精馏塔开题报告
甲苯—四氯化钛精馏塔毕业设计开题报告开题报告ppt
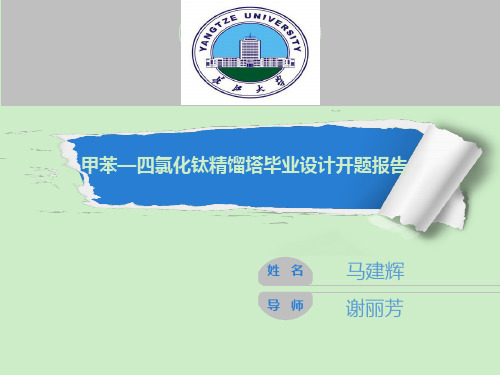
4 进度安排及完成情况
第7周:与指导老师交流,就前期设计中存在的问 题进行修改;
第8周:进行塔内其他构件的设计计算; 第9周:进行法兰和筒体零件图的绘制; 第10周:进行装配图的绘制; 第11周: 制定论文写作提纲,同时开始撰写论文; 第12周:完成论文初稿,并与指导老师交流进行
4 进度安排及完成情况
第1周:收集甲苯—四氯化钛精馏塔的相关资料; 第2周:对相关资料进行整理和分析,掌握甲苯—四氯
化钛精馏塔的工 作原理,完成开题报告; 第3周:确定总体设计方案,应用HYSYS软件模拟甲
苯—四氯化钛精馏塔的分离; 第4周:进行精馏塔的选择,分析填料塔与板式塔的优
缺点; 第5周:进行物料衡算和热量衡算,精馏塔塔体的主要
修改; 第13周:完成毕业设计工作,准备答辩。
谢谢您的聆听
C、其次塔的总体高度设计例:塔顶部空间高度; 进料部位空间高度;塔立体高度;
2 研究内容及方法
D、最后塔设备的机械设例:封头和筒体的 厚度;塔的质量;各种载荷的计算;筒体和 裙座危险截面的强度和稳定性校核;基础环 设计;地脚螺栓计算;开孔补强;
5、运用AutoCAD绘制精馏塔装配图和零件图。
填料塔结构
研究内容
4、进行物料衡算和热量衡算,确定精馏 塔的主要参数;
5、进行塔的附属设备设计和选择;
6、绘制精馏塔的装配图和主要零件图。
2 研究内容及方法
方案与措施
1、通过查阅资料、整理资料获得精馏塔的国 内外研究现状,同时掌握其工作原理;
2、根据HYSYS软件模拟甲苯—四氯化钛的分 离过程;
3、根据化工原理的知识从物料性质;操作条 件;塔设备的安装和维修等进行塔的选择, 由于四氯化钛受热或遇水分解 放热,并且 具有较强的腐蚀性;甲苯—四氯化钛中分 离程度很高;所以一般选填料塔;
(完整版)精馏塔开题报告

DN700甲醇精馏塔设计一、甲醇精馏塔设计的背景与意义精馏塔是化工工业中广泛使用,是分离工艺中的重要设备。
而精馏是甲醇生产的重要后处理工序,在甲醇生产中占据重要的位置。
甲醇精馏塔是精馏的核心设备,它与产品质量回收率消耗定额三废排放及处理等方面密切相关甲醇精馏塔既可采用板式塔,也可采用填料塔。
近年来,我国精馏塔内件技术有了长足发展,如高效导向筛板、新型垂直筛板、新型导向浮阀塔板及新型规整填料等技术开始被广泛采用[1]。
甲醇精馏装置是甲醇生产的重要处理工序,其能耗占甲醇生产总能耗20%左右。
甲醇精馏技术的好坏直接关系到精甲醇的质量;先进、节能、高效的精馏装置,对降低成本、节能降耗、提高产品竞争力和企业经济效益起到重要的作用。
加强对甲醇精馏塔的研究与改进,不断满足化学工业的要求,达到低成本、低耗能、节能环保、绿色高效等要求,有利于我国化学工业科学快速的发展,不断赶上国际以及发达国家的脚步,提升自己的竞争实力。
二、国内外对本课题的研究现状现阶段,国内外的研究聚焦于新型高效性能塔板的开发及工业应用;塔板设计、开发更趋于科学化的方向。
在填料塔研究方面,不断研究新型、高效的填料来提高填料塔的效能。
随着时代的发展,国内外对精馏塔的研究更趋向于经济、安全、高效、清洁方向发展,推动精馏设备的前进与发展。
2.1精馏塔的发展从精馏设备的历史发展来看,精馏技术与石油、化学加工工业的发展是相辅相成、相互刺激、共同进步的发展关系。
精馏技术的任何进步,都会极大刺激化学加工工业的技术发展,同样在石油、化学加工工业发展的每一个历史阶段都会对精馏设备技术提出更高的要求。
①.阶段一:20~50年代1920年,有溢流的泡罩塔板开始应用于炼油工业,开创了一个新的炼油时代泡罩塔板对设计水平要求不高、对各类操作的适应能力强、对操作控制要求低等特性在当时被认为是无可替代的板型Rachig环填料塔主要应用于较小直径的无机分离塔设备中,同时也开发了Pall环,标志着现代乱堆填料的诞生②.阶段二:50~70年代消除放大效应的研究:AIChE研究浮阀塔板的开发FRI的成立系统化的设计方法:1955年,Monsanto公司的Bolles发表了著名的“泡罩塔板设计手册”,首先提出了科学的、规范化塔板设计技术,该方法到目前为止仍然广泛流行大孔筛板的研究③.阶段三:70~90年代大型液体分布器的基础研究,使得填料塔的放大研究成功,并在减压塔中应用获得极大的经济效益和社会效益计算机应用(辅助精馏塔放大效应的研究,计算塔板效率;精馏过程设计)新型高性能浮阀塔板的开发及应用④.阶段四:80末至今新型高效性能塔板的开发及工业应用塔板设计、开发更趋于科学化的方向现有精馏设备的优点:结构简单,造价低;生产能力大,分离效率高;操作弹性大,精馏效率较高。
精馏塔爆炸事故影响分析及爆炸灾害控制技术研究的开题报告

精馏塔爆炸事故影响分析及爆炸灾害控制技术研究的开题报告1.研究背景精馏塔是在炼油、化工、制药等行业广泛应用的一种重要设备,其能够使原料经过物理或化学的加工处理,从而获得更高纯度的产品。
然而,精馏塔在使用过程中,由于操作不当、设备损坏、环境变化等原因常常会出现故障,严重时甚至会引发爆炸事故,造成巨大的人员伤亡和财产损失,严重威胁生产安全和社会稳定。
因此,对精馏塔的爆炸事故影响分析及其爆炸灾害控制技术研究具有重要的现实意义和应用价值。
2.研究目的本文旨在对精馏塔爆炸事故的影响进行分析,并对其爆炸灾害控制技术进行研究,以提出一套有效的措施,从而减少事故发生的可能性,降低爆炸事故带来的损失。
3.研究内容(1)分析精馏塔爆炸事故的成因及影响因素,总结其特点和规律,为制定防范措施提供理论依据和技术支持。
(2)探究精馏塔爆炸事故的灾害控制技术,包括安全阀、喷雾系统、泡沫灭火系统等多种控制手段的原理和工作方式,并对其效果进行实验研究和验证。
(3)结合实际情况,提出精馏塔爆炸事故的应急处置措施和预防措施,以及安全管理、培训等方面的建议。
4.研究方法(1)文献调研法:对专业书籍、期刊、报告等相关文献进行查阅,梳理整理有关精馏塔爆炸事故的原理、机理以及控制技术等资料。
(2)实验研究法:利用模拟装置进行实验验证,对精馏塔爆炸事故灾害控制技术进行测试和评估。
(3)案例分析法:通过分析近年来国内外精馏塔爆炸事故的典型案例,总结其经验和教训,为实际应用提供借鉴。
5.预期成果通过精馏塔爆炸事故影响分析及其灾害控制技术研究,预计取得以下成果:(1)形成完整的精馏塔爆炸事故分析方法体系,揭示其成因和影响因素,并建立可行的控制措施。
(2)提出适用于不同类型精馏塔的灾害控制技术,明确各种控制手段的优缺点,为相关行业和企业提供指导。
(3)总结精馏塔爆炸事故的应急处置措施和预防措施,对制定安全管理和培训方案提供有益参考。
6.可行性分析本研究旨在对精馏塔爆炸事故的成因、影响和控制技术进行系统分析和研究,具有较强的实践意义和理论意义。
连续精馏塔装置控制系统设计开题报告

连续精馏塔装置控制系统设计开题报告本科生毕业设计(论文)开题报告题目:连续精镏实验装置控制系统设计姓名:学号:200806220131年级:08 专业:化学化工与工艺指导教师:姓名董凯职称学科年月日说明一、开题报告前的准备毕业设计(论文)题目确定后,学生应尽快征求导师意见,讨论题意与整个毕业设计(论文)(或设计)的工作计划,然后根据课题要求查阅、收集有关资料并编写研究提纲,主要由以下几个部分构成:1.研究(或设计)的目的与意义。
应说明此项研究(或设计)在生产实践上或对某些技术进行改革带来的经济与社会效益。
有的课题过去曾进行过,但缺乏研究,现在可以在理论上做些探讨,说明其对科学发展的意义。
2.国内外同类研究(或同类设计)的概况综述。
