基于DCS的数据采集接口及实时数据库研究与应用
DCS与数字孪生技术的融合实现实时仿真与优化决策
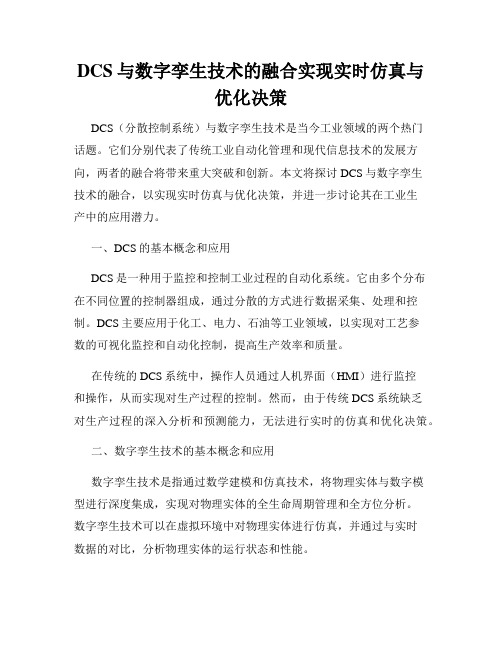
DCS与数字孪生技术的融合实现实时仿真与优化决策DCS(分散控制系统)与数字孪生技术是当今工业领域的两个热门话题。
它们分别代表了传统工业自动化管理和现代信息技术的发展方向,两者的融合将带来重大突破和创新。
本文将探讨DCS与数字孪生技术的融合,以实现实时仿真与优化决策,并进一步讨论其在工业生产中的应用潜力。
一、DCS的基本概念和应用DCS是一种用于监控和控制工业过程的自动化系统。
它由多个分布在不同位置的控制器组成,通过分散的方式进行数据采集、处理和控制。
DCS主要应用于化工、电力、石油等工业领域,以实现对工艺参数的可视化监控和自动化控制,提高生产效率和质量。
在传统的DCS系统中,操作人员通过人机界面(HMI)进行监控和操作,从而实现对生产过程的控制。
然而,由于传统DCS系统缺乏对生产过程的深入分析和预测能力,无法进行实时的仿真和优化决策。
二、数字孪生技术的基本概念和应用数字孪生技术是指通过数学建模和仿真技术,将物理实体与数字模型进行深度集成,实现对物理实体的全生命周期管理和全方位分析。
数字孪生技术可以在虚拟环境中对物理实体进行仿真,并通过与实时数据的对比,分析物理实体的运行状态和性能。
数字孪生技术主要应用于工业制造、能源、交通等领域。
通过数字孪生技术,可以实现对设备状态的监测与诊断、生产过程的预测与优化,从而提高工业生产的效率和可靠性。
三、DCS与数字孪生技术的融合DCS与数字孪生技术的融合,可以实现对生产过程的实时仿真和优化决策。
首先,利用DCS系统采集到的实时数据,构建数字孪生模型,实现对生产过程的虚拟仿真。
通过在数字孪生模型中进行实时仿真,并与实际生产过程进行对比,可以准确地分析和预测生产过程的状态和性能。
其次,在数字孪生模型的基础上,可以进行优化决策。
通过对生产参数和工艺流程进行调整和优化,可以最大程度地提高生产效率和产品质量。
基于数字孪生模型的优化决策可以通过DCS系统的控制器进行实时执行,从而实现对生产过程的实时优化。
化工厂DCS一体化智能系统的研究与分析
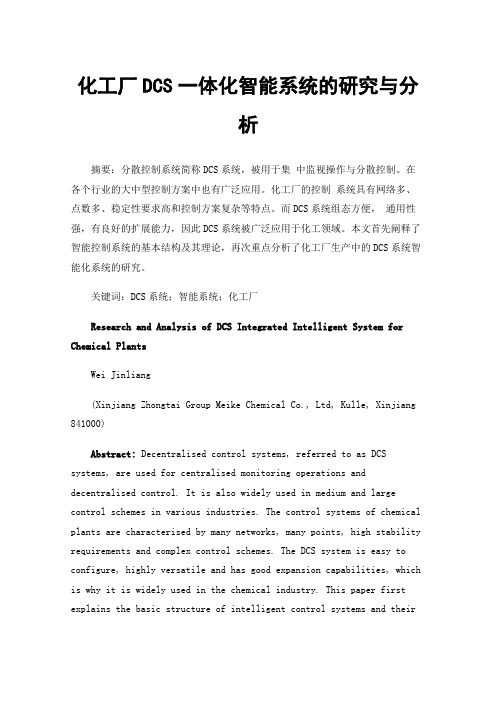
化工厂DCS一体化智能系统的研究与分析摘要:分散控制系统简称DCS系统,被用于集中监视操作与分散控制。
在各个行业的大中型控制方案中也有广泛应用。
化工厂的控制系统具有网络多、点数多、稳定性要求高和控制方案复杂等特点。
而DCS系统组态方便,通用性强,有良好的扩展能力,因此DCS系统被广泛应用于化工领域。
本文首先阐释了智能控制系统的基本结构及其理论,再次重点分析了化工厂生产中的DCS系统智能化系统的研究。
关键词:DCS系统;智能系统;化工厂Research and Analysis of DCS Integrated Intelligent System for Chemical PlantsWei Jinliang(Xinjiang Zhongtai Group Meike Chemical Co., Ltd, Kulle, Xinjiang 841000)Abstract: Decentralised control systems, referred to as DCS systems, are used for centralised monitoring operations and decentralised control. It is also widely used in medium and large control schemes in various industries. The control systems of chemical plants are characterised by many networks, many points, high stability requirements and complex control schemes. The DCS system is easy to configure, highly versatile and has good expansion capabilities, which is why it is widely used in the chemical industry. This paper first explains the basic structure of intelligent control systems and theirtheory, and then focuses on the study of intelligent systems for DCS systems in chemical plant production.Keywords: DCS system; intelligent system; chemical plant1智能控制系统概述在智能控制系统中,通常执行级需要较为精确的模型,来实现对精度要求较高的控制任务,其主要工作是完成所有信息进行检测、处理及获取,同时采用智能控制的方式对复杂的过程直接进行控制[1]。
力控实时数据库

其它 第三 方实 时数 据库
力控实时数据库主要特性(1)
完全的分布式结构,可任意组建应用模式 提供丰富的企业级信息系统客户端应用和工具 大容量支持企业级应用,灵活的扩展结构可满足各种需求
– 每台服务器可运行100 000个点, 支持多台服务器相互通信
OPC、DDE
CSV / XML
