福建石化码头海上钻孔灌注桩基础施工方案word参考模板
钻孔灌注桩基础施工专项方案
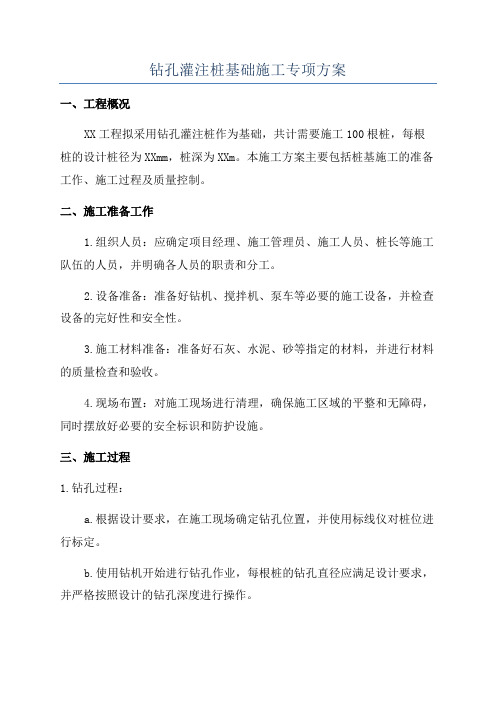
钻孔灌注桩基础施工专项方案一、工程概况XX工程拟采用钻孔灌注桩作为基础,共计需要施工100根桩,每根桩的设计桩径为XXmm,桩深为XXm。
本施工方案主要包括桩基施工的准备工作、施工过程及质量控制。
二、施工准备工作1.组织人员:应确定项目经理、施工管理员、施工人员、桩长等施工队伍的人员,并明确各人员的职责和分工。
2.设备准备:准备好钻机、搅拌机、泵车等必要的施工设备,并检查设备的完好性和安全性。
3.施工材料准备:准备好石灰、水泥、砂等指定的材料,并进行材料的质量检查和验收。
4.现场布置:对施工现场进行清理,确保施工区域的平整和无障碍,同时摆放好必要的安全标识和防护设施。
三、施工过程1.钻孔过程:a.根据设计要求,在施工现场确定钻孔位置,并使用标线仪对桩位进行标定。
b.使用钻机开始进行钻孔作业,每根桩的钻孔直径应满足设计要求,并严格按照设计的钻孔深度进行操作。
c.钻孔完毕后,使用泵车对孔内进行清洗,去除钻孔中的泥土和水分,并确保孔壁平整。
2.灌注过程:a.将混凝土材料(水泥、砂等)按照一定比例进行拌和制备,确保拌和均匀。
b.利用搅拌机搅拌好的混凝土材料通过泵车注入钻孔中,同时用长棍进行挤压和震动,以排除空隙和气泡。
c.灌注混凝土的速度应适中,以保证浆液能顺利填满钻孔,并采取措施防止堆积。
3.确认桩长:a.灌注完混凝土后,用测量工具对每根桩的高度进行测量,并与设计要求进行对比和确认。
b.如发现桩长不满足设计要求,则采取相应的措施修正。
四、质量控制1.施工过程中应对混凝土的配制比例、坍落度、龄期等进行严格的控制和检测。
2.对每根桩的钻孔位置、直径和深度进行记录,并与设计要求进行核对。
3.在灌注过程中,严格按照施工规范和要求进行振捣和震动,以确保混凝土填充到位,并排除空隙和气泡。
4.对每根桩的桩长进行测量和确认,并留存桩长记录,以备后续检查和验收。
5.施工过程中发现质量问题时,立即停工并进行整改,确保施工质量符合设计要求和规范。
码头工程钻孔灌注桩施工方案

码头工程钻孔灌注桩施工方案一、前言码头工程中钻孔灌注桩的施工方案具有重要意义,能够保证码头结构的稳定和安全。
本文将就钻孔灌注桩的施工方案进行详细探讨,以确保码头工程的顺利进行。
二、施工前准备在进行钻孔灌注桩施工前,需要进行以下准备工作: 1. 确定钻孔灌注桩的设计方案,包括数量、直径、深度等参数。
2. 制定施工计划,确定施工的时间节点和安排。
3. 调查土壤情况,确保对不同地质条件的应对措施。
4. 准备好必要的材料和设备,包括钻机、灌浆设备等。
三、钻孔灌注桩施工步骤钻孔灌注桩的施工一般包括以下步骤: 1. 孔口处理:清理孔口周围杂物,确保孔口清洁。
2. 定位:根据设计要求确定灌注桩位置。
3. 钻孔:使用钻机沿设计要求的位置进行钻孔。
4. 清孔:清除孔内的泥浆和杂物。
5. 灌浆:将混凝土灌入孔内,同时提前安装好钢筋。
6. 钢筋安装:根据设计要求在混凝土灌注过程中安装钢筋。
7. 桩身成型:待灌浆完成后,按照设计要求整齐成型。
四、施工注意事项在进行钻孔灌注桩的施工过程中,需要注意以下事项: - 土壤的承载力要满足设计要求,必要时进行加固处理。
- 注意孔内水土的稳定性,避免孔壁塌方。
- 灌浆时要保证混凝土的质量,避免出现空洞或虚浮情况。
- 钢筋的安装要按照设计规范进行,确保桩体的强度和稳定性。
五、施工质量验收钻孔灌注桩施工完成后,需要进行质量验收,主要包括以下内容: - 钻孔位置和尺寸是否符合设计要求。
- 桩体的强度和稳定性是否达标。
- 灌浆密实度和坍落度是否符合标准。
结语钻孔灌注桩作为码头工程中重要的施工方法,其施工方案的制定和实施至关重要。
只有严格按照设计要求和施工规范进行操作,才能确保码头工程的安全和稳定。
希望本文内容对您在码头工程钻孔灌注桩施工方案的制定和实施有所帮助。
灌注桩施工方案

施工方案报审表表A -1 监A-01工程名称: 福州港罗源湾港区淡头作业区14#、15#泊位工程编号: FABS-001 监理机构: 福建陆海建设监理所现报上福州港罗源湾港区淡头作业区14#、15#泊位工程《灌注桩施工方案》,已经我单位上级技术部门审查批准,请予审查和批准。
附件:1、灌注桩施工方案承包人:福建省港口工程有限公司福州港罗源湾港区淡头作业区14#、15#泊位工程项目经理部(章)负责人:日期:年月日监理机构审查意见:并于月日前报来监理工程师:日期:年月日福州港罗源湾港区淡头作业区14#、15#泊位工程灌注桩施工方案编制单位:福建省港口工程有限公司福州港罗源湾港区淡头作业区14#、15#泊位工程项目经理部编制:审核:日期:二○一四年十二月灌注桩施工方案一、编制依据1、福州港罗源湾港区淡头作业区14#、15#泊位工程施工组织设计;2、《福州港罗源湾港区淡头作业区14#、15#泊位工程施工图设计》文件;二.工程概况福州港罗源湾港区淡头作业区14#、15#泊位工程2#栈桥共有Ф1200mm灌注桩16根;1#栈桥共有Ф1000mm灌注桩18根.2座栈桥灌注桩设计桩顶标高均为7.1m;1#栈桥桩底标高分别为-48.8m、-49.8m和-50.8m,灌注桩进入强风化凝灰熔岩(碎块状)最小深度为1.5m;2#栈桥桩底标高均为-48.8m,灌注桩进入圆砾层、卵石层最小深度为1.8m.2、工程地质岩层情况:1#栈桥地质岩层情况:2#栈桥地质岩层情况:3、水文条件对桩施工的影响(1)、本工程所在水域,其潮汐属于规则半日潮,潮差较大,施工中可适当利用其潮差。
(2)、影响本港水上施工的主要因素为风浪,应注意风浪在下护筒过程中的影响。
灌注桩在施工的过程中应做好防台防洪措施,保证施工的质量。
