连接座三维模型及注塑模具的设计
连接器壳体注塑模具毕业设计

连接器壳体塑料注塑模具设计摘要本文是关于连接器壳体塑料注塑模具的设计,通过正确分析塑件工艺特点和ABS材料的性能后,最终设计出一副注塑模。
塑料制品具有原料来源丰富,价格低廉,性能优良等特点。
它在电脑、手机、汽车、电机、电器、仪器仪表、家电和通讯产品制造中具有不可替代的作用,应用极其广泛。
注射成形是成形热塑件的主要方法,因此应用范围很广。
注射成形是把塑料原料放入料筒中经过加热熔化,使之成为高黏度的流体,用柱塞或螺杆作为加压工具,使熔体通过喷嘴以较高压力注入模具的型腔中,经过冷却、凝固阶段,而后从模具中脱出,成为塑料制品。
本文详细介绍了模具的浇注系统、模具成型部分结构、顶出系统、冷却系统、注塑机的选择及有关参数的校核等等设计。
运用CAD、辅助工程PRO/E 等不同的软件分别对模具的设计、制造和产品质量进行分析。
连接器壳体塑料注塑模具设计,采用一般精度,利用CAD、PRO/E来设计或分析注射模的成型零部件,浇注系统,导向部件和脱模机构等等。
针对连接器的具体结构,该模具采用点浇口双分型面注射模具。
由于塑件内侧有小孔,需要设置斜导柱。
通过模具设计表明该模具能达到连接器的质量和加工工艺要求。
综合运用了专业基础、专业课知识设计,其核心知识是塑料成型模具、材料成型技术基础、机械设计、塑料成型工艺、模具CAD\CAM等。
关键词:连接器壳体;注塑模具;CAD;PRO/EThe connector shell plastic injection mold designAbstractThis article is about the connector shell plastic injection mold design, through the technological characteristics of plastics article of correct analysis and the performance of ABS material, the final design out a pair of injection mold. Plastic products have rich raw material sources, low price, good performance, etc. It in computers, cell phones, cars, motors, electrical appliances, instruments and meters, household appliances and communications products manufacturing has irreplaceable function, is widely applied. Injection molding is the main method of forming thermoplastic parts, so the application range is very wide.Injection molding is melt the plastic raw material into the cylinder through the heating, made of high viscosity fluid, pressurized with piston or screw as a tool, makes the melt through the nozzle at high pressure into mold cavity, after cooling and solidification stage, and then out of the mould, plastic products.Mould gating system are introduced in detail in this paper, the structure of the molding part, ejector system, cooling system, selection of injection molding machine and related parameters of checking, etc. Design. Using PRO/E CAD, auxiliary engineering such as different software respectively to the mold design, manufacturing and product quality are analyzed. Connector shell plastic injection mold design, using the general accuracy and the use of CAD, PRO/E to design or analysis of forming parts of injection mould, pouring system, guide parts and demoulding mechanism, and so on. According to the specific structure of the connector, the mould adopts the point gate double parting surface injection mould. Because there are holes plastic parts inside, need to set up the inclined guide pillar. Through the mold design shows that the mould can achieve connector quality and processing technology. Integrated use of the professional basis, professional class knowledge is designed, its core knowledge is the plastic molding mold, material molding technology base, mechanical design, plastic molding process, mould CAD/CAM, etc.Key words: the connector shell; Injection mould; CAD; PRO/E目录1 绪论 (1)1.1前言 (1)1.2模具发展现状及发展方向 (1)1.2.1国内外注塑模具的发展现状 (1)1.2.2国内外注塑模具的发展趋向 (3)1.3本课题的内容和具体要求 (3)1.3.1本课题的内容 (3)1.3.2具体要求 (3)2 零件材料分析及方案论证 (4)2.1零件的材料及材料的特性 (4)2.1.1零件的材料 (4)2.1.2 ABS材料的特点 (4)2.1.3 ABS注射成型工艺参数 (5)2.2 ABS注射成型的原理及工艺过程 (5)2.2.1注射成型的原理 (5)2.3注射模具的基本组成 (6)2.3.1基本组成 (6)3 注射成型机的选择与成型腔数的确定 (7)3.1注射成型机的选择 (7)3.1.1估算零件体积 (7)3.1.2估算零件的质量 (8)3.2锁模力 (8)3.3选择注射机型号及注射机的主要参数 (8)3.3.1注塑成型工艺简介注塑机的初步选择 (8)3.3.2注塑成型工艺条件 (9)3.3.3注塑机的初步选择 (10)3.3.4 XS-ZY-125型注塑机的主要参数如下 (10)3.4注塑机的校核 (10)3.5成型腔数的确定 (12)4 浇注系统的设计 (13)4.1浇注系统的作用 (13)4.2浇注系统的组成 (13)4.3主流道设计 (13)4.4分流道设计 (15)4.5浇口设计 (16)5 成型零件结构设计 (17)5.1分型面的设计 (17)5.1.1分型面选择原则 (17)5.2型腔的分布 (17)5.3凹模的结构设计 (17)5.4凸模的结构设计 (17)5.5成型零件工作尺寸的计算 (18)5.5.1影响塑件尺寸精度的因素 (18)5.5.2模具成型零件的工作尺寸计算 (18)5.6动模板的强度校核 (19)5.6.1厚度计算 (19)6 导向与脱模机构的设计 (20)6.1导向机构的作用和设计原则 (20)6.1.1导向机构的作用 (20)6.1.2导向机构的设计原则 (20)6.2导柱、导套的设计 (20)6.2.1导柱的设计 (20)6.2.2导套的设计 (21)6.2.3导向孔的总体布局 (22)6.3脱模机构的确定 (22)6.4推杆横截面直径的确定与校核 (22)6.4.1推杆横截面直径的确定 (22)6.4.2推杆横截面直径的校核 (22)6.4.3顶杆的形式 (23)6.5复位杆的结构设计 (24)6.5.1复位杆的作用 (24)6.5.2的结构 (24)6.6锁紧块 (24)6.6.1锁紧块的作用 (24)6.6.2锁紧块的设计 (25)6.6.3锁紧块的结构形式 (25)6.6.4锁紧块的具体结构形式 (25)7 侧向分型与抽芯机构的设计 (26)7.1斜导柱抽芯机构设计原则 (26)7.2抽芯机构的确定 (26)7.3斜导柱抽芯机构的有关参数计算 (26)7.3.1抽芯距S (26)7.3.2斜导柱倾斜角α的确定 (27)7.3.3斜导柱直径的确定 (28)7.3.4斜导柱长度的计算 (28)7.4滑块的设计 (29)7.5导滑槽的设计 (30)7.6滑块定位装置 (31)7.6.1作用 (31)7.6.2结构形式 (31)8 成型零件尺寸计算 (32)9 冷却系统 (34)9.1温度调节对塑件质量的影响 (34)9.2对温度调节系统的要求 (34)9.3模具冷却装置的设计 (34)9.3.1冷却装置的设计要点 (34)9.3.2水嘴的结构形式 (34)9.3.3冷却水道的结构 (35)10 模具的可行性分析 (36)10.1本模具的特点 (36)10.2市场前景与经济效益分析 (36)结论 (37)参考文献 (38)致谢 (39)毕业设计(论文)知识产权声明 ............................ 错误!未定义书签。
