硅片的腐蚀
p型硅片腐蚀电位

由于您提到的话题属于专业领域,我将尽力为您提供相关信息。
对于硅片腐蚀电位,下面是详细的解释。
硅片腐蚀电位的理论基础与影响因素1. 硅片腐蚀电位概述硅片腐蚀电位是指在硅片表面进行化学腐蚀时所需的电位值。
在硅片工艺中,腐蚀是一项重要的加工步骤,而腐蚀电位则直接影响着腐蚀过程的控制和效果。
2. 影响硅片腐蚀电位的因素a. pH值:溶液的pH值对腐蚀电位有着直接的影响,不同pH 值下硅片的腐蚀电位会有所差异。
b. 温度:溶液温度对腐蚀电位也有显著影响,通常情况下,温度越高,腐蚀电位越低。
c. 溶液成分:不同的溶液成分对硅片腐蚀电位也有着不同的影响,例如氧化剂、还原剂等都会对腐蚀电位产生影响。
硅片腐蚀电位的实验测定方法1. 极化曲线法极化曲线法是一种常用的测定硅片腐蚀电位的方法。
通过在特定条件下施加电势,观测电流随时间的变化,从而得到硅片的腐蚀电位。
2. 电化学阻抗谱法电化学阻抗谱法也是一种常用的测定方法,通过对不同频率的交流电信号的响应,得到硅片在不同电位下的阻抗谱,从而推断腐蚀电位。
硅片腐蚀电位的应用与意义1. 工艺优化通过准确测定硅片的腐蚀电位,可以优化腐蚀工艺参数,提高工艺的稳定性和可控性。
2. 质量控制腐蚀电位可以作为一个重要的质量控制参数,用于监控硅片腐蚀过程的稳定性,保证产品质量。
3. 新材料研发在新材料的研发过程中,腐蚀电位的测定可以帮助研究人员了解材料的耐蚀性能,指导新材料的设计与改进。
结语硅片腐蚀电位作为一个重要的工艺参数,在硅片工艺与新材料研究中具有重要意义。
深入了解硅片腐蚀电位的理论基础与测定方法,有助于推动相关领域的科研与工程实践。
硅片的化学腐蚀方法
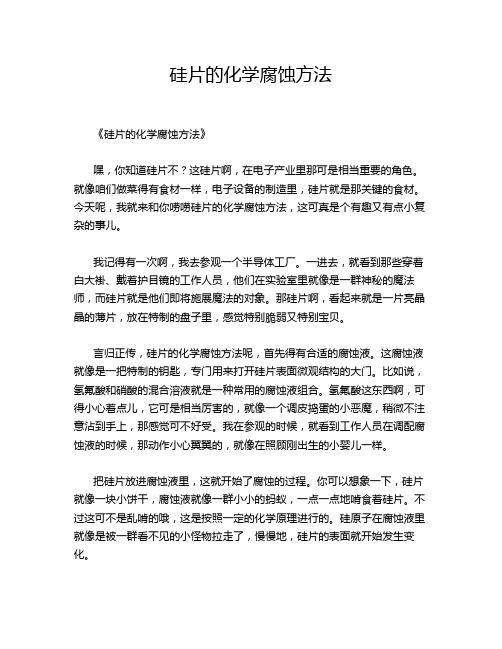
硅片的化学腐蚀方法《硅片的化学腐蚀方法》嘿,你知道硅片不?这硅片啊,在电子产业里那可是相当重要的角色。
就像咱们做菜得有食材一样,电子设备的制造里,硅片就是那关键的食材。
今天呢,我就来和你唠唠硅片的化学腐蚀方法,这可真是个有趣又有点小复杂的事儿。
我记得有一次啊,我去参观一个半导体工厂。
一进去,就看到那些穿着白大褂、戴着护目镜的工作人员,他们在实验室里就像是一群神秘的魔法师,而硅片就是他们即将施展魔法的对象。
那硅片啊,看起来就是一片亮晶晶的薄片,放在特制的盘子里,感觉特别脆弱又特别宝贝。
言归正传,硅片的化学腐蚀方法呢,首先得有合适的腐蚀液。
这腐蚀液就像是一把特制的钥匙,专门用来打开硅片表面微观结构的大门。
比如说,氢氟酸和硝酸的混合溶液就是一种常用的腐蚀液组合。
氢氟酸这东西啊,可得小心着点儿,它可是相当厉害的,就像一个调皮捣蛋的小恶魔,稍微不注意沾到手上,那感觉可不好受。
我在参观的时候,就看到工作人员在调配腐蚀液的时候,那动作小心翼翼的,就像在照顾刚出生的小婴儿一样。
把硅片放进腐蚀液里,这就开始了腐蚀的过程。
你可以想象一下,硅片就像一块小饼干,腐蚀液就像一群小小的蚂蚁,一点一点地啃食着硅片。
不过这可不是乱啃的哦,这是按照一定的化学原理进行的。
硅原子在腐蚀液里就像是被一群看不见的小怪物拉走了,慢慢地,硅片的表面就开始发生变化。
这个腐蚀的速度也是有讲究的。
如果腐蚀得太快,那就像是一场暴风雨把庄稼都给冲坏了一样,硅片可能就会被过度腐蚀,变得不符合要求。
如果腐蚀得太慢呢,就像蜗牛爬一样,效率太低,生产的时间成本可就上去了。
在那个工厂里,我看到他们有专门的仪器来监测腐蚀的速度。
那些仪器上有好多小灯和显示屏,就像科幻电影里的控制台一样,工作人员时不时地就去瞅一眼,看看腐蚀的情况是不是正常。
而且啊,这腐蚀的均匀性也很关键。
我看到一块硅片在腐蚀之后,工作人员拿起来在灯光下仔细地看。
那表情就像是在挑挑拣拣的买菜大妈,特别认真。
KOH溶液中(110)硅片腐蚀特性的研究

KOH溶液中(110)硅片腐蚀特性的研究KOH溶液中(11O)硅片腐蚀特性的研究贾翠萍,董玮,徐宝琨,潘(吉林大学电子科学与工程学院集成光电建旋,周敬然,陈维友子国家重点实验室,长春130012)摘要:研究了在KOH溶液中(110)硅片的腐蚀特性,在保证(1l0)面的平整和{ll1}面的光滑的腐蚀实验条件下,利用(1l0)面和{ll1}面腐蚀选择比大,采用湿法腐蚀技术可以制作高深宽比结构的方式,在(1l0)硅片上设计制作出光开关用微反射镜.在腐蚀过程中光开关悬臂的凸角处产生了削角现象,利用表面硅原子悬挂键的分布特征对产生削角的原因作了合理解释,这为以后研究凸角补偿提供了理论依据.关键词:KOH溶液:(1l0)硅片:凸角;悬挂键中图分类号:TN405.98文献标识码:A文章编号:1003.353X(2005)06.0052.04 StudyontheCharacteristicsofthe(1lo)SiliconEtchedinK0HSolutionJIACui—ping,DONGWei,XUBao—kun,PANJian—xuan,ZHOUJing—ran,CHENWei —youLStateKeyLabonIntegrateOptoelectronics.CollegeofElectronicSciences&Enginee ring,JilinUniversity,Changchgin13O012,China)Abstract:Thecharacteristicsofthe(110)siliconetchedinKOHsolutioniSstudied.Onthe experimentalconditionoftheflatetched(110)planeandthesmooth{111}planes,thehigh—respect—ratiostructurecanbefabricatedduetothehighetchratioofthe(110)planeto{111}planes.Inthi sway,themicromirrorfortheopticalswitchcanbefabricatedinthe(1101silicon.Butwhentheb eamoftheopticalswitchisformed,undercutOccursontheconvex.Anditcanbeexplainedbythe danglingbondsofthesiliconatom,whichisthebasictheoryforthefurtherstudyoftheconvex compensation.Keywords:KOHsolution;(110)silicon;convex;danglingbonds1引言采用KOH溶液进行各向异性腐蚀硅是微机械加工中的一项重要技术,利用它可以形成方形,矩形的硅膜片以及其他复杂的三维结构,在传感器,执行器及微机械制作领域具有非常广泛的应用.