转炉溅渣护炉技术
浅析转炉溅渣护炉技术的应用
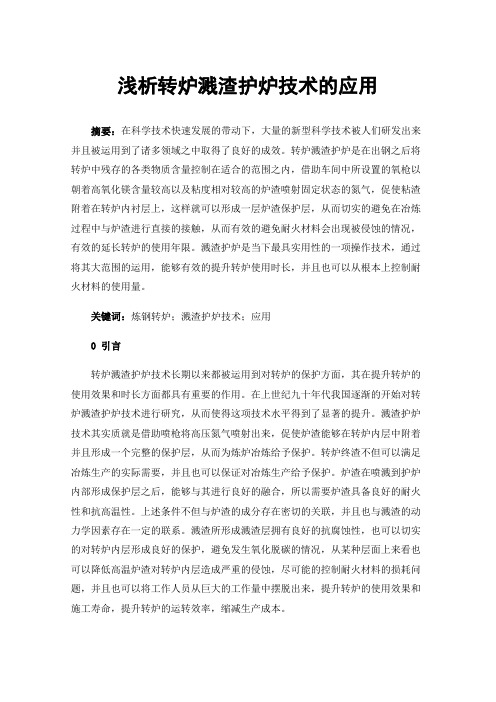
浅析转炉溅渣护炉技术的应用摘要:在科学技术快速发展的带动下,大量的新型科学技术被人们研发出来并且被运用到了诸多领域之中取得了良好的成效。
转炉溅渣护炉是在出钢之后将转炉中残存的各类物质含量控制在适合的范围之内,借助车间中所设置的氧枪以朝着高氧化镁含量较高以及粘度相对较高的炉渣喷射固定状态的氮气,促使粘渣附着在转炉内衬层上,这样就可以形成一层炉渣保护层,从而切实的避免在冶炼过程中与炉渣进行直接的接触,从而有效的避免耐火材料会出现被侵蚀的情况,有效的延长转炉的使用年限。
溅渣护炉是当下最具实用性的一项操作技术,通过将其大范围的运用,能够有效的提升转炉使用时长,并且也可以从根本上控制耐火材料的使用量。
关键词:炼钢转炉;溅渣护炉技术;应用0引言转炉溅渣护炉技术长期以来都被运用到对转炉的保护方面,其在提升转炉的使用效果和时长方面都具有重要的作用。
在上世纪九十年代我国逐渐的开始对转炉溅渣护炉技术进行研究,从而使得这项技术水平得到了显著的提升。
溅渣护炉技术其实质就是借助喷枪将高压氮气喷射出来,促使炉渣能够在转炉内层中附着并且形成一个完整的保护层,从而为炼炉冶炼给予保护。
转炉终渣不但可以满足冶炼生产的实际需要,并且也可以保证对冶炼生产给予保护。
炉渣在喷溅到护炉内部形成保护层之后,能够与其进行良好的融合,所以需要炉渣具备良好的耐火性和抗高温性。
上述条件不但与炉渣的成分存在密切的关联,并且也与溅渣的动力学因素存在一定的联系。
溅渣所形成溅渣层拥有良好的抗腐蚀性,也可以切实的对转炉内层形成良好的保护,避免发生氧化脱碳的情况,从某种层面上来看也可以降低高温炉渣对转炉内层造成严重的侵蚀,尽可能的控制耐火材料的损耗问题,并且也可以将工作人员从巨大的工作量中摆脱出来,提升转炉的使用效果和施工寿命,提升转炉的运转效率,缩减生产成本。
1溅渣护炉工艺的冶金因素及其优势就溅渣护炉工艺的实际操作流程来说,主要包括下面几个方面:第一,将钢水从转炉转移到大包中。
转炉冶炼低碳钢时的溅渣护炉技术
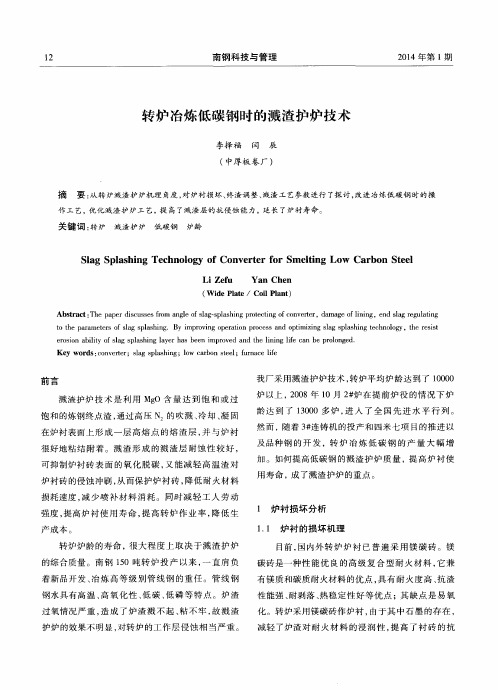
强度 , 提高炉衬 使用 寿命 , 提高 转炉 作业 率 , 降低生
产成本 。
1 炉 衬损坏 分 析
1 . 1 炉衬 的损 坏机 理
转炉炉龄 的寿命 , 很 大程度 上取 决于溅 渣护 炉 的综合质量 。南 钢 1 5 0吨转 炉投 产 以来 , 一 直肩 负
着新 品开发 、 冶炼 高 等级别 管线 钢 的重任 。管线 钢 钢水具有 高温 、 高氧化 性 、 低碳 、 低磷 等特 点 。炉 渣 过氧情况严 重 , 造 成 了炉渣 溅不 起 、 粘 不牢 , 故溅 渣
e r o s i o n a b i l i t y o f s l a g s p l a s h i n g l a y e r ha s be en i mp r o v e d a nd t h e l i n i n g l i f e ca n b e pr o l o n g e d. Ke y wo r ds: e o n v e  ̄e r;s l a g s p l a s hi n g;l o w c a r bo n s t e e l ;f ur n a c e l i f e
及 品种 钢 的 开 发 ,转 炉 冶 炼 低 碳 钢 的 产 量 大 幅 增
加 。如何提高低碳钢 的溅渣 护炉 质量 ,提高炉 衬使 用 寿命 , 成了溅渣护炉的重点 。
炉衬砖 的侵蚀 冲刷 , 从而保护炉衬 砖 , 降低耐 火材料
损耗 速 度 , 减 少 喷 补 材 料 消 耗 。 同 时 减 轻 工 人 劳 动
1 2
南 钢科 技与 管理
2 0 1 4年第 1 期
转 炉 冶炼 低碳 钢 时 的溅 渣 护 炉 技术
李择福 闫 辰
转炉溅渣护炉系统优化技术基础理论研究
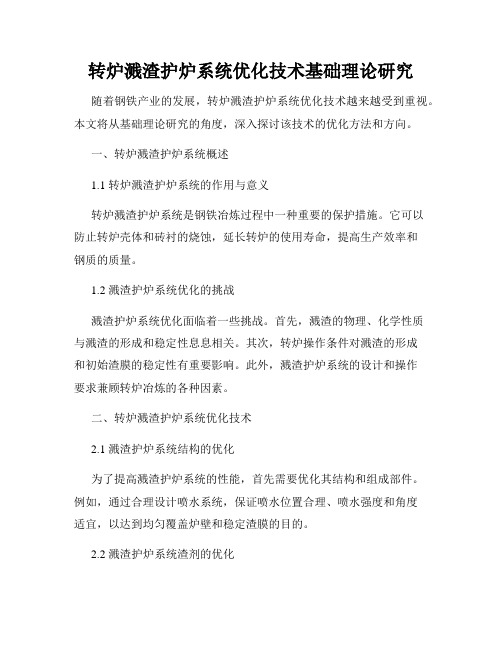
转炉溅渣护炉系统优化技术基础理论研究随着钢铁产业的发展,转炉溅渣护炉系统优化技术越来越受到重视。
本文将从基础理论研究的角度,深入探讨该技术的优化方法和方向。
一、转炉溅渣护炉系统概述1.1 转炉溅渣护炉系统的作用与意义转炉溅渣护炉系统是钢铁冶炼过程中一种重要的保护措施。
它可以防止转炉壳体和砖衬的烧蚀,延长转炉的使用寿命,提高生产效率和钢质的质量。
1.2 溅渣护炉系统优化的挑战溅渣护炉系统优化面临着一些挑战。
首先,溅渣的物理、化学性质与溅渣的形成和稳定性息息相关。
其次,转炉操作条件对溅渣的形成和初始渣膜的稳定性有重要影响。
此外,溅渣护炉系统的设计和操作要求兼顾转炉冶炼的各种因素。
二、转炉溅渣护炉系统优化技术2.1 溅渣护炉系统结构的优化为了提高溅渣护炉系统的性能,首先需要优化其结构和组成部件。
例如,通过合理设计喷水系统,保证喷水位置合理、喷水强度和角度适宜,以达到均匀覆盖炉壁和稳定渣膜的目的。
2.2 溅渣护炉系统渣剂的优化渣剂是溅渣护炉系统中起着关键作用的组成部分。
通过优化渣剂的物理、化学性质,可以改善渣膜的稳定性和降低溅渣对炉壁的侵蚀。
此外,选择合适的渣剂还可以提高转炉冶炼的效率和钢质的质量。
2.3 溅渣护炉系统操作参数的优化转炉冶炼中,操作参数的优化对溅渣护炉系统的性能影响巨大。
如合理控制氧枪的氧浓度和流速,可以影响转炉中的气体组成和温度分布,从而改善渣膜的稳定性和溅渣的产生。
三、转炉溅渣护炉系统优化的基础理论研究3.1 溅渣生成机制研究溅渣的生成机制是转炉溅渣护炉系统优化的基础。
通过研究渣剂的物理、化学性质和与炉壁的相互作用,可以揭示溅渣产生的机理和规律。
3.2 渣膜稳定性研究渣膜的稳定性影响整个溅渣护炉系统的工作效果。
通过研究渣膜在高温、高压环境下的性质和行为,可以为渣膜的稳定性优化提供理论依据。
3.3 操作参数对溅渣的影响研究操作参数对溅渣的形成和稳定性具有重要影响。
通过模拟实验和理论计算,可以探究操作参数对溅渣护炉系统的影响规律,并为优化操作参数提供理论指导。
转炉溅渣护炉技术

