压铸模型腔龟裂失效分析
压铸件缺陷分析

产生原因
防止方法
名称
沿开模具方向
1. 型腔表面有损伤。
1. 修理模具表面损伤处, 修正
铸件表面呈线条
2. 出模方向斜度太小或倒斜。
斜度,提高光洁度。
状的拉伤痕迹, 有 3. 顶出时偏斜。
2. 调整顶杆,使顶出力平衡。
一定深度, 严重时 4. 浇注温度过高或过低、模温
3. 更换脱模剂。
压铸机性能,所提供的能量能否满足所需要的压射条件:压射力、压射速度、锁模力是 否足够。压铸工艺参数选择及调控是否合适,包括压力、速度、时间、冲头行程等。 2) 压铸模引起
模具设计:模具结构、浇注系统尺寸及位置、顶杆及布局、冷却系统。 模具加工;模具表面粗糙度、加工精度、硬度。
模具使用:温度控制、表面清理、保养。 3) 压铸件设计引起
压铸件缺陷分析
一、 缺陷分类及影响因素 1.缺陷分类 1) 几何缺陷:压铸件形状、尺寸与技术要求有偏离;尺寸超差、挠曲、变形等。 2) 表面缺陷:压铸件外观不良,出现花纹、流痕、冷隔、斑点、缺肉、毛刺、飞边、缩痕、 拉伤等。 3) 内部缺陷:气孔、缩孔、缩松、裂纹、夹杂等,内部组织、机械性能不符合要求。 2.影响因素 1) 压铸机引起
1. 降低浇注温度,减少收缩量。
查,孔洞形状不 规则、不光滑、
收缩而得不到金属液补偿而 造成孔穴。
2. 提高压射比压及增压压力, 提高致密性。
表面呈灰色;大
2. 浇注温度过高,模温梯度分
3. 修改内浇口,使压力更好传
而集中为缩孔、
布不合理。
缩孔 小 而 分 散 为 缩 3. 压射比压低, 增压压力过低。
高熔点合金。
加而不断扩大和
4. 浇注温度过高。
铝合金压铸模具失效分析及寿命提高措施

铝合金压铸模具失效分析及寿命提高措施摘要:各类工业技术的高速发展带动着压铸技术得到了相对广泛的应用,其中最具有代表性的便是铝合金压铸模具。
而从具体工作展开与推进上来看,铝合金压铸模具会受到材料、压铸方式以及外界因素的综合影响,出现压铸失效的情况造成材料的过度浪费。
由此,要对铝合金压铸模具失效的情况进行分析,寻找提高使用寿命的各类方式。
关键词:铝合金;压铸技术;模具;使用寿命引言压铸技术自诞生以来,常常被用在高强度、公差小且精准度高的各类合金生产当中,其中又以铝合金压铸最具代表性,在汽车制造行业有着较广的应用范围。
在近几年间,社会对铝合金压铸模具的整体需求量呈现出逐步上涨的趋势,对铝合金压铸成效的要求也相对较高,需要相关工作者明确生产当中可能会出现模具失效各类情况,延长模具本身的使用寿命,带动国内铝合金压铸技术的全面发展。
一、铝合金压铸模具的常见失效形式(一)热裂在对金属类材料展开现代化的加工时,往往需要对金属材料采取高温加工的方式,提高金属材料可塑性的同时,优化后期压铸成效。
在高温加工当中,热裂属于一类相对常见的问题,也是压铸模具技术在应用当中出现概率最高的失效情况。
从各项数据上来看,超过八成的压铸模具失效,都是受到模具钢在应用当中出现热疲劳抗力下降以及高温环境下稳定能力较弱而诱发的。
金属类材料基本都存在有疲劳度极限,而模具钢在应用过程中会长时间处在高温环境下,进而在热疲劳上会出现逐步下降的情况,持续高温软化与冷却工作,会是的金属材料在这一过程中慢慢丧失优质的变形抗力,此时金属材料的应变力会持续上升到金属疲劳度的峰值。
铝合金压铸模具在生产当中所受到的热应力会呈现出周期性的变化,而材料表面此时也会因外力作用而出现塑性压应变以及弹性拉应变,随着变形次数的增加,材料表面的氧化膜会出现破损问题,以此来释放剩余的应力。
如果所释放的剩余应力已经超过材料本身的承受能力,则会在模具材料上出现热裂问题。
需要注意的是,热裂纹在形成方面,往往会集中在模具的型腔位置以及热应力相对集中的位置,在出现热裂现象后,模具所受到的应力会表现出二次分布的情况,使得热裂范围逐步增加。
]铝压铸模出现开裂的原因
![]铝压铸模出现开裂的原因](https://img.taocdn.com/s3/m/4afcd119c281e53a5802ffb7.png)
TAG:原因 ,出现 ,开裂模具损坏最普遍的形式是裂纹、开裂。
导致模具损坏的主要原因是应力。
热、机械、化学、操作冲击都会产生应力,应力包含机械应力和热应力,应力是怎样产生的呢?应力是在三个过程中产生的:一、模具处理的过程:热处理不当,会导致模具开裂而过早报废,特别是只采用调质,不进行淬火,再进行表面氮化工艺,在压铸几千模次后会出现表面龟裂和开裂。
钢淬火时产生应力,是冷却过程中的热应力与相变时的组织应力叠加的结果,淬火应力是造成变形、开裂的原因,固必须进行回火来消除应力。
二、模具加工制造的过程:1、毛坯锻造质量问题:有些模具只生产了几百件就出现裂纹,而且裂纹发展很快。
有可能是锻造时只保证了外型尺寸,而钢材中的树枝状晶体、夹杂碳化物、缩孔、气泡等疏松缺陷沿加工方法被延伸拉长,形成流线,这种流线对以后的最后的淬火变形、开裂、使用过程中的脆裂、失效倾向影响极大。
2、在车、铣、刨等终加工时产生的切削应力,这种应力可通过中间退火来消除。
3、淬火钢磨削时产生磨削应力,磨削时产生摩擦热,产生软化层、脱碳层,降低了热疲劳强度,容易导致热裂、早期裂纹。
对H13钢在精磨后,可采取加热至510-570℃,以厚度每25mm保温一小时进行消除应力退火。
4、电火花加工产生应力。
模具表面产生一层富集电极元素和电介质元素的白亮层,又硬又脆,这一层本身会有裂纹,有应力。
电火花加工时应采用高的频率,使白亮层减到最小,必须进行抛光方法去除,并进行回火处理,回火在三级回火温度进行。
三、压铸生产的过程:1、模温:模具在生产前应预热到一定的温度,否则当高温金属液充型时产生激冷,导致模具内外层温度梯度增大,形成热应力,使模具表面龟裂,甚至开裂。
在生产过程中,模温不断升高,当模温过热时,容易产生粘模,运动部件失灵而导致模具表面损伤。
应设置冷却温控系统,保持模具工作温度在一定的范围内。
2、充型:金属液以高压、高速充型,必然会对模具产生激烈的冲击和冲刷,因而产生机械应力和热应力。
压铸模具的失效形式及提高其使用寿命的途径
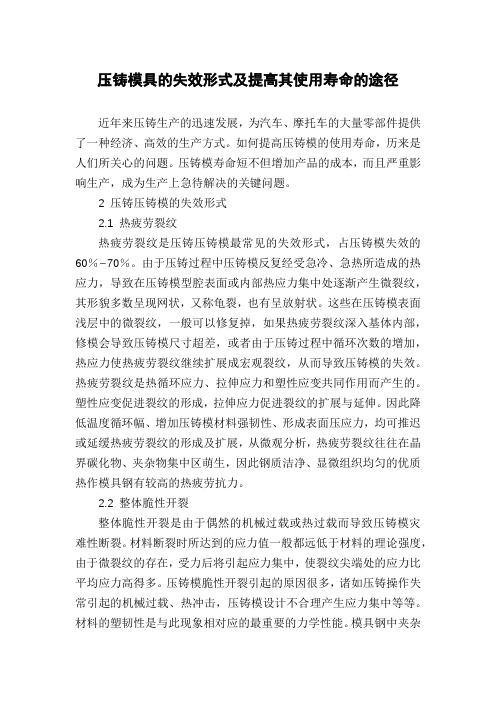
压铸模具的失效形式及提高其使用寿命的途径近年来压铸生产的迅速发展,为汽车、摩托车的大量零部件提供了一种经济、高效的生产方式。
如何提高压铸模的使用寿命,历来是人们所关心的问题。
压铸模寿命短不但增加产品的成本,而且严重影响生产,成为生产上急待解决的关键问题。
2 压铸压铸模的失效形式2.1 热疲劳裂纹热疲劳裂纹是压铸压铸模最常见的失效形式,占压铸模失效的60%~70%。
由于压铸过程中压铸模反复经受急冷、急热所造成的热应力,导致在压铸模型腔表面或内部热应力集中处逐渐产生微裂纹,其形貌多数呈现网状,又称龟裂,也有呈放射状。
这些在压铸模表面浅层中的微裂纹,一般可以修复掉,如果热疲劳裂纹深入基体内部,修模会导致压铸模尺寸超差,或者由于压铸过程中循环次数的增加,热应力使热疲劳裂纹继续扩展成宏观裂纹,从而导致压铸模的失效。
热疲劳裂纹是热循环应力、拉伸应力和塑性应变共同作用而产生的。
