热处理淬火开裂及预防
热处理常见缺陷分析与对策-学习总结
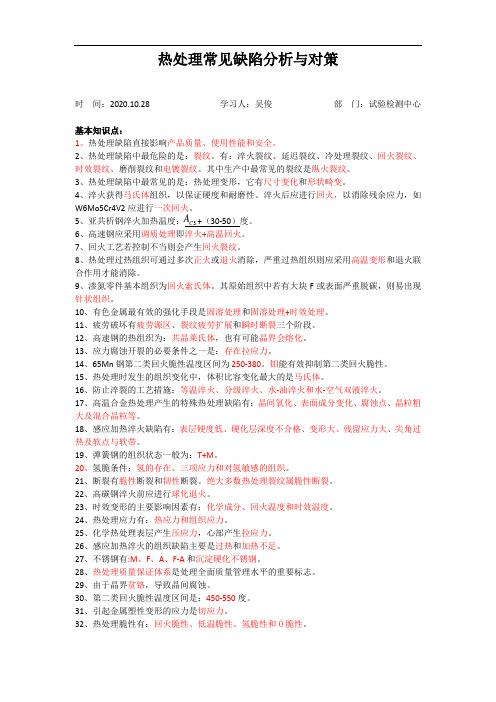
热处理常见缺陷分析与对策时 间:2020.10.28 学习人:吴俊 部 门:试验检测中心基本知识点:1、热处理缺陷直接影响产品质量、使用性能和安全。
2、热处理缺陷中最危险的是:裂纹。
有:淬火裂纹、延迟裂纹、冷处理裂纹、回火裂纹、时效裂纹、磨削裂纹和电镀裂纹。
其中生产中最常见的裂纹是纵火裂纹。
3、热处理缺陷中最常见的是:热处理变形,它有尺寸变化和形状畸变。
4、淬火获得马氏体组织,以保证硬度和耐磨性。
淬火后应进行回火,以消除残余应力,如W6Mo5Cr4V2应进行一次回火。
5、亚共析钢淬火加热温度: +(30-50)度。
6、高速钢应采用调质处理即淬火+高温回火。
7、回火工艺若控制不当则会产生回火裂纹。
8、热处理过热组织可通过多次正火或退火消除,严重过热组织则应采用高温变形和退火联合作用才能消除。
9、渗氮零件基本组织为回火索氏体。
其原始组织中若有大块F 或表面严重脱碳,则易出现针状组织。
10、有色金属最有效的强化手段是固溶处理和固溶处理+时效处理。
11、疲劳破坏有疲劳源区、裂纹疲劳扩展和瞬时断裂三个阶段。
12、高速钢的热组织为:共晶莱氏体,也有可能晶界会熔化。
13、应力腐蚀开裂的必要条件之一是:存在拉应力。
14、65Mn 钢第二类回火脆性温度区间为250-380。
钼能有效抑制第二类回火脆性。
15、热处理时发生的组织变化中,体积比容变化最大的是马氏体。
16、防止淬裂的工艺措施:等温淬火、分级淬火、水-油淬火和水-空气双液淬火。
17、高温合金热处理产生的特殊热处理缺陷有:晶间氧化、表面成分变化、腐蚀点、晶粒粗大及混合晶粒等。
18、感应加热淬火缺陷有:表层硬度低、硬化层深度不合格、变形大、残留应力大、尖角过热及软点与软带。
19、弹簧钢的组织状态一般为:T+M 。
20、氢脆条件:氢的存在、三项应力和对氢敏感的组织。
21、断裂有脆性断裂和韧性断裂。
绝大多数热处理裂纹属脆性断裂。
22、高碳钢淬火前应进行球化退火。
23、时效变形的主要影响因素有:化学成分、回火温度和时效温度。
42crmo淬火开裂危险尺寸

42crmo淬火开裂危险尺寸
摘要:
一、42CrMo 淬火开裂的定义和特点
二、42CrMo 淬火开裂的原因分析
1.原始材料原因
2.淬火原因
三、42CrMo 淬火开裂的预防措施
四、总结
正文:
一、42CrMo 淬火开裂的定义和特点
42CrMo 淬火开裂是指在42CrMo 钢经过淬火处理后产生的裂纹,这种裂纹往往在淬火过程中或淬火后的室温放置过程中产生,对钢材的性能和使用寿命有着重要的影响。
42CrMo 淬火开裂的特点是裂纹分布没有一定的规律,但一般容易在工件的尖角、截面突变处形成。
二、42CrMo 淬火开裂的原因分析
1.原始材料原因
42CrMo 钢在锻造过程中,可能会产生心部原始裂纹。
这些裂纹在淬火过程中会由于淬火应力而直接开裂。
另外,材料的元素偏析和原始组织粗大也可能导致开裂。
2.淬火原因
在淬火过程中,可能会出现以下几种情况:
a.淬火时使组织粗大,过热过烧组织,不同组织间的应力;
b.淬火油底下有一点水,引起的硬度不均匀;
c.淬火温度过高或过低,淬火后残余奥氏体过多或过少。
三、42CrMo 淬火开裂的预防措施
针对42CrMo 淬火开裂的产生原因,可以从以下几个方面进行预防:
1.严格控制淬火温度,避免过高或过低;
2.确保淬火油的质量和数量,避免油中混入水分;
3.合理设计工件结构,避免尖角、截面突变等容易产生应力集中的部位;
4.对原材料进行充分的热处理,减少原始裂纹。
四、总结
42CrMo 淬火开裂是一个严重影响钢材性能和使用寿命的问题。
TP347厚壁不锈钢管道热处理及裂纹预防措施

TP347厚壁不锈钢管道热处理及裂纹预防措施TP347不锈钢管是一种具有耐高温性能的不锈钢管,常用于化工、石化、石油和电力等领域的管道系统。
在使用过程中,由于管道的厚壁特性和工作环境的复杂性,需要进行热处理和裂纹预防措施,以确保管道的安全可靠运行。
本文将介绍TP347厚壁不锈钢管道的热处理工艺和裂纹预防措施。
1. 固溶处理固溶处理是不锈钢管道热处理的第一步,其目的是溶解不锈钢中的铁素体相和碳化物,提高管材的塑性和加工性能。
TP347不锈钢在固溶处理时应控制温度在1050-1100℃范围内,保持一定时间后迅速冷却,以防止管道产生过度固溶和晶粒长大。
2. 淬火处理淬火处理是为了使固溶后的不锈钢管道获得更高的强度和硬度。
经过固溶处理的TP347不锈钢管道在850-900℃温度范围内进行快速加热,然后迅速冷却,从而形成奥氏体组织,提高管道的抗拉伸强度和硬度。
冷处理是通过冷却不锈钢管道的表面,以增强其表面硬度和耐磨性。
TP347不锈钢管道在冷处理过程中,可以采用液氮或空气冷却的方式,使表面形成马氏体组织,提高管道的耐磨性和抗腐蚀性能。
1. 控制热处理过程在TP347不锈钢管道的热处理过程中,需要严格控制加热温度、保温时间和冷却速度,以避免热处理过程中产生过度固溶或快速冷却而引起的热裂纹。
还需要对管道进行预热和后热处理,以缓解热应力和提高管道的抗裂性能。
2. 选择合适的焊接材料和工艺TP347不锈钢管道在焊接过程中容易产生焊接裂纹,因此需要选择合适的焊接材料和工艺。
可以采用低氢焊接材料、预热焊接和控制焊接层减氢处理等措施,避免焊接过程中产生裂纹。
