转炉溅渣护炉的工艺原理与实际应用_胡勋
浅析转炉溅渣护炉技术的应用
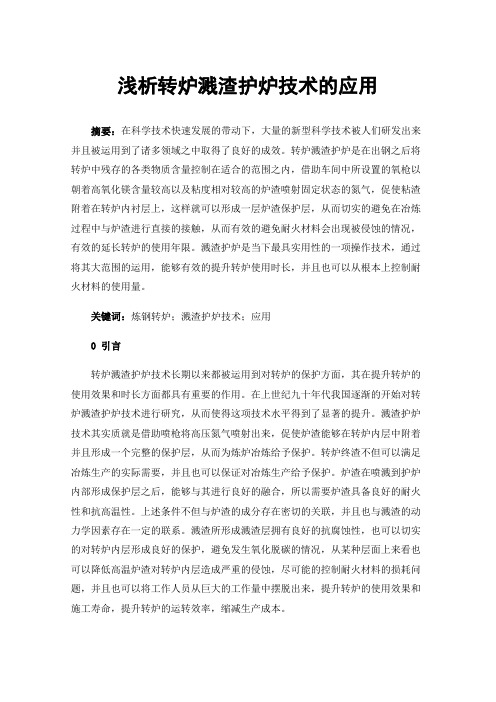
浅析转炉溅渣护炉技术的应用摘要:在科学技术快速发展的带动下,大量的新型科学技术被人们研发出来并且被运用到了诸多领域之中取得了良好的成效。
转炉溅渣护炉是在出钢之后将转炉中残存的各类物质含量控制在适合的范围之内,借助车间中所设置的氧枪以朝着高氧化镁含量较高以及粘度相对较高的炉渣喷射固定状态的氮气,促使粘渣附着在转炉内衬层上,这样就可以形成一层炉渣保护层,从而切实的避免在冶炼过程中与炉渣进行直接的接触,从而有效的避免耐火材料会出现被侵蚀的情况,有效的延长转炉的使用年限。
溅渣护炉是当下最具实用性的一项操作技术,通过将其大范围的运用,能够有效的提升转炉使用时长,并且也可以从根本上控制耐火材料的使用量。
关键词:炼钢转炉;溅渣护炉技术;应用0引言转炉溅渣护炉技术长期以来都被运用到对转炉的保护方面,其在提升转炉的使用效果和时长方面都具有重要的作用。
在上世纪九十年代我国逐渐的开始对转炉溅渣护炉技术进行研究,从而使得这项技术水平得到了显著的提升。
溅渣护炉技术其实质就是借助喷枪将高压氮气喷射出来,促使炉渣能够在转炉内层中附着并且形成一个完整的保护层,从而为炼炉冶炼给予保护。
转炉终渣不但可以满足冶炼生产的实际需要,并且也可以保证对冶炼生产给予保护。
炉渣在喷溅到护炉内部形成保护层之后,能够与其进行良好的融合,所以需要炉渣具备良好的耐火性和抗高温性。
上述条件不但与炉渣的成分存在密切的关联,并且也与溅渣的动力学因素存在一定的联系。
溅渣所形成溅渣层拥有良好的抗腐蚀性,也可以切实的对转炉内层形成良好的保护,避免发生氧化脱碳的情况,从某种层面上来看也可以降低高温炉渣对转炉内层造成严重的侵蚀,尽可能的控制耐火材料的损耗问题,并且也可以将工作人员从巨大的工作量中摆脱出来,提升转炉的使用效果和施工寿命,提升转炉的运转效率,缩减生产成本。
1溅渣护炉工艺的冶金因素及其优势就溅渣护炉工艺的实际操作流程来说,主要包括下面几个方面:第一,将钢水从转炉转移到大包中。
转炉溅渣护炉工艺的研究与应用

16Metallurgical smelting冶金冶炼转炉溅渣护炉工艺的研究与应用朱元涛(山东石横特钢集团有限公司,山东 肥城 271612)摘 要:介绍了石横特钢集团有限公司炼钢车间通过优化转炉溅渣工艺,转炉炉体安全稳定运行,熔池未出现侵蚀扩径现象,炉壳温度稳定,影响钢产量增加,溅渣护炉效果明显,炉型稳定,大面料补炉砖消耗降低,取得明显经济及社会效益,具有很好的推广应用价值。
关键词:转炉;溅渣层中图分类号:TF748.2 文献标识码:A 文章编号:11-5004(2021)06-0016-2 收稿日期:2021-03作者简介:朱元涛,男,生于1975年,汉族,山东泰安人,本科,经济师,研究方向:冶金工程。
目前转炉实行炉炉溅渣工艺,在生产过程中会出现炉底波动大、炉帽过厚、熔池侵蚀严重等不利于转炉冶炼的现象,导致停炉换包时修补熔池侵蚀部位,停炉时间长,影响产能降低、补炉料消耗升高,同时炉型发生变化后,影响冶炼稳定性喷溅、溢渣严重。
为稳定炉型,缩短转炉停炉辅助时间,降低补炉料消耗等,一炼钢成立技术攻关小组,在改进溅渣层质量,优化氮气压力、流量与枪位,控制合理的留渣量等三方面进行技术优化,综合生产成本降低。
1 溅渣护炉工艺原理1.1 溅渣护炉分析初期渣对炉衬的侵蚀在转炉冶炼初期,首先是铁水中Si、Mn 的大量氧化,生成大量的SiO 2等,石灰的熔化速度较缓慢(石灰活性度低时更差),炉渣碱度的提高需要一个较长的过程,在低碱度阶段炉渣对炉衬的侵蚀较严重。
因为在酸性渣中,MgO 可以有很高的溶解度,加速了炉衬中MgO 的熔解速度。
因此,在初期加入白云石造渣,使渣中有一定的MgO 可以减轻对炉衬的化学侵蚀。
实际生产中,溅渣层为高熔点的C 2S 和MgO 结晶体,熔化温度较高。
由于冶炼初期温度较低,溅渣层为不明显熔化。
初期渣对溅渣层的侵蚀较弱,当渣中FeO 含量相同时,高钙渣的侵蚀速度明显高于高镁渣。
因此提高溅渣层的碱度或MgO 含量,均有利于减轻炉渣的侵蚀。
转炉溅渣护炉技术

转炉溅渣护炉技术的应用方法1.溅渣护炉的基本原理,是在转炉出完钢后加入调渣剂,使其中的Mg与炉渣产生化学反应,生成一系列高熔点物质,被通过氧枪系统喷出的高压氮气喷溅到炉衬的大部分区域或指定区域,粘附于炉衬内壁逐渐冷凝成固态的坚固保护渣层,并成为可消耗的耐材层。
转炉冶炼时,保护层可减轻高温气流及炉渣对炉衬的化学侵蚀和机械冲刷,以维护炉衬、提高炉龄并降低耐材包括喷补料等消耗。
氧气顶吹转炉溅渣护炉是在转炉出钢后将炉体保持直立位置,利用顶吹氧枪向炉内喷射高压氮气(1. 0MPa) ,将炉渣喷溅在炉衬上。
渣粒是以很大冲击力粘附到炉衬上,与炉壁结合的相当牢固,可以有效地阻止炉渣对炉衬的侵蚀。
