压铸基本知识
压铸基本知识
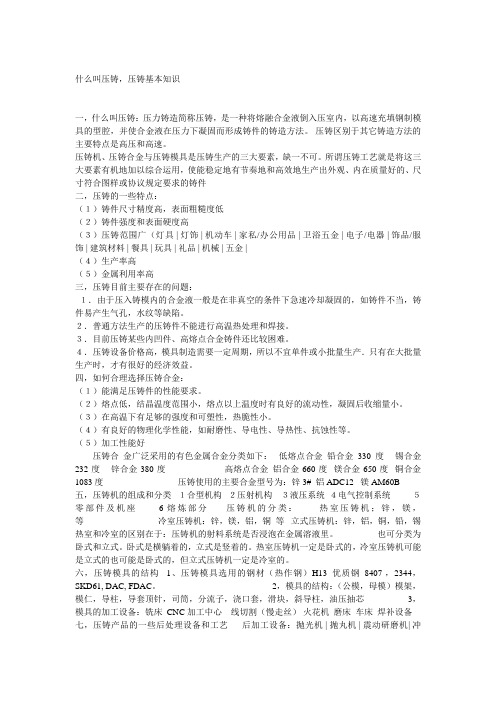
什么叫压铸,压铸基本知识一,什么叫压铸:压力铸造简称压铸,是一种将熔融合金液倒入压室内,以高速充填钢制模具的型腔,并使合金液在压力下凝固而形成铸件的铸造方法。
压铸区别于其它铸造方法的主要特点是高压和高速。
压铸机、压铸合金与压铸模具是压铸生产的三大要素,缺一不可。
所谓压铸工艺就是将这三大要素有机地加以综合运用,使能稳定地有节奏地和高效地生产出外观、内在质量好的、尺寸符合图样或协议规定要求的铸件二,压铸的一些特点:(1)铸件尺寸精度高,表面粗糙度低(2)铸件强度和表面硬度高(3)压铸范围广(灯具 | 灯饰 | 机动车 | 家私/办公用品 | 卫浴五金 | 电子/电器 | 饰品/服饰 | 建筑材料 | 餐具 | 玩具 | 礼品 | 机械 | 五金 |(4)生产率高(5)金属利用率高三,压铸目前主要存在的问题:1.由于压入铸模内的合金液一般是在非真空的条件下急速冷却凝固的,如铸件不当,铸件易产生气孔,水纹等缺陷。
2.普通方法生产的压铸件不能进行高温热处理和焊接。
3.目前压铸某些内凹件、高熔点合金铸件还比较困难。
4.压铸设备价格高,模具制造需要一定周期,所以不宜单件或小批量生产.只有在大批量生产时,才有很好的经济效益。
四,如何合理选择压铸合金:(1)能满足压铸件的性能要求。
(2)熔点低,结晶温度范围小,熔点以上温度时有良好的流动性,凝固后收缩量小。
(3)在高温下有足够的强度和可塑性,热脆性小。
(4)有良好的物理化学性能,如耐磨性、导电性、导热性、抗蚀性等。
(5)加工性能好压铸合金广泛采用的有色金属合金分类如下:低熔点合金铅合金330度锡合金232度锌合金380度高熔点合金铝合金660度镁合金650度铜合金1083度压铸使用的主要合金型号为:锌3# 铝ADC12 镁AM60B五,压铸机的组成和分类1合型机构2压射机构3液压系统4电气控制系统5零部件及机座 6 熔炼部分压铸机的分类:热室压铸机;锌,镁,等冷室压铸机:锌,镁,铝,铜等立式压铸机:锌,铝,铜,铅,锡热室和冷室的区别在于:压铸机的射料系统是否浸泡在金属溶液里。
《压铸安全知识》课件

减少企业财产损失
压铸设备和其他相关设施 昂贵,一旦发生事故可能 导致重大财产损失。
提高生产效率
安全的工作环境有助于员 工集中精力,提高工作效 率。
压铸生产中的主要危险源
高温金属液体
压铸过程中会产生高温金 属液体,如果防护措施不 当,可能导致烫伤。
高压射流
高压射流在将金属注入模 具时具有很高的动能,如 果不加以控制,可能对人 员和设备造成伤害。
01
压铸模具应安装安全防护装置
如机械手、气动夹具等,以防止操作员接触高温模具和熔融金属。
02
压铸模具应定期检查和维护
确保模具处于良好状态,防止因模具故障导致的事故。
03
压铸模具周围应设置安全警示标识
提醒操作员和其他人员注意安全,避免进入危险区域。
压铸工件后处理安全防护措施
工件后处理设备应安装安全防护装置
压铸机故障,造成人员伤亡。
事故原因
操作人员未经过专业培训,对压 铸机操作不熟悉,导致误操作。
事故教训
加强员工培训,确保操作人员熟 悉压铸机操作规程,提高安全意
识。
案例二:某公司压铸模具事故分析
事故经过
某公司生产过程中,压铸模具突然破裂,造成人 员伤亡。
事故原因
模具质量不过关,使用过程中出现疲劳裂纹。
压铸工件后处理操作规程
工件清理
对压铸完成的工件进行表面清 理,去除毛刺、飞边等杂质。
质量检查
对工件进行质量检查,包括尺 寸、外观、性能等方面,确保 符合要求。
涂装与包装
根据需要,对合格工件进行涂 装或包装,以保护表面不受损 伤或污染。
安全注意事项
在后处理过程中,应注意工件 温度,避免烫伤;操作人员应 佩戴防护用品,如口罩、手套
压铸工艺总结知识点

压铸工艺总结知识点压铸工艺是一种常用的金属加工工艺,通过对金属材料的加热融化后进行注入模具中,经过冷却固化后得到所需的零部件或产品。
它具有生产效率高、生产周期短、产品质量好等优点,被广泛应用于汽车制造、电子制造、机械制造等行业。
以下是对压铸工艺的总结知识点。
一、压铸工艺的基本原理1.压铸工艺的基本原理是利用金属在一定温度下的液态性质,在高压力下将熔融金属填充到模具腔中,并使其冷却凝固形成所需形状的零部件或产品。
2.压铸工艺主要涉及到金属材料的熔化、注入、冷却凝固等过程。
熔化过程通过加热金属到其熔点以上,使其变成液态;注入过程通过压力将熔融金属注入到模具中;冷却凝固过程通过降温,使金属从液态逐渐转变为固态。
二、压铸模具的结构和类型1.压铸模具是压铸工艺中最核心的设备之一,它包括上模和下模两部分。
上模为固定模,下模为动模。
2.压铸模具还包括模具腔、分型面、导向机构等部分。
模具腔是用来形成产品外形的腔体结构;分型面用于分离上模和下模;导向机构用于保证上下模的定位和运动方向。
三、压铸工艺的工艺参数1.压铸工艺中的主要参数包括注射压力、注射速度、保压时间、冷却时间等。
注射压力是指将熔融金属注入到模具腔中所施加的压力;注射速度是指熔融金属注入到模具腔中的速度;保压时间是指保持一定压力对熔融金属进行冷却固化的时间;冷却时间是指产品在模具中冷却至一定温度的时间。
2.合理的工艺参数能够保证产品的质量和生产效率,需要根据具体材料和产品要求进行调整和控制。
四、压铸材料的选择1.压铸工艺主要适用于铝合金、镁合金、锌合金等低熔点金属的加工,也可以用于一些高熔点金属材料的加工。
2.压铸材料的选择需要考虑产品的机械性能、导热性能、耐腐蚀性、成本等因素。
五、压铸工艺的优缺点1.压铸工艺具有生产效率高、生产周期短、产品质量好等优点,能够实现高精度、高复杂度的零部件生产。
2.压铸工艺的缺点是模具制造和维护成本较高,适用于大批量生产的零部件。
压铸知识培训资料
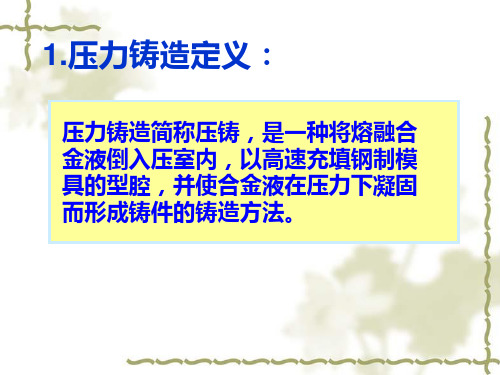
5.压铸机、压铸金属及压铸模具是组成压 铸工艺的3个要素。
卧式压铸机
立式压铸机
6.压铸机分类:
压铸机一般分为热压室压铸机和冷压室压铸机两大类。 冷压室压铸机按其压室结构和布置方式分为卧式压铸机 和立式压铸机(包括全立式压铸机)两种。 热压室压铸机(简称热空压铸机)压室浸在保温溶化坩 埚的液态金属中,压射部件不直接与机座连接,而是装 在坩埚上面。这种压铸机的优点是生产工序简单,效率 高;金属消耗少,工艺稳定。但压室,压射冲头长期浸 在液体金属中,影响使用寿命。并易增加合金的含铁量。 热压室压铸机目前大多用于压铸锌合金等低熔点合金铸 件,但也有用于压铸小型铝、镁合金压铸件。 冷室压铸机的压室与保温炉是分开的。压铸时,从保温 炉中取出液体金属浇入压室后进行压铸。
4.压力铸造适用材料及浇铸温度:
铝合金 铝硅系 610-650℃ 640-680℃ 600-620℃ 610650℃ 铝铜系 630-660℃ 660-700℃ 600-640℃ 630-660℃ 铝镁系 640-680℃ 660-700℃ 640-670℃ 650-690℃ 铝锌系 590-620℃ 620-660℃ 580-620℃ 600-650℃ 锌合金 420-440℃ 430-450℃ 400-420℃ 420-440℃ 镁合金 640-680℃ 660-700℃ 640-670℃ 650-690℃ 铜合金 普通黄铜 910-930℃ 940-980℃ 900-930℃ 900950℃ 硅黄铜 900-920℃ 930-970℃ 910-940℃ 910-940℃
7.压铸模具:
8.压铸工艺知识:
8-1、压力和速度的选择:按铸件结构确定。
