石膏型铸造
石膏型铸造讲义

石膏型铸造讲义
1
主要内容 概述 1、制石膏型用材料及其组成 2、石膏型精铸工艺
2
概述
1、工艺过程 石膏型精密铸造是20世纪70年代发展起来的一
种精密铸造新技术,其典型工艺过程见图0-1。 它是将熔模组装,并固定在专供灌浆用的砂箱
平板上,在真空下把石膏浆料灌入,待浆料凝结后 经干燥即可脱除熔模,再经烘干、焙烧成为石膏型, 在真空下浇注获得铸件。
3
概述
2、工艺特点
(1) 石膏浆料的流动性很好,又在真空下灌注成型, 其充型性优良,复模性优异,型精确、光洁。该工艺不 像一般熔模精密铸造受到涂挂工艺的限制,可灌注大型 复杂铸件用型。
(2) 石膏型的热导率很低,充型时合金液流动保持 时间长,适宜生产薄壁复杂件。
但铸型激冷作用差,组织粗大,当铸件壁厚差异大 时,厚大处容易出现缩松、缩孔等缺陷。
1.3
0.2
2.1-2.2 0.5 X10-6
3.25 3.1-4.3 X10-6 1.5
0.65
3.08-
5.3 X10-6
2.3
3.4
0.80
3.15
3.2-3.4 5.0 X10-6 2.6
4.6
0.85
3.95-
8.4 X10-6
2.0
3.5
0.65
4.02
5.73 7.2-10 X10-6
除石膏种类外,影响石膏强度的因素还有石膏的 细度、水固比、水温、搅拌时间等。
6
第一节 制石膏型用材料及其组成 2. 填料
为使石膏型具有良好的强度,减小其收缩和裂纹 倾向,需要在石膏中加入填料。
填料应有合适的熔点、耐火度,良好的化学稳定 性、合适的线膨胀率、发气量少,吸湿性小等性能, 常用作填料的材料及其性能见表1-1。
第2章石膏型精密铸造1

镁合金
1.2
1.6
锰黄铜 1.8~2.0 2.0~2.3
石膏型精密铸件的综合收缩率A可按下式计算:
A% (a c d)%
三、铸造斜度 石膏型精密铸件的铸造斜度可参考熔模铸造斜 度。
2.2.3浇注系统及冒口设计 石膏型精密铸件浇注系统及冒口设计可参考熔
模铸造或砂型铸造。应注意以下几点: 1、石膏导热性差,金属液保持流动时间长, 故浇注系统截面积尺寸可比砂型铸造减少 20%左右。
表2-3 尿素模料配方
序号 尿素
硼酸
硼酸钾 羧甲基纤维素
水
1 97~98 2~3
2 75~85
15~25
3
85
10
5
表2-4 无机盐模料配方
名称
KNO3 NaNO2 NaNO3 Al2(SO4)3 (NH4)2SO4 HO2
亚硝酸盐模料 55
45
—
—
—
—
硝酸盐模料 55
—
45
—
—
—
硫酸盐模料 —
2.1.2工艺特点 1、使用易熔模,不用开箱起模。 2、可制造尺寸精度高(可达CT4~6级)、大型 (1000mm×2000mm)、薄壁 (壁厚为1.5mm,局
部为0.5mm)、形状复杂的精密铸件。表面粗 糙度一般Ra1.6~3.2μm,最高可达0.8μm。 同时石膏型溃散性好,易于清除。
3、石膏型导热系数低,金属液浇入后保持流动 性时间长,铸件的成形性能好,但铸件凝固时间 长,致使铸件产生气孔、针孔、疏松、缩孔的倾 向大。
石膏型精铸专用模料主要有下列三方面要求: (1)模料强度高、韧性好,能承受石膏浆料灌
注的作用力而不变形损坏。 (2)模料线收缩小,保证熔模尺寸精确,防止
铸造工艺总汇-石膏型铸造与设计

图 1 石膏型精密铸造工艺过程
它是将熔模组装,并固定在专供灌浆用的砂箱平板上,在真空下把石膏浆料灌入,待浆料凝 结后经干燥即可脱除熔模,再经烘干、焙烧成为石膏型,在真空下浇注获得铸件。
7.1.2 工艺特点
1. 石膏浆料的流动性很好,又在真空下灌注成型,其充型性优良,复模性优异,型精确、光 洁。该工艺不像一般熔模精密铸造受到涂挂工艺的限制,可灌注大型复杂铸件用型。
3.2-3.4 3.95-4.02
5.73 4.7-4.9
12.5X10-6 0.5 X10-6 3.1-4.3 X10-6 5.3 X10-6
5.0 X10-6 8.4 X10-6 7.2-10 X10-6 5.1 X10-6
加入填料后石膏混合料强度 (Mpa)
7h 烘干 90℃,4h 焙烧 700℃,1h
取出母模(不可敲动),起模后应立即进行点火喷烧,否则易产生裂纹。 (五)喷烧 起模后应立刻点火并吹压缩空气进行喷烧,而使陶瓷型的表面有一定的强度和硬度。 (六)焙烧 焙烧的目的是使陶瓷型内残存的乙醇、水分和少量的有机物烧去,并使陶瓷层的强度增加。 全部由陶瓷浆料灌制的陶瓷型,焙烧温度可高达 800oC,焙烧时间 2~3h,出炉温度应在 2500C
