高炉风口参数的设计探讨(百度文库)
第五章高炉送风系统设计解析

特性如下:
①在某一转速下,管网阻力增加(或减小) 出口风压上升(或下降),风量将下降(或 上升); ②风量和风压随转数而变化,转速可做为调 节手段; ③风机转速愈高,风压——风量曲线曲率愈 大。
④概念:
临界压力:风压过高时,风量迅速减少,如 果再提高压力,则产生倒风现象,此时的风 机压力称为临界压力。 风机的飞动曲线:将不同转数的临界压力点 连接起来形成的曲线。 风机不能在飞动曲线的左侧工作,一般 在飞动曲线右侧风量增加 20%以上处工作。
三. 燃烧室:
燃烧室是燃烧煤气的空间,位于炉 内一侧紧靠大墙。 1. 断面形状有三种:
二. 轴流式鼓风机
1. 结构 示意图
轴流式鼓风机
1-机壳;2-转子;3-工作叶片;4-导流叶片; 5-吸气口;6-排气口
2. 工作原理: 依靠在转子上装有扭转一定角度 的工作叶片随转子一起高速旋转,由 于工作叶片对气体作功,使获得能量 的气体沿轴向流动,达到一定的风量 和风压。 3. 特性曲线:
2. 高炉鼓风压力 的确定:
P Pt PLS PFS
式中:
P ——鼓风机出口风压,Pa;
Pt——高炉炉顶压力,Pa;
△PLS——高炉料柱阻力损失,Pa;
△PFS——高炉送风系统阻力损失,Pa。
3. 风机风量、风压 的确定:
风量修正系数K:
( PS PH )T1 K P1T2
620 33500 上 7300 下 6780 4.94
1026 37000 8000 0 下 8000 4.95
1513 44450 9000 4.93
1800 44470 上 9330 下 9000 4.94
2050 54000 上 9960 下 9500 5.68
关于高炉风口面积调节方法的探讨解读

第17卷第12期2007年12月中国冶金China M e ta llur gyV ol .17,N o .12Decembe r .2007作者简介:吴狄峰(1982-,男,硕士生; E -mail :w udifeng 0121083@ ;修订日期:2007-09-13关于高炉风口面积调节方法的探讨吴狄峰1,程树森1,赵宏博1,王子金2(1.北京科技大学冶金与生态工程学院,北京100083;2.莱芜钢铁股份有限公司炼铁厂,山东莱芜271104摘要:通过建立高炉送风系统模型,模拟了风口尺寸对风口速度、流量和鼓风动能的影响,纠正了高炉操作认识上的一些错误。
研究表明,缩小少数几个风口面积会减小鼓风动能,但却增大了其它风口的鼓风动能;只有减小多个风口的面积,才会增大所有风口的鼓风动能。
减小少数几个风口的操作之所以能抑止边缘气流是其风量明显减少所致。
关键词:高炉;风口;风量;面积调节中图分类号:T F54文献标识码:A 文章编号:1006-9356(200712-0055-05Discussion of Tuyere Area Adjusting Method for Blast FurnaceWU Di -feng 1,CH ENG Shu -sen 1,ZH AO H ong -bo 1,WANG Zi -jin 2(1.Scho ol of M etallurg ical a nd Eco lo gical Eng ineering ,U nive rsity o f Science and Technology Beijing ,Beijing 100083China ;2.I ronmaking P lant of Laiw u I ron and Steel Co L td ,Laiwu 271104,Shandong ,China Abstract :A djusting tuye re area is an impor tant me tho d fo r blast furnace bo ttom adjustment .By building the bla st sendingsy stem o f blast furnace ,this paper simulated the effects of changing tuyere area o n tuye re velocity ,flo w and bla st kinetic energ y ,and cor rected misunde rstanding s o f some blast furnace operato rs as w ell .Re sults sho w that dec reasing the area of minor tuy eres w ill reduce the kine tic ene rgy o f these tuye res but increase the o the rs .O nly decreasing the area s of majo r tuy eres w ill increase the kine tic energ y of every tuy ere .The reason tha t dec rea -sing the areas of mino r tuyer es could re st rain the edge g as flow lied in the decrease of blast flo w in these tuy eres .Key words :blastfurnace ;tuyere ;blast flo w ;area adjusting调节风口面积是高炉下部调剂的重要手段。
高炉风口参数的设计探讨(百度文库)

高炉风口参数的设计探讨郭俊奎马铁林摘要风口是高炉送风系统的重要设备之一,通过对高炉风口参数进行分析、论述、探讨,阐述了风口数目,风口高度,风口角度、长度,风口直径对高炉冶炼操作、生产技术经济指标的影响,并从设计角度提出了风口参数的设计、计算参考数据和建议。
关键词高炉风口参数设计探讨0 前言高炉炼铁是一个综合的工艺过程,每一项工艺参数设计对高炉生产都有不同程度的影响,高炉风口是炼铁高炉重要的送风设备之一,有高炉炼铁生产工艺以来就存在风口,高炉鼓风、喷吹的燃料都是通过风口进入高炉内的。
风口参数主要包括风口数量、高度、直径、角度和长度等数据,风口参数对其本身寿命及炼铁高炉生产技术经济指标有重要影响,是高炉下部调剂的重要手段之一。
本文结合节能减排、降低能耗及新工艺的需要,更重要的是通过工业实践,对风口参数进行分析总结、论述探讨,提出了自己的看法,并从设计角度提出了风口参数的设计、计算参考数据和建议,希望使风口参数更加科学合理,做好风口参数设计,从而进一步提高炼铁生产技术经济指标。
1 风口数目的确定高炉风口数目是高炉工艺设计的重要参数之一,主要取决于炉缸直径大小和鼓风机能力,高炉风口数目增多目前是一种趋势,增加风口数目有利于高炉的强化冶炼。
风口数目在满足炼铁工艺要求的同时,还应符合风口的安装尺寸和结构要求。
风口数目的计算有多种方法,但还没有严格的理论计算公式,一般按经验公式粗略计算后确定。
设计手册要求风口弧长间距在1200mm~1400mm,国内曾采用如下公式[1]:f=2d+1式中:f—风口数目,个;d—炉缸直径,m。
式中计算出来的风口数目较少。
国外一般采用如下公式[1]:f=πd/(1.0~1.2)或f=3d风口数目一般为双数。
高炉风口数目的合理设计与高炉操作、技术指标有很大关系。
风口数目增多,风口弧长间距就小,高炉圆周进风相对均匀,可改善煤气流、温度分布,减少风口之间的“死料区”,炉缸燃烧均匀,可活跃炉缸,利于炉况顺行,有节焦、增产等作用,更有利于节能减排。
一种高炉风口进风面积的确定方法