复吹转炉溅渣护炉是将顶吹和底吹均切换成氮气,从上、下不同方向吹向转炉内炉渣,将炉渣溅起粘结在炉衬上以实现保护炉衬的目的。
溅渣护炉充分利用了转炉终渣并采用氮气作为喷吹动力,在转炉技术上是一个大的进步,它比干法喷补、火焰喷补、人工砌砖等方法更合理,其既能抑制炉衬砖表面的氧化脱碳,又能减轻高温渣对炉砖的侵蚀冲刷,从而保护炉衬砖,降低耐火材料蚀损速度,减少喷补材料消耗,减轻工人劳动强度,提高炉衬使用寿命,提高转炉作业率,减少操作费用,而且不需大量投资,较好地解决了炼钢生产中生产率与生产成本的矛盾。
因此,转炉溅渣护炉技术与复吹炼钢技术被并列为转炉炼钢的2项重大新技术。
2 溅渣护炉主要工艺因素2. 1 合理选择炉渣并进行终渣控制炉渣选择着重是选择合理的渣相熔点。
影响炉渣熔点的物质主要有FeO、MgO和炉渣碱度。
渣相熔点高可提高溅渣层在炉衬的停留时间,提高溅渣效果,减少溅渣频率,实现多炉一溅目标。
由于FeO易与CaO和MnO等形成低熔点物质,并由MgO和FeO的二元系相图可以看出,提高MgO的含量可减少FeO相应产生的低熔点物质数量,有利于炉渣熔点的提高。
从溅渣护炉的角度分析,希望碱度高一点,这样转炉终渣C2 S 及C3 S之和可以达到70%~75%。
溅渣护炉的基本原理

溅渣护炉的基本原理溅渣护炉是一种常见的钢铁冶炼过程中的热力学现象。
其基本原理是通过在炉内加入适当的物料,将炉内产生的溅渣与炉壁进行反应,从而保护炉内的炉壁不被腐蚀,延长炉壁的使用寿命。
本文将具体介绍溅渣护炉的基本原理及其应用。
一、溅渣护炉的基本原理在钢铁冶炼过程中,高温下会产生大量的溅渣,这些溅渣不仅会降低冶炼效率,还会对炉壁造成破坏。
为此,需要通过添加适当的物料进行溅渣护炉。
溅渣护炉的基本原理是添加一些特殊的反应剂,使其在高温下与溅渣发生反应,生成一种新的化合物,从而消耗掉大部分的溅渣。
这种化合物可以形成一层保护膜,在钢水和炉壁之间形成一个隔离层,减少溅渣对炉壁的侵蚀,从而有效地延长炉壁的使用寿命。
溅渣护炉的物料有很多种,其选择主要依据于冶炼工艺和物料的性质。
在整个钢铁冶炼过程中,常用的物料有镁球、石灰石、硅石等。
二、溅渣护炉的应用在钢铁冶炼过程中,溅渣护炉是一种常见的技术。
其应用可以有效地提高冶炼效率,降低生产成本,提高冶炼质量。
下面我们将分别介绍其应用在各个环节中的具体情况。
1.高炉在高炉冶炼中,溅渣护炉对炉壁保护尤为重要,可以有效地减少高炉的磨损和锈蚀。
目前,高炉冶炼中主要采用的溅渣护炉物料是镁球和石灰石。
镁球主要用于抑制磷和硫的生成,从而提高炉膛的可控性;石灰石则可以中和酸性物质,减少炉壁的腐蚀。
2.转炉在转炉冶炼中,溅渣护炉主要用于中和氧化物和碱性物质。
其主要物料是硅石和石灰石。
硅石主要用于中和氧化物,而石灰石则可以中和碱性物质,从而减少炉壁的腐蚀。
3.电炉在电炉冶炼中,溅渣护炉主要用于中和酸性物质。
其主要物料是石灰石和麻粉。
石灰石可以中和酸性物质,麻粉则可以降低炉壁的温度,从而减少炉壁的腐蚀。
总之,溅渣护炉在钢铁冶炼过程中起着非常重要的作用。
通过添加适当的物料,可以有效地保护炉壁不受腐蚀,延长炉壁的使用寿命。
转炉溅渣护炉的工艺原理与实际应用_胡勋

摘要:本文简要介绍了转炉溅渣护炉的工艺原理和总结了实际应用中几个例如氮气喷吹参数,设备维护等关键因素。
关键词:转炉溅渣护炉工艺原理应用为了提高转炉炉龄,降低生产成本,减轻工人劳动强度,炼钢工作者采取了许多方法例如改善耐火材料质量,采取有效的喷补技术等。
这些措施对提高炉龄均起到了积极的作用使转炉炉龄有了一定程度的提高,但是随着炼钢技术的发展,炼钢工作者对炉渣和炉衬侵蚀机理的进一步研究,上世纪九十年代初美国LTV 公司率先开发出了溅渣护炉技术,通过近几年国内外实践得出溅渣护炉技术对炉衬维护有着喷补,贴补不可比拟的效果。
可以说溅渣护炉技术是转炉炉衬维护的又一大进步。
一.溅渣护炉的工艺原理1总述溅渣护炉是指在转炉吹炼结束出钢后,将转炉内留渣的粘度和氧化镁含量调整到合适的范围,用转炉系统原有的氧枪或专用氧枪向高氧化镁含量高粘度的炉渣喷吹一定压力和流量的氮气,将粘渣吹溅到炉衬上,使炉渣全面地炉衬上涂挂,冷却,凝固成一层炉渣质的保护层,避免了下一炉冶炼时钢水及炉渣直接和炉衬接触,从而达到减缓炉衬耐火材料层的蚀损,延长转炉炉龄的效果。
经过过国内外许多钢厂结合自己本厂的资源,工艺特点,进行开发应用证明溅渣护炉工艺对提高转炉炉龄和降低耐火材料消耗的效果非常显著,转炉炉龄在采用溅渣护炉后都有成倍的提高。
2溅渣层保护炉衬机理溅渣护炉的微观过程就是:高速氮气由喷枪喷溅到炉渣液面上,炉渣在氮气的巨大剪切力作用下迅速微粒化,微粒获得动能离开液体渣系向各个方向飞溅,以不同角度(高度)打在炉衬上。
微粒在形成,飞溅,粘结过程中不断被氮气冷却,最后在炉衬上粘附,固化,反应而形成一层炉渣的固体层覆盖住炉衬,从而减小炉衬的侵蚀,延长了炉衬的寿命。