3. 加强检测和监控在TP347不锈钢管道的制造和使用过程中,需要加强对管道的检测和监控,及时发现管道表面和内部的裂纹,采取相应的修复和防护措施。
可以采用无损检测、压力测试和振动检测等手段,确保管道的完整性和安全性。
4. 优化设计和选材在工程设计阶段,需要根据不同的工作条件和环境要求,优化TP347不锈钢管道的设计和选材,选择合适的管道壁厚、材质和连接方式,减少管道的应力集中和热应力,降低管道的裂纹风险。
淬火处理常见裂纹类型及预防措施
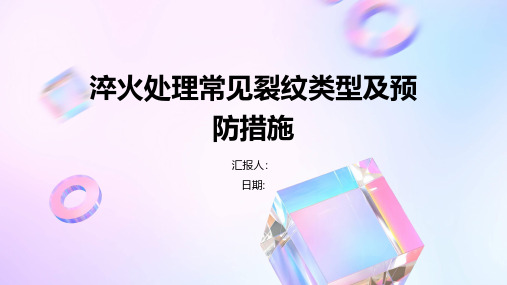
淬火处理常见裂纹类型及预防措施汇报人:日期:•淬火处理概述•淬火处理常见裂纹类型•淬火处理裂纹的预防措施目录•淬火处理的质量控制•淬火处理技术的发展趋势01淬火处理概述0102淬火处理的目的和原理淬火处理的原理是将金属材料加热到一定温度后迅速冷却,通过快速冷却使金属内部结构发生改变,从而实现性能的提升。
淬火处理的目的是提高金属材料的强度、硬度、耐磨性和韧性等性能。
将金属材料加热到一定温度。
保温一定时间,使金属内部结构调整均匀。
迅速冷却,使金属内部结构发生改变。
回火处理,进一步稳定金属内部结构,提高性能。
01020304淬火处理的基本步骤02淬火处理常见裂纹类型应力裂纹是在淬火过程中,由于工件内部温度不均匀,导致局部区域产生拉应力而产生的裂纹。
定义淬火过程中,工件内部温度变化大,导致内应力集中,尤其是在工件形状复杂或截面尺寸变化剧烈时,更容易产生应力裂纹。
原因采用缓慢淬火工艺,减小工件内外温差,降低淬火应力;合理设计工件结构,避免截面尺寸变化剧烈。
预防措施原因淬火后,工件内部仍存在一定的残余应力,当这些应力超过材料的屈服强度时,就会产生延迟裂纹。
定义延迟裂纹是淬火后,在工件冷却过程中,由于工件内部存在淬火应力,随着时间的推移,应力逐渐释放而产生的裂纹。
预防措施优化淬火工艺,降低淬火应力;淬火后进行回火处理,进一步释放内应力;采用喷丸、碾压等表面强化处理工艺,提高工件表面强度和抗疲劳性能。
淬火裂纹是由于淬火过程中,工件内部或表面局部区域温度过高或过低,导致相变不均匀,产生裂纹或开裂现象。
定义淬火过程中,工件内部或表面局部温度过高或过低,导致相变不均匀,产生淬火裂纹;淬火介质选择不当或冷却条件不良,也会引起淬火裂纹。
原因合理选择淬火介质和冷却条件;采用预冷、分级淬火等工艺措施,减小温度变化梯度;优化淬火工艺参数,避免出现过热、过冷现象。
预防措施淬火裂纹03淬火处理裂纹的预防措施预冷处理在淬火前进行预冷处理,可以减少工件在淬火过程中的温度变化,从而降低热应力。
钢的淬火裂缝产生原因及预防措施

工件淬火冷却时,如其瞬时内应力超过该时钢材的断裂强度,则将发生淬火裂缝。
因此产生淬火裂缝的主要原因是淬火过程中所产生的淬火应力过大。
若工件内存在着非金属夹杂物,碳化物偏析或其他割离金属的粗大第二相,以及由于各种原因存在于工件中的微小裂缝,则这些地方,钢材强度减弱。
当淬火应力过大时,也将由此而引起淬火裂缝。
在实际的生产中,往往会根据淬火裂缝特征来判断其产生的原因,从而采取措施预防其发生。
1、纵向裂缝沿着工件轴线方向由表面裂向心部的深度较大的裂缝,它往往在钢件完全淬透情况下发生。
从纵向裂纹方向看,恰好应力是在切向拉应力方向,而又常见于完全淬透情况下。
因此,纵向裂纹是因淬火时组织应力过大,使最大切向拉应力大于该时材料断裂抗力而发生。
纵向裂缝也可能是由于钢材沿轧制方向有严重带状夹杂物所致。
该带状夹杂物所在处,犹如既存裂缝,在淬火切向拉应力作用下,促进裂缝发展而成为宏观的纵向裂缝。
这时如果把钢材沿纵向截取试样,分析其夹杂物,常可发现有带状夹杂物存在。
纵向裂缝也可能由于淬火前既存裂缝在淬火时切向拉应力作用下扩展而成,这时如果垂直轴线方向截取金相试样观察附近情况,可以发现裂缝表面有氧化皮,裂缝两侧有脱碳现象。
2、横向裂缝和弧形裂缝横向裂缝常发生于大型轴类零件上,如轧辊、汽轮机转子或其他轴类零件。
其特征是垂直于轴向方向,由内往外断裂,往往在未淬透情况下形成,属于热应力所引起。
大锻件往往存在着气孔、夹杂物、锻造裂缝和白点等冶金缺陷,这些缺陷作为断裂的起点,在轴向拉应力作用下断裂。
3、表面裂缝这是一种分布在工件表面的深度较小的裂纹,裂纹分布方向与工件形状无关,但与裂纹深度有关。
当工件表面由于某种原因呈现拉应力状态,且表面材料的塑性又很小,在拉应力作用下不能发生塑性变形时就出现这种裂纹。
例如表面脱碳工件,淬火时表层的马氏体因含碳量低,其比体积比与其相邻的内层马氏体的小,因而脱碳的表面层呈现拉应力。
当拉应力值达到或超过钢的破断抗力时,则在脱碳层形成表面裂纹。
42crmo淬火开裂危险尺寸

42crmo淬火开裂危险尺寸
摘要:
1.42CrMo 钢材概述
2.42CrMo 淬火开裂的原因
3.42CrMo 淬火开裂的预防措施
4.结论
正文:
一、42CrMo 钢材概述
42CrMo 是一种合金结构钢,具有较高的强度、韧性和耐磨性,广泛应用于各种机械零件的制造。
在42CrMo 的加工过程中,淬火是提高其硬度和耐磨性的重要环节。
然而,42CrMo 在淬火过程中可能会出现开裂现象,给生产带来安全隐患。
二、42CrMo 淬火开裂的原因
1.原始材料原因:原材料中可能存在裂纹、夹杂物等缺陷,在淬火过程中这些缺陷会扩展,导致开裂。