在广泛查阅有关文献后,对该类课题研究(或设计)已取得的成就与尚存在的问题进行简要综述,只对本人所承担的课题或设计部分的已有成果与存在问题有条理地进行阐述,并提出自己对一些问题的看法。
3.课题研究(或设计)的内容。
要具体写出将在哪些方面开展研究,要重点突出。
研究的主要内容应是物所能及、力所能及、能按时完成的,并要考虑与其它同学的互助、合作。
4.研究(或设计)方法。
科学的研究方法或切合实际的具有新意的设计方法,是获得高质量研究成果或高水平设计成就的关键。
因此,在开始实践前,学生必须熟悉研究(或设计)方法,以避免蛮干造成返工,或得不到成果,甚至于写不出毕业设计(论文)或完不成设计任务。
5.实施计划。
要在研究提纲中按研究(或设计)内容落实具体时间与地点,有计划地进行工作。
二、开题报告1.开题报告可在导师所在教研室或系内举行,须适当请有关专家参加,导师必须参加。
报告最迟在毕业(生产)实习前完成。
2.本表(页面:A4)在开题报告通过论证后填写,一式三份,本人、导师、所在系(要原件)各一份。
三、注意事项1.开题报告的撰写完成,意味着毕业设计(论文)工作已经开始,学生已对整个毕业设计(论文)工作有了周密的思考,是完成毕业设计(论文)关键的环节。
乙醇精馏塔的开题报告

乙醇精馏塔的开题报告1. 引言乙醇精馏是一种常用的分离技术,广泛应用于工业生产和实验室研究中。
乙醇精馏塔作为乙醇精馏中的核心设备,起到了关键的作用。
本开题报告旨在对乙醇精馏塔进行初步的研究,为后续的详细设计提供依据。
2. 研究目的和意义乙醇精馏塔的设计和优化对乙醇的分离纯化具有重要的意义。
通过研究乙醇精馏塔的设计参数,可以提高乙醇产率和纯度,降低生产成本,实现经济效益和环境效益的双重提升。
因此,本研究的目的是对乙醇精馏塔的性能和操作进行深入的研究和优化。
3. 研究方法本研究将采用以下方法进行乙醇精馏塔的研究:1.文献调研:收集相关乙醇精馏塔的设计和优化方面的文献,对已有研究进行综述分析;2.实验研究:设计和搭建一个小型乙醇精馏塔实验装置,通过改变操作条件,测量和分析乙醇精馏塔的性能指标,如乙醇纯度、产率等;3.数值模拟:利用计算流体力学(CFD)软件对乙醇精馏塔进行数值模拟,探索不同操作参数对乙醇分离效果的影响。
4. 预期结果通过以上研究方法,我们预期可以得到以下结果:1.对乙醇精馏塔设计和优化方面的文献进行综述分析,总结目前已有的研究成果和不足之处;2.实验研究可以得到乙醇精馏塔在不同操作条件下的性能指标,如乙醇纯度和产率的变化规律;3.数值模拟可以模拟和分析乙醇精馏塔的内部传质和传热过程,揭示操作参数对乙醇分离效果的影响规律。
5. 计划安排本研究的计划安排如下:1.第一阶段(1个月):文献调研和综述分析,了解乙醇精馏塔的相关设计和优化研究;2.第二阶段(2个月):设计和搭建小型乙醇精馏塔实验装置,进行实验研究;3.第三阶段(2个月):收集实验数据,进行数据分析和结果总结;4.第四阶段(1个月):利用CFD软件进行乙醇精馏塔数值模拟研究;5.第五阶段(1个月):整理实验和模拟结果,撰写乙醇精馏塔的设计和优化报告。
6. 预期贡献本研究的预期贡献包括:1.对乙醇精馏塔设计和优化方面的文献进行综述分析,为后续研究提供参考;2.实验研究可以得到乙醇精馏塔的性能指标变化规律,为工业生产提供优化方案;3.数值模拟可以揭示乙醇精馏塔内部传质和传热过程的细节,为塔的设计和操作提供理论依据。
过控专业苯精馏浮阀塔毕业设计开题报告

2.2浮阀塔的缺点
(1)阀孔易磨损。
(2)阀片易脱落。
(3)不宜处理易结焦或黏度大的系统。
3课题研究的意义
塔设备是化工、炼油生产中最重要的设备之一。它可使气液或液液两相之间进行紧密接触,达到相际传质及传热的目的。在化工或炼油厂中,塔设备的性能对于整个装置的产品产量、质量、生产能力和消耗定额以及三废处理和环境保护等各个方面都有重大的影响。
负责人(院系公章):年月日
2浮阀塔介绍
浮阀塔是在筛板塔基础上,在每个筛孔除安装一个可上下移动的阀片。当筛孔气速高时,阀片被顶起上升,空速低时,阀片因自身重而下降。阀片升降位置随气流量大小自动调节,从而使进入夜层的气速基本稳定。又因气体在阀片下侧水平方向进入液层,既减少液沫夹带量,又延长气液接触时间,故收到很好的传质效果。浮阀塔有活动泡罩、圆盘浮阀、重盘浮阀和条形浮阀四种形式。浮阀主要有V型和T型两种。
该过程构造简单,造价低廉,具有足够操作弹性,且具有较强的工程使用价值。该过程的推广和普及,将加速我国工业生产过程节能技术的进步,带动一大批的相关技术和产业的发展。
【研究的主要内容及预期目标】
完成分离一定苯-对二甲苯精馏浮阀塔的设计计算,包括塔、塔板的设计及换热器设计两大部分。塔和塔板的设计主要是根据化工原理相关知识进行的设计计算,目的是确定精馏浮阀塔的工艺参数,包括确定塔的操作温度、操作压力及气、液相流量,塔的有效高度、实际塔板数、塔径、板间距、塔板结构及操作弹性等参数。换热器的设计是指附属设备设计部分,即计算塔顶冷凝器、塔釜再沸器的换热形式,换热器的面积,确定塔顶冷却水、塔釜加热蒸汽的流量;泵的设计亦属附属设备的设计部分,主要确定离心泵的类型。
Φ1000甲醇精馏塔设计任务书,开题报告

设计(论文)题目
甲醇精馏塔设计
设计(论文)题目来源
自选
设计(论文)题目类型
工程设计
起止时间
2009.1.6~6.8
一、设计(论文)依据及研究意义:
甲醇用途广泛,是基础的有机化工来自料和优质燃料。主要应用于精细化工,塑料等领域,用来制造甲醛、醋酸、氯甲烷、甲氨、硫酸二甲脂等多种有机产品,也是农药、医药的重要原料之一。甲醇在深加工后可作为一种新型清洁燃料,也加入汽油掺烧。因此,甲醇在现实中需求量是比较大的,甲醇的大量生产也是很有必要的。
设计图纸折合0#图3张以上(其中手工绘图不少于1张1#图)。设计说明书12000字以上,并有2000~3000字的外文文献翻译和300字左右中英文摘要。
三、毕业设计(论文)基本要求
设计符合最新国家标准及行业标准。设计图样达到工程设计施工图水平。
四、毕业设计(论文)进度安排
2013.1.7---2013.1.14 文献查阅
三、设计(论文)的研究重点及难点:
重点是::
物料衡算、热量衡算和塔设备的尺寸计算和确定以及强度计算和校核。
难点是:
一、由于甲醇精馏过程比较复杂以及现有理论的不完备,其难点为塔内的物料及热量衡算,并对其进行比较准确的计算。
二、由于本次设计的塔是满足常压下操作温度为120度的生产,其难点是对塔高、塔内径以及壁厚等进行比较优化的设计。
3、设计所需设计方法、软件、工具等。
六、指导教师意见:
签名:年月日
毕业设计(论文)任务书
学院:机械工程学院
题目Φ1000甲醇精馏塔设计
论文(设计)内容及要求:
一、毕业设计(论文)原始依据
装置参数:
操作压力常压
甲醇精馏工艺流程设计开题报告

