注塑模设计教程
UGNX MOLDWIZARD 注塑模设计实例教程

结果显示
19.对型芯型腔进行挖孔
对定模进行挖孔操作
调出型芯设置为静态线框模式
将冷却管道进出水口面WAVE出来
WAVE面2 WAVE面1
提取冷却管道中心线
中心线1 中心线2
选择导出IGES
导出冷却管道中心线IGES
选择线1 选择线2
将浇注系统设为工作部件
打开图层设置
显示所有对象
2
创建完成的结果
3
13. 选择标准模架
1 2
3
ห้องสมุดไป่ตู้
14.选择定位圈
1 2
15. 选择主流道衬套
16. 选择顶针
显示的结果
16. 修剪顶针
17. 进行冷却设计
选择冷却水道标准件
18. 进行流道设计—浇口
1 2
选择扇形浇口
进行分流道设计
1 2
选择定义流道的方式
3
选择两个点
4
生成分流道
UGNX4.0 MOLDWIZARD注塑模设计
LOGO
1. 装载part文件设置工程目录
1 2 3 4
2. 锁定Z轴坐标
1 2 3
3. 收缩率
1
2 3
4.设置Work Piece
1
2
5. 进行行腔布局
1 2
选择Auto Center
3
4
6. 分型
7. 进行补片
1
自动补片
2 3
8. 设置分型线
打开HSCAE3D
在数据管理器下新建一个零件phone
在零件Phone下新建一个分析方案
导入制品图形
打开充模设计模块
充模设计工具条
设计充模方向
注塑模具设计步骤(经典)

设计者:农文生
步骤2
【1】设计区域(之 后修补零件再分型)
【2】创建曲面补片 【3】编辑分型线段 【4】创建分型面 【5】创建型芯、型 腔 【6】型腔布局
步骤3
设计者:农文生
创建定位圈、 浇口套、流道 等
步骤4
说明:由于本塑造成品存在倒扣 现象故应设计滑块和斜顶机构
【滑块与顶料装置】
1创建滑块 2创建斜顶
设计者:农文生
பைடு நூலகம்
步骤5
【标准件管理】【顶杆】
1创建顶出系统
【冷却】
2创建冷却系统
(水嘴、冷却道、喉塞等)
设计者:农文生
整体效果 及 学习心得
细心+耐心+独 立思考+合作
设计者:农文生
谢
呼~呼、、完成任务、爬上去、嘻嘻!
谢 欣 赏
设计者:农文生
注射模具设计流程介绍
1总体设计思路分享 2基本设计步骤介绍 3整体效果及学习心得
设计者:农文生
总体设计思路分享
首先分析零件结构、分型、创建型芯型 腔,接着调用LKM-SG模架,然后创建定位 圈、浇口套、滑块、斜顶机构、顶出系统、 冷却系统等
设计者:农文生
基本设计步骤1
• 项目初始化、工件 • 在【注射模向导】工具条 中单击【项目初始化】按 钮,打开部件文件设置参 数及选项;调整WCS坐标 系,设计模具坐标 • 在【注射模向导】工具条 中单击【工件】在弹出的 【工件尺寸】对话框中设 置工件的参数及选项
第9章注塑模具设计
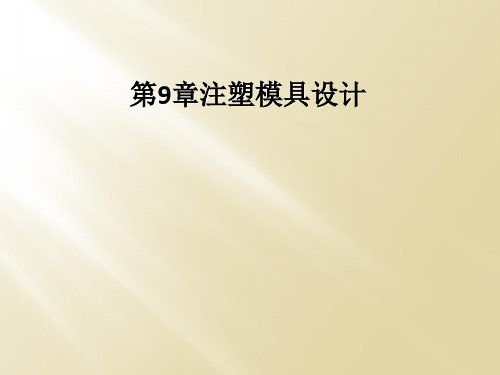
9.5 定义工件
• 工件是用来生成模具的型芯和型腔的实体,工件尺寸的确定以型芯任务9-1加载模型
根据图示的产品零件设置工件,完成产品模型的加载。
8
•
任务实施
1. 进入UG【建模】模块,打开源文件Chapter9/9.9.prt。 2. 进入【注塑模向导】设计模块。 3. 初始化项目 4. 设定模具坐标系 5. 定义工件
13
