活性石灰回转窑结圈原因分析及处理方法
回转窑窑内结球并且形成窑灰的解决方法

回转窑窑内结球并且形成窑灰的解决方法回转窑窑内结球是一种很常见的现象,水泥回转窑窑内结球的原因和处理时的相关措施,是每个用户所关心的问题。
窑内结球主要形成原因有:生料成分波动,液相量过多;加料不稳定,导致窑尾、分解炉温度时高时低,难以控制;设备故障率高,停机较为频繁;原、燃材料中,硫、氯、碱等有害成分含量较高;煤粉质量波动大,均化效果差;窑灰掺入不均匀;操作人员疏忽,温度控制不当或长时间打慢车等。
窑内结球可采取以下措施加以预防和处理。
(1)预防措施。
第一,可选择合适的配料方案,稳定生料成分。
一般采用高石灰饱和系数、高硅率的生料不易发生结球现象,且熟料质量比较好,但是这种料较耐火,对操作要求较高。
若低石灰饱和系数和低铝率的生料,它的烧结范围比较窄,而液相量偏多,结粒粗大,稍有不慎就会导致结球。
所以在生产中尽可能选择两高一中的配料方案,即高KH、高SM、中IM,这种配料易操作且熟料质量也相对较稳定。
第二,尽量选用含有害成分物质较低的原燃材料,特别是煤;要加强燃煤的均化,并在能够满足生产要求的同时尽可能的降低煤粉细度;煨烧过程中要加强风与煤混合,尽量避免煤粉过粗而引起的不完全燃烧;如使用挥发分较低的煤粉,因其着火速度慢、燃烧时间长,火力强度不集中,应尽量降低煤粉的细度和水分。
(2)处理措施。
若窑内已经形成料球,应对成球的原因进行全方位分析,取样化验,且要分别对球核、球壳进行化学全分析,找准原因,对症下药。
如料球比较小,操作上应适当增加窑内通风,使火焰顺畅,但必须注意窑尾温度的控制,使其不要过高;可略微减少窑头用煤,但必须保证煤粉的完全燃烧,并适当减少喂料量,稍降低窑速,让窑内的料球滚入烧成带;等料球到烧成带后,再降低一些窑速,用大火在短时间内将其烧垮或烧小,以免进入冷却机发生堵塞或砸坏篦板,但此时应特别注意窑皮的情况。
如果结球较大时,可采用冷热交替法进行处理;当料球在过渡带时不易前行进入烧成带,这时可将喷煤管伸进去,适当降低喂料量,烧1〜2h后将煤管拉出再烧1〜2h,周而复始,直到料球破裂;若实在不能使其破裂,便可停窑冷却1〜2h后点火升温,让料球因温差过大而破裂。
回转窑结圈的影响因素及解决措施

回转窑结圈的影响因素及解决措施-----龙仕连我司从11月23日开始窑内断断续续出现少量漏料,并出现了三次大料球,严重影响到窑的正常运转,公司及部门领导高度重视。
经分析是窑23米处结后圈导致窑尾漏料和结料球。
于25日开始处理后圈:1、窑减产到350 t/h煅烧;2、窑头煤管每个班移动两次,-200~+100冷热交替处理;3、每班清理煤管头部积料结焦4次,以保证头煤燃烧好,火焰集中;4、控制煤粉细度及水分,以保证煤粉燃烧效果(煤磨出磨温度控制在63~65度,入磨温度<300度。
内部控制煤粉细度<6.0);5、适当提高熟料KH。
通过3天的处理,23料处后圈薄了很多,并有缺口,于28日窑恢复了365 t/h正常生产。
出现这样的工艺事故,我们必须深度反思。
特别是工艺管理人员和窑操作员一定要密切关注窑皮的变化趋势及原燃材料的变化,及时调整窑参数,保证窑正常运转。
下面让我们再次学习一下窑内结圈的成因、危害及解决措施:结圈是指回转窑在正常生产中,由于原燃材料的变化,或者操作和热工制度的影响,窑内因物料过度粘结,在特定的区域形成一道阻碍物料运动的环形、坚硬的圈。
这种现象在回转窑内是一种不正常的窑况,它破坏了正常的热工制度,影响窑内通风,造成窑内来料波动很大,直接影响到回转窑的产量、质量、消耗和长期安全运转。
而且处理窑内结圈费时费力,严重时需停窑停产,危害极其严重。
结圈的成因及危害:结圈的形成: 结圈实际上是在烧成带末端与放热反应带交界处形成的窑皮,是回转窑内危害最大的结圈。
在熟料煅烧过程中,当物料温度达到1280℃时,其液相黏度较大,最容易形成结圈,而且冷却后比较坚固,不易除掉。
在正常的煅烧情况下,后结圈体的内径部分往往被烧熔而掉落,保持正常的圈体内径。
如果在1 250~l 280℃温度范围内出现的液相量偏多,往往会形成妨碍生产的后结圈。
后结圈一般结在烧成带的边界或更远,开始是烧成带后边的窑皮逐渐增长、增厚,发展到一定程度即形成后结圈。
宁钢石灰回转窑结圈的认识与处理分析

的, 同时使用 煤粉作 为 主要燃料 , 在操 作不 规范 时也
会加 速结 圈形 成 。首先石 灰石表 面 附带 的泥料在 石 灰石 物流 输送 阶段带 来易堵 料 、 污染 环境 、 磨 损胶 带
2 石 灰 回转 窑 结 圈主 要 危 害
