主体结构及防水质量通病防治措施
2024年房建工程质量通病防治关键点控制

1、选择测量精度高的激光垂准仪或者激光经纬仪,并经过计 量检定合格后,方能投入到工程测量中,施工过程中对测量仪 器及时进行保养、校准。 2、墙、柱支撑,保证底部位置准确。 3、支模时要拉水平、竖向通线,并设竖向垂直度控制线,以 保证模板水平、竖向位置准确。 4、混凝土浇筑前,对模板轴线、支架、顶撑、螺栓进行认真 检查、复核。浇筑过程中,应派专人进行看模,发现胀模或位 移,应立即停止浇筑混凝土,对模板进行加固。
1、地基与基础 开挖深度控制不严格
【产生原因】
1、采用机械开挖,操作控制不严,局部多挖。 2、测量放线错误。 3、交底不清。
【预防措施】
1、土方开挖应按从上往下分层分段依次进行。如用机械挖土, 在接近设计坑底标高或边坡边界时应预留 200~300mm厚的 土层,用人工开挖和修整,边挖边修坡,以保证不扰动土和标 高符合设计要求。(若建筑物地基为灌注桩等桩基时机械挖土 应预留至少 500mm 厚以上,待桩桩基施工结束后再进行二次 挖土直至设计标高)。 2、遇标高超挖时,不得用松土回填,应用砂、碎石或低强度 等级混凝土填压(夯)实到设计标高;当地基局部存在软弱土 层,不符合设计要求时,应与勘察、设计建设部门共同提出方 案进行处理。
交流目的
本次质量通病防治交流主要以《科技技术质量管理手册》、《西北公司强制性做法》、《住宅质量 通病防治手册》为基础,结合昌建外滩壹号项目验收、交房过程中出现的质量突出问题,提出解决措施。
第二部分
务实 创新 开拓
常见质量通病防治
1、地基与基础 边坡塌方
放坡、喷锚
【解决措施】
1、将塌方或掉落的废渣清理干净,修补被破坏的基础结构, 处理尚未塌方或即将滑坡的部分; 2、回填夯实空洞部位,坡面重新布筋、加厚喷锚该处位置、 底部做好防掩埋的围护措施。
房间防水通病防治措施

房间防水通病防治措施
一.通病表现形式:
管根、墙根、板底等部位易出现渗漏。
二.防治技术措施:
L材料
(1)室内防水工程宜使用聚氨酯防水涂料、聚合物乳液防水涂料、聚合物水泥防水涂料和水乳型沥青防水涂料等水性或反应型防水涂料。
不得使用溶剂型防水涂料。
(2)室内长期浸水的部位不宜使用遇水产生溶胀的防水涂料。
(3)地漏、大便器、排水立管等穿越楼板的管道根部,宜使用丙烯酸酯建筑密封胶或聚氨酯建筑密封胶嵌填。
(4)热水管根部、套管与穿墙管间隙及长期浸水的部位,宜使用硅酮建筑密封胶(F类)嵌填。
2、施工
(1)厨卫钢筋混凝土楼板浇筑时须原浆收光,并宜做24小时蓄水试验。
如楼板存在非结构性贯穿裂缝,则须在施工防水前按照规范要求进行封闭修补处理。
(2)厨卫间混凝土翻边在浇筑前须进行基层凿毛、清理、润浆处理,混凝土浇筑完成后几何成型尺寸须规正、密实,与基层结合紧密。
模板支设严禁采用铁丝穿拉固定,应采用夹模或夹具等方式进行支设。
(3)卫生间排气道周围应浇筑混凝土强度等级不低于C20混凝土翻边,高度为相邻房间建筑完成面以下50mm,宽度为50mm o混凝土浇筑前需进行凿毛、清理以及润浆处理。
浇筑完成后需在其周边进行24小时蓄水试验。
(4)厨卫间竖向管洞在管道或地漏安装好后,其四周的封堵必须采用
顶撑或卡箍的支模方式浇筑细石混凝土,严禁采用铁丝穿拉、苯板吊模修
补。
浇筑前须将洞内清理干净,充分润湿并涂刷素水泥浆。
第一次浇筑细石
混凝土高度为洞高2/3,第二次浇筑混凝土高度为洞高1/3并低于结构面
IOmm o浇筑完成后需进行24小时蓄水试验。
主体结构工程有哪些质量问题及防治措施?

主体结构工程有哪些质量问题及防治措施?,造成拉墙筋位置无法按模数置于砂浆中,起不到拉墙筋的作用。
为了解决此问题,就必须改变传统的拉墙筋埋设方法,采用砼成型后打孔埋设的办法,确保位置正确。
(一)主体砼梁、柱模板拼缝处漏浆,表面不平整现象出现该现象的主要原因是使用木制模板时拼缝不严,或模板多次使用后已发生翘曲变形,或模板干燥后收缩及配制的模板时所钉的钉子松动造成。
为了从根本上杜绝此类现象的发生,首先改变传统的模板材料,选用目前广泛使用的成品木制木模,一是减轻了配模工作量,二是大大降低的模板的拼缝率,使得模板的缝隙相对较少,同时,对于模板之间的拼缝,为了确保不漏浆,在模板的端部加设一层接头补缝用的泡沫双面胶。
此种方法在近几年的工程实践中,已被广泛认同,是行之有效的办法。
(二)框架柱在层高位置出现柱头偏移歪斜,几何形状不规则的现象产生该现象的主要原因是在该位置梁柱交叉,加之施工工序一般都是砼柱模板分两次安装,两次浇筑,造成柱头部位的模板刚度不够,而且不容易固定造成的。
为了解决该质量通病可以采取以下措施:1、柱头模板专门配制,增加柱头模板与砼柱的搭接长度,增加模板的固定范围;2、增加模板的刚度。
在模板的四角加设角铁架,增加模板抵抗侧向砼施工时的侧向压力,减小模板变形;3、确保下部砼浇筑时上口不变形,保证柱几何尺寸,使得上部模板固定时,截面不变形。
(三)砼柱表面流浆,观感不佳造成此种现象的主要原因是上部柱模板安装时与下部柱砼接触不牢,缝隙过大,造成流浆,同时,砼在浇筑时洒落造成的。
为了解决此类问题,在安装上部砼柱模板时,在端部的接触面上贴一层拼缝用的泡沫双面胶,将缝隙密封。
