工业工程(IE)作业分析
IE工业工程经典案例分析

IE工业工程经典案例分析IE工业工程(Industrial Engineering)是一门涵盖工程、管理和人文社会科学等多学科的学科,其主要研究内容包括工业系统的设计、改进和优化。
在实际应用中,IE工业工程经常被用于分析和解决现实问题,提高工作效率和生产效益。
下面将介绍一些IE工业工程经典案例的分析。
一、汽车生产线优化汽车生产线是典型的工业系统,工业工程可以通过优化生产线,提高生产效率和质量。
例如,一家汽车制造公司发现生产线上存在许多不必要的工序和物料的运输,在IE工业工程师的帮助下,对整个生产线进行了分析和改进。
首先,IE工业工程师对生产线进行了布局分析,优化了工序之间的距离和物料传递的路径,降低了物流成本和生产周期。
其次,IE工业工程师使用工程技术手段,如自动化设备和机器人,取代了一些繁琐和重复的工序,提高了生产效率。
最后,IE工业工程师还设计了一个智能化的生产调度系统,通过实时监控,优化了生产计划和资源分配,实现了生产线的高效运行。
通过以上优化措施,该汽车制造公司成功提高了生产效率和质量,降低了生产成本,增强了市场竞争力。
二、物流配送优化IE工业工程师通过数据收集和分析,对物流网络进行了建模和优化。
他们利用运筹学方法,设计了一个最优的配送路线和调度策略,使得快递员的送货路线最短,减少了送货时间和成本。
此外,IE工业工程师还设计了一个智能化的仓储和分拣系统,通过自动化设备和信息技术,快速准确地将包裹分拣和装车,提高了工作效率和准确率。
通过上述优化措施,该快递公司成功提高了物流配送的效率和准确率,降低了成本,增加了客户满意度。
三、医疗服务流程改进IE工业工程在改善医疗服务流程方面也有着重要应用。
例如,一家医院发现其就诊流程存在许多瓶颈和低效的环节,患者等待时间长,医生工作效率低下。
IE工业工程师通过对整个就诊流程进行了分析和改进,提出了一系列优化方案。
首先,IE工业工程师通过调查和模拟实验,找出了就诊流程中的瓶颈环节和低效操作。
IE工业工程分析

工业工程概论(I E)I n d u s t r i a l E n g i n e e r i n g古往今来,不知有多少先贤曾感叹过时光易逝,韶华难追。
懂得利用时间的人觉得时间很宝贵,一分一秒都不让他白过。
不懂得利用时间的人觉得时间很无情,总在时间消逝之后来追悔自己碌碌无为。
对于追求投资回报的企业来说,“时间就是金钱,”这句话真是至理名言啊,不同的人利用时间的能力有高有低,不同的企业利用的时间也参差不齐,这也是企业成败的一大关键呀!在同样的时间里,谁的产出多,谁的效率就高,谁占有竞争优势,这是毋庸置疑的。
许多企业都知道要提高效率,却总是以定性的方法来进行,结果许多时间在不知不觉中浪费掉了却不感到可惜。
须知,效率是以时间为基准来衡量的。
对时间和产出进行定量的分析才是提高效率的堂堂正正之道。
目录第一章:I E概述第二章:动作分析简介第三章:沙布利克分析与作业改善第四章:动作经济原则第五章:动作分析改善实例第六章:工程分析概述第七章:制品工程分析第八章:作业者工程分析第九章:联合工程分析第十章:事务工程分析第十一章:时间分析概述第十二章:标准时间与生产平衡分析第一章I E概述一、IE的开始IE是英文Industrial Engineering的简称,直译为工业工程,是以人、物料、设备、能源和住处组成的集成系统为主要研究对象,综合应用工程技术、管理科学和社会科学的理论与方法等知识,对其进行规划、设计、管理、改进和创新等活动,使其达到降低成本,提高质量和效益的目的的一项活动。
简单地说,IE是改善效率、成本、品质的方法科学。
一般认为泰勒(Frederick W.Taylor 1856~1915)和吉尔布雷斯(Frank B.Gilbreth 1868~1924)是IE的开山鼻祖。
十九世纪八十年代,泰勒和吉尔布雷斯分别通过自己的实践,仔细观察工人的作业方式,再寻找效率最高的作业方法,并且设定标准时间进行效率评估。
工业工程四项分析方法简介
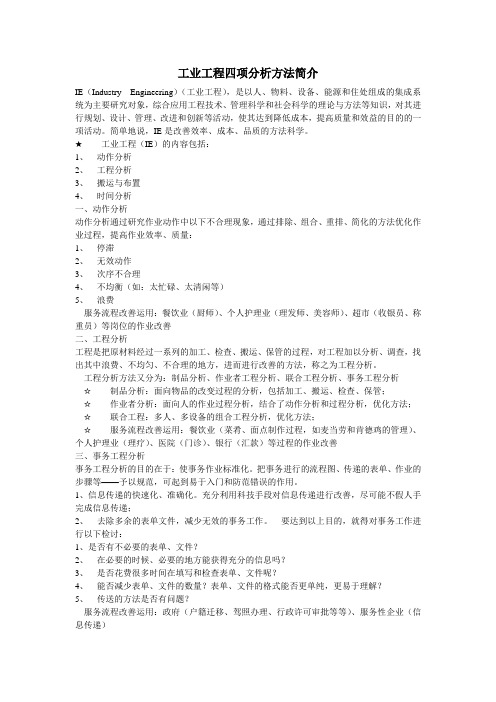
工业工程四项分析方法简介IE(Industry Engineering)(工业工程),是以人、物料、设备、能源和住处组成的集成系统为主要研究对象,综合应用工程技术、管理科学和社会科学的理论与方法等知识,对其进行规划、设计、管理、改进和创新等活动,使其达到降低成本,提高质量和效益的目的的一项活动。
简单地说,IE是改善效率、成本、品质的方法科学。
★工业工程(IE)的内容包括:1、动作分析2、工程分析3、搬运与布置4、时间分析一、动作分析动作分析通过研究作业动作中以下不合理现象,通过排除、组合、重排、简化的方法优化作业过程,提高作业效率、质量:1、停滞2、无效动作3、次序不合理4、不均衡(如:太忙碌、太清闲等)5、浪费服务流程改善运用:餐饮业(厨师)、个人护理业(理发师、美容师)、超市(收银员、称重员)等岗位的作业改善二、工程分析工程是把原材料经过一系列的加工、检查、搬运、保管的过程,对工程加以分析、调查,找出其中浪费、不均匀、不合理的地方,进而进行改善的方法,称之为工程分析。
工程分析方法又分为:制品分析、作业者工程分析、联合工程分析、事务工程分析☆制品分析:面向物品的改变过程的分析,包括加工、搬运、检查、保管;☆作业者分析:面向人的作业过程分析,结合了动作分析和过程分析,优化方法;☆联合工程:多人、多设备的组合工程分析,优化方法;☆服务流程改善运用:餐饮业(菜肴、面点制作过程,如麦当劳和肯德鸡的管理)、个人护理业(理疗)、医院(门诊)、银行(汇款)等过程的作业改善三、事务工程分析事务工程分析的目的在于:使事务作业标准化。
