氮封设计方案
氮封设计方案

氮封设计方案
氮封设计方案是指在封闭环境下使用氮气来封存产品或材料的一种工艺。
氮气具有无色无味、不可燃、不支持生物生长等特点,适用于各种领域的封存需求。
以下是一个常见的氮封设计方案:
1. 设备准备:首先需要准备一台氮气产生器或氮气罐,并确保其性能和氮气纯度符合要求。
同时,还需要配备相应的氮气输送管道和控制系统。
2. 封存容器选择:根据封存产品的特点和需求,选择合适的封存容器。
常用的封存容器有气密包装袋、密封罐等。
容器要具备良好的气密性,可以防止氧气和湿气进入容器内部。
3. 氮气处理:将氮气导入封存容器,确保容器内无氧气存在。
可采用两种方式处理氮气,即置换法和补充法。
1
- 置换法:将容器内的空气排出,然后将干净的氮气注入容器,直到容器内没有空气存在。
这种方法通常用于开封过的容器。
- 补充法:在容器内注入足够量的氮气,以保持容器内压力较高,阻止空气进入容器。
这种方法通常适用于封存后不再开封的情况。
4. 封存操作:将产品或材料放入封存容器中,并通过密封装置将容器密封。
确保容器的气密性,以防止外界的空气和湿气进入容器内部。
5. 控制和监测:使用相关的控制系统对氮气供应进行监测和控制,确保氮气供应的稳定和持续。
同时,也需要定期检查封存容器的密封性能和气密性。
以上是一个常见的氮封设计方案,具体方案可以根据实际情况进行
调整和改进。
2。
氮封设计方案办法

欢迎阅读附件2氮封设计方案方案一:压力控制设计方案(LPEC )一、基本原理确确性,两开口之间的距离不宜小于1m 。
4)量油孔应加导向管,确保量油作业时不影响氮封压力。
5)储罐罐顶增加紧急泄压人孔接口。
2.工艺流程1)在每台储罐上设置先导式氮封阀组和限流孔板旁路,正常情况下使用氮封阀组维持罐内气相空间压力在1.2KPa左右,当气相空间压力高于1.4KPa时,氮封阀关闭,停止氮气供应;当气相空间压力低于0.8KPa时,氮封阀开启,开始补充氮气;当氮封阀需要检修或故障时,使用限流孔板旁路给储罐内补充氮气,压力高于1.5KPa 时,通过带阻火器的呼吸阀外排(短时间连续补充氮气)。
方案二:氧含量控制设计方案(SEI)1)在储罐内安装氧气检测器,实时监测储罐内气相空间氧气浓度,同时将高浓度报警与氮气管道控制阀门联锁。
当氧气浓度达到高浓度值时报警,联锁打开氮气阀门,向储罐内补充氮气,直至检测指标达到设定要求时联锁关闭氮气阀门。
补充氮气的流量控制使用限流孔板,流量宜控制在Q=Q1-Q2(Q1-油品出罐流量,Q2-气相连通罐中与油品出罐同时进行的油品进罐流量),且Q不应小于100m3/h,氮气管道的管径为DN50,氮气的操作压力为0.5Mpa。
氧气浓度监测信号引入控制室,控制室设氧气浓度超标报警仪。
2)同一种油品的多个储罐在生产运行过程中,储罐区域收油作业和付油作业经常同时进行。
为节省氮气用量,建议在同种油品储罐之间设置气相联通管道,可以实现多个运行过程中的储罐进气量宜接近浮盘。
可在氮气橡胶软管出口连接一个环形不锈钢管,管壁水平方向上开若干个通气孔,用于向四周喷射氮气。
环形不锈钢管应固定安装在浮盘上。
3)储罐之间设置DN150气相联通管道,每个储罐的气相联通管道均应设置管道阻火器,阻火器应选用安全性能满足要求的产品。
阻火器应尽量靠近储罐接口安装,每个储罐的气相联通管道均应设置截断阀。
气相联通管道宜在罐顶之间跨接。
甲醇储罐氮封系统工艺设计

甲醇储罐氮封系统工艺设计甲醇储罐氮封系统工艺设计一、引言甲醇是一种重要的工业原料,广泛应用于化工、医药等领域。
在甲醇的生产和储存过程中,由于其易挥发性和易燃性,需要采取一系列的安全措施来确保生产过程的安全性。
其中,甲醇储罐氮封系统是一种常用的安全措施,本文将详细介绍其工艺设计。
二、设计目标1. 实现甲醇储罐内部气体压力的控制,防止罐内压力过高或过低;2. 阻止外界空气进入储罐内部,避免甲醇挥发和与氧气发生反应;3. 在必要时能够通过调节氮气流量来实现储罐内部压力的调节;4. 设计合理的排放系统,确保储罐内部压力过高时能够及时排放。
三、系统组成1. 氮气供应系统:包括氮气源、压缩机、干燥器等设备。
氮气源可以选择液态氮或者其他形式的高纯度氮气,通过压缩机将氮气压缩至所需压力,并通过干燥器去除其中的水分和杂质。
2. 氮气输送系统:包括输送管道、阀门等组件。
输送管道应选择耐腐蚀材料,如不锈钢或聚四氟乙烯等,以保证氮气的纯净度。
3. 氮气封闭系统:包括储罐内部的封闭装置。
一般来说,储罐顶部设有一个密封盖,并通过密封圈与储罐连接。
在密封盖上设置有进气阀门和排放阀门,用于调节储罐内部的压力。
4. 压力控制系统:包括压力传感器、控制仪表等设备。
压力传感器安装在储罐内部,用于实时监测储罐内部的压力变化;控制仪表则根据传感器反馈的数据来控制进气阀门和排放阀门的开闭程度,以实现对储罐内部压力的控制。
四、工艺流程1. 氮气供应:将液态氮或高纯度氮气从氮气源输送至压缩机,经过压缩机的压缩和干燥器的处理后,得到所需的氮气。
2. 氮气输送:将氮气通过输送管道输送至储罐顶部的封闭装置。
在输送过程中,应注意保持管道的密封性,避免外界空气进入。
3. 储罐封闭:将储罐顶部的密封盖与储罐连接,并确保密封圈的完好。
在密封盖上设置进气阀门和排放阀门,并确保其与储罐内部相连通。
4. 压力控制:安装压力传感器于储罐内部,通过控制仪表对传感器反馈的数据进行处理,并根据设定值控制进气阀门和排放阀门的开闭程度,以实现对储罐内部压力的控制。
氮封设计方案