对于局部的流浆,在砼浇筑完毕后,进行及时的清理。
通过本措施,此类质量通病基本可以杜绝。
(四)砼柱底烂根,出现蜂窝麻面,炸模等现象造成此类问题的主要原因是施工缝处理不当,根部模板不严密,过振造成的。
解决此类问题:1、在处理接头缝时要将接头位置清理干净,在浇灌砼前先要浇灌10-20cm厚的与砼成份相同的水泥砂浆,且每次砼分层振捣的厚度略小于振动器的长度,以便于振捣时,控制振捣的深度,不致过振;2、模板与底部砼相连接触的部位,粘一层泡沫双面胶,确保接触部位拼缝严密不漏浆;3、加强底部模板的刚度,增加一个固定的抱箍。
防水施工方法质量通病处理办法
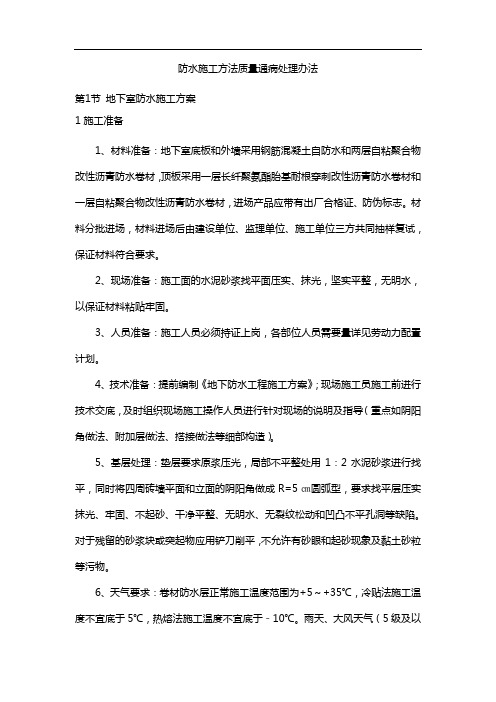
防水施工方法质量通病处理办法第1节地下室防水施工方案1施工准备1、材料准备:地下室底板和外墙采用钢筋混凝土自防水和两层自粘聚合物改性沥青防水卷材,顶板采用一层长纤聚氨酯胎基耐根穿刺改性沥青防水卷材和一层自粘聚合物改性沥青防水卷材,进场产品应带有出厂合格证、防伪标志。
材料分批进场,材料进场后由建设单位、监理单位、施工单位三方共同抽样复试,保证材料符合要求。
2、现场准备:施工面的水泥砂浆找平面压实、抹光,坚实平整,无明水,以保证材料粘贴牢固。
3、人员准备:施工人员必须持证上岗,各部位人员需要量详见劳动力配置计划。
4、技术准备:提前编制《地下防水工程施工方案》;现场施工员施工前进行技术交底,及时组织现场施工操作人员进行针对现场的说明及指导(重点如阴阳角做法、附加层做法、搭接做法等细部构造)。
5、基层处理:垫层要求原浆压光,局部不平整处用1:2水泥砂浆进行找平,同时将四周砖墙平面和立面的阴阳角做成R=5㎝圆弧型,要求找平层压实抹光、牢固、不起砂、干净平整、无明水、无裂纹松动和凹凸不平孔洞等缺陷。
对于残留的砂浆块或突起物应用铲刀削平,不允许有砂眼和起砂现象及黏土砂粒等污物。
6、天气要求:卷材防水层正常施工温度范围为+5~+35℃,冷贴法施工温度不宜底于5℃,热熔法施工温度不宜底于﹣10℃。
雨天、大风天气(5级及以上)不得进行防水卷材铺贴。
2地下室卷材防水施工要点1、卷材防水施工工艺流程清理基层→涂刷基层处理剂→卷材附加层铺贴→定位、弹线、试铺→铺贴卷材→收头处理、节点密封→清理、检查、修整→验收→保护层施工。
2、四周砌240砖胎模在混凝土垫层上距地下结构外皮50㎜(防水找平层+防水层+防水保护层)处放施工线,进行砖胎模砌筑。
结构外墙防水层外侧用1:3水泥砂浆砌筑永久性240砖保护墙,高度与底板上表面平,水泥砂浆抹面后再做防水,将防水甩头至砖墙外,然后再砌筑两皮砖做临时性保护墙。
永久性保护墙内表面用1:2.5水泥砂浆抹面,临时性保护墙用石灰砂浆砌筑,并用石灰砂浆抹面。
各分部分项工程质量通病防治措施

各分部分项工程质量通病防治措施1.基础工程质量通病防治措施:(1)加强基础设计的规划,确保施工过程中基础的准确定位和正确施工。
(2)严格按照设计施工,加强施工单位对基础工程施工质量的控制和监督。
(3)建立健全基础工程施工质量验收制度,对基础工程的质量进行全面检查,确保合格率达到标准要求。
2.主体结构工程质量通病防治措施:(1)严格按照设计施工,加强施工单位对主体结构施工质量的控制和监督。
(2)建立健全主体结构施工质量验收制度,对主体结构的质量进行全面检查,确保合格率达到标准要求。
(3)加强施工单位的技术交流和培训,提高施工人员的技术水平和质量意识。
3.装饰装修工程质量通病防治措施:(1)加强对装饰装修施工工艺的培训和指导,提高施工工人的技术水平。
(2)加强施工单位对装饰装修材料的管理和验收,确保材料的质量符合要求。
(3)建立装饰装修施工的整体验收制度,对整体装饰装修工程进行综合验收,确保合格率达到标准要求。
4.给水排水工程质量通病防治措施:(1)加强给水排水工程施工单位的管理和监督,确保施工工艺的正确性和施工质量的合格性。
(2)加强给水排水工程设备的检查和保养,保证设备的正常运行,减少故障和质量问题。
(3)建立给水排水工程的验收制度,对给水排水工程进行全面检查,确保合格率达到标准要求。
5.电气工程质量通病防治措施:(1)加强对电气工程施工质量的控制和监督,确保施工过程中的安全性和稳定性。
(2)加强对电气设备的检查和测试,保证设备的正常运行和安全使用。
(3)建立电气工程的验收制度,对电气工程进行全面检查,确保合格率达到标准要求。
总结起来,各分部分项工程质量通病的防治措施主要包括:加强施工单位的管理和监督,严格按照设计施工,建立健全的质量验收制度,提高施工人员的技术水平和质量意识,加强对材料和设备的检查和保养。
这些措施能够有效提升工程质量,确保施工过程中的安全性和稳定性,最终为工程的顺利竣工和正常使用提供保障。
建筑施工防水工程质量通病防治措施
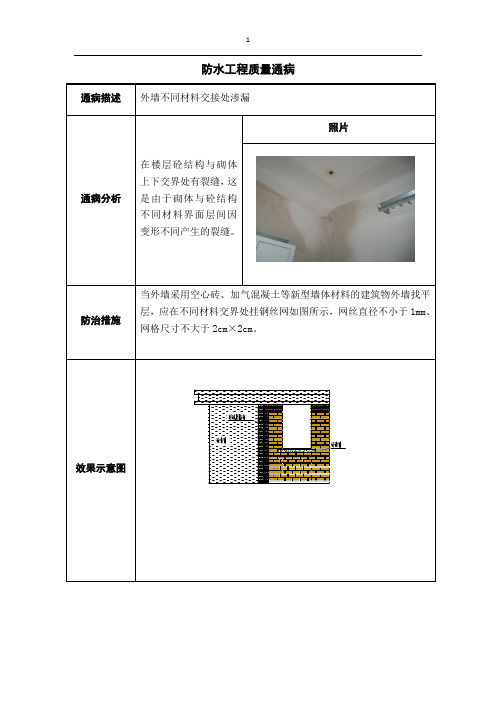
为了追求建筑形式而将泛水高度过分的降低,使屋面与屋面连接处、屋面与墙身交接处的防水高度,低于下暴雨瞬时积水高度;屋面变坡处、老虎窗与屋面连接等处防水处理不当,也是形成屋面渗漏的一大隐患。
⑶施工缝位置留设不当
如将施工缝位置留设在屋面变坡处、屋面与屋面的交接处,这些都是结构应力转换的部位,容易产生裂缝而导致屋面渗漏。