把事务进行的流程图、传递的表单、作业的步骤等——予以规范,可起到易于入门和防范错误的作用。
1、信息传递的快速化、准确化。
充分利用科技手段对信息传递进行改善,尽可能不假人手完成信息传递;2、去除多余的表单文件,减少无效的事务工作。
要达到以上目的,就得对事务工作进行以下检讨:1、是否有不必要的表单、文件?2、在必要的时候、必要的地方能获得充分的信息吗?3、是否花费很多时间在填写和检查表单、文件呢?4、能否减少表单、文件的数量?表单、文件的格式能否更单纯,更易于理解?5、传送的方法是否有问题?服务流程改善运用:政府(户籍迁移、驾照办理、行政许可审批等等)、服务性企业(信息传递)四、时间分析所谓时间分析,就是针对时间及产出做定量的分析,找出时间利用不合理的地方,从而进行改善的方法,是IE方法的一种基本方法;是改善生产效率的重要手段;设定标准工时的重要依据;制造系统规划和改善的依据;评价作业者技能和工程管理水平的依据;作为成本分析的重要依据。
精选工业工程IE线路图分析
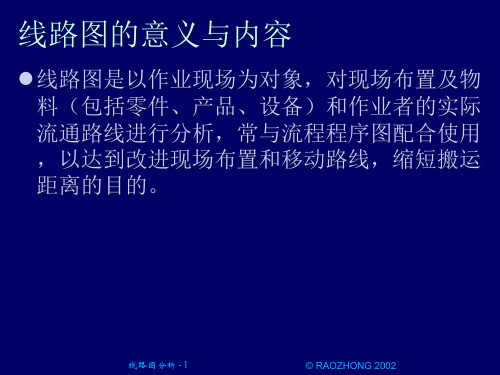
在接收台的对面开一个进库的新入口,使箱子可沿最短路线运进库房。箱子从送货车滑下滑板,直接放到手推车上,并送到开箱处。就在车上开箱,取出送货单。然后运到收货台,等待片刻,打开箱子,把零件放到工作台上,对照送货单点数并检查。检查与点数的工作台现已布置在收货台旁,因为可以用手传递零件来检查、测量并点数。最后,把零件放回纸盒,重新装箱。
9、静夜四无邻,荒居旧业贫。。10、雨中黄叶树,灯下白头人。。11、以我独沈久,愧君相见频。。12、故人江海别,几度隔山川。。13、乍见翻疑梦,相悲各问年。。14、他乡生白发,旧国见青山。。15、比不了得就不比,得不到的就不要。。。16、行动出成果,工作出财富。。17、做前,能够环视四周;做时,你只能或者最好沿着以脚为起点的射线向前。。9、没有失败,只有暂时停止成功!。10、很多事情努力了未必有结果,但是不努力却什么改变也没有。。11、成功就是日复一日那一点点小小努力的积累。。12、世间成事,不求其绝对圆满,留一份不足,可得无限完美。。13、不知香积寺,数里入云峰。。14、意志坚强的人能把世界放在手中像泥块一样任意揉捏。15、楚塞三湘接,荆门九派通。。。16、少年十五二十时,步行夺得胡马骑。。17、空山新雨后,天气晚来秋。。9、杨柳散和风,青山澹吾虑。。10、阅读一切好书如同和过去最杰出的人谈话。11、越是没有本领的就越加自命不凡。12、越是无能的人,越喜欢挑剔别人的错儿。13、知人者智,自知者明。胜人者有力,自胜者强。14、意志坚强的人能把世界放在手中像泥块一样任意揉捏。15、最具挑战性的挑战莫过于提升自我。。16、业余生活要有意义,不要越轨。17、一个人即使已登上顶峰,也仍要自强不息。
考察分析
问:第二个操作是码垛,第三个操作是卸箱,既然要卸箱为什么又要码起来?答:因为卸车比办接收快,为避免地上到处都是箱子,只好码起来。问:接收、检查、点数的地方为什么离得那么远?答:无意中安置在那里的。间:有无更好的办法?答:可以放在一起。问:应放在何处?答:可放在接收台处。问:为什么物品要绕一圈才能放到零件架上?答:因为贮存处(零件架)的门在检查台的那边。
IE的分析方法及工具

IE的分析方法及工具IE(Industiral Engineering),即工业工程,是一种研究工业生产中如何最优地运用人力、物力、财力等资源,以提高生产效益的学科。
在进行IE分析时,可以使用多种方法和工具来辅助。
以下是一些常用的IE分析方法及相关工具的简要介绍。
1.流程分析方法及工具:流程分析方法用于分析和优化工业生产过程中的流程。
常用的工具包括流程图、流程价值分析(PVA)、时间和动作研究(TAR)、价值流图(VSM)等。
流程图用于展示工业生产过程中的各个环节和关联性;PVA用于评估每个流程环节的价值并确定可能的改进点;TAR用于观察和分析工人在生产过程中的时间和动作,并提出相应的改进意见;VSM用于展示整个价值流程并识别可能的浪费环节。
2.工艺分析方法及工具:工艺分析方法用于分析和改善工业生产过程中的工艺。
常用的工具包括工艺路线图、标准操作程序(SOP)、工艺能力分析(PCA)等。
工艺路线图用于展示产品的生产流程和工艺要求;SOP用于明确每个工艺步骤的操作规范;PCA用于评估工艺的能力和稳定性,并提供改进建议。
3.人力分析方法及工具:人力分析方法用于分析和优化工业生产中的人力资源。
常用的工具包括时间研究、任务分析、工作分配、人力需求预测等。
时间研究用于测量工人在完成特定任务时所需的时间,并为人力资源的规划和管理提供依据;任务分析用于分析和描述每个工作岗位的任务要求和职责;工作分配用于合理分配人力资源以确保工作效率和质量;人力需求预测用于预测未来生产需求并相应地调整人力规模。
4.设备分析方法及工具:设备分析方法用于分析和改善工业生产中的设备使用效率和可靠性。
常用的工具包括设备维修与保养(PM)、总有效设备利用率(OEE)、故障模式和影响分析(FMEA)等。
设备维修与保养用于保障设备的正常运行和寿命延长;OEE用于评估设备的综合利用率,并提供可能的改善点;FMEA用于分析设备故障的模式和影响,并提出相应的预防和改进措施。
工业工程-IE与作业分析-ST推广及效率分析

