硅基片微型通孔加工技术
pdms硅微通道板产品制备

pdms硅微通道板产品制备PDMS硅微通道板是一种在硅基板上形成微型通道的复合材料,常被用于生物样品的处理和微流体应用中。
主要由两类材料组成:1)硅基板:由硅片、硅圆片或硅芯片组成,具有良好的热稳定性和电绝缘性能,适合深曝光技术、先进工艺制造所需的应用;2)PDMS(聚二甲基硅氧烷):PDMS有优异的化学稳定性和热稳定性,具有粘滞性能,可以有效地保持微通道板的圆滑表面和尺寸精度。
一、PDMS硅微通道板制备过程1. 制备光刻硅片:制备表面粗糙、金属化处理的硅片,并在硅片上进行光刻。
2. 密封处理:将PDMS高转换率连接到光刻的硅片,然后再将PDMS的外表面多次经过紫外线处理,使PDMS与硅片完全密封,形成一块微通道板。
3. 重新调节PDMS厚度:重新利用PDMS的表面拉伸或变形的特性处理,来调整其厚度。
4. 製作微通道:最后,使用微机械加工技术精确地建立微通道,将硅片裁剪成所需要的尺寸。
二、PDMS硅微通道板特点1. 表面质量优良:PDMS硅微通道板可以很好地满足微流体表面要求,可以有效地抑制结合物的吸附。
2. 半折痕強度高:PDMS的弹性模量比空气高,可以提供较高的折痕强度;宽带频率响应特性好,可在多个振荡周期频率范围内实现微流体应用。
3. 高灵敏度:由于PDMS具有良好的折形弹性性能,因此具有较高的微流体传感器灵敏度。
4. 抗化学牢度高:抗氧化性强,耐酸碱,耐腐蚀性能高,可以有效抗摩擦、抗坪硬化。
5. 灵活性高:相比于其他类型的微通道板,PDMS硅微通道板可以更大的应用于复杂的微流体系统,具有更高的灵活性。
三、PDMS硅微通道板的应用1. 用于样品处理:PDMS硅微通道板可以用于生物样品的制备、分离、检测等,可以有效地提高样品的处理质量。
2. 用于医学和生物学检测:PDMS硅微通道板可以作为先进的机器人系统和宏观系统中的微流体传感器,利用它完成生物学和医学检测,可以有效地提高检测精度。
3. 用于微型转换器研究:PDMS硅微通道板具有较高的折形弹性性能,通过引入复杂地零件,可以模拟自然界物质传递的微型转换器研究。
pdms硅微通道系统加工

pdms硅微通道系统加工
工艺
PDMS硅微通道系统是由支撑结构制备的微型管道系统,采用光刻技术进行制备的,可以用于在数百微米尺度上进行流体运动的模拟。
在实验室中可以运用PDMS硅微通道系统来调查微细管道内流体的特性,包括流动性能、流向变化、温度变化、最大浓度等等。
PDMS硅微通道系统的加工工艺可以总结为几个主要流程:
(1)首先,将原料PDMS释放在贴片机上,然后用贴片机对PDMS进行压缩,即烘烤处理模板,从而形成一个完美的薄膜。
(2)其次,将模板固定在光刻机上,用激光把所需要的管道图案刻到膜上,从而形成预先想要的微型管道。
(3)最后,将PDMS膜从模板中剥离,并做相应处理,以便更好的使用。
总结来说,PDMS硅微通道系统的加工工艺主要包括原料准备、压缩处理模板、激光刻管道图案、取出膜的四个步骤。
聚合物硅微通道板器件制备

聚合物硅微通道板器件制备
近年来,随着技术的不断发展,各类微通道板封装技术的实现,出现了许多新的应用前景,未来的微系统发展将在聚合物硅微通道板器件制备上具有重要意义。
聚合物硅微通道板,也称为硅基微通道板,是一种结构简单的微通道板,采用微米尺度的硅片与硅胶结合而成,并通过化学成膜技术将聚合物薄膜形成微通道,满足特定应用要求。
聚合物硅微通道板器件制备主要由几个步骤组成:首先,要确定自己要制作的微通道板,包括通道形状、尺寸、材料,将所有的信息输入计算机,然后根据计算机的要求,按照设计要求,将面板进行切割成多个模块,切割模片可以采用有机玻璃,硅胶等;其次,要根据设计方案,在切割好的模片上开孔,然后将所需材料一一放置;接着,将模片粘合在一起,形成微通道板,将微通道板表面进行化学处理,使其具有其他功能;最后,将处理好的微通道板,装入配套的设备中进行测试,反复进行测试,使得产品具有功能要求。
聚合物硅微通道板的性能良好,为各种小型微系统的技术支持,提供了可靠的硬件保证。
它们具有良好的化学稳定性,可以高温处理,可以应用于传感器、流控器、化学分析仪、微流控设备以及能源转换器等领域。
