活性染料Rf值和织物回潮率对轧染色差的影响
活性染料的性能指标及测定方法溶解性高品质的活性染料商品应
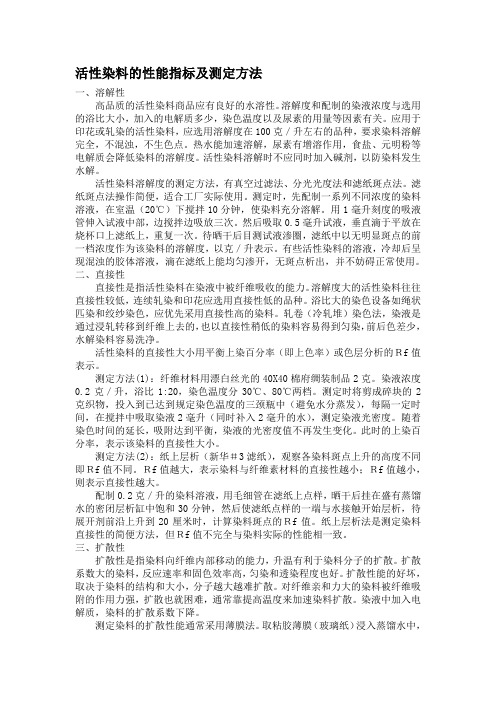
活性染料的性能指标及测定方法一、溶解性高品质的活性染料商品应有良好的水溶性。
溶解度和配制的染液浓度与选用的浴比大小,加入的电解质多少,染色温度以及尿素的用量等因素有关。
应用于印花或轧染的活性染料,应选用溶解度在100克/升左右的品种,要求染料溶解完全,不混浊,不生色点。
热水能加速溶解,尿素有增溶作用,食盐、元明粉等电解质会降低染料的溶解度。
活性染料溶解时不应同时加入碱剂,以防染料发生水解。
活性染料溶解度的测定方法,有真空过滤法、分光光度法和滤纸斑点法。
滤纸斑点法操作简便,适合工厂实际使用。
测定时,先配制一系列不同浓度的染料溶液,在室温(20℃)下搅拌10分钟,使染料充分溶解。
用1毫升刻度的吸液管伸入试液中部,边搅拌边吸放三次。
然后吸取0.5毫升试液,垂直滴于平放在烧杯口上滤纸上,重复一次。
待晒干后目测试液渗圈,滤纸中以无明显斑点的前一档浓度作为该染料的溶解度,以克/升表示。
有些活性染料的溶液,冷却后呈现混浊的胶体溶液,滴在滤纸上能均匀渗开,无斑点析出,并不妨碍正常使用。
二、直接性直接性是指活性染料在染液中被纤维吸收的能力。
溶解度大的活性染料往往直接性较低,连续轧染和印花应选用直接性低的品种。
浴比大的染色设备如绳状匹染和绞纱染色,应优先采用直接性高的染料。
轧卷(冷轧堆)染色法,染液是通过浸轧转移到纤维上去的,也以直接性稍低的染料容易得到匀染,前后色差少,水解染料容易洗净。
活性染料的直接性大小用平衡上染百分率(即上色率)或色层分析的Rf值表示。
测定方法(1):纤维材料用漂白丝光的40X40棉府绸装制品2克。
染液浓度0.2克/升,浴比1:20,染色温度分30℃、80℃两档。
测定时将剪成碎块的2克织物,投入到已达到规定染色温度的三颈瓶中(避免水分蒸发),每隔一定时间,在搅拌中吸取染液2毫升(同时补入2毫升的水),测定染液光密度。
随着染色时间的延长,吸附达到平衡,染液的光密度值不再发生变化。
此时的上染百分率,表示该染料的直接性大小。
轧染色差的原因及预防措施
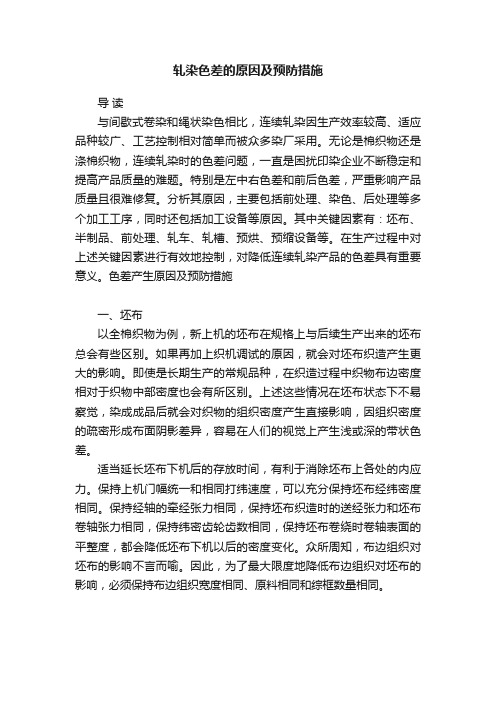
轧染色差的原因及预防措施导读与间歇式卷染和绳状染色相比,连续轧染因生产效率较高、适应品种较广、工艺控制相对简单而被众多染厂采用。
无论是棉织物还是涤棉织物,连续轧染时的色差问题,一直是困扰印染企业不断稳定和提高产品质量的难题。
特别是左中右色差和前后色差,严重影响产品质量且很难修复。
分析其原因,主要包括前处理、染色、后处理等多个加工工序,同时还包括加工设备等原因。
其中关键因素有:坯布、半制品、前处理、轧车、轧槽、预烘、预缩设备等。
在生产过程中对上述关键因素进行有效地控制,对降低连续轧染产品的色差具有重要意义。
色差产生原因及预防措施一、坯布以全棉织物为例,新上机的坯布在规格上与后续生产出来的坯布总会有些区别。
如果再加上织机调试的原因,就会对坯布织造产生更大的影响。
即使是长期生产的常规品种,在织造过程中织物布边密度相对于织物中部密度也会有所区别。
上述这些情况在坯布状态下不易察觉,染成成品后就会对织物的组织密度产生直接影响,因组织密度的疏密形成布面阴影差异,容易在人们的视觉上产生浅或深的带状色差。
适当延长坯布下机后的存放时间,有利于消除坯布上各处的内应力。
保持上机门幅统一和相同打纬速度,可以充分保持坯布经纬密度相同。
保持经轴的牵经张力相同,保持坯布织造时的送经张力和坯布卷轴张力相同,保持纬密齿轮齿数相同,保持坯布卷绕时卷轴表面的平整度,都会降低坯布下机以后的密度变化。
众所周知,布边组织对坯布的影响不言而喻。
因此,为了最大限度地降低布边组织对坯布的影响,必须保持布边组织宽度相同、原料相同和综框数量相同。
二、半制品半制品的加工质量对成品质量的影响远远大于染色工序本身。
所以,从坯布准备开始,翻布、打印、缝头等准备工序的每次加工都会影响棉织物练漂的加工质量。
烧毛、退浆、煮练、漂白、丝光、轧水和烘干工序都可以决定染色质量。
半制品质量问题通常会在染色才体现出来,因此,严格控制棉织物前处理加工各工序的工艺参数、工艺配方和工艺流程就显得非常重要。
活性染料的性能
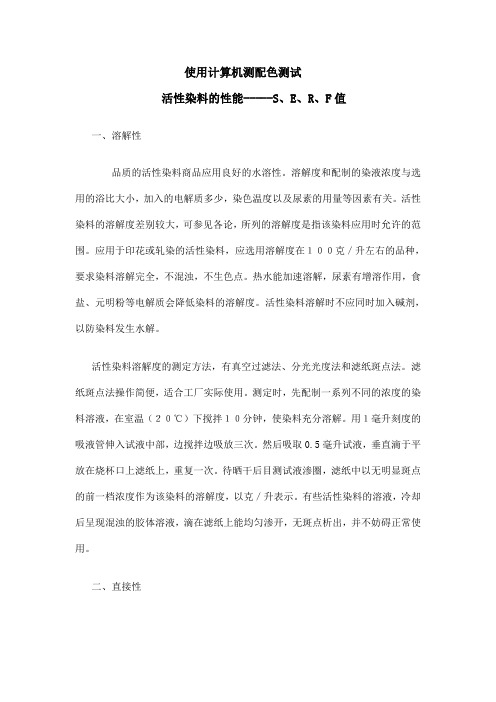
使用计算机测配色测试活性染料的性能-----S、E、R、F值一、溶解性品质的活性染料商品应用良好的水溶性。
溶解度和配制的染液浓度与选用的浴比大小,加入的电解质多少,染色温度以及尿素的用量等因素有关。
活性染料的溶解度差别较大,可参见各论,所列的溶解度是指该染料应用时允许的范围。
应用于印花或轧染的活性染料,应选用溶解度在100克/升左右的品种,要求染料溶解完全,不混浊,不生色点。
热水能加速溶解,尿素有增溶作用,食盐、元明粉等电解质会降低染料的溶解度。
活性染料溶解时不应同时加入碱剂,以防染料发生水解。
活性染料溶解度的测定方法,有真空过滤法、分光光度法和滤纸斑点法。
滤纸斑点法操作简便,适合工厂实际使用。
测定时,先配制一系列不同的浓度的染料溶液,在室温(20℃)下搅拌10分钟,使染料充分溶解。
用1毫升刻度的吸液管伸入试液中部,边搅拌边吸放三次。
然后吸取0.5毫升试液,垂直滴于平放在烧杯口上滤纸上,重复一次。
待晒干后目测试液渗圈,滤纸中以无明显斑点的前一档浓度作为该染料的溶解度,以克/升表示。
