轴承使用寿命
滚动轴承的寿命计算
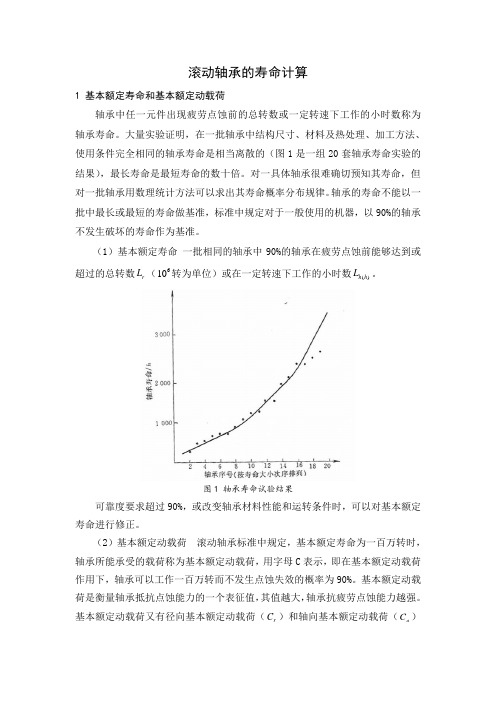
滚动轴承的寿命计算1 基本额定寿命和基本额定动载荷轴承中任一元件出现疲劳点蚀前的总转数或一定转速下工作的小时数称为轴承寿命。
大量实验证明,在一批轴承中结构尺寸、材料及热处理、加工方法、使用条件完全相同的轴承寿命是相当离散的(图1是一组20套轴承寿命实验的结果),最长寿命是最短寿命的数十倍。
对一具体轴承很难确切预知其寿命,但对一批轴承用数理统计方法可以求出其寿命概率分布规律。
轴承的寿命不能以一批中最长或最短的寿命做基准,标准中规定对于一般使用的机器,以90%的轴承不发生破坏的寿命作为基准。
(1)基本额定寿命 一批相同的轴承中90%的轴承在疲劳点蚀前能够达到或超过的总转数r L (610转为单位)或在一定转速下工作的小时数()h h L 。
图1 轴承寿命试验结果可靠度要求超过90%,或改变轴承材料性能和运转条件时,可以对基本额定寿命进行修正。
(2)基本额定动载荷 滚动轴承标准中规定,基本额定寿命为一百万转时,轴承所能承受的载荷称为基本额定动载荷,用字母C 表示,即在基本额定动载荷作用下,轴承可以工作一百万转而不发生点蚀失效的概率为90%。
基本额定动载荷是衡量轴承抵抗点蚀能力的一个表征值,其值越大,轴承抗疲劳点蚀能力越强。
基本额定动载荷又有径向基本额定动载荷(r C )和轴向基本额定动载荷(a C )之分。
径向基本动载荷对向心轴承(角接触轴承除外)是指径向载荷,对角接触轴承指轴承套圈间产生相对径向位移的载荷的径向分量。
对推力轴承指中心轴向载荷。
轴承的基本额定动载荷的大小与轴承的类型、结构、尺寸大小及材料等有关,可以从手册或轴承产品样本中直接查出数值。
2 当量动载荷轴承的基本额定动载荷C (r C 和a C )是在一定条件下确定的。
对同时承受径向载荷和轴向载荷作用的轴承进行寿命计算时,需要把实际载荷折算为与基本额定动载荷条件相一致的一种假想载荷,此假想载荷称为当量动载荷,用字母P 表示。
当量动载荷P 的计算方法如下:同时承受径向载荷r F 和轴向载荷a F 的轴承()P r a P f XF YF =+(1)受纯径向载荷r F 的轴承(如N 、NA 类轴承)P r P f F =(2)受纯轴向载荷a F 的轴承(如5类、8类轴承)P a P f F =(3)式中:X ——径向动载荷系数,查表1; Y ——轴向动载荷系数,查表1; P f 冲击载荷系数,见表2。
滚动轴承寿命计算公式
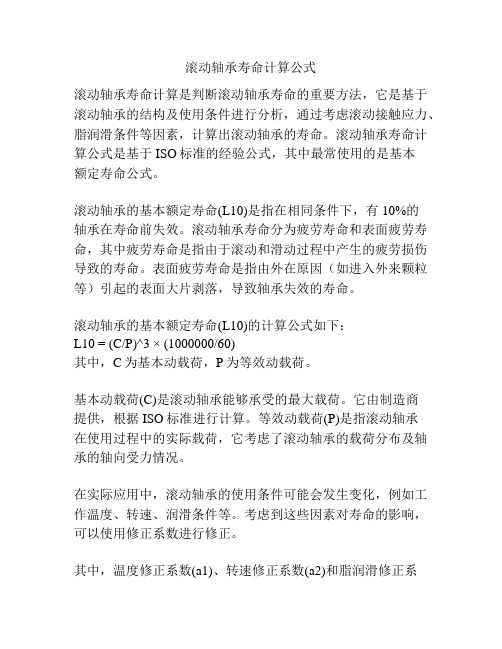
滚动轴承寿命计算公式滚动轴承寿命计算是判断滚动轴承寿命的重要方法,它是基于滚动轴承的结构及使用条件进行分析,通过考虑滚动接触应力、脂润滑条件等因素,计算出滚动轴承的寿命。
滚动轴承寿命计算公式是基于ISO标准的经验公式,其中最常使用的是基本额定寿命公式。
滚动轴承的基本额定寿命(L10)是指在相同条件下,有10%的轴承在寿命前失效。
滚动轴承寿命分为疲劳寿命和表面疲劳寿命,其中疲劳寿命是指由于滚动和滑动过程中产生的疲劳损伤导致的寿命。
表面疲劳寿命是指由外在原因(如进入外来颗粒等)引起的表面大片剥落,导致轴承失效的寿命。
滚动轴承的基本额定寿命(L10)的计算公式如下:L10 = (C/P)^3 × (1000000/60)其中,C为基本动载荷,P为等效动载荷。
基本动载荷(C)是滚动轴承能够承受的最大载荷。
它由制造商提供,根据ISO标准进行计算。
等效动载荷(P)是指滚动轴承在使用过程中的实际载荷,它考虑了滚动轴承的载荷分布及轴承的轴向受力情况。
在实际应用中,滚动轴承的使用条件可能会发生变化,例如工作温度、转速、润滑条件等。
考虑到这些因素对寿命的影响,可以使用修正系数进行修正。
其中,温度修正系数(a1)、转速修正系数(a2)和脂润滑修正系数(a3)是常见的修正系数。
它们表示滚动轴承在不同工况下寿命与基本额定寿命之间的比值。
修正后的寿命(L)可以根据以下公式计算:L = L10 × a1 × a2 × a3同时,还有其他一些公式可以用于计算滚动轴承的寿命,例如基本动载荷的计算公式和等效载荷的计算公式。
这些公式可以根据具体的应用要求和实际情况进行选择和计算。
综上所述,滚动轴承寿命计算公式是根据滚动轴承的结构和使用条件进行分析的重要方法。
通过计算基本额定寿命和修正系数,可以得到滚动轴承的寿命。
计算公式的准确性和合理性对于滚动轴承的设计和选用非常重要,可以提高轴承的使用寿命和可靠性。
带座轴承使用寿命-概述说明以及解释

带座轴承使用寿命-概述说明以及解释1.引言1.1 概述座轴承是一种常用的机械配件,其作用是支撑和转动机械的轴。
座轴承在不同的工业领域广泛应用,例如汽车、机械设备、航空航天等。
它们承载着机械设备的重量,并且根据轴的旋转使整个系统得以顺畅运行。
座轴承的使用寿命是衡量其质量和性能的重要指标。
使用寿命长短直接关系到机械设备的运行效率和稳定性。
如果座轴承使用寿命过短,会导致设备频繁更换和维修,增加了企业的成本和工作量。
因此,延长座轴承的使用寿命对于企业和用户来说都具有重要意义。
本文将重点探讨影响座轴承使用寿命的因素,并提供延长座轴承寿命的方法和建议。
通过深入了解座轴承的定义、作用以及影响其使用寿命的各个因素,我们可以为机械设备的选择、使用和维护提供有益的指导。
最终目的是帮助企业和用户更好地使用座轴承,减少设备故障和维修,提高工作效率,降低成本。
通过对座轴承使用寿命的重要性的总结,以及提出延长其寿命的方法和建议,读者将能够更好地理解座轴承的性能特点,并在实践中获得更好的使用体验。
1.2文章结构文章结构部分的内容可以包括以下几点:1.2 文章结构本文将按照以下结构进行论述:1. 引言:首先对座轴承的使用寿命进行概述,介绍座轴承在机械设备中的作用和重要性。
同时,说明本文旨在探讨影响座轴承使用寿命的因素以及延长座轴承使用寿命的方法和建议。
2. 正文部分:在正文部分,将逐一阐述影响座轴承使用寿命的因素。
这包括但不限于以下几个方面:(在2.2节中详细讨论)2.1.1 座轴承的质量和材料选择座轴承的质量和选材直接影响其使用寿命和性能。
本节将介绍如何选择合适的座轴承材料和制造工艺,以确保其质量可靠和使用寿命可持续。
2.1.2 维护和润滑措施维护和润滑是延长座轴承使用寿命的重要手段。
本节将讨论如何正确进行座轴承的维护和润滑,以减少磨损和摩擦,提高使用寿命。
2.1.3 工作环境和工作条件工作环境和工作条件对座轴承的使用寿命有着重要影响。
滚动轴承寿命计算
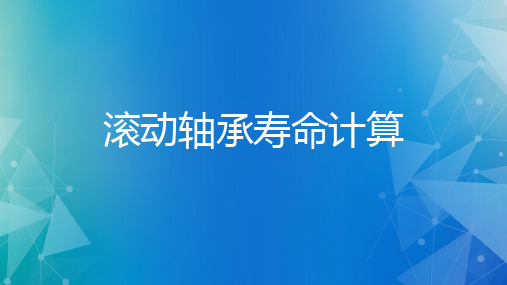
谢谢观看
基本概念
当量动载荷:在进行寿命计算时,需将作用在轴承
上的实际载荷Fr、Fa折算成与上述条件相当的载荷,即当量 动载荷P。