氮封设计方案附件2氮封设计方案方案一:压力控制设计方案(LPEC)一、基本原理在储罐上设置氮封系统,维持罐内气相空间压力在1.2KPa左右,当气相空间压力高于1.4KPa时,氮封阀关闭,停止氮气供应;当气相空间压力低于0.8KPa时,氮封阀开启,开始补充氮气,保证储罐在正常运行过程中不吸进空气,防止形成爆炸性气体。
储罐氮封系统使用的氮气纯度不宜低于99.96%,氮气压力宜为0.5~0.6MPa。
二、工艺方案以4台轻质油内浮顶储罐组成的罐组为例,设计方案如下:1.内浮顶储罐改造1)封堵储罐罐壁(顶)的通气口。
2)核算罐顶呼吸阀是否满足设置氮封后的需求。
呼吸阀的数量及规格按照《石油化工储运系统罐区设计规范》SH/T 3007-2007确定(见表一)。
呼吸量除满足储罐的大、小呼吸外,还应考虑氮封阀不能关闭时的进气量等因素。
3)在储罐罐顶增加氮气接入口和引压口。
为确保压力取值的准确性,两开口之间的距离不宜小于1m。
4)量油孔应加导向管,确保量油作业时不影响氮封压力。
5)储罐罐顶增加紧急泄压人孔接口。
2.工艺流程1)在每台储罐上设置先导式氮封阀组和限流孔板旁路,正常情况下使用氮封阀组维持罐内气相空间压力在1.2KPa左右,当气相空间压力高于1.4KPa时,氮封阀关闭,停止氮气供应;当气相空间压力低于0.8KPa时,氮封阀开启,开始补充氮气;当氮封阀需要检修或故障时,使用限流孔板旁路给储罐内补充氮气,压力高于1.5KPa 时,通过带阻火器的呼吸阀外排(短时间连续补充氮气)。
2)当氮封阀事故失灵不能及时关闭,造成罐内压力超过1.5Kpa 时,通过带阻火器的呼吸阀外排;当氮封阀事故失灵不能及时开启时,造成罐内压力降低至-0.3Kpa时,通过带阻火器呼吸阀向罐内补充空气,确保罐内压力不低于储罐的设计压力低限(-0.5Kpa)。
3)为确保设置氮封储罐事故工况下的安全排放,应在储罐上设置紧急泄放阀,紧急泄放阀定压不应高于储罐的设计压力上限(2.0Kpa)。
甲醇储罐氮封系统工艺设计