有些活性染料的溶液,冷却后呈现混浊的胶体溶液,滴在滤纸上能均匀渗开,无斑点析出,并不妨碍正常使用。
二、直接性直接性是指活性染料在染液中被纤维吸收的能力。
溶解度大的活性染料往往直接性较低,连续轧染和印花应选用直接性低的品种。
浴比大的染色设备如绳状匹染和绞纱染色,应优先采用直接性高的染料。
轧卷(冷轧堆)染色法,染液是通过浸轧转移到纤维上去的,也以直接性稍低的染料容易得到匀染,前后色差少,水解染料容易洗净。
活性染料的直接性大小用平衡上染百分率(即上色率)或色层分析的Rf值表示。
测定方法(1):纤维材料用漂白丝光的40X40棉府绸装制品2克。
染液浓度0. 2克/升,浴比20:1,染色温度分30℃、80℃两档。
测定时将剪成碎块的2克织物,投入到已达到规定染色温度的三颈瓶中(避免水分蒸发),每隔一定时间,在搅拌中吸取染液2毫升(同时补入2毫升的水),测定染液光密度。
技术中温型活性翠蓝浸染染色,为什么容易产生色点、色渍染疵?该如何预防?

技术中温型活性翠蓝浸染染色,为什么容易产生色点、色渍染疵?该如何预防?1产生原因中温型活性翠蓝浸染染色时,之所以容易产生色点、色渍染疵,是由于活性翠蓝存在耐盐、碱溶解稳定性差的缺陷所致。
中温型活性翠蓝在电解质的常规浓度(<80g/L)下,耐盐溶解稳定性尚好。
染料的凝聚程度不足以危害染色质量。
在纯碱的常规浓度(<25g/L)下,耐碱溶解稳定性良好, 染料的聚集不明显。
但在盐、碱共存的固色液中,其溶解稳定性则会大幅度下降。
经检测,固色浴中的盐、碱混合浓度,一旦>80g/L,染液中的染料不仅会发生显著甚至严重的“絮聚”,而且会在染液液面形成含有染料絮聚体的大量泡沫。
这些泡沫一旦黏附到织物上,便会造成色点色渍染疵。
导致活性翠蓝在固色浴中产生絮聚的原因有以下两个:①在固色浴中盐、碱共存(纯碱也是电解质),使染液中的钠离子(Na+)浓度大幅度提高方面,由于同离子效应的影响,使染料中的亲水性基团电离度变小,从而导致染料的亲水性下降。
D-SO3 Na←→D-SO3+Na亲水性较弱亲水性较强另一方面,由于Na+具有较大的水合能力,它能以直接或间接水化层的形式吸附大量极性水分子,从而对已溶解的染料产生较大的盐析作用。
②在碱性浴中,染料中的β羟乙基砜硫酸酯活性基,会发生消去反应,硫酸酯基脱落,变为乙烯砜基。
从而使原本亲水性的基团变为疏水性基团,使染料自身的水溶性显著下降。
染料的亲水性骤然变小,受水的排斥力骤然增大,水中的染料为求得稳定而发生相互聚集。
2预防的措施电解质的施加①.施加浓度。
活性翠蓝的水溶性高。
在80℃的软化水中,其溶解度可达150g (注:活性翠蓝与其他活性染料有所不同,其染液的胶凝性十分突出,但与染料的凝聚性有着本质的区别,它不会因此产生色点、色渍染疵)。
所以,其竭染率受电解质的制约性较大,只有在较多电解质的存在下染色,才能获得较高的上染量。
然而,电解质浓度必须适当。
倘若浓度过高,最终的平衡上染率提高不明显,反而会使固色液的盐、碱混合浓度超高(>80g/L),导致染料发生过度凝聚,产生色点、色渍危害染色质量。
活性染料染全棉织物中常见疵病及预防措施

活性染料染全棉织物中常见疵病及预防措施1前言棉织物尤其是高档针织物用活性染料染色十分广阔,从目前形式看高质量、低成本、快速交货是工厂赖以生存的基础,因此如何减少棉织物的病疵,是我们的首要考虑因素。
然而要减少疵病的产生,不仅要考虑棉织物的质量,活性染料的好坏还必须要考虑到助剂、温度、PH值等多重因素。
本文对活性染料染棉织物常出现的病庛进行分析,并由此提出措施和方法[1]。
1.1活性染料的特点活性染料是在化学结构上带反应性基团的水溶性染料,在染色过程中,染料与纤维发生反应,最终生成共价键(酯和醚键),活性染料具有水溶性和直接性,根据结构不同又可分为X型、K型、KN型等,特点如下:(1)吸湿性能优良、手感柔软、穿着舒服(2)湿态强度大于干态强度,但整体上坚牢耐用(3)染色性能好,光泽柔和,有自然美感(4)耐碱,耐高温(5)抗皱性差,缩水率大1.2棉织物的特点棉织物是指以棉纱或棉型化纤混纺纱线织成的纺织品,特点如下:(1) 吸湿性能强,缩水率比较大,约为4%~10%(2)耐酸,织物对无机酸很不稳定,即使较弱的酸也会使棉织物受到破坏,但有机酸对棉织物作用微弱,几乎起不到破坏作用。
棉织物比较耐碱,一般弱碱在常温下对棉布不发生作用,但强碱作用后,棉布强度会下降。
常利用20%的烧碱液处理棉布,可得到“丝光”棉布。
(3)耐热性能一般,在阳光与大气中棉织物会缓慢地被氧化,使强力下降。
长期高温作用会使棉织物遭受破坏,但棉织物可以耐受125℃~150℃短暂高温处理。
(4)微生物对棉织物有破坏作用,表现在棉织物不耐霉菌。
1.3活性染料的染色理论染料之所以在较短时间内会如此快速的上染,是因为在活性染料中存在可与纤维发生反应的活性基。
活性染料的结构有别于其他染料,它们的结构可用下面的通式表示:S-D-B-R式中:S是水溶性基团;D为染料母体;B为桥基;R为活性基。
活性基是活性染料的核心,染色通过它与纤维发生化学键合,这一部分决定了活性染料的反应活性、固色率、色牢度和应用条件。
学习│回潮率的定义以及对染色面料的影响
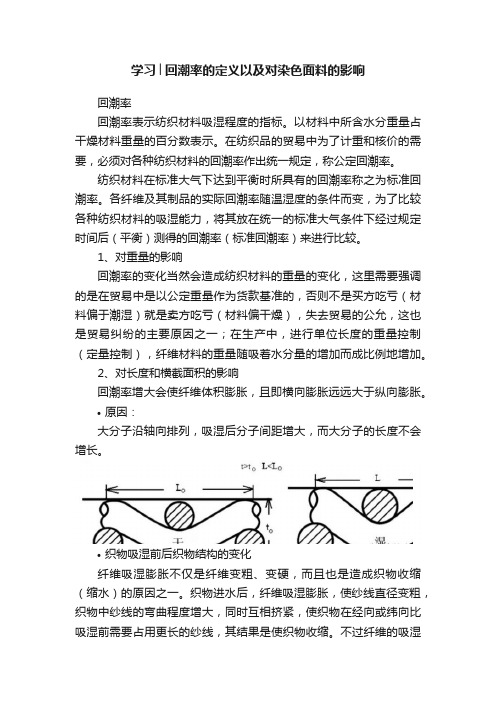
学习│回潮率的定义以及对染色面料的影响回潮率回潮率表示纺织材料吸湿程度的指标。
以材料中所含水分重量占干燥材料重量的百分数表示。
在纺织品的贸易中为了计重和核价的需要,必须对各种纺织材料的回潮率作出统一规定,称公定回潮率。