转炉溅渣护技术东北大学冶金技术研究所二OO五年四月目录第一章转炉炉龄技术的发展 ----------------------------------------- 1 第二章转炉溅渣护炉工艺参数 ---------------------------------------- 42.1转炉氧枪枪位、顶吹气体流量及留渣量与溅渣量的关系 ------- 42.1.1转炉氧枪枪位对溅渣护炉的影响 ------------------------- 62.1.2氧枪氮气流量对溅渣护炉的影响 ------------------------- 72.1.3转炉留渣量对溅渣护炉的影响 --------------------------- 82.2溅渣时间 ----------------------------------------------- 92.3溅起的炉渣在转炉炉衬内表面上分布 ----------------------- 112.4氧枪喷头结构对溅渣护炉的影响 --------------------------- 122.5底吹对复吹转炉溅渣护炉的影响 --------------------------- 132.6枪位、炉渣粘度对溅渣护炉的炉渣飞溅高度的影响 ----------- 16第三章转炉溅渣护炉改渣剂的研究与应用 ------------------------------ 17第四章转炉溅渣层与炉衬结合机理 ------------------------------------ 214.1溅渣层与炉衬结合形貌 ----------------------------------- 214.2溅渣层与炉衬结合机理分析 ------------------------------- 27第五章溅渣与喷补的结合 ------------------------------------------- 305.1转炉炉衬的毁损 ----------------------------------------- 305.2喷补 --------------------------------------------------- 30第一章转炉炉龄技术的发展转炉炉衬由工作层、填充层和永久层的耐火材料组成,工作层直接与高温钢水、高氧化性炉渣和炉气接触,不断受到物理的、机械的和化学的侵蚀作用。
溅渣护炉

转炉溅渣护炉的效果,决定于溅渣层与炉衬间的结合状态。
溅渣层与炉衬的结合原理包括炉渣如何与炉衬砖有机地相结合,炉渣层如何有效地保护转炉炉衬。
1 溅渣层的成分与结构生产实践证明,采用溅渣护炉在转炉炉衬表面形成的溅渣层,在成分和岩相结构方面,不仅和炉衬砖有明显的差距,而且和转炉终渣(或改质处理后的炉渣)也有区别。
这种区别是由于反复溅渣过程中,炉衬耐火材料与炉渣间经过长时间的高温化学反应扩散渗透与溶解脱熔、熔化与析出、剥落与烧结等复杂的过程逐步形成的。
2 溅渣层成分的变化(1)在溅渣过程中,炉渣成分(指终渣溅后渣和溅在炉壁表面上的炉渣)不会发生明显的变化,喷溅到炉壁上的炉渣(或溅后渣)成分与终渣大致相同。
(2)由于炉衬表面温度不同和炉衬传热热流密度的差别,在溅渣过程中炉渣成分也会发生微小的变化。
这主要是由于溅渣中发生了“异相分流”效应,使渣射到炉衬表面上的一些液态低熔氧化物流失。
这就导致溅渣层表面高熔点化合物浓度稍有增加(如MgO结晶,C2S 和C3S),而低熔点氧化物(如FeO等)减少(溅后渣成分变化的趋势则相反),溅渣中“异相分流”引起的成分变化一般不超过2%。
(3)溅渣层的成分与转炉终渣有明显的区别,高熔点化合物(MgO结晶,C2S和C3S)的浓度明显增加;有一些氧化物(如MnO,P2O5,Al2O3,SiO2等)显著减少。
(4)对于不同的溅渣工艺,溅渣层的成分有明显的区别。
采用高FeO炉渣溅渣,溅渣层中MgO含量很高,达到58.4%;而TFe含量比终渣略有降低,CaO、SiO2等成分显著降低。
这说明高FeO炉渣溅渣形成的溅渣层主要以MgO,(MgO,Fe2O3)为主相。
采用低FeO 炉渣溅渣,溅渣层中CaO和MgO含量富集,SiO2含量略有降低,碱度升高,说明该溅渣层是以C3S为主相,以C2S和MgO结晶为辅相。
根据上述溅渣层与转炉中渣有成分上的明显差异,可以得到进一步推论如下:(1)溅渣层是通过炉渣与炉衬耐火材料间在较长时间内发生化学反应逐渐生成的。
转炉溅渣护炉技术9

9.什么是转炉溅渣护炉技术?答:转炉溅渣技术是近年来开发的一种提高炉龄的新技术。
它是在20世纪70年代广泛应用过的、向炉渣中加入含MgO的造渣剂造黏渣挂渣护炉技术的基础上,利用氧枪喷吹高压氮气,在2—4min内将出钢后留在炉内的残余炉渣喷溅涂敷在整个转炉内衬表面上,形成炉渣保护层的护炉技术。
该项技术可以大幅度提高转炉炉龄,且投资少、工艺简单、经济效益显著。
此项技术是由美国Praxair气体公司开发、在美国共和钢公司的GreatLakes(大湖)分厂最先应用,在大湖厂和GraniteCity厂实施后,并没有得到推广。
1991年美国LTV公司的Indiana HaBOr厂用溅渣作为全面护炉的一部分。
1994年9月该厂252t顶底复吹转炉的炉衬寿命达到15658炉,喷补料消耗降到0.37kg /t钢,喷补料成本节省66%,转炉作业率由1987年的78%提高到1994年的97%。
溅渣护炉技术能使炉衬在炉役期中相当长的时间内保持均衡,实现“永久性”炉衬。
10.溅渣护炉技术的基本原理是什么?答:溅渣护炉技术的基本原理,是在转炉出钢后,调整余留终点渣成分,利用MgO含量达到饱和或过饱和的终点渣,通过高压氮气的吹溅,在炉衬表面形成一层与炉衬很好烧结附着的高熔点溅渣层,如图2—1所示。
这个溅渣层耐蚀性较好,并可减轻炼钢过程对炉衬的机械冲刷,从而保护了炉衬砖,减缓其损坏程度,使得炉衬寿命得以提高。
11.溅渣护炉对炉渣的组成与性质有哪些要求?答:炉渣成分是指构成炉渣的各种矿物的成分,它决定了炉渣的基本性质。
一般说来,初期渣的主要成分是SiO2、MnO、CaO、MgO和FeO等,随着吹炼过程进行,石灰熔化、渣量增加,使SiO2、MnO的含量逐渐降低,CaO、MgO的含量逐渐增加。
13.底吹对复吹转炉溅渣的影响有哪些?答:在复吹转炉溅渣过程中,由于底吹射流的介入,熔池中炉渣的搅动增强。