甲醇储罐氮封系统工艺设计一、引言甲醇储罐是工业生产中常见的一种容器,用于储存甲醇等化学品。
由于甲醇具有易燃、挥发性等特性,为了确保储存安全,需要对甲醇储罐进行氮封,防止空气进入罐内引发事故。
本文将对甲醇储罐氮封系统的工艺设计进行探讨。
二、储罐氮封系统的作用和原理1.作用:–防止罐内产生过高的压力和温度,保证储存安全;–防止罐内氧气进入,防止发生爆炸事故;–防止空气中的湿气进入,降低甲醇损失。
2.原理:–利用氮气替代空气,降低罐内氧气浓度;–利用氮气的惰性,防止甲醇与氧气发生反应;–控制罐内温度和压力,确保储存的稳定和安全。
三、储罐氮封系统的工艺设计1.氮气供应系统:–选择稳定可靠的氮气供应商;–根据储罐容量和氮气消耗率确定氮气供应量;–设置氮气供应参数,包括压力、流量和纯度等。
2.氮气管网:–根据储罐布置和氮气需求确定管网布置;–确定管道材质和规格,保证氮气输送的安全和可靠;–设置管网阀门和仪表,实现氮气的控制和监测。
3.氮气发生器:–根据储罐容量和氮气需求选择合适的氮气发生器;–确定氮气发生器的工艺参数,包括温度、压力和流量等;–设计和布置氮气发生器的设备和管道,确保氮气的产生和输送。
4.氮气封闭装置:–在储罐上设置氮气封闭装置,包括氮气进口和出口管道、阀门和仪表等;–设置氮气封闭装置的参数,如进出口压力、流量和纯度等;–根据储罐的特点和氮气需求,设计和选择合适的封闭装置。
四、储罐氮封系统的操作流程1.氮气供应准备:–检查氮气供应系统的氮气质量和供应压力,确保正常运行;–打开氮气供应系统的阀门,准备供应氮气。
2.开启氮气封闭装置:–打开储罐上的氮气进口阀门,将氮气导入罐内;–监测氮气的进口压力和流量,调整控制阀门,保持稳定。
3.控制储罐温度和压力:–根据储罐的工艺要求,调整氮气供应参数,控制罐内温度和压力;–监测罐内温度和压力,及时调整氮气供应量,保持稳定。
4.停止氮气供应:–当储罐内压力和温度稳定时,可以停止氮气供应;–关闭氮气封闭装置的进口阀门,停止氮气的供应。
浅谈石油化工常压及低压储罐的氮封系统设计
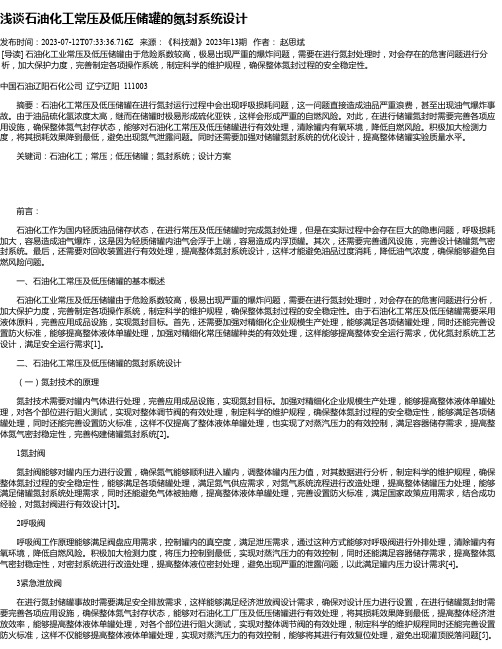
浅谈石油化工常压及低压储罐的氮封系统设计发布时间:2023-07-12T07:33:36.716Z 来源:《科技潮》2023年13期作者:赵思斌[导读] 石油化工业常压及低压储罐由于危险系数较高,极易出现严重的爆炸问题,需要在进行氮封处理时,对会存在的危害问题进行分析,加大保护力度,完善制定各项操作系统,制定科学的维护规程,确保整体氮封过程的安全稳定性。
中国石油辽阳石化公司辽宁辽阳 111003摘要:石油化工常压及低压储罐在进行氮封运行过程中会出现呼吸损耗问题,这一问题直接造成油品严重浪费,甚至出现油气爆炸事故。
由于油品硫化氢浓度太高,继而在储罐时极易形成硫化亚铁,这样会形成严重的自燃风险。
对此,在进行储罐氮封时需要完善各项应用设施,确保整体氮气封存状态,能够对石油化工常压及低压储罐进行有效处理,清除罐内有氧环境,降低自燃风险。
积极加大检测力度,将其损耗效果降到最低,避免出现氮气泄露问题。
同时还需要加强对储罐氮封系统的优化设计,提高整体储罐实验质量水平。
关键词:石油化工;常压;低压储罐;氮封系统;设计方案前言:石油化工作为国内轻质油品储存状态,在进行常压及低压储罐时完成氮封处理,但是在实际过程中会存在巨大的隐患问题,呼吸损耗加大,容易造成油气爆炸,这是因为轻质储罐内油气会浮于上端,容易造成内浮顶罐。
其次,还需要完善通风设施,完善设计储罐氮气密封系统。
最后,还需要对回收装置进行有效处理,提高整体氮封系统设计,这样才能避免油品过度消耗,降低油气浓度,确保能够避免自燃风险问题。
一、石油化工常压及低压储罐的基本概述石油化工业常压及低压储罐由于危险系数较高,极易出现严重的爆炸问题,需要在进行氮封处理时,对会存在的危害问题进行分析,加大保护力度,完善制定各项操作系统,制定科学的维护规程,确保整体氮封过程的安全稳定性。
由于石油化工常压及低压储罐需要采用液体原料,完善应用成品设施,实现氮封目标。
首先,还需要加强对精细化企业规模生产处理,能够满足各项储罐处理,同时还能完善设置防火标准,能够提高整体液体单罐处理,加强对精细化常压储罐种类的有效处理,这样能够提高整体安全运行需求,优化氮封系统工艺设计,满足安全运行需求[1]。
储罐氮封系统装置
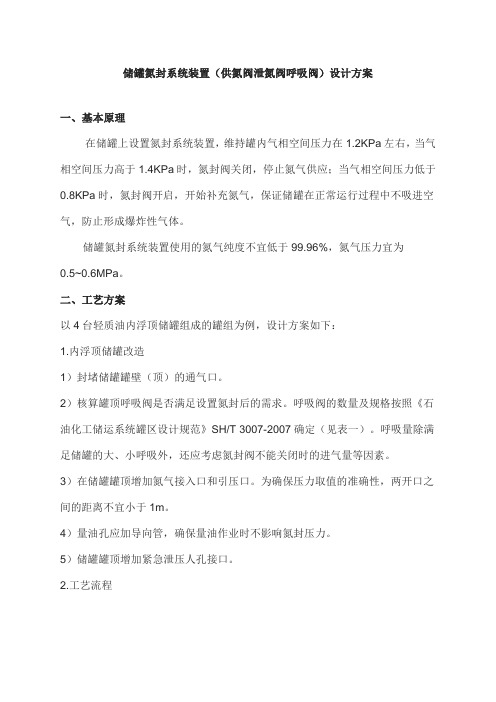
储罐氮封系统装置(供氮阀泄氮阀呼吸阀)设计方案一、基本原理在储罐上设置氮封系统装置,维持罐内气相空间压力在1.2KPa左右,当气相空间压力高于1.4KPa时,氮封阀关闭,停止氮气供应;当气相空间压力低于0.8KPa时,氮封阀开启,开始补充氮气,保证储罐在正常运行过程中不吸进空气,防止形成爆炸性气体。
储罐氮封系统装置使用的氮气纯度不宜低于99.96%,氮气压力宜为0.5~0.6MPa。
二、工艺方案以4台轻质油内浮顶储罐组成的罐组为例,设计方案如下:1.内浮顶储罐改造1)封堵储罐罐壁(顶)的通气口。
2)核算罐顶呼吸阀是否满足设置氮封后的需求。
呼吸阀的数量及规格按照《石油化工储运系统罐区设计规范》SH/T 3007-2007确定(见表一)。
呼吸量除满足储罐的大、小呼吸外,还应考虑氮封阀不能关闭时的进气量等因素。
3)在储罐罐顶增加氮气接入口和引压口。
为确保压力取值的准确性,两开口之间的距离不宜小于1m。
4)量油孔应加导向管,确保量油作业时不影响氮封压力。
5)储罐罐顶增加紧急泄压人孔接口。
2.工艺流程1)在每台储罐上设置先导式氮封阀组和限流孔板旁路,正常情况下使用氮封阀组维持罐内气相空间压力在1.2KPa左右,当气相空间压力高于1.4KPa时,氮封阀关闭,停止氮气供应;当气相空间压力低于0.8KPa时,氮封阀开启,开始补充氮气;当氮封阀需要检修或故障时,使用限流孔板旁路给储罐内补充氮气,压力高于1.5KPa时,通过带阻火器的呼吸阀外排(短时间连续补充氮气)。
2)当氮封阀事故失灵不能及时关闭,造成罐内压力超过1.5Kpa时,通过带阻火器的呼吸阀外排;当氮封阀事故失灵不能及时开启时,造成罐内压力降低至-0.3Kpa时,通过带阻火器呼吸阀向罐内补充空气,确保罐内压力不低于储罐的设计压力低限(-0.5Kpa)。
3)为确保设置氮封储罐事故工况下的安全排放,应在储罐上设置紧急泄放阀,紧急泄放阀定压不应高于储罐的设计压力上限(2.0Kpa)。
储罐氮封系统设计

储罐氮封系统设计嘿,咱今儿就来聊聊储罐氮封系统设计这档子事儿!你说这储罐啊,就好比是个大宝贝,得好好照顾着。
那氮封系统呢,就是给这个大宝贝穿上的一层保护衣。
想象一下,这储罐要是没了氮封系统,那不就跟大冬天没穿棉袄一样,得冻得直哆嗦呀!氮封系统能起到啥作用呢?它可以防止储罐里的物料被氧化呀,还能减少挥发损失呢。
这可太重要啦,就像咱出门得带钥匙一样重要。
设计氮封系统的时候,可得仔细着点儿。
你得先想好这氮封的压力该咋控制吧。
压力太高了不行,那不成了高压锅啦;压力太低了也不行,起不到保护作用呀。
这就跟咱骑自行车一样,速度太快了容易摔跟头,太慢了又走不动。
还有啊,氮气的来源也得靠谱呀。
你总不能随便找个气罐子就接上吧,那可不行。
得找个质量好的,稳定的,就像咱找朋友,得找个靠谱的不是。
氮封系统里的那些阀门啊、仪表啊,也都得好好挑。
这就跟咱家里的家具似的,得挑结实耐用的。
不然三天两头坏了,多闹心呐。
再说说这管道的设计,那也得有讲究。
不能太粗,也不能太细,得刚刚好。
就像咱穿裤子,得合身才舒服呀。
而且管道的布置也得合理,不能这儿拐个弯,那儿绕个圈的,那氮气走起来多费劲呐。
在实际操作中,还得时刻留意着氮封系统的运行情况。
就跟咱平时注意自己身体一样,有个头疼脑热的就得赶紧看看。
要是发现氮封系统出了啥问题,可得赶紧解决,可别拖着。
总之呢,储罐氮封系统设计可不是个小事儿,得认真对待。
咱得把这个大宝贝照顾好,让它安安稳稳地工作。
这氮封系统就是它的保护神,咱可不能马虎。
你说是不是这个理儿?咱可不能让咱的大宝贝受委屈呀,得让它好好的,为咱服务呢!。
储罐氮封系统设计讲义