第2章石膏型精密铸造2

1-石英 2-高铝矾土 3-高岭土 4-氧化铝 5-规线石 6-莫来石
三、添加剂 为改善石膏浆料某方面性能,还应加入添加剂。
添加剂分别可作增强剂、促凝剂、缓凝剂、减缩
剂。
1、增强剂—增加石膏型的湿强度、焙烧后强 度和高温强度。这类增强剂有两类:
一类如硫酸镁,以硫酸盐为主体的复合增强 剂,其本身有胶凝特性,能与填料、杂质起作用 促凝石膏; 另一类如硅溶胶,本身为粘结剂,能增强石膏 强度。
表2-11 填料种类对石膏混合料浆体凝时间的影响
填料 硅石粉 硅线石 高岭土 莫来石 高铝 矾土 工业 氧化铝 锆英粉 α 半水石 膏100%
处凝时间 7.0 终凝时间 10.0
8.5 10.5
8.0 10.0
10.0 12.0
12.0 13.5
9.0 11.0
10.0 12.0
8 10
填料种类对石膏混合料线膨胀率的 影响(加入量60%)
填料 灌浆后2h 灌浆后7d 烘干90℃/4h 700℃焙烧后 硅石粉 0.25 0.50 1.30 0.20 硅线石 0.40 1.50 2.80 0.65 莫来石 0.75 2.30 3.40 0.80 高岭土 0.80 2.40 3.80 0.86 高铝矾土 工业氧化铝 1.00 2.60 4.60 0.85 0.80 2.00 3.50 0.65
加水量多少(亦即水固比大小),与多种因素
有关,既受到固态粉料中石膏、填料、添加剂的
品种及其比例的影响,又受粉料粒度、水温等的 影响。
表2-12 石膏浆料配比
序号 石膏 硅石粉砂 1 2 3 4 5 6 7 30 30 30 30 30 30 35.5 35 — 29.0 70 35 20 石英玻璃 — — — — 35 — 35.5 其他材料 — 铝矾土粉砂 35 上店土粉砂 50 莫来石粉砂 70 — 铝矾土粉砂 70 硅藻土2
石膏铸造注意事项

石膏铸造注意事项石膏铸造是一种常见的制造工艺,广泛应用于艺术品制作、建筑装饰、医疗器械、工艺品等领域。
以下是石膏铸造时需要注意的事项:1. 原材料选择:石膏是石膏铸造的主要材料,应选择质量好、无杂质的石膏。
同时,可以根据不同的需求选择不同类型的石膏,如增强型石膏、特种石膏等。
2. 模具设计:模具是石膏铸造中至关重要的一环。
设计模具时需要确保模具结构合理、稳定,能够完整地复制所需的物体。
同时,要注意模具的开口方向以便于浇注和脱模。
3. 浇注粘度控制:控制石膏的粘度是石膏铸造中的关键步骤。
粘度过高会导致石膏流动性差,难以充填模具;粘度过低则容易形成气泡和缺陷。
因此,需要根据具体要求控制石膏的水石比,控制好水的用量,以获得适当的粘度。
4. 前处理:在浇注石膏之前,需要对模具进行预处理。
首先,要保证模具表面干净,没有灰尘和杂质。
其次,可以在模具表面涂抹一层脱模剂,以便于石膏脱模时不易粘连。
5. 浇注操作:浇注时要缓慢、均匀地将石膏倒入模具中,避免产生气泡和未充填的空隙。
同时,要控制浇注的速度和角度,以确保石膏能够充分填充模具。
6. 振动除气:在浇注完成后,可以通过轻轻震动模具来排除石膏中的气泡。
振动过程中要逐渐加大力度,同时避免过度振动导致石膏移位或损坏模具。
7. 固化和硬化:浇注完成后,需要将石膏模具放置在通风干燥的环境中进行固化和硬化。
固化时间通常为数小时到数天,具体时间要根据石膏类型和环境条件而定。
8. 脱模操作:石膏完全固化后,可以进行脱模操作。
需要注意的是,应轻轻敲击模具,使石膏从模具中脱离。
如遇到模具卡住的情况,可以使用适当的工具轻轻拍打或使用少许脱模剂帮助脱模。
9. 后处理:脱模后,可以对石膏制品进行一些修整和润饰。
可以使用砂纸、刀具等工具去除毛边和不平整的地方,使石膏制品表面光滑、细腻。
10. 储存和保护:完成石膏铸造后,要妥善储存和保护石膏制品。
可以使用密封袋或包装纸将石膏制品包裹好,避免受潮、受阳光直射和摩擦。
石膏型熔模铸造流程
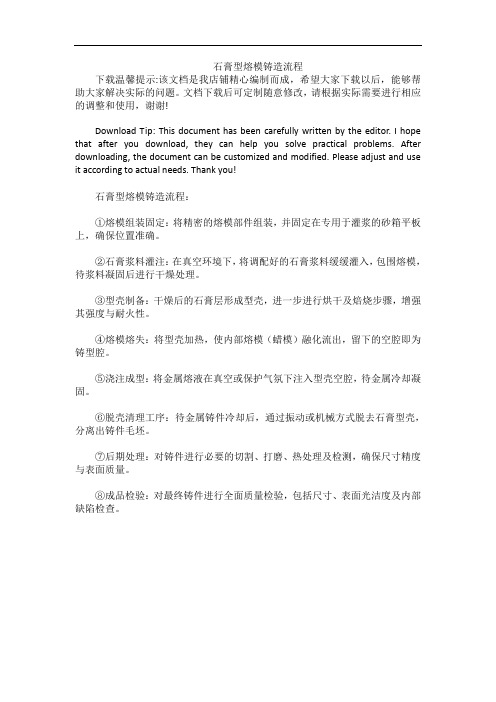
石膏型熔模铸造流程
下载温馨提示:该文档是我店铺精心编制而成,希望大家下载以后,能够帮助大家解决实际的问题。
文档下载后可定制随意修改,请根据实际需要进行相应的调整和使用,谢谢!