纺织材料在标准大气下达到平衡时所具有的回潮率称之为标准回潮率。
各纤维及其制品的实际回潮率随温湿度的条件而变,为了比较各种纺织材料的吸湿能力,将其放在统一的标准大气条件下经过规定时间后(平衡)测得的回潮率(标准回潮率)来进行比较。
1、对重量的影响回潮率的变化当然会造成纺织材料的重量的变化,这里需要强调的是在贸易中是以公定重量作为货款基准的,否则不是买方吃亏(材料偏于潮湿)就是卖方吃亏(材料偏干燥),失去贸易的公允,这也是贸易纠纷的主要原因之一;在生产中,进行单位长度的重量控制(定量控制),纤维材料的重量随吸着水分量的增加而成比例地增加。
2、对长度和横截面积的影响回潮率增大会使纤维体积膨胀,且即横向膨胀远远大于纵向膨胀。
•原因:大分子沿轴向排列,吸湿后分子间距增大,而大分子的长度不会增长。
•织物吸湿前后织物结构的变化纤维吸湿膨胀不仅是纤维变粗、变硬,而且也是造成织物收缩(缩水)的原因之一。
织物进水后,纤维吸湿膨胀,使纱线直径变粗,织物中纱线的弯曲程度增大,同时互相挤紧,使织物在经向或纬向比吸湿前需要占用更长的纱线,其结果是使织物收缩。
不过纤维的吸湿膨胀也有有利的一面,如水龙带和雨衣可以利用它们遇水后纤维吸湿变粗使织物更加紧密,而使水更难通过。
膨胀在织物的起皱、干燥和染色等工艺过程中也是一个重要因素。
3、对密度的影响从上图可以看出。
纤维的密度随着回潮率的增加密度先上升而后下降。
4、对机械性质的影响对于大多数纤维而言,其强力随着回潮率的增加而下降,少数纤维几乎不变,个别纤维(棉、麻)的强力上升。
绝大多数纤维的断裂伸长率随着回潮率的增加而上升,少数纤维几乎不变。
这主要由于水分子进入之后拆开了大分子之间的交联,分子间力减小,大分子易滑脱,故强力降低。
活性染料Rf值和织物回潮率对轧染色差的影响
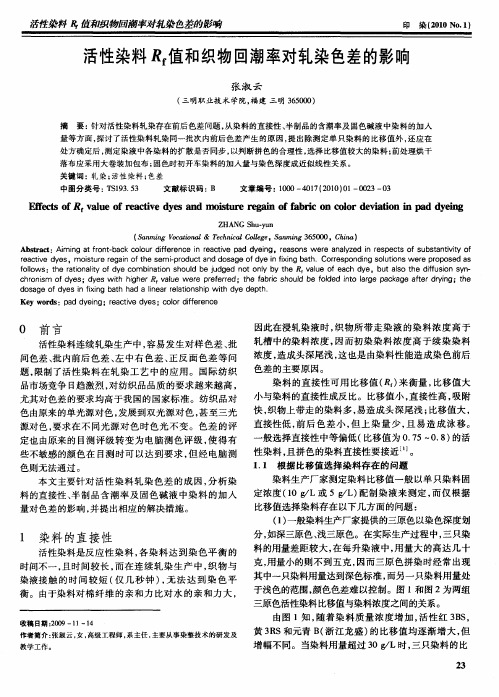
flws tert n l f y o i t ns o l b d e o n yteR au fe c y 。b ta o ted u i y— ol o : h ai ai o ec mbn i h ud ej g d n to l b h f l o a hd e u l h i s ns n o t y d ao u y v e s f o
题, 限制 了活性 染 料 在 轧染 工 艺 中 的应 用 。 国际 纺 织 色 差 的主要原 因 。 染 料 的直 接性 可 用 比移 值 ( ) 衡 量 , 蜀 来 比移 值 大 品市场竞 争 日趋 激烈 , 纺织 品品质 的要 求 越来 越 高 , 对 直 吸 尤其 对色 差 的要 求均 高于 我 国的 国家标 准 。纺 织 品对 小 与染料 的直 接性 成反 比。 比移值 小 , 接性 高 , 附 织物 上带走 的染料 多 , 易造成 头 深尾 浅 ; 比移 值大 , 色 由原来 的单光 源对 色 , 发展 到双 光 源对 色 , 至三 光 快 , 甚
d s g fd e n f ig b t a i e rr lt n hp w i y e t . o a e o y s i i n a h h d a l a ea i s i t d e d p h x n o h Ke r s:p d d e n y wo d a y ig;r a t e d e e c i y s;c l i e e c v oor f r n e d f
前 但 且 源对 色 , 求在 不 同光源 对 色 时 色 光 不 变 。色 差 的评 直 接性低 , 后 色 差 小 , 上 染 量 少 , 易 造 成 泳 移 。 要 般选择 直接性 中等偏低 ( 比移值 为 0 7 0 8 的 活 .5— . ) 定 也 由原 来 的 目测评 级 转 变 为 电脑 测 色 评 级 , 得 有 使
活性染料染深色的色差控制
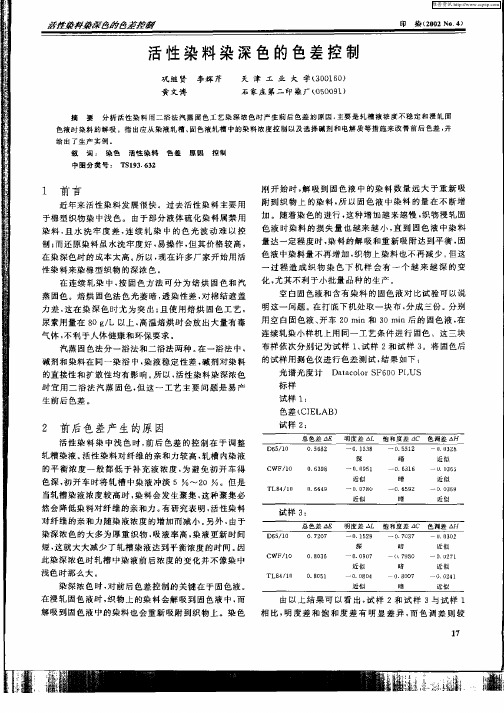
过 程造 成 织物 染 色下 机样 会 有 一 个 越 来 越 深 的变 空 白固色 液和 含有染 料 的固色 液对 比试验 可 以说
化 , 其不 利 于小批量 品种 的生产 。 尤
力 差 , 在染 深 色 时 尤 为突 出 ; 使用 焙 烘 固色 工艺 , 这 且
尿素用 量在 8 / 0g L以上 , 高温 焙烘 时 会放 出大 量有毒 气 体 , 利 于人体健 康 和环保 要求 。 不
汽 蒸 固色法 分一 浴法 和二 浴法两种 。 一 浴法 中 , 在
明这一 问题 。在打底 下机 处取 一块 布 , 分成 三份 。分别 用空 白固色 液 、 车 2 n和 3 n后 的 固色 液 , 开 0mi 0mi 在 连续 轧染小样 机 上用 同一 工 艺条 件进 行 固色 。这 三块 布样 依次 分别 记为试 样 1 试样 2和试 样 3 、 。将 固色后 的试 样用 测色 仪进行 色差 测试 , 结果 如 下 : 光 谱光 度计
刷 开始 时 , 吸 到 固色 液 中 的染 料 数 量远 大 于重 新 吸 解 附 到织 物 上 的染 料 , 以 固色 液 中染 料 的量 在不 断增 所 加 。随着染 色的进行 , 这种增 加 越 来越慢 , 物浸 轧 固 织 色 液 时染 料 的损 失 量 也 越来 越 小 , 到 固色 液 中 染料 直 量达 一定 程 度时 , 料 的解 吸和 重新 吸 附达 到平 衡 , 染 固 色液 中染料 量 不再增 加 , 织物上 染料 也不 再减 少 但这
4 2 工 艺 流 程 .
