窑内结圈、结球的原因及处理措施
回转窑结圈的原因及处理方法

回转窑结圈的原因及处理方法1、结圈的危害回转窑“结圈”的部位一般在距窑口一定距离的固体燃料集中燃烧点附近的耐火窑衬上,厚度可达200-500 mm左右。
“结圈”对球团生产的危害有以下几方面:(1)降低产量,增加劳动强度窑圈一经形成,对燃料烧烧所产生的热气流势必起阻碍作用,如图-1所示。
热气流被部分阻挡在A区,影响了球团的焙烧效果。
同时,由于链篦机上生球的干燥、预热过程是利用窑尾废气进行的,故此,结圈也对生球的干燥、预热产生不良影响。
具体地说,就是透气性差,火焰不进,后部温度低,干燥时水分不易脱除,生球爆裂、粉化严重,成品率低,从而降低了劳动生产率。
另外,圈结形成后,如不及时处理,就会使圈的纵向长度、厚度增加,当圈掉下时,必然增加工人的劳动强度,有时甚至需停机处理,也影响了球团矿的产量。
(2) 增加了设备负荷如图-1所示,一定面积及厚度的结圈使物料流被阻于B区,此时,被阻的料量要高出正常时许多,加之圈本身的重量,必然增加了托轮、轴承的磨损,同时,增加了电机的负荷,甚至烧毁。
(3) 浪费能源在实际看火操作中,当出现“结圈”现象后,由于热气流被阻于A区,为保证链篦机的干燥和预热效果,看火工往往采用加大给煤量的方式,这无疑造成了能源浪费。
2、结圈的原因结圈的原因,在生产中主要可以归纳为操作不当。
具体地说,是由于上料量过大,干燥效果差,生球爆裂,粉化严重,致使透气性差,使得引风机抽动火焰的作用不明显,火焰只在窑内一定距离燃烧。
在大于1 200℃的高温下,未完全氧化的Fe3O4就与磁铁矿中一定数量的SiO2发生反应形成液相。
2Fe3O4+3SiO2+2CO=3Fe2SiO4+2CO22FeO+SiO2=Fe2SiO4另外,当给煤量较大时,在1 150℃条件下,Fe2O3也会部分分解为Fe3O4,与SiO2作用而生成2FeO·SiO2,形成渣相粘结。
这就使得物料在流经焙烧带时,所产生的液相、渣相极易粘附在窑衬的表面,同时粘结物料而产生结圈现象。
回转窑结圈的影响因素及解决措施

回转窑结圈的影响因素及解决措施-----龙仕连我司从11月23日开始窑内断断续续出现少量漏料,并出现了三次大料球,严重影响到窑的正常运转,公司及部门领导高度重视。
经分析是窑23米处结后圈导致窑尾漏料和结料球。
于25日开始处理后圈:1、窑减产到350 t/h煅烧;2、窑头煤管每个班移动两次,-200~+100冷热交替处理;3、每班清理煤管头部积料结焦4次,以保证头煤燃烧好,火焰集中;4、控制煤粉细度及水分,以保证煤粉燃烧效果(煤磨出磨温度控制在63~65度,入磨温度<300度。
内部控制煤粉细度<6.0);5、适当提高熟料KH。
通过3天的处理,23料处后圈薄了很多,并有缺口,于28日窑恢复了365 t/h正常生产。
出现这样的工艺事故,我们必须深度反思。
特别是工艺管理人员和窑操作员一定要密切关注窑皮的变化趋势及原燃材料的变化,及时调整窑参数,保证窑正常运转。
下面让我们再次学习一下窑内结圈的成因、危害及解决措施:结圈是指回转窑在正常生产中,由于原燃材料的变化,或者操作和热工制度的影响,窑内因物料过度粘结,在特定的区域形成一道阻碍物料运动的环形、坚硬的圈。
这种现象在回转窑内是一种不正常的窑况,它破坏了正常的热工制度,影响窑内通风,造成窑内来料波动很大,直接影响到回转窑的产量、质量、消耗和长期安全运转。
而且处理窑内结圈费时费力,严重时需停窑停产,危害极其严重。
结圈的成因及危害:结圈的形成: 结圈实际上是在烧成带末端与放热反应带交界处形成的窑皮,是回转窑内危害最大的结圈。
在熟料煅烧过程中,当物料温度达到1280℃时,其液相黏度较大,最容易形成结圈,而且冷却后比较坚固,不易除掉。
在正常的煅烧情况下,后结圈体的内径部分往往被烧熔而掉落,保持正常的圈体内径。
如果在1 250~l 280℃温度范围内出现的液相量偏多,往往会形成妨碍生产的后结圈。
后结圈一般结在烧成带的边界或更远,开始是烧成带后边的窑皮逐渐增长、增厚,发展到一定程度即形成后结圈。
窑内结圈、结球的原因及处理措施

窑内结圈、结球的原因及处理措施中控室侯素克结圈是指窑内在正常生产中因物料过度黏结,在窑内特定的区域形成一道阻碍物料运动的环形、坚硬的圈。
这种现象在回转窑内是一种不正常的窑况,他破坏正常的热工制度,影响窑内通风,造成来料波动很大,直接影响回转窑的产量、质量、消耗和长期安全运转。
尤其频繁结圈的回转窑,不仅破坏了窑内正常热工制度,而且损害操作人员的身体健康,给生产造成经济损失。
引起回转窑结圈的因素很多,它与原料性质、生料成分、燃料的灰分和细度、窑型、窑内还原气氛及热工制度等有关。
1 结圈的形成回转窑内形成结圈的因素很多,但液相的产生和固化是结圈的主要形成过程。
而衬料温度、物料温度、煤灰和生料组成又是决定液相的生成和固化的主要因素。
在正常情况下,窑皮保持在200mm左右的厚度,该温度条件及区域内若熔化和固化的过程达到平衡,窑皮就不会增厚。
当熔化的少固化的多,其厚度增长到一定程度,即形成圈。
当衬料与物料的温差大时,在足够液相的条件下,圈体越结越厚。
1.1前结圈的形成前圈结在烧成带和冷却带交界处,由于风煤配合不好,或者煤粉粒度过粗,煤灰和水分大,影响煤粉燃烧,使黑火头长,烧成带像窑尾方向移动,熔融的物料凝结在窑口处使“窑皮”增厚,发展成前圈,或者由于煤粉落在熟料上,在熟料中形成还原性燃烧,铁还原成亚铁,形成熔点低的矿物或者由于煤灰分中氧化铝含量高而使熟料液相量增加,黏度增大,当遇到入窑二次风温降温、冷却,就会逐渐凝结在窑口处形成圈。
前圈形成的主要原因是煤粉的质量,熟料中溶剂矿物含量过高或氧化铝含量过高,燃烧器在窑口断面的位置不合理,影响煤粉燃烧,使结圈速度加快,前温急烧,导致温差相差大,造成液相冷却凝固形成前圈,1.2熟料圈的形成原因熟料圈(又称后圈),是结在窑内烧成带与放热反应带之间的圈,也是回转窑内危害最大的结圈。
