炼钢生产过程及流程图详解(全)
炼钢生产过程以及流程图详解(全)
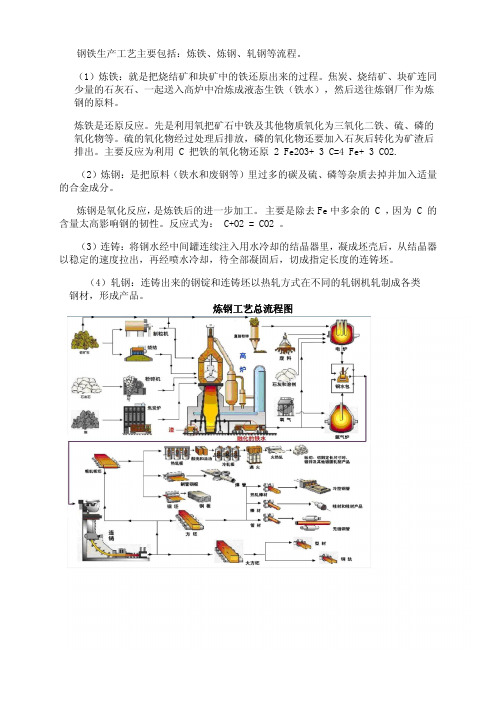
钢铁生产工艺主要包括:炼铁、炼钢、轧钢等流程。
(1)炼铁:就是把烧结矿和块矿中的铁还原出来的过程。
焦炭、烧结矿、块矿连同少量的石灰石、一起送入高炉中冶炼成液态生铁(铁水),然后送往炼钢厂作为炼钢的原料。
炼铁是还原反应。
先是利用氧把矿石中铁及其他物质氧化为三氧化二铁、硫、磷的氧化物等。
硫的氧化物经过处理后排放,磷的氧化物还要加入石灰后转化为矿渣后排出。
主要反应为利用 C 把铁的氧化物还原 2 Fe2O3+ 3 C=4 Fe+ 3 CO2.(2)炼钢:是把原料(铁水和废钢等)里过多的碳及硫、磷等杂质去掉并加入适量的合金成分。
炼钢是氧化反应,是炼铁后的进一步加工。
主要是除去Fe中多余的 C ,因为 C 的含量太高影响钢的韧性。
反应式为: C+O2 = CO2 。
(3)连铸:将钢水经中间罐连续注入用水冷却的结晶器里,凝成坯壳后,从结晶器以稳定的速度拉出,再经喷水冷却,待全部凝固后,切成指定长度的连铸坯。
(4)轧钢:连铸出来的钢锭和连铸坯以热轧方式在不同的轧钢机轧制成各类 钢材,形成产品。
炼钢工艺总流程图炼焦生产流程:炼焦作业是将焦煤经混合,破碎后加入炼焦炉内经干馏后产生热焦碳及粗焦炉气之制程。
烧结生产流程:烧结作业系将粉铁矿,各类助熔剂及细焦炭经由混拌、造粒后,经由布料系统加入烧结机,由点火炉点燃细焦炭,经由抽气风车抽风完成烧结反应,高热之烧结矿经破碎冷却、筛选后,送往高炉作为冶炼铁水之主要原料。
还原气体,还原铁矿石,产生熔融铁水与熔渣之炼铁制程。
转炉生产流程:炼钢厂先将熔铣送前处理站作脱硫脱磷处理,经转炉吹炼后,再依订单钢种特性及品质需求,送二次精炼处理站(RH真空脱气处理站、Ladle Injection盛桶吹射处理站、VOD真空吹氧脱碳处理站、STN搅拌站等)进行各种处理,调整钢液成份,最后送大钢胚及扁钢胚连续铸造机,浇铸成红热钢胚半成品,经检验、研磨或烧除表面缺陷,或直接送下游轧制成条钢、线材、钢板、钢卷及钢片等成品。
炼钢工艺流程介绍(PPT47页)

炼钢转炉--氧枪设备
❖ 氧枪系统主要设备 ❖ 氧枪横移装置。 ❖ 氧枪升降装置 ❖ 氧枪滑道装置 ❖ 氧枪本体 ❖ 氧枪(氧、氮、水)
阀门站
炼钢转炉-(-次)除尘设备
❖ 蒸发冷却塔系统装置 ❖ 静电除尘器系统装置 ❖ 切换站系统装置 ❖ 轴流风机系统装置 ❖ 煤气冷却器系统装置 输灰系统 ❖ 输灰系统装置 ❖ 放散点火装置 ❖ CO气体检测报警
❖电弧炉炼钢法 ❖平炉炼钢法
Байду номын сангаас
炼钢流程图
钢产线流程图
炼钢工艺与设备
根据炼钢工艺流程, 可以把炼钢作业分为4部分:
1、冶炼前的铁水预处理工序 2、铁水冶炼 3、钢水精炼 4、钢水浇铸
炼钢 预处理
在铁水进入炼钢炉冶 炼前,除去其中的某 些有害成分或提取其 中某些有益成分的工 艺过程。 可分为普通铁水预处 理和特殊铁水预处理。前者有铁水预脱硫,铁水 预脱硅,铁水预脱磷;后者有铁水提钒,铁水提 铌,铁水脱铬等。
炼钢 预处理
重要的工艺节点: 兑铁(如果不是专用的预处理罐则没有) 前扒渣 预处理(脱硫、脱磷等) 后扒渣 出铁
炼钢 预处理
炼钢 混铁炉
高炉和转炉之间的 炼钢辅助设备。 主要用于调节和均 衡高炉和转炉之间 铁水供求的设备, 保证不间断地供给 转炉需要的铁水, 铁水在混铁炉中储 存和混匀铁水成份 及均匀温度,对转 炉炼钢非常有利。
炼钢工艺与设备
炼钢工程概述
❖ 本项目为山东焦化北海新区节能新工艺示范工程配套建设 项目,
❖ 拟建炼钢车间生产规模为年产合格钢水500万吨。项目分 两期完成,
❖ 一期配置1座600t混铁炉(预留)、2套复合喷吹脱硫装 置、2座120t顶底复吹转炉、2套150tLF、2套R9m8 机8流方坯连铸机,年产合格钢水250万吨。
