铸件缺陷产生原因及应对措施
铸造缺陷原因及其解决方法

铸造缺陷原因及其解决方法
铸造缺陷是铸造行业经常出现的一类问题,对铸件的功能和使用寿命有负面影响。
在近年来,随着材料科学领域的进步,铸铁、钢、金属等的性能越来越高,越来越多的新型铸造形式和新型工艺方法被开发出来,但是铸造缺陷依然存在,需要及时解决。
铸造缺陷的原因很复杂,主要有以下几类:一是铸件的铸造工艺参数不当,包括铸件尺寸参数不合理,成型材料未能满足要求,流体特性、温度、压力等参数不足;二是模具设计过程中出现问题,包括模具结构设计不当、表面材质不满足要求等;三是原料误差,原料中病害比例高,导致铸件组织结构不稳定,抗拉强度低。
解决铸造缺陷的方法:一是针对工艺参数不当,应采取有效的治理措施,进行工艺参数的优化及控制,在模具设计中加强细部处理或使用更高性能的材料;二是对原材料误差,应采取措施分离优良料和劣料,保证原料质量,增加试验对原料力学和化学性质检测,改善铸件质量;三是在成型前,应做出正确的实验,要求较高,确保模具尺寸精度,应用胶粉注射成型增加工艺性能。
通过科学的铸造工艺参数设计,优质的原材料配置,模具精细设计,合理的实验控制,减少不合格品,增加铸件质量,都可以有效地解决铸造缺陷的问题。
只有把解决这些铸造缺陷的解决方案扎实,从技术、过程、品质等角度进行多方面开展,才能保证铸件的功能以及使用寿命,有助于企业提升铸件的整体质量水平,建立良好的企业形象。
铸造工艺流程中的铸件缺陷分析与改进策略

铸造工艺流程中的铸件缺陷分析与改进策略铸造工艺是一种重要的金属加工方法,用于制造各种形状的金属件。
然而,在铸造过程中,铸件缺陷是一个常见的问题,它会影响到铸件的质量和性能。
因此,对于铸造工艺流程中的铸件缺陷进行深入分析,并提出改进策略,对于提高铸件质量和工艺效率具有重要意义。
一、铸件缺陷的分类与原因分析在铸造工艺中,铸件缺陷可以分为表面缺陷和内部缺陷两类。
常见的表面缺陷包括气孔、砂眼、砂洞等;内部缺陷主要有夹杂物、孔洞、收缩系数不均匀等。
1.1 气孔气孔是铸造工艺中最常见的表面缺陷之一。
其形成的原因通常有两个方面,一是液态金属中溶解气体含量过高,二是在金属凝固过程中,气体生成而未能有效排除。
造成气孔的常见因素包括砂芯质量不佳、浇注温度过高、浇注速度过快等。
1.2 砂眼和砂洞砂眼是指铸件表面局部凹陷的缺陷,而砂洞是指铸件内部或边缘凹陷的缺陷。
主要原因包括模具缺陷、浇注系统设计不合理、浇注金属温度过低等。
1.3 夹杂物夹杂物是指铸件中存在的杂质,如炉渣、油污等。
其主要原因包括铁水净化不彻底、砂芯质量不佳等。
1.4 孔洞孔洞是指铸件内部存在的封闭空腔。
常见的孔洞形式包括气孔和收缩孔。
造成孔洞的原因主要有铁水中含气量高、铸型泥浆含水量高等。
1.5 收缩系数不均匀收缩系数不均匀是指铸件不同部位的收缩量不一致。
这可能会引起铸件的内部应力集中,从而导致开裂和变形。
收缩系数不均匀的原因包括铸造合金的特性、浇注温度的控制等。
二、改进策略为了减少铸件缺陷,提高铸件质量和工艺效率,以下是一些改进策略的具体措施:2.1 优化模具设计模具设计是影响铸件质量的关键因素之一。
通过优化模具结构、提高模具材料质量和表面光洁度,可以减少砂眼、砂洞等表面缺陷的产生。
2.2 控制浇注温度和速度浇注温度和速度对铸件质量有着直接的影响。
合理控制浇注温度和速度,可以降低气孔和夹杂物等缺陷的产生。
2.3 改进铸型材料和工艺选择合适的铸型材料,对铸件质量和工艺效率的提高至关重要。
2.压铸产品铸造缺陷产生原因及处理办法
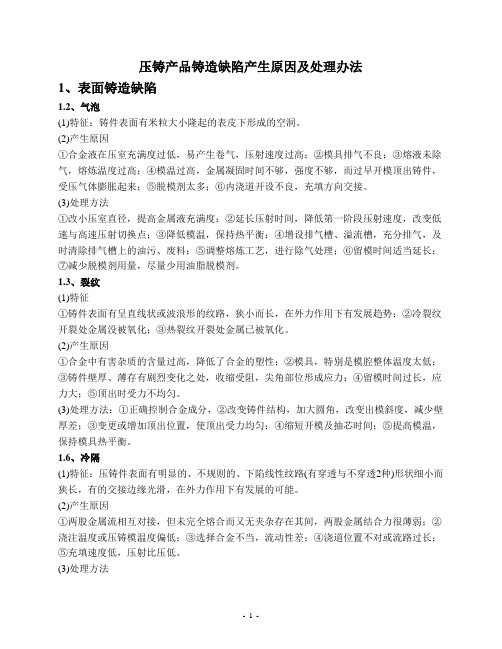
压铸产品铸造缺陷产生原因及处理办法1、表面铸造缺陷1.2、气泡(1)特征:铸件表面有米粒大小隆起的表皮下形成的空洞。
(2)产生原因①合金液在压室充满度过低,易产生卷气,压射速度过高;②模具排气不良;③熔液未除气,熔炼温度过高;④模温过高,金属凝固时间不够,强度不够,而过早开模顶出铸件,受压气体膨胀起来;⑤脱模剂太多;⑥内浇道开设不良,充填方向交接。
(3)处理方法①改小压室直径,提高金属液充满度;②延长压射时间,降低第一阶段压射速度,改变低速与高速压射切换点;③降低模温,保持热平衡;④增设排气槽、溢流槽,充分排气,及时清除排气槽上的油污、废料;⑤调整熔炼工艺,进行除气处理;⑥留模时间适当延长;⑦减少脱模剂用量,尽量少用油脂脱模剂。
1.3、裂纹(1)特征①铸件表面有呈直线状或波浪形的纹路,狭小而长,在外力作用下有发展趋势;②冷裂纹开裂处金属没被氧化;③热裂纹开裂处金属已被氧化。
(2)产生原因①合金中有害杂质的含量过高,降低了合金的塑性;②模具,特别是模腔整体温度太低;③铸件壁厚、薄存有剧烈变化之处,收缩受阻,尖角部位形成应力;④留模时间过长,应力大;⑤顶出时受力不均匀。
(3)处理方法:①正确控制合金成分,②改变铸件结构,加大圆角,改变出模斜度,减少壁厚差;③变更或增加顶出位置,使顶出受力均匀;④缩短开模及抽芯时间;⑤提高模温,保持模具热平衡。
1.6、冷隔(1)特征:压铸件表面有明显的、不规则的、下陷线性纹路(有穿透与不穿透2种)形状细小而狭长,有的交接边缘光滑,在外力作用下有发展的可能。
(2)产生原因①两股金属流相互对接,但未完全熔合而又无夹杂存在其间,两股金属结合力很薄弱;②浇注温度或压铸模温度偏低;③选择合金不当,流动性差;④浇道位置不对或流路过长;⑤充填速度低,压射比压低。
(3)处理方法①适当提高浇注温度和模具温度;②提高压射比压,缩短充填时间;③提高压射速度,同时加大内浇道截面积;④改善排气、填充条件;⑤正确选用合金,提高合金流动性。
铸件常见缺陷的产生原因及防止方法
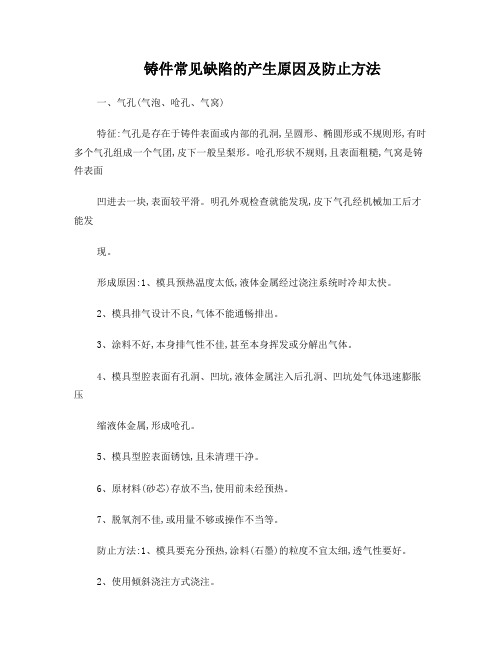
铸件常见缺陷的产生原因及防止方法一、气孔(气泡、呛孔、气窝)特征:气孔是存在于铸件表面或内部的孔洞,呈圆形、椭圆形或不规则形,有时多个气孔组成一个气团,皮下一般呈梨形。
呛孔形状不规则,且表面粗糙,气窝是铸件表面凹进去一块,表面较平滑。
明孔外观检查就能发现,皮下气孔经机械加工后才能发现。
形成原因:1、模具预热温度太低,液体金属经过浇注系统时冷却太快。
2、模具排气设计不良,气体不能通畅排出。
3、涂料不好,本身排气性不佳,甚至本身挥发或分解出气体。
4、模具型腔表面有孔洞、凹坑,液体金属注入后孔洞、凹坑处气体迅速膨胀压缩液体金属,形成呛孔。
5、模具型腔表面锈蚀,且未清理干净。
6、原材料(砂芯)存放不当,使用前未经预热。
7、脱氧剂不佳,或用量不够或操作不当等。
防止方法:1、模具要充分预热,涂料(石墨)的粒度不宜太细,透气性要好。
2、使用倾斜浇注方式浇注。
3、原材料应存放在通风干燥处,使用时要预热。
4、选择脱氧效果较好的脱氧剂(镁)。
5、浇注温度不宜过高。
二、缩孔(缩松)特征:缩孔是铸件表面或内部存在的一种表面粗糙的孔,轻微缩孔是许多分散的小缩孔,即缩松,缩孔或缩松处晶粒粗大。
常发生在铸件内浇道附近、冒口根部、厚大部位,壁的厚薄转接处及具有大平面的厚薄处。
形成原因:1、模具工作温度控制未达到定向凝固要求。