Download Tip: This document has been carefully written by the editor. I hope that after you download, they can help you solve practical problems. After downloading, the document can be customized and modified. Please adjust and use it according to actual needs. Thank you!
石膏型熔模铸造流程:
①熔模组装固定:将精密的熔模部件组装,并固定在专用于灌浆的砂箱平板上,确保位置准确。
②石膏浆料灌注:在真空环境下,将调配好的石膏浆料缓缓灌入,包围熔模,待浆料凝固后进行干燥处理。
③型壳制备:干燥后的石膏层形成型壳,进一步进行烘干及焙烧步骤,增强其强度与耐火性。
④熔模熔失:将型壳加热,使内部熔模(蜡模)融化流出,留下的空腔即为铸型腔。
⑤浇注成型:将金属熔液在真空或保护气氛下注入型壳空腔,待金属冷却凝固。
⑥脱壳清理工序:待金属铸件冷却后,通过振动或机械方式脱去石膏型壳,分离出铸件毛坯。
⑦后期处理:对铸件进行必要的切割、打磨、热处理及检测,确保尺寸精度与表面质量。
⑧成品检验:对最终铸件进行全面质量检验,包括尺寸、表面光洁度及内部缺陷检查。
石膏型熔模精密铸造工艺历史
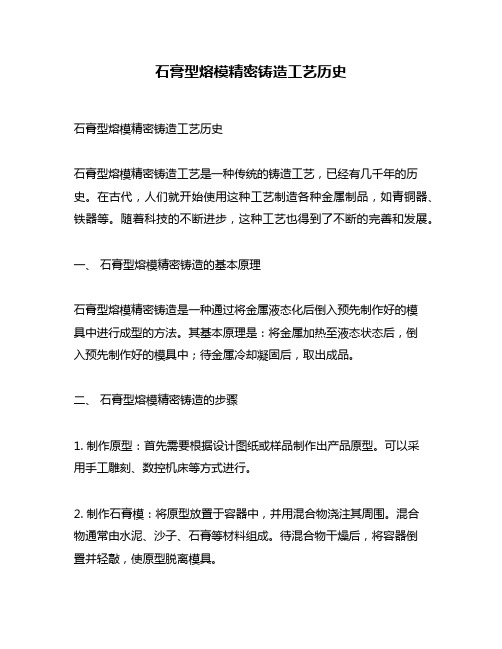
石膏型熔模精密铸造工艺历史石膏型熔模精密铸造工艺历史石膏型熔模精密铸造工艺是一种传统的铸造工艺,已经有几千年的历史。
在古代,人们就开始使用这种工艺制造各种金属制品,如青铜器、铁器等。
随着科技的不断进步,这种工艺也得到了不断的完善和发展。
一、石膏型熔模精密铸造的基本原理石膏型熔模精密铸造是一种通过将金属液态化后倒入预先制作好的模具中进行成型的方法。
其基本原理是:将金属加热至液态状态后,倒入预先制作好的模具中;待金属冷却凝固后,取出成品。
二、石膏型熔模精密铸造的步骤1. 制作原型:首先需要根据设计图纸或样品制作出产品原型。
可以采用手工雕刻、数控机床等方式进行。
2. 制作石膏模:将原型放置于容器中,并用混合物浇注其周围。
混合物通常由水泥、沙子、石膏等材料组成。
待混合物干燥后,将容器倒置并轻敲,使原型脱离模具。
3. 烘干石膏模:将制作好的石膏模放入烤箱中进行加热,以去除其中的水分。
一般需要在200℃左右加热2-3小时。
4. 浇注金属:将金属加热至液态状态后,倒入预先制作好的模具中。
注意要控制好浇注时的温度和速度,以保证成品质量。
5. 取出成品:待金属冷却凝固后,取出成品,并进行后续的加工和处理。
三、石膏型熔模精密铸造的优点1. 精密度高:由于使用了精密的模具,在铸造过程中可以得到高精度、高质量的成品。
2. 适用范围广:可以用于铸造各种形状、大小不同的零件和产品。
3. 成本低:相比其他铸造工艺,该工艺所需材料和设备较少,也更容易操作。
4. 生产效率高:一旦制作好了模具,就可以进行大批量生产,并且生产速度较快。
四、石膏型熔模精密铸造的应用领域石膏型熔模精密铸造工艺广泛应用于各种制造业领域,如航空航天、汽车、电子、医疗器械等。
其中,最常见的应用是在珠宝和首饰制造中。
由于该工艺可以制作出高精度、高质量的成品,因此很受珠宝和首饰行业的青睐。
总之,石膏型熔模精密铸造工艺是一种传统而又实用的铸造方法。