(4)外窗台与窗框之间打胶不严密;
(5)外窗台泛水坡度反坡,窗框内积水。
照片
防治措施
(1)按施工方案外墙砌到设计标高,浇筑窗台梁,上部留出斜面(如图);
(2)窗框安装前先粉刷好防水护框,每次粉刷前均必须清理松动部分,并洒水湿润;
(3)每次粉刷不得超过12mm,粉刷后注意加强保养,确保不裂缝不渗水;
⑷做好混凝土施工技术管理工作。根据施工季节和屋面倾角大小,选择最佳坍落度,并且加强振捣。对已灌筑好的混凝土斜板,应在灌筑10~12h及时进行浇水养护,保证混凝土处在足够的湿润状态,连续养护期不少于15d,以提高混凝土斜板抗拉强度剂及抗裂性。
通病描述
外墙门窗渗漏
通病分析
(1)密封不好,构造处理不妥,未按设计要求选择密封材料。
⑷现浇钢筋混凝土板施工坍落度选择不当
如施工时用水量过多,混凝土在凝固水化过程中,由于内部多余的水分蒸发后,在混凝土中形成微小的空隙,而混凝土体积减小产生收缩,这些空隙连在一起便形成毛细孔隙,成为雨水渗入的通道,从而引发裂缝产生。
⑸施工方法不当
斜屋面的坡度在30°以上时,如仍采用板底支模法灌筑,则容易造成施工质量事故,如局部板厚不满足设计要求,致使结构出现裂缝;钢筋配置不到位,负筋很容易被踩低,无法和混凝土一起抵挡弯矩而使板产生裂缝;混凝土振捣不密实,也是屋面渗漏的隐患。
建筑工程防水工程质量通病问题分析及防治措施

常见防水工程问题分析及防治措施一、防水材料类问题(一)热熔类卷材铺贴后产生空鼓原因分析:1、基层潮湿,沥青胶结材料与基层粘结不良;2、由于人员走动或其他工序的影响,找平层表面被泥水沾污,与基层粘结不良;3、立墙卷材的铺贴,操作比较困难,热作业容易造成铺贴不实不严预防措施:1、应把地下水位降至垫层以下不少于500mm。
垫层上应抹1:2.5水泥砂浆找平层,以创造良好的基层表面,同时防止由于毛细水上升造成基层潮湿;2、保持找平层表面干燥洁净,必要时应在铺贴卷材前采取刷洗、晾干等措施;3、铺贴卷材前1~2天,喷或刷1~2道冷底油,以保证卷材与基层表面粘结。
(二)卷材收缩变形原因分析:1、卷材储存不当,胎体进水,导致在加热过程中水分蒸发,胎体收缩;2、带有板岩类的热熔型卷材在施工时短边搭接没有进行压岩处理,搭接剥离强度小造成;3、卷材在施工时没有对卷材进行提前展卷,卷材应力过大;4、施工过程中,野蛮施工,用力“踢”“拽”卷材,使卷材受力过大拉长卷材。
预防措施:1、卷材施工时可进行提前展卷,释放应力;2、禁止在施工完成的防水层进行损坏性施工;3、施工前检查卷材是否潮湿,如果潮湿,展卷后晾晒至干燥后施工。
(三)湿铺卷材粘结不牢原因分析:1、水泥砂浆太薄没有与基层粘牢;基层没有涂刷水泥砂浆;2、水泥砂浆过干;3、温度低水泥的水化反应没有完全;4、搭接边有杂物、浮灰,粘结力不够;5、基层过干吸收水泥中的水,水泥水化反应不完全;6、过早在卷材表面行走。
预防措施:1、基层充分润湿;2、基层应平整、干净、没有凹凸不平;3、施工时应在卷材表面与基层上同时涂刷水泥砂浆(3mm-5mm);4、卷材施工温度应在5-35摄氏度之间(四)聚氨酯防水涂料涂膜起泡原因分析:1、天气过于潮湿或下雨。
基面潮湿;2、在使用时添加了低沸点稀释剂,稀释剂快速挥发易出现气泡或小孔;3、天气炎热,基层温度高;4、疏松多孔基层;5、单组分产品:一次涂膜太厚;6、双组分产品:避免因过高速度搅拌引入大量气泡;配比不对,也会有气泡产生。
地下室防水质量通病及治理
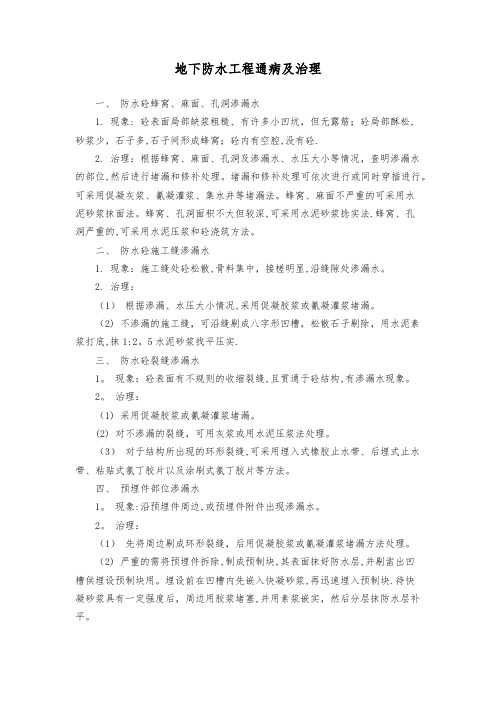
地下防水工程通病及治理一、防水砼蜂窝、麻面、孔洞渗漏水1. 现象: 砼表面局部缺浆粗糙、有许多小凹坑,但无露筋;砼局部酥松,砂浆少,石子多,石子间形成蜂窝;砼内有空腔,没有砼.2. 治理:根据蜂窝、麻面、孔洞及渗漏水、水压大小等情况,查明渗漏水的部位,然后进行堵漏和修补处理。
堵漏和修补处理可依次进行或同时穿插进行。
可采用促凝灰浆、氰凝灌浆、集水井等堵漏法。
蜂窝、麻面不严重的可采用水泥砂浆抹面法。
蜂窝、孔洞面积不大但较深,可采用水泥砂浆捻实法.蜂窝、孔洞严重的,可采用水泥压浆和砼浇筑方法。
二、防水砼施工缝渗漏水1. 现象:施工缝处砼松散,骨料集中,接槎明显,沿缝隙处渗漏水。
2. 治理:(1)根据渗漏、水压大小情况,采用促凝胶浆或氰凝灌浆堵漏。
(2) 不渗漏的施工缝,可沿缝剔成八字形凹槽,松散石子剔除,用水泥素浆打底,抹1:2。
5水泥砂浆找平压实.三、防水砼裂缝渗漏水1。
现象:砼表面有不规则的收缩裂缝,且贯通于砼结构,有渗漏水现象。
2。
治理:(1) 采用促凝胶浆或氰凝灌浆堵漏。
(2) 对不渗漏的裂缝,可用灰浆或用水泥压浆法处理。
(3)对于结构所出现的环形裂缝,可采用埋入式橡胶止水带、后埋式止水带、粘贴式氯丁胶片以及涂刷式氯丁胶片等方法。
四、预埋件部位渗漏水1。
现象:沿预埋件周边,或预埋件附件出现渗漏水。
2。
治理:(1)先将周边剔成环形裂缝,后用促凝胶浆或氰凝灌浆堵漏方法处理。
(2) 严重的需将预埋件拆除,制成预制块,其表面抹好防水层,并剔凿出凹槽供埋设预制块用。
埋设前在凹槽内先嵌入快凝砂浆,再迅速埋入预制块.待快凝砂浆具有一定强度后,周边用胶浆堵塞,并用素浆嵌实,然后分层抹防水层补平。