2、涂料选择不当,不同部位涂料层厚度控制不好。
3、铸件在模具中的位置设计不当。
4、浇冒口设计未能达到起充分补缩的作用。
5、浇注温度过低或过高。
防治方法:1、提高磨具温度。
2、调整涂料层厚度,涂料喷洒要均匀,涂料脱落而补涂时不可形成局部涂料堆积现象。
3、对模具进行局部加热或用绝热材料局部保温。
4、热节处镶铜块,对局部进行激冷。
5、模具上设计散热片,或通过水等加速局部地区冷却速度,或在模具外喷水,喷雾。
6、用可拆缷激冷块,轮流安放在型腔内,避免连续生产时激冷块本身冷却不充分。
7、模具冒口上设计加压装置。
8、浇注系统设计要准确,选择适宜的浇注温度。
铸件缺陷及解决方法
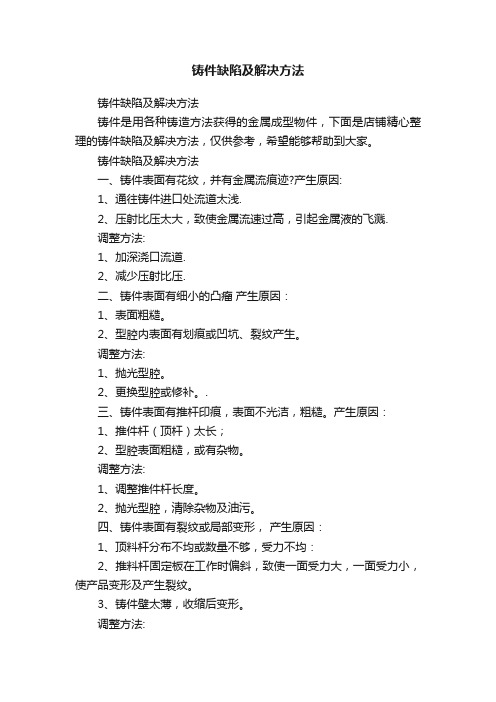
铸件缺陷及解决方法铸件缺陷及解决方法铸件是用各种铸造方法获得的金属成型物件,下面是店铺精心整理的铸件缺陷及解决方法,仅供参考,希望能够帮助到大家。
铸件缺陷及解决方法一、铸件表面有花纹,并有金属流痕迹?产生原因:1、通往铸件进口处流道太浅.2、压射比压太大,致使金属流速过高,引起金属液的飞溅.调整方法:1、加深浇口流道.2、减少压射比压.二、铸件表面有细小的凸瘤产生原因:1、表面粗糙。
2、型腔内表面有划痕或凹坑、裂纹产生。
调整方法:1、抛光型腔。
2、更换型腔或修补。
.三、铸件表面有推杆印痕,表面不光洁,粗糙。
产生原因:1、推件杆(顶杆)太长;2、型腔表面粗糙,或有杂物。
调整方法:1、调整推件杆长度。
2、抛光型腔,清除杂物及油污。
四、铸件表面有裂纹或局部变形,产生原因:1、顶料杆分布不均或数量不够,受力不均:2、推料杆固定板在工作时偏斜,致使一面受力大,一面受力小,使产品变形及产生裂纹。
3、铸件壁太薄,收缩后变形。
调整方法:1、增加顶料杆数量,调整其分布位置,使铸件顶出受力均衡。
2、调整及重新安装推杆固定板。
五、压铸件表面有气孔,产生原因:1、润滑剂太多。
2、排气孔被堵死,气孔排不出来。
调整方法:1、合理使用润滑剂。
2、增设及修复排气孔,使其排气通畅。
六、铸件表面有缩孔:产生原因:压铸件工艺性不合理,壁厚薄变化太大。
金属液温度太高。
调整方法:1、在壁厚的地方,增加工艺孔,使之薄厚均匀。
2、降低金属液温度。
七、铸件外轮廓不清晰,成不了形,局部欠料,产生原因:1、压铸机压力不够,压射比压太低。
2、进料口厚度太大;3、浇口位置不正确,使金属发生正面冲击。
调整方法:1、更换压铸比压大的压铸机;2、减小进料口流道厚度;3、改变浇口位置,防止对铸件正面冲击。
八、铸件部分未成形,型腔充不满,产生原因:1、压铸模温度太低;2、金属液温度低;3、压机压力太小,4、金属液不足,压射速度太高;5、空气排不出来。
调整方法:1、 2、提高压铸模,金属液温度;3、更换大压力压铸机。
常见铸造缺陷产生的原因及防止方法

常见铸造缺陷产生的原因及防止方法铸件缺陷种类繁多,产生缺陷的原因也十分复杂.它不仅与铸型工艺有关,而且还与铸造合金的性制、合金的熔炼、造型材料的性能等一系列因素有关.因此,分析铸件缺陷产生的原因时,要从具体情况出发,根据缺陷的特征、位置、采用的工艺和所用型砂等因素,进行综合分析,然后采取相应的技术措施,防止和消除缺陷.一、浇不到1、特征铸件局部有残缺、常出现在薄壁部位、离浇道最远部位或铸件上部.残缺的边角圆滑光亮不粘砂.2、产生原因1 浇注温度低、浇注速度太慢或断续浇注;2 横浇道、内浇道截面积小;3 铁水成分中碳、硅含量过低;4 型砂中水分、煤粉含量过多,发气量大,或含泥量太高,透气性不良;5 上砂型高度不够,铁水压力不足.3、防止方法1 提高浇注温度、加快浇注速度,防止断续浇注;2 加大横浇道和内浇道的截面积;3 调整炉后配料,适当提高碳、硅含量;4 铸型中加强排气,减少型砂中的煤粉,有机物加入量;5 增加上砂箱高度.二、未浇满1、特征铸件上部残缺,直浇道中铁水的水平面与铸件的铁水水平面相平,边部略呈圆形.2、产生原因1 浇包中铁水量不够;2 浇道狭小,浇注速度又过快,当铁水从浇口杯外溢时,操作者误认为铸型已经充满,停浇过早.3、防止方法1 正确估计浇包中的铁水量;2 对浇道狭小的铸型,适当放慢浇注速度,保证铸型充满.三、损伤1、特征铸件损伤断缺.2、产生原因1 铸件落砂过于剧烈,或在搬运过程中铸件受到冲撞而损坏;2 滚筒清理时,铸件装料不当,铸件的薄弱部分在翻滚时被碰断;3 冒口、冒口颈截面尺寸过大;冒口颈没有做出敲断面凹槽.或敲除浇冒口的方法不正确,使铸件本体损伤缺肉.3、防止方法1 铸件在落砂清理和搬运时,注意避免各种形式的过度冲撞、振击,避免不合理的丢放;2 滚筒清理时严格按工艺规程和要求进行操作;3 修改冒口和冒口颈尺寸,做出冒口颈敲断面,正确掌握打浇冒口的方向.四、粘砂和表面粗糙1、特征粘砂是一种铸件表面缺陷,表现为铸件表面粘附着难以清除的砂粒;如铸件经清除砂粒后出现凹凸不平的不光滑表面,称表面粗糙.2、产生原因1 砂粒太粗、砂型紧实度不够;2 型砂中水分太高,使型砂不易紧实;3 浇注速度太快、压力过大、温度过高;4 型砂中煤粉太少;5 模板烘温过高,导致表面型砂干枯;或模板烘温过低,型砂粘附在模板上.3、防止方法1 在透气性足够的情况下,使用较细原砂,并适当提高型砂紧实度;2 保证型砂中稳定的有效煤粉含量;3 严格控制砂水分;4 改进浇注系统,改进浇注操作、降低浇注温度;5 控制模板烘烤温度,一般与型砂温度相等或略高.五、砂眼1、特征在铸件内部或表面充塞有型砂的孔眼.2、产生原因1 型砂表面强度不够;2 模样上无圆角或拔模斜度小导致钩砂、铸型损坏后没修理或没修理好就合箱;3 砂型在浇注前放置时间过长,风干后表面强度降低;4 铸型在合箱时或搬运过程中损坏;5 合箱时型内浮砂未清除干净,合箱后浇口杯没盖好,碎砂掉进铸型.3、防止方法1 提高型砂中粘士含量、及时补加新砂,提高型砂表面强度;2 模样光洁度要高,并合理做出拔模斜度和铸造圆角.损坏的铸型要修好后再合箱;3 缩短浇注前砂型的放置时间;4 合箱或搬运铸型时要小心,避免损坏或掉入砂型腔砂粒;5 合箱前清除型内浮砂,并盖好浇口.六、披缝和胀砂1、特征披缝常出现在铸件分型面处,是垂直于铸件表面,且厚薄不均匀的薄片状金属突起物. 胀砂是铸件内、外表面局部胀大,形成不规则的瘤状金属突起物.2、产生原因1 紧实度不够或不匀;2 面砂强度不够、或型砂水分过高;3 液态金属压头过大、浇注速度太快.3、防止方法1 提高铸型紧实度、避免局部过松;2 调整混砂工艺、控制水分,提高型砂强度;3 降低液态金属的压头、降低浇注速度.七、抬箱1、特征铸件在分型面处有大面积的披缝,使铸型外形尺寸发生变化.抬箱过大,造成跑火——铁水自分型面外溢,严重时造成浇不足缺陷.2、产生原因1 砂箱未紧固、压铁质量不够或去除压铁过早;2 浇注过快,冲击力过大;3 模板翅曲.3、防止方法1 增加压铁重量,特铁水凝固后再去除压铁;2 降低浇包位置,降低浇注速度;3 修正模板.八、掉砂1、特征铸件表面上出现的块状金属突起物,其外形与掉落的砂块很相似.