一种高炉风口进风面积的确定方法高炉是冶金工业中常用的设备,用于将铁矿石转化为熔融的铁水。
高炉的风口进风面积对高炉的正常运行和炉渣排出有着重要的影响。
本文将介绍一种确定高炉风口进风面积的方法。
确定高炉风口进风面积的方法主要有两种。
一种是基于经验公式,另一种是基于数值模拟。
基于经验公式的方法是通过分析和总结大量的高炉运行数据和实际经验得出的。
这种方法在实践中被广泛应用并取得了一定的效果。
根据经验公式,高炉风口进风面积与高炉产量、风口气压和风速有关。
一般来说,高炉产量越大,风口进风面积也应相应增大;风口气压越高,进风面积也应相应增大;风速越大,进风面积也应相应增大。
通过对这些因素的综合考虑,可以得到一个经验公式来确定高炉风口进风面积。
基于数值模拟的方法是通过计算机模拟高炉内部流场来确定风口进风面积。
这种方法需要进行复杂的数值计算,需要考虑多个因素的相互作用,如高炉内部的温度分布、气体流动速度等。
通过数值模拟,可以得到高炉内部流场的详细信息,并根据这些信息来确定风口进风面积。
这种方法的优点是能够考虑更多的因素,并能够得到更精确的结果。
然而,由于计算量大且复杂,所以在实际应用中较少采用。
在确定高炉风口进风面积时,还需要考虑一些其他因素。
首先是高炉的设计参数,如高炉容积、高炉型号等。
不同的高炉具有不同的设计参数,所以在确定进风面积时需要考虑这些因素。
其次是高炉的运行状态,如高炉的炉温、炉压等。
不同的运行状态对进风面积的要求也有所不同。
最后是高炉的环保要求。
随着环保意识的增强,对高炉的排放要求也越来越高,所以在确定进风面积时还需要考虑环保因素。
确定高炉风口进风面积是一个复杂的问题,需要考虑多个因素的相互作用。
基于经验公式和基于数值模拟的方法是目前常用的确定方法。
根据实际情况选择适合的方法,可以有效地确定高炉风口进风面积,保证高炉的正常运行和炉渣排出。
2#炉风口调整方案及建议

2#炉风口调整方案及建议为了完成公司下达的生产任务,遵从领导指示,为了在保证高冶强的情况下保证炉顶温度控制在规定范围内,特制订本风口调整方案。
一、风口调整方案1、10#、13#风口由φ115mm的直风口更换为φ120mm的直风口;2、3#、5#、7#、9#、14#、16#使用寿命到期(服役时间2017/3/29),原来尺寸进行更换。
3、调整理由:(1)鉴于2#炉一直存在炉缸铁口区侧壁温度高的威胁,且自9月份开始就一直钛矿护炉至今,为了避免引起煤气流大的变化而影响到炉缸侧壁温度的变化,本着少调微调的原则计划增加两个扩径风口。
(2)因为两铁口相比,北出铁场铁口比南出铁场铁口温度相对较低,铁口区侧壁保护较好,铁口工作也比较稳定,所以两个扩径风口选择在北出铁场方向。
二、风口扩径后的预计不利状况1、我们现在两座高炉的炉缸侧壁温度都偏高,特别是九、十两个月,两座高炉炉缸侧壁温度高点都有突破800℃,为了有效控制炉缸侧壁温度在合理的相对安全区,在高炉加钛矿护炉一个月没有效果的情况下,2#、1#炉先后调整缩小了风口直径,结合其它综合手段,两座高炉炉缸侧壁温度的上升趋势才得以扭转,个人认为下部风口的调整作用要大些。
所以风口再扩径后,高炉煤气流有利于边缘的开放,操作炉型会有一个重新修正形成的过程,在高冶强的状态下有可能破坏现在2#炉炉缸侧壁温度相对稳定的状态。
2、现在两座高炉的风口配置,1#炉φ115mm风口有5个,2#炉φ115mm风口有8个,两高炉相比较2#炉的铁口区侧壁温度要稳定的多。
1#炉风口调整后至今,风口区侧壁温度有两次上探过程,其中第一次10月28日南口东最高温度827℃,第二次是11月26日北口东最高温度874℃,这个温度为历史最高;而2#炉在风口调整后的炉缸侧壁温度一直稳定在750℃左右,没有再出现温度超常失控现象。
个人认为除了操作原因以外主要原因是2#炉比1#炉多三个φ115mm风口,更有利于高炉风口回旋区的延伸,能有效活跃炉缸中心,有利于炉缸侧壁温度有关。
高炉主要工艺参数计算公式_第三次讨论(10.13)

高炉主要工艺参数计算公式1、风口标准风速:V标=Q/(F*60)式中V标--风口标准风速,m/sQ――风量,m3/minF――风口送风总面积,m22、风口实际风速:V实= V标*(T+273)*0.1013/ (0.1013+P)*(273+20)式中V实--风口实际风速,m/sV标--风口标准风速,m/sT--风温,℃P--鼓风压力,MPa3、鼓风动能:E=0.412 * 1/n * O3/F2 * (T+273)2/(P+P0)2式中E--鼓风动能,j/sQ--风量,m3/minn--风口数目,个F--风口总截面积,m3T--热风温度,℃P--热风压力,MPaP0--标准大气压,等于101325PaV――炉缸煤气量,m3宝信疑问:O3是否就是Q3?Q:风量,m3/min;(是的)(动能公式按确认文件中宝信理解计算)V――炉缸煤气量,m3,公式中未使用;(不用)6、焦炭负荷:P=Q矿/Q焦式中P--焦炭负荷Q矿--矿石批重,kgQ焦--焦炭(干基)批重,kg7、综合负荷:P=Q矿/Q焦式中P--综合负荷Q矿--矿石批重,,kgQ综焦--综合干焦量批重(干焦量十其它各种燃料量×折合干焦系数批重,)kg宝信疑问:报表上的负荷采取焦炭负荷还是综合负荷;其中干基是否就是干焦(是的);(参照新发给你的报表)8、休风率: u=t/T×100%式中 u――休风率,%t ——高炉休风停产时间,minT——规定日历作业时间(日历时间减去计划达中休时间),min9、生铁合格率生铁合格率是指检验合格生铁占全部检验生铁的百分比。
其计算公式为:生铁合格率(%)= 生铁检验合格量(吨)×100%生铁检验总量(吨)生铁检验合格量是否同下面焦比中合格生铁产量一个概念(不是,生铁检验合格量不进行折算,而焦比中合格生铁产量要进行折算)或者说它们的关系如何计算说明:(1)高炉开工后,不论任何原因造成的出格生铁,均应参加生铁合格率指标的计算。
4高炉送风系统设计

6.3 高炉送风系统高炉送风系统是为高炉冶炼提供足够数量和高质量风的鼓风设施,送风系统的设备主要包括高炉鼓风机,热风炉,加湿或脱湿装置,送风管道和阀门等。
6.3.1 高炉鼓风机高炉鼓风机是高炉冶炼的重要动力设备。
它不仅直接为高炉冶炼提供所需的氧气,还为炉内煤气流的运动克服料柱阻力提供必需的动力,使高炉生产中各种气体循环流动。
高炉鼓风机是高炉的“心脏”。
6.3.1.1 高炉鼓风机技术要求(1) 有足够的送风系统能力,即不仅能提供高炉冶炼所需要的风量,而且鼓风机的出口压力要能够足以克服送风系统的阻力损失,高炉料柱阻力损失以保证有足够高的炉顶煤气压力。
(2) 风机的风量及风压要有较大宽的调节范围,即风机的风量和风压均应适应与炉况的顺行。
冶炼强度的提高与降低,喷吹燃料与富氧操作以及其他的多种因数变化的影响。
(3) 送风均匀而稳定,即风压变动时,风量不得自动的产生大幅度变化。
(4) 能够保证长时间连续,安全及高效率运行。
6.3.1.2 高炉鼓风机选择 (1) 鼓风机出口风量的计算鼓风机出口风量包括入炉风量、送风系统漏风量和热风炉换炉时的充风量之和。
计算时用标准状态下的风量表示。
1)高炉入炉风量的计算1440j u v Iq V q =式中: v q ——高炉入炉风量,min/m 3; u V ——高炉有效容积,3m ;I ——冶炼强度,d t/m3⋅,一般取综合冶炼强度,本设计为1.1; j q ——每吨干焦的耗风量,t /m3。
每吨干焦的耗风量与焦炭的灰分含量和风的湿度有关,焦炭灰分为12%时,每吨干焦的耗风量一般为2550t /m 3。
min /m 33.6233144025501.1320014403j u v =⨯⨯==Iq V q2)送风系统漏风量损失计算v o q ηq ⋅=式中 o q ——送风系统漏风量损失,min/m 3; η——漏风系数,正常情况,大型高炉为10%左右,中小型高炉为%15左右。
高炉风口的设计与调整

