关于原油加工过程中防治氯化物腐蚀的建议
原油加工过程氯的腐蚀与防治问题

原油加工过程氯的腐蚀与防治问题摘要:对于原油加工而言,腐蚀问题历来是管理重点和难题,其中氯化物的腐蚀最为突出,既影响了设备性能,也对炼厂安全构成了威胁,故必须加以有效防治。
对此,笔者阐述了原油加工中氯化物腐蚀的危害,并以其腐蚀机理为切入点提出了几点防治措施,希望对缓解原油加工中氯的腐蚀现状有所助益。
关键词:原油加工;氯化物腐蚀;防治近年来,原油重质化、劣质化问题日益严重,尤其是氯元素的不断增加,对设备性能和炼厂安全构成了极大的威胁,进而使得氯化物超标问题备受关注。
这就要求我们重视原油加工中氯腐蚀的高危害性,并立足实际采取切实有效的措施加以防治,通过减少氯的含量,促进原油加工朝着安全、高效、优质的方向发展。
一、原油加工过程中氯腐蚀的危害由于油田时常会遇到油井堵塞问题,制约了采油产量的提高,所以往往会加入含有氯代烷烃的清蜡剂、降凝剂、降粘剂、清解堵剂等诸多化学药剂来改善采收率,当其与原油一同进入炼油系统时,便会直接或间接的腐蚀炼油设备和装置。
具体的说,当化学药剂中的氯代烷烃经高温水解形成氯化物后会在蒸馏塔中严重腐蚀减压蒸馏装置、冷凝装置,使其难以安全生产,而且还可能引发管道阻塞、催化剂中毒等问题,如某炼油厂的常减压装置在氯化物的腐蚀下出现了多次泄露、塌陷、浮阀脱落问题,高压换热器和空冷也存在严重的腐蚀等等,二次加工装置也难以幸免。
故原油加工过程中氯的腐蚀无论是对炼油生产装置的安全运行使用寿命,还是企业的经济效益,均带来了巨大的不良影响,亟待改善。
二、原油加工过程中氯的腐蚀机理之所以在原油加工过程氯腐蚀的防治问题中分析氯的腐蚀机理,是因为只有了解其形成过程,才能对症下药提高防治措施的有效性,更好的解决氯腐蚀问题。
研究发现,原油加工过程中的氯主要分为有机氯化物和无机氯化物,虽然两者属性不同,但均会造成设备腐蚀以及催化剂中毒,而且腐蚀设备的过程都与 HCl有关。
无机氯化物可与水直接发生化学反应生成 HCl,而有机氯化物则难以发生水解,但当其到达减压塔时,经电脱盐处理后的水 PH 值会有所提升变为碱性,致使部分有机氯化物发生水解产生气体 HCl,并随油气流一同到达减压塔顶部,当其遇到水便会形成腐蚀性强的稀盐酸,最终腐蚀设备,同时少量的水蒸气达到冷凝系统变成冰时,气体 HCl 会溶于其中形成稀盐酸环境,进而对周围设备造成腐蚀[1]。
石油炼制设备腐蚀的防治措施

石油炼制设备腐蚀的防治措施发布时间:2021-05-19T08:37:27.576Z 来源:《中国科技人才》2021年第8期作者:王烨[导读] 近年来,高硫原油被中国大规模炼化,设备腐蚀问题明显,造成严重经济损失也让企业难以进一步发展。
石油炼制装置的腐蚀种类和程度与原油的种类和含量密切相关。
天津石化炼油部天津 300270摘要:在石油炼制的过程中,由于长时间使用会使炼制设备被腐蚀,因此耐腐蚀能力直接影响石油炼制工作。
在本文中,我们讨论了石油炼制装置的防治措施。
关键词:石油炼制;设备;腐蚀;防治措施前言:近年来,高硫原油被中国大规模炼化,设备腐蚀问题明显,造成严重经济损失也让企业难以进一步发展。
石油炼制装置的腐蚀种类和程度与原油的种类和含量密切相关。
市场上对石油需求的增加,以及部分油田走上衰败。
随着原油质量的恶化,炼油厂采取经济有效的对策成为重要的课题。
一、设备腐蚀的原因1.腐蚀的定义广义上,腐蚀的定义可以解释为材料被环境中的某些物质所影响,产生一些化学反应,破坏了该材料的性质。
在狭义上,腐蚀的定义可以解释为被破坏金属性质的金属材料接触了周围的环境中一些物质,其二者产生化学反应或物理溶解。
最直接和最简单的理解是,材料的性质和功能在一些物质的影响下受到损伤,材料原有功能的损伤是由于腐蚀造成的。
2.设备腐蚀的主要原因在石油提炼和制造过程中,产生大量二氧化硫、硫化氢、硫化物等有害化学物质。
这些有害化学物质在特定条件下相互反应,是一些物质也会与设备的材料发生反应,导致设备的腐蚀。
二、石油炼制设备腐蚀的类型1.冲刷腐蚀侵蚀本身可以使FES膜被破坏,由于腐蚀介质的作用,金属总是不断的被清洗。
更多的新鲜金属表面由于冲刷不断的暴露,不断增加腐蚀介质与金属表面接触机会,加剧腐蚀。
2.应力腐蚀应力腐蚀是金属被固定拉应力和特定介质一起作用而引起的裂纹。
当金属或合金中发生应力腐蚀时,大部分表面不会腐蚀,局部出现从表面到内部的微小裂纹。
加工高氯原油对炼油设备的腐蚀与防护

2 0 1 3年 5月下旬 以来 , 由于 胜利 管 输原 油有
原油 正 常 情 况 下 有 机 氯 质 量 浓 度 小 于 2 . 0
机氯含量大幅升高 , 造成炼油企业部分装置 降量
或 停工 , 加 大 了全 厂 油品加 工的调度 难度 , 影 响生
●
、 _ 一
^ 、
化铵) 堵塞 、 腐蚀 泄 漏 等 , 尤 其 是 氯 化 物对 不 锈 钢
材 质 的设备 易造 成应 力开 裂 。 目前 暂未 找到 更有 效 的脱 氯办 法 , 而 且 高含 有 机 氯 原 油加 工 对 生 产 和设备 的潜 在影 响仍 将延 续 。
琶
暑
=、
●
F i g . 2 Di s t r i b u t i o n f o r t h e d i s t i l l a t e s o f o r g a n o e h l o r i n e i n c r u d e o i l
总氯; —— 初馏~ 2 0 4  ̄ C ; 一
时间 月一 日)
图 2 原 油 有 机 氯 的 馏 分 分 布
1 高 含氯原 油特 点及 对生 产影 响 1 . 1 高 含氯 原油 分布 特点 2 0 1 3年 5月 下 旬 开 始 , 山东 、 华北、 沿江 l 0 家 炼油 企业 先后 发现 胜利 管输 原油 有机 氯含 量大 幅升高 , 质量 浓度 经 常大 于 1 0 mg / L ( 见图 1 ) 。
产任务的完成 , 而且高氯原油的加工对设备腐蚀