炼钢生产过程及流程图详解(全)

钢铁生产工艺主要包括:炼铁、炼钢、轧钢等流程。
(1)炼铁:就是把烧结矿和块矿中的铁还原出来的过程。
焦炭、烧结矿、块矿连同少量的石灰石、一起送入高炉中冶炼成液态生铁(铁水),然后送往炼钢厂作为炼钢的原料。
炼铁是还原反应。
先是利用氧把矿石中铁及其他物质氧化为三氧化二铁、硫、磷的氧化物等。
硫的氧化物经过处理后排放,磷的氧化物还要加入石灰后转化为矿渣后排出。
主要反应为利用 C 把铁的氧化物还原 2 Fe2O3+ 3 C=4 Fe+ 3 CO2.(2)炼钢:是把原料(铁水和废钢等)里过多的碳及硫、磷等杂质去掉并加入适量的合金成分。
炼钢是氧化反应,是炼铁后的进一步加工。
主要是除去Fe中多余的 C ,因为 C 的含量太高影响钢的韧性。
反应式为: C+O2 = CO2 。
(3)连铸:将钢水经中间罐连续注入用水冷却的结晶器里,凝成坯壳后,从结晶器以稳定的速度拉出,再经喷水冷却,待全部凝固后,切成指定长度的连铸坯。
(4)轧钢:连铸出来的钢锭和连铸坯以热轧方式在不同的轧钢机轧制成各类 钢材,形成产品。
炼钢工艺总流程图炼焦生产流程:炼焦作业是将焦煤经混合,破碎后加入炼焦炉内经干馏后产生热焦碳及粗焦炉气之制程。
烧结生产流程:烧结作业系将粉铁矿,各类助熔剂及细焦炭经由混拌、造粒后,经由布料系统加入烧结机,由点火炉点燃细焦炭,经由抽气风车抽风完成烧结反应,高热之烧结矿经破碎冷却、筛选后,送往高炉作为冶炼铁水之主要原料。
还原气体,还原铁矿石,产生熔融铁水与熔渣之炼铁制程。
转炉生产流程:炼钢厂先将熔铣送前处理站作脱硫脱磷处理,经转炉吹炼后,再依订单钢种特性及品质需求,送二次精炼处理站(RH真空脱气处理站、Ladle Injection盛桶吹射处理站、VOD真空吹氧脱碳处理站、STN搅拌站等)进行各种处理,调整钢液成份,最后送大钢胚及扁钢胚连续铸造机,浇铸成红热钢胚半成品,经检验、研磨或烧除表面缺陷,或直接送下游轧制成条钢、线材、钢板、钢卷及钢片等成品。
钢铁生产流程详解图
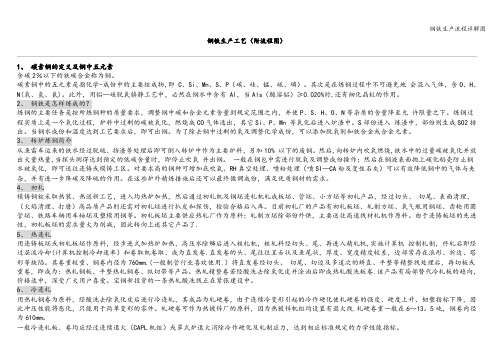
钢铁生产工艺(附流程图)1、碳素钢的定义及钢中五元素含碳2%以下的铁碳合金称为钢。
碳素钢中的五元素是指化学-成份中的主要组成物,即 C、Si、Mn、S、P(碳、硅、锰、硫、磷)。
其次是在炼钢过程中不可避免地会混入气体,含O、H、N(氧、氢、氮)。
此外,用铝—硅脱氧镇静工艺中,必然在钢水中含有 Al,当Als(酸溶铝)≥0.020%时,还有细化晶粒的作用。
2、钢铁是怎样炼成的?炼钢的主要任务是按所炼钢种的质量要求,调整钢中碳和合金元素含量到规定范围之内,并使P、S、H、O、N等杂质的含量降至允许限量之下。
炼钢过程实质上是一个氧化过程,炉料中过剩的碳被氧化,燃烧成CO气体逸出,其它Si、P、Mn 等氧化后进入炉渣中。
S部份进入炼渣中,部份则生成SO2排出。
当钢水成份和温度达到工艺要求后,即可出钢。
为了除去钢中过剩的氧及调整化学成份,可以添加脱氧剂和铁合金或合金元素。
3、转炉炼钢简介从鱼雷车运来的铁水经过脱硫、挡渣等处理后即可倒入转炉中作为主要炉料,另加10% 以下的废钢。
然后,向转炉内吹氧燃烧,铁水中的过量碳被氧化并放出大量热量,当探头测得达到预定的低碳含量时,即停止吹氧并出钢。
一般在钢包中需进行脱氧及调整成份操作;然后在钢液表面抛上碳化稻壳防止钢水被氧化,即可送往连铸或模铸工区。
对要求高的钢种可增加底吹氩、RH真空处理、喷粉处理(喷SI—CA粉及变性石灰)可以有效降低钢中的气体与夹杂,并有进一步降碳及降硫的作用。
在这些炉外精炼措施后还可以最终微调成份,满足优质钢材的需求。
4、初轧模铸钢锭采取热装、热送新工艺,进入均热炉加热,然后通过初轧机及钢坯连轧机轧成板坯、管坯、小方坯等初轧产品,经过切头、切尾、表面清理,(火焰清理、打磨)高品质产品则还需对初轧坯进行扒皮和探伤,检验合格后入库。