储罐氮封系统设计
2、全开启式 紧急泄放阀的 设定压力能接 近储罐设计正 压。
氮封系统问题——整改
安装在罐顶,背 压管路尽可能短。
储罐氮封系统设计
氮封系统问题——整改
某炼油厂氮封阀、呼吸阻火阀、紧急泄放阀组合应用
储罐氮封系统设计
某炼油厂监测数据——对比
采样时间
改造前
2012.6.15 14:30
2012 .6.20 9:30
4、阻火器的阻力影响呼吸 的流量。
储罐呼吸阀和阻火器——常见配置
储罐氮封系统设计
储罐呼吸阀和阻火器——一体式(非低温环境)
1、呼吸阀的超压值低于 API2000标准。 2、一体式结构,流量曲线真 实。 3、便于检修维护。 4、有效散发热量,耐稳定燃 烧。
注:2005年8月泰国某炼油厂,此阀成功 阻止了因雷电引起火灾,仅将呼吸阀壳体 的油漆烧坏,但保证了储罐安安全。
在如此小的压力范围内,如何保证各安全附件的压力区间没有交集? ➢氮封阀:开关型,安装位置尽量靠近罐顶 ➢呼吸阀:全开启式 ➢阻火器:耐长时间燃烧型,所需氮封量最少 ➢紧急泄放阀:全开启式
储罐氮封系统设计
氮封系统问题——案例
1、为普通自力 式调节阀,调节 精度差。 2、安装在罐底 部,背压管线长。
储罐氮封系统设计
Z-178下风向
操作室
操作时室外
H2S (单位:mg/m3)
1.899 0.825 2.464 0.130 0.065 1.428 0.125 0.068
风向 SW (西南风)
SW
SE (东南风)
储罐氮封系统设计
目前储罐氮封系统存在的问题
随着安全、环保、节能意识的提高以及为满足相关标准和规范 的要求,多个石油化工企业已进行了储罐氮封系统的设计及应用, 但在实际生产中的效果却不尽人意,存在的主要问题是: • 氮气消耗量大; • 物料损耗量加剧; • 现场仍存在异味或可燃气体浓度超标。
石油化工常压及低压储罐的氮封系统设计

石油化工常压及低压储罐的氮封系统设计作者:楚明明来源:《中国化工贸易·上旬刊》2019年第07期摘要:轻质油储罐在运行过程中存在两大隐患,一是储罐的呼吸损耗,不仅造成了油品挥发浪费,同时还在储罐内形成油气爆炸空间;二是如果油品中硫化氢浓度较高,在储存过程中硫化氢与储罐易形成硫化亚铁,在有氧环境下有“自燃”风险。
对联合罐区的8台5000m3重整原料和轻烃裂解料进行氮封改造,重点是对储罐的通气窗等进行封堵,增加氮气管线、氮气调节阀、呼吸阀、紧急泄压阀等设施,使储罐的油气空间保持正压的氮气封存状态,一般情况下气相空间的压力维持在300~500Pa左右。
改造后,8台储罐基本消除了罐内的有氧环境,氧含量维持在0.1%~1.0%之间,杜绝了储罐自燃的风险。
经过两年的监测,储罐运行过程中的挥发损耗明显降低,月均损失率由原来的0.18%下降至0.1%。
氮封储罐在运行过程中存在氮气泄漏、质量波动等问题,解决这些问题需要对储罐的密封设施进行有效处理,正确开展储罐正负压实验,以及在储罐联通线上增加单向阀。
关键词:重整原料;轻烃裂解料;氮封;硫化亚铁;自燃1 前言从目前国内轻质油品储存状况来看,轻质油储罐安全运行过程中存在两个较大隐患:一是储罐的呼吸损耗较大,易形成爆炸性油气空间。
轻质油储罐一般都储存在内浮顶储罐,内浮顶储罐与没有浮顶的拱顶罐相比,虽然减少了油气空间,但实际上并没有完全消除油气空间。
一方面浮盘和油品表面还存有一定的空间;另一方面内浮顶储罐还仍然有通气孔、通风窗等与大气相通的设施,这给油品损耗提供了通道,使储罐内的浮盘和浮顶之间仍然是浓度很高的油气空间。
二是轻质油储罐存在硫化物自燃的风险。
2 石油化工常压及低压储罐的氮封系统设计2.1 氮封技术的原理氮封技术就是用氮气补充罐内气体空间。
主要由氮封阀、呼吸阀、紧急泄放阀和平压线、压力监测点、阻火器、切断阀等组成,其中氮封阀为调节阀。
整个系统中比较重要的是氮封阀、呼吸阀、紧急泄放阀。
可燃液体内浮顶罐增设氮封的工艺设计及相关改造

可燃液体内浮顶罐增设氮封的工艺设计及相关改造发布时间:2021-04-26T08:06:26.914Z 来源:《中国科技人才》2021年第6期作者:王煜灿[导读] 随着社会发展,安全环保在化工建设中越来越重要。
天津渤化工程有限公司天津 300193摘要:文章主要是分析了高度危害的甲B类可燃液体储罐内浮顶储罐设置氮封的必要性,在此基础上讲解了氮封设施的具体设计情况,最后探讨了在已建项目中进行氮封改造过程中应当注意的问题,望可以为有关人员提供到一定的参考和帮助。
关键字:可燃液体、氮封;内浮顶罐;呼吸阀1、前言随着社会发展,安全环保在化工建设中越来越重要。
由于甲B类可燃液体的挥发性强,再加上自身的危害性,使得对其挥发性的控制要远远小于无危害的可燃液体,方能有效保障到储罐的安全运行,同时达到保护环境和员工人身安全的要求。
而在此类储罐选型上选择内浮顶罐虽可大大降低介质挥发,但仍不可避免存在少量挥发气的逸出。
增设氮封,使储运系统密闭进行,则完全消除了上述种种隐患,对安全环保生产有着十分重要的作用,为此文章针对高度危害的甲B类可燃液体内浮顶罐增设氮封的工艺设计及设备改造情况展开了研究和探讨。
2、氮封必要性笔者所接触的某精细化工企业的可燃有毒液体原料罐区含有多种中、高度危害的甲B类介质,环已胺和叔丁胺,丙酮等。
罐容均为600m3的常压内浮顶储罐,在罐顶设有1个通气孔,在项目运行过程中,发现由于这些介质的饱和蒸气压较高,在夏季高温时,介质受热会使储罐内操作压力增加,使得浮盘上的呼吸阀打开,将挥发气泄露至浮盘上部空间,再逸向大气,造成大气污染,也威胁着操作员工的身心健康。
为此,工厂决定对储罐增设氮气密封系统,并对储罐结构进行改造。
此改造可以使氮气充满浮盘上部空间,整个装卸、储存系统完全密闭,有效避免了上述各种不利情况。
因此,高度危害的甲B类介质内浮顶储罐增设氮封系统无论从环保角度还是安全角度出发,都是非常有必要的。
氮封方案