8-2、浇注温度:从压定进入型腔时液态金属的平均温度。 8-3、压铸型的温度:在压铸前应进行预热。
铝合金压铸管理培训资料
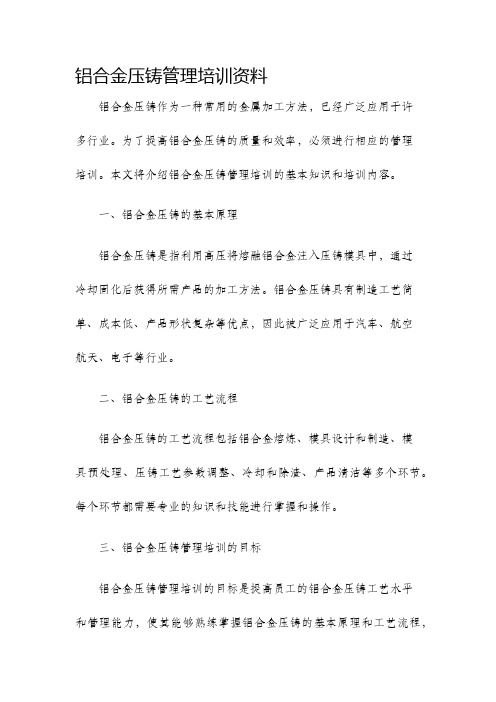
铝合金压铸管理培训资料铝合金压铸作为一种常用的金属加工方法,已经广泛应用于许多行业。
为了提高铝合金压铸的质量和效率,必须进行相应的管理培训。
本文将介绍铝合金压铸管理培训的基本知识和培训内容。
一、铝合金压铸的基本原理铝合金压铸是指利用高压将熔融铝合金注入压铸模具中,通过冷却固化后获得所需产品的加工方法。
铝合金压铸具有制造工艺简单、成本低、产品形状复杂等优点,因此被广泛应用于汽车、航空航天、电子等行业。
二、铝合金压铸的工艺流程铝合金压铸的工艺流程包括铝合金熔炼、模具设计和制造、模具预处理、压铸工艺参数调整、冷却和除渣、产品清洁等多个环节。
每个环节都需要专业的知识和技能进行掌握和操作。
三、铝合金压铸管理培训的目标铝合金压铸管理培训的目标是提高员工的铝合金压铸工艺水平和管理能力,使其能够熟练掌握铝合金压铸的基本原理和工艺流程,能够根据产品的要求进行模具设计和制造,能够合理调整压铸工艺参数,确保产品的质量和效率。
四、铝合金压铸管理培训的内容1.铝合金压铸的基本知识:包括铝合金的特性和性能、熔炼工艺、模具设计和制造的基本原理等。
2.铝合金压铸的工艺流程:包括熔炼、模具预处理、压铸参数调整、冷却和除渣等各个环节的操作方法和注意事项。
3.模具设计和制造:包括模具材料的选择、模具结构设计、模具加工和调试等。
4.压铸工艺参数调整:包括压铸机的调试和操作、壁厚控制、铸造温度和压力设置等。
5.质量控制和产品检验:包括产品的缺陷检查和修复、产品外观检验和尺寸检测等。
6.安全生产和环境保护:包括压铸过程中的安全操作和环境保护要求。
五、铝合金压铸管理培训的方法1.课堂培训:通过讲师的讲解和演示,向学员传授铝合金压铸的基本知识和技能。
2.实训操作:通过实际操作压铸设备和模具,让学员熟练掌握铝合金压铸的工艺流程和操作方法。
3.案例分析:通过分析铝合金压铸的典型案例,让学员了解实际生产中遇到的问题和解决方法。
4.考试评估:对学员进行理论和实际操作的考试评估,以评价培训的效果。
压铸基本知识
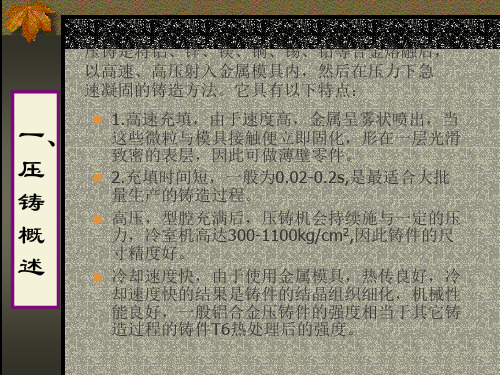
补缩。
压铸工艺条件
压力:压铸时型腔的压力叫压射比压,比压与铸件的致 密程度,轮廓的清晰程度密切相关。与相关的有增压压 力(压射缸压力)与冲头面积和压射缸面积。
温度:合金温度越高,合金的流动性与填充性能越好, 对成形有好处,但是太高会产生粘模、拉伤等现象;模 具温度会影响铸件的表面精度、收缩性、流动性、铸造 周期、变形程度,铝合金模温一般在180-300度之间为 宜,锌合金在150-200度为好。
冷却管堵塞
冷却设计不 佳 模具温度分布不均
压铸工艺
模具
分流锥太长
浇口太 薄
增压压力传 递不佳
增压传递受 阻
其它
加工余量大
人
压铸机
铝料
喷涂调整不当压射速度不良
冲头磨损
机械手舀料时 多时少
脱模剂过稀
冲头发卡
冲头漏水
精炼时间或温度不够
铝液除气不净
气 精炼剂不合格 孔
二、
1.热室机:射出部分浸在熔汤内的压铸机。 由于射料机构浸在熔汤内,所以合金的熔
压
点不能太高,否则影响射料机构的寿命,
铸
因此热室压铸机只适用锌、铅、锡等低熔 点的合金。
机 2.冷室机:射出部分不浸在熔汤内的压铸机,
简
适用于铜、铝等高熔点的合金。
介
镁合金则热室机与冷室机均可使用。冷室
压铸机还可按射料系统的摆放方式分为卧
时间:留模时间与喷涂时间
压铸模简介
勿用置疑,对铸件的质量影响最大的是压铸 模的好坏,一套压铸模的设计包括以下几个 方面:
分型面的设计 浇注系统的设计 排溢系统的设计 冷却系统的设计 抽芯机构的设计 顶出机构的设计
包括内浇口、直浇道、 横浇道的设计,是压铸 模设计的重中之重,需 慎之又慎
压铸模具设计基础知识

压铸模具设计基础知识一、概述压铸模具是用于压铸工艺的模具,在金属、塑料等材料的制品生产过程中起到关键作用。
压铸模具的设计质量直接影响产品的质量和生产效率。
本文将介绍压铸模具设计的基础知识,包括设计原则、材料选择、结构设计等内容。
二、设计原则1.功能性原则压铸模具应该符合产品的设计要求,能够满足产品的结构、尺寸、表面质量等要求。
设计过程中需要充分考虑产品的功能性需求,确保模具能够满足生产要求。
2.可制造性原则在设计压铸模具时,需要考虑到模具的加工工艺和生产成本。
设计应尽量简化,避免复杂的结构和加工工艺,以降低生产成本。
3.可靠性原则压铸模具在长期使用中需要具有稳定可靠的性能。
设计中需要考虑模具的寿命、耐磨性等因素,确保模具能够长时间稳定运行。
4.易维护性原则模具在使用过程中可能会有损坏或磨损,设计时需要考虑模具的易维护性,便于维修和更换受损部件。
三、材料选择压铸模具的材料选择直接影响模具的寿命和性能。
常用的模具材料包括工具钢、合金钢、硬质合金等。
在选择材料时需要考虑以下因素:1.硬度模具材料应具有足够的硬度和强度,能够抵抗压力和磨损,确保模具的稳定性和寿命。
2.热稳定性压铸过程中温度较高,模具材料需要具有良好的热稳定性,不易变形或烧损。
3.耐磨性压铸模具在长期使用中会有磨损,需要选择耐磨性好的材料,延长模具的使用寿命。
4.耐蚀性部分压铸过程中会有化学物质接触,模具材料需要具有良好的耐腐蚀性,避免腐蚀损坏。
四、结构设计压铸模具的结构设计直接影响产品质量和生产效率。
在设计时需要考虑以下因素:1.分型设计合理的分型设计能够提高产品的成型效率和质量,减少缺陷产生。
分型设计应考虑产品的结构特点和成型过程中的收缩变形。
2.冷却系统设计冷却系统设计影响压铸过程中的温度控制和冷却速度,直接影响产品的组织和性能。
设计时应考虑冷却系统的布局和冷却介质的选择。
3.排气系统设计在压铸过程中需要排除模具内的气体,避免气泡和气孔产生。
压铸知识培训完整版doc

压铸知识培训完整版doc标题:压铸知识培训完整版一、引言压铸作为一种重要的金属成型工艺,被广泛应用于汽车、摩托车、家电、通讯、航空航天等行业。
为了提高员工的专业技能和综合素质,使企业更好地适应市场需求,我们特举办本次压铸知识培训。
本文档将详细阐述压铸工艺的基本原理、设备、模具、原材料、工艺参数以及常见问题及解决方法等内容,旨在帮助员工全面了解压铸知识,提高实际操作能力。
二、压铸工艺基本原理1. 压铸定义:压铸是一种利用高压将熔融金属迅速注入模具型腔,并在压力作用下凝固成型的金属成型方法。
3. 压铸特点:压铸具有生产效率高、成型精度高、力学性能好、表面质量好、材料利用率高等优点。
三、压铸设备1. 压铸机:压铸机是压铸生产中的关键设备,主要由合模机构、注射机构、液压系统、电气控制系统等组成。
2. 辅助设备:辅助设备包括熔化炉、保温炉、输送系统、模具冷却系统、喷涂料装置等。
四、压铸模具1. 模具结构:压铸模具主要由动模、定模、型腔、浇注系统、冷却系统、顶出系统等组成。
2. 模具材料:模具材料应具备良好的导热性、耐磨性、抗热疲劳性、抗腐蚀性等性能。
3. 模具设计要点:模具设计应考虑产品结构、分型面、浇注系统、冷却系统、顶出系统等因素。
五、压铸原材料1. 常用压铸材料:压铸材料主要包括铝合金、锌合金、镁合金、铜合金等。
2. 材料选择原则:根据产品性能要求、生产成本、工艺特点等因素选择合适的压铸材料。
六、压铸工艺参数1. 压力:压力是压铸过程中的关键参数,包括合模力、注射力、保压力等。
2. 温度:温度控制对压铸产品质量具有重要影响,包括熔融金属温度、模具温度等。