3 控 制前 后色 差 的方 法
3 1 初开 车染液 轧槽 冲淡 . 上述 已分 析 了染 深 浓色 时 , 槽 中染 液 的前 后 浓 轧
活性染料轧染工艺研究与实践

活性染料轧染工艺研究与实践17/5/7 8:21:05--> 一、织物预备活性染料轧一烘_车L一蒸连续染色工艺流程为:浸轧染液一红外预烘一热风烘干和烘筒烘干一浸轧固色液一汽蒸一洗涤(去除残余化学品和水解染料)一烘干1.1 半成品半成品必需不含润滑剂、浆料和漂白剂,而且要求白度全都,吸湿性好,pH值中性。
织物左、中、右含潮率全都,布面完全冷却。
通过渗圈试验可以检查织物的吸湿性。
其方法为:用5 dE 锡丽翠蓝(SiriusTurquoise)S-FBL溶液滴一滴在织物表面,1~5 S 后观看渗圈外形(检验时间视织物而定),假如渗圈外形圆形,表示前处理效果较好;假如渗圈外形不规章,说明前处理效果较差。
1.2 碘/碘化钾溶液检查淀粉浆用TEGEWA卡评级,共分为9级。
织物含淀粉及其衍生物显示深蓝色,织物含淀粉、PVA浆料、上浆剂等显示蓝绿色,其中9级为不含淀粉,6级为染色可接受。
1.3 pH 值染色工艺用水水质要求无色、无味、pH值7~8,硬度(德弗硬度)小于3。
~5。
(5O~90 mg/kg,USA),化料时肯定要用软水。
二、染料配伍性和芯吸试验 2.1 活性染料吸尽率和固色率活性染料染色存在的技术问题主要是提高吸尽率和固色率,最有效方法是在活性染料分子中引入两个异种或同种活性基,即一氯均三嗪基和乙烯砜基。
对于用含两个异种活性基和合适的母体染料与连接基组成的新型活性染料来说,除了具有各个组成活性基的特性(如低的酸性水解率、优良的可洗涤性、良好的色牢度和较小的吸尽率与固色率之差)外,还具有这两个不同活性基之间的协同增效作用,而产生的新特性,如更好的耐酸性水解和过氧化物洗涤的力量、更高的固色率、更宽的染色温度范围和更好的染色重现性。
因此,这类活性染料的产量已占全部染色用活性染料的2/3,已成为棉织物轧染的主体染料。
2.2 染料的配伍性染料的配伍性是指拼色时一组染料在纤维中集中的快慢和染料对纤维的亲和力大小的差异。
针织棉活性浅色容易出现色渍的原因方法及避免方案

针织棉活性浅色容易出现色渍的原因方法及避免方案获取最新印染资讯印染技术招聘信息活性染料染色牢度较好、色谱齐全、色泽艳丽,广泛应用于纯棉针织物的染色。
在生产中,深色(黑、深灰、藏青、咖啡等)染色发生色差的概率要比浅色大;三拼色发生色差的概率要比二拼色或单色大。
因此,色差与染料的性能及染料之间的配伍性有密切关系,同时还与染色前布面质量、工艺条件的合理性有关。
1前处理前处理的目的是为了改善织物的毛效、白度,以利于染料均匀快速地上染纤维。
通过对进布顺序、时间、加料方式及水洗流程的合理设计,可获得均匀的毛效、白度、PH值等。
2染料由于二拼色或三拼色大多易产生色差,所以,分析染料之间的配伍性,对减少色差有重要意义。
可通过渗圈实验法对染料进行初步筛选,选择提升力相近的染料。
另外,所拼染料的上染率曲线相近与否,对色差也有一定影响,上染率曲线相近的染料,其配伍性要好一些。
3加料及升温曲线活性染料染色过程分三个阶段:吸附、扩散、固着。
4染色设备纯棉针织物的染色大多采用溢流喷射绳状染色机。
大多数染色机的主泵流量、喷嘴压力可调,每管布速可独立控制,因此,可根据不同织物的结构特点(如薄与厚、紧与疏、每管布的长与短),对流量、压力、布速进行调节,以形成最佳的染色条件。
由于染液在染色机内的循环速度决定染料分子与棉纤维的接触频率,接触频率越高越有利于匀染,所以,加快织物在染色机内循环的速度,加大主泵的流量,提高喷嘴压力,都能在一定程度上减少色差的产生。
但这些工艺参数不可能被无限量提高,而且会在一定程度上损伤织物强力,需在实践中摸索出一个最佳的结合点,才能获得一个合适的工艺。
5染色助剂1、匀染剂染浅色时需要使用一定的匀染剂,以达到均匀染色;而染深色时,则不必加入匀染剂。
在生产中,三拼色往往以一种染料为基色(占总染料用量的80%~90%),另外两种染料为辅助色(占总染料量的10%~20%)。
若将基色去除,另外两种染料其实就是浅色用量,因此,在一些易出现色差的颜色中,使用一定比例的匀染剂,对减少色差是有帮助的。
干货活性染料染棉色泽较深较暗,色泽不亮,碱剂、氧漂、氯漂减色处理技术工艺

干货活性染料染棉色泽较深较暗,色泽不亮,碱剂、氧漂、氯漂减色处理技术工艺棉织物经活性染料染色后,倘若色泽较深、较暗或光头较足,直接“加色”修色会导致色泽更深。
所以,只能采用先“减色”再加色的方法进行修色。
即先将色泽减浅,再根据需要加色修色。
1碱剂减色法此法是将准备修色的织物,在纯碱或烧碱的沸温溶液中进行处理。
1、碱剂减色原理活性染料与棉纤维之间在染色过程中形成的化学结合键,在高温碱性浴中会发生不同程度的水解断键,原本固着在纤维上的染料会脱落下来,而产生减色(变浅)效果。
有些活性染料在高温碱性浴中,不仅发生断键落色,染料母体中的发色团也会产生破坏而消色。
染料-纤维结合键的耐酸碱稳定性(表1)表1 活性染料-纤维素纤维结合键的耐酸碱稳定性注:① 染料用量1%(owf);② 处理条件:浴比l:60,红外线染样机;100℃处理60min,水洗,二次高温皂洗、水洗、烘干;Datacolor SF 600X测色仪测染色物的相对得色深度。
③ pH值以冰醋酸和烧碱液调整。
结果分析:❶在常用中温型活性染料中,无论是带乙烯砜活性基的染料,或带一氯均三嗪活性基的染料,还是带异双活性基的染料,其耐酸稳定性都远远高于耐碱稳定性。
❷活性艳蓝KN-R、活性翠蓝B-BGFN等乙烯砜型染料和活性红M-3BE等异双活性基染料,在碱性条件下处理,染色物的表面色深会严重变浅,而处理残液的色泽也相应变深。
这表明,这两种类型的染料在碱性条件下所发生的化学变化,主要是染料.纤维结合键水解断裂,从而导致大量染料溶落。
❸以B-6GLN为代表的活性嫩黄却与众不同。
在以上酸性条件下处理,染色物的表面色深几乎不下降。
而在以上碱性条件下处理,染色物的表面色深下降严重,而相应的处理残液的色泽却很淡,几乎是无色。
这表明活性嫩黄色染料,在以上碱性条件下所发生的化学反应,主要是染料母体结构中的发色体系遭到破坏而消色,并非只是染料-纤维结合键断裂而落色。
这里有两点值得注意:第一,碱剂减色率的高低,随处理条件(如碱性的强弱、处理温度的高低、处理时间的长短等)的不同而不同。
提高活性染料轧染得色稳定性的实用技术

剂—— 纯碱与烧碱 、抗还 原剂—— 防染盐s 等组成 。
防 染 盐S
在汽 蒸箱 中通 常有还 原 性气体 存在 。这 容 易导
致活性染料 的色光变萎 暗, ( 浅色较 明显 )。防染 染
盐S 具有 弱氧化性 ,可 以抵消还 原性气 体对染料色 光
的影响。
所 以 ,固色浴 中施 加较 高浓度 的 电介质 是 必须
基才 能与 纤维 素负 离子产 生亲 核取代 反应 ,生产 纤
p 值 ,总是低 于外 相溶液 的 。这对提 高染 料—— 纤 H 维 间 的固色速 率 与 固色 率具 有负面 影 响 。电介质 的
收稿 日期 :2 1—40 020—6
维素 酯 。 乙烯砜 基才 能与 纤维 负离子 生亲 核加 成反 应 ,生产 纤维素 醚 。从而 使染料 分 子成为 纤维 素大