在现代制造业中,它仍然具有重要的地位,并且得到不断地发展和完善。
《陶瓷作品素材》课件——陶瓷石膏浇铸

2021年3月26日
一、石膏浇铸介绍
石膏浇铸(也称注浆成型)是将制备 好的泥浆注入多孔模型(石膏模)内,贴 近模壁的一层泥浆中的水分被模具(如石 膏)吸收后便形成了一定厚度的均匀泥层; 将余浆倒出后,泥坯因脱水收缩而与模型 脱离开来形成毛坯。从广义来说,凡是坯 料具有一定液态流动性,注入模型中凝固 成型的成型方法都可称为注浆成型法。
陶瓷 咖啡 杯绘 制训 练
作业要求:
1.绘制石膏浇铸工艺流程图1张。
2.工艺流程正确。
3.线条清晰明了。
4.画面整洁,题写姓名。
5.把自己完成的作饰计—茶与杯制制作作
泥浆泥浆注入石膏模,石膏模吸水形成薄泥层。 动力:石膏模的毛细管力。毛细管越细,水的表面张力越大,脱水推动力越大。 阻力:石膏模和坯体。 薄泥层的形成:石膏模—颗粒间;颗粒吸附于石膏模,形成薄泥层。
四、注浆成型方法
1. 普通注浆成型 空心注浆(单面注浆)
空心注浆对泥浆性能要求:比重小,稳定性好,触变性较小,细度较好。 空心注浆多用于浇注杯、壶、水箱等类产品的坯体。
四、注浆成型方法
1. 普通注浆成型 实心注浆(双面注浆)
空心注浆对泥浆性能要求:比重小,稳定性好,触变性较小,细度较好。 空心注浆多用于浇注杯、壶、水箱等类产品的坯体。
四、注浆成型方法
2. 强化注浆 压力注浆:用加大泥浆压力的方法加速水分扩散,从而加快吸浆速度。 真空注浆:用真空装置在石膏模外抽真空,或将石膏模放入真空室内。 离心注浆:使模型在旋转情况下注浆,泥浆受离心力左右紧靠模壁面成致密的坯体。
一、石膏浇铸介绍
注浆成型工艺简单,适于生产一些形状复杂且不规则、外观尺寸要求不严格、壁 薄及大型厚胎的制品。
铝合金石膏型熔模铸造工艺
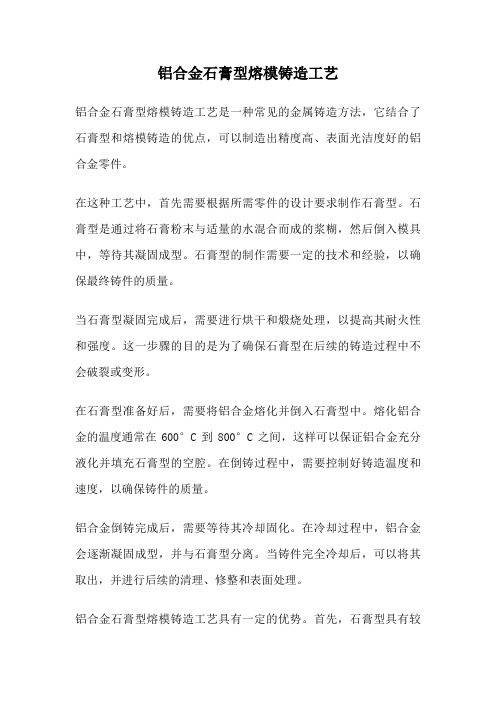
铝合金石膏型熔模铸造工艺铝合金石膏型熔模铸造工艺是一种常见的金属铸造方法,它结合了石膏型和熔模铸造的优点,可以制造出精度高、表面光洁度好的铝合金零件。
在这种工艺中,首先需要根据所需零件的设计要求制作石膏型。
石膏型是通过将石膏粉末与适量的水混合而成的浆糊,然后倒入模具中,等待其凝固成型。
石膏型的制作需要一定的技术和经验,以确保最终铸件的质量。
当石膏型凝固完成后,需要进行烘干和煅烧处理,以提高其耐火性和强度。
这一步骤的目的是为了确保石膏型在后续的铸造过程中不会破裂或变形。
在石膏型准备好后,需要将铝合金熔化并倒入石膏型中。
熔化铝合金的温度通常在600°C到800°C之间,这样可以保证铝合金充分液化并填充石膏型的空腔。
在倒铸过程中,需要控制好铸造温度和速度,以确保铸件的质量。
铝合金倒铸完成后,需要等待其冷却固化。
在冷却过程中,铝合金会逐渐凝固成型,并与石膏型分离。
当铸件完全冷却后,可以将其取出,并进行后续的清理、修整和表面处理。
铝合金石膏型熔模铸造工艺具有一定的优势。
首先,石膏型具有较高的精度和光洁度,可以制造出形状复杂、尺寸精确的铝合金零件。
其次,石膏型可以重复使用,降低生产成本。
此外,由于铝合金的低熔点和良好的流动性,石膏型熔模铸造工艺适用于各种铝合金材料。
然而,铝合金石膏型熔模铸造工艺也存在一些限制。
首先,由于石膏型的制备和处理过程较为复杂,需要一定的时间和技术。
其次,石膏型在高温下容易破裂或变形,需要特殊的处理和保护措施。
此外,由于铝合金的热膨胀系数较大,在铸造过程中需要考虑收缩和变形的问题。