回转 窑结 圈可 以形 成 任 意 形状 , 且 形 成 一定 厚 度 的窑皮 。一般 将 具 有一 定 高 度 的 、 由大 块 和燃 料
等 问题 。其 次 , 进入 预热 器 后这 些 泥 料 经过 高温 干 燥, 大部 分被 推杆 推 入 窑 内 。进 入 窑 内后 开始 受 抽
力 影 响悬 浮 在窑 内。再 与未完 全燃烧 的燃 料所 产生
的灰分 和石 灰石 内部 低熔 点杂 质 烧 结在 一 起 , 最 终 不 断 的翻滚 形成 大 块 或 泥饼 。为 判 断 其 主要 成 分 ,
c o mmi s s i o n e d i n J u n e 2 0 0 8, h a v e b e e n i n s t a b l e o p e r a t i o n a t p r e s e n t wi t h s o u n d e c o n o mi c a n d t e c h n i —
4 . 4 安 全 措 施
换, 该 过程 十分 重视 加 强 砌 筑 质量 的过 程 监 管 和 施
工 作业 人员 的安全监 管 。所 以如何 鉴别 和确 定清 理 的时 间和周 期 十分关 键 。
( 1 )护 目镜 、 手套 、 口罩 、 安 全标志 牌 。 ( 2 )高 温 隔热服 、 安全 帽 。 ( 3 )安 全 的走 行 通道 , 必要 的架子 和平 台 。 ( 4 )无关 人员 禁 止 停 窑 期 间进 入 窑 内, 必 要 时
窑内结圈、结球的原因及处理措施

窑内结圈、结球的原因及处理措施中控室侯素克结圈是指窑内在正常生产中因物料过度黏结,在窑内特定的区域形成一道阻碍物料运动的环形、坚硬的圈。
这种现象在回转窑内是一种不正常的窑况,他破坏正常的热工制度,影响窑内通风,造成来料波动很大,直接影响回转窑的产量、质量、消耗和长期安全运转。
尤其频繁结圈的回转窑,不仅破坏了窑内正常热工制度,而且损害操作人员的身体健康,给生产造成经济损失。
引起回转窑结圈的因素很多,它与原料性质、生料成分、燃料的灰分和细度、窑型、窑内还原气氛及热工制度等有关。
1 结圈的形成回转窑内形成结圈的因素很多,但液相的产生和固化是结圈的主要形成过程。
而衬料温度、物料温度、煤灰和生料组成又是决定液相的生成和固化的主要因素。
在正常情况下,窑皮保持在200mm左右的厚度,该温度条件及区域内若熔化和固化的过程达到平衡,窑皮就不会增厚。
当熔化的少固化的多,其厚度增长到一定程度,即形成圈。
当衬料与物料的温差大时,在足够液相的条件下,圈体越结越厚。
1.1前结圈的形成前圈结在烧成带和冷却带交界处,由于风煤配合不好,或者煤粉粒度过粗,煤灰和水分大,影响煤粉燃烧,使黑火头长,烧成带像窑尾方向移动,熔融的物料凝结在窑口处使“窑皮”增厚,发展成前圈,或者由于煤粉落在熟料上,在熟料中形成还原性燃烧,铁还原成亚铁,形成熔点低的矿物或者由于煤灰分中氧化铝含量高而使熟料液相量增加,黏度增大,当遇到入窑二次风温降温、冷却,就会逐渐凝结在窑口处形成圈。
前圈形成的主要原因是煤粉的质量,熟料中溶剂矿物含量过高或氧化铝含量过高,燃烧器在窑口断面的位置不合理,影响煤粉燃烧,使结圈速度加快,前温急烧,导致温差相差大,造成液相冷却凝固形成前圈,1.2熟料圈的形成原因熟料圈(又称后圈),是结在窑内烧成带与放热反应带之间的圈,也是回转窑内危害最大的结圈。
造成熟料圈的原因很多,主要有生料化学成分,熟料圈行成往往在物料刚出现液相的地方,物料在1200~1300度范围内为防止结圈,配料时应考虑液相不易过多,液相黏度不易过大;原燃材料中的有害成分,原燃材料中的有害成分过多,降低物料的熔点,结圈的可能性就增大,正常情况下,此类结圈大多发生在放热反应带以后的地方;煤的影响,煤灰中氧化铝的含量较高,当煤灰掺入物料中时,使物料液相量增加往往易结圈;操作和热工制度的影响,头煤加入量较多,产生还原气氛,形成低熔点矿物,使液相提前出现,容易结圈,二三次风配合不当,火焰过长,液相提前出现,特别是在分解率高的情况下,结圈的可能性更大。
回转窑窑后结圈原因分析及处理方法

回转窑窑后结圈原因分析及处理方法巩义市恒昌冶金建材设备厂生产的1000t/d熟料生产线是由天津水泥工业设计研究院有限公司设计的,主要包括TDF型分解炉、单系列五级旋风预热器、Φ3.2m×50m回转窑及TC-836篦式冷却机。
自2007年2月以来,窑后频繁发生结圈、结球的工艺事故,巩义市恒昌冶金建材设备厂技术人员现将原因分析及解决措施介绍如下,供同仁参考。
1、结圈情况2007年3月19日最为严重,窑前返火,窑尾有漏料现象,无法操作煅烧,迫使停窑处理。