有关(100)硅片的各向异性腐蚀技术的研究和应用比较多,而(1l0)硅片在腐蚀时,表现出与(100)硅片不同的特性,能够形成的垂直于衬底的{lll}面,可以提供大面积,高质量的光学表面,在光基金项目:国家重点计划863项目(2002AA312023)52半导体技术第30卷第6期学领域具有广泛的应用.在KOH溶液中,腐蚀(1l0)面与{lll}面的选择比很高,可以形成高深宽比微结构.利用可以实现高深宽比结构的方式在(1l0)硅片上制作的微反射镜【1】已应用于分束器,硅标准器,法布里.珀罗干涉仪和迈克尔逊干涉仪等.本文主要研究了在KOH溶液中(1l0)硅片的腐蚀特性,即KOH溶液的浓度和温度对腐蚀的(1l0)衬底表面和垂直于衬底的{lll}侧面平整度和光滑性的影响.利用在KOH溶液中(1l0)面和{lll}面腐蚀选择比大的特点,可以在(1l0)硅片上设计制作光开关用微反射镜.但在腐蚀过程2005年6月2tr.#-g丝术■log)中,光开关悬臂凸角处产生了削角,本文从表面硅原子悬挂键}2_,】的分布特征对削角产生的原因进行了解释.2实验研究在(110)硅片上有4个与硅片水平(110)面垂直的{111}面,它们分别是(1.I1),(一11—1),(_l11)和(1_I_I),如图1所示.这四个晶面两两平行,彼此间的夹角为70.53..实验中首先用扇形定位结构[4】在(110)硅片上精确确定{111}晶面的方位.在光刻对版时,图形方位与晶体内部{1l1}面的方位稍有偏离,腐蚀出的{111}侧面就会出现侧棱现象.因此为得到光滑平整的{111}面,必须采用定位结构来确定{111}晶面方位.腐蚀后得到侧面为垂直于(110)面的U形槽结构,如图2所示.u型槽的侧面是{111}面,底面为(110)面.图l(1l0)硅片上{ll1}面的分布情况{lll}面图2KOH溶液腐蚀后的(1l0)面和{lll}面采用KOH溶液腐蚀在(110)硅片上制作微结构,不仅要有垂直光滑的{1111侧面,也需要有平整的(110)底面.因此进行器件结构制作前要对它们在KOH溶液中腐蚀呈现表面平整光滑的条件有所了解.图3为温度为70℃不同浓度KOH溶液利用磁力搅拌器腐蚀的(110)面情况.由图中可以明显看到KOH溶液浓度低于40%时,腐蚀得到一簟■一■图370℃不同浓度KOH溶液腐蚀(1】0)面的SEM图的(110)表面有许多的棱状结构,整个表面起伏不平;而溶液浓度大于40%时,(110)面的表面出现丘状突兀,同样表面也是凸凹不平;只有溶液浓度在40%的情况下腐蚀得到的(110)面平整性比较好.因此,实验选用浓度为40%的KOH腐蚀溶液.除了KOH溶液浓度对腐蚀的(110)面有影响外,腐蚀液的温度也是必不可少的考虑因素.图4为不同温度下40%KOH溶液腐蚀的(110)面.由图可以直接观察到腐蚀的(110)面随KOH溶液温度的升高光滑度有所增加.一一■_-图4不同温度40%K0H溶液腐蚀(1】0)面的SEM图实验还发现,{111}面的光滑程度随KOH溶液浓度和温度的变化基本保持不变.70℃下40%的KOH溶液腐蚀的{111}面,用原子力显微镜测量其粗糙度仅为10nm,是较好的光学表面.(110)面和{111}面在KOH溶液中腐蚀速率有很大的差别,图5为(110)面与{111}面的选择比随70~C下KOH溶液浓度的变化情况.K0H溶液浓度在30%~50%,(110)面与{111}面的选择比都在130以上,利用这个特性可以设计制作高深宽比微结SemiconductorTechnologyV o1.30No.653=一:~^=丑辙蚓K0H浓度/wt%图5(1l0)面与{lll}面的选择比随70℃下KOH溶液浓度的变化构.我们在(110)硅片上已制作出了应用于光开关的微反射镜.图6为微反射镜的扫描电镜图,该反射镜的垂直性优于在(100)硅片上制作的微反射镜.图6(1l0)硅片上制作的微反射镜SEM图在(110)硅片上制作光开关,用KOH溶液腐蚀制作悬臂时,悬臂凸角处产生了削角现象,如图7所示,A+,B+定义为凸角,由图可以看出A+,B+两凸角处出现了很明显的削角.产生凸角现象的原因可以通过分析凸角处的表面硅原子悬挂键的分布特征来解释.图8是凸角处表面硅原子的悬挂键情况,由图可以看出对应于A+凸角顶端处的硅原子AA'连线上每个硅原子有两个悬挂键,而相邻的处于{111}面上的每个硅原子只有一个悬挂键.由于两处表面硅原子悬挂键的密度不同,即凸角A+处表面硅原子的悬挂键密度比相邻的处于{111}面上的表面硅原子悬挂键密度大, 致使在化学反应中两处的稳定性有差别,凸角处的54半导体技术第30卷第6期图7KOH溶液腐蚀后的光开关悬臂A图8凸角腐蚀速率较{111)面的大,由此产生了凸角削角.再看B+凸角处BB'连线附近的硅原子悬挂键情况, 和{111}表面硅原子一样,每个硅原子也只有一个悬挂键.但是凸角处表面硅原子的排列密度比{111}面的要大,换句话也可以说是凸角处表面硅原子的悬挂键密度较{111}面硅原子的大.同样由于悬挂键密度的差异使得凸角处和相邻{111}面的腐蚀速率不一致,凸角处的腐蚀速率比{111}面的大,在该处也产生了削角现象.