2.1液态炉渣对炉衬的侵蚀机理炉渣对Mg-C 砖的侵蚀过程是:渣中(FeO)扩散到炉衬—渣界面,并与炉衬中的C 发生氧化还原反应而析出单质铁,同时对砖脱C 形成孔隙,铁单质进入炉渣,炉渣渗入孔隙与MgO 生成FeO ·MgO 固熔体进入渣中。
转炉炼钢工艺(溅渣护炉)

溅渣护炉的负面影响
吹炼终点[%C] ·[%O]积随炉龄变化情 吹炼终点 积随炉龄变化情 况
关于经济炉龄的问题
生产率、 生产率、成本与炉龄关系
溅渣护炉的优点
大幅度降低耐材消耗; 大大提高转炉作业率,达到高效增产目的; 投资回报率高; 溅渣护炉综合效益每吨钢约为2~10元。
溅渣护炉的负面影响
底吹透气砖覆盖渣层厚度与吹炼终点[%C] ·[%O]积的关 底吹透气砖覆盖渣层厚度与吹炼终点 积的关 系
溅渣护炉的负面影响
底吹透气砖覆盖渣层厚度与吹炼终点[%C] ·[%O]积的关 底吹透气砖覆盖渣层厚度与吹炼终点 积的关 系
炉渣粘度的控制
过低的炉渣粘度有利溅渣的操作,即易溅起、挂 渣且均匀,但由于渣层过薄,会在摇炉时挂渣流 落; 而粘度过大,溅渣效果差,耳轴!渣线处不易溅到, 且炉底易上涨,炉膛变形,所以粘度需要根据实 际情况合理调整; 炉渣过热度增高,粘度下降。
溅渣操作参数控制
为了在尽可能短的时间内将炉渣均匀喷 敷在整个炉衬表面而形成有足够厚度的 致密溅渣层。必须控制好溅渣操作手段, 即根据炉形尺寸,来控制喷吹N2气压力 和流量、枪位和喷枪结构尺寸等喷溅参 数。
其它参数
喷溅时间:通常为2.5~4min; 喷枪夹角:许多厂家的经验表明采用12 度夹角比较理想。
需要采取的其它措施
炉衬材质不能因实行溅渣护炉技术而降 低,对使用镁碳砖而言,其碳含量应控 制为下限; 控制和降低终渣FeO含量; FeO 合理调整终渣MgO含量; 提高溅渣层熔化性温度,降低炉渣过热 度; 降低出钢温度。
溅渣护炉技术在转炉上的应用

溅渣护炉技术在转炉上的应用
溅渣护炉技术是一项新兴的技术,它可以提高转炉的燃烧效率,减少对环境的影响。
溅渣护炉技术是通过把大量的液体或气体加到炉内,使溅射出来的渣滓变得更轻而易于把它带走而得以应用于转炉上。
这样可以大大提高转炉的燃烧效率,减少对环境的影响。
溅渣护炉技术的主要原理是在炉子内部加入溅射液体或气体,使溅射出来的渣滓变得更轻,而且更易于把它带走。
此外,溅渣护炉技术还可以改善炉子内部燃烧状态,提高燃烧效率,从而降低炉子本身的耗能。
溅渣护炉技术在转炉上的应用主要体现在以下几个方面:
1、降低转炉内部的温度:在转炉内部加入溅射液体或气体,使渣滓变得更轻,从而降低转炉内部的温度,提高转炉的燃烧效率。
2、减少对环境的污染:由于转炉内部的温度较低,因此溅渣护炉技术也可以减少对环境的污染。
3、改善转炉内部燃烧状态:在转炉内部加入溅射液体或气体后,可以改善转炉内部的燃烧状态,从而提高燃烧效率,减少渣滓的生成。
4、降低燃料的消耗:由于溅渣护炉技术可以提高转炉的燃烧效率,从而降低燃料的消耗,节省能源,降低成本。
总之,溅渣护炉技术可以有效提高转炉的燃烧效率,减少对环境的污染,节省能源,降低成本。
在转炉上应用溅渣护炉技术,将会带来很好的经济效益和社会效益。
炼钢转炉溅渣护炉技术的应用与实践

炼钢转炉溅渣护炉技术的应用与实践介紹了炼钢转炉溅渣护炉技术的主要工艺参数,本钢集团北营炼钢厂在实际应用中遇到的问题。
为稳定氮气吹溅的运行现状,提高使用精度,自主创新了溅渣氮气智能管理系统技术,实现了优化溅渣工艺,缩短溅渣时长,降低溅渣氮气消耗,达到国内先进水平。
在一定程度上减轻了高温渣对炉衬砖的侵蚀冲刷,降了低耐火材料损耗速度,同时减轻工人劳动强度,提高炉衬使用寿命,提高转炉作业率,降低生产成本。
标签:溅渣;炉衬;氮气;挂渣引言转炉溅渣护炉技术是多年以来用于保护转炉提高炉龄的一项技术。
我国自90年代开始着手研发适应国情的转炉溅渣护炉工艺。
溅渣护炉技术就是将高压氮气通过喷枪喷出,渣通过喷射撞击区的孔穴外侧喷溅,并吸附到转炉炉衬上面从而形成一层渣层,这样可以对下一炉冶炼起到保护炉衬的作用。
转炉终渣不仅可以满足冶炼过程的要求,还应该符合溅渣护炉的条件,也就是说炉渣应易于喷溅到炉衬上,且溅到炉衬上的炉渣能很好地与之结合,所溅的炉渣应具有一定的耐火与抗高温侵蚀能力[1]。
近年来,节能环保与提质增效的工作要求越来越严格。
因此,研究溅渣护炉工艺中影响溅渣层寿命的主要因素,并在溅渣护炉工艺中进行量化控制,实现溅渣护炉工艺的科学量化,这些正是现代炼钢科技工作者需要着手解决的问题。
1溅渣的重要工艺参数1.1渣成分转炉一般都使用镁碳砖作为它的炉衬,减少炉衬侵蚀的重点就在于提高渣中氧化镁含量。
当渣中氧化镁的含量接近饱和时,炉衬中氧化镁的溶解量就很少,也就提高了炉衬的寿命。
炉渣碱度也是影响渣中氧化镁含量的重要因素,如果终渣碱度为三左右时,氧化镁含量则在百分之八左右就能使氧化镁达到炮和。
所以国内各种外转炉溅渣的氧化镁含量一般控制在百分之八到十四。