目前初轧厂的产品有初轧板坯、轧制方坯、氧气瓶用钢坯、齿轮用圆管坯、铁路车辆用车轴坯及塑模用钢等。
初轧板坯主要供应热轧厂作为原料;轧制方坯除部份外供,主要送往高速线材轧机作原料。
钢铁生产工艺流程图

钢铁生产工艺流程炼焦生产流程:炼焦作业是将焦煤经混合,破碎后加入炼焦炉内经干馏后产生热焦碳及粗焦炉气之制程。
资源来源:台湾中钢公司网站。
烧结生产流程:烧结作业系将粉铁矿,各类助熔剂及细焦炭经由混拌、造粒后,经由布料系统加入烧结机,由点火炉点燃细焦炭,经由抽气风车抽风完成烧结反应,高热之烧结矿经破碎冷却、筛选后,送往高炉作为冶炼铁水之主要原料。
资源来源:台湾中钢公司网站。
高炉生产流程:高炉作业是将铁矿石、焦炭及助熔剂由高炉顶部加入炉内,再由炉下部鼓风嘴鼓入高温热风,产生还原气体,还原铁矿石,产生熔融铁水与熔渣之炼铁制程。
资源来源:台湾中钢公司网站。
转炉生产流程:炼钢厂先将熔铣送前处理站作脱硫脱磷处理,经转炉吹炼后,再依订单钢种特性及品质需求,送二次精炼处理站(RH真空脱气处理站、Ladle Injection盛桶吹射处理站、VOD真空吹氧脱碳处理站、STN搅拌站等)进行各种处理,调整钢液成份,最后送大钢胚及扁钢胚连续铸造机,浇铸成红热钢胚半成品,经检验、研磨或烧除表面缺陷,或直接送下游轧制成条钢、线材、钢板、钢卷及钢片等成品。
资源来源:台湾中钢公司网站。
连铸生产流程:连续铸造作业乃是将钢液转变成钢胚之过程。
上游处理完成之钢液,以盛钢桶运送到转台,经由钢液分配器分成数股,分别注入特定形状之铸模内,开始冷却凝固成形,生成外为凝固壳、内为钢液之铸胚,接着铸胚被引拔到弧状铸道中,经二次冷却继续凝固到完全凝固。
经矫直后再依订单长度切割成块,方块形即为大钢胚,板状形即为扁钢胚。
此半成品视需要经钢胚表面处理后,再送轧钢厂轧延。
资源来源:台湾中钢公司网站。
热轧生产流程。
热轧生产流程。
资源来源:台湾中钢公司网站。
热轧生产流程>第一热轧钢带生产流程:热轧钢带工场主要制程是将扁钢胚加热后,经粗轧机及精轧机轧延成钢带,并以层流冷却系统喷水冷却至适当温度,再由盘卷机卷成粗钢卷。
资源来源:台湾中钢公司网站。
热轧生产流程>一号调质重卷线布置图:主要功能为将原料钢卷上线解卷、调质轧延、分切、重卷及包装为成品H.R COIL 或H.R BAND〔HR BAND 未调质轧延〕。
炼钢工艺流程图
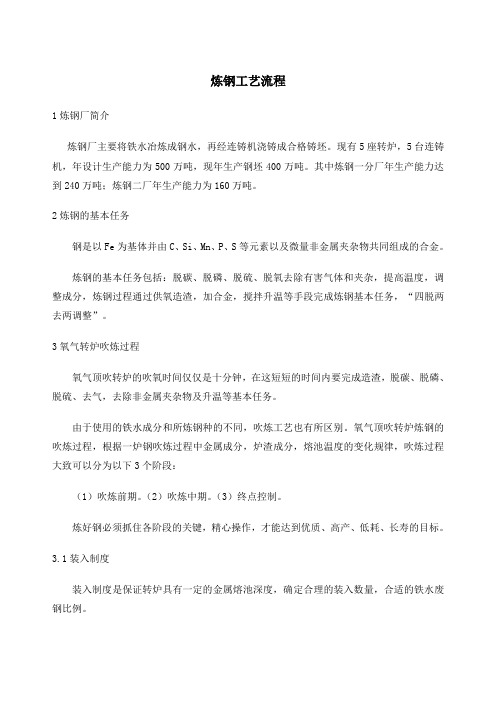
炼钢工艺流程1炼钢厂简介炼钢厂主要将铁水冶炼成钢水,再经连铸机浇铸成合格铸坯。
现有5座转炉,5台连铸机,年设计生产能力为500万吨,现年生产钢坯400万吨。
其中炼钢一分厂年生产能力达到240万吨;炼钢二厂年生产能力为160万吨。
2炼钢的基本任务钢是以Fe为基体并由C、Si、Mn、P、S等元素以及微量非金属夹杂物共同组成的合金。
炼钢的基本任务包括:脱碳、脱磷、脱硫、脱氧去除有害气体和夹杂,提高温度,调整成分,炼钢过程通过供氧造渣,加合金,搅拌升温等手段完成炼钢基本任务,“四脱两去两调整”。
3氧气转炉吹炼过程氧气顶吹转炉的吹氧时间仅仅是十分钟,在这短短的时间内要完成造渣,脱碳、脱磷、脱硫、去气,去除非金属夹杂物及升温等基本任务。
由于使用的铁水成分和所炼钢种的不同,吹炼工艺也有所区别。
氧气顶吹转炉炼钢的吹炼过程,根据一炉钢吹炼过程中金属成分,炉渣成分,熔池温度的变化规律,吹炼过程大致可以分为以下3个阶段:(1)吹炼前期。
(2)吹炼中期。
(3)终点控制。
炼好钢必须抓住各阶段的关键,精心操作,才能达到优质、高产、低耗、长寿的目标。
3.1装入制度装入制度是保证转炉具有一定的金属熔池深度,确定合理的装入数量,合适的铁水废钢比例。