为进一步完善器件的结构,需要进行合理的凸角补偿设计,这部分工作有待于进一步的研究.3结论用KOH溶液腐蚀(110)硅片,腐蚀出垂直于衬底表面的{111}面可以提供大面积,高质量的光学表面,并已被应用到很多的光学元件中.实验研究了KOH溶液浓度和温度对腐蚀的(110)面和{111}面平整度和光滑性的影响,70℃,40%的KOH溶液腐蚀的(110)面比较平整,并且40%KOH溶液腐蚀的(110)面随溶液温度的升高,光滑度有所增加,而腐蚀出的{111}面的平整2005年6月支撑丝木■ii面ogY性基本不随KOH溶液温度和浓度改变.在70℃下KOH溶液浓度为40%的条件下腐蚀出的{111}面,用原子力显微镜测得其表面粗糙度仅为10nm,是较好的光学表面.并且在70℃时KOH溶液浓度在35%~50%范围内测得(110)面和{111{面的选择比都在130以上,可以利用这种特性和相应的工艺条件设计制作高深宽比微结构.我们在(110)硅片上已设计制作出光开关用微反射镜,垂直性优于在(1O0)硅片上制作的反射镜.但在用KOH溶液腐蚀制作光开关悬臂时,悬臂凸角处产生了削角现象,本文从硅原子悬挂键的分布特征对产生削角的原因做了解释,为以后完善器件结构,进行补偿图形的设计提供了较好的理论依据.参考文献:【11UENISHIY,TSUGAIM,MEHREGANYMl Microoptomechanicaldevicefabricatedbyanisotro—picetchingof(100)silicon[J].JMicromechMicroeng, 1995,5:305—312.【2】PALIKED,eta1.Ellipasometricstudyoforientation—dependentetchingofsiliconinaqueousKOH【J】.J Electrochem.Soc,1985,132(4):871.【31PALIKED,eta1.Studyoftheetch—stopmechanism insilicon[J].JElectrochemSoc,l982,l29(9):2051.【4】CIARLODR.Alatchingaccelerometerfabricatedby theanisotropiCetchingOf(110)Orientedsilic0nwafers[J】.JMicromechMicroeng,l992,2:12一l3.(收稿日期:2004l201)作者简介:贾翠萍(1979.),女,山东人,博士研究生,主要研究方向为MOEMS光通信器件;陈维友(1965一),男,博士生导师,主要从事OEDCAD和光电通信器件的研究.(上接第51页)时,R.川.等于O.026(K/W),即使其厚度为100uin,R.All.h也只等于0.131(K/W);当选用热沉粘接胶Ablefilm5020K,:O.7W/m?K,同时其厚度等于20laIll时,.h等于1.457(K/W),当其厚度为1001.tin时,.A¨.h等于7.286(K/W);当我们选用导电型芯片粘接胶Ablebond84—1LMISR4,=2.5W/m?K,同时其厚度等于20l-t1"13时,R.All.h等于0.408(K/W),当其厚度为100lain时,.Alt.h等于2.041(K/W).因此,选用不同的粘接材料对其热阻存在很大的影响,同时,在印刷或涂敷芯片粘接材料时,如何降低材料厚度也十分重要.4结语LED芯片结温最高允许125℃,如果其最差工作环境温度为65℃,则对一个1W的大功率LED来说,考虑到从大功率器件外部热沉的热阻一般为4O(K/W),器件pn结至器件的热阻应小于20(K/W).而对一个5w的大功率LED来说,如果其最差工作环境温度为65℃,则从pn结至环境的热阻要小于12w才能保证芯片结温不超过125℃,而如果选用Ablefilm5020K热沉粘接胶,=O.7w/Ill?K同时其厚度为100laIll,仅芯片粘贴材料的热阻..h就等于7.286(K/W).因此,在Flipchip大功率LED器件的封装中,选用合适的芯片衬底粘贴材料并在批量生产工艺中保证粘贴厚度尽量小,对保证器件的可靠性和出光特性是十分重要的.参考文献:【l】DANIELAS,JEROMECB,DAVEC,eta1.Illumination withsolidstatelightingtechnology[J】.IEEEJonSe- lectedTopicsinQuantumElectronics,2002,8(2):310—320.【2】ApplicationBriefAB23,ThermaldesignconsiderationsforLuxeon5wattpowerlightsources【EB/0L】.http://WWW.1um订.2002—0l—O8.【3】ThermalmanagementofgoldendragonLED[EB/OL].http://www.osram?.2002—0l—l1.(收稿日期:2004ll05)作者简介:余彬海(1965.),男,湖北鄂州人,博士后,电子高级工程师,l997年4月毕业于华中理工大学机电一体化专业,获工学博士学位,现在佛山市国星光电科技有限公司任副总经理,总工程师,主要从事半导体发光器件和半导体照明产品开发工作,专业是半导体发光器件和半导体照明技术研究,主要研究方向为新型大功率发光器件,器件可靠性.SemiconductorTechnologyV o1.30No.655。
硅片腐蚀工作步骤及工作事项

硅片腐蚀㈠、目的和原理:利用氢氧化钠对多晶硅腐蚀作用,去除硅片在多线切割锯切片时产生的表面损伤层,同时利用氢氧化钠对硅腐蚀的各向异性,争取表面较低反射率较低的表面织构。
解释:①现有多晶硅片是由长方体晶锭在多线切割锯切成一片片多晶硅方片。
由于切片是钢丝在金刚砂溶液作用下多次往返削切成硅片,金刚砂硬度很高,会在硅片表面带来一定的机械损伤。
如果损伤不去除,会影响太阳电池的填充因子。
②氢氧化钠俗称烧碱,是在国民经济生产中大量应用化工产品。
由电解食盐水而得,价格比较便宜,每500克6元。