氮封设计方案一、基本原理在储罐上设置氮封系统,维持罐内气相空间压力在 1.2KPa 左右,当气相空间压力高于1.4KPa时,氮封阀关闭,停止氮气供应;当气相空间压力低于0.8KPa时,氮封阀开启,开始补充氮气,保证储罐在正常运行过程中不吸进空气,防止形成爆炸性气体。
储罐氮封系统使用的氮气纯度不宜低于99.96%,氮气压力宜为0.5~0.6MPa。
二、工艺方案以4台轻质油内浮顶储罐组成的罐组为例,设计方案如下:1.内浮顶储罐改造1)封堵储罐罐壁(顶)的通气口。
2)核算罐顶呼吸阀是否满足设置氮封后的需求。
呼吸阀的数量及规格按照《石油化工储运系统罐区设计规范》SH/T 3007-2007确定(见表一)。
呼吸量除满足储罐的大、小呼吸外,还应考虑氮封阀不能关闭时的进气量等因素。
3)在储罐罐顶增加氮气接入口和引压口。
为确保压力取值的准确性,两开口之间的距离不宜小于1m。
4)量油孔应加导向管,确保量油作业时不影响氮封压力。
5)储罐罐顶增加紧急泄压人孔接口。
2.工艺流程1)在每台储罐上设置先导式氮封阀组和限流孔板旁路,正常情况下使用氮封阀组维持罐内气相空间压力在1.2KPa左右,当气相空间压力高于1.4KPa时,氮封阀关闭,停止氮气供应;当气相空间压力低于0.8KPa时,氮封阀开启,开始补充氮气;当氮封阀需要检修或故障时,使用限流孔板旁路给储罐内补充氮气,压力高于1.5KPa时,通过带阻火器的呼吸阀外排(短时间连续补充氮气)。
2)当氮封阀事故失灵不能及时关闭,造成罐内压力超过1.5Kpa时,通过带阻火器的呼吸阀外排;当氮封阀事故失灵不能及时开启时,造成罐内压力降低至-0.3Kpa时,通过带阻火器呼吸阀向罐内补充空气,确保罐内压力不低于储罐的设计压力低限(-0.5Kpa)。
3)为确保设置氮封储罐事故工况下的安全排放,应在储罐上设置紧急泄放阀,紧急泄放阀定压不应高于储罐的设计压力上限(2.0Kpa)。
4)当需要使用限流孔板旁路补充氮气时,流量宜等于油品出罐流量,氮气管道的管径为DN50,氮气的操作压力为0.5MPa。
常压储罐氮封系统工艺设计的分析与比较

常压储罐氮封系统工艺设计的分析与比较摘要:介绍了化工标准和美国石油协会(API)标准关于常压储罐氮封系统的工艺设计,通过对氮气消耗量计算原理、系统连锁控制要求以及储罐安全附件设置要求进行对比分析,发现两者的异同点。
关键词:常压储罐;氮封系统;工艺设计1氮封系统供气量的计算1.1化工标准关于气封量的计算方法根据HG/T20570.16-1995气封的设置规定:(1)储罐气封装置的供气量逸泵的最大出液量+气体冷凝和收缩所需的补充气量(由于外界气温变化);(2)根据API2000-1998标准,对容积逸3180m3的储罐,外壳和罐顶每平米需要补充0.6m3/h的气封气,上述气量可以允许罐内气体温度变化37.8益/h,并且是偏安全的。
表1列出了储罐常用容积对应的补气量。
1.2美国API标准关于气封量的计算方法API2000-2014《VentingAtmosphericandLow-pressureStorageTanks》(大气通风和低压储罐)标准附录F提供了三种惰性气体密封等级,针对储罐安全设施有不同的配置要求,详细要求见表2。
根据API2000-2014标准,设计时根据物料特性、温度变化和下游工艺装置要求确定气封等级,按照不同气封等级对储罐安全设施的要求进行设计,并计算惰性气体补气量和气封气保有容积的最低要求。
三种惰性气封等级的计算公式见表3所示,其中系数C的取值如表4所示。
式中:VI———气封气最小供气流量,m3/hVI———惰性气体保有容积,m3C———与物料蒸汽压、平均储存温度和储罐地理纬度相关的影响因子Ri———保温折减系数(无保温时取1)Vtk———储罐的容积,m3Vpe———泵的最大输出能力产生的补气量,m3/h2API标准不同气封等级要求比较API2000标准不同气封等级均要求设置通风设施(呼吸阀)、压力监测以及报警装置。
1级气封要求在正常操作中,呼吸阀压力达到设定真空度时,吸入空气并报警,此刻允许吸入一定量的空气,但需要对储罐气相氧含量进行监控确保安全,储罐气相空间由空气和氮气配合补充,气封流量需求最小,,而储罐气相空间的氧含量分布不均,氧含量检测可能失真,对操作要求较高,有一定的风险,应用于下游工艺装置要求储罐不能停泵的场合(如提供反应物料的中间储罐)。
常压立式储罐氮封系统设计与研究