(3) 如果埋件密集,可用水泥压浆法灌入快凝水泥浆,待凝固后,漏水量明显下降时,再参照本治理(1)和(2)方法处理。
五、管道穿墙或穿地部位渗漏水1. 现象:一般常温管道周边阴湿或有不同程度的渗漏.热力管道周边防水层隆起或酥浆,在此渗漏水。
项目所在地工程质量通病分析及防范措施

项目所在地工程质量通病分析及防范措施本项目为沿海地区,距离海边沿海较近,雨水较多,主要问题为主体结构出现质量问题以及渗漏问题,通过以下几个方面进行质量通病防范。
1.1.1主体工程:(1)模板工程:常见的质量通病有:爆模、未起拱、缝隙大等。
消除质量通病措施有:模板工程应有设计施工方案,模板支撑(架)应有足够的强度、刚度和稳定性,支撑(架)应能承受新浇筑混凝土的重量、模板重量、侧压力以及施工荷载;混凝土梁≥4m时应按规定起拱;木模板应弹线修边,安装拼板应严格控制缝隙;混凝土浇筑前,木模湿润水要足够;旧模板翻转使用时板上的灰疙瘩应消除干净。
(2)钢筋工程:常见的质量通病有:钢筋表面锈蚀、柱子外伸钢筋错位、绑扎节点松脱、钢筋保护层不足、梁抗震135°箍筋漏弯、钢筋闪光对焊接头弯折或偏心、钢筋搭接焊不符焊接规定、板的负弯筋没有设马凳或被踩弯等。
消除质量通病措施有:钢材应按公司指定的符合要求厂家采购。
对锈蚀严重、带有颗粒状或片状的老锈钢筋不得使用。
浇筑混凝土前对伸出板面的柱筋应认真核对位置,并至少绑有两个箍筋固定,以防错位.铁丝绑扎应尽量选用不易松脱的绑扎形式,如节点松脱时重新绑牢。
搭接焊的钢筋的预弯应保证两钢筋的轴线在一直线上,再行施焊。
钢筋的保护层数量应满足需要。
板的负弯筋应用垫块保护,安装预埋管线或浇筑混凝土时,不得踩踏板的负弯筋。
(3)混凝土工程:常见的质量通病有:表面损伤如蜂窝、露筋、孔洞、夹渣,成型规格偏差如板面不平、歪斜、凹凸,内部缺陷如强度偏低、匀质性差、裂缝等。
地下室底板及墙体的防裂是本工程的关键,为保证地下室不裂,除在浇捣工艺上按前面所述施工方法进行,重点加强对混凝土的养护,具体为:底板施工完7天内专门覆盖塑料薄膜进行保水养护,上部施工暂停,7天扣进行淋水养护,保证混凝土表面湿润。
外墙在未拆模之前,在模板外侧淋水,保证模板内侧的水分不过早蒸发,拆模后挂麻袋养护14天。
消除质量通病措施有:浇筑时应认真振捣、严防漏振。
主体结构质量控制标准及通病防治措施(混凝土部分)
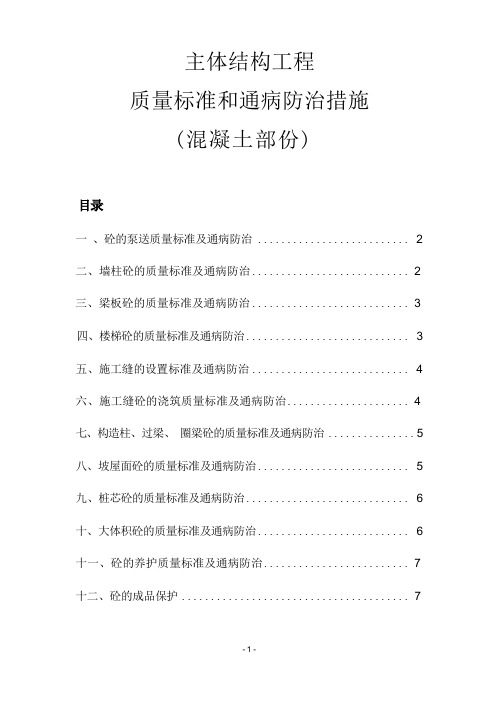
主体结构工程质量标准和通病防治措施(混凝土部份)一、砼的泵送质量标准及通病防治 (2)二、墙柱砼的质量标准及通病防治 (2)三、梁板砼的质量标准及通病防治 (3)四、楼梯砼的质量标准及通病防治 (3)五、施工缝的设置标准及通病防治 (4)六、施工缝砼的浇筑质量标准及通病防治 (4)七、构造柱、过梁、圈梁砼的质量标准及通病防治 (5)八、坡屋面砼的质量标准及通病防治 (5)九、桩芯砼的质量标准及通病防治 (6)十、大体积砼的质量标准及通病防治 (6)十一、砼的养护质量标准及通病防治 (7)十二、砼的成品保护 (7)① 砼运输时间过长。
②砼泵送之前搅拌不够充分。
③ 由于来料较干,现场工人向砼内随意加水。
④ 现场未检测砼的坍落度。
⑤ 泵送时砼泵机料斗内浆面高度保持不够。
⑥ 泵管弯头管接得太多,或者弯管角度太大。
⑦ 泵管在楼面及立面支撑、固定不符合要求。
⑧ 泵管砼出口处,砼堆积太高。
① 混凝土泵车设置处场地应平整、坚实,道路畅通,供料方便,距浇筑点近。
② 砼运输时间不宜超过 1.5 小时,来到现场泵车应进行二次搅拌后才干泵送。
③ 砼输送管不得直接支承在钢筋、模板、预埋件上,水平管每隔一定的距离用支架、台垫、吊具等固定。
④ 每次浇砼都应安排专人检测砼坍落度是否符合要求。
现场应专人看管,不得随便向砼内加水。
⑤ 砼泵启动后,应先送适量水、砂浆以湿润砼泵的料斗、管内壁等。
合格标准:如下图①墙柱砼浇筑前,根部没有先放入50 厚摆布的同配比砂浆或者减半石子砼。
②模内未湿水冲洗,根部存在垃圾等,造成夹渣。
③砼振捣不充分或者漏振,浮现蜂窝、孔洞、露筋等。
④ 墙柱未及时校核垂直度,导致墙柱倾斜。
⑤ 砼浇筑完成后表面处理不当。
柱头砼高于梁底模,影响梁底钢筋的排放。
⑥ 墙柱砼先浇时,浇完墙柱砼,在没有初凝的情况下用水冲刷墙柱头砼。
⑦墙柱砼裂缝。
⑧ 砼强度不符合要求。
① 墙、柱砼浇筑前先冲洗、排除模板内杂物及垃圾,并湿润所有模板。
主体结构质量通病防治

主体工程----模板
*
柱轴线移位 原因分析: 1、施工放线不到位 2、未设置定位筋,导致柱移位 防治措施: 1、施工放线时除放出柱位置线以外还应设置模板控制检查线(柱线向外便宜300mm) 2、支模时,先立两端柱模,校正垂直与位置无误后,柱模拉通线,再支中间各柱模板 3、在施工线范围内设置定位钢筋,防止柱移位
主体工程----钢筋
