现代纺纱环锭纺纱新技术
新型纺纱与环锭纺新技术—转杯纺工艺设计
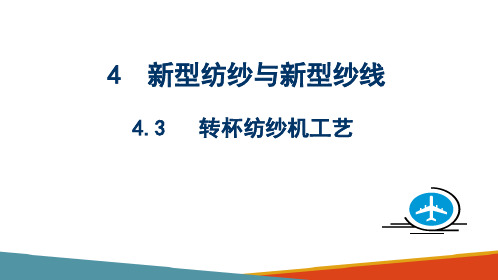
(省去粗纱和络筒工序)
⑥对原料的要求低 ⑦适纺中、低支纱
转杯纺属于自由端纺纱
转杯纺的原料
转杯纺纱
①天然纤维:棉、亚麻 ②再生纤维素纤维:粘胶、莫代尔、天丝 ③合成纤维(短纤维):涤纶、腈纶、维纶等 ④棉纺厂再用棉:精梳落棉、清花落棉、梳棉落棉
各种短纤维原料
适纺纱支范围
国内:10~36英支,国际:6~50英支
纺纱工艺设计与实施
4 新型纺纱与新型纱线 4.1 转杯纺特点
转杯纺纱机是什么? 转杯纺纱机
转杯纺纱
牵伸、加捻、 卷绕成形…..
制成筒子
并条机加
工好的熟条 转杯纺纱机,可以等同环锭纺的粗纱、细纱、络筒的工作
环锭纺的特点和存在的问题
■特点:
①加捻和卷绕不分 (同时由锭子、钢领、钢丝圈完成) ②成纱结构紧密,强度较高。 ③适纺不同线密度的纱线(细纱机牵伸范围大). 存在的问题: ①受钢丝圈和纱线张力的制约 ②气圈稳定性的影响。 ③产量很难大幅度提高。
纺纱器 纺纱器
纺纱器元件
纺纱器
分梳辊 转杯
转杯纺纱机工艺
转杯纺纱机工艺
1、喂入条子定量
根据所纺原料品种、纤维线密度和长度以及纺纱线密 度来决定。
2、转杯规格和速度
转杯规格:转杯直径、转杯形式、凝聚槽形状
(1)转杯直径:28mm~66mm (2)转杯速度:40000~150000r/min ▪速度高时配置小直径转杯,速度低时配置大直径转杯。 ▪纤维长度长时,采用大直径转杯,纤维长度短时,采用小直 径转杯。
①喂给喇叭口作用:使棉条在进入握持机构之前受到必要的 整理和压缩。
②喂给罗拉、喂给板作用:握持并积极向前输送纤维条。
纺纱器的重要组成--分梳辊
环锭纺纱技术的发展与创新

论 文PAPER纺纱是纺织产业链的第一道工序,其产品质量档次、生产效率与加工成本在整个产业链中具有十分重要的地位。
随着纺织科学技术的发展,目前在纺纱生产中普遍采用两类纺纱技术,一种是环锭纺文|赵亮 厉勇 李杰 张剑锋 王丽丽环锭纺纱技术的发展与创新近几年来,环锭纺纱技术通过不断改进与技术创新,在多种纺纱技术共同发展中继续保持领先地位。
紧密纺纱与复合纺纱技术显著提升了环锭纺纱线品质档次,并扩宽了环锭纺纱线的应用领域,是对环锭纺技术的发展与创新。
采用带自动落纱的环锭细纱长机与细络联合机是环锭纺技术进一步发展的方向。
要使环锭细纱机实现优质高产、效益最佳,选好主机是基础,配好器材专件是关键。
关键词:环锭纺 紧密纺 复合纺 低扭矩纺 发展 创新纱技术,从发明到应用已有100多年历史。
另一种是新型纺纱技术,如转杯纺、喷气纺、喷气涡流纺等,由于其成纱机理、成纱结构不同于环锭纺,并在纺纱工序缩短、劳动用工减少等方面具有一定优势,故近期得到快速发展,用新型纺纱技术生产的各类纱线比重逐年有较大增加。
但从总体分析,目前用环锭纺纱机生产的纱线仍占主导地位,国内外90%短纤纱线是在环锭纺纱机上加工生产的。
前言1环锭纺纱技术的发展跨入2l 世纪以来,随着纺纱技术的不断进步,环锭纺纱技术不但在纺纱方法上取得了重大突破与改进,而且在纺纱技术装备上运用高科技手段在智能化、自动化、机电一体化技术等方面也有重大创新,环锭纺纱技术正以崭新的面貌展示在纺纱领域,主要反映在以下5个方面。
(1)紧密纺技术(又称集聚纺)的研发成功与投入生产,标志着环锭纺纱技术进入了一个新的历史发展阶段,用紧密纺技术生产的纱线在可纺支数与品质方面比传统环锭纺及新型纺纱均具有明显优势。
(2)在环锭细纱机上采用多种形式复合纺纱技术,使环锭纺纱线不仅呈现原料、色泽多元化,而且形态结构多样化,进一步拓宽了环锭纺生产纱线的应用领域。