力控开放的、可自由伸缩的体系结构,满足企业信息化的整体需要 三维力控
力控或其它 应用程序
力控或其它 应用程序
其它应 用程序
网络
力控 I/O Server
可单独分布使 用的力控组件
数据库管 分布式实 理器 时数据库
可单独分布使 用的力控组件
管控一体化解决之道
通讯实用程序
分析应用和工具: 易于使用 功能强大 全面性 可扩展 可维护 可自定义
管控一体化解决之道
力控实时数据库的无限互联与应用扩展能力……
三维力控
优化控制 先进控制 控制策略
传统 历史数据
力控Web
SCADA
其他 HMI
DCS
称重系统
力控
实时数据库
OPC
CSV XML
智能设备
力控HMI
其他力控 数据库
高性能存储和查询, 包括毫秒采集
– 每秒可处理20 000个事件 – mS级数据采集速率 – 事件系统的时间分辨率为 1mS
力控实时数据库与HMI是完全分离运行的
三维力控
管控一体化解决之道
力控实时数据库主要特性(2)
三维力控
使用真正的瘦客户端,基于Web的管理器,客户端应用易于维护
– 管理工具提供十分易用和直观的接口
基于Web的DCS数据监控系统设计与实现
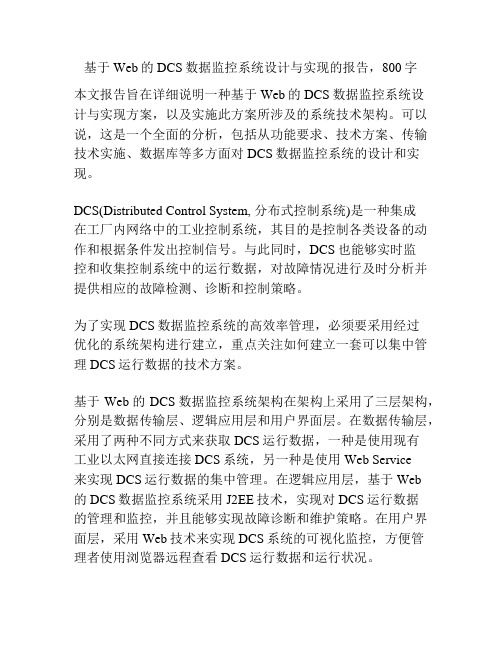
基于Web的DCS数据监控系统设计与实现的报告,800字本文报告旨在详细说明一种基于Web的DCS数据监控系统设计与实现方案,以及实施此方案所涉及的系统技术架构。
可以说,这是一个全面的分析,包括从功能要求、技术方案、传输技术实施、数据库等多方面对DCS数据监控系统的设计和实现。
DCS(Distributed Control System, 分布式控制系统)是一种集成在工厂内网络中的工业控制系统,其目的是控制各类设备的动作和根据条件发出控制信号。
与此同时,DCS也能够实时监控和收集控制系统中的运行数据,对故障情况进行及时分析并提供相应的故障检测、诊断和控制策略。
为了实现DCS数据监控系统的高效率管理,必须要采用经过优化的系统架构进行建立,重点关注如何建立一套可以集中管理DCS运行数据的技术方案。
基于Web的DCS数据监控系统架构在架构上采用了三层架构,分别是数据传输层、逻辑应用层和用户界面层。
在数据传输层,采用了两种不同方式来获取DCS运行数据,一种是使用现有工业以太网直接连接DCS系统,另一种是使用 Web Service来实现DCS运行数据的集中管理。
在逻辑应用层,基于Web的DCS数据监控系统采用J2EE技术,实现对DCS运行数据的管理和监控,并且能够实现故障诊断和维护策略。
在用户界面层,采用Web技术来实现DCS系统的可视化监控,方便管理者使用浏览器远程查看DCS运行数据和运行状况。
因此,基于Web的DCS数据监控系统的实施,可以将传统的繁琐的DCS监控系统变得简单易用,可有效改善管理者查看DCS运行状况的效率,加快DCS设备故障诊断和维护的策略,从而提高工业系统的运行效率和可靠性。
dcs系统的工作原理
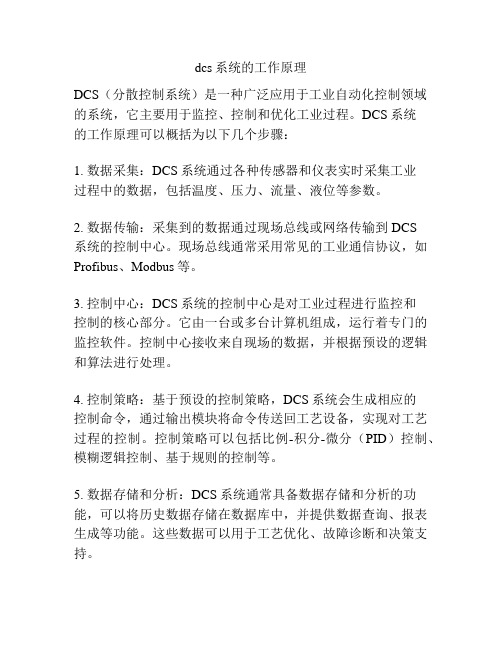
dcs系统的工作原理
DCS(分散控制系统)是一种广泛应用于工业自动化控制领域的系统,它主要用于监控、控制和优化工业过程。
DCS系统
的工作原理可以概括为以下几个步骤:
1. 数据采集:DCS系统通过各种传感器和仪表实时采集工业
过程中的数据,包括温度、压力、流量、液位等参数。
2. 数据传输:采集到的数据通过现场总线或网络传输到DCS
系统的控制中心。
现场总线通常采用常见的工业通信协议,如Profibus、Modbus等。
3. 控制中心:DCS系统的控制中心是对工业过程进行监控和
控制的核心部分。
它由一台或多台计算机组成,运行着专门的监控软件。
控制中心接收来自现场的数据,并根据预设的逻辑和算法进行处理。
4. 控制策略:基于预设的控制策略,DCS系统会生成相应的
控制命令,通过输出模块将命令传送回工艺设备,实现对工艺过程的控制。
控制策略可以包括比例-积分-微分(PID)控制、模糊逻辑控制、基于规则的控制等。
5. 数据存储和分析:DCS系统通常具备数据存储和分析的功能,可以将历史数据存储在数据库中,并提供数据查询、报表生成等功能。
这些数据可以用于工艺优化、故障诊断和决策支持。
6. 人机界面:DCS系统提供友好的人机界面,用于操作员监
控和控制工艺过程。
操作员可以通过可视化界面查看实时数据、趋势曲线、报警状态等,并进行相应的操作和调整。
总体来说,DCS系统的工作原理是通过数据采集、传输、控
制中心处理和控制策略生成,实现对工业过程的监控和控制,并提供数据存储、分析和人机界面等功能,以提高工业过程的自动化程度和效率。
火电厂电气监控系统接入DCS方式的分析
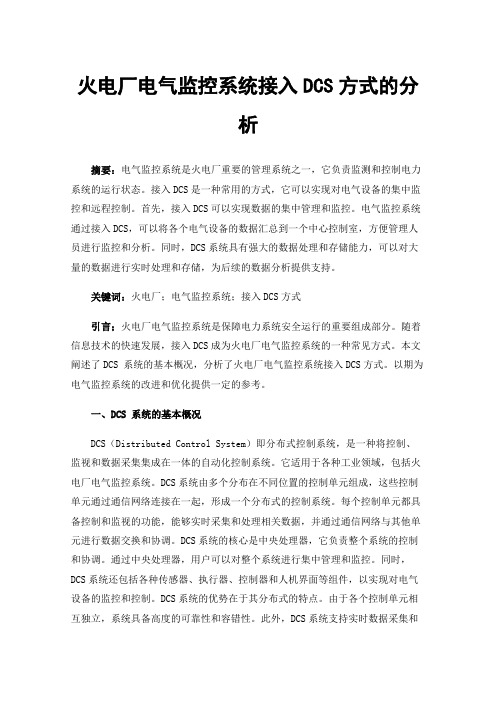
火电厂电气监控系统接入DCS方式的分析摘要:电气监控系统是火电厂重要的管理系统之一,它负责监测和控制电力系统的运行状态。
接入DCS是一种常用的方式,它可以实现对电气设备的集中监控和远程控制。
首先,接入DCS可以实现数据的集中管理和监控。
电气监控系统通过接入DCS,可以将各个电气设备的数据汇总到一个中心控制室,方便管理人员进行监控和分析。
同时,DCS系统具有强大的数据处理和存储能力,可以对大量的数据进行实时处理和存储,为后续的数据分析提供支持。
关键词:火电厂;电气监控系统;接入DCS方式引言;火电厂电气监控系统是保障电力系统安全运行的重要组成部分。
随着信息技术的快速发展,接入DCS成为火电厂电气监控系统的一种常见方式。
本文阐述了DCS 系统的基本概况,分析了火电厂电气监控系统接入DCS方式。
以期为电气监控系统的改进和优化提供一定的参考。