高炉风口的设计与调整1. 概述高炉风口是高炉冶炼过程中的关键组成部分,其主要功能是为高炉内注入新鲜空气,提供燃烧所需氧气,并促进炉料的下降和煤气上升本将详细介绍高炉风口的设计与调整方法2. 高炉风口的设计2.1 风口结构设计高炉风口主要由风口本体、风口套、风口芯和喷管等部件组成•风口本体:是风口的主体部分,通常采用铸铁或钢板焊接而成,具有良好的耐高温性能和足够的强度•风口套:安装在风口本体外部,通常采用耐火材料制成,以减少热损失和防止炉料进入•风口芯:位于风口套内部,用于引导气流和调节风量,通常采用耐高温、耐磨损的材料制成•喷管:连接风口芯和风口本体,用于引导气流和喷射炉料,通常采用耐高温、耐磨损的材料制成2.2 风口尺寸设计风口尺寸设计需要考虑高炉的直径、炉料的物理性质和冶炼要求等因素通常,风口直径和高炉直径的比例在 1:10-1:12 之间风口长度和风口套内径的比例通常在 1:1.5-1:2 之间2.3 风口材料选择风口材料需要具备耐高温、耐磨损、抗冲击等性能常用的风口材料包括铸铁、钢、铜和镍基合金等3. 高炉风口调整3.1 风口风量的调整风口风量的调整是高炉操作中常见的工作,可以通过调整风口芯的位置来控制风量风口芯的位置调整通常使用专门的机械装置完成3.2 风口角度的调整风口角度的调整可以影响高炉内的煤气流动和炉料下降通常,风口角度的调整使用专门的机械装置完成3.3 风口形状的调整风口形状的调整可以改善高炉内的煤气流动和炉料下降通常,风口形状的调整使用专门的机械装置完成4. 结论高炉风口的设计与调整是高炉冶炼过程中的关键环节正确的设计和调整可以提高高炉的冶炼效率和煤气利用率,降低能耗和提高产量高炉风口的设计需要考虑风口结构、尺寸和材料等因素高炉风口的调整主要包括风量的调整、角度的调整和形状的调整高炉风口的设计与维护1. 背景高炉作为现代钢铁工业的基础设备,其风口部分的作用至关重要风口不仅是高炉供氧的关键部位,同时也是影响煤气流分布和炉料下降速度的重要因素因此,高炉风口的设计与维护对于保障高炉高效、稳定运行具有重要意义2. 高炉风口的设计原则高炉风口设计应遵循以下原则:•合理的风口面积:风口面积需要与高炉的冶炼能力和煤气流量相匹配,以确保足够的氧气供应和适宜的煤气流速•材料选择:风口材料需要具备耐高温、耐腐蚀、耐磨损的特性,以适应高炉内部恶劣的环境•结构优化:风口的结构设计应简洁、合理,便于制造、安装和维护•热交换效率:风口应具有良好的热交换性能,以减少热量损失,提高能量利用效率3. 高炉风口的主要参数高炉风口的主要设计参数包括:•风口直径:风口直径根据高炉的大小和设计风量确定,通常与高炉炉膛直径成一定比例关系•风口长度:风口长度应确保煤气流有足够的长度进行热交换,同时也要考虑安装和维护的便利性•风口倾斜角度:风口倾斜角度影响煤气流的分布和炉料的下降速度,通常通过模拟和实验确定最佳角度•风口材料的热膨胀系数:材料的热膨胀系数应与高炉炉体材料相匹配,以减少由于温度变化引起的热应力4. 高炉风口的设计要点高炉风口的设计要点包括:•风口本体的结构设计:风口本体应采用模块化设计,便于更换和维护•风口套的结构与材料:风口套需要具有良好的密封性能,以防止炉料进入和煤气泄漏•风口芯的设计:风口芯是调节风量的关键部件,其设计应确保风量调节的准确性和稳定性•喷管的设计:喷管应具有良好的气流分布性能,以提高煤气流的动能和热交换效率5. 高炉风口的维护与管理高炉风口的维护与管理对于保证高炉长期稳定运行至关重要主要包括:•日常检查:定期检查风口是否有损坏、变形或磨损,及时发现并处理问题•清洁维护:定期清理风口积灰和堵塞物,保持风口的通畅•调整与校准:根据高炉的运行状态,调整风口的风量和角度,以优化煤气流分布和提高冶炼效率•材料更换:当风口材料磨损到一定程度时,应及时更换,以避免安全隐患6. 结论高炉风口的设计与维护是高炉生产中不可或缺的一环通过合理的设计和精心的维护,可以确保高炉的风量供应稳定,煤气流分布合理,从而提高高炉的冶炼效率和生产稳定性高炉风口的设计应遵循合理的原则,考虑主要参数和设计要点,而维护与管理则需要注重日常检查、清洁维护、调整校准和材料更换等方面只有这样,才能保证高炉安全、高效、稳定地运行应用场合高炉风口的设计与维护主要应用于以下场合:1.高炉生产运行:在钢铁冶炼行业中,高炉是生产铁水的基础设备,风口作为高炉的关键组成部分,直接关系到高炉的生产效率和稳定性2.热风炉操作:热风炉是高炉冶炼过程中提供热源的重要设备,风口的设计与维护同样适用于热风炉的操作3.冶炼实验与研究:在钢铁冶炼的科研和实验中,风口的设计参数和维护方法对于实验结果有着直接的影响4.冶金工程设计与施工:在冶金工程的设计和施工过程中,风口的设计和选型是必不可少的环节5.高炉维修与改造:在高炉的维修和改造过程中,对风口进行检查、调整和更换是确保高炉正常运行的关键步骤注意事项在高炉风口的设计与维护过程中,需要注意以下事项:1.风口设计的专业性:风口的设计需要由专业工程师进行,确保设计参数和结构符合实际生产需求2.材料选择的合理性:根据高炉的冶炼条件和环境,选择合适的风口材料,保证风口的使用寿命和性能3.结构与尺寸的精确性:风口的结构和尺寸应精确制造和安装,以确保其正常工作和避免因偏差导致的故障4.维护的及时性:定期对风口进行检查和维护,及时发现和处理问题,避免因忽视维护导致的风口故障5.操作的安全性:在风口的设计、维护和操作过程中,要严格遵守安全规程,确保人员安全和设备完好6.调整的合理性:根据高炉的运行状态和冶炼要求,合理调整风口的风量和角度,以优化煤气流分布和提高冶炼效率7.环境的适应性:风口的设计和维护应考虑高炉所在环境的特殊性,如温度、湿度、灰尘等因素,确保风口能够适应恶劣环境8.节能与环保:在风口的设计和维护中,要充分考虑节能减排和环保要求,采用高效、低能耗的风口结构和材料9.记录与反馈:在风口的设计、维护和操作过程中,要详细记录相关数据和问题,及时进行反馈和分析,不断优化风口的设计和维护方法10.培训与交流:对高炉操作人员和相关工程师进行风口设计与维护的培训,加强行业内的交流与合作,提高整个行业的高炉操作水平通过以上注意事项的遵循,可以确保高炉风口的设计与维护工作顺利进行,提高高炉的生产效率和稳定性,同时保障人员和设备的安全。
高炉风口小套技术标准

