力机,随后液压螺旋压力机成为我国锻压界的研究热门。
但是,国内只有华中科技大学研发成功6.3MN、16MN液压螺旋压力机,获我国锻压机械第一个国家发明奖(三等),并在生产中得到应用。
国外液压螺旋压力机最大吨位达140MN。
液压螺旋压力机性能优于摩擦压力机,但是存在以下问题:(1)液压系统复杂,管道敷设工作量大,液压泄漏对环境有污染。
(2)维修技术水平要求高,一般锻造工厂维修困难。
(3)价格远高于摩擦压力机。
3、离合器式螺旋压力机上世纪70年代末推出,又称高能螺旋压力机。
其特点是具有高的打击能量,滑块在小行程能输出额定能量值和达到最大锻击力;最大吨位为112MN。
但是存在以下问题:(1)机器结构十分复杂,既有机械离合器传动,又有用于滑块回程的液压传动。
(2)常用的滑块回程方式是采用液压缸推动滑块,同时使螺杆作反向运动。
螺旋压榨机

螺旋压榨机主要有:压榨装置,传动装置,进料装置,电机,出料装置,机座组成。
主要装置是压榨装置中的螺旋杆机构:锥度空心轴,螺旋叶片。
驱动装置:三相异步电动机,用联轴器将电机与螺旋轴相连。
原理:待加工材料从送料口送入后被螺旋叶片挤压,绞碎,并随着螺杆向前输送,由出料口送出。
联轴器的选用考虑榨汁机的工作环境和工作情况,主要是旋转轴有轴向位移。
可移式联铀器允许两轴有一定的安装误差,它对两轴间的偏移有一定的补偿能力。
所以选具有对两轴间的偏移有一定的补偿能力的可移式联铀器——十字滑块联轴器。
十字滑块联轴器由两个半联轴器与十字滑块组成。
十字滑块两侧互相垂直的凸携分别与两个十两联轴器的凹槽组成移动副。
联轴器工作时,十字滑块随两轴转动,同时又相对于两轴移动以补偿两轴的径向位移。
这种联轴器允许的径向偏量较大。
允许有不大的角度位移和轴向位移。
由于十字滑块偏心回转会产生离心力,不用于高速场合。
为了减少十字滑块相对移动时的磨损及提高传动效率,需要定期进行润滑。
螺旋轴的设计材料的选取螺旋杆是螺旋榨汁机的主要工作部件,采用不锈钢材料铸造后精加工制成。
产量2-3吨每小时螺旋直径300mm,查表选螺旋圈数6圈,螺距300mm(?),功率2.2KW,螺旋轴总长粗定为1700mm。
螺旋叶片与螺旋轴是整体加工还是分开铸造加工后焊接或螺钉固紧??螺旋叶片等螺距,半径不相同,倾斜式安装,利用重力是材料退回再次加工,或采用最后几圈为反向较小螺距叶片使材料返回再次加工。
轴承的选择,考虑实际情况受单向的轴向力和径向力,(轴向力的方向??)采用一端推力球轴承受轴向力,另一端可选深沟球。
螺旋轴采用空心轴,这是因为空心轴在承受相同扭矩的情况下空心材料所用的材料较少,而且抗扭能力更好。
那么空心轴和主轴怎么配合套在一起??螺旋叶片上力如何确定??锥形调节环:通过三组弹簧固定,可调节出产量,压缩比等,外筒由上下俩部分组成,下面部分与机座相连为一体,上下用法兰连接滤鼓的结构设计滤鼓是用不锈钢板卷制而成,制成对开式结构,其上钻有圆孔或锥形孔,也有的滤鼓上开滤缝。
全自动挤压机工作原理

全自动挤压机工作原理
全自动挤压机主要是通过电机驱动,实现挤压材料的连续输送、挤压成型的机械设备。
其工作原理如下:
1. 电机驱动:全自动挤压机通常由一台电机驱动,电机带动传动装置使模头(挤压螺杆和模具)运动。
2. 原料供给:原料通过料斗或输送系统从上方输入,落入螺旋式输送器中。
输送器依靠螺旋的旋转将原料推向出料口。
3. 挤压过程:当原料进入模头时,螺杆开始旋转。
螺杆的旋转将原料推入模具内部。
在模具内部,原料受到高温和高压的作用,根据模具形状被挤压成所需的产品形状。
4. 冷却和固化:挤压完成后,产品进入冷却区域,通过冷却装置快速冷却和固化。
冷却固化后的产品可立即脱模。
5. 自动化控制:全自动挤压机通常配备自动化控制系统,通过设置合适的参数和监控设备的运行状态,可以实现自动化生产,提高生产效率和产品质量。
总之,全自动挤压机主要通过电机驱动,将原料推入模具内部,并在高温高压条件下挤压成所需产品形状,最后通过冷却固化和自动化控制系统完成整个挤压过程。
- 1、下载文档前请自行甄别文档内容的完整性,平台不提供额外的编辑、内容补充、找答案等附加服务。
- 2、"仅部分预览"的文档,不可在线预览部分如存在完整性等问题,可反馈申请退款(可完整预览的文档不适用该条件!)。
- 3、如文档侵犯您的权益,请联系客服反馈,我们会尽快为您处理(人工客服工作时间:9:00-18:30)。
本文由万俊挤压机 和春翔挤压机配件 提供 螺旋挤压机
用于型焦用料预压成型的型焦制备设备。
其作用是:将煤料在螺旋挤压机内压成煤带,以提高煤料的密度,保证煤料均匀稳定地进入对辊成型机,增大型煤的致密性和提高成型机的成球率。
螺旋挤压机(见图)的筒体呈圆筒形,为防止煤料随螺旋轴运转,在筒体内壁衬以带沟槽、格子或波纹型的便于拆卸和更换的耐磨衬套,以增大煤料的回转阻力。
螺旋挤压机的工作部件为螺旋,螺旋叶片的截面垂直于轴线,以平行于轴向的分力朝变形嘴方向推进煤料,处于塑性状态的煤料,在变形嘴处,由于受到压缩而形成塑性煤带。
在入料口和筒体后壁之间应有1/4
螺距长度的螺旋叶片,以防煤料窜入轴承。
螺旋与筒体的间隙,一般不大于2~3mm ,以避免煤料的回流和提高挤压效率。
热压成型用的螺旋挤压机在400~500℃下挤压煤料,螺旋叶片和衬套易磨损,应选用耐热耐磨材料制做, 也可在螺旋叶片外沿上堆焊碳化钨,以提高其耐磨性。
变形嘴的作用是,将塑性煤料的环形断面约束成长方形断面。
两个断面积之比(环形:长方形)一般为1.0:1.3。
为增加螺旋的推力,将螺旋轴头部伸入变形嘴的空间。
活动嘴和变形嘴的联接断面(长方形)的尺寸,与变形嘴长方口的尺寸相同,其上部是一块活动压板,下部是长方形断面的槽,调节施加于活动压板上的力,便可调节预成型压力。
螺旋挤压机的传动装置由异步电动机带动齿轮变速箱传动。
螺旋挤压机的生产能力Q 取决于挤压机直径、螺旋的螺距和转速,可用下式计算:
式中,D 为筒体直径,m; d 为螺旋轴直径,m; s 为螺距,m;δ为螺旋叶片厚度,m; n 为螺旋转速,r/min;k 为有效利用系数,k 值受煤料性质、加热温度、维温时间等多种因素的影响,应通过试验求得。
在估计生产能力时, k 值一般可取0.25~0.40。
螺旋挤压机结构示意图。