甲醇精馏工艺流程设计开题报告英文回答:Title: Preliminary Report on the Design of Methanol Distillation Process.Introduction:The distillation process plays a crucial role in the separation and purification of chemicals. In this report, we will discuss the design of a methanol distillation process. The objective is to obtain high-purity methanol by separating impurities present in the crude methanol feed.Process Overview:The methanol distillation process typically consists of several stages, including preheating, distillation, and condensation. The crude methanol feed is first preheated to increase its vaporization efficiency. Then, it enters thedistillation column, where it is separated into different fractions based on their boiling points. The lighter components, such as water and methanol, vaporize and rise to the top of the column, while the heavier impurities remain at the bottom. Finally, the vaporized methanol is condensed and collected as the final product.Design Considerations:Several factors need to be considered during the design of the methanol distillation process. These include the selection of suitable column internals, determination of operating conditions (such as temperature and pressure), and optimization of reflux ratio. The choice of column internals, such as trays or packing, affects the separation efficiency and energy consumption. The operating conditions should be selected to ensure the desired separation while minimizing energy consumption. The reflux ratio, which represents the amount of condensed vapor returned to the column, also affects the separation efficiency.Simulation and Optimization:To design an efficient methanol distillation process, computer simulation tools can be used. Process simulation software, such as Aspen Plus or HYSYS, can model the distillation column and predict its performance under different operating conditions. By using these tools, engineers can optimize the process parameters to achieve the desired separation efficiency and minimize energy consumption.Conclusion:In conclusion, the design of a methanol distillation process requires careful consideration of various factors, such as column internals, operating conditions, and reflux ratio. Computer simulation tools can aid in the optimization of the process parameters. The successful design of an efficient methanol distillation process can lead to the production of high-purity methanol, which is essential for various industrial applications.中文回答:题目,甲醇精馏工艺流程设计开题报告。
筛板精馏塔毕业设计开题报告

五、指导教师意见 六、所在系意见
指导教师签名:
日期: 年 月 日
负责人签名(签章):
日期: 年 月 日
注:此件由学生本人填写,一式二份,院(部)、指导教师各存一份。
遍用作 H2S-H2O 双温交换过程的冷、热塔,应用于蒸馏、吸收和除尘等。筛板精馏塔属于
板式塔,筛板精馏塔具有结构简单,造价低,板上液面落差小,气体压降小,生产能力大,
气体分散均匀,传质效率高的优点,是化工生产中常见的单元操作设备之一。
(二)研究现状:
筛板塔始于 1830 年,是结构最简单的一种板型。由于其操作弹性小,当气量过小或
过大时,易发生严重漏液或过量液沫夹带现象;而且易堵塞,不宜处理粘度大、易结焦的
物料,一度时间曾影响到它的应用推广。20 世纪 50 年代后,随着林德塔板、导向塔板的
应用推广,筛板塔又重新启用并日趋广泛。导向筛板是 60 年代由美国联合碳化物公司林
德子公司开发应用的,国内有北京化工大学进行系统研究,他们认为导向筛板从导向喷出
定额,以及三废处理和环境保护等各个方面都有重大的影响。据有关资料报道,塔设备的
投资费用占整个工艺设备投资费用的油等行业的极大重视。
塔设备是化工、石油等工业中广泛使用的重要生产设备。它可使气(或汽)液或液液
两相之间进行紧密接触,达到相际传质及传热的目的。常见的、可在塔设备中完成的单元
(三)研究内容: 完成筛板精馏塔成套装置主体部分设计,包括工艺设计和结构设计两大部分。工艺设 计主要是根据化工原理相关知识进行的设计计算,目的是确定筛板精馏塔的工艺参数,包 括确定塔的操作温度,操作压力,气、液相流量,塔的有效高度,实际塔板数,塔径,板 间距,塔板结构及操作弹性等参数。结构设计是指压力容器设计部分,即计算塔的壁厚, 封头的结构及尺寸,精馏塔附件设计,接管设计等内容。最后绘制筛板精馏塔装备图及塔 板结构图。 (四)研究思路与方法: 拟采用以下设计步骤: 一、筛板精馏塔工艺设计计算部分 1.设计方案的确定; 2.精馏塔的物料衡算; 3.塔板数的确定; 4.精馏塔的工艺条件及有关物性数据的计算; 5.精馏塔的塔体工艺尺寸计算; 6.塔板主要工艺尺寸的计算; 7.筛板的流体力学验算; 8.塔板负荷性能图。
精馏塔自控系统设计开题报告

精馏是化工、石油化工、炼油生产过程中应用极为广泛的传质传热过程。精馏的目的是利用混合液中各组分具有不同挥发度,将各组分分离并达到规定的纯度要求。精馏过程的实质是利用混合物中各组分具有不同的挥发度,即同一温度下各组分的蒸汽分压不同,使液相中轻组分转移到气相,气相中的重组分转移到液相,实现组分的分离。
文献综述内容(在充分收集研究主题相关资料的基础上,分析国内外研究现状,提出问题,找到研究主题的切入点,)
精馏是分离液体混合物最常用的一种单元操作,在化工﹑炼油﹑石油化工等工业中得到广泛的应用.