一、DCS 系统的基本概况DCS(Distributed Control System)即分布式控制系统,是一种将控制、监视和数据采集集成在一体的自动化控制系统。
它适用于各种工业领域,包括火电厂电气监控系统。
DCS系统由多个分布在不同位置的控制单元组成,这些控制单元通过通信网络连接在一起,形成一个分布式的控制系统。
每个控制单元都具备控制和监视的功能,能够实时采集和处理相关数据,并通过通信网络与其他单元进行数据交换和协调。
DCS系统的核心是中央处理器,它负责整个系统的控制和协调。
通过中央处理器,用户可以对整个系统进行集中管理和监控。
同时,DCS系统还包括各种传感器、执行器、控制器和人机界面等组件,以实现对电气设备的监控和控制。
DCS系统的优势在于其分布式的特点。
由于各个控制单元相互独立,系统具备高度的可靠性和容错性。
此外,DCS系统支持实时数据采集和处理,能够实现对电气设备的精确控制和监测。
同时,DCS系统还具备灵活性和可扩展性,可以根据需要进行系统的扩展和升级。
在火电厂电气监控系统中,DCS系统的应用可以实现对电力设备的远程监控和控制,提高系统的安全性和稳定性。
OPC在DCS系统中数据采集中的应用

OPC技术在DCS数据采集系统中的应用何杨欢(中国石化长岭分公司计算机应用研究所,湖南省岳阳市414012)摘要:本文介绍了OPC技术在数据采集系统中的应用。
结合实际叙述了中国石化长岭分公司DCS数据采集系统及其软、硬件结构和功能特点,重点论述了OPC数据通讯技术和应用。
关键词: OPC DDEO 引言OPC全称是OLE for Process Control,是过程控制业中的新兴标准。
OPC新技术标准的出现为数据采集接口和现场过程控制DCS系统应用建立了桥梁。
在过去,为了实现不同生产装置的DCS系统和数据采集接口之间的数据通信,必须要花费很多时间去开发专用的通信接口程序。
在这种情况下,OPC标准应运而生。
OPC 以OLE/COM/DCOM机制作为应用程序级的通信标准,采用客户/服务器模式,把开发访问接口的任务放在硬件生产厂家或第三方厂家,以OPC服务器的形式提供给用户,解决了软、硬件厂商的矛盾,完成了系统的集成,提高了系统的开放性和可互操作性。
1OPC数据通讯技术1.1 OPC客户端与OPC服务器OPC技术的实现包括OPC服务器部分及OPC客户应用部分,其应用模式如图1所示。
OPC服务器收集现场设备数据信息,OPC客户端通过OPC标准接口获取OPC服务器的各种信息。
符合OPC标准的客户端可以访问来自任何生产厂商的OPC服务器。
图1 OPC客户端与OPC服务器连接图1.2 OPC服务器数据访问接口OPC标准以微软公司的OLE技术为基础,它是通过提供一套标准的OLE/COM接口完成的。
OPC服务器支持两种类型的访问接口:自动化接口(Automation interface);自定义接口(Custom interface)。
自动化接口是为基于脚本编程语言而定义的标准接口,可以使用VisualBasic、Delphi、PowerBuilder等编程语言开发OPC服务器的客户应用。
而自定义接口是专门为C++等高级编程语言而制定的标准接口。
基于DCS工业应用场景的以太网Link Down机制的研究
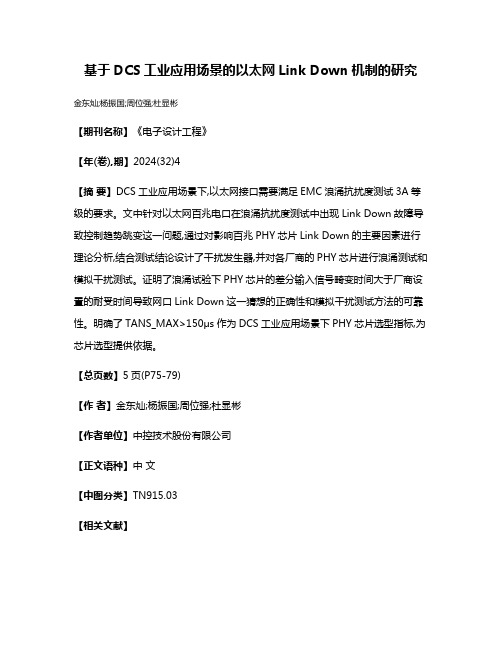
基于DCS工业应用场景的以太网Link Down机制的研究金东灿;杨振国;周位强;杜显彬
【期刊名称】《电子设计工程》
【年(卷),期】2024(32)4
【摘要】DCS工业应用场景下,以太网接口需要满足EMC浪涌抗扰度测试3A等级的要求。
文中针对以太网百兆电口在浪涌抗扰度测试中出现Link Down故障导致控制趋势跳变这一问题,通过对影响百兆PHY芯片Link Down的主要因素进行理论分析,结合测试结论设计了干扰发生器,并对各厂商的PHY芯片进行浪涌测试和模拟干扰测试。
证明了浪涌试验下PHY芯片的差分输入信号畸变时间大于厂商设置的耐受时间导致网口Link Down这一猜想的正确性和模拟干扰测试方法的可靠性。
明确了TANS_MAX>150μs作为DCS工业应用场景下PHY芯片选型指标,为芯片选型提供依据。
【总页数】5页(P75-79)
【作者】金东灿;杨振国;周位强;杜显彬
【作者单位】中控技术股份有限公司
【正文语种】中文
【中图分类】TN915.03
【相关文献】
1.基于工业以太网的多台西门子PLC与DCS的通信系统
2.基于工业以太网的高速现场总线GSK-Link
3.基于工业以太网的DCS远程IO控制站通讯卡设计
4.基于工业以太网的自动化生产线DCS控制系统设计
因版权原因,仅展示原文概要,查看原文内容请购买。
DCS系统中的数据管理与分析
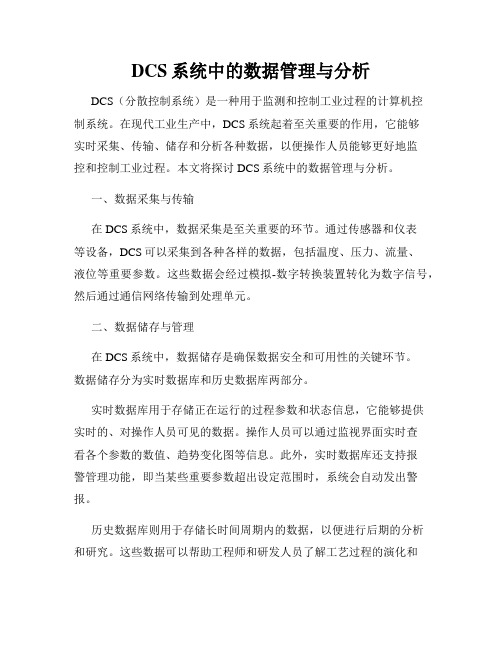
DCS系统中的数据管理与分析DCS(分散控制系统)是一种用于监测和控制工业过程的计算机控制系统。
在现代工业生产中,DCS系统起着至关重要的作用,它能够实时采集、传输、储存和分析各种数据,以便操作人员能够更好地监控和控制工业过程。
本文将探讨DCS系统中的数据管理与分析。
一、数据采集与传输在DCS系统中,数据采集是至关重要的环节。
通过传感器和仪表等设备,DCS可以采集到各种各样的数据,包括温度、压力、流量、液位等重要参数。
这些数据会经过模拟-数字转换装置转化为数字信号,然后通过通信网络传输到处理单元。
二、数据储存与管理在DCS系统中,数据储存是确保数据安全和可用性的关键环节。
数据储存分为实时数据库和历史数据库两部分。
实时数据库用于存储正在运行的过程参数和状态信息,它能够提供实时的、对操作人员可见的数据。