总的来说,铝合金石膏型熔模铸造工艺是一种高精度、高质量的铸造方法。
它不仅可以满足各种复杂零件的制造要求,还能够提高生产效率和降低生产成本。
随着技术的不断进步,铝合金石膏型熔模铸造工艺在各个领域的应用将会越来越广泛。
石膏型铸造

缓凝剂主要有三类: (a)磷酸盐、碱金属硼酸盐、硼砂、硼酸等。 (b)有机酸及可溶性盐,如柠檬酸及其盐、琥珀 酸钠、乙基酸钠、甲基酸钠、草酸等。 琥珀酸钠的缓凝作用很强,只需要加入千分之几 就有明显的效果。 (c)蛋白胶、皮胶、硅溶胶、纸浆废液等。
增强剂用来增加石膏型的湿强度、干强度、焙烧 后强度以及高温强度。一般用某些硫酸盐如 Na2SO4、K2SO4、NiSO4、MgSO4等,其中以 MgSO4的效果最好。
• 石膏型需随炉冷却,当温度降至300℃以下时才可 以出炉,否则石膏型容易开裂,对复杂型温度应低 些。
填料
α-
半水
硅
石膏 硅石粉 线
100
石
%
高 高岭 莫来 铝 土 石矾
土
工 业 氧 化 铝
锆 英 粉
石 英 玻 璃
300℃ 空冷
微裂
极轻微 裂
不 裂
不裂
不裂
不 裂
不 裂
不不 裂裂
700℃ 空冷
碎裂 微裂
4.3.2浇注系统及冒口设计
• 对于石膏型铸造,浇注系统应满足如下要求: • A良好的排气能力,能顺利排出型腔气体,在顶部和易裹
气处开设出气口。 • B保证金属液充型平稳,避免出现紊流,卷气现象。 • C合理设置冒口,保证补缩。 • D脱模时浇注系统先熔脱,减小熔模对石膏型的胀型力。 • E浇注系统在铸件凝固时尽可能不阻碍铸件收缩,以防止
650~700℃左右,加压压力0.07MPa左右。
4.2.3 石膏型应用实例
图4-6是铝合金轮胎样件模具的石膏型 铸造实例。该样件从三维实体造型,制造 LOM原型(图4-6b)、硅橡胶模(图46c)、石膏型(图4-6d)到将烘干及焙烧 完毕的石膏型温度降低至180℃,浇注铝合 金制造出模具(图4-6f),总制造周期为4 天。
铸造工艺有哪些?

铸造工艺有哪些?铸造是指通过将液态金属或合金浇注至铸型中,冷却凝固后得到所需形状、尺寸及性能的零件制造工艺。
根据铸造过程中金属液体与铸型接触方式的不同,可以将铸造工艺分为以下几种。
砂型铸造砂型铸造是最古老、应用最广泛的铸造工艺之一,其特点是成本低,加工工艺简单,同时可铸铁件、铜件、铝件、镁件等多种材料。
其原理为将铸造所需形状制作成沙模,将熔化的金属灌注至模型中,并进行冷却凝固,取出后即可得到所需的零部件。
石膏型铸造石膏型铸造是通过石膏制作铸型,适用于制作高精度零部件,特别是艺术品、珠宝与玩具等小件产品。
其特点是成本低,模具制作快速,同时不易变形。
但其适用范围较窄,只适合铸造铜、铝、锌、铅等非铁合金。
精密铸造精密铸造通过高精度的模具制作和精密的铸造工艺实现制造高质量、高精度的零部件。
其适用于制造高要求的汽车零部件、航空零件、工具零部件、机械零部件、医疗器械等。
相比传统的砂型铸造和石膏型铸造,精密铸造精度更高,其特点为成本较高,但可以生产出形状复杂、漂亮美观的产品。
压铸压铸指的是将熔融的金属或合金加热至一定温度后,压入模具中进行铸造的工艺。
压铸适用于生产大量数量的复杂铸造件,特别是汽车、摩托车、电器等大宗产品。
其特点是生产速度快,制作成本低,制品表面精度高,强度大。
快速凝固铸造快速凝固铸造又称为凝固化学,是运用金属的短时间凝固固化方式,制造纤维状或片状铸件的一种特殊的铸造工艺。
它通过在凝固过程中加强对金属结晶状态的控制,使得基体的构型和性能均达到理想的状态。