水洗烘干 。
但是 ,这里有一个技术 问题不可忽视 ,即固色浴
D 值 的高低 ,必须与所用染料的反应性能相适 应。不 H
然 ,势必会 导致 固着率 下 降 ,得色 变 浅 。原 因是 ,
母体 、架桥 基 、活性基 不 同的活性 染料 ,其 反应 能
( )固色液组成 ( / 、m / ): 2 gL gL
料 中,有许 多染 料在碱 性浴 中的溶解稳 定性 差 ,容
易发 生聚 集 、絮 集 。其凝聚 物会 随液 面泡沫 沾污 织
物 ,造 成 色点 、色渍染 疵 。而且 ,染料 浓度 越高 问
题越严 重 )。 ( )在碱 性 浴 中 ,纤 维素 纤 维 孔 隙 中溶 液 的 2
( )在碱 性条件下 ,活性染料 分子结构 中 的活 2 性基 团,才会 产生 强劲 的反应活 性 。其 中 ,均 三嗪
活性染料S、E、F、R值测试与影响因素的研究
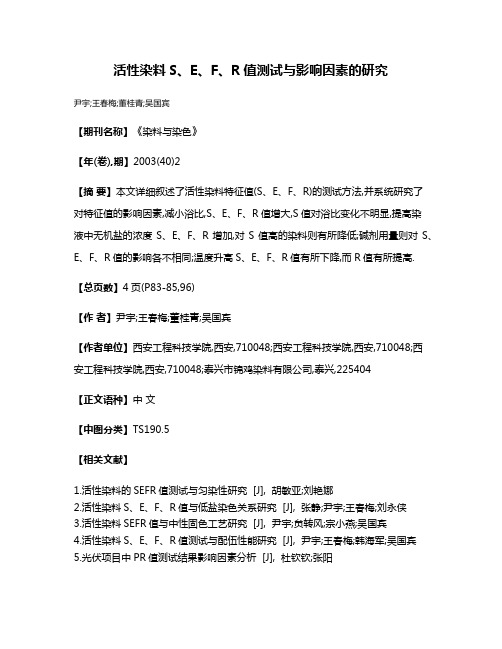
活性染料S、E、F、R值测试与影响因素的研究
尹宇;王春梅;董桂青;吴国宾
【期刊名称】《染料与染色》
【年(卷),期】2003(40)2
【摘要】本文详细叙述了活性染料特征值(S、E、F、R)的测试方法,并系统研究了
对特征值的影响因素,减小浴比,S、E、F、R值增大,S值对浴比变化不明显,提高染
液中无机盐的浓度S、E、F、R增加,对S值高的染料则有所降低;碱剂用量则对S、E、F、R值的影响各不相同;温度升高S、E、F、R值有所下降,而R值有所提高.【总页数】4页(P83-85,96)
【作者】尹宇;王春梅;董桂青;吴国宾
【作者单位】西安工程科技学院,西安,710048;西安工程科技学院,西安,710048;西
安工程科技学院,西安,710048;泰兴市锦鸡染料有限公司,泰兴,225404
【正文语种】中文
【中图分类】TS190.5
【相关文献】
1.活性染料的SEFR值测试与匀染性研究 [J], 胡敏亚;刘艳娜
2.活性染料S、E、F、R值与低盐染色关系研究 [J], 张静;尹宇;王春梅;刘永侠
3.活性染料SEFR值与中性固色工艺研究 [J], 尹宇;贠转风;宗小燕;吴国宾
4.活性染料S、E、F、R值测试与配伍性能研究 [J], 尹宇;王春梅;韩海军;吴国宾
5.光伏项目中PR值测试结果影响因素分析 [J], 杜钦钦;张阳
因版权原因,仅展示原文概要,查看原文内容请购买。
染色过程中产生边中色差及前后色差分析

分析染色半成品和染色过程中(中深色)产生边中色差及前后色差、色条、色花的影响因素,从染料、助剂、工艺控制和设备等诸方面,给出了预防措施。
1 半成品的影响在染色布的生产过程中,半成品的性能对色布的色光一致性、色泽稳定性及色差的调整至关重要。
半成品要求前处理匀透,半成品加工条件稍有变化,便反映在染色色泽上。
在生产中有的货单批量大,即使同是同一品种,也可能因坯布产地、上浆品种、上浆率、棉花品质和配棉、纺织生产工艺不同,造成半成品品质不同。
因此在生产中,每道工序都要严格把关,要及时测定练漂各工序工艺控制指标,保持工艺条件一致。
大批量的要带样生产,差距大的要及时调整处方,避免生产中前后色差变化大,造成回修和消耗增加。
为减少半成品对染色上染率的影响,应制定合理的练漂工艺。
对同一品种布,尤其是返单,要定机台,以成熟工艺生产,提高原单处方的染色重现性。
2 染色过程的影响2.1 染料、助剂的选用对色差的影响2.1.1 染料选用士林染料染色时,个别染料因上染速率慢而在染槽中沉积,染色布色光逐渐向上染速率慢的染料色光靠近,造成前后色差。
因此,如在生产橄榄绿时,常使用士林黄,为了稳定色光,我们采用士林橄榄绿或草绿。
另外,为了防止染料沉积,还可以在染料中加入分散剂,使料缸、料槽中的染液更均匀,防止发生聚集,以有效改善色差,并降低成本。
选用活性染料染色时,由于活性染料反应性较高,若染料性能差距较大,连续轧染时,色光难以控制,易产生前后色差。
因此,在生产过程中应选用配伍性一致或接近的染料。
2.1.2 助剂助剂对边中色差及花有和大的影响。
加入合适的助剂,可以有效改善因坯布、设备等原因造成的色差及条花。
但有时某种助剂的加入,并不能同时解决色差条花等诸多问题。
此时,在重新选用染化料基础上,使用效果较好的助剂才能生产出令客户满意的产品。
例如,在生产中加入防泳移剂,能改善由于风房、烘干温度不匀造成的染料泳移,有利于色差的调整;但它不能有效地改善布面织疵、棉杂、棉结。
活性染料染色耐光色牢度的影响因素分析

活性染料染色耐光色牢度的影响因素分析陈启宏1,杨 萍2,陆必泰2(1.邦达国际纺织有限公司,香港九龙;2.武汉科技学院化学工程学院,湖北武汉430073)摘 要:分析了活性染料品种、染色浓度、拼色、布面pH 值对棉织物耐光色牢度的影响,包括日晒牢度、汗光牢度;探讨了耐光色牢度提升剂对活性染料染浅色织物耐光色牢度的提升作用;研究了多种功能整理,如柔软、防皱、纳米防水防油和提高耐氯牢度整理,对浅色织物耐光色牢度和对耐光色牢度提升剂应用效果的影响。
结果表明,不同染料品种的耐光色牢度不同,浅色织物的耐光色牢度通常较深色织物低,拼色光牢度由其中耐光色牢度最差的染料决定;耐光色牢度提升剂对浅色织物耐光色牢度有很大的提升作用,并可与其它功能整理剂同浴整理。
关键词:染色;活性染料;耐光色牢度;棉织物中图分类号:TS1931632 文献标识码:B 文章编号:1000-4017(2007)01-0019-05Factors exerti n g i n fluence on li ght fa st ness of the reacti ve dye i n gsCHE N Q i 2hong 1,Y ANG Ping 2,LU B i 2tai21.B ondex International Textiles L i m ited,Ko w loon,Hong Kong;2.D epart m ent of Che mical Engineering,W uhan U niversity of Science and Engineering,W uhan 430073,ChinaAbstract:This paper discussed the influence of reactive dye type,dye concentrati on,m ixture of dyestuffs and pH value of fabric on col or fastness t o the combinati on of sunlight and pers p irati on .Effects of vari ous functi onal finishing on col or fastness were discussed,such as s of 2tening,wrinkle resistance,Nano 2Tex water and oil repellent,and i m p r oving the fastness t o chl orine .The results showed that col or fastness t o light was related t o reactive dyestuff