3. 时间:时间参数包括填充时间、保压时间、冷却时间等。
七、压铸常见问题及解决方法1. 缩孔:增加浇注系统截面积、提高模具温度、降低注射速度等方法。
2. 气孔:优化模具设计、提高熔融金属温度、增加注射压力等方法。
3. 疲劳裂纹:选用高强度模具材料、提高模具表面质量、控制模具温度等方法。
压铸基础必学知识点
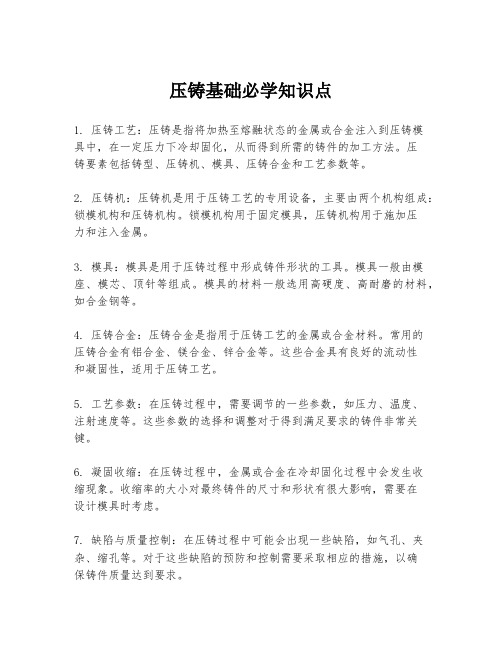
压铸基础必学知识点1. 压铸工艺:压铸是指将加热至熔融状态的金属或合金注入到压铸模具中,在一定压力下冷却固化,从而得到所需的铸件的加工方法。
压铸要素包括铸型、压铸机、模具、压铸合金和工艺参数等。
2. 压铸机:压铸机是用于压铸工艺的专用设备,主要由两个机构组成:锁模机构和压铸机构。
锁模机构用于固定模具,压铸机构用于施加压力和注入金属。
3. 模具:模具是用于压铸过程中形成铸件形状的工具。
模具一般由模座、模芯、顶针等组成。
模具的材料一般选用高硬度、高耐磨的材料,如合金钢等。
4. 压铸合金:压铸合金是指用于压铸工艺的金属或合金材料。
常用的压铸合金有铝合金、镁合金、锌合金等。
这些合金具有良好的流动性和凝固性,适用于压铸工艺。
5. 工艺参数:在压铸过程中,需要调节的一些参数,如压力、温度、注射速度等。
这些参数的选择和调整对于得到满足要求的铸件非常关键。
6. 凝固收缩:在压铸过程中,金属或合金在冷却固化过程中会发生收缩现象。
收缩率的大小对最终铸件的尺寸和形状有很大影响,需要在设计模具时考虑。
7. 缺陷与质量控制:在压铸过程中可能会出现一些缺陷,如气孔、夹杂、缩孔等。
对于这些缺陷的预防和控制需要采取相应的措施,以确保铸件质量达到要求。
8. 表面处理:压铸铸件的表面通常需要进行一些处理,以提高其表面质量和外观。
常见的表面处理方法有喷砂、抛光、喷漆等。
9. 机械加工:有些压铸铸件需要进行机械加工,以达到更高的精度和形状要求。
常见的机械加工方法有铣削、钻孔、车削等。
10. 环保与安全:在进行压铸工艺时,需要注意环保和安全要求。
例如,控制废气和废水的排放,遵守相关安全操作规程,确保工作人员的人身安全。
压铸常识知识点总结
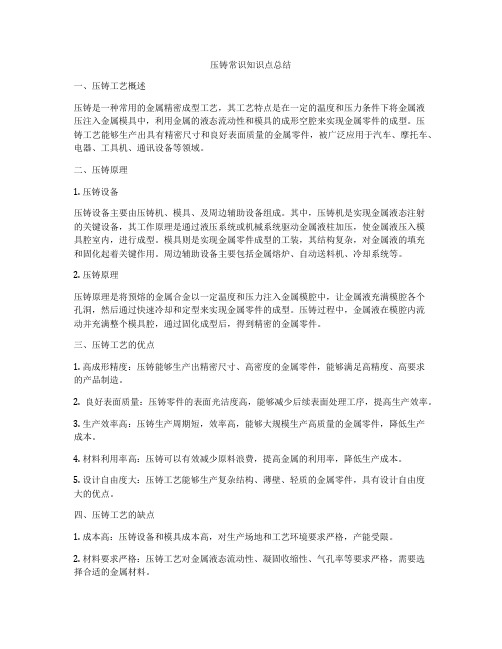
压铸常识知识点总结一、压铸工艺概述压铸是一种常用的金属精密成型工艺,其工艺特点是在一定的温度和压力条件下将金属液压注入金属模具中,利用金属的液态流动性和模具的成形空腔来实现金属零件的成型。
压铸工艺能够生产出具有精密尺寸和良好表面质量的金属零件,被广泛应用于汽车、摩托车、电器、工具机、通讯设备等领域。
二、压铸原理1. 压铸设备压铸设备主要由压铸机、模具、及周边辅助设备组成。
其中,压铸机是实现金属液态注射的关键设备,其工作原理是通过液压系统或机械系统驱动金属液柱加压,使金属液压入模具腔室内,进行成型。
模具则是实现金属零件成型的工装,其结构复杂,对金属液的填充和固化起着关键作用。
周边辅助设备主要包括金属熔炉、自动送料机、冷却系统等。
2. 压铸原理压铸原理是将预熔的金属合金以一定温度和压力注入金属模腔中,让金属液充满模腔各个孔洞,然后通过快速冷却和定型来实现金属零件的成型。
压铸过程中,金属液在模腔内流动并充满整个模具腔,通过固化成型后,得到精密的金属零件。
三、压铸工艺的优点1. 高成形精度:压铸能够生产出精密尺寸、高密度的金属零件,能够满足高精度、高要求的产品制造。
2. 良好表面质量:压铸零件的表面光洁度高,能够减少后续表面处理工序,提高生产效率。
3. 生产效率高:压铸生产周期短,效率高,能够大规模生产高质量的金属零件,降低生产成本。
4. 材料利用率高:压铸可以有效减少原料浪费,提高金属的利用率,降低生产成本。
5. 设计自由度大:压铸工艺能够生产复杂结构、薄壁、轻质的金属零件,具有设计自由度大的优点。
四、压铸工艺的缺点1. 成本高:压铸设备和模具成本高,对生产场地和工艺环境要求严格,产能受限。
2. 材料要求严格:压铸工艺对金属液态流动性、凝固收缩性、气孔率等要求严格,需要选择合适的金属材料。
3. 零件后处理工艺复杂:压铸后的零件可能需要进行除毛刺、研磨、喷漆等后处理工序,工艺复杂。
4. 高能耗:压铸过程需要耗费大量能源,对环境污染和能源消耗都有一定影响。
压铸常识知识点范文
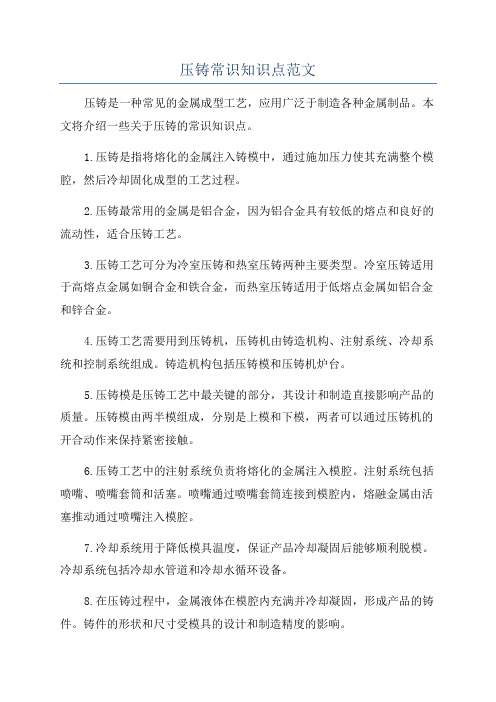
压铸常识知识点范文压铸是一种常见的金属成型工艺,应用广泛于制造各种金属制品。
本文将介绍一些关于压铸的常识知识点。
1.压铸是指将熔化的金属注入铸模中,通过施加压力使其充满整个模腔,然后冷却固化成型的工艺过程。
2.压铸最常用的金属是铝合金,因为铝合金具有较低的熔点和良好的流动性,适合压铸工艺。
3.压铸工艺可分为冷室压铸和热室压铸两种主要类型。
冷室压铸适用于高熔点金属如铜合金和铁合金,而热室压铸适用于低熔点金属如铝合金和锌合金。
4.压铸工艺需要用到压铸机,压铸机由铸造机构、注射系统、冷却系统和控制系统组成。
铸造机构包括压铸模和压铸机炉台。
5.压铸模是压铸工艺中最关键的部分,其设计和制造直接影响产品的质量。
压铸模由两半模组成,分别是上模和下模,两者可以通过压铸机的开合动作来保持紧密接触。
6.压铸工艺中的注射系统负责将熔化的金属注入模腔。
注射系统包括喷嘴、喷嘴套筒和活塞。
喷嘴通过喷嘴套筒连接到模腔内,熔融金属由活塞推动通过喷嘴注入模腔。
7.冷却系统用于降低模具温度,保证产品冷却凝固后能够顺利脱模。
冷却系统包括冷却水管道和冷却水循环设备。
8.在压铸过程中,金属液体在模腔内充满并冷却凝固,形成产品的铸件。
铸件的形状和尺寸受模具的设计和制造精度的影响。
9.压铸工艺可以实现高产量和高精度的制造。
通过合理调整压力和温度等工艺参数,可以获得不同材料和形状的铸件。
10.压铸工艺常用于制造汽车零件、家电产品、工业设备和通信设备等各种金属制品。
压铸工艺具有成本低、质量稳定、生产效率高的优势。
总之,压铸是一种重要的金属成型工艺,具有广泛的应用前景。
了解压铸工艺的基本知识,有助于正确选择和应用该工艺,提高产品的质量和生产效率。
压铸基本知识
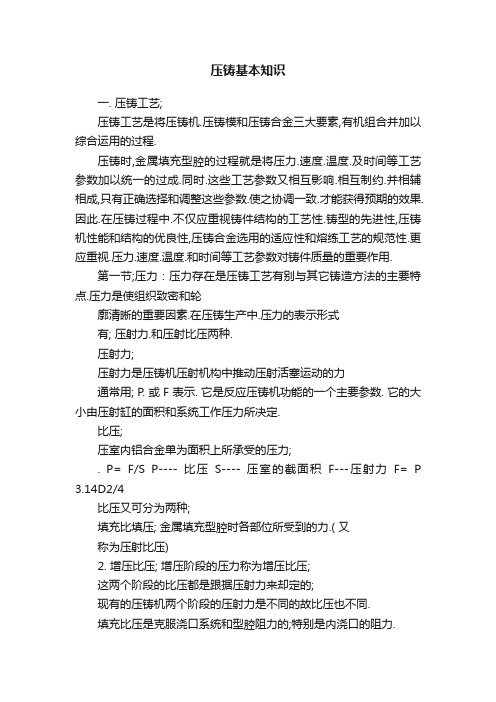
压铸基本知识一. 压铸工艺;压铸工艺是将压铸机.压铸模和压铸合金三大要素,有机组合并加以综合运用的过程.压铸时,金属填充型腔的过程就是将压力.速度.温度.及时间等工艺参数加以统一的过成.同时.这些工艺参数又相互影响.相互制约.并相辅相成,只有正确选择和调整这些参数.使之协调一致.才能获得预期的效果.因此.在压铸过程中.不仅应重视铸件结构的工艺性.铸型的先进性,压铸机性能和结构的优良性,压铸合金选用的适应性和熔练工艺的规范性.更应重视.压力.速度.温度.和时间等工艺参数对铸件质量的重要作用.第一节;压力:压力存在是压铸工艺有别与其它铸造方法的主要特点.压力是使组织致密和轮廓清晰的重要因素.在压铸生产中.压力的表示形式有; 压射力.和压射比压两种.压射力;压射力是压铸机压射机构中推动压射活塞运动的力通常用; P. 或 F 表示. 它是反应压铸机功能的一个主要参数. 它的大小由压射缸的面积和系统工作压力所决定.比压;压室内铝合金单为面积上所承受的压力;. P= F/S P---- 比压S---- 压室的截面积F---压射力F= P 3.14D2/4比压又可分为两种;填充比填压; 金属填充型腔时各部位所受到的力.( 又称为压射比压)2. 增压比压; 增压阶段的压力称为增压比压;这两个阶段的比压都是跟据压射力来却定的;现有的压铸机两个阶段的压射力是不同的故比压也不同.