当量静载荷:当量静载荷P0 是指承受最大载荷滚动
体与滚道接触中心处,引起与实际载荷条件下相当的接触应力 时的假想静载荷。
滚动轴承寿命计算
❖ 实际计算轴承寿命时,常用小时作为计算单位。
滚动轴承寿命计算
CONTENTS
1 基本概念
目
2 滚动轴承寿命计算
录
3 角接触轴承的轴向载荷计算 4 滚动轴承的静载荷计算
基本概念
轴承寿命:是指单个轴ຫໍສະໝຸດ (任一滚动体或套圈滚道)出现疲劳点
蚀前转过的总转数,或在一定转速下的工作小时数。
基本额定寿命:是指一批相同的轴承在相同条件下运转,
其中90%的轴承未发生疲劳失效时的总转数或在一定转速下所 能运转的总工作小时数,标准规定用L10或Lh表示基本额定寿 命。
得,方向沿轴线由轴承外圈的宽边指向窄边。(见教材) ❖ 2.角接触轴承轴向力Fa的计算 ❖ 为了使角接触轴承能正常工作,一般这种轴承都要成对使用,并将两个轴承对称
安装。 ❖ 常见有两种安装方式: ❖ 图a,为外圈窄边相对安装,称为正装或面对面安装; ❖ 图b,为两外圈宽边相对安装,称为反装或背靠背安装.
FS2 的大小和方向。 ❖ (2)绘制如上图所示的计算简图。标出上述三个力。 ❖ (3)将轴向外力 FA及与之同向的内部轴向力相加,取其之和与另一反向的内
部轴向力比较大小。
角接触轴承的轴向载荷计算
按下述方法确定各轴承所受的总轴向力:
❖ 若 FS1 +FA ≥FS2 ,根据计算简图,外圈固定不动,轴与固结在一起的内圈有右 移趋势,则轴承2被压紧,轴承1被放松。
轴承标准使用寿命
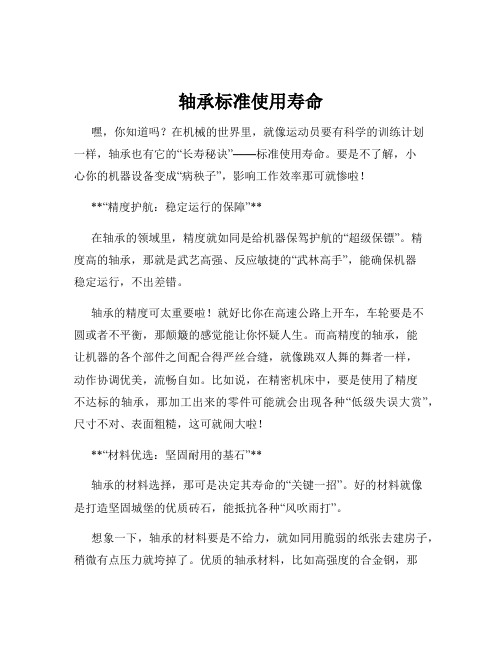
轴承标准使用寿命嘿,你知道吗?在机械的世界里,就像运动员要有科学的训练计划一样,轴承也有它的“长寿秘诀”——标准使用寿命。
要是不了解,小心你的机器设备变成“病秧子”,影响工作效率那可就惨啦!**“精度护航:稳定运行的保障”**在轴承的领域里,精度就如同是给机器保驾护航的“超级保镖”。
精度高的轴承,那就是武艺高强、反应敏捷的“武林高手”,能确保机器稳定运行,不出差错。
轴承的精度可太重要啦!就好比你在高速公路上开车,车轮要是不圆或者不平衡,那颠簸的感觉能让你怀疑人生。
而高精度的轴承,能让机器的各个部件之间配合得严丝合缝,就像跳双人舞的舞者一样,动作协调优美,流畅自如。
比如说,在精密机床中,要是使用了精度不达标的轴承,那加工出来的零件可能就会出现各种“低级失误大赏”,尺寸不对、表面粗糙,这可就闹大啦!**“材料优选:坚固耐用的基石”**轴承的材料选择,那可是决定其寿命的“关键一招”。
好的材料就像是打造坚固城堡的优质砖石,能抵抗各种“风吹雨打”。
想象一下,轴承的材料要是不给力,就如同用脆弱的纸张去建房子,稍微有点压力就垮掉了。
优质的轴承材料,比如高强度的合金钢,那就是坚不可摧的“钢铁侠”,能承受巨大的载荷和高速旋转带来的考验。
像一些重载设备中的轴承,如果材料不过关,用不了多久就会出现磨损、疲劳甚至断裂,这可真是“伤不起”啊!**“润滑呵护:顺滑运行的魔法”**润滑对于轴承来说,那简直是保持顺滑运行的“魔法药水”。
你想想看,要是没有良好的润滑,轴承就像是在沙漠中艰难行走的骆驼,干巴巴地摩擦,很快就会累趴下。
合适的润滑剂就像给轴承做了一场舒适的 SPA,让它们在工作时享受到丝滑的感觉。
比如说,在一些高温、高速的工况下,就得选用耐高温、高性能的润滑剂,不然轴承就会因为摩擦过热而“发脾气”,影响使用寿命。
**“安装正确:完美就位的关键”**安装轴承,这可是个技术活,就像给拼图找到正确的位置一样重要。
要是安装不当,那轴承就像是被放错位置的棋子,怎么也发挥不出应有的作用。
轴承全寿命划分

轴承全寿命划分:
一、额定寿命
额定寿命是指在规定的使用条件下,轴承能够运行的总公里数或转数。
其计算公式为:额定寿命L10=(C/P)^Pp。
其中,C为基本动载荷额定值,P为轴承在使用中的等效载荷系数,p为3,表示所选取的工作寿命约有90%的轴承寿命可达或超过额定寿命。
二、实际寿命
实际寿命是指在实际使用中,轴承能够运行的总公里数或转数。
轴承的实际寿命一般比额定寿命短,从而需要注意维护和保养等方面的问题。
三、极限寿命
极限寿命是指轴承在超过一定的条件下仍然能够运行的寿命。
其计算公式为:极限寿命Lna=a1a2a3...an/换算系数。
其中,a1、a2等为一系列基本的载荷、转速、温度和润滑等条件的修正系数,an为应力因素的修正系数,换算系数与采用的不同单位制有关。
轴承的寿命与计算
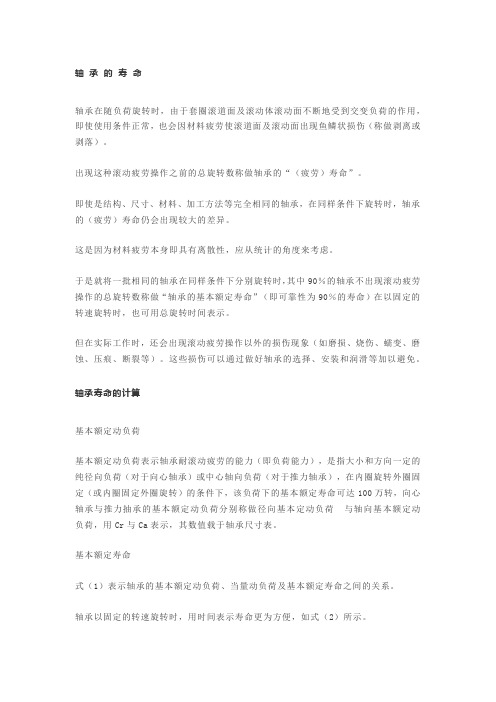
轴承的寿命轴承在随负荷旋转时,由于套圈滚道面及滚动体滚动面不断地受到交变负荷的作用,即使使用条件正常,也会因材料疲劳使滚道面及滚动面出现鱼鳞状损伤(称做剥离或剥落)。
出现这种滚动疲劳操作之前的总旋转数称做轴承的“(疲劳)寿命”。
即使是结构、尺寸、材料、加工方法等完全相同的轴承,在同样条件下旋转时,轴承的(疲劳)寿命仍会出现较大的差异。
这是因为材料疲劳本身即具有离散性,应从统计的角度来考虑。
于是就将一批相同的轴承在同样条件下分别旋转时,其中90%的轴承不出现滚动疲劳操作的总旋转数称做“轴承的基本额定寿命”(即可靠性为90%的寿命)在以固定的转速旋转时,也可用总旋转时间表示。
但在实际工作时,还会出现滚动疲劳操作以外的损伤现象(如磨损、烧伤、蠕变、磨蚀、压痕、断裂等)。
这些损伤可以通过做好轴承的选择、安装和润滑等加以避免。
轴承寿命的计算基本额定动负荷基本额定动负荷表示轴承耐滚动疲劳的能力(即负荷能力),是指大小和方向一定的纯径向负荷(对于向心轴承)或中心轴向负荷(对于推力轴承),在内圈旋转外圈固定(或内圈固定外圈旋转)的条件下,该负荷下的基本额定寿命可达100万转,向心轴承与推力抽承的基本额定动负荷分别称做径向基本定动负荷与轴向基本额定动负荷,用Cr与Ca表示,其数值载于轴承尺寸表。
基本额定寿命式(1)表示轴承的基本额定动负荷、当量动负荷及基本额定寿命之间的关系。
轴承以固定的转速旋转时,用时间表示寿命更为方便,如式(2)所示。
另外,对于铁路车辆或汽车等用行走距离(KM)表示寿命较多,如式(3)所示。
这里:L10:基本额定寿命,106转L10h:基本额定寿命,hL10s:基本额定寿命,kmP:当量动负荷,N{Kgf}厖......参照后面C:基本额定动负荷,N{Kgf}n:转速,rpmp:寿命指数球轴承..........p=3滚子轴承.......p=10/3D:车轮或轮胎直径,mm因此,作为轴承的使用条件,设当量动负荷为P,转速为n,则满足设计寿命所需要的轴承基本额定动负荷C可由式(4)计算,从轴承尺寸表中选出满足C值的轴承,即可确定轴承的尺寸。
轴承寿命计算
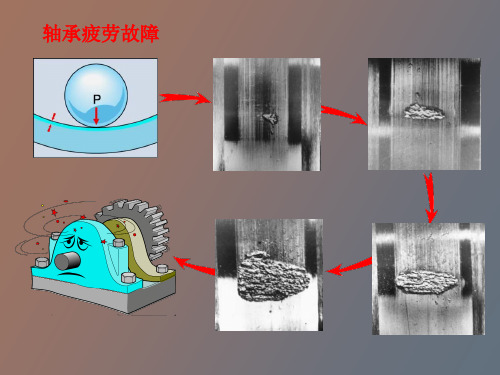
–
6005-Z 6205-Z 6305-Z