渣中氧化铁含量的高低严重影响着炉衬侵蚀和溅渣效果。
渣中氧化铁的矿物多为低熔点铁酸盐,熔点远远低于出钢温度,且氧化铁含量越高,铁酸盐也随之就越多,渣的流动性也就越好,造成对炉衬侵蚀作用加大且不容易附着在炉衬上。
对转炉溅渣护炉及长寿复吹工艺的分析

对转炉溅渣护炉及长寿复吹工艺的分析0.引言转炉溅渣护炉技术的常规原理主要是由于在转炉出钢后,在炉内势必会留下终渣,按照渣况实施相对应的改质,利用高压氮气喷吹溅炉渣,把炉渣吹溅至炉壁,从而造成溅渣层。
在进行下一炉的炼钢过程中,可以起到屏障炉衬,以此,来实现转炉长寿的作用。
当前对钢水质量标准的要求日益严格,而复吹工艺却显现出了炉底上涨、透气砖阻滞、底吹供气管道出现漏气等诸多层面的大小问题。
1.我国转炉溅渣护炉与长寿复吹工艺的原理与现状转炉溅渣护炉技术的原理,是在转炉出完钢之后融进适量的调渣剂,其目的旨在让里面的MgO和炉渣发生化学反应,能够形成生成系统的高熔点物质。
之后,再被氧枪系统发射的高压氮气喷溅至炉衬的大多数范围亦或是设计范围,以此,依附在炉衬内壁慢慢冷凝成为坚固、稳定的屏障保障,最终变成能够得以耗损的耐材层。
转炉冶炼的过程中,保护层能够较大的弱化高温气流和炉渣对转炉炉衬的化学性侵蚀与产生的冲刷,通过养护炉衬、延长炉龄而且缩减耐材耗损。
氧气顶吹转炉溅渣护炉是指在转炉出钢之后把炉体维续在直立的程度,再通过顶吹氧枪给炉内喷射1.0 MPa高压氮气,把炉渣喷溅至炉衬上面。
由于渣粒是通过极为强劲的力道依附至炉衬上面,因此必然会和炉壁契合的十分牢固,能够高效地阻滞炉渣给炉衬造成的化学侵蚀。
长寿复吹转炉溅渣护炉是指把顶吹与底吹都转换成氮气,由上到下的不同方向,吹到转炉内炉渣,将炉渣溅起后,使其得以粘附在炉衬内壁上,从而保护炉衬。
溅渣护炉技术最大程度上应用了转炉终渣且通过氮气视为喷吹动力,毫无疑问,这在转炉技术上是立竿见影的巨大进步。
其相较于,干法喷补、火焰喷补、人工砌砖等诸多办法更为科学、合理、可操作性,不但可以压制炉衬砖表面的氧化出现脱碳现象,还可以弱化高温渣对于炉砖所产生的化学侵蚀及机械冲刷,最终起到保护炉衬砖,缩减耐火材料蚀损的整体速率[1]。
更为重要的是,可以缩小由于喷补技術所造成的材料耗损,极大的降低了工人的劳动强度。
浅析转炉溅渣护炉及长寿复吹工艺
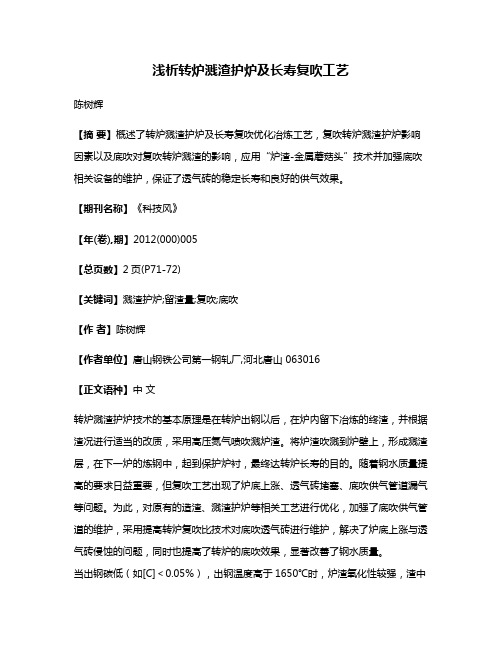
浅析转炉溅渣护炉及长寿复吹工艺陈树辉【摘要】概述了转炉溅渣护炉及长寿复吹优化冶炼工艺,复吹转炉溅渣护炉影响因素以及底吹对复吹转炉溅渣的影响,应用“炉渣-金属蘑菇头”技术并加强底吹相关设备的维护,保证了透气砖的稳定长寿和良好的供气效果。
【期刊名称】《科技风》【年(卷),期】2012(000)005【总页数】2页(P71-72)【关键词】溅渣护炉;留渣量;复吹;底吹【作者】陈树辉【作者单位】唐山钢铁公司第一钢轧厂,河北唐山 063016【正文语种】中文转炉溅渣护炉技术的基本原理是在转炉出钢以后,在炉内留下冶炼的终渣,并根据渣况进行适当的改质,采用高压氮气喷吹溅炉渣。
将炉渣吹溅到炉壁上,形成溅渣层,在下一炉的炼钢中,起到保护炉衬,最终达转炉长寿的目的。
随着钢水质量提高的要求日益重要,但复吹工艺出现了炉底上涨、透气砖堵塞、底吹供气管道漏气等问题。
为此,对原有的造渣、溅渣护炉等相关工艺进行优化,加强了底吹供气管道的维护,采用提高转炉复吹比技术对底吹透气砖进行维护,解决了炉底上涨与透气砖侵蚀的问题,同时也提高了转炉的底吹效果,显著改善了钢水质量。
当出钢碳低(如[C]<0.05%),出钢温度高于1650℃时,炉渣氧化性较强,渣中TFe含量高,炉渣熔点低,流动性强。
此种炉渣若不采取改制措施,就会造成溅渣时间大大延长,氧气用量大,溅到炉壁上的炉渣耐侵蚀性能差,降低了溅渣护炉效果,并将对下炉操作产生不良影响,增加了炼钢操作的难度。
不同的钢厂低碳钢比例不同,唐钢超低碳钢目前已达50%。
因此必须采取工艺措施提高高温低碳钢种的溅渣效果,主要经验是:1)降低渣中TFe含量。
此种炉渣的一个明显特点是TFe含量高,溅渣时应加入改质剂,以降低TFe含量,增加渣中MgO含量,降低炉渣温度,使炉渣黏度提高。
加入改质剂量应灵活掌握,不能加入量太大使渣变“干”,也不能加入量太少,合理的加入量应视出完钢后渣量大小,氧化性程度而定,改质剂的加入方法采用分批加入,溅渣前加一批,溅渣时视渣况加入1~2批。
溅渣护炉的应用上交

转炉的溅渣护炉操作【摘要】介绍氧气顶吹转炉溅渣护炉的理论与实践,对溅渣操作过程中出现的喷枪结瘤、炉底上涨及钢液脱磷等问题作了探讨。
【关键词】溅渣枪口结瘤炉底上涨脱磷前言钢铁工业一直面临着一种压力,即在不增加投资的条件下,提高产量,降低成本。
最早由新日铁奥进等人于1981年开发的转炉溅渣护炉工艺(亦称强制涂层工艺),就是一项不需要大的投资,而且增加生产率,降低操作费用,提高炉龄的新技术。