操作人员可以通过监视界面实时查看各个参数的数值、趋势变化图等信息。
此外,实时数据库还支持报警管理功能,即当某些重要参数超出设定范围时,系统会自动发出警报。
历史数据库则用于存储长时间周期内的数据,以便进行后期的分析和研究。
这些数据可以帮助工程师和研发人员了解工艺过程的演化和变化趋势,以便进行优化和改进。
历史数据库的数据储存可以按照时间周期进行划分,以方便后续的查询和分析。
三、数据分析与应用DCS系统中的数据分析是为了更好地理解工业过程、改善生产效率和优化产品质量。
数据分析可以通过各种方法进行,包括趋势分析、统计分析、模型建立等。
趋势分析是一种最常用的数据分析方法,它可以通过分析各个参数的变化趋势,帮助工程师识别异常情况、预测故障和优化过程。
例如,当某个参数的数值突然发生剧烈波动时,趋势分析能够及时发出警报,并且根据历史数据提供可能的原因和解决方案。
统计分析则是通过对大量数据进行处理和分析,以发现其中的规律和规律。
通过统计分析,工程师可以了解到不同因素之间的相互关系,进而针对性地进行优化和改进。
例如,通过统计分析可以确定某个因素与产品质量之间的相关性,从而找到改进产品品质的方法。
DCS系统的实时数据分析与决策支持

DCS系统的实时数据分析与决策支持DCS(分散控制系统)作为现代工业生产中的一种重要控制系统,在实时数据分析和决策支持方面起着关键作用。
本文将论述DCS系统在实时数据分析和决策支持方面的应用,以及该系统对于企业运营管理的重要意义。
一、DCS系统的实时数据分析1. 实时数据采集与传输DCS系统通过传感器、仪表等设备采集生产现场的数据,并将这些数据通过网络传输到控制中心。
数据的实时采集和传输确保了数据的准确性和实时性,在提供可靠的数据基础上,支持后续的实时数据分析和决策制定。
2. 实时数据监测与分析DCS系统可以对实时数据进行监测、分析和处理。
通过对数据的实时监测,可以及时发现异常情况和问题,提高生产系统的稳定性和安全性。
同时,通过数据的分析,可以对生产过程进行优化,提高生产效率和产品质量。
3. 数据可视化和报告DCS系统可以将实时数据以图形化的方式呈现,使操作人员可以直观地了解生产过程的状态和变化趋势。
并且,系统可以生成各种形式的报告,帮助管理人员进行决策分析和业绩评估。
二、DCS系统的决策支持1. 系统运行状态监控DCS系统可以对生产系统进行全面的监控和管理。
通过对实时数据的分析,系统可以帮助管理人员了解生产线的运行状态,掌握生产过程中的关键指标和关键节点,及时发现潜在问题,并采取相应的措施进行调整和优化。
2. 过程优化和控制策略调整基于实时数据的分析结果,DCS系统可以给出过程优化的建议和控制策略的调整方案。
管理人员可以根据系统提供的决策支持信息,及时采取措施优化生产过程,提高生产效率和产品质量。
3. 风险评估和预警提示DCS系统可以通过数据分析,对生产过程中可能存在的风险进行评估,并提供预警提示。
这有助于企业在生产过程中及时发现和解决潜在问题,降低潜在风险对企业运营的影响。
三、DCS系统对企业运营管理的重要意义1. 提高生产效率和产品质量DCS系统通过实时数据的监测和分析,可以帮助企业优化生产过程,提高生产效率和产品质量。
实时数据库系统解决方案
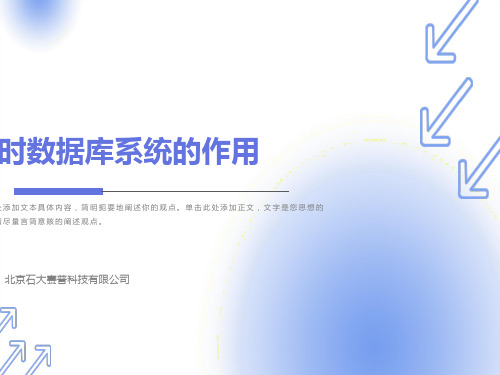
丰富的应用工具
流程图组态工具 流程图浏览 实时数据查询 实时数据趋势曲线 历史数据查询 实时报警监视 异常报警查询 数采状态监视
01
控制点监视
02
事故追忆
03
生产利润在线查询
辅助管理和分析工具
控制点监视
趋势图 平均值 平稳率
事故追忆
以事件为线索组织数据 分析事故原因
单击此处添加正文,文字是您思想的提炼,为了演示发布的良好效果,请言简意赅地阐述您的观点。您的内容已经简明扼要,字字珠玑,但信息却千丝万缕、错综复杂,需要用更多的文字来表述;但请您尽可能提炼思想的精髓,否则容易造成观者的阅读压力,适得其反。正如我们都希望改变世界,希望给别人带去光明,但更多时候我们只需要播下一颗种子,自然有微风吹拂,雨露滋养。恰如其分地表达观点,往往事半功倍。当您的内容到达这个限度时,或许已经不纯粹作用于演示,极大可能运用于阅读领域;无论是传播观点、知识分享还是汇报工作,内容的详尽固然重要,但请一定注意信息框架的清晰,这样才能使内容层次分明,页面简洁易读。如果您的内容确实非常重要又难以精简,也请使用分段处理,对内容进行简单的梳理和提炼,这样会使逻辑框架相对清晰。为了能让您有更直观的字数感受,并进一步方便使用,我们设置了文本的最大限度,当您输入的文字到这里时,已濒临页面容纳内容的上限,若还有更多内容,请酌情缩小字号,但我们不建议您的文本字号小于14磅,请您务必注意。单击此处添加正文,文字是您思想的提炼,为了演示发布的良好效果,请言简意赅地阐述您的观点。您的内容已经简明扼要,字字珠玑,但信息却千丝万缕、错综复杂,需要用更多的文字来表述;但请您尽可能提炼思想的精髓,否则容易造成观者的阅读压力,适得其反。正如我们都希望改变世界,希望给别人带去光明,但更多时候我们只需要播下一颗种子,自然有微风吹拂,雨露滋养。恰如其分地表达观点,往往事半功倍。当您的内容到达这个限度时,或许已经不纯粹作用于演示,极大可能运用于阅读领域;无论是传播观点、知识分享还是汇报工作,内容的详尽固然重要,但请一定注意信息框架的清晰,这样才能使内容层次分明,页面简洁易读。如果您的内容确实非常重要又难以精简,也请使用分段处理,对内容进行简单的梳理和提炼,这样会使逻辑框架相对清晰。为了能让您有更直观的字数感受,并进一步方便使用,我们设置了文本的最大限度,当您输入的文字到这里时,已濒临页面容纳内容的上限,若还有更多内容,请酌情缩小字号,但我们不建议您的文本字号小于14磅,请您务必注意。单击此处添加正文,