适用于生产高端的电子、光学、航空、军事等领域的零部件。
以上是常见的铸造工艺,每种铸造工艺都有其适用的范围和特点,选择时需要根据实际需要进行合理选择。
石膏模铸铜方法
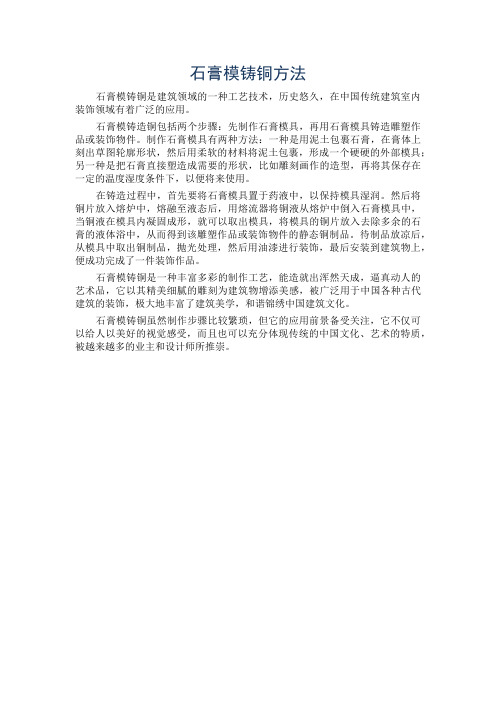
石膏模铸铜方法
石膏模铸铜是建筑领域的一种工艺技术,历史悠久,在中国传统建筑室内装饰领域有着广泛的应用。
石膏模铸造铜包括两个步骤:先制作石膏模具,再用石膏模具铸造雕塑作品或装饰物件。
制作石膏模具有两种方法:一种是用泥土包裹石膏,在膏体上刻出草图轮廓形状,然后用柔软的材料将泥土包裹,形成一个硬硬的外部模具;另一种是把石膏直接塑造成需要的形状,比如雕刻画作的造型,再将其保存在一定的温度湿度条件下,以便将来使用。
在铸造过程中,首先要将石膏模具置于药液中,以保持模具湿润。
然后将铜片放入熔炉中,熔融至液态后,用熔流器将铜液从熔炉中倒入石膏模具中,当铜液在模具内凝固成形,就可以取出模具,将模具的铜片放入去除多余的石膏的液体浴中,从而得到该雕塑作品或装饰物件的静态铜制品。
待制品放凉后,从模具中取出铜制品,抛光处理,然后用油漆进行装饰,最后安装到建筑物上,便成功完成了一件装饰作品。
石膏模铸铜是一种丰富多彩的制作工艺,能造就出浑然天成,逼真动人的艺术品,它以其精美细腻的雕刻为建筑物增添美感,被广泛用于中国各种古代建筑的装饰,极大地丰富了建筑美学,和谐锦绣中国建筑文化。
石膏模铸铜虽然制作步骤比较繁琐,但它的应用前景备受关注,它不仅可以给人以美好的视觉感受,而且也可以充分体现传统的中国文化、艺术的特质,被越来越多的业主和设计师所推崇。
石膏、熔模、砂型、离心、低压铸造优缺点

1.石膏型铸造分为:拔模型石膏铸造、失蜡铸造其特点为: 1.能够很好地复制出复杂的铸件。
由于石膏浆料的流动性能好,使得其充型性能优良,复膜性优异,型腔表面光洁。
制作出来的产品粗糙度等级能够达到Ra1.6um。
2.热导率低。
这一性能会使得金属液很好地填充模具,但亦会因凝结时间过长,而出现疏松、缩孔等缺陷。
3.透气性差。
因而要合理设置浇注系统以防止出现浇不足、气孔等缺陷。
4.耐火度不高,故只适用于中低温合金的铸造。
其浇注方式一般为:低压浇注、重力浇注、真空辅助浇注等2.熔模铸造是液态金属在重力作用下浇入由蜡模熔失后形成的中空型壳并在其中成形从而获得精密铸件的方法,又称为失蜡铸造。
熔模铸造的优点:⑴铸件精度高,表面粗糙度低,质量好,又称精密铸造。
⑵可铸出形状复杂的薄壁铸件。
⑶铸造合金种类不受限制,钢铁及非铁合金均可适用。
⑷生产批量不受限制,单件、小批、成批、大量生产均可适用。
熔模铸造的缺点:⑴工序复杂,生产周期长。
⑵原材料价格高,铸件成本高。
⑶铸件不能太大、太长,否则蜡模易变形,丧失原有精度。
3.离心铸造:优点:利用自由表面生产圆筒形或环形铸件时,可省去型芯和浇注系统,因而省工、省料,降低了铸件成本。
在离心力的作用下,铸件呈由外向内的定向凝固,而气体和熔渣因密度较金属小、则向铸件内腔(即自由表面)移动而排除,故铸件极少有缩孔、缩松、气孔、夹渣等缺陷。
便于制造双金属铸件。
如可在钢套上镶铸薄层铜材,用这种方法制出的滑动轴承较整体铜轴承节省铜料,降低了成本。
缺点:(1)依靠自由表面所形成的内孔尺寸偏差大,而且内表面粗糙,若需切削加工,必须加大余量;(2)不适于密度偏析大的合金及轻合金铸件,如铅青铜、铝合金、镁合金等。
此外,因需要专用设备的投资,故不适于单件、小批生产。
4.砂型铸造:粘土湿砂型铸造的优点是:①粘土的资源丰富、价格便宜。