底吹气体涌起熔渣高度与底吹气体射流搅拌能有关:εv. b=2×371KQT1/Vm ln (1+9.8ρL/P)式中εv. b——底吹气体射流的搅拌能,W/m3.s K——喷体体积增加率,%;Q——底吹气体流量(标态),m3/min;TL——底吹气体温度,℃;Vm——熔池体积,m3;ρL——熔池液体(熔渣)密度,m3/min;p——大气压力,Pa理论上分析增加底吹气体量Q,即增大底吹搅拌能εv. b ,有利于溅渣。
转炉溅渣护炉技术(讲座)PPT课件

实际上,溅渣护炉时残留在炉内的 终渣是一种最安全的留渣操作,它有利 于早化初渣,并可促进前期脱P。
首钢三炼钢在前炉溅渣和未溅渣两 种情况下,对吹炼3未溅渣的1.16%提高到1.95%。
(2)中期渣 转炉吹炼中期,铁水中Si、Mn已
转炉溅渣护炉技术
1、 溅渣护炉简介
图1 溅渣护炉示意图
•1991年美国LTV钢铁公司开始采用溅渣护 炉技术,现已有12个钢厂采用,其中内 陆钢厂1998年炉龄达33000次仍在吹炼。
•国内30吨以上转炉绝大部分采用溅渣护 炉技术,炉龄2万炉以上,莱钢30吨转炉 3万炉以上。
•国内部分15吨转炉采用溅渣护炉技术 (三明,安钢等)。 •武钢80吨复吹转炉底吹元件寿命与炉龄
同步,达1万炉以上。
2、溅渣护炉的炉渣控制
2.1溅渣护炉工艺过程
吹炼过程造好渣
出钢后将转炉摇正
降下氧枪吹氮2-3分钟
将多余炉渣倒出
2.2 造渣工艺
转炉采用溅渣护炉技术后, 造渣工艺可简单概括为“初渣早化, 过程渣化透,终渣做粘,溅渣挂 上”。
(1)初渣
在吹炼前期能否迅速形成高碱度的 炉渣,是减轻初渣对溅渣层及炉衬侵蚀 的一个重要环节。
当碱度从1.0提高到2.0时,MgO饱和值相应 由~12%降到~7%,早化初渣尽快提高碱度,MgO饱 和值会显著降低。因而,影响初渣MgO饱和溶解度 的主要因素是碱度。
温度升高,MgO饱和溶解度也相应增 加,大约是温度每提高50℃,MgO饱和 值增加1.0-1.3%。
当终渣碱度为3时,温度由1600℃ 升高到1700℃,MgO饱和值由6%增加到 8.5%。因此,影响终渣MgO饱和溶解度 的主要因素是温度。
在实施溅渣护炉后的造渣实践中,鞍 钢180t转炉使用活性石灰,并在开吹时 加入轻烧镁球、锰矿和复合球团,吹炼 5分钟时的初渣碱度由普通石灰的1.2提 高到2.0。
转炉溅渣护炉系统优化技术基础理论研究

转炉溅渣护炉系统优化技术基础理论研究摘要:在“转炉溅渣护炉系统优化技术开发”项目中,着重进行了熔池溅渣动力学、溅渣层粘结机理、炉渣对溅渣层的蚀损机理及合理的终渣成分控制等基础理论方面的研究工作。
介绍了上述几项研究工作的初步结果。
1前言溅渣护炉技术是在转炉吹炼结束后,通过顶吹氧枪高速喷吹氮气射流,冲击残留在熔池内的部分高熔点炉渣,使熔渣均匀地喷溅粘附在转炉炉衬表面,形成炉渣保护层,达到护炉的目的。
该技术在美国LTV厂成功后,使转炉炉龄从5000炉提高到15000炉以上,创造了目前世界上最高的转炉炉龄记录。
该项先进技术介绍到中国后,我国许多工厂结合本厂的资源、工艺特点,进行开发采用,获得了明显的经济效益。
尽管溅渣护炉技术已经在生产中广泛应用,并获得了巨大的成功。
但在溅渣护炉技术的基础理论研究方面,却处于空白状态。
最近该方面的研究已经引起国内外广大冶金学者的重视。
本文将简单总结钢铁研总院工艺所在下述领域里的研究结果:(1)熔池溅渣动力学的研究;(2)溅渣层与炉衬的结合机理;(3)溅渣层的浸蚀试验;(4)合理的终渣成分控制。
2熔池溅渣动力学的研究如何有效地利用高速氮气射流将炉渣均匀地喷溅在炉衬表面,是溅渣护炉的技术关键。
其效果决定于以下控制因素:(1)熔池内留渣量和渣层厚度;(2)熔渣的物理状态:炉渣熔点、过热度、表面张力与粘度;(3)溅渣气动力学参数:喷吹压力、枪位以及喷枪夹角和孔数等。
通过水力学模型试验和理论分析,研究了熔池溅渣动力学过程,初步提出优化溅渣的工艺参数。
2.1水模型测定(1)喷吹工艺对溅渣高度的影响1)对不同的介质,不同高度条件下的溅渣量的分布基本相似,随着溅渣高度的升高,溅渣量逐渐降低。
2)当溅渣高度hs/D=1.0时,不同高度下的溅渣量的分布规律发生变化。
当hs/D≤l.0时,溅渣量的比例高达总渣量的30%~60%,随着高度的增加,溅渣量将迅速降低。
在hs/D≥1.0以后溅渣量随高度增加,溅渣量减少的速率降低。
转炉炼钢工艺(溅渣护炉)

溅渣护炉的负面影响
吹炼终点[%C] ·[%O]积随炉龄变化情 吹炼终点 积随炉龄变化情 况
关于经济炉龄的问题
生产率、 生产率、成本与炉龄关系
溅渣护炉的优点
大幅度降低耐材消耗; 大大提高转炉作业率,达到高效增产目的; 投资回报率高; 溅渣护炉综合效益每吨钢约为2~10元。
溅渣护炉的负面影响
底吹透气砖覆盖渣层厚度与吹炼终点[%C] ·[%O]积的关 底吹透气砖覆盖渣层厚度与吹炼终点 积的关 系
溅渣护炉的负面影响
底吹透气砖覆盖渣层厚度与吹炼终点[%C] ·[%O]积的关 底吹透气砖覆盖渣层厚度与吹炼终点 积的关 系
炉渣粘度的控制
过低的炉渣粘度有利溅渣的操作,即易溅起、挂 渣且均匀,但由于渣层过薄,会在摇炉时挂渣流 落; 而粘度过大,溅渣效果差,耳轴!渣线处不易溅到, 且炉底易上涨,炉膛变形,所以粘度需要根据实 际情况合理调整; 炉渣过热度增高,粘度下降。
溅渣操作参数控制
为了在尽可能短的时间内将炉渣均匀喷 敷在整个炉衬表面而形成有足够厚度的 致密溅渣层。必须控制好溅渣操作手段, 即根据炉形尺寸,来控制喷吹N2气压力 和流量、枪位和喷枪结构尺寸等喷溅参 数。
其它参数
喷溅时间:通常为2.5~4min; 喷枪夹角:许多厂家的经验表明采用12 度夹角比较理想。
需要采取的其它措施
炉衬材质不能因实行溅渣护炉技术而降 低,对使用镁碳砖而言,其碳含量应控 制为下限; 控制和降低终渣FeO含量; FeO 合理调整终渣MgO含量; 提高溅渣层熔化性温度,降低炉渣过热 度; 降低出钢温度。
溅渣护炉技术在转炉上的应用

溅渣护炉技术在转炉上的应用
溅渣护炉技术是一项新兴的技术,它可以提高转炉的燃烧效率,减少对环境的影响。
溅渣护炉技术是通过把大量的液体或气体加到炉内,使溅射出来的渣滓变得更轻而易于把它带走而得以应用于转炉上。