3.1.1装入量的确定装入量是指转炉冶炼中每炉次装入的金属料总重量,它主要包括铁水和废钢量。
目前国内外装入制度大体上有三种方式:(1)定深装入;(2)分阶段定量装入;(3)定量装入3.2.2装入次序目前永钢的操作顺序为,钢水倒完后进行溅渣护炉溅渣完后装入废钢,然后兑入铁水。
为了维护炉衬,减少废钢对炉衬的冲击,装料次序也可以先兑铁水,后装废钢。
若采用炉渣预热废钢,则先加废钢,再倒渣,然后兑铁水。
如果采用炉内留渣操作,则先加部分石灰,再装废钢,最后兑铁水。
3.2供氧制度制订供氧制度时应考虑喷头结构,供氧压力,供氧强度和氧枪高度控制等因素。
3.2.1氧枪喷头转炉供氧的射流特征是通过氧枪喷头来实现的,因此,喷头结构的合理选择是转炉供氧的关键。
钢铁生产工艺流程图

钢铁生产工艺流程炼焦生产流程:炼焦作业是将焦煤经混合,破碎后加入炼焦炉内经干馏后产生热焦碳及粗焦炉气之制程。
资源来源:台湾中钢公司网站。
烧结生产流程:烧结作业系将粉铁矿,各类助熔剂及细焦炭经由混拌、造粒后,经由布料系统加入烧结机,由点火炉点燃细焦炭,经由抽气风车抽风完成烧结反应,高热之烧结矿经破碎冷却、筛选后,送往高炉作为冶炼铁水之主要原料。
资源来源:台湾中钢公司网站。
高炉生产流程:高炉作业是将铁矿石、焦炭及助熔剂由高炉顶部加入炉内,再由炉下部鼓风嘴鼓入高温热风,产生还原气体,还原铁矿石,产生熔融铁水与熔渣之炼铁制程。
资源来源:台湾中钢公司网站。
转炉生产流程:炼钢厂先将熔铣送前处理站作脱硫脱磷处理,经转炉吹炼后,再依订单钢种特性及品质需求,送二次精炼处理站(RH真空脱气处理站、Ladle Injection盛桶吹射处理站、VOD真空吹氧脱碳处理站、STN搅拌站等)进行各种处理,调整钢液成份,最后送大钢胚及扁钢胚连续铸造机,浇铸成红热钢胚半成品,经检验、研磨或烧除表面缺陷,或直接送下游轧制成条钢、线材、钢板、钢卷及钢片等成品。
资源来源:台湾中钢公司网站。
连铸生产流程:连续铸造作业乃是将钢液转变成钢胚之过程。
上游处理完成之钢液,以盛钢桶运送到转台,经由钢液分配器分成数股,分别注入特定形状之铸模内,开始冷却凝固成形,生成外为凝固壳、内为钢液之铸胚,接着铸胚被引拔到弧状铸道中,经二次冷却继续凝固到完全凝固。
经矫直后再依订单长度切割成块,方块形即为大钢胚,板状形即为扁钢胚。
此半成品视需要经钢胚表面处理后,再送轧钢厂轧延。
资源来源:台湾中钢公司网站。
热轧生产流程。
热轧生产流程。
资源来源:台湾中钢公司网站。
热轧生产流程>第一热轧钢带生产流程:热轧钢带工场主要制程是将扁钢胚加热后,经粗轧机及精轧机轧延成钢带,并以层流冷却系统喷水冷却至适当温度,再由盘卷机卷成粗钢卷。
资源来源:台湾中钢公司网站。
热轧生产流程>一号调质重卷线布置图:主要功能为将原料钢卷上线解卷、调质轧延、分切、重卷及包装为成品H.R COIL 或H.R BAND〔HR BAND 未调质轧延〕。
钢铁生产工艺流程图

钢铁生产工艺流程炼焦生产流程:炼焦作业是将焦煤经混合,破碎后加入炼焦炉内经干馏后产生热焦碳及粗焦炉气之制程。
资源来源:台湾中钢公司网站。
烧结生产流程:烧结作业系将粉铁矿,各类助熔剂及细焦炭经由混拌、造粒后,经由布料系统加入烧结机,由点火炉点燃细焦炭,经由抽气风车抽风完成烧结反应,高热之烧结矿经破碎冷却、筛选后,送往高炉作为冶炼铁水之主要原料。
资源来源:台湾中钢公司网站。
高炉生产流程:高炉作业是将铁矿石、焦炭及助熔剂由高炉顶部加入炉内,再由炉下部鼓风嘴鼓入高温热风,产生还原气体,还原铁矿石,产生熔融铁水与熔渣之炼铁制程。
资源来源:台湾中钢公司网站。
转炉生产流程:炼钢厂先将熔铣送前处理站作脱硫脱磷处理,经转炉吹炼后,再依订单钢种特性及品质需求,送二次精炼处理站(RH真空脱气处理站、Ladle Injection盛桶吹射处理站、VOD真空吹氧脱碳处理站、STN搅拌站等)进行各种处理,调整钢液成份,最后送大钢胚及扁钢胚连续铸造机,浇铸成红热钢胚半成品,经检验、研磨或烧除表面缺陷,或直接送下游轧制成条钢、线材、钢板、钢卷及钢片等成品。