成 为影 响装 置长 周期 运行 潜在 安全 隐患 。受 加工 高氯原 油影 响 的主要 装置 为 常减压 、 催化 裂化 、 焦 化 装置 分馏 塔顶 以及 催 化 重 整 、 加 氢 装 置反 应 器 后 换热 器 和 空 冷 系 统 , 主要 问题 表 现 为 结 盐 ( 氯
采油厂原油有机氯管控措施
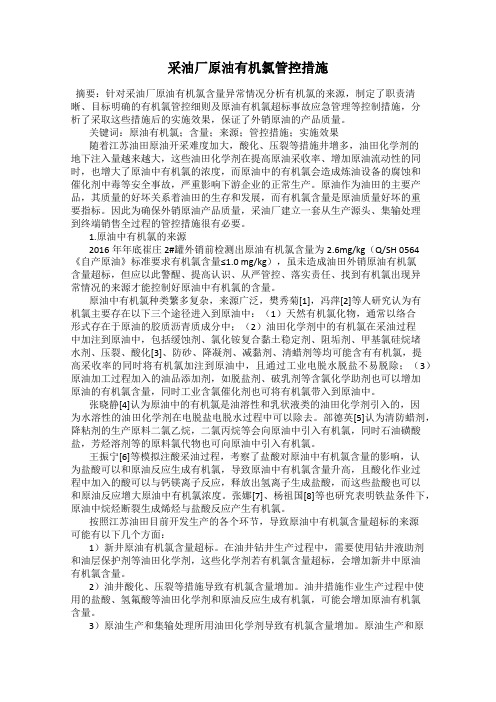
采油厂原油有机氯管控措施摘要:针对采油厂原油有机氯含量异常情况分析有机氯的来源,制定了职责清晰、目标明确的有机氯管控细则及原油有机氯超标事故应急管理等控制措施,分析了采取这些措施后的实施效果,保证了外销原油的产品质量。
关键词:原油有机氯;含量;来源;管控措施;实施效果随着江苏油田原油开采难度加大,酸化、压裂等措施井增多,油田化学剂的地下注入量越来越大,这些油田化学剂在提高原油采收率、增加原油流动性的同时,也增大了原油中有机氯的浓度,而原油中的有机氯会造成炼油设备的腐蚀和催化剂中毒等安全事故,严重影响下游企业的正常生产。
原油作为油田的主要产品,其质量的好坏关系着油田的生存和发展,而有机氯含量是原油质量好坏的重要指标。
因此为确保外销原油产品质量,采油厂建立一套从生产源头、集输处理到终端销售全过程的管控措施很有必要。
1.原油中有机氯的来源2016年年底崔庄2#罐外销前检测出原油有机氯含量为2.6mg/kg(Q/SH 0564《自产原油》标准要求有机氯含量≤1.0 mg/kg),虽未造成油田外销原油有机氯含量超标,但应以此警醒、提高认识、从严管控、落实责任、找到有机氯出现异常情况的来源才能控制好原油中有机氯的含量。
原油中有机氯种类繁多复杂,来源广泛,樊秀菊[1],冯萍[2]等人研究认为有机氯主要存在以下三个途径进入到原油中:(1)天然有机氯化物,通常以络合形式存在于原油的胶质沥青质成分中;(2)油田化学剂中的有机氯在采油过程中加注到原油中,包括缓蚀剂、氯化铵复合黏土稳定剂、阻垢剂、甲基氯硅烷堵水剂、压裂、酸化[3]、防砂、降凝剂、减黏剂、清蜡剂等均可能含有有机氯,提高采收率的同时将有机氯加注到原油中,且通过工业电脱水脱盐不易脱除;(3)原油加工过程加入的油品添加剂,如脱盐剂、破乳剂等含氯化学助剂也可以增加原油的有机氯含量,同时工业含氯催化剂也可将有机氯带入到原油中。
张晓静[4]认为原油中的有机氯是油溶性和乳状液类的油田化学剂引入的,因为水溶性的油田化学剂在电脱盐电脱水过程中可以除去。
油区防控治理原油有机氯(氧)污染探析

油区防控治理原油有机氯(氧)污染探析原油是一种重要的能源资源,但其开采、储运、加工过程中往往会产生有机氯(氧)污染物。
这些有机氯(氧)污染物对环境和人类健康造成了严重的威胁,因此对油区防控治理原油有机氯(氧)污染具有重要意义。
本文将从污染源、污染特性、防控技术等方面对原油有机氯(氧)污染进行探析。
一、污染源原油有机氯(氧)污染主要来自于原油开采、储运和加工过程。
在开采阶段,水力压裂、注水采油等作业会使得含氯、含氧有机物与地下水混合形成污染物质。
在储运阶段,由于管道腐蚀、泄漏等原因,也容易导致有机氯(氧)污染物的释放。
在加工过程中,原油中的含氯(氧)化合物在炼油过程中会被进一步转化成有机氯(氧)污染物,比如二硫化碳、有机氯乙烷等。
以上这些环节都是造成原油有机氯(氧)污染的主要源头。
二、污染特性原油中的有机氯(氧)污染物种类繁多,性质复杂,常见的有机氯(氧)污染物包括:二硫化碳、有机氯乙烷、苯并[a]芘等。
这些有机氯(氧)污染物具有高毒性、难降解、易挥发等特点。
其对环境的影响主要体现在土壤、地下水、大气等方面。
对土壤而言,有机氯(氧)污染物会降低土壤肥力,妨碍农作物生长;对地下水而言,有机氯(氧)污染物会使地下水污染,威胁地下水资源供应;对大气而言,有机氯(氧)污染物会引起空气污染,对人体健康造成威胁。
三、防控技术面对原油有机氯(氧)污染,需要采取一系列的防控技术,包括预防治理技术、污染控制技术和修复技术。
1. 预防治理技术预防治理技术主要包括源头控制、工艺优化等措施。
在开采阶段,可采用环境友好型开采技术,减少有机氯(氧)污染物的产生;在储运阶段,可加强管道设施的维护,减少泄漏事件的发生;在加工过程中,可优化炼油工艺,减少有机氯(氧)污染物的排放。
2. 污染控制技术污染控制技术主要包括吸附、氧化、光解等方法。
对于有机氯(氧)污染物的处理,可采用活性炭吸附、高温氧化等手段进行处理,减少其对环境的影响。
关于原油加工过程中防治氯化物腐蚀的建议

关于原油加工过程中防治氯化物腐蚀的建议生产运行处屈清洲摘要:介绍了原油中有机氯的来源及加工过程中的危害性,中石化主要炼厂氯腐蚀典型案例,针对我公司现状提出防治氯腐蚀的建议。
关键词:有机氯腐蚀蒸馏加氢裂化案例1 前言原油加工过程中,氯化物的存在具有巨大的危害性,特别近几年中石化发生多起因氯化物腐蚀造成事故,氯化物腐蚀已由常减压装置扩展到二次加工装置,威胁着炼油厂的安全生产。
在国外,日趋严重的氯化物腐蚀问题,促使国际腐蚀协会(NACE)属下的STG34(石油炼制与气体加工特别技术组)在2001年专门成立TG274工作组,负责行业调查和研究,并针对原油中无法经电脱盐脱除的氯化物产生的腐蚀与结垢问题开展工作。
2 有机氯来源原油中的氯化钠、氯化钙和氯化镁等无机氯大部分可以通过电脱盐脱除,一般要求脱后原油盐含量小于3mgNaCl/L,而有机氯不能够从电脱盐去除。
原油中的有机氯来源于采油过程中加入的含氯油田化学助剂。
在含蜡或沥青质原油的开采过程中,为防止油井内的蜡、沥青质沉积堵塞油井,降低产量,常常使用三氯乙烷等氯代烷烃清蜡剂来清洗油井,此外处于第三次采油期的油田不得不采取一系列的化学手段进行地下压裂、酸化、防砂、堵水、解堵、热采来提高产量,其中使用带氯的化学助剂有甲基氯硅烷堵水剂、硫化亚铜缓蚀剂等,随着原油一起进入到下游的加工装置。
原油中有机氯和少量无机氯经过加热炉加热后,能在常压塔顶分解成强酸性物质而造成塔顶冷凝系统的腐蚀,同时馏分油中要携带氯离子进入下游二次加工装置。