2.淬火温度和冷却速度原因:如果淬火温度过高或冷却速度过快,会导致钢材内部应力增大,超过钢材的抗拉强度,从而产生开裂。
3.淬火介质原因:淬火介质的性能和温度对钢材的淬火效果有重要影响。
如果淬火介质的性能不佳或温度不稳定,可能导致淬火效果不理想,进而引发开裂。
4.组织结构原因:在淬火过程中,钢材的组织结构会发生变化。
如果组织
结构过于粗大或不均匀,可能导致开裂。
三、42CrMo 淬火开裂的预防措施
1.选用高质量的原材料,避免使用有缺陷的钢材。
2.合理控制淬火温度和冷却速度,避免过高的温度和过快的冷却速度。
3.选择合适的淬火介质,并确保其性能和温度稳定。
4.通过调整热处理工艺,优化钢材的组织结构,降低开裂风险。
5.对淬火后的零件进行回火处理,以消除内部应力,提高韧性。
减少淬火变形和防止淬火开裂的措施
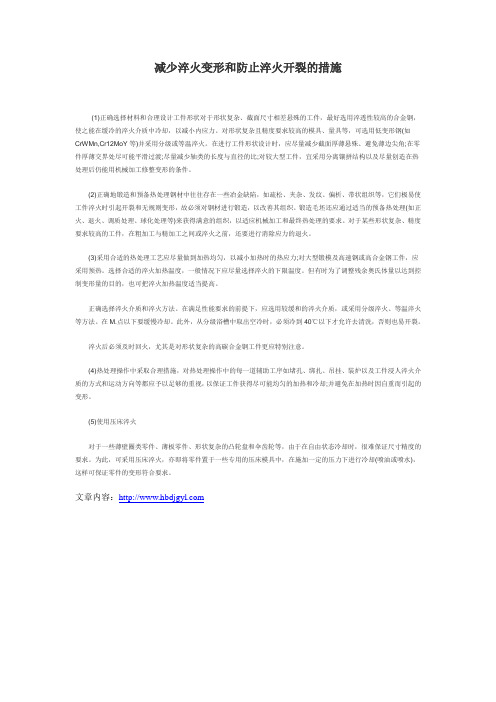
减少淬火变形和防止淬火开裂的措施(1)正确选择材料和合理设计工件形状对于形状复杂、截面尺寸相差悬殊的工件,最好选用淬透性较高的合金钢,使之能在缓冷的淬火介质中冷却,以减小内应力。
对形状复杂且精度要求较高的模具、量具等,可选用低变形钢(如CrWMn,Cr12MoY等)并采用分级或等温淬火。
在进行工件形状设计时,应尽量减少截面厚薄悬殊、避免薄边尖角;在零件厚薄交界处尽可能平滑过渡;尽量减少轴类的长度与直径的比;对较大型工件,宜采用分离镶拼结构以及尽量创造在热处理后仍能用机械加工修整变形的条件。
(2)正确地锻造和预备热处理钢材中往往存在一些冶金缺陷,如疏松、夹杂、发纹、偏析、带状组织等,它们极易使工件淬火时引起开裂和无规则变形,故必须对钢材进行锻造,以改善其组织。
锻造毛坯还应通过适当的预备热处理(如正火、退火、调质处理、球化处理等)来获得满意的组织,以适应机械加工和最终热处理的要求。
对于某些形状复杂、精度要求较高的工件,在粗加工与精加工之间或淬火之前,还要进行消除应力的退火。
(3)采用合适的热处理工艺应尽量做到加热均匀,以减小加热时的热应力;对大型锻模及高速钢或高合金钢工件,应采用预热。
选择合适的淬火加热温度,一般情况下应尽量选择淬火的下限温度。
但有时为了调整残余奥氏体量以达到控制变形量的目的,也可把淬火加热温度适当提高。
正确选择淬火介质和淬火方法。
在满足性能要求的前提下,应选用较缓和的淬火介质,或采用分级淬火、等温淬火等方法。
在M.点以下要缓慢冷却。
此外,从分级浴槽中取出空冷时,必须冷到40℃以下才允许去清洗,否则也易开裂。
淬火后必须及时回火,尤其是对形状复杂的高碳合金钢工件更应特别注意。
(4)热处理操作中采取合理措施,对热处理操作中的每一道辅助工序如堵孔、绑扎、吊挂、装炉以及工件浸人淬火介质的方式和运动方向等都应予以足够的重视,以保证工件获得尽可能均匀的加热和冷却;并避免在加热时因自重而引起的变形。
淬火时出现裂纹的原因及解决方法
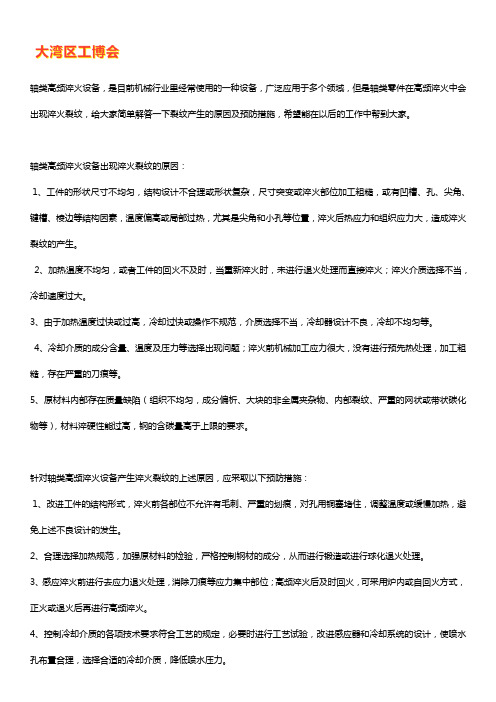
轴类高频淬火设备,是目前机械行业里经常使用的一种设备,广泛应用于多个领域,但是轴类零件在高频淬火中会出现淬火裂纹,给大家简单解答一下裂纹产生的原因及预防措施,希望能在以后的工作中帮到大家。
轴类高频淬火设备出现淬火裂纹的原因:1、工件的形状尺寸不均匀,结构设计不合理或形状复杂,尺寸突变或淬火部位加工粗糙,或有凹槽、孔、尖角、键槽、棱边等结构因素,温度偏高或局部过热,尤其是尖角和小孔等位置,淬火后热应力和组织应力大,造成淬火裂纹的产生。
2、加热温度不均匀,或者工件的回火不及时,当重新淬火时,未进行退火处理而直接淬火;淬火介质选择不当,冷却速度过大。
3、由于加热温度过快或过高,冷却过快或操作不规范,介质选择不当,冷却器设计不良,冷却不均匀等。
4、冷却介质的成分含量、温度及压力等选择出现问题;淬火前机械加工应力很大,没有进行预先热处理,加工粗糙,存在严重的刀痕等。
5、原材料内部存在质量缺陷(组织不均匀,成分偏析、大块的非金属夹杂物、内部裂纹、严重的网状或带状碳化物等),材料淬硬性能过高,钢的含碳量高于上限的要求。
针对轴类高频淬火设备产生淬火裂纹的上述原因,应采取以下预防措施:1、改进工件的结构形式,淬火前各部位不允许有毛刺、严重的划痕,对孔用铜塞堵住,调整温度或缓慢加热,避免上述不良设计的发生。
2、合理选择加热规范,加强原材料的检验,严格控制钢材的成分,从而进行锻造或进行球化退火处理。
3、感应淬火前进行去应力退火处理,消除刀痕等应力集中部位;高频淬火后及时回火,可采用炉内或自回火方式,正火或退火后再进行高频淬火。
4、控制冷却介质的各项技术要求符合工艺的规定,必要时进行工艺试验,改进感应器和冷却系统的设计,使喷水孔布置合理,选择合适的冷却介质,降低喷水压力。
淬火处理常见裂纹类型及预防措施

金属热处理知识专题
7、磨削裂纹 常发生在模具成品淬火、回火后磨削冷加工过 程中,多数形成的微细裂纹与磨削方向垂直,深约 0.05—1.0mm。 (1)原材料预处理不当,未能充分消除原材料块 状、网状、带状碳化物和发生严重脱碳; (2)最终淬火加热温度过高,发生过热,晶粒粗 大,生成较多残余奥氏体; (3)在磨削时发生应力诱发相变,使残余奥氏体 转变为马氏体,组织应力大,加上因回火不充分,留 有较多残余拉应力,与磨削组织应力叠加,或因磨 削速度、进刀量大及冷却不当,导致金属表层磨削 热急剧升温至淬火加热温度,随之磨削液冷却,造 成磨削表层二次淬火,多种应力综合,超过该材料 强度极限,便引起表层金属磨削裂纹。