制药实时数据采集方案

药厂实时数据采集系统项目解决方案1 背景1.1 引言随着国家大力推进走新型工业化道路,以信息化带动工业化,以工业化促进信息化。
工业面临着日趋激烈的竞争。
降低成本,提高生产效率,快速响应市场,是企业不断追求的目标。
要实现上述目标,必须把企业经营生产中的各个环节,包括市场分析、经营决策、计划调度、过程监控、销售服务、资源管理等全部生产经营活动综合为一个有机的整体,实现综合信息集成,使企业在经营过程中保持柔性,因此,建立全厂统一的生产实时数据平台,就成了流程企业今后生产信息化的关键。
1.2 目标“实时数据采集系统”是为生产过程进行实时综合优化服务信息系统提供数据基础。
企业信息化建设的关键问题是集成,即在获取生产流程所需全部信息的基础上,将分散的控制系统、生产调度系统和管理决策系统有机地集成起来,不同业务和系统间能够实时的交换和共享数据。
(以下是数据采集信息化的好处)(一)建立统一的企业数据模型。
(二)解决分期建设的不同应用系统、不同工厂之间彼此隔离、互不匹配、互不共享的信息孤岛问题。
(三)保证数据来源一致性,提高数据经过层层抽取之后的可信度。
(四)汇总、分析和展示企业历史的业务数据。
(五)企业管理层能够直接根据各工厂的真实数据进行统计数据、分析逐步钻取直到数据根源。
(六)透明底层的数据,监督统计分析数据的准确性。
(七)企业应用集成,规范企业业务的数据流程。
1.3 工厂架构(一)现场层:包括传感器,仪表,电机,气缸,阀门等执行器件。
也包括特定的设备及专业仪器,也涵盖简单的PLC、PAC、工控机、嵌入式控制单元和HMI等。
(二)控制层:主要就是高性能的PLC或工控机。
其实现将整个工厂的现场单元进行联网,数据集成,集中控制。
HMI为标配人机交互系统,其还会有SCADA系统,统一管理,实现人机交互。
(三)生产层:这里指MES系统(制造企业生产过程执行系统)。
是一套面向制造企业车间执行层的生产信息化管理系统。
MES为企业提供“制造数据管理”,“计划排程管理”,“生产调度管理”,“库存管理”,“质量管理”,“人力资源管理”,“电子看板管理”等功能。
分布式控制dcs系统功能模块

分布式控制dcs系统功能模块分布式控制系统(DCS)是一种基于计算机网络的控制系统,它将控制和监测功能分布在不同的计算机节点上,通过网络进行通信和协调,以实现对复杂工业过程的集中控制和管理。
DCS系统由多个功能模块组成,每个模块负责不同的任务,共同构成了一个完整的控制系统。
本文将介绍DCS系统中常见的功能模块。
1. 过程控制模块过程控制模块是DCS系统的核心模块,它负责监测和控制工业过程中的各种参数和变量。
通过传感器和执行器,该模块可以实时采集和反馈过程数据,并根据设定的控制策略进行调节。
过程控制模块通常包括PID控制器、逻辑控制器、模糊控制器等,能够满足不同的控制需求。
2. 数据采集模块数据采集模块负责从各个传感器和执行器中采集过程数据,并将其传输给过程控制模块进行处理。
该模块通常包括模拟输入模块和数字输入模块,能够接收不同类型的信号,并将其转换为数字信号进行处理。
数据采集模块还负责对采集的数据进行预处理,如滤波、线性化等,以提高数据质量和可靠性。
3. 人机界面模块人机界面模块是DCS系统与操作人员之间的接口,通过它可以实现对过程的监视、操作和控制。
该模块通常包括显示器、键盘、鼠标等硬件设备,以及操作界面和控制软件。
人机界面模块能够将过程数据以图形化的方式呈现给操作人员,并提供操作控制的功能,使操作人员能够直观地了解和控制工业过程。
4. 应用软件模块应用软件模块是DCS系统中的高级功能模块,主要用于实现特定的控制和管理功能。
该模块通常包括数据处理模块、报警管理模块、故障诊断模块等,能够对采集的数据进行分析、处理和存储。
应用软件模块还可以实现对系统状态的监测和报警,以及对设备故障的诊断和处理,提高系统的可靠性和安全性。
5. 通信模块通信模块是DCS系统中实现节点之间通信和数据传输的关键模块。
该模块负责建立和维护节点之间的通信连接,以及实现数据的传输和同步。
通信模块通常包括网络接口模块、通信协议模块等,能够支持各种通信方式和协议。
OPC技术在企业实时数据库系统中的应用

OPC技术在企业实时数据库系统中的应用【摘要】工业生产信息化是未来企业信息化发展趋势。
面对不同的生产控制系统,如何有效的进行数据集成,消除“信息化孤岛”,为生产管理者提供有效的数据分析与应用,OPC(OLE For Process Control)技术提供了一个很好的方法。
通过采集多种控制系统的实时数据,实现生产全流程在线监控管理,提升企业管理效率和水平。
【关键词】OPC技术;TCP/IP协议1.前言随着信息技术的发展,数据库技术应用日益广泛,许多企业都建设了自动化控制系统,实时掌握运行数据,进行科学的分析和数据处理,提供优化决策,不仅能够合理的进行资源分配,还可以收获客观的经济回报。
伴随着企业的不断发展,扩建不同地域的工厂,配备多套不同厂家和型号生产设备和控制系统,导致生产控制系统层的“信息孤岛”现象,生产数据无法集中共享,从而使生产管理人员无法从整个生产工艺流程的角度去指导生产,优化工艺。
因此大型的石化企业建设分布式实时数据库系统,是迫切需要解决的问题。
2.数据集成技术2.1 常见技术比较在多控制系统的集成过程中,由于特定厂家的控制系统使用的控制网络和信息格式不一致,因此彼此之间不兼容,难以实现不同厂家的控制系统间以及控制系统与信息系统间的互操作。
解决不同系统间的集成问题有以下几种常见技术。