(3)围绕减少纺纱用工提高劳动生产率,在环锭细纱机上广泛应用自动化、机电一体化等新技术,在国外带自动落纱细纱长车及细络联已得到广泛应用,在国内带集体络纱的细纱长机也取得长足进步,正在逐步推广应用,并正在向细络联与粗细联延伸,实现纺纱工序的连续化。
环锭细纱机的技术进步

环锭细纱机的技术进步内容摘要:当代环锭细纱机在牵伸加压形式、卷捻技术、传动方式、长车和细络联以及紧密纺纱技术等有了很大的发展,已形成了高科技的环锭纺纱机。
本文对上述几个方面进行了详细的讨论。
关键词伸形式钢领钢丝圈高速锭子变频调速紧密纺纱技术目前全世界约有1.7亿枚棉纺环锭细纱机,800万头转杯纺,其它新型纺纱如喷气纺、涡流纺等容量很少。
但转杯纱产量占全部纱线市场的42%,环锭纱占56%,其它如喷气纺占2%。
环锭纺是传统纺纱方法,工艺技术十分成熟,是纺纱生产中占比例最大、又十分重要的纺纱方式。
新型纺纱技术虽然生产效率高、工艺流程短,品种、纱支适应性好,但成纱结构及性能不如环锭纱,所以在相当长的时期内不可能完全取代环锭纱,因此,环锭纺仍然是现代纺纱生产中最主要的纺纱方式。
在20世纪后半期,环锭纺纱技术有很大进步,细纱机锭速达到25000转/分,一台细纱机锭数已发展到1400锭,牵伸倍数230倍左右,在牵伸形式、加压、锭子、钢领钢丝圈、吸棉、纱管、胶辊、胶圈、传动技术等方面都有了很大发展,在细纱与自动络纱联合技术上也有了新的突破,有不少机型都形成了细络联。
代表国际先进水平的机型有瑞士立达公司、德国绪森公司、意大利马佐里公司及以德国青泽公司生产的各种新型环锭细纱机,在高速、高效、节能、机电一体化及自动控制自动化方面都已达到很高水平。
1999年巴黎展览会上,瑞士立达、德国绪森等公司展出了紧密纺环锭细纱机,这是环锭纺纱技术新的突破,紧密环锭纺纱技术是在细纱牵伸区以外,增加了凝聚细纱须条的机构,消除了加捻三角区,成纱质量更为优越:减少了细纱毛羽,提高细纱强力,改善了细纱条干,为下游工序提高织物质量,减少上浆负担、取消烧毛等创造了条件,与此同时,细纱制成率提高,飞花减少,对提高经济效益及改善生产环境都有明显作用。
我国FA500系列环锭细纱机,在贯彻重加压,强控制、大牵伸的工艺路线上,吸收了国外先进环锭细纱机的经验及特点,结合我国国情进行较大改进,结构比较合理,制造精度有所提高,设备运转可靠性、稳定性也有进一步提高,适纺性能强,纺纱质量进一步提高。
环锭纺纱——精选推荐

环锭纺纱新技术——紧密纺(上)秦贞俊教授级高级工程师中国纺织工程学会棉纺织专业委员会当代环锭纺纱在短纤维纺纱体系中占有十分主要的地位,即使在20世纪后20年许多新型纺纱技术已有了很大发展,像转杯纺、喷气枋等新型纺纱体系统具有速度高,产量高及生产费用少的特点。
比环锭纱好,如毛羽、纱疵及条干均匀度等,但所生产纱线的特性在一些方面远不如环锭纱如单纱强力,手感等方面。
一、近期紧密纱环锭纱的研究与开发,使纱线质量得到很大改进,紧密环锭纱的毛羽显著减少,细纱强力进一步提高,断裂伸长率也得到改进,十分有利於生态环境的改进(飞花少),耐磨度提高,手感好及具有理想的纱线结构等。
紧密纺环锭纺纱技术展示了许多优势。
在传统的环锭纺中,从前罗拉钳口线引出的纤维受到加捻,加捻点与前罗拉钳口之间形成纺纱加捻三角区,加捻三角区的外侧纤维承受较大的张力,中间的纤维承受的张力较小。
大部分纤维会加捻成纱,而部分纤维会形成纱线毛羽及飞花。