化学反应方程式为:↑+↑+=+222222H Cl NaOH O H NaCl 电解。
分析纯氢氧化锂、氢氧化钾也可以与硅起反应,但价格较贵。
如氢氧化锂每500克23元,用于镉-镍电池电解液中。
↑+=++23222a 2H SiO N O H NaOH Si 加热③碱性腐蚀优点是反应生成物无毒,不污染空气和环境。
不像HF-HNO 3酸性系统会生成有毒的NO x 气体污染大气。
另外,碱性系统与硅反应,基本处于受控状态。
有利于大面积硅片的腐蚀,可以保证一定的平行度。
㈡、步骤:面产生出部分反射率较低的织构表面。
如果含有[100]晶向的晶粒,就可以长出金字塔体状的绒面。
第五步是通过盐酸中和残余的氢氧化钠,化学反应方程式为:O H NaCl NaOH HCl 2+=+。
第七步氢氟酸络合掉硅片表面的二氧化硅层,化学反应方程式为:O H SiF H HF SiO 26222][6+=+。
2. 我们就粗抛作过实验,投入50片硅片:a . 在20%NaOH 溶液中,温度为80℃,反应了10分钟,硅片厚度平均去掉了32μm 。
b . 在15%NaOH 溶液中,温度为80℃,反应了10分钟,硅片厚度平均去掉了25μm (此数据来源于小片实验)。
硅片粗抛是放热反应且反应激烈,反应速度与温度上升有点正反馈的态势:温度高,浓度高反应就会更激烈。
新硅片由于表面粗糙,表面积大一些反应也会激烈一些。
硅片腐蚀工艺

硅片腐蚀工艺
硅表面的化学腐蚀一般采用湿法腐蚀,硅表面腐蚀形成随机分布的微小原电池,腐蚀电流较大,一般超过100A/cm2,但是出于对腐蚀液高纯度和减少可能金属离子污染的要求,目前主要使用氢氟酸(HF),硝酸(HNO3)混合的酸性腐蚀液,以及氢氧化钾(KOH)或氢氧化钠(NaOH)等碱性腐蚀液。
现在主要用的是HNO3-HF腐蚀液和NaOH腐蚀液。
下面分别介绍这两种腐蚀液的腐蚀化学原理和基本规律。
1.HNO3-HF腐蚀液及腐蚀原理
通常情况下,硅的腐蚀液包括氧化剂(如HNO3)和络合剂(如HF)两部分。
其配置为:浓度为70%的HNO3和浓度为50%的HF以体积比10~2:1,有关的化学反应如下:3Si+4HNO3=3SiO2↓+2H2O+4NO↑
硅被氧化后形成一层致密的二氧化硅薄膜,不溶于水和硝酸,但能溶于氢氟酸,这样腐蚀过程连续不断地进行。
有关的化学反应如下:
SiO2+6HF=H2[SiF6]+2H2O
2.NaOH腐蚀液
在氢氧化钠化学腐蚀时,采用10%~30%的氢氧化钠水溶液,温度为80~90℃,将硅片浸入腐蚀液中,腐蚀的化学方程式为
Si+H2O+2NaOH=Na2SiO3+2H2↑
对于太阳电池所用的硅片化学腐蚀,从成本控制,环境保护和操作方便等因素出发,一般用氢氧化钠腐蚀液腐蚀深度要超过硅片机械损伤层的厚度,约为20~30um。
电池制造工艺硅片的化学腐蚀
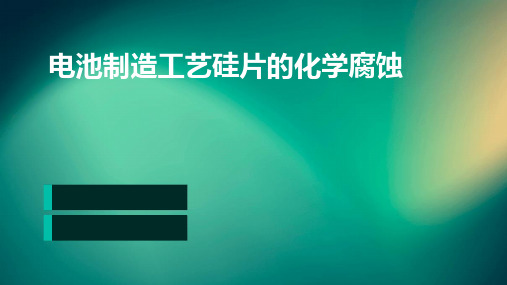
硅片腐蚀的影响因素
腐蚀剂种类
不同的腐蚀剂对硅片的腐蚀速率 和程度不同。例如,氢氟酸对硅 片的腐蚀速率较快,而硝酸对硅
片的腐蚀速率较慢。
温度
温度是影响化学腐蚀速率的重要因 素。在一定范围内,温度越高,化 学腐蚀速率越快。
电极对硅片的影响
电极材料
电极材料与硅片的兼容性对硅片的腐 蚀有重要影响。不同电极材料与硅片 的反应程度不同,可能导致硅片表面 质量下降。
电极结构
电极的结构设计也会影响硅片的腐蚀 。电极的粗糙度、孔隙率等因素都可 能影响电解液的流动和分布,从而影 响硅片的腐蚀。
温度和压力对硅片腐蚀的影响
温度
随着温度的升高,化学反应速率会增加,因此温度对硅片的腐蚀有显著影响。 高温条件下,硅片的腐蚀速率会加快。
压力
在一定的压力范围内,压力对硅片腐蚀的影响较小。但是,过高的压力可能导 致电解液对硅片的腐蚀加剧。
04 硅片化学腐蚀的预防和解 决方案
选择合适的材料
选择高纯度硅材料
高纯度硅材料可以减少杂质和缺陷,降低化学腐蚀的风险。
选用耐腐蚀材料
在制造电池时,可以选择耐腐蚀的电极材料,如镍、钴、锰等,以提高硅片的耐 腐蚀性。
深入研究硅片化学腐蚀的机理
开发新型防腐蚀材料和技术
进一步探究硅片化学腐蚀的机理和影响因 素,为预防和减缓腐蚀提供理论支持。
研究和开发新型的防腐蚀材料和技术,以 提高硅片的耐腐蚀性能和电池的稳定性。
提高生产过程的控制水平
加强安全评估和监控
加强生产过程的控制和管理,提高硅片的 质量和一致性,降低腐蚀风险。
硅片腐蚀率的因素

硅片腐蚀率的因素
硅片腐蚀率的主要因素包括以下几点:
1. 浓度:腐蚀液的浓度是影响腐蚀速率的重要因素。
通常情况下,浓度越高,腐蚀速率越快。
2. 温度:温度是影响腐蚀速率的重要因素之一。
一般来说,温度越高,腐蚀速率越快。
3. 接触时间:腐蚀物质与硅片接触的时间也会对腐蚀速率产生影响。
接触时间越长,腐蚀速率越快。
4. 溶液pH值:溶液的pH值也会对腐蚀速率产生影响。
pH值过高或过低都会加速硅片的腐蚀。
5. 氧气浓度:氧气的浓度也会对硅片的腐蚀速率产生影响。
氧气浓度越高,腐蚀速率越快。
6. 杂质含量:腐蚀液中杂质的含量会直接影响腐蚀速率。
杂质含量越高,腐蚀速率越快。
7. 溶液搅拌:溶液的搅拌方式和强度也会对硅片的腐蚀速率产生影响。
搅拌充
分能够加速腐蚀反应,提高腐蚀速率。
以上是硅片腐蚀率的一些主要影响因素,不同情况下可能还会有其他因素的影响。
硅片腐蚀碱洗作业指导书

4操作步骤:
4.1彩片用HF浸泡5小时左右,用自来水洗净;
4.2把洗过的彩片和片料放入配置30-35%的NAOH溶液中3分钟(当中要不停的搅拌)。迅速的放入纯水中反复冲洗(2分钟);
4.3把碱洗好的片料放入配置好的HCI槽内(浓度为18%)反复搅拌洗(5分钟)。用纯水反复冲洗(经过3个漂洗槽,每槽5分钟时间);
江苏淮安标准操作文件
编号:
硅片腐蚀(碱洗)作业指导书
版本:
受控状态:
批 准
审 核
编 制
日 期
日 期
日 期
1目的:
使已经有污染的硅片腐蚀、清洗干净能用于拉制太阳能级单晶的原材料;
2使用材料:
HF(49%)、NAOH(99%)、HCL(37%)、片料、烘箱。
3常用工具、设备:
碱洗蓝、漂洗槽、超声波发声器、纯水、烘箱、封装机等。
硅片酸腐蚀与碱腐蚀工艺比较
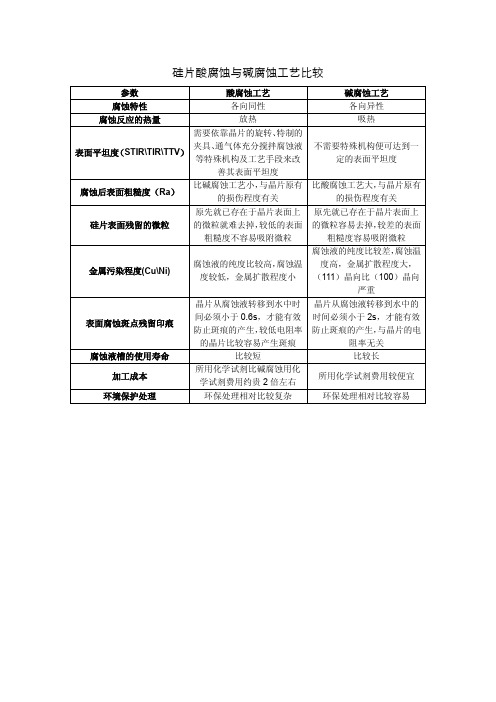
硅片表面残留的微粒
金属污染程度(Cu\Ni)
表面腐蚀斑点残留印痕
腐蚀液槽的使用寿命 加工成本 环境保护处理
需要依靠晶片的旋转、 特制的 夹具、 通气体充分搅拌腐蚀液 表面平坦度 (STIR\TIR\TTV) 等特殊机构及工艺手段来改 善其表面平坦度 腐蚀后表面粗糙度(Ra) 比碱腐蚀工艺小, 与晶片原有 的损伤程度有关 原先就已存在于晶片表面上 的微粒就难去掉, 较低的表面 粗糙度不容易吸附微粒 腐蚀液的纯度比较高, 腐蚀温 度较低,金属扩散程度小 晶片从腐蚀液转移到水中时 间必须小于 0.6s,才能有效 防止斑痕的产生, 较低电阻率 的晶片比较容易产生斑痕 比较短 所用化学试剂比碱腐蚀用化 学试剂费用约贵 2 倍左右 环保处理相对比较复杂
硅片酸腐蚀与碱腐蚀工艺比较
参数 腐蚀特性 腐蚀反应的热量 酸腐蚀工艺 各向同性 放热 碱腐蚀工艺 各向异性 吸热 不需要特殊机构便可达到一 定的表面平坦度 比酸腐蚀工艺大, 与晶片原有 的损伤程度有关 原先就已存在于晶片表面上 的微粒容易去掉, 较差的表面 粗糙度容易吸附微粒 腐蚀液的纯度比较差, 腐蚀温 度高,金属扩散程度大, (111)晶向比(100)晶向 严重 晶片从腐蚀液转移, 与晶片的电 阻率无关 比较长 所用化学试剂费用较便宜 环保处理相对比较容易
硅片酸腐蚀与碱腐蚀工艺比较参数酸腐蚀工艺碱腐蚀工艺腐蚀特性腐蚀反应的热量各向同性各向异性放热吸热表面平坦度stirtirttv需要依靠晶片的旋转特制的夹具通气体充分搅拌腐蚀液等特殊机构及工艺手段来改善其表面平坦度不需要特殊机构便可达到一定的表面平坦度腐蚀后表面粗糙度ra比碱腐蚀工艺小与晶片原有的损伤程度有关比酸腐蚀工艺大与晶片原有的损伤程度有关硅片表面残留的微粒原先就已存在于晶片表面上的微粒就难去掉较低的表面粗糙度不容易吸附微粒原先就已存在于晶片表面上的微粒容易去掉较差的表面粗糙度容易吸附微粒金属污染程度cuni腐蚀液的纯度比较高腐蚀温度较低金属扩散程度小腐蚀液的纯度比较差腐蚀温度高金属扩散程度大111晶向比100晶向严重表面腐蚀斑点残留印痕晶片从腐蚀液转移到水中时间必须小于06s才能有效防止斑痕的产生较低电阻率的晶片比较容易产生斑痕晶片从腐蚀液转移到水中的时间必须小于2s才能有效防止斑痕的产生与晶片的电阻率无关腐蚀液槽的使用寿命比较短比较长加工成本所用化学试剂比碱腐蚀用化学试剂费用约贵2倍左右所用化学试剂费用较便宜环境保护处理环保处理相对比较复杂环保处理相对比较容易
硅片酸腐蚀与碱腐蚀工艺比较
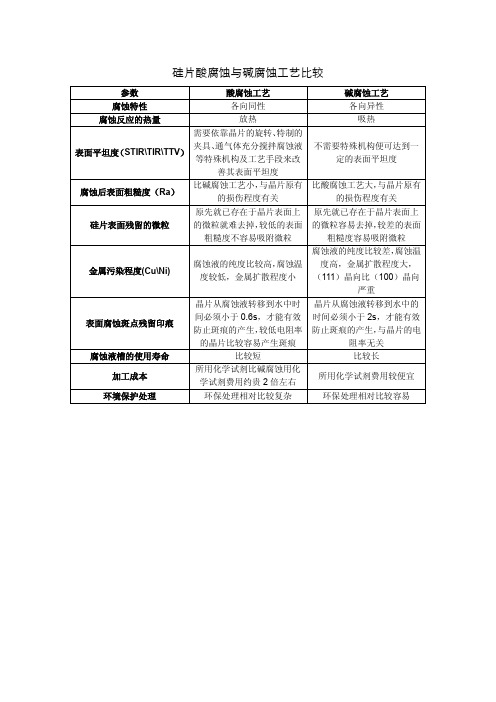
需要依靠晶片的旋转、 特制的 夹具、 通气体充分搅拌腐蚀液 表面平坦度 (STIR\TIR\TTV) 等特殊机构及工艺手段来改 善其表面平坦度 腐蚀后表面粗糙度(Ra) 比碱腐蚀工艺小, 与晶片原有 的损伤程度有关 原先就已存在于晶片表面上 的微粒就难去掉, 较低的表面 粗糙度不容易吸附微粒 腐蚀液的纯度比较高, 腐蚀温 度较低,金属扩散程度小 晶片从腐蚀液转移到水中时 间必须小于 0.6s,才能有效 防止斑痕的产生, 较低电阻率 的晶片比较容易产生斑痕 比较短 所用化学试剂比碱腐蚀用化 学试剂费用约贵 2 倍左右 环保处理相对比较复杂
硅片表面残留的微粒
金属污染程度(Cu\Ni)
表面腐蚀斑点残留印痕
腐蚀液槽的使用寿命 加工成本 环境保护处理
硅片酸腐蚀与碱腐量 酸腐蚀工艺 各向同性 放热 碱腐蚀工艺 各向异性 吸热 不需要特殊机构便可达到一 定的表面平坦度 比酸腐蚀工艺大, 与晶片原有 的损伤程度有关 原先就已存在于晶片表面上 的微粒容易去掉, 较差的表面 粗糙度容易吸附微粒 腐蚀液的纯度比较差, 腐蚀温 度高,金属扩散程度大, (111)晶向比(100)晶向 严重 晶片从腐蚀液转移到水中的 时间必须小于 2s,才能有效 防止斑痕的产生, 与晶片的电 阻率无关 比较长 所用化学试剂费用较便宜 环保处理相对比较容易
koh腐蚀硅角度

koh腐蚀硅角度本文将详细介绍硅片使用KOH腐蚀溶液的腐蚀过程及其相关因素,如腐蚀硅角度和最佳蚀刻时间等。
我们还将提供一些实践经验,以帮助读者在实际操作中更好地控制腐蚀过程,以达到最佳的蚀刻效果。
一、硅片腐蚀原理硅片在KOH溶液中的腐蚀是一种化学腐蚀过程,主要依靠氢氟酸和KOH的化学反应来实现。
硅片中的硅与氢氟酸反应生成四氟化硅和硅氢键,这个反应是可逆的。
当溶液中存在足够多的OH⁻离子时,生成的硅氢键会进一步与OH⁻离子反应,生成水和KHS,从而加速了硅片的腐蚀过程。
二、腐蚀硅角度在KOH溶液中,硅片表面的腐蚀程度会受到角度的影响。
当硅片被放置在溶液中时,不同角度的倾斜会导致溶液在硅片表面的停留时间和渗透深度不同,从而影响腐蚀程度。
一般来说,当硅片与溶液呈45°角时,腐蚀程度最为均匀。
这是因为在这个角度下,溶液在硅片表面上的渗透深度和停留时间都相对均衡,从而保证了蚀刻效果的均匀性。
三、最佳蚀刻时间除了腐蚀硅角度外,蚀刻时间也是影响蚀刻效果的重要因素。
过短的蚀刻时间会导致硅片表面未充分腐蚀,而过长的蚀刻时间则会导致硅片表面过度腐蚀,影响最终的形状和尺寸精度。
因此,需要根据硅片的材质、厚度以及应用需求来选择合适的蚀刻时间。
一般来说,通过多次试验和经验积累,可以找到最佳的蚀刻时间,从而获得最佳的蚀刻效果。
四、实践经验分享1. 清洗硅片:在开始腐蚀之前,需要确保硅片表面干净,以避免杂质影响腐蚀效果。
可以使用超声波清洗剂来清洗硅片。
2. 控制温度:KOH溶液的温度会影响腐蚀速度,因此需要确保溶液温度适中,以获得最佳的蚀刻效果。