3 氯离子含量控制标准中石化《炼油生产装置工艺防腐蚀管理规定》规定了蒸馏塔顶挥发线“三注”后塔顶冷凝水应达到的技术控制指标:表1 蒸馏塔顶冷凝水控制指标“三注”后排水的pH值、铁离子含量、氯离子含量的分析频率为每周至少3次,应保持各项指标的合格率在90%以上,并有真实完整、随时可查的数据记录。
此外,针对二次加工装置该规定第二十一条“如将减压蜡油做加氢裂化装置的原料时,应重点监测蜡油中铁离子和氯离子的含量,分析频率每周至少1次。
氯化物对炼油加工过程的危害与防治措施探讨
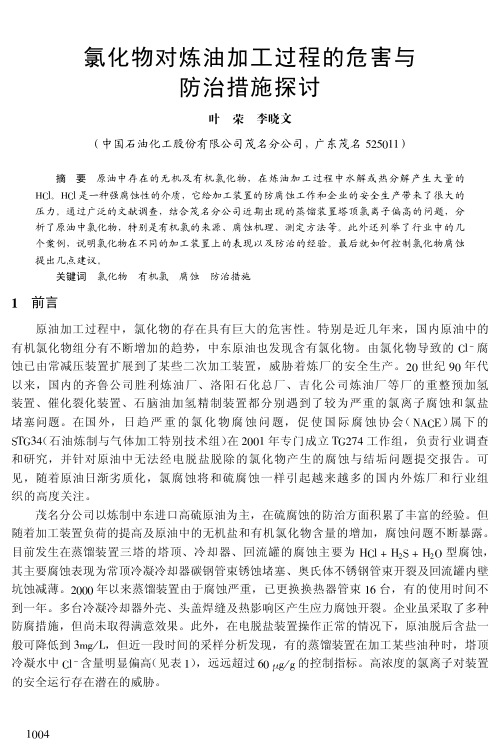
! 行业案例及防治经验
表 ! 列举了一些行业上报道的氯腐蚀事故及采取的防治措施,借以说明氯腐蚀在炼制过 程中的表现。
表"
地点 (炼厂) 时间 & 年ቤተ መጻሕፍቲ ባይዱ装置
氯腐蚀事故及防治措施
腐蚀表现及影响 常 压塔 0 台 一 级 换热 器 先后 出 现 突 然 泄 漏, 多 次 重复维修和更换管束 反应器出口串联一台脱氯 ( 台 , 型管换热器内漏, 罐,采取高温部位脱氯,先 管束 铵 盐 结 垢 严 重, 装 置 后使用 1# 5 ! 和 62 5 0.7 型 被迫多次停车检修 脱氯剂,氯腐蚀得到控制 催化 裂化 分 馏 塔 结 盐 使 塔 操作 失 常。被 迫 采 用 水 洗 的方 法,影 响 了 装 置 的 正 常生产和产品质量 反 应器 出 口 线 排 凝 管 穿 提高脱盐效率;催化裂化 进料再次电脱盐、脱钙,改 善进料性质 防治措施
[5] 物,聚合季铵类氯化物等) 。
& 氯化物分布的研究现状
[$] 没有发现系统研究各种原油氯化物分布规律的报道。洛阳石化工程公司炼制研究所
’>>> 年曾对某油田各厂的原油油样和其大于 $(() 馏分、小于 $(() 馏分进行了氯化物含量 分析。同时,对混合管输原油在实沸点蒸馏装置上进行了详细的窄馏分蒸馏切割,对各窄馏
压蒸馏 D 减压蒸馏 D 延迟焦化工艺过程中含氯化合物的分布情况。 根据前人的研究结果和行业案例报道,炼油过程中的氯化物分布有以下几点表现: ’)不同的原油分析得到的氯化物分布情况可能不尽相同,因为原油中所含的有机氯、 ’((0
浅谈含硫原油的腐蚀及保护措施
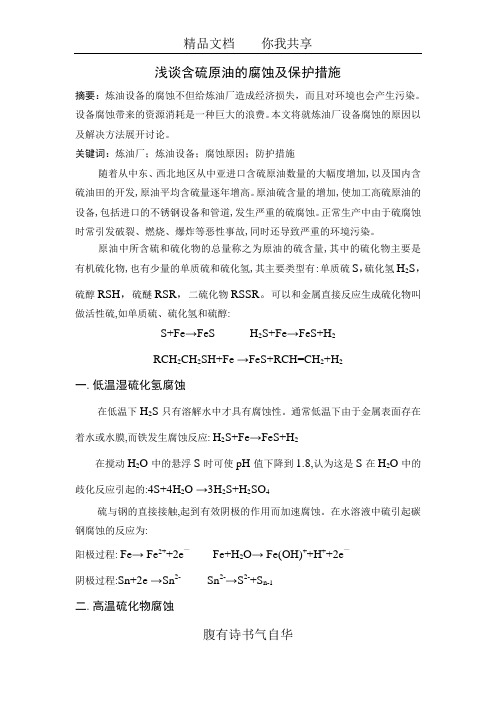
浅谈含硫原油的腐蚀及保护措施摘要:炼油设备的腐蚀不但给炼油厂造成经济损失,而且对环境也会产生污染。
设备腐蚀带来的资源消耗是一种巨大的浪费。
本文将就炼油厂设备腐蚀的原因以及解决方法展开讨论。
关键词:炼油厂;炼油设备;腐蚀原因;防护措施随着从中东、西北地区从中亚进口含硫原油数量的大幅度增加,以及国内含硫油田的开发,原油平均含硫量逐年增高。
原油硫含量的增加,使加工高硫原油的设备,包括进口的不锈钢设备和管道,发生严重的硫腐蚀。
正常生产中由于硫腐蚀时常引发破裂、燃烧、爆炸等恶性事故,同时还导致严重的环境污染。
原油中所含硫和硫化物的总量称之为原油的硫含量,其中的硫化物主要是有机硫化物,也有少量的单质硫和硫化氢,其主要类型有:单质硫S,硫化氢H2S,硫醇RSH,硫醚RSR,二硫化物RSSR。
可以和金属直接反应生成硫化物叫做活性硫,如单质硫、硫化氢和硫醇:S+Fe→FeS H2S+Fe→FeS+H2RCH2CH2SH+Fe →FeS+RCH=CH2+H2一.低温湿硫化氢腐蚀在低温下H2S只有溶解水中才具有腐蚀性。
通常低温下由于金属表面存在着水或水膜,而铁发生腐蚀反应: H2S+Fe→FeS+H2在搅动H2O中的悬浮S时可使pH值下降到1.8,认为这是S在H2O中的歧化反应引起的:4S+4H2O →3H2S+H2SO4硫与钢的直接接触,起到有效阴极的作用而加速腐蚀。
在水溶液中硫引起碳钢腐蚀的反应为:阳极过程: Fe→ Fe2++2e—Fe+H2O→ Fe(OH)++H++2e—阴极过程:Sn+2e →Sn2- Sn2-→S2-+S n-1二.高温硫化物腐蚀腹有诗书气自华高温下硫和硫化氢能直接与金属发生反应,生成金属的硫化物,其主要腐蚀反应过程为:S+Fe→FeS H2S+Fe→FeS+H2高温下H2S可发生分解,产生的元素硫具有很高的活性,与Fe发生反应极为强烈:H2S →H2+S S+Fe→ FeS原油中含的部分硫醇,在200℃以上也可以与铁直接发生反应产生硫化铁腐蚀产物:RCH2CH2SH+Fe→RCH2CH3+FeS+H2连多硫酸的形成及其腐蚀过程,如在催化裂化装置烟气管道中,高温部位(400~600℃)又有SO2和CO存在时:SO2+2CO →2CO2+S S+Fe→ FeS2SO2+O2→2SO3 SO3+H2O →H2SO4FeS+H2SO4→FeSO4+H2S H2S+H2SO4→4H2SxO6+S反应过程使在运行中形成的FeS膜破坏,腐蚀反应过程中形成的S和H2S又可参与金属的腐蚀过程,所以对材料的腐蚀具有自催化作用,过程中形成的亚硫酸,应力腐蚀开裂有诱发作用。
关于石油炼制设备腐蚀的防治措施

关于石油炼制设备腐蚀的防治措施发布时间:2021-06-25T05:58:11.668Z 来源:《防护工程》2021年6期作者:王勇[导读] 开发和炼制石油的主要目的是满足我国经济建设发展的实际需要,促进国家工业化建设进程。
在实际炼制过程中,因为多种因素的共同作用,设备容易受到腐蚀,不利于石油炼制工作的安全顺利开展。
王勇中石化股份有限公司天津分公司炼油部联合三车间天津 300270摘要:开发和炼制石油的主要目的是满足我国经济建设发展的实际需要,促进国家工业化建设进程。
在实际炼制过程中,因为多种因素的共同作用,设备容易受到腐蚀,不利于石油炼制工作的安全顺利开展。
关键词:石油炼制;设备;腐蚀;防治措施引言中国作为石油化工大国,也是成品油消耗大国,石油化工行业是人们生活以及工业生产的重要方面,石油化工产业链是否可以满足人们的需要是一个至关重要的问题。