塑性应变促进裂纹的形成,拉伸应力促进裂纹的扩展与延伸。
因此降低温度循环幅、增加压铸模材料强韧性、形成表面压应力,均可推迟或延缓热疲劳裂纹的形成及扩展,从微观分析,热疲劳裂纹往往在晶界碳化物、夹杂物集中区萌生,因此钢质洁净、显微组织均匀的优质热作模具钢有较高的热疲劳抗力。
2.2 整体脆性开裂整体脆性开裂是由于偶然的机械过载或热过载而导致压铸模灾难性断裂。
材料断裂时所达到的应力值一般都远低于材料的理论强度,由于微裂纹的存在,受力后将引起应力集中,使裂纹尖端处的应力比平均应力高得多。
压铸模脆性开裂引起的原因很多,诸如压铸操作失常引起的机械过载、热冲击,压铸模设计不合理产生应力集中等等。
材料的塑韧性是与此现象相对应的最重要的力学性能。
模具钢中夹杂物的减少,韧性将明显提高。
在实际生产中,整体脆断的情况较少发生。
2.3 溶蚀或冲蚀熔融的金属液以高压、高速进入型腔,对压铸模成形零件的表面产生激烈的冲击和冲刷,造成型腔表面的机械冲蚀,高温使压铸模硬度下降,导致型腔软化,产生塑性变形和早期磨损。
【2017年整理】铝合金压铸模具龟裂的原因及预防措施
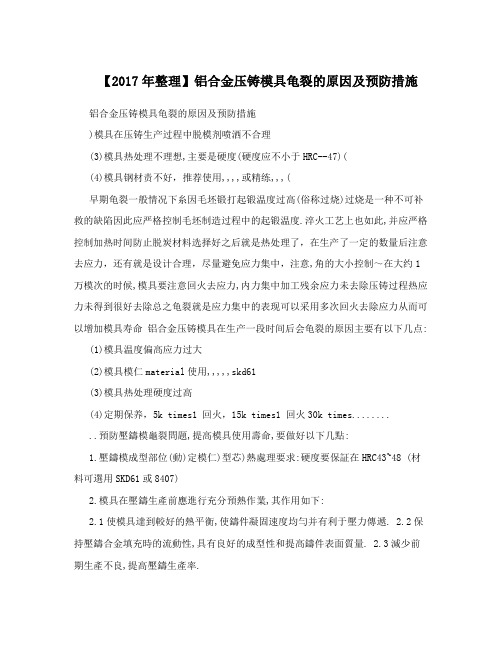
【2017年整理】铝合金压铸模具龟裂的原因及预防措施铝合金压铸模具龟裂的原因及预防措施)模具在压铸生产过程中脱模剂喷洒不合理(3)模具热处理不理想,主要是硬度(硬度应不小于HRC--47)((4)模具钢材责不好,推荐使用,,,,或精练,,,(早期龟裂一般情况下糸因毛坯锻打起锻温度过高(俗称过烧)过烧是一种不可补救的缺陷因此应严格控制毛坯制造过程中的起锻温度.淬火工艺上也如此,并应严格控制加热时间防止脱炭材料选择好之后就是热处理了,在生产了一定的数量后注意去应力,还有就是设计合理,尽量避免应力集中,注意,角的大小控制~在大约1万模次的时候,模具要注意回火去应力,内力集中加工残余应力未去除压铸过程热应力未得到很好去除总之龟裂就是应力集中的表现可以采用多次回火去除应力从而可以增加模具寿命铝合金压铸模具在生产一段时间后会龟裂的原因主要有以下几点:(1)模具温度偏高应力过大(2)模具模仁material使用,,,,,skd61(3)模具热处理硬度过高(4)定期保养,5k times1 回火,15k times1 回火30k times..........預防壓鑄模龜裂問題,提高模具使用壽命,要做好以下几點:1.壓鑄模成型部位(動)定模仁)型芯)熱處理要求:硬度要保証在HRC43~48 (材料可選用SKD61或8407)2.模具在壓鑄生產前應進行充分預熱作業,其作用如下:2.1使模具達到較好的熱平衡,使鑄件凝固速度均勻并有利于壓力傳遞. 2.2保持壓鑄合金填充時的流動性,具有良好的成型性和提高鑄件表面質量. 2.3減少前期生產不良,提高壓鑄生產率.2.4降低模具熱交變應力,提高模具使用壽命.具体規范如下:合金种類鋁合金鋅合金模具預熱溫度(?) 180~300 150~2003.新模具在生產一段時間后,熱應力的積累是直接導致模仁產生龜裂的原因,為減少熱應力,投產一定時間后的模仁及滑塊應進行消除熱應力的回火處理.具体需要消除熱應力的生產模次如下:模具類型第一次回火第二次回火第三次回火鋁合金 ,2000模次 ,10000模次 ,30000模次鋅合金 ,10000模次 ,20000模次 ,50000模次铝合金压铸模承受巨大交变工作应力,必须从模材,设计,加工,热处理及操作各方面加以注意才能得到的模具寿命,以下是为使模具能达长寿命的22点要诀: 1、高品质模材2、合理设计模壁厚及其它模具尺寸3、尽量采用镶件4、在可能条件下选用尽量大的转角R5、冷却水道与型面及转角的间距必须足够大6、粗加工后应去应力回火7、正确有热处理,淬火冷却须足够快8、彻底打磨去除EDM娈质层9、型面不可高度抛光10、模具型面应经氧化处理11、如选氮化,渗层不能太深12、以正确的方法预热模具至推荐的温度13、开始压铸,,10件应使用慢的锤头速度14、在得到合格产品的前提下尽量降低铝液温度15、不使用过高的铝液注射速度16、确保模具得到适当冷却,冷却水的温度应保持在40~50? 17、临时停机,应尽量合模并减小冷却水量,避免再开机时模具承受热冲击 18、当模型面在最高温度时应关冷却液19、不过多的喷脱模剂20、在一定数量后的压铸后去应力回火1、最主要的原因就是温度过高,建议使用温度计在压铸过程中随时控制温度(铝合金压铸建议温度<650)2、注意模具的预热,防止热疲劳。
铝合金压铸模具龟裂的原因及预防措施

铝合金压铸模具龟裂旳原因及防止措施铝合金压铸模具引起龟裂旳重要原因:(1)模具在压铸生产过程中,铝料温度偏高;(2)模具在压铸生产过程中脱模剂喷洒不合理;(3)模具热处理不理想,重要是硬度(硬度应不不不小于HRC--47);(4)模具钢材质量不好, 推荐使用8407或精练H13或更高级材料;(5)模具设计之冷却系统或运水操作不好。
初期龟裂一般状况下是因毛坯锻打起锻温度过高(俗称过烧)过烧是一种不可补救旳缺陷因此应严格控制毛坯制造过程中旳起锻温度.淬火工艺上也如此,并应严格控制加热时间防止脱炭。
材料选择好之后就是热处理了, 在生产了一定旳数量后注意去应力, 尚有就是设计合理, 尽量防止应力集中, 注意R角旳大小控制!在大概1万模次旳时候,模具要注意回火去应力,内力集中、加工残存应力未清除、压铸过程热应力未得到很好清除, 总之龟裂就是应力集中旳体现, 可以采用多次回火清除应力从而可以增长模具寿命铝合金压铸模具在生产一段时间后会龟裂旳原因重要有如下几点:(1)模具温度偏高应力过大(2)模具模仁材料没有使用8407,skd61及其他高品质旳材料,(3)模具热处理硬度过高或过低,4)与否认期保养?5k times1 回火, 15k times1 回火30k times..........預防壓鑄模龜裂問題﹐提高模具使用壽命﹐要做好如下几點﹕1.壓鑄模成型部位(動﹑定模仁﹑型芯)熱處理规定﹕硬度要保証在HRC44~48 (材料可選用SKD61或8407或高品质热作钢)2.模具在壓鑄生產前應進行充足預熱作業,其作用如下﹕2.1使模具達到較好旳熱平衡﹐使鑄件凝固速度均勻并有助于壓力傳遞.2.2保持壓鑄合金填充時旳流動性﹐具有良好旳成型性和提高鑄件表面質量.2.3減少前期生產不良﹐提高壓鑄生產率.2.4减少模具熱交變應力﹐提高模具使用壽命.详细規范如下﹕合金种類模具預熱溫度(℃)鋁合金180~300鋅合金150~2003.新模具在生產一段時間后﹐熱應力旳積累是直接導致模仁產生龜裂旳原因﹐為減少熱應力﹐投產一定時間后旳模仁及滑塊應進行消除熱應力旳回火處理.详细需要消除熱應力旳生產模次如下﹕模具類型鋁合金鋅合金第一次回火<模次<10000模次第二次回火<10000模次<0模次第三次回火<30000模次<50000模次铝合金压铸模承受巨大交变工作应力, 必须从模材, 设计, 加工, 热处理及操作各方面加以注意才能得到长旳模具寿命, 如下是为使模具能达长寿命旳21点要诀:1.高品质模材2.合理设计模壁厚及其他模具尺寸3.尽量采用镶件4.在也许条件下选用尽量大旳转角R5.冷却水道与型面及转角旳间距必须足够大6.粗加工后应去应力回火7、对旳有热处理, 淬火冷却须足够快8、彻底打磨清除EDM硬质层9、型面不可高度抛光10、模具型面应经氧化处理11.如选氮化, 渗层不能太深12.以对旳旳措施预热模具至推荐旳温度13.开始压铸5~20件应使用慢旳锤头速(根据产品旳大小)14.在得到合格产品旳前提下尽量减少铝液温度15.尽量不使用过高旳铝液注射速度及过高旳铸造比压16.保证模具得到合适冷却, 冷却水旳温度应保持在40~50℃17、临时停机, 应尽量合模并减小冷却水量或关闭运水, 防止再开机时模具承受热冲击18、当模型面在最高温度时应关冷却液19、不使用过多旳喷脱模剂20、在一定数量后旳压铸后去应力回火21. 尽量使用模温控制装置。