从窑内看,主窑皮长达22m,副窑皮长到窑尾,35~37m处形成后结圈,结圈最小孔洞呈不规则状,直径约l.5m,进窑观察该圈明显分为两层,且层次明确、清晰,第一层厚约150mm,呈黄白色,第二层厚约460mm,呈黑色,圈体非常致密。
对圈体取样分析见表1。
表1 圈体取样分析结果从表l可以看出,第一层硫碱含量较高,是硫碱圈,第二层明显是煤粉圈,熟料液相出现过早、过多导致结圈。
2、原因分析(1)由于2006年煤价不断上涨,加之公路运输距离远,为了降低成本,采用当地劣质煤煅烧,煤质下降,灰分高,挥发分低,发热值低,煤工业分析如表2、3。
实际生产中,煤可燃性差,煤粉燃烧不完全,大量煤灰不均掺入生料中,液相在窑后面提前出现,而未燃尽的煤灰产生沉积及液相的提前出现结圈。
(2)2007年以来,由于机械原因,高温风机l号轴与密封圈强烈摩擦,产生局部高温,使轴侧曲,水平振动最高达6.4mm/s。
为了降低振动,不得不降低高温风机转速,由原来的1130r/min降至l060r/min,有时更低,严重影响了窑内通风,加上煤质又差,更多的窑头燃烧不完全的煤粉沉积在窑后燃烧,使窑内后部温度升高,液相量增加,加速了窑后结圈的形成。
(3)为了处理窑后结圈,我厂在迫不得已的情况下停窑烧后圈,由于煤质差,二、三次风温低,燃料不完全或未燃烧的煤粉落在圈上及圈后的积料上,不断燃烧,造成物料发粘,不但圈未烧掉,反而越结越厚,这也是第一层圈形成的主要原因。
回转窑结圈的原因
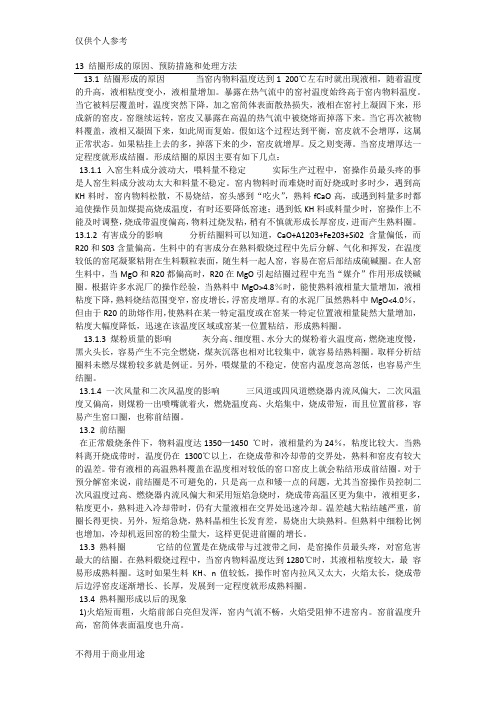
13 结圈形成的原因、预防措施和处理方法13.1 结圈形成的原因当窑内物料温度达到1 200℃左右时就出现液相,随着温度的升高,液相粘度变小,液相量增加。
暴露在热气流中的窑衬温度始终高于窑内物料温度。
当它被料层覆盖时,温度突然下降,加之窑简体表面散热损失,液相在窑衬上凝固下来,形成新的窑皮。
窑继续运转,窑皮又暴露在高温的热气流中被烧熔而掉落下来。
当它再次被物料覆盖,液相又凝固下来,如此周而复始。
假如这个过程达到平衡,窑皮就不会增厚,这属正常状态。
如果粘挂上去的多,掉落下来的少,窑皮就增厚。
反之则变薄。
当窑皮增厚达一定程度就形成结圈。
形成结圈的原因主要有如下几点:13.1.1 入窑生料成分波动大,喂料量不稳定实际生产过程中,窑操作员最头疼的事是人窑生料成分波动太大和料量不稳定。
窑内物料时而难烧时而好烧或时多时少,遇到高KH料时,窑内物料松散,不易烧结,窑头感到“吃火”,熟料fCaO高,或遇到料量多时都迫使操作员加煤提高烧成温度,有时还要降低窑速;遇到低KH料或料量少时,窑操作上不能及时调整,烧成带温度偏高,物料过烧发粘,稍有不慎就形成长厚窑皮,进而产生熟料圈。
13.1.2 有害成分的影响分析结圈料可以知道,CaO+A1203+Fe203+Si02含量偏低,而R20和S03含量偏高。
生料中的有害成分在熟料煅烧过程中先后分解、气化和挥发,在温度较低的窑尾凝聚粘附在生料颗粒表面,随生料一起人窑,容易在窑后部结成硫碱圈。
在人窑生料中,当MgO和R20都偏高时,R20在MgO引起结圈过程中充当“媒介”作用形成镁碱圈。
根据许多水泥厂的操作经验,当熟料中MgO>4.8%时,能使熟料液相量大量增加,液相粘度下降,熟料烧结范围变窄,窑皮增长,浮窑皮增厚。
有的水泥厂虽然熟料中MgO<4.0%,但由于R20的助熔作用,使熟料在某一特定温度或在窑某一特定位置液相量陡然大量增加,粘度大幅度降低,迅速在该温度区域或窑某一位置粘结,形成熟料圈。
石灰竖窑窑内结瘤及处理办法

石灰竖窑窑内结瘤及处理办法石灰回转窑结瘤石灰石生成石灰是一个简单的化学反应,热量输入过多造成温度过高或反应时间过长,就会出现过烧。
石灰相互粘连在一起,或与周围正常状态下的物料粘连起来,或粘附在窑壁上,形成结瘤。
一、轻微过烧粘连当窑温过高、频繁或大幅调产后会出现局部温度过高造成粘连,但采用敲打等方式很易破碎。
在窑底卸灰过程中观测到有个別烧融、粘连的情况。
降低产品活性度,影响窑体通透性,是结瘤的诱因。
解决办法:立即降低温度,检査设备,手工或自动卸料加速粘连物卸出,恢复窑体通透性,避免更严重的结瘤发生。
二、大面积结瘤轻微粘连如若未能及时发现,很快就会发展成大面积粘连结瘤,卡在窑底不能卸料,并在卸料区产生高温,损坏卸料平台和液压缸。
卸料平台温度急剧上升,窑顶料面出现倾斜,卸料平台动作次数明显增多。
损坏卸料平台、风帽和液压设备,严重影响石灰质量和产量,处理费时费力,短则10h以上,长则需要10~15日。
解决办法:1、立即降产降温避免结瘤。
2、打开卸料平台入孔,观测结瘤是否已经移动到卸料平台,如果没有就手动卸料,避免损坏卸料平台,加快结瘤的移动以避免粘结更大。