type and dye concentrati on .Col or fastness t o light of fabric in light shade was poorer than that in dark .L ight col orfastness of fabric dyed with m ixed dyestuffs is generally dependent upon the dye with the poorest light fastness .The p r omoter t o light col or fastness,which is compatible with other functi onal finishing che m icals,can significantly i m p r ove light col or fastness .Key words:dyeing;reactive dyes;col or fastness t o sunlight;cott on fabric0 前言活性染料色谱齐全、价格便宜、生产控制方便、湿牢度好,是目前印染厂最常用的棉用染料。
纤维素纤维纺织品活性染料轧染理论和工艺_一_
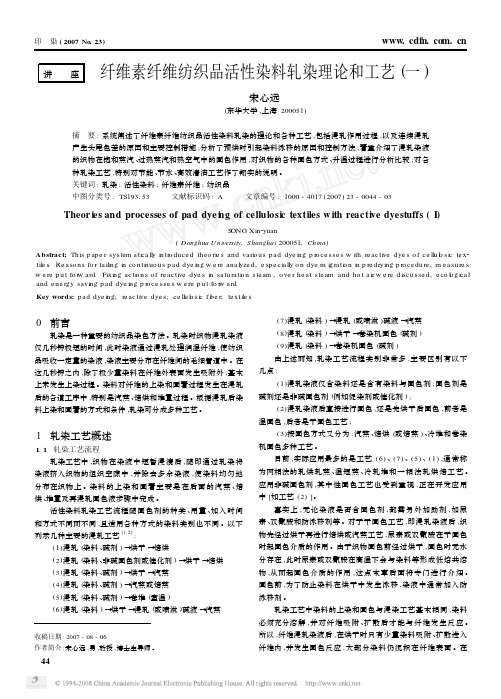
讲 座纤维素纤维纺织品活性染料轧染理论和工艺(一)宋心远(东华大学,上海200051)摘 要:系统阐述了纤维素纤维纺织品活性染料轧染的理论和各种工艺,包括浸轧作用过程,以及连续浸轧产生头尾色差的原因和主要控制措施;分析了预烘时引起染料泳移的原因和控制方法;着重介绍了浸轧染液的织物在饱和蒸汽、过热蒸汽和热空气中的固色作用,对织物的各种固色方式、升温过程进行分析比较;对各种轧染工艺,特别对节能、节水、高效清洁工艺作了翔实的说明。
关键词:轧染;活性染料;纤维素纤维;纺织品中图分类号:TS193153 文献标识码:A 文章编号:1000-4017(2007)23-0044-03Theor i es and processes of pad dye i n g of cellulosi c textiles w ith reacti ve dyestuffs(I)S ONG Xin2yuan(D onghua U niversity,Shanghai200051,China)Abstract:Th is p ap e r system a ti ca ll y i n tr o duce d theo ri e s and va ri o u s p ad dye i ng p r o ce s se s w ith reac ti ve dye s o f ce ll u l o si c te x2 til e s.Re a so n s fo r ta ili ng i n co n ti nuo u s p ad dye i ng w e re ana l yzed,e sp e c i a ll y o n dye m i g ra ti o n i n p re d ryi ng p r o ce du re,m e a su re s w e re p u t fo r w a rd.Fi xi ng ac ti o n s o f re ac ti ve dye s i n sa tu ra ti o n s te am,o ve r he a t s te am and ho t a ir w e re d iscu s sed,e co l o g i ca l and e ne rgy savi ng p ad dye i ng p r o ce s se s w e re p u t fo r w a rd.Key words:p ad dye i ng;re ac ti ve dye s;ce ll u l o s i c fi be r;te xtil e s0 前言轧染是一种重要的纺织品染色方法。
活性翠蓝浸染染疵成因分析与防范措施
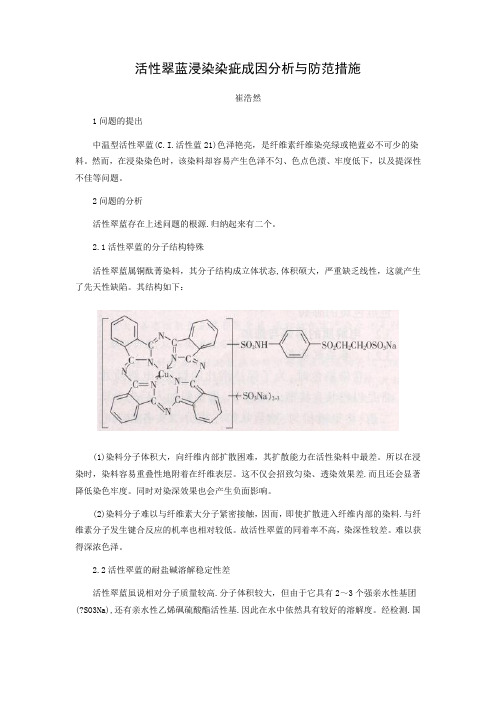
活性翠蓝浸染染疵成因分析与防范措施崔浩然1问题的提出中温型活性翠蓝(C.I.活性蓝21)色泽艳亮,是纤维素纤维染亮绿或艳蓝必不可少的染料。
然而,在浸染染色时,该染料却容易产生色泽不匀、色点色渍、牢度低下,以及提深性不佳等问题。
2问题的分析活性翠蓝存在上述问题的根源.归纳起来有二个。
2.1活性翠蓝的分子结构特殊活性翠蓝属铜酞菁染料,其分子结构成立体状态,体积硕大,严重缺乏线性,这就产生了先天性缺陷。
其结构如下:(1)染料分子体积大,向纤维内部扩散困难,其扩散能力在活性染料中最差。
所以在浸染时,染料容易重叠性地附着在纤维表层。
这不仅会招致匀染、透染效果差.而且还会显著降低染色牢度。
同时对染深效果也会产生负面影响。
(2)染料分子难以与纤维素大分子紧密接触,因而,即使扩散进入纤维内部的染料.与纤维素分子发生键合反应的机率也相对较低。
故活性翠蓝的同着率不高,染深性较差。
难以获得深浓色泽。
2.2活性翠蓝的耐盐碱溶解稳定性差活性翠蓝虽说相对分子质量较高.分子体积较大,但由于它具有2~3个强亲水性基团(?SO3Na),还有亲水性乙烯砜硫酸酯活性基.因此在水中依然具有较好的溶解度。
经检测.国产活性翠蓝在含六偏磷酸钠2 g/L的中性水中,40℃时可溶解至100 g/L;80℃时可溶解至150 g/L。
问题是:活性翠蓝的水溶液与其它活性染料有所不同,其凝胶性质十分突出。
即,随着溶液浓度的提高,其溶液会逐渐呈现出胶冻状态。
然而染料溶液滴在滤纸上仍能均匀渗开,并无染料的斑点显现.只是渗圈较小而已。
这表明活性翠蓝溶液的这种凝冻现象并非等同于染料的凝聚现象。
但值得注意的是:电解质的加入,会破坏活性翠蓝胶体溶液的稳定性,尤其是当电解质的质量浓度过高(>80 g/L)时,染料便会发生凝聚或絮集,甚至染料与水分离而析出。
由此可见,活性翠蓝在软水中的溶解稳定性是好的,而在含盐量高的染浴中,溶解稳定性却是比较差的。
实验证明,纯碱的加入,会使活性翠蓝在盐化水中的凝聚倾向进一步加剧。
活性染料产生色点、凝聚、染色不均匀等质量问题原因

活性染料产生色点、凝聚、染色不均匀等质量问题原因活性染料(reactiondye)的染色原理:又叫反应性染料。
分子中含有化学性活泼的基团,能在水溶液中与棉、毛等纤维反应形成共键结合的染料。
活性染料由于其用母体染料、连结基和活性基组成,使其在使用时能与纤维形成牢固的共价键结合。
活性染料活性染料在水中具有极良好的溶解状态,活性染料主要依靠染料分子上的磺酸基团,溶解于水中,对于含乙烯砜基的中温型活性染料而言,除磺酸基团外,其β-乙基砜基硫酸根也是极良好的溶解基团。
在水溶液中,磺酸基及-乙基砜基硫酸基上的钠离子发生水化反应使染料形成负离子而溶解于水中,活性染料的染色是依靠染料的负离子上染到纤维上去的。
活性染料的溶解度均超过100克/升,大多数染料的溶解度在200~400克/升,个别染料甚至可达到450克/升。