造成熟料圈的原因很多,主要有生料化学成分,熟料圈行成往往在物料刚出现液相的地方,物料在1200~1300度范围内为防止结圈,配料时应考虑液相不易过多,液相黏度不易过大;原燃材料中的有害成分,原燃材料中的有害成分过多,降低物料的熔点,结圈的可能性就增大,正常情况下,此类结圈大多发生在放热反应带以后的地方;煤的影响,煤灰中氧化铝的含量较高,当煤灰掺入物料中时,使物料液相量增加往往易结圈;操作和热工制度的影响,头煤加入量较多,产生还原气氛,形成低熔点矿物,使液相提前出现,容易结圈,二三次风配合不当,火焰过长,液相提前出现,特别是在分解率高的情况下,结圈的可能性更大。
回转窑窑后结圈原因分析及处理方法

回转窑窑后结圈原因分析及处理方法巩义市恒昌冶金建材设备厂生产的1000t/d熟料生产线是由天津水泥工业设计研究院有限公司设计的,主要包括TDF型分解炉、单系列五级旋风预热器、Φ3.2m×50m回转窑及TC-836篦式冷却机。
自2007年2月以来,窑后频繁发生结圈、结球的工艺事故,巩义市恒昌冶金建材设备厂技术人员现将原因分析及解决措施介绍如下,供同仁参考。
1、结圈情况2007年3月19日最为严重,窑前返火,窑尾有漏料现象,无法操作煅烧,迫使停窑处理。
从窑内看,主窑皮长达22m,副窑皮长到窑尾,35~37m处形成后结圈,结圈最小孔洞呈不规则状,直径约l.5m,进窑观察该圈明显分为两层,且层次明确、清晰,第一层厚约150mm,呈黄白色,第二层厚约460mm,呈黑色,圈体非常致密。
对圈体取样分析见表1。
表1 圈体取样分析结果从表l可以看出,第一层硫碱含量较高,是硫碱圈,第二层明显是煤粉圈,熟料液相出现过早、过多导致结圈。
2、原因分析(1)由于2006年煤价不断上涨,加之公路运输距离远,为了降低成本,采用当地劣质煤煅烧,煤质下降,灰分高,挥发分低,发热值低,煤工业分析如表2、3。
实际生产中,煤可燃性差,煤粉燃烧不完全,大量煤灰不均掺入生料中,液相在窑后面提前出现,而未燃尽的煤灰产生沉积及液相的提前出现结圈。
(2)2007年以来,由于机械原因,高温风机l号轴与密封圈强烈摩擦,产生局部高温,使轴侧曲,水平振动最高达6.4mm/s。
为了降低振动,不得不降低高温风机转速,由原来的1130r/min降至l060r/min,有时更低,严重影响了窑内通风,加上煤质又差,更多的窑头燃烧不完全的煤粉沉积在窑后燃烧,使窑内后部温度升高,液相量增加,加速了窑后结圈的形成。
(3)为了处理窑后结圈,我厂在迫不得已的情况下停窑烧后圈,由于煤质差,二、三次风温低,燃料不完全或未燃烧的煤粉落在圈上及圈后的积料上,不断燃烧,造成物料发粘,不但圈未烧掉,反而越结越厚,这也是第一层圈形成的主要原因。
窑内结圈形成原因及处理

• 2、减少原燃料带入的有害成分 • 一般粘土中碱含量高,煤中含硫量高。因此,如果窑上经常 • • • •
出现结圈时,视结圈料分析结果,最好能改变粘土或原煤的供 货矿点,以减少有害成分对结圈的影响。 3、控制煤粉细度,确保煤粉充分燃烧 。 4、调整燃烧器控制好火焰形状确保风、煤混合均匀并有一定的 火焰长度。经常移动喷煤管,改变火点位置。 5、提高快转率 三个班统一操作方法,稳定烧成系统的热工制度。在保持喂 料喂煤均匀,加强物料预烧的基础上尽量加快窑速。采取薄料 快转、长焰顺烧,提高快转率,这对防止煤、料量可以不变,只要把喷煤管往外拉出一定距离, •
就可以把前圈烧垮。 (2)如果前圈离下料口比较近,并在喷嘴口前则将喷嘴往里伸, 使圈体温度下降而脱落。如果圈体不垮,则有两种处理方法 ① 把喷煤管往外拉出,同时适当增加内流风和二次风温度,这 样可以提高烧成温度,使烧成带前移,把火点落在圈位上。一 般情况下,圈能在2~3h内逐渐被烧掉。但在烧圈过程中应根 据进入烧成带料量多少,及时增减用煤量和调整火焰长短,防 止损伤窑皮或跑生料。 ② 如果用前一种方法无法把圈烧掉时,则把喷煤管向外拉出并 把喷嘴对准圈体直接烧。待窑后预烧较差的物料进入烧成带后, 火焰会缩得更短,前圈将被强火烧垮。但是必须指出,采用这 种处理方法,由于喷煤管拉出过多,生
• 在高温的热气流中被烧熔而掉落下来。当它再次被物料覆盖,
•
液相又凝固下来,如此周而复始。假如这个过程达到平衡,窑 皮就不会增厚,这属正常状态。如果粘挂上去的多,掉落下来 的少,窑皮就增厚。反之则变薄。当窑皮增厚达一定程度就形 成结圈。形成结圈的原因主要有如下几点: 1、入窑生料成分波动大,喂料量不稳定 实际生产过程中,窑操作员最头疼的事是人窑生料成分波动太 大和料量不稳定。窑内物料时而难烧时而好烧或时多时少,遇 到高KH料时,窑内物料松散,不易烧结,窑头感到“吃火”, 熟料fCaO高,或遇到料量多时都迫使操作员加煤提高烧成温度, 有时还要降低窑速;遇到低KH料或料量少时,窑操作上不能及 时调整,烧成带温度偏高
窑结大球原因分析
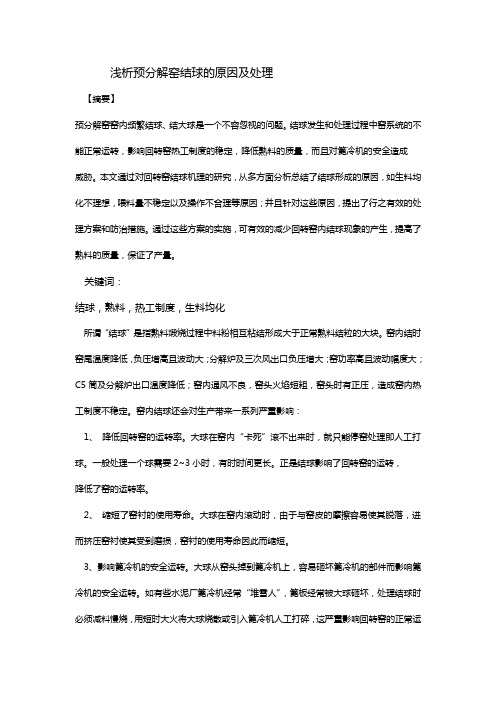
浅析预分解窑结球的原因及处理【摘要】预分解窑窑内频繁结球、结大球是一个不容忽视的问题。
结球发生和处理过程中窑系统的不能正常运转,影响回转窑热工制度的稳定,降低熟料的质量,而且对篦冷机的安全造成威胁。
本文通过对回转窑结球机理的研究,从多方面分析总结了结球形成的原因,如生料均化不理想,喂料量不稳定以及操作不合理等原因;并且针对这些原因,提出了行之有效的处理方案和防治措施。
通过这些方案的实施,可有效的减少回转窑内结球现象的产生,提高了熟料的质量,保证了产量。
关键词:结球,熟料,热工制度,生料均化所谓“结球”是指熟料煅烧过程中料粉相互粘结形成大于正常熟料结粒的大块。
窑内结时窑尾温度降低,负压增高且波动大;分解炉及三次风出口负压增大;窑功率高且波动幅度大;C5筒及分解炉出口温度降低;窑内通风不良,窑头火焰短粗,窑头时有正压,造成窑内热工制度不稳定。
窑内结球还会对生产带来一系列严重影响:1、降低回转窑的运转率。