钢筋表面锈蚀较严重 1.现象:钢筋表面出现红色浮锈,日久后变为暗褐色,甚至发生鱼鳞片剥落现象。 2.危害:钢筋表面较严重锈蚀,浇筑在混凝土中时,影响钢筋与混凝土间的握裹力。钢筋锈蚀发展,会使混凝土产生锈蚀裂缝。 3.原因分析:保管不善,受雨雪侵蚀;存放期过长;环境潮湿,通风不良。 4.预防措施: (1)已成型钢筋可用水灰比为0.3~0.6的普通硅酸盐水泥灰浆涂抹到钢筋表面,有1~2年防锈效果,浇筑前,原则上应将灰浆清除。 (2)钢筋不得直接堆置在地面上,必须用东西垫起使离地面20cm以上:根据天气情况,必要时加盖雨布;场地四周有排水设施,且地势要高;尽量缩短堆放期,先进场的先用。 5.治理方法:钢筋上的红褐色锈斑要清除,清除可采用手工或机械方法。盘条钢筋可通过冷拉或调直过程除锈。已成型的钢筋及粗钢筋采用专用除锈机除锈。对锈蚀严重,锈皮剥落,因麻坑。斑点损伤截面的,应降级使用。
主体工程----钢筋
锥 螺 纹 接 头
主体工程----钢筋
*
直螺纹连接丝头过细,不符合要求
主体工程----钢筋
钢筋保护层垫块不合格 原因分析: 1.在浇筑砼或受施工荷载冲击时导致垫块位移或压碎。 2.梁板墙等主筋上未安装垫块或安装数量少,导致露筋或受力钢筋的保护层小。 3.选用不符合设计尺寸要求的垫块 防治措施: 选用合适尺寸的垫块,垫块按梅花状放置,应布置适宜,距离不得过大,并放置牢固,严禁松动、位移、脱落,振捣砼时注意防止垫块位移。
建筑工程主体结构工程质量通病问题分析及防治措施

一、钢筋工程1.箍筋不方正(1)原因:箍筋边长成型尺寸与图纸要求误差过大;没有严格控制弯曲角度;一次弯曲多个箍筋时没有逐根对齐。
(2)防治措施:注意操作,使成型正确;当一次弯曲多个箍筋时,应在弯折处逐根对齐。
2.成型尺寸不准确已成型的钢筋尺寸和弯曲角度不符合设计要求。
(1)原因:下料不准确;画线方法不对或误差大;用手工弯曲时,扳距选择不当;角度控制没有采取保证措施。
(2)防治措施:加强钢筋配料管理工作,预先确定各种形状钢筋下料长度调整值。
根据钢筋弯制角度和钢筋直径确定好扳距大小。
为保证弯曲角度符合要求,在设备和工具不能自行达到准确角度的情况下,可在成型案上画出角度准线或采取钉扒钉做标志的措施。
3.已成型的钢筋变形钢筋成型后外形准确,但在堆放或搬运过程中发现弯曲、歪斜、角度偏差。
(1)原因:成型后,往地面摔得过重,或因地面不平,或与别的物体或钢筋碰撞成伤;堆放过高或支垫不当被压弯;搬运频繁,装卸“野蛮”。
(2)防治措施:搬运、堆放要轻抬轻放,放置地点要平整,支垫应合理;尽量按施工需要运至现场并按使用先后堆放,以避免不必要的翻垛。
4.圆形钢筋直径不准(1)原因:圆形螺旋筋成型所得的直径尺寸与绑扎时拉开的螺距和钢筋原材料弹性性能有关,直径不准是由于没有很好的考虑这两点因素。
(2)防治措施:应根据钢筋原材料实际性能和构件所要求的螺距大小预先确定卷筒的直径。
当盘缠在圆筒上的钢筋放松时,螺旋筋就会往外弹出一些,拉开螺距后又会使直径略微缩小,其间差值应有计算确定。
5.钢筋代换后根数不能均分同一编号的钢筋分几处配置,配料时进行规格代换后因根数变动,不能均分于几处。
(1)原因:在钢筋材料表中,该号钢筋只写总根数,在钢筋进行代换时忽略了钢筋分几处布置的情况。
(2)防治措施:在配料加工钢筋前进行钢筋代换计算时,要预先参看施工图,看该号钢筋是否分几处布置,如果是应按分根数考虑代换方案。
6.箍筋弯钩形式不对箍筋末端未按规定不同的使用条件制成相应的弯钩形式。
主体结构施工常见10种质量通病

主体结构施工10种质量通病原因分析及防治措施一、钢筋工程1.表现形式楼板小直径钢筋间距、位置难以保证;负弯矩钢筋位置位移;梁、柱角部主筋保护层厚度偏小;模板拆除后箍筋外漏。
2.楼板钢筋防治措施设计阶段,在满足结构安全和造价经济的前提下,应优先选用小直径三级钢筋。
因为三级钢筋强度大于一级钢筋,在施工中不易踩踏。
施工阶段,浇筑混凝土时应采取措施,在模板上垫上马凳,铺上架木板,施工人员在板上操作,不要直接踩踏钢筋。
3.楼板负弯矩钢筋防治措施施工阶段:钢筋绑扎时,应在负弯矩钢筋下面增设足够强度的马凳支撑,在混凝土浇筑完毕,抹面时用专用工具随时将钢筋上提至准确位置,混凝土终凝前,严禁上人踩踏;4.梁、柱主筋保护层防治措施制作梁、柱箍筋时,应严格按照设计的截面尺寸加工制作。
尤其在箍筋的弯折部位,有效折弯半径在规范允许的条件下,应通过现场试验确定弯折半径,防止弯折过小,导致主筋绑扎时不能紧靠箍筋,而使保护层过大(减小构件截面尺寸)。
二、模板通病及防治1.表现形式:拼缝不严,造成混凝土振捣时出现漏浆,混凝土表面不平整,出现蜂窝麻面等缺陷。
2.治理措施模板在拼装完成后,在接缝处粘贴一道透明胶带是解决漏浆的较好方法,但往往在钢筋绑扎时,由于钢筋的拖动,将粘贴的胶带破坏,反而对混凝土造成不利。
在模板拼缝之间采用双面胶棉,粘贴在板边,基本会杜绝混凝土浇筑漏浆的通病。
三、混凝土通病1.表现形式混凝土振捣不密实或漏振,模板拆除后出现孔洞、漏筋、表面疏松、裂缝等2.治理措施加强管理人员的旁站意识,混凝土浇筑时,监理、甲方必须现场全程监管,尤其是一些关键部位,象高层建筑的基础、转换层等部位。
四、非承重墙裂缝1.表现形式填充墙与混凝土结构的柱、墙、梁之间出现裂缝;砌块墙体抹灰本身的裂缝。
2.治理措施材料选择:砌筑时,蒸压加气混凝土砌块、轻骨料混凝土小型砌块的龄期不得少于28d;优先选用专用的砌筑砂浆。
组砌方法:非承重砌体应分次砌筑,每次砌筑高度不应超过1.5m。
工程质量通病防治措施方案
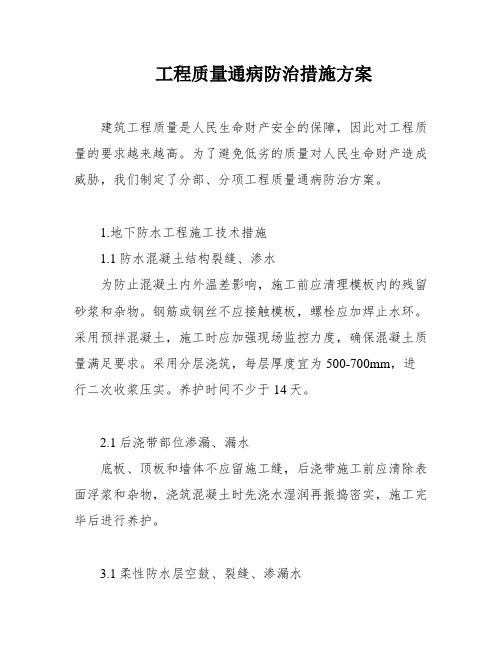