填充比压是克服浇口系统和型腔阻力的;特别是内浇口的阻力.增压比压决定了正在凝固的金属所受的压力.以及这时所形成的涨型力的大小.比压增大.结晶细. 细晶层增厚.由于填充特性改善.表面质量提高.气孔影响减轻.抗拉强度提高.但延伸率降低.合金属液在高比压作用下填充型腔.合金温度升高.流动性改变.有利与铸件质量的提高.影响压力的因素;1.温度越高有效比压越大2.模具温度过底.压力损失增大.3铸件结构和浇注系统的设计.填充阻力越大.压力降低大.影响压力的还有;机床的性能.液压系统的灵敏度.密封性.氮气的压力.油液温度的变化所引起粘度的波动.压射头与料筒之间的配合情况.五; 压射过程中的速度;一般的取值范围为; 一速0.3m/S;高速; 1---5m/S ;建压时间;0.03---0.05m/S.压射结束后.保持增压压力.直到铸件完全凝固.六; 比压的选择铸件一般分为两种; 有强度要求和无强度要求.比压的选择要跟据壁厚来选择;在一般情况下.压铸薄臂铸件时.由与型腔中的金属液流动阻力较大.因内浇口也薄,所以有较大的阻力,故要有较大的填充比压才能保证达到须要的内浇口速度.对与厚壁铸件,一方面选定的内浇口速度较低,并且金属的凝固时间较长,可以采用较小的填充比压;另一方面,为使铸件具有一定的致密度,还需要有足够的增压比压才能满足够要求对于形状复杂的铸件,填充比压应选择高一些. 但要考虑合金的类别;如合金.内浇口的速度.压机的合模力等因素填充比压的大小,主要是根据所选定的内浇口速度计算的.而增压比压的大小,主要是根据不同合金的类别选用不同的数值.当模具排气良好且内浇口与铸件臂厚设计恰当,可选小点,反之就要选大点.有气密性要求.面大.壁薄一般应为;50---60MPa第二节压射速度压射过程中,压射速度既受压力的直接影响,又与压力共同对铸件内部质量,表面要求和轮廓清晰程度起着重要作用. 速度的表示形式常为压射速度和内浇口速度,压射速度.压射头推动金属向前移动的速度称为压射速度.压射速度又分为多级( 一般有; 慢速.一快.二快)慢速; 也叫慢压射速度. 它是指冲头开始运动到封住熔杯口的速度一快; 也叫一级压射速度; 它是指从慢速结束开始到金属充满内浇口时的速度.二快;也叫二级压射速度;也叫快压射速度; 它是指从一快结束到金属全部把型腔填充完全时的速度.一快要求压室中的金属液充满压室,在既不过多降底合金属温度,又有利于排除压室中的气体的原则下,该阶段的速度应尽量的底,一般应底于O.3M/S,二快该速度由压铸机的特性决定,现有的国产压铸机一般在4-----10m/S,该速度是压铸机的主要参数之一,但在保正铸件内外质量的前提下速度越底越好.这样有利于按顺序填充.减少气孔的存在.二快的作用;(1)对铸件力学性能的影响;提高压射速度.则动能转化为热能,可提高合金的流动性.有利与消除流痕,冷隔等缺陷.可改变力学性能和表面质量.但速度过快时.合金液呈雾状与气体混合,产生严重的乱流.力学性能下降.铸件局部产生针孔.(2); 压射速度对填充特性的影响;提高压射速度可改变压射条件.可压铸出质量优良的复杂薄壁铸件.但速度过快时.填充条件恶化,在厚壁铸件中最显著.二快速度的选择和该考虑的因素;1; 要考虑熔化潜热,凝固温度范围.2; 模具温度高时.压射速度可适当降底;为提高模具寿命也可适当限制压射速度.3当铸件壁薄,形状复杂且对表面要求高时.应采用较高的压射速度.内浇口速度熔融金属在冲头作用下,经过横浇道到达内浇口,然后进入型腔,进入型腔的快慢.就叫内浇口速度.通常采用的内浇口速度范围是15-----70m/S同发生变化,这种变化的熔融金属进入型腔流动时,由与型腔的型状复杂.厚度不同.模具温度梯度不等因素的影响.流动的速度随时发生变化.这个速度称为填充速度.内浇口速度的高底对铸件力学性能的影响极大.内浇口速度太底.铸件强度就会下降.内浇口速度提高.强度就会上升.而过高又会导致强度下降.冲头.压射速度.与内浇口速度的关系;根据连续性原理;冲头压射速度越高.则金属流经内浇口的速度越快1.速度的选择;在压铸生产过程中,速度与压力共同对铸件内在质量.表面质量和轮廓.清晰度起着重要的作用.如果对压铸件的力学性能较高的要求.则不应选用过大的内浇口速度这样能降底乱流.所造成的涡流.因为涡流中含有空气和型腔内的涂料所挥发的气体.随着卷入涡流内的空气和蒸气的增多.压铸件内部的气孔就会增多.并切力学性能明显下降和变坏.如果压铸件是复杂的薄臂件.并切对表面质量提出了较高的要求.就应该选用较高的压射速度和内浇口速度.这一点是非常重要的.常用的铸件平均壁厚与内浇口速度的关系;见下表格;铸件壁厚内浇口速度铸件壁厚内浇口速度1 46----55 5 32----401.5 44----53 6 30----372 42----50 7 28----342.5 40----48 8 26----323 38----46 9 24----293.5 36----44 10 24----274 34----42以上单为; mm 内浇口速度; m/S内浇口速度与压射速度和压室直径内浇口截面积有直关系. 注; 这一点非常关键.(记住了这一点可以解决很多问题)内浇口速度可以调整以下三个方面; 生产中想提高压射速度1.调整冲头速度;(即;提高压射速度.开大节流伐)2.改变压室直径;(即;更换熔杯.大换小)3.改变内浇口截面积;(既;修模)压力; 速度;的分析;一快过慢铝液热损失过大.对填充不利.过快铝液不稳定易产生卷气.出现气孔.二快起点过早.会将料筒里的气体和浇道里的气体卷入型腔对质量严重不利.当二快过早迟.合金液会进入型腔.在快速来后铝液前沿与后来铝液不能完全融合.型成冷隔.或者流痕.增压起点对压铸件质量的影响;1.增压缸提前动作(也就是增压来的过早)待型腔填充完毕.增压缸活塞动作也终止,故无法行成增压后的高比压.铸件在较底压力下结晶成型.严重影响质量.(铸件内会出现缩孔)2.增压来的过迟(晚)铸件已凝固.增压虽建立.但已无效.不能起到作用.3.正确的增压转换点.应选在型腔基本填补满前.立既增压.才能获得预期的效果.4.压射头磨损受阻.压射不畅对工艺参数影响很大.对4的分析如下;4.1 压射冲头被咬伤卡住.会严重影响压力的传递和压射速度的稳定以及铸件质量和生产的正常进行.原因很多;主要原因是由与温度的影响波动.使压射头与压室的间隙也处与不断变化的状态. 这种间隙变化.在大直径的压室中最明显.故压射室直径越大.冲头受命越短.压射室浇料口下方.经常处与高温合金的冲击下.与上方形成明显的温度差,在不同膨胀量的作用下.产生扭曲.轴线同轴度可偏0.2mm,如果冲头配合间隙小与0.1mm压射杆又是刚性连接的情况.则冲头拉伤磨损情况会更加严重.故为了发挥压射系统的效率.必需合理选择压室和压射头的配合间隙.并解决温度差的影响.温度压铸过程中.温度对填充的热状态.操作的效率起着重要的作用.压铸中所指的温度是;1.浇铸温度;2.模具温度.温度的控制是获得优良铸件的重要因素.1;浇铸温度;汤汋里的铝合金注入料筒时的温度.(这时的温度测量不方便,一般以保温炉取汤口的温度表示.下面谈浇铸温度的作用和影响;随着合金液温度的升高.力学性能有所改变.但超过一定限度后.性能会恶化;原因;1.气体在合金中的溶解度随温度的升高而增大.虽然溶解在合金中的气体量较少.但在压铸过程中难以排出.对铸件质量是有影响的.2.含铁量随合金温度升高而增加.使流动性降低.结晶粗大.性能恶化.3.铝合金.镁合金随温度升高氧化加剧.氧化夹杂物使合金性能恶化.因此合金过热易产生缩孔.裂纹.气孔和氧化夹杂物.使产品力学性能变差.漏气.4.合金温度过底.