新型紧密纺环锭纺纱体系,使处於罗拉钳口与加捻点之间三角区的纤维受到控制,从前罗拉钳口引出的纤维束在牵伸区完成牵伸后,受到设在三角区负压的凝聚,在负压凝聚力的作用下,使纤维受控到达加捻点进行加捻,因此,纺纱三角区基本不存在,使所有纺纱三角区中的纤维被凝聚全部被纺成纱。
在普通环锭细纱机中,如图1所示,在离开前罗拉钳口线之前,牵伸区中的纤维束宽度为B,它取决许多因素如纺纱支数,粗纱捻度及牵伸状况。
假如纤维须条离开前罗拉钳口线即开始加捻,对於特定的纱线即一定的纱支并伸直的纤维束,纺纱三角区宽度大小主要取决於卷绕张力P,纺纱三角区b与卷绕张力P成反比,这个关系表明:纺纱三角区的宽度小於喂入须条的宽度,三角区边缘的纤维与纱体连接差的纤维,一端伸在纱体外而另一端被捻入纱体中或者出现不被捻入纱体的情况,由此会产生飞花及纱线毛羽。
与普通环锭纺相反,在紧密环锭纺中,纤维受负压气流的作用,在离开主牵伸区前罗拉钳口的会出现凝聚现象。
open-end纺纱技术
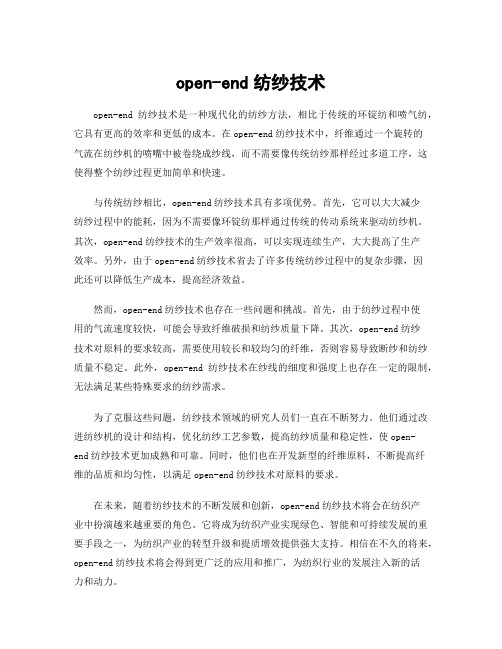
open-end纺纱技术open-end纺纱技术是一种现代化的纺纱方法,相比于传统的环锭纺和喷气纺,它具有更高的效率和更低的成本。
在open-end纺纱技术中,纤维通过一个旋转的气流在纺纱机的喷嘴中被卷绕成纱线,而不需要像传统纺纱那样经过多道工序,这使得整个纺纱过程更加简单和快速。
与传统纺纱相比,open-end纺纱技术具有多项优势。
首先,它可以大大减少纺纱过程中的能耗,因为不需要像环锭纺那样通过传统的传动系统来驱动纺纱机。
其次,open-end纺纱技术的生产效率很高,可以实现连续生产,大大提高了生产效率。
另外,由于open-end纺纱技术省去了许多传统纺纱过程中的复杂步骤,因此还可以降低生产成本,提高经济效益。
然而,open-end纺纱技术也存在一些问题和挑战。
首先,由于纺纱过程中使用的气流速度较快,可能会导致纤维破损和纺纱质量下降。
其次,open-end纺纱技术对原料的要求较高,需要使用较长和较均匀的纤维,否则容易导致断纱和纺纱质量不稳定。
此外,open-end纺纱技术在纱线的细度和强度上也存在一定的限制,无法满足某些特殊要求的纺纱需求。
为了克服这些问题,纺纱技术领域的研究人员们一直在不断努力。
他们通过改进纺纱机的设计和结构,优化纺纱工艺参数,提高纺纱质量和稳定性,使open-end纺纱技术更加成熟和可靠。
同时,他们也在开发新型的纤维原料,不断提高纤维的品质和均匀性,以满足open-end纺纱技术对原料的要求。
在未来,随着纺纱技术的不断发展和创新,open-end纺纱技术将会在纺织产业中扮演越来越重要的角色。
它将成为纺织产业实现绿色、智能和可持续发展的重要手段之一,为纺织产业的转型升级和提质增效提供强大支持。
相信在不久的将来,open-end纺纱技术将会得到更广泛的应用和推广,为纺织行业的发展注入新的活力和动力。
棉纺5种实用纺纱方法

棉纺5种实用纺纱方法
1.环锭纺纱法:这种方法是目前最常用的棉纺方法之一。
将纤维放在环锭上,并在锭子周围绕着钩针上。
随着锭子的旋转,纤维就被拉伸并旋转成线。
这种方法适用于各种不同类型的棉纤维。
2. 摇杆纺纱法:这种方法是一种古老的技术,但仍然在某些地区使用。
它需要手动操作,使用一个摇杆来拉伸并旋转纤维成线。
这种方法通常用于生产特定类型的面料和纤维,如丝绸。
3. 吸气纺纱法:这种方法将纤维放在一个吸气管上,然后使用吸气力将纤维拉伸并旋转成线。
这个过程非常快,因此适用于大批量棉纺生产。
4. 水力纺纱法:这种方法使用高压水流将纤维拉伸并旋转成线。
这种方法非常快速和高效,但需要先将纤维处理成一定程度的湿润状态。
5. 气流纺纱法:这种方法使用空气流动将纤维拉伸并旋转成线。