此外,聚合物硅微通道板还可以制作各种尺寸的微型器件,如微型抽样泵、变色滴定仪、毛细管混合器、微流控阀等。
聚合物硅微通道板可以满足不同尺寸,不同操作要求,从而完成复杂的微系统技术。
因此,聚合物硅微通道板器件制备等技术是微系统技术领域的重要研究内容,将对提高微通讯设备的效率,为实现智能设备的可持续发展贡献力量,是未来技术发展的重要方向。
纸基硅微通道生物芯片加工

纸基硅微通道生物芯片加工近年来,随着生物科技的发展,芯片技术在生物医学、药物研究、生物技术安全控制以及设备可靠性的检测等领域中的应用日益增多。
芯片技术正成为一种微小的、高度集成的工具,用于检测和分析大量生物样本,提高实验效率和更好地理解物理后果。
然而,由于芯片技术由微小器件组成,其制作成本较高,使得大多数人无法接触到。
目前,为了解决这一问题,研究人员提出了一种新的芯片技术,即纸基硅微通道生物芯片加工技术。
它将微小的硅晶片和纸一起组合在一起,形成一种微型、紧密集成的材料,可以实现高精度、低成本的生物芯片加工。
纸基硅微通道生物芯片加工技术的工作原理是将微小的硅晶片与纸张相连接,形成微型结构,该结构具有微型通道,能实现微流体控制,从而实现微型生物测试。
该技术可以显著提高微型生物测试的效率,可以将表面的活性部分对比度处理,以及采用PCR技术,可以增强芯片的信号。
由于它具有微小的特性,而且相比传统的芯片技术,其制作成本也更低,因此,在生物测试研究中显得尤为重要且成功。
此外,纸基硅微通道生物芯片加工技术还可以用于各种其他应用,比如液体传感器、气体传感器、环境检测器、抗生素检测器等。
它可以有效地实现物料调控、物质分离和物质分离等作用,从而满足不同类型的实验需求。
总之,纸基硅微通道生物芯片加工技术是一种低成本的微型生物测试技术,它可以显著提高实验的准确性和效率,可以用于多种生物和仪器测试,降低整体成本,满足多种不同的实验要求。
因此,该技术是一项重要的研究和开发,可以为生物和医学领域提供实用的工具,以便更好地了解和研究生物和药物的相关性。
本文仅介绍了纸基硅微通道生物芯片加工技术的基本原理,为了进一步提高该技术的应用效果,还需要进一步的研究和创新。
希望研究人员和未来的学者在此基础上不断创新,探索出更加有效的生物芯片加工技术,为社会做出更大贡献。
技术、生物科技和药物研究领域都是非常复杂的,也非常必要的。
纸基硅微通道生物芯片加工技术,正好满足了这些领域的实验需求,提供了一种低成本、高精度的解决方案。
硅通孔技术加工流程

硅通孔技术加工流程全文共四篇示例,供读者参考第一篇示例:硅通孔技术是一种常见的半导体加工技术,用于在硅片上制造微小的通孔,可用于集成电路的制造和其他应用领域。
在这篇文章中,我们将详细介绍硅通孔技术的加工流程,以及每个步骤的相关工艺和设备。
1. 原料准备硅通孔技术的原料主要是硅片,通常采用P型或N型硅片,其厚度通常在几毫米到几十毫米之间。
硅片需要进行表面处理和清洁,确保表面平整,无杂质和污染,以保证通孔加工的精度和质量。
2. 掩膜加工需要在硅片表面涂布一层光刻胶,然后使用光刻机对光刻胶进行曝光和显影,形成图案。
这个图案即为通孔的布局和大小。
在曝光和显影过程中,要确保光刻胶的质量和厚度一致,以保证通孔加工的精度和稳定性。
3. 离子注入在形成的光刻图案上,进行离子注入。
离子注入是一种常用的加工方法,可利用离子束在硅片表面形成通孔的起始。
注入进入硅片后,会产生损伤层,使硅片产生开孔的倾向。
4. 腐蚀加工在离子注入后,需要进行腐蚀加工,以完成通孔的加工。
常用的腐蚀方法有湿法和干法两种。
湿法腐蚀是将硅片浸泡在特定的腐蚀液中,使其表面受到腐蚀,形成通孔。
干法腐蚀是利用气体等的化学反应,将硅片表面进行腐蚀。
5. 清洗和检测通孔加工完成后,需要对硅片进行清洗,去除残留的腐蚀物和杂质。
然后,对通孔进行检测,检查其质量和精度是否符合要求。
通常会采用显微镜、扫描电镜等设备对通孔进行检测和分析。
6. 后处理需要对通孔进行后处理,可以采用化学沉积、物理气相沉积等方法,填充通孔,提高其导电性和机械稳定性。
也可以进行封装和保护措施,以增加通孔的使用寿命和可靠性。