金属热处理知识专题
预防措施 (1)应使模具钢化学渗层浓度与硬 度由表至内平缓降低,增强渗层与基体 结合力,渗后进行扩散处理能使化学渗 层与基体过渡均匀; (2)模具钢化学处理之前进行扩散 退火、球化退火、调质处理,充分细化 原始组织,能有效防止和避免剥离裂纹 产生,确保产品质量。
金属热处理知识专题
金属热处理知识专题
4、剥离裂纹 模具服役时在应力作用下,淬火硬化层一块块从钢基 体中剥离。因模具表层组织和心部组织比容不同,淬火 时表层形成轴向、切向淬火应力,径向产生拉应力,并向 内部突变,在应力急剧变化范围较窄处产生剥离裂纹,常 发生于经表层化学热处理模具冷却过程中,因表层化学 改性与钢基体相变不同时性引起内外层淬火马氏体膨胀 不同时进行,产生大的相变应力,导致化学处理渗层从基 体组织中剥离。如火焰表面淬硬层、高频表面淬硬层、 渗碳层、碳氮共渗层、渗氮层、渗硼层、渗金属层等。 化学渗层淬火后不宜快速回火,尤其是300~C以下低温回 火快速加热,会促使表层形成拉应力,而钢基体心部及过 渡层形成压缩应力,当拉应力大于压缩应力时,导致化学 渗层被拉裂剥离。
热处理淬火开裂及预防
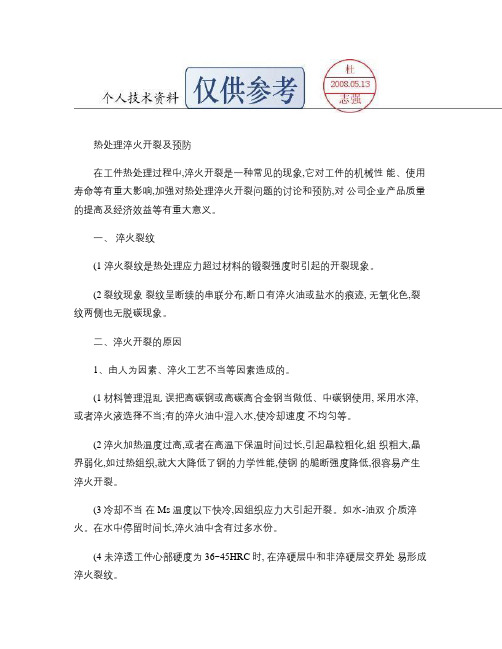
(4正确预先热处理,避免正火、退火组织缺陷(魏氏组织等。
(5正确选择加热参数。减少因加热温度过高、加热速度过快等原因引起的开裂。
(6正确的选择淬火介质和淬火工艺(方法。
(7合理的安排热处理工艺,尽量减少截面突变等容易引起冷却速度不均匀,应力增大的开裂现象。
(8对工件容易开裂的部位,如尖角、薄壁、孔等进行局部包扎。1、(9
3、
力较大,易在内孔壁上形成纵向分布的裂纹,从端面看呈放射状。
4、
时间差很大,形成很大的组织应力,以至产生裂纹。例如小件头部毛坯裂纹。5、应力集中引起裂纹钢件上有尖角、缺口等存在的情况下,易在淬火时造成Байду номын сангаас力集中而产生裂纹,尤其在应力集中和截面急剧变化的共同作用下淬裂危险更大。
6、网状裂纹这种裂纹具有任意方向性而与工件形状无关,网状裂纹的深度一般在0.01~0.15范围内,是一种表现裂纹,高碳工具钢和合金工具钢表面脱碳后淬火医形成网状裂纹。
(3冷却不当在Ms温度以下快冷,因组织应力大引起开裂。如水-油双介质淬火。在水中停留时间长,淬火油中含有过多水份。
(4未淬透工件心部硬度为36~45HRC时,在淬硬层中和非淬硬层交界处易形成淬火裂纹。
(5重复淬火前未经中间退火,过热倾向大,前项淬火的应力未能完全消
除,以及多次加热引起表面脱碳,都会促使淬火开裂。
(3具有最危险淬火尺寸的工件易形成淬火裂纹。工件的全部淬透时有一最危险的的淬火尺寸,其直径(或厚度是:水淬时约8~15㎜;油淬时约25~40㎜。尺寸小于最危险的尺寸时,心部与表面温差小,淬火应力小,不易开裂。工件尺寸大于最危险尺寸时,淬火应力虽然大,但拉应力峰值远离表面,淬火倾向反而减小。只有中间某一尺寸(最危险尺寸的工件,拉应力峰靠近表面,且数值也较大对淬裂最敏感。4、典型裂纹现象
热处理裂纹及其预防

热处理裂纹及其预防热处理裂纹的分类:⾮淬⽕裂纹——表⾯龟裂、表⾯边缘T型裂纹;淬⽕裂纹——纵裂(组织应⼒型)、弧裂(局部拉应⼒型)、⼤型⼯件淬⽕裂纹(纵断、横断)、边廓表⾯裂纹(局部拉应⼒型)、脱裂、第⼆类应⼒裂纹。
纵裂⑴纵裂的宏观形态沿细长零件表⾯启裂,在沿纵向扩展的同时,⼜以垂直表⾯的⽅向向截⾯内部扩展,形成外宽内尖的楔形裂⼝。
纵裂的扩展总是终⽌于截⾯的中⼼处附近,外观上看纵向单条裂纹和横截⾯上的楔形裂⼝,是纵裂的基本宏观形态。
⑵纵裂的形成条件淬透是纵裂形成的必要条件。
⼩⼯件淬透后的应⼒状态属于组织应⼒型残余应⼒,⼀般情况下组织应⼒的切向应⼒显著⼤于轴向应⼒。
因此形成组织应⼒型残余应⼒是纵裂的应⼒条件。
⑶纵裂预防措施①采⽤较缓慢的冷却介质,如油等。
也可⽤⽔、油双液淬⽕,但⽔、油双液淬⽕对于⼀些⼩件⽆实际使⽤价值。
②⼯件加热避免过热,出炉后可适当预冷,淬⽕后及时回⽕。
③加强技术管理技术培训,切实对有关⼯艺操作⼈员进⾏淬裂理论教育。
弧裂⑴弧裂形成的条件应同时具备整体快速冷却、不能淬透、具有弧裂的⼏何敏感部位的结构形式。
⑵⼏何敏感部位的结构形式有孔洞、凹⾯和碗⾯、截⾯尺⼨突变、轴肩。
⑶⼏何敏感部位的缓冷效应具有上述结构形式在淬⽕冷却过程中的主要作⽤是显著降低那⾥的实际冷却速度,产⽣缓冷效应。
⑷⼏何敏感部位处的组织⼏何敏感部位缓冷效应,要么使局部未淬硬产⽣淬⽕屈⽒体并处在马⽒体的包围之中(在⾦相的宏观或微观上可看出);要么淬硬层被局部明显减薄。
在热处理⽣产中产⽣的弧裂中,前⼀种占绝⼤多数。
⑸弧裂的形成扩展⽅式及典型宏观形态弧裂⾸先在⼏何敏感部位的表⾯上形成,并由此沿曲(弧)⾯先向截⾯内部定向扩展,严重时可穿越零件的其余截⾯,再向零件的外表⾯延伸,直到在那⾥呈弧形露出;严重时常使相应部位沿弧裂脱落(或经敲击即可脱落)。
开裂⾯通常为形状各异的曲(弧)⾯,最典型的是从⼏个不同的⽅向观察时都呈弧形,是判定弧裂的重要依据。
课堂淬火开裂及防止方法
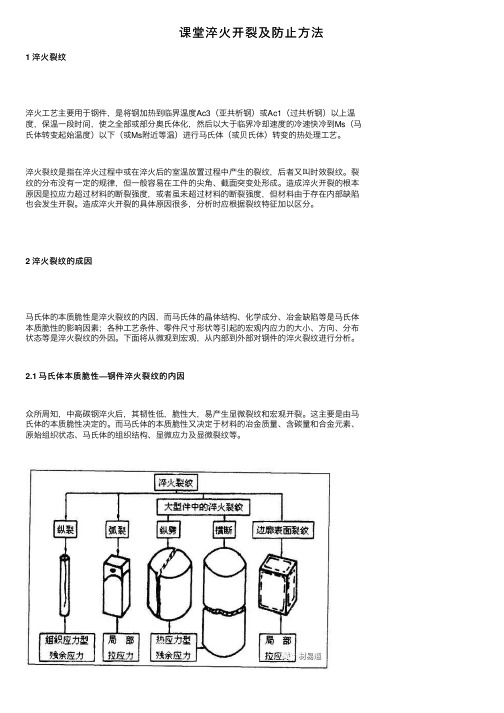
课堂淬⽕开裂及防⽌⽅法1 淬⽕裂纹淬⽕⼯艺主要⽤于钢件,是将钢加热到临界温度Ac3(亚共析钢)或Ac1(过共析钢)以上温度,保温⼀段时间,使之全部或部分奥⽒体化,然后以⼤于临界冷却速度的冷速快冷到Ms(马⽒体转变起始温度)以下(或Ms附近等温)进⾏马⽒体(或贝⽒体)转变的热处理⼯艺。