这个过程非常快,因此适用于大批量棉纺生产。
但它需要特殊的设备来产生足够的气流。
- 1 -。
新型环锭纺纱技术的种类

新型环锭纺纱技术的种类
新型的环锭纺纱技术主要包括环锭改革的纺纱新技术和新型纺纱。
前者是在传统的环锭纺细纱机的基础上进行革新,如赛络纺、赛络菲尔纺、缆型纺、紧密纺等,它们也可以说是环锭纺纱技术的新发展。
后者还成纱机理与环锭纺完全不同的成纱方法,如转杯纺、喷气纺、喷气涡流纺、摩擦纺、涡流纺和自捻纺等,它们按纺纱原理还可进一步分为自由端纺纱和非自由端纺纱两大类。
此外,双面纺纱技术是近年来发展起来的一种环锭纺纱技术。
传统的环锭纺纱只能在一侧纺纱,而双面纺纱技术可以在同一台机器上同时进行两面纺纱,大大提高了纺纱效率。
环锭纺纱新技术

1 A
2 赛络纺
和传统的纺纱不同的是 ,赛络纺是双粗纱平
行 喂 入 ,两 股 须 条 在 细 纱 机 上牵 伸 区 内互 不 干
涉,一直到出前箝 口后才汇合一起 。见罔二() 1。
在 汇 合 之 前 两 股 须 条 分 别 在加 捻 力 的 作 用 下 捻 。 当两 股带有 一 定捻 度 的纤 维 束 汇合 后将在 纺
包 芯纱 6 。
说说 我 的看 法 。
、
环 锭 纺 纱 新 技 术
1包 芯纱
在环 锭 细 纱 机 上生 产 包 : ,大都 是 囚弹 芷纱 .
性纱 而起 的。让 纱线 有 弹性 的力‘ 有好 多 。但不 法
很 明显采用 这样 的装 置虽 然可 以达到 包芯 的 效 果 ,但 要 有 良好 的包 芯 效 果 还 需 1艺 的 配
调 整 长 丝 和 纤 维 须 条 的位 置 和 张 力 .可 以
产 生 不 同 的包缠 方 法 ,或长 丝 和 纤 维相 互包 缠 ,
打破 ,在纺 纱 张 力的作 用下 B O须 条纱 线将 向右 偏移 到 B E位 置 _ ,在移 动过程 中 ,具 有一 定 张 _ I
或长 丝包缠纤 维 ,或 者纤 维包 缠长 丝 。在纺 制纤
间有 一个 _角 区( 『 ) 随着纺 纱 的进 行 ,长 二 见冬 1 。
囤 二 | 群络 纺 1 ) 1粗纱须条 2 前集合器
丝呈螺旋 状地包 复在羊 毛纤 维的外 1 。长丝乖 j 6 = 『 ¨毛
3 前罗拉
4 纱 线
纤 维 都 有… 定 的 捻 度 。 m于 纱 线 中有 长丝 的存 一 在 ,纱线 的强力和仲 长明显增加 ,还有 闪色效. 。
新型纺纱技术的发展与传统环锭纺纱技术的进步
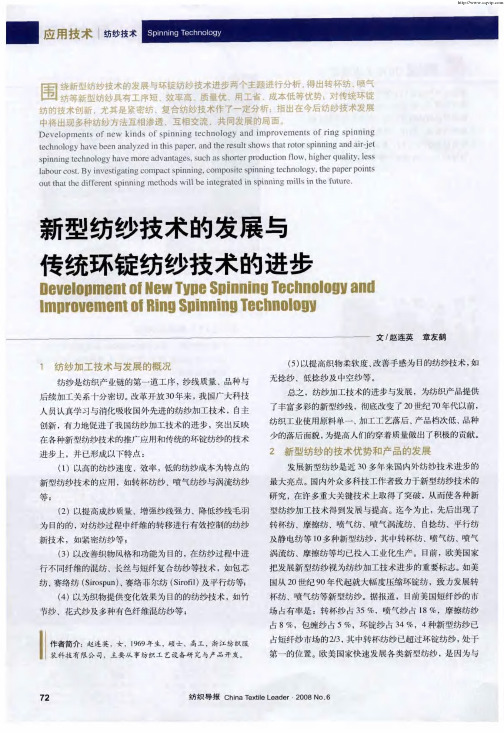
、 、
在 纺 纱 过 程 中进
,
涡流纺
、
摩 擦 纺 等 均 已 投 入 工 业 化生 产
目前
欧美国家
。
长 丝 与 短 纤 复 合 纺 纱 等技 术
n
、
如 包芯
把 发 展 新 型 纺 纱 视 为 纺 纱加 工 技 术进 步 的 重 要 标 志 如 美
国从 2 0 世 纪 9 0 年 代 起 就 大 幅 度 压 缩 环 锭 纺 杯纺
工省 、成本 低的 优势 。
( )纱 线的 耐摩性 优 于环锭 纱 5
因为喷 气纱 、 气涡 流纱 均有 纱芯和 外 包纤维 两部 分 喷 组成 , 条表 面包 有 不规 则的缠 绕纤 维 ,不 易解体 , 纱 纱 且 线表 面摩擦 系数大 , 在织 物 中纱 与纱之 间的 抱合 良好 ,不
装科枝 有 限 公 司
主要从 事纺织
艺 设 备 研 究 与产 品 开 发
第
一
的位 置
。
欧 美 国 家快 速 发 展 各 类 新 型 纺 纱
,
是 因为 与
72
纺织导报
C h in
a
T e x t ile L e
a
de
r
.