石油不像其他必需品,它从开采到生产粗精加工是有一定难度的,所以对石油行业所需要的石油化工设备也有很高的要求。
是否能够利用好石油化工设备,并且在实际工作中能否更好地对化工设备进行防腐维护和管理,决定了石油行业尤其是精加工的质量与效率。
因此,找到一个好的防腐措施或方法去保护石油化工设备,对该产业的可持续发展具有重大意义。
1?腐蚀类型1.1?缝隙腐蚀缝隙腐蚀的发生位置主要在管板和管束之间,随着设备使用周期的延长,缝隙会随着加大加深,最终导致设备因为腐蚀严重无法正常运行。
正常情况下,炼油设备的缝隙本身不会出现腐蚀现象,但在进行石油炼制操作的时候,其石油中所含的阴离子会游走在缝隙之中,如果此时缝隙内部刚好有阳离子附着,则当温度达到一定条件后,阴阳离子就会发生化学反应,产生质变,腐蚀设备内壁,并且会产生穿透作用,不利于设备的正产使用。
1.2?冲刷腐蚀进行石油炼制的过程中,因为原油及其产物自身具有流动性,会对炼油设备起到冲刷作用,降低设备自身属性和厚度,形成冲刷腐蚀。
1.3?氢腐蚀石油炼制的过程中,油气中往往会有硫化氢以及水分的存在,硫化氢和水分会发生分解反应,产生出氢硫酸,氢硫酸与油气设备内壁的铁又会反应生成氢气,导致管壁内出现细小的裂纹,发生氢脆现象,这都直接对油气设备内壁造成了不同程度的腐蚀。
原油中氯的来源分析与防治对策

原油中氯的来源分析与防治对策随着油田勘探开发的发展,近年来,以注水开发为主、多种采油集输技术的应用和深度开采,原油及注水中的成分越来越复杂,导致炼化原油中的氯含量不断上升。
本文针对原油中氯化物的来源、分布及危害进行评价和分析,并对氯化物的脱除提出合理的控制措施。
标签:原油;无机氯;有机氯;腐蚀;对策1 前言近年来,随着原油开采深度的增加,原油重质、劣质化日趋严重,原油中的氯化物含量也呈不断增大的趋势。
生产实践证明氯化物能够造成设备的腐蚀及催化剂中毒,原油中存在的氯化物已不仅仅威胁常减压装置的安全生产,甚至对原油的二次加工设备也产生了较大的危害,尤其近几年来最为明显,例如:减压塔顶腐蚀加剧,加氢改质装置高压空冷管束结盐严重,重整装置预加氢循环氢压缩机吸排气阀铵盐结晶堵塞阀片,苯抽提装置苯的酸洗比色间或出现不合格,烷基化装置碱洗塔T202顶出口馏出物管线腐蚀泄漏等等。
原油氯含量的增加,不仅给原油及污水的处理造成困难,而且对炼油装置的平稳操作、设备腐蚀、产品质量带来严重危害,对炼厂生产和设备运行造成很大的负面影响,严重威胁炼油设备的完整性和炼厂的安全、平稳、长周期运行。
越来越多的炼油厂都存在着处理原油蒸馏装置或轻质油加氢处理装置的腐蚀和结垢,追根究底为氯化物含量的突增,而这些突增的氯化物避过电脱盐并且难以检测,因此业内人士提出“不可萃取氯化物”、“不可脱盐的氯化物”来形容它们。
这也表明用常规的脱氯工艺措施已很难满足工业化生产装置防腐蚀的要求,因此脱除原油中氯化物的技术开发迫在眉睫,目前,原油中的氯含量也日益引起人们的重视。
为了控制原油中的氯化物含量,减少经济损失,必须对原油中的氯化物的来源及影响进行正确地评价,确定氯化物的组成及分布,并对氯化物的危害程度进行正确地评价,提出合理的控制措施。
2 原油中氯化物的来源及分布原油中的氯化物分为两种:一种是无机氯化物,另一种是有机氯化物。
2.1原油中无机氯化物的来源、分布2.1.1原油中无机氯化物的来源原油采出时含有一定的盐和水,大部分盐主要以NaCl、CaCl2和MgCl2等碱金属或碱土金属形式存在,并溶解于原油含有的微量水,或以乳状液、悬浮颗粒的状态存在,这些盐溶解在采出水中被称为相应的盐水,主要阳离子为钠、钙、镁,经过破乳脱盐,原油中的大部分无机盐可被电脱盐装置脱除,但是残存的少量无机盐,在一定条件下通过水解可产生腐蚀介质HCl。
石油炼制设备腐蚀的防治措施

石油炼制设备腐蚀的防治措施摘要:石油炼制设备是石油加工过程中最关键的组成部分之一。
然而,由于石油中含有大量的硫、氮、氯等腐蚀性物质,石油炼制设备容易受到腐蚀的影响。
腐蚀会导致设备的性能下降,甚至造成设备的损坏和停机,给石油炼制工业带来巨大的损失。
设备腐蚀不仅会影响设备的正常运行,还会导致设备损坏、生产事故,甚至可能威胁到人身安全。
因此,对石油炼制设备进行防腐措施是十分重要的。
关键词:石油炼制设备;腐蚀机理;防腐措施;1石油炼制设备腐蚀类型石油炼制设备的腐蚀类型主要包括腐蚀、磨损腐蚀、高温腐蚀、酸性腐蚀和微生物腐蚀等。
(1)腐蚀是石油炼制设备最常见的腐蚀类型之一。
腐蚀是指金属表面与介质中的化学物质发生反应,使金属表面产生物理或化学变化的过程。
石油中的硫、氮、氯等物质易与金属发生化学反应,形成金属盐,导致设备发生腐蚀。
腐蚀会使设备表面产生腐蚀坑、腐蚀层等,降低设备的强度和使用寿命。
(2)磨损腐蚀是石油炼制设备容易出现的腐蚀类型。
磨损腐蚀是指介质中的颗粒物或流体的冲击和摩擦作用下,引起金属表面局部的磨损和腐蚀。
石油中含有大量的杂质和颗粒物,这些杂质会在设备内部引起磨损腐蚀。
磨损腐蚀会导致设备表面磨损、凹陷、开裂等,降低设备的密封性和耐久性。
(3)高温腐蚀是石油炼制设备在高温环境下容易受到的腐蚀类型。
高温下,金属与介质中的氧、硫、氯等物质发生反应,形成金属氧化物、硫化物、氯化物等,造成设备表面发生高温腐蚀。
高温腐蚀会使设备表面产生脱层、剥落等现象,降低设备的强度和耐腐蚀性能。
(4)酸性腐蚀也是石油炼制设备常见的腐蚀类型之一。
酸性腐蚀是指介质中的酸性物质对金属表面产生腐蚀作用。
石油中的硫酸、盐酸等酸性物质容易引起设备表面的酸性腐蚀。
酸性腐蚀会使设备表面产生腐蚀坑、腐蚀层等,降低设备的强度和使用寿命。
(5)微生物腐蚀也是石油炼制设备容易受到的腐蚀类型之一。
微生物腐蚀是指微生物在介质中生长繁殖,产生酸性物质和粘附物,导致金属表面产生腐蚀的现象。
含氯原油加工腐蚀与防护