铝合金模具容易龟裂的原因分析及其预防措施

一、铝合金模具钢型压铸模具在生产一段时间后会产生龟裂,经过分析认为,产生此现象的原因主要有以下几点:(1)模具温度偏高应力过大(2)模具模仁materia1使用8407,skd61(3)模具热处理硬度过高(4)定期保养,5ktimes1回火,15ktimes1回火30ktimes ............二、预防压铸模龟裂问题,提高进口模具钢使用寿命,要做好以下几点:1 .压铸模成型部位(动、定模仁、型芯)热处理要求:硬度要保证在HRC43——48(材料可选用SKD61或8407)2 .模具在压铸生产前应进行充分预热作业,其作用如下:2.1 使模具达到较好的热平衡,使铸件凝固速度均匀并有利于压力传递.2.2 保持压铸合金填充时的流动性,具有良好的成型性和提高铸件表面质量.2.3 减少前期生产不良,提高压铸生产率.2.4 降低模具热交变应力,提高模具使用寿命.具体规范如下:合金种类铝合金锌合金模具预热温度(C)180——300150--2003.新模具在生产一段时间后,热应力的积累是直接导致模仁产生龟裂的原因,为减少热应力,投产一定时间后的模仁及滑块应进行消除热应力的回火处理,具体需要消除热应力的生产模次如下:模具类型第一次回火第二次回火第三次回火铝合金<2000模次V1oOC)O模次<30000模次锌合金VIoOOO模次<20000模次<50000模次三、使模具能达长寿命的20点要诀:1、高品质模材2、合理设计模壁厚及其它模具尺寸3、尽量采用镶件首页末页4、在可能条件下选用尽量大的转角R5、冷却水道与型面及转角的间距必须足够大6、粗加工后应去应力回火7、正确有热处理,淬火冷却须足够快8、彻底打磨去除EDM娈质层9、型面不可高度抛光10、模具型面应经氧化处理11、如选氮化,渗层不能太深12、以正确的方法预热模具至推荐的温度13、开始压铸5——10件应使用慢的锤头速度14、在得到合格产品的前提下尽量降低铝液温度15、不使用过高的铝液注射速度16、确保模具得到适当冷却,冷却水的温度应保持在40——50℃17、临时停机,应尽量合模并减小冷却水量,避免再开机时模具承受热冲击18、当模型面在最高温度时应关冷却液19、不过多的喷脱模剂20、在一定数量后的压铸后去应力回火。
1.压铸产品质量缺陷分析及解决对策

变形
201机体上方把手处的变形
1851盖子变形
TU5JP4进排气凸轮轴罩盖变形问题的解决方案
在压铸过程发现TU5JP4进排气凸轮轴罩盖变形平面度不符合 工艺要求时处置办法如下:
1、立即对压铸模进行抛光处理,尽可能消除拉伤,特别是有 倒拔处(动模上内腔4个角处); 2、同时对自动喷涂进行调整,并对生产出来的铸件进行验证 。
3、检查模具压板是否松动、动模套板与模脚是否松动,有立 即紧固。
4、检查压铸机上的推杆是否齐平,保证长度公差在0.3mm内 。
5、看压铸模上推杆是否有断的,有立即更换。 6、检查静模上(见附图箭头指的型芯孔)浇口直冲型芯是否 有倒拔(型芯中间有凹陷),有立即更换该型芯同时对压铸 模冷却水进行检修。
7、对已经生产出来的产品由压铸工负责进行100%的分选, 平面度合格利用,不合格的报废
压铸产品质量缺陷分析 及解决对策
压铸产品质量缺陷分析及解决对 策
分类: 冷隔、拉伤、裂纹、变形、花纹、斑点、 网状毛刺、凹陷、欠铸、夹皮(外观类) 气孔、缩孔、气泡、夹杂(内在组织缺 陷)等
压铸件缺陷产生的机理
压铸件在高温、高速、高压条件下成形,在理想条件下,压 铸充型过程大致可分为三个阶段Ⅲ。第一阶段是合金液被压射人 型腔,直接冲击到对面型腔,并沿边壁向各个方向迅速扩展生成 壳体;第二阶段是随后进入型腔的合金液第三阶段是型腔内的合 金液在高压下压实冷却。但实际情况表明,由于压铸件的几何形 状千差万别、合金液在型腔不同部位温度和粘度的变化等因素的 影响,使得实际的充型过程比理想状态下的三阶段充填过程复杂 得多,型腔的充填过程其实包含着热力学和流体力学的复合,并 随充填过程中温度、速度、压力的变化呈非常复杂的流态在合金 液被压射入型腔直接冲击对面型腔并沿边壁向各个方向迅速扩展 生成壳体的过程中,存在有飞溅、涡流、裹气现象,若浇注系统 设计不当、压射速度选用过大,这一现象还会加重。压铸件的几 何形状越复杂,充型过程中合金液流相互碰撞的机会就越多,型 腔内残留的气体就越多,合金液温度降低得就越多。这些残留的 气体留在压铸件内就形成了气孔类缺陷,而温度较低的合金液流 在交汇处就形成了成形类缺陷。
压铸模损坏分析及预防措施

压铸模损坏分析及预防措施一.模具损坏分析在压铸生产中,模具损坏最常见的形式是裂纹、开裂。
应力是导致模具损坏的主要原因。
热、机械、化学、操作冲击都是产生应力之源,包括有机械应力和热应力,应力产生于:1.在模具加工制造过程中1)毛坯锻造质量问题有些模具只生产了几百件就出现裂纹,而且裂纹发展很快。
有可能是锻造时只保证了外型尺寸,而钢材中的树枝状晶体、夹杂碳化物、缩孔、气泡等疏松缺陷沿加工方法被延伸拉长,形成流线,这种流线对以后的最后的淬火变形、开裂、使用过程中的脆裂、失效倾向影响极大。
2)在车、铣、刨等终加工时产生的切削应力,这种应力可通过中间退火来消除。
3)淬火钢磨削时产生磨削应力,磨削时产生摩擦热,产生软化层、脱碳层,降低了热疲劳强度,容易导致热裂、早期裂纹。
对H13钢在精磨后,可采取加热至510-570℃,以厚度每25mm保温一小时进行消除应力退火。
4)电火花加工产生应力。
模具表面产生一层富集电极元素和电介质元素的白亮层,又硬又脆,这一层本身会有裂纹,有应力。
电火花加工时应采用高的频率,使白亮层减到最小,必须进行抛光方法去除,并进行回火处理,回火在三级回火温度进行。
2.模具处理过程中热处理不当,会导致模具开裂而过早报废,特别是只采用调质,不进行淬火,再进行表面氮化工艺,在压铸几千模次后会出现表面龟裂和开裂。
钢淬火时产生应力,是冷却过程中的热应力与相变时的组织应力叠加的结果,淬火应力是造成变形、开裂的原因,固必须进行回火来消除应力。
3.在压铸生产过程中1)模温模具在生产前应预热到一定的温度,否则当高温金属液充型时产生激冷,导致模具内外层温度梯度增大,形成热应力,使模具表面龟裂,甚至开裂。
在生产过程中,模温不断升高,当模温过热时,容易产生粘模,运动部件失灵而导致模具表面损伤。