精馏塔是精馏过程中关键的设备,它是一个非常复杂的现象。在精镏操作中,被控变量多,可以选用的操作变量亦多,它们之间又可以有各种不同组合,所以控制方案亦多。由于精馏塔对象的通道很多,反应缓慢,内在机理复杂,变量之间相互关联,加以对控制要求又较高,因此必须深入分析工艺特征,总结实验经验,结合具体情况,才能设计出合理的控制方案。
昆明理工大学毕业设计(论文)
开 题 报 告
题 目:精馏塔自控系统应用设计学 Leabharlann :信息工程与自动化学院专 业:
学生姓名:
指导教师:
日 期:2015/3/13
一.毕业设计(论文)的主要内容:
主要内容:1了解精馏塔的工艺过程及相关监控参数;2完成监控系统方案设计;3完成设备软硬件选型;4完成系统配柜设计及接线图设计;5完成系统编程设计;
作为在工业过程控制中应用广泛的先进控制算法,预测控制与自适应控制在精馏装置中的应用受到了广泛关注。Karacan[4]等对预测控制技术在精馏塔上的应用做了一系列的研究,提出并使用多种预测控制算法用于精馏试验装置的控制。在他们的研究中。采用了当过程输出与模型输出的偏差增大时向控制量中加入伪随机信号并使用Bierman算法对模型进行重新辨识的方法,保持控制器始终能有良好的控制效果。Bezzo针对一种中槽连续精馏结构,构建了基于MPC的MIMO控制系统。Fileti将可编程自适应控制器(PAC)、自整定调节器和基于神经网络建模的模型预测控制算法用于实验间歇精馏装置的控制。Tian为降低模型要求,提出了基于模式模糊预测的预测控制,克服输入输出模型仅在特定工作点有效的局限性。Roffel对精馏塔建立机理模型,并在多变量MPC中引入了系统输入的约束,以避免暂时性的输入饱和,与使用增益调度的单回路PID方法相比,控制效果有明显的改善。Volk将多变量预测控制与前馈策略应用于原油分馏塔的实际生产中,并通过降低压力减小能量消耗,收到了良好的效果。Engelien纠与Skogestad通过数值仿真,研究了自优化控制技术在热集成精馏系统中的应用,以期在系统变化的情况下控制系统仍能保持较好的性能。Karacan。则将广义最小方差自适应控制和极点配置方法应用于填料精馏塔的控制。Oisiovici设计了基于塔顶塔底物料平衡的带有遗忘因子和前馈自调节控制器,通过调节回流比控制塔顶组分含量的控制系统。
板式精馏塔开题报告
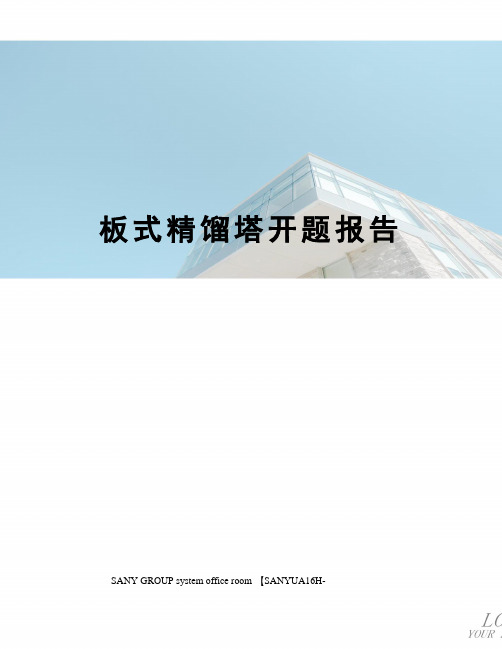
板式精馏塔开题报告 SANY GROUP system office room 【SANYUA16H-
榆林职业技术学院神木校区
毕业设计(论文)开题报告
板式精馏塔的设计
年级: 13级
学号: 13080355
姓名: ****
专业: 应用化工
指导老师: 刘
榆林职业技术学院印制
二零一六年五月
的设计→筛板的流体力学验算
4. 可行性论证
(1)精馏塔节能优化的研究
精馏塔研究内容即控制目标是在保证产品质量合格的前提下,使塔的回收率达到最高、能耗可以最低。
当前精馏塔的节能低耗一直是理论及实践研究的热点和难点,经过众多科技人员的努力取得了如下一系列成果:
①提高冷凝器或再沸器的换热效果;
②应用多效精馏技术,改变多塔精馏过程的流程,减少其回流比从而改变精馏塔操作压力;
③开发出替代普通板式塔和低效填料的高效规整填料;
④将热泵技术应用于精馏塔节能控制中。
(2)精馏塔控制策略的研究
精馏过程是一种多变量系统,其具有较长的死时延滞,且变量之间多是相互关联的,所以对其进行动态分析是很复杂且很困难的,变量配对较困难,这些都导致了精馏过程的控制一直都是过程控制界的理论研究及实践的热点和难点。
精馏塔控制的相关研究主要集中于以下方面:
①精馏过程是非线性的,所以如何把非线性控制技术应用在精馏塔的控制中一直是研究热点;
②智能控制方法,如模糊控制、神经网络等,在精馏塔控制中的应用;
③精馏塔的控制系统设计。
尤其是线性多变量控制技术、预测控制、自适应控制及鲁棒控制算法等的研究和开发;
④精馏塔的节能控制中控制和优化策略的运用。
注:栏目空间不够可另加附页。
精馏过程的控制系统设计-开题报告

开题报告书
精馏过程的控制系统设计题目
拟采取的研究方法、技术路线、实验方案及可行性分析
研究方法:
前期查阅资料了解本次设计的目的及意义,并充分了解精馏过程的静态特性及动态特性。
根据已有资料和工程经验,确定主控制变量和辅助控制变量。
然后分析系统各变量的耦合关系,通过控制相关变量达到控制要求。
最后利用内模控制算法建立精馏控制系统并搭建Simulink仿真模型进行验证。
技术路线
精馏是一个多变量、强耦合、难以建立精确的数学模型的过程。
选取塔顶的温度和塔底的温度为被控变量。
对于塔顶温度选取塔顶的回流量作为操纵变量;对于塔底的温度选取塔底再沸器的蒸汽流量作为操纵变量。
二者均采用串级控制的方案;串级控制的主控制器采用内模控制的算法,由于副回路包括的扰动主要为反应快速的流量扰动,故仅采用简单的PI控制即可。
塔顶与塔底的温度存在着强耦合,故还需要对两个控制变量进行解耦。
控制系统方框图如下,
其中R1为塔顶回流量R2为塔底再沸器的蒸汽流量;G C11G C21 G C12 G C22 为内模解耦控制器,G C1 G C2为副控制器,G P1 G P2为流量模型,G P11 G P21 G P12 G P22为实际温度模型, G m11
