模具高速切削加工工艺关键技术论文
模具高速切削关键技术研究进展
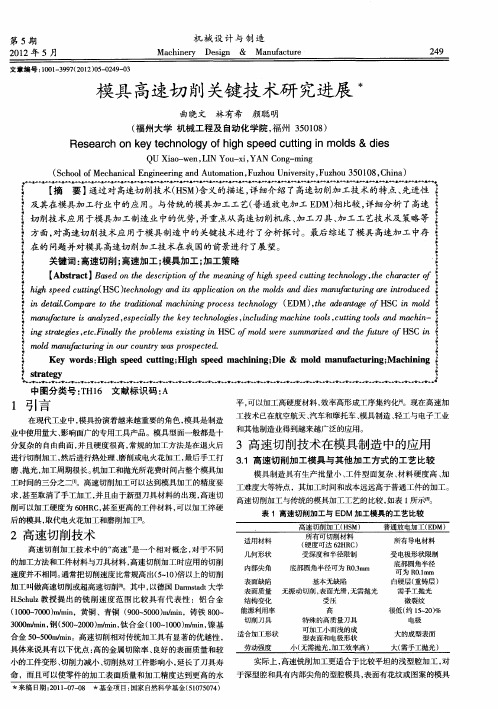
高速切 削加工与传统的模具加工工艺的比较, 如表 I 所示 。
表 1高速切削加工与 E M加工模具的工艺 比较 D
高速切 ̄J ] ( S I I IH M) ]] ]
适用材料 几何形状 ( )
2高速切削技术
高速切削加工技 术中的“ 高速” 是一个相对概念 , 对于不 同 的加工方法和工件材料与刀具材料 , 高速切削加工时应用 的切削
及其在模具加工行业中的应用。与传统的模具加工工艺( 普通放电加工 E M) D 相比较 , 详细分析 了高速 切 削技 术应 用于模 具加 工制造业 中的优 势 , 重点从 高速切 削机床 、 工 刀具 、 Y_ 艺技 术及 策略等 并 加 7 -Y  ̄- - --
方面 , 高速切 削技 术应 用于模具 制造 中的 关键技 术进行 了分析探讨 。最后 综述 了模具 高速加 工 中存 对
32 高速切 削在模具 工业 中的应用 _
高速切 削加工技术引进到模具. 业 ,主要应用于以下几个 [
方面 :
4高速切削加工模具 的关键技术
高速切削加工技术是在高速切削机床 、 搞性能 C C控制系 N () 1淬硬模具型腔的直接加工 利用高速切 削可加工硬材料 统 、 高性能刀柄 、 性能刀具材料及刀具设计制造技术 、 商 高效高精 的特点直接加_淬硬后 的模具型腔 , T 特别是浅腔 、 大曲率 的模具 度测试技术 、 高速切削加_ T理论 、 高速切削加1 工艺等诸多相关 二
3高速切削技术在模具制造 中的应用
进 行 切削 加 工 , 进 行热 处 理 、 削或 电火 花 加 工 , 手 工 打 31高速切  ̄ m -模 具与其他 加工方式 的工艺 比较 然后 磨 最后 . U r 磨、 抛光 , 加工周期很长 。 机加工和抛光所花费时间 占整个模具加 模具制造具有生产批量小 、 工件 型面复杂 、 材料硬度高 、 加
高速加工技术论文高速加工论文

高速加工技术论文高速加工论文高速加工技术在模具加工中的应用初探摘要:文章在概述高速加工的技术优势的基础上,探讨模具高速加工工艺技术与策略,并论述模具高速加工对加工系统的要求。
关键词:高速加工技术模具加工应用随着数控加工设备和高性能加工刀具技术的发展而日益成熟,模具加工的速度也大大提高,加工工序也随之减少,缩短甚至消除了耗时的钳工修复工作,从而大大的缩短了模具的生产周期。
高速加工技术在模具加工中的使用逐渐成为模具工业技术改造最主要的内容之一。
1 高速加工的技术优势与传统加工方式相比,在常规切削加工中备受困扰的一系列问题,通过高速切削加工的应用得到了解决。
高速加工时间短,产品精度高,可以获得十分光滑的加工表面,能有效地加工高硬度材料和淬硬钢,避免了电极的制造和费时的电加工 (EDM)时间,大幅度减少了钳工的打磨与抛光量。
同时,模具表面因电加工 (EDM)产生白硬层消失了,提高了模具的寿命,减少了返修。
因为电极的制造工作不需要了,所以模具改型只需通过CAD/CAM,使改型加快。
一些市场上越来越需要的薄壁模具工件,高速加工可又快又好地完成。
而且在高速铣削CNC加工中心上模具一次装夹可完成多工步加工。
大量生产实践表明,应用高速切削技术可节省模具后续加工中约80%的手工研磨时间,节约加工成本费用近30%,模具表面加工精度可达1μm,刀具切削效率可提高一倍。
2 模具高速加工工艺技术与策略2.1 粗加工时采用的加工策略模具粗加工的主要目标是追求单位时间内材料的去除率,并为半精加工准备工件的几何轮廓。
在切削过程中因切削层金属面积发生变化,导致刀具承受的载荷发生变化,使切削过程不稳定,刀具磨损速度不均匀,加工表面质量下降。
可通过以下措施保持切削条件恒定,从而获得良好的加工质量:(1)通过计算获得恒定的切削层面积和材料去除率,使切削载荷与刀具磨损速率保持均衡,以提高刀具寿命和加工质量。
(2)应避免刀具轨迹中走刀方向的突然变化,以免因局部过切而造成刀具或设备的损坏。
模具制造论文
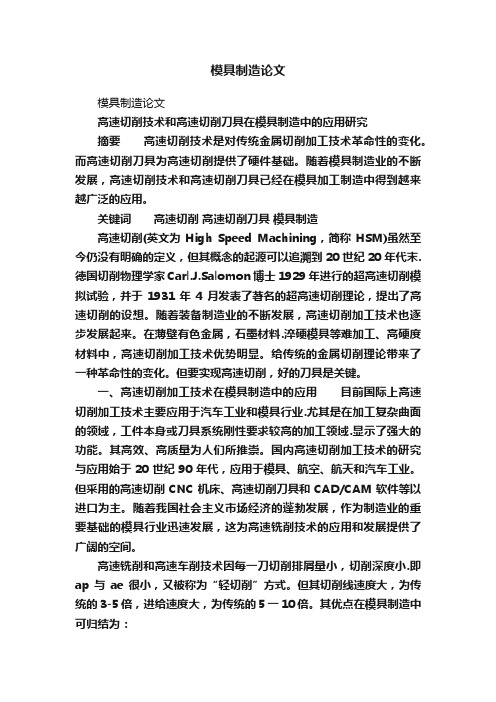
模具制造论文模具制造论文高速切削技术和高速切削刀具在模具制造中的应用研究摘要高速切削技术是对传统金属切削加工技术革命性的变化。
而高速切削刀具为高速切削提供了硬件基础。
随着模具制造业的不断发展,高速切削技术和高速切削刀具已经在模具加工制造中得到越来越广泛的应用。
关键词高速切削高速切削刀具模具制造高速切削(英文为High Speed Machining,简称HSM)虽然至今仍没有明确的定义,但其概念的起源可以追溯到20世纪20年代末.德国切削物理学家Carl.J.Salomon博士1929年进行的超高速切削模拟试验,并于1931年4月发表了著名的超高速切削理论,提出了高速切削的设想。
随着装备制造业的不断发展,高速切削加工技术也逐步发展起来。
在薄壁有色金属,石墨材料.淬硬模具等难加工、高硬度材料中,高速切削加工技术优势明显。
给传统的金属切削理论带来了一种革命性的变化。
但要实现高速切削,好的刀具是关键。
一、高速切削加工技术在模具制造中的应用目前国际上高速切削加工技术主要应用于汽车工业和模具行业.尤其是在加工复杂曲面的领域,工件本身或刀具系统刚性要求较高的加工领域.显示了强大的功能。
其高效、高质量为人们所推崇。
国内高速切削加工技术的研究与应用始于20世纪90年代,应用于模具、航空、航天和汽车工业。
但采用的高速切削CNC机床、高速切削刀具和CAD/CAM软件等以进口为主。
随着我国社会主义市场经济的蓬勃发展,作为制造业的重要基础的模具行业迅速发展,这为高速铣削技术的应用和发展提供了广阔的空间。
高速铣削和高速车削技术因每一刀切削排屑量小,切削深度小.即ap与ae很小,又被称为“轻切削”方式。
但其切削线速度大,为传统的3-5倍,进给速度大,为传统的5一10倍。