会使成份不均匀,流动性差.影响填充.使产品充型不良.合金温度对填充流速有直接影响.浇铸温度过高.而且在高速的作用下.易产生涡流包气,对与凝固温度范围较宽的合金可采用高压.底温.底速.这样有利与型成顺序填充.提高铸件质量.但易引起粘模和溶蚀.不利与模具热平衡.降低模具寿命.故正确选择合金温度十分重要.影响浇铸温度的主要因素;1.合金的性质. 熔点. 热容量. 凝固范围;对与凝固范围宽的合金,可采用底温.底速.高压.和较厚的内浇口.这样.对厚壁铸件质量可以取得良好的效果.2.铸件结构的复杂成度;3.模具温度;4.比压和压射速度;因为动能转化为热能.可使合金温度升高.合金浇铸温度的选择通常在保证成型和所要求的表面内在质量的前提下.尽可能采用底的温度.(浇铸温度一般应高与合金液相合金类别锌合金铝合金镁合金浇铸温度410--450 610--700 640--700 线温度20---30度.)内浇口速度对合金温度的影响;合金液高速通过内浇口时.因摩擦会使温度升高(能量守恒原理.动能转变为热能)如; 当内浇口速度为40m/S时.铝合金液进入型腔时的温度将增加8度.而内浇口速度越大.温度就增加的越多.模具温度在压铸过程中.模具需要一定的温度.模具的温度是压铸工艺中又一重要的参数.它对提高生产率和获得优良铸件有着重要的作用.1.模具温度的作用和影响;在填充过程中.模具对金属液流温度.粘度.流动性.填充时间和填充流态等均有较大影响.模具温度过底时.表层冷凝后又被高速液流激破.产生表面缺陷.大的破碎块会被卡在内浇口处.严重影响填充速度和填充效果.使表面质量和内在质量下降.严重时产品不能成型.这种情况在生产中可经常看到.模具温度过高时.虽有利与获得光洁的铸件表面.但易出现缩裂和凹陷.2 . 模具温度对合金液冷却速度.结晶壮态.收缩应力有明显的影响.模具温度过底.收缩应力增大.铸件易产生裂紋.3 . 模具温度对模具寿命影响很大,强烈的温度变化.形成复杂的应力状态.频繁的应力交变.是导致模具过早龟裂的主要原因.4 . 模具温度对铸件尺寸公差等级有一定影响.模具温度稳定则铸件收缩率也相应稳定.5 . 影响模具温度的主要因素;5.1. 合金浇注温度.浇注量.热容量.和导热性.5.2 浇注系统和溢流槽的设计.用以调整平衡状态.5.3 压铸比压和压射速度.5.4 模具设计.( 模具体积大.则热容量大.模具温度波动小.模具材料导热性好.则温度分布就越均衡.有利与改善热平衡5.5 模具合理预热提高初温.有利与改善热平衡.可大大的提高模具寿命.5.6 生产频率快.模具温度升高.只要保持在一定范围对产品和模具都是十分有利的.5.7 合理的喷涂能起到隔热和散热的作用.6 . 模具温度对铸件力学性能的影响;模具温度提高.改善了填充条件.使力学性提高.模具温度过高.合金液冷却速度就会下降.细晶层(激冷层)厚度减薄.晶粒较粗大.强度下降.(漏气率升高)因此.为了获得质量稳定的优质铸件.必需将模具温度严格地控制在最佳的工艺范围内.(最好应用模温机)以保证模具在恒定范围内工作..7. 模具温度的选择和控制;7.1模具温度的选择应根据铸件的形状. 复杂成度.臂厚.臂厚差浇铸温度.合金的性质等因素来综合考虑.(铝合金一般应在220—280度)7.2模具温度冷却装置;为了获得稳定的模具工作温度.宜采用模具温度控制装制(即;温控装制.模温机)目前我司模具温控手段落后.只是通水冷却.通水量也未加控制.迫切需要以载热油为介质.用电子温度计进行控制.将模具温度稳定在工艺范围之内.只有这样才能降低质量的波动.提高成品率8 . 模具的热平衡;为了保正生产的连续进行.模具工作温度应保持在一定的范围内.这就必需使模具处与热平衡状态.模具热平衡指的是.在每一个压铸循环中.金属液传给模具的热量.等与冷却系统带走的和模具自然散发的热量第四节-时间压铸机工艺上的时间指的是;1.填充时间;2.增压建立时间. (建压时间)3.保压时间;4.留模时间;(冷却时间)5.顶出.顶回时间;6.循环时间;7.压射时间;时间是一个多元复合的因素.它与压力.速度温度.合金液的物理性质.铸件的结构有着密切的关系.(还与内浇口的截面积有关).所以在压铸工艺中是至关重要的.1. 填充时间;从金属进入型腔到型腔被完全充满.所需的时间;铸件填充所需的时间长短.与以上所说的压力.速度.温度.以及合金.铸件结构有着直接原因.可做分析;如压力小模具温度底.合金温度也底.肯定所需填充时间就长.反之.就短.(一般薄臂件填充时间要短.如;散热器.反之.就要长.具体多少为好必需根据实际情况而定.跟据经验和计算.铸件平均壁厚与填充时间应选在如下;平均壁厚填充时间平均壁厚填充时间1.0 0.01—0.04 5 0.048—0.0721.5 0.014—0.02 6 0.056—0.0842.0 0.018—0.026 7 0.066—0.102.5 0.022—0.032 8 0.076—0.1163.0 0.028—0.040 9 0.088—0.1383.5 0.034—0.05 10 0.1—0.164.0 0.040—0.062. 填充时间的选择;2.1 合金浇铸温度高时.填充时间可选长些;2.2. 模具温度高时.填充时间可选长些;2.3 .铸件厚壁且离浇口远时.填充时间可选长些;3; 增压建压时间;即从压射比压上升到增压比压所需的时间;从压铸工艺上说建压时间越短越好.但是.这个时间受压射系统的增压装置和油路设计的限制.性能很好的压铸机.其最短的建压时间也不会少与10m/s从压铸工艺上来说.建压时间的长短.取决与模具中合金液的凝固时间.凝固时间少长的合金.增压建压时间也可少长.但应短与合金液的凝固时间.因此.在机器压射系统和增压装置上.建压时间的可调性是非常重要的.若建压时间少长这时合金已成半固态或固态.压力就无法传递.失去了增压的作用.(铸件产生缩松.漏气)4; 保压时间;定义; 即从型腔填满到在增压比压作用下凝固的这段时间.称为保压时间.保压时间的作用;---冲头将压力通过还未凝固的料饼.传递到型腔.使正在凝固的金属在压力作用下结晶.从而获得致密的铸件.(保压不正常漏气比例会上升).一般来说有以下归率;1.合金结晶范围大.保压时间应选的长些;2.铸件平均厚度大.保压时间应的长些;3.内浇口厚.保压时间应选的长些;5 留模时间;定义; 从保压结束到开模顶出铸件的这段时间;足够的留.模时间.能够保正铸件在模具内凝固.冷却.使铸件建立足够的强度.在开模和顶出时.不致产生变形和拉裂.留模时间的选择.通常以开模和顶出不变型.不开裂的最短时间为宜.然而.过长也不好.降低了生产效率.降低了模温.不易脱模.由与合金有热脆性和收缩性.而引起产生裂纹.综上所述.压铸生产中的压力.速度.温度.时间等工艺参数可按下列原则进行调整;1.铸件壁越厚.结构越复杂.则压射力应越大;2.铸件壁越薄.结构越复杂.压射速成应越快;3.铸件壁越厚.留模时间应越长;4.铸件壁越薄.结构越复杂.浇铸温度应越高.冲满度的含义;浇入料筒里的金属占料筒总容量的成度.叫压室(或料筒)的充满度;充满度对与卧式冷室压铸机有着特殊的意义.因为.卧式压铸机的料筒在浇入合金后.并不是完全充满.而是在金属液面上方留有一定的空间.这个空间所占空间越大.存有空气就多.压入模具中的气体就越多.产品中的气体含量就多(产品中的气孔就越多)而充满度太小也不好.因为.合金在料筒里的温度下降的太快.激冷层厚.对填充十分不利.一般应在40—80%.最好是在65—75%之间.第六节压铸涂料压铸涂料包括;1. 料筒与冲头的配合部位;2.型腔表面;3.浇道表面;4.活动部位的配合部位; 以上所说的四个方面都要根据要求喷上或刷上不同润滑材料.这种不同的润滑材料通称为压铸涂料.涂料的正确选择和合理使用是一个非常重要的环节.它对模具寿命.铸件质量.生产效率.以及后道工续的表面处理有着重大的影响.涂料必须起到的作用;(应具备的特性)1.高温下具有良好的润滑作用;且发气量小.闪点高.2.具有良好的成膜性.(减小铸件与模具之间的摩擦使出模顺利)3. 保温性; 减少瞬间的热扩散.提高充型性具体的还可以这样解释;1.挥发点底.在100—150度时.能很快的挥发.不增加或少增加型腔中的气体.2.覆盖性好.与高温下结成薄膜层.但不易产生堆积.3.无味.不晰出或分解有害气体.4.性能稳定.在规定的保存期内不沉淀.不分解.5.对环境汚染小.涂料的使用;1.均匀;不要太厚.也不要漏涂.2.涂料的浓度尽可能的小;3.涂完后一定用气吹匀;涂料挥发后方可合模,压射.不然型腔中有大量的气体.使铸件产生气孔.甚至这些气体产生高的反压力.使铸件成型困难.4.生产中应特别注意模具排气道的清理.避免涂料聚集堵塞排气道.5.对与转弯内凹部位应避免涂料沉积.碳化.(喷完后多吹气)。