G m21 G m12 G m22内部对象模型,Y1 Y2为塔顶和塔底的温度的输出值。
实验方案及可行性分析
运用MATLAB中的Simulink模块构建系统模型,对系统进行调试和仿真。
本设计利用抗扰特性优良的串级控制和可以克服时间滞后的内模控制的控制策略构成多回路的系统。
此种控制方法可以用于非线性、时变的系统,克服多种扰动,并且易于实现,可行性高。
化学毕业论文开题报告范文

化学毕业论文开题报告范文开题报告是提高选题质量和水平的重要环节,它主要说明这个课题研究的意义以及可行性,下面是搜集整理的化学毕业论文开题报告范文,供大家阅读查看。
论文题目:用工业酒精年产10000吨纯酒精的精馏塔的设计一.论文研究目的及意义:随着生产的发展和技术的进步,对酒精的理化指标和感官指标提出了更高的要求。
对于高纯度酒精我们并不陌生,我国早在50年代就已按酒精质量不同将其分为四类,即高纯度酒精、精馏酒精、医药酒精、工业酒精。
高纯度酒精要求不低于96.2%(v/v),是一种严格中性没有杂味的酒精,专供国防工业、电子工业与化学试剂用。
目前能够规模化生产高纯度酒精的方法有共沸精馏法、萃取精馏法、膜分离法和吸附法。
共沸精馏(恒沸精馏)工艺是在常压无法制取无水乙醇的情况下,通过向乙醇溶液添加夹带剂(如苯、环己烷、戊烷等)进行精馏的,夹带剂与乙醇溶液中的乙醇和水形成三元共沸物,可获得纯度很高的乙醇。
其主要优点是产量大、质量好、生产稳定、技术成熟。
缺点是能耗较高,且在夹带剂操作不当时会引起环境污染。
因此,在工业化生产纯酒精的同时如何能提高酒精的纯度和减少能源的消耗成为目前最首要的目的。
参考文献:[1]沈之申,等.酒精生产技术的回顾与探讨[M][2]天津大学技术开发中心.高纯度酒精差压精馏技术[J]酒精工业,15(2)[3]天津冠达实业总公司.高纯度酒精差压境馏技术[J]酒精工业,15(1)[4]王君高.正确理解挥发系数与精馏系数[J]酿酒科技1998,(3)52-54[5]王君高.酒精蒸馏杂醇油比甲醇易分离[J]酒精工业,10(2)[6]王君高.酒精蒸馏杂质分类依据的讨论[J]酒精工业,11(2)(B2)昭62-19833酒精蒸馏法[J][7]BGl8350?2001,变性原料乙醇使用标准(S).[8]唐艳红,无水乙醇制各方法的研究进展(J).中国酿造,20XX,(5)4-6.[9]ZALDIVAR,NIELSENJ,OLSSONL.FuelethanolproductionfromLigno cellulose:Achallengeformetabolicengineeringandprocessintegr ation[J].ApplMicrobiolBiot,2001,56:17-34[10]KHESHGIHS,PRINCERC,MARLANDG.Thepotentialofbiomassfuelsi nthecontextofglobalclimatecchange:Focusontransportationfuel s[J].AnnuRevEnviron,2000,25:199-244[11]LADISCHMR,DYCKK.DehydrationofEthano:lNewapproachgivespo sitiveenergybalance[J]Sc,i1979,205:898-900二.本课题要研究或解决的问题和拟采用的研究手段(途径):研究:苯三元恒沸精馏脱水是纯酒精生产的传统工艺。
开题报告

西南科技大学城市学院毕业设计(论文)开题报告学院专业班级过程装备与控制工程0901 姓名学号题目苯—氯苯分离过程板式精馏塔的设计题目类型设计开发一、选题背景及依据(简述国内外研究现状、生产需求状况,说明选题目的、意义,列出主要参考文献)1、国内外研究现状气—液传质设备主要分为板式塔和填料塔两大类。
精馏操作既可采用板式塔,也可采用填料塔。
板式塔为逐级接触型气-液传质设备,其种类繁多,根据塔板上气-液接触元件的不同。
可分为泡罩塔、浮阀塔、筛板塔、穿流多孔板塔、舌形塔、浮动舌形塔和浮动喷射塔等多种。
板式塔在工业上最早使用的是泡罩塔(1813年)、筛板塔(1832年),其后,特别是在本世纪五十年代以后,随着石油、化学工业生产的迅速发展,相继出现了大批新型塔板,如S型板、浮阀塔板、多降液管筛板、舌形塔板、穿流式波纹塔板、浮动喷射塔板及角钢塔板等。
目前从国内外实际使用情况看,主要的塔板类型为筛板塔、浮阀塔及泡罩塔,而前者使用尤为广泛。
2、生产需求状况(1)市场需求现状随着各行各业的消费水平的提高,化工行业的苯与氯苯的需求也在不断的增大,所以相应的设备也在不断的改进,不断地发展。
现在筛式精馏塔还是比较成熟,但是还要不断地完善日益增长的生产需求。
要做到安全,高效率,高质量,自动化程度高。
在国内外生产苯等的一系列物质在染料、农药、医药等领域运用比较广泛,所以其生产设备也是必需的,也有市场空间。
(2)产业发展现状20世纪60年代初,美国精馏研究公司(FRI)又以工业的规模,使用不同物系,在不同操作压强下,广泛地改变了筛孔直径、开孔率、堰高等结构参数,对筛板塔进行了系统研究。
这些研究成果,使筛板塔的设计更加完美善,其中关于大孔径筛板的设计方法属于专利。
国内对大孔径筛板也做过某些研究。