溅渣护炉工艺的基本思想是在转炉出钢后,将终渣留在炉内,然后适当调整终渣成分(主要是MgO含量),然后高压氮气通过吹氧枪吹渣,使终渣溅起附在炉衬上(见图1),形成炉衬的保护层,从而减轻炼钢过程对炉衬的机械冲刷和化学侵蚀,达到保护炉衬,大幅度提高炉龄的目的。
图1 溅渣示意图溅渣护炉工艺是转炉补炉方法上的根本性突破,使转炉炉龄大幅度提高,美国LTV公司1991年开发应用这项新技术并在1994年获得成功,炉龄已突破20000炉,转炉作业率由1984年的78%提高到1994年的97%,北美国家转炉炉龄平均都在5000炉以上,有6个厂已超过10000炉。
我国炼钢界从1996年开发这项工作并应用在大、中、小型转炉上。
宝钢于1996年末引进了美国LTV公司的溅渣(MgO)控制等工艺,使炉龄从原来的3500~5000炉跃升到10000炉左右。
鞍钢第三炼钢厂180t复吹转炉溅渣后不更换底吹原件,炉龄从2000炉左右提高到5700炉以上。
太钢二炼钢50t转炉炉龄由不溅渣平均1419次提高到1996年平均3774次,最高炉龄达8580炉,拆炉时残砖仍有200mm左右。
马钢三炼钢50t转炉首次试验时在已见保险砖的情况下用溅渣护炉工艺又冶炼了800多炉,炉龄达到1800炉。
小型转炉方面,南京钢厂已达2500炉水平,莱芜、济南钢厂也已超过3000炉,首钢一炼钢30t转炉最高炉龄达3361炉,平均炉龄2200炉左右。
福建三明钢厂15t小转炉已达到6000~7000炉的水平。
转炉溅渣护炉技术

技术特点
1)操作简便 根据炉渣粘稠程度调整成分后, 根据炉渣粘稠程度调整成分后, 利用氧枪和自动控制系统,改供氧气为供氮气, 利用氧枪和自动控制系统,改供氧气为供氮气, 即可降枪进行溅渣操作; 2)成本低 充分利用了转炉高碱度终渣和制 氧厂副产品氮气, 加少量调渣剂( 如菱镁球、 氧厂副产品氮气 , 加少量调渣剂 ( 如菱镁球 、 轻烧白云石等) 就可实现溅渣 , 轻烧白云石等 ) 就可实现溅渣, 还可以降低吨 钢石灰消耗; 3)时间短 一般只需3—4min即可完成溅渣护 一般只需3 min即可完成溅渣护 炉操作, 炉操作,不影响正常生产; 4)溅渣均匀覆盖在整个炉膛内壁上,基本上 4)溅渣均匀覆盖在整个炉膛内壁上,基本上 不改变炉膛形状; 不改变炉膛形状;
基本工艺参数
1)熔池内的合适渣量 1)熔池内的合适渣量 按照溅渣实践,对于出钢量在65—70t的太 按照溅渣实践,对于出钢量在65 70t的太 65— 钢转炉,附着在炉衬上的炉渣重量为2t左右 炉渣重量为2t左右。 钢转炉,附着在炉衬上的炉渣重量为2t左右。 根据冷态试验结果,各种顶吹气体流量条件下, 根据冷态试验结果,各种顶吹气体流量条件下, 均以11 渣量溅渣效果最好。 11% 均以11%渣量溅渣效果最好。图2为溅渣量与 顶枪枪位、气体流量及渣量之间的关系。目前, 顶枪枪位、气体流量及渣量之间的关系。目前, 鞍钢三炼钢厂渣量控制在80--110kg 80--110kg/ 鞍钢三炼钢厂渣量控制在80--110kg/t钢,溅 渣效果良好。 渣效果良好。国内几家钢厂溅渣实践和效果表 渣量在100kg 100kg/ 较为合适。 明,渣量在100kg/t较为合适。
发展概况
进入80年代,转炉普遍采用镁碳砖,综合砌炉, 进入80年代,转炉普遍采用镁碳砖,综合砌炉, 使用活性石灰造渣,改进操作,采用挂渣、喷 补相结合的护炉方法,使转炉炉龄又有明显提 高。 溅渣护炉是近年来开发的一项提高炉龄的新技 术。该技术最先是在美国共和钢公司的大湖分 厂(GreatLakes),由普莱克斯(Praxair)气体 (GreatLakes),由普莱克斯(Praxair)气体 有限公司开发的。 1991年,美国LTV公司的印地安那哈的厂用溅 1991年,美国LTV公司的印地安那哈的厂用溅 渣作为全面护炉的一部分。1994年 渣作为全面护炉的一部分。1994年9月该厂 232t顶吹转炉的炉衬寿命达到15658炉,喷补 232t顶吹转炉的炉衬寿命达到15658炉,喷补 料消耗降到0.38kg/ 钢,喷补料成本节省66 料消耗降到0.38kg/t钢,喷补料成本节省66 %,转炉作业率由1984年的78%提高到1994年 %,转炉作业率由1984年的78%提高到1994年 的97%。 97%。
半钢炼钢条件下的溅渣护炉技术

半钢炼钢条件下的溅渣护炉技术
半钢炼钢工艺是将废钢、铁水和生铁锭进行混炼后进行炼钢的一种方法。
由于废钢中含有许多杂质,如氧化物、氮化物、碳化物以及磷、
硫等元素,这些杂质在炼钢过程中易于溶解在钢水中,从而影响钢的
品质和性能,甚至引起冷断、裂纹等缺陷。
溅渣护炉技术是半钢炼钢
过程中常用的一种保护方法,它可以减少杂质的加入,提高钢水的品质。
一、溅渣护炉技术原理
在炼钢的过程中,钢水表面容易被氧化而形成钢水残渣(即溅渣),
溅渣会将氧气与钢水交换,从而造成氧化损失和变质。