其优点在模具制造中可归结为:l、减少了加工环节,简化加工工序。
提高效率.延长模具使用寿命高速铣削加工技术加工时问短,产品精度高。
可以获得十分光滑的加工表面,避免了电极的制造和费时的电加工(EDM)时间,大幅度减少了钳工的打磨与抛光量。
高速切削加工技术论文

高速切削加工技术摘要:介绍高速切削加工的定义,高速切削加工中机床的选择,高速切削加工刀具材料的介绍及高速切削加工工艺的有关知识。
关键词:高速切削加工;高速切削刀具;高速切削工艺;高速切削技术是近十年来迅速崛起的一项先进制造技术。
由于高速切削技术具有切削效率高、加工质量高、能直接加工淬硬钢件和良好的经济性,使航空、模具、汽车、轻工和信息等行业的生产效率与制造质量显著提高,并引起加工工艺及装备相应的更新换代。
因此如同数控技术一样,高速切削和高速加工已成为21世纪机械制造业一场影响深远的技术革命。
目前,适应HSC要求的高速加工中心和其他高速数控机床在发达国家已呈普及趋势,我国近来也在加快发一、高速切削技术高速切削加工的特点是高效、高精度和低成本。
在当今社会已经成为机械制造领域的新秀和主要加工手段。
高速切削技术特征主要表现在如下方面:与传统加工相比,高速切削提高了切削速度,工件与前刀面的摩擦增大,切屑和刀具接触面温度急剧升高,很容易达到工件材料的熔点,使得工件变软甚至液化,大大减小了对切削刀具的阻力,使得切削变得中国金属加工在线版权所有轻快。
由于加工产生热量的70% ~80%都集中在切屑上,而高速切屑的去除速度很快,热量很难传导到工件上,从而提高了加工精度和质量、提高了生产效率。
因此,高速切削加工是一种在不增加设备数量的同时,大幅度提高加工效率的一种高科技。
论文发表,高速切削技术。
论文发表,高速切削技术。
二、高速切削刀具高速切削技术的关键是高速切削刀具,高速切削刀具是实现高速加工技术的关键。
高速切削的切削速度很快,加工线速度主要受刀具限制,在目前机床所能达到的高速范围内,速度越高,刀具的磨损越快。
因此,高速切削对刀具材料提出了更高的要求,除了具备普通刀具材料的一些基本性能之外,还应突出表现在高速切削刀具具备更高的耐热性、抗热冲击性、良好的高温力学性能及更高的可靠性。
高速切削技术的发展在很大程度上得益于超硬刀具材料的出现及发展。
毕业设计(论文)模具高速铣削加工技术与数控编程

1概述模具作为模压产品生产的关键工装,其设计与生产周期日益成为决定新产品开发周期的决定因素。
目前工业发达国家的航空航天、汽车、机械、模具、机床等行业首先得益于该项新技术,使上述行业的产品质量明显提高,成本大幅度降低,获得了市场竞争优势。
在汽车工业中,过去新车型的开发周期一般为10年,现在缩短为2~3年。
福特、通用、丰田等公司的新车型开发周期仅为1年半,这一切都得益于企业模具设计与制造手段的现代化水平的提高。
高速切削技术逐渐应用于加工铸铁和硬铝合金,尤其是加工大型覆盖件冲压模、锻模、压铸模和注射模,目的是在减少加工时间和研制时间的同时提高尺寸公差和表面一致性。
目前国际上高速切削加工技术主要应用于汽车工业、模具行业、航空航天行业,尤其是在加工复杂曲面的领域,工件本身或刀具系统刚性要求较高的加工领域,显示了强大的功能。
国内高速切削加工技术的研究与应用始于20世纪90年代,也是主要应用于模具、航空、航天和汽车工业,但采用的高速切削cnc机床、高速切削刀具和cad/cam软件等以进口为主。
2总体设计模具的设计包括:熟悉模具的概念、组成、分类与性能,掌握常用模具的牌号类别及性能特点;熟悉并掌握注射成型、压缩成型、压注成型、挤出成型原理及工艺;了解其它模具成型工艺设计的过程:设计任务.制定设计任务书提供方案进行评价按照选定的方案进行模具高速铣削加工分析和掌握数控编程工艺设计:根据总体设计的结果考虑结构工艺等条件按照要求绘制零件图。
整理设计文献和编写设计说明书模具设计是目标是要满足使用要求和经济要求,因此常常需要经过反复多次的修改才能达到满意的效果,设计过程的各个阶段是相互联系的。
影响模具的尺寸有很多因数,不能按照计算的尺寸来定模具的尺寸,要根据实际的情况来做适当的调整,以方便使用为原则。
要考虑结构加工和装配工艺,经济性和使用条件等要求。
理论计算只是为了确定提供一个方面的的依据,有些经验公式也只是考虑了主要因素的要求,所以求的是近似值。
高速切削技术在模具加工中的关键工艺分析

高速切削技术在模具加工中的关键工艺分析[摘要]随着经济和科学技术的不断发展,人们对产品的要求不仅仅停留在质量上,产品的外观和造型更是成为人们关注和在意的方面。
而传统的加工设备和制造方法已经难以适应人们多样化的需求,新的、高水平的技术手段引进到模具加工中是社会发展的一种必然趋势。
本文从高速切削技术入手,详细的描述其在模具加工中的关键工艺和优势、特点等。
[关键词]高速切削技术;模具加工;关键工艺中图分类号:tg76文献标识码:a文章编号:1009-914x(2013)21-0000-01社会的发展和需求通常是催生一项新的技术的最主要的动力,在经济发展的过程中,由于传统的加工技术不能满足人们对于产品的需求,为了适应这种市场需求,高速切削技术就应运而生。
它运用其先进的工艺提高了切削加工的效率和质量,是二十多年来制造业中发展速度超快的一种高新技术,是国际上最重要、效率最高的先进的制造技术之一。
一、高速切削技术的概述1、高速切削技术的概念由于加工方式的不同或者不同的切削材料对切削速度和加工参数的要求不同,到目前为止,有关高速切削的定义还未达成统一的共识。
但通常情况下,高速切削技术是指加工制造的过程中在保证加工精度和加工质量的前提下,采用质地超硬的刀、磨具并兼用一些自动化的高速切削设备对将要加工或制造的材料进行高速、高效的切除的一种加工技术。
高速切削技术是在机床结构及材料、高性能刀夹系统、高速切削机理、快进系统等多种系统或者技术的相关硬件与软件技术均得到充分发挥的基础之上综合而成的。