4、灌注桩工程量表三、工程技术规格及主要设备1、遵循的技术规范标准(1)交通部《港口工程桩基规范》(JTJ/T245-98);(2)交通部《港口工程嵌岩桩设计与施工规程》(JTJ285-2000);(3)交通部《港口工程灌注桩设计与施工规程》(JTJ248-2001);地质勘测部门提供的《岩土工程勘察报告》;设计部门提供的《施工图设计图纸》;2、工程质量要求(1)建立以生产管理为核心的施工、技术、材料、安全和质量管理小组,开展质量教育工作,使每个职工都能树立良好的质量意识。
海中钻孔灌注桩专项施工方案(完整常用版)

海中钻孔灌注桩专项施工方案(完整常用版)1. 引言本施工方案旨在介绍海中钻孔灌注桩的施工过程及相关要点,以确保施工的安全性、有效性和质量。
2. 工程准备2.1 确定施工位置和雷达勘察结果在施工前,应准确确定钻孔灌注桩的施工位置,并进行雷达勘察,获取地下情况,以避免施工过程中的意外情况。
2.2 确保施工设备和材料的可行性施工前需检查和保证所使用的钻机、注浆机和材料等设备的正常运行和可行性,以确保顺利进行施工作业。
2.3 制定安全措施和防护措施在施工过程中,应制定和实施必要的安全措施和防护措施,包括人员安全、材料储存和安全装卸等方面,以确保工程安全。
3. 施工过程3.1 钻孔操作3.1.1 按照设计要求确定钻孔的位置和尺寸。
3.1.2 使用合适的钻机进行钻孔作业,确保钻孔的垂直度和水平度符合要求。
3.1.3 钻孔过程中要及时清理钻孔内的岩屑和泥浆。
3.2 灌注桩操作3.2.1 根据设计要求选择合适的注浆材料,并进行混合和搅拌。
3.2.2 使用注浆机将注浆材料注入钻孔内,确保注浆的均匀性和完整性。
3.2.3 注浆过程中要注意控制注浆压力和注浆量,确保灌注桩的质量。
3.3 后续工作3.3.1 完成灌注桩施工后,对施工现场进行清理和整理。
3.3.2 进行必要的监测和测试,确保灌注桩的稳定性和承载能力。
3.3.3 编制施工记录和验收报告,进行后续评估和归档。
4. 安全控制4.1 施工过程中要严格遵守相关的安全操作规程,保证人员安全。
5. 质量控制5.1 施工过程中要根据相关规范和要求进行严格的质量控制,确保施工质量。
6. 总结本施工方案详细介绍了海中钻孔灌注桩的施工过程和要点,强调了安全控制和质量控制的重要性。
通过合理的施工方案和严格的执行,可以确保施工的安全性、有效性和质量。
水上钻孔桩施工专项方案 Microsoft Word 文档
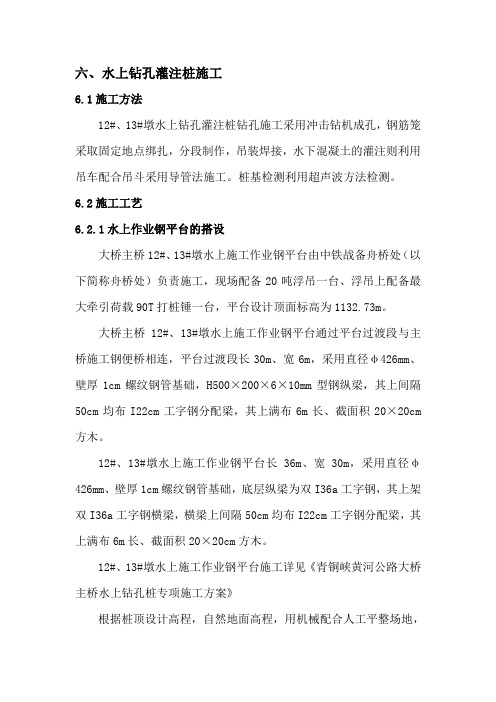
六、水上钻孔灌注桩施工6.1施工方法12#、13#墩水上钻孔灌注桩钻孔施工采用冲击钻机成孔,钢筋笼采取固定地点绑扎,分段制作,吊装焊接,水下混凝土的灌注则利用吊车配合吊斗采用导管法施工。
桩基检测利用超声波方法检测。
6.2施工工艺6.2.1水上作业钢平台的搭设大桥主桥12#、13#墩水上施工作业钢平台由中铁战备舟桥处(以下简称舟桥处)负责施工,现场配备20吨浮吊一台、浮吊上配备最大牵引荷载90T打桩锤一台,平台设计顶面标高为1132.73m。
大桥主桥12#、13#墩水上施工作业钢平台通过平台过渡段与主桥施工钢便桥相连,平台过渡段长30m、宽6m,采用直径φ426mm、壁厚1cm螺纹钢管基础,H500×200×6×10mm型钢纵梁,其上间隔50cm均布I22cm工字钢分配梁,其上满布6m长、截面积20×20cm 方木。
12#、13#墩水上施工作业钢平台长36m、宽30m,采用直径φ426mm、壁厚1cm螺纹钢管基础,底层纵梁为双I36a工字钢,其上架双I36a工字钢横梁,横梁上间隔50cm均布I22cm工字钢分配梁,其上满布6m长、截面积20×20cm方木。
12#、13#墩水上施工作业钢平台施工详见《青铜峡黄河公路大桥主桥水上钻孔桩专项施工方案》根据桩顶设计高程,自然地面高程,用机械配合人工平整场地,根据钻孔桩实际桩位的布置情况,在桩位附近修筑钻孔平台、钢筋笼摆放场地及施工机械进出场道路。
施工场地面积要满足安置钻机,钢筋笼摆放的需求。
场地平面尺寸应按照桩基设计的平面尺寸、钻机数量和钻机移位要求进行布置。
6.2.2桩位放样及护筒埋设在水中平台施工过程中,将12#、13#墩钻孔桩施工用钢护筒锤击入坚实的河床中,12#钻孔桩施工需要16根长12m、直径2.4m、壁厚1.5cm钢护筒,13#钻孔桩施工需要16根长12m、直径2.4m、壁厚1.5cm钢护筒。
钢护筒锤击施工由25吨浮吊完成,浮吊上配备最大牵引荷载90T双夹打桩锤一台。
钻孔灌注桩施工组织方案doc.完整版

钻孔灌注桩施工组织方案doc.完整版一:钻孔灌注桩施工组织方案1. 前言本文档旨在编制钻孔灌注桩施工组织方案,为项目的顺利进行提供指导和参考。
2. 项目概况2.1 项目名称2.2 施工地点2.3 施工时间2.4 施工单位3. 工程内容3.1 工程范围3.2 工程目标3.3 工期计划4. 施工准备4.1 设备准备4.2 人员组织4.3 材料准备5. 施工方案5.1 钻孔施工方案5.1.1 钻孔机械选择与布置5.1.2 钻孔参数设定5.1.3 钻孔进度计划5.2 灌注施工方案5.2.1 灌注桩混凝土配合比5.2.2 灌注施工工艺5.2.3 灌注桩的质量控制6. 安全防护措施6.1 作业人员安全6.2 设备安全6.3 施工环境安全6.4 紧急救援预案7. 环境保护措施7.1 施工过程中的环境保护7.2 施工废弃物的处理7.3 土地复原与恢复8. 预算与成本控制8.1 施工预算编制8.2 成本控制措施9. 项目管理9.1 施工进度管理9.2 质量管理9.3 安全管理9.4 环境管理9.5 合同管理附件:施工图纸、技术规范标准等。
法律名词及注释:1. 施工单位:指承担施工的企事业单位或个体工商户。
2. 钻孔灌注桩:是指采用钻孔方式在地基中穿过软土层,孔底可能进入坚硬的黄土、粘土、砂砾土等固体层,然后在孔内灌注钢筋混凝土进行加固的一种基础处理方式。
------------------------二:钻孔灌注桩施工组织方案1. 引言本文档旨在编制钻孔灌注桩施工组织方案,详细描述了施工过程中的各项工作步骤和措施。