6006-Z 6206-Z 6306-Z
6007-Z 6207-Z 6307-Z
6008-Z 6208-Z 6308-Z
6009-Z 6209-Z 6309-Z
6005-2Z 6205-2Z 6305-2Z
6006-2Z 6206-2Z 6306-2Z
6007-2Z 6207-2Z 6307-2Z
速度级别 润滑 润滑脂 润滑油
重量
型号 带有一个 带有两个 防护罩 防护罩
r/min
kg
15 000 12 000 11 000
18 000 15 000 14 000
0,080 0,13 0,23
12 000 15 000 0,12 10 000 13 000 0,20 9 000 11 000 0,35
轴承疲劳故障
轴承寿命的计算准则
对一般工作条件下的回转滚动轴承——经常发生点蚀, 主要进行寿命计算,必要时进行静强度校核;
对于不转动、摆动或转速低(n≦10 r/min)的轴承,要 求控制塑性变形,只需进行静强度计算;
对于高速轴承——由于发热而造成的粘着磨损、烧伤常常 是突出的矛盾,除进行寿命计算外,还需校验极限转速。
10 000 13 000 0,16 9 000 11 000 0,29 8 500 10 000 0.46
9 500 8 500 7 500
12 000 0,19 10 000 0,37 9 000 0,63
9 000 7 500 6 700
11 000 0,25 9 000 0,41 8 000 0,83
45 75 16 85 19 100 25
动态负荷值
轴承使用寿命
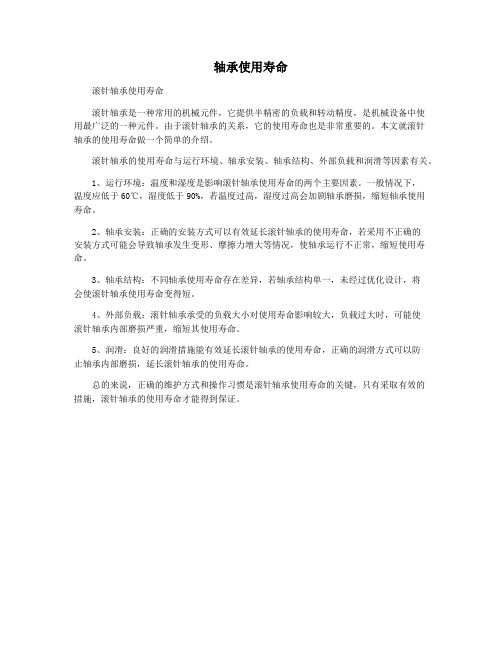
轴承使用寿命
滚针轴承使用寿命
滚针轴承是一种常用的机械元件,它提供半精密的负载和转动精度,是机械设备中使
用最广泛的一种元件。
由于滚针轴承的关系,它的使用寿命也是非常重要的。
本文就滚针
轴承的使用寿命做一个简单的介绍。
滚针轴承的使用寿命与运行环境、轴承安装、轴承结构、外部负载和润滑等因素有关。
1、运行环境:温度和湿度是影响滚针轴承使用寿命的两个主要因素。
一般情况下,
温度应低于60℃,湿度低于90%,若温度过高,湿度过高会加剧轴承磨损,缩短轴承使用
寿命。
2、轴承安装:正确的安装方式可以有效延长滚针轴承的使用寿命,若采用不正确的
安装方式可能会导致轴承发生变形、摩擦力增大等情况,使轴承运行不正常,缩短使用寿命。
3、轴承结构:不同轴承使用寿命存在差异,若轴承结构单一,未经过优化设计,将
会使滚针轴承使用寿命变得短。
4、外部负载:滚针轴承承受的负载大小对使用寿命影响较大,负载过大时,可能使
滚针轴承内部磨损严重,缩短其使用寿命。
5、润滑:良好的润滑措施能有效延长滚针轴承的使用寿命,正确的润滑方式可以防
止轴承内部磨损,延长滚针轴承的使用寿命。
总的来说,正确的维护方式和操作习惯是滚针轴承使用寿命的关键,只有采取有效的
措施,滚针轴承的使用寿命才能得到保证。
轴承寿命
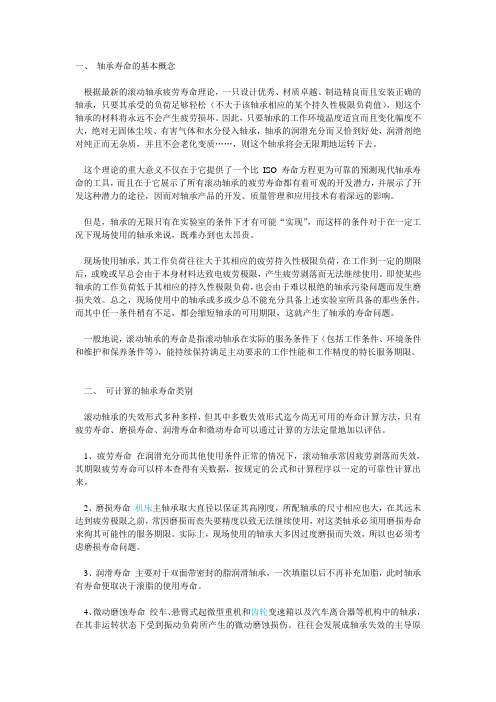
一、轴承寿命的基本概念根据最新的滚动轴承疲劳寿命理论,一只设计优秀、材质卓越、制造精良而且安装正确的轴承,只要其承受的负荷足够轻松(不大于该轴承相应的某个持久性极限负荷值),则这个轴承的材料将永远不会产生疲劳损坏。
因此,只要轴承的工作环境温度适宜而且变化幅度不大,绝对无固体尘埃、有害气体和水分侵入轴承,轴承的润滑充分而又恰到好处,润滑剂绝对纯正而无杂质,并且不会老化变质……,则这个轴承将会无限期地运转下去。
这个理论的重大意义不仅在于它提供了一个比ISO寿命方程更为可靠的预测现代轴承寿命的工具,而且在于它展示了所有滚动轴承的疲劳寿命都有着可观的开发潜力,并展示了开发这种潜力的途径,因而对轴承产品的开发、质量管理和应用技术有着深远的影响。
但是,轴承的无限只有在实验室的条件下才有可能“实现”,而这样的条件对于在一定工况下现场使用的轴承来说,既难办到也太昂贵。
现场使用轴承,其工作负荷往往大于其相应的疲劳持久性极限负荷,在工作到一定的期限后,或晚或早总会由于本身材料达致电疲劳极限,产生疲劳剥落而无法继续使用。
即使某些轴承的工作负荷低于其相应的持久性极限负荷,也会由于难以根绝的轴承污染问题而发生磨损失效。
总之,现场使用中的轴承或多或少总不能充分具备上述实验室所具备的那些条件,而其中任一条件稍有不足,都会缩短轴承的可用期限,这就产生了轴承的寿命问题。
一般地说,滚动轴承的寿命是指滚动轴承在实际的服务条件下(包括工作条件、环境条件和维护和保养条件等),能持续保持满足主动要求的工作性能和工作精度的特长服务期限。
二、可计算的轴承寿命类别滚动轴承的失效形式多种多样,但其中多数失效形式迄今尚无可用的寿命计算方法,只有疲劳寿命、磨损寿命、润滑寿命和微动寿命可以通过计算的方法定量地加以评估。
1、疲劳寿命在润滑充分而其他使用条件正常的情况下,滚动轴承常因疲劳剥落而失效,其期限疲劳寿命可以样本查得有关数据,按规定的公式和计算程序以一定的可靠性计算出来。
轴承的使用寿命
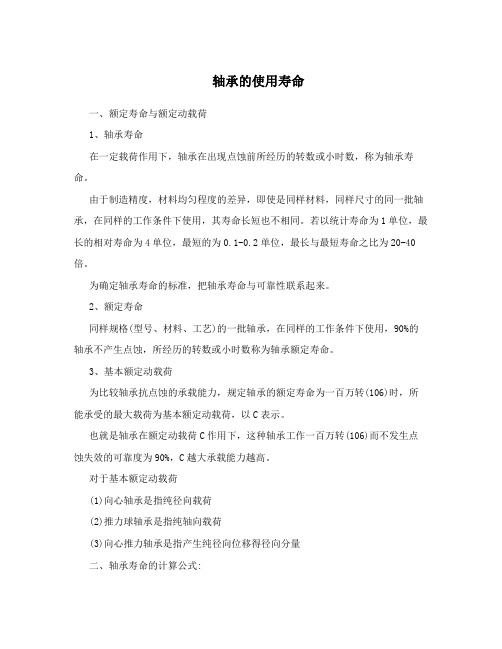
轴承的使用寿命一、额定寿命与额定动载荷1、轴承寿命在一定载荷作用下,轴承在出现点蚀前所经历的转数或小时数,称为轴承寿命。
由于制造精度,材料均匀程度的差异,即使是同样材料,同样尺寸的同一批轴承,在同样的工作条件下使用,其寿命长短也不相同。
若以统计寿命为1单位,最长的相对寿命为4单位,最短的为0.1-0.2单位,最长与最短寿命之比为20-40倍。
为确定轴承寿命的标准,把轴承寿命与可靠性联系起来。
2、额定寿命同样规格(型号、材料、工艺)的一批轴承,在同样的工作条件下使用,90%的轴承不产生点蚀,所经历的转数或小时数称为轴承额定寿命。
3、基本额定动载荷为比较轴承抗点蚀的承载能力,规定轴承的额定寿命为一百万转(106)时,所能承受的最大载荷为基本额定动载荷,以C表示。
也就是轴承在额定动载荷C作用下,这种轴承工作一百万转(106)而不发生点蚀失效的可靠度为90%,C越大承载能力越高。
对于基本额定动载荷(1)向心轴承是指纯径向载荷(2)推力球轴承是指纯轴向载荷(3)向心推力轴承是指产生纯径向位移得径向分量二、轴承寿命的计算公式:洛阳轴承厂以208轴承为对象,进行大量的试验研究,建立了载荷与寿命的数字关系式和曲线。
式中:L10--轴承载荷为P时,所具有的基本额定寿命(106转)C--基本额定动载荷 Nε--指数对球轴承:ε=3对滚子轴承:ε=10/3P--当量动载荷(N)把在实际条件下轴承上所承受的载荷: A、R ,转化为实验条件下的载荷称为当量动载荷,对轴承元件来讲这个载荷是变动的,实验研究时,轴承寿命用106转为单位比较方便(记数器),但在实际生产中一般寿命用小时表示,为此须进行转换L10×106=Lh×60n所以滚动轴承寿命计算分为:1、已知轴承型号、载荷与轴的转速,计算Lh;2、已知载荷、转速与预期寿命,计算C ,选取轴承型号。