含氯原油加工腐蚀与防护谈平庆【摘要】介绍了原油中氯的来源,分析了氯腐蚀的特点.根据某石化公司生产流程建腐蚀流模型,从原油进厂、储存、调合后进常减压、二次加工到产品出厂进行分析,经评估需重点对常减压蒸馏装置、重整装置、加氢装置、裂解装置进行关注并采取预防性措施:第一,对原油中氯含量进行监控,调合后的原油总氯质量分数控制在30 μg/g以下(参考值),对各装置原料总氯质量分数进行监测,建议分析频率1次/d;第二,通过适当工艺调整将NH4Cl结盐点控制在固定注水点之后;及时调整高压换热器和空冷前各注水点的注水量.并控制高分含硫污水NH4HS质量分数小于4%;第三,加强临时注水管理.注水的pH值控制在略偏碱性,使加氢含硫污水保持碱性(8~9为宜);第四,停工检修期间,对反应流出物系统的不锈钢管道焊缝做100%射线探伤检测,对不锈钢材质的低点排凝、引压管、热电偶接管等做渗透检,以保证装置的平稳运行.【期刊名称】《石油化工腐蚀与防护》【年(卷),期】2015(032)005【总页数】4页(P18-21)【关键词】氯;原油;腐蚀与防护【作者】谈平庆【作者单位】中国石油化工股份有限公司镇海炼化分公司,浙江宁波315207【正文语种】中文2013 年5 月底开始,胜利原油出现有机氯异常偏高的问题,对华北和沿江地区10 家炼油企业的安全生产造成严重影响,其中对加氢装置的冲击最为突出,带来结盐堵塞、设备腐蚀、产品含氯高等问题,已造成装置50 多次被迫停工。
某石化公司结合自身实际情况,制订加工含氯原油的预防措施。
1 原油中氯的来源原油中的有机氯化物主要有以下3 个来源[1]:(1)天然存在的有机氯化物;(2)来自采油过程中添加的化学助剂;(3)炼油过程使用的一些化学助剂也可能含有有机氯化物,如破乳剂、脱盐剂、输油管线及油罐清洗剂等,这些含氯助剂均有可能污染原油及二次加工的原料。
根据原油评价,该公司加工原油中以锡瑞原油、伊朗重油、索鲁士原油及贝莱纳克原油含氯较为明显。
原油加工中氯化物的检测及控制
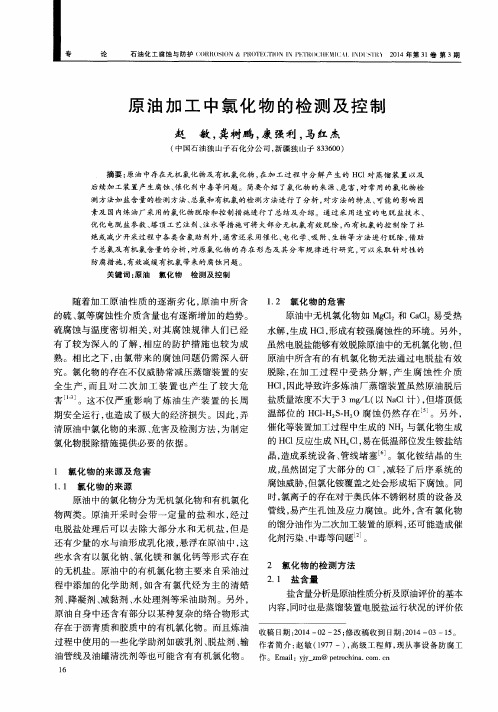
原油 中的氯化 物分 为无机 氯化 物和 有机 氯化
物 两类 。原油 开 采 时会 带 一 定 量 的盐 和水 , 经 过
电脱 盐处 理后 可 以去 除大 部 分水 和无 机 盐 , 但 是 还 有少量 的水 与油 形成 乳化 液 , 悬 浮在 原油 中 , 这 些 水含有 以氯化 钠 、 氯 化 镁 和氯 化 钙 等 形 式存 在 的无机盐 。原 油 中的有 机氯化 物 主要来 自采 油过
存 在 于沥青 质 和胶质 中 的有 机氯 化物 。而 且炼油
过 程 中使用 的一 些化 学助剂 如破 乳剂 、 脱盐 剂 、 输 作者 简介 : 赵敏( 1 9 7 7一) , 高级 工程 师 , 现从事设 备 防腐工
油 管线 及油 罐清洗 剂 等也 可能含 有有 机氯 化物 。 作 。E m a i l : y J y — z m@ p e t r o c h i n a . c o n r . c n
测 方法如 盐含量 的检测 方法、 总氯和有机氯的检 测方法进行 了分析 , 对方 法的特点 、 可能的影响 因 素及 国 内炼油厂采 用的氯化物脱 除和控制措施进行 了总结及介 绍。通过采 用适 宜的 电脱 盐技 术、 优化 电脱 盐参数 、 塔 顶工艺注剂、 注水等措施 可将 大部分无机 氯有效脱除 , 而有机氯 的控 制除 了杜 绝或减 少开采过程 中各类含氯助剂外 , 通常还采用催 化、 电化 学、 吸 附、 生物等 方法进行脱 除, 借助
专
论
石 油 化 工 腐蚀 与 防护 ( 【 ) R R O S 1 0N& P H O ( r I ( ) I N I ' E m( ) I I F MI C、 1 I N I ) l 。 I l { 、 2 0 1 4年 第 3 1 卷 第 3期
常减压蒸馏装置加工高氯原油腐蚀分析
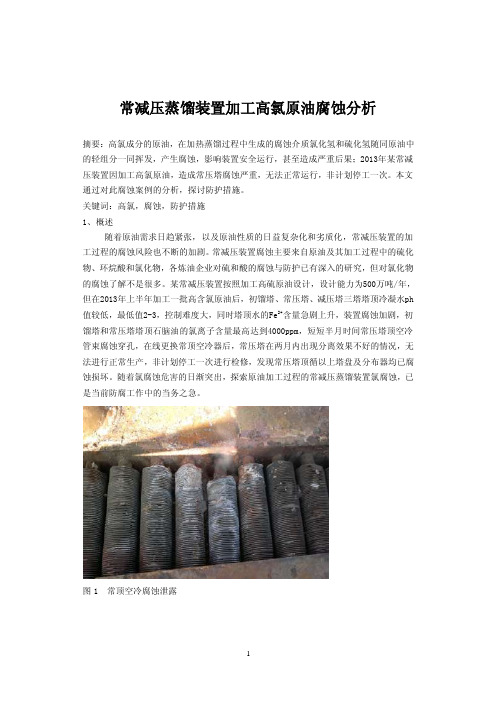
常减压蒸馏装置加工高氯原油腐蚀分析摘要:高氯成分的原油,在加热蒸馏过程中生成的腐蚀介质氯化氢和硫化氢随同原油中的轻组分一同挥发,产生腐蚀,影响装置安全运行,甚至造成严重后果;2013年某常减压装置因加工高氯原油,造成常压塔腐蚀严重,无法正常运行,非计划停工一次。
本文通过对此腐蚀案例的分析,探讨防护措施。
关键词:高氯,腐蚀,防护措施1、概述随着原油需求日趋紧张,以及原油性质的日益复杂化和劣质化,常减压装置的加工过程的腐蚀风险也不断的加剧。
常减压装置腐蚀主要来自原油及其加工过程中的硫化物、环烷酸和氯化物,各炼油企业对硫和酸的腐蚀与防护已有深入的研究,但对氯化物的腐蚀了解不是很多。
某常减压装置按照加工高硫原油设计,设计能力为500万吨/年,但在2013年上半年加工一批高含氯原油后,初馏塔、常压塔、减压塔三塔塔顶冷凝水ph 值较低,最低值2-3,控制难度大,同时塔顶水的Fe2+含量急剧上升,装置腐蚀加剧,初馏塔和常压塔塔顶石脑油的氯离子含量最高达到4000ppm,短短半月时间常压塔顶空冷管束腐蚀穿孔,在线更换常顶空冷器后,常压塔在两月内出现分离效果不好的情况,无法进行正常生产,非计划停工一次进行检修,发现常压塔顶循以上塔盘及分布器均已腐蚀损坏。
随着氯腐蚀危害的日渐突出,探索原油加工过程的常减压蒸馏装置氯腐蚀,已是当前防腐工作中的当务之急。
图1 常顶空冷腐蚀泄露图2 常顶循分布器腐蚀脱落2、氯的腐蚀机理原油中的氯的存在形式主要无机氯和有机氯。
无机氯是石油从地下采出时含有的盐,主要成分为氯化钠、氯化镁和氯化钙。
原油自身存在的有机氯化物或者在原油开采过程中加入的含氯的油田化学助剂,这部分有机氯无法通过电脱盐有效地去除,且在一定条件下会水解或热解产生腐蚀性介质氯化氢。
在原油加工过程中,氯化物受热分解可造成设备腐蚀,影响装置的安全运行,这种腐蚀作用都是通过HCL这一腐蚀介质来完成的。
常减压装置的塔顶低温腐蚀主要为HCl-H2S-H2O型腐蚀。
油区防控治理原油有机氯(氧)污染探析

油区防控治理原油有机氯(氧)污染探析原油是一种主要由碳氢化合物组成的矿藏资源,在开采、运输、储存和加工过程中,容易受到外界环境的污染。