它的实施和操作是一项复杂的系统工程,在操作的过程中会涉及到很多不同的方面,但是也正是这诸多方面的考虑和综合使得高速切削技术的效率很高,运用好得到的质量很好。
2、高速切削技术的特点2.1 切削加工的精度高高速切削技术的高速旋转型是传统的技术和设备所不能比的,其在高速旋转的过程中,刀具会因其激励频率远离工艺系统的受迫振动而有一个良好的加工状态。
高速切削加工技术在模具制造中的应用简析
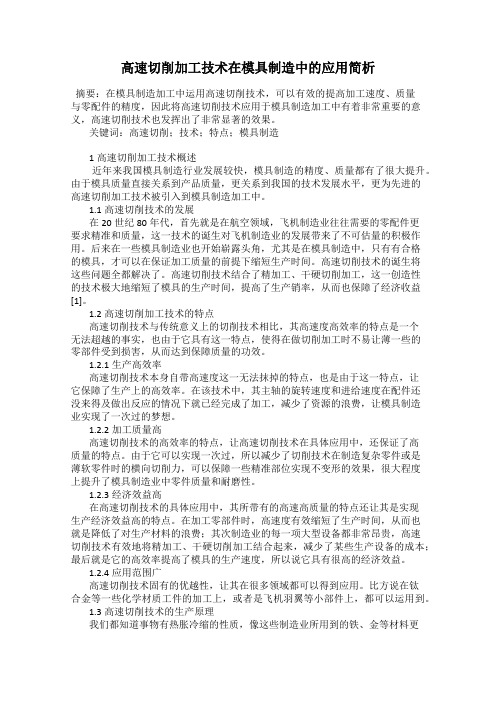
高速切削加工技术在模具制造中的应用简析摘要:在模具制造加工中运用高速切削技术,可以有效的提高加工速度、质量与零配件的精度,因此将高速切削技术应用于模具制造加工中有着非常重要的意义,高速切削技术也发挥出了非常显著的效果。
关键词:高速切削;技术;特点;模具制造1高速切削加工技术概述近年来我国模具制造行业发展较快,模具制造的精度、质量都有了很大提升。
由于模具质量直接关系到产品质量,更关系到我国的技术发展水平,更为先进的高速切削加工技术被引入到模具制造加工中。
1.1高速切削技术的发展在20世纪80年代,首先就是在航空领域,飞机制造业往往需要的零配件更要求精准和质量,这一技术的诞生对飞机制造业的发展带来了不可估量的积极作用。
后来在一些模具制造业也开始崭露头角,尤其是在模具制造中,只有有合格的模具,才可以在保证加工质量的前提下缩短生产时间。
高速切削技术的诞生将这些问题全都解决了。
高速切削技术结合了精加工、干硬切削加工,这一创造性的技术极大地缩短了模具的生产时间,提高了生产销率,从而也保障了经济收益[1]。
1.2高速切削加工技术的特点高速切削技术与传统意义上的切削技术相比,其高速度高效率的特点是一个无法超越的事实,也由于它具有这一特点,使得在做切削加工时不易让薄一些的零部件受到损害,从而达到保障质量的功效。
1.2.1生产高效率高速切削技术本身自带高速度这一无法抹掉的特点,也是由于这一特点,让它保障了生产上的高效率。
在该技术中,其主轴的旋转速度和进给速度在配件还没来得及做出反应的情况下就已经完成了加工,减少了资源的浪费,让模具制造业实现了一次过的梦想。
1.2.2加工质量高高速切削技术的高效率的特点,让高速切削技术在具体应用中,还保证了高质量的特点。
由于它可以实现一次过,所以减少了切削技术在制造复杂零件或是薄软零件时的横向切削力,可以保障一些精准部位实现不变形的效果,很大程度上提升了模具制造业中零件质量和耐磨性。
模具高速切削加工工艺的关键技术
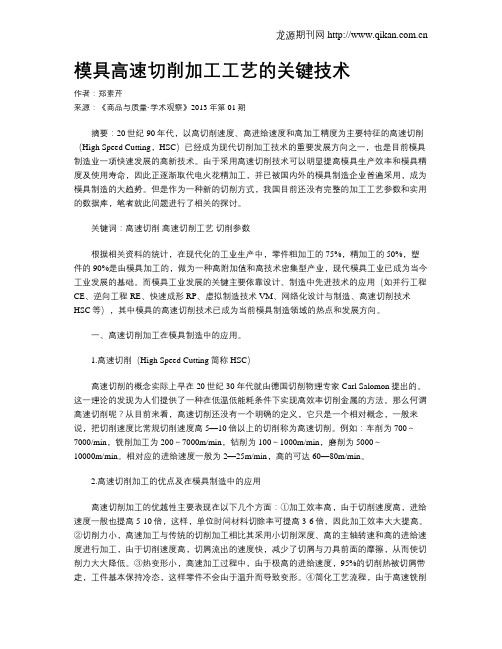
模具高速切削加工工艺的关键技术作者:郑素芹来源:《商品与质量·学术观察》2013年第01期摘要:20世纪90年代,以高切削速度、高进给速度和高加工精度为主要特征的高速切削(High Speed Cutting,HSC)已经成为现代切削加工技术的重要发展方向之一,也是目前模具制造业一项快速发展的高新技术。
由于采用高速切削技术可以明显提高模具生产效率和模具精度及使用寿命,因此正逐渐取代电火花精加工,并已被国内外的模具制造企业普遍采用,成为模具制造的大趋势。
但是作为一种新的切削方式,我国目前还没有完整的加工工艺参数和实用的数据库,笔者就此问题进行了相关的探讨。
关键词:高速切削高速切削工艺切削参数根据相关资料的统计,在现代化的工业生产中,零件粗加工的75%,精加工的50%,塑件的90%是由模具加工的,做为一种高附加值和高技术密集型产业,现代模具工业已成为当今工业发展的基础。
而模具工业发展的关键主要依靠设计、制造中先进技术的应用(如并行工程CE、逆向工程RE、快速成形RP、虚拟制造技术VM、网络化设计与制造、高速切削技术HSC等),其中模具的高速切削技术已成为当前模具制造领域的热点和发展方向。
一、高速切削加工在模具制造中的应用。
1.高速切削(High Speed Cutting 简称HSC)高速切削的概念实际上早在20世纪30年代就由德国切削物理专家Carl Salomon提出的。
这一理论的发现为人们提供了一种在低温低能耗条件下实现高效率切削金属的方法。
那么何谓高速切削呢?从目前来看,高速切削还没有一个明确的定义,它只是一个相对概念,一般来说,把切削速度比常规切削速度高5—10倍以上的切削称为高速切削。
例如:车削为700~7000/min,铣削加工为200~7000m/min,钻削为100~1000m/min,磨削为5000~10000m/min。
相对应的进给速度一般为2—25m/min,高的可达60—80m/min。
基于高速切削的模具加工技术

基于高速切削的模具加工技术摘要伴随装备制造业的发展和科技进步,我国的数控产业持续高位运行,产值逐年增长,特别是以五轴联动为代表的多轴数控加工设备与技术不仅已列为国家“十二五”重大科技攻关和推广项目,并日趋在企业生产中得到广泛应用。
文章结合当前形势对当前高速切削的模具加工技术进行了分析和研究。
关键词高速切削;加工工艺;模具加工模具是制造业中较为重要的工艺型装备,在当前的工业生产中占有相当重要的地位。
使用模具所生产具体成品都具有相当高的精度、高生产率、高一致性、高复杂程度的特点,这在所有的加工制造的方法是无法实现的。
模具的加工有着具体的特殊性比如精度高、工件比较精细等特点,与通常的机械加工是有着很大的差异的,由于模具得形状比较复杂,其工作的部分通常都属于多维的复杂曲面所构成;其所选用的材料一般情况下都是硬度比较高的,通常都是由硬质合金或淬火工具钢所特殊制成的;其制造的周期通常都比较短。
最为常见的模具的加工方法都属于电火花加工和普通切削加工,整个过程因为需要抛光、手工打磨,从而直接导致了加工的效率比较低下,而加工的精度上也是大打折扣。
如果选用了高速切削技术的加工模具,就能大大提高加工精度、生产效率、使用寿命等。
1 高速切削机床的选择实现高速切削的关键和前提,就是是否选择了性能良好的高速切削机床,具有高精度的高速主轴是高速切削机床技术的基础。