高炉风口小套技术标准1 风口小套性能要求:1.1机械性能:抗拉强度δ≥180Mpa 延伸率δb≥30% 硬度H≥40 电导率≥85%IACS。
1.2化学成份:Cu≥ 99.9%。
1.3风口小套铜铜焊接,焊缝要求改进,图纸供需双方签字认可。
焊接要求采用氩弧保护焊,要求焊缝强度不低于母材,焊后应保温处理,焊接风口应保证焊缝平滑过渡,焊接后并对焊缝进行100%着色或探伤检验。
达到ASTME272-75标准中所规定的2-3级为合格。
1.4 耐压试验:产品制造完成均需进行耐压(水压或气密性)试验。
1.4.1 风口小套水压试验(清水)压力2.0Mpa,保压30分钟,并用橡胶锤轻击小套,以不冒汗、不漏水、无异常现象为合格。
1.4.2 风口小套气密性试验,压力1.8Mpa的压缩空气试验时在小套整个表面上涂以肥皂水,并用橡胶锤轻击,保压30分钟,并以不泄漏为合格。
1.5冷却通道阻力损失:1.5.1 高炉风口水压工作压力在 1.6Mpa时,风口小套水流量应38—40m3/h,且风口流量要稳定,该工作状态下风口通道(从进口到出口)阻力损失在≤0.5Mpa为合格。
1.5.2 要求每个风口的水流量一定要均匀、稳定、近似相等。
1.6 风口小套内壁前端堆焊耐磨合金,堆焊层不宜过高,高度为2-3mm。
1.7风口堆焊的耐磨层要保证使用质量,不能有和风口剥离和和脱落现象,要保证每个风口所焊接的耐磨材料在使用中的完好性。
2 随机资料交接:2.1每件风口小套超声波探伤合格证二份。
2.2每件风口耐压(水压或气密性)试验报告二份。
2.3每件风口的流量报告书二份。
2.4每件产品的合格证一份。
2.5本批次风口所用铜原料的材质分析报告(铜板需提供原供货厂家的分析报告)。
2.6风口的化学成分应逐炉检验,并做出保证铜纯度的报告。
2.7每件风口随机配件:2.7.1配套压紧法兰2件。
2.7.2配套双头丝压紧螺栓4条。
2.7.3风口进、退水口配套密封环垫圈。
风口尺寸对高炉操作影响的研究

© 1994-2009 China Academic Journal Electronic Publishing House. All rights reserved.
·20 ·
钢 铁
第 43 卷
图 2 5 号风口面积调整后各风口速度 Fig. 2 Blast velocity at each tuyere with
了探讨 。
叙述 ,请参阅文献[ 1 ] 。模型边界条件如下 :
1 物理和数学模型
(1) 热风总管入口给定速度 ,根据热风总流量 和尺寸求得该速度为 30 m/ s ,炉缸上部出口给定压
1. 1 物理模型
力 0. 3 M Pa ;
图 1 所示为炉容为1 200 m3 的高炉送风系统模
(2) 对称面上满足法向物理量梯度为零 ;
面积成正比了 ,如图 3 所示 ,3 种情况 5 号风口的风
量依次增大 。因此 ,当总送风量不变时 ,减小一个或
几个风口的直径会使各个风口的速度都增大 ,且增
大到相同值 ,但直径减小了的风口流量会变小 ,即调
整风口直径是对风口流量的重新分配 ,而不是对速
度的重新分配 。
上述现象可以解释如下 :假设炉缸上部出口压
风围管看作一个热风分配器 ,把一股大流分成多股 小流后分别进入大容器 。由于该送风模型具有对称
2 计算结果和讨论
性 ,故取一半作为研究对象 。为方便叙述 ,给各个风 2. 1 风口尺寸一致时的供风特性
口编号 ,以离围管入口最近处的风口为 1 号 ,对面风
为了比较改变风口尺寸后各风口的供风特性 ,
口为 9 号 ,依次编号 ,与之相对称的风口编号分别为 如各风口的流量 、速度和鼓风动能的变化 ,有必要给
高炉风口理论燃烧温度(Tf)分析(改)

高炉风口理论燃烧温度(Tf)分析李肇毅(宝山钢铁股份有限公司炼铁厂,上海201900)摘要:通过对高炉风口前理论燃烧温度(Tf)的剖析,建立与理论分析相对应的经验多项式。
通过检验发现目前各厂广泛使用的Tf经验公式偏离较多。
本文还把Tf值与煤质挂钩,使其更为实用。
关键词:高炉,理论燃烧温度,Tf,煤质Analysis of flame temperature in the front of tuyeres for blast furnaceLi Zhaoyi(Ironmaking branch, Baoshan Iron &Steel Co., Ltd., Shanghai 201900,China)Abstract: By analysis of flame temperature in the front of tuyeres for blast furnace, a multi-item equation of experience have be set up according to theoretical analysis. A gap is checked out for Tf experiential formula of many plant using. Relation is made between Tf and coal quality for better practicality.Key words: blast furnace, flame temperature, Tf, coal quality风口前理论燃烧温度(简称Tf)是高炉炼铁工作者普遍关注的炉缸工作参数。
它存在一个较宽的适宜范围。
但当高炉的鼓风参数有大幅度调整时(如大幅度提高喷煤,或高富氧),必须对Tf值有一个正确估计,以避免由此而引起炉况失常[1]。
1 各国高炉对Tf值的控制表1 各国Tf的取值2 Tf经验式a. 加拿大钢铁公司Y=1111.1-21.06BH+0.7287BT-13.348OIL+82.393O2, F ----(1) BH----鼓风湿分(格令/英尺3)BT----热风温度(F)OIL----喷油(美加仑/时1000英尺3干风)O2----含氧%(干风体积的%,如空气=21)b. 澳大利亚BHP公司Tf=1570+0.808BT-5.85BH +4370O2-4400OIL, ℃----(2)c. 日本君津厂Tf=1559+0.839BT-6.033BH +4972O2-4972OIL, ℃----(3)d. 宝钢Tf=1559+0.839BT-6.033BH +4972O2-3250COAL, ℃----(4) BT----热风温度(℃)BH----鼓风湿分(g/m3)O2----富氧量(m3/m3风)OIL----喷油(kg/m3风)COAL----喷煤(kg/m3风)宝钢公式是在君津公式的基础上对喷吹项作修改而得(当初修改主要考虑煤与油的发热值差异,按比例折成现有的参数)。
1泰钢450m高炉参数