有机氯和有机氧化物是常见的原油污染物,对环境和人体健康都具有一定的危害。
对原油中的有机氯(氧)污染进行防控治理具有重要意义。
有机氯是一类含有氯原子的有机化合物,在原油中主要包括氯代烃和氯酚类物质。
这些有机氯污染物具有很强的毒性和生物蓄积性,容易对水体和土壤造成污染。
在原油开采过程中,有机氯常常与原油一起抽出地下,并随着水一起分离出来。
这些有机氯污染物会通过各种渠道进入水体,对水生生物和人类健康造成威胁。
有机氧化物是一类富含氧原子的有机化合物,包括醇、醚、酮等。
这些有机氧化物在原油石窑和储存过程中会逐渐氧化生成,其中以醇和醚的形式较为常见。
有机氧化物对环境具有一定的毒性和腐蚀性,会对土壤、水体和空气造成污染。
有机氧化物也会对储存和加工设备造成腐蚀,引发事故。
针对原油中的有机氯(氧)污染问题,需要采取一系列措施进行防控治理。
需要对原油进行采样和检测,明确有机氯(氧)污染的程度和类型。
可以采用物理和化学方法对原油进行处理,去除有机氯(氧)污染物。
物理方法包括沉淀、过滤和吸附等,而化学方法可以利用氧化剂进行氧化分解。
还可以采用生物技术对有机氯(氧)污染物进行降解,主要通过微生物的作用来实现。
在原油的开采和运输过程中,需要加强环境保护和事故应急措施。
加强油田环境监测,及时发现和处理有机氯(氧)污染问题。
在原油运输过程中,要加强设备和管道的检修和维护,防止泄漏和事故的发生。
一旦发生有机氯(氧)污染事故,要立即采取应急措施,包括围堰、搭建临时隔离墙等,防止污染扩散。
对于原油储存和加工过程中的有机氯(氧)污染问题,也需要采取措施进行防控治理。
在储存过程中,要保持储罐的密封性,防止有机氯(氧)污染物挥发到大气中。
在加工过程中,要加强设备的防腐蚀和维护,减少有机氯(氧)污染物的生成。
原油有机氯对油田处理系统的危害及预防措施

原油有机氯对油田处理系统的危害及预防措施【摘要】原油中的氯化物一般认为有两种,即以氯代烃存在的有机氯化物和与碱金属或碱土金属离子形成的无机氯化物。
这两种形式存在的氯化物在原油加工过程中均可造成催化剂中毒和设备腐蚀。
无机氯化物可在原油脱盐脱水过程中随水而脱除。
但是有机氯化物采用常规方法不易脱除,脱盐后原油有机氯含量几乎不降低。
有机氯的存在会给油田处理系统尤其是炼化企业的安全生产造成很大的安全隐患,如何采取有效的预防措施来降低有机氯迫在眉睫。
【关键词】原油有机氯油田处理系统危害预防措施1 原油有机氯在油田处理系统的认识现状随着塔河油田原油开采深度的增加,酸压、裂化等措施井的增多,原油中的有机氯含量也呈不断增大趋势。
塔河油田对于原油有机氯的认识较晚,在2012年以前所处理的外输原油只要保证含水在标准范围之内,即可进行外输。
对于原油有机氯含量检测直到2012年2月才引起重视,局分公司连续下发三个文件要求尽快解决原油有机氯的超标问题。
2 原油有机氯的来源(1)天然存在的有机氯,在原油中有机氯化合物以某种复杂的络合物形式天然存在,主要浓缩在沥青质和胶质中;塔河油田高含胶质沥青质,部分油井胶质沥青质含量高达50%以上,高含胶质沥青导致原油有机氯偏高。
(2)来自采油过程中所添加的油田化学助剂,随着油藏开发时间的延长,油藏压力等参数的逐渐下降,胶质沥青质随之不断析出。
为解决胶质沥青质堵塞井筒的问题,采油厂引进了部分油田化学助剂,引进药剂未经有机氯检测环节直接投入油井导致原油有机氯含量大幅提高。
据塔石化检测结果表明,其中WD-06型高效溶胶分散剂有机氯含量高达570000μg/g,SY-601型清洗剂有机氯含量高达125355μg/g;塔河油田TH10403X单井原油有机氯含量为5182.45μg/g,TP115CH单井有机氯含量为41.79μg/g,S115-5X单井有机氯含量为12.61μg/g,这些单井的原油有机氯含量大大超过了原油有机氯含量标准。
原油氯化物来源及应对措施浅析
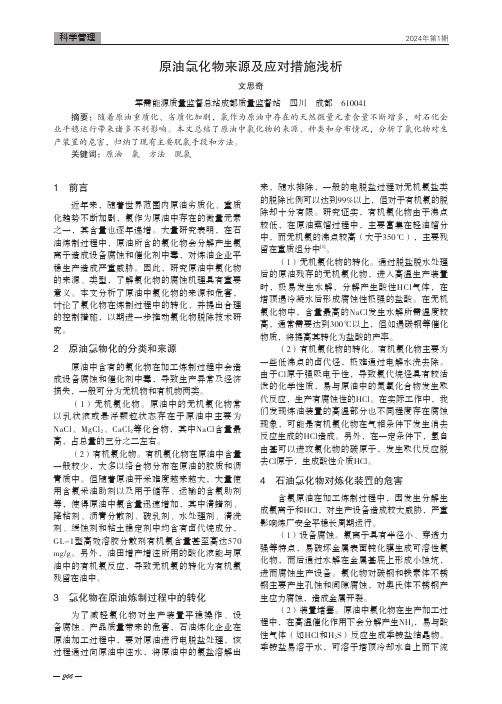
2441 前言近年来,随着世界范围内原油劣质化、重质化趋势不断加剧,氯作为原油中存在的微量元素之一,其含量也逐年递增。
大量研究表明,在石油炼制过程中,原油所含的氯化物会分解产生氯离子造成设备腐蚀和催化剂中毒,对炼油企业平稳生产造成严重威胁。
因此,研究原油中氯化物的来源、类型,了解氯化物的腐蚀机理具有重要意义。
本文分析了原油中氯化物的来源和危害,讨论了氯化物在炼制过程中的转化,并提出合理的控制措施,以期进一步推动氯化物脱除技术研究。
2 原油氯物化的分类和来源原油中含有的氯化物在加工炼制过程中会造成设备腐蚀和催化剂中毒,导致生产异常及经济损失,一般可分为无机物和有机物两类。
(1)无机氯化物。
原油中的无机氯化物常以乳状液或悬浮颗粒状态存在于原油中主要为NaCl、MgCl 2、CaCl 2等化合物,其中NaCl含量最高,占总量的三分之二左右。
(2)有机氯化物。
有机氯化物在原油中含量一般较少,大多以络合物分布在原油的胶质和沥青质中。
但随着原油开采难度越来越大,大量使用含氯采油助剂以及用于储存、运输的含氯助剂等,使得原油中氯含量迅速增加,其中清蜡剂、降粘剂、沥青分散剂、破乳剂、水处理剂、清洗剂、缓蚀剂和粘土稳定剂中均含有卤代烷成分,GL-1型高效溶胶分散剂有机氯含量甚至高达570 mg/g。
另外,油田增产增注所用的酸化液能与原油中的有机氯反应,导致无机氯的转化为有机氯残留在油中。
3 氯化物在原油炼制过程中的转化为了减轻氯化物对生产装置平稳操作、设备腐蚀、产品质量带来的危害,石油炼化企业在原油加工过程中,要对原油进行电脱盐处理,该过程通过向原油中注水,将原油中的氯盐溶解出来,随水排除,一般的电脱盐过程对无机氯盐类的脱除比例可以达到99%以上,但对于有机氯的脱除却十分有限。
研究证实,有机氯化物由于沸点较低,在原油蒸馏过程中,主要富集在轻油馏分中,而无机氯的沸点较高(大于350℃),主要残留在重质组分中[1]。
(1)无机氯化物的转化。
原油加工过程中氯化物腐蚀防治探讨