(1)DDE技术DDE(Dynamic Data Exchange)是在Windows平台下两个进程之间的数据交换及命令的传递,是基于消息的并且利用通常的Windows中的通信联络系统进行内部进程间的相互通信。
当通信数据量大时,数据刷新速度慢,容易出现死机现象。
因此,DDE只适合于配置简单的小型系统。
(2)ODBC技术ODBC(Open Database Connecticity,开放的数据库互连)是一个Microsoft 建议并开发的数据库访问API标准,目的是实现异构数据库的互连,为异构数据库提供一个框架,实现最大限度的互操作性。
化工装置DCS技术要求中的数据采集与分析要求

化工装置DCS技术要求中的数据采集与分析要求在化工生产过程中,DCS(分布式控制系统)技术被广泛应用于各种装置和设备的自动化控制。
而数据采集与分析是DCS技术中至关重要的一环,其准确性和及时性直接影响到生产过程的稳定性和效率。
本文将就化工装置DCS技术要求中的数据采集与分析要求进行详细探讨。
1. 数据采集要求首先,化工装置DCS系统对数据采集的要求十分严格。
在实际操作中,各种传感器、执行器等设备通过DCS系统进行数据采集,包括温度、压力、流量、液位等各种参数。
这些数据必须准确、全面地采集到系统中,并实时更新,以保证操作人员及时了解装置运行状态,确保生产过程的正常运行。
此外,数据采集的频率也是一个重要考量因素。
某些参数可能需要高频率的数据采集,以实时监测过程变化,及时调整控制策略;而另一些参数则可以适量降低采集频率,以减少数据传输和存储的压力。
2. 数据分析要求数据采集之后,数据分析是DCS技术的另一重要环节。
合理的数据分析可以帮助操作人员更好地了解生产过程中的各种变化,并及时做出反应。
在化工装置DCS系统中,数据分析主要包括以下几个方面的要求:(1)实时监测和故障诊断:DCS系统应具备实时监测功能,能够及时发现和诊断各种逾限、故障等异常情况,为操作人员提供及时的报警信息和处理建议。
(2)趋势分析和预测:DCS系统应能够对历史数据进行趋势分析,发现隐含的规律和趋势,并通过数据模型进行预测,帮助操作人员做出合理的生产决策。
(3)质量控制和工艺优化:通过对生产过程中的数据进行统计分析,可以实现质量控制和工艺优化,提高生产效率和产品质量。
3. 总结综上所述,数据采集与分析在化工装置DCS技术中的重要性不言而喻。
只有做好数据采集工作,才能为后续的数据分析提供可靠的数据基础;而正确的数据分析则可以帮助操作人员更好地掌握生产过程的变化,提高生产效率和产品质量。
因此,在化工装置DCS技术应用中,充分重视数据采集与分析要求,不仅是技术的需求,更是生产的需要。
基于MCGS系统的DCS总线接口的设计与实现

基于MCGS系统的DCS总线接口的设计与实现作者:吕涛李理来源:《现代电子技术》2008年第04期摘要:MCGS系统需要控制和处理多种现场设备。
介绍一种新型的DCS总线接口设备的硬、软件的设计与实现过程,该设备能够使MCGS组态软件接入DCS总线成为控制系统,实现信息采集、传输和控制功能。
该接口设备使用LPC213E作为微处理器,面向的DCS系统使用RS 485线路作为通信、驱动总线。
该总线接口在数据实时采集和监控中可以取得较好的控制效果。
关键词:DCS总线接口设备;MCGS RS485;LPC2136中图分类号:TP391.41文献标识码:B文章编号:1004—373X(2008)04—098—021 引言MCGS(Monitor and Control Generated System)是一套基于Windows平台,用于快速构造和生成上位机监控系统的组态软件系统,为用户提供解决实际工程问题的完整方案和开发平台,能够完成现场数据采集、实时和历史数据处理、报警和安全机制、流程控制、动画显示、趋势曲线和报表输出及企业监控网络等功能。
MCGS需要完成对现场设备或现场仪表的数据采集和控制功能,必须依靠现场总线和MCGS的载机进行通信。
而现场系统组成复杂,设备较多,设备间通信协议门类众多,繁简不一,因此研究与开发一种高效便利的总线接口技术,将具有很好的应用价值和市场前景。
本文主要讨论在MCGS系统中DCS总线接口设备的设计与实现。
2概述MCGS工控组态软件开发工具基于Windows操作平台,支持快速构造、生成工业设备驱动,具有良好的扩充能力。
具体地说,MCGS用Active DLL构件的方式实现设备驱动程序,通过规范的OLE接口挂接其中,无缝接入,构成一个整体。
设备驱动构件和MCGS运行在同一个进程,故运行速度快、可靠性高、数据流通顺畅、传输无延时,符合监控系统的要求。
OLE是一个可扩充的开放标准,只要遵守MCGS的接口规范,就可以使用VB,VC,Delphi等语言编制MCGS的设备驱动程序。
基于数据湖的实时数据管理平台设计
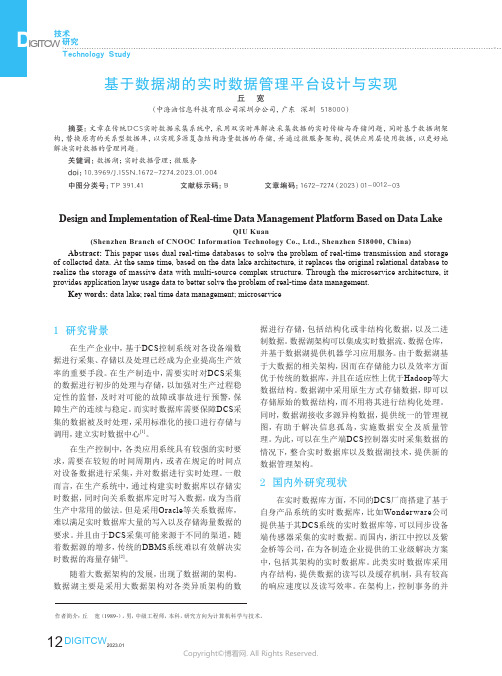
I G I T C W技术 研究Technology Study12DIGITCW2023.011 研究背景在生产企业中,基于DCS 控制系统对各设备端数据进行采集、存储以及处理已经成为企业提高生产效率的重要手段。
在生产制造中,需要实时对DCS 采集的数据进行初步的处理与存储,以加强对生产过程稳定性的监督,及时对可能的故障或事故进行预警,保障生产的连续与稳定。
而实时数据库需要保障DCS 采集的数据被及时处理,采用标准化的接口进行存储与调用,建立实时数据中心[1]。
在生产控制中,各类应用系统具有较强的实时要求,需要在较短的时间周期内,或者在规定的时间点对设备数据进行采集,并对数据进行实时处理。