利用UG进行连接座后盖的三维模型及注塑模具设计
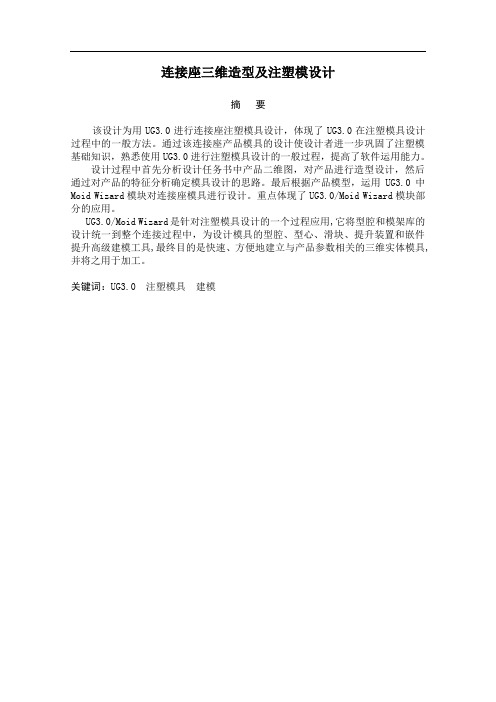
连接座三维造型及注塑模设计摘要该设计为用UG3.0进行连接座注塑模具设计,体现了UG3.0在注塑模具设计过程中的一般方法。
通过该连接座产品模具的设计使设计者进一步巩固了注塑模基础知识,熟悉使用UG3.0进行注塑模具设计的一般过程,提高了软件运用能力。
设计过程中首先分析设计任务书中产品二维图,对产品进行造型设计,然后通过对产品的特征分析确定模具设计的思路。
最后根据产品模型,运用UG3.0中Moid Wizard模块对连接座模具进行设计。
重点体现了UG3.0/Moid Wizard模块部分的应用。
UG3.0/Moid Wizard是针对注塑模具设计的一个过程应用,它将型腔和模架库的设计统一到整个连接过程中,为设计模具的型腔、型心、滑块、提升装置和嵌件提升高级建模工具,最终目的是快速、方便地建立与产品参数相关的三维实体模具,并将之用于加工。
关键词:UG3.0 注塑模具建模ABSTRACTThe design for linking with UG3.0 Block Injection Mold Design, UG3.0 reflected in the injection mold design process in general. Block, through the connection of the die design products enable designers to further consolidate the injection mold basic knowledge, UG3.0 familiar with the use of injection mold for the general design process, enhance the ability to use the software.First the design process analysis and design tasks products 2D map book, the product modeling design, Then the characteristics of the product analysis mold design ideas. Finally, according to product model, which use UG3.0 Moid Wizard module to connect Block mold design. Focus reflects the UG3.0/Moid Wizard module of the application.UG3.0/Moid Wizard against injection mold design an application process, It will die-cavity and the design of the unity of the whole process of connecting to the design of the mold cavity, heart-type, slider, upgrade equipment and upgrade inlay pieces High modeling tools, with the ultimate aim is rapid, to facilitate the establishment and product parameters related to the 3D mold, and use them for processing.Key words : UG3.0 injection mold modeling目录摘要 (I)绪论 (1)1.模具行业发展现状及发展趋势 (1)2.UG及其在模具设计工程中的应用 (2)3.关于连接座注塑模具设计 (4)4.本课题的意义、目的及应达到的要求 (4)第1章零件结构及工艺分析............................................................... (6)1.1 分型面的选择 (6)1.2 型腔布局 (7)1.3 浇注系统设计 (7)1.4 推出机构设计 (7)第2章产品造型设计........................................................................ (8)第3章连接座注塑模具设计 (12)3.1装载产品 (12)3.2模具坐标系 (13)3.3设定收缩率 (13)3.4设定工件 (14)3.5分型 (14)3.6添加模架 (18)3.7添加标准部件 (19)3.8冷却系统设计 (20)3.9建腔 (23)3.10添加螺钉 (23)第4章模具结构的虚拟装配及二维工程图 (24)第5章模具零件清单导出 (25)第6章结束语 (26)致谢............................................................................................. (28)参考文献 (29)绪论模具是生产各种工业产品的重要工艺装备,随着塑料工业的迅速发展以及塑料制品在航空、航天、电子、机械、船舶和汽车等工业部门的推广应用,产品对模具的要求越来越高,传统的模具设计方法已无法适应产品更新换代和提高质量的要求。
毕业设计(论文)-连接座模具设计
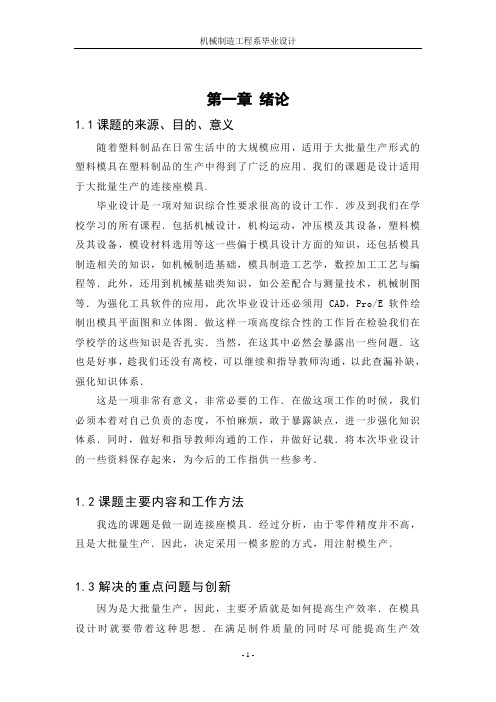
第一章绪论1.1课题的来源、目的、意义随着塑料制品在日常生活中的大规模应用,适用于大批量生产形式的塑料模具在塑料制品的生产中得到了广泛的应用.我们的课题是设计适用于大批量生产的连接座模具.毕业设计是一项对知识综合性要求很高的设计工作.涉及到我们在学校学习的所有课程.包括机械设计,机构运动,冲压模及其设备,塑料模及其设备,模设材料选用等这一些偏于模具设计方面的知识,还包括模具制造相关的知识,如机械制造基础,模具制造工艺学,数控加工工艺与编程等.此外,还用到机械基础类知识,如公差配合与测量技术,机械制图等.为强化工具软件的应用,此次毕业设计还必须用CAD,Pro/E软件绘制出模具平面图和立体图.做这样一项高度综合性的工作旨在检验我们在学校学的这些知识是否扎实.当然,在这其中必然会暴露出一些问题.这也是好事,趁我们还没有离校,可以继续和指导教师沟通,以此查漏补缺,强化知识体系.这是一项非常有意义,非常必要的工作.在做这项工作的时候,我们必须本着对自己负责的态度,不怕麻烦,敢于暴露缺点,进一步强化知识体系.同时,做好和指导教师沟通的工作,并做好记载.将本次毕业设计的一些资料保存起来,为今后的工作指供一些参考.1.2课题主要内容和工作方法我选的课题是做一副连接座模具.经过分析,由于零件精度并不高,且是大批量生产.因此,决定采用一模多腔的方式,用注射模生产.1.3解决的重点问题与创新因为是大批量生产,因此,主要矛盾就是如何提高生产效率.在模具设计时就要带着这种思想.在满足制件质量的同时尽可能提高生产效率.结合实际情况和模具开合模过程中机构的可靠性.决定采用瓣合模的方式成型塑件外型.同时是一模两腔.这样做一来可以满足制件的质量要求,二来可以提高生产效率.两个主要矛盾都得到了较好的解决.第二章产品的设计与制作2.1塑件成型工艺性分析1、塑件(连接座)分析1)、塑件:见下图2)、塑料名称:ABS3)、生产纲领:大批量4)、塑件的结构及成型工艺性分析:该零件是一个柱形零件,内部有阶梯孔。
连接座塑件注射模设计 大学毕业设计

从模具使用角度考虑,要求高效率、自动化、操作简便;从模具制造角度,要求结构合理、制造简易、成本低廉。模具是决定最终产品性能,规格,形状尺寸精度的载体。塑料成型模具是使塑料成型生产过程顺利进行、保证塑料成型制件质量不可缺少的工艺装备,是体现塑料成型设备高效率、高性能和合理先进塑料成型工艺的具体实施者,也是新产品开发的决定性环节。随着我国经济与国际的接轨和国家经济建设持续稳定的发展,塑料制作的应用快速提升,模具设计与制造的塑料成型的各类企业日益增多,塑料成型工业在基础工业中的地位和对国民经济的影响日益重要 !