2 0 0 8 No
.
6
重庆维普
传统的环 锭纺 纱 比较具 有工 序短 、 产效率 高 、 生 质量优 、 用
2
。
并 已形 成 以 下特 点
、
:
新 型 纺 纱 的技 术 优 势 和 产 品 的 发展
发展新 型 纺纱是近
。
( 1 ) 以高 的 纺纱 速 度
效率
,
纺纱概论—新型纺纱

(4)纱条引出后经电子清纱 器去除疵点后被卷绕在筒子上。
新型纺纱—喷气纺纱
喷气纺纱的成纱结构特点
• 1、喷气涡流纺(MVS)纱 的结构特点 涡流纱也是一种双重结构的纱,纱条的芯纤维是平行排列的、无
捻度,依靠旋转气流的作用使末端纤维包覆缠绕于芯纤维外部加捻成 纱。但与喷气纱不同的是,涡流纱的外层覆盖纤维比重大(约60 %),以致内部未加捻的纤维几乎被完全覆盖,表面纤维排列则更近 似于环锭纱。纱线毛羽很少,织物起球现象亦减少,染色性能及耐磨 性好。 • 2、 喷气纺(MJS)纱线结构
新型纺纱
新型纺纱概述
新型纺纱概述
1、环锭纺的特点和存在的问题 •特点: ①加捻和卷绕不分 (同时由锭子、钢领、钢丝圈完成) ②成纱结构紧密,强度较高。 ③适纺不同线密度的纱线。(细纱机牵伸范围大) •存在的问题: ①钢丝圈和纱线张力的制约 ②气圈稳定性的影响。 ③产量很难大幅度提高。
新型纺纱概述
新型纺纱---自由端纺纱
1、转杯纺原料
①天然纤维:棉、亚麻 ②再生纤维素纤维:粘胶、莫代尔、天丝 ③合成纤维(短纤维):涤纶、腈纶、 ④棉纺厂再用棉:精梳落棉、清花落棉、梳棉落棉
2、适纺纱支范围
国内:10~30英支,国际:6~40英支
3、转杯纺工艺流程
①开清棉 → 梳棉→并条 (二道)→ 转杯纺纱机
(二)非自由端纺纱 一般经过罗拉牵伸——加捻——卷绕三 个工艺过程,即纤维条自喂入端到输出端呈连续状态,加捻器 置于喂入端和输出端之间,对须条施以假捻,依靠假捻的退捻 力矩,使纱条通过并合或纤维头端包缠而获得真捻。自捻纺纱 、喷气纺纱、粘合纺纱就属于这种方法。
新型纺纱
纺织材料的加工技术与创新研究

纺织材料的加工技术与创新研究纺织业作为人类历史上最古老的产业之一,其发展与人们的生活息息相关。
从最初的手工纺织到现代的大规模机械化生产,纺织材料的加工技术经历了无数次的变革与创新。
在当今时代,随着科技的飞速进步和人们对生活品质要求的不断提高,纺织材料的加工技术正面临着新的挑战和机遇。
本文将对纺织材料的加工技术及其创新进行深入探讨。
一、传统纺织材料加工技术1、纺纱技术纺纱是将纤维原料制成纱线的过程。
传统的纺纱方法包括环锭纺纱、气流纺纱和涡流纺纱等。
环锭纺纱是最常见的纺纱方法,其原理是通过罗拉牵伸将纤维束拉长变细,然后在锭子的高速旋转下加捻成纱。
气流纺纱则是利用高速气流将纤维束吹散并凝聚成纱,具有生产效率高、纱线结构蓬松等特点。
涡流纺纱则是通过涡流的作用使纤维束形成纱线,纱线的强力较高。
2、织造技术织造是将纱线制成织物的过程。
传统的织造方法包括机织和针织。
机织是通过经纱和纬纱的交织形成织物,常见的机织织物有平纹、斜纹和缎纹等。
针织则是通过线圈的相互串套形成织物,分为纬编和经编两种。
纬编针织织物具有良好的弹性和延伸性,常用于制作内衣和运动服装;经编针织织物的结构较为紧密,常用于制作泳衣和窗帘等。
3、染整技术染整是对纺织材料进行染色、印花和整理的过程。
传统的染色方法包括浸染、轧染和印花等。
浸染是将织物浸泡在染液中进行染色,适用于小批量生产;轧染是通过轧辊将染液均匀地轧压在织物上进行染色,适用于大批量生产。
印花则是通过印版将染料或颜料印在织物上形成图案,常见的印花方法有筛网印花、滚筒印花和数码印花等。