2. 项目概述2.1 项目名称2.2 施工地点2.3 施工时间2.4 施工单位3. 施工内容3.1 工程范围3.2 工程目的和目标3.3 工期计划4. 施工准备4.1 设备准备4.1.1 钻孔机选择与布置4.1.2 钻具选型和配备4.2 人员组织4.2.1 施工人员配备与培训4.2.2 管理人员配备与职责4.3 材料准备4.3.1 混凝土配合比确定4.3.2 钢筋加工与配送4.3.3 其他辅助材料采购5. 施工方案5.1 钻孔施工方案5.1.1 钻孔机械布置与调试5.1.2 钻孔参数设定5.1.3 钻孔进度计划安排5.2 灌注施工方案5.2.1 混凝土搅拌设备布置5.2.2 灌注桩混凝土浇筑方法5.2.3 灌注桩质量控制方案6. 安全防护措施6.1 岗位安全教育与培训6.2 现场安全监控与警示标识6.3 危险区域限制与防护设施6.4 应急预案与事故处理7. 环境保护措施7.1 施工现场环境保护要求7.2 废弃物处理措施7.3 建筑废弃物合理利用方案8. 质量控制措施8.1 施工质量监督与检验8.2 钻孔质量监控措施8.3 灌注混凝土质量控制9. 合同和造价管理9.1 合同执行与变更管理9.2 造价控制与预算编制附件:1. 相关施工图纸2. 设备、人员资质证书3. 技术规范标准等本文所涉及的法律名词及注释:1. 施工单位:指承担施工的企事业单位或个体工商户。
钻孔灌注桩基础-施工方案范本
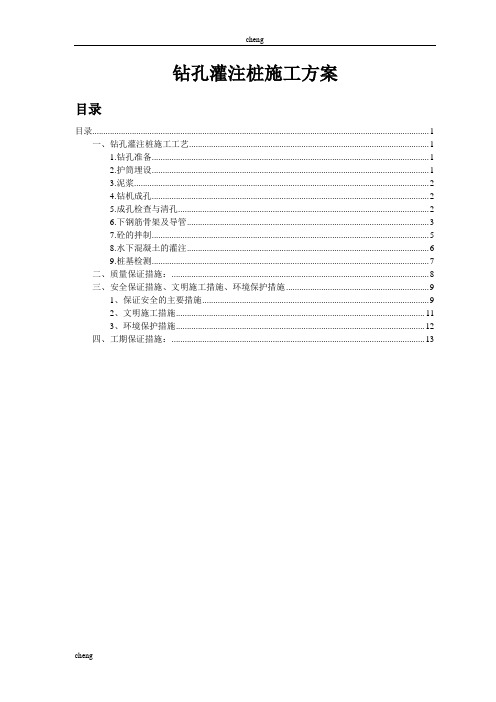
钻孔灌注桩施工方案目录目录 (1)一、钻孔灌注桩施工工艺 (1)1.钻孔准备 (1)2.护筒埋设 (1)3.泥浆 (2)4.钻机成孔 (2)5.成孔检查与清孔 (2)6.下钢筋骨架及导管 (3)7.砼的拌制 (5)8.水下混凝土的灌注 (6)9.桩基检测 (7)二、质量保证措施: (8)三、安全保证措施、文明施工措施、环境保护措施 (9)1、保证安全的主要措施 (9)2、文明施工措施 (11)3、环境保护措施 (12)四、工期保证措施: (13)钻孔灌注桩施工方案一、钻孔灌注桩施工工艺1.钻孔准备钻孔灌注桩工作平台布置时从以下方面考虑:钻孔灌注桩位于旱地时,规划施工所需面积,先清除杂物,换除软土,回填砂砾,整平并夯实,保证工作平台牢固稳定,承受工作时动荷载与施工机械的安全进出。
2.护筒埋设钻孔灌注桩护筒埋设时从以下方面考虑:(1).在整平夯实的工作平台上按设值定出桩位中心,并用十字线延长护桩,固定桩位中心,各方向延长护桩不少于两个。
(2).护筒采用0.8厘米厚的钢板制做,护筒内径大于桩径40cm。
(3).护筒下沉采用人工挖埋进行,护筒四周所填粘土必须分层夯实,埋设好的护筒按十字垂线方向用全站仪检查并在护筒口用漆标点,以便随时检查钻孔偏位情况。
(4).埋设好的护筒口应高出地面30cm,护筒平面位置的偏差不大于50mm,护筒倾斜率的偏差不大于1%。
(5).护筒埋设时底标高应略高于桩顶设计标高。
(6).根据地质情况确定护筒埋设长度,保证钻孔和灌注混凝土顺利进行。
3.泥浆钻孔灌注桩成孔采用泥浆护壁,泥浆的造浆以当地原料为主,采用塑性指数大于15的优质红粘土、膨润土与外加剂组成,对孔内泥浆或池内泥浆分批定期作出试验数据,并根据试验结果不断及时调整孔内泥浆。
在钻孔过程中,护筒内的泥浆顶面应始终高出筒外水位或地下水位1.0m。
使用后的泥浆要用泥浆泵抽到下一处泥浆池重复使用,避免造成浪费和污染。
4.钻机成孔根据本合同段的地质状况和工程数量,钻孔采用回旋钻机进行,钻孔前钻孔设备要检查完好,并且由有经验的施工员主持钻孔和填写钻孔记录,钻孔记录按每个工作班做好交接记录。
钻孔灌注桩施工方案doc.完整版

钻孔灌注桩施工方案doc.完整版【文档一】钻孔灌注桩施工方案一、施工概况1.1 工程概述1.2 目标和目的1.3 施工单位1.4 项目时间计划1.5 监理单位二、前期准备工作2.1 场地勘测2.2 文档准备2.3 施工人员组织三、施工设备与材料3.1 钻机选型3.2 钻杆和钻头选择3.3 灌注桩材料3.4 其他施工辅助设备四、施工工艺流程4.1 钻孔工艺流程4.2 钻孔灌注桩施工工艺流程4.3 护壁材料施工工艺4.4 灌浆工艺五、施工质量控制5.1 施工方案的可行性论证5.2 施工现场质量控制5.3 压浆试验5.4 砼强度试验六、安全管理6.1 安全交底6.2 安全措施6.3 灾害防治七、施工进度管理7.1 施工计划7.2 监测施工进度7.3 处理施工延误八、环境保护措施8.1 噪音控制8.2 扬尘治理8.3 废弃物处理九、沟通与协调9.1 内部沟通与协调9.2 项目相关方沟通与协调9.3 沟通记录附件:施工图纸、各类分析报告、进度计划表、安全交底记录表和会议纪要等。
【文档二】钻孔灌注桩施工方案一、施工概况及工程介绍1.1 工程背景1.2 施工目标和目的1.3 项目范围二、施工管理组织2.1 施工单位2.2 监理单位2.3 项目负责人2.4 施工人员组织三、施工前期准备工作3.1 场地勘测与设计3.2 施工方案编制3.3 材料准备四、施工设备与材料4.1 钻机选型与配置4.2 施工机械设备4.3 材料选用及质量要求五、施工工艺流程5.1 钻孔工艺流程5.2 灌注桩施工工艺流程5.3 桩身加固及防护工艺5.4 灌浆工艺六、施工质量控制6.1 质量控制管理体系6.2 灌注桩施工质量控制6.3 砼强度试验6.4 施工缺陷处理七、施工安全管理7.1 安全生产责任7.2 施工现场安全防护7.3 灾害防治措施八、施工进度及管理8.1 施工进度计划8.2 施工现场监控8.3 施工进度调整九、环境保护与建设9.1 环境保护措施9.2 废弃物处理附件:1. 技术文件2. 监测报告3. 工程图纸4. 安全交底记录5. 会议纪要附:法律名词及注释1. 施工单位:指承担具体工程建设的企业、事业单位和其他经济组织。
桩基础工程专项施工方案(钻孔灌注桩)
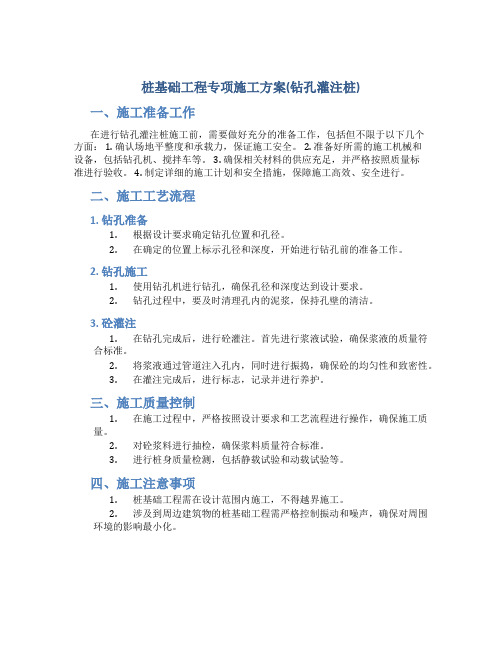
桩基础工程专项施工方案(钻孔灌注桩)一、施工准备工作在进行钻孔灌注桩施工前,需要做好充分的准备工作,包括但不限于以下几个方面: 1. 确认场地平整度和承载力,保证施工安全。