7. 总结硅通孔技术是一种重要的半导体加工技术,具有广泛的应用前景。
通过对硅通孔技术的加工流程的了解,可以更好地掌握其工艺原理和关键步骤,进一步提高通孔加工的效率和质量。
希望本文能对硅通孔技术的研究和应用提供一定的参考和帮助。
第二篇示例:硅通孔技术加工是一种常见的硅加工工艺,主要用于制作各种微型电子器件和传感器。
硅通孔技术TSV研究ppt课件

GaAs 基TSV 20/03/2020
10μm 引脚间距
8μm厚 1.6μm
3.3μm
5
TSV的研究动态
概述
TSV应用市场预测
发展 状况
TSV的 应用
据法国调查公司Yole Development提供,到2015年,逻辑 和存储器方面的应用占TSV应用的比 例将大于30%,接触式图像传感器、 微机电系统,传感器占30%的市场, 存储器堆叠形成的动态随机存取存储
技术(电镀、化学气相沉积、高分子涂布等); ➢ 工艺流程——先通孔(via first)或后通孔(via 1ast)技术; ➢ 堆叠形式——晶圆到晶圆、芯片到晶圆或芯片到芯片; ➢ 键合方式——直接Cu-Cu键合、粘接、直接熔合、焊接和
混合等; ➢ 超薄晶圆的处理——是否使用载体。
GaAs 基TSV 20/03/2020
TSV的 应用
GaAs 基TSV 20/03/2020
Samsung’s 32-memory stacking (each chip is 20μm thick)
17
概述
发展 状况
TSV的研究动态
2011年10月,意法半导体宣布将TSV技术引入MEMS 芯片量产,在其多款MEMS产品(智能传感器、多轴惯性 模块)内,TSV以垂直短线方式取代传统的芯片互连方法, 在尺寸更小的产品内实现更高的集成度和性能。
硅通孔技术加工流程

硅通孔(Through Silicon Via, TSV)技术的加工流程通常包括以下几个关键步骤:
1. 通孔定义:
- 光刻:首先在硅晶圆上通过光刻工艺定义出TSV 的位置,使用光刻胶作为掩膜。
- 蚀刻:接着采用干法或湿法刻蚀技术,在硅晶圆中垂直方向上形成通孔。
2. 绝缘层沉积:
- 通孔形成后,需要在其内壁沉积绝缘材料,如二氧化硅(SiO₂)、氮化硅(Si₂N₂)等,以保证后续金属填充时不会与硅衬底短路。
3. 种子层沉积:
- 在绝缘层内部沉积一层薄金属层,作为后续电镀填充金属的种子层,常用材料为铜(Cu)。
4. 金属填充:
- 通过电化学沉积(Electroplating)或物理气相沉积(PVD)方法将金属(通常是铜)填入绝缘层覆盖的通孔内,形成垂直互连导体。
5. 平坦化及背面减薄:
- 对完成金属填充后的晶圆进行化学机械抛光(CMP)处理,使晶圆表面变得平整,以便后续堆叠和封装。
- 可能还需要对晶圆背面进行减薄,以实现芯片的超薄化,满足高密度封装需求。
6. 端口开窗及焊盘制作:
- 在TSV上方和下方打开窗口,并形成焊盘或凸点结构,以便与其他芯片或基板连接。
7. 键合与封装:
- 使用直接Cu-Cu键合、微凸点键合、混合键合等方式将多层芯片或晶圆堆叠起来,并进行封装,形成最终的3D集成电路产品。
整个硅通孔加工流程涉及到精密的半导体制造技术和设备,旨在提高芯片间的互联密度、减少信号延迟以及缩小封装尺寸。
硅通孔技术

ASE Confidential / Security -B
© ASE Group. All rights reserved.
10
ASE Confidential / Security -B
© ASE Group. All rights reserved.
11
TSV与常规封装技术有一个明显的不同点,TSV的制作可以集成到制造工艺的不同阶段。在 晶圆制造CMOS或BEOL步骤之前完成硅通孔通常被称作Via-first。此时,TSV的制作可以在 Fab厂前端金属互连之前进行,实现core-to-core的连接。Via-first也可以在CMOS完成之后 再进行TSV的制作,然后完成器件制造和后端的封装。
ASE Confidential / Security -B
© ASE Group. All rights reserved.