淬⽕裂纹是指在淬⽕过程中或在淬⽕后的室温放置过程中产⽣的裂纹,后者⼜叫时效裂纹。
裂纹的分布没有⼀定的规律,但⼀般容易在⼯件的尖⾓、截⾯突变处形成。
造成淬⽕开裂的根本原因是拉应⼒超过材料的断裂强度,或者虽未超过材料的断裂强度,但材料由于存在内部缺陷也会发⽣开裂。
造成淬⽕开裂的具体原因很多,分析时应根据裂纹特征加以区分。
2 淬⽕裂纹的成因马⽒体的本质脆性是淬⽕裂纹的内因,⽽马⽒体的晶体结构、化学成分、冶⾦缺陷等是马⽒体本质脆性的影响因素;各种⼯艺条件、零件尺⼨形状等引起的宏观内应⼒的⼤⼩、⽅向、分布状态等是淬⽕裂纹的外因。
下⾯将从微观到宏观,从内部到外部对钢件的淬⽕裂纹进⾏分析。
2.1 马⽒体本质脆性—钢件淬⽕裂纹的内因众所周知,中⾼碳钢淬⽕后,其韧性低,脆性⼤,易产⽣显微裂纹和宏观开裂。
这主要是由马⽒体的本质脆性决定的。
⽽马⽒体的本质脆性⼜决定于材料的冶⾦质量、含碳量和合⾦元素、原始组织状态、马⽒体的组织结构、显微应⼒及显微裂纹等。
图1 淬⽕裂纹的宏观形态图2.1.1 材料冶⾦质量缩孔和严重的轧制缺陷造成材料明显的不均匀性,这时材料是不宜进⾏热处理的。
⽽不少材料的冶⾦缺陷均可能单独与宏观或微观的内应⼒发⽣作⽤,促发淬⽕裂纹。
这些冶⾦质量问题包括:宏观偏析、固溶体偏析、固溶氢、锻轧缺陷、夹渣、铁素体珠光体带状组织及碳化物带状组织等。
图2 沿夹杂物扩展的淬⽕裂纹2.1.2 材料含碳量和合⾦元素含碳量增加将降低马⽒体的断裂强度。
根据脆性固体理论断裂强度:,其中E、d值与含碳量相关,含碳量提⾼,马⽒体中铁原⼦间结合⼒降低,弹形模量也降低,钢的断裂强度也随之降低。
如何解决淬火工件的开裂和形状畸变问题
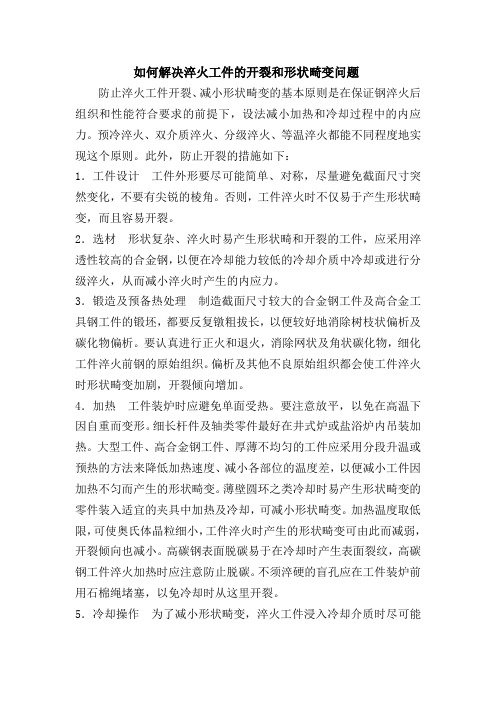
如何解决淬火工件的开裂和形状畸变问题防止淬火工件开裂、减小形状畸变的基本原则是在保证钢淬火后组织和性能符合要求的前提下,设法减小加热和冷却过程中的内应力。
预冷淬火、双介质淬火、分级淬火、等温淬火都能不同程度地实现这个原则。
此外,防止开裂的措施如下:1.工件设计工件外形要尽可能简单、对称,尽量避免截面尺寸突然变化,不要有尖锐的棱角。
否则,工件淬火时不仅易于产生形状畸变,而且容易开裂。
2.选材形状复杂、淬火时易产生形状畸和开裂的工件,应采用淬透性较高的合金钢,以便在冷却能力较低的冷却介质中冷却或进行分级淬火,从而减小淬火时产生的内应力。
3.锻造及预备热处理制造截面尺寸较大的合金钢工件及高合金工具钢工件的锻坯,都要反复镦粗拔长,以便较好地消除树枝状偏析及碳化物偏析。
要认真进行正火和退火,消除网状及角状碳化物,细化工件淬火前钢的原始组织。
偏析及其他不良原始组织都会使工件淬火时形状畸变加剧,开裂倾向增加。
4.加热工件装炉时应避免单面受热。
要注意放平,以免在高温下因自重而变形。
细长杆件及轴类零件最好在井式炉或盐浴炉内吊装加热。
大型工件、高合金钢工件、厚薄不均匀的工件应采用分段升温或预热的方法来降低加热速度、减小各部位的温度差,以便减小工件因加热不匀而产生的形状畸变。
薄壁圆环之类冷却时易产生形状畸变的零件装入适宜的夹具中加热及冷却,可减小形状畸变。
加热温度取低限,可使奥氏体晶粒细小,工件淬火时产生的形状畸变可由此而减弱,开裂倾向也减小。
高碳钢表面脱碳易于在冷却时产生表面裂纹,高碳钢工件淬火加热时应注意防止脱碳。
不须淬硬的盲孔应在工件装炉前用石棉绳堵塞,以免冷却时从这里开裂。
5.冷却操作为了减小形状畸变,淬火工件浸入冷却介质时尽可能使各部位均匀冷却,同时注意使介质对工件浸入的阻力尽可能小。
6.校直通常是在工件冷至室温后或回火进行。
7.裂纹的检查一般情况下表面裂纹可用肉眼看出。
为了更清晰地显现裂纹,可用煤油清洗工件,晾干后涂一层粉笔末,这时裂纹会显现为湿润的条纹。
热处理淬火裂纹产生的原因及防止措施分析

热处理淬火裂纹产生的原因及防止措施分析摘要:在热处理生产实践时,常常会遇到一些零件和工具,特别是形状复杂时,淬火过程因处理不当以及一些其他因素,造成工件内部存在有强大的淬火应力,以致引起淬火裂纹。
淬火裂纹直接导致零件的报废,产生的原因和条件及防止方法具有很摘要的现实意义。
关键词:淬火裂纹的实质产生原因和条件防止方法一、淬火裂纹的实质钢件在进行淬火是,在冷却的过程中同时产生了热应力和组织应力。
由于温度的降低使零件内部产生了热应力,由于奥氏体向马氏体的转变使内部产生了组织应力,组织应力是钢件表面淬火时拉应力,钢件表面在拉应力的作用下,有开裂的危险。
根据淬火裂纹断口形式和外观状态分析,淬火裂纹是在内应力作用下的脆性断裂。
二、淬火裂纹产生的原因和条件1、钢的化学成分对淬火裂纹敏感性的影响在一定的淬火介质中冷却时,钢的化学成分对热处理裂纹形成的影响,是由于它使钢件的内应力分布于应力集中的敏感性和钢的机械性能发生了改变的缘故。
合金元素对内应力的影响,则主要是由于合金元素对钢的组织结构影响的结果。
在钢中含有的所有元素中,碳对钢机械性能的影响最大,随着含碳量的增加,钢件淬火后组织应力也有所增大,由于组织应力作用的结果,使钢的表面具有危险的拉应力。
因此,淬裂倾向将随着含碳量的增多而增大。
钢中其他常存因素,如硫、磷等夹杂物较多,呈条状、网状分布时,往往在正常淬火条件下形成裂纹。