3、在结瘤凹陷处凿出小洞,用铁管引压缩空气直吹洞中,加速结瘤局部冷却。
产生的应力将结瘤分裂开,将较大的结瘤分裂成小块,顺利掏出。
如果是更大或多个结瘤,可将多个入孔打开,同时进行此操作。
4、如采结瘤块非常坚固,需要用风镐等工具,配合降温措施,将结瘤块打碎成小的结瘤块,从卸料平台掏出。
5、如果结瘤块过大,不能随着物料下降,则需停产,降至常温,进入窑内进行破碎。
三、粘在窑壁上这是较严重的结瘤,一般出现在煅烧带,往往伴随着大面积结瘤而产生,是不好处理的,属于严重的生产事故。
早期会出现窑顶料面倾斜,卸料不均衡,石灰生烧或过烧,质量严重分化,出现偏窑现象。
在窑壁外侧可测出高温点,严重时将外壁油漆烧毁,卸料平台处可见到红灰。
严重影响窑体寿命,处理不当会导致窑内耐材报废。
结圈形成的原因、预防措施和处理方法
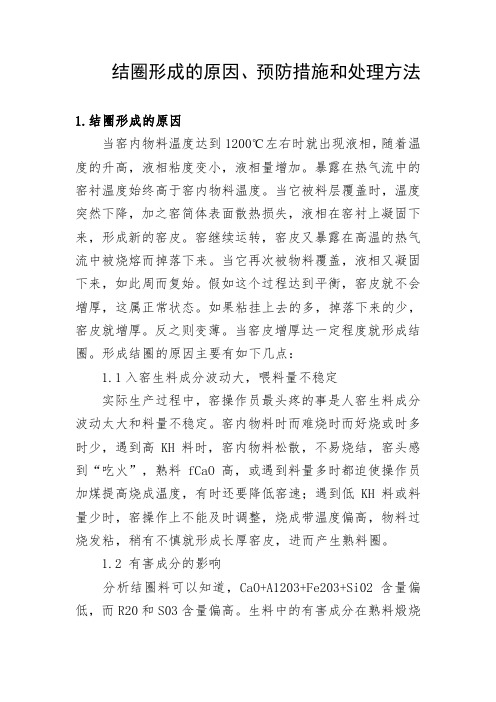
结圈形成的原因、预防措施和处理方法1.结圈形成的原因当窑内物料温度达到1200℃左右时就出现液相,随着温度的升高,液相粘度变小,液相量增加。
暴露在热气流中的窑衬温度始终高于窑内物料温度。
当它被料层覆盖时,温度突然下降,加之窑简体表面散热损失,液相在窑衬上凝固下来,形成新的窑皮。
窑继续运转,窑皮又暴露在高温的热气流中被烧熔而掉落下来。
当它再次被物料覆盖,液相又凝固下来,如此周而复始。
假如这个过程达到平衡,窑皮就不会增厚,这属正常状态。
如果粘挂上去的多,掉落下来的少,窑皮就增厚。
反之则变薄。
当窑皮增厚达一定程度就形成结圈。
形成结圈的原因主要有如下几点:1.1入窑生料成分波动大,喂料量不稳定实际生产过程中,窑操作员最头疼的事是人窑生料成分波动太大和料量不稳定。
窑内物料时而难烧时而好烧或时多时少,遇到高KH料时,窑内物料松散,不易烧结,窑头感到“吃火”,熟料fCaO高,或遇到料量多时都迫使操作员加煤提高烧成温度,有时还要降低窑速;遇到低KH料或料量少时,窑操作上不能及时调整,烧成带温度偏高,物料过烧发粘,稍有不慎就形成长厚窑皮,进而产生熟料圈。
1.2 有害成分的影响分析结圈料可以知道,CaO+A1203+Fe203+Si02含量偏低,而R20和S03含量偏高。
生料中的有害成分在熟料煅烧过程中先后分解、气化和挥发,在温度较低的窑尾凝聚粘附在生料颗粒表面,随生料一起人窑,容易在窑后部结成硫碱圈。
在人窑生料中,当MgO和R20都偏高时,R20在MgO引起结圈过程中充当“媒介”作用形成镁碱圈。
根据许多水泥厂的操作经验,当熟料中MgO>4.8%时,能使熟料液相量大量增加,液相粘度下降,熟料烧结范围变窄,窑皮增长,浮窑皮增厚。
有的水泥厂虽然熟料中MgO<4.0%,但由于R20的助熔作用,使熟料在某一特定温度或在窑某一特定位置液相量陡然大量增加,粘度大幅度降低,迅速在该温度区域或窑某一位置粘结,形成熟料圈。
回转窑后结圈的原因分析与解决措施

回转窑后结圈的原因分析与解决措施发布时间:2022-04-25T02:30:40.147Z 来源:《工程管理前沿》2022年1期作者:田硕[导读] 近年来,由于国家倡导节能减排的生产,从而加大了对一些浪费资源和污染比较大的企业改革田硕山东申丰水泥集团有限公司山东省枣庄市 277300引言:近年来,由于国家倡导节能减排的生产,从而加大了对一些浪费资源和污染比较大的企业改革,这就给了新型熟料回转窑一个重要的市场,让他们可以快速的发展起来。
熟料回转窑设备结构坚固、运转平稳、出窑产品质量高。
此外,在环保方面,利用熟料窑焚烧危险废物、垃圾,这不仅使废物减量化、无害化,而且将废物作为燃料利用,节省煤粉,做到废物的资源化。
关键词:回转窑后结圈解决措施摘要:熟料回转窑后结圈往往形成于烧成带和过渡带之间。
在熟料煅烧过程中,当窑内温度达到1280℃时,其液相粘度较大,此时,如果生料的KH、n率值较低,操作使窑内拉风较大,火焰太长,烧成带后边浮窑皮逐渐增长、增厚,发展到一定程度就形成了熟料回转窑的后结圈。
一、后结圈情况A企业配置一条5000t/d预分解熟料回转窑。
于2021年10月份在窑尾38米、43米处出现两道结圈,严重时窑尾出现漏料,窑投料量下降,熟料质量波动,窑况很不稳定。
二、原因分析2.1原煤内水偏高加剧了结圈的发生2021年煤价不断上涨,原煤库存为0吨,原煤随来随用,严重影响煤的均化效果。
煤粉内水偏高,窑头喷煤管燃烧速度慢、燃烧时间长,火焰的热力分散,燃烧时热力强度低,高温点后移,烧成带拉长,高温点不集中,熟料烧结不致密,二次风温偏低,恶性循环更加加剧了火焰燃烧速度。