溅渣护炉技术
即通过在钢水表面形成一层密闭的溅渣,来保护钢水不受氧化和污染。
二、溅渣护炉技术的特点
1. 可以有效减少杂质的加入和钢水的损耗;
2. 可以增加钢水中的活性元素,提高钢的成分和性能;
3. 可以减少冒烟量和环保污染。
三、溅渣护炉技术的实施方法
1. 在加料前,先加入一定量的铝粉;
2. 加入适量的钙质,以提高溅渣的碱性和稠度;
3. 注意控制钢水的温度,以保证溅渣的形成和稳定。
四、注意事项
1. 在实施溅渣护炉技术时应注意合理控制溅渣的稠度,过稠或过稀的溅渣都会对炼钢质量产生不利影响;
2. 注意控制加铝和加钙量的比例,过量的加铝会导致炉渣的过热,损失过大;过量的加钙会导致炉渣的碱度过高,造成炉渣过稠或过软等问题。
总之,溅渣护炉技术是半钢炼钢中不可或缺的一种保护方法,它可以有效提高钢水的品质和性能,降低生产成本,是炼钢过程中不可或缺的一项技术手段。
溅渣护炉技术

溅渣护炉溅渣护炉原理溅渣护炉工艺是把氮气通过氧枪吹入炉膛,高速氮气流股与渣面相遇后把一部分炉渣击碎成尺寸不等的液滴向四周飞溅。
由于流股的能量高,把熔池渣层击穿并形成凹坑,氮气流股遇到炉底后以一定角度形成反射气流,反射气流与渣坑表面的磨擦作用会带起一部分渣滴,使其飞到炉壁上。
通过这样的连续吹氮气,炉渣温度不断下降,渣滴不断黏附在炉衬上,直到溅渣操作结束。
由于炉渣的分熔现象(也叫选择性熔化或异相分流),是指附着于炉衬表面的溅渣层,其矿物组成不均匀,当温度升高时,溅渣层中低熔点物首先熔化,与高熔点相相分离,并缓慢地从溅渣层流淌下来;而残留于炉衬表面的溅渣层为高熔点矿物,反而提高了溅渣层的耐高温性能。
在溅渣层的形成过程中,经过多次“溅渣-熔化-溅渣”的循环和反复使溅渣层表面一些低熔点氧化物发生“分融”现象。
使溅渣层MgO结晶和C2S(2CaO·SiO2)等高熔点矿物逐渐富集,从而提高了溅渣层的抗高温性能,炉衬得到保护。
溅渣层保护炉衬的机理(1)对镁碳砖表面脱碳层的固化作用吹炼过程中镁碳砖表面层碳被氧化,使MgO颗粒失去结合能力,在熔渣和钢液的冲刷下大颗粒MgO松动→脱落→流失,炉衬被蚀损。
溅渣后,熔渣渗入并充填衬砖表面脱碳层的孔隙内,或与周围的MgO颗粒反应,或以镶嵌固溶的方式形成致密的烧结层。
由于烧结层的作用,衬砖表面大颗粒的镁砂不再会松动→脱落→流失,从而防止了炉衬砖的进一步被蚀损。
(2)减轻了熔渣对衬砖表面的直接冲刷蚀损溅渣后在炉衬砖表面形成了以MgO结晶,或C2S和C3S为主体的致密烧结层,这些矿物的熔点明显地高于转炉终点渣,即使在吹炼后期高炉温度下不易软熔,也不易剥落。
因而有效地抵抗高温熔渣的冲刷,大大减轻了对镁碳砖炉衬表面的侵蚀。
(3)抑制了镁碳砖表面的氧化,防止炉村砖体再受到严重的蚀损溅渣后在炉衬砖表面所形成的烧结层和结合层,质地均比炉衬砖脱碳层致密,且熔点高,这就有效地抑制了高温氧化渣,氧化性炉气向砖体内的渗透与扩散,防止镁碳砖体内部碳被进一步氧化,从而起到保护炉衬的作用。
转炉溅渣护炉综述

转炉溅渣护炉综述
柳春桃
【期刊名称】《涟钢科技与管理》
【年(卷),期】1997(000)005
【摘要】转炉溅渣护炉是一项提高炉龄行之有效的方法,本文综述其工艺原理、操作、应用技术条件及国内外使用效果。
【总页数】5页(P1-5)
【作者】柳春桃
【作者单位】钢研所
【正文语种】中文
【中图分类】TF713.3
【相关文献】
1.炼钢转炉溅渣护炉技术的应用与实践 [J], 夏学超;李新民
2.60t转炉溅渣护炉技术控制实践 [J], 杨贺;姜成;陈彦川
3.60t转炉溅渣护炉技术控制实践 [J], 杨贺;姜成;陈彦川
4.转炉溅渣护炉工艺的研究与应用 [J], 朱元涛
5.推广溅渣护炉,提高转炉炉龄技术探讨 [J], 钟国
因版权原因,仅展示原文概要,查看原文内容请购买。
- 1、下载文档前请自行甄别文档内容的完整性,平台不提供额外的编辑、内容补充、找答案等附加服务。
- 2、"仅部分预览"的文档,不可在线预览部分如存在完整性等问题,可反馈申请退款(可完整预览的文档不适用该条件!)。
- 3、如文档侵犯您的权益,请联系客服反馈,我们会尽快为您处理(人工客服工作时间:9:00-18:30)。
摘要:本文简要介绍了转炉溅渣护炉的工艺原理和总结了实际应用中几个例如氮气喷吹参数,设备维护等关键因素。
关键词:转炉溅渣护炉工艺原理应用为了提高转炉炉龄,降低生产成本,减轻工人劳动强度,炼钢工作者采取了许多方法例如改善耐火材料质量,采取有效的喷补技术等。
这些措施对提高炉龄均起到了积极的作用使转炉炉龄有了一定程度的提高,但是随着炼钢技术的发展,炼钢工作者对炉渣和炉衬侵蚀机理的进一步研究,上世纪九十年代初美国LTV 公司率先开发出了溅渣护炉技术,通过近几年国内外实践得出溅渣护炉技术对炉衬维护有着喷补,贴补不可比拟的效果。
可以说溅渣护炉技术是转炉炉衬维护的又一大进步。