在铸件其它部位,则往往出现砂眼或残缺.2、产生原因1 模样上有深而小的凹槽,同于结构特征或拔模斜度小,起模时将砂型带坏或震裂;2 紧实度不匀,铸型局部强度不足;3 合箱、搬运铸型时,不小心使铸型局部砂块掉落.3、防止方法1 模样拔模斜度要合适、表面光洁;2 铸型紧实度高且均匀;3 合箱、搬运过程中,操作小心.九、错型错箱1、特征铸件的一部分与另一部分在分型面的接缝处错开,发生相对位移,使铸件外形与图纸不相符合.2、产生原因1 模样制作不良,上下模没有对准或模样变形;2 砂箱或模板定位不准确,或定位销松动;3 挤压造型机上零件磨损,例如正压板下衬板、反压板轴承的磨损等;4 浇注时用的套箱变形,搬运、围箱时不注意,使上下铸型发生位移.3、防止方法1 加强模板的检查和修理;定2 经常检查砂箱、模板的定位销及销孔、并合理地安装;3 检查挤压造型机的有关零件,及时调整,磨损大的要更换;4 定期对套箱整形.脱箱后的铸型在搬运时要小心.在面浇注的砂型,应该做一排砂型围一排.十、灰口和麻点1、特征铸件断口呈灰黑色或出现黑色小点,中心部位较多,边部较少,金相观察可见到片状石墨.2、产生原因1 铁水化学成分不合要求,碳、硅含量过高;2 炉前孕育的铋加入浇包内过早或过迟,或是铋量不足.3、防止方法1 正确选择化学成分,合理配料,使铁水中碳、硅量在规定范围内;2 增加铋的加入量并严格炉前孕育工艺.十一、裂纹热裂、冷裂1、特征铸件外部或内部有穿透或不穿透的裂纹.热裂时带有暗色或黑色的氧化表面断口外形曲折.冷裂是较干净的脆性裂纹,断口较平,具有金属光泽或轻微的氧化色泽.2、产生原因1 铁水中碳、硅含苞欲放量过低,含硫量过高;2 浇注温度过高;3 冒口颈过大、过短,造成局部过热严重,或重口太小,补缩不好;4 铸件在清理、运输过程中,受冲击过大.3、防止方法1 控制铁水化学成分在规定的范围内;2 降低浇注温度;3 合理设计冒口系统;4 铸件在清理、运输过程中避免过度冲击.十二、气孔1、特征气孔的孔壁光滑明亮,形状有圆形、梨形和针状,孔的尺寸有大有小,产生在铸件表面或内部.铸件内部的气孔在敲碎后或机械加工时才能被发现.2、产生原因1 小炉料潮湿、锈蚀严重或带有油污,使铁水含气量太多、氧化严重;2 出铁孔、出铁槽、炉衬、浇包衬未洪干;3 浇注温度较低,使气体来不及上浮和逸出;4 炉料中含铝量较高,易造成氢气孔;5 砂型透气性不好、型砂水分高、含煤粉或有机物较多,使浇注时产生大量气体且不易排出.3、防止方法1 炉料要妥善管理,表面要清洁;2 炉缸、前炉、出铁口、出铁槽、浇包必须烘干;3 提高浇注温度;4 不使用铝量过高的废钢;5 适当降低型砂的水分、控制煤粉加入量,扎通气孔等.十三、缩松、疏松1、特征分散、细小的缩孔,带有树枝关结晶的称缩松,比缩松更细小的称疏松.常出现在热世部位.2、产生原因1 铁水中碳、硅含量过低,收缩大;2 浇注速度太快、浇注温度过高,使得液态收缩大;3 浇注系统、冒口设计不当,无法实现顺序凝固;4 冒口太小,补缩不充分.3、防止方法1 控制铁水的化学成分在规定范围内;2 降低浇注速度和浇注温度;3 改进浇冒口系统,利用顺序凝固;4 加大冒口体积,保证充分补缩.十四、反白口1、特征铸件断口内部出现白口组织,边缘部分出现灰口.2、产生原因1 碳、硅含量较高的铁水,含氢量过高;2 炉料中带入的铬等白口形成元素过多;3 元素偏析严重;3、防止方法1 控制化学成分、碳、硅含量不宜过高;2 炉衬、包衬要烘干;型砂水分不宜过高;3 加强炉料管理,减少带入白口化元素.。
压铸件常见缺陷及解决办法手册 (完整版)
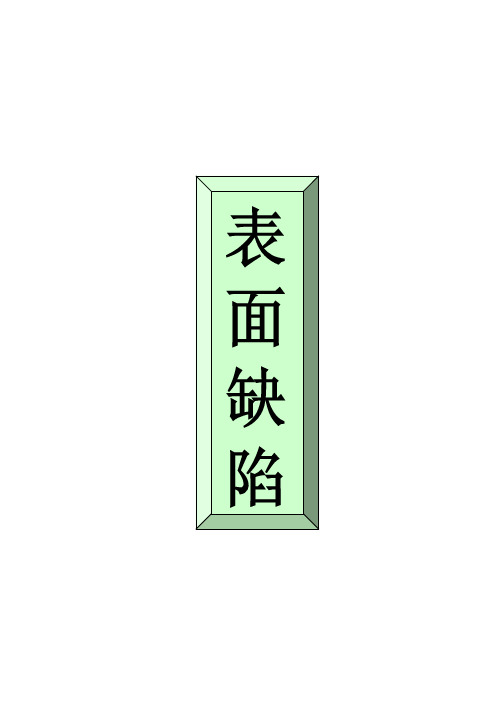
产生原因分析判断及解决办法1、金属液浇注温度低或模具温度低;2、合金成分不符合标准,流动性差;3、金属液分股填充,熔合不良;4、浇口不合理,流程太长;5、填充速度低或排气不良;6、压射比压偏低。
1、产品发黑,伴有流痕。
适当提高浇注温度和模具温度;2、改变合金成分,提高流动性;3、烫模件看铝液流向,金属液碰撞产生冷隔出现一般为涡旋状,伴有流痕。
改进浇注系统,改善内浇口的填充方向。
另外可在铸件边缘开设集渣包以改善填充条件;4、伴有远端压不实。
更改浇口位置和截面积,改善排溢条件,增大溢流量;5、产品发暗,经常伴有表面气泡。
提高压射速度,6、铸件整体压不实。
提高比压(尽量不采用)。
缺陷1 ---- 冷隔缺陷现象:温度较低的金属流互相对接但未熔合而出现的缝隙,呈不规则的线形,有穿透的和不穿透的两种,在外力的作用下有发展的趋势。
其他名称:冷接(对接)缺陷2 ---- 擦伤其他名称:拉伤、拉痕、粘模伤痕缺陷现象:顺着脱模方向,由于金属粘附,模具制造斜度太小而造成铸件表面的拉伤痕迹,严重时成为拉伤面甚至产生裂纹。
产生原因 分析判断及解决办法 1、型芯、型壁的铸造斜度太小或出现倒斜度; 2、型芯、型壁有压痕; 3、合金粘附模具;4、铸件顶出偏斜,或型芯轴线偏斜;5、型壁表面粗糙;6、涂料常喷涂不到;7、铝合金中含铁量低于0.6%; 8、合金浇注温度高或模具温度太高;9、浇注系统不正确, 直接冲击型壁或型芯 ; 10、填充速度太高;11、型腔表面未氮化。
1、产品一般拉出亮痕,不起毛。
修正模具,保证制造斜度; 2、产生拉毛甚至拉裂。
打光压痕、更换型芯或焊补型壁; 3、拉伤起毛。
抛光模具; 4、单边大面积拉伤,顶出时有异声修正模具结构; 5、拉伤为细条状,多条。
打磨抛光表面; 6、模具表面过热,均匀粘铝。
涂料用量薄而均匀,不能漏喷涂料; 7、型腔表面粘附铝合金。
适当增加含铁量至0.6~0.8%;8、型腔表面粘附铝合金,尤其是内浇口附近。
常见铸件缺陷及方案改善对策
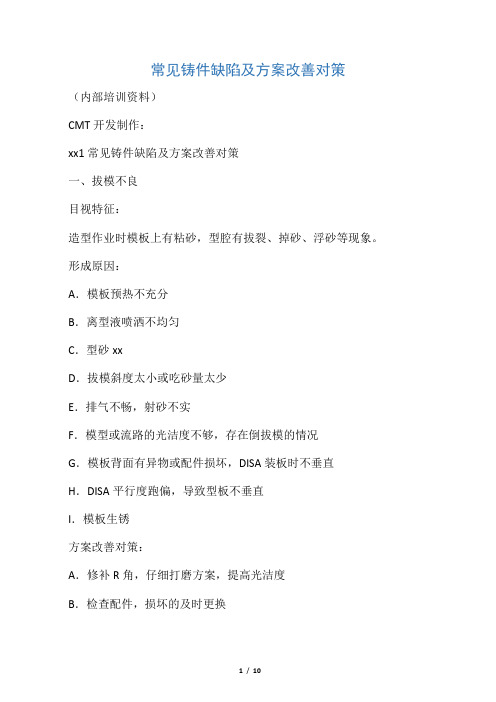
常见铸件缺陷及方案改善对策(内部培训资料)CMT开发制作:xx1常见铸件缺陷及方案改善对策一、拔模不良目视特征:造型作业时模板上有粘砂,型腔有拔裂、掉砂、浮砂等现象。
形成原因:A.模板预热不充分B.离型液喷洒不均匀C.型砂xxD.拔模斜度太小或吃砂量太少E.排气不畅,射砂不实F.模型或流路的光洁度不够,存在倒拔模的情况G.模板背面有异物或配件损坏,DISA装板时不垂直H.DISA平行度跑偏,导致型板不垂直I.模板生锈方案改善对策:A.修补R角,仔细打磨方案,提高光洁度B.检查配件,损坏的及时更换C.必要时增加拔模斜度,若流路拔模不良,用补土补大斜度或使用2a铝流路D.增加透气孔(网)数量,避免射砂不实造成拔模不良E.用气铣刀抛光拔模不良部位F.在通孔内粘贴橡胶头G.直径较小、xx大的孔内建议镶铜套H.最好的方案设计二、砂眼、挤砂目视特征:铸件表面或内部包容着砂粒的孔穴或明显少肉形成原因:A.流路或模具拔模不良,有拔裂、掉砂B.流路设计不当,浇注时铁水冲刷造成砂眼C.设计不当,冲型时间长,长时间的烘烤及“水分迁移”造成局部型砂强度低,形成砂眼D.型砂含水量低E.型腔内有“落砂”,如造型室磨损,浇口杯下沉,压型(实)器压到浇口或造型室上方有落砂F.造型室磨损,反板抬起时有“甩砂”现象G.砂芯有毛刺或浮砂,下芯时未吹干净H.MASK下芯时铲砂或合模时挤砂I.模板变形,造成挤砂、落砂J.