压铸模具结构基础知识

压铸模具结构基础知识压铸模具,听起来是不是很高大上?别担心,今天我们就来聊聊这个看似复杂其实很有趣的话题。
压铸模具其实就是用来生产金属零件的一种工具,它们的结构就像是机械界的“画板”,把金属液体像画颜料一样,一股脑儿地倒进去,等它冷却下来,就变成了我们需要的零件。
听起来简单吧?但背后的门道可多了。
1. 压铸模具的基本构造1.1 模具的主要部件首先,压铸模具的结构可以说是五花八门,但基本上离不开几个主要部件。
你想啊,模具里有一个“型腔”,就是我们说的零件的模样。
这一部分就像是你做蛋糕的模具,倒进去液体金属后,等它冷却下来,就能拿到你想要的形状。
除此之外,还有“型芯”,这东西可不是开玩笑的,它负责在模具中创造出复杂的内部形状,想想看,蛋糕里如果你想要个洞,必须得有个“芯”才能做出来。
接着,我们还得提到“合模系统”。
这个系统就像模具的心脏,负责把模具的两部分紧紧合在一起,防止金属液体从缝隙里漏出去。
不然一不小心,整个车间都成了“金属河”,那可就麻烦了!另外还有“冷却系统”,想象一下,金属液体在模具里翻滚得热火朝天,这时候得有冷却水道来帮忙降温,不然模具可是会变得“热火朝天”的哦。
1.2 模具的工作原理说到这里,可能有小伙伴会问,压铸模具到底是怎么工作的呢?简单来说,就是把金属加热到液态,然后用高压把它们注入模具型腔里。
听起来是不是有点像“万里长征走一回”?没错,压铸的过程就像是一场冒险,液体金属要穿越各种管道,最终落到“家”里——型腔中。
一旦金属注入,冷却系统就开始发挥作用,帮忙把这股热量赶走。
冷却完成后,模具打开,零件就“呼之欲出”了!这时,像是经历了一场“历险”的金属,终于变成了我们所需的产品,真是个让人兴奋的时刻。
2. 压铸模具的应用领域2.1 日常生活中的应用压铸模具的应用可谓是无处不在。
想想你的手机、汽车,甚至是厨房里的炊具,很多零件都是通过压铸模具制作出来的。
你见过那些闪亮亮的铝合金轮毂吗?没错,它们也是压铸的结果!生活中很多看似不起眼的小物件,背后其实都藏着压铸模具的智慧。
压铸必备知识点总结

压铸必备知识点总结一、压铸的原理及工艺流程1. 压铸的原理压铸是一种通过高压将金属液态材料注入模具中,使其凝固成型的金属制造工艺。
它可以制造复杂形状的零部件,并且具有较高的生产效率和成型精度。
2. 工艺流程(1)原料准备:首先需要将金属材料加热至液态状态。
(2)模具设计:根据零部件的形状和尺寸,设计相应的压铸模具。
(3)注射成型:将液态金属材料通过高压注入模具中,使其凝固成型。
(4)冷却处理:待零部件凝固后,进行冷却处理,确保其尺寸稳定。
(5)去除模具:将成型的零部件从模具中取出,进行去毛刺和表面处理。
二、压铸的材料及设备1. 压铸材料常见的压铸材料包括铝合金、锌合金、镁合金、铜合金等。
不同的材料有着不同的物理性能和适用范围,需要根据具体的使用要求进行选择。
2. 压铸设备(1)压铸机:是进行压铸的主要设备,通常由注射系统、射压系统、液压系统等组成。
(2)模具:根据产品的形状和尺寸,设计相应的压铸模具。
(3)辅助设备:包括加热炉、冷却设备、去毛刺机等,用于辅助完成压铸工艺的各个环节。
三、压铸工艺的注意事项1. 温度控制在压铸过程中,材料的温度控制非常重要。
过低的温度会影响材料的流动性,导致产品表面不光滑;而过高的温度则会引起材料氧化、蒸发,损害产品质量。
2. 压力控制压铸过程中施加的压力能够决定产品的密实度和形状精度。
因此,需要根据产品的具体要求,合理控制压铸的压力大小。
3. 模具设计合理的模具设计能够有效提高产品的成型质量。
需要考虑产品的结构特点、浇口设计、冷却系统等因素,以提高产品的整体性能。
4. 表面处理压铸后的产品通常需要进行去毛刺、抛光等表面处理工艺,以提高产品的表面质量和外观。
四、压铸的应用领域压铸工艺被广泛应用于汽车、机械、电子、航空航天等领域。
常见的应用包括汽车零部件、电子设备外壳、家用电器等。
五、压铸的发展趋势随着科技的不断进步,压铸工艺也在不断发展。
未来,压铸工艺将更加注重产品的高精度、高复杂度,推动压铸工艺向着智能化、自动化方向发展。
《压铸基本知识》课件

压铸技术逐渐应用于航空航天领域,如飞机零部件、卫星结构件等 。
环保要求
1 2
环保法规
随着全球环保意识的提高,各国政府对压铸行业 的环保法规日益严格,要求企业采取有效措施降 低环境污染。
节能减排
压铸企业应积极采取节能减排措施,如余热回收 、废弃物再利用等,以降低能耗和减少排放。
3
绿色生产
项参数。
02
操作过程
按照工艺流程,依次完成合模 、填充、增压、保压、开模等 步骤,确保压铸件的质量和稳
定性。
03
注意事项
注意安全操作,避免烫伤和机 械伤害,同时要定期维护和保 养设备,确保设备的正常运行
和使用寿命。
03
压铸模具
模具设计
03
模具结构设计
分模面选择
浇注系统设计
根据产品需求,设计合理的模具结构,确 保产品成型效果和生产效率。
推广绿色生产技术,使用环保材料和工艺,从源 头减少污染物的产生,促进压铸行业的可持续发 展。
THANKS
模具维护
定期检查
维修与更换
定期对模具进行检查,确保其处于良 好状态。
Hale Waihona Puke 对于损坏的模具部件,应及时进行维 修或更换。
保养与润滑
定期对模具进行保养和润滑,延长其 使用寿命。
04
压铸工艺
压铸温度
压铸温度
压铸过程中,模具和金属液的温 度是影响压铸件质量的重要因素 。合适的温度可以提高金属液的 流动性,减少气孔和裂纹等缺陷
《压铸基本知识》ppt课件
目录
• 压铸简介 • 压铸机 • 压铸模具 • 压铸工艺 • 压铸产品缺陷及防止措施 • 压铸行业发展趋势
压铸培训教程

压铸培训教程在现代制造业中,压铸工艺因其高效、高精度和可批量生产复杂形状零件的特点,被广泛应用于汽车、航空航天、电子等众多领域。
为了让大家更好地掌握压铸技术,接下来为大家详细介绍一下压铸的相关知识和操作要点。
一、压铸工艺概述压铸是一种金属铸造工艺,将熔化的金属在高压、高速下注入模具型腔,使其快速凝固成型。
压铸工艺的优点包括生产效率高、尺寸精度高、表面质量好、能够制造复杂形状的零件等。
但同时也存在一些局限性,如模具成本高、只适用于熔点较低的金属等。
二、压铸设备1、压铸机压铸机是压铸生产的核心设备,根据不同的分类方式可分为热室压铸机和冷室压铸机。
热室压铸机适用于熔点较低的锌、锡等金属,而冷室压铸机则适用于熔点较高的铝、镁、铜等金属。
2、模具模具是决定压铸零件形状和尺寸精度的关键因素。