一.溅渣护炉的工艺原理1总述溅渣护炉是指在转炉吹炼结束出钢后,将转炉内留渣的粘度和氧化镁含量调整到合适的范围,用转炉系统原有的氧枪或专用氧枪向高氧化镁含量高粘度的炉渣喷吹一定压力和流量的氮气,将粘渣吹溅到炉衬上,使炉渣全面地炉衬上涂挂,冷却,凝固成一层炉渣质的保护层,避免了下一炉冶炼时钢水及炉渣直接和炉衬接触,从而达到减缓炉衬耐火材料层的蚀损,延长转炉炉龄的效果。
经过过国内外许多钢厂结合自己本厂的资源,工艺特点,进行开发应用证明溅渣护炉工艺对提高转炉炉龄和降低耐火材料消耗的效果非常显著,转炉炉龄在采用溅渣护炉后都有成倍的提高。
2溅渣层保护炉衬机理溅渣护炉的微观过程就是:高速氮气由喷枪喷溅到炉渣液面上,炉渣在氮气的巨大剪切力作用下迅速微粒化,微粒获得动能离开液体渣系向各个方向飞溅,以不同角度(高度)打在炉衬上。
微粒在形成,飞溅,粘结过程中不断被氮气冷却,最后在炉衬上粘附,固化,反应而形成一层炉渣的固体层覆盖住炉衬,从而减小炉衬的侵蚀,延长了炉衬的寿命。
2.1液态炉渣对炉衬的侵蚀机理炉渣对Mg-C 砖的侵蚀过程是:渣中(FeO)扩散到炉衬—渣界面,并与炉衬中的C 发生氧化还原反应而析出单质铁,同时对砖脱C 形成孔隙,铁单质进入炉渣,炉渣渗入孔隙与MgO 生成FeO ·MgO 固熔体进入渣中。
炉渣对耐火材料的侵蚀速度受固—液界面相边界层中传质速度控制,主要受渣中(FeO )的传质速度的控制。
转炉炉衬采用碱性MgO 或白云石质耐火材料做炉衬砖,炉衬中受侵蚀的关键物相为MgO ,MgO 在CaO-MgO-FeO-SiO 2熔体中的饱和溶解度曲线如下图所示。
其产物为MgO ·FeO 固熔体。
从图上可以得出当碱度大于2时,渣的成分对MgO 饱和溶解度影响不大。
MgO 的溶解度随温度的上升,氧化性的增强及碱度的下降而增高。
转炉冶炼前期炉渣碱度低,(FeO)含量高,因而前期渣的MgO 饱和溶解度高,对炉衬侵蚀教严重,中后期因碱度提高(FeO 低,渣中MgO 饱和溶解度低,所以后期的侵蚀主要是高温和强烈的冲刷造成的。
所以溅渣护炉的首要任务就是在前期完全保护炉衬,同时兼顾中后期对炉衬的保护。
转炉溅渣护炉的工艺原理与实际应用炼轧厂生产科胡勋48--2.2溅渣层保护炉衬的机理溅渣后,炉渣直接接触的是一层致密的溅渣层,炉衬基本不受炉渣和钢水的冲刷和侵蚀,溅渣层代替炉衬承受兑铁水和加废钢时的机械冲击,承受高温气—液混合相的冲刷,但由于溅渣层中的C3S 和方镁石熔点高达2000℃以上,所以它们不会完全熔化掉,保护炉衬不受过多的冲刷,MgO在渣中的饱和溶解度较大,MgO易向渣中扩散,溅渣层的致密性还阻止了炉渣和钢水向炉衬、气孔的渗透,对炉衬来说,溅渣层就相当与一层自耗性保护膜,溶进炉渣中的MgO在冶炼前期进入初渣而提高了碱度,相应降低了SiO2的活度,从而也减轻了对碱性炉衬的侵蚀。
溅渣层对转炉初期渣有较强的抗侵蚀能力,能够起到保护炉衬的作用。
但对高温终渣的抗侵蚀能力较差,所以进一步提高溅渣层的熔点是提高溅渣层抗侵蚀能力的关键。
2.3溅渣层与炉衬的结合机理1600℃,MgO在CaO—MgO—FeO—SiO2熔体中的饱和溶解度炉渣被溅到炉衬被粘附后,溅渣层与炉衬MgO-C砖在结合部发生了物理的和化学的发应,炼钢工作者发现其结合部分可分为三个区域:(1)烧结层:铁酸钙盐(C2F)沿镁碳表面的显微气孔和裂缝,向致密的氧化镁机体扩散,溶解与MgO颗粒反应生成镁橄榄石(MgO-Fe2O3)烧结层。
(2)结合层:在溅渣层--MgO砖表面,溅渣层中的铁酸钙将砖衬中突出的MgO颗粒包裹起来,形成镁铁橄榄石的化学结合,同时,溅渣层中的C3S,C2S和MgO颗粒在气流的作用下镶嵌在粗造的耐火衬表面,形成机械结合。
(3)溅渣层:以粗大的高熔点颗粒状C3S,C2S和MgO晶团为骨架,固熔在RO相和铁酸钙结合相中。
由此可见,溅渣层与炉衬砖的结合机理如下:在溅渣初期,低熔点经济性强的富铁炉渣首先溅射到炉衬表面,渣中FeO和C2F沿衬砖表面里微气孔和裂纹向MgO机体内扩散,与周围MgO颗粒烧结固溶在一起。
冷却后形成以(MgO·CaO)Fe2O3为主的烧结层。
随溅渣的继续,颗粒状的高熔点氧化物(C3S,C2S和MgO)被气流溅射到炉衬砖表面,并在高速气流的冲击下镶嵌在砖衬粗糙表面的间隙内,形成以镶嵌为主的机械结合。
同时富铁的低熔炉渣包裹在耐火砖表面突出的MgO颗粒周围形成化学结合层。
随着溅渣的进一步进行,使大颗粒C3S,C2S和MgO晶团溅射到结合层表面并与铁酸钙和RO相结合,冷却固溶形成衬砖表面溅渣层。
二、转炉溅渣护炉工艺操作1操作的几个步骤在正常生产过程中,如没有钢水严重氧化发生,既可进行溅渣护炉操作(当然对新砌炉座考虑到炉膛容积的问题,可暂不进行溅渣护炉)其操作如下:--49(1)转炉吹炼终点由冶炼操作人员出钢完毕,确认炉内钢水出尽,留下全部或部分炉渣,并确认炉渣状况。
(2)把转炉摇至零位(正常吹炼时)并根据炉渣状况确定是否加炉渣改质剂(通常有菱镁球、白云石、石灰石等)。