工程质量通病防治措施方案建筑工程质量是人民生命财产安全的保障,因此对工程质量的要求越来越高。
为了避免低劣的质量对人民生命财产造成威胁,我们制定了分部、分项工程质量通病防治方案。
1.地下防水工程施工技术措施1.1防水混凝土结构裂缝、渗水为防止混凝土内外温差影响,施工前应清理模板内的残留砂浆和杂物。
钢筋或钢丝不应接触模板,螺栓应加焊止水环。
采用预拌混凝土,施工时应加强现场监控力度,确保混凝土质量满足要求。
采用分层浇筑,每层厚度宜为500-700mm,进行二次收浆压实。
养护时间不少于14天。
2.1后浇带部位渗漏、漏水底板、顶板和墙体不应留施工缝,后浇带施工前应清除表面浮浆和杂物,浇筑混凝土时先浇水湿润再振捣密实,施工完毕后进行养护。
3.1柔性防水层空鼓、裂缝、渗漏水施工前应清理干净、干燥的找平层表面。
柔性防水层施工期间,地下水位应降至垫层300mm以下。
先涂刷基层处理剂,采用满贴法铺贴卷材,确保铺贴严密,防水材料应薄涂多遍成活。
施工完毕后应采取可靠的保护措施。
以上是对地下防水工程的施工技术措施,希望能够提高工程质量,保障人民生命财产安全。
2.1 砌体裂缝1.在填充墙砌至接近梁底、底板时,应留有一定的空隙。
填充墙砌筑完并间隔15天以后,方可将其补砌挤紧。
补砌时,对双侧竖缝用高强度等级的水泥砂浆嵌填密实。
2.框架柱间填充墙拉结筋应满足砖模数要求,不应折弯压入砖缝。
拉结筋宜采用预埋法留置。
3.填充墙采用粉煤灰砖、加气混凝土砌块等材料时,框架柱与墙的交接处宜用15mm×15mm木条预先留缝,在加贴网片前浇水湿润,再用1:3水泥砂浆嵌实。
4.通长现浇钢筋混凝土板带应一次浇筑完成。
5.砌体结构砌筑完成后应等待60天再抹灰,并不少于30天。
6.每天砌筑高度应控制在1.8米以下,并应采取严格的防风、防雨措施。
7.严禁在墙体上交叉埋设和开凿水平槽。
竖向槽须在砂浆强度达到设计要求后,用机械开凿,且在粉刷前,加贴钢丝网片等抗裂材料。
房屋建筑主体结构施工质量问题及防治措施

房屋建筑主体结构施工质量问题及防治措施摘要:随着社会的不断发展进步,房屋建筑工程的规模也不断扩大,建筑施工工艺也变得越来越繁杂,在这种情况下,确保房屋建筑工程的施工质量是至关重要的。
房屋建筑主体作为承担全部结构的组成部分,其施工质量的优劣直接着一个房屋建筑主体的品质,但是由于施工技术的制约或监管因素的负面影响,目前房屋建筑结构施工仍存在一系列质量问题,需要强化对建筑主体结构施工质量的监管监控,以确保房屋建筑工程的安全、高效、可持续发展。
经过对住宅建筑主体结构施工质量问题的深入分析,我们提出了一系列有效的防治措施,以期为施工人员提供有效的参考,以确保房屋建筑主体结构的安全性和可靠性。
关键词:房屋建筑;主体结构;施工质量;防治措施1.引言随着社会的进步,房屋建筑主体的形式和结构发生了巨大的变化,呈现出多元化的特征,房屋建筑施工面临着前所未有的挑战和要求。
房屋建筑的整体结构是房屋建筑的重要组成部分,它不仅决定着当前房屋建筑的风格,还影响着房屋建筑的安全性、可靠性和实用性。
为了满足当今社会发展的需求,我们必须不断改进房屋建筑主体结构的技术,完善施工流程,强化对建筑主体结构施工质量的监督和管理,以进一步提高房屋建筑工程技术水平。
2.房屋建筑主体结构施工质量问题分析2.1模板工程2.1.1模板出现移位的质量问题在房屋建筑物模板工程施工步骤中,最经常出现的主体结构施工质量问题便是模板工程主轴的转移,这种情况通常表现为:当混凝土浇筑完成后,通过一段时间的晾晒,混凝土会固化,而在拆卸模块的整个过程中,墙体和立柱的部位会出现位移,从而影响房屋建筑物的整体稳定性。
一般来说,导致移位的主要原因有两个:首先,翻样不够精确;其次,在模板工程技术交底步骤中,缺乏足够的细节和完善。
2.1.2偏差质量问题模板工程中除了上述已经论述的移位质量问题之外,在模板工程的施工建设作业过程中,还存着偏差的质量问题,这种问题也非常的常见。
通常情形下,这个现象是由于钢筋混凝土框架层的高程和预留毛裂缝高程不当造成的。
地下工程防水工程质量通病及防治措施

地下工程防水工程质量通病及防治措施摘要:地下工程施工能有效地提高土地利用率,而地下工程施工直接影响到高层建筑的稳定性。
尽管地下室已设置了防水层,但仍有大量地下室渗漏,严重影响建筑质量,需采取相应措施防止渗漏。
文章分析了目前地下室防水工程中常见的质量缺陷,旨在有效处理地下室防水工程中出现的各种问题,实现地下室防水工程全过程质量管理,有效促进建筑行业的稳步发展。
关键词:地下室;防水工程;防渗漏处理1地下室防水工程质量通病1.1变形缝渗水建筑工人在建造地下室时,常常需要将地下室与其周围的建筑物直接连接起来,在建筑物的主体部分,就会发现沉降缝与地下室保持连接,通过沉降缝可有效避免建筑物因竖向不均匀造成的沉降。
但在现阶段,变形缝结构的缝设计还存在许多不足,无论是施工工艺还是具体的构造点都存在不均匀性,容易导致变形缝渗水。
通常变形缝渗水主要是由于特殊设置和处理程序不当所致。
施工人员一般需要40至60天来安装后浇带。
早期若不清理基层,很容易留下渗水的隐患。
在进行变形缝二次浇注时,若变形缝内多余垃圾及毛刺未清除干净,混凝土就很难保持紧密。