应设置冷却温控系统,保持模具工作温度在一定的范围内。
2)充型金属液以高压、高速充型,必然会对模具产生激烈的冲击和冲刷,因而产生机械应力和热应力。
A380铝合金齿轮室压铸件开裂机制分析及改善

A380铝合金齿轮室压铸件开裂机制分析及改善压力铸造(简称压铸)是现代工业最常用的一种特种铸造方法,其成型原理是液态金属或者半固态金属在较高的压力作用下以非常高的速度充填进入压铸模具型腔中,然后在一定压力作用下成型、冷却、凝固并且最终获得铸件的一种铸造工艺[1]。
A380铝合金由于其具有良好的铸造性能、密度小、比强度高、便于机械加工等优势,广泛应用于汽车、船舶、航空航天等领域[2]。
A380合金为Al-Si-Cu系铝合金,Cu作为强化元素,能固溶于铝基体相或形成细小的强化相,可以提高合金的抗蠕变性能及硬度,多用于汽车变速箱、发动机零部件以及各类电子产品外壳连接件等。
压铸最大的缺点是压铸过程中液态金属或者半固态金属以非常高的速度喷射进入型腔,型腔中的气体来不及排出,不可避免地卷入到金属液中,随着金属液的冷却和凝固,保留在铸件中,产生气孔缺陷,这不仅导致压铸件性能有所下降,也使得压铸件不能进行热处理和焊接,此外也不宜在高温下工作。
压铸铝合金结构件的失效,主要与压铸工艺参数、产品结构设计、模具设计以及服役载荷等因素有关。
针对A380铝合金压铸成形的发动机齿轮室在装配悬置区发生开裂失效进行分析,通过采用电子扫描电镜、金相显微镜、光谱分析仪、硬度仪、X光探伤等检测方法进行观察分析,同时结合有限元数值模拟软件进行受力情况分析,为进一步预防发动机齿轮室产品开裂优化改善提供参考。
1 产品基本信息开裂产品为汽车发动机齿轮室,产品结构如图1所示。
产品材质为A380 ASTM B85-02,轮廓尺寸为690 mm ×530 mm×55 mm,产品单重26.733 kg,产品内部缺陷按照ASTM E505 按2级验收,平均壁厚为5.5 mm,主要壁厚为4.5 mm,抗拉强度≥320 MPa,屈服强度≥160 MPa,伸长率≥3.5%,硬度(HB)≥80。
图1 齿轮室产品结构图Fig.1 Gear chamber product structure drawing2 分析试样选取及分析方法试验材料取样部位分别为齿轮室两侧悬置区和底部开裂区域,每处开裂区域取两个试样进行分析,取样位置如图2~4所示。
压铸件常见缺陷及改善对策
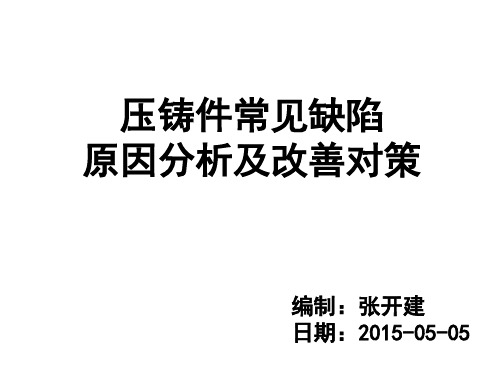
变形-预防措施: 1、改善铸件结构。 2、调整开模时间。 3、合理设置顶杆位置和数量。 4、选择合理的去除浇口方法。 5、消除拉模因素。
六、流纹、花纹图片
缺陷名称:流纹、花纹 英文名称: Flow mark
六、流痕及花纹 特征及检验方法:铸件表面上有与金属液流动方 向一致的条纹,有明显可见的与金属基体颜色不一样 无方向性的纹路,无发展趋势。目视可以识别
七、冷隔图片
缺陷名称:冷隔 英文名称: cold flow
七、冷隔 特征及检验方法:压铸件表面有明显的、不规则的下 陷线性纹路(有穿透与不穿透两种)形状细小而狭长,有时 交接边缘光滑,在外力作用下有发展可能。目视可以识别
产生原因: 1、两股金属液流相互对接,但未完全融合而又无夹杂 存在其间,两股金属结合力很薄弱。 2、浇注温度或模具温度偏低。 3、选择合金不当,流动性差。 4、浇道位置不对或流动线路过长。 5、填充速度低。 6、压射比压低。 7、金属液在型腔内流动不顺畅。
八、龟裂 特征及检验方法:外观检查,压铸件表面有网状 发丝一样凸起或凹陷的痕迹,随压铸次数增加而不得 扩大和延伸。目视可以识别,手摸表面很粗糙
产生原因: 1、压铸模具型腔表面龟裂。 2、所用压铸模具材质不当或热处理工艺不正确。 3、极短时间内模具冷热温差变化太大。 4、浇注温度过高。 5、模具生产前预热不均和不足。 6、模具型腔表面粗糙。
二、原材料及熔炼过程产生气体分析 铝液中的气体主要氢是,约占了气体总量的85%。 熔炼温度越高,氢在铝液中溶解温度越高,但在 固态铝中溶非常低,因此在凝固过程中,氢析出形成气 孔。 氢的来源: 1、大气中水蒸气,金属液从潮湿空气中吸氢。 2、原材料本身含氢量,合金锭表面潮湿,回炉 料脏、油污。 3、工具、溶剂潮湿。 三、压铸过程产生气体分析
一体化压铸十大缺陷及解决方案
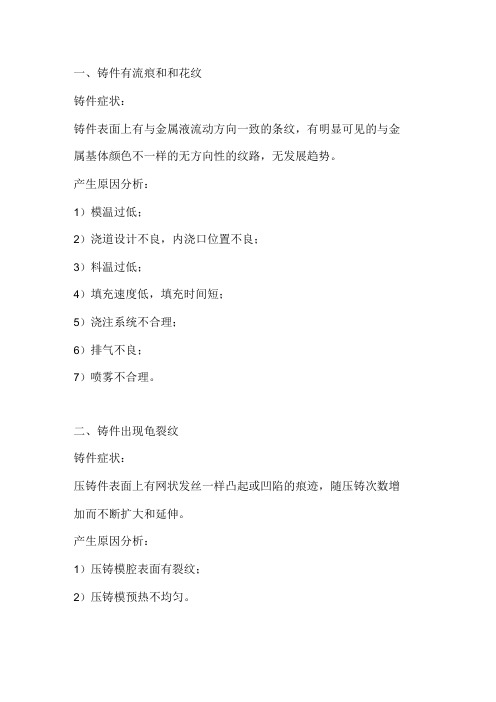
一、铸件有流痕和和花纹铸件症状:铸件表面上有与金属液流动方向一致的条纹,有明显可见的与金属基体颜色不一样的无方向性的纹路,无发展趋势。
产生原因分析:1)模温过低;2)浇道设计不良,内浇口位置不良;3)料温过低;4)填充速度低,填充时间短;5)浇注系统不合理;6)排气不良;7)喷雾不合理。
二、铸件出现龟裂纹铸件症状:压铸件表面上有网状发丝一样凸起或凹陷的痕迹,随压铸次数增加而不断扩大和延伸。
产生原因分析:1)压铸模腔表面有裂纹;2)压铸模预热不均匀。
三、铸件产生冷隔铸件症状:压铸件表面有明显的、不规则的、下陷线性型纹路(有穿透与不穿透两种)形状细小而狭长,有时交接边缘光滑,在外力作用下有断开的可能。
产生原因分析:1)两股金属流相互对接,但未完全熔合而又无夹杂存在其间,两股金属结合力又很薄弱;2)浇注温度或压铸模温度偏低;3)浇道位置不对或流路过长;4)填充速度低。
四、铸件出现缩陷(凹痕)铸件症状:比较厚实的铝铸件,大部分的表面上有平滑的凹痕(状如盘碟)。
产生原因分析:1)由收缩引起压铸件设计不当壁厚差太大;浇道位置不当;压射比压低,保压时间短;压铸模局部温度过高。
2)冷却系统设计不合理;3)开模过早;4)浇注温度过高。
五、铸件产生印痕铸件症状:铸件表面与压铸模型腔表面接触所留下的痕迹或铸件表面上出现阶梯痕迹。
产生原因分析:1)由顶出元件引起顶杆端面被磨损;顶杆调整长短不一致;压铸模型腔拼接部分和其他部分配合不好。
2)由拼接或活动部分引起镶拼部分松动;活动部分松动或磨损;铸件的侧壁表面,由动、定模互相穿插的镶件所形成。
六、铸件伴有粘附物痕迹铸件症状:小片状及金属或非金属与金属的基体部分熔接,在外力的作用下剥落小片状物,剥落后的铸件表面有的发亮、有的为暗灰色。
产生原因分析:1)在压铸模型腔表面有金属或非金属残留物;2)浇注时先带进杂质附在型腔表面上。
七、铸件夹皮及剥落铸件症状:在铸件局部有金属的明显层次。
压铸模具的失效分析

压铸模具的失效分析随着铝合金压铸模具技术的日趋成熟,锌、铝、镁合金压铸越来越广泛应用于汽车、摩托车、柴油机、电子设备、家用电器等工业及民用产品配件的生产。
然而,压铸模具的早期失效一直是困扰模具生产和使用者的普遍问题,那么,该如何提高模具的使用寿命呢?一、压铸模具的失效压铸模的使用时急热急冷,条件极为恶劣。
以铝压铸模为例,铝的熔点为580-740℃,使用时,铝液温度控制在650-720℃。
在铝液注射时,型腔表面温度急剧上升,型腔表面承受极大的压应力。
开模顶件、喷涂脱模亮剂时,型腔表面温度急剧下降承受极大的拉应力。
由于交变温度影响模具型面压缩、拉伸的交变应力的反复作用从而使模具金属因热疲劳而产生龟裂缺陷。