18
超薄晶圆减薄技术
3D-TSV封装技术需要将晶圆/芯片进行多层叠层键合,同时还必须满足总封装厚度要求,必须 对晶圆厚度减薄至30~100 μm。传统单一晶圆减薄技术(表4)无法满足工艺要求,需要开发超 薄晶圆减薄技术当晶圆减薄至30 μm极限厚度时,要求表面和亚表面损伤尽可能小,一般采用 机械磨削+CMP、机械磨削+湿式刻蚀、机械磨削+干法刻蚀、机械磨削+干式抛光等四种减薄工 艺方案。
ASE Confபைடு நூலகம்dential / Security -B
© ASE Group. All rights reserved.
16
阻挡层及种子层金属淀积
通常TSV工艺采用电镀铜工艺进行通孔填充。Cu在SiO2介质中扩散速度很快,易使其介电性能 严重退化;Cu对半导体的载流子具有很强的陷阱效应,Cu扩散到半导体本体材料中将严重影响 半导体器件电性特征;Cu和SiO2的粘附强度较差,必须在二者中间淀积一层Ta、TaN/Ta、TiN 、TiW、Cr、Ti等扩散阻挡层,防止铜扩散并提高种子层的粘附强度。通常TSV硅通孔深宽比大 于7:1,甚至达到12:1~15:1。常规磁控溅射技术难以在高深宽比通孔侧壁上淀积连续的金属层 ,设备厂商开发了高离子化金属等离子磁控溅射技术。
cmos通孔技术加工流程

CMOS通孔(Through-Silicon Via,简称TSV)技术是一种用于三维集成电路的关键技术,它允许在多层硅片之间建立电气连接。
这种技术通常用于MEMS(微机电系统)制造和高级封装技术中,以提高芯片的性能和功能密度。
下面是CMOS通孔技术的一个基本的加工流程:晶圆制备:首先制备一个或多层硅晶圆,这些晶圆将作为后续加工的基础。
光刻:使用光刻技术在硅晶圆上形成通孔的图案。
这通常涉及到使用光敏化学物质形成掩模,然后通过紫外光曝光来定义通孔的位置。
刻蚀:在光刻之后,需要对硅晶圆进行刻蚀,以实际形成通孔。
刻蚀可以是湿法刻蚀或干法刻蚀,取决于所需的通孔形状和大小。
孔填充:在刻蚀形成通孔后,需要将这些孔洞填充with 导电材料,如铜或铝,以便形成电连接。
填充过程可能涉及化学气相沉积(CVD)或物理气相沉积(PVD)等技术。
化学机械抛光(CMP):为了确保填充材料平坦化并去除任何残留的杂质,通常需要进行化学机械抛光。
去除掩模:抛光后,需要去除用于光刻的掩模,这通常是通过刻蚀或湿法去除来完成。
后续加工:根据具体的应用需求,可能还需要进行其他加工步骤,如离子注入、化学气相沉积、物理气相沉积等,以形成额外的电特性或结构特性。
封装:通孔形成和填充后,通常会进行晶圆级封装,将多层硅晶圆堆叠并封装在一起,形成最终的产品。
测试:在整个加工流程结束后,需要对芯片进行电性能测试,以确保其符合设计要求和功能标准。
这个过程需要精密的设备控制和严格的工艺参数管理,以确保通孔的尺寸、形状和电性能符合设计要求。
硅通孔制造工艺

硅通孔制造工艺硅通孔制造工艺,这可是个挺有趣又有点复杂的事儿呢。
咱就把硅通孔制造工艺想象成盖房子打地基开洞的过程。
硅就好比是那块地,又硬又平的,是我们要进行操作的基础。
这个硅啊,它可不像咱们平常看到的泥土那么好摆弄。
硅是那种很稳定,很固执的材料,就像一个很有原则的老顽固,你想在它上面弄出通孔来,可不是简单地拿个工具戳一戳就行的。
那怎么开始这个制造通孔的过程呢?这得用到一些高科技的设备和特殊的工艺。
比如说光刻技术,这光刻技术啊,就像是在硅这个大地上画地图一样。
通过光照,就好像拿着一支特殊的笔,在硅的表面标记出我们想要打孔的地方。
这个光啊,可不是咱们家里的那种普通灯光,那是经过特殊处理的,有着精确的波长和能量的光。
就好比是一群训练有素的小士兵,按照特定的路线和指令,准确地在硅的表面进行标记。
标记好了之后呢,就要开始真正的打孔啦。
这时候就需要蚀刻技术登场了。
蚀刻就像是用小铲子一点一点地把硅给挖掉,挖出我们想要的通孔形状。