通常取机器的中修或大修界限为轴承的设计寿命,一般取Lh'=5000,对于高温下工作的轴承应引入温度系数ftCt=ftCt ?120 125 150 200 300ft 1 0.95 0.90 0.80 0.60上两式变为:对于向心轴承对于推力轴承三、当量动载荷P的计算在实际生产中轴承的工作条件是多种多样的,为此,要把实际工作条件下的载荷折算为假想寿命相同的实验载荷--当量载荷。
轴承设计寿命计算公式汇总
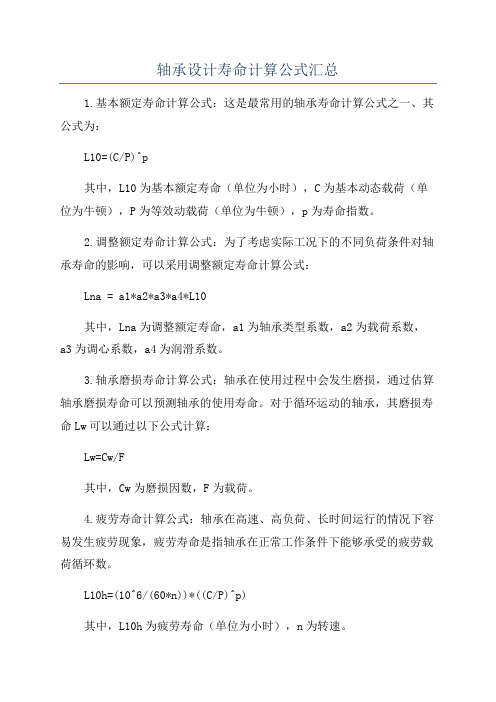
轴承设计寿命计算公式汇总
1.基本额定寿命计算公式:这是最常用的轴承寿命计算公式之一、其公式为:
L10=(C/P)^p
其中,L10为基本额定寿命(单位为小时),C为基本动态载荷(单位为牛顿),P为等效动载荷(单位为牛顿),p为寿命指数。
2.调整额定寿命计算公式:为了考虑实际工况下的不同负荷条件对轴承寿命的影响,可以采用调整额定寿命计算公式:
Lna = a1*a2*a3*a4*L10
其中,Lna为调整额定寿命,a1为轴承类型系数,a2为载荷系数,a3为调心系数,a4为润滑系数。
3.轴承磨损寿命计算公式:轴承在使用过程中会发生磨损,通过估算轴承磨损寿命可以预测轴承的使用寿命。
对于循环运动的轴承,其磨损寿命Lw可以通过以下公式计算:
Lw=Cw/F
其中,Cw为磨损因数,F为载荷。
4.疲劳寿命计算公式:轴承在高速、高负荷、长时间运行的情况下容易发生疲劳现象,疲劳寿命是指轴承在正常工作条件下能够承受的疲劳载荷循环数。
L10h=(10^6/(60*n))*((C/P)^p)
其中,L10h为疲劳寿命(单位为小时),n为转速。
5.温度因子计算公式:轴承在工作时会产生热量,可以通过计算温度因子来估算轴承的使用寿命。
温度因子aISO可以通过以下公式计算:aISO=a*〖10(ΔT/10)〗^b
其中,a、b为轴承类型参数,ΔT为温度变化。
以上是一些常用的轴承设计寿命计算公式汇总。
需要注意的是,不同类型的轴承有不同的设计寿命计算公式,具体应根据实际情况选择合适的计算方法。
此外,在进行寿命计算时还需要考虑轴承材料、润滑方式、工作温度等因素对轴承寿命的影响。
机械工程中轴承的寿命预测与可靠性分析

机械工程中轴承的寿命预测与可靠性分析轴承作为机械设备中的重要零部件,在机械工程中具有至关重要的作用。
然而,长期以来,轴承的可靠性一直是机械工程师们关注的焦点。
轴承的失效对机械设备的正常运行造成严重的影响,因此,对轴承使用寿命进行准确的预测和可靠性的分析显得尤为重要。
一、轴承的使用寿命预测轴承的使用寿命是指在一定条件下,轴承失效前可以正常工作的时间。
准确预测轴承的使用寿命有助于合理安排维护和更换计划,避免因轴承失效而导致的生产中断和不必要的经济损失。
使用寿命的预测通常采用经验公式和理论分析方法两种途径。
其中,经验公式是根据大量实验数据总结得出的,简单易用。
理论分析方法则是基于轴承使用寿命与载荷、转速、工作条件等相关因素的数学模型建立,更加准确。
但是,由于机械设备在不同工况下的复杂性,使用寿命预测并非一件容易的事情。
因此,结合经验公式和理论分析方法,综合考虑各种因素,才能得出更准确的预测结果。
二、轴承的可靠性分析可靠性是指在一定时间内正常工作的概率,是对轴承工作质量的度量。
轴承的可靠性分析可以帮助工程师评估轴承的可靠性指标,为轴承的设计和维护提供依据。
可靠性分析的方法有很多,常见的有故障模式及影响分析(Failure Mode and Effect Analysis, FMEA)和可靠性块图法(Reliability Block Diagram, RBD)等。
FMEA方法通过分析轴承可能的故障模式和对机械设备的影响程度来评估轴承的可靠性。
而RBD方法则通过将机械系统分解为可靠性块,综合考虑各个部件的故障概率,来计算系统的可靠性。
除了故障模式及影响分析和可靠性块图法,还有一些其他方法可以用于轴承的可靠性分析,比如故障树分析(Fault Tree Analysis, FTA)和可靠度重要性分析(Importance Measure, IM)等。
这些分析方法用于确定轴承在整个系统中的重要程度以及可能导致故障的原因,为提高轴承的可靠性提供了有益的参考。
滚动轴承寿命计算公式

滚动轴承寿命计算公式滚动轴承是一种常见的机械元件,用于支撑和定位机器中旋转部件。
由于滚动轴承在机械运动中承受很大的力和磨损,因此其寿命是一个重要的参数。
滚动轴承的寿命计算公式是根据轴承的工作条件来确定的。
下面将详细介绍滚动轴承寿命计算的相关参考内容。
滚动轴承的寿命可以用基本额定寿命和调整因素来计算。
基本额定寿命是指在给定的负载条件下,轴承经过100万转(或行走一定的距离)后的寿命。
调整因素是考虑到轴承在实际工作条件下可能受到的额外影响。
滚动轴承的基本额定寿命可以由以下的一般计算公式得出:L10h = (C/P)^p其中,L10h是基本额定寿命,单位是小时;C 是基本动载荷额定值,单位是N;P 是相对磨损参数,通常取为3;p 是磨损指数,取决于轴承类型和使用条件。
磨损指数p的取值范围通常为3-10,具体数值需要根据具体的轴承类型和使用条件进行确定。
不同类型的轴承有不同的磨损指数。
滚动轴承的调整因素主要包括以下几个方面:1.负载系数(fT):通过考虑工作条件下的轴承负载大小和方向,计算负载系数。
一般情况下,负载系数在1以下。
2.可靠性调整因素(a1、a2、a3):根据滚动轴承的可靠性要求,计算可靠性调整因素。
这些因素通常是根据统计数据和经验值得出的。
3.寿命调整因素(aISO、aSKF):在计算基本额定寿命的基础上,根据轴承的使用条件和特殊要求进行修正。
4. 温度调整因素(aT):考虑轴承运行温度的影响,计算温度调整因素。
以上的调整因素可以通过一定的计算公式得出,具体的计算方法可以参考相关滚动轴承的手册、标准或经验数据。
除了上述计算寿命的方法外,还可以通过实际运行数据进行判断和预测轴承寿命。
例如,通过监测轴承的振动、温度等参数,结合历史数据和经验,可以进行寿命预测和故障诊断。
总结起来,滚动轴承寿命的计算公式包括基本额定寿命的公式和各种调整因素的计算。
这些公式和因素的取值需要根据具体的轴承类型和使用条件来确定。
电机 轴承 寿命 2800
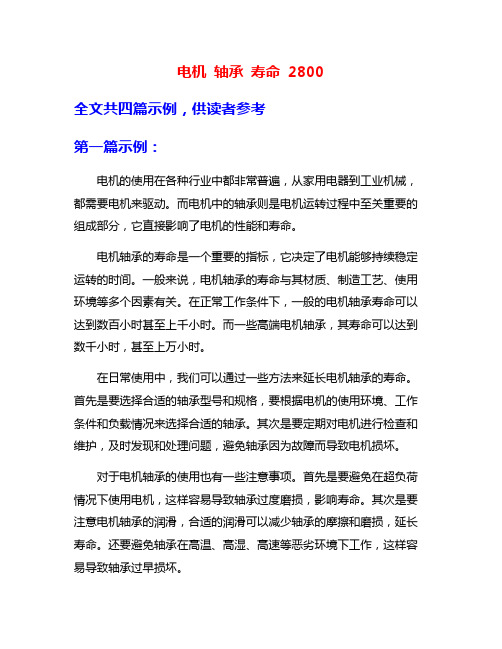
电机轴承寿命2800全文共四篇示例,供读者参考第一篇示例:电机的使用在各种行业中都非常普遍,从家用电器到工业机械,都需要电机来驱动。
而电机中的轴承则是电机运转过程中至关重要的组成部分,它直接影响了电机的性能和寿命。
电机轴承的寿命是一个重要的指标,它决定了电机能够持续稳定运转的时间。