模型镶板时没装平,造成型腔挤砂K.DISA夹板或因有凸起物把砂模夹裂,将砂型挤压变形,造成挤砂或砂眼方案改善对策:A.重新计算方案,建议尽量减少冒口入水,以利砂渣上浮B.抛光模型、打磨流路,减少因拔模不良造成的砂渣眼2C.方案设计时采用综合浇注系统,提高浇注系统的挡渣效果D.若浇注时间太长或不能同时冲型,重新计算方案E.增加底注或侧入水F.模具配件若有磨损及时更换G.若有挤砂,确认镶板无问题时,在挤砂位置合模线处R角或做出防压条H.造型时,若型板后面喷砂、甩砂,确认模板尺寸,磨损严重时进行焊补维修I.减薄入水片或压边量,提高挡渣能力J.若下芯铲砂时调整MASK,确认芯钉过盈量K.改变入水口位置,避开易冲砂部位(入水不要做在砂芯吹砂口上)L.在方案上做出集渣包M.横流路用4A流路,xx浮渣三、冷隔(浇不足)目视特征:外观铸件不完整,有裂纹状的间隙或断流,裂纹或断流处的金属边缘呈圆滑状原因:A.浇注作业时断续浇注,没有满杯浇注B.浇注温度过低,铁水流动性差C.方案设计不合理,浇注时间太长或不能同时冲型D.多处入水的液流头产生了凝固堵塞或流头氧化造成两股流头不能融合在一起方案对策:A.重新计算方案,加快浇注速度B.增加排气道,加快冲型速度,降低冲型阻力C.合理设置入水口位置,避免距离浇口较远部位因铁水氧化和降温出现冷隔D.在冷隔位置增加入水,提高该处温度四、缩孔(松)目视特征:缩孔:铸件中容积大,孔壁表面粗糙,形状极不规则的孔洞缩松:铸件截面上分布着弥散的大量形状不规则的微小孔眼或裂隙状孔洞形成原因:A.冒口设置位置或大小不合理,铁水凝固过程中体积收缩且得不到补偿而出现体积亏损,体积亏损集中在一处形成缩孔,在局部分散分布形成缩松B.冒口颈形状或截面积不合理,补缩通道堵塞,使冒口未能起到补缩作用C.冒口温度低,凝固早补缩作用差D.金属液CE值低方案改善对策:A.增加冒口体积B.加大(或减小)冒口颈C.增加冒口入水,提高冒口温度D.改变冒口位置或形状,改变凝固顺序使原本不能得到补偿的收缩部位可以得到补偿,消除缩孔或缩松E.在适当位置放置冷铁(如TRW支架系列)F.改变入水位置,以获得合理的温度场和凝固顺序五、气孔:1.侵入性气孔:气孔尺寸一般较大,呈圆球形、团球形或梨形;梨形的小头指向外3部气源方向;孔壁平滑,侵入气体成份主要为CO时孔壁呈蓝色,侵入气体成份主要为氢气时孔壁呈金属本色且发亮,侵入气体成份主要为水蒸气时孔壁呈氧化色且发暗。
铸造件问题原因及措施
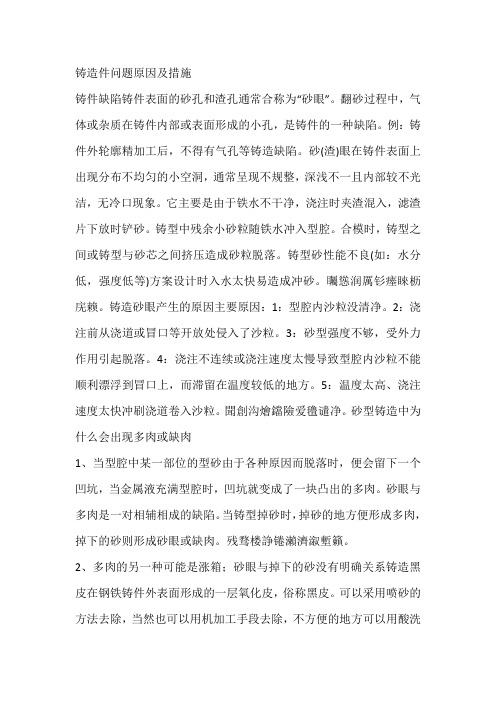
铸造件问题原因及措施铸件缺陷铸件表面的砂孔和渣孔通常合称为“砂眼”。
翻砂过程中,气体或杂质在铸件内部或表面形成的小孔,是铸件的一种缺陷。
例:铸件外轮廓精加工后,不得有气孔等铸造缺陷。
砂(渣)眼在铸件表面上出现分布不均匀的小空洞,通常呈现不规整,深浅不一且内部较不光洁,无冷口现象。
它主要是由于铁水不干净,浇注时夹渣混入,滤渣片下放时铲砂。
铸型中残余小砂粒随铁水冲入型腔。
合模时,铸型之间或铸型与砂芯之间挤压造成砂粒脱落。
铸型砂性能不良(如:水分低,强度低等)方案设计时入水太快易造成冲砂。
矚慫润厲钐瘗睞枥庑赖。
铸造砂眼产生的原因主要原因:1:型腔内沙粒没清净。
2:浇注前从浇道或冒口等开放处侵入了沙粒。
3:砂型强度不够,受外力作用引起脱落。
4:浇注不连续或浇注速度太慢导致型腔内沙粒不能顺利漂浮到冒口上,而滞留在温度较低的地方。
5:温度太高、浇注速度太快冲刷浇道卷入沙粒。
聞創沟燴鐺險爱氇谴净。
砂型铸造中为什么会出现多肉或缺肉1、当型腔中某一部位的型砂由于各种原因而脱落时,便会留下一个凹坑,当金属液充满型腔时,凹坑就变成了一块凸出的多肉。
砂眼与多肉是一对相辅相成的缺陷。
当铸型掉砂时,掉砂的地方便形成多肉,掉下的砂则形成砂眼或缺肉。
残骛楼諍锩瀨濟溆塹籟。
2、多肉的另一种可能是涨箱;砂眼与掉下的砂没有明确关系铸造黑皮在钢铁铸件外表面形成的一层氧化皮,俗称黑皮。
可以采用喷砂的方法去除,当然也可以用机加工手段去除,不方便的地方可以用酸洗的方法去除。
有这层氧化皮后,由于这层氧化皮可能脱落,外观变得不好看,不易采取油漆电镀等防腐措施,如果浸在液体中使液体出现杂质。
应该讲没有多少正面作用。
酽锕极額閉镇桧猪訣锥。
1、提高浇铸温度,采用保温冐口,铁水防氧化保护。
适当增加加工余量2、有可能是加工时刀具磨损过度导致刀具和零件产生摩擦产生的。
请检查更换刀具。
3、适当增加加工余量1常见的铸造缺陷有哪些形成的原因及解决办法一、气孔形成原因:1.液体金属浇注时被卷入的气体在合金液凝固后以气孔的形式存在于铸件中2.金属与铸型反应后在铸件表皮下生成的皮下气孔3.合金液中的夹渣或氧化皮上附着的气体被混入合金液后形成气孔解决方法及修补1.浇注时防止空气卷入2.合金液在进入型腔前先经过滤网以去除合金液中的夹渣、氧化皮和气泡3.更换铸型材料或加涂料层防止合金液与铸型发生反应4.在允许补焊部位将缺陷清理干净后进行补焊二、疏松形成原因1.合金液除气不干净形成疏松2.最后凝固部位不缩不足3.铸型局部过热、水分过多、排气不良解决方法及修补1.保持合理的凝固顺序和补缩2.炉料静洁3.在疏松部位放置冷铁4.在允许补焊的部位可将缺陷部位清理干净后补焊三、夹杂形成原因1.外来物混入液体合金并浇注人铸型2.精炼效果不良3.铸型内腔表面的外来物或造型材料剥落解决方法及修补1.仔细精炼并注意扒查2.熔炼工具涂料层应附着牢固3.浇注系统及型腔应清理干净4.炉料应保持清洁5.表面夹杂可打磨去除,必要时可进行补焊四、夹渣形成原因1.精炼变质处理后除渣不干净2.精炼变质后静置时间不够3.浇注系统不合理,二次氧化皮卷入合金液中2.4精炼后合金液搅动或被污染解决方法及修补1.严格执行精炼变质浇注工艺要求2.浇注时应使金属液平稳地注入铸型3.炉料应保持清洁,回炉料处理及使用应严格遵守工艺规程五、裂纹形成原因1.铸件各部分冷却不均匀2.铸件凝固和冷却过程受到外界阻力而不能自由收缩,内应力超过合金强度而产生裂纹解决方法及修补1.尽可能保持顺序凝固或同时凝固,减少内应力2.细化合金组织3.选择适宜的浇注温度4.增加铸型的退让性六、偏析形成原因合金凝固时析出相与液相所含溶质浓度不同,多数情况液相溶质富集而又来不及扩散而使先后凝固部分的化学成分不均匀解决方法1.熔炼过程中加强搅拌并适当的静置2.适当增加凝固冷却速度七、成分超差形成原因1.中间合金或预制合金成分不均匀或成分分析误差过大2.炉料计算或配料称量错误3.熔炼操作失当,易氧化元素烧损过大4.熔炼搅拌不均匀、易偏析元素分布不均匀解决方法1.炉前分析成分不合格时可适当进行调整2.最终检验不合格时可会同设计使用部门协商处理八、针孔形成原因合金在液体状态下溶解的气体(主要为氢),在合金凝固过程中自合金中析出而形成的均布形成的孔洞解决方法及修补1.合金液体状态下彻底精炼除气2.在凝固过程中加大凝固速度防止溶解的气体自合金中析出3.3铸件在压力下凝固,防止合金溶解的气体析出4.炉料、辅助材料及工具应干燥彈贸摄尔霁毙攬砖卤庑。
常见铸件缺陷及其预防措施