2. 准备好所需的施工机械和设备,包括钻孔机、搅拌车等。
3. 确保相关材料的供应充足,并严格按照质量标准进行验收。
4. 制定详细的施工计划和安全措施,保障施工高效、安全进行。
二、施工工艺流程1. 钻孔准备1.根据设计要求确定钻孔位置和孔径。
2.在确定的位置上标示孔径和深度,开始进行钻孔前的准备工作。
2. 钻孔施工1.使用钻孔机进行钻孔,确保孔径和深度达到设计要求。
2.钻孔过程中,要及时清理孔内的泥浆,保持孔壁的清洁。
3. 砼灌注1.在钻孔完成后,进行砼灌注。
首先进行浆液试验,确保浆液的质量符合标准。
2.将浆液通过管道注入孔内,同时进行振捣,确保砼的均匀性和致密性。
3.在灌注完成后,进行标志,记录并进行养护。
三、施工质量控制1.在施工过程中,严格按照设计要求和工艺流程进行操作,确保施工质量。
2.对砼浆料进行抽检,确保浆料质量符合标准。
3.进行桩身质量检测,包括静载试验和动载试验等。
四、施工注意事项1.桩基础工程需在设计范围内施工,不得越界施工。
2.涉及到周边建筑物的桩基础工程需严格控制振动和噪声,确保对周围环境的影响最小化。
五、总结钻孔灌注桩是一种常用的桩基础工程施工方式,合理的施工方案和严格的质量控制能够保障工程的顺利进行和质量安全。
在实际施工中,需要根据具体情况制定详细的施工方案,并严格执行,以确保工程的质量和安全。
(完整版)钻孔灌注桩施工方案
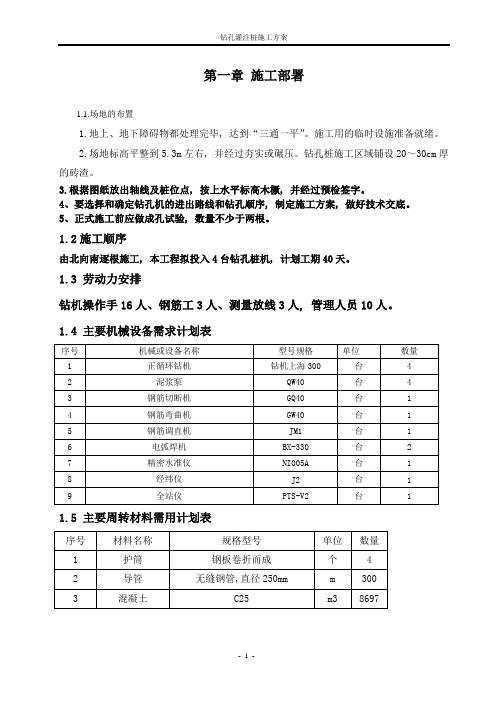
第一章施工部署1.1.场地的布置1.地上、地下障碍物都处理完毕, 达到“三通一平”。
施工用的临时设施准备就绪。
2.场地标高平整到5.3m左右, 并经过夯实或碾压。
钻孔桩施工区域铺设20~30cm厚的砖渣。
3.根据图纸放出轴线及桩位点, 按上水平标高木橛, 并经过预检签字。
4、要选择和确定钻孔机的进出路线和钻孔顺序, 制定施工方案, 做好技术交底。
5、正式施工前应做成孔试验, 数量不少于两根。
1.2施工顺序由北向南逐根施工, 本工程拟投入4台钻孔桩机, 计划工期40天。
1.3 劳动力安排钻机操作手16人、钢筋工3人、测量放线3人, 管理人员10人。
1.4 主要机械设备需求计划表1.5 主要周转材料需用计划表第二章施工方法2.1施工准备:1.材料: 混凝土采用商品混凝土2、主要机具: 正循环钻机、混凝土导管、套管、水泵、水箱、泥浆池、管等。
2.2 施工工艺流程钻孔灌注桩施工工艺流程图2.3 施工方法及技术要求2.3.1.埋设护筒1、护筒一般用3mm厚的钢板卷制而成, 其内径应大于钻头直径200mm。
护筒的顶部应开设溢浆口, 并高出地面≥200mm。
2、护筒用挖埋的方法埋置, 挖埋时, 护筒与坑壁之间用现场原土填实, 护筒中心应与桩位中心应重合, 偏差不得大于50mm, 护筒埋置深度在粘性土中不宜小于0.5m, 在砂土中不宜小于1m, 本工程埋深为80cm。
2.3.2.泥浆制备1.根据场地情况合理规划布置泥浆池、沉淀池、循环槽等泥浆循环系统。
泥浆池的容积为钻孔容积的1.2~1.5倍, 一般不宜小于4m3。
2、在粘性土层中成孔的泥浆, 可在原土注入清水造浆。
在砂土中成孔的泥浆, 应先在泥浆池中投入高塑性粘土或膨润土造浆。
3、以原土造浆的循环泥浆比重应控制在1.1~1.3;以高塑性粘土或膨润土造浆的循环泥浆比重在砂土层中控制在1.2~1.3, 在砂卵石层或容易塌孔的土层应加大至1.3~1.5, 泥浆的控制指标:粘度18~22S;含砂率不大于8%;胶体率不小于90%。
(完整版)钻孔灌注桩基础施工方案

钻孔灌注桩基础施工方案一、施工方法1.准备场地、测量放线:施工前应进行场地平整,清除杂物,钻机位置处平整夯实,准备场地,同时对施工用水、泥浆池位置,动力供应,砂石料场,拌和机位置,钢筋加工场地,施工便道,做统一的安排。
测量放线,根据设计图纸用经纬仪(或全站仪)现场进行桩位精确放样,在桩中心位置钉以木桩,并设护桩,放线后由主管技术人员进行复核,施工中护桩要妥善看管,不得移位和丢失。
2.埋设护筒护筒因考虑多次周转,采用3一10mm钢扳制成,护筒内径,使用旋转钻机时比桩径大10一20cm,使用冲击钻时比桩径大20一30cm,埋置护筒要考虑桩位的地质和水文情况,为保持水头护筒要高出施工水位(或地下水位)1.5m,无水地层护筒宜高出地面0.3—0.5m,为避免护筒底悬空,造成蹋孔,漏水,漏浆,护筒底应坐在天然的结实的土层上(或夯实的粘土层上),护筒四周应回填粘土并夯实,护筒平面位置的偏差应不超5cm。
护筒埋置深度:在无水地区一般为1一2倍的护筒直径。
在有水地区一般为入土深度与水深的0.8一1.1倍(无冲刷之前)。
3.选择钻孔机械:正循环钻机:粘性土、砂类土:砾、卵石粒径小于2cm,钻孔直径80-250cm,孔深30一100m。
反循环钻机:粘性土、砂类上、卵石粒径小于钻杆内径2/3,钻孔直径80一250cm,孔深泵吸<40m,气举100m。
正循环潜水钻机:淤泥、粘性上、砂类土、砾卵石粒径小于10cm,钻孔直径60一150cm,孔深50m。
全套管冲扳抓和冲击钻机:适用于各类土层,孔径80一150cm,孔深30一40m。
在钻孔过程中,钻机(架)必须保持平稳,不能发生位移和沉陷。
因此钻机安装就位时,底座应用枕木垫实塞紧,顶端用风绳固定平稳。
4.制备泥浆应选用塑性指数IP>10的粘性土或膨润土,对不同上层泥浆比重可按下列数据选用:粘性土和亚粘土可以就地造浆,泥浆比重1.1一1.2间。
粉土和砂土应制备泥浆,泥浆比重1.5—1.25:砂卵石和流砂层应制备泥浆,泥浆比重1.3—1.5。
(完整版)钻孔灌注桩基础施工方案