一般来说,电机轴承的寿命与其材质、制造工艺、使用环境等多个因素有关。
在正常工作条件下,一般的电机轴承寿命可以达到数百小时甚至上千小时。
而一些高端电机轴承,其寿命可以达到数千小时,甚至上万小时。
在日常使用中,我们可以通过一些方法来延长电机轴承的寿命。
首先是要选择合适的轴承型号和规格,要根据电机的使用环境、工作条件和负载情况来选择合适的轴承。
其次是要定期对电机进行检查和维护,及时发现和处理问题,避免轴承因为故障而导致电机损坏。
对于电机轴承的使用也有一些注意事项。
首先是要避免在超负荷情况下使用电机,这样容易导致轴承过度磨损,影响寿命。
其次是要注意电机轴承的润滑,合适的润滑可以减少轴承的摩擦和磨损,延长寿命。
还要避免轴承在高温、高湿、高速等恶劣环境下工作,这样容易导致轴承过早损坏。
对于电机轴承寿命2800小时的电机来说,这已经是一个比较理想的寿命。
但是在实际使用中,我们还是要注意对电机的维护和保养,以确保其能够稳定运转并延长寿命。
只有在做好这些方面的工作后,我们才能充分发挥电机的性能,提高工作效率,降低维护成本。
电机轴承的寿命是一个重要的指标,它直接关系到电机的运转稳定性和使用寿命。
通过选择合适的轴承型号和规格、定期检查和维护、注意使用注意事项等措施,我们可以有效延长电机轴承的寿命,提高电机的性能,降低维护成本,从而实现更好的效果。
【2000字】第二篇示例:电机是一种常见的机电设备,在各种工业生产中都有广泛的应用。
而轴承则是电机中非常重要的一个部件,它承载着电机的旋转部分,并保证其正常运转。
轴承的寿命是电机运行稳定性和使用寿命的重要指标之一。
滚动轴承寿命计算公式
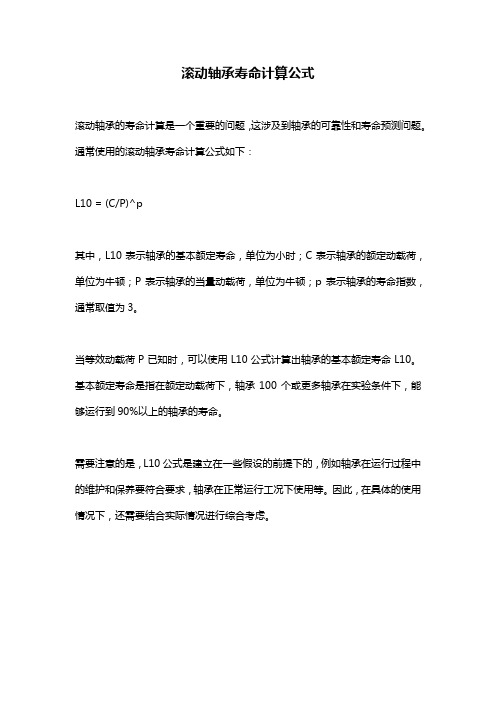
滚动轴承寿命计算公式
滚动轴承的寿命计算是一个重要的问题,这涉及到轴承的可靠性和寿命预测问题。
通常使用的滚动轴承寿命计算公式如下:
L10 = (C/P)^p
其中,L10表示轴承的基本额定寿命,单位为小时;C表示轴承的额定动载荷,单位为牛顿;P表示轴承的当量动载荷,单位为牛顿;p表示轴承的寿命指数,通常取值为3。
当等效动载荷P已知时,可以使用L10公式计算出轴承的基本额定寿命L10。
基本额定寿命是指在额定动载荷下,轴承100个或更多轴承在实验条件下,能够运行到90%以上的轴承的寿命。
需要注意的是,L10公式是建立在一些假设的前提下的,例如轴承在运行过程中的维护和保养要符合要求,轴承在正常运行工况下使用等。
因此,在具体的使用情况下,还需要结合实际情况进行综合考虑。
电机轴承采用标准
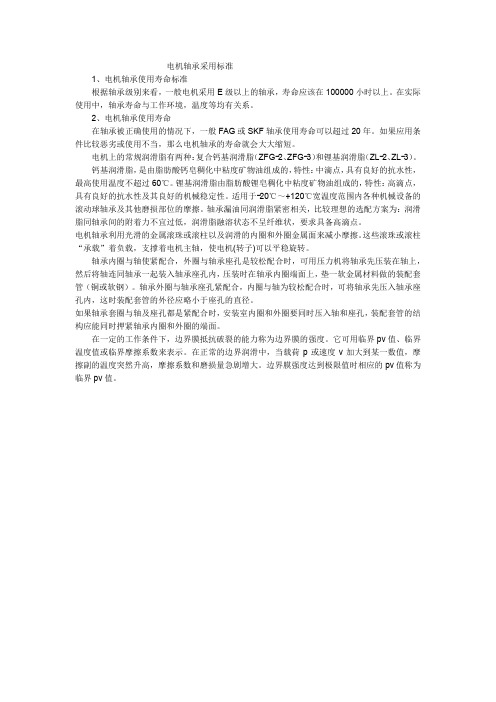
电机轴承采用标准1、电机轴承使用寿命标准根据轴承级别来看,一般电机采用E级以上的轴承,寿命应该在100000小时以上。
在实际使用中,轴承寿命与工作环境,温度等均有关系。
2、电机轴承使用寿命在轴承被正确使用的情况下,一般FAG或SKF轴承使用寿命可以超过20年。
如果应用条件比较恶劣或使用不当,那么电机轴承的寿命就会大大缩短。
电机上的常规润滑脂有两种:复合钙基润滑脂(ZFG-2、ZFG-3)和锂基润滑脂(ZL-2、ZL-3)。
钙基润滑脂,是由脂肪酸钙皂稠化中粘度矿物油组成的,特性:中滴点,具有良好的抗水性,最高使用温度不超过60℃。
锂基润滑脂由脂肪酸锂皂稠化中粘度矿物油组成的,特性:高滴点,具有良好的抗水性及其良好的机械稳定性。
适用于-20℃~+120℃宽温度范围内各种机械设备的滚动球轴承及其他磨损部位的摩擦。
轴承漏油同润滑脂紧密相关,比较理想的选配方案为:润滑脂同轴承间的附着力不宜过低,润滑脂融溶状态不呈纤维状,要求具备高滴点。
电机轴承利用光滑的金属滚珠或滚柱以及润滑的内圈和外圈金属面来减小摩擦。
这些滚珠或滚柱“承载”着负载,支撑着电机主轴,使电机(转子)可以平稳旋转。
轴承内圈与轴使紧配合,外圈与轴承座孔是较松配合时,可用压力机将轴承先压装在轴上,然后将轴连同轴承一起装入轴承座孔内,压装时在轴承内圈端面上,垫一软金属材料做的装配套管(铜或软钢)。
轴承外圈与轴承座孔紧配合,内圈与轴为较松配合时,可将轴承先压入轴承座孔内,这时装配套管的外径应略小于座孔的直径。
如果轴承套圈与轴及座孔都是紧配合时,安装室内圈和外圈要同时压入轴和座孔,装配套管的结构应能同时押紧轴承内圈和外圈的端面。
在一定的工作条件下,边界膜抵抗破裂的能力称为边界膜的强度。
它可用临界pv值、临界温度值或临界摩擦系数来表示。
在正常的边界润滑中,当载荷p或速度v加大到某一数值,摩擦副的温度突然升高,摩擦系数和磨损量急剧增大。
边界膜强度达到极限值时相应的pv值称为临界pv值。
SKF轴承机械使用的寿命表

SKF轴承机械使用的寿命表
该表格为正常安装后的SKF轴承使用寿命估算值,不受型号限制,但受到安装及工作环境限制。
1、机械类型:家用电器,农业机械,医疗设备,仪器设备约定;工作时间:300-3000
2、机械类型:短时间间接性的使用,电动工具,车间起重设备,建筑设备和机械约定;工作时间:3000-8000
3、机械类型:短时间或间歇性使用的设备,但要求较高的运行可靠性,例如升降机(电梯)用于包装货物的起重机械或吊索轮约定;工作时间:8000-12000
4、机械类型:每天工作8小时,但并非全部时间运行的机械,一般使用齿轮传动结构,例如工业电机,转盘式碎石机约定;工作时间:10000-250000
5、机械类型:每天工作8小时,但并非全部时间运行的机械,例如机床,木材机械,连续生产的机械,例如起重机械,通风设备,输送机,印刷设备,分离机,离心机等约定;工作时间:20000-30000
6、机械类型:24小时运转的机械,轧钢厂用的齿轮,中型电机,压缩机,采矿用起重机,泵或纺织机械;工作时间:40000-50000
7、机械类型:风电机械设备,包括主轴,摆动机构,齿轮箱,发电机轴承;工作时间:30000-100000
8、机械类型:自来水厂用的机械,如转炉,电缆搅股架等;工作时间:60000-100000
9、机械类型:大型电机,发电厂设备,矿井水泵,矿场用通风设备,远洋轮的主轴轴承;工作时间:>100000。
轴承寿命标准

轴承寿命标准轴承是机械设备中常见的零部件,其寿命直接影响到设备的运行稳定性和使用寿命。
轴承寿命标准是指在一定的工作条件下,轴承在规定的寿命期内能够保持正常运转的能力。
轴承的寿命标准不仅关乎设备的正常运行,也关系到设备的安全性和经济性。
因此,制定和遵守轴承寿命标准对于保障设备的正常运行和延长设备的使用寿命具有重要意义。
轴承寿命标准的制定是基于轴承的设计、制造和使用经验以及相关的科学理论和技术规范。
在实际应用中,轴承寿命标准的制定需要考虑到轴承的使用环境、负荷、转速、润滑、材料等因素。
一般来说,轴承寿命标准是通过寿命试验和统计分析得出的,以确保轴承在规定的寿命期内能够正常运行。