所以说选择可靠的机床,是实现高速切削加工的关键,在具体的工作中我们必须要结合实际情况,经过综合的考虑分析和详细了解了模具加工整个过程的具体要求和加工企业的具体经济环境等一系列因素。
才能选择出适合企业工作环境的高速切削加工模具的机床。
1.1 良好的工艺适应性所选择的机床功能一定要完全符合需要加工的模具的实际形状以及模具的尺寸精度以及生产过程中的一些具体要求。
1.2 高的性能价格比通常情况下,模具加工都是以高转速作为唯一特征的HSM型高速加工中心。
1.3 大功率和高主轴转速在涉及到模具型的腔曲面进行的高速加工过程中,选用刀具的直径相比都很小,而且机床主轴转速要求又是很高(通常都是80,000r/min~20,000 r/min之间);为了实现一次装夹就能顺利实现模具的精加工和粗加工,所以对主轴的功率要求都是很大。
模具高速切削加工工艺的关键技术
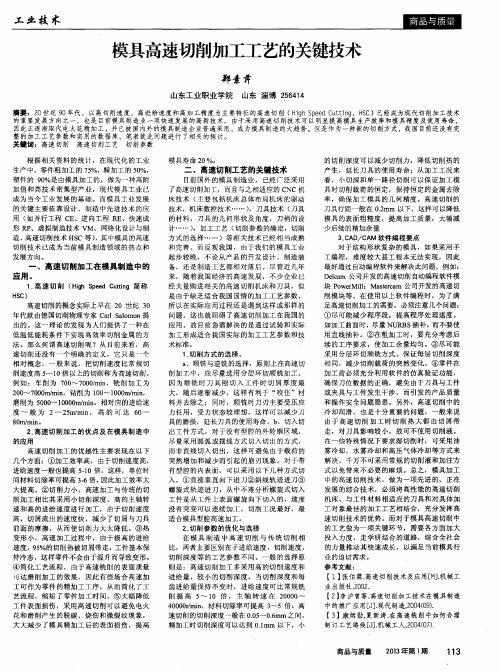
根据相 关资料 的统计 ,在现代化 的工业 生产中,零件粗加工 的 7 5 %,精加 工的 5 0 %, 塑件的 9 0 %是 由模具加 工的,做为一种 高附 加 值和 高技术 密集 型产业 ,现代模具 工业 已 成为 当今 工业发展 的基础 。而模具 工业发展 的关键主 要依靠设 计、制造 中先进技 术的应 用 ( 如 并 行 工 程 CE 、 逆 向工 程 R E、快 速 成 形R P、虚拟制造技术 VM、网络化设计与制 造 、高速切削技术 HS C等 ) ,其 中模具 的高速 切削技术 已成为 当前模具 制造领域 的热点和 发展方向 。
、
高速 切削加 工在模 具制造 中的
应 。
1 . 高速 切 削 ( H i g h S p e e d C u t t i n g 简称
HS C)
高速切削 的概念实 际上早在 2 O 世纪 3 0 年代就 由德国切削物理专家 C a r l S a l o mo n提 出的 。这 一理 论的发现为人 们提供 了一种在 低温低 能耗条件下 实现高 效率切削金 属的方 法 。那 么何谓 高速 切削昵 ?从 目前来 看 ,高 速切削 还没有一个 明确 的定义 ,它 只是一个 相对概 念,一般 来说 ,把 切削速度 比常规切 削速度 高 5 一l O倍 以上的切削称为 高速切 削。 例如 :车 削为 7 0 0 ~7 0 0 0 / mi n ,铣削 加工 为
模具高速加工技术与策略
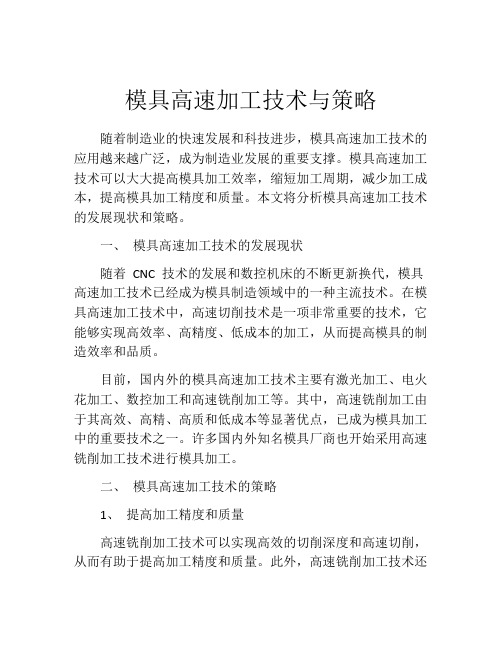
模具高速加工技术与策略随着制造业的快速发展和科技进步,模具高速加工技术的应用越来越广泛,成为制造业发展的重要支撑。
模具高速加工技术可以大大提高模具加工效率,缩短加工周期,减少加工成本,提高模具加工精度和质量。
本文将分析模具高速加工技术的发展现状和策略。
一、模具高速加工技术的发展现状随着CNC 技术的发展和数控机床的不断更新换代,模具高速加工技术已经成为模具制造领域中的一种主流技术。
在模具高速加工技术中,高速切削技术是一项非常重要的技术,它能够实现高效率、高精度、低成本的加工,从而提高模具的制造效率和品质。
目前,国内外的模具高速加工技术主要有激光加工、电火花加工、数控加工和高速铣削加工等。
其中,高速铣削加工由于其高效、高精、高质和低成本等显著优点,已成为模具加工中的重要技术之一。
许多国内外知名模具厂商也开始采用高速铣削加工技术进行模具加工。
二、模具高速加工技术的策略1、提高加工精度和质量高速铣削加工技术可以实现高效的切削深度和高速切削,从而有助于提高加工精度和质量。
此外,高速铣削加工技术还可以减少加工表面的残留应力,从而保证模具制品的稳定性和寿命。
2、提高生产效率和降低成本在高速铣削加工技术中,合理的刀具设计可以提高加工效率和降低成本。
此外,高速铣削加工技术还可以大大缩短加工周期和加工工艺,从而提高生产效率和降低成本。
3、采用先进的数控系统和刀具高速铣削加工技术的应用需要采用先进的数控系统和刀具,从而确保加工精度和质量。
此外,通过合理的刀具设计和选择,可以大大提高加工效率和降低成本。
4、加强人才培养和技术创新高速铣削加工技术需要专业的技术人才进行操作和调试。
因此,加强人才培养和技术创新是高速铣削加工技术应用的必要条件。
此外,也需要不断推陈出新,改进技术,以适应市场的需求。
三、结语随着制造业的发展和技术的不断更新换代,模具高速加工技术的应用越来越广泛,将成为未来制造业的重要发展方向。
我们应该通过加强人才培养、技术创新等方面来推动模具高速加工技术的发展,为推动制造业的发展做出贡献。
模具加工方法高速切削

模具加工方法高速切削1. 引言模具加工是制造行业中不可或缺的一部分,它在制造各种产品的过程中起着至关重要的作用。
随着科技和工艺的不断发展,高速切削已经成为模具加工中的一种重要方法。
本文将介绍模具加工中的高速切削方法,包括其原理、工具、技术要点和应用。
2. 高速切削的原理高速切削是指在高速旋转刀具的作用下,通过切削运动将材料去除的过程。
其原理主要包括以下几个方面:•切削力和切削温度增大:高速切削的切削速度较快,相应地,切削力也会增大。
同时,高速切削还会导致切削温度的增大,这是由于切削过程中的摩擦和热变形引起的。
•切削振动减小:高速切削时,切削力的增大并不会引起切削振动的增加,反而会减小。
这是因为高速切削时,刀具和工件之间的接触面积减小,摩擦力也随之减小,从而减小了切削振动。
•切削表面质量提高:高速切削由于切削速度快,可以减小切屑对刀具磨损的影响,从而提高切削表面的质量。
3. 高速切削的工具在高速切削中,选择合适的切削工具是非常重要的。
常见的高速切削工具有以下几种:3.1 钨钢刀具钨钢刀具是高速切削中最常用的切削工具之一。
它具有硬度高、刚性好、磨损小的特点,适用于加工硬度较高的材料。
3.2 多齿刀具多齿刀具是指具有多个切削齿的刀具,它可以提高切削效率和切削精度。