但是在染色过程,染料的溶解度会由于各种不同原因而下降(甚至完全不溶解),当染料溶解度下降以后,部分染料将会从单只的游离态负离子转变为粒子,由于粒子之间电荷斥力大大降低,粒子与粒子会互相吸引产生凝聚,这种凝聚先是染料粒子集合成凝聚体,然后转变为集聚体,最后转变为絮聚体,絮聚体尽管是一种松弛的集合,但由于在其周围由正电荷和负电荷形成的双电层,一般染液循环时的切变力很难将其分解,絮聚体很易在织物上沉淀,形成表面染色或玷污。
一旦染料产生这样的凝聚,染色牢度都会明显下降,同时会造成不同程度的色花、色斑、色渍。
对某些染料,其絮聚体在染液的切变力下会进一步加快集合,造成脱水盐析。
一旦发生盐析,染色的颜色会变得极浅,甚至染不上色,即使染上色,也是严重色花、色渍。
染料产生凝聚的原因主要原因还是电解质引起的,在染色过程中,主要的电解质是促染剂(元明粉和盐),促染剂中含有钠离子,而染料分子中的钠离子当量远低于促染剂的钠离子当量数,在正常染色过程中正常的促染剂浓度对染浴中的染料溶解度不会造成太大影响。
但是当促染剂用量增加时,其溶液中钠离子的浓度也相应增加,过量的钠离子会抑制染料分子的溶解基团上钠离子的电离,从而降低了染料的溶解度,当促染剂浓度超过200克/升以后,大多数染料均会发生不同程度的凝聚,当促染剂浓度超过250克/升以后,这种凝聚程度将会加剧,先形成凝聚体,然后在染液切变力下很快形成集聚体及絮聚体,对于溶解度低的一些染料则部分盐析出来,甚至脱水,不同分子结构的染料抗凝聚及耐盐析性能也不同,溶解度越低,抗凝聚及耐盐析性能越差。
科普│纯棉活性印花的色差原因和解决办法

科普│纯棉活性印花的色差原因和解决办法纯棉织物印花大多采用活性染料。
提高纯棉活性印花一次成功率,将色差控制在合理范围内,对于提高生产效率、节能减排和大幅度降低生产成本具有重要意义。
本文根据生产实践,总结分析生产过程中易造成色差的因素,并给出相应的控制措施。
生产过程中易造成色差的因素01前处理前处理均匀一致,才能为控制色差提供准备。
若前处理不能满足要求,后续加工也很难达到预期效果。
因此,控制色差,要从前处理抓起。
02翻布缝头同一布车要求用同一种规格、同一厂家、同批次的坯布缝在一起。
如果单子太小,不同批次的布需要拼车,一定要做好标记,以便于后道工序区分。
03烧毛坯布浆料中一般含有大量化学浆料,如果车速忽快忽慢,或者火口不均匀,织物经过火口时布面不平整,会导致退浆不匀,引起色差。
所以,烧毛车速应一致,布面平整,火口均匀。
04练漂煮练时,烧碱和助剂的用量要严格控制,汽蒸时间、温度、轧余率和水洗等工艺条件要稳定。
煮练后,双氧水漂白要充分水洗,防止双氧水残留。
烘干落布幅宽一致,含潮相同。
05丝光严格控制车速和烧碱浓度,落布后测试毛效、钡值。
丝光进布的含潮差异不能过大,特别是一些厚重织物。
因为布面含潮不匀,会导致丝光效果不一致,使印花效果产生差异。
棉纤维充分丝光,染料对纤维的亲和力增加,吸附后不易随水分迁移,且在汽蒸过程中与纤维发生共价键结合,使织物表面得色深且饱满均匀。
06磨毛磨毛布磨毛效果要均匀一致。
砂皮不建议太粗,最好在280目以上。
磨毛过程中,张力和车速应均匀一致,砂皮也要经常更换。
因为磨毛时间过长,砂皮表面粗槌度降低,磨毛效果下降。
磨毛不均匀也会导致印花得色不一致,从而产生色差。
印花处方和工艺条件色浆处方01染料印花所选染料的反应性要适中且相近。
反应性太强,色浆的稳定性不好,特别在夏季,随着储存时间的延长,染料色浆得色明显下降;反应性太弱,汽蒸过程中染料不能充分反应,随工艺条件波动会产生明显色差。
拼色时,同一处方的染料反应性应尽量接近,这样不会因为工艺条件波动而产生明显的色相变化。
活性印花敏感色色牢度和色差控制

Abstract Reactive dyes are commonly used in printing of cellulose fibers with bright colors, chromatography, good color fastness, while the impact on the product is small. However, some of the color fastness of reactive dyes is not very satisfactory, including the sun fastness, climate fastness, acid fastness perspiration fastness, and color stability. These actual problems in production often troubled the smooth printing. Fabrics, clothing, or home textile productsoften appear discoloration in the fold discolorationduring the process of storage. , In the event of discoloration at the crease, it is difficult to remedy, resulting in a direct economic loss. In the dyeing factory production, for some gray, brown, olive green and other sensitive colors, color fastness and color stability have been the production of printing and dyeing factory problems, without a good solution. The dye fastness and weather fastness, have aroused the concern of the industry. Corresponding research has also been done for acidic and alkaline perspiration fastness of white
- 1、下载文档前请自行甄别文档内容的完整性,平台不提供额外的编辑、内容补充、找答案等附加服务。
- 2、"仅部分预览"的文档,不可在线预览部分如存在完整性等问题,可反馈申请退款(可完整预览的文档不适用该条件!)。
- 3、如文档侵犯您的权益,请联系客服反馈,我们会尽快为您处理(人工客服工作时间:9:00-18:30)。
活性染料Rf值和织物回潮率对轧染色差的影响
0前言
活性染料连续轧染生产中,容易发生对样色差、批间色差、批内前后色差、左中右色差、正反面色差等问题,限制了活性染料在轧染工艺中的应用。
国际纺织品市场竞争日趋激烈,对纺织品品质的要求越来越高,尤其对色差要求均高于我国的国家标准。
纺织品对色由原来单光源对色,发展到双光源对色,甚至三光源对色,要求在不同光源对色时色光不变。
色差的评定也由原来的目测评级转变为电脑测色评级,使得有些不敏感的颜色在目测时可以达到要求,但经电脑测色则无法通过。
本文主要针对活性染料轧染色差的成因,分析染料的直接性、半制品含潮率及固色碱液中染料的加入量对色差的影响并提出相应的解决措施。
1 染料的直接性
活性染料是反应性染料,各染料达到染色平衡的时间不一,且时间较长,而在连续轧染生产中,织物与染液接触的时间较短(仅几秒钟),无法达到染色平衡。