不过这小铲子可不是咱们家里的那种铁铲子,那是各种化学试剂或者离子束之类的东西。
化学试剂就像是一群小小的蚂蚁,它们按照光刻标记的路线,慢慢地啃食硅,把不需要的部分去掉。
离子束呢,就更厉害了,就像一群超级小的子弹,高速地射向硅,把硅给打下来。
在这个过程中啊,还得保证通孔的质量。
这通孔的质量可重要啦,就像房子的地基要是打歪了,房子肯定不稳当。
通孔要是质量不好,比如说孔壁不光滑,或者孔径大小不一致,那在后面往硅片上装各种电子元件的时候就会出大问题。
这就好比你做一个蛋糕,要是模具都是歪歪扭扭的,那做出来的蛋糕肯定也不好看,说不定还会影响口感呢。
要做出高质量的硅通孔,就得精确控制各种参数。
比如说蚀刻的时间啦,化学试剂的浓度啦,离子束的能量啦。
这就像炒菜一样,盐放多少,火候多大,时间多长,都得拿捏得准准的。
要是蚀刻时间太长,可能就把孔打得太大了,就像炒菜炒过火了,菜都焦了一样。
化学试剂浓度不合适,可能就蚀刻不均匀,就像做菜的时候调料放得不均匀,有的地方咸,有的地方淡。
硅微通道板产品制备

硅微通道板产品制备
本文将详细讨论硅微通道板产品制备技术这一研究内容。
硅微通道板是硅基复合材料制品,是一种具有精密蜂巢结构的微细孔道集合体,具有优异透气性、良好的可编程控制功能和稳定的**电化学表征性能**。
由于其独特的精密结构,硅微通道板在液体、气体及其他物质的分离、洗涤、扩散、蒸发及反应等方面具有显著优势,因此广泛应用于分离、催化及过滤方面的工程。
在制备硅微通道板之前,一般采用微细加工技术制作原材料,因其具有独特优越的性能,硅微通道板大多以硅材料为基础材料,经过薄膜制备,聚酰胺聚合物(polyimide)、热塑性树脂(thermoplastic)等材料均可用于制备硅微通道板。
一般通过以下几种方法制备硅微通道板。
*1. 激光焊接法*在聚酰胺薄膜上通过激光焊接技术制备复合材料,通过控制聚酰胺薄膜上微细孔道位置,形成具有精密结构的微细通道。
*2. 注入型聚合物*在硅中加入聚酰胺树脂及硅基复合物,经过高温加热聚合形成高密度的硅蜂巢结构,同时注入要衔接的材料获得更佳的复合性能。
*3. 电阻加热法*在硅基板表面加热通过热加压烘烤,然后结合硅基材料及电介质的双重孔道,形成硅微通道。
经过上述制备过程之后,硅微通道板得以制备完毕,可以应用在物质分离、过滤、蒸发和表面活性化等实际工程领域中。
本文介绍了硅微通道板产品制备技术的基本原理,主要包括激光焊接法、注入型聚合物和电阻加热法等,并介绍了它们在制备硅微通道板中的应用,为实际工程领域提供了有力的支持。
同时,硅微通道板具有优异的电化学表征性能,唯一的缺点就是价格昂贵,这可以通过更高效的制备工艺进一步改善。
硅微通道芯片加工
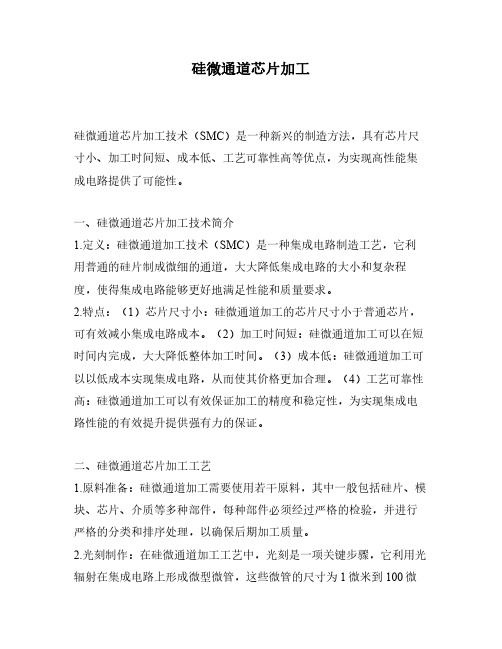
硅微通道芯片加工硅微通道芯片加工技术(SMC)是一种新兴的制造方法,具有芯片尺寸小、加工时间短、成本低、工艺可靠性高等优点,为实现高性能集成电路提供了可能性。
一、硅微通道芯片加工技术简介1.定义:硅微通道加工技术(SMC)是一种集成电路制造工艺,它利用普通的硅片制成微细的通道,大大降低集成电路的大小和复杂程度,使得集成电路能够更好地满足性能和质量要求。
2.特点:(1)芯片尺寸小:硅微通道加工的芯片尺寸小于普通芯片,可有效减小集成电路成本。
(2)加工时间短:硅微通道加工可以在短时间内完成,大大降低整体加工时间。
(3)成本低:硅微通道加工可以以低成本实现集成电路,从而使其价格更加合理。
(4)工艺可靠性高:硅微通道加工可以有效保证加工的精度和稳定性,为实现集成电路性能的有效提升提供强有力的保证。
二、硅微通道芯片加工工艺1.原料准备:硅微通道加工需要使用若干原料,其中一般包括硅片、模块、芯片、介质等多种部件,每种部件必须经过严格的检验,并进行严格的分类和排序处理,以确保后期加工质量。