(3)把氮氧切换阀开至氮气位置,调好枪位,下枪吹氮(控制氮流量9000-14000m3/h压力1.0-1.4MPa),先从距炉底最低位开吹。
(4)溅渣时间由操作人员控制,一般2-3分钟。
(5)提枪停止吹氮,倒尽流淌的渣,如溅渣效果好,一般很少有流淌的渣。
2操作过程的几个关键因素决定溅渣效果的几个关键因素是:氮气喷吹参数、终渣条件和具体操作的相互协调统一。
这几个参数决定了溅渣的成功率。
2.1氮气喷吹参数这一参数包括氮气压力、流量、枪位、吹氮时间和氧枪喷头参数等。
现分述如下:(1)氮气压力:一般来说正常吹炼和溅渣护炉用的是同根氧枪,所以以氮气压力与正常吹炼时氧气压力相匹配。
我国太钢的试验参数为(入炉后)0.6-0.8MPa,首钢0.6-1.0MPa,酒钢1.0-1.2MPa。
(2)氮气流量:流量的最佳值尚无定论,目前根据前人经验,建议为氧气流量的80%-90%。
美国LTV 钢铁公司的氮气流量为510-620m3/min。
我国太钢氮气流量为150-195m3/min。
酒钢150-240m3/min。
(3)溅渣时间:溅渣时间由操作人员掌握。
要求能保证炉衬全面挂渣。
美国LTV钢铁公司吹氮时间为2-3min,我国太钢最初预设吹氮时间为1.5-2min,实践中发现溅渣效果不理想,后改为2.5-3min,效果明显好转。
酒钢设定为2.5-3min,如遇特殊情况可适当延长。
(4)枪位:溅渣枪位一般与吹氧枪位接近或取吹氧的下限位。
美国LTV公司克利夫兰东方分厂为2.0m(距炉底),首钢为1.5-2.2m,酒钢规定溅渣枪位距冶炼最低枪位以下0.4m左右。
(5)氧枪喷头参数:主要为喷孔数目及喷孔轴线与喷枪轴线的夹角。
印第安那哈伯厂236吨转炉使用4孔喷枪,曾经做过10°12°14°的试验,发现12°时效果最好,10°时溅渣太高,14°溅渣太低。
这是由于不同公称容量的转炉炉型具有不同的高径比(H/D)。
转炉溅渣所需的能量主要不决定于转炉容量的大小,而决定于炉型几何尺寸,如(H/D)小的矮胖型转炉,要求的溅渣能量反而小,(H/D)值较大的小型转炉(我国以中小型转炉居多)角度究竟选多大合适,应根据具体炉型的高径比来选取。
酒钢采用168mm4孔拉瓦尔喷枪,喷孔轴线与喷枪轴线的夹角为12度。
2.2适宜溅渣护炉炉渣条件炉渣条件主要是指炉渣成分温度及,留渣量、溅渣率等。
(1)炉渣成分:炉渣成分影响炉渣粘度,炉渣太干根本不能与炉衬粘附,太稀则容易顺炉衬流下,粘附效果也不好,如果终渣粘度较低,提高粘度最现实的方法就是提高渣中MgO含量。
溅渣要求渣中MgO达到8%-14%,调节措施是出钢后加入MgO基原料。
如石灰石,白云石等。
(2)炉渣温度:出钢后温度太高会使溅渣层脱落,同时粘度低也不利于炉渣的粘附,因此降低炉渣过热度可以考虑:1)争取一次拉碳成功,减少补吹。
2)加入调节剂降温。
3)增加吹N2时间。
(3)留渣量:这由预期的溅渣层厚度,炉型尺寸及残渣量决定,过低的留渣量达不到所需的溅渣厚度,影响溅渣效果,而过大的渣量会增加溅渣成本,宝钢留渣量2t左右(实践发现偏少),马钢第三炼钢厂溅渣量控制在总渣量的50%-70%约5t左右,效果良好,酒钢留渣量在3t左右,效果良好。
(4)当溅渣层较薄或出钢温度高,需要有较高的溅渣率。
如太钢溅渣率在70%左右,鞍钢溅渣率90%,酒钢溅渣率80%以上。
实践证明溅渣率和转炉炉龄成正比关系,因此,在各方面条件允许的情况下,尽可能提高溅渣率。
--503操作的相互协调统一溅渣护炉计算主要由炼钢工负责,决定是否溅渣和溅渣时间,但也要与转炉区域其他人员做好配合,如炉下渣罐,炉前兑铁加废钢工以及生产调度人员等。
4实践结果实行溅渣护炉工艺的优越性最终体现在转炉炼钢工序经济效率的增长,经济效率的增长主要表现在转炉炉龄的大幅度提高,耐火材料消耗大幅度减小,最直观的就是时间和产量上的收益。
还有因为溅渣护炉相对喷补,补贴时间短,工人劳动强度小,所以说溅渣护炉对解放生产力做出了一大贡献。
5溅渣护炉存在的问题及处理措施任何一个新技术的诞生和应用过程中都会产生一些问题,溅渣护炉也不例外地产生一些新问题。
例如:炉底上涨和氧枪粘结,辅助设备的维修、维护以及溅渣护炉的安全问题都值得关注:5.1炉底上涨问题溅渣护炉易造成炉底上涨。
根据酒钢生产经验,溅渣吹氮枪位过高,流量较小时,易造成炉底上涨,溅渣吹氮枪位低,流量大时不易形成。
因此,预防办法是控制好留渣量,溅渣时间,氮气参数以及枪位,尽量把炉渣吹起来。
对于已上涨的炉底酒钢采用吹氧而熔化炉底有结渣层,同时根据具体情况摇炉,有针对性地洗掉结渣。
5.2氧枪粘结问题氧枪粘结问题在未采用溅渣护炉之前就出现了,一些炼钢厂引进这项技术后更加恶化,如果再遇到钢水出不尽的炉次则问题更为严重。
预防的办法就是在整个吹炼过程中化好渣,避免引起金属喷溅,同时出钢时一定要把钢水出干净,避免钢渣混溅,防止钢渣混粘。