由于燃料对棉纤维的亲和力大,因此在浸轧染液时,织物所带走染液的染料浓度高于轧槽中的染料浓度,因而初染染料浓度高于续染染料浓度,造成头深尾浅,这也是由染料的性能造成染色前后色差的主要元因。
染料的直接性可用比移值(R f)来衡量,比移值大小与染料的直接性成反比。
比移值小,直接性高,吸附快,织物上带走的染料就多,易造成头深尾浅;比移值大,直接性低。
前后色差小,但上染量少,且易造成泳移。
一般选择直接性中等偏低(比移值为0.75~0.8)的活性染料,且拼色的染料直接性要接近。
1.1根据比移值选择染料存在的问题
染料生产厂家测定染料比移值一般以单只染料固定浓度(10g/L或5g/L)配制染液来测定,而仅根据比移值选择染料存在以下几方面问题:
(1)一般染料生产厂家提供的三原色以染色深度划分,如深三原色、浅三原色。
在实际生产过程中,三只染料的用量差距较大,在每升染液中,用量大的高达几十克,用量小的则不到五克,因而三原色拼染时经常出现其中一只染料用量达到深色标准,而另一种染料用量处于浅色的范围,颜色色差难以控制。
图1和图2为两组三原色活性染料比移值与染料浓度之间的关系。
实验说明,随着染料质量浓度增加,活性红3BS,黄3RS和元青B的比移值均逐渐增大,但增幅不同。
当染料超过30g/L时,三只染料的比移值趋于一致,即三只染料的用量都要达到30g/L以上,该组染料拼色才可获得较好的稳定性和较小的色差;若三只染料的用量差距大,则比移值偏差较大,拼色的稳定性差。
用量相同时,染料红3BS和黄3RS的比移值基本一致;两只染料用量相差10g/L,比移值的差距不大,因而在实际生产中红黄拼色的色差容易控制。
当用量低于30g/L时,元青B与红3BS和黄3RS的比移值差距较大,而在生产中往往是以元青B为主色拼红3BS和黄3RS,元青B用量远大于红黄染料的用量,因此在实际生产中色差很难控制。
对于某些易出现色差的颜色,如中灰色等,不宜选用活性染料,而改用还原染料染色。
由此可以看出,在燃料用量相同的条件下,活性C系列三原色染料的比移值基本一致。
三只染料的用量差距较小时,比移值差距较小,色差易控制。
因此,用该组染料拼染浅色时,稳定性较好,色差较小。
由上可知,对于任何一组在某一特定浓度下测定的比移值接近的染料,在实际生产中,随着染料用量的变化,比移值会出现较大的差异,直接影响色差的控制。
(2)比移值的测定误差大。
在实际测定中发现,染料和水在滤纸的上升轨迹并不是一条直线,而是呈锯齿形,因此读数时会产生误差。
若以单只染料来分别测定,则误差更大。
(3)染料中添加剂对染料比移值的影响。
染料生产厂家在燃料中要加入一定量的添加剂,如无机盐和扩散剂、增溶剂等表面活性剂,这些添加剂会影响比移值的测定。
以下是盐用量对染料比移值的影响。
对于活性CA系列三原色而言,加入无机盐后,CA蓝的比移值变化不大,而CA红和CA黄的比移值分别增加了10%和15%;3BS红和3RS黄的比移值分别增加了13%和10%,而RIS蓝的比移值变化较小。
同样,各种表面活性剂对各染料比移值的影响也有所不同。
1.2比移值测定方法的改进
由于影响比移值的因素众多,仅采用单只染料在特定浓度下的比移值作为拼色染料组合的依据不够准确,因而在确定染色处方后,应按处方的要求配制染液,取染液滴在滤纸上观察各染料扩散的程度是否同步,是否出现分层,进而判断该组染料拼色的合理性。
1.3 染料比移值对前后色差的影响
对轧染而言,选择比移值大的染料,则染料向织物转移的速度慢,初染的浓度与续染的浓度差异较小,头尾色差小,但易出现泳移;选择比移值小的染料,则初染染料浓度与续染
染料的浓度差异较大,头尾色差大,但不容易出现泳移。
在实际生产中,染料的泳移可通过加入防泳移剂,或改进烘干方式加以解决;而初染染料浓度与续染染料浓度的差异却难以解决,通常采用开车冲淡的方式,或提高补充液浓度的方法来解决。
冲淡系数或追加染料的系数会因染料不同、染料用量不同以及织物不同而不同,在实际操作中难度较大。
由于生产批量小,而初染染料浓度与续染染料浓度的平衡需要400~600m布。
因此根据比移值选择染料首先要考虑是减少头尾色差,可选择比移值较大的染料。
实践证明,深三原色的染料或染料浓度高时,比移值较大,因而染深色时初染染料浓度与续染染料浓度差异很小,甚至可以开车无需冲淡轧槽染液;而浅中色染料或染料用量少时,比移值一般较小,初染染料浓度与续染染料浓度差异大,需冲淡染液。
2半制品的含潮率
织物前处理的质量对染色前后色差影响较大,主要影响因素有:半制品的毛效,丝光效果,布面pH值,退浆效果以及半制品的含潮率。
其中半制品含潮率的影响常被忽视。
棉织物的回潮率一般为7%~8%。
印染车间的湿度大,加之在前处理的烘燥过程中,经常过烘落布,堆放在储布车上的织物很快吸湿,造成布边与中间、外层与内部的含潮率不同。
半制品的干湿度对活性染料的浸染影响不大,但对轧染则影响很大。
从而可以看出,半制品水分含量越高,则上染率越低,某些颜色上染率甚至相差15%以上。
由于轧染的轧余率是设定的,半制品局部的含潮率不同,浸轧染液带走的染液量不等,导致织物各部分由于吸附染料的不等而产生色差。
这类色差一般无法通过调整轧车轧余率而纠正,尤其是左中右色差。
实际上,除了半制品的含潮率,印染车间内空气中各种酸、碱、还原剂等对对方的半制品也会产生影响,造成染色色差。
因此,半制品对方过程中要加强现场管理,合理安排前处理的生产量,改进落布堆放方式、采用大卷装加包布,设立半制品对房间,隔离堆放。
3固色碱液中染料的加入量
活性染料轧染常用的染色工艺是轧烘轧蒸法,织物浸轧染液烘干后,再浸轧碱固色液汽蒸固色。
由于织物染液烘干后,染料并未与纤维形成化学结合,而只是物理吸附,浸轧碱液
时织物上的染料会溶落到碱液中,再沾染至后面的织物,从而出现刚开车的布色浅,后续的布色深的现象。
这可以通过开车时在浸轧的碱液中追加染料来克服。
但是在实际生产中,染料的加入量较难掌握,不同颜色、不同深度加入的染料量不同,完全凭经验操作,在生产中会产生批与批之间的色差。
通过对大样生产的跟踪,发现染料的加入量与染色深度以及染料的直接性有关
得知,固色碱液中染料的加入量随着染色深度增加而增大,染色深度在2g/L以下时可以不用加入染料。
同时,染料的加入量还与染料的直接性有关,直接性大,加入量小;直接性小,则加入量大。
实验发现,染料的加入量与染料的比移值有关,当染色深度超过10g/L时,染料的加入量与染色深度成近似线性关系:
染料的加入量=染色深度×比移值/20
对大多数颜色,用上述公式计算染液的加入量,可基本解决由于固色液染料浓度不平衡带来的前后色差,同时,也在很大程度上减少了翻单生产批与批之间的色差。
4总结
(1)活性染料轧染的色差与染料的比移值有关,除了测定单只染料的比移值,还应在处方确定后,测定染液中各种染料的扩散是否同步,是否出现分层,从而判断拼色的合理性。
(2)根据比移值选择染料对解决轧染前后的色差至关重要,选择比移值较大的染料可以解决由于染料直接性带来的前后色差。
(3)半制品的含潮率对染色的影响很大,前处理烘干落布应采用大卷装加包布,并加强现场管理。
(4)固色碱液中染料的加入量与染色深度和染料的比移值有关,加入量与染色深度成近似线性关系。