连接座塑件注射模设计
学院
专业
班级
学号
姓名
指导教师
负责教师
沈阳航空航天大学
2015年6月
摘
此连接座注射模具,采用双分型面一模两腔三板式结构,由于制件壁厚大部分均匀,而且型腔深度适中,所以采用推杆推出平稳;塑件生产批次较大,所以型芯采用组合镶拼式,磨损后便于更换。先分型机构采用定距拉杆配合弹簧使用,结构简单并且动作可靠。模具型腔的充填采用点浇口的进料方式,有利于塑料熔体均匀的充填型腔。侧向分型与抽芯机构采用斜导柱驱动侧型芯滑块来实现侧抽动作。侧型芯与侧型芯滑块分开加工,侧型芯滑块在动模板上滑动,导滑槽单独加工,这些同样是为了方便磨损后可以局部更换。
Keywords:three-plate;combination spacing;length bolt;angleguide pillar
1
1.1
塑料成型所用的模具称为塑料成型模,是用于成型塑料制作的模具,它是型腔模的一种类型。目前,塑料制件几乎已经进入了一切工业部门以及人民日常生活的各个领域,因此,对塑料模具生产不断向前发展起着推动作用。
D30等径三通注塑模具设计

D30等径三通注塑模具设计摘要三通管作为一种日常生活中广泛使用的连接件,本设计对三通管的注塑模具设计方法进行了阐述。
通过本设计可以对注塑模具有一个全面的了解,以及设计中需要注意的一些细节,了解模具的结构和工作原理。
此次设计为D30等径三通管注塑模具设计,利用pro/e进行三维造型,确定塑件体积质量等参数。
设计包括对塑件材料的选择和结构的分析;进行三通接头成型工艺分析、确定成型方案;注塑机型号的选择、确定收缩率和分型面,进行模具尺寸计算;浇注系统的形式和浇口的设计、导向定位机构、侧向分型与抽芯机构;脱模机构和分型面、排气系统以及温度调节系统等。
根据塑件的产品数量要求,以及结构要求,该模具采用一模两腔。
利用pro/e、CAD 软件设计成形零件,从而进行全方面的参数化设计,即对模具进行分模、生产元件、装配、试模、开模设计。
关键词:三通管,注塑模具,导向定位,浇注系统,分型D30 Tee injection mold designABSTRACTOnly material by molding with the use of various products to bee the value of the molding die is used having a certain shape and size of major process equipment ofvarious products are widely used in many materials processing industry.As a tee connector widely used in daily life, the paper injection mold design tee described. Injection mold can have a preliminary understanding, as well as some of the design details that need attention through the design and understanding of the structure and working principle of mold. The design for the D30 Tee pipe injection mold design, the use of pro / e for three-dimensional modeling, to determine the volume of plastic parts quality and other parameters. Design includes analysis of the choice of materials and structure of the plastic parts, injection molding machine model selection, casting gating system design form and guide positioning mechanism, side parting and pulling mechanism, stripping agencies and sub-surface , the exhaust system and the temperature regulation system.KEY WORDS:Tee, Injection mold, oriented positioning, gating system, type目录前言1第1章概论31.1 塑料模具的意义31.1.1 塑料模具成型在国民经济的地位31.1.2 塑料模具成型在塑料工业的重要性31.2 塑料模具的发展状况和趋势41.2.1 国外模具的发展状况和趋势41.2.2 国模具的发展状况和趋势5第2章成型工艺分析72.1 塑件材料分析72.1.1 塑件分析72.1.2 材料特征82.2 塑料成型工艺性能分析92.2.1 流动性92.2.2 收缩性92.2.3 吸湿性102.3 塑料成型工艺性能分析102.3.1 可行性分析102.3.2 塑件尺寸精度分析102.3.3 塑件表面质量分析 (11)2.3.4 塑件结构分析 (11)第3章注射机的选择与校核123.1 注射机的选择123.1.1 制件的体积计算123.1.2 注射机的选择 (13)3.2 注射机的校核133.2.1 最大注射量的校核133.2.2 锁模力的校核143.2.3 最大注射压力的校核143.2.4 抽芯距离的校核143.2.5开模行程的校核15第4章注射模的设计164.1 浇注系统的设计164.1.1 主流道的设计164.1.2 分流道的设计174.1.3 浇口的设计 (18)4.1.4 冷料穴设计 (18)4.2 模架的选取194.2.1 塑料注射模架结构 (19)4.2.2 标准模架的选用 (20)4.3 分型面的选择与型腔数目的确定214.3.1分型面的选择 (21)4.3.2 型腔数目的选择 (22)4.3.3 型腔的布置方式 (22)4.3.4 排气槽的设计 (23)第5章成型零件的结构设计与计算255.1 成型零件的结构设计255.1.1凹模的结构形式 (25)5.1.2凹模的结构设计 (25)5.2 成型零件工作尺寸的计算265.2.1凹模和型芯径向尺寸的计算 (26)5.3 冷却系统的设计275.3.1冷却效率对生产的影响 (27)5.3.2冷却系统的设计原则 (28)第6章推出机构与抽芯机构的设计296.1 脱模机构设计原则296.1.1 脱模力的计算 (29)6.2 侧向抽芯机构设计306.2.1 侧型芯结构设计 (30)6.2.2 脱模力 (31)6.2.3 斜导柱的结构形式 (32)6.2.4 楔紧块的设计 (32)6.2.5 合模导向机构设计 (33)6.2.6 侧滑块设计 (33)6.2.7 滑块导滑槽设计 (34)6.2.8 导向零件 (34)6.2.9 支承零部件设计 (35)6.3 装配总图35结论37辞38参考文献39外文资料翻译42前言塑料工业是当今世界上增长最快的工业门类之一,随着现代高新科学技术的飞速发展,越来越多的具有优异性能的高分子材料不断涌现,促进了塑料工业的飞速发展,现在塑料产品的已经占领人们生活生产的很大市场,并已经成为我们生产生活中不可或缺的一部分,在我国的国民经济中发挥着越来越重要的作用。