泰钢450m³高炉运行参数
一、高炉操作制度
1、送风制度
风口配置(16个)全部使用直径105㎜风口,斜7°,长度为360、380㎜,送风面积为0.1385㎡。
正常生产时风温1080℃,风压控制245~250kpa,表显风量1680m³/min,富氧4500 m³/h。
2、装料制度
泰钢高炉使用大矿批操作,现矿批为21300kg/批,焦批5000 kg/批(焦炭水分6%)。
料线均为1.3m,布料角度见下表:
3、渣、铁成分控制
生铁[Si]0.5%,[S]保二类,炉渣R2控制1.1,渣中MgO含量控制11%~11.5%,Al2O3在16~17%。
二、原、燃料情况
泰钢入炉料综合品位为57.5%,当日配比为:纽曼块矿14%、球团18%、烧结68%。
烧结矿品位55%,R2控制1.85,MgO控制2.7%,Al2O3含量达2.6%,高炉配加菱镁石。
焦炭为自产湿熄焦,灰分12.5~13%,含硫量为0.7~0.8%,槽下焦炭振筛为12㎜棒条筛。
喷吹
用煤为全无烟煤。
从槽下目测烧结状况,烧结粒度整体偏小,色泽呈青蓝色,焦炭粒度及外观与东阿焦炭相仿。
三、经济技术指标情况
泰钢高炉平均日产1750~1850吨铁,煤比控制170 kg/t铁,入炉焦比350 kg/t铁,综合焦比485~490 kg/t铁,其实际炉容接近500m³。
浅析高炉风口布局的选择原则

浅析高炉风口布局的选择原则作者:smoke一前言炼铁人都知道高炉操作:“以风为纲,有风就有铁”。
高炉如人,风对于高炉来说就好比人的呼吸。
气顺,则身体健康,活力四溢,气阻,则百病惭生,精神萎靡.所以正确调整高炉入炉风量参数,是保证高炉高产,优质,低耗,长寿的关健,而决定高炉风量参数的除风机能力之外,起决定作用的无非就是对风口参数的选择及风口布局的选择,某种意义上讲,除原燃料条件外,风口参数的选择及风口的布局对高炉顺行及各项指标起着至关重要的作用。
二风速与鼓风动能风口面积的定位和风口的合理布局决定着初始煤气流的分布。
高炉的顺行讲究的是“上稳下活”,即上部要通过装料制度的调剂使气流趋于稳定;下部说的就是风口,风口带要保证有足够的回旋区,每个风口前应保持有足够的鼓风动能以利于煤气流的穿透和活跃炉缸。
风口面积的大小主要取决于高炉的风机能力和原燃料条件。
谚语说,“大风治百病”。
原则上要将风机的风用尽,发挥出风机的最大能力。
然后根据原燃料条件确定合适的冶炼强度,原燃料条件好时可适当提高冶强,原燃料差时要适当控制冶强,此时要着重考虑风速和鼓风动能的因素。
下面给出风速(V)和鼓风动能(E)的计算公式:V标=Q/S;V实=V标*(T+273)/T*1.033/(P+1.033)E=1/2*Q*1.293/(n*9.8)*V2实V,风速,单位m/s;Q,风量,单位m3/s;S,风口总面积,单位m2;T,风温,单位℃;P,风压,单位kg/m2;E,鼓风动能,单位KJ;n,风口个数。
风口回旋区前端距风口水平距离(DR)计算公式:DR=DT*0.409*pf0.693DT,风口直径;pf,穿透因子。
pf=ρ0/(ρs*Dp)* V标2*T/(P*298)ρ0,炉腹煤气密度;ρs,焦炭粒子密度;Dp,风口焦平均粒度;T,回旋区煤气温度。
由此可见,除焦碳质量因素外,风速在一定意义上代表着风的穿透能力,足够的风速为风口回旋区提供了保证,也是保证足够鼓风动能的必要参数。
合理调整高炉风口参数的数学模型及措施

合理调整高炉风口参数的数学模型及措施
合理调整高炉风口参数的数学模型及措施
2015-09-07 14:04:00
高炉的下部调节是高炉调剂的重要组成部分,为了维持合理的炉缸工作状态,调节风口尺寸是经常采取的方法,最常用的手段是调节风口长度和风口直径。
更换风口至少需要几十分钟的休风时间,影响高炉的稳定、顺行及后续钢铁生产工序。
当前,如何调整风口长度和风口面积来实现活跃炉缸中心,还没有统一的数学模型作为指导。
合理调整风口对大型高炉吹透中心、活跃炉缸十分重要。
目前,实际操作常常认为增加风口长度、增加风口回旋区深度、缩小风口面积能提高风速,进而提高鼓风动能,以利于吹透中心。
北京科技大学的学者建立了调整风口参数的数学模型,并以某厂3200m3高炉为例,给出了在总风量不变的条件下,增加1个风口长度、减小1个风口面积以及多个风口尺寸调整时,各风口风量、风速和鼓风动能的变化。
发现增加部分风口的长度时,对应风口风量、风速、鼓风动能降低。
缩小少数风口的面积,会降低对应风口的风量;只有在缩小多数风口的面积时,已调整的风口风速和鼓风动能才可能提高,而未调整的风口风量、风速和鼓风动能提高幅度更大。
根据该数学模型,定量化给出该高炉调整风口的相关参数,可用于调整炉缸煤气流的均匀性,维持高炉稳定、顺行。
高炉炼铁中风口布置优化对冶炼效率的影响分析