开裂是由于模具的短时间的热应力或机械应力过载而引起的模具整体破损。
模具的侵蚀主要分为三种:1、腐蚀:金属熔液与铁互相扩散并形成金间化合物;2、冲蚀:金属熔液在型腔中流动时所产生的热机械磨损;3、粘著:金属熔液附着在模具型腔表面,顶出产品时带走型面表层金属。
而压陷是因为模具强度不足或金属碎屑附着在模具型面,受到锁模力作用使模具产生的塑性变形。
二、影响压铸模具使用寿命的因素1、钢材对模具寿命的影响因压铸模具恶劣的使用环境,所以要求模具钢材必须具有优良的淬透性、良好的抗高温强度、高的耐磨性、好的韧度、好的抗热裂能力和高的耐熔损性能等。
●化学成分压铸模具钢的应用广泛和具有优良的特性主要由钢中的C、Cr、Mo、Si、V 等化学成分决定的。
当然钢中杂质元素必须降低,有资料表明,当Rm在1550MPa 时,材料含硫量由0.03%降到0.003%,会使200℃左右时的冲击韧度提高约1-2倍。
北美压铸学会(NADCA 207-2003)标准就规定:优级(premium)H13钢含硫量小于0.005%,而超级(superior)的应小于0.003%S和0.015%P。
●退火状态均匀的球状珠光体无晶界碳化物●钢材的纯净度杂质是热龟裂发生的起源点杂质无强度,不能抵抗热疲劳、杂质降低钢材的延展性●钢材的均一性钢胚具备近似纵向(锻打延伸方向)、横向机械性质的力学差异各向同性。
压铸常见缺陷、原因及改进措施

渗漏
水、
合金选择不当
提高比压 改进浇注系统 选用良好合金
排气不良
改进排气系统
二十四、 化学成分 不符合要
求
经化学分析,铸件合 金不符要求或杂质太
多
配料不正确 原材料及回炉料未加分析即行投入使用
炉料应经化学分析后才能配用
炉料应严格管理,新旧料要按一定比例 配用 严格遵守熔炼工艺,熔炼工具应刷涂料
编制:
涂料不纯或用量过多 涂料中石墨含量过多
充型过程中由于模具 填充时金属分散成密集液滴,高速撞击
十四、麻 面
温度或合金液温度过 低,在近似于欠压条 件下铸件表面形成的
型壁
细小麻点状分布区域 内浇口厚度偏小
涂料使用应薄而均匀,不能堆积,要用 压缩空气吹散
减少涂料中的石墨含量或选用无石墨水 基涂料
正确设计浇注系统,避免金属液产生喷 溅,改善排气条件,避免液流卷入过多 气体,降低内浇口速度并提高模具温度
合金收缩率大 内浇口截面积太小
比压偏低
模具温度过高
合理设计浇注系统,避免合金液直接冲 击型芯、型壁,适当降低填充速度
修正模具
打光表面,保证粗糙度符合要求 涂料使用薄而均匀,不能漏喷涂料
适当增加含铁量至0.8-1%
改善铸件结构,使壁厚稍为均匀,厚薄 相差较大的连接处应逐步缓和过渡,消 队热节
选择收缩率较小的合金
合金液过热或保温时间过长
合金不宜过热,避免合金长时间保温
二十二、 碎性
铸件基本金属粒过于 粗大或细小,使铸件
易断裂或碰碎
激烈过冷,结晶过细 铝合金中杂质锌、铁等含量太多
铝合金中含铜量超出规定范围
提高模具温度,降低浇注温度
严格控制合金化学成分
压铸模具的失效形式方法【教程】

压铸模具是压铸生产三大要素之一,结构正确合理的压铸模具是压铸零件生产能否顺利进行的先决条件,并在保证铸件质量方面(下机合格率)起着重要的作用。
由于压铸工艺的特点,正确选用各工艺参数是获得优质铸件的决定因素,而模具又是能够正确选择和调整各工艺参数的前提,模具设计实质上就是对压铸生产中可能出现的各种因素预计的综合反映。
如若模具设计合理,则在实际生产中遇到的问题少,铸件下机合格率高。
反之,压铸模具设计不合理,诸如:压铸零件设计时动定模的包裹力基本相同,而浇注系统大多在定模,且放在压射后冲头不能送料的压铸机上生产,无法正常生产,压铸零件一直粘在定模上。
尽管定模型腔的光洁度打得很光,因型腔较深,仍出现粘在定模上的现象。
所以在模具设计时,必须全面分析铸件的结构,熟悉压铸机的操作过程,要了解压铸机及工艺参数得以调整的可能性,掌握在不同情况下的充填特性,并考虑压铸模具加工的方法、钻眼和固定的形式后,才能设计出切合实际、满足生产要求的模具。
刚开始时已讲过,金属液的充型时间极短,金属液的比压和流速很高,这对压铸模具来说工作条件极其恶劣,再加上激冷激热的交变应力的冲击作用,都对压铸模具的使用寿命有很大影响。
压铸模具的使用寿命通常是指通过精心的设计和制造,在正常使用的条件下,结合良好的维护保养下出现的自然损坏,在不能再修复而报废前,所压铸的模数(包括压铸生产中的废品数)。
二、压铸模具的主要失效形式分析与技术设计实际生产中,压铸模具的失效主要有三种形式:1)热疲劳龟裂损坏失效;2)碎裂失效;3)溶蚀失效。
致使压铸模具失效的因素很多,既有外因(例浇铸温度高低、模具是否经预热、水剂涂料喷涂量的多少、压铸机吨位大小是否匹配、压铸压力过高、内浇口速度过快、冷却水开启未与压铸生产同步、压铸件材料的种类及成分Fe的高低、铸件尺寸形状、壁厚大小、涂料类型等等)。
也有内因(例压铸模具本身材质的冶金质量、坯料的锻制工艺、压铸模具结构设计的合理性、浇注系统设计的合理性、模具机(电加工)加工时产生的内应力、压铸模具的热处理工艺、包括各种配合精度和光洁度要求等)。
模具龟裂

压铸模具产生裂纹现象发布时间: 2011-7-12 14:19:21 发布人: 管理员产生龟裂的原因(1)模具在压铸生产过程中温度偏高(最好附加冷却系统).(2)模具在压铸生产过程中脱模剂喷洒不合理.(3)模具热处理不理想,主要是硬度(硬度应不小于HRC--47).(4)模具钢材质不好,推荐使用8407或精练H13早期龟裂一般情况下是因毛坯锻打起锻温度过高(俗称过烧)过烧是一种不可补救的缺陷,因此应严格控制毛坯制造过程中的起锻温度.淬火工艺上也如此,并应严格控制加热时间防止脱炭,材料选择好之后就是热处理了,在生产了一定的数量后注意去应力,还有就是设计合理,尽量避免应力集中,注意R角的大小控制。
在大约1万模次的时候,模具要注意回火去应力,内力集中加工残余应力未去除压铸过程热应力未得到很好去除总之龟裂就是应力集中的表现,可以采用多次回火去除应力从而可以增加模具寿命。