若混凝土本身的水土比不够科学,振动不够密实,甚至振动完成后未组织施工人员进行定期养护,就有可能导致变形缝处出现收缩裂缝,进而引起渗水。
1.2主水平施工缝渗水一般在建造地下室时,都要在混凝土墙内设置水平缝。
但许多地下室工程完工后,没有专业人员进行水平施工缝的清理,或者止水钢板的埋设不当,不符合设计要求,容易造成水沿止水钢板渗入。
水平施工缝渗水主要是由于施工缝处理不当或止水钢板、止水带的铺设不当等原因。
按照现行的建筑工程施工规范,建筑外墙板的施工高度大多在300 mm至500 mm之间,并在外墙板后加一条止水带。
在进行底板混凝土振捣施工时,一次振捣混凝土密实度差,二次振捣施工困难,易造成渗漏隐患。
1.3主体结构施工失当引起渗水除沉降缝、后浇带等变形缝及主体水平施工缝渗水外,主体结构施工不当也易引起地下室渗漏。
- 1、下载文档前请自行甄别文档内容的完整性,平台不提供额外的编辑、内容补充、找答案等附加服务。
- 2、"仅部分预览"的文档,不可在线预览部分如存在完整性等问题,可反馈申请退款(可完整预览的文档不适用该条件!)。
- 3、如文档侵犯您的权益,请联系客服反馈,我们会尽快为您处理(人工客服工作时间:9:00-18:30)。
主体结构及防水质量通病防治措施1 模板工程1.1 模板质量检查模板安装前,先检查模板材质量,不符质量标准的不得投入使用。
1.2 梁模板通病现象:梁身不平直、梁底不平及下挠、梁侧模炸模、局部模板嵌入柱梁间、拆除困难。
防治措施:支模时应遵守边模包底模的原则,梁模与柱模连接处,下料尺寸一般应略为缩短3-5mm;梁侧模必须有压脚板、斜撑、拉线通直后将梁模钉固。
梁底模板按规定起拱;混凝土浇筑前,模板应充分用水浇透。
1.3 柱模板通病现象:炸模、断面尺寸鼓出、漏浆、混凝土不密实,或蜂窝麻面、偏斜、柱身扭曲、烂根。
防治措施:根据规定的间距,加设牢固的柱箍;成排柱模支模时,先立两端柱模,校直与复核位置无误后,顶部拉通长线,再立中间柱模;四周斜撑要牢固;柱子支模前必须先校正钢筋位置;柱轮廓线放好后,在楼板面上,将柱模板覆盖区域用1:2水泥砂浆找平,这样支模时模板根部就和楼板面保证不漏浆。
另外,为保证边柱、建筑物边缘处剪力墙不烂根,下层墙柱最上部的模板同本层墙柱模板一起拆除。
1.4 板模板通病现象:板中部下挠,板底混凝土面不平。
防治措施:楼板模板厚度要一致,搁栅要料要有足够的强度和刚度,搁栅面要平整;支顶要符合规定的保证项目要求;板模按规定起拱。
1.5 墙模板通病现象:炸模、倾斜变形;墙体厚度不一,墙面高低不平;墙根跑浆漏筋;墙角模板拆不出。
防治措施:墙体模板应拼装平整,符合质量检验评定标准;墙身中间应有足够的对拉螺栓承担混凝土的侧压力,确保不炸模,对拉螺栓上应有保证墙体厚度的横挡,严格控制每层混凝土的浇筑厚度;剪力墙模板支好后,浇筑混凝土前,用1:2水泥砂浆将模板根部的缝隙喂严。
2 钢筋工程2.1 竖向钢筋偏位质量通病的防治措施在梁绑扎过程中,钢筋自身防偏位措施必须严格执行。
在梁柱节点钢筋密集处,在柱与梁顶交界处,扎筋时给框架柱增加一个限位箍筋,用电焊将它与梁的箍筋点焊固定,再将柱主筋逐一绑扎牢固,并沿柱高临时绑扎间距不大于@500的箍筋,确保节点处柱筋在浇筑时不会发生偏位。
加强混凝土的现场浇筑管理工作,认真进行技术交底,严禁将整车或整料斗的混凝土直接灌注到柱、墙内,不得随意冲撞构件的钢筋骨架,应先将混凝土卸在盘板上。
再均匀下料,分层浇筑,分层振捣,这样既能保证混凝土的施工质量,又可防止撞偏钢筋骨架。
在进行竖向钢筋的机械连接前先搭好脚手架,在上部通过吊线,用钢管固定出上部的托筋位置,使接长的钢筋能准确地套在箍筋范围内,这样在脚手架上安装柱的钢筋,绑扎箍筋,既安全,又能保证框架柱骨架不扭曲、不倾斜,还能提高工效。
2.2 钢筋加工钢筋下料切断尺寸不准:切断机进场时,认真检查固定刀片与冲切刀片的间隙,间隙控制在0.5-1mm为宜。
根据结构钢筋的所在部位和钢筋切断后的误差情况,确定调整或返工。
钢筋成型尺寸不准确,箍筋歪斜,外形误差超过质量标准允许值:注意操作,使成型尺寸准确,加强钢筋配料管理工作,根据设备情况和传统操作经验,预先确定各种形状钢筋的下料长度调整值,配料时考虑周到。
2.3 钢筋绑扎与安装钢筋骨架外形尺寸不准:绑扎时宜将多根钢筋端部对齐,防止绑扎时,钢筋偏离规定位置及骨架扭曲变形。
保护层花岗岩块准确,垫块间距取800×800,否则导致平板悬臂板面出现裂缝,梁底柱侧露筋。
钢筋骨架绑扎完成后,会出现斜向一方,绑扎时铁线应绑成八字形。
左右口绑扎发现箍筋遗漏、间距不对要及时调整好。
柱子箍筋接头无错开放置:绑扎前先检查,绑扎完成再检查,若有错误立即纠正。
浇筑混凝土时,受到侧压钢筋位置出现位移时,及时调整。
梁、底板钢筋勾头倒向一边或杂乱无章:在弯头钢筋的中部用1根直径为12的螺纹钢与弯头钢筋绑扎牢固。
3 混凝土工程3.1 蜂窝产生原因:振捣不实或漏振;模板缝隙过大导致水泥浆流失,钢筋较密或石子粒径相应过大。
预防措施:按规定使用和移动振动器。
中途停歇后再浇捣时,新旧接缝范围要小心振捣。
模板安装前应清理模板表面及模板拼缝处的黏浆,才能使接缝严密。
若接缝宽度超过2.5mm,应用泡沫双面胶或胶带以填封,梁筋过密时应选择相应的石子粒径。