c l rd s i h n o n r d i e p c al h s fo g n c c l r d s h o i e n t e i c mi g c u e o l s e i l t o e o r a i h o i e .Co r s o c a i m fc l rd sa d t s t o s a e , y r o i n me h n s o h o i e n e t me h d r
维普资讯
20 0 6年 第 4期 第3 3卷 总 笫 1W WW dc e .om g hm c
原油 ̄ m, 中氯化物腐蚀 防治探讨 J 过程 n
叶 荣
( 中国石化股份茂名分公司 信息中心 , 广东 茂名 5 5 1 ) 2( 1 1
原油加工过程 中,氯化物 的存在具有 巨大的危 害性 。特别 是近几年来, 内原油中的有机氯化物组分有不断增加 的趋势, 国 中东原油也发现含 有氯化物 . 由氯化物导致 的 c l 己由常减 I 腐蚀
Hc +H:+H2 型腐 蚀 ,其主要腐蚀表现为常项冷凝冷却器 l s O
碳钢管束锈蚀堵塞 、奥 氏体不锈钢管束开裂及 回流簟 内壁坑蚀
b if e l wi . n l h a e u o wa d s v r l u g si n rt ec n r l f h o i ec r o i n re y d a t t Fi a l t e p p rp t r r e e a g e t s o h o to l r d o r s o . l h y f s o f o c Ke wo d : c u eo l c l rd  ̄ o g n cc l rd  ̄ c r o in c n r l y rs r d i: h o i e r a i h o i e o r so o t o
关于石油炼制设备腐蚀的防治措施

关于石油炼制设备腐蚀的防治措施发布时间:2021-11-22T01:28:03.769Z 来源:《工程管理前沿》2021年6月第18期作者:邢连栋[导读] 近年来,随着社会的发展,各行各业不断发展,石油已经成为我国工业发展中的主要能源,更是促进经济稳定发展的基础。
邢连栋中石化股份有限公司天津分公司天津 300270摘要:近年来,随着社会的发展,各行各业不断发展,石油已经成为我国工业发展中的主要能源,更是促进经济稳定发展的基础。
石油提炼过程是比较复杂的,其中的各种化工产品会腐蚀相关的设备。
因此,在新时期,需要对石油炼制设备腐蚀控制措施进行分析,然后结合其中的材料性能和防腐内容,完善控制和防护方案。
关键词:石油炼制;设备;腐蚀;防治措施引言石油炼制企业出现设备腐蚀问题的几率是比较高的,需要引起高度重视并加大解决对策。
若是设备出现腐蚀,会影响其使用年限和功能,甚至会造成人身伤亡,不利于企业发展。
因此,石油炼制企业要根据腐蚀产生的原因,采取有效的应对措施,并且还需要分析总结经验,采用先进的防腐技术,才能保证生产的安全运行,从而实现石油炼制企业的长远发展。
1石油炼制设备腐蚀的原因 1.1炼油装置腐蚀为了促进石油炼化企业在社会中的持续发展,对国内原油现状进行了分析,在原油加工中出现了比较明显的问题,这会导致原油腐蚀程度不断增加。
同时,国内的各大炼化企业原油一般包括大庆原油、吐哈原油和青海原油等产出的原油,但是相关企业并没有对各地区油品进行合理化应用,并且受到原油差异化腐蚀作用的影响,装置设备的实际腐蚀情况比较严重,如果不对其进行有效处理,就会加剧腐蚀程度。
1.2设备自身的原因一般来说,石油炼制设备材料会造成腐蚀问题的产生,尤其是金属设备更容易出现腐蚀。
石油炼制设备材料主要是金属材质的,同时不同金属材质产生腐蚀的情况也不一样。
然而在实际生产中,我国大部分石油炼制企业为追求经济效益,往往采购便宜的材料,这些材料晶粒直径较大,没有抗腐蚀性。
原油有机氯对油田处理系统的危害及预防措施

原油有机氯对油田处理系统的危害及预防措施【摘要】原油中的氯化物一般认为有两种,即以氯代烃存在的有机氯化物和与碱金属或碱土金属离子形成的无机氯化物。
这两种形式存在的氯化物在原油加工过程中均可造成催化剂中毒和设备腐蚀。
无机氯化物可在原油脱盐脱水过程中随水而脱除。
但是有机氯化物采用常规方法不易脱除,脱盐后原油有机氯含量几乎不降低。
有机氯的存在会给油田处理系统尤其是炼化企业的安全生产造成很大的安全隐患,如何采取有效的预防措施来降低有机氯迫在眉睫。
【关键词】原油有机氯油田处理系统危害预防措施1 原油有机氯在油田处理系统的认识现状随着塔河油田原油开采深度的增加,酸压、裂化等措施井的增多,原油中的有机氯含量也呈不断增大趋势。
塔河油田对于原油有机氯的认识较晚,在2012年以前所处理的外输原油只要保证含水在标准范围之内,即可进行外输。
对于原油有机氯含量检测直到2012年2月才引起重视,局分公司连续下发三个文件要求尽快解决原油有机氯的超标问题。
2 原油有机氯的来源(1)天然存在的有机氯,在原油中有机氯化合物以某种复杂的络合物形式天然存在,主要浓缩在沥青质和胶质中;塔河油田高含胶质沥青质,部分油井胶质沥青质含量高达50%以上,高含胶质沥青导致原油有机氯偏高。
(2)来自采油过程中所添加的油田化学助剂,随着油藏开发时间的延长,油藏压力等参数的逐渐下降,胶质沥青质随之不断析出。
为解决胶质沥青质堵塞井筒的问题,采油厂引进了部分油田化学助剂,引进药剂未经有机氯检测环节直接投入油井导致原油有机氯含量大幅提高。
据塔石化检测结果表明,其中WD-06型高效溶胶分散剂有机氯含量高达570000μg/g,SY-601型清洗剂有机氯含量高达125355μg/g;塔河油田TH10403X单井原油有机氯含量为5182.45μg/g,TP115CH单井有机氯含量为41.79μg/g,S115-5X单井有机氯含量为12.61μg/g,这些单井的原油有机氯含量大大超过了原油有机氯含量标准。
- 1、下载文档前请自行甄别文档内容的完整性,平台不提供额外的编辑、内容补充、找答案等附加服务。