整理则是通过化学或物理方法改善织物的性能,如柔软整理、防皱整理和防水整理等。
二、现代纺织材料加工技术1、新型纺纱技术随着科技的发展,出现了许多新型纺纱技术,如紧密纺纱、赛络纺纱和转杯纺纱等。
紧密纺纱通过减少纱线中的毛羽,提高了纱线的质量和强度;赛络纺纱则是将两根粗纱同时喂入细纱机,形成具有类似股线结构的纱线;转杯纺纱是利用转杯的高速旋转加捻成纱,适用于生产粗支纱。
现代环锭细纱机的技术创新
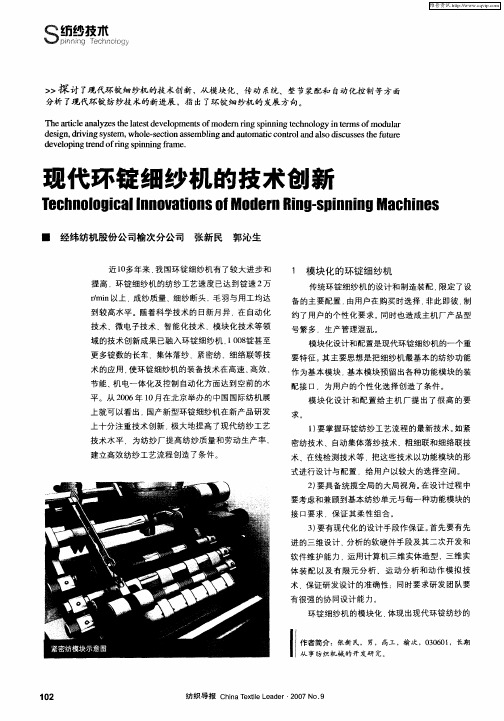
更多锭数的长车.集体落纱,紧密纺 细络联等技
术 的应 用 . 使环 锭细 纱机 的装备 技术 在高 速 效 , 高
节能 、 电一 体化 及控 制 自动化 方面达 到 空前 的水 机 平 。从 2 0 0 6年 1 0月在 北京 举办 的 中国 国际纺 机展 上就 可 以看 出 . 国产新 型环 锭细 纱机在 新产 品研 发
提 高 .环 锭细 纱机 的纺纱 工艺 速度 已达 到锭 速 2万
1 模块化的环锭细纱机
传统环 锭细 纱机 的设计 和制造 装配 , 限定 了设
mn i 以上 . 纱质 量 细 纱断 头 . 成 毛羽 与用 工均达 到 较高水 平 。随着科 学技 术 的 日新 月异 . 自动化 在
技 术 、微 电子技术 、智能化 技术 ,模 块 化技 术等领
12 0
纺 织 导 报 C i e t e d r 2 0 o 9 h aT x l L a e . 0 7N . n i e
维普资讯
纺 纱 技 7 f t
一
技 术创 新和 进步 , 为用 户 的个 性 化需 求和 产 品的升 级 换代 创造 了条 件 。
细纱 机 同时要 提供 报 警和联 机 网络接 口控 制 。
1 h ri l nay e elts e eo me t f ] ea t ea l z st e t v l p n so c h a d mod r n p nnn e hn l g r f o u a e nr g s i ig tc o o yi t mso d lr i ne m d sg d ii g y tm, o e s ci na s mb i ga da t e in, rvn s se wh l— e t s e ln uomai o to da s ic s e ef tr o n tcc n r l n l a od s u s st uu e h d v l p n r n f ngs i n n r me e eo i gte do r i p n i gfa .
环锭纺纱的原理

环锭纺纱的原理环锭纺纱是目前应用广泛的纺纱技术之一。
它采用了一种独特的结构,可以高效生产纤维成纱。
本文将详细介绍环锭纺纱的工作原理。
概述环锭纺纱是一种摩擦纺纱技术,它不需要拉伸纤维。
相反,它的绳环旋转并将纤维拉进锭上,形成纱线。
该技术的优点是可以处理各种纤维类型,并且生产过程非常高效。
由于它的简单性和可靠性,环锭纺纱被广泛应用于纺织工业。
下面将详细介绍环锭纺纱的原理。
工作原理环锭纺纱机的主要构成部分包括纱锭、绳环、供纱器、卷绕器和马达。
纱锭是一根金属棒,上面有一个圆形的凸轮,称为锭头。
绳环则是一个光滑的小金属圆环,用于将纤维拉入锭头。
供纱器具有进给和张力系统,用于把纤维从纱锭上提供到绳环中。
卷绕器则收集绳环中形成的纱线。
马达提供动力,配合其他系统协同工作。
纺纱的过程分为四个阶段:进料、拉伸、细化和卷绕。
下面将详细说明这些阶段的工作原理。