模具通常由钢材制成,其结构复杂,需要经过精心设计和制造。
模具的设计要考虑到零件的形状、尺寸、脱模方式、冷却系统等因素。
3、熔化炉熔化炉用于将金属原料熔化至合适的温度和成分。
常见的熔化炉有坩埚炉、感应炉等。
三、压铸材料1、铝合金铝合金是压铸中最常用的材料之一,具有良好的机械性能、耐腐蚀性和可加工性。
常见的铝合金牌号有 ADC12、A380 等。
2、锌合金锌合金熔点低,流动性好,常用于制造小型、薄壁的零件。
3、镁合金镁合金具有重量轻、强度高的特点,在汽车和航空航天领域有广泛的应用前景。
四、压铸工艺参数1、压铸压力压铸压力是指金属液在注入模具型腔时所受到的压力,它直接影响到零件的致密度和力学性能。
2、压铸速度压铸速度指的是金属液注入模具型腔的速度,合适的压铸速度可以避免金属液在型腔中产生卷气、冷隔等缺陷。
3、浇注温度浇注温度是指金属液注入模具时的温度,过高或过低的浇注温度都会影响零件的质量。
4、模具温度模具温度对零件的凝固速度和质量有重要影响,通常需要通过冷却系统来控制模具温度。
五、压铸模具设计1、分型面的选择分型面的选择要考虑零件的形状、脱模方式和模具结构的复杂性等因素,应尽量选择在零件外形最大轮廓处,且便于脱模。
压铸工艺理论概述学习知识

压铸工艺理论概述学习知识一.压铸是压力铸造的简称,其实质量将熔融或半熔融金属注入压铸机的压室,随后在高压作用下,以极高的速度充填压铸型腔,并在压力作用下使其迅速冷却凝固成型的精密铸方法之一。
二.压铸工艺特点:A) 优点:(1)可以制造形状复杂,轮廓清晰,薄壁深腔的金属零件。
(2)压铸件尺寸精度较高。
(3)材料利用率高。
(4)可将其它材料嵌件直接嵌铸在压铸件上。
(5)铸件组织致密,具有较高的强度和硬度。
(6)可以实现自动化生产。
B) 缺点:(1)由于高速充填,快速冷却,型腔中气体来不及排出,致使压铸件常有气孔及氧化夹杂物存在从而降低了压铸件质量。
(2)压铸机及压铸模费用昂贵,不适合小批量生产。
(3)压铸件尺寸受到限制。
(4)压铸合金种类受限制。
三.压铸过程简述:1 ↓ 涂 料↓ 模 喷(刷)压 开→ 具 → 合 模 →铸 →模 → 预 成取 热 浇 注 型件↓ 5 保 温 4 2四.典型的压铸填充理论:(一).金属的填充理论:压铸过程中金属液的填充形态与铸件致密度、气孔率、力学性能、表面粗糙度等质量因素密切相关,在极短的填充瞬间它受到压铸件结构、填充速度、比压、温度、内浇口与压铸件断面厚度之比、合金液的粘度及表面张力、浇注系统的形状等制约。
长期以来人们对它进行了广泛的研究,提出了一些论点,但这些论点都是在特定的试验条件下得到的,有一定局限性,要求人们在应用中具体情况具体分析,使填充理论进一步完善和深化。
金属填充理论归纳起来有如下三种:1.喷射填充理论:当液流在速度、压力不变时,保持内浇口截面的形状喷射至对面型壁,称为喷射阶段;由于对面型壁的阻碍,部分金属呈涡流状态返回,部分金属向所有其他方向喷溅并沿型腔壁由四面向内浇口方向折回,称为涡流阶段。
涡流中容易卷入空气及涂料燃烧产生的气体,使压铸件凝回后形成0.1∽1米的孔洞,降低了压铸件的致密度。
当内浇口截面积S与型腔截面积A之比S/A>(1/3∽1/4)和内浇口速度为0.5∽15米/S,且撞击型腔壁或液流遇到阻碍时容易产生喷射填充。
压铸基础知识
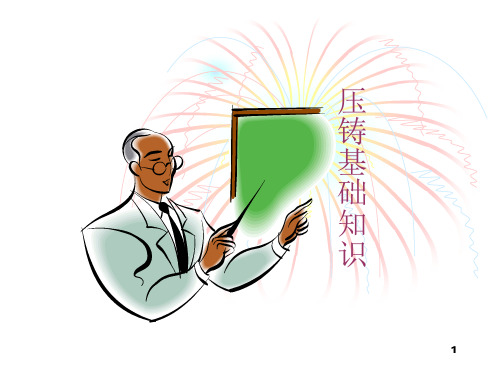
冷却料
浇口
主浇道
第一部分:模具
8
1.1.1按作用分类:
3 导向部分 导柱 导套 确保公母模合模时的位置精度
导套
导柱
第一部分:模具
9
1.1.1按作用分类:
4 顶出机构 顶针 顶出固定板 顶针垫板 支承钉 复位杆 实现零件的正常脱模
第一部分:模具
10
1.1.1按作用分类:
5 抽芯机构
斜导柱 实现与开模方向不一致的侧孔, 滑块 侧凹之型芯的脱模 压紧块 块定位装置 抽芯油缸 型芯
第四部分:表面处理
37
3.4、挫 3.4.1挫刀
大平方挫
三角挫
小圆挫
半圆挫
小平挫
旋转挫
38
第四部分:表面处理
3.4.2 品质控制重点
挫缺
挫刀选用 不当表面 太粗 挫刀选用 不当表面 太粗
挫缺
第四部分:表面处理
39
3.5、打磨 3.5.1打磨片
圆型打磨片 打磨片型号
第四部分:表面处理
40
3.6、喷砂 3.6.1喷砂机
3
压铸件目前存在的问题?
1.由于压入铸模内的合金液一般是在非真空的条件下急速冷却凝固的,如 铸件不当,铸件易产生气孔,水纹等缺陷。 2.普通方法生产的压铸件不能进行高温热处理和焊接。 3.目前压铸某些内凹件、高熔点合金铸件还比较困难。 4.压铸设备价格高,模具制造需要一定周期,所以不宜单件或小批量生 产.只有在大批量生产时,才有很好的经济效益。
第三部分:压铸
24
2.3、安全注意事项 • • • • 合模线处严禁站人 加料必须戴安全帽 高温熔炉内严禁放入带水物品或有水溅入 天车吊物行走时物品高出地面不得超过1M
压铸常识知识点

压铸常识知识点什么是压铸?压铸是一种常见的金属成型工艺,也被称为压力铸造。
它是通过将熔化金属注入到特殊的铸模中,然后施加高压力冷却和固化金属来制造金属零件的过程。
压铸通常用于生产复杂形状的零件,如汽车发动机零件、电子设备外壳等。
压铸工艺步骤1.设计模具:首先需要根据产品的设计要求,制作合适的压铸模具。
模具的设计应考虑到产品的形状、尺寸和材料等因素。
2.加热金属:将所需的金属材料(通常是铝合金或锌合金)加热至熔点以上,使其变为液态。
3.充填模具:将熔化的金属注入到事先准备好的压铸模具中。
注入时需要控制注入速度和压力,以确保金属能够充分填充模具中的空腔。
4.施加压力:在金属充填完毕后,施加高压力以冷却和固化金属。
通过施加压力,可以确保金属紧密填充模具,并使其在冷却过程中保持形状稳定。
5.开模和取出:待金属充分冷却后,拆卸模具并取出铸件。
这一步通常需要使用专业的工具和设备,以确保铸件的完整性和质量。
6.后处理:根据实际需求,对铸件进行一些后续处理,如去除余料、打磨、抛光、热处理等,以获得最终的产品。
压铸的优势和应用压铸作为一种高效的金属成型工艺,具有以下优势:1.生产效率高:压铸可以实现自动化生产,大大提高了生产效率。
每个模具往往可以生产多个产品,而且生产周期相对较短。
2.零件质量好:压铸可以生产出形状复杂、尺寸精确的金属零件,具有较高的一致性和稳定性。
同时,压铸可以提供优良的表面光洁度和一致的机械性能。
3.节约材料:压铸过程中可以循环利用金属材料,减少了材料的浪费。
并且,由于压铸零件具有较高的强度和刚度,可以减少零件的数量,达到节约材料的目的。
压铸广泛应用于各个领域,包括汽车工业、电子设备、家电、通信设备等。
它可以制造出各种复杂形状的零件,如汽车发动机零件、手机外壳、航空航天部件等。
压铸还可以与其他加工工艺结合使用,如机加工、表面处理等,满足不同的产品需求。
压铸的未来发展随着科技的不断进步,压铸工艺也在不断发展和改进。
- 1、下载文档前请自行甄别文档内容的完整性,平台不提供额外的编辑、内容补充、找答案等附加服务。
- 2、"仅部分预览"的文档,不可在线预览部分如存在完整性等问题,可反馈申请退款(可完整预览的文档不适用该条件!)。
- 3、如文档侵犯您的权益,请联系客服反馈,我们会尽快为您处理(人工客服工作时间:9:00-18:30)。
壓 鑄 模 設 計
2. 3. 4.
2012/7/28
Macherchen
3
二. 壓鑄概論
壓鑄設備
熱室 壓鑄機 冷室 立式(全) 卧式
噴嘴
坩堝
進口 沖頭
壓 鑄 模 設 計
壓室
熱室壓鑄機的壓室通常浸入坩鍋的
金屬液中,如圖示.