②使用过的粘土湿砂经适当的砂处理后,绝大部分均可回收再用。
③制造铸型的周期短、工效高。
第八篇第七章-石膏型铸造285页
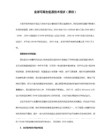
第七章石膏型铸造第一节石膏型铸造的工艺特点石膏型铸造采用易熔模料、硅橡胶、金属或木材等材质制成光洁精细的模样,灌以石膏浆料制成铸型,经烘干焙烧后浇注合金液最终获得光洁精密铸件。
因石膏浆料成形性及复制性很好,可浇出复杂薄壁精细的锌、铝、铜、金、银等有色合金铸件,铸件的最小壁厚可小于!"",表面粗糙度一般为!$%&!"左右,尺寸精度可达’(%()*#(%!(""+&)"";石膏型浇注后溃散性好便于清理;石膏对人体无害,不污染环境,价格较低,资源丰富。
石膏型铸造的缺点是石膏的热导率很小,铸型的透气性极低,易使铸件晶粒粗大和形成针孔,故主要用来生产整体大型复杂薄壁精密铸件和用其他方法难以铸造及有特殊要求的铸件。
第二节石膏型铸造方法的分类、工艺过程及应用一、石膏型铸造方法的分类按脱模方法不同可分为熔模石膏型铸造及模石膏型铸造两类,前者是加热熔模使其从石膏型中流出,后者是通过人力或机械方法将模样从型中拔出。
模石膏型铸造又可分为普通石膏型和发泡石膏型。
二、石膏型铸造的工艺过程三种石膏型铸造的工艺过程,见图,-.-!。
・・&/,$图!"#"$熔模石膏型铸造工艺过程图!"#"%发泡石膏型铸造工艺过程图!"#"&普通石膏型铸造工艺过程三、石膏型铸造的应用(一)熔模石膏型铸造主要用于整体复杂薄壁精密铸件,如大型电子仪器设备的框架、壳体、底座、飞机、导弹、雷达、宇航等行业用的泵体、附件壳体、机匣、叶轮、微波元件等,亦可用来铸造金银首饰,复制雕塑文物等艺术品。
(二)普通石膏型铸造主要用来生产各种模具如塑料、橡胶成形用模具,铸造模具,金属冲模等。
(三)发泡石膏型铸造用来生产叶轮类、框架类铸件和精密模具等。
・’(&%・第三节石膏及石膏型的理论基础一、石膏的名称、类型以及各种变体(一)石膏一般指二水石膏,化学式为!"#$%・&’&$。
第4章_石膏型铸造
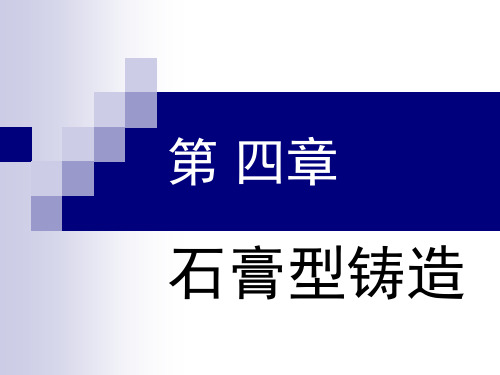
• 〔4模样材料
• 对于熔模石膏型:熔模材料〔中小件与熔 模铸造通用,中大件或尺寸精度要求高的铸 件,使用专用模料、气化模〔聚苯乙烯泡沫 等、水溶性模〔尿素模料、无机盐模料等.
• 对于起模石膏型:金属、硬质木材、橡胶、 塑料等.脱模剂有变压器油、凡士林、肥皂 液、经煤油稀释的石蜡硬脂酸等.
4.2.2 石膏混合浆料的制备及灌浆
100
石
%
高 高岭 莫来 铝 土 石矾
土
工 业 氧 化 铝
锆 英 粉
石 英 玻 璃
300℃ 空冷
微裂
极轻微 裂
不 裂
不裂
不裂
不 裂℃ 空冷
碎裂 微裂
极轻
极
不 微裂 极轻 轻
裂 或不 微裂 微
裂
裂
轻 微 裂
轻 微 裂
不 裂
• 〔4石膏型的浇注
•
焙烧好的石膏型在空气中很容易受
潮,必须尽快浇注.考虑到石膏型透气性低,导
知识回顾 Knowledge Review
β
8
5~7
7~ 12
50
5
• 〔2填料
• 单纯使用α型石膏并不能用于铸型制作,须加 入耐火材料的填料.其主要目的是减小石膏 型的线收缩和裂纹倾向.填料应具有合适的 熔点、耐火度、良好的化学稳定性、合适 的线膨胀率、发气量少、吸湿性小等性能. 常用填料的种类较多,其中以SiO2-Al2O3系 材料应用较广泛.各种填料对石膏型性能的 影响见下表.