轴承寿命标准通常采用寿命L10来表示,即在一定的负荷、转速和润滑条件下,有百分之九十的轴承能够达到或超过规定的寿命。
L10寿命是指在相同条件下,有百分之九十的轴承能够正常运行的寿命,而有百分之十的轴承可能无法达到规定的寿命。
因此,制定轴承寿命标准时需要考虑到这一因素,以确保大多数轴承能够正常运行并且尽可能延长轴承的使用寿命。
轴承寿命标准的制定需要考虑到轴承的工作环境和使用条件。
在不同的工作条件下,轴承的寿命可能会有所不同。
例如,在高速旋转和高温环境下,轴承的寿命可能会受到影响,因此需要制定相应的寿命标准。
另外,不同类型和规格的轴承也会有不同的寿命标准,需要根据具体情况来制定。
为了保证轴承能够达到规定的寿命,需要在设计、制造、安装和维护过程中严格遵守轴承寿命标准。
在轴承的选型和设计过程中,需要考虑到轴承的寿命标准,选择合适的轴承类型和规格。
在轴承的制造和安装过程中,需要严格按照相关的技术规范和操作规程进行,确保轴承能够正常运行。
在轴承的维护和保养过程中,需要定期检查和更换轴承,以延长轴承的使用寿命。
总之,轴承寿命标准是保障设备正常运行和延长设备使用寿命的重要依据。
制定和遵守轴承寿命标准对于提高设备的可靠性和安全性具有重要意义,需要在设计、制造、安装和维护过程中严格遵守相关的技术规范和操作规程,以确保轴承能够达到规定的寿命,并且延长设备的使用寿命。
- 1、下载文档前请自行甄别文档内容的完整性,平台不提供额外的编辑、内容补充、找答案等附加服务。
- 2、"仅部分预览"的文档,不可在线预览部分如存在完整性等问题,可反馈申请退款(可完整预览的文档不适用该条件!)。
- 3、如文档侵犯您的权益,请联系客服反馈,我们会尽快为您处理(人工客服工作时间:9:00-18:30)。
轴承使用寿命摘要:自然界苛刻的工作条件会导致轴承的失效,但是如果遵循一些简单的规则,轴承正常运转的机会是能够被提高的。
在轴承的使用过程当中,过分的忽视会导致轴承的过热现象,也可能使轴承不能够再被使用,甚至完全的破坏。
但是一个被损坏的轴承,会留下它为什么被损坏的线索。
通过一些细致的侦察工作,我们可以采取行动来避免轴承的再次失效。
关键词:轴承失效寿命导致轴承失效的原因很多,但常见的是不正确的使用、污染、润滑剂使用不当、装卸或搬运时的损伤及安装误差等。
诊断失效的原因并不困难,因为根据轴承上留下的痕迹可以确定轴承失效的原因。
然而,当事后的调查分析提供出宝贵的信息时,最好首先通过正确地选定轴承来完全避免失效的发生。
为了做到这一点,再考察一下制造厂商的尺寸定位指南和所选轴承的使用特点是非常重要的。
1 轴承失效的原因在球轴承的失效中约有40%是由灰尘、脏物、碎屑的污染以及腐蚀造成的。
污染通常是由不正确的使用和不良的使用环境造成的,它还会引起扭矩和噪声的问题。
由环境和污染所产生的轴承失效是可以预防的,而且通过简单的肉眼观察是可以确定产生这类失效的原因。
通过失效后的分析可以得知对已经失效的或将要失效的轴承应该在哪些方面进行查看。
弄清诸如剥蚀和疲劳破坏一类失效的机理,有助于消除问题的根源。
只要使用和安装合理,轴承的剥蚀是容易避免的。
剥蚀的特征是在轴承圈滚道上留有由冲击载荷或不正确的安装产生的压痕。
剥蚀通常是在载荷超过材料屈服极限时发生的。
如果安装不正确从而使某一载荷横穿轴承圈也会产生剥蚀。
轴承圈上的压坑还会产生噪声、振动和附加扭矩。
类似的一种缺陷是当轴承不旋转时由于滚珠在轴承圈间振动而产生的椭圆形压痕。
这种破坏称为低荷振蚀。
这种破坏在运输中的设备和不工作时仍振动的设备中都会产生。
此外,低荷振蚀产生的碎屑的作用就象磨粒一样,会进一步损害轴承。
与剥蚀不同,低荷振蚀的特征通常是由于微振磨损腐蚀在润滑剂中会产生淡红色。
消除振动源并保持良好的轴承润滑可以防止低荷振蚀。
给设备加隔离垫或对底座进行隔离可以减轻环境的振动。
另外在轴承上加一个较小的预载荷不仅有助于滚珠和轴承圈保持紧密的接触,并且对防止在设备运输中产生的低荷振蚀也有帮助。
造成轴承卡住的原因是缺少内隙、润滑不当和载荷过大。
在卡住之前,过大的摩擦和热量使轴承钢软化。
过热的轴承通常会改变颜色,一般会变成蓝黑色或淡黄色。
摩擦还会使保持架受力,这会破坏支承架,并加速轴承的失效。
材料过早出现疲劳破坏是由重载后过大的预载引起的。
如果这些条件不可避免,就应仔细计算轴承寿命,以制定一个维护计划。
另一个解决办法是更换材料。
若标准的轴承材料不能保证足够的轴承寿命,就应当采用特殊的材料。
另外,如果这个问题是由于载荷过大造成的,就应该采用抗载能力更强或其他结构的轴承。
蠕动不象过早疲劳那样普遍。
轴承的蠕动是由于轴和内圈之间的间隙过大造成的。
蠕动的害处很大,它不仅损害轴承,也破坏其他零件。
蠕动的明显特征是划痕、擦痕或轴与内圈的颜色变化。
为了防止蠕动,应该先用肉眼检查一下轴承箱件和轴的配件。
蠕动与安装不正有关。
如果轴承圈不正或翘起,滚珠将沿着一个非圆周轨道运动。
这个问题是由于安装不正确或公差不正确或轴承安装现场的垂直度不够造成的。
如果偏斜超过0.25°,轴承就会过早地失效。
检查润滑剂的污染比检查装配不正或蠕动要困难得多。
污染的特征是使轴承过早的出现磨损。
润滑剂中的固体杂质就象磨粒一样。
如果滚珠和保持架之间润滑不良也会磨损并削弱保持架。
在这种情况下,润滑对于完全加工形式的保持架来说是至关重要的。
相比之下,带状或冠状保持架能较容易地使润滑剂到达全部表面。
锈是湿气污染的一种形式,它的出现常常表明材料选择不当。
如果某一材料经检验适合工作要求,那么防止生锈的最简单的方法是给轴承包装起来,直到安装使用时才打开包装。
2 避免失效的方法解决轴承失效问题的最好办法就是避免失效发生。
这可以在选用过程中通过考虑关键性能特征来实现。
这些特征包括噪声、起动和运转扭矩、刚性、非重复性振摆以及径向和轴向间隙。
扭矩要求是由润滑剂、保持架、轴承圈质量(弯曲部分的圆度和表面加工质量)以及是否使用密封或遮护装置来决定。
润滑剂的粘度必须认真加以选择,因为不适宜的润滑剂会产生过大的扭矩,这在小型轴承中尤其如此。
另外,不同的润滑剂的噪声特性也不一样。
举例来说,润滑脂产生的噪声比润滑油大一些。
因此,要根据不同的用途来选用润滑剂。
在轴承转动过程中,如果内圈和外圈之间存在一个随机的偏心距,就会产生与凸轮运动非常相似的非重复性振摆(NRR)。
保持架的尺寸误差和轴承圈与滚珠的偏心都会引起NRR。
和重复性振摆不同的是,NRR是没有办法进行补偿的。
在工业中一般是根据具体的应用来选择不同类型和精度等级的轴承。
例如,当要求振摆最小时,轴承的非重复性振摆不能超过0.3微米。
同样,机床主轴只能容许最小的振摆,以保证切削精度。
因此在机床的应用中应该使用非重复性振摆较小的轴承。
在许多工业产品中,污染是不可避免的,因此常用密封或遮护装置来保护轴承,使其免受灰尘或脏物的侵蚀。