铸件缺陷常见铸件缺陷及其预防措施1).冷紋:原因:熔汤前端的温度太低,相叠时有痕迹.改善方法:1.检查壁厚是否太薄(設計或制造) ,较薄的区域应直接充填.2.检查形狀是否不易充填;距离太远、封閉区域(如鳍片(fin) 、凸起) 、被阻挡区域、圆角太小等均不易充填.並注意是否有肋点或冷点.3.缩短充填时间.缩短充填时间的方法:…4.改变充填模式.5.提高模温的方法:…6.提高熔汤温度.7.检查合金成分.8.加大逃气道可能有用.9.加真空裝置可能有用.2).裂痕:原因:1.收缩应力.2.頂出或整缘时受力裂开.改善方式:1.加大圆角.2.检查是否有热点.3.增压时间改变(冷室机).4.增加或缩短合模时间.5.增加拔模角.6.增加頂出銷.7.检查模具是否有錯位、变形.8.检查合金成分.3).气孔:原因:1.空气夾杂在熔汤中.2.气体的来源:熔解时、在料管中、在模具中、离型剂.改善方法:1.适当的慢速.2.检查流道转弯是否圆滑,截面积是否渐減.3.检查逃气道面积是否够大,是否有被阻塞,位置是否位於最后充填的地方.4.检查离型剂是否噴太多,模温是否太低.5.使用真空.4).空蚀:原因:因压力突然減小,使熔汤中的气体忽然膨胀,冲击模具,造成模具損伤.改善方法:流道截面积勿急遽变化.5).缩孔:原因:当金属由液态凝固为固态时所占的空间变小,若无金属补充便会形成缩孔.通常发生在较慢凝固处.改善方法:1.增加压力.2.改变模具温度.局部冷却、噴离型剂、降低模温、.有时只是改变缩孔位置,而非消缩孔.6).脫皮:原因:1.充填模式不良,造成熔汤重叠.2.模具变形,造成熔汤重叠.3.夾杂氧化层.改善方法:1.提早切換为高速.2.缩短充填时间.3.改变充填模式,浇口位置,浇口速度.4.检查模具強度是否足夠.5.检查銷模裝置是否良好.6.检查是否夾杂氧化层.7).波紋:原因:第一层熔汤在表面急遽冷却,第二层熔汤流過未能将第一层熔解,却又有足夠的融合,造成組织不同. 改善方法:1.改善充填模式.2.缩短充填时间.8).流动不良产生的孔:原因:熔汤流动太慢、或是太冷、或是充填模式不良,因此在凝固的金属接合处有孔.改善方法:1.同改善冷紋方法.2.检查熔汤温度是否稳定.3.检查模具温充是否稳定.9).在分模面的孔:原因:可能是缩孔或是气孔.改善方法:1.若是缩孔,減小浇口厚度或是溢流井进口厚度.2.冷却浇口.3.若是气孔,注意排气或捲气問题.10).毛边:原因:1.鎖模力不足.2.模具合模不良.3.模具強度不足.4.熔汤温度太高.11).缩陷:原因:缩孔发生在压件表面下面.改善方法:1.同改善缩孔的方法.2.局部冷却.3.加热另一边.12).积碳:原因:离型剂或其他杂质积附在模具上.改善方法:1.减小离型剂喷洒量.2.升高模温.3.选择适合的离型剂.4.使用软水稀釋离型剂.13).冒泡:原因:气体捲在铸件的表面下面.改善方式:1.減少捲气(同气孔).2.冷却或防低模温.14).粘模:原因:1.鋅积附在模具表面.2.熔汤冲击模具,造成模面损坏.改善方法:1.降低模具温度.2.降低划面粗糙度.3.加大拔模角.4.镀膜.5.改变充填模式.6.降低浇口速度序缺陷名称缺陷特征预防措施1气孔在铸件内部、表面或近于表面处,有大小不等的光滑孔眼,形状有圆的、长的及不规则的,有单个的,也有聚集成片的。
铸造缺陷特征原因及预防措施图文并茂
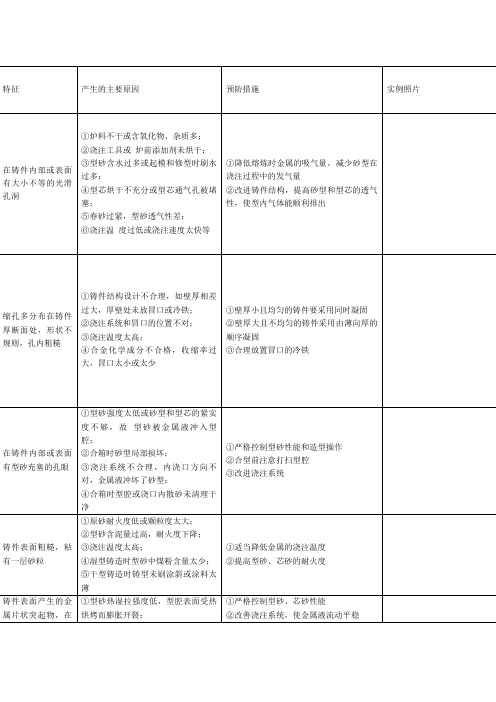
特征产生的主要原因预防措施实例照片在铸件内部或表面有大小不等的光滑孔洞①炉料不干或含氧化物、杂质多;②浇注工具或炉前添加剂未烘干;③型砂含水过多或起模和修型时刷水过多;④型芯烘干不充分或型芯通气孔被堵塞;⑤春砂过紧,型砂透气性差;⑥浇注温度过低或浇注速度太快等①降低熔炼时金属的吸气量,减少砂型在浇注过程中的发气量②改进铸件结构,提高砂型和型芯的透气性,使型内气体能顺利排出缩孔多分布在铸件厚断面处,形状不规则,孔内粗糙①铸件结构设计不合理,如壁厚相差过大,厚壁处未放冒口或冷铁;②浇注系统和冒口的位置不对;③浇注温度太高;④合金化学成分不合格,收缩率过大,冒口太小或太少①壁厚小且均匀的铸件要采用同时凝固②壁厚大且不均匀的铸件采用由薄向厚的顺序凝固③合理放置冒口的冷铁在铸件内部或表面有型砂充塞的孔眼①型砂强度太低或砂型和型芯的紧实度不够,故型砂被金属液冲入型腔;②合箱时砂型局部损坏;③浇注系统不合理,内浇口方向不对,金属液冲坏了砂型;④合箱时型腔或浇口内散砂未清理干净①严格控制型砂性能和造型操作②合型前注意打扫型腔③改进浇注系统铸件表面粗糙,粘有一层砂粒①原砂耐火度低或颗粒度太大;②型砂含泥量过高,耐火度下降;③浇注温度太高;④湿型铸造时型砂中煤粉含量太少;⑤干型铸造时铸型未刷涂斜或涂料太薄①适当降低金属的浇注温度②提高型砂、芯砂的耐火度铸件表面产生的金属片状突起物,在①型砂热湿拉强度低,型腔表面受热烘烤而膨胀开裂;①严格控制型砂、芯砂性能②改善浇注系统,使金属液流动平稳金属片状突起物与铸件之间夹有一层型砂②砂型局部紧实度过高,水分过多,水分烘干后型腔表面开裂;③浇注位置选择不当,型腔表面长时间受高温铁水烘烤而膨胀开裂;④浇注温度过高,浇注速度太慢③大平面铸件要倾斜浇注④适当调整浇注温度和浇注速度铸件沿分型面有相对位置错移①模样的上半模和下半模未对准;②合箱时,上下砂箱错位;③上下砂箱未夹紧或上箱未加足够压铁,浇注时产生错箱④砂箱或模板定位不准确,或定位销松动①定期检查砂箱、模板的定位销及销孔、并合理地安装;②定期对套箱整形,脱箱后的铸型在搬运时要小心。
压铸件常见的缺陷分析及其改善措施
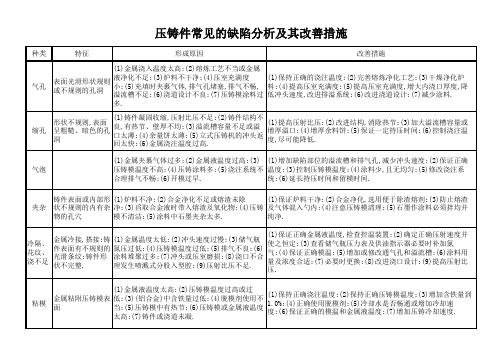
粘模
金属粘附压铸模表 面
(1)金属液温度太高;(2)压铸模温度过高或过 低;(3)(铝合金)中含铁量过低;(4)脱模剂使用不 当;(5)压铸模中有热节;(6)压铸模或金属液温度 太高;(7)铸件或浇道未凝.
(1)保持正确浇注温度;(2)保持正确压铸模温度;(3)增加含铁量到 1.0%;(4)正确使用脱模剂;(5)冷却水是否畅通或增加冷却速 度;(6)保证正确的模温和金属液温度;(7)增加压铸冷却速度.
纯净.
ቤተ መጻሕፍቲ ባይዱ
冷隔、 花纹、 浇不足
金属冷接,搭接;铸 (1)金属温度太低;(2)冲头速度过慢;(3)储气瓶
件表面有不规则的 氮压过低;(4)压铸模温度过低;(5)排气不良;(6)
光滑条纹;铸件形 涂料堆聚过多;(7)冲头或压室磨损;(8)浇口不合
状不完整.
理发生喷溅式分股入型腔;(9)压射比压不足.
(1)保证正确金属液温度,检查控温装置;(2)确定正确压射速度并 使之恒定;(3)查看储气瓶压力表及供油指示器必要时补加氮 气;(4)保证正确模温;(5)增加或修改通气孔和溢流槽;(6)涂料用 量及浓度合适;(7)必要时更换;(8)改进浇口设计;(9)提高压射比 压.
气泡
(1)金属夹裹气体过多;(2)金属液温度过高;(3) (1)增加缺陷部位的溢流槽和排气孔,减少冲头速度;(2)保证正确
压铸模温度不高;(4)压铸涂料多;(5)浇注系统不 温度;(3)控制压铸模温度;(4)涂料少,且无均匀;(5)修改浇注系
合理排气不畅;(6)开模过早.
统;(6)延长持压时间和留模时间.