(完整版)钻孔灌注桩基础施工方案范本 1:钻孔灌注桩基础施工方案1. 引言1.1 项目概述1.2 目的1.3 范围1.4 术语定义(法律名词及注释)2. 前期准备工作2.1 地质勘察2.2 方案设计2.3 材料采购3. 钻孔设备与工具准备3.1 钻机选型3.2 桩材质准备3.3 钻孔设备与工具清单4. 施工过程4.1 钻孔平台搭建4.2 钻孔操作规范4.3 钻孔过程中的注意事项4.4 钻孔质量控制5. 灌注桩制作5.1 混凝土配合比设计5.2 灌注过程控制5.3 桩混凝土强度监测5.4 灌注桩质量控制6. 工程施工安全措施6.1 钻孔过程的安全注意事项 6.2 灌注过程的安全控制6.3 安全事故应急预案7. 附录7.1 施工工艺图纸7.2 施工材料证明书7.3 施工质量检测报告8. 结论8.1 项目总结8.2 施工效果评价附件:1. 工程图纸2. 材料证明书3. 施工质量检测报告法律名词及注释:1. 钻孔灌注桩:一种构筑物基础形式,通过钻孔施工并灌入混凝土,以达到加固地基的目的。
2. 地质勘察:针对工程所在区域的地质条件进行详细调查和研究的过程。
3. 施工效果评价:对工程施工结果进行评估和总结的过程。
范本 2:钻孔灌注桩基础施工方案1. 引言1.1 项目背景1.2 目的与范围1.3 术语定义(法律名词及注释)2. 基础设计2.1 地质勘察报告分析2.2 施工方案设计2.3 材料选用及规格3. 前期工作准备3.1 施工设备准备3.2 环境保护准备3.3 周边交通组织4. 钻孔施工4.1 钻孔设备及工具配置4.2 钻孔平台搭建4.3 钻孔操作流程4.4 钻孔质量控制5. 灌注桩制作5.1 混凝土配合比控制5.2 灌注过程要点5.3 灌注桩质量检验5.4 灌注桩质量控制6. 施工安全措施6.1 钻孔安全注意事项 6.2 灌注过程安全控制6.3 灾害事故应急预案7. 施工质量控制7.1 施工工艺与技术管控 7.2 施工质量监督检查7.3 现场质量控制要点8. 结尾8.1 工程总结8.2 建议和改进意见附件:1. 地质勘察报告2. 混凝土配合比设计表3. 施工设备配置清单法律名词及注释:1. 钻孔灌注桩:一种基于地下土层特性,通过钻孔施工并灌注混凝土,用于地基加固的建造工程形式。
钻孔灌注桩基础施工技术方案

钻孔灌注桩基础施工技术方案一、工程概述二、技术方案1.前期准备(1)制定工程施工方案,明确施工目标和施工步骤。
(2)组织专业技术人员进行现场勘察,确定施工方案的具体参数和要求。
(3)摆放、组装施工设备,包括钻机、钻具、灌浆设备等。
2.钻孔灌注桩施工(1)确定钻孔位置和孔径,并在地面上标注出孔位。
(2)启动钻机,逐渐下钻到设计孔深,并及时记录孔深和钻孔进度。
(3)钻孔完成后,进行清孔作业,将钻孔内的泥浆和杂物清除干净。
(4)进行砌筑钢筋笼,并将钢筋笼下沉至设计位置。
(5)注浆灌注,将预先调配好的灌浆料注入钻孔中,使灌浆料充分填满钻孔空间,并确保钢筋笼固定牢固。
(6)灌注完成后,进行养护,保持灌注桩在充分固结的条件下进行下一步的施工。
3.施工注意事项(1)钻孔施工期间要做好孔眼的保护,防止倒土或灰浆流入钻孔,以免对灌注桩的质量造成影响。
(2)注浆时要注意控制注浆压力和速度,确保灌浆料充分均匀地填满钻孔,并防止浆液外溢。
(3)钢筋笼要根据设计要求进行砌筑和放置,严格控制钢筋的质量和位置。
(4)施工期间要严格按照施工工艺进行施工,不得随意更改施工步骤。
(5)施工期间要进行充分的工地安全管理,确保施工人员的人身安全。
三、质量控制1.施工前,要进行地质勘察,确定施工地点的地质情况,以及设计要求和参数。
2.施工过程中要严格按照设计要求进行施工,如钻孔深度、孔径、钢筋笼的质量和位置等。
3.注浆灌注时要控制注浆压力和速度,确保灌浆料能够充分填满钻孔,并且浆液外溢情况要得到控制。
4.施工完成后要进行养护,保持灌注桩在充分固结的条件下进行下一步的施工。
5.施工结束后,要进行验收,检查灌注桩的质量是否符合设计要求和施工规范。
四、总结钻孔灌注桩基础是一种常用的地基处理方式,适用于土质较差或要求较高的地区。
施工过程中要严格按照设计要求和施工规范进行施工,并进行质量控制和验收。
只有确保施工质量,才能保证灌注桩的使用寿命和地基的稳定性。
水上钻孔灌注桩施工方案.docx
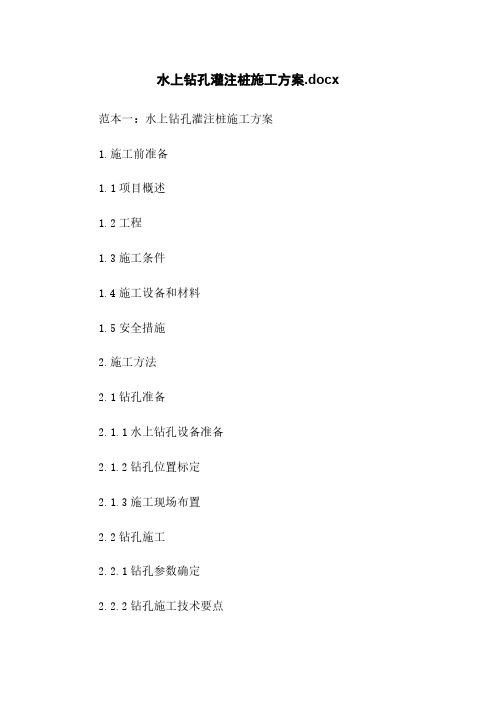
水上钻孔灌注桩施工方案.docx 范本一:水上钻孔灌注桩施工方案1.施工前准备1.1项目概述1.2工程1.3施工条件1.4施工设备和材料1.5安全措施2.施工方法2.1钻孔准备2.1.1水上钻孔设备准备2.1.2钻孔位置标定2.1.3施工现场布置2.2钻孔施工2.2.1钻孔参数确定2.2.2钻孔施工技术要点2.2.3钻孔质量控制2.3灌注桩施工2.3.1灌注桩钢筋配置预制2.3.2灌注桩灌注施工2.3.3灌注桩质量控制3.监测控制与质量保证3.1监测设备和方法3.2施工过程监测3.3质量保证3.3.1材料质量控制3.3.2施工质量控制3.3.3现场巡查与监督4.施工进度与组织4.1施工进度计划4.2施工组织及施工人员安排4.3施工报验与验收4.4施工管理5.施工安全与环境保护5.1施工安全措施5.2防护设施5.3环境监测与保护6.附录6.1施工图纸6.2材料供应合同6.3工艺文件及质量验收记录附件:1.施工图纸2.合同复印件法律名词及注释:1.施工前准备:进行工程施工前的各项准备工作,包括项目概述、工程、施工条件、施工设备和材料准备等。
2.钻孔施工:使用钻孔设备在地下钻孔,为后续灌注桩施工做准备。
3.灌注桩施工:将预制好的灌注桩钢筋放入钻孔中,再进行灌注施工,形成稳定的地基。
4.监测控制与质量保证:对施工过程进行监测,确保施工质量符合标准要求,并采取相应的质量保证措施。
5.施工进度与组织:制定施工进度计划,安排施工人员及施工组织,确保施工按时完成。
6.施工安全与环境保护:制定施工安全措施,保护施工现场及周围环境的安全与环境。
7.附录:补充的相关文件材料,包括施工图纸、合同复印件等。