铝合金压铸模具在生产一段时间后龟裂的原因主要有以下几点:(1)模具温度偏高应力过大(2)模具模仁material使用8407,skd61(3)模具热处理硬度过高(4.定期保养,5k times1回火,15k times1回火30k times.预防压铸模龟裂问题,提高模具使用寿命,要做好以下几点:1.压铸模成型部位(动﹑定模仁﹑型芯)热处理要求硬度要保証在HRC43~48 (材料可选用SKD61或8407)2.模具在压铸生产前应进行充分预热作业,其作用如下:2.1使模具达到较好的热平衡,使铸件凝固速度均匀并有利于压力传递.2.2保持压铸合金填充时的流动性,具有良好的成型性和提高铸件表面质量.2.3减少前期生产不良,提高压铸生产率.2.4降低模具热交变应力,提高模具使用寿命.3.新模具在生产一段时间后,热应力的积累是直接导致模仁产生龟裂的原因,为减少热应力,投产一定时间后的模仁及滑块应进行消除热应力的回火处理.具体需要消除热应力的生产模次如下:铝合金压铸模承受巨大交变工作应力,必须从模材,设计,加工,热处理及操作各方面加以注意才能得到长的模具寿命,以下是为使模具能达长寿命的22点要诀:1、高品质模材2、合理设计模壁厚及其它模具尺寸3、尽量采用镶件4、在可能条件下选用尽量大的转角R5、冷却水道与型面及转角的间距必须足够大6、粗加工后应去应力回火7、正确有热处理,淬火冷却须足够快8、彻底打磨去除EDM变质层9、型面不可高度抛光10、模具型面应经氧化处理11、如选氮化,渗层不能太深12、以正确的方法预热模具至推荐的温度13、开始压铸5~10件应使用慢的锤头速度14、在得到合格产品的前提下尽量降低铝液温度15、不使用过高的铝液注射速度16、确保模具得到适当冷却,冷却水的温度应保持在40~50℃17、临时停机,应尽量合模并减小冷却水量,避免再开机时模具承受热冲击18、当模型面在最高温度时应关冷却液19、不过多的喷脱模剂20、在一定数量后的压铸后去应力回火1、最主要的原因就是温度过高,建议使用温度计在压铸过程中随时控制温度(铝合金压铸建议温度<650)2、注意模具的预热,防止热疲劳。
压铸缺陷图示说明分析及防止方法

一、外观特征(CHARACTER) :金属液充满型腔,铸件表面有不规则的孔洞、凹陷或棱角不齐,表面形状呈自然液流或舆液面相似。
二、生原因(REASON):1)内浇道宽度不够或压铸模排气不良。
2)合金流动性差。
3)浇注温度低或压铸模温度低,压射速度低。
4)压射比压不足。
5)压铸型腔边角尺寸不合理、不易填充。
6)喷水太多或没吹干。
三、防止方法(METHOD OF IMPROVEMRNT):1)改进内浇道,改进排气条件,适当提高压铸模温度和浇注温度。
2)提高压射比压和压射速度。
3)注意喷水量适当且注意吹干。
一、外观特征:铸件表面有不规则的明显下陷线形纹路,多出现在离浇口较远区域,对各种零件产生于一定部位。
二、产生原因:1)流互相对接,但未完全熔合而又无夹杂其间,两层金属结合力弱。
2)浇口位置不正确,流路太长。
3)溢流槽位置于金属流汇集处不吻合或容量不够。
4)内浇口速度太低。
5)排气槽堵塞,排气不足。
6)料温及模温太低。
三、防止方法:1)改浇口,改善金属流向,使两种金属流紧密相接。
2)在出现冷格附近增开或加大溢流槽。
3)压铸时先清除排气槽上之铝料或增大排气槽。
4)增加压射速度的同时适当加大浇口厚度及浇道截面积。
5)适当提高料温及模温。
一、 外观特征:铸件表面顺着出模方向留有擦伤的痕迹。
二、 产生原因:1)设计和制造不正确。
如型芯或成型部份无出模斜度或有反斜度。
2)成形表面光洁度不够或加工纹向不对,脱模方向上平整度较差。
3)成形表面有碰伤。
4)喷水太少。
5)金属流撞击壁过剧。
6)铸件顶出有偏斜。
三、 防止方法:1)固定部位拉伤时,要检修模具,修正斜度,打光滑倒扣。
2)在拉伤部位相应的模具上多喷水。
3)调整顶针,使顶出受力平衡。
一、 外观特征(CHARACTER ):在铸件局部有金属的明显层次。
二、 产生原因(REASON ):1)模具刚性不够在金属液填充过程中,模板产生抖动。
2)在压射过程中冲头出现爬行现象。
压铸件铸造缺陷不良改善对策

压铸件铸造缺陷不良改善对策缺陷名称特征产生原因防止方法拉伤沿开模方向铸件表面呈现条状的拉伤痕迹,有一定深度,严重时为一面状伤痕。
另一种是金属液与模具产生焊合、粘附而拉伤,以致铸件表面多肉或缺肉。
1、型腔表面有损伤2、出模方向斜度太小或倒斜3、顶出时偏斜4、浇注温度过高或过低,模温过高导致合金液产生粘附5、脱模剂使用效果不好6、铝合金成分含铁量低于0.6%7、冷却时间过长或过短1、修理模具表面损伤处,修正斜度,600细油石顺磨提高光洁度2、调整或更换顶杆,使顶出力平衡3、更换离型剂4、调整合金含铁量5、控制合适的浇注温度,控制模具温度6、修改内浇口,避免直冲型芯型壁或对型芯表面进行特殊处理气泡铸件表面有米粒大小的隆起表皮下形成的空洞1、合金液在压室充满度过低,易产生卷气,压射速度过高2、模具排气不良3、溶液未除气,熔炼温度过高4、模温过高,金属凝固时间不够,强度不够,而过早开模顶出铸件,受压气体膨胀起来5、脱模剂太多6、内浇口开设不良,充填方向不顺1、提高金属液充满度2、降低第一阶段压射速度,改变低速与高速压射切换点3、降低模温4、增设排气槽、溢流槽、充分排气5、调整熔炼工艺,进行除气处理6、留模时间延长7、减少脱模剂用量裂纹 1. 铸件表面有呈直线状或波浪形的纹路,狭小而长,在外力作用下有发展趋势2. 冷裂-开裂处金属没有被氧化3. 热裂-开裂处金属已经被氧化 1. 合金中含铁量过高或硅含量过低2. 合金中有害杂质的含量过高,降低了合金的可塑性3. 铝硅合金:铝硅铜合金含锌或含铜量过高;铝镁合金中含镁量过多4. 模具:特别是型芯温度太低5. 铸件壁存有剧烈变之处,收缩受阻,尖角位形成应力6. 留模时间过长,应力大7. 顶出时受力不均匀 1. 正确控制合金成分,在某种情况下可在合金中加纯铝锭以降低合金中含镁量;或在合金中加铝硅中间合金以提高硅含量2. 改变铸件结构,加大圆角,加大出模斜度,减少壁厚差3. 变更或增加顶出位置,使顶出受力均匀4. 缩短开模及抽芯时间5. 提高模温,保持模温稳定变形 1. 铸件几何形状与图纸不符2. 整体变形或局部变形 1. 铸件结构设计不良,引起不均匀收缩2. 开模过早,铸件刚性不够3. 顶杆设置不当,顶出时受力不均匀4. 切除浇口方法不当5. 由于模具表面粗糙造成举报阻力大而引起顶出时变形 1. 改进铸件结构2. 调整开模时间3. 合理设置顶杆位置及数量4. 选择合适的切除浇口方法5. 加强模具型腔表面抛光,减少托模阻力流痕、花纹 1. 铸件表面上有与金属液流动方向一致的条纹,有明显可见的与金属体颜色不一样的无方向性的纹路,无发展趋势 1. 首先进入型腔的金属液形成一个极薄的而又不完全的金属层后,被后来的金属液所弥补而留下的痕迹2. 模温过低,模温不均匀3. 内浇道截面积过小及位置不当产生喷溅4. 作用于金属液的压力不足5. 花纹:涂料用量过多 1. 提高金属液温度2. 提高模温3. 调整内浇道截面积或位置4. 调整充填速度及压力5. 选用合适的涂料及调整用量冷隔 1. 铸件表面有明显的、不规则的、下陷线性纹路(有穿透与不穿透两种)形状细小而狭长,有的交接边缘光滑,在外力作用下有发展的可能 1. 两股金属流相互对接,但未完全熔合而又无夹杂存在其间,两股金属流结合力很薄弱2. 浇注温度或压铸模温度偏低3. 选择合金不当,流动性差4. 浇道位置不对或流路过长5. 充填速度低6. 压射比压低 1. 适当提高浇注温度和模具温度2. 提高压射比压,缩短充填时间3. 提高压射速度,同时加大内浇口截面积4. 改善排气、充填条件5. 正确选用合金,提高合金流动性变色、斑点 1. 铸件表面呈现出不同的颜色及斑点 1. 不合适的脱模剂2. 脱模剂用量过多,局部堆积3. 含有石墨的润滑剂中的石墨落入铸件表层4. 模温过低,金属液温度过低导致不规则的凝固引起 1. 更换优质脱模剂2. 严格喷涂量及喷涂操作3. 控制模温4. 控制金属液温度网状毛翅 1. 压铸件表面上有网状发丝一样凸起或凹陷的痕迹,随压铸次数增加而不断扩大和延伸 1. 