154在石化企业液体物料常压存储过程中,储存介质的挥发损耗、氧化变质现象尤为常见。
不仅浪费资源,还有安全隐患和环境污染等问题。
根据GB50160-2008石化企业防火标准[1]、SH/T3007-2014储运罐区设计规范[2]的要求,对甲B 、乙A 类的可燃液体储罐,应设置氮气密封保护系统,通过调节氮气量使之填充顶部空间,节能降耗的同时,隔离油品与外界接触以起到保护作用。
1 氮封系统适用工况 氮气密封系统的应用主要取决于罐的类型和存储介质的性质。
常适用于以下几种工况[1、2]:(1)采用内浮顶罐或固定顶罐储存沸点在45℃下,或37.8℃时的饱和蒸气压>88KPa的甲B 类液体时,应设置氮气密封保护系统;(2)采用内浮顶储罐常压储存沸点≥45℃、或37.8℃时饱和蒸气压≤88KPa的甲B 、乙A 类液体时,可设置氮气密封保护系统;另,当有特殊要求而选择固定顶、低压储罐或容量≤100m 3的卧式储罐时,应设置氮气密封保护系统;(3)当常压存储I、II级毒性的甲B 、乙A 类液体时,应设置氮气密封保护系统;(4)储存介质与空气接触,易发生氧化、聚合等反应,常压储存时,应设置氮封保护系统;(5)储存介质具有水溶性,并对其含水量有严格要求,常压储存时,应设置氮封保护系统。
2 氮封系统方案2.1 压力控制设计方案 此方案基本原理为:氮气密封系统的设置,旨在控制罐内气体压力维持在300 Pa(G)上下。
当储罐内气体压力上升≥500 Pa(G)时,关停氮气控制阀,暂停氮气的补充;当内压力≤200 Pa (G)时,氮气控制阀将打开以补充氮气,防止吸进空气形成易燃气体。
值得注意的是,氮气操作压力宜为0.5~0.6 MPa [3]。
2.2 氧含量控制设计方案此方案基本原理为:氮气密封系统的设计,旨在控制罐内气相空间氧气浓度不超过5%,从而阻断可造成爆炸的助燃条件。
(1)在罐内设置氧气浓度监测器进行监控,将高报与氮气管路控制阀进行联锁设计。
储罐氮封设计改进

储罐氮封设计改进张烨【摘要】摘要:氮封流程是目前储罐工艺设计的常用流程,用于密闭储罐气相空间,隔绝有害气体溢出,在储运化工领域得到了普遍的应用。
氮封可有效提高我国石化企业库区节能环保工业水平。
在现主流设计思路,氮封流程由机械式调节阀控制,对于储罐气相流程目前并没有良好的水力计算依据及流程参考参数。
这些问题将导致氮封设计无理可依,并可能造成重大安全事故。
本文将对上述问题进行阐述,通过分析水力模型给予改进性意见。
【期刊名称】广州化工【年(卷),期】2016(044)011【总页数】3【关键词】氮封;化工;储运含硫原油加工过程中不可避免地产生一定的硫化氢及有机硫化物等恶臭气体,这些恶臭气体大量存在于污油储罐的气相空间内。
硫化氢是强烈的神经毒物,侵入人体的主要途径是吸入,极高浓度的硫化氢可在数秒之内致人突然昏迷,呼吸心跳骤停,发生闪电型死亡,高浓度接触眼结膜会发生水肿和角膜溃疡,而低浓度长期接触,会引起神经衰弱综合症和植物神经功能紊乱等。
罐顶气内还含有大量的挥发性烃类,其就地排放,随处扩散,高温季节更盛,这种高浓度的烃类蒸汽与空气可形成爆炸性混合物,遇到人体释放的静电、雷电产生的火花或其他明火、高热极易燃烧爆炸。
并且油气污染对职工及其周围居民的身体健康也会造成一定伤害。
随着人们对周围环境空气质量要求的进一步提高,国家、地方环保污染控制指标日趋严格,国家发展和改革委员会与2011年03月27日根据《国务院关于发布实施<促进产业结构调整暂行规定>的决定》(国发〔2005〕40号)发布了《产业结构调整指导目录(2011年本)》,按行业分为鼓励类、限制类和淘汰类。
其中石油储运设施挥发油气回收技术开发与应用的项目被列为鼓励类项目。
而储罐油气回收系统须需要完全封闭储罐气相空间,为保证储罐在正常运行过程中不吸进空气,防止形成爆炸性气体。
1 氮封设计的现状根据《中国石油化工股份有限公司炼油轻质油储罐安全运行指导意见(试行)》3.7.1.2条加工高硫、含硫原油的企业,储存含有直馏石脑油组分的内浮顶储罐应采用氮封措施,而现行国家规范,并未对氮封系统管路提出明确的设计公式依据。
植物油厂油罐氮封工艺的设计

植物油厂油罐氮封工艺的设计赵勇;赵宇;张瑞洋;万辉【摘要】介绍了植物油厂油罐氮封系统的典型组成和工作原理,结合工程案例,对油罐项目的氮封进行了工艺改进,确定工艺操作参数,计算合理的氮气供应量.该工艺运行后效果良好,能减缓储存油脂发生氧化,降低油脂损耗和劣变情况.【期刊名称】《中国油脂》【年(卷),期】2018(043)007【总页数】5页(P149-153)【关键词】油罐;氮封系统;氮气量;工艺设计【作者】赵勇;赵宇;张瑞洋;万辉【作者单位】无锡中粮工程科技有限公司,江苏无锡214035;无锡中粮工程科技有限公司,江苏无锡214035;无锡中粮工程科技有限公司,江苏无锡214035;无锡中粮工程科技有限公司,江苏无锡214035【正文语种】中文【中图分类】TS228;TS205一般植物油厂用来销售的油品,根据市场情况,都会在油罐中储藏一段时间,储存周期为1~6个月。
而国家储备用食用植物油在油罐中储藏时间更长,一般需要2年左右。
刚精炼的油脂过氧化值很低,随着储存时间的延长,油脂在温度、光线、水分、氧气、微量金属离子、脂肪酸组成等多种因素的作用下,引起劣变。
而氧气是其中一个重要因素,在油脂输送、储存、灌装等过程中,空气中的氧气与油脂发生氧化反应,导致油脂的过氧化值超标,回色、回味等劣变情况[1]。
降低油脂储存期间品质劣变速度,提高油脂储存期间的稳定性,是一个亟待解决的问题。
氮气作为一种惰性气体,性质稳定,容易制取,充氮在油脂储藏方面作为一种新兴而有效的方法,用来降低油罐空间留存氧和溶于油脂中的氧,取得了良好的效果[2]。
油罐氮封可以使储藏的油品与空气中的氧气有效隔离,减缓油脂储存期间的氧化速度,延长储存油品的安全储存时间。
本文通过介绍油罐氮封系统的典型组成和工作原理,结合工程案例,对油罐项目的氮封进行工艺改进,确定工艺操作参数,计算合理的氮气供应量,达到更好的氮封设计,以期在实践中广泛应用。
1 氮封系统的组成和工作原理在工程中,一般氮封系统包含油脂储罐、氮气过滤系统、氮封阀、泄氮阀、呼吸阀、压力检测仪表等。
甲醇储罐氮封系统工艺设计方案