连接座模具注塑课程设计

连接座模具注塑课程设计一、课程目标知识目标:1. 学生能理解连接座模具注塑的基本概念,掌握模具结构、注塑过程及其相关参数。
2. 学生能掌握注塑成型原理,了解不同材料在注塑过程中的特性。
3. 学生能了解连接座模具的设计要点,掌握相关设计规范。
技能目标:1. 学生能够运用CAD软件进行连接座模具的设计,具备一定的模具设计能力。
2. 学生能够分析注塑过程中可能出现的问题,并提出相应的解决方法。
3. 学生能够通过实际操作,完成连接座模具的注塑过程,具备一定的动手操作能力。
情感态度价值观目标:1. 学生对模具设计与制造产生兴趣,培养良好的学习态度。
2. 学生通过合作学习,培养团队协作精神,增强沟通与表达能力。
3. 学生认识到连接座模具在制造业中的重要性,增强对制造行业的尊重和认同。
本课程针对高年级学生,结合学科特点,注重理论与实践相结合。
课程目标既包括对模具注塑基本知识的掌握,又强调实际操作能力的培养。
通过本课程的学习,学生将能够具备一定的模具设计、制造和问题分析解决能力,为今后从事相关工作奠定基础。
同时,课程注重培养学生的团队协作和沟通能力,提高学生对制造业的认识和认同。
二、教学内容1. 连接座模具结构及工作原理:讲解连接座模具的组成、各部分功能及其工作原理,结合教材相关章节,让学生理解模具的基本结构。
2. 注塑成型工艺参数:介绍注塑过程中涉及的压力、温度、速度等关键参数,分析这些参数对成型质量的影响,结合教材内容进行讲解。
3. 模具设计要点及规范:分析连接座模具设计的关键技术,如分型面设计、型腔布局、浇注系统设计等,遵循教材中的设计规范,指导学生完成模具设计。
4. CAD软件操作与模具设计:教授CAD软件的基本操作,指导学生运用软件进行连接座模具的设计,结合教材实例进行讲解。
5. 注塑成型操作与问题分析:讲解注塑机的操作步骤,引导学生完成实际注塑过程,分析可能出现的质量问题,如气泡、变形等,并提出解决方案。
连接座模具注塑课程设计
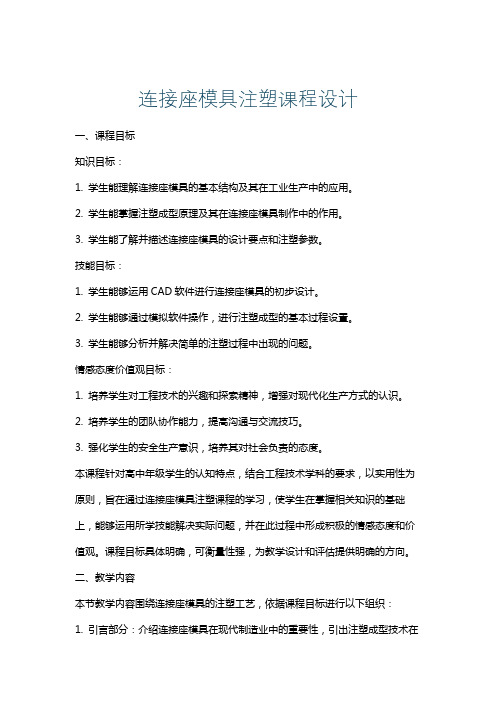
连接座模具注塑课程设计一、课程目标知识目标:1. 学生能理解连接座模具的基本结构及其在工业生产中的应用。
2. 学生能掌握注塑成型原理及其在连接座模具制作中的作用。
3. 学生能了解并描述连接座模具的设计要点和注塑参数。
技能目标:1. 学生能够运用CAD软件进行连接座模具的初步设计。
2. 学生能够通过模拟软件操作,进行注塑成型的基本过程设置。
3. 学生能够分析并解决简单的注塑过程中出现的问题。
情感态度价值观目标:1. 培养学生对工程技术的兴趣和探索精神,增强对现代化生产方式的认识。
2. 培养学生的团队协作能力,提高沟通与交流技巧。
3. 强化学生的安全生产意识,培养其对社会负责的态度。
本课程针对高中年级学生的认知特点,结合工程技术学科的要求,以实用性为原则,旨在通过连接座模具注塑课程的学习,使学生在掌握相关知识的基础上,能够运用所学技能解决实际问题,并在此过程中形成积极的情感态度和价值观。
课程目标具体明确,可衡量性强,为教学设计和评估提供明确的方向。
二、教学内容本节教学内容围绕连接座模具的注塑工艺,依据课程目标进行以下组织:1. 引言部分:介绍连接座模具在现代制造业中的重要性,引出注塑成型技术在模具制作中的应用。
- 教材章节:第二章 工程材料与成型技术2. 理论知识:- 连接座模具的结构与设计原则- 注塑成型原理及工艺参数- 常见注塑缺陷及其解决方法- 教材章节:第三章 模具设计与制造3. 实践操作:- 使用CAD软件进行连接座模具设计- 注塑成型模拟软件操作- 分析实际注塑过程中可能出现的问题并给出解决方案- 教材章节:第四章 计算机辅助设计与制造4. 案例分析:分析实际生产中的连接座模具注塑案例,强化理论与实践相结合。
- 教材章节:第五章 生产案例分析教学内容按照教学大纲进行系统安排,确保学生在学习过程中逐步掌握模具设计、注塑工艺和相关技能。
在教学过程中,教师需关注学生对理论知识的理解、实践操作的熟练度以及案例分析的综合运用能力,使学生在完成课程学习后能够具备一定的工程技术素养。
基于UG3.0的连接座三维造型及注塑模具设计

基于 UG3.0 的连接座三维造型及注塑模具设计绪论模具是生产各种工业产品的重要工艺装备,随着塑料工业的迅速发展以及塑 料制品在航空、航天、电子、机械、船舶和汽车等工业部门的推广应用,产品对 模具的要求越来越高,传统的模具设计方法已无法适应产品更新换代和提高质量 的要求。
CAD/CAM/CAE技术已成为塑料产品开发、模具设计及产品加工中这些薄弱 环节的最有效的途经。
同传统的模具设计相比,CAD/CAM/CAE技术无论在提高生产 率、保证产品质量,还是在降低成本、减轻劳动强度等方面,都具有很大的优越 性。
近几年,CAD/CAM/CAE技术在汽车、家电、电子通讯、化工和日用品等领域逐 步地得到了广泛应用。
(一)、模具工业行业现状和发展趋势1、国内模具现状和发展趋势随着我国经济的迅速发展,采用模具的生产技术得到愈来愈广泛的应用。
近 年来,随着我国产品制造业蓬勃发展,模具制造业也相应进入了高速发展时期。
据中国模具工业协会统计,1995年我国模具工业总产值约为145亿,而2003年已 达450亿左右,年均增长14%。
另据统计,我国(不含台湾、香港、澳门地区)现 有模具生产厂点已超过20000家,从业人员有 60万人,模具年产值在一亿以上的 企业已达十多家。
可以预见,我国经济的高速发展将对模具提出更为大量、更为 迫切的需求,特别需要发展大型、精密、复杂、长寿命的模具。
同时要求模具设 计、制造和生产周期要达到全新的水平。
我国模具制造业面临着发展的机遇,但同时也面临着更大的挑战。
虽然我国 模具发展还远远不能适应国民经济发展的需要,差距和不足依然存在,但我国模 具工业的技术水平近年来也取得了长足的进步,其发展也是明显的,特别是大型、 精密、复杂、高效和长寿命模具上了一个新台阶。
大型复杂冲模以汽车覆盖件模 具为代表,已能生产部分新型轿车的覆盖件模具。
体现高水平制造技术的多工位 级进模的覆盖面,已从电机、电器铁芯片模具,扩展到接插件、电子枪零件、空 调器散热片等家电零件模具。
连接座注塑模具课程设计
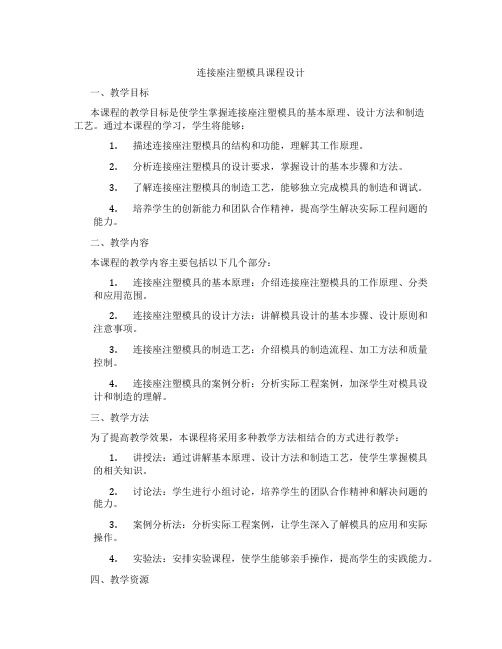
连接座注塑模具课程设计一、教学目标本课程的教学目标是使学生掌握连接座注塑模具的基本原理、设计方法和制造工艺。
通过本课程的学习,学生将能够:1.描述连接座注塑模具的结构和功能,理解其工作原理。
2.分析连接座注塑模具的设计要求,掌握设计的基本步骤和方法。
3.了解连接座注塑模具的制造工艺,能够独立完成模具的制造和调试。
4.培养学生的创新能力和团队合作精神,提高学生解决实际工程问题的能力。
二、教学内容本课程的教学内容主要包括以下几个部分:1.连接座注塑模具的基本原理:介绍连接座注塑模具的工作原理、分类和应用范围。
2.连接座注塑模具的设计方法:讲解模具设计的基本步骤、设计原则和注意事项。
3.连接座注塑模具的制造工艺:介绍模具的制造流程、加工方法和质量控制。
4.连接座注塑模具的案例分析:分析实际工程案例,加深学生对模具设计和制造的理解。