资源来源:台湾中钢公司网站。
连铸生产流程:连续铸造作业乃是将钢液转变成钢胚之过程。
上游处理完成之钢液,以盛钢桶运送到转台,经由钢液分配器分成数股,分别注入特定形状之铸模内,开始冷却凝固成形,生成外为凝固壳、内为钢液之铸胚,接着铸胚被引拔到弧状铸道中,经二次冷却继续凝固到完全凝固。
经矫直后再依订单长度切割成块,方块形即为大钢胚,板状形即为扁钢胚。
此半成品视需要经钢胚表面处理后,再送轧钢厂轧延。
资源来源:台湾中钢公司网站。
热轧生产流程。
热轧生产流程。
资源来源:台湾中钢公司网站。
热轧生产流程>第一热轧钢带生产流程:热轧钢带工场主要制程是将扁钢胚加热后,经粗轧机及精轧机轧延成钢带,并以层流冷却系统喷水冷却至适当温度,再由盘卷机卷成粗钢卷。
资源来源:台湾中钢公司网站。
热轧生产流程>一号调质重卷线布置图:主要功能为将原料钢卷上线解卷、调质轧延、分切、重卷及包装为成品H.R COIL 或H.R BAND〔HR BAND 未调质轧延〕。
钢铁生产工艺设计流程图
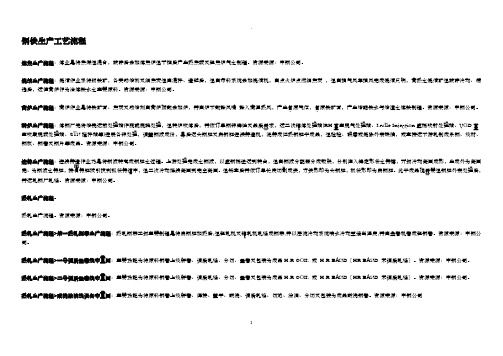
钢铁生产工艺流程炼焦生产流程:炼业是将焦煤经混合,破碎后参加炼焦炉经干馏后产生热焦碳及粗焦炉气之制程。
资源来源:中钢公司。
烧结生产流程:烧结作业系将粉铁矿,各类助熔剂及细焦炭经由混拌、造粒后,经由布料系统参加烧结机,由点火炉点燃细焦炭,经由抽气风车抽风完成烧结反响,高热之烧结矿经破碎冷却、筛选后,送往高炉作为冶炼铁水之主要原料。
资源来源:中钢公司。
高炉生产流程:高炉作业是将铁矿石、焦炭及助熔剂由高炉顶部参加炉,再由炉下部鼓风嘴鼓入高温热风,产生复原气体,复原铁矿石,产生熔融铁水与熔渣之炼铁制程。
资源来源:中钢公司。
转炉生产流程:炼钢厂先将熔铣送前处理站作脱硫脱磷处理,经转炉吹炼后,再依订单钢种特性及品质需求,送二次精炼处理站(RH真空脱气处理站、Ladle Injection盛桶吹射处理站、VOD真空吹氧脱碳处理站、STN搅拌站等)进展各种处理,调整钢液成份,最后送大钢胚及扁钢胚连续铸造机,浇铸成红热钢胚半成品,经检验、研磨或烧除外表缺陷,或直接送下游轧制成条钢、线材、钢板、钢卷及钢片等成品。
资源来源:中钢公司。
连铸生产流程:连续铸造作业乃是将钢液转变成钢胚之过程。
上游处理完成之钢液,以盛钢桶运送到转台,经由钢液分配器分成数股,分别注入特定形状之铸模,开场冷却凝固成形,生成外为凝固壳、为钢液之铸胚,接着铸胚被引拔到弧状铸道中,经二次冷却继续凝固到完全凝固。
经矫直后再依订单长度切割成块,方块形即为大钢胚,板状形即为扁钢胚。
此半成品视需要经钢胚外表处理后,再送轧钢厂轧延。
资源来源:中钢公司。
热轧生产流程。
热轧生产流程。
资源来源:中钢公司。
热轧生产流程>第一热轧钢带生产流程:热轧钢带工场主要制程是将扁钢胚加热后,经粗轧机及精轧机轧延成钢带,并以层流冷却系统喷水冷却至适当温度,再由盘卷机卷成粗钢卷。
资源来源:中钢公司。
热轧生产流程>一号调质重卷线布置图:主要功能为将原料钢卷上线解卷、调质轧延、分切、重卷及包装为成品H.R COIL 或H.R BAND〔HR BAND 未调质轧延〕。
炼钢工艺流程图