3. 保持恒定的蚀刻速度:在蚀刻过程中,可以通过控制溶液中的OH⁻离子浓度来保持恒定的蚀刻速度,从而保证蚀刻效果的均匀性。
4. 及时取出硅片:当达到预设的蚀刻时间时,需要及时将硅片取出,以免过度腐蚀。
5. 避免过度搅拌:过度搅拌会加速硅片的腐蚀速度,导致过度侵蚀,因此需要避免。
硅的湿法腐蚀特点

硅的湿法腐蚀特点《硅的湿法腐蚀特点:微观世界里的奇妙“魔法”》硅,这个在现代科技世界里如同明星般的存在,它的湿法腐蚀有着很多独特又有趣的特点,就像是一场微观世界里的奇特秀。
首先呢,硅的湿法腐蚀有着高度的选择性。
这就好比是一个超级挑剔的美食家,腐蚀液只会对特定的硅区域“下手”,而对其他的部分则视而不见。
比如说在集成电路制造中,我们想要加工出极其复杂的电路图案,这种选择性就像是一个精确无比的雕刻刀,能够准确地去除不需要的硅材料,留下那些组成精密电路的部分。
这一特点就像是在微观的硅世界里展开了一场别具特色的寻宝游戏,腐蚀液熟门熟路地找到该腐蚀的地方,神奇得很!再者,湿法腐蚀的速度有时候很像一个调皮捣蛋的小精灵,难以捉摸。
它受到很多因素影响,像温度啊、腐蚀液的浓度呢,就好像腐蚀液的工作心情取决于这些条件一样。
在温度低的时候,腐蚀液可能就像个懒洋洋的小虫子,慢慢悠悠地腐蚀着硅;而当温度升高,腐蚀液就像打了鸡血似的,速度一下子就快了起来。
这种速度的多变让工程师们又爱又恨,爱的是可以通过调整参数来控制腐蚀进程,恨的是稍微不注意它就跑偏了。
曾经我就听闻一个工程师调侃说:“这湿法腐蚀速度啊,就跟女朋友的脾气似的,变幻无常,得小心伺候着。
”还有啊,湿法腐蚀是个湿式的过程,这意味着在硅片表面总会有液体的流动和交换。
这就好像是在给硅片洗一场独特的“化学浴”。
但这澡洗得可不容易,因为液体流动如果不均匀,就像搓澡的时候用力不均,硅片的腐蚀效果也就不一样了。
有时候硅片的一头腐蚀得刚刚好,另一头却像遭遇了过度揉捏的面团,过度腐蚀了。
这就要求在整个腐蚀过程中必须精心维护那个“浴室”的环境,让腐蚀液乖乖听话,均匀地发挥它的作用。
总的来说,硅的湿法腐蚀充满了魅力和挑战。
它就像是一个微观魔法,虽然有着各种各样让人头疼的小脾气,但一旦掌握了它的规律和特点,就能在硅的世界里创造出无数的奇迹,从小小的电子芯片到大型的光伏板,都有着湿法腐蚀的功劳,这个微观世界里的魔法可千万别小瞧它。
两种基本的刻蚀工艺:干法刻蚀和湿法腐蚀

两种基本的刻蚀工艺:干法刻蚀和湿法腐蚀
在半导体制造中有两种基本的刻蚀工艺:干法刻蚀和湿法腐蚀。
干法刻蚀是把硅片表面曝露于气态中产生的等离子体,等离子体通过光刻胶中开出的窗口,与硅片发生物理或化学反应(或这两种反应),从而去掉曝露的表面材料。
干法刻蚀是亚微米尺寸下刻蚀器件的最重要方法。
而在湿法腐蚀中,液体化学试剂(如酸、碱和溶剂等)以化学方式去除硅片表面的材料。
湿法腐蚀一般只是用在尺寸较大的情况下(大于3微米)。
湿法腐蚀仍然用来腐蚀硅片上某些层或用来去除干法刻蚀后的残留物。
干法刻蚀也可以根据被刻蚀的材料类型来分类。
按材料来分,刻蚀主要分成三种:金属刻蚀、介质刻蚀、和硅刻蚀。
介质刻蚀是用于介质材料的刻蚀,如二氧化硅。
接触孔和通孔结构的制作需要刻蚀介质,从而在ILD中刻蚀出窗口,而具有高深宽比(窗口的深与宽的比值)的窗口刻蚀具有一定的挑战性。
硅刻蚀(包括多晶硅)应用于需要去除硅的场合,如刻蚀多晶硅晶体管栅和硅槽电容。
金属刻蚀主要是在金属层上去掉铝合金复合层,制作出互连线。
刻蚀也可以分成有图形刻蚀和无图形刻蚀。
有图形刻蚀采用掩蔽层(有图形的光刻胶)来定义要刻蚀掉的表面材料区域,只有硅片上被选择的这一部分在刻蚀过程中刻掉。
有图形刻蚀可用来在硅片上制作多种不同的特征图形,。
硅片的湿法刻蚀的各向异性加工出V形槽条纹
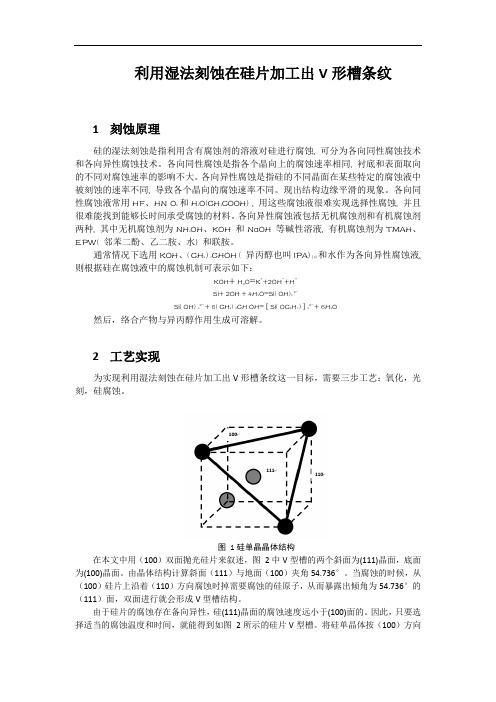
利用湿法刻蚀在硅片加工出V形槽条纹1刻蚀原理硅的湿法刻蚀是指利用含有腐蚀剂的溶液对硅进行腐蚀, 可分为各向同性腐蚀技术和各向异性腐蚀技术。
各向同性腐蚀是指各个晶向上的腐蚀速率相同, 衬底和表面取向的不同对腐蚀速率的影响不大。
各向异性腐蚀是指硅的不同晶面在某些特定的腐蚀液中被刻蚀的速率不同, 导致各个晶向的腐蚀速率不同。
现出结构边缘平滑的现象。
各向同性腐蚀液常用HF、HN O3 和H2O(CH3COOH) , 用这些腐蚀液很难实现选择性腐蚀, 并且很难能找到能够长时间承受腐蚀的材料。
各向异性腐蚀液包括无机腐蚀剂和有机腐蚀剂两种, 其中无机腐蚀剂为NH4OH、KOH 和NaOH 等碱性溶液, 有机腐蚀剂为TMAH、EPW( 邻苯二酚、乙二胺、水) 和联胺。
通常情况下选用KOH、( CH3 ) 2CHOH ( 异丙醇也叫IPA) [ 8] 和水作为各向异性腐蚀液, 则根据硅在腐蚀液中的腐蚀机制可表示如下:KOH+ H3O=K++2OH-+H+Si+ 2OH- + 4H2O=Si( OH)6 2-Si( OH) 62-+ 6( CH3) 2CH OH= [ Si( OC3H7 ) ] 62-+ 6H2O然后,络合产物与异丙醇作用生成可溶解。
2工艺实现为实现利用湿法刻蚀在硅片加工出V形槽条纹这一目标,需要三步工艺:氧化,光刻,硅腐蚀。
图1硅单晶晶体结构在本文中用(100)双面抛光硅片来叙述,图2中V型槽的两个斜面为(111)晶面,底面为(100)晶面。
由晶体结构计算斜面(111)与地面(100)夹角54.736°。
当腐蚀的时候,从(100)硅片上沿着(110)方向腐蚀时掉需要腐蚀的硅原子,从而暴露出倾角为54.736°的(111)面,双面进行就会形成V型槽结构。
由于硅片的腐蚀存在备向异性,硅(111)晶面的腐蚀速度远小于(100)面的。
因此,只要选择适当的腐蚀温度和时间,就能得到如图2所示的硅片V型槽。
硅片腐蚀技巧
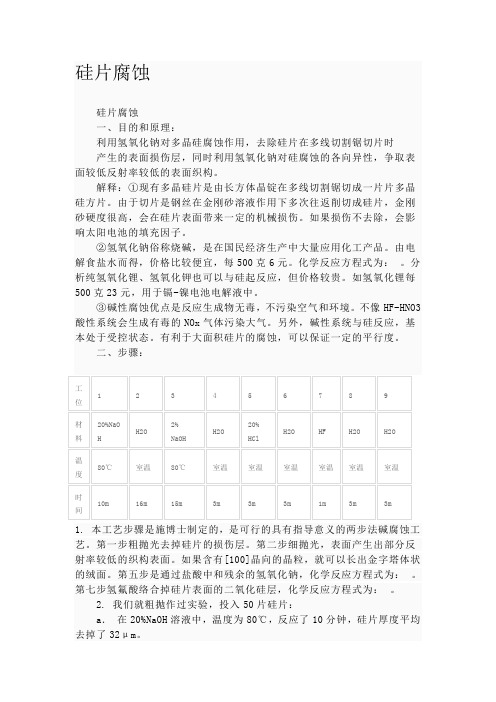
b.在15%NaOH溶液中,温度为80℃,反应了10分钟,硅片厚度平均去掉了25μm(此数据来源于小片实验)。