3.2 露筋产生原因:主筋保护层垫块不足,导致钢筋紧贴模板;振捣不实。
预防措施:钢筋垫块夺取度要符合设计规定的保护层厚度;垫块放置间距适当,钢筋直径较小时垫块部距宜密些,使钢筋自重挠度减少;使用振动器必须待混凝土中气泡完全排除后才能移动。
3.3 麻面产生原因:模板表面不光滑;模板湿润不够;漏涂隔离剂。
预防措施:模板应平整光滑,安装前要把粘浆清除干净,并满涂隔离剂,浇捣前对模板要浇水湿润。
3.4 孔洞产生原因:在钢筋较密的部位,混凝土被卡住或漏振。
预防措施:对钢筋较密的部位(如梁柱接头)应分次下料;机械振捣有困难时,应采用人工捣固配合;预留空洞处应在两侧同时下料;按照规程使用振动器;加强施工技术管理和质量检查工作。
3.5 缝隙及夹渣产生原因:施工缝没有按规定进行清理和凿除浮浆,特别是柱头和梯板脚。
预防措施:在已硬化的混凝土表面浇筑混凝土前,应除掉表面浮浆和松动的石子,并充分湿润和清洗干净;浇注前对柱头、施工缝、梯板脚等部位重新检查,清理杂物、泥沙、木屑。
3.6 墙柱底部缺陷(烂脚)产生原因:模板下口缝隙不严密,导致漏水泥浆;或浇筑前没有先浇灌足够50mm厚以上水泥砂浆。
预防措施:支模前,模板底部应用水泥砂浆找平;模板缝隙宽度超过2.5mm 应予以填塞严密,特别防止侧板吊脚;浇注混凝土前先浇足50-110m厚的水泥砂浆。
3.7 梁柱结点处(接头)断面尺寸偏差过大产生原因:柱头模板刚度差,或把安装柱头模板放在楼层模板安装的最后阶段,缺乏质量控制和监督。
预防措施:安装梁板模板前,先安装梁柱接头模板,并检查其断面尺寸、垂直度、刚度,符合要求才允许接驳梁模板。
3.8 楼板表面平整度差产生原因:振捣后没有用拖板、刮尺抹平;梯级和斜水部位没有符合尺寸的模具定位;混凝土未达终凝就在上面行人和操作。
预防措施:浇捣楼面应提倡使用拖板或刮尺抹平,梯级要使用平直、厚度符合要求和模具定位;混凝土达到1.2Mpa后才允许在混凝土面上操作。
3.9 基础轴线位移,螺孔、埋件位移产生原因:模板支撑不牢,埋件固定措施不当,浇筑时受到碰撞引起。
预防措施:基础混凝土是属厚大构件,模板支撑系统要予以充分考虑;当混凝土捣至螺孔底时,要进行复线检查,及时纠正。
浇注混凝土时应在螺孔周边均匀下料,对重要的预埋螺栓尚应采用钢架固定。
必要时二次浇筑。
3.10 混凝土表面不规则裂缝产生原因:一般是淋水保养不及时,湿润不足,水分蒸发过快或厚大构件温差收缩,没有执行有关规定。
预防措施:混凝土板表面在初凝前应进行二次收浆处理;混凝土终凝后立即进行淋水保养;高温或干燥天气要加麻袋等覆盖,保持构件有较久的湿润时间。
厚大构件参照大体积混凝土施工的有关规定。
墙、柱混凝土表面应涂刷养护剂。
3.11 缺棱掉角产生的原因:投料不准确,搅拌不均匀,出现局部强度低;或拆模板过早,拆模板方法不当。
预防措施:指定专人监控投料,投料计量准确;搅拌时间要足够;拆模应在混凝土强度能保证其表面及棱角在拆除模板不受损坏时方能拆除。
拆除时对构件棱角应予以保护。
3.12 钢筋保护层垫块脆裂产生原因:垫块强度低于构件强度;沉置钢筋笼时冲力过大。
预防措施:垫块的强度不得低于构件强度,并能抵御钢筋放置时的冲击力;当承托较大的梁钢筋时,垫块中应加钢筋或铁丝增强;执块制作完毕应浇水养护。
4 防水卷材7.13.4.1 空鼓⑴现象铺贴后的卷材表面,经敲击或手感检查,出现空鼓声。
⑵原因分析①基层潮湿,沥青胶结材料与基层粘接不良。
②由于人员走动或其他工序的影响,找平层的表面被泥水沾污,与基层粘接不良。
③立墙卷材的铺贴,操作比较困难,热作业容易造成铺贴不严不实。
⑶预防措施①保持找平层表面干燥洁净。
②铺贴卷材前一、二天,刷基层处理剂,以保证卷材与基层表面粘接。
③铺贴卷材时气温不宜低于5ºC。
雨季施工应有防雨措施,或错开雨天施工。
⑷治理方法对于检查出的空鼓部位,应剪开重新分层粘贴。
4.2 卷材转角部位后期渗漏⑴现象防水工程完后,转角部位出现渗漏。
⑵原因分析①在转角部位,卷材未能按转角轮廓铺贴严实,后做找平层时遭破坏。
②所选用的卷材韧性较差,转角处操作不便,沥青胶结过高或过低,不能确保转角处卷材铺贴严密。
③转角处未按有关要求增设防水附加层。
⑶预防措施①基层转角处应做成圆弧形或钝角。
②转角处应选用强度高、延伸率大、韧性好的卷材。
③沥青胶结料的温度应严格按有关要求控制。
涂刷厚度应力求均匀一致,各层卷材均要铺贴牢实,并增设卷材附加层。
⑷治理方法当转角部位出现粘贴不牢、不实现象时,应将该处卷材剪开,灌入聚氨酯,逐层补好。
4.3 管道处铺贴不严密⑴现象卷材与管道壁粘结不严,出现张口、翘边现象,一般管径越小,上述现象越严重。
⑵原因分析①管道未进行认真的清理、除锈,不能确保卷材与管道的粘结。
②穿管处四周呈死角,使卷材不易铺贴严实。
⑶预防措施管道表面的尘垢和铁锈要清除干净。
在管道穿越砖石结构处,管道四周宜用细石混凝土包裹,其厚度不应小于300mm。
抹找平层时,应将管道跟部抹成直径不小于50mm的圆角。
卷材应按转角要求铺贴严实。
亦可在穿管处埋设带法兰的套管,将卷材防水层粘贴在法兰盘上,粘贴宽度至少为100mm,并用夹板将卷材压紧。
发烂盘及夹板都应清理干净,刷上沥青,夹板下面应加油毡衬垫。