2.光刻制作:在硅微通道加工工艺中,光刻是一项关键步骤,它利用光辐射在集成电路上形成微型微管,这些微管的尺寸为1微米到100微米,它们的形状由低级别的灯板来控制。
3.刻蚀:刻蚀是在集成电路加工过程中的一项关键步骤,它利用腐蚀剂和气体的作用将集成电路上的金属材料进行加工,以形成微小的通道。
4.填充:填充是硅微通道加工工艺中最重要的一项,它是将纳米粒子密封在硅片内,形成硅微通道网络,使之可以控制集成电路的触发和关断。
5.封装:封装是集成电路加工过程中的最后一步,它是将集成电路加工完毕后进行封装,以保护集成电路,确保其在使用过程中的可靠性。
三、硅微通道芯片加工技术的优点1.减小了产品的体积:硅微通道加工技术使得芯片的体积大幅度减小,具体来说可以减少整机的体积,进而降低产品的总体成本。
2.加速研发流程:硅微通道加工可以加快研发整体流程,在此过程中加入自动化操作,大大缩短集成电路的研发周期。
- 1、下载文档前请自行甄别文档内容的完整性,平台不提供额外的编辑、内容补充、找答案等附加服务。
- 2、"仅部分预览"的文档,不可在线预览部分如存在完整性等问题,可反馈申请退款(可完整预览的文档不适用该条件!)。
- 3、如文档侵犯您的权益,请联系客服反馈,我们会尽快为您处理(人工客服工作时间:9:00-18:30)。
收稿日期:2004203202;修订日期:2004203229 基金项目:2003年中国科学技术大学青年基金资助项目(K B0910) 作者简介:赵钢(1977-),男,河北人,博士,研究方向为基于并行压电探针的超高密度信息存储技术、微机电系统器件的加工与工艺技术研究;褚家如(1963-),男,安徽人,教授,博士生导师,博士,研究方向为三维微纳米器件的加工,微型传感器、致动器的集成以及微纳机电系统的封装技术等。
文章编号:100328213(2004)022*******硅基片微型通孔加工技术赵 钢,褚家如,徐 藻(中国科学技术大学精密机械与精密仪器系,合肥230027)摘要:介绍了硅基片微型通孔的用途及在微机电系统发展中的重要性,从原理、过程、优缺点等方面详细叙述了激光打孔法、湿法刻蚀法、深度反应离子刻蚀法(DRIE )和光辅助电化学刻蚀法(PAECE )等四种硅基片微型通孔的加工方法,并对各种方法进行了比较,提出了各种方法的适用范围。
关 键 词:微型通孔;微机电系统;深度反应离子刻蚀法;光辅助电化学刻蚀法中图分类号:TN405 文献标识码:A1 引言硅基片微型通孔是指贯穿硅片的孔径在微米量级。
在通孔中填充金属可使之成为导电通孔,常用于微机电系统(M EMS )和多层半导体器件的电信号传输。
图1为硅基片导电通孔的示意图。
使用微型导电通孔进行电信号的传输,有助于减小基片单面布线的复杂程度,提高阵列器件的排列密度,促进多层半导体结构的发展。
图2所示的悬臂梁探针阵列[1]采用倒装片技术,电信号通过导电通孔传导到硅片背面,这既可以避免引线接线柱对探针阵列并行工作时的干涉,又可以减小器件所在面的复杂程度,降低制造的难度。
图3所示的是多层硅片层叠的结构[2-3],导电通孔所起的作用是完成不同层之间电信号的传输,这种结构大大提高了系统的集成度。
图1 硅基片导电通孔示意图与硅基片导电通孔类似,在印刷电路板上也有承担传导电信号任务的通孔,但由于M EMS 对器件尺寸和阵列排列密度的要求,第2期2004年6月微细加工技术MICROFABRICA TION TECHNOLO GY №.2J un.,2004图2 悬臂梁探针阵列的示意图图3 多层硅片层叠结构硅基片微型通孔有其独特之处[4]:(1)硅基片通孔孔径远小于印刷电路板通孔孔径;(2)硅基片通孔的深宽比远大于印刷电路板通孔的深宽比;(3)硅基片通孔的密度远大于印刷电路板通孔的密度。
基于以上特点,硅基片微型通孔的加工有别于传统的通孔加工方法,因此其研究对M EMS和半导体工艺的发展起着极其重要的作用。