三、教学方法为了提高教学效果,本课程将采用多种教学方法相结合的方式进行教学:1.讲授法:通过讲解基本原理、设计方法和制造工艺,使学生掌握模具的相关知识。
2.讨论法:学生进行小组讨论,培养学生的团队合作精神和解决问题的能力。
3.案例分析法:分析实际工程案例,让学生深入了解模具的应用和实际操作。
4.实验法:安排实验课程,使学生能够亲手操作,提高学生的实践能力。
四、教学资源为了支持本课程的教学,我们将准备以下教学资源:1.教材:选用权威、实用的教材,为学生提供系统、全面的知识体系。
2.参考书:提供相关的参考书籍,丰富学生的知识储备。
3.多媒体资料:制作精美的课件、视频等资料,提高学生的学习兴趣。
4.实验设备:准备完善的实验设备,保证实验课程的顺利进行。
通过以上教学资源的支持,相信能够提高本课程的教学质量,帮助学生更好地掌握连接座注塑模具的相关知识。
五、教学评估本课程的评估方式将包括以下几个方面,以保证评估的客观性和公正性:1.平时表现:通过课堂参与、提问、讨论等环节,评估学生的学习态度和积极性。
连接座注塑模模具设计说明书

*********学院课程设计说明书题目:连接座注塑模模具设计学院:机电工程学院专业:模具设计与制造班级: **********姓名: **********学号: **********指导老师: **********时间: ****年*月*日目录前言 (4)一、零件工艺性分析 (5)二、注塑模的结构确定 (6)三、模具设计的有关计算 (11)四、模具调节温度设计 (14)五、模具闭合高度的确定 (16)六、注塑机有关参数的校核 (16)七、绘制模具总装图 (17)总结 (18)参考文献 (18)引言注塑模具课程设计比较全面的训练,其意义在于为以后的设计工作打基础,培养学生在设计过程中严肃认真、刻苦钻研、一丝不苟、精益求精的态度,使其在设计思想、方法和技能等各方面均获得锻炼和提高。
经过一学期对塑料模具整体结构和细节的学习和了解,为了更进一步的了解模具制造和加工,利用所学模具知识设计一套简单的注塑模具,来巩固所学模具知识。
通过完成模具课程设计,综合应用和巩固模具设计课程以及相关课程的理论基础和专业知识,系统地掌握产品零件的成型工艺分析、模具结构设计的基本方法和步骤、非标准模具零件的设计等模具设计基本方法。
同时,学会准确运用技术标准和资料,培养了认真负责、踏实细致的工作作风和严谨的工作态度,强化了质量意识和时间观念,从而形成了从业的基本职业素质。
第二部分:模具设计实例一、零件工艺性分析工件为图1所示的落料冲孔件,材料为ABS,尺寸精度为4级,生产批量为大批量。
工艺性分析内容如下:技术要求:表面光亮无划伤痕迹1:塑件的原材料分析塑件的材料采用工程塑料ABS,属热塑性塑料,是由丙烯腈,丁二烯和苯乙烯组成的三不共聚物。
本身耐热性和溶性比HIPS佳,且具有光泽性。
由于丙烯腈的腈基极性较强,所以冲击强度,拉伸强度及塑料件的表面硬度均较HIPS佳。
综合物理-力学性能更是优良。
ABS树脂为浅黄色粒状或珠状树脂,熔融温度为217-237℃,热分解温度为250℃以上,无毒,无味,吸水率低,具有优良的综合物理-力学性能,优异的低温抗冲击性能,尺寸稳定性,电性能,耐磨性,抗化学药品性,染色性,成型加工和机械加工较好。
某连接件注塑模具设计

铸造技术10/2010生产技术与经验交流图2 焊缝高度偏差信息图图3 焊缝偏左图当I1-I2<0时,焊枪位置偏右,这时应向左移动焊枪,如图4所示。
当I1-I2=0时,焊枪位置适中。
运用以上特性,机器人控制柜NX100下载弧焊电流波动数据,并将此信号传送到外部PLC,实时调整图4 焊缝偏右图机器人运动轨迹,实现弧焊机器人焊缝轨迹跟踪。
4 结论焊缝跟踪技术是弧焊机器人应用的一个重要的研究方向。
随着智能控制技术的发展和焊缝识别与实时控制等一系列问题的解决,摆动电弧焊缝跟踪技术将得到更加广泛的应用。
参考文献[1] 毛鹏军,黄石生,李 阳,等.焊接机器人技术发展的回顾与展望[J].焊接,2001,(8):6 9.[2] 熊震宇,张 华,潘际銮.电弧传感器的发展状况及应用前景[J].焊接技术,2001,30(5):2 5.收稿日期:2009 06 16; 修订日期:2009 07 18作者简介:殷际英(1950 ),河南安阳人,教授.主要研究方向为机器人技术、固体力学和传热学的工程应用、软件开发.某连接件注塑模具设计窦 涛,韩健美(永城职业学院,河南永城476600)3D Design of the Connecting Fitting Injection MoucdDOU Tao,HAN Jian mei(Yongcheng Vocational College,Yongcheng476600,China)中图分类号:T G76 文献标识码:B 文章编号:1000 8365(2010)10 1387 02要获得一件完美的塑料制品,需根据制品的使用和外观形状要求,从塑料的力学性能、产品造型、成型工艺、塑料模设计和制造等多方面进行全面考虑。
从塑料的力学性能和成型工艺性及简化模具结构方面考虑,需要注意的一些设计要点有:塑件的物理性能,塑料的成型工艺性,塑件的结构应能使模具总体结构尽可能简化,特别是避免侧向分型抽芯机构和简化脱模机构。
塑料模课程设计1连接座成型模具设计
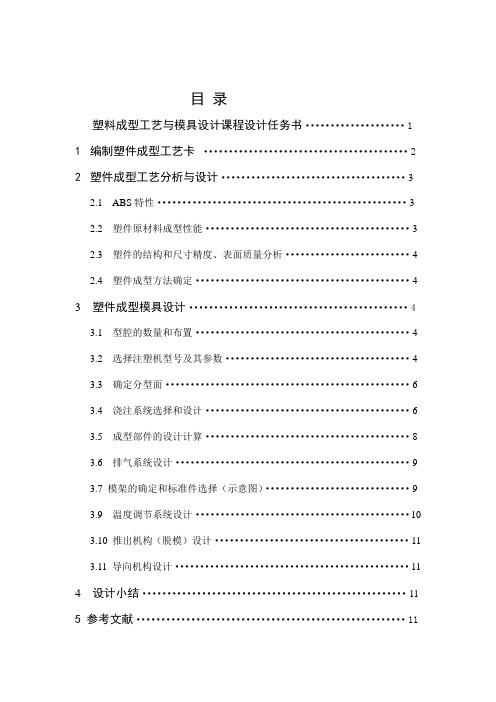
目录塑料成型工艺与模具设计课程设计任务书 (1)1编制塑件成型工艺卡 (2)2塑件成型工艺分析与设计 (3)2.1 ABS特性 (3)2.2 塑件原材料成型性能 (3)2.3 塑件的结构和尺寸精度、表面质量分析 (4)2.4 塑件成型方法确定 (4)3 塑件成型模具设计 (4)3.1 型腔的数量和布置 (4)3.2 选择注塑机型号及其参数 (4)3.3 确定分型面 (6)3.4 浇注系统选择和设计 (6)3.5 成型部件的设计计算 (8)3.6 排气系统设计 (9)3.7 模架的确定和标准件选择(示意图) (9)3.9 温度调节系统设计 (10)3.10 推出机构(脱模)设计 (11)3.11 导向机构设计 (11)4 设计小结 (11)5 参考文献 (11)附录(模具总装图和零件图) (11)“塑料成型工艺与模具设计”课程设计任务书课题设计名称:连接座的注射模设计塑件图:设计内容:1、编制模塑成型工艺规程(即填写“塑件成型工艺卡”)2、绘制塑件注射模总装图(A3图纸1张)3、绘制该模具凸模、凹模的零件图各一套(A3图纸多张)4、编写完善模具设计说明书(按A4打印纸装订)1 塑件成型工艺卡塑件成型工艺卡2 塑件成型工艺分析与设计2.1 ABS的特性(1)化学和物理特性ABS是由丙烯腈、丁二烯和苯乙烯共聚物三种化学单位合成,每种单体都有不同特性;丙烯腈有高强度,热稳定性及化学稳定性;丁二烯具有坚韧性,抗冲击特性;苯乙烯具有易加工,高光洁及高强度。
从形态上看,ABS是非结晶性材料。
三种单体的聚合产生了具有两相的三元共聚物,一个是苯乙烯—丙烯腈的连续相,另一个是聚丁二烯胶分散相。
这就决定了ABS材料的耐高温性、抗冲击性及易加工性等多种特性。
缩水率为0.5%。
ABS有良好的机械强度和一定的耐磨性、耐寒性、耐油性、耐水性、化学稳定性和电气性能,有一定的硬度和尺寸稳定性,易于成型加工且易着色,几乎不受酸、碱、盐及水和无机化合物的影响。
毕业设计(论文)连接器支架塑件的成型模具设计.