这样可以大大提高转炉的燃烧效率,减少对环境的影响。
溅渣护炉技术的主要原理是在炉子内部加入溅射液体或气体,使溅射出来的渣滓变得更轻,而且更易于把它带走。
此外,溅渣护炉技术还可以改善炉子内部燃烧状态,提高燃烧效率,从而降低炉子本身的耗能。
溅渣护炉技术在转炉上的应用主要体现在以下几个方面:
1、降低转炉内部的温度:在转炉内部加入溅射液体或气体,使渣滓变得更轻,从而降低转炉内部的温度,提高转炉的燃烧效率。
2、减少对环境的污染:由于转炉内部的温度较低,因此溅渣护炉技术也可以减少对环境的污染。
3、改善转炉内部燃烧状态:在转炉内部加入溅射液体或气体后,可以改善转炉内部的燃烧状态,从而提高燃烧效率,减少渣滓的生成。
4、降低燃料的消耗:由于溅渣护炉技术可以提高转炉的燃烧效率,从而降低燃料的消耗,节省能源,降低成本。
总之,溅渣护炉技术可以有效提高转炉的燃烧效率,减少对环境的污染,节省能源,降低成本。
在转炉上应用溅渣护炉技术,将会带来很好的经济效益和社会效益。
转炉溅渣护炉技术
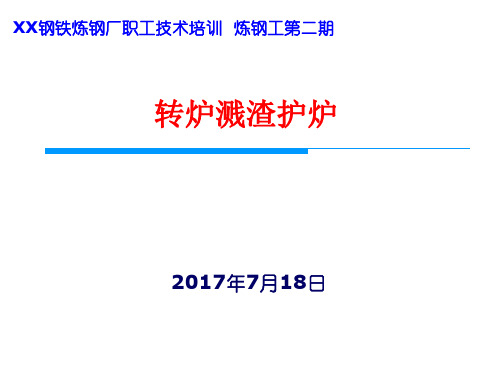
工艺措施
打击方式 抽真空 真空油浸 原料纯度 颗粒配比 树脂质量 抗氧化剂数量 模具质量
碳含量
如何延长转炉炉衬的使用寿命
4 转炉砌筑
减少衬砖损坏 背紧靠实,砖缝0.5mm-1mm 合缝位置在耳轴 避免倒插门 砌后细料扫填 开炉前减少摇炉
如何延长转炉炉衬的使用寿命
刚吹炼时,石灰难熔化,是因为石灰的熔化靠吹氧使铁水氧化形成的FeO 很少,这一段时间渣的碱度上不来,故炉衬的受浸蚀量大。上述两个原因导致吹炼 前期炉衬浸蚀是最严重的。
一、刚开吹时投入含FeO材料使炉渣中的氧化铁含量迅速增加,从而促 进石灰迅速熔化,提高炉渣碱度,降低渣中MgO的饱和熔解度。
二、刚开始吹炼时加入轻烧白云石或轻烧镁球,从渣中本身就会有 8%~9%的MgO,以减少炉渣为保持自己的饱和熔解度而对炉衬的浸蚀。
MgO含量在炉衬与炉渣中的平衡 氧化镁在炼钢渣中的饱和溶解度,渣中FeO含量越高,炉渣碱度
越小,炉渣的温度越高,MgO在渣在溶解度越大。
炉渣中的MgO在没有达到饱和时,就要从炉衬中浸取MgO,努力达到饱和 浓度,这也叫平衡,而MgO在炉渣中的含量和溶解度随炉渣的碱度R(CaO/SiO2) 的减小而迅速增大。当R=3.5时,其饱和熔解度为8%~9%,可是刚刚开吹时,石 灰没全熔化而铁水中Si氧化成二氧化硅(SiO2)量又很大,所以CaO/SiO2值很小 只有1%左右,这时MgO在渣中的熔解度远远大于8%~9%,有时达到30%,必然 要大量从炉衬中浸取熔解MgO使炉衬受到大量熔损。
9 转炉的维护 维护方式 1、喷补; 2、换出钢口管,及内出钢口修补; 3、垫补前大面。
转炉炉衬的垫补、喷补方式
1、湿法喷补 料与水先混合; 2、半干法喷补 料水在喷枪出口处混合; 3、火焰喷补 料经出口火熘部分熔化。
对转炉溅渣护炉及长寿复吹工艺的分析

对转炉溅渣护炉及长寿复吹工艺的分析0.引言转炉溅渣护炉技术的常规原理主要是由于在转炉出钢后,在炉内势必会留下终渣,按照渣况实施相对应的改质,利用高压氮气喷吹溅炉渣,把炉渣吹溅至炉壁,从而造成溅渣层。
在进行下一炉的炼钢过程中,可以起到屏障炉衬,以此,来实现转炉长寿的作用。
当前对钢水质量标准的要求日益严格,而复吹工艺却显现出了炉底上涨、透气砖阻滞、底吹供气管道出现漏气等诸多层面的大小问题。
1.我国转炉溅渣护炉与长寿复吹工艺的原理与现状转炉溅渣护炉技术的原理,是在转炉出完钢之后融进适量的调渣剂,其目的旨在让里面的MgO和炉渣发生化学反应,能够形成生成系统的高熔点物质。
之后,再被氧枪系统发射的高压氮气喷溅至炉衬的大多数范围亦或是设计范围,以此,依附在炉衬内壁慢慢冷凝成为坚固、稳定的屏障保障,最终变成能够得以耗损的耐材层。
转炉冶炼的过程中,保护层能够较大的弱化高温气流和炉渣对转炉炉衬的化学性侵蚀与产生的冲刷,通过养护炉衬、延长炉龄而且缩减耐材耗损。
氧气顶吹转炉溅渣护炉是指在转炉出钢之后把炉体维续在直立的程度,再通过顶吹氧枪给炉内喷射1.0 MPa高压氮气,把炉渣喷溅至炉衬上面。
由于渣粒是通过极为强劲的力道依附至炉衬上面,因此必然会和炉壁契合的十分牢固,能够高效地阻滞炉渣给炉衬造成的化学侵蚀。
长寿复吹转炉溅渣护炉是指把顶吹与底吹都转换成氮气,由上到下的不同方向,吹到转炉内炉渣,将炉渣溅起后,使其得以粘附在炉衬内壁上,从而保护炉衬。
溅渣护炉技术最大程度上应用了转炉终渣且通过氮气视为喷吹动力,毫无疑问,这在转炉技术上是立竿见影的巨大进步。
其相较于,干法喷补、火焰喷补、人工砌砖等诸多办法更为科学、合理、可操作性,不但可以压制炉衬砖表面的氧化出现脱碳现象,还可以弱化高温渣对于炉砖所产生的化学侵蚀及机械冲刷,最终起到保护炉衬砖,缩减耐火材料蚀损的整体速率[1]。
更为重要的是,可以缩小由于喷补技術所造成的材料耗损,极大的降低了工人的劳动强度。
溅渣护炉技术
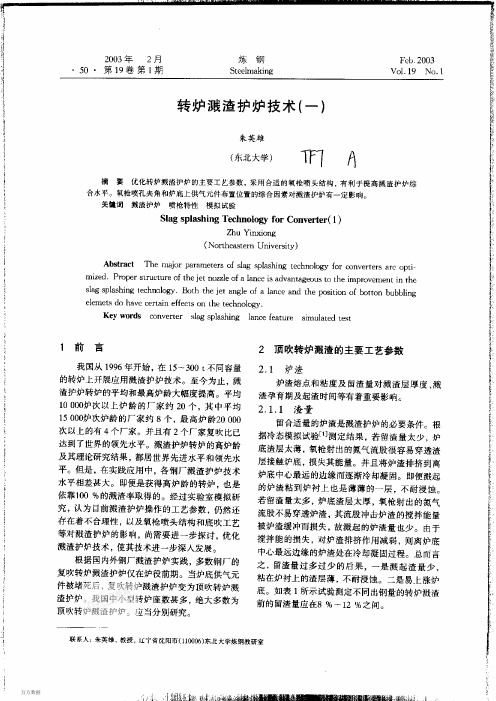
2 11 渣量 .. 留合适量的炉渣是溅渣护炉的必要条件。根
据冷态 模拟试 t 验[测定结果, 渣量太少, l 若留 炉
底渣层太薄, 氧枪射出的氮气流股很容易穿透渣 层接触炉底, 损失其能量。并且将炉渣排挤到离 炉底中心最远的边缘而逐渐冷却凝固。即便溅起 的炉渣粘到炉衬上也是薄薄的一层, 不耐浸蚀。 若留渣量太多, 炉底渣层太厚, 氧枪射出的氮气 流股不易穿透炉渣, 其流股冲击炉渣的搅拌能量 被炉渣缓冲而损失, 故溅起的炉渣量也少。由于 搅拌能的损失, 对炉渣排挤作用减弱, 则离炉底 中 心最远边缘的炉渣处在冷却 凝固 过程。总而言 之, 留渣量过多过少的后果, 一是溅起渣量少, 粘在炉衬上的渣层薄, 不耐浸蚀。二是易上涨炉 底。如表 1 所示试验测定不同出钢量的转炉溅渣 前的留渣量应在8%一论 %之间。
K y rs ne e l slh g ne tr iu t t t e w d c vr r a p si l c f ue m le e o o t sg a n a e s a d a s
1前
言
2 顶吹转炉溅渣的主要工艺参数
2 1 炉渣 .