物料预烧不好,容易产生不完全燃烧,没有燃尽的煤粉颗粒和CO不能在烧成带燃烧,部分聚集在窑尾燃烧,促使液相在过渡带提前出现,将未熔的物料黏结在一起,形成后结圈。
停窑后取结圈料化学分析结果发现:正常熟料烧失量为0.42%,结圈料为1.66%、2.06%也验证了这一点。
回转窑结圈的原因及处理方法
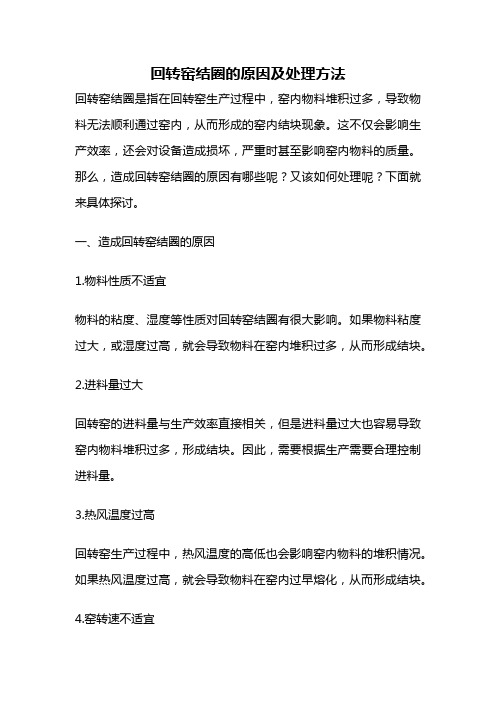
回转窑结圈的原因及处理方法回转窑结圈是指在回转窑生产过程中,窑内物料堆积过多,导致物料无法顺利通过窑内,从而形成的窑内结块现象。
这不仅会影响生产效率,还会对设备造成损坏,严重时甚至影响窑内物料的质量。
那么,造成回转窑结圈的原因有哪些呢?又该如何处理呢?下面就来具体探讨。
一、造成回转窑结圈的原因1.物料性质不适宜物料的粘度、湿度等性质对回转窑结圈有很大影响。
如果物料粘度过大,或湿度过高,就会导致物料在窑内堆积过多,从而形成结块。
2.进料量过大回转窑的进料量与生产效率直接相关,但是进料量过大也容易导致窑内物料堆积过多,形成结块。
因此,需要根据生产需要合理控制进料量。
3.热风温度过高回转窑生产过程中,热风温度的高低也会影响窑内物料的堆积情况。
如果热风温度过高,就会导致物料在窑内过早熔化,从而形成结块。
4.窑转速不适宜回转窑的转速也会影响窑内物料的堆积情况。
如果转速过快,就会导致物料在窑内无法均匀分布,从而形成结块。
二、回转窑结圈的处理方法1.减少进料量当回转窑结圈发生时,可以适当减少进料量,以缓解窑内物料堆积过多的情况。
2.调整热风温度如果回转窑结圈是由于热风温度过高导致的,可以适当降低热风温度,以减少窑内物料的过早熔化。
3.调整窑转速如果回转窑结圈是由于窑转速不适宜导致的,可以适当调整窑转速,以保证物料在窑内均匀分布。
4.清理窑内物料当回转窑结圈严重时,需要停窑清理窑内物料。
清理时需要注意安全,避免对设备造成损坏。
5.加入流化剂在窑内加入一定量的流化剂,可以有效地缓解回转窑结圈现象。
流化剂可以使物料在窑内均匀分布,减少结块的情况。
6.调整物料配比如果回转窑结圈是由于物料配比不合理导致的,可以适当调整物料配比,以保证物料在窑内均匀分布,减少结块的情况。
回转窑结圈是一种常见的生产问题,多种因素都可能导致其发生。
因此,在回转窑生产过程中,需要做好预防措施,保证物料在窑内均匀分布,避免结块的发生。
同时,一旦发生回转窑结圈,需要及时采取相应的处理措施,以保证生产效率和产品质量。
活性石灰回转窑工艺操作规程
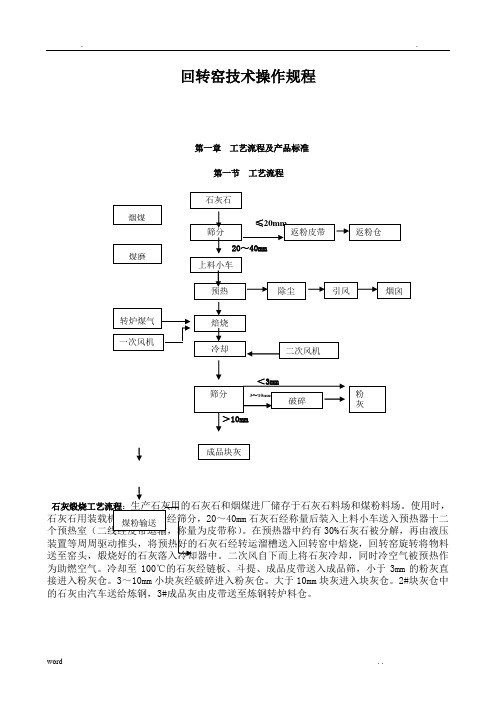
回转窑技术操作规程第一章工艺流程及产品标准第一节工艺流程生产石灰用的石灰石和烟煤进厂储存于石灰石料场和煤粉料场。
使用时,20~40mm石灰石经称量后装入上料小车送入预热器十二。
在预热器中约有30%石灰石被分解,再由液压为助燃空气。
冷却至100℃的石灰经链板、斗提、成品皮带送入成品筛,小于3mm的粉灰直接进入粉灰仓。
3~10mm小块灰经破碎进入粉灰仓。
大于10mm块灰进入块灰仓。
2#块灰仓中的石灰由汽车送给炼钢,3#成品灰由皮带送至炼钢转炉料仓。
第二节原料(石灰石)第三节燃料(烟煤)第四节主要经济指标第二章技术操作规程第一节开机操作接开机指令后,通知各岗位检查所属设备,检查本岗位所属设备,确认无误后,汇报工长,得到工长允许后,按下列顺序进行操作1挂上操作牌并记录2引入煤气,做爆发试验,准备点火3点火前通知其它各相关岗位4点火(执行点火操作标准)5按顺序开机待提升开机运转正常后,启动链板出灰机点火后:启动助燃风机—启动冷风套风机辅机转窑:挂上慢传联轴器—启动慢传电机()主机转窑:脱开慢传联轴器—启动主电机—调整窑速6向调度、工长汇报开机时间,向调度汇报煤气点火时间第二节停机操作正常停机分为熄火停窑和不熄火停窑,接停机指令后,按下列程序停机熄火停窑1、接停窑指令后,进行减料操作,做好停窑准备2、减料操作过程中,逐步降低风量、煤粉量和煤气量3、冷却器上部溜管插入钢钎,排空预热器推头上部物料。
4、停料后,停止喷煤粉,在窑内物料逐渐减少的过程中逐渐减少煤气量以及一次风、二次风量5、待窑内物料全部进入煅烧带后,停煤气及一次风,预热器及窑内料排空后停窑6、窑内料排空后,根据冬、夏季节生产情况,采取停引风机自然降温或降低引风量进行匀速降温7、停窑后,每隔30分钟转窑1/3~1/4圈,预热器进口温度降至500℃以下后,每隔60分钟砖窑1/3~1/4圈,直到窑冷却为止,以防窑变形8、停窑后,将冷却器内物料排空,同时处理预热器横梁上部结块。
回转窑结圈的原因及处理方法

回转窑结圈的原因及处理方法回转窑是制造水泥的重要设备,而回转窑结圈是影响生产效率和质量的常见问题。