但是,由于轴承内外圈的运动,使轴承的密封不可能达到完美的程度,因此润滑油的泄漏和污染始终是一个未能解决的问题。
一旦轴承受到污染,润滑剂就要变质,运行噪声也随之变大。
如果轴承过热,它将会卡住。
当污染物处于滚珠和轴承圈之间时,其作用和金属表面之间的磨粒一样,会使轴承磨损。
采用密封和遮护装置来挡开脏物是控制污染的一种方法。
噪声是反映轴承质量的一个指标。
轴承的性能可以用不同的噪声等级来表示。
噪声的分析是用安德逊计进行的,该仪器在轴承生产中可用来控制质量,也可对失效的轴承进行分析。
将一传感器连接在轴承外圈上,而内圈在心轴以1800r/min的转速旋转。
测量噪声的单位为anderon。
即用um/rad表示的轴承位移。
根据经验,观察者可以根据声音辨别出微小的缺陷。
例如,灰尘产生的是不规则的劈啪声;滚珠划痕产生一种连续的爆破声,确定这种划痕最困难;内圈损伤通常产生连续的高频噪声,而外圈损伤则产生一种间歇的声音。
轴承缺陷可以通过其频率特性进一步加以鉴定。
通常轴承缺陷被分为低、中、高三个波段。
缺陷还可以根据轴承每转动一周出现的不规则变化的次数加以鉴定。
低频噪声是长波段不规则变化的结果。
轴承每转一周这种不规则变化可出现1.6~10次,它们是由各种干涉(例如轴承圈滚道上的凹坑)引起的。
可察觉的凹坑是一种制造缺陷,它是在制造过程中由于多爪卡盘夹的太紧而形成的。
中频噪声的特征是轴承每旋转一周不规则变化出现10~60次。
这种缺陷是由在轴承圈和滚珠的磨削加工中出现的振动引起的。
轴承每旋转一周高频不规则变化出现60~300次,它表明轴承上存在着密集的振痕或大面积的粗糙不平。
利用轴承的噪声特性对轴承进行分类,用户除了可以确定大多数厂商所使用的ABEC标准外,还可确定轴承的噪声等级。
ABEC标准只定义了诸如孔、外径、振摆等尺寸公差。
随着ABEC级别的增加(从3增到9),公差逐渐变小。
但ABEC等级并不能反映其他轴承特性,如轴承圈质量、粗糙度、噪声等。
因此,噪声等级的划分有助于工业标准的改进。
EXTENDING BEARING LIFEAbstract:Nature works hard to destroy bearings, but their chances of survival can be improved by following a few simple guidelines. Extreme neglect in a bearing leads to overheating and possibly seizure or, at worst, an explosion. But even a failed bearing leaves clues as to what went wrong. After a little detective work, action can be taken to avoid a repeat performance.Keywords: bearings failures lifeBearings fail for a number of reasons,but the most common are misapplication,contamination,improper lubricant,shipping or handling damage,and misalignment. The problem is often not difficult to diagnose because a failed bearing usually leaves telltale signs about what went wrong.However,while a postmortem yields good information,it is better to avoid the process altogether by specifying the bearing correctly in The first place.To do this,it is useful to review the manufacturers sizing guidelines and operating characteristics for the selected bearing.Equally critical is a study of requirements for noise, torque, and runout, as well as possible exposure to contaminants, hostile liquids, and temperature extremes. This can provide further clues as to whether a bearing is right for a job.1 Why bearings failAbout 40% of ball bearing failures are caused by contamination from dust, dirt, shavings, and corrosion. Contamination also causes torque and noise problems, and is often the result of improper handling or the application environment.Fortunately, a bearing failure caused by environment or handling contamination is preventable,and a simple visual examination can easily identify the cause.Conducting a postmortem il1ustrates what to look for on a failed or failing bearing.Then,understanding the mechanism behind the failure, such as brinelling or fatigue, helps eliminate the source of the problem.Brinelling is one type of bearing failure easily avoided by proper handing and assembly. It is characterized by indentations in the bearing raceway caused by shock loading-such as when a bearing