炉渣熔点和粘度及留渣量对溅渣层厚度、 溅 渣孕育期及起渣时间等有着重要影响。
第1 期
朱英雄 : 转炉溅渣护炉技术( ) 一
表 1 顶吹转炉戮渣时的最佳留渣f
厂
家
出钢星i t l l2 12 冷态模拟留 渣量/ % 实际留渣量/ 1 % 0一1 6-S' 0一1 2 1 2 》 因双渣操作 , 终渣量少
纂 80
梅钢
150
本钢
父
纂
酒钢
新钢
5 1 1 31
{ 一
1 - 1 8一 l 0 2 0 6一R“ 6 ̄8“
转炉渣控制及溅渣护炉技术
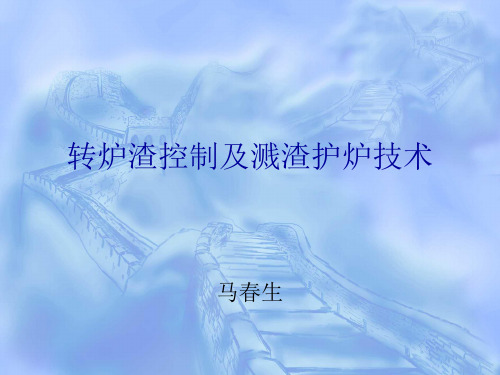
溅渣层组成
1。高氧化铁炉渣: 氧化镁 2。低氧化铁渣: 硅酸二钙、硅酸三钙
渣子成分
为了保证良好的溅渣效果,并使溅渣层有耐 下一炉炉渣高温侵蚀的性能,可在出钢后根 据渣中FeO含量来调节渣中的MgO含量及炉 渣的粘度。 T FeO 10—12% (MgO) ~7.5—8% T FeO 12—16% (MgO) ~8—9% T FeO 16—20% (MgO) ~9—10%
理论依据
加白云石造渣:使渣中含MgO量达到6—8%, 使其进入饱和状态,减少炉衬中MgO向渣中 扩散。减轻炉渣在冶炼中对炉衬的侵蚀。提 高炉衬寿命。 溅渣护炉:使含有MgO、C2S、C3S量较高的 渣被溅挂在炉衬表面,凝固使形成耐火度较 高的溅渣层,保护炉衬少被侵蚀。
五、溅渣工艺参数的选择
MgO饱和溶解度受碱度和FeO含量影 响图
当初期渣R=1—2,渣中FeO含量10—40%时, MgO饱和溶解度较高。而且这个时候MgO含量的增 大可将炉渣的熔点急剧下降。因此: 1、初期渣要一次将MgO将入,可以促进化渣。 2、初期渣中碱度低,FeO含量高,MgO饱和溶解 度高,极容易使炉衬中MgO进入渣中。因此多加 MgO有两个重大意义:尽快化渣、提高碱度,和减 缓炉渣对镁碳砖侵蚀的重要措施。而这两个作用是 相互促进或相互恶化的
影响溅渣效果的主要因素有: 1、搅动气体—氮氧的流量 2、枪位 3、留渣量 4、溅渣时机 5、炉渣的成份
枪位对溅渣量的影响
当枪位较低时,各部位溅渣量都较低,当提 高炉位时,溅渣量有所增加。当枪位增加到 一定数值时,溅渣量最大。继续提高枪位, 溅渣量反而下降。这是因为:枪位低时冲击 面积小,供给的能量大部分消耗在穿透和搅 拌渣池。枪位过高时,冲击面积大,射流冲 击强度低,每个渣滴得到能量少。理想的枪 位为0.6—0.7D。
浅谈复吹转炉炉衬寿命与溅渣护炉技术
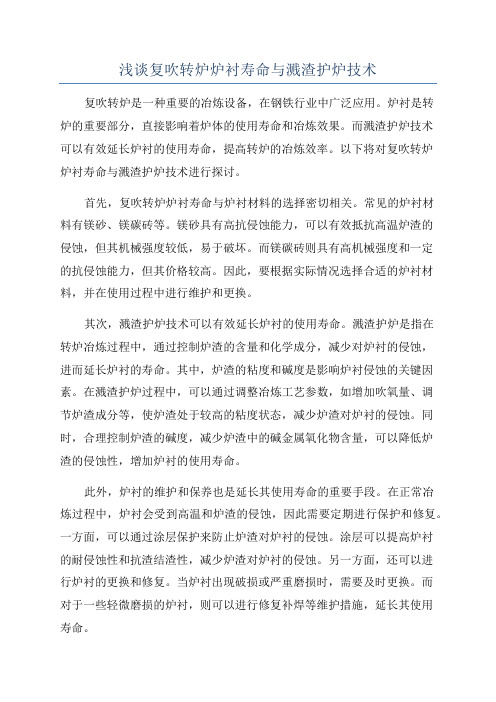
浅谈复吹转炉炉衬寿命与溅渣护炉技术复吹转炉是一种重要的冶炼设备,在钢铁行业中广泛应用。
炉衬是转炉的重要部分,直接影响着炉体的使用寿命和冶炼效果。
而溅渣护炉技术可以有效延长炉衬的使用寿命,提高转炉的冶炼效率。
以下将对复吹转炉炉衬寿命与溅渣护炉技术进行探讨。
首先,复吹转炉炉衬寿命与炉衬材料的选择密切相关。
常见的炉衬材料有镁砂、镁碳砖等。
镁砂具有高抗侵蚀能力,可以有效抵抗高温炉渣的侵蚀,但其机械强度较低,易于破坏。
而镁碳砖则具有高机械强度和一定的抗侵蚀能力,但其价格较高。
因此,要根据实际情况选择合适的炉衬材料,并在使用过程中进行维护和更换。
其次,溅渣护炉技术可以有效延长炉衬的使用寿命。
溅渣护炉是指在转炉冶炼过程中,通过控制炉渣的含量和化学成分,减少对炉衬的侵蚀,进而延长炉衬的寿命。
其中,炉渣的粘度和碱度是影响炉衬侵蚀的关键因素。
在溅渣护炉过程中,可以通过调整冶炼工艺参数,如增加吹氧量、调节炉渣成分等,使炉渣处于较高的粘度状态,减少炉渣对炉衬的侵蚀。
同时,合理控制炉渣的碱度,减少炉渣中的碱金属氧化物含量,可以降低炉渣的侵蚀性,增加炉衬的使用寿命。
此外,炉衬的维护和保养也是延长其使用寿命的重要手段。
在正常冶炼过程中,炉衬会受到高温和炉渣的侵蚀,因此需要定期进行保护和修复。
一方面,可以通过涂层保护来防止炉渣对炉衬的侵蚀。
涂层可以提高炉衬的耐侵蚀性和抗渣结渣性,减少炉渣对炉衬的侵蚀。
另一方面,还可以进行炉衬的更换和修复。
当炉衬出现破损或严重磨损时,需要及时更换。
而对于一些轻微磨损的炉衬,则可以进行修复补焊等维护措施,延长其使用寿命。
综上所述,复吹转炉炉衬寿命与溅渣护炉技术密切相关。
炉衬材料的选择、溅渣护炉技术的应用以及炉衬的维护和修复,都能够对炉衬的寿命起到一定的影响。
因此,在实际生产中,需要根据具体情况采取相应的措施,实现炉衬的最大利用价值,提高转炉的冶炼效果。
溅渣护炉
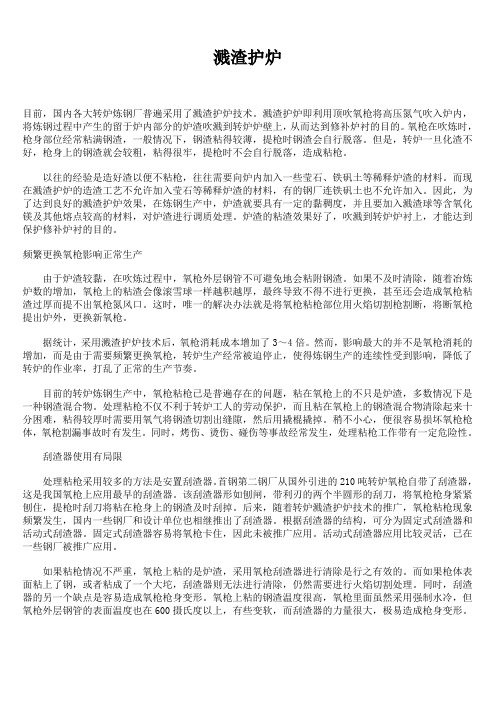
溅渣护炉目前,国内各大转炉炼钢厂普遍采用了溅渣护炉技术。
溅渣护炉即利用顶吹氧枪将高压氮气吹入炉内,将炼钢过程中产生的留于炉内部分的炉渣吹溅到转炉炉壁上,从而达到修补炉衬的目的。
氧枪在吹炼时,枪身部位经常粘满钢渣,一般情况下,钢渣粘得较薄,提枪时钢渣会自行脱落。
但是,转炉一旦化渣不好,枪身上的钢渣就会较粗,粘得很牢,提枪时不会自行脱落,造成粘枪。
以往的经验是造好渣以便不粘枪,往往需要向炉内加入一些莹石、铁矾土等稀释炉渣的材料。
而现在溅渣护炉的造渣工艺不允许加入莹石等稀释炉渣的材料,有的钢厂连铁矾土也不允许加入。
因此,为了达到良好的溅渣护炉效果,在炼钢生产中,炉渣就要具有一定的黏稠度,并且要加入溅渣球等含氧化镁及其他熔点较高的材料,对炉渣进行调质处理。
炉渣的粘渣效果好了,吹溅到转炉炉衬上,才能达到保护修补炉衬的目的。
频繁更换氧枪影响正常生产由于炉渣较黏,在吹炼过程中,氧枪外层钢管不可避免地会粘附钢渣。