------------------------------------------------------------------范本二:防火门安装工艺标准1.工程概述1.1项目名称及地址1.2工程内容1.3防火门类型及要求1.4安全措施2.材料准备2.1防火门材料规格2.2配件及附件准备2.3质量验收3.工程准备3.1施工设备及工具3.2工程现场布置3.3施工人员组织4.安装工艺4.1防火门加工及预装配4.2门框安装4.3门扇安装4.4金属门框抹灰4.5防火门调试4.6保护措施5.质量验收5.1尺寸检查5.2防火性能测试5.3门扇开启关闭试验5.4防火门标志标识6.施工管理和安全保护6.1施工管理6.2安全保护附件:1.防火门材料规格及质检报告2.施工图纸3.验收报告法律名词及注释:1.工程概述:对工程项目进行概括性的描述,包括项目名称、地址、工程内容等。
[福建]石化码头海上钻孔灌注桩基础施工方案
![[福建]石化码头海上钻孔灌注桩基础施工方案](https://img.taocdn.com/s3/m/3ddac9082f60ddccda38a0b2.png)
灌注桩施工方案1 工程概况本工程嵌岩桩数量为163根,嵌岩深度2~4.5m。
其中:Ф1200嵌岩桩24根(直桩)、Ф1500嵌岩桩78根(直桩22根、斜桩56根),Ф1700嵌岩桩61根(直桩)。
2 施工工艺流程本工程嵌岩桩数量较多,直桩采用冲孔桩机施工,斜桩采用钻孔施工,施工难度较大,尤其是斜桩施工工艺复杂,是施工控制的关键项目,对整个工程资金投入及工期影响较大。
因此施工时要根据工程的具体情况,做到科学、合理的安排。
嵌岩桩总体施工工艺流程图施工准备(如图2-1所示)。
施工平台搭设冲孔机(钻机)就位冲孔(钻孔)一次清孔下放钢筋笼钢筋笼制作二次清孔水下浇灌砼图2-1 嵌岩桩施工工艺流程图3 施工方法3.1施工准备根据灌注桩检验与试验计划,开工前须进行灌注桩施工方案报批、施工技术与安全交底、人、材、机报审,待监理工程师审核通过后方可开工。
制定材料进场计划,确保原材料供应的及时。
材料进场后对钢筋、水泥、砂、石子等原材料进行抽样检测,配合比进行复验,检验合格后方可用于本工程。
开工前进行循环泥浆的试配,确定泥浆的制浆比例。
3.2施工平台搭投本工程灌注桩施工平台有单排桩施工平台、双排桩及群桩施工平台。
本工程灌注桩平台顶标高基本与设计桩顶标高持平,部分桩顶标高在施工高水位以下的桩需提高平台标高,以保证冲钻孔施工平台在施工高水位以上,成孔施工不受潮位的影响。
其中单排桩施工平台桩基采用φ529钢管桩,施工时采用振动锤打入全风化花岗岩岩面。
双排桩及群桩直接利用自身作施工平台桩基。
施工平台面为梁板结构,主梁为40a工字钢,采用拉杆反吊工艺;次梁采用28a工字钢;平台面板采用δ50mm木板密铺并固定。
施工平台的四周设置栏杆,高度为1M,确保平台施工人员的安全。
单排桩灌注桩施工平台见图3.1-1,双排桩及群桩灌注桩施工平台见图3.1-2,¦Υ图3.1-1 单排桩灌注桩施工平台平面图图3.1-2 双排桩灌注桩施工平台平面图在灌注桩平台搭设好后,采用1.5m宽简易便桥连接各平台,便桥底标高比墩台(横梁)顶标高高20~30cm。
钻孔灌注桩码头施工方案

钻孔灌注桩码头施工方案1. 概述本文档旨在提供钻孔灌注桩码头施工方案,确保施工过程安全有效。
钻孔灌注桩是一种常用的桥梁和码头建设方法,它能够提供良好的承载能力和稳定性。
2. 施工流程2.1 设计阶段在施工前,需进行细致的设计和计划。
设计阶段包括以下几个步骤:- 确定码头的设计要求和规格;- 进行地质勘察,评估施工地点的地质条件和土层情况;- 制定桩基设计方案,确定桩的数量、直径和深度。
2.2 施工准备在进入施工阶段之前,需要进行充分的准备工作:- 准备施工所需的设备和工具;- 确定施工人员的培训需求,并进行必要的培训;- 确保施工现场的安全措施和环境保护措施已落实。
2.3 钻孔施工钻孔施工是钻孔灌注桩施工的关键步骤之一。
以下是钻孔施工的主要步骤:1. 根据桩基设计方案,确定钻孔的位置和深度;2. 使用适当的钻机设备进行钻孔;3. 在钻孔过程中,定期检查钻孔的直径和垂直度;4. 钻孔完成后,清理钻孔内的杂物和泥浆。
2.4 灌注施工灌注是钻孔灌注桩施工的最后一步。
下面是灌注施工的主要步骤:1. 准备灌注材料,如混凝土;2. 在钻孔中安装钢筋和钢模板,确保灌注材料的均匀分布和固化;3. 将混凝土泵送至钻孔中,并在灌注过程中进行震动以排除空隙;4. 灌注完成后,浇注表面平整并进行养护。
3. 质量控制为了确保施工质量,需要进行严格的质量控制。
以下是几个关键方面:- 强制执行施工规范和标准;- 进行混凝土强度检测;- 对桩基进行负载试验,验证其承载能力;- 定期检查施工现场和设备的安全状况。
4. 安全措施在施工过程中,必须始终确保施工现场的安全。
以下是几个重要的安全措施:- 提供必要的个人防护装备,如安全帽、手套和安全鞋;- 为施工人员提供必要的培训,并确保他们了解安全操作规程;- 清理施工现场的杂物和障碍物,保持通道畅通;- 安装防护栏杆和警示标志,警示施工现场的危险区域。
5. 环境保护在施工过程中,必须充分考虑环境保护。
码头工程钻孔灌注桩施工方案
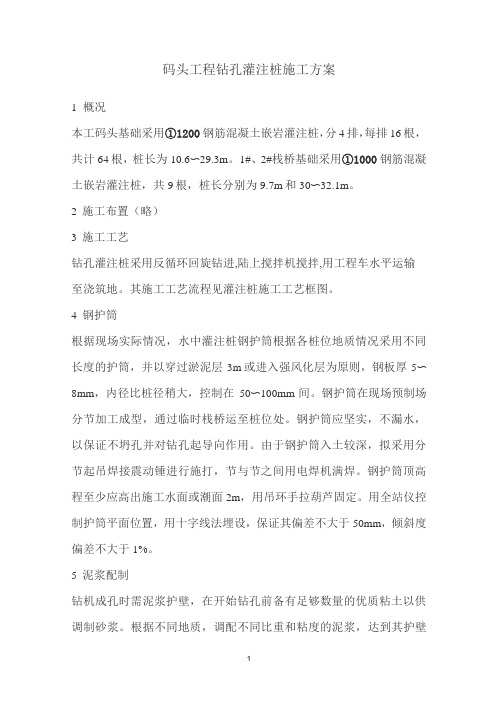
码头工程钻孔灌注桩施工方案1概况本工码头基础采用①1200钢筋混凝土嵌岩灌注桩,分4排,每排16根,共计64根,桩长为10.6〜29.3m。
1#、2#栈桥基础采用①1000钢筋混凝土嵌岩灌注桩,共9根,桩长分别为9.7m和30〜32.1m。
2施工布置(略)3施工工艺钻孔灌注桩采用反循环回旋钻进,陆上搅拌机搅拌,用工程车水平运输至浇筑地。
其施工工艺流程见灌注桩施工工艺框图。
4钢护筒根据现场实际情况,水中灌注桩钢护筒根据各桩位地质情况采用不同长度的护筒,并以穿过淤泥层3m或进入强风化层为原则,钢板厚5〜8mm,内径比桩径稍大,控制在50〜100mm间。
钢护筒在现场预制场分节加工成型,通过临时栈桥运至桩位处。
钢护筒应坚实,不漏水,以保证不坍孔并对钻孔起导向作用。
由于钢护筒入土较深,拟采用分节起吊焊接震动锤进行施打,节与节之间用电焊机满焊。
钢护筒顶高程至少应高出施工水面或潮面2m,用吊环手拉葫芦固定。