作业效率= 良品完成工时/总出勤工时 效率=良品所需工时/直接工时 能率=良品完成工时/纯作业工时 可动率=实动工时/直接工时
6/17
工时的构成
效率的计算(另外一种分析方法)
运
综
转
合作 效 效业 率 率效
率
总出勤工时
作业者的实绩工时(测定 管理者责任
带来的材料等待,
作业等待,设备故
障,会议,议论等。
7/17
标准时间在效率计算中的重要性
1.应该是具有科学根据的标准时间 -适当性:管理者和作业者认为是适当的尺度,误差应该少。 -普遍性:具备一般的标准作业速度,稳定的尺度。 -公正性:使大家认为公平,且国际通用的。
※所谓科学的含义并不意味着细分时间,重要的是设定过程和思考方法具有科学性。
比较
•未包含设备的使用效率(加动率分析)
• 标台的概念有利于财务的核算 • 对所有彩电工厂的横向比较提供
了参考
• 有利于各彩电厂的效率目标制定
2/17
标准工时及效率改善实施办法
为了尽快提高我公司的效率及成本核算的准确性,又由于ST制作项目组已基本建立了标准 时间(ST)的计算方法,所以建议在我彩电厂的F线先使用ST代替现在的工时定额,并改变效 率的计算方法,随后推广到整个彩电厂,具体实施计划如下:
-正常速度是在稳当的监督下面,没有效率工资和刺激下工作的平均工作速度值 -
8/17
效率提高中监督者的作用
- 生产线监督者应有的姿态
1. 一线监督者应该在现场经常监督和指导作业者 2. 一线监督者应该自觉地直接指导和监督作业者
(不能通过下边的小组长进行间接监督) 3. 指导,监督应对每个人具体地做
工业工程IE案例 分析

左手可以直接将卡拿起,不必经过换手这一步了。这样做的优点是,可以减少一次右手往返动作, 即减少了 2*5MOD 值;在拿卡的过程中,减少了 3MOD 值。一共节省了 13 个 MOD 值。
14. Excel 表中,第 127-129 行
根据 ECRS 原则的消除原则和动作经济原则中“双手的动作应同时而对称”原则,将第 128 中左 手“把卡和小单子移至右手”的动作,替换为左手“把小单子和卡交给顾客”动作,同时,右手将 大单子放在桌上。优化后,三步削减为一步,MOD 值又原来的 10 变为 5,即减少了 5 个 MOD 值。
在“验钞”操作中,该业务员一共检验了 5 次,而在一般情况下并不需要如此多次。根据 ECRS 原则的消除原则,消除不必要的工序以及动作。我们将之优化为 2 次,即删除 60-68 行,减少了 33
6
个 MOD 值,这样一来,既节约了时间也可以保证检验的有效性。 10. Excel 表中,第 101-102 行
用何种方法适合此次优化,定下了粗略的计划安排。最终讨论结果是,优化我们平时经常去 并且经常会浪费很长时间排队的第三大街的邮局,并确定了以 MOD 法分析动作并以此基础 进行优化的计划。 2. 进行实地考察。我们带着摄像及照相设备,准备对业务员办理业务的全部流程进行录像,以 便回来后可以根据录像进行分析。我们找了一个普通工作日的下午,办理业务的顾客人数适 中,具有代表性。这样既可以排除周末高峰时段的特殊情况,又可以让我们能有较为宽敞的 拍摄空间。但在实际考察过程中,我们的这些设想在实施的过程中遇到了很大的困难。因为 银行是个特殊的场所,只有经过邮局上层领导的批准才能进行拍摄,所以那边的工作人员出 于安全考虑,禁止我们用摄像机去记录业务的动作。我们在录像进行到一半时就被制止了,
IE工业工程分析方法

IE工业工程分析方法1.系统分析:系统分析是IE工程师的核心工作之一、该方法通过对生产系统中各个组成部分的深入研究,识别瓶颈和问题,并提出解决方案。
系统分析需要对各个层级的细节进行分析,以便全面了解整个系统的功能和工作方式。
2.流程分析:流程分析是IE工程师用来评估和改进生产流程的一种方法。
它通过对流程中的每个步骤和活动进行详细分解和分析,识别出低效的环节和改进的机会。
流程分析可以帮助确定流程中的瓶颈,并提出优化方案来提高生产效率。
3.时间研究:时间研究是IE工程师用来确定工作站和生产线的工作标准的方法。
它通过对员工工作时间的观察和测量,确定每个任务所需的时间,并建立工作标准以指导员工完成工作。
时间研究可以帮助管理者更好地分配资源和计划生产进度。
4.价值流分析:价值流分析是一种用来评估价值流程并识别浪费的方法。
它通过对价值流程中的每个步骤和活动进行分析,找出不增值的环节,并提出改进策略。
价值流分析可以帮助提高生产过程中的效率和质量,减少浪费和成本。
5.人工程学:人工程学是IE工程师用来改进员工工作环境和工作流程的方法。
它通过对员工的行为和工作环境进行观察和分析,提出改进措施以提高员工的工作效率和舒适度。
人工程学可以帮助减少员工疲劳和错误率,提高生产效率和质量。
6.效益分析:效益分析是IE工程师用来评估生产过程改进方案的方法。
它通过对改进方案的成本和效益进行权衡,确定改进的经济效益和回报周期。
效益分析可以帮助管理者决策是否实施改进方案以提高生产过程的效率和利润。
7.运筹学方法:运筹学方法是IE工程师用来优化生产计划和资源分配的方法。
它通过数学模型和算法来解决生产规划、调度和资源分配等问题,以最大化生产效率和利润。
运筹学方法可以帮助管理者制定合理的生产计划和资源分配方案,提高生产系统的灵活性和响应能力。
通过运用这些分析方法,IE工程师可以全面了解生产系统和过程,并提出改进方案来提高生产效率、降低成本、优化资源分配和提高产品质量,从而实现企业的持续增长和竞争优势。
工业工程IE人机操作分析