1连接器支架塑件的成型模具设计系别:材料工程系学生姓名:专业班级:模具设计与制造专业一班学号:指导教师:2011年3月4日独创性声明本人声明所呈交的毕业论文是我个人在导师指导下进行的研究工作及取得的成果。
尽我所知,除文中已经标明引用的内容外,本论文不包含任何其他个人或集体已经发表或撰写过的研究成果。
对本文的研究做出贡献的个人和集体,均已在文中以明确方式标明。
本人完全意识到本声明的法律结果由本人承担。
论文作者签名:杨凯日期:2011 年 3 月 4 日毕业论文版权使用授权书本毕业论文作者完全了解学校有关保留、使用毕业论文的规定,即:学校有权保留并向有关部门或机构送交论文的复印件和电子版,允许论文被查阅和借阅。
本人授权郑州职业技术学院要以将本论文的全部或部分内容编入有关数据库进行检索,可以采用影印、缩印或扫描等复制手段保存和汇编本论文。
保密□,在________年解密后适用本授权书.本论文属于不保密□。
(请在以上方框内打“√”)毕业论文作者签名:指导教师签名:日期:年月日日期:年月日目录中文摘要 (I)外文摘要 (II)第一章塑料模具的现状及展望 (2)1.1模具工业在国民生产中的作用 (2)塑料模具工业的现状 (2)塑料模具工业的发展趋势 (3)第二章塑件产品的分析 (5)2.1产品材料的选用 (5)2.2连接件塑件产品的测绘 (6)2.3连接器支架塑件三维造型 (7)第三章成型设备的选用 (9)3.1注塑机的选择 (9)3.2模架的选择 (10)3.3模具参数的校核 (11)第四章模具结构形式的拟订 (13)4.1确定型腔数量及排列方式 (13)4.2注射模分型面的选择 (14)模具侧向分型与抽芯机构的分析与确定 (14)侧向抽芯机构的分类与组成 (14)4.3.2抽芯力与抽芯距的确定 (16)4.3.3侧滑块的设计 (16)4.3.4侧型芯的设计 (18)第五章浇注系统形式和浇口的设计 (20)主流道设计 (20)5.2分流道设计 (21)5.3浇口设计 (23)第六章成型零部件设计 (25)6.1成型零部件的结构设计 (25)6.2成型零部件尺寸的计算 (25)第七章导向机构设计 (26)第八章推出机构和复位机构的设计 (27)推出机构的设计 (27)8.2推杆设计 (28)第九章模具冷却系统 (30)9.1冷却水管管道的设置 (30)第十章支承与连接零件的设计与选择 (32)10.1固定板 (32)10.2支承板和垫块 (32)第十一章应用 MOLDFLOW进行注射阶段流动分析 (33)11.1最佳浇口位置及数量的确定 (33)11.2模拟结果分析 (34)第十二章结论 (36)参考文献 (40)致谢 (41)摘要本文分析了连接器支架塑件的成型特点,对模具结构各工艺参数,包括锁模力、流道截面尺寸等模具参数的进行了计算校核,设计了一模一腔含有两分型面的,带有侧向分型与抽芯机构并且有很多小型芯所组成的点浇口注射模具。
连接座三维模型和注塑模具的设计

绪论模具是生产各样工业产品的重要工艺装备,跟着塑料工业的快速发展以及塑料制品在航空、航天、电子、机械、船舶和汽车等工业部门的推行使用,产品对模具的要求愈来愈高,传统的模具设计方法已没法适应产品更新换代和提高质量的要求。
1.模具行业发显现状及发展趋向1.1 国内模具发显现状及发展趋向跟着我国经济的快速发展,采纳模具的生产技术获得愈来愈宽泛的使用。
最近几年来,跟着我国产品制造业蓬勃发展,模具制造业也相应进入了高速发展期间。
据中国模具工业协会统计, 1995 年我国模具工业总产值约为 145 亿,而 2003 年已达450 亿左右,年均增加 14%。
另据统计,我国(不含台湾、香港、澳门地域)现有模具生产厂点已超出 20000 家,从业人员有 60 万人,模具年产值在一亿以上的公司已达十多家。
能够预示,我国经济的高速发展将对模具提出更为大批、迫切的需求,特别需要发展大型、精细、复杂、长寿命的模具。
同时要求模具设计、制造和生产周期要达到崭新的水平。
我国模具制造业面对着发展的机会,但同时也面对着更大的挑战。
固然我国模具行业发展快速,但还远远不可以适应公民经济发展的需要。
我国模具行业尚存在很大的不足,主要表此刻以下几个方面 :第一、体系不全,基础单薄。
“三资”公司固然已经对中国模具工业的发展起了踊跃的推进作用,私营公司最近几年来发展较快,国企改革也在进行之中,但整体来看,体系和体制尚不适应市场经济,再加上国内模具工业基础单薄,所以,行业发展还不尽善尽美,特别是整体水平易高新技术方面。
第二、开发能力较差,经济效益欠佳。
我国模具公司技术人员比率低,水平较低,且不重视产品开发,在市场中常常处于被动地位。
我国每个模具员工均匀年创立产值约合 1 万美元,外国模具工业发达国家大多是15~20 万美元,有的高达 25~30 万美元,和之相对的是我国相当一部分模具公司还沿用过去作坊式管理,真实实现现代化公司管理的公司较少。
第三、工艺装备水平低,且配套性不好,利用率低。
RJ45水晶头接线座塑料模具设计(含全套CAD图纸)
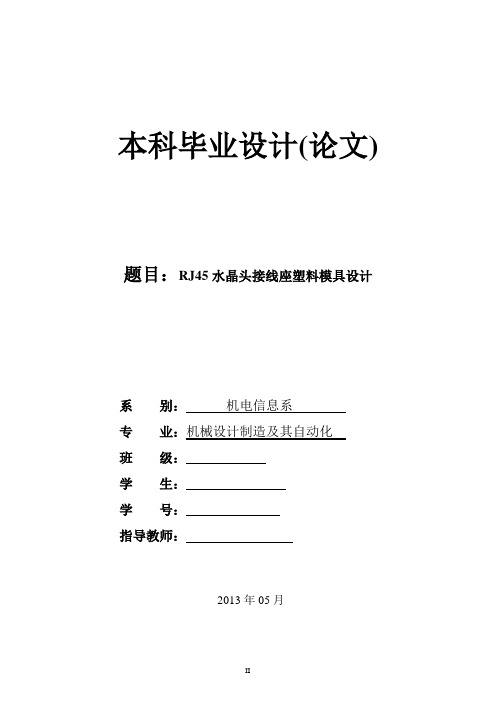
本科毕业设计(论文) 题目:RJ45水晶头接线座塑料模具设计系别:机电信息系专业:机械设计制造及其自动化班级:学生:学号:指导教师:2013年05月RJ45水晶头接线座塑料模具设计摘要随着社会的发展,不同品种和功能的塑料的出现,塑料产品与我们的日常生活越来越密切。
RJ45水晶头接线座是我们日常生活中经常接触到的接口设备之一,其主要用于连接网卡端口、交换机、电话等;计算机网络用的RJ45接线座是标准的8位模块化接口。
本次毕业设计的题目是“RJ-45水晶头接线座注塑模设计”。
该设计主要是通过对塑件的结构形状、尺寸精度和成型要求来进行注射成型工艺的可行性分析,并完成注射模具的设计。
其中,塑件的成型工艺分析主要包括:塑料的成型特性、塑件结构特点、表面粗糙度、达到的使用要求和脱模分析。
以此来确定型腔数目、分型面位置、浇注方式、脱模方式等。
最后完成一幅完整的模具设计总图,包含成型部分、合模导向机构、推出机构、侧向分型抽芯机构、冷却系统等的设计,设计的过程包括了对成型零件的计算、抽芯机构的校核计算等。
在设计的过程主要应用了PRO/E软件完成对塑件的实体造型,并对塑件的体积、质量等进行分析,最后通过Auto CAD完成零件图和装配图,并最终完成塑料模具的设计过程。
关键词:塑料;成型工艺;注射模具设计;抽芯机构;脱模机构AbstractWith the development of society, different varieties and function plastic appearance in our lives, plastic productions have closer to our daily lives.RJ-45 terminal block is one of the interface device in our daily life that we often come into contact with. It often used for network cards, switches, telephones, etc; Computer network wiring blocks using a standard 8-bit modular interface. The subject of the graduation project is “injection mould design for RJ-45 terminal block ” Through the feasibility ana lysis the plastic part structure and shape, the size and shape require for injection molding process, and complete the injection mold design. Analyze and determine the die's parting plane, the number of die cavity, gate’s forming, gate’s position and its s ize. Besides, we need to analysis the stress, the registration and the guide mechanism's