- 2、"仅部分预览"的文档,不可在线预览部分如存在完整性等问题,可反馈申请退款(可完整预览的文档不适用该条件!)。
- 3、如文档侵犯您的权益,请联系客服反馈,我们会尽快为您处理(人工客服工作时间:9:00-18:30)。
关于原油加工过程中防治氯化物腐蚀的建议
生产运行处屈清洲
摘要:介绍了原油中有机氯的来源及加工过程中的危害性,中石化主要炼厂氯腐蚀典型案例,针对我公司现状提出防治氯腐蚀的建议。
关键词:有机氯腐蚀蒸馏加氢裂化案例
1 前言
原油加工过程中,氯化物的存在具有巨大的危害性,特别近几年中石化发生多起因氯化物腐蚀造成事故,氯化物腐蚀已由常减压装置扩展到二次加工装置,威胁着炼油厂的安全生产。
在国外,日趋严重的氯化物腐蚀问题,促使国际腐蚀协会(NACE)属下的STG34(石油炼制与气体加工特别技术组)在2001年专门成立TG274工作组,负责行业调查和研究,并针对原油中无法经电脱盐脱除的氯化物产生的腐蚀与结垢问题开展工作。
2 有机氯来源
原油中的氯化钠、氯化钙和氯化镁等无机氯大部分可以通过电脱盐脱除,一般要求脱后原油盐含量小于3mgNaCl/L,而有机氯不能够从电脱盐去除。
原油中的有机氯来源于采油过程中加入的含氯油田化学助剂。
在含蜡或沥青质原油的开采过程中,为防止油井内的蜡、沥青质沉积堵塞油井,降低产量,常常使用三氯乙烷等氯代烷烃清蜡剂来清洗油井,此外处于第三次采油期的油田不得不采取一系列的化学手段进行地下压裂、酸化、防砂、堵水、解堵、热采来提高产量,其中使用带氯的化学助剂有甲基氯硅烷堵水剂、硫化亚铜缓蚀剂等,随着原油一起进入到下游的加工装置。
原油中有机氯和少量无机氯经过加热炉加热后,能在常压塔顶分解成强酸性物质而造成塔顶冷凝系统的腐蚀,同时馏分油中要携带氯离子进入下游二次加工装置。
3 氯离子含量控制标准
中石化《炼油生产装置工艺防腐蚀管理规定》规定了蒸馏塔顶挥发线“三注”后塔顶冷凝水应达到的技术控制指标:
表1 蒸馏塔顶冷凝水控制指标
“三注”后排水的pH值、铁离子含量、氯离子含量的分析频率为每周至少3次,应保持各项指标的合格率在90%以上,并有真实完整、随时可查的数据记录。
此外,针对二次加工装置该规定第二十一条“如将减压蜡油做加氢裂化装置的原料时,应重点监测蜡油中铁离子和氯离子的含量,分析频率每周至少1次。
加氢裂化装置应根据蜡油中铁离子和氯离子含量的变化,采取相应措施,确保生产周期”。
4 中石化主要炼厂氯腐蚀典型案例
4.1 镇海石化蒸馏装置氯腐蚀
镇海石化加工伊朗重油和索鲁士原油后塔顶腐蚀速率急剧上升,通常常压塔顶的腐蚀速率控制在0.2mm/a以下,当加工伊朗重油的比例增加时,腐蚀速率达到0.5mm/a。
造成腐蚀速率变大的原因主要是伊朗重油和索鲁士原油中含有较高含量的有机氯,炉内分解后在塔顶形成无机氯,从而造成腐蚀。
从抽出的I常常顶换热器管束外表面看,坑蚀遍布整根管束,严重部位的坑蚀达到1mm。
在采取措施方面,对伊朗重油、索鲁士、贝拉伊姆、拉塔姆原油在炼制时及时调整缓蚀剂、中和剂的注入量和注水量,另一方面在购置原油时,尽量不购或少购含氯高的原油,必要时要求原油供货方说明是否使用含氯脱蜡剂及有机氯的含量。
在2009年的原油采购计划中降低了对该类原油的采购量。
4.2 齐鲁石化加氢裂化氯腐蚀
齐鲁石化140万吨/年加氢裂化装置加工一部分第一常减压减二线和减三线油,该部分原料氯盐含量高,造成加氢裂化原料总体氯盐含量高,2007年至今氯盐含量平均为1.86mgNacl/l,超过加氢裂化原料氯盐含量1.0mgNacl/l的指标,约有70%以上的数据超标。
造成加氢裂化反应流出物蒸汽发生器E403腐蚀。
E403是由意大利生产的螺纹锁紧环式高压换热器,壳程设计压力2.5MPa,壳程设计温度200℃;管程设计压力18.63MPa,管程设计温度330℃。
2004年8月份
检修期间打开发现较多氯化铵盐结晶物,E403腐蚀泄漏,堵管24根,经分析泄漏的主要原因为氯化铵的应力腐蚀。
在正常生产期间,由于原料油的变化,E403处出现过多次氯化铵盐结晶的情况,对设备的安全运行造成严重影响。
其次,原料中的氯盐经高压反应后与反应生成物中的氨生成氯化铵,由于E403处操作温度为170℃~250℃,氯化铵盐在此结晶,堵塞换热器管和管道,从而引起热高分(D-403)与冷高分(D-405)之间压降升高,严重影响安全生产。
4.3扬子石化加氢裂化氯腐蚀
扬子石化100万吨/年中压加氢裂化装置采用石油化工科学研究院RIPP的RMC专利技术,设计以第二套常减压装置(加工中东高含硫原油为主)的减一线、减二线、减三线油为原料,装置设计指标为系统压力11.2MPa,原料油硫含量≯2.5%、氮含量≯1000ppm、Cl-≯1ppm。
由于高硫、高酸、重质等劣质原油加工比例增加,管输原油、进口原油性质差,加氢装置原料性质波动频繁,进装置氯离子平均4.34ppm,超出Cl-≯1ppm指标。
自2005年1月投用以来,高压空冷已经发生了13次泄漏,更换了18台空冷器管束,给装置带来了极大的安全隐患和
Cl 经济损失。
主要原因:⑴结晶铵盐露点腐蚀;⑵衬管尾部的湍流腐蚀;⑶ NH
4
盐垢下腐蚀。
5 建议
针对氯化物对炼油厂腐蚀日趋严重,结合我公司的现状,建议如下:
1、制定进罐原油有机氯上限,控制有机氯的来源,减轻加工过程中氯腐蚀
的压力。
2、开好电脱盐,优化操作工艺以及进行必要的技术改造,尽快启动一蒸馏
加工劣质原油电脱盐智能响应控制技术,做好评价和公司内普及;开发
针对二次加工进料的电脱盐工艺。
3、做好二次加工装置原料调和工作,严格控制二次加工装置原料氯离子含
量不超标。
4、尽快建立和完善无机氯、有机氯相关的实验室分析手段。
5、优化“一脱三注”操作,评估在目前原油品种日渐复杂、原油质量日渐
劣质化的情况下,原有的防腐工艺是否合适。
6、考虑提高设备的设计选材标准,选用抗HCl和氯离子腐蚀强的钢材,耐蚀合金,甚
至钛及钛合金,提高设备的应变能力。