如果不及时清除,随着冶炼炉数的增加,氧枪上的粘渣会像滚雪球一样越积越厚,最终导致不得不进行更换,甚至还会造成氧枪粘渣过厚而提不出氧枪氮风口。
这时,唯一的解决办法就是将氧枪粘枪部位用火焰切割枪割断,将断氧枪提出炉外,更换新氧枪。
据统计,采用溅渣护炉技术后,氧枪消耗成本增加了3~4倍。
然而,影响最大的并不是氧枪消耗的增加,而是由于需要频繁更换氧枪,转炉生产经常被迫停止,使得炼钢生产的连续性受到影响,降低了转炉的作业率,打乱了正常的生产节奏。
目前的转炉炼钢生产中,氧枪粘枪已是普遍存在的问题,粘在氧枪上的不只是炉渣,多数情况下是一种钢渣混合物。
处理粘枪不仅不利于转炉工人的劳动保护,而且粘在氧枪上的钢渣混合物清除起来十分困难,粘得较厚时需要用氧气将钢渣切割出缝隙,然后用撬棍撬掉。
稍不小心,便很容易损坏氧枪枪体,氧枪割漏事故时有发生。
同时,烤伤、烫伤、碰伤等事故经常发生,处理粘枪工作带有一定危险性。
刮渣器使用有局限处理粘枪采用较多的方法是安置刮渣器。
转炉溅渣护炉技术

技术特点
1)操作简便 根据炉渣粘稠程度调整成分后, 根据炉渣粘稠程度调整成分后, 利用氧枪和自动控制系统,改供氧气为供氮气, 利用氧枪和自动控制系统,改供氧气为供氮气, 即可降枪进行溅渣操作; 2)成本低 充分利用了转炉高碱度终渣和制 氧厂副产品氮气, 加少量调渣剂( 如菱镁球、 氧厂副产品氮气 , 加少量调渣剂 ( 如菱镁球 、 轻烧白云石等) 就可实现溅渣 , 轻烧白云石等 ) 就可实现溅渣, 还可以降低吨 钢石灰消耗; 3)时间短 一般只需3—4min即可完成溅渣护 一般只需3 min即可完成溅渣护 炉操作, 炉操作,不影响正常生产; 4)溅渣均匀覆盖在整个炉膛内壁上,基本上 4)溅渣均匀覆盖在整个炉膛内壁上,基本上 不改变炉膛形状; 不改变炉膛形状;
基本工艺参数
1)熔池内的合适渣量 1)熔池内的合适渣量 按照溅渣实践,对于出钢量在65—70t的太 按照溅渣实践,对于出钢量在65 70t的太 65— 钢转炉,附着在炉衬上的炉渣重量为2t左右 炉渣重量为2t左右。 钢转炉,附着在炉衬上的炉渣重量为2t左右。 根据冷态试验结果,各种顶吹气体流量条件下, 根据冷态试验结果,各种顶吹气体流量条件下, 均以11 渣量溅渣效果最好。 11% 均以11%渣量溅渣效果最好。图2为溅渣量与 顶枪枪位、气体流量及渣量之间的关系。目前, 顶枪枪位、气体流量及渣量之间的关系。目前, 鞍钢三炼钢厂渣量控制在80--110kg 80--110kg/ 鞍钢三炼钢厂渣量控制在80--110kg/t钢,溅 渣效果良好。 渣效果良好。国内几家钢厂溅渣实践和效果表 渣量在100kg 100kg/ 较为合适。 明,渣量在100kg/t较为合适。
发展概况
进入80年代,转炉普遍采用镁碳砖,综合砌炉, 进入80年代,转炉普遍采用镁碳砖,综合砌炉, 使用活性石灰造渣,改进操作,采用挂渣、喷 补相结合的护炉方法,使转炉炉龄又有明显提 高。 溅渣护炉是近年来开发的一项提高炉龄的新技 术。该技术最先是在美国共和钢公司的大湖分 厂(GreatLakes),由普莱克斯(Praxair)气体 (GreatLakes),由普莱克斯(Praxair)气体 有限公司开发的。 1991年,美国LTV公司的印地安那哈的厂用溅 1991年,美国LTV公司的印地安那哈的厂用溅 渣作为全面护炉的一部分。1994年 渣作为全面护炉的一部分。1994年9月该厂 232t顶吹转炉的炉衬寿命达到15658炉,喷补 232t顶吹转炉的炉衬寿命达到15658炉,喷补 料消耗降到0.38kg/ 钢,喷补料成本节省66 料消耗降到0.38kg/t钢,喷补料成本节省66 %,转炉作业率由1984年的78%提高到1994年 %,转炉作业率由1984年的78%提高到1994年 的97%。 97%。
溅渣护炉技术

溅渣护炉溅渣护炉原理溅渣护炉工艺是把氮气通过氧枪吹入炉膛,高速氮气流股与渣面相遇后把一部分炉渣击碎成尺寸不等的液滴向四周飞溅。
由于流股的能量高,把熔池渣层击穿并形成凹坑,氮气流股遇到炉底后以一定角度形成反射气流,反射气流与渣坑表面的磨擦作用会带起一部分渣滴,使其飞到炉壁上。
通过这样的连续吹氮气,炉渣温度不断下降,渣滴不断黏附在炉衬上,直到溅渣操作结束。
由于炉渣的分熔现象(也叫选择性熔化或异相分流),是指附着于炉衬表面的溅渣层,其矿物组成不均匀,当温度升高时,溅渣层中低熔点物首先熔化,与高熔点相相分离,并缓慢地从溅渣层流淌下来;而残留于炉衬表面的溅渣层为高熔点矿物,反而提高了溅渣层的耐高温性能。
在溅渣层的形成过程中,经过多次“溅渣-熔化-溅渣”的循环和反复使溅渣层表面一些低熔点氧化物发生“分融”现象。
使溅渣层MgO结晶和C2S(2CaO·SiO2)等高熔点矿物逐渐富集,从而提高了溅渣层的抗高温性能,炉衬得到保护。
溅渣层保护炉衬的机理(1)对镁碳砖表面脱碳层的固化作用吹炼过程中镁碳砖表面层碳被氧化,使MgO颗粒失去结合能力,在熔渣和钢液的冲刷下大颗粒MgO松动→脱落→流失,炉衬被蚀损。
溅渣后,熔渣渗入并充填衬砖表面脱碳层的孔隙内,或与周围的MgO颗粒反应,或以镶嵌固溶的方式形成致密的烧结层。
由于烧结层的作用,衬砖表面大颗粒的镁砂不再会松动→脱落→流失,从而防止了炉衬砖的进一步被蚀损。
(2)减轻了熔渣对衬砖表面的直接冲刷蚀损溅渣后在炉衬砖表面形成了以MgO结晶,或C2S和C3S为主体的致密烧结层,这些矿物的熔点明显地高于转炉终点渣,即使在吹炼后期高炉温度下不易软熔,也不易剥落。
因而有效地抵抗高温熔渣的冲刷,大大减轻了对镁碳砖炉衬表面的侵蚀。