高炉炼铁中风口布置优化对冶炼效率的影响
分析
1. 引言
高炉炼铁是重要的铁矿石冶炼技术之一,风口布置是炼焦煤与矿石
冶炼过程中重要的环节。
合理的风口布置能够优化高炉冶炼过程,提
高冶炼效率。
本文将对高炉炼铁中风口布置优化对冶炼效率的影响进
行分析。
2. 高炉炼铁的基本过程
(这里可以概述高炉炼铁的基本过程,如逐步还原、熔化等)
3. 风口布置的作用
3.1. 风口布置的基本原理
(这里可以阐述风口布置的目的,如提供足够的氧气、保证良好的
热传导等)
3.2. 风口布置的要求
(这里可以介绍风口布置的要求,如风口布置均匀、数量适当等)
4. 风口布置优化对冶炼效率的影响
4.1. 合理布置风口提高冶炼效率的机制
(这里可以介绍合理风口布置如何提高冶炼效率,如增加燃烧温度、增加产量等)
4.2. 风口布置不当对冶炼效率的影响
(这里可以讨论风口布置不当可能引发的问题,如燃烧不完全、堵塞、产量下降等)
5. 风口布置优化的研究进展
5.1. 风口布置优化的方法
(这里可以介绍目前用于风口布置优化的方法,如数值模拟、实验研究等)
5.2. 风口布置优化的案例研究
(这里可以列举一些相关研究,说明风口布置优化对冶炼效率的实际影响)
6. 结论
本文通过分析高炉炼铁中风口布置优化对冶炼效率的影响,认识到了风口布置对高炉冶炼效率的重要性。
合理布置风口能够提高冶炼效率,增加产量,同时避免了风口布置不当引发的问题。
未来,可以进一步深入研究风口布置优化方法,提高高炉炼铁的效率和质量。
(以上内容仅供参考,根据实际需求和具体要求进行适当修改。
)。
高炉主要实用工艺全参数计算公式_第三次讨论(10.13)
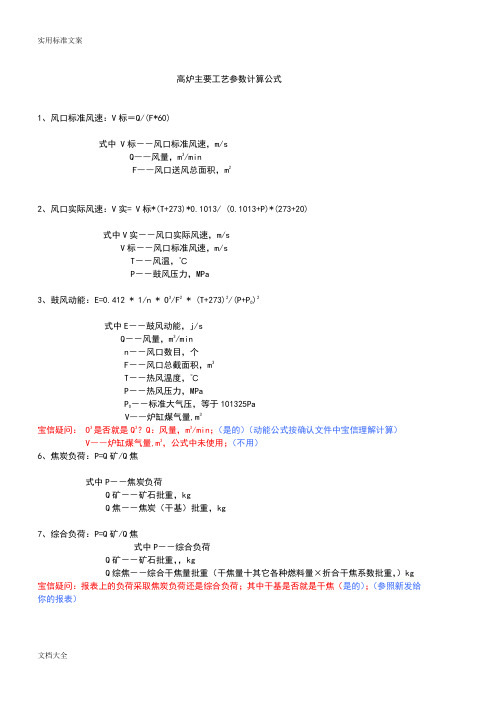
高炉主要工艺参数计算公式1、风口标准风速:V标=Q/(F*60)式中 V标--风口标准风速,m/sQ――风量,m3/minF――风口送风总面积,m22、风口实际风速:V实= V标*(T+273)*0.1013/ (0.1013+P)*(273+20)式中V实--风口实际风速,m/sV标--风口标准风速,m/sT--风温,℃P--鼓风压力,MPa3、鼓风动能:E=0.412 * 1/n * O3/F2 * (T+273)2/(P+P0)2式中E--鼓风动能,j/sQ--风量,m3/minn--风口数目,个F--风口总截面积,m3T--热风温度,℃P--热风压力,MPaP0--标准大气压,等于101325PaV――炉缸煤气量,m3宝信疑问: O3是否就是Q3?Q:风量,m3/min;(是的)(动能公式按确认文件中宝信理解计算)V――炉缸煤气量,m3,公式中未使用;(不用)6、焦炭负荷:P=Q矿/Q焦式中P--焦炭负荷Q矿--矿石批重,kgQ焦--焦炭(干基)批重,kg7、综合负荷:P=Q矿/Q焦式中P--综合负荷Q矿--矿石批重,,kgQ综焦--综合干焦量批重(干焦量十其它各种燃料量×折合干焦系数批重,)kg 宝信疑问:报表上的负荷采取焦炭负荷还是综合负荷;其中干基是否就是干焦(是的);(参照新发给你的报表)8、休风率: u=t/T×100%式中 u――休风率,%t ——高炉休风停产时间,minT——规定日历作业时间(日历时间减去计划达中休时间),min9、生铁合格率生铁合格率是指检验合格生铁占全部检验生铁的百分比。
其计算公式为:生铁合格率(%) = 生铁检验合格量(吨)×100%生铁检验总量(吨)生铁检验合格量是否同下面焦比中合格生铁产量一个概念???(不是,生铁检验合格量不进行折算,而焦比中合格生铁产量要进行折算)或者说它们的关系如何???计算说明:(1)高炉开工后,不论任何原因造成的出格生铁,均应参加生铁合格率指标的计算。
高炉炼铁中的风口设计与炉渣排出控制

定期检查风口的密封情况, 确保风口的密封性能
定期检查风口的冷却系统, 确保冷却效果良好
炉渣是炼铁过程 中的副产品,其 成分和性质对炼 铁过程有重要影 响
炉渣的化学成分 会影响铁水的质 量和产量
炉渣的物理性质 会影响炉渣的排 出和回收利用
炉渣的排出控制 对高炉炼铁的效 率和环境保护有 重要影响
考虑风口的形 状和材质
考虑风口的维 护和更换成本
耐高温性:能够承受高炉炼铁的高 温环境
耐腐蚀性:能够抵抗炉渣中的酸性 物质和碱性物质的腐蚀
添加标题
添加标题
添加标题
添加标题
耐磨性:能够承受炉渣的冲刷和磨 损
导热性:具有良好的导热性能,能 够快速传递热量,提高炼铁效率
风口位置:根据高炉形状和尺寸,合理 布置风口位置
协同优化方案 的设计原则
协同优化方案 的具体实施步
骤
协同优化方案 在实际应用中
的效果评估
协同优化方案 的改进与优化
方向
提高生产效率:协同 优化可以提高高炉炼 铁的效率,降低生产
成本。
技术挑战:协同优化 需要复杂的计算和优 化算法,技术难度较
大。
减少环境污染:协同 优化可以减少炉渣排 出,降低对环境的污
实践案例:某钢铁公司炉渣排出 控制的改进实践
效果分析:改进前后炉渣排出效 果的对比分析
自动化控制技术的应 用:实现炉渣排出的 自动化控制,提高生
产效率和稳定性
节能技术的应用:采用节 能技术,降低炉渣排出过
程中的能耗
环保技术的应用:采用环 保技术,减少炉渣排出对
环境的影响
智能化技术的应用:利用 智能化技术,实现炉渣排
浅议鼓风动能与风口布局

摘 要 就鼓风动能的计算公式展开讨论,重点描述鼓风动能在高炉不同位置风口间的变化以及不同尺寸风口对鼓风动能的影响,从而给失败的调节寻找原因,并给风口调节提供另一种思路。
关键词 风口;调节;鼓风;动能;动量前言高炉在实际生产中,难免由于设备、施工、气流分布、炉体冷却、风口布局等原因造成炉型不规则,严重时形成偏行,影响煤气利用,破坏生产指标,甚至引起恶性炉况。
而且,和完美的人一样,完美的高炉几乎也是不存在的,难免存在某个方面的缺憾。
所以,高炉工作者就要在生产中针对不同情况利用不同的手段进行调节,不外乎严格监督施工、精确安装设备、密切控制炉体冷却、保持合理煤气流分布。
而煤气流的分布调节起来十分困难,原因就是影响煤气流分布的因素多,比如风口布局、软融带位置形状、炉墙形状、上部布料及炉料性能、操作方针等,而且煤气在炉内进行三次分布,各个环节都有可能影响到煤气的最终利用情况,进而影响操作技术经济指标甚至影响到基本顺行。
煤气初始分布的调节其实也就是对回旋区进行合理控制。
回旋区是高炉稳定操作的重要反应区,其形状对高炉生产影响很大,是化学能和热能的主要来源地。
回旋区的形状和尺寸大小将直接影响高炉下部煤气的分布、上部炉料的均衡下降以及整个高炉内的传热传质过程。
在高炉操作调节中,下部调节就是通过调节回旋区的形状和大小分布来控制炉况的,向来是其他调节手段的基础。
以下部调节为基础,上中下部调节相结合是基本的调节原则。
风口调节就是一项根本的调节方法,通过调节风口在高炉不同位置的不同尺寸来控制煤气流的初始分布在生产中经常用到。
但是,调整的效果怎么样?各个高炉调节的方法不同,幅度不同,效果也就不言而喻。
风口调节与风口鼓风有着直接的关系,通过理论和实践寻找这一关系并运用之,是我们最关心的。
1 鼓风动能与鼓风动量的概念我们的技术书籍上给出了一个鼓风动能的经典公式[2],如下: E=21mv 2=21×8.9293.1×n Q (nA Q ×273273t ×P101.0) J/s 式中:E--------鼓风动能, J/s ;m ------ 鼓风质量,Kg ;v ------ 风速,m/s ;Q ------ 风量,Nm 3/s ;n--------风口个数,个;A--------1个风口的面积,m 2t--------鼓风温度,℃P--------鼓风工作压力,MPa1.293----鼓风密度,Kg/m 3我们且不说这个公式的正确与否,只看单位就可以看出,计算出来的不是能量,而是动量。
第五章 高炉送风系统设计