2012/7/28
Macherchen
4
三. 壓鑄制程溶湯的流動方式
(一)噴射及噴射流
降低鋅合金的可加工性
Macherchen
22
五.壓鑄合金及其性能
熱室壓鑄鋅合金中的合金元素
----結論
熱室壓鑄用鋅合金必須是以特高純度鋅為 基礎,加入特高純度鋁,鎂和銅
壓 鑄 模 設 計
2012/7/28
嚴格控制壓鑄溫度,避免攪拌 水口料重熔時,一定要嚴格控制重熔溫度以 避免鋁和鎂的損耗
Macherchen
鋁: 2.0~2.5(最小直徑)
(六)文字: 凸凹紋﹐直紋
壓 鑄 模 設 計
例:平行紋(直紋)高0.7MM﹐間距1MM﹐角度60.5。 外俓Φ34.5mm 共104牙
2012/7/28
Macherchen
11
四.成型工藝
(七)螺紋﹐齒輪
合金 最小螺距(P) 最小螺紋外徑 最大螺紋長度
鋅
壓 鑄 模 設 計
壓力 運動能(碰壁) 熱能和壓力
壓 鑄 模 設 計
2012/7/28
由噴射﹑噴射流轉變為壓力流
Macherchen
5
三. 壓鑄制程溶湯的流動方式
(二)壓力流
因沖撞,磨擦和氣體阻力等(抽象),運動能量耗盡(常發生在加強筋, 凸台,遠離澆口之部位),具有接受後繼金屬液中供給的壓力能,從而使金 屬液沿著型腔內壁前進的特性.利用這特性,可便以型腔排氣.在壓力流充
抗 拉 強 度 (Kg/mm ) 機 降 伏 強 度 (Kg/mm ) 伸 長 率 (%) 械 剪 切 強 率 (Kg/mm ) 硬 度 (勃 式 ) 衝 擊 強 度 (J) 質 疲勞強度 (Kg/mm ,5%10
2 3 2 2 2
2
28.8 -10 21.8 82 30.2 4.85 42 錠
性
壓 強 度 (Kg/mm )
我們經常遇到這樣的情況,工件剛壓鑄成型時,其表面 質量一切正常.可是,在室溫下存放數星期或幾個月後,表面 出現鼓泡.
Macherchen
19
五.壓鑄合金及其性能
熱室壓鑄鋅合金中的合金元素
---雜質元素-錫
錫在鋅合金錠中的含量絕對不能>0.001%, 在太鑄件中的含量不能>0.002%
造成合金晶間腐蝕 壓 鑄 模 設 計
2012/7/28
降低合金的抗沖擊性能 降低合金的抗拉伸強度 引起尺寸不穩定
Macherchen
20
五.壓鑄合金及其性能
熱室壓鑄鋅合金中的合金元素 ---雜質元素-鐵 鋅合金中鐵元素含不能>0.02%,鐵 元素可:
增加合金的硬度
壓 鑄 模 設 計
2012/7/28
但同時
增加合金的脆性
Macherchen
16
五.壓鑄合金及其性能
熱室壓鑄鋅合金中的合金元素 ----合金元素-銅 銅的加入可
增加合金的強度 提高合金的硬度
壓 鑄 模 設 計
2012/7/28
改善合金的抗磨損性能 降低合金的可延伸性 造成壓鑄件的尺寸不穩定性(產生時效脹大) (當銅的含量>1.25%時)
和合金中的鋁發生反應形成Al5Fe2金屬間化合物, 造成鋁元素的損耗並形成浮渣
在壓鑄件中出現硬點
Macherchen
21
五.壓鑄合金及其性能
熱室壓鑄鋅合金中的合金元素 ---雜質元素-硅 硅在鋅合金中的含量絕對不能0.02%, 提高鋅合金的脆性轉變溫率~20度 壓 鑄 模 設 計
2012/7/28
2012/7/28
Macherchen
15
五.壓鑄合金及其性能
熱室壓鑄鋅合金中的合金元素 ---合金元素-鋁 鋁的加入可`
降低合金對鐵的反應能力,因此降低了合金對鋅鍋,鵝 頸及模具的侵蝕
壓 鑄 模 設 計
2012/7/28
降低合金的熔點 增加合金的流動性能 改善合金的機械性能 產生Fe2 Al5浮渣,造成其含量的下降
0.75 1
外 6
內 10
外 8P
內 5P
鋁
(八)嵌件
2012/7/28
10
20
6P
4P
Macherchen
12
五.壓鑄合金及其性能
(一)壓鑄合金
鋁(Al),鋅(Zn),镁(Mg),鉛(Pb),錫(Sn),銅(Gu)
(二)壓鑄合金之鋅合金 熱室壓鑄用鋅合金中
壓 鑄 模 設 計
2012/7/28
有效合金元素:鋁(Al),銅(Gu),鎂(Mg) 有害雜質元素:鐵(Fe),硅(Si),鉛(Pb),鎘(Gd),錫(Sn) 來源於鋁 來源於鋅
6.64 382~387 27 113
熔解溫度℃ 物 導 電 係 數 (%ACS) 熱 傳 導 係 數 (W/M° K) 性 熱 膨 脹 係 數 (20~100 ℃ )(µm/m°k) 比 熱 kg ℃ 收縮率
381~386 26 109
381~387 27 113
27.36 0.419 6/1000
.004 .003 .002 -餘 6.64
.005 .004 .003 -餘
.004 .003 .002 -餘 6.64 379~390 25 105
.002 .002 .001
.005~.002
.003 .002 .001
.005~.002
份
Cd Sn Ni Zn 密 度 g/cm
餘 6.64
餘
23
六.壓鑄工藝
影響金屬液充填成型的因素很多﹐主要有﹕壓射壓力﹐壓射速度﹐充填時間﹐ 壓鑄模溫。
(一)壓射壓力的概念 定義1﹕壓射力指壓射沖頭作用于金屬液面上的力。
(這個力在壓鑄過程中不是恆定不變的,它大小隨不同的壓鑄階段變化而改變.)
壓射液壓缸 壓射沖頭 壓室熔液
壓 力 F
模具型腔
二. 壓鑄概論
壓力鑄造概念: (鋁,錫,鋅,镁,鉛,銅,合金)
即將溶融合金在高壓,高速條件下充型並在高壓下冷卻凝固成型的一 種精密鑄造方法, 簡稱壓鑄,其最終產品是壓鑄件.
1.
壓力鑄造特性: 高速充填:通常澆口速度達30~60m/s之間. 充填時間很短:中小型件通常為0.02~0.2s之間. 高壓充填:熱室機壓力通常為70~350kg/c㎡ 溶湯的冷卻速度快
。
β
2012/7/28
Macherchen
9
四.成型工藝
(四)圓角
當h 1=h 時﹕
r最小=Kh r最大= h
R=r+h
K值
鋅﹕1/4 鋁﹕1/2
壓 鑄 模 設 計
當h1=h時﹕ r≧ R=r+
2012/7/28
h+h1 3 h+h1 2
Macherchen
10
四.成型工藝
(五)孔
鋅: 0.8~1.5(最小直徑)
2012/7/28
3﹐與料流方向一致﹐避免亂流. 4﹐避免在肋上設置任何零部件.
Macherchen
8
四.成型工藝
(三)脫模斜度
合金 配合面 非配合面
壓 鑄 模 設 計
外(α) 內(β) 外(α) 內(β) 鋅合金 10' 15' 15' 45' 鋁合金 15' 通常外為內的一半 30' 30' 1
JIS壓鑄鋅合金成份標準
種類 鋅合金錠1種 鋅合金壓鑄件1種 鋅合金錠1種 鋅合金壓鑄件1種 編號
ZDC1 ZDC2
壓 鑄 模 設 計
化 學 成 份 備注 AI Cu Mg Pb Fe Cd Sn Zn 合金特性 應用例 3.9~4.3 0.75~1.25 0.03~0.06 0.003 0.075 0.002 0.001 餘 機械性質耐 剎車缸體,汽車 3.5~4.3 0.75~1.25 0.02~0.06 0.005 0.1 0.004 0.003 餘 腐蝕性佳 安全帶機構 3.9~4.3 0.03~0.06 0.003 0.075 0.002 0.001 餘 鑄造性,電鍍 水箱飾罩,化油 0.03 3.5~4.3 0.25 0.02~0.06 0.005 0.1 0.004 0.003 餘 性佳 器
壓 鑄 (三)再噴射 模 設 (四)補縮金屬流(保壓時間) 計
2012/7/28
填的部位,匯集著由噴射和噴射流所充填部分的氣體﹐必須開設排氣槽.
Macherchen
6
四.成型工藝
(一)壁厚 鋅合金: 0.3MM (最小) 鋁﹕0.5MM
最小孔徑: 0.7MM
壓 鑄 模 設 計
螺紋螺距﹕0.75MM
18
五.壓鑄合金及其性能
熱室壓鑄鋅合金中的合金元素
---雜質元素-鎘,鉛
鎘在合金中的含量絕對不能>0.003% 降低合金的機械性能 造成合金晶間腐蝕 鉛在合金中的翎量絕對不能>0.003% 降低合金的時效機械性能
壓 鑄 模 設 計
2012/7/28
當含量超過0.005%時,造成合金晶間腐蝕
各元素對鋅合金性質的影響
有益 鋁 (Al) 鋇 (Ba) 鈷 銅 鎂 鎳 鍶 (Co) (Cu) (Mg) (Ni) (Sr) 無益且無害 鉻 (Cr) 錳 (Mn) 鉬 (Mo) 鉀 (K) 銀 (Ag) 有害 銻 (Sb) 砷 (As) 鈹 (Be) 鎘 (Cd) 鈣 (Ca) 鉛 (Pb) 鋰 (Li) 矽 (Si) 鈉 (Na) 錫 (Sn) 鈦 (Ti) 釩 (V) 鋯 (Zr)