用全站仪控制护筒平面位置,用十字线法埋设,保证其偏差不大于50mm,倾斜度偏差不大于1%。
5泥浆配制钻机成孔时需泥浆护壁,在开始钻孔前备有足够数量的优质粘土以供调制砂浆。
根据不同地质,调配不同比重和粘度的泥浆,达到其护壁要求。
根据工程需要,在现场设4艘泥浆船,负责泥浆的供应和循环,在码头后方陆域上设废浆池,废浆用泥浆泵从泥浆船输送至废浆池沉淀后,按监理工程师要求掩埋或外运到指定地点废弃。
6成孔6.1钻孔工艺设备及钻头选择成孔主要考虑采用反循环旋转钻机成孔,钻机采用可以加压的旋转钻机,钻头在淤泥及强风化层中用硬质合金刮刀钻,在进入硬质中风化岩层时,采用牙轮钻头。
6.2钻孔水上灌注桩钻机安放在由钢管、槽钢搭建的平台上。
成孔时根据不同的地质情况采取不同的钻孔工艺,确定进尺速度,经常检查孔径、倾斜度,并应检查钻机的平整程度,防止孔位偏斜,应根据地质变化情况选择合理的泥浆指标,钻进过程中,必须始终保持孔内水位高于护筒外海面平面1〜1.5m,同时,专人用泥浆比重仪检测泥浆的施工过程变化,控制泥浆浓度,以起到护壁作用,不至于坍孔。
- 1、下载文档前请自行甄别文档内容的完整性,平台不提供额外的编辑、内容补充、找答案等附加服务。
- 2、"仅部分预览"的文档,不可在线预览部分如存在完整性等问题,可反馈申请退款(可完整预览的文档不适用该条件!)。
- 3、如文档侵犯您的权益,请联系客服反馈,我们会尽快为您处理(人工客服工作时间:9:00-18:30)。
灌注桩施工方案1 工程概况本工程嵌岩桩数量为163根,嵌岩深度2~4.5m。
其中:Ф1200嵌岩桩24根(直桩)、Ф1500嵌岩桩78根(直桩22根、斜桩56根),Ф1700嵌岩桩61根(直桩)。
2 施工工艺流程本工程嵌岩桩数量较多,直桩采用冲孔桩机施工,斜桩采用钻孔施工,施工难度较大,尤其是斜桩施工工艺复杂,是施工控制的关键项目,对整个工程资金投入及工期影响较大。
因此施工时要根据工程的具体情况,做到科学、合理的安排。
嵌岩桩总体施工工艺流程图(如图2-1所示)。
图2-1 嵌岩桩施工工艺流程图3 施工方法3.1施工准备根据灌注桩检验与试验计划,开工前须进行灌注桩施工方案报批、施工技术与安全交底、人、材、机报审,待监理工程师审核通过后方可开工。
制定材料进场计划,确保原材料供应的及时。
材料进场后对钢筋、水泥、砂、石子等原材料进行抽样检测,配合比进行复验,检验合格后方可用于本工程。
开工前进行循环泥浆的试配,确定泥浆的制浆比例。
3.2施工平台搭投本工程灌注桩施工平台有单排桩施工平台、双排桩及群桩施工平台。
本工程灌注桩平台顶标高基本与设计桩顶标高持平,部分桩顶标高在施工高水位以下的桩需提高平台标高,以保证冲钻孔施工平台在施工高水位以上,成孔施工不受潮位的影响。
其中单排桩施工平台桩基采用φ529钢管桩,施工时采用振动锤打入全风化花岗岩岩面。
双排桩及群桩直接利用自身作施工平台桩基。
施工平台面为梁板结构,主梁为40a工字钢,采用拉杆反吊工艺;次梁采用28a工字钢;平台面板采用δ50mm木板密铺并固定。
施工平台的四周设置栏杆,高度为1M,确保平台施工人员的安全。
单排桩灌注桩施工平台见图3.1-1,双排桩及群桩灌注桩施工平台见图3.1-2,图3.1-1 单排桩灌注桩施工平台平面图图3.1-2 双排桩灌注桩施工平台平面图在灌注桩平台搭设好后,采用1.5m宽简易便桥连接各平台,便桥底标高比墩台(横梁)顶标高高20~30cm。
便桥由5号角钢焊接而成。
便桥只考虑行人、电缆、地泵等荷载。
3.3 冲孔机(钻机)就位待灌注桩平台搭设好后,根据灌注桩分项工程检验与试验计划,请监理工程师对施工平台的顶标高、平台的稳定性、钢套筒位置、垂直度、顶标高(须高出施工期最高水位)以及冲孔机(钻机)设备、施工人员资质进行审核,待监理工程师审核通过后即可进行冲孔机(钻机)就位。
本工程采用起重船协助就位。
就位后,应对钻机设备进行检查,包括配套设备及水电供应。
应检查桩机底座和顶端是否平稳,检查桩机顶部的起吊滑轮缘、转盘中心和孔中心三者是否在同一直线上。
3.4 泥浆的循环系统岸上设置黏土库,平台上设置小型的泥浆池,钢套筒与泥浆池之间设置溜槽,溢出的泥渣经过溜槽上时大部分由人工铲到平台上,泥浆通过溜槽流到泥浆池,经过沉淀后可以利用的泥浆用吸泥泵抽回正在成孔的钢套筒中。
在泥浆循环的过程中要经常测试泥浆的比重,每工作班至少测定一次以上,比重不足要加入粘土自行造浆或直接补给泥浆。
在施工中防止泥浆溢出钢套筒,报废的泥浆风干后必须清理出平台。
不得随意将泥浆排入海中。
3.5直桩冲孔3.5.1 成孔冲孔机带冲击实心锤,重 4.5~6t。
桩机开始冲孔前要检查操作性能,检查桩锤的锤径、锤齿、锤体型状,并检查大螺杆、大弹簧垫,保护环、钢丝绳及卡扣等能否符合使用要求,根据不同工程的具体特点确定锤齿长度。
锤齿不宜过长,一般以2m为宜,锤齿应向外倾斜,倾斜度以1:5为宜,开孔前应将冲锤悬吊距平台面1m左右,检查锤体的偏心程度,对明显偏心的冲锤严禁使用。
开孔前应对钢套筒进行内层清理。
开孔时低锤密击,锤高冲程不大于2m,以免产生偏孔。
对于岩石层厚度较大,硬度较高的工程,锤齿采用耐磨钢块,能更好提高工作效率。
当遇到岩层表面不平或倾斜,应抛入20~30cm厚块石,使孔底表面略平,然后低锤快击使成一紧密平台后,再进行正常冲击,同时泥浆比可降到1.25左右,以减少粘锤阻力。
但又不能过低,避免岩渣无法上浮,排渣困难。
每班安排专人负责清渣,每次清渣后必须视泥浆比重情况,适时加入粘土造浆,也可直接补给泥浆。
冲孔过程中,钢丝绳上要设有标记,提升落锤高度要适宜,防止提锤过高击断锤齿,提锤过低进尺慢,工作效率低。
松绳不应太少以防止打空锤,也不宜松绳太多,容易偏孔或卡锤。
在冲孔时应视地质条件认真控制好泥浆比重,一般以1.25~1.35为宜,泥浆过浓易斜孔、吸锤,进尺较慢;而泥浆过稀则易塌孔,多沉碴,进尺也慢。
在强风化岩冲孔泥浆比重以1.3~1.35为宜;在砂粘土层冲孔泥浆比重,控制在1.25左右。
冲孔施工桩位对准开冲时,在护筒内加入粘土或泥浆,开孔2m内,起锤高度不宜大于1m。