结圈的原因有很多,如窑内温度不均、烧成温度过低、原材料成分不合适等。
本文将从原因和处理方法两个方面详细介绍回转窑结圈问题。
一、结圈的原因1. 窑内温度不均:回转窑内部温度分布不均会导致部分区域的烧成程度不够,形成未熟料,容易粘在窑壁上,最终导致结圈。
2. 烧成温度过低:如果烧成温度过低,则无法将原材料完全反应,也容易导致未熟料粘附在窑壁上。
3. 原材料成分不合适:原材料中含有过多的游离SiO2、Al2O3等物质,会使得反应速率变慢,在高温下难以完全反应。
同时,如果含有过多的碱金属氧化物,则会使得产生大量液态相,增加了结圈的风险。
4. 进出料方式不当:进出料口位置设置不合理,或者进出料速度过快或过慢,都会导致窑内物料分布不均,从而增加结圈的风险。
二、处理方法1. 调整窑内温度:调整窑内温度是解决结圈问题的关键。
可以通过改变燃烧器位置、调整燃料供给量等方式来调整窑内温度分布,使得各个区域的温度均匀。
2. 提高烧成温度:提高烧成温度可以促进原材料反应,减少未熟料生成的可能性。
但是需要注意控制好温度,避免超出窑的承载能力。
3. 调整原材料成分:在生产过程中要严格控制原材料的成分,避免含有过多的游离SiO2、Al2O3等物质和碱金属氧化物。
如果发现原材料成分不合适,则需要及时停机清理,并重新投入符合要求的原材料。
4. 改善进出料方式:调整进出料口位置和速度可以改善窑内物料分布不均的问题。
可以采用多点进出料口、减缓进出料速度等方式来改善这一问题。
5. 定期清理窑壁:定期清理窑壁可以有效减少未熟料的积累,降低结圈的风险。
清理时需要注意安全,避免对设备造成损伤。
综上所述,回转窑结圈是影响水泥生产效率和质量的常见问题。
通过调整窑内温度、提高烧成温度、调整原材料成分、改善进出料方式和定期清理窑壁等方式可以有效解决这一问题。
回转窑结圈的原因分析及防治
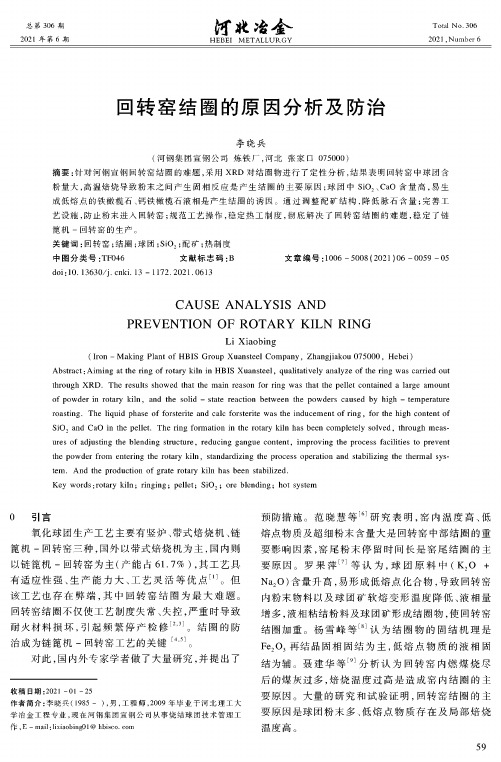
关键词:回转窑;结圈;球团;SiO2;配矿;热制度
中图分类号:TF046
文献标志码:B
doi:10. 5630/(. ccki. 03 -152.2021.0613
文章编号:1006 -5008(2021)06 -0059 -05
CAUSE ANALYSIS AND PREVENTION OF ROTARY KILN RING
粉量大,高温焙烧导致粉末之间产生固相反应是产生结圈的主要原因;球团中SiCO'CaO含量高,易生 成低熔点的铁橄榄石、钙铁橄榄石液相是产生结圈的诱因。通过调整配矿结构,降低脉石含量;完善工
艺设施,防止粉末进入回转窑;规范工艺操作,稳定热工制度,彻底解决了回转窑结圈的难题,稳定了链
篦机-回转窑的生产。
B
61.94
4.88
C
63.05
2. 34
D
60 .90
8 90
CaO 5. 91 2 33 1.3 3 0 34
MgO 1. 5 1.91 1.39 1. 5
TO. 0 89 2. 42 4 06 5. 5
S 0 57 0 09 5. 9 7 0 69
P 5. 52 0 07 0 06 0 06
AS2 O3
(b)黏结球团结圈物
图2结圈物衍射能谱
Fig. 2 Diffraction eneroy spactram of the ringing
由图2可知,两种结圈物的成分相似,其中 铁橄榄石(2FeO・St?)和钙铁辉石;对于黏结球团
Fa2O3代表赤铁矿,Fa2SiO4代表铁橄榄石,CaFx 结 ,其主要矿
2.2.2布料系统优化
布料系统主要设备有布料车、辐筛、流料板等,
回转窑窑后结圈的原因和处理结果

回转窑窑后结圈的原因和处理结果一、回转窑窑后结圈的原因回转窑是一种常用于石灰生产和水泥生产的设备,但在使用过程中,有时会出现窑后结圈的情况。
结圈是指窑内物料在烧结过程中出现结块现象,导致窑内热量传递不畅,影响生产效率和产品质量。
而窑后结圈的原因主要有以下几个方面:1.原料成分不稳定:回转窑生产过程中,原料成分的不稳定性是导致结圈的主要原因之一。
原料成分中的各种氧化物、硅酸盐和铝酸盐等物质,对烧结过程中的矿物相转化和结构稳定性起着重要作用。
如果原料成分的变化超出了窑内控制范围,就容易引起结圈。
2.燃烧条件不理想:回转窑的燃烧条件对结圈问题也有一定影响。
燃料的选择、供氧方式、燃烧温度等因素都会影响窑内气氛的稳定性和热量分布情况。
如果燃烧条件不理想,窑内温度分布不均匀,就容易导致结圈的发生。
3.窑内温度过高:窑内温度是影响回转窑结圈的重要因素之一。
当窑内温度过高时,原料中的一些物质会发生过度烧结,形成块状物质,从而导致结圈。