炼钢厂工艺流程与设备规格性能一、炼钢厂工艺流程图二、炼钢厂示意图1、转炉示意图及工艺参数工艺参数转炉炉体1.1炉体总高(包括炉壳支撑板):7050mm1.2炉壳高度:6820mm1.3炉壳外径:Φ4370mm1.4高宽比: H/D=1.561.5炉壳内径:Φ4290mm1.6公称容量:50t1.7有效容积:39.5m31.8熔池直径: Φ3160mm1.9炉口内径:Φ1400mm1.10出钢口直径:140mm1.11出钢口倾角(与水平):20°1.12炉膛内径:Φ3160mm1.13炉容比:0.79m3 /t.s1.14熔池深度:1133mm1.15炉衬厚度:熔池:500mm 炉身:500mm 炉底:465mm 炉帽:550mm 1.16炉壳总重:77.6t1.17炉衬重量:120t1.18炉口结构:水冷炉口1.19炉帽结构:水冷炉帽1.20挡渣板结构:双层钢板焊接式1.21托圈结构:箱式结构(水冷耳轴)倾动装置型式:四点啮合全悬挂扭力杆式(交流变频器调速)最大工作倾动力矩:100t*m最大事故倾动力矩:300t*m倾动角度:±360°倾动速度:0.2~1r/min二、方坯连铸示意图大包中包方坯弧形连铸机铸机基本参数:机型:全弧形铸机弧型半径:R6000/12000mm;机~流:5~5流间距:1250mm弯曲:连续弯曲矫直:连续矫直铸坯规格:120mm × 120mm;150mm × 150mm;100mm × 173mm;130mm × 173mm;拉速:120mm × 120mm 3.2~3.76 m/min;150mm × 150mm 2.0~3.0 m/min;100mm × 173mm; 2.8~3.4 m/min;130mm × 173mm; 2.0~3.0 m/min;冶金长度: 14.69 m(全凝固矫直);17.27 m(带液芯矫直)铸机长度:16.16m(铸机外弧基准线至固定挡板)定尺长度:3~6m铸机有效作业率:85%钢水收得率:96.8%设计年产量:80万吨/年三、板坯连铸大包中包结晶器板坯连铸机示意图铸机基本参数:机型:立弯式连铸机铸机弧型半径:6000mm;机~流:2~2流间距:4700mm弯曲:8点弯曲,R65000mm、R30600mm、R19300mm、R14000mm、R11000mm、R9000mm、R7200mm、R6000mm矫直:6点矫直,R6000mm、R7200mm、R9000mm、R11700mm、R16700mm、R31600mm 铸坯规格:150mm × 350~680mm;180mm × 350~680mm;200mm × 350~680mm;拉速:150mm × 350~680mm; V max:1.6 m/min; 180mm × 350~680mm; V max:1.5 m/min;200mm × 350~680mm; V max:1.2 m/min;冶金长度:17.43 m铸机长度:17.43 m定尺长度:6500m铸机有效作业率:82%钢水收得率:97%设计年产量:60万吨/年。
炼钢厂基本工艺流程图
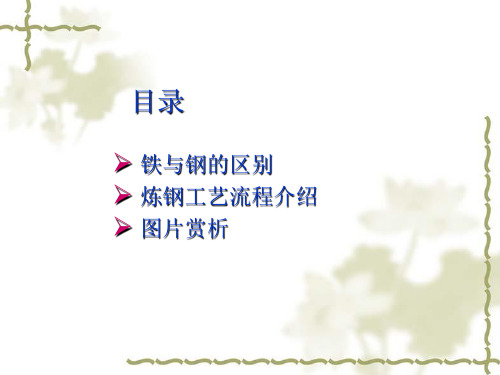
• 4:目前大转炉多采用电除尘、副枪、气动挡
渣、自动炼钢等技术
转炉冶炼
石灰、轻烧、 烧结矿、萤石
氧枪
O2 N2 炉气(CO+CO2) 副枪
氧枪喷头
氧气流股
熔池钢水 氧气流股冲击区 转炉吹炼示意图
乳浊液
(CO气泡、炉渣、铁粒)
TSC、TSO偶头
底吹(N2/Ar)
除尘系统
一文
重力脱水器 烟道
功能:
• 1:炼钢与炼铁的衔接 • 2:适时的给转炉提供合适重量、合
适成分的铁水
• 3:目前最先进的组织方式是铁水直兑,这是
节能的要求
• 4:发展趋势 : 混铁炉 鱼雷罐 直兑
二、铁水脱硫
• 1:脱硫剂:碱性氧化物(CaO,Na2O,),Mg剂 • 2:优点:还原环境,最有利的脱硫环境;成本最
低的脱硫方式;可深脱硫达到(﹤0.005%) Mg(S)+[S]=MgS(s)
• 可浇性好保证在浇铸过程中,钢水有良好流
动性.水口不堵塞、(控制含AL钢的AL含量, Ca含量,硫含量)
3. 拉速控制
• 拉速单位是m/min。拉速是连铸工艺的重要参数。
正确的拉速控制目的是:a、保证浇注顺利,力求 事故率最低;b、充分发挥连铸机生产能力;c、 改善铸坯质量。
• 最大拉速受到以下环节的限制:a、 受连铸机冶
谢谢各位!