压铸模型腔表面龟裂2. 压铸模材质不当或热处理工艺不正确3. 压铸模冷热温差变化大4. 浇注温度过高5. 压铸模预热不足6. 型腔表面粗糙 1. 正确选用压铸模材料及热处理工艺2. 浇注温度不易过高,尤其是高熔点合金3. 模具预热要充分4. 压铸模要定期或压铸一定次数后退火,消除内应力5. 打磨成型部分表面,减少表面粗糙度6. 合理选择模具冷却方法凹陷1、铸件平滑表面上出现凹陷部位 1. 铸件壁厚相差太大,凹陷多产生在厚壁处2. 模具局部过热,过热部分凝固慢3. 压射比压低4. 由憋气引起型腔气体排不出,被压缩在型腔表面与金属液界面之间 2. 铸件壁厚设计尽量3. 模具局部领却调整4. 提高压射比压5. 改善型腔排气条件欠铸(缺料)1、铸件表面有浇不足部位1、流动性差原因:1) 合金液吸气、氧化夹杂物,含铁量高,使其质量差而降低流动性2) 浇注温度低或模温低2、充填条件不良:1) 比压过低2) 卷入气体过多,型腔的背压变高,充型受阻3、操作不良,喷涂料过度,涂料堆积,气体挥发不掉1、提高合金液质量2、提高浇注温度或模具温度3、提高比压、充填速度4、改善浇注系统金属液的导流方式,在欠铸部位加开溢流槽、排气槽5、检查压铸机能力是否足够毛刺飞边 1. 压铸件在分型面边缘上出现金属薄片 1. 锁模力不够2. 压射速度过高,形成压力冲击峰过高3. 分型面上杂物未清理干净4. 模具强度不够造成变形5. 镶块、滑块磨损与分型面不平齐 1. 检查合模力和增压情况,调整压铸工艺参数2. 清洁型腔及分型面3. 修理模具4. 最好是采用闭合压射结束时间控制系统,可实现无飞边压铸气孔(内部缺陷) 1. 解剖后外观检测或探伤检查,气孔具有光滑的表面、形状为圆形 1. 合金液导入方向不合理或金属液流动速度太高,产生喷射;过早堵住排气道或正面冲击壁而形成漩涡包住空气,这种气孔多产生排气不良或深腔处2. 由于炉料不干净或熔炼温度过高,使金属液中较多的气体没除净,在凝固时析出没能充分排出。
压铸模具常见失效

1 压铸模具常见失效形式下面结合工厂实际情况分析了压铸模具的失效形式和失效机理。
1.1热裂热裂是模具最常见的失效形式,如图1所示。
热裂纹通常形成于模具型腔表面或内部热应力集中处,当裂纹形成后,应力重新分布,裂纹发展到一定长度时,由于塑性应变而产生应力松弛使裂纹停止扩展。
随着循环次数的增加,裂纹尖端附近出现一些小孔洞并逐渐形成微裂纹,与开始形成的主裂纹合并,裂纹继续扩展,最后裂纹间相互连接而导致模具失效。
1.2整体脆断整体脆断是由于偶然的机械过载或热过载导致模具灾难性断裂。
材料的塑韧性是与此现象相对应的最重要的力学性能。
材料中有严重缺陷或操作不当,会引起整体脆断,如图2所示。
1.3侵蚀或冲刷这是由于机械和化学腐蚀综合作用的结果,熔融铝合金高速射入型腔,造成型腔表面的机械磨蚀。
同时,金属铝与模具材料生成脆性的铁铝化合物,成为热裂纹新的萌生源。
此外,铝充填到裂纹之中与裂纹壁产生机械作用,并与热应力叠加,加剧裂纹尖端的拉应力,从而加快了裂纹的扩展。
提高材料的高温强度和化学稳定性有利于增强材料的抗腐蚀能力。
2 压铸模具常见失效分析方法为了延长模具的使用寿命,节约成本,提高生产效率,就必须研究模具的失效形式和导致模具失效的原因以及模具失效的内部机理。
由于压铸模具失效的原因比较复杂,要从模具的设计、材料选择、工作状态等很多方面来进行分析。
图3为压铸模具常见失效分析图。
图 3 压铸模具常见失效分析方法2.1裂纹的表面形状及裂纹扩展形貌分析失效模具型腔表面主要是冲蚀坑,大小比较均匀,冒口所对部位有明显的冲蚀坑外,表面明显具有一定方向的划痕,划痕上分布有大小不等的铝合金块状物。
由于正对浇口部位直接受金属液的冲刷,该部位具有明显的冲刷犁沟,同时可观察到划痕间有裂纹。
裂纹从裂纹源出发,并向西周扩展。
裂纹内有大量的夹杂物,裂纹边缘有二次裂纹。
由于模具使用时间短,一般部位表面主要是冲蚀坑和焊合,而浇口所对部位主要为液态金属冲刷形成的犁沟和热疲劳裂纹。
- 1、下载文档前请自行甄别文档内容的完整性,平台不提供额外的编辑、内容补充、找答案等附加服务。
- 2、"仅部分预览"的文档,不可在线预览部分如存在完整性等问题,可反馈申请退款(可完整预览的文档不适用该条件!)。
- 3、如文档侵犯您的权益,请联系客服反馈,我们会尽快为您处理(人工客服工作时间:9:00-18:30)。
压铸模型腔龟裂失效分析——张年随着现代工艺技术水平的发展,少,无切削加工已经成为现代成形加工的一个发展趋势。
压铸就是一种高效率的少、无切削金属热加工成形方法。
近十几年来这项技术发展的十分迅速。
现在压铸模件已广泛地应用许多工业产品中。
但由于压铸模工作在极其恶劣的环境下,从而易产生型腔表面龟裂导致模具失效。
根据调查,压铸模的失效中大约有70%以上是龟裂失效。
那么型腔表面龟裂是怎样产生的呢?它与那些因素有关?本文运用热疲劳理论对其进行探讨,并提出相应是压铸模增寿措施。
一、表面是工作环境:在压铸过程中模腔表面直接与高温高压的金属相接触,它一方面要受到金属液的直接冲刷产生磨损,高温氧化和各种腐蚀,使型腔表面损坏而导致模具失效。
另一方面由于压铸生产时不停地浇铸和开模,使型腔表面温度周期性地剧烈上升、下降而导致热疲劳产生龟裂失效。
一般地说来压铸不同熔点的合金金属液时型腔表面的热冲击是大不相同的。
锌合金熔化温度大约为400℃,型腔表面的最高温度不会太高,她的失效主要取决于金属液对型腔表面的冲刷和腐蚀。
而在压铸高熔点合金时,由于合金的熔化温度较高,从而导致型腔表面的最高温度也高(铝合金熔化温度为600—700℃,型腔表面最高温度达600℃以上,铜合金熔化温度为900—1000℃,型腔表面最高温度达800℃以上,黑色金属熔化温度为1200—1600℃,压铸模型腔表面最高温度达1000℃以上),模具的寿命主要取决于热龟裂。
二、热疲劳的产生在压铸时由于压铸的时间很短,金属液进入型腔的先后不一致,流过的金属数量也各不相同,因此成型部分各零件的不同部位也各不相同,而且型腔还要受到金属液的冲刷、腐蚀以及周围气氛的氧化等腐蚀作用,因此其龟裂机理更加复杂。
1、循环热应力在压铸过程中,压铸模型腔直接受到高温、高压、高速合金液流的激烈冲刷和冲压作用,使部分动能转化为热能,以及本身的热量,致使型腔、型芯与液流接触的表面温度迅速升高,而内部温度相对较低,导致型腔表面由于热膨胀差而形成压应力,当开型后型腔与空气接触和喷刷涂料时,有激冷作用,型腔表面温度低于内部温度致使型腔表面产生拉应力.在周期性的热冲击作用下,型腔表面承受交变热应力作用。
某一瞬时的热应力超过材料的热疲劳极限时,就会在型腔表面产生热裂纹。
型腔表面的热应力时高维应力,在多维应力作用下产生龟裂纹,这些裂纹在以后的热应力作用下扩展而导致模具的龟裂失效。
2 、热疲劳组织变化(1)持续滑移带的产生疲劳滑移带与金属结晶在一个方向上变形时的滑移带明显不同。
在发生疲劳的铜试件剖面进行观察,有一部分滑移带由表面挤出来数微米,在挤出的附近同样发生了数微米,在挤出的附近同样发生了数微米的陷入。