合金元素能够在不同程度上使奥氏体的等温曲线的位置右移,即增大其淬透性,这样可以用缓慢的冷却介质进行淬火。
从而残余应力较小,是钢的马氏体转变温度降低,则残余奥氏体数量增多,组织应力减小,有利于降低钢件的淬裂倾向。
2、原材料缺陷对淬火时形成裂纹的影响钢件内部的发纹、皮下气泡、较严重的碳化物偏析以及非金属夹杂等在淬火过程中,有可能在这些缺陷处产生裂纹。
各种锻件加工时,不论是温度过高或过低都容易在锻轧过程出现细小裂纹。
由于毛坯在锻轧后,表面上存在一些氧化皮,因此这些细小裂纹便不容易被发现。
淬火裂纹及预防措施
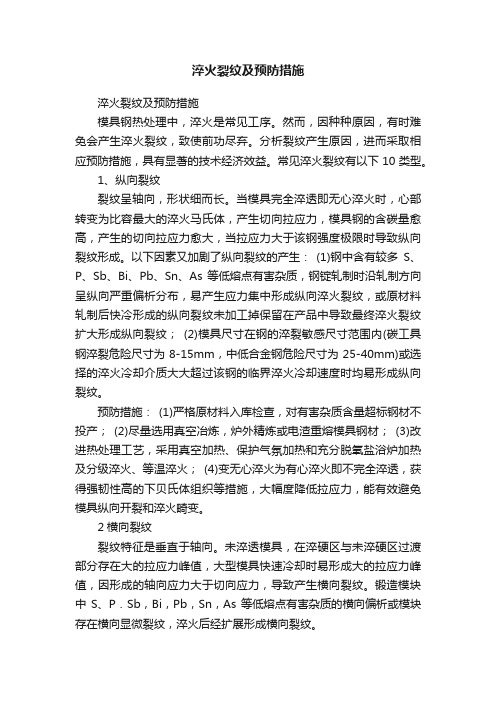
淬火裂纹及预防措施淬火裂纹及预防措施模具钢热处理中,淬火是常见工序。
然而,因种种原因,有时难免会产生淬火裂纹,致使前功尽弃。
分析裂纹产生原因,进而采取相应预防措施,具有显著的技术经济效益。
常见淬火裂纹有以下10类型。
1、纵向裂纹裂纹呈轴向,形状细而长。
当模具完全淬透即无心淬火时,心部转变为比容最大的淬火马氏体,产生切向拉应力,模具钢的含碳量愈高,产生的切向拉应力愈大,当拉应力大于该钢强度极限时导致纵向裂纹形成。
以下因素又加剧了纵向裂纹的产生:(1)钢中含有较多S、P、Sb、Bi、Pb、Sn、As等低熔点有害杂质,钢锭轧制时沿轧制方向呈纵向严重偏析分布,易产生应力集中形成纵向淬火裂纹,或原材料轧制后快冷形成的纵向裂纹未加工掉保留在产品中导致最终淬火裂纹扩大形成纵向裂纹;(2)模具尺寸在钢的淬裂敏感尺寸范围内(碳工具钢淬裂危险尺寸为8-15mm,中低合金钢危险尺寸为25-40mm)或选择的淬火冷却介质大大超过该钢的临界淬火冷却速度时均易形成纵向裂纹。
预防措施:(1)严格原材料入库检查,对有害杂质含量超标钢材不投产;(2)尽量选用真空冶炼,炉外精炼或电渣重熔模具钢材;(3)改进热处理工艺,采用真空加热、保护气氛加热和充分脱氧盐浴炉加热及分级淬火、等温淬火;(4)变无心淬火为有心淬火即不完全淬透,获得强韧性高的下贝氏体组织等措施,大幅度降低拉应力,能有效避免模具纵向开裂和淬火畸变。
2横向裂纹裂纹特征是垂直于轴向。
未淬透模具,在淬硬区与未淬硬区过渡部分存在大的拉应力峰值,大型模具快速冷却时易形成大的拉应力峰值,因形成的轴向应力大于切向应力,导致产生横向裂纹。
锻造模块中S、P.Sb,Bi,Pb,Sn,As等低熔点有害杂质的横向偏析或模块存在横向显微裂纹,淬火后经扩展形成横向裂纹。
预防措施:(1)模块应合理锻造,原材料长度与直径之比即锻造比最好选在2—3之间,锻造采用双十字形变向锻造,经五镦五拔多火锻造,使钢中碳化物和杂质呈细、小,匀分布于钢基体,锻造纤维组织围绕型腔无定向分布,大幅度提高模块横向力学性能,减少和消除应力源;(2)选择理想的冷却速度和冷却介质:在钢的Ms点以上快冷,大于该钢临界淬火冷却速度,钢中过冷奥氏体产生的应力为热应力,表层为压应力,内层为张应力,相互抵消,有效防止热应力裂纹形成,在钢的Ms—Mf之间缓冷,大幅度降低形成淬火马氏体时的组织应力。
高合金钢淬火裂纹的产生和解决方法

高合金钢淬火产生的裂纹的原因和解决方法高合金钢是指在钢铁中有一种合金元素在10%以上时的合金钢。
淬火是指将金属工件加热到某一适当温度并保持一段时间,随即浸入淬冷介质中快速冷却的金属热处理工艺。
高合金钢淬火时由于内应力超过材料的断裂强度,将导致工件产生淬火裂纹(尤其是在应力集中处)。
而同时又由于高合金钢一般加热温度较高,而Ms点又较低,用普通方法有可能产生较严重的的裂纹。
由于高合金钢的合金元素较大而随着合金元素的增加,若采用较大加热与冷却速度时,也会因加热与冷却的不均匀产生强大的内应力而淬裂。
同时若合金钢的零件的设计不合理造成应力集中侧更加大淬裂倾向,原始组织中的严重带状和网装碳化物,晶粒粗大等在淬火时也会加大淬裂的倾向。
同时如果合金里面含有氢也会对合金的淬裂纹有很大影响,一些有害杂质如磷,锑,铋,铅,锡等在淬火时容易产生应力集中从而形成纵向裂纹。
高合金钢的热处理是为了改善其力学性能,化学性能,物理性能,提高产品的使用寿命和提高效能。
但是高合金钢一旦产生或形成裂纹,侧产品不得不报废,造成很大的经济损失,因此解决淬火裂纹的产生有很重要的经济意义。
工作应该从产品的设计开始,在设计时应正确选择材料,合理进行结构设计,提出恰当的热处理技术要求。
零件设计完成后合理制定热处理工艺,并按照工艺流程正确热处理。
其几个重要解决淬火裂纹的环节如下:1 确定恰当的加热参数在热处理中,加热不当是引起淬火开裂的主要因素。
因此要正确选择加热介质,加热温度,加热速度和保温时间等加热参数。
2 选定合适的淬火方法合适的淬火方法可以很好的解决淬火裂纹的产生,其中可分为:(1)预冷淬火预冷淬火是淬火时零件先在空气,油,热浴中,预冷到略高A r3的温度后,再迅速置于淬火介质中淬火。
45钢轴类零件断裂分析及预防

eat TreatmentH热处理45安徽省宿州模具热处理研究中心 (234000) 赵昌胜安徽省煤田地质局水文勘探队机厂 (234000) 杨 峰 崔 晴45钢由于价格便宜,来源方便,加工性能好,淬火后具有较高的硬度,调质处理后具有良好的强韧性、高的强度和一定的耐磨性,被广泛地应用于中低档的轴类零件。
但是45钢轴在热处理过程中,由于材料本身的原因,热加工不当和热处理工艺安排不合理,往往容易产生热处理断裂或在工作中发生早期失效,造成产品报废,严重影响生产。