在高速切削中,多齿刀具由于其大体积和较高的切削速度,可以减小切削振动,提高加工效率。
3.3 超硬刀具超硬刀具是指采用超硬材料制成的刀具,常见的超硬材料有氮化硅和氮化硼等。
超硬刀具具有硬度极高、耐磨性好的特点,适用于加工硬度极高的材料。
4. 高速切削的技术要点在进行高速切削时,要注意以下几个技术要点:4.1 切削速度的选择选择合适的切削速度是高速切削的关键。
切削速度过低会导致切削效率低下,切削速度过高则会增加切削力和切削温度,甚至引起刀具损坏。
因此,要根据具体材料的硬度、刀具的材质和刀具结构等因素来选择合适的切削速度。
4.2 工艺参数的优化在高速切削过程中,还需要对工艺参数进行优化。
模具高速铣削加工实例分析及其关键技术系统
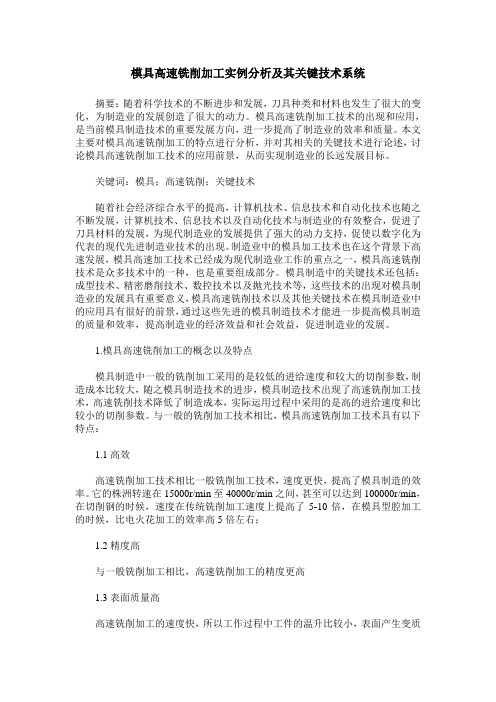
模具高速铣削加工实例分析及其关键技术系统摘要:随着科学技术的不断进步和发展,刀具种类和材料也发生了很大的变化,为制造业的发展创造了很大的动力。
模具高速铣削加工技术的出现和应用,是当前模具制造技术的重要发展方向,进一步提高了制造业的效率和质量。
本文主要对模具高速铣削加工的特点进行分析,并对其相关的关键技术进行论述,讨论模具高速铣削加工技术的应用前景,从而实现制造业的长远发展目标。
关键词:模具;高速铣削;关键技术随着社会经济综合水平的提高,计算机技术、信息技术和自动化技术也随之不断发展,计算机技术、信息技术以及自动化技术与制造业的有效整合,促进了刀具材料的发展,为现代制造业的发展提供了强大的动力支持,促使以数字化为代表的现代先进制造业技术的出现。
制造业中的模具加工技术也在这个背景下高速发展,模具高速加工技术已经成为现代制造业工作的重点之一,模具高速铣削技术是众多技术中的一种,也是重要组成部分。
模具制造中的关键技术还包括:成型技术、精密磨削技术、数控技术以及抛光技术等,这些技术的出现对模具制造业的发展具有重要意义,模具高速铣削技术以及其他关键技术在模具制造业中的应用具有很好的前景,通过这些先进的模具制造技术才能进一步提高模具制造的质量和效率,提高制造业的经济效益和社会效益,促进制造业的发展。
1.模具高速铣削加工的概念以及特点模具制造中一般的铣削加工采用的是较低的进给速度和较大的切削参数,制造成本比较大,随之模具制造技术的进步,模具制造技术出现了高速铣削加工技术,高速铣削技术降低了制造成本,实际运用过程中采用的是高的进给速度和比较小的切削参数。
与一般的铣削加工技术相比,模具高速铣削加工技术具有以下特点:1.1高效高速铣削加工技术相比一般铣削加工技术,速度更快,提高了模具制造的效率。
它的株洲转速在15000r/min至40000r/min之间,甚至可以达到100000r/min,在切削钢的时候,速度在传统铣削加工速度上提高了5-10倍,在模具型腔加工的时候,比电火花加工的效率高5倍左右;1.2精度高与一般铣削加工相比,高速铣削加工的精度更高1.3表面质量高高速铣削加工的速度快,所以工作过程中工件的温升比较小,表面产生变质层、微裂纹以及热变形的可能性小,减少了模具制造的工作量,提高了模具制造的效率和质量。
试论模具制造中的高速加工技术
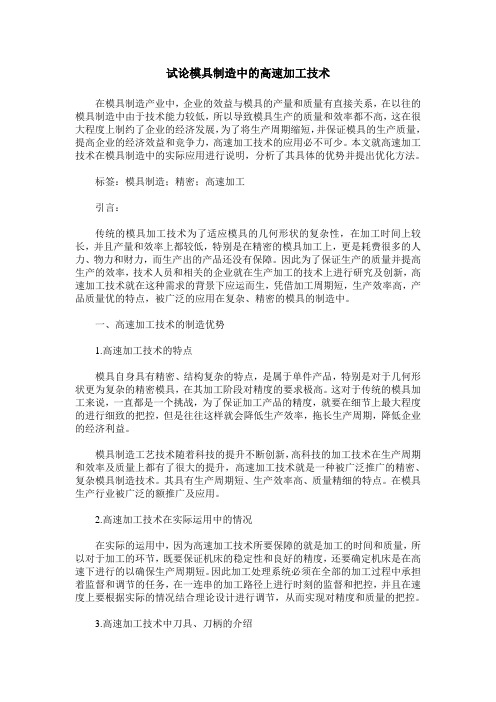
试论模具制造中的高速加工技术在模具制造产业中,企业的效益与模具的产量和质量有直接关系,在以往的模具制造中由于技术能力较低,所以导致模具生产的质量和效率都不高,这在很大程度上制约了企业的经济发展,为了将生产周期缩短,并保证模具的生产质量,提高企业的经济效益和竞争力,高速加工技术的应用必不可少。
本文就高速加工技术在模具制造中的实际应用进行说明,分析了其具体的优势并提出优化方法。
标签:模具制造;精密;高速加工引言:传统的模具加工技术为了适应模具的几何形状的复杂性,在加工时间上较长,并且产量和效率上都较低,特别是在精密的模具加工上,更是耗费很多的人力、物力和财力,而生产出的产品还没有保障。
因此为了保证生产的质量并提高生产的效率,技术人员和相关的企业就在生产加工的技术上进行研究及创新,高速加工技术就在这种需求的背景下应运而生,凭借加工周期短,生产效率高,产品质量优的特点,被广泛的应用在复杂、精密的模具的制造中。
一、高速加工技术的制造优势1.高速加工技术的特点模具自身具有精密、结构复杂的特点,是属于单件产品,特别是对于几何形状更为复杂的精密模具,在其加工阶段对精度的要求极高。
这对于传统的模具加工来说,一直都是一个挑战,为了保证加工产品的精度,就要在细节上最大程度的进行细致的把控,但是往往这样就会降低生产效率,拖长生产周期,降低企业的经济利益。
模具制造工艺技术随着科技的提升不断创新,高科技的加工技术在生产周期和效率及质量上都有了很大的提升,高速加工技术就是一种被广泛推广的精密、复杂模具制造技术。
其具有生产周期短、生产效率高、质量精细的特点。
在模具生产行业被广泛的额推广及应用。
2.高速加工技术在实际运用中的情况在实际的运用中,因为高速加工技术所要保障的就是加工的时间和质量,所以对于加工的环节,既要保证机床的稳定性和良好的精度,还要确定机床是在高速下进行的以确保生产周期短。
因此加工处理系统必须在全部的加工过程中承担着监督和调节的任务,在一连串的加工路径上进行时刻的监督和把控,并且在速度上要根据实际的情况结合理论设计进行调节,从而实现对精度和质量的把控。
超高速磨削技术下的机械加工论文【精编版】
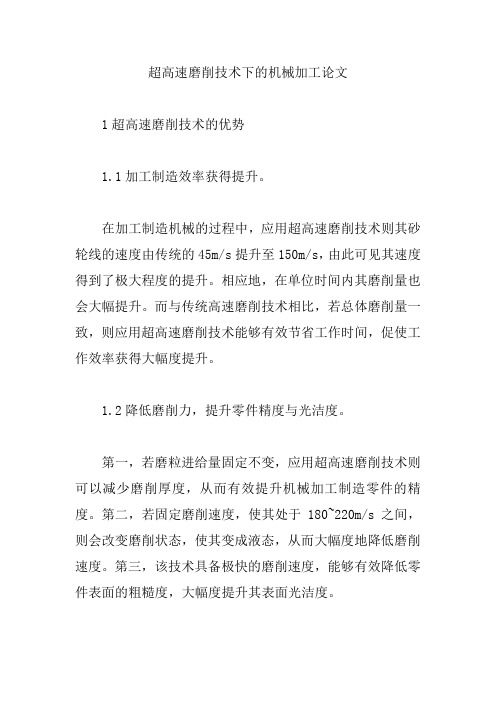
超高速磨削技术下的机械加工论文1超高速磨削技术的优势1.1加工制造效率获得提升。
在加工制造机械的过程中,应用超高速磨削技术则其砂轮线的速度由传统的45m/s提升至150m/s,由此可见其速度得到了极大程度的提升。
相应地,在单位时间内其磨削量也会大幅提升。