大球在窑内“卡死”滚不出来时,就只能停窑处理即人工打球。
一般处理一个球需要2~3小时,有时时间更长。
正是结球影响了回转窑的运转,降低了窑的运转率。
2、缩短了窑衬的使用寿命。
大球在窑内滚动时,由于与窑皮的摩擦容易使其脱落,进而挤压窑衬使其受到磨损,窑衬的使用寿命因此而缩短。
3、影响篦冷机的安全运转。
大球从窑头掉到篦冷机上,容易砸坏篦冷机的部件而影响篦冷机的安全运转。
如有些水泥厂篦冷机经常“堆雪人”,篦板经常被大球砸坏,处理结球时必须减料慢烧,用短时大火将大球烧散或引入篦冷机人工打碎,这严重影响回转窑的正常运转,影响回转窑的热工制度的稳定,降低了熟料的质量。
因此,研究结球极其重要,绝不容忽视。
一、结球的机理简析近年来,很多人对回转窑结球的机理进行了探讨,研究报道中都有对结蛋料和正常料化学成分的对比,并探讨结蛋形成的机理。
有水泥专业技术人员曾经从预分解窑生料圈后面(过渡带)发现许多直径达1m的大球,并从中取出10个大球,从中间锯开,发现这些球中间都有一个褐色、细粒、白垩状的内核及灰褐色多孔状的外壳。
结圈形成的原因、预防措施和处理方法
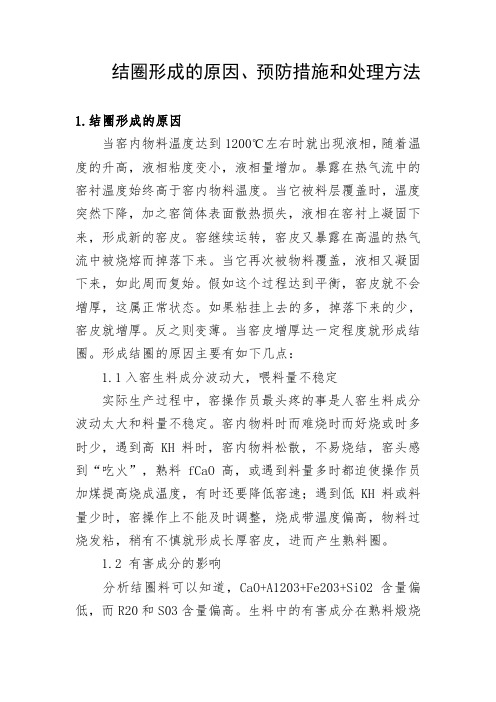
结圈形成的原因、预防措施和处理方法1.结圈形成的原因当窑内物料温度达到1200℃左右时就出现液相,随着温度的升高,液相粘度变小,液相量增加。
暴露在热气流中的窑衬温度始终高于窑内物料温度。
当它被料层覆盖时,温度突然下降,加之窑简体表面散热损失,液相在窑衬上凝固下来,形成新的窑皮。
窑继续运转,窑皮又暴露在高温的热气流中被烧熔而掉落下来。
当它再次被物料覆盖,液相又凝固下来,如此周而复始。
假如这个过程达到平衡,窑皮就不会增厚,这属正常状态。
如果粘挂上去的多,掉落下来的少,窑皮就增厚。
反之则变薄。
当窑皮增厚达一定程度就形成结圈。
形成结圈的原因主要有如下几点:1.1入窑生料成分波动大,喂料量不稳定实际生产过程中,窑操作员最头疼的事是人窑生料成分波动太大和料量不稳定。
窑内物料时而难烧时而好烧或时多时少,遇到高KH料时,窑内物料松散,不易烧结,窑头感到“吃火”,熟料fCaO高,或遇到料量多时都迫使操作员加煤提高烧成温度,有时还要降低窑速;遇到低KH料或料量少时,窑操作上不能及时调整,烧成带温度偏高,物料过烧发粘,稍有不慎就形成长厚窑皮,进而产生熟料圈。
1.2 有害成分的影响分析结圈料可以知道,CaO+A1203+Fe203+Si02含量偏低,而R20和S03含量偏高。
生料中的有害成分在熟料煅烧过程中先后分解、气化和挥发,在温度较低的窑尾凝聚粘附在生料颗粒表面,随生料一起人窑,容易在窑后部结成硫碱圈。
在人窑生料中,当MgO和R20都偏高时,R20在MgO引起结圈过程中充当“媒介”作用形成镁碱圈。
根据许多水泥厂的操作经验,当熟料中MgO>4.8%时,能使熟料液相量大量增加,液相粘度下降,熟料烧结范围变窄,窑皮增长,浮窑皮增厚。
有的水泥厂虽然熟料中MgO<4.0%,但由于R20的助熔作用,使熟料在某一特定温度或在窑某一特定位置液相量陡然大量增加,粘度大幅度降低,迅速在该温度区域或窑某一位置粘结,形成熟料圈。
关于窑结圈分析
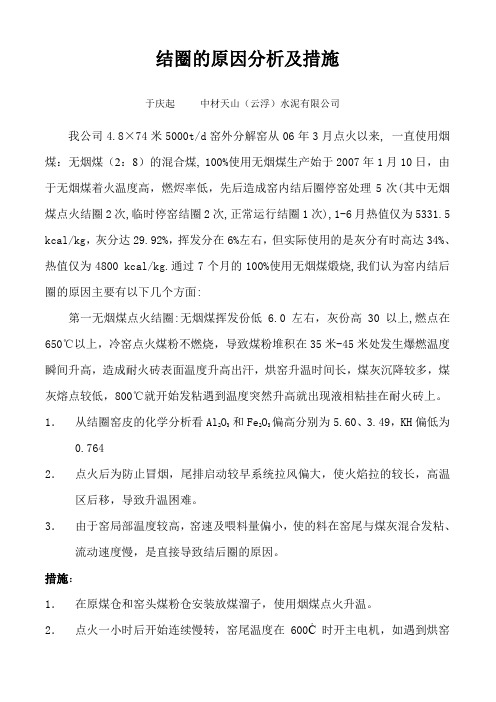
结圈的原因分析及措施于庆起中材天山(云浮)水泥有限公司我公司4.8×74米5000t/d窑外分解窑从06年3月点火以来,一直使用烟煤:无烟煤(2:8)的混合煤, 100%使用无烟煤生产始于2007年1月10日,由于无烟煤着火温度高,燃烬率低,先后造成窑内结后圈停窑处理5次(其中无烟煤点火结圈2次,临时停窑结圈2次,正常运行结圈1次),1-6月热值仅为5331.5 kcal/kg,灰分达29.92%,挥发分在6%左右,但实际使用的是灰分有时高达34%、热值仅为4800 kcal/kg.通过7个月的100%使用无烟煤煅烧,我们认为窑内结后圈的原因主要有以下几个方面:第一无烟煤点火结圈:无烟煤挥发份低 6.0左右,灰份高30以上,燃点在650℃以上,冷窑点火煤粉不燃烧,导致煤粉堆积在35米-45米处发生爆燃温度瞬间升高,造成耐火砖表面温度升高出汗,烘窑升温时间长,煤灰沉降较多,煤灰熔点较低,800℃就开始发粘遇到温度突然升高就出现液相粘挂在耐火砖上。
1.从结圈窑皮的化学分析看Al2O3 和Fe2O3偏高分别为5.60、3.49,KH偏低为0.7642.点火后为防止冒烟,尾排启动较早系统拉风偏大,使火焰拉的较长,高温区后移,导致升温困难。
3.由于窑局部温度较高,窑速及喂料量偏小,使的料在窑尾与煤灰混合发粘、流动速度慢,是直接导致结后圈的原因。
措施:1.在原煤仓和窑头煤粉仓安装放煤溜子,使用烟煤点火升温。
2.点火一小时后开始连续慢转,窑尾温度在600Ċ时开主电机,如遇到烘窑点火可在开启主传动后投入少量的生料,对窑内沉降的煤灰进行稀释。
3.调整好系统负压,保证窑内风速不易过大,使其提高窑前温度给煤粉燃烧创造有利条件。
4.投料时系统温度及设备满足的情况下,投料量尽量加大,如窑速2.5Rpm以上,投料量250t/h以上。
第二临时停窑结圈:一方面停窑不能过快,过度带高温物料已经开始出现液相,直接停窑容易造成粘挂窑皮,如需紧急停车也应立即将辅助电机转起来.另一方面由于临时停窑前后煤粉仓、原煤仓全部都是无烟煤,如果停窑时间不是太长窑内需要保温,给煤粉燃烧创造条件.首先停掉篦冷机关小冷却风机风门,关小排风适当喂入前煤,开启油泵保证窑前火焰明亮不熄火,并保证煤粉完全燃烧.第三正常运行结圈:分解炉煤粉不完全燃烧造成分解炉出口温度、中部温度开始下降分别为840℃和810℃,分解炉加煤以后分解炉温度不上一级温度上升至370℃,五级出口温度和窑尾温度升高(五级出口温度和分解炉出口温度出现倒挂现象),说明有煤粉通过五级进入窑内在窑的过度带进行燃烧,造成47-60米开始出现薄层并逐渐加厚,虽然采取减料控制分解炉用煤量和冷热交替方法处理结圈,但是效果不大最终造成后窑口倒料停窑处理.根据结圈窑皮的化学分析AL2O3含量为4.58、SO3达23.64、K2O为2.13,说明窑内还原气氛较浓煤灰沉降较多,有煤粉不完全然烧现象,通过上述现象我们认为结圈原因为:1.分解炉喂煤量大且不稳定,尤其是停磨以后断煤现象更加严重,二、三次风温不稳定,没有完全燃烧的煤粉带入五级通过下料管入窑,在窑的过度带进行燃烧,造成窑尾温度升高,在47-60米开始出现薄层并逐渐加厚,这是结后圈的主要原因。