A点:夏季、高压操作、 最高冶炼强度工作点;
B点:夏季、常压操作、 最高冶炼强度工作点; C点:冬季、常压操作、 最低冶炼强度工作点;
D点:冬季、高压操作、 最低冶炼强度工作点。
高压高炉鼓风机工况区示意图
5.1.4 风机的并联与串联
一. 风机并联:
是把两台鼓风机的出口管道,顺 着风的流动方向合并成一条管道送往 高炉。
1. 工作原理: 靠装有许多叶片的工作叶轮旋转 所产生的离心力,使空气达到一定的 风量和风压。
2 结构示意图:
四级离心式鼓风机
1-机壳;2-进气口;3-工作叶轮;4-扩散器;5-固定导向叶片;6-排气口
3. 特性曲线:在一定的吸气条件下,风机的风
量与风压的关系曲线 。
K-4250-41-1型离心式鼓风机特性曲线
5 送风系统
高炉送风系统包括 :
鼓风机、冷风管道、热风炉、热风管路以 及管路上的各种阀门等
5.1 高炉鼓风机
1400M3/tFe水;富氧1300M3风; 1M3炉容2.5~3.5M3风/min
①通风机<0.1MPa鼓出压,主要控 制风量Q,抽烟机; 鼓风机 0.1MPa<鼓<0.4MPa,既 要用P又要用风;
2560 47250 10000 4.72
二 工作原理
燃烧室和蓄热室砌在同一炉壳内,之间用隔墙隔 开。煤气和空气由管道经阀门送入燃烧器并在燃 烧室内燃烧,燃烧的热烟气向上运动经过拱顶时 改变方向,再向下穿过蓄热室,然后进入大烟道 经烟囱排入大气。在热烟气穿过蓄热室时,将蓄 热室内的格子砖加热。格子砖被加热并蓄存一定 热量后,热风炉停止燃烧,转入送风。送风时冷 风从下部冷风管道经冷风阀进入蓄热室,空气通 过格子砖时被加热,经拱顶进入燃烧室,再经热 风出口、热风阀、热风总管送至高炉。
- 1、下载文档前请自行甄别文档内容的完整性,平台不提供额外的编辑、内容补充、找答案等附加服务。
- 2、"仅部分预览"的文档,不可在线预览部分如存在完整性等问题,可反馈申请退款(可完整预览的文档不适用该条件!)。
- 3、如文档侵犯您的权益,请联系客服反馈,我们会尽快为您处理(人工客服工作时间:9:00-18:30)。
高炉风口参数的设计探讨郭俊奎马铁林摘要风口是高炉送风系统的重要设备之一,通过对高炉风口参数进行分析、论述、探讨,阐述了风口数目,风口高度,风口角度、长度,风口直径对高炉冶炼操作、生产技术经济指标的影响,并从设计角度提出了风口参数的设计、计算参考数据和建议。
关键词高炉风口参数设计探讨0 前言高炉炼铁是一个综合的工艺过程,每一项工艺参数设计对高炉生产都有不同程度的影响,高炉风口是炼铁高炉重要的送风设备之一,有高炉炼铁生产工艺以来就存在风口,高炉鼓风、喷吹的燃料都是通过风口进入高炉内的。
风口参数主要包括风口数量、高度、直径、角度和长度等数据,风口参数对其本身寿命及炼铁高炉生产技术经济指标有重要影响,是高炉下部调剂的重要手段之一。
本文结合节能减排、降低能耗及新工艺的需要,更重要的是通过工业实践,对风口参数进行分析总结、论述探讨,提出了自己的看法,并从设计角度提出了风口参数的设计、计算参考数据和建议,希望使风口参数更加科学合理,做好风口参数设计,从而进一步提高炼铁生产技术经济指标。
1 风口数目的确定高炉风口数目是高炉工艺设计的重要参数之一,主要取决于炉缸直径大小和鼓风机能力,高炉风口数目增多目前是一种趋势,增加风口数目有利于高炉的强化冶炼。
风口数目在满足炼铁工艺要求的同时,还应符合风口的安装尺寸和结构要求。
风口数目的计算有多种方法,但还没有严格的理论计算公式,一般按经验公式粗略计算后确定。
设计手册要求风口弧长间距在1200mm~1400mm,国内曾采用如下公式[1]:f=2d+1式中:f—风口数目,个;d—炉缸直径,m。
式中计算出来的风口数目较少。
国外一般采用如下公式[1]:f=πd/(1.0~1.2)或f=3d风口数目一般为双数。
高炉风口数目的合理设计与高炉操作、技术指标有很大关系。
风口数目增多,风口弧长间距就小,高炉圆周进风相对均匀,可改善煤气流、温度分布,减少风口之间的“死料区”,炉缸燃烧均匀,可活跃炉缸,利于炉况顺行,有节焦、增产等作用,更有利于节能减排。
中小高炉其效果十分明显,大高炉次之。
通过某140m3级高炉工业试验,风口由8个改为10个,和同等条件高炉相比,可提高日产量80 t~100 t,降低焦比10~15 kg/t.Fe。
高炉炉缸8个风口时,风口中心线水平间夹角为45°,高炉改为10个风口时风口中心线水平夹角为36°,两者相差9°,也就是说8个风口时,相当于高炉炉缸内圆周72°(9°×8)范围内“无风口”,极大影响了炉缸的工作制度,对高炉技术经济指标影响较大。
上述试验表明,增加风口数目,炉缸燃料燃烧相对均匀、有效,有利于炉内煤气流的初始分布、温度分布、热量分布,可以活跃炉缸,利于炉况顺行,降低能耗,提高产量,有利于提高高炉的技术经济指标和经济效益,是节能减排的重要手段之一。
风口数目的增加,必须与风量、风压及风口直径等参数紧密配合,才能体现出增加风口数目的意义所在,否则,也会带来负面影响,达不到预期效果,反而影响高炉的强化冶炼。
笔者建议风口数目的确定应以炉缸风口之间的弧长间距为依据,以缩小风口弧长距离为原则,确定风口数目。
建议风口弧长距离控制在1000 mm~1100 mm,不超过1200 mm。
2 风口高度计算和风口角度铁口中心线至风口中心线的垂直高度距离称为风口高度(H f)。
风口与渣口的高度差应能保障容纳上渣量和一定的燃烧空间,风口高度计算公式如下[2]:H f = H z / k式中:H z 为渣口高度k为渣口高度与风口高度之比,一般k=0.5~0.6,渣量大取低值。
从上式可以看出,风口高度与渣口高度有一定关系,而随着原燃料条件的改善,精料水平的提高,渣量减少是趋势,因此,可以认为风口高度也应是趋于减小,而现在设计中,风口高度的确定更多是参阅、类比同级高炉。
我们通过对高炉风口高度数据的数理统计、实践,通过控制适当的高径比,趋于矮胖的炉型,使用平风口时,风口高度与高炉有效高度的比值约为1/8.76。
这一数据对中小高炉风口高度设计有一定的指导意义,而且通过实践,取得了比较好的技术经济指标。
但此值有待在大高炉上实践、验证。