(2) 二次冷却
铸坯二次冷却是带液芯的铸坯从结晶器出口进入二次冷却区,进 行喷水或气、水雾化冷却及空冷散热,但是冷却强度必须要适 宜,使铸坯进一步冷却,完成铸坯“完全凝固”的冷却过程, 为避免或减轻铸坯的各种缺陷,如裂纹、缩孔,偏析等。因此 铸坯在二冷区冷却要求如下:
转炉炼钢生产工艺简介及工艺流程图

转炉炼钢生产工艺简介及工艺流程图炼铁厂将炼出的合格铁水用内燃机车运到炼钢厂,用天车将铁水 兑入混铁炉,中和成份,保持铁水温度,为转炉冶炼创造良好的条件。
用铁水包将铁水兑入转炉,加入废钢、铁块,开始加料冶炼。
造渣剂、 合金、原料已由备料工段预先存入料仓,直接用电脑控制即可实行加 料操作。
吹炼过程中进行煤气回收,经除尘后送入煤气柜。
冶炼的炉渣经渣车运往渣场,由外运包工队处理,回收含铁钢渣 二次利用。
除尘系统后的浊环污泥,一部分制做成污泥球,作为冶炼原料, 另一部分运往烧结重复利用。
吹炼完毕进行测温取样,达到要求后,加脱氧剂、合金,出钢, 向钢包内加覆盖剂,同时实行在线吹氩,均匀成份,使夹杂物充分上 浮,均匀钢水温度,确保钢水的纯净度。
温度高时可加切割好的冷坯, 进行调温。
将钢水吊往连铸浇注平台,做到大包旋转台上,盖上大包盖。
将 预先烤好的中间包,用中包车开到结晶器上方,大包转包开浇。
拉钢 完成铸坯浇注结晶,拉出的坯子经辊道切割、运输,将不合格坯挑出 处理,可以调温、回炉冶炼或经轧钢厂同意降级处理。
用天车和升降 辊道为轧钢进行合格坯热送或存放。
不合格坯要单独码放。
汽车铁水罐(来自炼铁厂的铁水)散装料地下料仓混铁炉烧结厂至地下料仓垂直输送机 转运站电振给料机 称量漏斗铁水包 来自制氧厂 的 O2、Ar转炉(4×60t)污泥处理处理系统 除尘系统煤气放散系统煤气柜铁合金旋流槽汇总漏斗钢水包中间仓渣盘车2×60tLF(预留)称量斗废钢区钢渣堆放区连铸机轧钢厂堆放区电振给料机 铁合金料仓汽车图 2-1 转炉炼钢工艺流程框图铁合金料罐。
- 1、下载文档前请自行甄别文档内容的完整性,平台不提供额外的编辑、内容补充、找答案等附加服务。
- 2、"仅部分预览"的文档,不可在线预览部分如存在完整性等问题,可反馈申请退款(可完整预览的文档不适用该条件!)。
- 3、如文档侵犯您的权益,请联系客服反馈,我们会尽快为您处理(人工客服工作时间:9:00-18:30)。
钢铁生产工艺主要包括:炼铁、炼钢、轧钢等流程。
(1)炼铁:就是把烧结矿和块矿中的铁还原出来的过程。
焦炭、烧结矿、块矿连同少量的石灰石、一起送入高炉中冶炼成液态生铁(铁水),然后送往炼钢厂作为炼钢的原料。
炼铁是还原反应。
先是利用氧把矿石中铁及其他物质氧化为三氧化二铁、硫、磷的氧化物等。
硫的氧化物经过处理后排放,磷的氧化物还要加入石灰后转化为矿渣后排出。
主要反应为利用 C 把铁的氧化物还原 2 Fe2O3+ 3 C=4 Fe+ 3 CO2.
(2)炼钢:是把原料(铁水和废钢等)里过多的碳及硫、磷等杂质去掉并加入适量的合金成分。
炼钢是氧化反应,是炼铁后的进一步加工。
主要是除去Fe中多余的 C ,因为 C 的含量太高影响钢的韧性。
反应式为: C+O2 = CO2 。
(3)连铸:将钢水经中间罐连续注入用水冷却的结晶器里,凝成坯壳后,从结晶器以稳定的速度拉出,再经喷水冷却,待全部凝固后,切成指定长度的连铸坯。
(4)轧钢:连铸出来的钢锭和连铸坯以热轧方式在不同的轧钢机轧制成各类 钢材,形成产品。
炼钢工艺总流程图
炼焦生产流程:炼焦作业是将焦煤经混合,破碎后加入炼焦炉内经干馏后产生热焦碳及粗焦炉气之制程。
烧结生产流程:烧结作业系将粉铁矿,各类助熔剂及细焦炭经由混拌、造粒后,经由布料系统加入烧结机,由点火炉点燃细焦炭,经由抽气风车抽风完成烧结反应,高热之烧结矿经破碎冷却、筛选后,送往高炉作为冶炼铁水之主要原料。
还原气体,还原铁矿石,产生熔融铁水与熔渣之炼铁制程。
转炉生产流程:炼钢厂先将熔铣送前处理站作脱硫脱磷处理,经转炉吹炼后,再依订单钢种特性及品质需求,送二次精炼处理站(RH真空脱气处理站、Ladle Injection盛桶吹射处理站、VOD真空吹氧脱碳处理站、STN搅拌站等)进行各种处理,调整钢液成份,最后送大钢胚及扁钢胚连续铸造机,浇铸成红热钢胚半成品,经检验、研磨或烧除
表面缺陷,或直接送下游轧制成条钢、线材、钢板、钢卷及钢片等成品。
连铸生产流程:连续铸造作业乃是将钢液转变成钢胚之过程。
上游处理完成之钢液,以盛钢桶运送到转台,经由钢液分配器分成数股,分别注入特定形状之铸模内,开始冷却凝固成形,生成外为凝固壳、内为钢液之铸胚,接着铸胚被引拔到弧状铸道中,经二次冷却继续凝固到完全凝固。
经矫直后再依订单长度切割成块,方块形即为大钢胚,
板状形即为扁钢胚。
此半成品视需要经钢胚表面处理后,再送轧钢厂轧延.