浇不足等缺陷. • 5石膏型耐火度低,适于生产铝、锌、铜、
• 石膏型铸造的应用范围:
• 适用于生产尺寸精确\表面光洁的精密 铸件,尤其是大型复杂薄壁铝合金铸件, 最小壁厚可达0.5mm.
- 1、下载文档前请自行甄别文档内容的完整性,平台不提供额外的编辑、内容补充、找答案等附加服务。
- 2、"仅部分预览"的文档,不可在线预览部分如存在完整性等问题,可反馈申请退款(可完整预览的文档不适用该条件!)。
- 3、如文档侵犯您的权益,请联系客服反馈,我们会尽快为您处理(人工客服工作时间:9:00-18:30)。
5.浇注系统及冒口设计
1. 石膏型精密铸造的浇冒系统应满足下列要求: (1)有良好的排气能力,能顺利排出型腔中气 体,在顶部和易憋气处要开设出气口。 (2)要保证合金液在型腔中流动平稳,顺利充 满型胶,避免出现涡流,卷气现象。 (3)合理设置冒口,保证补缩。 (4)脱模时浇注系统应先蒋先,减小熔模对石 膏型的膨胀力。 (5)浇注系统在铸件凝固过程中应尽可能不阻 碍铸件收缩,以防止件变形和开裂。
7.石膏浆料
1.真空灌浆 为提高浆料的充填能力,应在真空条件 下灌浆。 2.熔模脱除和石膏型烘干 3.石膏型焙烧 石膏型焙烧的主要目的是去除残留于石 膏型中的模料、结晶水以及其它发气物, 同时完成石膏型中一些组成物的相变过程, 使其体积稳定。焙烧炉可用天然气炉、电 阻炉。
4.合金熔炼及浇注 (1) 合金熔炼 石膏型精密铸造以铝合金为主,一般适用于砂 型铸造的铝合金亦能用于石膏型精铸,其中以铝 硅类合金用得最多。为获得优质的铝铸件,一定 要采用最有效的精炼除气工艺和变质处理方法。 (2) 浇注工艺参数 金属液的浇注温度和石膏型温度两者应合理配 合,以取得优良铸件质量,石膏型温度可控制在 150~300℃之间,铝合金浇注温度一般可低于其 它铸造方法,控制在700℃左右,对大型薄壁铸件 浇注温度可适当提高。 5.铸件清整 对大型复杂薄壁铝精铸件必须进行大量细致的 清理、修补和校正等工作。
4.应用范表面 光洁的精密铸件,特别适宜生产大型复杂 薄壁铝合金铸件,也可用于锌、铜、金、 银等合金铸件。铸件最大尺寸达 1000×2000mm、重量0.03~908kg,壁厚 0.8~1.5mm(局部0.5mm)。石膏型精密铸 造己被广泛应用于航空、宇航、兵器、电 子、船舶、仪器、计算机等行业的零件制 造上。
2. 浇注系统类型选择 一般浇注系统可分顶注、中间注、 底注和阶梯注几种。对高度大的薄 壁筒形、箱形件也可用缝隙式或阶 梯式浇注系统。对某些铸件亦可采 用平注和斜注。
3. 内浇口位置选择 石膏型表面硬度不够高、热导率小,因此 内浇口一般不应直对型壁和型芯,防止冲 刷型壁和型芯,而应沿着型壁和型芯设内 浇口。对复杂的薄壁件为防止件变形及裂 纹,内浇口应均匀分布,避免局部过热及 浇不足缺陷。内浇口应尽可能设在铸件热 节处,利于补缩。
石膏型铸造
2011071107 夏天
1 概述
石膏型精密铸 造是用世纪70 年代发展起来 的一种精密铸 造新技术其工 艺过程见图。
2.定义
它是将熔模组装,并固定在专供 灌浆用的砂箱平板上,在真空下把 石膏浆料灌入,待浆料凝结后经干 燥即可脱除熔模,再经烘干、焙烧 成为石膏型,在真空下浇注获得铸 件。
6.石膏浆料的原材料
1. 石膏 天然石膏为CaSO4· 2H20,又称二水石膏。二水 石膏有七种变体。α型半水石膏做石膏型更为合适。 除石膏种类外,影响石膏强度的因素还有石膏的 细度、水固比、水温、搅拌时间等。 2. 填料 为使石膏型具有良好的强度,减小其收缩和裂 纹倾向,需要在石膏中加入填料。填料应有合适 的熔点、耐火度,良好的化学稳定性、合适的线 膨胀率、发气量少,吸湿性小等性能 3. 添加剂 为提高石膏型焙烧后强度、改变石膏型凝结时 间和清理性,改变其线膨胀率等需在石膏浆料中 加人添加物。
3.工艺特点
1. 石膏浆料的流动性很好,又在真空下灌注成型, 其充型性优良,复模性优异,型精确、光洁。该 工艺不像一般熔模精密铸造受到涂挂工艺的限制, 可灌注大型复杂铸件用型。 2. 石膏型的热导率很低,充型时合金液流动保持 时间长,适宜生产薄壁复杂件。但铸型激冷作用 差,当铸件壁厚差异大时,厚大处容易出现缩松、 缩孔等缺陷。 3. 石膏型透气性极差,铸件易形成气孔、浇不足 等缺陷,应注意合理设置浇注及排气系统。