工业工程(IE)人机操作分析1. 简介工业工程(Industrial Engineering,简称IE)是一门综合性的工程学科,研究如何优化现有系统的运作效率和效益。
其中,人机操作是IE领域的一个重要研究方向,涉及到人与机器在工作环境中的互动和协作。
本文将对工业工程中的人机操作分析进行介绍和探讨。
2. 人机操作的概念人机操作是指人与机器之间进行沟通、交互和协作的过程。
在工业工程中,人机操作分析是通过对人机交互过程的研究和评估,来优化生产系统的运作效率和人机协作的质量。
人机操作分析的核心目标是改善工作环境,提高工人工作效率和舒适度。
3. 人机操作分析的方法3.1 观察法观察法是人机操作分析中常用的一种方法。
通过实地观察和记录工人与机器之间的交互过程,可以获取到真实可靠的数据,并对工作环境进行评估。
观察法可以从定量和定性两个方面进行,定量观察法主要关注交互的时间、频率和顺序等数据,而定性观察法则是关注工人的态度、满意度和工作体验等主观感受。
3.2 实验法实验法是通过设计和进行实验来评估人机操作的效能和质量。
在实验过程中,可以对参与者进行各种任务和操作,并记录并分析操作的效果和效率。
实验法通常需要精心设计实验方案,控制变量,并借助科学化的指标来衡量操作的质量。
3.3 问卷调查法问卷调查法是一种广泛应用的数据收集方法,可以通过询问参与者的主观意见和感受来评估人机操作的质量。
问卷调查法可以较全面地了解工人对人机交互的满意度、难易程度和改进建议等,为改进和优化人机操作提供有价值的参考意见。
3.4 人机交互设计模型人机交互设计模型是一种基于人工智能和人机工程学的方法,旨在优化人机交互的质量和效率。
通过建立并优化人机交互设计模型,可以提升工人的工作效率和满意度,并减少错误和事故的发生。
常见的人机交互设计模型包括认知工程学模型、人机协同模型和心理物理学模型等。
4. 人机操作分析的应用领域4.1 生产线优化在工业生产线上,人机操作的效率对整体生产线的运作至关重要。
IE效率分析流程
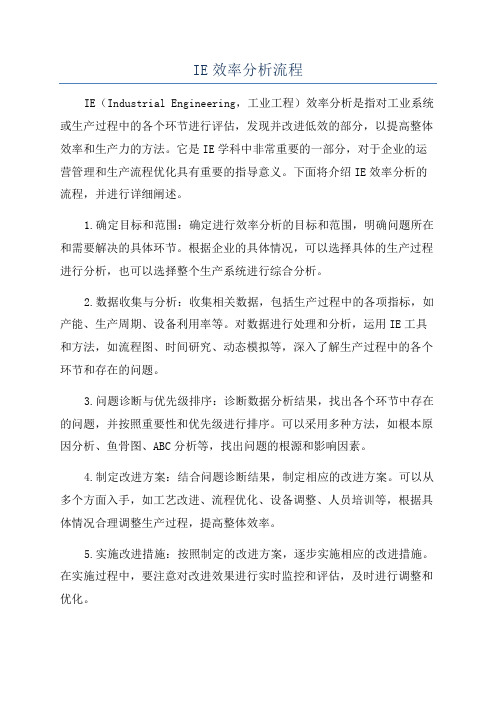
IE效率分析流程IE(Industrial Engineering,工业工程)效率分析是指对工业系统或生产过程中的各个环节进行评估,发现并改进低效的部分,以提高整体效率和生产力的方法。
它是IE学科中非常重要的一部分,对于企业的运营管理和生产流程优化具有重要的指导意义。
下面将介绍IE效率分析的流程,并进行详细阐述。
1.确定目标和范围:确定进行效率分析的目标和范围,明确问题所在和需要解决的具体环节。
根据企业的具体情况,可以选择具体的生产过程进行分析,也可以选择整个生产系统进行综合分析。
2.数据收集与分析:收集相关数据,包括生产过程中的各项指标,如产能、生产周期、设备利用率等。
对数据进行处理和分析,运用IE工具和方法,如流程图、时间研究、动态模拟等,深入了解生产过程中的各个环节和存在的问题。
3.问题诊断与优先级排序:诊断数据分析结果,找出各个环节中存在的问题,并按照重要性和优先级进行排序。
可以采用多种方法,如根本原因分析、鱼骨图、ABC分析等,找出问题的根源和影响因素。
4.制定改进方案:结合问题诊断结果,制定相应的改进方案。
可以从多个方面入手,如工艺改进、流程优化、设备调整、人员培训等,根据具体情况合理调整生产过程,提高整体效率。
5.实施改进措施:按照制定的改进方案,逐步实施相应的改进措施。
在实施过程中,要注意对改进效果进行实时监控和评估,及时进行调整和优化。
6.效果评估和总结:对改进后的效果进行评估和总结,分析改进的成果和效益。
可以通过比较数据、指标的变化,以及员工的反馈和评价等进行评估,重新进行IE效率分析并寻找进一步改进的空间。
IE效率分析需要运用一系列的工具和方法,如流程图、时间研究、动态模拟、根本原因分析、鱼骨图、ABC分析等。
这些方法的运用可以帮助分析人员全面了解生产过程中的各个环节,找出存在的问题,并制定相应的改进方案。
在IE效率分析的实施过程中,需要充分发挥团队的作用。
团队成员可以来自不同的部门和岗位,通过各自的专业知识和经验,共同进行效率分析,并制定改进方案。
现代工业工程(ie)最佳实践

现代工业工程(IE)是指通过科学的管理方法和技术手段,对生产过程进行优化和改进,旨在提高生产效率、降低成本、提高产品质量,并最终实现企业的可持续发展。
在现代制造业日益竞争激烈的环境下,IE的最佳实践对于企业的发展至关重要。
本文将结合相关理论和实践经验,系统介绍现代工业工程的最佳实践。
I. IE的基本原理IE作为一种管理科学,主要应用于生产系统的规划、设计和管理。
其基本原理可以总结为以下几点:1. 系统观念:IE强调整体观念,即将生产过程看作一个系统,包括人、机、料、法、环境等多个要素,通过系统分析和优化,实现生产过程的高效运行。
2. 标准化和规范化:IE倡导标准化和规范化的生产方法,通过制定标准作业程序、工艺流程等,提高生产的稳定性和一致性。
3. 过程优化:IE通过工艺改进、生产线平衡、作业分析等手段,对生产过程进行优化,提高生产效率。
4. 人力资源优化:IE注重人力资源的科学管理,包括工作安排、培训、激励等方面,提高员工的生产效率和满意度。
II. IE的最佳实践在实际应用中,IE的最佳实践主要包括以下几个方面:1. 强调质量管理IE倡导在生产过程中强调质量管理,包括质量控制、质量检验、质量改进等方面。
通过建立质量管理体系,实现产品质量的稳定和提升。