热轧生产流程。
热轧生产流程>第一热轧钢带生产流程:热轧钢带工场主要制程是将扁钢胚加热后,经粗轧机及精轧机轧延成钢带,并以层流冷却系统喷水冷却至适当温度,再由盘卷机卷成粗钢卷。
热轧生产流程>热轧厚板剪切线布置图:主要功能为将原料钢卷上线解卷、切边、切片、整平、堆叠、及包装为成品钢板叠(HR PLATE)。
热轧生产流程>热轧薄板剪切线布置图:主要功能为将原料钢卷上线解卷、调质精整、切边、切片、整平、堆叠、及包装为成品钢片叠(H.R. SHEET)。
热轧生产流程>一号调质重卷线布置图:主要功能为将原料钢卷上线解卷、调质轧延、分切、重卷及包装为成品H.R COIL 或 H.R BAND〔HR BAND 未调质轧延〕。
热轧生产流程>二号调质重卷线布置图:主要功能为将原料钢卷上线解卷、调质轧延、分切、重卷及包装为成品H.R COIL 或 H.R BAND〔HR BAND 未调质轧延〕。
热轧生产流程>酸洗涂油线设备布置图:主要功能为将原料钢卷上线解卷、焊接、整平、酸洗、调质轧延、切边、涂油、分切及包装为成品酸洗钢卷。
热轧生产流程>第二热轧钢带生产流程:热轧钢带工场主要制程是将扁钢胚加热后,经粗轧机及精轧机轧延成钢带,并以层流冷却系统喷水冷却至适当温度,再由盘卷机卷成粗钢卷。
热轧生产流程>三号调质重卷线布置图:主要功能为将原料钢卷上线解卷、调质轧延、分切、重卷及包装为成品H.R COIL 或 H.R BAND〔HR BAND 未调质轧延〕。
热轧生产流程>四号调质重卷线布置图:主要功能为将原料钢卷上线解卷、调质轧延、分切、重卷及包装为成品H.R COIL 或 H.R BAND〔HR BAND 未调质轧延〕。
第一酸洗冷轧线:第一酸洗冷轧线接收热轧钢卷,经过解卷、焊接、整平、盐酸酸洗、裁边之后,再经由串列式冷轧机轧延成厚度较薄之冷轧钢卷。
第二酸洗冷轧线:第二酸洗冷轧线是利用张力整平机及酸洗去除热轧钢卷锈皮,清洗、烘干去除钢带表面残酸,由裁边机将钢带裁至下游产线所需宽度及经四站六重式轧延机将热轧钢卷轧至客户所需厚度,并藉自动板形控制器来改善钢带板形,是一连续式酸洗冷轧制程产线。
热轧生产流程>热轧厚板剪切线布置图:主要功能为将原料钢卷上线解卷、切边、切片、整平、堆叠、及包装为成品钢板叠(HR PLATE)。
连续热浸镀锌线:热浸镀锌线是一条连续性生产线,酸洗冷轧后钢卷送入本产线经过焊接、表面清洗及退火之后进入锌槽镀锌(GI材)或再加热产生锌铁合金(GA材),接着再经过调质轧延及张力整平,最后再依不同需求实施后处理
或涂油作业。
第一连续退火线:第一连续退火线包括清洗、退火、调质及精整等制程。
钢带经由焊接机焊接后,进入退火炉退火,而退火炉依不同钢种赋予不同退火温度,使其达到应有的机械性质,最后再依客户订单赋予钢带表面粗糙度、涂油
量、分切及包装。
第二连续退火线:第二连续退火线包括清洗、退火、调质及精整等制程。
先将冷轧后钢带表面残留之轧延油洗净,再将其加热至700~850℃,以去除钢带内部应力,并且使其再结晶及调整组织内固溶碳含量,以确保机械性质的稳定,再利用调质轧延以消除降伏点伸长,改善其材质及平坦度,并赋予钢带所需之表面粗糙度。
最后依客户订单将钢带涂防锈油、分切及包装。
封盒退火炉:封盒退火炉之功能系将冷轧钢卷在H2或HN气氛下,进行钢卷之再结晶及光辉退火。
电解清洗线:电解清洗线接收冷轧钢卷,经过解卷、焊接以及电解碱洗,产制电解清洗钢卷。
连续涂覆线:连续涂覆线有两项主要产品,电磁钢卷及彩色钢卷。
生产电磁钢卷的作业是接收第一连续退火线之母材后,经过清洗、水性绝缘涂料涂覆、烘焙、冷却的制程。
生产彩色钢卷作业是接收冷轧母材后,经过清洗及磷
酸皮膜处理、底漆涂覆、面漆涂覆、烘焙、冷却的制程。
母材后经过清洗,涂上水性绝缘涂料、烘焙、冷却的制程。
电气镀锌线:电气镀锌生产作业是将冷轧钢卷经由前段进料区、清洗与酸洗区、电镀区、后处理区、抗指纹涂覆区及后段出料区,产出电气镀锌钢卷成品。
调质线:制程及功能: 1. 改变退火后钢卷的机械性质,并消除降伏点伸长。
2. 赋与钢带表面符合订单之粗糙度。
3. 修正入料钢卷的不良板形。
重卷线:重卷线功能系将退火及调质后冷轧钢卷施以涂油、重卷及分切制程之后,加以包装入库。
往复式冷轧机:往复式冷轧机接收热轧酸洗钢卷(未退火与预退火),经过解卷、穿引之后,再经由六重式冷轧机轧延成厚度较薄之冷轧钢卷。
水平式退火涂覆线:水平式退火涂覆线包括清洗、退火、涂覆及切边等制程。
钢带经由焊接机焊接后,进入退火炉退火,而退火炉依不同钢种赋予不同退火温度,使其达到应有的铁损值,再依客户订单涂覆不同之水性绝缘涂料,涂膜厚度,分切及包装。
张力整平线(TLL):张力整平线功能系将退火及调质后冷轧钢卷施以涂油、整平及分切制程之后,加以包装入库。
编者注本资源来源:台湾中钢公司网站。