窑内结球的原因分析及预防
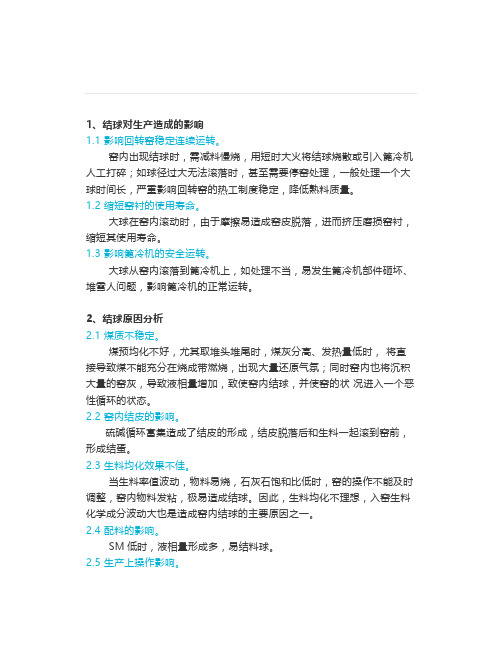
1、结球对生产造成的影响1.1 影响回转窑稳定连续运转。
窑内出现结球时,需减料慢烧,用短时大火将结球烧散或引入篦冷机人工打碎;如球径过大无法滚落时,甚至需要停窑处理,一般处理一个大球时间长,严重影响回转窑的热工制度稳定,降低熟料质量。
1.2 缩短窑衬的使用寿命。
大球在窑内滚动时,由于摩擦易造成窑皮脱落,进而挤压磨损窑衬,缩短其使用寿命。
1.3 影响篦冷机的安全运转。
大球从窑内滚落到篦冷机上,如处理不当,易发生篦冷机部件砸坏、堆雪人问题,影响篦冷机的正常运转。
2、结球原因分析2.1 煤质不稳定。
煤预均化不好,尤其取堆头堆尾时,煤灰分高、发热量低时,将直接导致煤不能充分在烧成带燃烧,出现大量还原气氛;同时窑内也将沉积大量的窑灰,导致液相量增加,致使窑内结球,并使窑的状况进入一个恶性循环的状态。
2.2 窑内结皮的影响。
硫碱循环富集造成了结皮的形成,结皮脱落后和生料一起滚到窑前,形成结蛋。
2.3 生料均化效果不佳。
当生料率值波动,物料易烧,石灰石饱和比低时,窑的操作不能及时调整,窑内物料发粘,极易造成结球。
因此,生料均化不理想,入窑生料化学成分波动大也是造成窑内结球的主要原因之一。
2.4 配料的影响。
SM低时,液相量形成多,易结料球。
2.5 生产上操作影响。
①喂料不稳定。
中控操作具有滞后特点,有时跟不上喂料的变化,加减煤不及时。
②中控室操作员缺乏经验,风煤料窑速匹配不好,温度控制波动大,热工制度长期得不到稳定,导致局部温度过高,提前出现液相,形成结球。
③有时为追求产量加煤过多,造成不完全燃烧现象,尤其头煤的影响,窑头负压控制不稳定,煤粉不完全燃烧或者煤管定位不合适,沉落入物料中熔融粘结翻滚而形成结球。
3.结球处理及预防(1)窑内出现料球一般表现为窑电流波动幅度大,窑电流峰值高有毛刺(伴随窑皮不平整,窑后有结圈现象),若结成大蛋在窑下可听见“咚…咚…”的响声,处理料球大蛋一般采用减产提高窑内通风加强煅烧,移动煤管冷热交替处理使其破裂,再放出到篦冷机固定蓖床或熟料破碎机上,人工清理打碎,存在一定的安全隐患,需特别注意穿戴好专用耐火服套装。
回转窑结圈的原因及处理方法
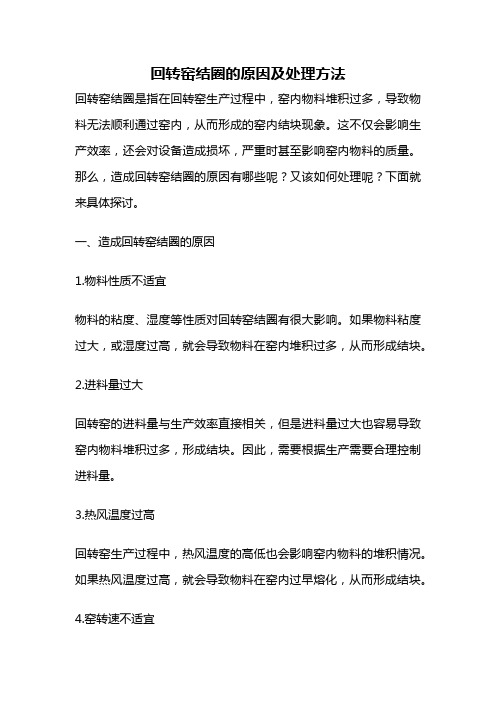
回转窑结圈的原因及处理方法回转窑结圈是指在回转窑生产过程中,窑内物料堆积过多,导致物料无法顺利通过窑内,从而形成的窑内结块现象。
这不仅会影响生产效率,还会对设备造成损坏,严重时甚至影响窑内物料的质量。
那么,造成回转窑结圈的原因有哪些呢?又该如何处理呢?下面就来具体探讨。
一、造成回转窑结圈的原因1.物料性质不适宜物料的粘度、湿度等性质对回转窑结圈有很大影响。
如果物料粘度过大,或湿度过高,就会导致物料在窑内堆积过多,从而形成结块。
2.进料量过大回转窑的进料量与生产效率直接相关,但是进料量过大也容易导致窑内物料堆积过多,形成结块。
因此,需要根据生产需要合理控制进料量。
3.热风温度过高回转窑生产过程中,热风温度的高低也会影响窑内物料的堆积情况。
如果热风温度过高,就会导致物料在窑内过早熔化,从而形成结块。
4.窑转速不适宜回转窑的转速也会影响窑内物料的堆积情况。
如果转速过快,就会导致物料在窑内无法均匀分布,从而形成结块。
二、回转窑结圈的处理方法1.减少进料量当回转窑结圈发生时,可以适当减少进料量,以缓解窑内物料堆积过多的情况。
2.调整热风温度如果回转窑结圈是由于热风温度过高导致的,可以适当降低热风温度,以减少窑内物料的过早熔化。
3.调整窑转速如果回转窑结圈是由于窑转速不适宜导致的,可以适当调整窑转速,以保证物料在窑内均匀分布。
4.清理窑内物料当回转窑结圈严重时,需要停窑清理窑内物料。
清理时需要注意安全,避免对设备造成损坏。
5.加入流化剂在窑内加入一定量的流化剂,可以有效地缓解回转窑结圈现象。
流化剂可以使物料在窑内均匀分布,减少结块的情况。
6.调整物料配比如果回转窑结圈是由于物料配比不合理导致的,可以适当调整物料配比,以保证物料在窑内均匀分布,减少结块的情况。
回转窑结圈是一种常见的生产问题,多种因素都可能导致其发生。
因此,在回转窑生产过程中,需要做好预防措施,保证物料在窑内均匀分布,避免结块的发生。
同时,一旦发生回转窑结圈,需要及时采取相应的处理措施,以保证生产效率和产品质量。
窑内结球的有效调节措施

文献标识码: B
文 章 编 号 : 0 7 0 8 (0 8 0 — 1 0 10 — 3 9 2 0 ) 6 3 — 2
园国鳕圆国曰既羽 岛国
薛俊 东 -王艳春 z 张建 明 - , ,
( . 东水 泥丰润有 限责任公 司, 1冀 河北 唐 山 0 4 1; . 6 0 1 2 启新水泥 有限公司 中控 室 ,河北 唐 山 0 30 ) 6 0 0
( 编 辑 :徐 凤 娟 )
( 校对 : 沈 新 )
— —
调 节 后 的 熟 料 率值
( 收 原 稿 日期 :2 0 0 8 0 4
10
)
下 期 要 目
基于
L a bv ie
w
软 件 的 回 转 窑 筒 体 椭 圆度 测 量 仪
… … …
…
…
…
…
…
…
…
…
…
…
…
…
…
张
,
云,Βιβλιοθήκη 。黄如 昌,
聚 羧 酸 系液 态 高 效 减 水 剂 固 态 化 的 研 究
.