2. 实施精益生产精益生产是IE的重要实践内容,通过消除浪费、提高生产效率、优化供应链等手段,实现生产过程的精益化管理,降低成本、缩短交付周期。
3. 应用先进技术IE强调应用先进技术,包括信息技术、智能制造技术、自动化技术等,提高生产过程的自动化程度和智能化水平,提高生产效率和产品质量。
4. 优化生产布局生产布局的合理优化是IE的重要实践内容,通过合理规划生产车间、生产线、设备布局等,提高生产效率和空间利用率。
5. 优化物流管理IE强调优化物流管理,包括供应链管理、库存管理、物料搬运等方面,通过优化物流管理,降低库存成本、提高物料周转率。
6. 强调人力资源管理在IE的实践中,注重人力资源管理至关重要,包括员工技能培训、绩效考核、激励机制等方面,提高员工的生产效率和工作满意度。
IE工业工程分析过程

IE工业工程分析过程1.收集数据和定义目标:这是IE工程师确定系统分析和优化的起点。
他们需要收集相关的数据,包括流程图、工艺参数、设备能力等,并明确定义目标,比如提高生产效率、降低成本、提高质量、减少等待时间等。
2.建立模型:建立数学模型是IE工程师进行分析和优化的关键步骤。
他们可以使用线性规划、统计模型、模拟等方法,将实际系统抽象为数学模型,以便进行分析和优化。
3.分析系统:IE工程师使用建立的数学模型对系统进行分析。
他们可以通过模拟实验、数据分析、统计方法等手段,从不同的角度分析系统的运行情况,找出存在的问题和瓶颈,并确定改进的方向。
4.优化方案设计:在系统分析的基础上,IE工程师提出优化方案。
他们可以通过重组流程、调整设备配置、改进工艺参数等方式,设计出最佳的生产或服务方案。
同时,他们还会考虑相关的约束条件,比如设备的能力、人力资源的限制等。
5.实施改进:在确定了优化方案之后,IE工程师需要制定详细的实施计划,并与相关部门进行沟通和协调。
他们需要考虑到实施的可行性和成本,并制定相应的措施来确保改进的顺利实施。
6.监控和调整:一旦实施了改进方案,IE工程师需要对其进行监控和调整。
他们可以使用控制图、关键绩效指标等工具,跟踪改进效果,并根据需要进行调整和优化。
7.绩效评估:IE工程师在系统分析和优化的过程中,需要对改进的绩效进行评估。
他们可以比较改进前后的指标,比如生产效率、成本、质量等,并对改进结果进行总结和归纳,为以后的工作提供经验和参考。
总的来说,IE工业工程的分析过程是一个循环迭代的过程。
IE工程师不断收集数据、建立模型、分析系统、设计优化方案、实施改进、监控和调整,并进行绩效评估,不断优化和改进系统的运行效率和效果。
这种方法可以帮助组织提高生产力、降低成本、提高质量、提升竞争力,并在不断变化的环境中保持持续的改进和创新能力。
经典工业工程实验报告(3篇)

第1篇一、实验背景随着我国经济的快速发展,工业生产规模不断扩大,对生产效率和质量的要求也越来越高。
为了提高生产效率、降低生产成本、优化生产流程,工业工程(IE)作为一种系统性的工程方法,在工业生产中发挥着越来越重要的作用。
本实验旨在通过实际操作,让学生深入了解工业工程的基本原理和方法,提高学生的实际操作能力和解决实际问题的能力。
二、实验目的1. 理解工业工程的基本概念和原理;2. 掌握工业工程常用工具和方法;3. 学会运用工业工程的方法分析和解决实际问题;4. 提高学生的团队合作能力和沟通能力。
三、实验内容本次实验选择了某电子产品组装生产线作为研究对象,通过以下步骤进行实验:1. 现场观察与调查首先,我们对生产线进行了现场观察和调查,收集了以下信息:(1)生产线的基本情况:包括生产线长度、宽度、高度,生产线上的设备数量和类型等;(2)生产线上的工作流程:包括原材料入库、加工、组装、检测、包装等环节;(3)生产线上的操作人员:包括操作人员数量、工种、技能水平等;(4)生产线的物料流动情况:包括原材料、半成品、成品等物料的流动路径、流量、时间等。
2. 工作研究(1)人机操作分析:通过观察操作人员的动作,分析其操作过程中的不合理之处,如重复动作、无效动作、动作幅度过大等,并提出改进建议;(2)双手操作分析:分析操作人员双手的动作规律,找出双手操作的瓶颈,提出优化方案;(3)动作分析:运用ETM(Equivalence Time Method)等方法,对操作人员的动作进行时间分析,找出影响生产效率的关键因素。
3. 生产线布局优化根据工作研究的成果,对生产线进行布局优化,主要包括:(1)调整生产线长度:缩短生产线长度,减少物料运输距离;(2)优化设备布局:将设备按照加工顺序排列,减少操作人员的行走距离;(3)设置缓冲区:设置缓冲区,减少生产线上的物料积压,提高生产效率。
4. 生产线仿真模拟利用仿真软件对优化后的生产线进行模拟,验证优化效果,并对可能出现的问题进行预测和调整。
IE(工业工程)——动作分析
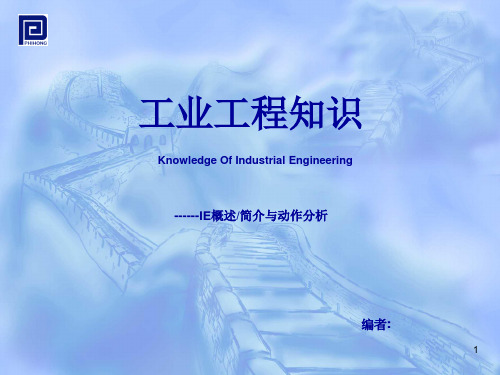
(2)以器具来握取时,应视为[应用]而非[握取];至于戴手套握取时,则为[握取]而非[应
用],因手套之目的在于保护手。 (3广义解释,除手外,身体之某一部分(如足)用以控制物体时,皆可称为[握 取]。 改善: (1)减少握取之次数。 (2)尽量以[触取]代替[拾取]。 A.拾取:物体确实被捡上而取之于手,並須充分控制方能移动。 B.觸取:只以手指按住物體,即可以將物體移行(或滑行)。 (3)检讨有无工具可代替。
IE的6541原则:6=5W1H;5=问题解决5步法;4=ECRS;1=一个不忘
成本意识
现场七大浪费 管理的七大浪费
品质意识 …………
7
IE的基本意识---什么是浪费??