压铸件常见的缺陷分析及其改善措施
种类
特征
形成原因
改善措施
气孔
(1)金属浇入温度太高;(2)熔炼工艺不当或金属
干货:铸造五大缺陷及其解决对策

干货:铸造五大缺陷及其解决对策缺陷一:铸造缩孔主要原因有合金凝固收缩产生铸造缩孔和合金溶解时吸收了大量的空气中的氧气、氮气等,合金凝固时放出气体造成铸造缩孔。
解决的办法:1)放置储金球。
2)加粗铸道的直径或减短铸道的长度。
3)增加金属的用量。
4)采用下列方法,防止组织面向铸道方向出现凹陷。
a.在铸道的根部放置冷却道。
b.为防止已熔化的金属垂直撞击型腔,铸道应成弧形。
c.斜向放置铸道。
缺陷二:铸件表面粗糙不光洁缺陷型腔表面粗糙和熔化的金属与型腔表面产生了化学反应,主要体现出下列情况。
(华亨铸件,最专业的的双金属锤头铸造商)1)包埋料粒子粗,搅拌后不细腻。
2)包埋料固化后直接放入茂福炉中焙烧,水分过多。
3)焙烧的升温速度过快,型腔中的不同位置产生膨胀差,使型腔内面剥落。
4)焙烧的最高温度过高或焙烧时间过长,使型腔内面过于干燥等。
5)金属的熔化温度或铸圈的焙烧的温度过高,使金属与型腔产生反应,铸件表面烧粘了包埋料。
6)铸型的焙烧不充分,已熔化的金属铸入时,引起包埋料的分解,发生较多的气体,在铸件表面产生麻点。
7)熔化的金属铸入后,造成型腔中局部的温度过高,铸件表面产生局部的粗糙。
解决的办法:a.不要过度熔化金属。
b.铸型的焙烧温度不要过高。
c.铸型的焙烧温度不要过低(磷酸盐包埋料的焙烧温度为800度-900度)。
d.避免发生组织面向铸道方向出现凹陷的现象。
e.在蜡型上涂布防止烧粘的液体。
缺陷三:铸件发生龟裂缺陷有两大原因,一是通常因该处的金属凝固过快,产生铸造缺陷(接缝);二是因高温产生的龟裂。
1)对于金属凝固过快,产生的铸造接缝,可以通过控制铸入时间和凝固时间来解决。
铸入时间的相关因素:蜡型的形状、铸到的粗细数量、铸造压力(铸造机)。
包埋料的透气性。
凝固时间的相关因素:蜡型的形状。
铸圈的最高焙烧温度。
包埋料的类型。
金属的类型。
铸造的温度。
2)因高温产生的龟裂,与金属及包埋料的机械性能有关。
下列情况易产生龟裂:铸入温度高易产生龟裂;强度高的包埋料易产生龟裂;延伸性小的镍烙合金及钴烙合金易产生龟裂。
铝铸件常见缺陷的形成原因及整改方式
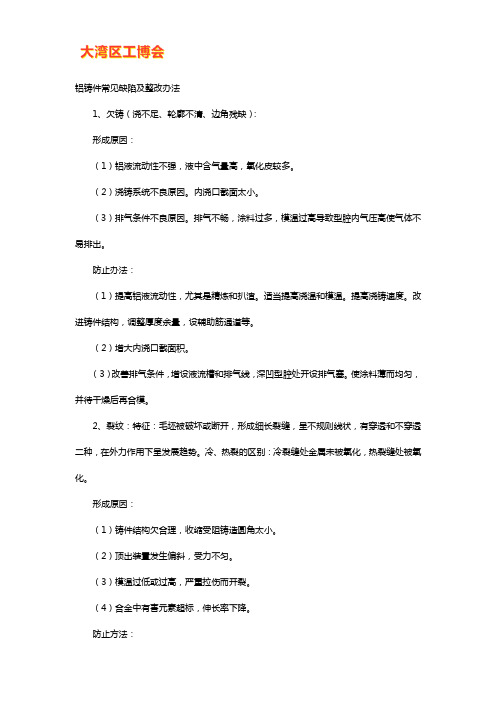
铝铸件常见缺陷及整改办法1、欠铸(浇不足、轮廓不清、边角残缺):形成原因:(1)铝液流动性不强,液中含气量高,氧化皮较多。
(2)浇铸系统不良原因。
内浇口截面太小。
(3)排气条件不良原因。
排气不畅,涂料过多,模温过高导致型腔内气压高使气体不易排出。
防止办法:(1)提高铝液流动性,尤其是精炼和扒渣。
适当提高浇温和模温。
提高浇铸速度。
改进铸件结构,调整厚度余量,设辅助筋通道等。
(2)增大内浇口截面积。
(3)改善排气条件,增设液流槽和排气线,深凹型腔处开设排气塞。
使涂料薄而均匀,并待干燥后再合模。
2、裂纹:特征:毛坯被破坏或断开,形成细长裂缝,呈不规则线状,有穿透和不穿透二种,在外力作用下呈发展趋势。
冷、热裂的区别:冷裂缝处金属未被氧化,热裂缝处被氧化。
形成原因:(1)铸件结构欠合理,收缩受阻铸造圆角太小。
(2)顶出装置发生偏斜,受力不匀。
(3)模温过低或过高,严重拉伤而开裂。
(4)合金中有害元素超标,伸长率下降。
防止方法:(1)改进铸件结构,减小壁厚差,增大圆角和圆弧R,设置工艺筋使截面变化平缓。
(2)修正模具。
(3)调整模温到工作温度,去除倒斜度和不平整现象,避免拉裂。
(4)控制好铝涂成份,成其是有害元素成份。
3、冷隔:特征:液流对接或搭接处有痕迹,其交接边缘圆滑,在外力作用下有继续发展趋势。
形成原因:(1)液流流动性差。
(2)液流分股填充融合不良或流程太长。
(3)填充温充太低或排气不良。
(4)充型压力不足。
防止方法:(1)适当提高铝液温度和模具温度,检查调整合金成份。
(2)使充填充分,合理布置溢流槽。
(3)提高浇铸速度,改善排气。
(4)增大充型压力。
4、凹陷:特征:在平滑表面上出现的凹陷部分。
形成原因:(1)铸件结构不合理,在局部厚实部位产生热节。
(2)合金收缩率大。
(3)浇口截面积太小。
(4)模温太高。
防止方法:(1)改进铸件结构,壁厚尽量均匀,多用过渡性连接,厚实部位可用镶件消除热节。
(2)减小合金收缩率。
铝合金铸造常见缺陷与对策
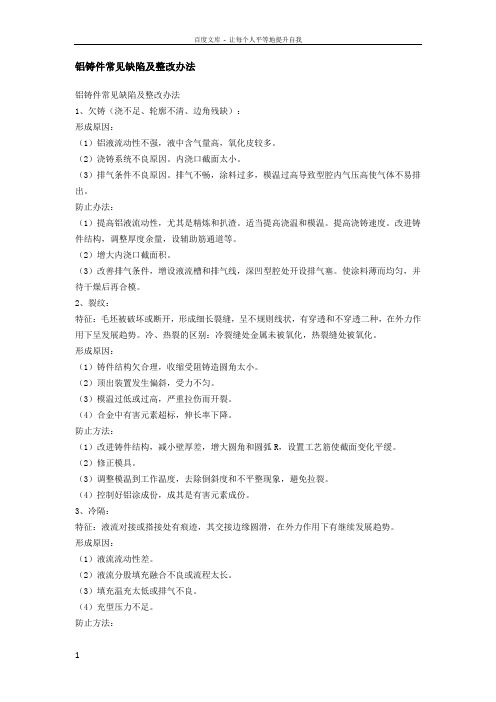
铝铸件常见缺陷及整改办法铝铸件常见缺陷及整改办法1、欠铸(浇不足、轮廓不清、边角残缺):形成原因:(1)铝液流动性不强,液中含气量高,氧化皮较多。
(2)浇铸系统不良原因。
内浇口截面太小。
(3)排气条件不良原因。
排气不畅,涂料过多,模温过高导致型腔内气压高使气体不易排出。
防止办法:(1)提高铝液流动性,尤其是精炼和扒渣。
适当提高浇温和模温。
提高浇铸速度。
改进铸件结构,调整厚度余量,设辅助筋通道等。
(2)增大内浇口截面积。
(3)改善排气条件,增设液流槽和排气线,深凹型腔处开设排气塞。
使涂料薄而均匀,并待干燥后再合模。
2、裂纹:特征:毛坯被破坏或断开,形成细长裂缝,呈不规则线状,有穿透和不穿透二种,在外力作用下呈发展趋势。
冷、热裂的区别:冷裂缝处金属未被氧化,热裂缝处被氧化。
形成原因:(1)铸件结构欠合理,收缩受阻铸造圆角太小。
(2)顶出装置发生偏斜,受力不匀。
(3)模温过低或过高,严重拉伤而开裂。
(4)合金中有害元素超标,伸长率下降。
防止方法:(1)改进铸件结构,减小壁厚差,增大圆角和圆弧R,设置工艺筋使截面变化平缓。
(2)修正模具。
(3)调整模温到工作温度,去除倒斜度和不平整现象,避免拉裂。
(4)控制好铝涂成份,成其是有害元素成份。
3、冷隔:特征:液流对接或搭接处有痕迹,其交接边缘圆滑,在外力作用下有继续发展趋势。
形成原因:(1)液流流动性差。
(2)液流分股填充融合不良或流程太长。
(3)填充温充太低或排气不良。
(4)充型压力不足。
防止方法:(1)适当提高铝液温度和模具温度,检查调整合金成份。
(2)使充填充分,合理布置溢流槽。
(3)提高浇铸速度,改善排气。
(4)增大充型压力。
4、凹陷:特征:在平滑表面上出现的凹陷部分。
形成原因:(1)铸件结构不合理,在局部厚实部位产生热节。
(2)合金收缩率大。
(3)浇口截面积太小。
(4)模温太高。
防止方法:(1)改进铸件结构,壁厚尽量均匀,多用过渡性连接,厚实部位可用镶件消除热节。
铸造缺陷及其解决方法
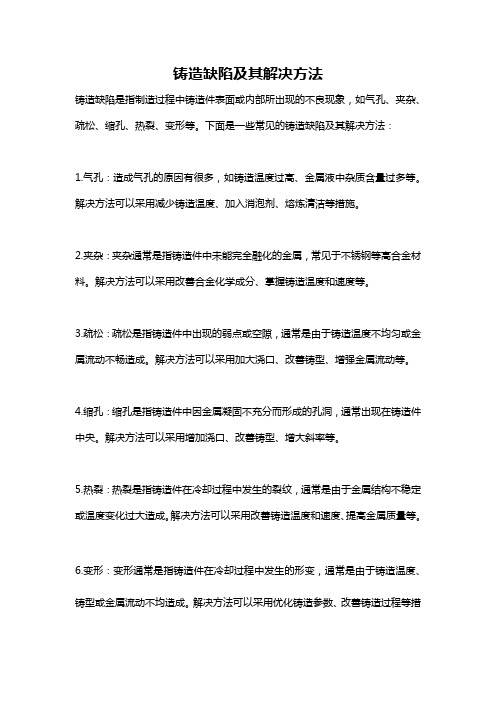
铸造缺陷及其解决方法
铸造缺陷是指制造过程中铸造件表面或内部所出现的不良现象,如气孔、夹杂、疏松、缩孔、热裂、变形等。
下面是一些常见的铸造缺陷及其解决方法:
1.气孔:造成气孔的原因有很多,如铸造温度过高、金属液中杂质含量过多等。
解决方法可以采用减少铸造温度、加入消泡剂、熔炼清洁等措施。
2.夹杂:夹杂通常是指铸造件中未能完全融化的金属,常见于不锈钢等高合金材料。
解决方法可以采用改善合金化学成分、掌握铸造温度和速度等。
3.疏松:疏松是指铸造件中出现的弱点或空隙,通常是由于铸造温度不均匀或金属流动不畅造成。
解决方法可以采用加大浇口、改善铸型、增强金属流动等。
4.缩孔:缩孔是指铸造件中因金属凝固不充分而形成的孔洞,通常出现在铸造件中央。
解决方法可以采用增加浇口、改善铸型、增大斜率等。