阶段一:进料进料是将纤维送入供纱器的过程。
这通常是从纱锭上引导纤维的过程。
在此阶段,绳环保持相对静止,纤维则进入绳环,之后流入纱锭上的空槽中。
阶段二:拉伸一旦纤维进入槽中,绳环就开始旋转并拉伸纤维。
它的加速度和速度可以根据所使用纤维的类型和特性进行调整。
拉伸的长度通常是根据纤维类型和细度确定的。
这个过程产生了相当高的摩擦力,这有助于将纤维牢固地拉入锭上。
阶段三:细化在第二阶段,拉伸后的纤维被送到了锭头的等离子体。
这个过程继续拉伸纤维,直到它达到所需的细度和强度。
细化过程也涉及调整马达的速度,以便在不同的纤维长度和细度下达到最佳效果。
阶段四:卷绕最后一个阶段是将纱线从纱锭上缠绕到卷绕器中。
这个过程需要在绳环和卷绕器之间设置一个张力控制系统。
通过控制这个张力系统,可以保证纱线的牢固性,并防止出现断纱情况。
结论环锭纺纱技术非常简单,可以高效生产各种类型的纤维。
这是一个基于摩擦原理的技术,不需要拉伸纤维,因此不会对纤维造成损害。
尽管它有一些限制,例如它的工作速度较慢,但环锭纺纱技术仍然被纺织行业广泛应用,可以生产出高品质的织物。
现代纺纱技术:第四章 新型纺纱及其发展
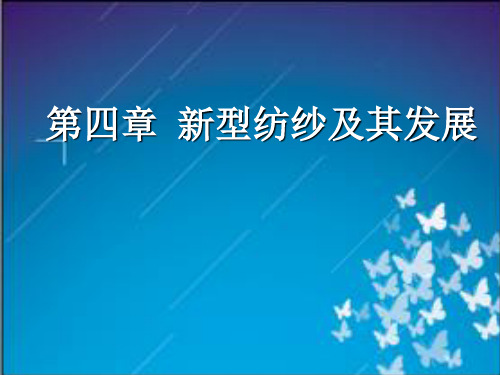
导纱钩
钢丝圈
纱管 钢领
加捻卷绕一体化--速度与卷装的矛盾
细纱加捻卷绕的气圈张力和钢丝圈受力分析中,得到如下的基本 方程式 ,其中: ns-锭子速度 H-卷装高度 D-钢领直径 (卷装的直径) C-常数
导纱钩
钢丝圈
纱管 钢领
三、新型纺纱的发展历程
早在1907年,森莫•威廉就曾提出过把加捻作用和卷绕作用 分开的设想。1937年,百塞尔森提出了转杯纺的雏型。
直到1965年波尔诺(Brno)展出了由捷克研制成功的KS200型转杯纺样机,才在实用上首次获得突破性的进展。
1967年在瑞士巴塞尔第五界国际纺织机械展览会展出了较完 善的BD-200型转杯纺纱机。
转杯纺的成功指出了新型纺纱技术的发展方向。
1971年,在巴黎展出了由澳大利亚研制的MKI型自捻纺纱机。 1975年,在米兰展出了由波兰研制的PF-1型涡流纺纱机,同时展
当代出现的转杯纺、摩擦纺、涡流纺、静电纺、管道纺、喷 气纺、平行纺、自捻纺等新型纺纱技术出现,纺纱速度是环 锭纺的几倍到几十倍。
但由于环锭纺纱机可以纺特细特纱以及成纱质量高,迄今还 没有任何一种新的纺纱机能够完全替代环锭纺纱机。
英国工业革命后的棉纺车间 现代纺纱车间
二、环锭纺纱的局限性
纺
纱
(一)钢丝圈速度和纺纱张力
出了由奥地利研制的DREF型摩镲纺纱机和荷兰研制的Twilo无捻 纺纱机。 1981年在大阪展出了由日本研制的MJS型喷气纺纱机。 所列各种纺纱方法,都在机构上克服了高速生产和大卷装之间的 固有矛盾,单位产量可比环锭纺提高2-10倍,卷装容量可比环 锭纺增加数十倍。
四、新型纺纱的分类 (一)按成纱原理分: 1.自由端纺纱 自由端纺纱是指由喂入点到加捻点之间的须条是断开的
各种纺纱方法简介

各种纺纱方法简介中国是纺织大国,也是纺织技术的发源地之一,纺织在我国有着悠久的历史。
今天主要来谈一下,纺纱技术的分类,纺织发展到今天主要的纺纱技术还是环锭纺,但也呈现出越来越多新形式,总结起来主要有如下一些:(1)环锭纺纱(ring spinning),是现时市场上用量最多,最通用之纺纱方法,条子或粗纱经牵伸后的纤维条通过环锭钢丝圈旋转引入,筒管卷绕速度比钢丝圈快,棉纱被加拈制成细纱。
广泛应用于各种短纤维的纺纱工程。
如普梳,精梳及混纺,钢丝圈由筒管通过纱条带动绕钢领回转。