什么是浪费?
■ 不增加价值的活动,是浪费; ■ 尽管是增加价值的活动,所用的资源超过了“绝对最少”的界限,也是浪费.
第二 类 阻碍第一类工作要素之进行(9~13) 第三类: 对工作无益之要素(14~17)
20
第一类动素--1
1. 1.伸手(Reach-RE) 记号为:
定义:空手移动,或称[运空](Transport empty)。
起点:当手开始朝向目的物之瞬间。 终点:当手抵达目的物之瞬间。 特性: (1)当手朝向目的物或某一动素完成,手须伸回时发生[伸手]动素。 (2)[伸手]途中常有[预对]伴生。 (3)[伸手]常在[放手]之后,而在[握取]之前发生。 改善: (1)缩短距离。 距离之测量应实际路径为准,而非两端之直线距离。 (2)减少[伸手]时之方向意识(sence of orientation)。 [伸手]依难易可分为下列数类: A.伸手至一固定位置 B.伸手至每次位置略有变动之目的物。
4.生产过剩之浪费 5.整修、不良、退 货之浪费
IE工业工程与事务工程分析

IE工业工程与事务工程分析工业工程:英文Industrial Engineering简称I E。
定义:工业工程是指有关人员,物料,设备,信息和能源等整体制度之设计,改进及制定事项的一门科学,它应用自然科学与社会科学之专门知识及计巧,并运用工程分析与设计的原理和方法,来推测并评估自此系统中所获得的结果。
IE的机能:设计,改良,实施人员,物料,设备,信息能源的综合体系。
I E的方法:运用通过数学、自然科学,社会科学专门化后的识、技术以及工程分析、工程设计的原则、方法来规定.二、I E的要紧工作内容:1. 作业标准与标准时刻的设定。
2. 工程设计(工具、设备、加工方法、装配方法等)。
3. 制品设计(价值工程/分析、成本数据之作成等)。
4. 生产、存量、质量、成本等治理体系的设计。
5. 工厂布置、设备布置、物料搬运之设计。
6. 设备投资方案之打算与分析。
7. 生产方式、生产途径之设计。
8. 职务方式与工作评判。
9. 绩效治理制度之设计与营运。
10. 奖工制度的设计与营运。
11. 规划教育训练方案与实施。
12. 工业安全之有关事项。
13. 安防系统的设计。
14. 物料消耗(金耗)操纵。
15. 品质检验标准及方法的制定。
三、标准工时之结构与应用1. 标准工时之定义:经由合格之操作者,关于指定工作在既定状态下,以正常速度去完成操作所用之全部谓之标准工时(Standard Time 简写S.T)以上之意涵条件如下:(1) 合格之操具有担任该项操作所必需之聪慧与体力并受过适当训练,有足够验,可将工作做为中意之质量标准,且其技术与操作能力为所属组织成员之平均程度。
(2) 既定状态:a.现况操作方法及设备,其包括操作程序使用之工具、材料等。
b.既定工作环境。
(3) 正常速度(Normal Pace):其基准为「在0.45分种内将52张扑克牌分成四堆之速度」或「以0.35分钟内走完100呎的距离」。
亦即MTM中100%之速度。
IE工业工程分析方法及工具

IE工业工程分析方法及工具1. 引言IE工业工程(Industrial Engineering)是一门研究如何在生产过程中有效利用人力、设备、材料、资金等资源的学科。
IE工业工程分析方法及工具是指在IE工业工程领域中应用的各种方法和工具,用于分析和改进生产过程,提高生产效率和质量。
本文将介绍一些常用的IE工业工程分析方法及工具。
2. 价值流图价值流图(Value Stream Mapping)是一种用于分析和改进生产流程的工具。
它通过绘制生产过程中各个环节的流程图,并标注出每个环节的价值添加和非价值添加时间,帮助识别生产过程中的瓶颈和浪费,并提出改进方案。
3. 工序分析工序分析是一种通过对生产流程中每个工序进行详细分析,找出其中的问题和改进空间的方法。
通过分析每个工序的工作内容、工时、工艺和操作方法等,可以识别出瓶颈和浪费,提出改进建议。
4. 时间研究时间研究是一种通过观察和测量工人完成特定任务所需的时间,来评估生产效率的方法。
通过时间研究,可以识别出工艺中的瓶颈和浪费,改进工艺,提高生产效率。
5. 作业分析作业分析是一种通过观察和分析工人在特定作业中的动作和姿势,评估工作负荷和人体工效学的方法。
通过作业分析,可以识别出工作中存在的人体工效学问题和健康风险,提出改进建议。
6. 数据分析数据分析是一种通过收集和分析生产过程中的数据,了解生产过程的状态和性能的方法。
通过数据分析,可以识别出生产过程中的异常和问题,采取相应的措施进行改进。
7. 品质管理工具品质管理工具是一些用于识别和解决生产过程中的质量问题的方法和工具。
常见的品质管理工具包括:散点图、柏拉图、直方图、Pareto图、因果图等。
8. 线平衡线平衡是一种通过合理分配工序中的工作量,达到生产线上工人负荷均衡的方法。
通过线平衡,可以提高生产线的效率和生产能力。
9. 人因工程人因工程是一种通过研究人与设备、工作环境之间的适应性、相互关系等,改进生产过程的方法。
工业工程IE流程分析

添加标题
找出最经济的移动方法;
添加标题
尽可能地减少在制品的贮存。
操作
搬运
考虑下列因素,哪些搬运可以取消、合并、重排、简化 取消某些操作; 改变物品存放的场所或位置; 改变工厂布置; 改变搬运方法; 改变工艺过程或工作顺序; 改变产品设计; 改变原材料或零部件的规格。
由于预定的次一行动(主要是操作、检验可搬运)即刻产生之时间空档为非必要,或非控制情况之下。
工序图示记号(JIS)
大类
说 明
小类
说 明
说 明 例
类
物品受到本质或位置变化的单位工序
加 工
物品被变形、变质装配、分解的单位工序
第3加工工序 B零件的第5加工工序 加工中同时做产品检验
B.运
指材料、零件、半成品、成品从某一位置被子移动至另一位置。 记号:约为加工的大圆记号的1/2大小的小圆,内侧可注明搬运的机器或工具。 ……指用卡车搬运。 有时因与大圆的记号不易区别,也有使用箭头记号( 或 )