is dropped-or incorrect assembly. Brinelling usually occurs when loads exceed the material yield point(350,000 psi in SAE 52100 chrome steel).It may also be caused by improper assembly, Which places a load across the races.Raceway dents also produce noise,vibration,and increased torque.A similar defect is a pattern of elliptical dents caused by balls vibrating between raceways while the bearing is not turning.This problem is called false brinelling. It occurs on equipment in transit or that vibrates when not in operation. In addition, debris created by false brinelling acts like an abrasive, further contaminating the bearing. Unlike brinelling, false binelling is often indicated by a reddish color from fretting corrosion in the lubricant.False brinelling is prevented by eliminating vibration sources and keeping the bearing well lubricated. Isolation pads on the equipment or a separate foundation may be required to reduce environmental vibration. Also a light preload on the bearing helps keep the balls and raceway in tight contact. Preloading also helps prevent false brinelling during transit.Seizures can be caused by a lack of internal clearance, improper lubrication, or excessive loading. Before seizing, excessive, friction and heat softens the bearing steel. Overheated bearings often change color,usually to blue-black or straw colored.Friction also causes stress in the retainer,which can break and hasten bearing failure.Premature material fatigue is caused by a high load or excessive preload.When these conditions are unavoidable,bearing life should be carefully calculated so that a maintenance scheme can be worked out.Another solution for fighting premature fatigue is changing material.When standard bearing materials,such as 440C or SAE 52100,do not guarantee sufficient life,specialty materials can be recommended. In addition,when the problem is traced back to excessive loading,a higher capacity bearing or different configuration may be used.Creep is less common than premature fatigue.In bearings.it is caused by excessive clearance between bore and shaft that allows the bore to rotate on the shaft.Creep can be expensive because it causes damage to other components in addition to the bearing.0ther more likely creep indicators are scratches,scuff marks,or discoloration to shaft and bore.To prevent creep damage,the bearing housing and shaft fittings should be visually checked.Misalignment is related to creep in that it is mounting related.If races are misaligned or cocked.The balls track in a noncircumferencial path.The problem is incorrect mounting or tolerancing,or insufficient squareness of the bearing mounting site.Misalignment of more than 1/4·can cause an early failure.Contaminated lubricant is often more difficult to detect than misalignment or creep.Contamination shows as premature wear.Solid contaminants become an abrasive in the lubricant.In addition。