1. 柴油机曲轴热处理产生的裂纹及预防某柴油机厂生产一批柴油机曲轴,该工厂采用圆钢锻造,为了赶工期,采取的加工工序是:下料→锻造→粗加工→调质→精加工→检验入库。
该批曲轴在淬火后,一部分曲轴的曲拐处产生裂纹,造成了产品报废。
分析工序安排可看出,因为锻后没有进行退火或正火,钢材在锻造时产生的锻造应力没有很好地被消除,因此在热处理淬火时,淬火产生的应力和原来轴中存在的应力叠加,当叠加应力超过材料的强度极限时,45钢曲轴表面应力集中处即产生裂纹。
针对45钢锻造曲轴产生裂纹原因,对45钢锻造后的曲轴进行正火热处理,不仅消除了锻造产生的1. 喷砂清理采用手动压缩空气(0.5~0.6MPa)喷枪,经过压缩空气带动细石英砂向螺纹部表面喷射清理。
喷砂清理时注意,应及时转动齿轮,不得过度清理某处,以防其尺寸减小。
喷砂采用的压缩空气应经过滤,保证无油、无水。
此方法特点是清理效率较高,但现场粉尘较大,应安装除尘装置。
图5为齿轮喷砂清理示意。
2. 钢丝轮清理利用电动机带动钢丝轮传动机构,设计并制成合理的主动齿轮卡位机构,以利于对主动齿轮尾部螺纹等进行均匀、彻底、安全的清理。
此方法特点是清理干净,效率高。
图6为主动齿轮螺纹清理机示意。
图5 齿轮喷砂清理示意1.转台2.喷嘴3.枪体4.主动齿轮3.化学清理将涂覆涂料部位浸泡在温度为60~80℃的10%~15%NaOH溶液中2~3h,可使其残留的防渗涂层溶解。
45钢淬火开裂解决方案
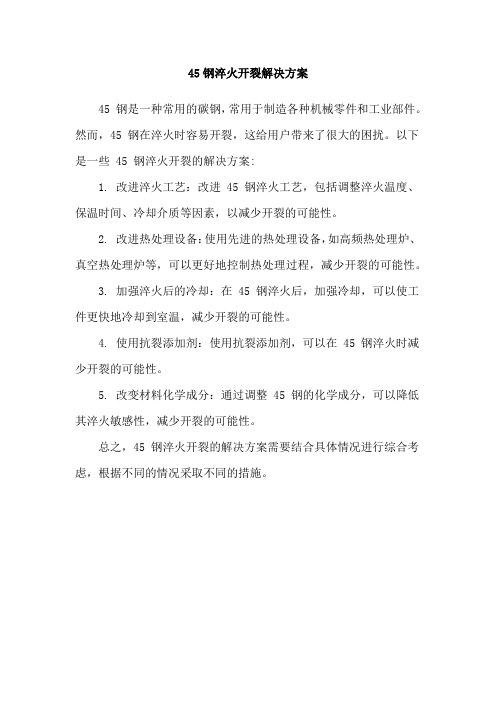
45钢淬火开裂解决方案
45 钢是一种常用的碳钢,常用于制造各种机械零件和工业部件。
然而,45 钢在淬火时容易开裂,这给用户带来了很大的困扰。
以下是一些 45 钢淬火开裂的解决方案:
1. 改进淬火工艺:改进 45 钢淬火工艺,包括调整淬火温度、保温时间、冷却介质等因素,以减少开裂的可能性。
2. 改进热处理设备:使用先进的热处理设备,如高频热处理炉、真空热处理炉等,可以更好地控制热处理过程,减少开裂的可能性。
3. 加强淬火后的冷却:在 45 钢淬火后,加强冷却,可以使工件更快地冷却到室温,减少开裂的可能性。
4. 使用抗裂添加剂:使用抗裂添加剂,可以在 45 钢淬火时减少开裂的可能性。
5. 改变材料化学成分:通过调整 45 钢的化学成分,可以降低其淬火敏感性,减少开裂的可能性。
总之,45 钢淬火开裂的解决方案需要结合具体情况进行综合考虑,根据不同的情况采取不同的措施。
金属零件裂纹类型及预防措施

金属零件常见裂纹类型和预防措施南京科润技术中心王学平裂纹是钢铁零件最为忌讳的破坏性缺陷。
在零件加工生产过程中,必然会经历锻造、铸造或轧制、热处理、机械加工、磨削等一系列的工艺过程,常因材料或操作不当等原因引起各类裂纹的产生,往往在零件加工制作完成后才得以发现,将直接造成零件报废,影响产品的正常安装使用,带来一定的经济损失。
因此,为了避免各类裂纹缺陷的发生,,我们针对原材料,热处理,机械加工等工序可能会出现的裂纹特征、预防措施进行了探讨,从而在生产过程中对裂纹进行预防与控制。
(一)原材料裂纹原材料裂纹是工件表面和内部因冶金因素或上道工序不当而存在的裂纹缺陷,常发生于原材料的供货状态。
原材料缺陷如缩孔,疏松,白点,夹杂物、偏析等在锻造时,都有可能形成裂纹,致使工件报废。
1、特征原材料裂纹一般深度较深,裂痕清晰,呈直线或弯曲线条。
1.1 宏观特征:非金属夹杂物引起的裂纹呈锯齿形,且裂纹两侧和尾部有夹杂物分布,裂纹有粗变细,尾端呈圆凸状。
折叠裂纹,锻造热裂纹、铸造热裂纹主要为沿晶扩展,其形状粗细不均,曲折而不规则,常伴有树晶枝;裂纹表面呈氧化色或深褐色,无金属光泽,铸造钢件裂纹表面近似黑色,而铝合金则呈暗灰色。
铸造,锻造冷裂纹往往为穿晶扩展,外形呈宽度均匀细长的直线或折线状,两端有尖角,端口表面清洁,有金属光泽或 轻度氧化色,裂纹走向平滑。
1.2 折叠、锻造、铸造裂纹微观特征:裂纹两侧的显微组织与基体明显不同,有脱碳和氧化现象存在,如图1所示45钢转轴锻件热裂纹形貌为典型的原材料裂纹特征形态。
2、预防措施:⑴材料的化学成分应严格复合标准。
对有害元素S、P、O、N等容易形成夹杂物的元素及 Sn、Sb等微量元素应加以控制。
⑵ 严格控制冶炼浇铸过程。
这是提高材料纯净度,消除冶金缺陷,防止裂纹产生的重要环节。
⑶ 选择正确的铸造、锻造工艺。
铸造零件时,合理设置浇冒口的位置和尺寸,使铸件壁厚不均匀的部位均匀过度,采用合理的圆角尺寸,控制好金属模具的工作温度,开箱时间,冷却速度,以及合适的抽芯开模,确保铸件各部分的冷却速度尽量均匀一致,实现内外同时凝固,有效地减少裂纹倾向。
- 1、下载文档前请自行甄别文档内容的完整性,平台不提供额外的编辑、内容补充、找答案等附加服务。
- 2、"仅部分预览"的文档,不可在线预览部分如存在完整性等问题,可反馈申请退款(可完整预览的文档不适用该条件!)。
- 3、如文档侵犯您的权益,请联系客服反馈,我们会尽快为您处理(人工客服工作时间:9:00-18:30)。
热处理淬火开裂及预防
在工件热处理过程中,淬火开裂是一种常见的现象,它对工件的机械性能、使用寿命等有重大影响,加强对热处理淬火开裂问题的讨论和预防,对公司企业产品质量的提高及经济效益等有重大意义。
一、淬火裂纹
(1)淬火裂纹是热处理应力超过材料的锻裂强度时引起的开裂现象。
(2)裂纹现象 裂纹呈断续的串联分布,断口有淬火油或盐水的痕迹,无氧化色,裂纹两侧也无脱碳现象。