C.查
指材料、零件、半成品或成品的品质特性或数量用方法加以检测,并将其结果与基准比较作为判别合格或秒合格。 记号: ……品质检查 ……数量检查 ……品质与数量的检查
程序分析的目的
取消不必要的程序(工艺、操作、动作)。 合并一些过于细分或重复的工作。 改变部分操作程序,以避免重复。 调整布局,以节省搬运。 重排和简化剩余的程序,重新组织一个效率更高的程序
工序系列组合是否合于目的性、经济性。 别工序前后的关连性。
程序分析的主要意义
人型的流程程序图 物型的流程程序图
搬 运
变化物品位置的单位工序
男工搬运 卡车搬运
类
物品检验的单位工序
- 1、下载文档前请自行甄别文档内容的完整性,平台不提供额外的编辑、内容补充、找答案等附加服务。
- 2、"仅部分预览"的文档,不可在线预览部分如存在完整性等问题,可反馈申请退款(可完整预览的文档不适用该条件!)。
- 3、如文档侵犯您的权益,请联系客服反馈,我们会尽快为您处理(人工客服工作时间:9:00-18:30)。
☺ 所谓作业分析是指为了作业改善及消除浪费而充分理解作业内容中的构成因素及作业的区分,并掌握好其组合是否有浪费,为了进行改善分析要素作业的方法。
☺所谓的要素作业是指作业分割时的一个精确度的单位,一般用秒表测试的最小单位;比如说“夹起配件”或“印A面”等存在的某种目的的最小单位;一般把要素作业可称之为比单位作业小,但又比动作大一个台阶的作业的综合。
1)通过对作业进行详细分解,调查是否有遗漏,甚至能发现平常作业时是感觉不到的细微的浪费。
2) 根据现象的定量掌握,准确地掌握好目前的方法;为了彻底清除浪费及有效的作业有必要更具体地观察并理解目前的作业。
3) 为了改善要素作业及其周围的工器具、设备、加工条件、配件的精确度等进行第一阶段。
☺ 作业分析分为基本分析和重点分析☺ 基本分析又分为单独作业分析和组合作业分析;组合作业分析又分为人与人的组合作业分析及人与设备之间的组合作业分析。
图I4—1图I4—2(1)将作业按要素作业分割的单位越小越好,但一定要保证能检测到的大小。
(3/100分~5/100分为界限)(2)分为主要目的要素和辅助目的要素①主要目的要素:磨,切削,装配,分割等②辅助目的要素:夹配件,放材料等(3)作业分为作业者要素及设备要素;比如以机加工为中心的作业时又分为人的作业时间和设备作业时间。
(4)尽可能把要素作业分为不同的目的;比如加工、移动、检查、等待等。
(5)分为规则要素及不规则要素①规则要素:每一个作业或一个周期所发生的要素。
例:把配件安装在设备上,把配件从设备上拆除。
②不规则要素:作业中需要,但跟规则或基本要素作业的周期相比无规则间距所发生的因素。
例:用测试仪测数据,刷掉刀架上的铁屑等。
☺首先对测试对象进行充分的预备调查。
(1) 调查对象作业是否正常地按规定进行。
(2) 调查材料是否与正规的一致。
(3)调查是否使用规定的设备设备或工具。
(4) 调查现场配置是否处于规定的状态。
(5) 其它条件是否在规定的状态下进行。
☺ 预备测试完成后,对以下具体的要素进行实际的测试(1) 对作业进行分割后把情况按照作业顺序记录在测试表的作业栏上,并确认其作业顺序记录是否正确。
(2) 作为作业对象的部件或现场配置尽可能详细地进行描述。
(1) 贴分析符号是为了让大家看清楚分析内容,并能马上理解作业的进行过程及作业的内容。
(2) 加工以大“○”来表示;准备及收尾等为了进行加工的机械操作、材料、前工序完成品取放等都以加工符号来表示。
① 将轴和弹簧拿起,进行装配;② 拿起喷漆用喷头,喷外板后,放下喷头;③ 从工装上拿起已完成的铸件,放在托盘上等等。
(3) 检查用“◇、□”来表示① 检查内容有系数、计量、质量检查,但实际是分为如下两个部分; ② 量的检查是用“□”;质的检查是用“◇”来表示。
(4) 移动是用小“○”来表示,工序内两步以上步行的移动,用大车搬运材料、成品或工具等的移动和有时作业人员空手移动。
(5) 等待是用“▽ ”来表示。
材料、配件等尚未加工检查的处于等待的状态。
(1)观测准备① 准备1/100分或1/60分刻度的秒表; ② 观测次数为最好是可连续观测约5-10次;③ 准备观测板、铅笔、卡尺、千分尺、尺、计算器等。
(2) 观测位置和姿势① 选择能看清楚作业情况,但不影响主要的位置; ② 站在作业动作区分与表、眼睛能达到直线的位置; ③ 应小心不要把秒表掉在地面等。
(3) 观测时的要点① 作业人员说清楚观测的目的,得到他们的协助以得到更好的结果; ② 确认作业状态及内容是否正常;③ 为了能充分理解作业内容,多观察几个循环后进行测试;观测时将作业分割成容易观测的单元; ④ 测试时以要素作业为单位把观测的时间记录下来,每个要素作业要有决定时间的代表值; ⑤ 除去异常数据后,取平均值作为改善研究的依据。
☺ 时间观测作为观测法的一种,不管是好的结果还是坏的结果能明确地表现出来,因此要特别注意不要给现场施加异常的刺激或人际关系上出现问题。
☺ 为此要与现场有关人员进行充分的沟通,解释清楚测试对象作业、时机,时间等以求谅解,最好避免擅自行动或观测分析。
☺ 观测时必须提前打开秒表,连续测试作业的重复。
☺ 观测时间的记录要领如下:(1) 作业的一个循环的最初和最终以分来记录,测试中有异常发生时下一个作业的时间值同样用分来记录。
(2) 如发生不规则作业时应及时在空白的预备栏上记录下来。
(3) 由于作业的细微的动作反复需要了解其次数时,利用时间栏记录其次数。
(4) 观测中需要改善事项尽量详细地记录,以便在以后改善时利用。
(5) 对每个时间进行计算,除去异常值后算出平均值。
轴研磨作业的连续测试事例(1)明确人与人、人与设备、设备与设备的作业分工;(2)明确作业量的不均匀状态;(3)掌握人员的等待与设备的非运转部分,提高运转率。