而与传统高速磨削技术相比,若总体磨削量一致,则应用超高速磨削技术能够有效节省工作时间,促使工作效率获得大幅度提升。
1.2降低磨削力,提升零件精度与光洁度。
第一,若磨粒进给量固定不变,应用超高速磨削技术则可以减少磨削厚度,从而有效提升机械加工制造零件的精度。
第二,若固定磨削速度,使其处于180~220m/s之间,则会改变磨削状态,使其变成液态,从而大幅度地降低磨削速度。
第三,该技术具备极快的磨削速度,能够有效降低零件表面的粗糙度,大幅度提升其表面光洁度。
1.3使砂轮的使用寿命更长。
在整个磨削过程中磨粒承受着极小的负荷,致使磨粒磨削耗时变长。
如果是进行金属切除工作,若概率一致,则应用超高速磨削技术时其砂轮速度会提升至一般状态下的8.5倍,即若常规速度为80m/s,则应用超高速磨削技术的速度便为200m/s。
由于缩短了磨削时间,因此砂轮寿命得以延长。
1.4提升零件使用效能。
对于硬脆材料而言,普通磨削技术无法正常磨削,而超高速磨削技术则可以,且在使用过程中其厚度较小,促使磨削材料变为流动状态,与此同时零件也获得了更高的抗疲劳性。
2机械加工制造中超高速磨削技术的应用2.1深磨技术的应用在机械加工制造过程中为了实现提升磨削工作效率的目标就需要使用深磨技术。
对于该项技术而言,其具备超快的砂轮线转动速度,同时也能够有效提升零件表面的细腻程度,使其更加光滑,这与一般磨削技术存在差异。
深磨技术的重点在于对磨削整体工作流程予以完善,与此同时其速度一般控制在60~250m/s之间,若砂轮为陶瓷材质的则速度保持在120m/h左右即可,其磨除率与普通磨削技术相比在其百倍甚至千倍以上。
高速切削技术结课论文

高速切削技术结课论文高速切削机床的关键技术摘要: 分析高速切削技术的关键技术, 研究高速切削机床的结构特点,介绍高速加工技术在航空、汽车、模具制造行业的应用。
关键词: 高速切削; 数控加工; 数控机床Key technology application of high-speed cutting machine toolLIXIAOFENG (Shenyang ligong university )Abstract Analyze key technology of highr speed cutting technology study structure chrecter of high-speed cutting machine tool introduce application of highr speed cutting technologyin aviation automobile,mould making field.Key words Highr speed cutting NC maining NC machine tool0引言高速、超高速加工不但可以大幅度提高零件的加工效率、缩短加工时间和降低加工成本, 而且可以使零件的加工表面质量和加工精度达到更高的水平。
随着高速和超高速切削机理、大功率高速主轴单元、高加 / 减速直线进给电动机、磁悬浮以及动 / 静压气浮、液压高速主轴轴承、超硬耐磨长寿命刀具材料、磨料、磨具和高性能的控制系统等一系列技术领域中关键技术初步得到解决, 已使得高速、超高速加工从理论研究进入到具体实施的阶段。
高速加工是一种不需增加设备数量而大幅度提高加工效率所必不可少的技术, 其切削速度范围因不同的工件材料、不同的切削方式而异。
目前, 超高速切削各种材料的切速范围为: 铝合金已超过 1600 m / min , 铸铁为1500m / min , 超耐热镍合金达 300m/min , 钛合金达 150~1000 m / min , 纤维增强塑料为2000~ 9000m/ min 。
高速切削技术在模具加工中的运用

高速切削技术在模具加工中的运用摘要:高速切削技术凭借其效率、精度以及表面质量高等特点,成为了近年来被广泛应用的先进加工技术。
高速切削技术中的“高速”是一个相对概念,不同加工方法与加工材料,加工时所用的切削速度也是不同的,不可简单用某一具体切削速度来定义。
但是,从实际应用情况来分析,高速切削中的“高速”,既是一个技术指标,也是一个经济指标,能在一定程度上提升加工产品的经济效益。
在模具领域中,高速切削通常应用典型的高转速、多速进给、低切深的加工模式,尤其在淬火钢件的加工上,其效果更为显著。
关键词:高速切削技术;模具加工;应用策略引言:人们在生产过程中,不断的寻求新的技术,新的方法,从而提高生产效率,减少生产成本。
在模具的加工过程中,也在不断的尝试,不断的创新,高速切削技术的出现,让模具加工的周期大大的减少,同时也有效的提高了生产效率,降低了生产成本。
因此,高速切削技术应该在模具加工过程中得到很好的运用。
1高速切削加工技术的特点1.加工质量的提升高速切削技术一是可以有效提高加工的效率,二是能有效降低走刀距离,以此来实现工件精度的提高。
高速切削技术作用于模具制造,不会因为热量过高而导致变形问题的出现。
另外,该技术可以有效避免表面损伤问题,在实施加工技术之后,表面属于压应力状态,可以有效提高工件的耐磨程度。
2.加工范围的拓展热压纸技术的应用,能够对钛合金等一些具备较高加工难度的材料进行高效切割。
另外,基于工件发热程度较小的优势,其能够对一些熔点较低的材料进行加工,模具加工后的表面不会产生质变问题,因此质量能够保证,精度也有所提高。
3.经济方面的提升高速切削技术应用于模具加工之中,其经济优势也较为明显,能够有效减少加工时间,不断发挥模具制造工序的集约化优势。
高速切削技术要求工艺装备更加精致,因此所投入的资本也较高。
相较于普通机床的价格,高速加工性能的机床价格要高出三成或一倍。
基于上述特点,一些模具制造企业会选择利用CAD/CAM技术来降低加工成本,减少周期。
模具加工中的高速切削技术