5.热裂:热裂是指铸造件在冷却过程中发生的裂纹,通常是由于金属结构不稳定或温度变化过大造成。
解决方法可以采用改善铸造温度和速度、提高金属质量等。
6.变形:变形通常是指铸造件在冷却过程中发生的形变,通常是由于铸造温度、铸型或金属流动不均造成。
解决方法可以采用优化铸造参数、改善铸造过程等措
施。
铸件常见缺陷及防止方法

一、表面缺陷和内部缺陷
产生原因
防止方法
A、欠铸(浇不到):液体金属未充满型腔造成铸件缺肉
1、浇铸温度和型壳温度低,流动性差
2、金属液含气量大,氧化严重以致流动性下降
3、铸件壁太薄
4、浇铸系统大小和设置位置不合理,直浇道高度不够
5、型壳焙烧不充分或型壳透气性差,在铸型中形成气袋
6、浇铸速度过慢或浇注时金属液断流
2、壳烧不充分,没排除蜡残余及壳中发气杂质
3、冷壳浇铸,型壳受潮
4、钢水含气多,脱氧不良
5、浇铸系统设计不合理,浇铸时卷入气体
1、改善壳透气性,
2、充分焙烧型壳
3、热壳浇铸,防止受潮
4、改进脱氧方法
5、改进浇铸系统结构
N、多孔性气孔和针孔:铸件上的细小、分散或密集的孔眼
1、炉料不干净,
2、钢水脱氧不良,镇静时间不够,含气量高
1、水玻璃型壳热水脱蜡时,脱蜡液碱性偏大,模料皂化,造成型壳内层局部酥软煮烂
2、面层涂料粘度过大,局部堆积,硬化不透,热水脱蜡时,局部面层涂料层不规则脱落
3、模料熔失不充分,焙烧不彻底,使皂化物和其它有害杂质沉积在型壳内表面某个部位
4、水玻璃型壳的水玻璃模数高、密度大、硬化不充分,造成型壳局部钠盐集聚
5、改进涂料配方,适当增加层数,必要时可采用一些局部强化措施
H、铁刺:铸件表面上出现许多分散或密集的小突刺
1、面层涂料中粉料量少,粘度低
2、面层涂料相对易熔模的涂挂性差
3、面层涂料配制时搅拌时间不充分,涂挂时面层涂料中的粉料趋向撒砂砂粒分布
4、表面层撒砂砂粒较大
1、适当增加面层涂料中粉料加入量,提高粘度
2、严格控制涂料粘度,涂料要涂均匀,力求减少局部堆积,合理选择硬化工艺参数
铸件缺陷及其对策
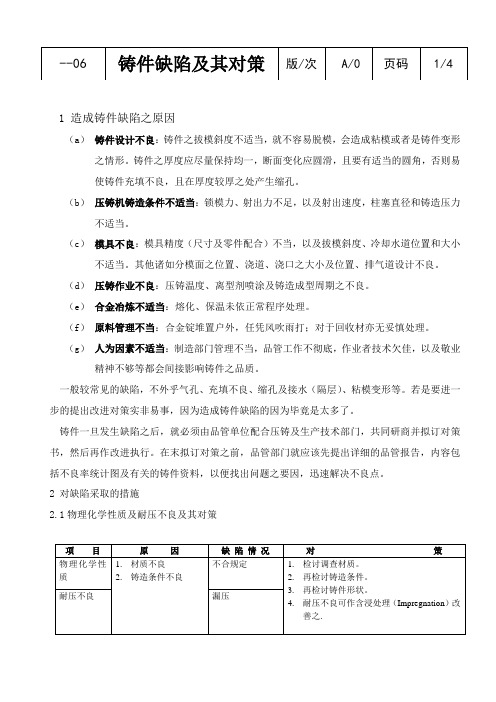
1 造成铸件缺陷之原因
(a)铸件设计不良:铸件之拔模斜度不适当,就不容易脱模,会造成粘模或者是铸件变形之情形。
铸件之厚度应尽量保持均一,断面变化应圆滑,且要有适当的圆角,否则易
使铸件充填不良,且在厚度较厚之处产生缩孔。
(b)压铸机铸造条件不适当:锁模力、射出力不足,以及射出速度,柱塞直径和铸造压力不适当。
(c)模具不良:模具精度(尺寸及零件配合)不当,以及拔模斜度、冷却水道位置和大小不适当。
其他诸如分模面之位置、浇道、浇口之大小及位置、排气道设计不良。
(d)压铸作业不良:压铸温度、离型剂喷涂及铸造成型周期之不良。
(e)合金冶炼不适当:熔化、保温未依正常程序处理。
(f)原料管理不当:合金锭堆置户外,任凭风吹雨打;对于回收材亦无妥慎处理。
(g)人为因素不适当:制造部门管理不当,品管工作不彻底,作业者技术欠佳,以及敬业精神不够等都会间接影响铸件之品质。
一般较常见的缺陷,不外乎气孔、充填不良、缩孔及接水(隔层)、粘模变形等。
若是要进一步的提出改进对策实非易事,因为造成铸件缺陷的因为毕竟是太多了。
铸件一旦发生缺陷之后,就必须由品管单位配合压铸及生产技术部门,共同研商并拟订对策书,然后再作改进执行。
在末拟订对策之前,品管部门就应该先提出详细的品管报告,内容包括不良率统计图及有关的铸件资料,以便找出问题之要因,迅速解决不良点。
2 对缺陷采取的措施
2.1物理化学性质及耐压不良及其对策
2.2尺寸缺陷及措施
2.3 材质缺陷及措施
2.4铸件内部缺陷及其对策。
铸造缺陷特征、原因及预防措施(图文并茂)

缺陷名称特征产生的主要原因预防措施实例照片气孔在铸件内部或表面有大小不等的光滑孔洞①炉料不干或含氧化物、杂质多;②浇注工具或炉前添加剂未烘干;③型砂含水过多或起模和修型时刷水过多;④型芯烘干不充分或型芯通气孔被堵塞;⑤春砂过紧,型砂透气性差;⑥浇注温度过低或浇注速度太快等①降低熔炼时金属的吸气量,减少砂型在浇注过程中的发气量②改进铸件结构,提高砂型和型芯的透气性,使型内气体能顺利排出缩孔与缩松缩孔多分布在铸件厚断面处,形状不规则,孔内粗糙①铸件结构设计不合理,如壁厚相差过大,厚壁处未放冒口或冷铁;②浇注系统和冒口的位置不对;③浇注温度太高;④合金化学成分不合格,收缩率过大,冒口太小或太少①壁厚小且均匀的铸件要采用同时凝固②壁厚大且不均匀的铸件采用由薄向厚的顺序凝固③合理放置冒口的冷铁编辑版word砂眼在铸件内部或表面有型砂充塞的孔眼①型砂强度太低或砂型和型芯的紧实度不够,故型砂被金属液冲入型腔;②合箱时砂型局部损坏;③浇注系统不合理,内浇口方向不对,金属液冲坏了砂型;④合箱时型腔或浇口内散砂未清理干净①严格控制型砂性能和造型操作②合型前注意打扫型腔③改进浇注系统粘砂铸件表面粗糙,粘有一层砂粒①原砂耐火度低或颗粒度太大;②型砂含泥量过高,耐火度下降;③浇注温度太高;④湿型铸造时型砂中煤粉含量太少;⑤干型铸造时铸型未刷涂斜或涂料太薄①适当降低金属的浇注温度②提高型砂、芯砂的耐火度夹砂铸件表面产生的金属片状突起物,在金属片状突起物与铸件之间夹有一层型砂①型砂热湿拉强度低,型腔表面受热烘烤而膨胀开裂;②砂型局部紧实度过高,水分过多,水分烘干后型腔表面开裂;③浇注位置选择不当,型腔表面长时间受高温铁水烘烤而膨胀开裂;④浇注温度过高,浇注速度太慢①严格控制型砂、芯砂性能②改善浇注系统,使金属液流动平稳③大平面铸件要倾斜浇注④适当调整浇注温度和浇注速度编辑版word错型铸件沿分型面有相对位置错移①模样的上半模和下半模未对准;②合箱时,上下砂箱错位;③上下砂箱未夹紧或上箱未加足够压铁,浇注时产生错箱④砂箱或模板定位不准确,或定位销松动①定期检查砂箱、模板的定位销及销孔、并合理地安装;②定期对套箱整形,脱箱后的铸型在搬运时要小心。
- 1、下载文档前请自行甄别文档内容的完整性,平台不提供额外的编辑、内容补充、找答案等附加服务。
- 2、"仅部分预览"的文档,不可在线预览部分如存在完整性等问题,可反馈申请退款(可完整预览的文档不适用该条件!)。
- 3、如文档侵犯您的权益,请联系客服反馈,我们会尽快为您处理(人工客服工作时间:9:00-18:30)。
2. 提高压射比压,缩短填充时间 3.提高压射速度,同时加大内浇口截面 积 4.改善排气、填充条件
5.填充速度低
5.正确选用合金,提高合金流动性
6.压射比压低
1.不合适的脱模剂
2. 脱模剂用量过多,局部堆积
1.更换优质脱模剂
7
变色、斑点
铸件表面上呈现出不同的颜色 及斑点
3.含有石墨的润滑剂中的石墨落入铸 件表层
阻,尖角位形成应力
6.留模时间过长,应力大
7. 顶出时受力不均匀
1.正确控制合金成分,在某些情况下可 在合金中加纯铝锭以降低合金中含镁 量;或在合金中加铝硅中间合金以提 高硅含量 2.改变铸件结构,加大圆角,加大出模 斜度,减少壁厚差 3.变更或增加顶出位置,使顶出受力均 匀 4.缩短开模及抽芯时间 5.提高模温,模温要稳定
1.锁模力不够
1.检查合模力和增压情况,调整压铸工
2.压射速度过高,形成压力冲击峰过 艺参数
11
毛刺飞边
压铸件在分型面边缘上出现金 高
属薄片
3.分型面上杂物未清理干净
2. 清洁型腔及分型面 3.修整模具
4.模具强度不够造成变形
4.最好是采用闭合压射结束时间控制系
5. 镶块、滑块磨损与分型面不平齐 统,可实现无飞边压铸
金属液与模具产生焊合、粘附 致合金液产生粘附
4.调整合金含铁量
而拉伤,以致铸件表面多肉或 5.脱模剂使用效果不好
缺肉