窑内温度过高可能是由于燃烧条件不理想、窑内热量分布不均匀等原因引起的。
4.窑内物料层厚度不均匀:窑内物料层厚度的不均匀也容易导致结圈。
如果窑内物料层厚度不均匀,热量传递不均匀,就会导致部分物料温度过高,发生结圈。
二、回转窑窑后结圈的处理结果针对回转窑窑后结圈的问题,可以采取一系列措施进行处理,以保证生产的正常进行和产品质量的稳定。
1.优化原料配比和成分控制:通过对原料配比和成分的优化,可以减少原料成分的波动范围,降低结圈的发生概率。
同时,加强对原料成分的在线监测和调控,及时发现和处理原料成分异常,以避免结圈的发生。
2.改进窑内燃烧条件:优化燃料选择、供氧方式和燃烧温度等因素,改善窑内燃烧条件,提高窑内气氛的稳定性和热量分布的均匀性。
通过调整燃烧条件,可以有效预防和减少结圈的发生。
3.控制窑内温度:合理控制窑内温度,避免温度过高或过低,对窑内物料进行适当的保护和调控。
通过优化燃烧条件、改善窑内热量分布等措施,可以有效降低窑内温度的波动,减少结圈的发生。
宝钢活性石灰回转窑结圈机理研究
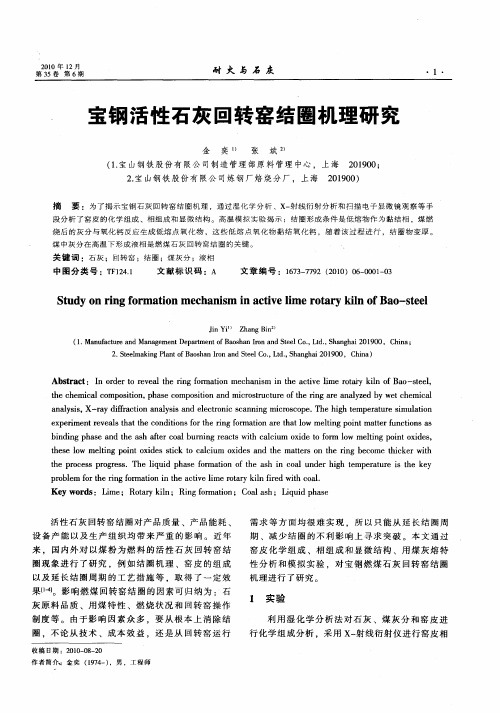
关 键 词 :石灰 ;回转窑 ;结圈 ;煤灰分 ;液相 中 图分 类 号 :T 141 F 2. 文 献 标 识 码 :A 文 章 编 号 :17— 72 (00 6 00 —3 6379 2 1)0—0 10
S u n i o m a in m e h n s a tv i er t r in o o se l t dyo rngf r to c a im i ci elm o a yk l fBa - t e n
第3卷 第6 5 期
21 0 0年 l 2月
硪 火 岛 不 度
・1・
宝钢活性石灰 回转窑结囤机理研 究
金 奕 。 张 斌
(. 1宝山钢铁 股份 有 限公 司制 造 管理部 原 料 管理 中心 ,上 海 2 1 0 ; 0 9 0
2 宝 山钢 铁股 份有 限公 司炼钢 厂焙 烧分 厂 ,上 海 2 1 0 ) . 0 9 0 摘 要 :为了揭示宝钢石灰回转窑结圈机理,通过湿化学分析、x 射线衍射分析和扫描电子显微镜观察等手 一
J Yi i
Z a gBi h n n
( . n fcuea dMa ae n p r n f a s a rna dSe l o, i.S a g a 0 9 0,C ia 1 Ma ua tr n n g me t De at t o h nI n te .L d, h n h i 1 0 me o B o C 2 hn ;
段 分析 了 窑 皮 的 化学 组成 、相 组成 和 显 微 结 构 。 高 温 模 拟 实 验 揭 示 :结 圈 形 成 条 件 是 低 熔 物 作 为 黏 结 相 ,煤 燃 烧 后 的 灰 分 与 氧 化 钙 反应 生成 低 熔 点 氧 化 物 ,这 些 低熔 点 氧 化 物 黏 结 氧化 钙 ,随 着 该 过 程 进 行 ,结 圈 物 变 厚 。 煤 中灰 分 在 高 温 下 形 成 液 相 是 燃 煤 石 灰 回 转 窑 结 圈 的 关键 。
回转窑焚烧炉窑内结圈原因分析及对策
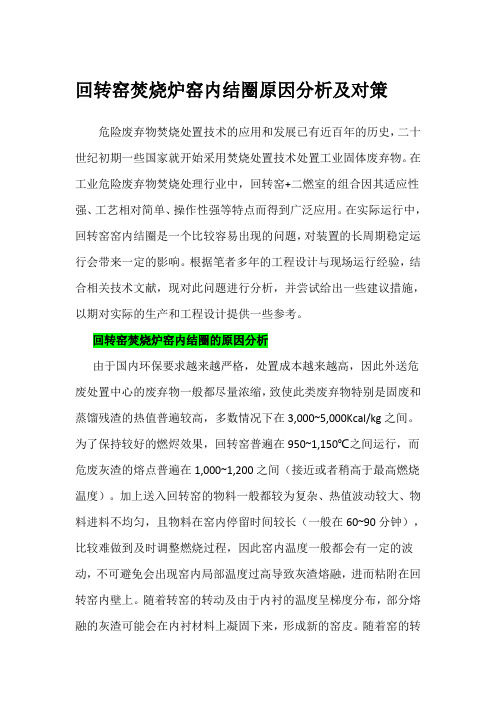
回转窑焚烧炉窑内结圈原因分析及对策危险废弃物焚烧处置技术的应用和发展已有近百年的历史,二十世纪初期一些国家就开始采用焚烧处置技术处置工业固体废弃物。
在工业危险废弃物焚烧处理行业中,回转窑+二燃室的组合因其适应性强、工艺相对简单、操作性强等特点而得到广泛应用。
在实际运行中,回转窑窑内结圈是一个比较容易出现的问题,对装置的长周期稳定运行会带来一定的影响。
根据笔者多年的工程设计与现场运行经验,结合相关技术文献,现对此问题进行分析,并尝试给出一些建议措施,以期对实际的生产和工程设计提供一些参考。
回转窑焚烧炉窑内结圈的原因分析由于国内环保要求越来越严格,处置成本越来越高,因此外送危废处置中心的废弃物一般都尽量浓缩,致使此类废弃物特别是固废和蒸馏残渣的热值普遍较高,多数情况下在3,000~5,000Kcal/kg之间。
为了保持较好的燃烬效果,回转窑普遍在950~1,150℃之间运行,而危废灰渣的熔点普遍在1,000~1,200之间(接近或者稍高于最高燃烧温度)。
加上送入回转窑的物料一般都较为复杂、热值波动较大、物料进料不均匀,且物料在窑内停留时间较长(一般在60~90分钟),比较难做到及时调整燃烧过程,因此窑内温度一般都会有一定的波动,不可避免会出现窑内局部温度过高导致灰渣熔融,进而粘附在回转窑内壁上。
随着转窑的转动及由于内衬的温度呈梯度分布,部分熔融的灰渣可能会在内衬材料上凝固下来,形成新的窑皮。