结球
.
运转
料 的烧失量 只有
0 28%
.
,
叫
(f
Ca O)
也 只有 0 3 %
.
说 明生 料 的易烧性很 好
。
为 降低 入 窑 物 料 的 分 解
口
,
率
速
,
我 们采 取 降低分解 炉 出
温度
,
并 提 高窑
作 【 者 简 介 】 薛俊 东 ( 19 7 4 )
一
,
男
,
毕 业 于 长 春 建 材 学校
窑结料球的原因及处理方法
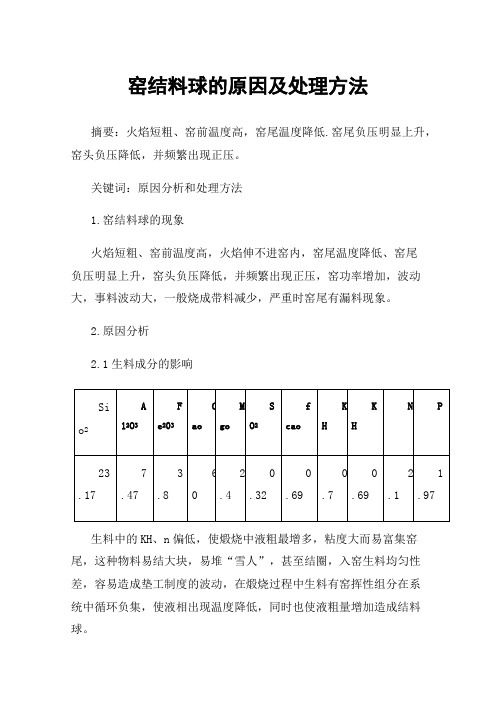
窑结料球的原因及处理方法摘要:火焰短粗、窑前温度高,窑尾温度降低.窑尾负压明显上升,窑头负压降低,并频繁出现正压。
关键词:原因分析和处理方法1.窑结料球的现象火焰短粗、窑前温度高,火焰伸不进窑内,窑尾温度降低、窑尾负压明显上升,窑头负压降低,并频繁出现正压,窑功率增加,波动大,事料波动大,一般烧成带料减少,严重时窑尾有漏料现象。
2.原因分析2.1生料成分的影响生料中的KH、n偏低,使煅烧中液粗最增多,粘度大而易富集窑尾,这种物料易结大块,易堆“雪人”,甚至结圈,入窑生料均匀性差,容易造成垫工制度的波动,在煅烧过程中生料有窑挥性组分在系统中循环负集,使液相出现温度降低,同时也使液粗量增加造成结料球。
2.2操作方法的影响用煤过多,产生还原气氛,物中三价铁还原成二价铁,易形成低熔点矿物液粗提早出现,易出“黄心料”,熟料质量差。
2.3热工制度的影响一、二、三次中配合不当,二次风温不稳定,低温火焰煅烧使物料预烧较好,液粗出现早,窑快转率低,窑事故较多,操作参数不合理,导致窑热工制度不稳定,哇煤管长时间不移动,后部窑皮生长快。
3解决措施3.1抓好进厂原燃材料质量,稳定生料成分1)化验室每周不定期对石灰石各开采区分别取样测其Cao质量,并确定搭配开采方案。
2)做好煤粉均化,搭配使用。
燃烧状况良好,火焰发亮,增长了高温带,提高了窑热力强度,避免了煤粉的不完全燃烧现象。
3)化验专职人员监督把关,不合格原料不准进厂,依质堆放,合理搭配使用。
4)对窑操作进行培训、考试,加强理论知识培训。
3.2调整配料方案KH、n适当高点,减少液相粘度和总量,防止液相过早出现,而结料球,结大块,结“雪人”的现象出现..3.3操作参数的制度1)分解炉860℃2)窑尾温度950-980℃3)3)喂料量:80-83t/h4)4)窑速:3.5-3.8r/min5)5)每班必须放料球两次6)6)每班要移动喷煤管两次.7)7)采用“三大一块”的操作思路8)3.4处理料球的方法9)1)喷煤管提前1小时全部伸入窑内煅烧10)2)在喂料量不变(80t/h)的情况下,将窑速由3.8r/min降至2.0r/mm煅烧30分钟。
回转窑系统结圈原因

回转窑系统结圈原因.事故怎样判断和安全处理(一)、回转窑结圈 1.造成结圈的主要原因a、精矿粉品位低,SIO2高在有FeO存在的情况下,容易生存低熔点硅酸盐矿物。
b、生球强度低,在运输过程中容易产生粉末。
c、链篦机干球焙烧强度低,入窑后再次产生粉末。
d、操作不当回转窑窑温度控制过高,造成局部高温。
e、煤粉灰分含水量量高,灰分的熔点低,当灰分的熔点低于或接近焙烧温度时容易结圈。
f、高温状态下停窑。
2.防止结圈的措施a、严格控制原、燃料成分达到技术要求。
b、提高生球强度。
c、控制焙烧质量,入窑球抗压强度控制在800N/个球以上杜绝粉末入窑。
d、严格控制窑温,不造成局部长时间高温。
e、严禁高温停窑。
3.回转窑清圈机处理方法(1)旧的方法、冷却法除圈:,除圈的人工方法。
采用风镐、钎子、大锤等工具(2)、新旧方法烧圈.热窑机械去除结圈:a、冷烧及热烧交替烧法。
首先减少或停止入窑料(视结圈程度而定),在窑内结圈处增加煤量和风量,提高结圈处温度,再停止喷煤降低结圈处温度这样反复处理使圈受冷热交替相互作有用,造成开裂而脱落。
;b、冷烧:在正常生产时,在结圈部位造成低温气氛使其自行脱落。
新型快速方法停窑用回转窑结圈清圈机快速处理结圈(二)、回转窑结块原因1、结块的原因:是由于生球质量差,在链篦机内粉化或链篦机焙烧球强度不够,在回转窑内破裂后结块或排入环冷机后粘结成块2.控制措施:a、严控进厂原、燃料质量,把好造球关;b、造球机启动控制;c、布料厚度与机速;d、提高生球和链篦机上干球质量;e、稳定热工制度防止局部出现高温。
3.结块处理方法:发现固定筛上有大块及时打碎或扒出。
(三)、回转窑红窑原因及处理方法回转窑调火岗位除经常观察窑内状况外,每小时检查窑体表面温度,窑体表面温度300℃左右时没有危险;如果超过400℃调火人员必须严加注意;温度达到400∽600℃在夜间可看出窑体颜色变化,若出现暗红色即红窑;当窑体温度超过650℃时,窑体变为亮红,窑体可能翘曲。
回转窑结圈的原因及处理方法

回转窑结圈的原因及处理方法回转窑是制造水泥的重要设备,而回转窑结圈是影响生产效率和质量的常见问题。
结圈的原因有很多,如窑内温度不均、烧成温度过低、原材料成分不合适等。
本文将从原因和处理方法两个方面详细介绍回转窑结圈问题。
一、结圈的原因1. 窑内温度不均:回转窑内部温度分布不均会导致部分区域的烧成程度不够,形成未熟料,容易粘在窑壁上,最终导致结圈。
2. 烧成温度过低:如果烧成温度过低,则无法将原材料完全反应,也容易导致未熟料粘附在窑壁上。
3. 原材料成分不合适:原材料中含有过多的游离SiO2、Al2O3等物质,会使得反应速率变慢,在高温下难以完全反应。
同时,如果含有过多的碱金属氧化物,则会使得产生大量液态相,增加了结圈的风险。
4. 进出料方式不当:进出料口位置设置不合理,或者进出料速度过快或过慢,都会导致窑内物料分布不均,从而增加结圈的风险。
二、处理方法1. 调整窑内温度:调整窑内温度是解决结圈问题的关键。
可以通过改变燃烧器位置、调整燃料供给量等方式来调整窑内温度分布,使得各个区域的温度均匀。
2. 提高烧成温度:提高烧成温度可以促进原材料反应,减少未熟料生成的可能性。
但是需要注意控制好温度,避免超出窑的承载能力。