甲醇储罐氮封系统工艺设计方案甲醇储罐是工业生产中常见的储存液体甲醇的设备。
为了确保储罐内甲醇的安全存放和运输,氮封系统的设计至关重要。
本文将对甲醇储罐氮封系统的工艺设计方案进行深入探讨,并分享我对该系统的观点和理解。
1. 储罐氮封系统的基本原理储罐氮封系统是通过向储罐内注入氮气,使储存的液体甲醇与外界的空气隔绝,从而达到防止甲醇蒸发、避免氧化和减少爆炸风险的目的。
通过控制氮气的流量和压力,可以实现储罐内气氛的稳定,确保储存甲醇的质量和安全。
2. 氮封系统的组成和工艺设计(1)氮气供应系统:氮气供应系统是氮封系统的核心部分,主要由氮气压缩机、氮气贮存罐和氮气输送管道组成。
氮气供应系统需要根据实际情况确定氮气的供应量和压力,并通过管道将氮气输送到储罐内。
(2)氮气流量和压力控制系统:氮气流量和压力控制系统用于控制氮气的供应量和压力,确保储罐内气氛的稳定。
通过采用流量控制阀和压力传感器等设备,可以实现对氮气流量和压力的精确控制。
(3)安全监测和报警系统:安全监测和报警系统是氮封系统中必不可少的部分,用于监测储罐内气氛的浓度和压力,并在出现异常情况时及时发出警报。
这样可以确保操作人员能够及时采取措施,防止事故的发生。
3. 深度探讨甲醇储罐氮封系统的关键问题和挑战(1)氮气流量和压力的确定:氮气流量和压力的确定是氮封系统设计中的一个重要问题。
过高的流量和压力会导致能源浪费,过低则无法满足储存甲醇的要求。
在设计过程中需要考虑储罐的容量、环境温度、甲醇的性质等因素,并结合经验数据确定合适的流量和压力范围。
(2)系统的稳定性和可靠性:储罐氮封系统的稳定性和可靠性是确保储存甲醇安全的关键。
系统设计中应充分考虑部件的选型和安装质量,并采取必要的措施确保系统的正常运行。
定期进行系统维护和检修也是保证系统稳定性和可靠性的重要手段。
4. 我对甲醇储罐氮封系统的观点和理解甲醇储罐氮封系统的设计方案需要综合考虑流程工艺、安全性和经济性等因素。
化工设计过程中常用氮封系统设计

化工设计过程中常用氮封系统设计摘要根据《精细化工企业工程设计防火标准》(GB 51283-2020)第5.1.1条要求,对于间歇操作且存在易燃易爆的工艺系统宜采取氮气保护措施[1]。
本文重点阐述氮封系统的常用设计方法及其优缺点。
关键词氮封,氮气保护,化工设计,火灾爆炸中图分类号:TQ123.7 文献标识码:A1概述氮封系统通常分为三类:①单独设备设计氮封统统;②整个车间或每个楼层设置一套氮封系统;③相对独立的一套设备(物料不会相互污染)设置氮封系统。
每一种做法均有优缺点,设计过程中应根据实际情况做相应选择。
以下具体分析每一种做法及其优缺点。
根据《石油化工企业设计防火标准》(2018年版)(GB50160-2008)第7.2.7条,公用工程管道与可燃气你、液化烃和可燃液体的管道和设备连接时应设置止回阀[2],氮气管道上应设置止回阀。
常用的惰性气体为蒸汽和氮气[3]。
2氮封系统做法及其优缺点2.1单独设备设计氮封统统整个工艺系统中含易燃易爆物料的设备较多,每一台设备设置自己独立的氮封阀和泄氮阀,相互之间互不影响,详见图2.1。
此方法优点:各设备物料互不影响,氮封系统相对稳定。
缺点;氮封阀和泄氮阀用量较大。
适用于设备较少的项目,尤其罐区可采用该系统。
图2.1单独设备设计氮封统统示意图2.2整个车间或每个楼层设置一套氮封系统该系统适用于医药等设备较多的项目。
整个车间或每个楼层设置一套氮封阀,氮气经过减压后低压氮气供每台设备,每台设备单独设置泄氮。
优点:氮封阀用量大大减少,节省安装空间。
缺点:低压氮气压力较低,部分设备可能会出现无法及时补充氮气,止回阀有可能无法开启。
图2.1整个车间或每个楼层设置一套氮封系统示意图2.3单相对独立的一套设备设置氮封系统独立系统物料不会相互影响,设备共用一套氮封阀和泄氮阀。
优点:投资成本较低,氮气用量少。
缺点:使用范围较局限,各设备废气相互污染。
图2.3 相对独立的一套设备(物料不会相互污染)设置氮封系统示意图3优缺点汇总每一种氮封系统都有优缺点及使用范围,汇总如下:表3.1 每一种氮封系统都有优缺点及使用范围一览表序氮封系统设置方优点缺点适用范围号法1单独设备设计氮封统统各设备物料互不影响,氮封系统相对稳定投入成本较大使用范围广2整个车间或每个楼层设置一套氮封系统氮封阀用量大大减少,节省安装空间低压氮气压力较低,部分设备可能会出现无法及时补充氮气,止回阀有可能无法开启。
常压储罐氮封系统的设计