3、选题的目的及意义本题目是根据过程装备与控制工程专业的培养目标而拟定的毕业设计题目,目的是提高学生理论联系工程实际和实际工程设计能力。
毕业设计丙烯精馏塔开题报告
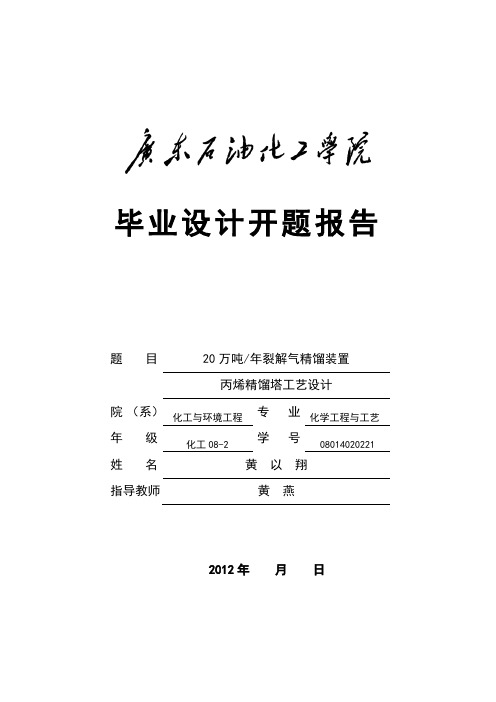
毕业设计开题报告
题目20万吨/年裂解气精馏装置
丙烯精馏塔工艺设计
院(系)
化工与环境工程专业
化学工程与工艺
年级
化工08-2 学号
08014020221
姓名黄以翔
指导教师黄燕
2012年月日
毕业设计开题报告
题目
20万吨/年裂解气精馏装置 丙烯精馏塔工艺设计 时
间 2012年2月29日起至2012年6月8日
本课题的目的意义
(含国内外的研究现状分析)
设计(论文)的基本条件
及设计(论文)依据
本课题的主要内容、
重点解决的问题
1、了解丙烯的性质,用途及质量标准
2、了解乙烯厂丙烯车间的基本生产工艺
3、了解国内外丙烯市场的基本情况
4、熟悉多组分精馏过程计算方法及浮阀塔设计基本步骤
5、对丙烯精馏塔进行工艺设计和强度计算
本课题欲达到的目的
或预期研究的结果
计 划 进 度
时 间 工 作 内 容 备 注
指 导 教 师 意 见
指导教师签名:
年 月 日 专 业 教 研 室 意 见
教研室主任签名:
年 月 日。
反应精馏隔壁塔合成碳酸二乙酯工艺的模拟与控制研究的开题报告
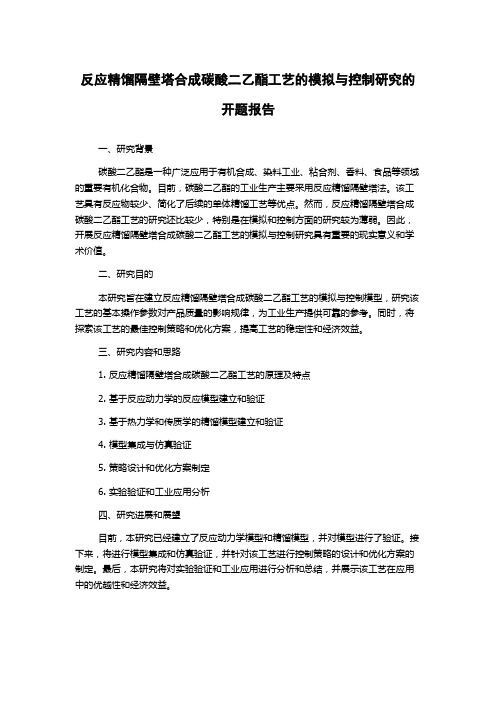
反应精馏隔壁塔合成碳酸二乙酯工艺的模拟与控制研究的
开题报告
一、研究背景
碳酸二乙酯是一种广泛应用于有机合成、染料工业、粘合剂、香料、食品等领域的重要有机化合物。
目前,碳酸二乙酯的工业生产主要采用反应精馏隔壁塔法。
该工艺具有反应物较少、简化了后续的单体精馏工艺等优点。
然而,反应精馏隔壁塔合成碳酸二乙酯工艺的研究还比较少,特别是在模拟和控制方面的研究较为薄弱。
因此,开展反应精馏隔壁塔合成碳酸二乙酯工艺的模拟与控制研究具有重要的现实意义和学术价值。
二、研究目的
本研究旨在建立反应精馏隔壁塔合成碳酸二乙酯工艺的模拟与控制模型,研究该工艺的基本操作参数对产品质量的影响规律,为工业生产提供可靠的参考。
同时,将探索该工艺的最佳控制策略和优化方案,提高工艺的稳定性和经济效益。
三、研究内容和思路
1. 反应精馏隔壁塔合成碳酸二乙酯工艺的原理及特点
2. 基于反应动力学的反应模型建立和验证
3. 基于热力学和传质学的精馏模型建立和验证
4. 模型集成与仿真验证
5. 策略设计和优化方案制定
6. 实验验证和工业应用分析
四、研究进展和展望
目前,本研究已经建立了反应动力学模型和精馏模型,并对模型进行了验证。
接下来,将进行模型集成和仿真验证,并针对该工艺进行控制策略的设计和优化方案的制定。
最后,本研究将对实验验证和工业应用进行分析和总结,并展示该工艺在应用中的优越性和经济效益。
乙烯精馏塔非平衡级建模与仿真的开题报告

乙烯精馏塔非平衡级建模与仿真的开题报告一、选题背景及研究意义随着现代化工工艺的不断发展,乙烯已成为工业上的重要烃类,广泛应用于塑料、橡胶、合成纤维等领域。
乙烯精馏是制取高纯度乙烯的重要过程,其主要原理是利用不同组分之间的差异进行分离浓缩。
乙烯精馏塔作为乙烯精馏过程的核心设备,其性能优劣直接影响精馏效果和生产成本。
因此,对乙烯精馏塔进行建模与仿真分析是工程实践上必要的一环。
对于非平衡级的乙烯精馏塔,设计者需要对其进行动态稳定性分析,寻找最优的工艺参数,以保障其分离效果和处理能力。
而基于MATLAB/Simulink等软件进行建模仿真,有助于精馏塔的动态响应分析、传热和传质性能优化、控制方案设计等方面的研究。
因此,研究乙烯精馏塔非平衡级建模与仿真的方法和技术,具有重要的理论与应用价值。
二、研究内容、目标和要求1. 研究内容(1)乙烯精馏塔非平衡级精馏过程的数学模型建立;(2)利用MATLAB/Simulink开展乙烯精馏塔非平衡级仿真分析;(3)对乙烯精馏塔的性能进行参数优化,提高其工作效率。
2. 研究目标(1)建立乙烯精馏塔非平衡级的精馏过程数学模型,实现动态响应分析;(2)利用MATLAB/Simulink软件对乙烯精馏塔的动态响应进行仿真分析,验证数学模型的可靠性;(3)优化乙烯精馏塔的性能,提高其分离效率和处理能力。
3. 研究要求(1)对乙烯精馏塔精馏过程的动态特性和不稳定性有深入的理解;(2)具备数学建模和计算机仿真的基础知识;(3)具有较强的分析和解决问题的能力。
三、研究方法(1)文献综述:阅读相关文献,了解乙烯精馏塔的精馏过程以及模型化和仿真的方法和技术;(2)建模与仿真:使用MATLAB/Simulink软件,基于乙烯精馏塔的实际工艺参数,建立乙烯精馏塔精馏过程的数学模型,并进行仿真分析;(3)优化分析:对精馏塔的参数进行优化、分析,提高其分离效率和处理能力。
四、预期研究成果通过本研究,将得到以下成果:(1)对乙烯精馏塔的精馏过程建立非平衡级数学模型,实现动态响应分析;(2)利用MATLAB/Simulink软件对乙烯精馏塔的动态响应进行仿真分析,验证数学模型的可靠性;(3)优化乙烯精馏塔的性能,提高其分离效率和处理能力。
- 1、下载文档前请自行甄别文档内容的完整性,平台不提供额外的编辑、内容补充、找答案等附加服务。
- 2、"仅部分预览"的文档,不可在线预览部分如存在完整性等问题,可反馈申请退款(可完整预览的文档不适用该条件!)。