2 加工方法对于硅基片微型通孔来说,用于微型传感器和驱动器的导电通孔孔径为30μm~150μm,用于多层布线的导电通孔孔径更小,小于10μm[5]。
不同器件对硅基片的厚度有不同的要求,常见的硅基片的厚度为300μm~500μm,因此硅基片微型通孔的深宽比一般为几到几十。
硅基片中的导电通孔的深宽比较大,对准直性的要求也较高,而且通孔的加工不能影响后续的其它工序,因此使用与标准半导体加工技术相兼容的方法,加工出孔壁与硅片表面垂直的小孔径深孔是最理想的情况。
不同的加工方法各有利弊,下面对激光打孔法、湿法刻蚀法、深度反应离子刻蚀法(Deep Reactive Ion Etching,DRIE)和光辅助电化学刻蚀法(Photo Assisted Electro2Chemical Etching,PAECE)等四种方法进行具体分析。
2.1 激光打孔法早在上世纪70年代末期就有关于使用激光在半导体基片上打通孔的研究,报道显示当时有能力在325μm厚的基片上打出孔径小到12μm的通孔,深宽比达到26[4]。
1981年,Anthony在厚330μm的基片上用脉冲激光打出了10×10的微型通孔阵列,阵列中各孔的孔径不同,变化量从15μm~150μm,增量为15μm。
较小孔径的孔(15μm~60μm)是通过改变激光束径打成的,较大孔径的孔(75μm~150μm)是由多个单孔叠合而构成的。
竖直光滑的孔壁是通过适当地调整激光焦平面和基片相对位置而获得的[6]。
激光打孔是串行操作,一般是利用脉冲激光,靠热效应将孔烧蚀而成。
上面所说的Anthony在厚330μm的基片上打孔,每一个孔大约需要9个激光脉冲才能打穿[6]。
这在加工大规模孔阵列的时候对加工效率有一定影响。
更重要的是孔和孔之间相对位置的精确度完全靠进给机构保证,在孔阵列加工时易产生累积误差,不如使用光刻工艺加工,因为光刻工艺加工孔阵列是并行的,可以同时加工出阵列中所有的孔,孔和孔之间相对位置的精确度取决于光刻模板设计的精度以及光刻时的传递精度。
因此在加工大规模孔阵列的时候激光打孔法并非首选方案。
2.2 湿法刻蚀法湿法刻蚀是最常规的一种方法,这种方法在IC工艺和微细加工工艺中普遍使用,目前对湿法刻蚀的研究也较为透彻,能够比较好地对刻蚀过程进行控制,以达到预期的结构。
16第2期 赵钢等:硅基片微型通孔加工技术如图4所示,湿法刻蚀通常是先在硅基片背面沉积一层氧化硅或者氮化硅薄膜(图4a ),然后在需要打孔的位置刻蚀氧化层或者氮化层(图4b ),使用氧化层或者氮化层作为掩模,利用KOH 水溶液对硅片进行各向异性腐蚀,直到将硅片刻透(图4c )。
通孔的加工至此完成,后续工序还有在孔壁上沉积绝缘层和金属层,以达到导电的目的。
图4 湿法加工通孔工艺图 此方法简便易行,而且湿法刻蚀设备是半导体加工和微细加工常见而且必备的设备。
但是各向异性刻蚀在不同的晶向上有不同的刻蚀速率,这使得刻蚀出的通孔实际上是倒金字塔形,孔壁不与硅片表面垂直,而是成57.4°角,这就造成通孔两端尺寸差别很大,在硅片背面会被占去很大部分的面积,对于一般的硅基片(厚度为400μm 左右),背面刻蚀孔的直径(或边长)会达到100μm 以上。
因此这种方法无法加工高密度的孔阵列,只适合单个孔或者相距较远的若干个孔的加工。
2.3 深度反应离子刻蚀法(DRIE )在湿法刻蚀中由于孔壁和硅片表面成57.4°角,所以造成背面刻蚀孔过大,不适合于孔阵列的加工,如果孔壁能和硅片表面垂直,就能大大减小刻蚀孔的尺寸,因此深度反应离子刻蚀法(DRIE )也被尝试用作加工硅基片微型通孔。
DRIE 是一种能够得到较大深宽比的体加工方法,实验证明,用这种方法加工出的结构深宽比和宽度有很大关系,如图5所示[5]。
图图5 刻蚀深度和刻蚀结构宽度的关系 中纵坐标表示刻蚀深度,横坐标表示结构宽度;正方形标记表示刻蚀结构的截面图形为正方形,L 表示正方形边长;三角形标记表示刻蚀结构的截面形状为长方形,长方形长为1000μm ,宽为L 。