一般而言,在生产系统中,通过构建实时数据库以存储实时数据,同时向关系数据库定时写入数据,成为当前生产中常用的做法。
但是采用Oracle 等关系数据库,难以满足实时数据库大量的写入以及存储海量数据的要求。
并且由于DCS 采集可能来源于不同的渠道,随着数据源的增多,传统的DBMS 系统难以有效解决实时数据的海量存储[2]。
随着大数据架构的发展,出现了数据湖的架构。
数据湖主要是采用大数据架构对各类异质架构的数据进行存储,包括结构化或非结构化数据,以及二进制数据。
数据湖架构可以集成实时数据流、数据仓库,并基于数据湖提供机器学习应用服务。
由于数据湖基于大数据的相关架构,因而在存储能力以及效率方面优于传统的数据库,并且在适应性上优于Hadoop 等大数据结构。
数据湖中采用原生方式存储数据,即可以存储原始的数据结构,而不用将其进行结构化处理。
同时,数据湖接收多源异构数据,提供统一的管理视图,有助于解决信息孤岛,实施数据安全及质量管理。
为此,可以在生产端DCS 控制器实时采集数据的情况下,整合实时数据库以及数据湖技术,提供新的数据管理架构。
2 国内外研究现状在实时数据库方面,不同的DCS 厂商搭建了基于自身产品系统的实时数据库,比如Wonderware 公司提供基于其DCS 系统的实时数据库等,可以同步设备端传感器采集的实时数据。
DCS系统在风能发电中的应用
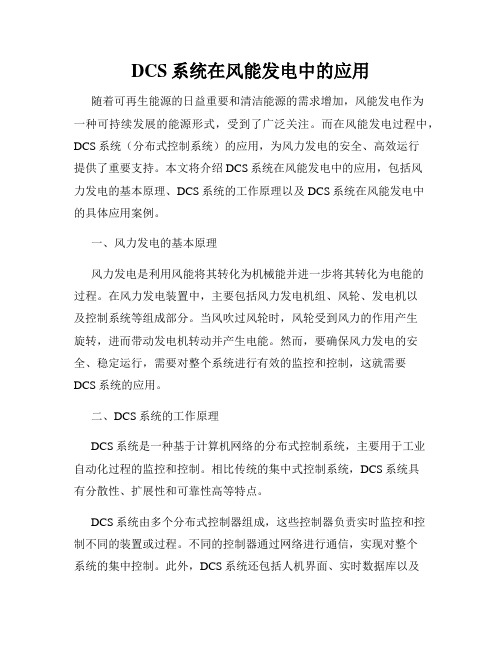
DCS系统在风能发电中的应用随着可再生能源的日益重要和清洁能源的需求增加,风能发电作为一种可持续发展的能源形式,受到了广泛关注。
而在风能发电过程中,DCS系统(分布式控制系统)的应用,为风力发电的安全、高效运行提供了重要支持。
本文将介绍DCS系统在风能发电中的应用,包括风力发电的基本原理、DCS系统的工作原理以及DCS系统在风能发电中的具体应用案例。
一、风力发电的基本原理风力发电是利用风能将其转化为机械能并进一步将其转化为电能的过程。
在风力发电装置中,主要包括风力发电机组、风轮、发电机以及控制系统等组成部分。
当风吹过风轮时,风轮受到风力的作用产生旋转,进而带动发电机转动并产生电能。
然而,要确保风力发电的安全、稳定运行,需要对整个系统进行有效的监控和控制,这就需要DCS系统的应用。
二、DCS系统的工作原理DCS系统是一种基于计算机网络的分布式控制系统,主要用于工业自动化过程的监控和控制。
相比传统的集中式控制系统,DCS系统具有分散性、扩展性和可靠性高等特点。
DCS系统由多个分布式控制器组成,这些控制器负责实时监控和控制不同的装置或过程。
不同的控制器通过网络进行通信,实现对整个系统的集中控制。
此外,DCS系统还包括人机界面、实时数据库以及数据采集等模块,通过这些模块可以实现对风能发电过程的参数监测、故障诊断以及运行状态分析等功能。
三、DCS系统在风能发电中的应用案例1. 远程监控与控制DCS系统可以通过远程监控技术,实现对风能发电机组的远程监测与控制。
运维人员可以通过互联网或专用通信网络,远程监控风能发电系统的运行状态、实时数据以及设备状态等信息。
一旦发现异常情况,如风能发电机组运行异常或设备故障,可以及时发出警报并采取相应措施。
通过远程监控与控制,可以提高风力发电的可靠性和运行效率。
2. 故障诊断与维修DCS系统可以通过对风能发电系统中的故障诊断与数据分析,帮助运维人员及时发现故障并进行维修。
通过DCS系统采集的实时数据,可以对风能发电系统的运行状态进行分析,判断设备是否存在故障或潜在问题。
- 1、下载文档前请自行甄别文档内容的完整性,平台不提供额外的编辑、内容补充、找答案等附加服务。
- 2、"仅部分预览"的文档,不可在线预览部分如存在完整性等问题,可反馈申请退款(可完整预览的文档不适用该条件!)。
- 3、如文档侵犯您的权益,请联系客服反馈,我们会尽快为您处理(人工客服工作时间:9:00-18:30)。
,以及面向行业应用的突出特点,目前已经广泛地应用于军事国防、消费电子、网络通信、工业控制等各个领域。伴随着网络时代的来临在高端嵌入式应用中,32位微处理器的应用将成为主流,以ARM为内核的微处理器就是其中一种被广泛应用RISC(精简指令集计算机)芯片。
本文概述了工业控制自动化技术和现场总线的产生、类型以及优点,并对其中的控制器局域网CAN(Controller Aera Network)总线进行分析,论述了CAN总线的应用,结构及协议。依托一种基于CAN协议通信的嵌入式监控系统为研究对象,在ARM芯片可扩展的CAN接口基础上,构建CAN网络嵌入式智能监控节点,实现了节点与上位机的数据通信,提高了监控系统的实时性和可靠性,对其硬件和软件进行了描述,并介绍了相关的CAN器件。
9.学位论文王静漪广播发射机分布式计算机监控系统设计1998
针对广播发射台强电磁环境,该文提出了一种运用STD总线技术和分布式计算机控制技术,对广播发射机实现自动实时控制的系统.该系统由一台PC机(上位机)和4台STD工业控制机(下位机)组成.利用BITBUS通信网实现上、下位机之间的数据交换.在上位机中,将WINDOWS操作系统作为软件运行环境,充分利用其良好的图形界面和动态链接库技术开发了上位机控制程序.在强调上位机管理的同时,加强了下位机独立工作能力,使下位机完成了定时开关机、故障报警与倒机、数据采集与存档、键控等功能.从而使整个系统实现了对4台发射机进行分布测控和集中管理.该文对系统的设计思想和软硬件结构做了详细的阐述.研究人员进行了大量实验和多次现场调度.广播发射机对系统的干扰是非常严重的.因此,在设计中采取了多种干扰措施,效果良好.一套机器在联机测试中已正常运行.这为今后的工作奠定了基础.