3. 调整原材料成分:在生产过程中要严格控制原材料的成分,避免含有过多的游离SiO2、Al2O3等物质和碱金属氧化物。
如果发现原材料成分不合适,则需要及时停机清理,并重新投入符合要求的原材料。
4. 改善进出料方式:调整进出料口位置和速度可以改善窑内物料分布不均的问题。
可以采用多点进出料口、减缓进出料速度等方式来改善这一问题。
5. 定期清理窑壁:定期清理窑壁可以有效减少未熟料的积累,降低结圈的风险。
清理时需要注意安全,避免对设备造成损伤。
综上所述,回转窑结圈是影响水泥生产效率和质量的常见问题。
通过调整窑内温度、提高烧成温度、调整原材料成分、改善进出料方式和定期清理窑壁等方式可以有效解决这一问题。
回转窑窑后结圈的原因和处理结果

回转窑窑后结圈的原因和处理结果一、回转窑窑后结圈的原因回转窑是一种常用于石灰生产和水泥生产的设备,但在使用过程中,有时会出现窑后结圈的情况。
结圈是指窑内物料在烧结过程中出现结块现象,导致窑内热量传递不畅,影响生产效率和产品质量。
而窑后结圈的原因主要有以下几个方面:1.原料成分不稳定:回转窑生产过程中,原料成分的不稳定性是导致结圈的主要原因之一。
原料成分中的各种氧化物、硅酸盐和铝酸盐等物质,对烧结过程中的矿物相转化和结构稳定性起着重要作用。
如果原料成分的变化超出了窑内控制范围,就容易引起结圈。
2.燃烧条件不理想:回转窑的燃烧条件对结圈问题也有一定影响。
燃料的选择、供氧方式、燃烧温度等因素都会影响窑内气氛的稳定性和热量分布情况。
如果燃烧条件不理想,窑内温度分布不均匀,就容易导致结圈的发生。
3.窑内温度过高:窑内温度是影响回转窑结圈的重要因素之一。
当窑内温度过高时,原料中的一些物质会发生过度烧结,形成块状物质,从而导致结圈。
窑内温度过高可能是由于燃烧条件不理想、窑内热量分布不均匀等原因引起的。
4.窑内物料层厚度不均匀:窑内物料层厚度的不均匀也容易导致结圈。
如果窑内物料层厚度不均匀,热量传递不均匀,就会导致部分物料温度过高,发生结圈。
二、回转窑窑后结圈的处理结果针对回转窑窑后结圈的问题,可以采取一系列措施进行处理,以保证生产的正常进行和产品质量的稳定。
1.优化原料配比和成分控制:通过对原料配比和成分的优化,可以减少原料成分的波动范围,降低结圈的发生概率。
同时,加强对原料成分的在线监测和调控,及时发现和处理原料成分异常,以避免结圈的发生。
2.改进窑内燃烧条件:优化燃料选择、供氧方式和燃烧温度等因素,改善窑内燃烧条件,提高窑内气氛的稳定性和热量分布的均匀性。
通过调整燃烧条件,可以有效预防和减少结圈的发生。
3.控制窑内温度:合理控制窑内温度,避免温度过高或过低,对窑内物料进行适当的保护和调控。
通过优化燃烧条件、改善窑内热量分布等措施,可以有效降低窑内温度的波动,减少结圈的发生。
窑内结大蛋和窑后结圈的现象、判断及处理

一、窑内结大蛋现象:窑尾温度降低,负压增高且波动大;三次风、分解炉出口负压增大;窑功率高,且波动幅度大; C5和分解炉出口温度低;在筒体外面可听到有振动声响;窑内通风不良,窑头火焰粗短,窑头时有正压。
原因判断:①配料不当,SM、IM低,液相量大,液相粘度低;②生料均化不理想,入窑生料化学成分波动大,导致用煤量不易稳定,热工制度不稳,此时易造成窑皮粘结与脱落,烧成带窑皮不易保持平整牢固,均易造成结大蛋;③喂料量不稳定,煤粉燃烧不完全,煤灰不均匀掺入物料;④火焰过长,火头后移,窑后局部高温,分解炉温度过高,使入窑物料提前出现液相;⑤煤灰分高,细度粗;原料中有害万分(碱、氯)高。
处理措施:①发现窑内结蛋后,应适当增加窑内拉风,顺畅火焰,保证煤粉燃烧完全,并减料慢窑,让大蛋“爬”上窑皮进入烧成带,用短时大火把大蛋烧散或烧小,以免进入篦冷机发生堵塞,或者砸坏篦板,同时要避免大蛋碰坏喷煤管。
②若已进入篦冷机,应及时止料,停窑,将大蛋停在低温区,人工打碎。
二、窑后结圈现象:火焰短粗,窑前温度升高,火焰伸不进窑内;窑尾温度降低,三次风和窑尾负压明显上升;窑头负压降低,并频繁出现正压;窑功率增加,波动大;来料波动大,一般烧成带料减少;严重时窑尾密封圈漏料。
原因判断:①生料化学成分影响;生料中SM偏低,使煅烧中液相量增多粘度大而易富集在窑尾;入窑生料均匀性差,造成窑热工制度容易波动,引起后结圈;煅烧过程中,生料中有害挥发性组分在系统中循环富集,从而使液相出现温度降低,同时也使液相量增加,造成结圈。
②煤的影响:煤灰中Al203较高,当煤灰集中沉落到烧成带末端的物料上会使液相出现温度大大降低,液相增加,液相发粘,往往易结圈。
煤灰沉降量就大。
当煤粉粗、灰分高、水分大时,燃烧速度变慢,火焰拉长,高温带后移,窑皮拉长易结后圈。
③操作中热工制度的影响:用煤过多,产生还原气氛,物料中三价铁还原为二价铁,形成低熔点矿物,使液相提早出现,易结圈;一、二次风配合不当,火焰过长,使物料预烧很好,液相出现早,也易结圈;窑喂料过多,操作参数不合理导致热工制度不稳定,窑速波动大,也易结圈。
干法窑结后圈的形成及处理
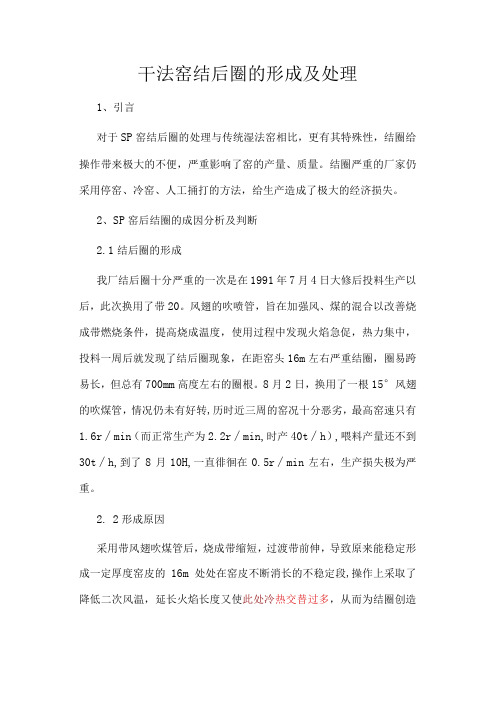
干法窑结后圈的形成及处理1、引言对于SP窑结后圈的处理与传统湿法窑相比,更有其特殊性,结圈给操作带来极大的不便,严重影响了窑的产量、质量。
结圈严重的厂家仍采用停窑、冷窑、人工捅打的方法,给生产造成了极大的经济损失。
2、SP窑后结圈的成因分析及判断2.1结后圈的形成我厂结后圈十分严重的一次是在1991年7月4日大修后投料生产以后,此次换用了带20。
风翅的吹喷管,旨在加强风、煤的混合以改善烧成带燃烧条件,提高烧成温度,使用过程中发现火焰急促,热力集中,投料一周后就发现了结后圈现象,在距窑头16m左右严重结圈,圈易跨易长,但总有700mm高度左右的圈根。
8月2日,换用了一根15°风翅的吹煤管,情况仍未有好转,历时近三周的窑况十分恶劣,最高窑速只有1.6r∕min(而正常生产为2.2r∕min,时产40t∕h),喂料产量还不到30t∕h,到了8月10H,一直徘徊在0.5r∕min左右,生产损失极为严重。