硅片粗抛是放热反应且反应激烈,反应速度与温度上升有点正反馈的态势:温度高,浓度高反应就会更激烈。
新硅片由于表面粗糙,表面积大一些反应也会激烈一些。
c.由于每次投片量较大,125×125可投300片,103×103可投400片,因而反应会很激烈,通过积累可以求出在受控条件下最佳浓度和时间。
d.按照施博士的意见硅片去掉20~25μm的厚度,硅片损伤层也就去除干净了,这也可以作为检验标准。
e.本反应以125×125的硅片计,每一片每次反应去掉25μm的厚度为准,每片将消耗0.9克硅,也将消耗2.6克氢氧化钠,300片硅片将消耗780克氢氧化钠,加上溶液加热蒸气带走一部分氢氧化钠,先加上1000克氢氧化钠为宜。
f.同理,如e那样每次生成832克硅酸钠,反应槽内的溶剂以170千克计,一旦溶液出现明显白色絮状硅酸钠,就应更换氢氧化钠溶液。
g.工序3中利用氢氧化钠对硅腐蚀的各向异性,用2%氢氧化钠溶液在多晶硅表面产生反射率较低织构表面,在[100]晶向的晶粒表面上会腐蚀出金字塔体的绒面来。
多晶硅总会存在着[100]晶向的晶粒,只是多少而已。
h.溶液配比方法是采取重量百分比法,如20%氢氧化钠溶液是1000ml 纯水中加200克氢氧化钠。
三、注意事项:1.在工序1和3中氢氧化钠溶液与硅片反应时会有碱蒸气产生,故设备运行时请关闭有机玻璃门。
2.盐酸是挥发性强酸,不不要去闻其味道。
3.氢氟酸会腐蚀玻璃,故不与玻璃器械接触,也不要去闻氢氟酸的味道。
4.如果酸或碱不小心溅入眼内或溅到脸上,请立即打开洗脸洗眼池上盖冲洗。
【半导体抛光】硅片腐蚀和抛光工艺的化学原理
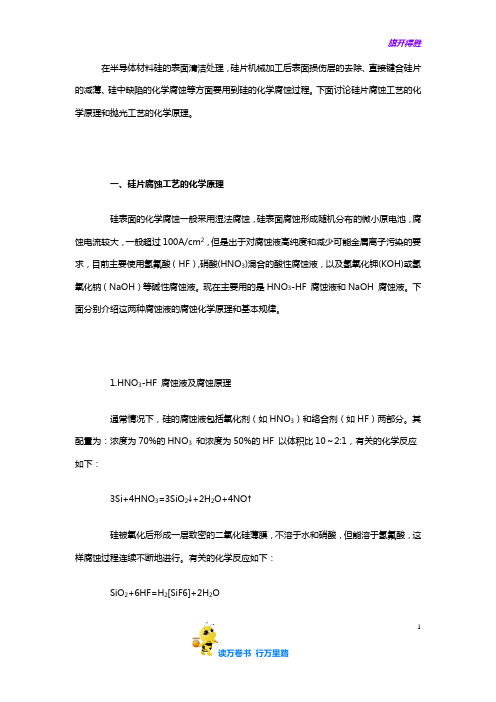
在半导体材料硅的表面清洁处理,硅片机械加工后表面损伤层的去除、直接键合硅片的减薄、硅中缺陷的化学腐蚀等方面要用到硅的化学腐蚀过程。
下面讨论硅片腐蚀工艺的化学原理和抛光工艺的化学原理。
一、硅片腐蚀工艺的化学原理硅表面的化学腐蚀一般采用湿法腐蚀,硅表面腐蚀形成随机分布的微小原电池,腐蚀电流较大,一般超过100A/cm2,但是出于对腐蚀液高纯度和减少可能金属离子污染的要求,目前主要使用氢氟酸(HF),硝酸(HNO3)混合的酸性腐蚀液,以及氢氧化钾(KOH)或氢氧化钠(NaOH)等碱性腐蚀液。
现在主要用的是HNO3-HF 腐蚀液和NaOH 腐蚀液。
下面分别介绍这两种腐蚀液的腐蚀化学原理和基本规律。
1.HNO3-HF 腐蚀液及腐蚀原理通常情况下,硅的腐蚀液包括氧化剂(如HNO3)和络合剂(如HF)两部分。
其配置为:浓度为70%的HNO3和浓度为50%的HF 以体积比10~2:1,有关的化学反应如下:3Si+4HNO3=3SiO2↓+2H2O+4NO↑硅被氧化后形成一层致密的二氧化硅薄膜,不溶于水和硝酸,但能溶于氢氟酸,这样腐蚀过程连续不断地进行。
有关的化学反应如下:SiO2+6HF=H2[SiF6]+2H2O12.NaOH 腐蚀液在氢氧化钠化学腐蚀时,采用10%~30%的氢氧化钠水溶液,温度为80~90℃,将硅片浸入腐蚀液中,腐蚀的化学方程式为Si+H2O+2 NaOH =Na2SiO3+2H2↑对于太阳电池所用的硅片化学腐蚀,从成本控制,环境保护和操作方便等因素出发,一般用氢氧化钠腐蚀液腐蚀深度要超过硅片机械损伤层的厚度,约为20~30um。
二、抛光工艺的化学原理抛光分为两种:机械抛光和化学抛光,机械抛光速度慢,成本高,而且容易产生有晶体缺陷的表面。
现在一般采用化学-机械抛光工艺,例如铜离子抛光、铬离子抛光和二氧化硅-氢氧化钠抛光等。
1. 铜离子抛光铜离子抛光液由氯化铜、氟化铵和水,一般以质量比60:26:1000 组成,调节PH=5.8 左右,或者以质量比80:102.8:1000,其反应原理如下:Si+2CuCl2+6NH4F=(NH4)2[SiF6]+4NH4Cl+2Cu铜离子抛光一般在酸性(pH 为5~6)条件下进行,当pH﹥7 时,反应终止,这是因为pH=7 时铜离子与氨分子生成了稳定的络合物-铜氨络离子,这时铜离子大大减2少,抛光作用停止了。
湿法腐蚀硅制作PDMS微流控芯片

湿法腐蚀硅制作PDMS微流控芯片PDMS(聚二甲基硅氧烷)是一种常用的微流控芯片材料,具有优良的化学稳定性、生物相容性和机械特性,因此广泛应用于生物医学、化学分析等领域的微流控芯片制作中。
在制作PDMS微流控芯片时,通常使用湿法腐蚀硅(Wet Etching)的方法来制作芯片的模具。
湿法腐蚀是一种通过在化学溶液中将硅表面暴露于特定的腐蚀剂中,以产生所需的芯片结构的方法。
在PDMS微流控芯片制作中,通常使用的腐蚀剂是一种含有氢氟酸(HF)的溶液。
制作PDMS微流控芯片的过程主要可以分为以下几个步骤:1.制备硅片:首先从硅片(通常是p型硅)中切割出所需的芯片尺寸。
然后进行清洗和去背面处理,以去除多余的杂质和薄化芯片厚度。
2.制备光刻胶并涂布:将光刻胶溶液倒在硅片表面,利用旋涂技术将光刻胶均匀涂布在整个硅片上。
然后使用烘箱将光刻胶加热固化。
3.光刻图案制作:将设计好的芯片结构图案通过投影机照射在光刻胶上,光照后的光刻胶在特定的显影剂中进行显影,从而形成所需的图案。
4.硅片腐蚀:将显影后的光刻胶作为腐蚀保护层,将硅片浸泡在HF溶液中,将光刻胶未保护的部分暴露在腐蚀剂中。
在一定的时间和温度下,HF溶液将会腐蚀硅片,形成PDMS微流控芯片的通道结构。
腐蚀时间的长短可以控制通道的深度和宽度。
5.光刻胶去除和清洗:将腐蚀后的芯片用显影液将未腐蚀的光刻胶去除。
然后进行洗涤和清洁处理,以去除腐蚀剂和杂质。
6.PDMS模具制作:将PDMS与硅片接触的一侧涂覆相应的硅橡胶,形成PDMS模具。
在特定的条件下,PDMS会与硅片上的微流控通道结构黏附在一起。
7.PDMS微流控芯片制作:将制作好的PDMS模具与另一块PDMS片子接触,通过加热与压力使两者黏合固化。
然后将固化好的PDMS芯片从硅片上剥离下来,即可得到完整的PDMS微流控芯片。