北京化工大学
硕士学位论文
基于DCS的数据采集接口及实时数据库研究与应用
姓名:温泉
申请学位级别:硕士
专业:计算机应用技术
指导教师:靳其兵
20090530
基于DCS的数据采集接口及实时数据库研究与应用
10.期刊论文李川香.李池水.Li ChanxiangБайду номын сангаасLi Chishui直流系统绝缘在线监测智能控制-武汉工业大学学报
2000,22(4)
分析了以MCS-51系列单片机为核心,采用12位并行A/D转换器,组成一个多路并行数据采集作为下位机,通过RS-485串行口进行数据传输,实现直流系统绝缘在线监测集散控制.
6.学位论文李四明基于DCS的锅炉控制系统的研究2004
该课题来源于大连海事大学的锅炉房改建工程.以锅炉控制系统为研究对象,根据当前集散控制系统的发展方向与形式,设计开发网络化分布式集散监控系统.论文根据锅炉房现场的特点,介绍了集散系统的基本结构和锅炉系统的组成和工作原理,系统分析了影响集散控制系统安全性与可靠性的诸多因素,提出了相应的对策;分析了集散控制系统的特点,组成.针对锅炉房现场中各个传感器以及输入设备之间数据通信的特点,以及有利于原有技术的继承和改造的特点,确定出集散控制系统的结构.并且根据系统的需要确定了系统的开发软件和硬件的选型;分析了锅炉控制对象的特点和基本的控制过程,根据计算机监控系统应满足的各项功能要求,设计完成计算机监控系统中数据采集,上下位机通讯及上位机管理子系统.论文基于对集散系统设计的总体分析和设计要点,根据实际的锅炉房的参数要求设计出集散控制系统,并把它用于大连海事大学的锅炉改造工程.并且根据现场实际应用的结果,提出了系统存在的不足以及可行的改进的方法.
本文链接:/Thesis_Y1557783.aspx
授权使用:北京理工大学(北京理工大学),授权号:06bcd7b6-977d-4d27-8ad1-9dfa0140ee13
下载时间:2010年9月23日
7.会议论文李柱权一种新型数据采集和控制系统——LONWORKS1996
8.学位论文姚圣卓粮库温度巡检系统的设计1998
目前,工业测控系统是向集散式系统这一趋势发展的,它摆脱了工业测控仅局限于单片机控制的束缚,实现多机互联的网络结构.通常由一台PC微机计算作管理和控制中心,携带多台单片机采集系统,协同工作,做到真正意义上的集中管理、分散控制,尤其适用于大规模、大范围的多点测控.该文以设计开发粮库温度巡检系统为目的,着重论述了集散控制思想在该系统中的应用,其中,涉及到的关键性技术都给予了比较详尺的分析和说明,力图从根本上阐述各项技术措施的重要性和必要性.全文主要内容分三部分:第一部分介绍了现代工业测控系统的特点,粮温巡检的目的和意义,并通过分析给出了设计框架和使用到的技术手段;第二部分给出了系统的硬件电路设计主要从多机通讯、数据采集以及抗干扰能力方面加以论述、剖析;第三部分给出了系统的软件设计,主要从通讯协议建立、对Windows编程技术以及该软件功能等方面加以介绍,并给出了主要程序的流程框图.另外,该文还就系统的改进措施及应用等方面作了简要的叙述.
实际问题往往千差万别,但是通过本课题的研究工作,希望能为开发性能良好的真空炉集散控制系统提供一条有效的参考途径。
2.期刊论文李涛.陈宇.刘镇基于集散控制的智能型柴油机稳流气道试验系统设计-仪表技术与传感器2004,""(7) 在柴油机气缸设计和检验中都需要使用稳流气道试验系统对气缸的气道进行试验.过去柴油机稳流气道试验主要采用人工方法测量相关参数,无法进行精确和快速的测量.介绍了一种智能型稳流气道试验系统,该系统采用集散控制实现了数据采集和控制过程的自动化,通过串行接口实现了上位机与下位机的通信,且有效地抑制了干扰,同时开发了一套处理软件对数据进行及时有效的处理,并提供了友好的用户界面.
本文采用32位ARM7核的芯片LPC2290为主控制器,完成系统的硬件电路设计;系统引入了嵌入式实时操作系统μC/OS-Ⅱ,实现在ADS编译环境下完成μC/OS-Ⅱ的移植,最后通过μC/OS-Ⅱ来完成任务调度:基于集成CAN控制器的ARM7芯片组建现场监控网络,充分发挥了32位控制器的优势,实现了基于ARM的CAN网络通信:最终完成工控现场数据采集系统的应用研究。
作者:温泉
学位授予单位:北京化工大学
1.学位论文李希涛真空炉集散控制技术研究2006
计算机技术、控制技术和通信技术的发展,为实现高水平自动化提供了强有力的技术工具,给生产过程自动化的发展带来了深远的影响。工业控制系统已经从常规仪表和继电器逻辑控制系统发展到了PLC和集散控制系统(DCS),在基础自动化级和过程控制管理级普遍采用计算机网络技术,工业自动化进入到计算机集成系统时代。
3.学位论文谢志丹基于CAN总线工控现场数据采集处理系统的研制2008
在工业过程控制领域,计算机控制占主导地位。其阶段己从集中控制,集散控制发展到现场总线控制。现场总线是当今自动化领域技术发展的一个热点,被誉为自动化领域的计算机局域网。它的出现,标志着工业控制技术领域又一个新时代的开始,并对该领域的发展产生了重要的影响。控制器局域网CAN(Controller Aera Network)属于现场总线的范畴,CAN总线的数据通信具有极高的可靠性、实时性和灵活性的特点,是一种有效支持集散控制系统和实时控制的多主串行总线。CAN作为一种新兴的总线技术,具有高性能、高可靠性的特点,以其为基础构成的分布式网络方便、低成本地实现了工程实际要求。
4.会议论文张俊波集散控制中的数据采集系统1994
5.期刊论文包广清.骆东松.毛开富农业种植大棚计算机集散控制系统研究-工业控制计算机2002,15(2)
针对现代农业种植大棚的发展要求,本系统以89C52单片机和32位微机为核心,通过对大型联体温室大棚内各种环境参数的实时监控,自动调节大棚气候因子,为种植作物提供最佳生长发育环境,可广泛适用于各种类型的农业种植大棚。
本课题的主要内容是对真空炉集散控制系统的开发流程和使用性能进行研究。具体包括控制系统的总体设计、软硬件选择和架构、系统优化、安装调试等内容。整个系统可以分为三个部分:上位机(PC)和下位机(PLC),另外还包括通信线、电缆、各类仪表等配套设备。上位机与下位机之间通过RS-232/422进行通讯,把上位机编制的程序和控制指令下载到PLC中,同时把PLC中的数据传递给上位机显示、存储。上位机与温控仪之间采用RS-232/422进行通讯,可以把温度曲线号、PID控制参数、报警方式等指令发送给温控仪,温控仪可以把当前的温度值反馈到上位机。上位机软件开发采用可视化编程工具VB6.0,利用面向对象的软件开发思想设计,程序包含数据处理、参数显示、控制调整、安全报警等模块。下位机程序编制使用PLC自带软件包,程序主要完成数据采集、转换、传递任务以及实现各种工艺控制、连锁保护等控制回路功能。最后,总结了控制系统应用的效果并提出未来的技术发展方向。