6. 铝合金成分铁含量低于
5.控制合适的浇注温度,控制模温 6.修改内浇口,避免直冲型芯型壁或
7.冷却时间过长或过短
对型芯表面进行特殊处理
气泡
1.合金液在压室充满度过低,易产生
卷气,压射速度过高
铸件缺陷产生原因及应对措施
一、表面缺陷
序号 1 2
3
缺陷名称
特征
产生原因
防止措施
拉伤
1.型腔表面有损伤
1.修理模具表面损伤处,修正斜度,提
沿开模方向铸件表面呈现条状 2.出模方向斜度太小或倒斜
高光洁度
的拉伤痕迹,有一定深度,严 3. 顶出时偏斜
2.调整顶杆,使顶出力平衡
重时为一面状伤痕;另一种是 4.浇注温度过高或过低、模温过高 导 3.更换脱模剂
2.严格喷涂量及喷涂操作 3.控制模温
4.模温过低,金属液温度过低导致不 4. 控制金属液温度
规则的凝固引起
1.正确选用压铸模材料及热处理工艺
1.压铸模型腔表面龟裂
2.浇注温度不宜过高,尤其是高熔点合
2. 压铸模材质不当或热处理工艺不正 金
网状发丝一样凸起或凹陷的痕 确
3. 模具预热要充分
8 网状毛翅 迹,随压铸次数增加而不断扩 3.压铸模冷热温差变化大
1.首先进入型腔的金属液形成一个极
5
薄的而又不完全的金属层后,被后来
铸件表面上有与金属液流动方 的金属液所弥补而留下的痕迹
流痕和花纹
向一致的条纹,有明显可见的 与金属体颜色不一样的无方向
2.模温过低,模温不均匀 3. 内浇道截面积过小及位置不当产生
性的纹路,无发展趋势
喷溅
4.作用于金属液的压力不足
1.提高金属液温度 2.提高模温 3.调整内浇道截面积或位置 4.调整充填速度及压力 5. 选用合适的涂料及调整用量
清
1.比压过低
3.提高比压、充填速度 4.改善浇注系统金属液的导流方式,在
2.卷入气体过多,型腔的背压变高, 欠铸部位加开溢流槽、排气槽
充型受阻
5.检查压铸机能力是否足够
三、操作不良,喷涂料过度,涂料堆
积,气体挥发不掉
1.锁模力不够
1.检查合模力和增压情况,调整压铸工
2.压射速度过高,形成压力冲击峰过 艺参数
1.铝合金中杂质锌、铁超过规定范围 1.严格控制金属中杂质成分
4
脆性
铸件基体金属晶粒过于粗大或 2.合金液过热或保温时间过长,导致 2.控制熔炼工艺
极小,使铸件易断裂或磁碎 晶粒粗大
3.降低浇注温度
3.激烈过冷,使晶粒过细
4.提高模具温度
1.压力不足,基体组织致密度差
1.提高比压
5
渗漏
压铸件经耐压试验,产生漏气 、渗水
2. 内部缺陷引起,如气孔、缩孔、渣 孔、裂纹、缩松、冷隔、花纹 3.浇注和排气系统设计不良
2.针对内部缺陷采取相应措施 3.改进浇注系统和排气系统 4.进行浸渗处理,弥补缺陷
4.压铸冲头磨损,压射不稳定
5.更换压室、冲头
机械加工过程或加工后外观检 一、非金属硬点:
查或金相检查:铸件上有硬度 1.混入了合金液表面的氧化物
性 3.修改内浇口,使压力更好传递,有利 于液态金属补缩作用 4.改变铸件结构,消除金属积聚部位, 壁厚尽可能均匀
剧烈
5.加快厚大部位冷却
6.金属液浇注量偏小,余料太薄,起 6.加厚料柄,增加补缩的效果
不到补缩作用
3
夹杂
1.炉料不洁净,回炉料太多
混入压铸件内的金属或非金属 2.合金液未精炼
杂质,加工后可看到形状不规 3.用勺取液浇注时带入熔渣
则,大小、颜色、亮度不同的 4.石墨坩埚或涂料中含有石墨脱落混
点或孔洞
入金属液中
5.保温温度高,持续时间长
1.使用清洁的合金料,特别是回炉炉上 脏物必须清理干净 2.合金熔液须精炼除气,将熔渣清干净 3.用勺取液浇注时,仔细拨开液面,避 免混入熔渣和氧化皮 4.清理型腔、压室 5.控制保温温度和减少保温时间
二、内部缺陷
序号 缺陷名称
特征
产生原因
防止措施
1.合金液导入方向不合理或金属液流
动速度太高,产生喷射;过早堵住排 气道或正面冲击型壁而形成漩涡包住
1.采用干净炉料,控制熔炼温度,进行 排气处理。
1
气孔
空
解剖后外观检查或探伤检查, 气孔具有光滑的表面、形状为 圆形
气,这种气孔多产生于排气不良或深 腔处 2.由于炉料不干净或熔炼温度过高, 使金属液中较多的气体没除净,在凝
1.熔炼铝硅合金时,不要使用硅元素粉
末
7
硬点
机械加工过程或加工后外观检 二、金属硬点
查或金相检查:铸件上有硬度 1.混入了未溶解的硅元素
高于金属基体的细小质点或块 2.初晶硅
状物使刀具磨损严重,加工后 3.铝液温度较低,停放时间较长,Fe
常常显示出不同的亮度
、Mn元素偏析,产生金属间化合物
2. 调整合金成分时,不要直接加入硅 元素,必须采用中间合金 3. 提高熔化温度、浇注温度 4.控制合金成分,特别是Fe杂质量 5.避免Fe、Mn等元素偏析 6.合金中含Si量不宜接近或超过共晶成
5.花纹:涂料用量过多
1.两股金属流相互对接,但未完全熔
合而又无夹杂存在其间,两股金属结 1.适当提高浇注温度和模具温度
压铸件表面有明显的、不规则 合力很薄弱
6
冷隔
的、下陷线性纹路(有穿透与 不穿透两种)形状细小而狭 长,有的交接边缘光滑,外力 作用下有发展的可能
2. 浇注温度或压铸模温度偏低 3.选择合金不当,流动性差 4. 浇道位置不对或流路过长
4. 压铸模要定期或压铸一定次数后退
大和延伸
4.浇注温度过高
火,消除内应力
5.压铸模预热不足
5. 打磨成型部分表面,减少表面粗糙
6. 型腔表面粗糙
度Ra值
6.合理选择模具冷却方法
1.铸件壁厚相差太大,凹陷多产生在
厚壁处
1.铸件壁厚设计尽量均匀
9
凹陷
铸件平滑表面上出现凹陷部位
2. 模具局部过热,过热部分凝固慢 3.压射比压低
分。对原材料控制基体金相组织中的
初晶硅数量
裂纹
1.合金中铁含量过高或硅含量过低
2.合金中有害杂质的含量过高,降低
了合金的可塑性
铸件表面有呈直线状或波浪形 的纹路,狭小而长,在外力作 用下有发展趋势。冷裂:开裂 处金属没被氧化.热裂:开裂处 金属已被氧化.
3.铝硅合金:铝硅铜合金含锌或含铜 量过高;铝镁合金中含镁量过多 4.模具,特别是型芯温度太低 5.铸件壁存有剧烈变化之处,收缩受
2. 模具排气不良
铸件表面有米粒大小的隆起表 皮下形成的空洞
3. 熔液未除气,熔炼温度过高 4.模温过高,金属凝固时间不够,强 度不够,而过早开模顶出铸件,受压
气体膨胀起来
5.脱模剂太多
6.内浇口开设不良,充填方向不顺
1.提高金属液充满度 2.降低第一阶段压射速度,改变低速与 高速压射切换点 3.降低模温 4.增设排气槽、溢流槽、充分排气 5.调整熔炼工艺,进行除气处理 6.留模时间延长 7.减少脱模剂用量
固时析出,没能充分排出。
3.涂料发气量大或使用过多,在浇注
前未浇净,使气体卷入铸件,这种气
2.选择合理工艺参数、压射速度、高速 切换点 3.引导金属液平衡,有序充填型腔,有 利气体排出 4. 排气槽、溢流槽要有足够的排气能 力 5.选择发气量小的涂料及控制排气量
孔多呈暗灰色表面
1.铸件在凝固过程中,因产生收缩而
6
硬点 高于金属基体的细小质点或块 2.合金与炉衬的反应物
状物使刀具磨损严重,加工后 3.金属料混入异物
常常显示出不同的亮度
4.夹杂物
1.铸造时不要把合金液表面的氧化物舀 入勺内 2.清除铁坩埚表面的氧化物后,再上涂 料。及时清理炉壁,炉底的残渣 3.清除勺子等工具上的氧化物 4.使用与铝不产生反应的炉衬材料 5.金属料干净、纯净
得不到金属液补偿而造成孔穴
1.降低浇注温度,减少收缩量
2.浇注温度过高,模温梯度分布不合 2.提高压射比压及增压压力,提高致密
解剖或探伤检查,孔洞形状不
缩孔、缩松
规则、不光滑、表面呈暗色。 大而集中为缩孔