二、淬火开裂的原因
1、由人为因素、淬火工艺不当等因素造成的。
(1)材料管理混乱 误把高碳钢或高碳高合金钢当做低、中碳钢使用,采用水淬,或者淬火液选择不当;有的淬火油中混入水,使冷却速度
不均匀等。
(2)淬火加热温度过高,或者在高温下保温时间过长,引起晶粒粗化,组织粗大,晶界弱化,如过热组织,就大大降低了钢的力学性能,使钢
的脆断强度降低,很容易产生淬火开裂。
(3)冷却不当 在Ms温度以下快冷,因组织应力大引起开裂。
如水-油双介质淬火。
在水中停留时间长,淬火油中含有过多水份。
(4)未淬透工件心部硬度为36~45HRC时,在淬硬层中和非淬硬层交界处易形成淬火裂纹。
(5)重复淬火前未经中间退火,过热倾向大,前项淬火的应力未能完全消
除,以及多次加热引起表面脱碳,都会促使淬火开裂。
(6)大截面高合金钢工件,淬火加热时未经预热或加热速度过快,加热时热应力和组织应力增大,引起开裂。
(7)高速钢、高铬钢分级淬火,工件工件未冷至室温,急于清洗(Ms以下快冷)引起开裂。
(8)深冷处理因急冷急热形成的热应力和组织应力都比较大,且低温时材料的脆断强度低,易产生淬火开裂。
(9)淬火后未及时回火工件内部的显微裂纹在淬火应力作用下扩展形成宏观裂纹。
(10)淬火后产生应力不平衡,未使工件开裂,但在后来机加工中或者在搬运过程中,受外力过大,造成开裂。
2、内部组织不良原因造成的
(1)严重表面脱碳易形成网状裂纹。
严重脱碳的高碳工具钢工件,脱碳层
马氏体比未脱碳层马氏体体积小,收到拉应力作用易形成网状裂纹。
(2)原始组织不良,如高碳钢球化质量欠佳,其组织是细片状珠光体或点状珠光体,过热倾向大;晶粒粗化,马氏体碳含量高,淬火开裂倾向
大。
(3)原材料显微裂纹,非金属夹杂物,严重碳化物偏析淬开裂倾向大,如非金属夹杂物或严重碳化物沿轧制方向形成带状分布,由于力学性能
的各向异性,其横向性能比纵向性能低30%~50%,在表面最大拉应力作
用下。
常沿非金属夹杂物或碳化物分布方向呈纵向裂纹。
(4)淬透性低的钢,用钳子夹持淬火时,被夹持部位冷却速度慢在非马
氏体组织,钳口位于淬硬层与非淬硬层交界处,其拉应力大,容易开裂。
3、设计工艺不合理等原因造成开裂。
(1)内径较小的深孔工件(如机筒),由于内表面冷却速度较外表面小的多,残余热应力小,所受的残余拉应力较外表面大,外壁较内壁收缩的
快,因此如果加上材料偏析,内壁就容易开裂。
(2)工件的尖角、孔、截面突变及粗加工刀痕等因冷却速度不均,应力集中引起开裂。
(3)具有最危险淬火尺寸的工件易形成淬火裂纹。
工件的全部淬透时有一最危险的的淬火尺寸,其直径(或厚度)是:水淬时约8~15㎜;油
淬时约25~40㎜。
尺寸小于最危险的尺寸时,心部与表面温差小,淬
火应力小,不易开裂。
工件尺寸大于最危险尺寸时,淬火应力虽然大,
但拉应力峰值远离表面,淬火倾向反而减小。
只有中间某一尺寸(最危
险尺寸)的工件,拉应力峰靠近表面,且数值也较大对淬裂最敏感。
4、典型裂纹现象
(1)锻造裂纹在淬火时扩大,在普通炉内淬火加热时,开裂的破断面有
黑色的氧化皮,裂纹两侧有脱碳层。
(2)过烧裂纹。
裂纹多呈网状,晶界有氧化或熔化现象。
三、淬火开裂的防止措施:
(1)原材料应避免显微裂纹,及严重的非金属夹杂物和材料组织偏析。
(2)合理选择钢材,形状复杂容易开裂的工件,应选择淬透性高的合金钢制造,以便采用冷却速度缓慢的的淬火介质,减少淬火应力。
(3)改进工件结构,截面力求均匀,不同截面处有圆角过渡,尽量减
少不通孔、尖角、避免应力集中引起开裂。
(4)正确预先热处理,避免正火、退火组织缺陷(魏氏组织等)。
(5)正确选择加热参数。
减少因加热温度过高、加热速度过快等原因
引起的开裂。
(6)正确的选择淬火介质和淬火工艺(方法)。
(7)合理的安排热处理工艺,尽量减少截面突变等容易引起冷却速度不 均匀,应力增大的开裂现象。
(8)对工件容易开裂的部位,如尖角、薄壁、孔等进行局部包扎。
1、(9)易开裂的工件淬火后应及时回火或带温回火纵向裂纹亦称轴向裂纹,
是典型的组织应力(切向应力)引发的裂纹,由表面向内开裂,裂纹深而长。
常发生与脆透的工件。
钢中有严重的带状碳化物偏析或沿纵向排列的非金属夹杂物等缺陷会增大形成纵向裂纹的敏感性。
2、横向裂纹或弧状裂纹,裂纹经常发生于工件尖角处。
未淬透的高碳钢件或渗碳
件的过渡区易产生拉应力峰值,此类裂纹常萌生于一定深度的表层或工件内部。
淬火件上有软点时,也易形成细小的弧性形裂纹。
3、内孔纵向裂纹钢的淬透足够大时内孔表面的内应力以组织应力为主,切向应
力较大,易在内孔壁上形成纵向分布的裂纹,从端面看呈放射状。
4、截面薄厚悬殊引起的淬火裂纹冷却时在薄厚相差悬殊的部位马氏体相变的
时间差很大,形成很大的组织应力,以至产生裂纹。
例如小件头部毛坯裂纹。
5、应力集中引起裂纹钢件上有尖角、缺口等存在的情况下,易在淬火时造成
应力集中而产生裂纹,尤其在应力集中和截面急剧变化的共同作用下淬裂危险更大。
6、网状裂纹这种裂纹具有任意方向性而与工件形状无关,网状裂纹的深度一
般在0.01~0.15范围内,是一种表现裂纹,高碳工具钢和合金工具钢表面脱碳后淬火医形成网状裂纹。
7、原材料缺陷引起的淬火裂纹原材料中的夹杂、网状碳化物、塑性成型过程
中的表面折叠、加热时过热组织都可能成为裂纹源,在淬火时会暴露出来或进一步扩展。
解决此类裂纹,应从控制淬火前的原材料质量着手。