冲锤起得过高时冲锤晃动大,会破坏护筒的稳定,泥浆无法在护筒口指定位置排出。
当护筒埋设好后,要设置一条排浆沟槽,沟槽截面不得太小,以免泥浆溢出流到海里,使护筒口与指定的泥浆罐相连。
同时,在开孔前泥浆应调配合适,如果不合理使用会造成孔内沉渣,影响施工进度。
每工作班要2~3次将冲锤提出孔口清洗检查,检查锤头是否变成蒜头锤,有无断齿,钢丝绳扎口是否松动,大罗杆的磨损程度,大弹簧是否拆断等,发现问题应及时向主管工程师报告,并进行解决处理。
如换用新焊锤齿的冲锤,应与原冲锤比较锤径大小,若新锤径大于原冲锤,孔内应回填块石进行修孔,以免卡锤。
每工作班至少测孔深3次,进入基岩要及时取样,并通知监理工程师等有关部门确认,每次取出的岩样要详细做好记录,并晒干保留作为工程验收依据。
交接班应详细交接冲孔情况及注意问题,发现异常情况马上纠正,因故停冲时冲锤要提出孔外以防埋锤,并随即切除电源。
冲孔过程中桩机上必须设有记录本,由操作人员做好各项原始记录,一般每2小时记录1次,遇特殊情况每半小时记录1次,终孔后将原始记录一份交给资料员保留作为工程竣工资料。
3.5.2冲孔过程可能遇到问题的处理及预防措施出现异常情况时,及时与监理工程师联系。
在施工中可能遇见的问题为:(1)遇探头石处理冲孔过程中可能遇到孔内一边有大块孤石伸进孔内,其余孔边是砂层或土层时(俗称探头石),往下冲孔时会发生偏孔现象,可向孔内填入块石至高出探头石0.5~1m处,然后冲锤冲孔,开始冲程要适当降低,待块石冲实后,冲锤冲击时受力均匀,换用较高冲程,将探头石及块石一起击碎,若此后还有偏孔,重复上述方法继续修正。
(2)卡锤处理在施工过程中当冲孔形成梅花形孔、锤偏心过大或不圆容易造成卡锤。
一旦卡锤应立即采取措施,进行处理,可用以下方法处理:a.用桩机小钢丝绳栓住打捞钩,放入孔内勾住锤体保护钢箍,主钢丝绳与小钢丝绳同时一松一紧拉锤,将锤拔出。
b.若第一种方法不能将锤拉出,可采用第二种方法:在桩机底盘前方栓上定滑轮,主钢丝绳通过滑轮改变受力方向,与小钢丝绳同时紧拉拔锤,定滑轮可在底盘正前方及左右两边多个角度安放,以便得到最佳拔锤位置。
c.可利用起重设备配合桩机同时拔锤,但起重设备应设保护绳,以防发生安全事故。
d.若以上三种方法还未能拉上冲锤,可采用爆破法:用空压机气举清除孔内沉渣及沉积泥土,同时做好爆破申报工作,得到上级主管部门批准后才能爆破作业。
当孔内泥渣清理干净后,测量绳实测锤头标高确定卡锤位置,按预定位置放入炸药,桩机操作员紧拉钢丝绳的同时引爆炸药使桩锤松动,并立即拉上冲锤。
随后检查卡锤原因,必要时更换冲锤。
继续冲孔时,应回填块石进行修孔,桩锤变形或磨损较大的必须更换。
(3)漏浆处理由于本工程灌注桩的钢套筒为钢管桩,钢管桩施打时已施打至强风化岩层,因此理论上本工程存在漏浆的机率较小。
如果钻孔中突然出现泥浆大量损耗,可向孔内不断投入粘土块挤压空隙堵塞漏洞,直到堵漏为止,并加稠泥浆,并在重新开始钻孔前征询监理工程师的意见后方可继续冲孔。
(4)卡锤预防措施定期检查锤齿磨损情况,入岩后提锤不能太低,防止出现梅花形孔;偏心过大或不圆的锤不能使用;锤顶弹簧应灵活,损坏及时更换;注意新换锤的直径变化情况,开始冲程不宜过大;卡锤后打捞时注意不要让铁件掉入孔内。
3.6 斜桩钻孔3.6.1 斜桩钻孔施工方法本工程斜桩采用GJQ-15-1工程钻机岩石层钻孔。
具体施工方法如下:1)斜桩钻机的安装。
在桩机就位后进行斜孔安装,安装时要根据斜桩的钢管斜度和斜向方位等安装好钻机,经反复校正后完全符合要求才能进行固定钻机,在钻机固定时,必须做到前后左右用枕木或钢绳固定之后才能进行下一工序。
2)钻进。
钻进前应对钢套筒进行内层清理。
钻机在斜桩安装固定完毕后经检查运转试钻没有任何问题,才能进行正常钻进。
钻进时采用清水泵吸反循环钻进配用Φ150mm法兰式钻杆,法兰连接处采用O型密封圈密封,在钻杆中间每隔5m加上扶正器,每根桩共须加3~4个扶正器。
3)开动钻机嵌岩钻孔至基岩,经工程师、监理及设计认可基岩的起算标高后,再向下钻入设计要求的钻入深度。
在钻入过程中,每钻入0.5米取岩石样品,存入塑料袋中储存,请业主工程师、监理及设计共同在现场对岩样进行鉴定,确认基岩标高。
在钻至所规定的入基岩深度后,即可进行下一道工序—清孔。
3.6.2 斜桩工艺相关参数大口径钻进工艺参数正确与否,对提高成桩效率的作用要比小口径钻进更为重要。
目前常采用恒压自动给进的钻进工艺。
即根据岩土层所需钻压来控制钻速。
泵吸反循环灌注斜桩的施工工艺和方法基本上保持大口径直桩施工的工艺方法,工艺参数不同于直桩,桩的斜度越大,钻进中摩阻力越大,钻速越低。
桩的长度越大,轴心压力受侧压力分解,钻进效率下降。
施工选取合理钻进技术参数是提高效率的关键。
(1)钻压泵吸反循环回转斜孔钻进确定钻压的原则与正循环回转钻进相同,根据斜桩特点与钻头类型选择钻压。
一般情况下,单轴抗压≤5Mpa,钻压86—109KN左右,实际上根据钻进中不同情况加以修正。
(2)转数选取转数原则与正循环回转钻进相同,钻进转数是根据地层情况来确定的。
可选取钻头转速14-33转/min。
(3)泵量泵吸反循环斜孔钻进中选择泵量,应从排渣、节能和护孔三方面来考虑:从排渣角度来考虑,泵量必须保证钻杆内冲洗液上升的流速大于钻渣下沉的速度;从节能的角度来考虑,泵量能满足排渣的要求即可,并非越大越好;从护孔的角度来考虑,泵量过大易使不稳地层发生跨孔。
施工中选取冲洗液沿孔壁下流的速度不超过10m/min(600m/n)。
(4)斜桩施工的钻头配重与导向原则斜桩施工的钻头重量(即轴心压力)必须是达到能破碎所钻的土、岩层压力。
其导向原则是导向器的长度必须是钻头长度的三倍,根据工程的特点不宜采有导向器的,应在钻杆中间适当位置加上扶正器,保证钻孔斜度与钢管桩外孔径斜度一致,防止钻孔倾斜面下垂而影响钻进效率。
3.7 一次清孔终孔后孔深达到设计标高后,采用反循环法清孔。
(将泥浆管导入孔底,将合格的泥浆泵送至孔内,通过泥浆的上浮力将沉渣排出。