- 3、如文档侵犯您的权益,请联系客服反馈,我们会尽快为您处理(人工客服工作时间:9:00-18:30)。
DN700甲醇精馏塔设计一、甲醇精馏塔设计的背景与意义精馏塔是化工工业中广泛使用,是分离工艺中的重要设备。
而精馏是甲醇生产的重要后处理工序,在甲醇生产中占据重要的位置。
甲醇精馏塔是精馏的核心设备,它与产品质量回收率消耗定额三废排放及处理等方面密切相关甲醇精馏塔既可采用板式塔,也可采用填料塔。
近年来,我国精馏塔内件技术有了长足发展,如高效导向筛板、新型垂直筛板、新型导向浮阀塔板及新型规整填料等技术开始被广泛采用[1]。
甲醇精馏装置是甲醇生产的重要处理工序,其能耗占甲醇生产总能耗20%左右。
甲醇精馏技术的好坏直接关系到精甲醇的质量;先进、节能、高效的精馏装置,对降低成本、节能降耗、提高产品竞争力和企业经济效益起到重要的作用。
加强对甲醇精馏塔的研究与改进,不断满足化学工业的要求,达到低成本、低耗能、节能环保、绿色高效等要求,有利于我国化学工业科学快速的发展,不断赶上国际以及发达国家的脚步,提升自己的竞争实力。
二、国内外对本课题的研究现状现阶段,国内外的研究聚焦于新型高效性能塔板的开发及工业应用;塔板设计、开发更趋于科学化的方向。
在填料塔研究方面,不断研究新型、高效的填料来提高填料塔的效能。
随着时代的发展,国内外对精馏塔的研究更趋向于经济、安全、高效、清洁方向发展,推动精馏设备的前进与发展。
2.1精馏塔的发展从精馏设备的历史发展来看,精馏技术与石油、化学加工工业的发展是相辅相成、相互刺激、共同进步的发展关系。
精馏技术的任何进步,都会极大刺激化学加工工业的技术发展,同样在石油、化学加工工业发展的每一个历史阶段都会对精馏设备技术提出更高的要求。
①.阶段一:20~50年代●1920年,有溢流的泡罩塔板开始应用于炼油工业,开创了一个新的炼油时代●泡罩塔板对设计水平要求不高、对各类操作的适应能力强、对操作控制要求低等特性在当时被认为是无可替代的板型●Rachig环填料塔主要应用于较小直径的无机分离塔设备中,同时也开发了Pall环,标志着现代乱堆填料的诞生②.阶段二:50~70年代●消除放大效应的研究:AIChE研究●浮阀塔板的开发●FRI的成立●系统化的设计方法:1955年,Monsanto公司的Bolles发表了著名的“泡罩塔板设计手册”,首先提出了科学的、规范化塔板设计技术,该方法到目前为止仍然广泛流行●大孔筛板的研究③.阶段三:70~90年代●大型液体分布器的基础研究,使得填料塔的放大研究成功,并在减压塔中应用获得极大的经济效益和社会效益●计算机应用(辅助精馏塔放大效应的研究,计算塔板效率;精馏过程设计)●新型高性能浮阀塔板的开发及应用④.阶段四:80末至今●新型高效性能塔板的开发及工业应用●塔板设计、开发更趋于科学化的方向现有精馏设备的优点:●结构简单,造价低;●生产能力大,分离效率高;●操作弹性大,精馏效率较高。
所存在的问题:●对原材料的适应性存在差异;●容易堵塞,不宜处理易结焦、粘度大的物料;●生产能力和工作效率有待提高。
新型精馏设备的研究与发展趋向是全面的把高速、高效与简化结构结合起来。
较之旧型设备,性能都有所改进,材料与加工方面也有节约。
但它们都多少还存在某些问题和不足,如操作稳定性尚差,气液分配还有一定的缺陷。
当然随着进一步研究和生产数据的完善,新型精馏设备和其他化工设备一样,将不断更新换代,日趋完善。
为国际化学生产服务,为经济社会发展服务。
2.2国内对甲醇精馏塔的研究现状我国塔设备技术的发展,经历了一个漫长而又艰辛的过程。
自新中国成立以后,随着我国工业的快速发展,我国陆续建立了一批现代化的石油化工装置。
随着这些装置引进的新型塔设备,不仅在操作、使用这些设备方面提供了大量的第一手资料,还带动了塔设备的科研、设计工作,加速了这方面的技术开发。
塔器是工业广泛应用的重要单元设备。
在目前操作的塔器中,仍以板式塔为主,但开发应用新塔,则以填料塔为主导。
其中,金属环矩鞍、阶梯环、朗博帕克和各种波纹填料已接近理想填料,具有传质效率高、通量大、压降低和价格合理等特点,性能优于传统填料,集中代表了现代塔填料水平。
填料塔的放大技术取得重大突破,出现了新型填料塔不仅取代传统填料塔而且也部分代替大型板式塔,乃至形成在炼油和石油化工行业与板式塔抗衡的新局面。
估计世界应用新型填料塔已不下万座,产生了巨大的经济效益和社会效应。
这就是新型填料塔分离技术主要发展趋势。
我国要继续跟踪国外塔分离技术最新发展动向,在已有基础上及时赶上和达到国际先进水平,创造更大经济效益和社会效益[2]。
在化工生产中,无论是精馏还是吸收、解析或萃取,其目的都是为了使得混合液中不同馏程的组分得以分离。
目前,我国常用的板式塔型仍为泡罩塔、浮阀塔、筛板塔和舌形塔等[3]。
目前板式塔的形式已有一百多种,在化工生产中最广泛应用的是泡罩塔、浮阀塔及筛板塔。
塔板技术的发展:●开孔方式及其新开孔构件的发展;●塔板空间的合理利用;●新降液管结构●气液接触构型的复合和交融通过以上对现有塔设备技术发展的评述得出,国内现有板式塔设备技术的发展是在传统简单机制技术基础上的深化和完善,并在当前工业应用中表现出优良的操作性能,获得了可以满足现有生产要求的操作效果。
精馏是应用最广和规模最大的传质分离过程。