(3)抑制了镁碳砖表面的氧化,防止炉村砖体再受到严重的蚀损溅渣后在炉衬砖表面所形成的烧结层和结合层,质地均比炉衬砖脱碳层致密,且熔点高,这就有效地抑制了高温氧化渣,氧化性炉气向砖体内的渗透与扩散,防止镁碳砖体内部碳被进一步氧化,从而起到保护炉衬的作用。
- 1、下载文档前请自行甄别文档内容的完整性,平台不提供额外的编辑、内容补充、找答案等附加服务。
- 2、"仅部分预览"的文档,不可在线预览部分如存在完整性等问题,可反馈申请退款(可完整预览的文档不适用该条件!)。
- 3、如文档侵犯您的权益,请联系客服反馈,我们会尽快为您处理(人工客服工作时间:9:00-18:30)。
转炉溅渣护炉技术的应用方法1.溅渣护炉的基本原理,是在转炉出完钢后加入调渣剂,使其中的Mg与炉渣产生化学反应,生成一系列高熔点物质,被通过氧枪系统喷出的高压氮气喷溅到炉衬的大部分区域或指定区域,粘附于炉衬内壁逐渐冷凝成固态的坚固保护渣层,并成为可消耗的耐材层。
转炉冶炼时,保护层可减轻高温气流及炉渣对炉衬的化学侵蚀和机械冲刷,以维护炉衬、提高炉龄并降低耐材包括喷补料等消耗。
氧气顶吹转炉溅渣护炉是在转炉出钢后将炉体保持直立位置,利用顶吹氧枪向炉内喷射高压氮气(1. 0MPa) ,将炉渣喷溅在炉衬上。
渣粒是以很大冲击力粘附到炉衬上,与炉壁结合的相当牢固,可以有效地阻止炉渣对炉衬的侵蚀。
复吹转炉溅渣护炉是将顶吹和底吹均切换成氮气,从上、下不同方向吹向转炉内炉渣,将炉渣溅起粘结在炉衬上以实现保护炉衬的目的。
溅渣护炉充分利用了转炉终渣并采用氮气作为喷吹动力,在转炉技术上是一个大的进步,它比干法喷补、火焰喷补、人工砌砖等方法更合理,其既能抑制炉衬砖表面的氧化脱碳,又能减轻高温渣对炉砖的侵蚀冲刷,从而保护炉衬砖,降低耐火材料蚀损速度,减少喷补材料消耗,减轻工人劳动强度,提高炉衬使用寿命,提高转炉作业率,减少操作费用,而且不需大量投资,较好地解决了炼钢生产中生产率与生产成本的矛盾。
因此,转炉溅渣护炉技术与复吹炼钢技术被并列为转炉炼钢的2项重大新技术。
2 溅渣护炉主要工艺因素2. 1 合理选择炉渣并进行终渣控制炉渣选择着重是选择合理的渣相熔点。
影响炉渣熔点的物质主要有FeO、MgO和炉渣碱度。
渣相熔点高可提高溅渣层在炉衬的停留时间,提高溅渣效果,减少溅渣频率,实现多炉一溅目标。
由于FeO易与CaO和MnO等形成低熔点物质,并由MgO和FeO的二元系相图可以看出,提高MgO的含量可减少FeO相应产生的低熔点物质数量,有利于炉渣熔点的提高。
从溅渣护炉的角度分析,希望碱度高一点,这样转炉终渣C2 S 及C3 S之和可以达到70%~75%。
这种化合物都是高熔点物质,对于提高溅渣层的耐火度有利。
但是,碱度过高,冶炼过程不易控制,反而影响脱磷和脱硫效果,且造成原材料浪费,还容易造成炉底上涨。
实践证明,终渣碱度控制在2. 8~3. 2为好。
由于溅渣层对转炉初渣具有很强的抗侵蚀能力,而对转炉终渣的高温侵蚀的抵抗能力很差,转炉终渣对溅渣层的侵蚀机理主要表现为高温熔化,因此合理控制转炉终渣,尽可能提高终渣的熔化温度是溅渣护炉的关键环节。
合理控制终渣应着重从终渣的MgO 含量和FeO含量着手。
2. 1. 1 终渣MgO含量的控制在一定条件下提高终渣MgO含量,可进一步提高炉渣的熔化温度,这种高熔点炉渣在冶炼初期产生的溅渣层减轻了渣对炉衬的机械冲刷,并与渣中SiO2 、FeO反应,避免了渣对炉衬的化学侵蚀;在冶炼中期,溅渣层中的MgO与炉渣中的FeO生成高熔点物质,在下一次溅渣操作中成为溅渣层的主要组成部分;同时由于溅渣层被反复利用,减少了炼钢中造渣剂的使用,降低了生产和操作成本。
因此,终渣MgO 含量应在保证出钢温度前提下超过饱和值,但含量也不宜过高,以免增加溅渣护炉成本,一般控制在9%~10%。
调渣剂国外一般在出钢后加入,国内由于转炉操作水平较低,炉况不稳定,终渣成分变化大,且出钢后加入调渣剂化渣不彻底,因此大多数钢厂在冶炼初期便加入化渣剂,以轻烧白云石为主,亦有采用镁质冶金石灰或菱镁矿作为化渣剂的。
2. 1. 2 终渣FeO控制在溅渣护炉技术中,渣中FeO含量的多少起着截然相反的作用:渣中FeO含量高,炉渣的熔点低、流动性好,容易沿衬砖内细小气孔和裂纹渗透和扩散,有利于溅渣层与炉衬砖的结合,保护炉衬不受侵蚀。
但是随着渣中FeO含量增高,由于溅渣层内FeO会与MgO反应使溅渣层中MgO相减少,导致溅渣层熔点降低,不利于溅渣层寿命提高。
国内操作一般控制在20%以下,国外由于调渣剂在出钢后加入,所以FeO含量很高。
一般认为只要在溅渣前把渣中MgO 含量调整在合适的范围内,对终渣氧化铁含量并不须特殊处理,即终渣氧化铁无论高低都可取得较好的溅渣护炉效果。
但如果终渣氧化铁含量很低,渣中铁酸钙少,故应在保证足够的耐火度的情况下,降低渣中MgO含量,这样溅渣护炉的成本较低,容易取得高炉龄。
从操作上讲,在同样温度、碱度和MgO条件下,氧化铁含量低,渣的粘度大,起渣快,可以减少溅渣时间,而不影响溅渣效果。
2. 2 合理控制留渣量在溅渣护炉中,转炉留渣量的多少不仅是溅渣护炉本身重要的工艺参数,而且决定了溅渣层的厚度。
合理的留渣量一方面要保证炉渣在炉衬表面形成10~20mm溅渣层,另一方面随炉内留渣量的增加,炉渣的可溅性增强,对溅渣操作有利。
转炉上部溅渣主要依靠氮气射流对熔池炉渣的溅射而获得。
渣量少,渣层过薄,气流易于穿透渣层,削弱气流对于渣层的乳化和破碎作用,不利于转炉上部溅渣。
转炉留渣量过大,在溶池内易形成浪涌,同样不利于转炉上部溅渣。
即便强化了转炉上部溅渣的效果,也往往造成炉口粘渣变小,影响正常的冶炼操作。
溅渣的厚度:渣量过少,溅渣层过薄,且不均匀,将影响溅渣护炉的效果。