摘 要: 高速切 削是 一项 复杂 的 系统 工程 。 高速切 削不 只是切 削速 度 的提 高 , 的发展 涉及 到 机床 、 它 刀具 、 艺和 材料 等诸 多领域 的 工 技 术 配合 和技 术创新 。 关键 词 : 模具 加工 ; 高速切 削 ; 用 应
1模 具加工 的特 点
2 . 2高速 进 给系统
瞄国陆盈口团困
丽UNI Z I … d U U 'l I .
工 业 技 术
模具 ] c m- 中的高速切 削技术
郑 华 新 张 清 胜
(、 1 海马郑州汽车有限公司 , 河南 郑州 4 0 1 2 河南安飞 电子玻璃有限公 司 506 、 河南 郑州 40 1 ) 5 0 6
—
高速 切 削要 求 刀 具材 料具 有 如 下 性 能 : 由曲面组成。 所用的材料硬度高, 一般模具都 高硬 度 、 强 度 和耐 磨性 : 高 高韧 度 、 良好 的耐 是由淬火工具钢或硬质合金制成 ,运用传统 热冲击性 ; 高热硬性、 良好的化学稳定性。日 的加 工方法 加工较 为 困难 。 目前 在模 具加 工 前, 高速切削加工常用的刀具材料有 : 涂层刀 制造 过程 中 ,主要 以普通 机 加工 和 电火花 加 具 、 瓷刀 具 、 方 氮 化硼 (B ) 陶 立 C N材料 和聚 品 工为 主 。 要缩 短制造 周期 并降低 成本 , 广 金刚 石(C ) 等 。 必须 P D材料 泛采 用先进 切削加 工技 术加 工模 具 。而作 为 3 高速 切 削刀具 系统 . 2 先进 制造技 术 的高速切 削技 术 的 出现 ,正 是 刀具几 何 参数对加 工 质量 和刀具 耐用 度 满 足了模具 加工 这些要 求和特 点 。 有很 大影 响 ,一般 高速切 削刀 具 的前角 比普 2高速 切削机 床技术 通 切 削刀具 约 小 1。后 角 约大 5一。 刀具 O, o8。 性能 良好 的高速切 削机 床是 实现 高速 切 在 高速旋 转时 , 会承受 很大 的离 心力 , 大小 其 削 的前提 和关键 ,而具 有 高精度 的 高速 主轴 远 远超过 切削 力 , 为刀具 的 主要 载荷 , 以 成 足 和 控制精 度高 的高速 进给 系统 ,则 是高 速切 导致 刀体 破碎 , 造成重 大事 故 。
高速切削加工技术及应用论文

浅谈高速切削加工技术及应用摘要:高速切削(high speed cutting,hsc)是近年来迅速崛起的一项先进制造技术。
本文就高速切削加工技术的发展、特点、关键技术及其应用作一简要的研究与阐述。
关键词:高速切削加工;技术;研究;应用中图分类号:tg659 文献标识码:a 文章编号:1006-3315(2011)11-175-0011931年4月德国物理学家carl.j.saloman最早提出了高速切削(high speed cutting)的理论,并于同年申请了专利。
他指出:在常规切削速度范围内,切削温度随着切削速度的提高而升高,但切削速度提高到一定值之后,切削温度不但不会升高反而会降低,且该切削速度vc与工件材料的种类有关。
对于每一种工件材料都存在一个速度范围,在该速度范围内,由于切削温度过高,刀具材料无法承受,切削加工不可能进行。
要是能越过这个速度范围,高速切削将成为可能,从而大幅度地提高生产效率。
由于实验条件的限制,当时高速切削无法付诸实践,但这个思想给后人一个非常重要的启示。
一、高速切削加工概述1.高速切削历史和现状高速切削的起源可追溯到20世纪20年代末期。
德国的切削物理学家萨洛蒙博士于1929年进行了超高速切削模拟试验。
1931年4月发表了著名的超高速切削理论,提出了高速切削假设。
我国早在20世纪50年代就开始研究高速切削,但由于各种条件限制,进展缓慢。
近10年来成果显著,至今仍有多所大学、研究所开展了高速加工技术及设备的研究。
2.切削速度的划分根据高速切削机理的研究结果,高速切削不仅可以大幅度提高单位时间材料切除率,而且还会带来一系列的其他优良特性。
高速切削的速度范围定义在这样一个给切削加工带来一系列优点的区域。
这个切削速度区比传统的切削速度高得多,因此也称超高速切削。
通常把切削速度比常规高出5~10倍以上的切削加工叫做高速切削或超高速切削。
3.高速切削的优势高速切削具有以下特点:①可提高生产效率;②降低了切削力;③提高加工质量;④高速切削的切削热对工件的影响小;⑤加工能耗低,节省制造资源;⑥高速切削可以加工难加工材料;⑦简化了加工工艺流程;⑧可降低加工成本。
- 1、下载文档前请自行甄别文档内容的完整性,平台不提供额外的编辑、内容补充、找答案等附加服务。
- 2、"仅部分预览"的文档,不可在线预览部分如存在完整性等问题,可反馈申请退款(可完整预览的文档不适用该条件!)。
- 3、如文档侵犯您的权益,请联系客服反馈,我们会尽快为您处理(人工客服工作时间:9:00-18:30)。
模具高速切削加工工艺的关键技术摘要:20世纪90年代,以高切削速度、高进给速度和高加工精度为主要特征的高速切削(high speed cutting,hsc)已经成为现代切削加工技术的重要发展方向之一,也是目前模具制造业一项快速发展的高新技术。
由于采用高速切削技术可以明显提高模具生产效率和模具精度及使用寿命,因此正逐渐取代电火花精加工,并已被国内外的模具制造企业普遍采用,成为模具制造的大趋势。
但是作为一种新的切削方式,我国目前还没有完整的加工工艺参数和实用的数据库,笔者就此问题进行了相关的探讨。
关键词:高速切削高速切削工艺切削参数
根据相关资料的统计,在现代化的工业生产中,零件粗加工的75%,精加工的50%,塑件的90%是由模具加工的,做为一种高附加值和高技术密集型产业,现代模具工业已成为当今工业发展的基础。
而模具工业发展的关键主要依靠设计、制造中先进技术的应用(如并行工程ce、逆向工程re、快速成形rp、虚拟制造技术vm、网络化设计与制造、高速切削技术hsc等),其中模具的高速切削技术已成为当前模具制造领域的热点和发展方向。
一、高速切削加工在模具制造中的应用。
1.高速切削(high speed cutting 简称hsc)