在化学工业中精馏设备的研究占有较大的比重,特别是在改革开放初期,设备研究论文数量比例较大,精馏过程模拟也是被普遍关注的研究课题,这与我国化学工业的高速发展对精馏装备及其设计的需求是相适应的。
进入21世纪以来,对采用反应精馏等非常规精馏方法实现精馏过程强化研究的关注显著增加,反映出我国精馏研究向复合过程创新研究方面发展的趋势。
这和我国化学工业的发展以及节能的倡导有所相关[4]。
精馏塔设备在生产过程中维持一定的压力、温度和规定的气液流量等工艺条件,其设备的性能对产品质量、产量、生产能力和原材料消耗以及三废处理和环境保护等,都有重要的影响。
是化工生产过程中必不可少的设备。
中国甲醇装置的整体技术装备水平,低生产工艺落后,发达国家以天然气合成甲醇的单位能耗一般低于30 GJ/t ,而中国生产能力较大的甲醇装置能耗多在40~50GJ/t小装置,由于采用国外已淘汰的高压法,单位能耗大多在60 GJ/t左右,显然满足燃料甲醇大宗化、低成本生产的需要,采用先进工艺、建设(超)大型化装置是唯一出路[5]。
甲醇精馏技术的好坏直接关系到甲醇的质量,先进、节能、高效的精馏装置,对降低成本、节能降耗、提高产品竞争力和企业经济效益起到重要的作用。
目前甲醇三塔精馏技术具有热利用率高、消耗低、易操作、产品质量好、环保效益高等特点,越来越多地被广泛推广和应用[6]。
填料塔具有结构简单、压降小,且可用各种材料制造等优点。
在处理容易产生泡沫的物料以及用于真空操作时,有其独特的优越性。
过去由于填料本体及塔内构件的不够完善,填料塔大多局限于处理腐蚀介质或不适宜安装塔板的小直径塔。
近年来由于填料结构的改进,新型高效、高负荷填料的开发,即提高了塔的通过能力和分离效能,又保持了压力降小及性能稳定的特点,因此填料塔已被推广到所有大型气液中,在某些场合,还代替了传统的板式塔。
随着对填料塔的研究和开发,性能优良的填料塔已被大量的应用于工业生产中。
2.3国外甲醇精馏塔的研究现状国外目前塔设备的研究方向是“在提高处理能力和简化结构的前提下,保持适当的操作弹性和压力降,并尽量提高塔盘的效率”,在新型填料方面则在努力的研究发展有利于气液分布均匀、高效和制造方便的填料。
国外出现了分隔壁精馏塔(Divided Wall Column,简称DWC)是一种完全热耦合的蒸馏塔,具有能耗低、投资少的优点。
早在1933年,Luster因裂解气分离而提出了DWC概念,并申请了美国专利。
最简单的隔板塔是在普通精馏塔中放人1块隔板,这样相当于2个精馏塔。
因此更大程度的利用了能量,降低了能耗。
DWCs[7]利用于一个广泛的化学物质的分离,如碳氢化合物、醇类、醛类、酮类、缩醛和胺。
原则上,DWCs都应用在板式塔和填料塔。
然而,到目前为止,绝大多数已经由Montz建造和由BASF SE利用作为填料塔。
现有的DWCs在具体特征上的细节是主要的秘密。
DWCs通常比普通蒸馏塔大,它们的直径可达5米。
对于超过三种成分混合物的分离,仅仅只有两个工业应用程序被报道过。
DWC共沸概念的集成、采掘和反应蒸馏原理表明显著降低了投资和运营成本。
目前,工业应用领域只存在萃取蒸馏(BASF SE和UOP)。
关于共沸和采掘的DWCs的文献是很稀少的。
一些调查已经进行了,从实验和理论上来讲,对于反应性DWCs。
一些模型已经被发展了,但是没有可以用的工业应用。
相比与传统的蒸馏塔,DWCs更加节能,需要的投资资本更少。
最近DWC应用的快速扩张允许我们预计大约350个工业应用可以预见直到2015年。
近几年来, 国外对DWC技术的研究和应用都十分重视。
美国、德国、日本、英国等都有专门的研究机构。
而我国在这方面还没有进行研究, 加快这一技术的开发和工业化步伐,有自己的知识产权, 是推进我国炼油、石化及化工行业的一项重要内容。
总之, DWC 技术是具有独特作用的精馏。
它在化学工业中的应用越来越广泛, 将取得的成果逐步加以推广, 必将创造极大的经济效益。
三、甲醇精馏塔的设计3.1甲醇精馏塔设计的原始资料设计一套甲醇回收装置,进料温度86℃,回流液温度63℃,进料中含甲醇76.39%(质量),进料流量2000kg/h,塔顶出料中含甲醇99.5%,经精馏后残液含甲醇1%。
精馏塔直径为Φ700,设计压力0.55MPa,设计温度160℃,介质为甲醇和水的混合物;再沸器直径为Φ1100,采用内置管盘加热,管内压力为0.9MPa,设计温度200℃,介质为水蒸汽。
再沸器采用立式容器结构,整套装置支撑在裙座上。
3.2设计要求完成装置总体结构设计,重点完成再沸器结构设计,以及各零部件的强度计算。
●完成设计说明书1份●完成设计图纸(总装配图和零部件图等折合3张零号图纸)●完成文献综述1份●完成外文翻译1份3.3设计步骤本设计的研究方法主要是结合设计内容和设计条件,参阅相关塔设备设计的资料,按照塔设备设计的要求进行设计,以达到培养我们设备设计工程概念的目的。
塔设备的设计一般主要包括两个部分:工艺设计和机械设计。
工艺设计中要初步确定各阶段混合物的物理特性,由计算得出的具体数据再进行塔高、塔径的最基本设计,主要是与填料有关的各种计算,在工艺设计的最后还要进行塔的附属设备设计。
进入塔设备的机械设计部分后,塔的结构形式渐渐明朗化。
机械部分要解决的问题,除了确定塔设备的各细节结构外,更重要的就是要做各种校核工作,以保证设计完成的塔设备不仅能够正常运转,而且必须符合国家安全生产的标准。