2.2形成原因采用带风翅吹煤管后,烧成带缩短,过渡带前伸,导致原来能稳定形成一定厚度窑皮的16m处处在窑皮不断消长的不稳定段,操作上采取了降低二次风温,延长火焰长度又使此处冷热交替过多,从而为结圈创造了条件。
另外,可能是衬砖因素所致,我们一般在2〜18m范围内使用普通镁络砖,而在18〜25m处则使用磷酸盐砖。
而此处结圈正是在镁破范围内,可能镁砖导致结圈的可能性更大,特别在温度不太高的情况下(1200℃左右)。
2.3结后圈的判断结后圈的部位及断面图见图1。
后结圈一旦形成,则在许多参数上可以判断,筒体上红外线扫描仪比较清楚地显示其位置,见图2,在窑尾压力表上也可以看出,见图3o3结后圈的处理方法3.1采用传统的处理湿法窑后结圈的方法我厂湿改干后第一次结后圈时间延续这么久,主要是因为缺乏处理干法窑结圈的经验,沿用传统的处理湿法窑后结圈的方法,效果不明显,我们采用了各种改变结圈部位温度的方法,如调整喷煤管位置、低喂料快窑速的快转薄烧法、低窑速长火焰法,甚至采用放生料法等均因圈根牢固而告失败。
回转窑焚烧炉窑内结圈原因分析及对策
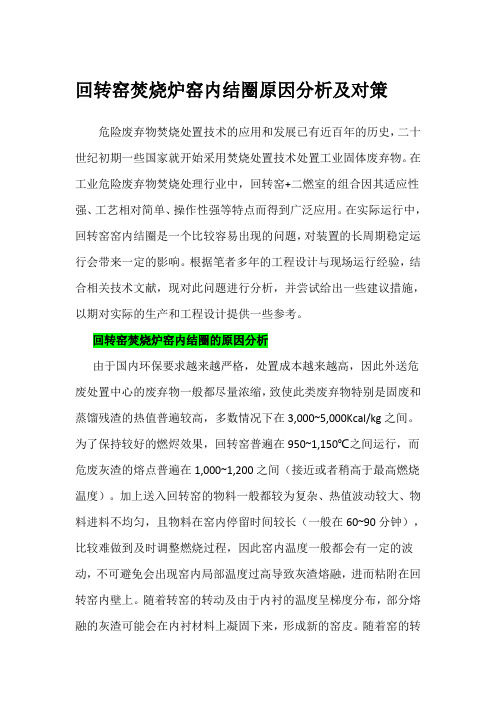
回转窑焚烧炉窑内结圈原因分析及对策危险废弃物焚烧处置技术的应用和发展已有近百年的历史,二十世纪初期一些国家就开始采用焚烧处置技术处置工业固体废弃物。
在工业危险废弃物焚烧处理行业中,回转窑+二燃室的组合因其适应性强、工艺相对简单、操作性强等特点而得到广泛应用。
在实际运行中,回转窑窑内结圈是一个比较容易出现的问题,对装置的长周期稳定运行会带来一定的影响。
根据笔者多年的工程设计与现场运行经验,结合相关技术文献,现对此问题进行分析,并尝试给出一些建议措施,以期对实际的生产和工程设计提供一些参考。
回转窑焚烧炉窑内结圈的原因分析由于国内环保要求越来越严格,处置成本越来越高,因此外送危废处置中心的废弃物一般都尽量浓缩,致使此类废弃物特别是固废和蒸馏残渣的热值普遍较高,多数情况下在3,000~5,000Kcal/kg之间。
为了保持较好的燃烬效果,回转窑普遍在950~1,150℃之间运行,而危废灰渣的熔点普遍在1,000~1,200之间(接近或者稍高于最高燃烧温度)。
加上送入回转窑的物料一般都较为复杂、热值波动较大、物料进料不均匀,且物料在窑内停留时间较长(一般在60~90分钟),比较难做到及时调整燃烧过程,因此窑内温度一般都会有一定的波动,不可避免会出现窑内局部温度过高导致灰渣熔融,进而粘附在回转窑内壁上。
随着转窑的转动及由于内衬的温度呈梯度分布,部分熔融的灰渣可能会在内衬材料上凝固下来,形成新的窑皮。
随着窑的转动,部分灰渣可能会被再次熔融,并达到一定的平衡,这样窑皮就不会增厚。
但是如果没有达到平衡,掉落下来的灰渣少,窑皮就会逐步增厚,达到一定程度后就形成结圈,如下图所示:形成结圈的主要原因有如下几点:1.回转窑的操作模式根据操作温度的不同,回转窑有两种操作模式:干渣模式和熔渣模式。
干渣操作模式在危废焚烧中最为常见,也被证明是最为可靠的一种操作模式,常规一般认为925℃以下为干渣模式,正常配伍可以保证灰渣不会熔融,此种操作模式结圈的可能性比较小。
回转窑结圈的原因及处理方法

回转窑结圈的原因及处理方法回转窑是一种常用于水泥生产过程中的设备,它通过高温和旋转运动将原料进行煅烧,以产生水泥熟料。
然而,有时候在回转窑的运行过程中,会出现结圈现象,这会严重影响设备的正常运行和水泥生产的质量。
了解回转窑结圈的原因及处理方法是至关重要的。
一、回转窑结圈的原因1. 原料成分不理想:回转窑的结圈问题与原料中的成分有很大的关系。
如果原料的化学成分不理想,其中含有过多的硫酸钠、硫酸镁等物质,将会导致煅烧过程中产生黏性物质,从而引起结圈。
2. 烧成温度过低:回转窑烧成温度过低也是导致结圈的一个重要原因。
当烧成温度过低时,原料中的化学反应无法完全进行,会导致部分物质残留在窑内,形成结圈。
3. 运行时间过长:长时间的运行也是回转窑结圈的一个重要原因之一。
当回转窑的运行时间超过其设计要求时,窑内结构会变得粘性,给结圈问题的发生提供了条件。
二、回转窑结圈的处理方法1. 优化原料配比:通过调整原料的化学成分,合理设计原料的配比,可以减少结圈问题的发生。
降低硫酸钠和硫酸镁等物质的含量,增加硅酸盐等成分,从而降低结圈的风险。
2. 提高烧成温度:增加回转窑的烧成温度可以有效地解决结圈问题。
适当提高温度可以加速化学反应的进行,降低黏性物质的生成,从而减少结圈发生的可能性。
3. 控制运行时间:合理控制回转窑的运行时间,确保在规定的运行时间内对窑内进行清理和维护。
定期对窑内进行清扫,清除可能产生结圈的物质,可以预防结圈问题的发生。
4. 使用防结圈剂:可以考虑在回转窑的煅烧过程中添加一定量的防结圈剂。
这些防结圈剂可以改变物料表面的化学性质,降低物料的粘性,减少结圈的风险。
5. 加强设备维护:定期对回转窑进行维护保养,保持设备的正常运行状态。
清理窑内的积存物,检查窑体和内衬的磨损情况,修复和更换损坏的部件,可以有效地预防结圈问题的发生。
总结与回顾:回转窑结圈问题是水泥生产过程中的常见现象,它会严重影响生产效率和产品质量。
窑内结球处理
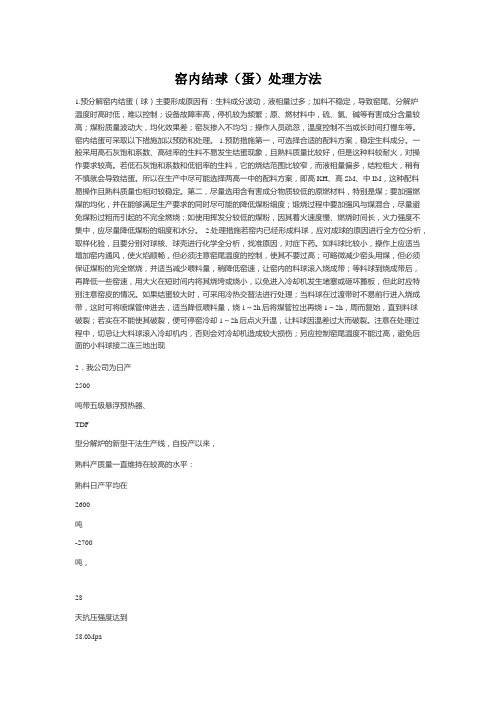
从理论分析,在水泥生料未出现液相之前,硅酸三钙不会大量生成。到达最低共熔温度
(一
般硅酸盐水泥熟料在通常煅烧制度下约为
1250
℃)后,开始出现液相。在高温液相中,硅
酸二钙和游离氧化钙都逐步溶解于液相中,以
Ca
2+
离子扩散与硅酸钙离子、硅酸二钙反应,
形成硅酸盐水泥的主要矿物硅酸三钙。其反应式如下:
C
2
2.8
-
3.0r/min
运转,
这样窑内物料的填充率过大,
也影响了窑内的通风,
增大了窑内的还原气氛。
在这种高还原气氛的作用下,多种共熔物中的部分
Fe
2
O
3
转变为
FeO
,进一步降低了共熔矿
物的软化温度而提早出现液相。
1.3