进行加拈同时,钢领的摩擦使其转速略小于筒管而得到卷绕。
纺纱速度高,环锭纱的形态,为纤维大多呈内外转移的圆锥形螺旋线,使纤维在纱中内外缠绕联结,纱的结构紧密,强力高,适用于制线以及机织和针织等各种产品。
环锭纺(精梳)流程:清花间--梳棉--预并条--条并卷--精梳--头道并条--二道并条--粗纱--细纱--络筒环锭纺(普梳)流程:清花间--梳棉--头道并条--二道并条--粗纱--细纱--络筒(2)无拈纺纱(twistless processing)使用粘合剂使纤维条中的纤维互相粘合成纱的一种纺纱方法。
粗纱经牵伸装置牵伸后,须条被送到加捻滚筒上,回滚筒上来自槽箱中的薄层粘合剂接触。
纤维条由数根回转的小压辊与滚筒一起向前输送,其中一根小压辊还同时作轴向往复运动,将纤维条搓成圆形截面,并使每根纤维都能均匀地接触到粘合剂。
圆形纤维条通过加热器烘燥,纤维互相粘牢成纱。
纺纱速度可比常规纺纱方法大2~4倍,制成的纱可供织造用。
(3)自拈纺纱(self-twist spinning)一种非传统纺纱方法。
(siro yarn类同)将两根纤维条经牵伸装置拉细,由前罗拉、搓捻辊输出,在导纱钩处合。
搓捻辊除回转外,并快速轴向往复运动,搓转纱条,使搓捻辊前后的纱条获得方向相反的捻回。
在导纱钩处合后的两根纱条,依靠它们本身的抗扭力矩自行拈合成双股自拈纱(ST纱),卷绕成筒子。
新型纺纱技术的发展与传统环锭纺纱技术的进步
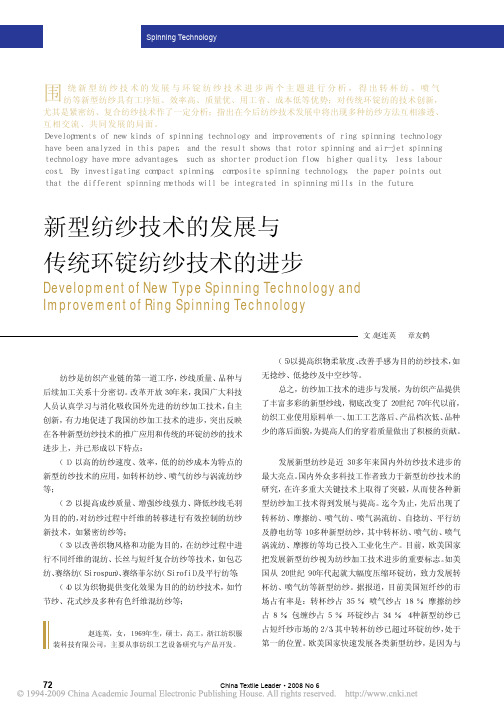
纺纱技术|应用技术Suessen(绪森)公司的依丽纺(Elite)、瑞士Rieter(立达)公司的卡摩纺(Com4)、德国Zinser(青泽)公司(现并入Oerlikon Schlafhorst) — Tex700集聚纺等。
在国内外已批量生产的紧密纺细纱机及紧密纺装置还有:经纬纺机榆次公司生产的1530型、上海二纺机生产的138JCB型、东台马佐里生产的139型、海军4806工厂生产的ZJ1298型、日本Toyota(丰田)EST紧密纺以及瑞士RoCos磁紧密纺等紧密纺细纱机以及宁波韵升集团德昌纺机自主研发的紧密纺装置与江阴华方科技公司生产的紧密纺装置等。
其中经纬纺机榆次公司紧密纺细纱机配置Suessen公司依丽纺装置。
东台马佐里紧密纺细纱机多数是配德昌的紧密纺装置。
纵观已在生产中使用的紧密纺细纱机,虽其型号不一,形式多样,除RoCos磁性紧密纺装置外,都是在加捻三角区采用负压集聚原理,即在前罗拉加装一套控制元件来加强对纤维的控制,其中下罗拉有吸风集聚作用,使须条较紧密地排列,大大减少了传统细纱机中加捻三角区中须条宽度,以利于将须条中的纤维捻卷到纱条中,从而可较大幅度减少成纱中尤其是3 mm以上的有害毛羽。
同时,负压吸风也有利于纤维在加捻卷绕时有一次的伸直机会,使纱线强力得以提高。
从众多使用厂实践证实,在同样半制品的条件下,采用紧密纺细纱比原环锭细纱机成纱毛羽减少80 %左右,强力可提高5 % ~ 10 %。
同时,因纱的条干均匀度改善,纱疵减少,纺纱时断头率降低,使生产效率也可提高10 %左右。
由于紧密纺纱线强力提高,毛羽减少,在后续工序中,整经时断头率可降低30 %,浆纱时可减少上浆率,织造时经纬纱断头率可分别降低50 %与30 %,从而提高布机生产效率。
紧密纺纱线在针织机上加工时,可免去上蜡,减少布面的起毛起球,提高针织物质量。
紧密纺纱技术虽然在国内推广应用时间还较短,但以其独特的纺纱机理、优良的成纱性能、较好的经济回报受到纺纱企业的高度重视,其发展速度将会加快。