根据钢铁研究总院得出的公式,合理的留渣量为[10,11]:Qs =0. 301Wn式中Qs ———转炉单炉留渣量,t ;W———转炉公称吨位,t ;n———系数,取值为0. 583~0. 650。
2. 3 合理控制出钢温度用溅渣护炉工艺后,转炉出钢温度对炉龄的影响非常明显。
随着出钢温度的降低,炉龄与出钢温度的关系为:N=208529~12019t 。
其中N为炉龄,t为出钢温度。
在同样的溅渣技术条件下,每降低出钢温度一度,将提高炉龄121炉。
因此,合理控制转炉出钢温度,对采用溅渣护炉工艺的转炉进一步提高炉龄有重要意义。
2. 4 枪位控制枪位应按照早化渣,化好渣,保证溅渣厚度和溅渣面积的原则确定。
高枪位易于炉渣的破碎和乳化,有利于转炉上部的溅渣。
当枪位过高时,炉渣溅到炉膛位置较低,还容易冲刷已溅到炉墙上的炉渣,更容易引起炉底上涨。
低枪位易于造成渣液面剧烈波动,对渣的冲击面积小,冲击深度增大,供给的能量大部分消耗于熔池内部, 有利于转炉的下部溅渣,同时由于渣滴能量大,也可溅到炉口。
溅渣时枪位控制要根据炉渣的流动性和所要溅的部位而定。
通常情况采取前高后低方法,既保证了炉渣的形成,溅渣效果也好,且可防止炉底上涨。
转炉溅渣护炉技术的现状目前国外采用溅渣护炉技术的转炉炉龄已平均达到20000炉以上,美国伊斯帕特内陆钢公司转炉的炉龄最高已达36000炉。
国外某些钢厂的管理人员甚至认为30000炉将成为转炉的标准炉龄。
国内冶金工作者在积极摸索适合自身特点的溅渣护炉工艺上取得了巨大进步,开发出了适合不同炉型和工艺条件的溅渣护炉工艺方案。
目前我国复吹转炉的炉龄已超过30000炉[我国由于转炉容量小(以30~50t 为主) 、铁液条件差(硅含量偏高、硫含量波动较大,某些企业还采用中磷铁液或提钒后的半钢炼钢) 、装备水平低(一般无铁液预处理设备、未采用计算机控制等) 、生产节奏快(一般冶炼时间少于30min,生产负荷大)等,使得我国转炉的溅渣护炉具有不同于国外的自身特点。
我国自1996年开展溅渣护炉技术研究以来,迅速开发了适合于中国国情的各种转炉溅渣护炉技术,已使我国转炉的炉龄发生了质的飞跃,与采用溅渣技术前相比,我国转炉龄提高了5~10倍。
目前我国转炉平均炉龄已接近万炉,同时我国在小型转炉、半钢冶炼转炉及复吹转炉领域的溅渣护炉技术,居世界前列,已形成具有中国特色的专利技术。
3. 1 小型转炉溅渣护炉的现状及特点小型转炉在我国已达200座以上,在我国的炼钢生产能力中占较大的比重。
这类转炉铁液及副原料一般质量较差,铁液Si 波动大;生产率高、冶炼周期短,班产炉数高;铁液普遍不进行预处理,转炉冶炼脱硫、脱磷负荷大;无精炼设施,为适应连铸的节奏要求,出钢温度一般高达1700 ℃;由于溅渣频率高,N2 普遍不足。
这些因素使得小型转炉溅渣时间短、炉渣温度高及渣中TFe高。
我国炼钢工作者结合上述国情,开发出了适用于小型转炉的转炉溅渣护炉技术。
(1) 优化炼钢工艺,控制过程温度及终点温度。
优化供氧制度,降低过程枪位,减少渣中TFe。
同时加强管理,保证足够的溅渣频率及溅渣时间。
(2) 注重对终渣的调整。
调渣剂除采用常规轻烧白云石等,普遍采用含碳炉渣改质剂(碳含量一般在15%~40%) ,保证渣中MgO含量超过饱和值,同时调整炉渣粘度和过热度,使之适于炉膛喷溅挂渣,并降低终渣的氧化铁及温度,减少高FeO对溅渣层的侵蚀。
(3) 采用优质材料做转炉绝热层(如采用低绝热系数的多晶纤维板) ,减少炉壳变形。
通过上述转炉溅渣护炉技术及相关技术的开发,我国的小型转炉的炉龄普遍已达10000炉,最高炉龄已超过25000炉。
3. 2 半钢冶炼转炉溅渣护炉的现状及特点我国攀钢和承钢是采用半钢(经提钒后的铁液)冶炼工艺的典型厂家,由于此类铁液含碳低(一般小于3. 5%) 、铁液的含Si 量仅为痕迹(一般小于0. 03%) ,造成炼钢热量不足。
同时由于在造渣过程中,SiO2 、TiO2 等酸性氧化物来源少,致使渣系单一,初渣形成困难,终渣碱度高达6. 5以上,所以炼钢化渣困难。
为了降低炉渣的熔点和粘度,半钢冶炼必须依靠大量生成的FeO溶解石灰,保证脱磷、脱硫效果,故形成了冶金性能不良的铁- 钙渣系,严重影响了溅渣护炉作用的充分发挥。
针对半钢冶炼的特点,开发了如下的溅渣工艺:(1) 选用合适的调渣剂。
由于半钢冶炼碱度很高,对化渣不利,因此有效调整第一批渣料中含SiO2酸性材料的用量,以控制前期炉渣的碱度非常重要。
攀钢半钢冶炼在吹炼前期分别加入轻烧白云石和富锰矿,使炉渣中具有一定量的MgO和MnO含量,以加速初渣的快速形成,同时相应降低了渣中的TFe。
(2) 根据终点[C]和终渣TFe以及出钢温度,合理控制终渣MgO含量。
对于高中碳钢,由于终点[C]较高,TFe较低(8%~14%) ,出钢温度仅为1610~1640 ℃,所以将终渣MgO含量控制在7%~9%就能达到终渣调质的目的。
对于低碳钢,渣中TFe含量为15%~23%,出钢温度高达1 640~1710 ℃,需将MgO含量控制在9%~12%,才能将渣做粘。
(3) 优化冶炼工艺,控制终渣FeO含量。
半钢炼钢由于缺少热量,经常采用后吹来提高钢液温度,终点渣过氧化现象十分严重,TFe高达25%~30%。
采取如下措施降低终渣TFe: ①优化提钒工艺,提高半钢质量,使入转炉的半钢[C] ≥3. 4%,温度≥1280 ℃。
承钢在提钒过程中通过有效控制冷料的加入量,已可将半钢的入炉温度稳定在1350 ℃; ②采用热补措施。
承钢在转炉吹炼前,根据半钢条件,加入类石墨或无烟煤,以增加半钢冶炼时的热收入,取得了很好的效果; ③控制过程的炉渣碱度,避免长时间高枪位操作,渣中的TFe可降低2%~3%。