design of the dies, the mould emptier design, the cooling system's design, etc. At last, we should finish the die's general assembly drawing. The design have mostly used the Pro/E soft to progress the solid modeling, then analysis the volume and quality of the plastic part. And it has been through the Auto CAD to finish de detail drawing and the assembly drawing, then finish the design processes of injection mold.Key word: Plastic;mold forming;Inject mold design;core pulling mechanism;mould emptier目录1 绪论 (1)2 RJ-45水晶头接线座分析 (2)3 塑料材料分析 (3)3.1 PVC基本特性 (3)3.2 PVC成型工艺分析 (3)4 塑件的工艺分析 (5)4.1 塑件的结构分析 (5)4.2 塑件尺寸及精度分析 (6)4.3 塑件表面质量分析 (6)4.4 塑件脱模斜度分析 (6)4.5 塑件的壁厚分析 (7)4.6 塑件的体积和质量 (7)5 注射机的型号和规格选择及校核 (8)5.1 初选注射机规格 (8)5.2 注射机工艺参数校核 (8)5.3 注射机安装部分与模具相关尺寸校核 (9)6 塑料制件在模具中的位置 (11)6.1 型腔数目的确定 (11)6.2 型腔的布局 (11)6.3 分型面的设计 (11)7 浇注系统的设计 (13)7.1 主流道设计 (13)7.2 分流道设计 (14)7.3 浇口设计 (16)7.3.1 浇口的截面形状和尺寸 (16)7.3.2 浇口位置的选择 (17)7.4 冷料穴和拉料杆设计 (18)8 成型零部件设计 (19)8.1 成型零部件结构设计 (19)8.1.1 凹模结构设计 (19)8.1.2 型芯结构设计 (20)8.2 成型零部件工作尺寸计算 (20)8.2.1 型腔和型芯径向尺寸计算 (21)8.2.2型腔深度和型芯高度尺寸计算 (24)8.2.3 中心距尺寸的计算 (25)9 结构零部件设计 (27)9.1 标准注射模架的选取 (27)9.2 支承件设计 (28)9.3 限位钉设计 (28)9.4 定模座板与动模座板设计 (29)9.5 合模导向机构设计 (29)9.5.1 导柱设计 (29)9.5.2 导套设计 (30)10 推出机构设计 (32)10.1 推出方式的选取 (32)10.2 推出力计算 (32)10.3 推出机构设计 (33)10.3.1 推杆推出机构设计 (33)10.3.2 推出机构导向与复位 (35)11 侧向分型与抽芯机构的设计 (36)11.1 侧向分型与抽芯机构的选择 (36)11.2 斜导柱侧向分型与抽芯机构的设计 (37)11.2.1 斜导柱设计 (38)11.2.2 侧滑块设计 (40)11.2.3 侧滑块定位装置设计 (41)11.2.4 导滑槽设计 (42)11.2.5 楔紧块设计 (42)12 温度调节系统的设计 (43)12.1 冷却回路的尺寸确定 (43)12.2 冷却回路布置 (44)13 模具可行性分析 (46)13.1本模具的特点 (46)13.2市场效益及经济效益分析 (46)结论 (47)致谢 (49)参考文献 (50)1 绪论1 绪论在当今工业生产中,塑料工业业已形成从设计、生产、检测到标准和教学的一整套完整的工业体系,这促进了塑料产品的研发和使用范围,塑料制品的应用从航天领域到日常生活,无所不在。
连接座注塑模设计
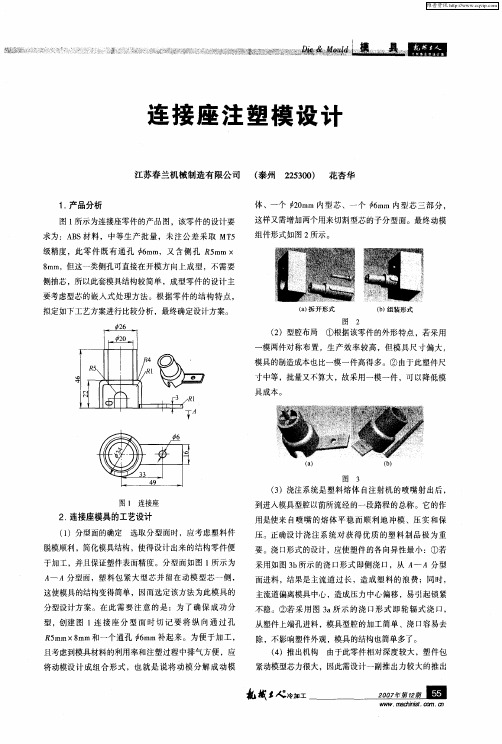
(j a
霪
(j b
图
3
()浇注系统是塑料熔体 自注射机的喷嘴射出后, 3
图 1 连接座
到进入模具型腔以前所流经 的一段路程 的总称。它的作 用是使来 自喷嘴 的熔 体平 稳 而顺 利地 冲模 、压实 和保
压 。正确设计 浇注 系统 对获 得优 质 的塑 料制 品极 为重
2 连接座模具的工艺 时定模板与动模板从分型 面处 分开 ,动模 向后
运动 ,浇注系统 的冷凝料及塑料制 品一起 向后运动 ,当
主流道中的冷凝料完全拉 出一段距离后 , 注射机 的顶杆 作用在下推板 1 上 ,使得浇注 系统 中的冷凝 料和塑 料 8 制品连接座一起推出 , 完成脱模过程 ;合模时 注塑机 顶
方案。
( )冷却 部分 5
冷却部
分是为保证 在制 品 的生产过
◎。
一
。 ◎
o
程 中模 具保 持一定 恒温 ,避
免模具局部 温差 过大 而影 响 制品的 质量 ,为此 而设 计 的 图 4的循环 冷却水 回路 。其
1
◎。
。 ◎
图5 模具结构
1 固定板导套 、 . 导柱 2 侧支承 3 导柱 4 导套 . . . 1. 1 定模框 1. 2 定模芯 1 3动模芯
维普资讯
圈
: L
& o u Ml d
机构。若 采用推管与推杆联合推 出,推 出平 稳 , 推出 但 机构复杂 ,制造 与装配成 本上 升。若采 用推件 板推 出, 就能平稳顶出塑件 ,这样塑件不易发生顶 出变形 ,且能
确保塑件质量 ,因此推件板推出为本次模具设计 的优选
从塑件上端孔进料 , 具型腔的加工简单 、浇 口容 易去 模 除 ,不影 响塑件外观 , 模具 的结构也简单多了。 ()推 出机构 由于此零件相对深度较 大,塑 件包 4 紧动模 型芯力很大 ,因此需设计 一副推出力较 大的推出
- 1、下载文档前请自行甄别文档内容的完整性,平台不提供额外的编辑、内容补充、找答案等附加服务。
- 2、"仅部分预览"的文档,不可在线预览部分如存在完整性等问题,可反馈申请退款(可完整预览的文档不适用该条件!)。
- 3、如文档侵犯您的权益,请联系客服反馈,我们会尽快为您处理(人工客服工作时间:9:00-18:30)。
绪论模具是生产各种工业产品的重要工艺装备,随着塑料工业的迅速发展以及塑料制品在航空、航天、电子、机械、船舶和汽车等工业部门的推广应用,产品对模具的要求越来越高,传统的模具设计方法已无法适应产品更新换代和提高质量的要求。
1.模具行业发展现状及发展趋势1.1国内模具发展现状及发展趋势随着我国经济的迅速发展,采用模具的生产技术得到愈来愈广泛的应用。
近年来,随着我国产品制造业蓬勃发展,模具制造业也相应进入了高速发展时期。
据中国模具工业协会统计,1995年我国模具工业总产值约为145亿,而2003年已达450亿左右,年均增长14%。
另据统计,我国(不含台湾、香港、澳门地区)现有模具生产厂点已超过20000家,从业人员有60万人,模具年产值在一亿以上的企业已达十多家。
可以预见,我国经济的高速发展将对模具提出更为大量、迫切的需求,特别需要发展大型、精密、复杂、长寿命的模具。
同时要求模具设计、制造和生产周期要达到全新的水平。
我国模具制造业面临着发展的机遇,但同时也面临着更大的挑战。
虽然我国模具行业发展迅速,但还远远不能适应国民经济发展的需要。
我国模具行业尚存在很大的不足,主要表现在以下几个方面:第一、体制不全,基础薄弱。
“三资”企业虽然已经对中国模具工业的发展起了积极的推动作用,私营企业近年来发展较快,国企改革也在进行之中,但总体来看,体制和机制尚不适应市场经济,再加上国内模具工业基础薄弱,因此,行业发展还不尽如人意,特别是总体水平和高新技术方面。
第二、开发能力较差,经济效益欠佳。
我国模具企业技术人员比例低,水平较低,且不重视产品开发,在市场中经常处于被动地位。
我国每个模具职工平均年创造产值约合1万美元,国外模具工业发达国家大多是15~20万美元,有的高达25~30万美元,与之相对的是我国相当一部分模具企业还沿用过去作坊式管理,真正实现现代化企业管理的企业较少。
第三、工艺装备水平低,且配套性不好,利用率低。
虽然国内许多企业采用了先进的加工设备,但总的来看装备水平仍比国外企业落后许多,特别是设备数控化率和CAD/CAM应用覆盖率要比国外企业低得多。
由于体制和资金等原因,引进设备不配套,设备与附配件不配套现象十分普遍,设备利用率低的问题长期得不到较好解决。