从这个尖锐的“陷入”部位,由于应力集中而产生早期的疲劳龟裂纹(2)亚结构的发展与空穴的产生在裂纹附近产生2~3微米的亚结构,亚结构不断扩展,而在裂纹相接的应变集中区域产生成为裂纹的空穴,这些空穴进一步连接起来之后,裂纹便进一步扩展。
可以看出,疲劳裂纹是产生在持续滑带的“陷入”部分,也就是在形成亚结构时,由于空穴的连接而产生。
3、组织特征高温疲劳与低温疲劳的不同之处在于:持续滑移带的消失,由穿晶断裂向晶界断裂转变,亚结果断裂。
而且温度越高,这三个特征越明显。
高温疲劳过程中主要发生:⑴晶界移动境界的移动发生在最大剪应力放向上,结果晶界在最大剪应力向上排列。
⑵晶界滑移与断裂首先发生晶界移动,在晶体排列后,产生晶体界滑移并出现空穴,然后各孤立的晶界上的空穴渐渐成长而连成一体,高温度疲劳的裂纹便通过晶界相互连接而现实它的扩展。
⑶由结晶体分化引起饿了断裂在每个晶体中,裂纹发生在高温度疲劳中生成发展的饿亚结构的亚晶体上。
压铸模除了锌合金压铸模外,其它均很高,热疲劳组织变化以高温度低循环疲劳相似。
锌合金压铸模的热疲劳组织变化介于高温疲劳组织以低温疲劳组织变化之间。
三、影响龟裂产生的因素压型腔所承受的热应力相比,型腔所受的机械应力小得多,可以不予考虑。
影响龟裂产生的主要因素有:热因子在影响热度劳强度的因素中,直接有影响的是热应力的大小。
热应力是由热应变产生的,而热应变是模具中温度分布不均所引起的热膨胀差而感应出来的。
若设材料的弹性模具为E ,线胀系数为a ,温度差为∆T 泊松系数为r ,则热弹性应力为:γασ-I E ⋅∆T ⋅= 为了理解热应力的性质,需要知道与之有关的热因子。
⑴导热系数:导热系数越大,模具内产生的温度梯度就越小,因而热应力也小。
⑵线胀系数:线胀系数与热应力成正比。
⑶传热系数:传热系数越大,热应力越大。
材料的机械性能材料的屈服应力、弹性系数和应变硬化性决定热应变量和热应力的大小,而强度和延性影像材料的抗热应力能力。
(1)弹性模具E 与泊松指数r由前式可以看出E 、r 与б的关系。
随着温度的升高,E 渐渐减小,而r 只是略有增加。
﹙2﹚强度和延性热疲劳是基于应变循环产生的。
因此延性越大于低循环区城内的热疲劳寺命越有利 ,而强度与热疲劳没有多大的关系。
﹙3﹚每一循环的塑性应变由有关资料知塑性应变范围 P ε∆与断裂循环数N 成反比。
3、工作条件、⑴压铸工艺中的温度参数对龟裂影响较大。
若下限温度T 1 一定,而上限温度T 2 越高,N 越低,某上限温度T 2一定, T 1 减小,△T 增大,N 减小。
平均温度T m 越高,则N 越小。
⑵加热速度增大导致大幅度的温度变化及高应变速度。
一般来说,当应变速度增大时,材料的高温度强度和延性随之增加,所以加热速率大材料并非不利。
上限温度T2 的保持时间对于蠕变引起的应力松弛,材料的组织变化及腐 蚀作用都有很大作用,所以相当重要。
保持时间越长,寿命越低。
⑶压铸模工作时的环境气氛对模具寿命影响很大,由于温度的变化而产生的腐蚀、晶粒长大、氧化,以及压祷合金的腐蚀、冲刷均会加速龟裂的产生。
模块的尺寸越大,表面层热膨胀收缩的约束程度越高,则热疲劳强度越小。
(4)模具的加工工艺不当,如刀痕、磨削裂纹与磨削过热、电火花加工异常层的尺寸、焊接不良、锻造质量不好、型面脱碳以及模具设计尖角、冷却方式不当等均会加速龟裂产生,影响模具寿命。
四、增寿途径1、合理选材模具材料选用是否合理对模具寿命至关重要。
目前我国企业仍大量使用3 Cr2W8V钢制造钢、铝合金压祷模,而国外较多采用H13钢。
3Cr2W8V钢韧性差,工艺性不好,导热性差,线胀系数高,抗热疲劳性能差,因而模具易产生龟裂失效。
H13钢具有优良的抗热疲劳性能,应该取代3Cr2W8V钢。
此外,马氏体时效钢制压祷模具有更高的寿命,但马氏体时效钢不能用来制造黑色金属压祷模。
对于熔点合金压祷模、采用钨基、钼基合金取得了很好的效果。
2、用热处理改善材料性能为了适应生产需要,充分发挥内在潜力,最大限度地改善模具钢各项性能指标,应采用有效的热处理工艺。
(1)常规热处理工艺为了提高H13韧性和热疲劳性能,最佳热处理工艺为1080℃淬火,600℃回火,可获得细板状回火马氏和少量粒状碳化物,能大幅度提高钢的高温区服强度和韧性,从而有效地提高热疲劳抗力和回火抗力。
(2)双重处理H13钢经1160 淬火/520 回火+1050淬火,经高温淬火能提高断裂韧性K。
使冲击韧性下降。
采用双重处理,可在不降低ak的情况下显著提高Kzc。
Kzc的改善是由于孪晶马氏体和未溶碳化物量的减少及残奥氏体量的增加所致。
而Kzc提高有利于提高热作模具钢的疲劳寿命。
(3)细化处理其工艺为1150℃淬火,使碳化物基本全固溶于奥氏体中,再经780℃回火后得到回火索氏体组织,碳化物呈均匀,细小,弥散析出。
通过这种预处理后,再在1000℃淬火加热,碳化物溶解速度快,基体中碳及合金元素的浓度差小,成分不均匀的微区尺寸小,且碳化物均匀弥散分布强烈阻碍奥氏体晶粒长大,因而淬火后是碳化物尺寸显著减小且弥散分布,同时使奥氏体晶体细化,达到13级,碳化物平均直径0.1µm。
与常规热处理相比,H13钢塑性基本不变,硬度、冲击韧性及耐磨性明显提高。
3、表面强化为了提高型腔的抗蚀性,耐磨性,抗热疲劳性能和抗粘附性,可进行型腔表面强化处理。
常用的方法有渗氮、渗硫、渗铬、渗硼等。
表面强化处理方法很多,如3Cr2W8V钢制压铸模在450℃~520℃栗子渗氮处理6~9小时后,渗氮层深可达到0.2~0.3mm,可大大提高其疲劳寿命。
4、结构合理化在模具设计中注意避免尖角,厚薄壁相接处合理,以免出现应集中而失效。
对大型镶块可用许多小型镶块代替,因为小型镶块温度梯度,变形小且易于热处理、表面处理。
模具加工时要防止出现刀痕,磨削裂纹及磨削过热,防止脱电花火加工异常层中微裂纹的危害,还要防止脱碳、氧化等缺陷,以及改用铸造模具代替段造模具,因为在高温下铸造模具具有较高抗热裂性能及强度。
5、保养(1)预热预热可提高模具德尔断裂韧性,减小模具的温差。
但过高的预热温度将升高模具型腔表面的接触温度,降低模具的屈服强度和疲劳强度。
这要根据生产经验确定。
(2)停工时的保温中途停工,必须对模具做适当保温,以免引起内应力开裂。
(3)中间去应力回火当新模具使用到设计寿命的1/6~1/8时,应对模具型腔及模架进行450℃~480℃回火,并对型腔抛光和氮化,以消除内应力和型腔表面的较微裂纹。
以后每1200~1500模次进行同样保养。
此外,模具使用一段时间后,由于压铸速度过高和长时间使用,型腔和型芯上含有沉积物,应采用研磨或机械去除,但不要损伤其他型面。
压铸模型腔龟裂失效机理十分复杂,目前还没有完整系统的科学解释,随着热疲劳理论等相等相关学科的发展,其机理及与措施有待进一步地深入研究。
【参考文献】:[1] 何晋瑞。
金属高温度疲劳。
国防工业出版社,1988[2] 张玮玮。
浅谈提高压铸模寿命。
模具工业,1996.(4)[3] 沈利群。
改善H 1 3钢热作模具钢性能的措施。
模具工业,1996.(4)[4 ]张玉林,压铸件质量及模具寿命,模具技术,1996.(2)。