高速切削的概念实际上早在20世纪30年代就由德国切削物理专家carl salomon提出的。
这一理论的发现为人们提供了一种在低温低能耗条件下实现高效率切削金属的方法。
那么何谓高速切削
呢?从目前来看,高速切削还没有一个明确的定义,它只是一个相对概念,一般来说,把切削速度比常规切削速度高5—10倍以上的切削称为高速切削。
例如:车削为700~7000/min,铣削加工为200~7000m/min,钻削为100~1000m/min,磨削为5000~10000m/min。
相对应的进给速度一般为2—25m/min,高的可达60—80m/min。
2.高速切削加工的优点及在模具制造中的应用
高速切削加工的优越性主要表现在以下几个方面:①加工效率高,由于切削速度高,进给速度一般也提高5-10倍,这样,单位时间材料切除率可提高3-6倍,因此加工效率大大提高。
②切削力小,高速加工与传统的切削加工相比其采用小切削深度、高的主轴转速和高的进给速度进行加工,由于切削速度高,切屑流出的速度快,减少了切屑与刀具前面的摩擦,从而使切削力大大降低。
③热变形小,高速加工过程中,由于极高的进给速度,95%的切削热被切屑带走,工件基本保持冷态,这样零件不会由于温升而导致变形。
④简化工艺流程,由于高速铣削的表面质量可达磨削加工的效果,因此有些场合高速加工可作为零件的精加工工序,从而简化了工艺流程,缩短了零件加工时间。
⑤大幅降低工件表面损伤,采用高速切削可以避免电火花和磨削产生的脱碳、烧伤和微裂纹现象,大大减少了模具精加工后的表面损伤,提高模具寿命20 %。
二、高速切削工艺的关键技术
目前国外的模具制造业,已经广泛采用了高速切削加工,而且与之相适应的cnc机床技术(主要包括机床总体布局机床的驱动技
术,机床数控技术……),刀具技术(刀具的材料,刀具的几何形状及角度,刀柄的设计……),加工工艺(切削参数的确定,切削方式的选择……)等相关技术已经相当成熟和完善。
而反观我国,由于我们的模具工业起步较晚,不论从产品的开发设计、制造装备,还是制造工艺都相对落后。
尽管近几年来,随着我国经济的高速发展,不少企业已经大量购进相关的高速切削机床和刀具,但是由于缺乏适合我国国情的加工工艺参数,所以在实际应用过程还是遇到这样或那样的问题,这也就阻碍了高速切削加工在我国的应用。
故目前急需解决的是通过试验和实际加工形成适合我国实际的加工
工艺参数和技术标准。
1.切削方式的选择。
a、顺铣与逆铣的选择,原则上在高速切削加工中,应尽量选用分层环切顺铣加工。
因为顺铣时刀具刚切入工件时切屑厚度最大,随后逐渐减少,这样有利于“咬住”材料并去除之;同时,顺铣时刀刃主要受压应力任用,受力状态较理想,这样可以减少刀具的磨损,延长刀具的使用寿命。
b、切入切出工件方式。
对于没有型腔的外轮廓区域,尽量采用圆弧或摆线方式切入切出的方式,而非直线切入切出,这样可避免由于载荷的突然增加和减少而引起的崩刃现象。
对于带有型腔的内表面,可以采用以下几种方式切入,①直接垂直向下进刀②斜线轨迹进刀③螺旋式轨迹进刀,从中不难分析螺旋式切入工件是从工件上表面螺旋向下切入的,速度没有突变可以连续加工,切削工况最好,最适合模具型腔高速加工。
2.切削参数的优化与选择
在模具制造中高速切削与传统切削相比,两者主要区别在于进给速度,切削速度,切削深度等的工艺参数不同。
一般的选择原则是:高速切削加工多采用高的切削速度和进给量,较小的切削深度。
当切削深度和每齿进给量保持不变时,进给速度可比常规铣削提高5~10倍,主轴转速在20000~40000r/min,材料切除率可提高3~5倍。
高速切削的切削深度一般在0.05~0.6mm之间,精加工时切削深度可以达到0.1mm以下,小的切削深度可以减少切削力,降低切削热的产生,延长刀具的使用寿命;从加工工况来看,小切深和单一路径切削可以保证加工模具时切削载荷的恒定,保持恒定的金属去除率,确保加工模具的几何精度。
高速切削的刀具行距一般在0.2mm以下,这样可以降低模具的表面粗糙度,提高加工质量,大幅减少后续的精加余量
3.cad/cam软件编程要点
对于结构形状复杂的模具,如果采用手工编程,难度较大甚工根本无法实现,因此最好通过自动编程软件来解决此问题,例如:delcam公司开发的高速切削自动编程软件模块powermill;mastercam公司开发的高速切削模块等。
在使用以上软件编程时,为了满足高速切削加工的需要,必须注意几个问题:①尽可能减少程序段,提高程序处理速度。
如加工曲面时,尽量nurbs插补,而不要使用直线插补。
②在粗加工时,要充分考虑后续的工序要求,使加工余量均匀。
③尽可能采用分层环切顺铣方式。
保证每层切削
深度相同,减少切削载荷的突然变化。
④零件在加工前必须充分利用软件的仿真验证功能,确保刀位数据的正确,避免由于刀具与工件或夹具与工件发生干涉,而引发的产品质量和操作安全问题隐患。
另外,高速切削中的冷却润滑,也是十分重要的问题,一般来说由于高速切削加工时切削热大都由切屑带走,对刀具影响较小,故可不使用切削液。
在一些特殊情况下要求湿切削时,可采用油雾冷却,水雾冷却和高压气体冷却等方式来解决,千万不可采用常规的切削液和加注方式以免带来不必要的麻烦。
总之,模具加工中的高速切削技术,做为一项先进的、正在发展的综合技术,必须将高性能的高速切削机床、与工件材料相适应的刀具和对具体加工对象最佳的加工工艺相结合,充分发挥高速切削技术的优势。
而对于模具高速切削中的工艺做为一项关键环节,需要各方面加大投入力度,走学研结合的道路,综合全社会的力量推动其快速成长,以满足当前模具行业的迫切需求。
参考文献:
【1】张伯霖.高速切削技术及应用[m].机械工业出版社,2002.
【2】李沪曾等.高速切削加工技术在模具制造中的推广应用[j].现代制造,2004(09).
【3】康炳勋,夏新涛.在高速铣削中如何合理制订工艺路线[j].机械工人,2004(07).。