某1750 m3高炉生产指标不是太好,其风口高度为3700 mm,通过分析探讨,笔者认为此高炉的风口高度宜在3200 mm左右,现在高了约500 mm,对生产指标有影响。
当然还有其它综合性因素的影响。
风口高度的大小与高炉内直接还原、间接还原的程度,以及高炉炉内直接还原区、间接还原区大小有很大关系,似是一个“分界线”,对炉内燃料的热能和化学能利用有影响。
此值不合理,高炉不会有好的生产指标,易引起炉内事故,炉况不顺,焦比升高,不利于节能降耗。
高炉是非标准设备,风口高度对高炉内直接还原和间接还原有影响,对高炉生产、节焦、增产十分重要。
同时也应认识到大中小高炉的风口高度在高炉内的“适应性”是有区别的。
实践表明,小高炉的炉缸直径小,风口相对也少,风口高度对高炉炉况的影响十分明显,只要相差正负75mm,就对生产影响极大。
大高炉,特别是特大型高炉,风口数目多,距高炉中心相对远,风口燃烧的放射性鼓风作用等引起的风口高度“适应性”相对小高炉要强,也就是说特大型高炉的风口高度调整余地大,对高炉生产影响相对小,这也是大型高炉目前的风口高度差别大,也能适应高炉生产变化的一个重要原因。
但是,大高炉、特大型高炉也应该有个最佳值,对生产才最有利。
风口角度是指风口中心线向下倾斜的角度,是调节高炉生产的手段之一。
只要有角度,鼓风动能利用相对就差,直观分析就是三角形直角边与斜边的关系。
风口有角度,风口距离高炉中心就远,不利于吹透中心。
风口高度与风口角度有相辅相成的关系,两者应紧密配合,高炉生产才会有好的技术指标。
一般建议选零度平风口,不要有角度。
笔者认为,不研究风口高度而研究风口角度意义不大。
3 风口直径和长度3.1 风口直径风口直径一般是指风口小套的内直径,表示高炉鼓风进入高炉时进风面积的大小。
风口直径由风口的出口风速确定,一般风口的出口标态风速在100 m/s以上[2],巨型高炉有的高达200 m/s。
风口直径的计算有一些参考公式,主要是要保证风口的鼓风动能,可以作为一个重要的参考数据。
推荐的风口面积计算公式为[3]:S=1.803×10-4×(273+t)×(γV b3)-2÷((101.325+P b)×(n3E)-2)式中:S——风口面积,m2/个;E——鼓风动能,(kg·m)/s;t——热风温度,℃;P b——热风压力,kPa;γ——气体密度,kg/m³;V b——风量,m3/min;n——工作风口数目。
当喷吹燃料时,V混(换成m3/min)代替V b,用t混代替t即可。
风口直径的计算涉及变量参数比较多,特别是有的参数是瞬间变化的,要取值计算准确比较难。
每座高炉有其各自的生产特点和规律,也是随时在变化的,而不是一个固定的值。
计算值只是一个相对参考值,必须通过生产实践使用检验,应该以满足高炉生产操作工艺要求、炉况顺行、效益最大为原则。
改变风口面积大小是高炉操作下部调剂的重要手段之一,是对各风口流量的重新分配,从而影响风口回旋区的形状、大小,影响气流和温度的分布以及炉缸的均匀、活跃程度。
当高炉炉缸煤气流分布不合理、炉缸工作不活跃时,有必要改变风口直径,调节各风口的进风压力、流量,使整个全炉缸内的燃烧、温度、煤气流分布尽可能均匀、合理,达到调节炉况顺行的目的。
有人建议高炉铁口两侧的二个风口直径应小2 mm~3 mm,这个观点直观分析可行,但有待于生产操作实践的检验、证实。
在一定的冶炼条件下,高炉都有其适宜的操作制度与冶炼强度,风口直径一般不宜经常变动。
3.2 风口长度风口长度有两个概念,一是风口小套的加工成品长度,二是风口小套伸入炉缸内的长度。
我们探讨风口长度是指风口小套伸进炉缸内的长度。
设计手册要求风口小套前端伸进炉缸20 mm~50 mm,但笔者分析认为,在保证风压的前提下,风口小套不应该伸进炉缸内,超出炉墙,反而应缩回炉墙内。
原因如下:1)缩回炉墙内60 mm左右,与伸进炉缸30 mm~50 mm相差约100 mm,对风口本身没有任何影响,但相当于“炉缸直径”大了约200 mm,这对提高产量,促进燃烧,活跃炉缸有益,但必须有风压做保证。
2)风口小套全部或部分裸露在炉缸内,引起多种弊病:铁水滴落冲刷风口小套,小套损坏风险增加;风口小套后端和炉墙之间形成一个“回旋区”,对风口套极为不利;冷却水压力低时,易损坏,休风率高,备件消耗高;而风口小套缩回炉墙内,可有效解决上述问题。
3) 风口位于炉缸上部,直接与渣、铁、高温气流接触,工作条件十分恶劣。
风口烧损的部位,多为风口伸入炉内部分的前端上缘和下缘。
由于其与渣、铁接触,局部区域的热流强度超过了风口材质所能承受的临界热流强度,产生过热而被熔化所致[4]。
高炉炉墙冲涮、侵蚀是必然的,高炉寿命越长,炉缸侵蚀越大,风口小套缩回炉墙有利于保护风口小套,延长风口小套寿命。
风口缩回炉墙,一可以保护风口,二必然要增加燃烧面积,活跃炉缸。
有的学者提出和炉墙平齐,风口缩回炉墙内会促进缩回部分耐火砖的破损,也不利于形成合理炉型。
但笔者认为,缩回炉墙是方向,定量缩回多少,大中小高炉应有区别。
高炉生产炉内耐火材料砖衬必然磨损浸蚀,炉缸必然扩大,但是如何使高炉砖衬寿命长,侵蚀小,保持一定的工作炉型很重要。
因此,在保证高炉风压、风速的前提下,风口小套建议缩回墙内50 mm~100 mm,而且随着炉衬的侵蚀,应随时调整。
通过在中小高炉上的工业实践表明,风口缩回炉墙,有利于延长风口寿命,而且炉况顺行,产量高,焦比低,对高炉操作无负面影响。
4 结论通过分析、实践,笔者认为:1)高炉风口在不影响其安装、维护的前提下,数目宜多。
2)风口高度应有一个相对合理、“固定”的数值,对高炉的稳定操作有益,与炉内直接还原和间接还原有很大关系。
3)风口直径不宜经常变动,且应使用平风口或小角度风口,并缩回炉墙内。
5 参考文献[1] ×××.炼铁设计参考资料[M].北京:冶金工业出版社,1979:139.[2] 张树勋.钢铁厂设计原理(上册)[M].北京:冶金工业出版社,2005:77,78.[3] 周传典.高炉炼铁生产技术手册[M].北京:冶金工业出版祉,2002:321[4] 万新.炼铁设备及车间设计[M].北京:冶金工业出版社,2007:50.E-mail:*************。