(1)减少或去除人员的等待时间比率;(2)减少或去除设备休息、停止时间的比率;(3)利用工器具的改善、设备的改良、自动化等措施、减少或去除人与人、人与设备的合作作业;(4)将人与人的合作作业利用工器具、设备的使用等措施,实现单独作业化;(5)考虑是否取消移动作业或合并等等;(6)研究是否缩短设备的运转时间。
表I4—3☺ 彻底地调查及分析制造现场中的作业人员及物品的现象,并利用其结果找出其中的原因即为重点分析,其目标是明确每个要素作业的因果关系,减少或去除不必要的因素。
☺重点分析的目标明确每个要素作业的因果关系,除掉不必要的因素,实现问题或浪费因素的零化。
☺ 重点分析的关键(1) 基本分析中存在问题的每个内容要掌握清楚;(2) 更具体,更详细地分析问题的核心部分;(3) 此结果为基础,研究改善方案并执行。
☺ 调查主要作业的设备设备的性能、精确度、保养状况等。
此分析的目标是调查清楚主要作业设备是否按照平常标准的性能及能力运转。
☺ 调查工装、工具、辅助工具、检查仪器、其它工具等的实际状态及性能、精度、数量等,另外对保修、管理方面的因素也要考虑。
☺ 实际作业时要分析加工条件,发现最佳状态为目标。
☺ 作业中以作业人员为中心,调查分析物理及精神的环境影响到人的活动、产品、设备状态的周围环境,并进行改善。
☺ 调查分析作业人员的经验、技术、体格、技能、视听觉、性格等主要条件是否适合此作业,并进行改善。
☺ 调查分析产品机能、材料、组装及加工顺序、结合程度、材质、形状、工序等后,探讨材料的节约、结构的简单化、加工的容易性、部件的损耗程度的改善并力求加工作业、组装作业的简单化。
☺ 调查分析作业或作业条件对质量、精度的影响,并以改善此结果为目标;对象为作业的设备、附件、刀具、检查仪器等的精度和其附着精度对产品的精度、纯度的影响程度,并进行研究改善。
主作业设备分析加工条件分析表I4—5(1) 推广改善的基本为了充分利用改善的课题或好的构思,最重要的是充分引导好推广方法的基本。
(2) 目的原因分析的思考方式作业分析的结果与改善结合在一起时,分析每个作业的目的、原因、技能就可知道改善方案;不过一般在分析时能记在头脑中,经常忘了记录;改善事项是要整理、发展的,为了给别人说明,最好是都记录下来。
(3) 目的原因分析①作业的确认:内容、方法、时间、移动距离②想好每个作业的目的,并记录下来‘此作业的目的是什么?’ 记录例:为了……③想好每个作业的原因,并记录下来‘为什么要做此作业?’ 例:因为……④想好每个作业的机能,并记录下来‘此作业能起到什么作用?’ 例:起……的作用⑤记录改善方案‘内容以跟排除有关的内容为主’ 例:可否……☺改善的目标应从“重点思考”中设想,即使改善的课题本身再有魅力,但从其改善效果来看没有期待价值时,应考虑其它改善项目。
☺重点思考判断要点(1)为了促进提高安全性、减轻疲劳、提高质量、提高生产性、费用节俭的有效改善活动,准确无误地掌握好现场或作业中的需要改善的问题就是改善的目的;(2)安全(让作业人员能安心工作);(3)舒适(能减轻作业人员的疲劳),好(提高产品质量);(4)快(缩短作业时间);便宜(尽量减少经费)(1) 考虑排除(E : Eliminate)带着有些事情或作业没有也可以的疑问,不要去做不必要的事情,排除对整个改善都有必要。
(2) 考虑结合与分散(C : Combine)应考虑不能排除的事情或作业用什么方法去做才好呢?不要受传统观念或偏见的影响,尽量用简单的方法去重新整理思路,这就是结合和分散。
(3) 考虑交替和代替(R : Rearrange)在这里我们应探讨什么时候进行,按什么顺序来进行,用什么方法去做才容易进行作业等等,有时这么做会有很大的改善效果。
(4) 考虑简化(S : Simplify)简化是一个不能缺少的重要的一点,应考虑每个作业的简化,舒适,缩短距离,减轻重量等方面的改善。
(1) 是继续生产还是重复生产,要不就是个别订单生产?(2) 批量(LOT)的大小?(3) 此工序的完成标准对成品有何意义? (4) 有没有设计变更的空间?(5) 变更材料的质量、形状、尺寸等的方法能否取消此作业或让它更容易?(1) 设备是否适合作业目的,比如利用自动化或专用化设备是否更简单? (2) 设备能力是否充分利用了?(3) 有没有提高设备运转率的余地?比如增员或有效利用自动运转时的时间? (4) 工器具不能再改善吗?比如能否改善附着数量,自动运转中能否附着等等? (5) 是否充分利用工具,比如使用方法是否恰当,能否组合起来使用等等?(1) 改善作业安排,能否缩短作业人员移动或搬运的距离?(2) 是否有效地利用作业空间,比如缩短材料或设备等之间的距离,减少在制品,利用立体空间,作业顺序是否整齐合理?(1) 能否有效的利用重力来改善,比如能否用滑动,是否可以考虑从上往下扔的方法? (2) 材料和产品是否放在方便拿的位置? (3) 搬运是否有人负责,能否搞专门化? (4) 有没有中介搬运,有没有积压? (5) 能否改善材料及产品的包装? (6) 搬运方法上有没有改善的余地?(1)此项作业从整个作业的最终目的来看有什么意义?(2) 此项作业所发生的真正原因在哪里? (3) 前后工序之间的关系如何? (4) 此项作业能否排除?(5) 此项作业的运转情况不能再改善吗? (6) 此项作业能否实现机械化? (7) 此项作业能否变更为手操作? (8) 此项作业在其他工序中受到什么影响? (9) 此项作业的发生频率是多少?1次或不规则? (10) 有没有作业时间的不规则性,其原因是? (11) 能否重新编排作业顺序? (1) 作业人员的名称、年龄、性别、工龄是多少? (2) 从此作业人员的体力,技术的角度分析是否最合适? (3) 作业速度有没有改善的余地? (4) 等待的发生是不是作业人员的责任? (5) 动作的顺序是否稳定?(6) 安全方面有没有问题? (7) 通道的宽度和采光是否充足?(8) 是否采取了消除可能影响作业环境的因素的手段? (9) 在附近通过的搬运车辆是否存在危险☺什么叫作业分析?为了推进作业改善及减少浪费,充分理解作业内容,掌握其组合是否有浪费,为了改善而分析要素作业的方法。