进厂煤的质量较差且波动较大
由于煤炭供应紧张,
造成了进厂煤的质量较差,
煤灰分较高且波动较大,
至出现了头尾煤的倒挂,
这样煤粉的燃烧不完全,
造成后燃烧现象的出现,
使窑皮过厚过长,
更加重了窑内还原性气氛。
1.2.3
由于入窑生料
KH
值过低,铁、铝含量增高,煤粉中的灰分增加,操作参数不合理等
诸多因素的出现,导致窑系统结后圈严重。
1.2.4
为加强熟料的锻烧,中控操作员采取降窑速的处理方法,使窑速长时间维持在
%
编号
K
2
O
Na
2
O
SO
3
CL
—
备注
I
1.57
0.24
0.80
0.42
II
1.51
0.27
0.67
0.39
- 1、下载文档前请自行甄别文档内容的完整性,平台不提供额外的编辑、内容补充、找答案等附加服务。
- 2、"仅部分预览"的文档,不可在线预览部分如存在完整性等问题,可反馈申请退款(可完整预览的文档不适用该条件!)。
- 3、如文档侵犯您的权益,请联系客服反馈,我们会尽快为您处理(人工客服工作时间:9:00-18:30)。
窑内结圈、结球的原因及处理措施
中控室侯素克结圈是指窑内在正常生产中因物料过度黏结,在窑内特定的区域形成一道阻碍物料运动的环形、坚硬的圈。
这种现象在回转窑内是一种不正常的窑况,他破坏正常的热工制度,影响窑内通风,造成来料波动很大,直接影响回转窑的产量、质量、消耗和长期安全运转。
尤其频繁结圈的回转窑,不仅破坏了窑内正常热工制度,而且损害操作人员的身体健康,给生产造成经济损失。
引起回转窑结圈的因素很多,它与原料性质、生料成分、燃料的灰分和细度、窑型、窑内还原气氛及热工制度等有关。
1 结圈的形成
回转窑内形成结圈的因素很多,但液相的产生和固化是结圈的主要形成过程。
而衬料温度、物料温度、煤灰和生料组成又是决定液相的生成和固化的主要因素。
在正常情况下,窑皮保持在200mm左右的厚度,该温度条件及区域内若熔化和固化的过程达到平衡,窑皮就不会增厚。
当熔化的少固化的多,其厚度增长到一定程度,即形成圈。
当衬料与物料的温差大时,在足够液相的条件下,圈体越结越厚。
1.1前结圈的形成
前圈结在烧成带和冷却带交界处,由于风煤配合不好,或者煤粉粒度过粗,煤灰和水分大,影响煤粉燃烧,使黑火头长,烧成带像窑尾方向移动,熔融的物料凝结在窑口处使“窑皮”增厚,发展成前圈,或者由于煤粉落在熟料上,在熟料中形成还原性燃烧,铁还原成亚铁,形成熔点低的矿物或者由于煤灰分中氧化铝含量高而使熟料液相量增加,黏度增大,当遇到入窑二次风温降温、冷却,就会逐渐凝结在窑口处形成圈。
前圈形成的主要原因是煤粉的质量,熟料中溶剂矿物含量过高或氧化铝含量过高,燃烧器在窑口断面的位置不合理,影响煤粉燃烧,使结圈速度加快,前温急烧,导致温差相差大,造成液相冷却凝固形成前圈,
1.2熟料圈的形成原因
熟料圈(又称后圈),是结在窑内烧成带与放热反应带之间的圈,也是回转窑内危害最大的结圈。
造成熟料圈的原因很多,主要有生料化学成分,熟料圈行成往往在物料刚出现液相的地方,物料在1200~1300度范围内为防止结圈,配料时应考虑液相不易过多,液相黏度不易过大;原燃材料中的有害成分,原燃材料中的有害成分过多,降低物料的熔点,结圈的可能性就增大,正常情况下,此类结圈大多发生在放热反应带以后的地方;煤的影响,煤灰中氧化铝的含量较高,当煤灰掺入物料中时,使物料液相量增加往往易结圈;操作和热工制度的影响,头煤加入量较多,产生还原气氛,形成低熔点矿物,使液相提前出现,容易结圈,二三次风配合不当,火焰过长,液相提前出现,特别是在分解率高的情况下,结圈的可能性更大。
2 结圈的预防和处理
前结圈和熟料圈形成的主要因素是由于物料在不该产生液相的区域内产生液相,在衬料与物料间温差大的条件下容易产生结圈。
因此防止结圈的办法在于适当地减少物料中的初期液相量,尽量减少衬料和物料间的温差。
(1)选择适宜的配料方案,稳定生料成分,提高煅烧操作水平。
配料方案应采用较高饱和比和较高硅酸率适当减少熔媒矿物的配料方案,对防止结圈有利。
(2)降低煤粉细度,加强风煤混合,消除不完全燃烧。
(3)加大对进厂原燃材料质量的监管力度,减少原材料中有害成分的含量。
(4)在生产中要确定一个经济合理的产量指标,适当快速转窑操作,对防止回转窑结圈是一个有利措施。
窑内结球是预分解窑出现的一种不正常工况,结球严重的时候,会接二连三的出现,给生产带来影响,大球出窑后,掉到篦冷机上,还不容易通过熟料破碎金,造成停窑事故。
造成结球的因素有很多,总结主要有:
1.成分对结球的影响,生料中有害成分含量高时结球的主要原因,有害成
分含量高则促使液相量提前出现,过早形成“球核”在窑内翻滚,提
高结球的可能性。
2.厚料层操作是窑内结大料求的关键因素,在生产过程中,由于窑内物料
较多,料层厚,填充率大,造成窑内物料翻滚较慢,不灵活,易堆
积,特别在出现液相的过渡带,物料本身黏度较大,加之堆积,极易
形成料球(即大料球的核心),且越滚越大,形成大料求。
3.操作控制的不当,窑尾烟室温度过高,造成液相量提前出现,目前本厂
的原煤发热量高,灰分低,挥发分高,这种煤的特性极易燃烧,使高
温点出现位置较靠前,烟室温度控制1050左右即可,如果烟室温度过
高,极有可能是窑头煤用量过多,这样还容易在窑内产生还原气氛,
生成低熔点矿物,更易形成料球核心。
根据形成大球的原因,只要找准原因,采取相应措施,这样的现象均可避免。
1.限制原燃材料中的有害物质的含量,主要是石灰石中的有害成分与原煤
中的有害成分。
2.稳定生料成分,熟料煅烧时的液相量不易过大,液相量控制在25%左
右。
3.保证快窑速运转,只有快窑速运转可降低窑内物料的填充率。
4.合理用风,保证煤粉燃烧充分,减少煤粉不完全燃烧现象的发生。
5.加强操作控制,稳定入窑物料的分解率,稳定窑工况。
回转窑结圈、结球的因素是多方面的,只要找出问题的主要原因,本着“以防为主,以除为辅”的原则,煅烧操作中只有及时发现,及时处理,方法正确,结圈与结球问题才能真正得到解决。
从而实现回转窑的优质、高产、低耗、安全、文明生产。