从图中可得,如果加工20μm ×20μm 的孔,那么加工深度最大为200μm ,所以一般厚度为400μm 左右的硅片要采用双面刻蚀的方式,才能保证通孔加工成功。
斯坦福的E 1M 1Chow 等人用双面刻蚀的方式在厚400μm 的硅片上加工出直径为20μm 的通孔,深宽比达20,如图6所示[7]。
这种加工方法与标准的半导体加工工艺图6 400μm 厚的硅基片中直径为20μm 的通孔26微细加工技术2004年相兼容,而且不受硅片类型和晶向的限制,p 型、n 型或者SO I 基片都可以作为被加工材料,这种方法加工出的通孔孔壁垂直性很好,大大优于湿法刻蚀法。
但这种加工的缺点是加工深度不能太深,在400μm 的硅片上加工直径为20μm 的通孔需要双面加工,这就要求非常精确的双面对准曝光,否则会影响成孔的导电性,因此也有使用湿法刻蚀和DRIE 相结合的方法[8],将硅片一面使用湿法刻蚀另一面使用DRIE ,这样避免了高对准精度的双面曝光,但是硅片的一面还是会被湿法刻蚀孔占去较大的面积,不利于高密度孔阵列的加工。
另外加工成本高也在一定程度上限制了DRIE 的应用。
2.4 光辅助电化学刻蚀法(PAECE )经A 1Satoh 提出[9],T 1Takizawa 等人发展[10],形成了PAECE 方法,使用这种方法可以加工出直径4.4μm ,间距15μm ,深度为480μm 的孔阵列,深宽比达到109,如图7所示[11]。
图7 深宽比达109的孔阵列截面图 PAECE 法的原理如图8所示,n 型(100)硅片在一定能量光照的作用下受到激发,在内部产生带正电荷的空穴。
而参与反应的电解液为稀释氢氟酸溶液,溶液中存在大量的带有负电荷的电子。
在外加电场的作用下,空穴和电子相向运动,在硅片表面预先加工出的倒金字塔形结构的尖端聚集,并发生如下方程式所示的化学反应,从而达到去除材料的目的。
图8 PAECE 的基本原理 反应方程式:Si +6HF +2hole (+)→H 2SiF 6+H 2+2H +这种方法的特点是:(1)巧妙地利用了光能量激发硅片中的空穴,并与电解液中带有负电荷的电子发生化学反应,生成可溶性物质,去除了被加工材料的残余,并无加工附产物堆积,不会对深部加工产生影响;(2)可以加工出一般刻蚀方法无法得到的较大深宽比结构;(3)是真正的并行加工方法,不仅可以加工单个孔,还可一次完成孔阵列中所有孔的加工;(4)原理简单明确,反应装置易于搭建,加工成本低,适合于实验室进行研究。
但这种方法也有其局限性,它只能应用于n 型(100)硅片。
表1对上述四种加工方法从不同方面进行了比较。
由于激光打孔法是串行操作,而湿法刻蚀法中被刻蚀孔在硅片背面占去很大面积,因此这两种方法不适用于大规模、高密度孔阵列的加工;DRIE 和PAECE 法都可以用于孔阵列的加工,DRIE 与标准的半导体工艺相兼容,对被加工的硅片没有特殊要求,但是DRIE 的加工成本较高,而且要加工较36第2期 赵钢等:硅基片微型通孔加工技术深的孔需要精确的双面对准曝光,这增大了加工的难度;PAECE 法加工成本低,实验装置简单,便于自行搭建,但这种方法只适用于n 型(100)硅片。
表1 四种加工方法的比较激光打孔法湿法刻蚀法DRIE PAECE 成孔质量最小孔径/μm12-20 4.4深宽比26-20109孔壁形状垂直于硅片表面 孔壁与硅片表面成57.4°角 垂直于硅片表面垂直于硅片表面与标准半导体工艺的兼容性不兼容兼容兼容不兼容局限性无局限有晶向要求无局限n 型(100)硅片加工成本高低高低加工方式串行并行并行并行3 结论硅基片微型通孔是微机电系统和半导体器件加工的基础工序之一,尤其是针对当前器件尺寸的微型化、元件的高密度化和系统的高集成度化,微型通孔在传导电信号方面更有其用武之地。
在硅片上进行微型通孔的加工主要有激光打孔法、湿法刻蚀法、深度反应离子刻蚀法(DRIE )和光辅助电化学刻蚀法(PAECE )等四种方法。