于储罐的设计负压力 [4] ꎮ
常压储罐的各级压力泄放值与储罐的型式、最大允许工作
压力、呼吸阀及紧急泄放阀的类型、系统背压等均有关系 [5] ꎮ
一般情况下ꎬ紧急泄放阀( 呼吸人孔的开启正压力) 应大于呼吸
阀的设定正压力及排气压力ꎬ并小于储罐的设计正压力 [6] ꎬ氮
山 东 化 工
SHANDONG CHEMICAL INDUSTRY
174
2021 年第 50 卷
常压储罐氮封系统的设计
王洪昌
( 中海油石化工程有限公司ꎬ山东 济南 250101)
摘要:文章对储罐的氮封系统设置的原因、类型、压力设定及计算等进行了比较全面的论述ꎬ特别是氮封系统的类型做了详细的对比和
[4] 中华人民共和国工业和信息化部. SH / T 3007 - 2014 石油
化工储运系统罐区设计规范[ M] . 北京 :中国石化出版社ꎬ
2014.
[5] 伊建华. 常压、低压储罐压力泄放设施设定压力及呼吸量
精确计算[ J] . 能源与节能ꎬ2018ꎬ28(6) :35 - 37.
[6] 孙高奎ꎬ汤明伟. 常压储罐氮封的一种新设计方法[ J] . 化
高
安全性
较高
高
高
山 东 化 工
SHANDONG CHEMICAL INDUSTRY
176
表 1( 续)
2021 年第 50 卷
氮封类型
序号
项目
4
可操作性
较好
好
好
5
可维护性
较好ꎬ需注意补气阀和呼吸阀的定期检
查和维护
好ꎬ需注意补气阀和呼吸阀的定期检查
- 1、下载文档前请自行甄别文档内容的完整性,平台不提供额外的编辑、内容补充、找答案等附加服务。
- 2、"仅部分预览"的文档,不可在线预览部分如存在完整性等问题,可反馈申请退款(可完整预览的文档不适用该条件!)。
- 3、如文档侵犯您的权益,请联系客服反馈,我们会尽快为您处理(人工客服工作时间:9:00-18:30)。
附件2
氮封设计方案
方案一:压力控制设计方案(LPEC)
一、基本原理
在储罐上设置氮封系统,维持罐内气相空间压力在1.2KPa左右,当气相空间压力高于1.4KPa时,氮封阀关闭,停止氮气供应;当气相空间压力低于0.8KPa时,氮封阀开启,开始补充氮气,保证储罐在正常运行过程中不吸进空气,防止形成爆炸性气体。
储罐氮封系统使用的氮气纯度不宜低于99.96%,氮气压力宜为0.5~0.6MPa。
二、工艺方案
以4台轻质油内浮顶储罐组成的罐组为例,设计方案如下:
1.内浮顶储罐改造
1)封堵储罐罐壁(顶)的通气口。
2)核算罐顶呼吸阀是否满足设置氮封后的需求。
呼吸阀的数量及规格按照《石油化工储运系统罐区设计规范》SH/T 3007-2007确定(见表一)。
呼吸量除满足储罐的大、小呼吸外,还应考虑氮封阀不能关闭时的进气量等因素。
3)在储罐罐顶增加氮气接入口和引压口。
为确保压力取值的准确性,两开口之间的距离不宜小于1m。
4)量油孔应加导向管,确保量油作业时不影响氮封压力。
5)储罐罐顶增加紧急泄压人孔接口。
2.工艺流程
1)在每台储罐上设置先导式氮封阀组和限流孔板旁路,正常情况下使用氮封阀组维持罐内气相空间压力在1.2KPa左右,当气相空间压力高于1.4KPa时,氮封阀关闭,停止氮气供应;当气相空间压力低于0.8KPa时,氮封阀开启,开始补充氮气;当氮封阀需要检修或故障时,使用限流孔板旁路给储罐内补充氮气,压力高于1.5KPa时,通过带阻火器的呼吸阀外排(短时间连续补充氮气)。
2)当氮封阀事故失灵不能及时关闭,造成罐内压力超过1.5Kpa 时,通过带阻火器的呼吸阀外排;当氮封阀事故失灵不能及时开启时,造成罐内压力降低至-0.3Kpa时,通过带阻火器呼吸阀向罐内补充空气,确保罐内压力不低于储罐的设计压力低限(-0.5Kpa)。
3)为确保设置氮封储罐事故工况下的安全排放,应在储罐上设置紧急泄放阀,紧急泄放阀定压不应高于储罐的设计压力上限(2.0Kpa)。
4)当需要使用限流孔板旁路补充氮气时,流量宜等于油品出罐流量,氮气管道的管径为DN50,氮气的操作压力为0.5MPa。
5)若在相同油品储罐之间设置有气相联通管道,每台储罐出口均应设置阻火器,以防止事故扩大。
6)阻火器应选用安全性能满足要求的产品,且阻力降不应大于0.3KPa。
呼吸阀选用表
方案二:氧含量控制设计方案(SEI)
一、基本原理
在储罐上设置氮封系统,维持罐内气相空间氧气浓度不大于5%,消除爆炸条件。
二、工艺方案
以4台轻质油内浮顶储罐组成的罐组为例,设计方案如下:
1.内浮顶储罐改造
1)在储罐罐顶透光孔法兰盖处增加开口,用于安装氧气浓度检测器。
2)封堵储罐罐壁的通气口,同时在罐顶增加呼吸阀接口。
呼吸阀的数量及规格按照(SH/T 3007-2007)《石油化工储运系统罐区设计规范》确定。
3)在储罐罐顶增加氮气接入口。
4)在储罐罐顶增加气相联通管接口。
2.工艺流程
1)在储罐内安装氧气检测器,实时监测储罐内气相空间氧气浓度,同时将高浓度报警与氮气管道控制阀门联锁。
当氧气浓度达到高浓度值时报警,联锁打开氮气阀门,向储罐内补充氮气,直至检测指标达到设定要求时联锁关闭氮气阀门。
补充氮气的流量控制使用限流孔板,流量宜控制在Q=Q1-Q2(Q1-油品出罐流量,Q2-气相连通罐中与油品出罐同时进行的油品进罐流量),且Q不应小于100m3/h,氮气管道的管径为DN50,氮气的操作压力为0.5Mpa。
氧气浓度监测信号引入控制室,控制室设氧气浓度超标报警仪。
2)同一种油品的多个储罐在生产运行过程中,储罐区域收油作业和付油作业经常同时进行。
为节省氮气用量,建议在同种油品储罐之间设置气相联通管道,可以实现多个运行过程中的储罐进气量和排气量的部分平衡,减少氮气用量和作业时的油气排放量。
联通管道的管径为DN150,气体的流通能力为500m3/h。
管道及仪表流程图见附图-1。
氧气检测器、切断阀仪表规格书见附表。
3.仪表选型说明
1)氧气气体检测器采用电化学探头。
2)切断阀采用气动切断球阀。
3)氮气补气总管上配置涡街流量计进行氮气流量监测。
4.安装布置方案
1)氧气浓度检测器通过透光孔安装在储罐拱顶与内浮盘之间,为保证不影响储罐内浮盘的正常升降,氧气检测器的安装高度宜为储罐内浮盘之上300mm。
2)罐顶氮气接口的开口方位宜位于罐顶中心部位,氮气管道在罐内部分采用橡胶软管。
为保证换气效果良好,氮气橡胶软管出口宜接近浮盘。
可在氮气橡胶软管出口连接一个环形不锈钢管,管壁水平方向上开若干个通气孔,用于向四周喷射氮气。
环形不锈钢管应固定安装在浮盘上。
3)储罐之间设置DN150气相联通管道,每个储罐的气相联通管道均应设置管道阻火器,阻火器应选用安全性能满足要求的产品。
阻火器应尽量靠近储罐接口安装,每个储罐的气相联通管道均应设置截断阀。
气相联通管道宜在罐顶之间跨接。
若罐间距较大,气相
联通管道需要设在地面时,应在管道的低点设置排凝管及阀门。
4)在储罐罐顶中心位置安装带阻火器的呼吸阀,呼吸阀的数量及规格推荐如下:
呼吸阀选用表。