装备水平低,带来中国模具企业钳工比例过高等问题。
第四、专业化、标准化、商品化的程度低、协作差。
由于长期以来受“大而全”“小而全”影响,许多模具企业观念落后,模具企业专业化生产水平低,专业化分工不细,商品化程度也低。
目前国内每年生产的模具,商品模具只占45%左右,其余为自产自用。
模具企业之间协作不好,难以完成较大规模的模具成套任务,第1章零件结构及工艺分析零件原始资料为:产品零件图如下图所示:设计要求:1 材料:ABS;2 生产批量:中等批量;3 未注公差取MT5级精度。
此零件既有通孔又含侧孔,但这一类侧孔可直接在开模方向上成型,不需要侧抽芯,所以此套模具结构比较简单,成型零件的设计主要考虑型心的嵌入式处理,也不太复杂。
根据零件的结构特点,拟定如下工艺方案进行比较分析。
1.1 分型面的选择分析零件结构可知,分型面应设在零件最大截面处,塑料包紧大型心并留在动模一侧。
1.2 型腔布局方案一:塑件中等尺寸,批量不大,采用一模一件可以降低模具成本。
方案二:一模两件对称布置,生产效率较高,但模具尺寸偏大,制造成本较一模一件高。
方案三:一模四件对称布置,生产效率较高,但模具尺寸更大,制造成本较高。
通过以上三种方案的分析比较,根据经济合理的原则,选择方案一最合适。
1.3 浇注系统设计方案一:采用侧浇口,从分型面进料,主流道过长,造成塑料的浪费,同时主流道偏离模具中心,造成压力中心偏移。
方案二:采用轮辐式浇口,从塑件上端孔进料,加工简单,浇口容易去除,不影响塑件外观,模具结构简单。
通过对以上两种设计方案的分析比较,采用第二种方案较好。
1.4 推出机构设计关于该模具的推出机构设计有两种方案可供选择。
方案一:推管推杆联合推出。
推出平稳,但机构复杂,制造与装配成本上升。
方案二:推件板推出。
此零件相对深度大,塑件包紧型芯的力很大,为了平稳顶出,在分型面处用推件板推出,这样塑件不容易发生顶出变形。
通过以上分析比较,方案二较好,故选之。
第2章产品造型设计此类零件虽然既含有通孔又含有侧孔,但零件整体结构并不复杂,根据任务书中所给零件二维图及相关尺寸要求,在保证满足使用要求的前提下,根据便于模具设计及生产制造的原则,产品造型过程如下:1、在Windows环境下,依次选择单击【开始】→【程序】→【NX3.0】→【NX3.0】命令,进入UG NX3.0的操作界面。
2、单击【新建】按钮,弹出【新部件文件】对话框,然后输入新文件名lianjiezuo,单位选择【毫米】,单击【OK】按钮。
3、在【应用程序】工具条中单击【建模】按钮,进入建模环境界面。
4、在【成型特征】工具条中单击【草图】按钮,进入二维草图绘制模块。
5、在悬浮的工具条中选择XC-ZC面,单击【确定】按钮,进行二维草图绘图。
6、绘出如下图所示的二维轮廓。
7、完成二维轮廓绘制后,单击【完成草图】按钮,返回实体编辑状态。
8、移动光标选择上步所绘制的轮廓呈高亮显示,然后在【成型特征】工具条中单击【回转体】按钮,通过旋转特征构建成实体,完成旋转特征后构建的实体如下图所示:9、在【成型特征】工具条中单击【草图】按钮,进入二维草图绘制模块。
10、在悬浮的工具条中选择XC-YC面,单击【确定】按钮,三维绘图区转为二维绘图状态,绘制草图轮廓。
11、完成轮廓绘制后,单击【完成草图】按钮,返回实体编辑状态。
12、移动光标选择上步绘制的轮廓呈高亮显示,然后在【成型特征】工具条中单击【拉深】按钮,在对话框中输入距离3,选择布尔运算并集,点击确定完成操作过程。
13、再次在【成型特征】工具条中单击【草图】按钮,进入二维草图绘制模块。
完成草绘,返回实体编辑状态。
14、移动光标选择上步绘制的轮廓呈高亮显示,然后在【成型特征】工具条中单击【拉伸】按扭,在对话框内选择合适的方向、距离、差集运算。
完成操作如图所示。
显示的线框图所示,是要达到的预期零件图。
15、显示可见轮廓线的效果图。
16、创建完成的连接座产品三维实体模型,零件着色,并隐藏面的边,最后的效果图如下。
至此,整个连接座产品造型设计完成,在【文件】工具栏中单击【保存】按钮,将构建的产品保存到文件夹中。
第3章连接座注塑模具设计U 例因子去补偿当冷却时产品材料的收缩。
UG3.0/Mold Wizard将所产生的放大后的产品造型命名为“Shrink part”,此造型将用于定义模具的型心和型腔。
收缩率的类型有三种:1均匀:按各方向都相同比例计算缩放,要求提供一个比例系数。
2轴对称:沿指定轴的轴向设一个比例值,另外两个方向设一个比例值。
3一般:沿X、Y、Z三个方向设定不同比例缩放。
要求提供三个比例系数。
任何时候都可以重新选择编辑比例按钮编辑收缩率。
单击收缩按钮,弹出编辑比例对话框,对零件设置收缩率,该模具中设定其收缩率为1.006。
3.4 设定工件成型镶件(Work Piece)/模型镶件(Mold Insert)是模具中的型心和型腔部分。
UG3.0/Mold Wizard用一个比产品体积略大的材料容积包容产品,通过分模工具使其成型,作为模具的型腔和型心。
单击工件按钮,弹出工件尺寸对话框,在对话框最上部列出四个选项:1 【标准长方体】:链接预先定义好的子块,以后通过分模将形成型腔面和型心面两部分。
2 【型腔和型心】:用户将毛坯定义为型腔和型心,UG3.0/Mold Wizard使用Wave 的方法链接建造实体。
3 【仅型腔】:定义用作型腔侧的毛坯。
4 【仅型心】:定义用作型心侧的毛坯。
根据本零件的结构特点,成功。
4在【分型管理器】中单击【创建型心和型腔】按钮,进行型心和型腔的创建。
5 在成功创建型心和型腔后,在【型心和型腔】对话框中点击【后退】按钮,再关闭【分型管理器】对话框。
3.6 添加模架UG3.0/Mold Wizard包含有电子表格驱动的模架库,模架库中的模架和标准件可以加入到模具的装配中,还可以依用户需要扩展这些库,进行客户化。
在模架库对话框中标准模架目录包含DME、Hasco、Futaba(公制)和Ommi (英制)等标准模架系列。
在这些目录中便可为模具选择一套合适的模架。
在选择模架时应为冷却系统和流道等留出空间。
模架索引列表中所示的尺寸是所选的标准模架在X-Y平面投影的有效尺寸,系统将根据多腔模布局确定最合适的尺寸作为默认选择。
在【注塑模向导】工具条中单击【模架】按钮,模架类型选择FUTABA-S并设置参数如图所示:完成操作过程后点击【确定】按钮,系统自动加载模架。
添加完成后的结果效果图如图所示:3.7添加标准部件单击标准件工具栏,打开【标准件管理】对话框,在此对话框中可以调用常用的各种模具标准件的参数库,可以在调出后进行适当的修改然后直接置入布局分型后的工作环境中形成模具装配结构。
在【Catalog】下拉列表中,列出相应的标准件类型冷却系统的具体设计过程如下:所有水道布置完成后的效果图如图所示。
为冷却水道的端部添加喉塞,添加完成喉塞的效果图如图所示。
为了防止模具漏水,需要添加防水垫圈,参照上面的步骤,添加防水圈,添加防水圈后的效果图所示。
添加型腔板的冷却水道,为操作方便,打开【装配导航器】,隐藏其余全部部件,只显示型腔板。
在型腔板上布置冷却水道与型腔上已经布置的水道相连接,实现冷却水的循环流动。
型腔板上冷却水道布置完成后的效果图如图所示。
继续单击【冷途径,实际上是产品质量、成本、设计周期等方面最有利的保证。
以波音公司为例,在数字化代表产品——波音777的展示中,不像以往那样重点宣传新型飞机本身性能如何优越,而是强调他们充分利用数字化研制技术以及产品研发人员的重新编队等方面。
波音777飞机项目顺利完成的关键是依赖三维数字化设计与综合设计队伍(238个Team)的有效实施,保证飞机设计、装配、测试以及试飞均在计算机上完成。
研制周期从过去的8年时间缩减到5年,其中虚拟装配的工程设计思想在研制过程中发挥了巨大的作用。
虚拟装配是指通过计算机对产品装配过程和装配结果进行分析和仿真,评价和预测产品模型,做出与装配相关的工程决策,而不需要实际产品作支持。
该技术是在虚拟设计环境下,完成对产品的总体设计进程控制并进行具体模型定义与分析的过程。
它可有效支持自顶向下的并行产品设计以及与Master Model相关的可制造性设计和可装配性设计,以缩短产品开发周期。
在许多世界级大企业中被广泛应用的计算机辅助三维设计(CAD)的高端主流软件UG(Unigraphics)的装配模块就采用了虚拟装配技术,即便是在产品设计的初期阶段,所产生的最初模型也可以放入虚拟环境进行实验,可以在虚拟环境中创建产品模型。