随着窑的转动,部分灰渣可能会被再次熔融,并达到一定的平衡,这样窑皮就不会增厚。
但是如果没有达到平衡,掉落下来的灰渣少,窑皮就会逐步增厚,达到一定程度后就形成结圈,如下图所示:形成结圈的主要原因有如下几点:1.回转窑的操作模式根据操作温度的不同,回转窑有两种操作模式:干渣模式和熔渣模式。
干渣操作模式在危废焚烧中最为常见,也被证明是最为可靠的一种操作模式,常规一般认为925℃以下为干渣模式,正常配伍可以保证灰渣不会熔融,此种操作模式结圈的可能性比较小。
回转窑结圈的机理和防治措施
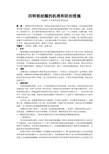
回转窑结圈的机理和防治措施太原理工大学现代科技学院冶金摘要:随着科学技术的发展,回转窑直接还原技术也有了很大的提高,特别是缺乏焦煤和天然气的地区,回转窑直接还原技术无疑对国家的建设提供了很大的帮助。
因此,如何更好、更快的生产,是当前所要面临的首要任务。
然而,由于工艺上的缺陷,结圈问题一直是回转窑使用上的一个常见障碍,它不仅影响设备的使用,更降低了生产效益。
因此,针对回转窑生产出现的结圈现象,将从使用的煤种、原料、回转窑的工作参数、热工制度等方面对结圈产生的原因进行分析与探讨,从而找出结圈产生的原因,并提出预防和处理结圈的措施及方法,提高设备的运转率,降低生产成本,提高经济效益。
关键词:回转窑;结圈;分析;处理方法l 引言随着钢铁企业的迅猛发展以及市场对钢铁质量的要求,国内许多大型企业为了提高冶金的质量及活性度,都上了不同规格的回转窑,以此满足企业冶炼高品质钢材的需求。
但是在使用燃煤式回转窑时,经常出现结圈,直接破坏正常的热工制度,影响回转窑的产量、质量和长期安全运行。
结圈现象已经成为当今钢铁企业一个重大问题,如果回转窑结圈问题得到有效控制,不仅能提高设备的运转率,而且能降低生产成本,提高产品质量,使综合经济水平有较大幅度的提高。
我通过自己查相关资料,找出了回转窑结圈的原因,来和大家分享。
2 现状结圈实际上是烧成带与吸热带反应交界处挂上一层窑皮,当窑皮达到一定厚度时,就形成结圈,结圈使窑内的物料填充系数增大,回转窑主电机电流增大,有时会出现跳闸现象,给窑炉的安全运行带来了隐患。
为了保证窑炉的正常运行,不得不停窑处理结圈,导致无法连续生产。
3 原因分析回转窑结圈是物理、化学、工艺诸因素综合作用的结果。
众所周知,回转窑的料层内部充满还原气氛,而窑气空间处于氧化状况。
这样窑衬经受着两种气氛不断交替的作用。
在回转窑旋转过程中,窑壁被料层理盖的时间约占旋转一周所需时间的四分之一,其余时间与热窑气(氧化气氛)接触。
回转窑结圈的原因及处理方法

回转窑结圈的原因及处理方法回转窑是一种常用于水泥生产过程中的设备,它通过高温和旋转运动将原料进行煅烧,以产生水泥熟料。
然而,有时候在回转窑的运行过程中,会出现结圈现象,这会严重影响设备的正常运行和水泥生产的质量。
了解回转窑结圈的原因及处理方法是至关重要的。
一、回转窑结圈的原因1. 原料成分不理想:回转窑的结圈问题与原料中的成分有很大的关系。
如果原料的化学成分不理想,其中含有过多的硫酸钠、硫酸镁等物质,将会导致煅烧过程中产生黏性物质,从而引起结圈。
2. 烧成温度过低:回转窑烧成温度过低也是导致结圈的一个重要原因。
当烧成温度过低时,原料中的化学反应无法完全进行,会导致部分物质残留在窑内,形成结圈。
3. 运行时间过长:长时间的运行也是回转窑结圈的一个重要原因之一。
当回转窑的运行时间超过其设计要求时,窑内结构会变得粘性,给结圈问题的发生提供了条件。
二、回转窑结圈的处理方法1. 优化原料配比:通过调整原料的化学成分,合理设计原料的配比,可以减少结圈问题的发生。
降低硫酸钠和硫酸镁等物质的含量,增加硅酸盐等成分,从而降低结圈的风险。
2. 提高烧成温度:增加回转窑的烧成温度可以有效地解决结圈问题。
适当提高温度可以加速化学反应的进行,降低黏性物质的生成,从而减少结圈发生的可能性。
3. 控制运行时间:合理控制回转窑的运行时间,确保在规定的运行时间内对窑内进行清理和维护。
定期对窑内进行清扫,清除可能产生结圈的物质,可以预防结圈问题的发生。
4. 使用防结圈剂:可以考虑在回转窑的煅烧过程中添加一定量的防结圈剂。
这些防结圈剂可以改变物料表面的化学性质,降低物料的粘性,减少结圈的风险。
5. 加强设备维护:定期对回转窑进行维护保养,保持设备的正常运行状态。
清理窑内的积存物,检查窑体和内衬的磨损情况,修复和更换损坏的部件,可以有效地预防结圈问题的发生。
总结与回顾:回转窑结圈问题是水泥生产过程中的常见现象,它会严重影响生产效率和产品质量。