最后,需要注意的是,在PDMS微流控芯片制作的过程中需要控制好腐蚀时间和温度,以及严格的操作和安全措施,以避免对人体和环境造成伤害。
腐蚀工艺——精选推荐

化学腐蚀一、实验目的1.了解化学腐蚀在半导体器件制造过程中的重要作用。
2.掌握不同材料的化学腐蚀原理。
3.掌握各类腐蚀液的配制方法。
4.掌握硅,二氧化硅,铝等材料的腐蚀方法。
二、实验原理1.硅的腐蚀硅的腐蚀目前广泛采用浓硝酸和氢氟酸的混合腐蚀液。
硝酸和氢氟酸的体积比一般为10:1到2:1。
氧化剂硝酸的作用是使单质硅氧化为二氧化硅。
其反应如下:3Si + 4HNO3 === 3SiO2 + 2H2O + 4NO↑但是由于二氧化硅是难溶的物质,它既不溶于水,也不溶于硝酸。
同时,由于硅表面被硝酸氧化,表面形成一层非常紧密的二氧化硅薄膜,这个氧化膜对硅起保护作用,能阻碍氧化剂硝酸对硅进一步腐蚀,所以硝酸也不能有效地腐蚀硅,而只能在硅表面形成一层很薄地二氧化硅薄膜。
但是,如果腐蚀液不是单纯的氧化剂硝酸,而是氧化剂硝酸和络合剂氢氟酸的混合液,那么,由于二氧化硅能与氢氟酸生成可溶于水的络合物六氟硅酸,而使硅片表面的二氧化硅膜溶解。
其反应如下:SiO2 + 6HF === H2[SiF6] + 2H2O在硝酸和氢氟酸混合腐蚀液中,由于有氢氟酸的存在,使硅表面的二氧化硅薄膜被破坏了,所以硅能不断地被硝酸氧化,同时,生成的二氧化硅又能不断地被氢氟酸溶解,因此硝酸和氢氟酸混合腐蚀液对硅能进行有效地腐蚀。
在常用的硅酸腐蚀液中,还有CP4腐蚀液,其配方如下:硝酸:氢氟酸:冰醋酸:溴 === 5 :3 :3 :0.06它除了包含氧化剂硝酸和络合剂氢氟酸外,还含有缓和剂和附加剂。
常用的缓和剂有醋酸或水,缓和剂的作用是控制反映速度,使硅表面光亮。
常用的附加剂是在腐蚀液中加入一种氧化剂(如溴,碘等)或还原剂(如碘化钾等)或加一些金属盐类(如硝酸银,硝酸汞,硫酸铜等),CP4腐蚀液中加入的附加剂溴就是一种强氧化剂,它能大大加快腐蚀反应的速度。
此外,由于硅具有能与碱作用的性能,所以热浓碱溶液(如10%—30%氢氧化钠或氢氧化钾溶液)也是硅材料的一种强的腐蚀液。
- 1、下载文档前请自行甄别文档内容的完整性,平台不提供额外的编辑、内容补充、找答案等附加服务。
- 2、"仅部分预览"的文档,不可在线预览部分如存在完整性等问题,可反馈申请退款(可完整预览的文档不适用该条件!)。
- 3、如文档侵犯您的权益,请联系客服反馈,我们会尽快为您处理(人工客服工作时间:9:00-18:30)。
实验三 硅片的腐蚀
一、实验目的
1.掌握Si 单晶片的位错侵蚀方法和位错密度的计算方法
2.了解腐蚀Si 单晶位错原理,正确使用金相显微镜,
二、实验原理
位错是晶体的线缺陷,它标志着晶体结构的完整程度,它对半导体材料的电学性能有很大影响,通常制造器件要求位错密度要低,或是无位错晶体,而且还要求晶体位错分布均匀,位错高低直接影响晶体做器件的质量。
测量单位体积内位错的方法有X 射线法,电子显微镜法和铜缀饰红外投射法等,但这些方法设备昂贵,工艺复杂,所以生产上很少采用。
目前生产上广泛使用的是腐蚀金相法(腐蚀坑法)。
它是将样品进行化学腐蚀,然后用金相显微镜测定样品表面上出现的腐蚀坑数目。
因为每一腐蚀坑代表与被测表面相交的一条位错线的露头处,所以位错密度是指单位被测表面积上相交的位错线(坑)的个数。
N D = S
n (1) N D 为位错密度,单位个数/厘米2 ,n 是位错线的(坑)的个数,S 是面积。
为什么在晶体表面位错露头的地方,经化学腐蚀后会出现腐蚀坑呢?这是因为在位错线的地方,原子排列不规则,存在差应力场,使该处的原子具有较高的能量和较大的应力,当我们用某种化学腐蚀剂腐蚀晶体时,有位错处的腐蚀速度大于完整晶体的腐蚀速度,这样经过一定时间腐蚀后,就会在位错线和样品表面的相交处显示出凹的蚀坑,由于晶体具有各向异性,因此在不同的结晶面腐蚀速度不同,在不同晶面上其蚀坑形状亦不同。
如图1所示,在(111)面上经腐蚀出现正三角形腐蚀坑,在(100)面上出现正四边形腐蚀坑,在(110)面上为矩形腐蚀坑。
图2.1-1位错蚀坑的形状
用金相显微镜观测位错密度是一种近似的方法,因为位错在晶体中的分布是不规则的,有些位错并不一定在被观测的面形成蚀坑,有些位错非常临近,几个临近的位错只形成一个蚀坑,所以蚀坑与位错并不是一一对应的,它只能近似地反应出晶体中的位错密度大小。
三、实验仪器和化学药品
金相显微镜、天平、塑料烧杯、镊子、量桶、硝酸、氢氟酸,自配铬酸溶液、乙醇等。
四、实验步骤
1.位错腐蚀前准备工作
在显示位错之前,应将晶体表面用金刚砂研磨,研磨后的表面应进行化学抛光,以便除去由机械研磨形成的表面破坏层对位错显示的严重影响,Si用单晶用HF:HNO3=1:3(体积比),腐蚀时间2-3mins
2.腐蚀位错
称取5gCrO3溶于10ml水中,制成铬酸溶液,按HF:铬酸溶液=1:1的配比,配制成腐蚀液,HF和铬酸各取10ml倒入塑料烧杯中,然后将样品放入,在温室腐蚀10-30mins(10mins可观察层错,20mins可观察位错)腐蚀过程中要求样品不能露出水面,腐蚀完用大量水冲至中性,用乙醇脱水,烘干待用,在化学腐蚀操作时,要牢记操作要点,即要两准一快,配比要准,时间要准,脱酸要快。
3.错密度观测与计算
(1) 视场面积测定
将每格为0.0 1mm 精度的标准计量板放在显微镜的载物台上,从显微镜中测出视场面积的直径D ,然根据公式(2)计算出视场面积S
S = πr 2 =4
1πD 2 (2) (2) 位错密度观测
将样品放在显微镜的载舞台上,观测5个视场,然后对每个视场所观测到的位错数目取其平均值。
(3) 计标位错密度
位错密度=视场面积
视场个数各视场内位错的总数⨯
N D =S
n n n n n ⨯++++554321 (3) 五、实验报告要求
1.实验目的;
2.简述位错腐蚀原理及位错显示、观察的过程;
3.按所观察到的位借蚀坑形貌、分布绘出示意图,判断观察面是何晶面,确定位错密度。
4.总结实验中存在的问题。