2. 实体修补 创建方块属于实体修补功能,主要用于填充未封闭的区域和简化产品模型。
14
9.9 分型设置
• 分型的目的是用
分型面将工件分开, 从而得到模具的 型芯和型腔。
15
9.10 注塑模高级应用功能 9.10.1 模架设置
• 模架是注塑模的骨架和基体,模具的各个组成部分都依附于模架之中。设计模具时应尽量选用合适
第9章注塑模具设计
9.1 进入注塑模向导模块
• 进入注塑模向导模块一般有以下两种方式:
1. 单击【标准】工具栏的 令。
按钮,在弹出的下拉菜单中选择【所有应用模块】/【注塑模向导】命
2. 单击如图9.1所示的【应用】工具栏中
的 按钮。
2
图9.1 【应用模块】工具栏
图9.2 【注塑模向导】工具栏 3
9.2 初始化项目
• 初始化项目命令可以设置创建模具装配的目录以及相关文件的名称,并载入需要进行模具设计的产
品零件,是使用注塑模向导模块进行模具设计的第一步。
4
9.3 定义模具坐标系
• 定义模具坐标系,就是将产品子装配从工作坐标系转移到模具装配的绝对坐标系,并以绝对坐标系
作为模具坐标系。
5
9.4 收缩率 收缩率是指塑件成型后尺寸的变动范围。
9
注塑模具设计操作流程
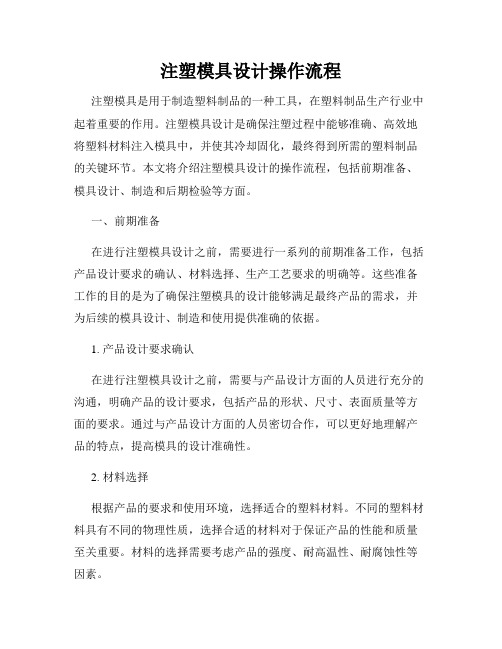
注塑模具设计操作流程注塑模具是用于制造塑料制品的一种工具,在塑料制品生产行业中起着重要的作用。
注塑模具设计是确保注塑过程中能够准确、高效地将塑料材料注入模具中,并使其冷却固化,最终得到所需的塑料制品的关键环节。
本文将介绍注塑模具设计的操作流程,包括前期准备、模具设计、制造和后期检验等方面。
一、前期准备在进行注塑模具设计之前,需要进行一系列的前期准备工作,包括产品设计要求的确认、材料选择、生产工艺要求的明确等。
这些准备工作的目的是为了确保注塑模具的设计能够满足最终产品的需求,并为后续的模具设计、制造和使用提供准确的依据。
1. 产品设计要求确认在进行注塑模具设计之前,需要与产品设计方面的人员进行充分的沟通,明确产品的设计要求,包括产品的形状、尺寸、表面质量等方面的要求。
通过与产品设计方面的人员密切合作,可以更好地理解产品的特点,提高模具的设计准确性。
2. 材料选择根据产品的要求和使用环境,选择适合的塑料材料。
不同的塑料材料具有不同的物理性质,选择合适的材料对于保证产品的性能和质量至关重要。
材料的选择需要考虑产品的强度、耐高温性、耐腐蚀性等因素。
3. 生产工艺要求明确在确定了产品的设计要求和材料选择之后,需要明确生产工艺要求。
生产工艺要求涉及到注塑过程中的各个环节,包括注塑机的选择、注塑温度的控制、注塑时间的控制等。
明确生产工艺要求可以帮助设计师更好地进行模具的设计。
二、模具设计模具设计是注塑模具设计操作流程中的核心环节,包括模具结构设计和模腔设计。
1. 模具结构设计模具结构设计是根据产品的形状和要求,确定模具的结构,包括模具的分模方式、模具的开合方式、配件的布置等。
模具结构设计需要考虑到产品的复杂性、生产效率等因素,确保模具能够满足生产需求。
2. 模腔设计模腔设计是模具设计的关键环节之一,是根据产品的形状和尺寸来确定模腔的形状和尺寸。
模腔的设计需要考虑到产品的收缩率、表面质量等因素,通过合理的模腔设计可以提高产品的成型质量。
注塑模具实用教程第8章注塑模结构件设计ppt课件
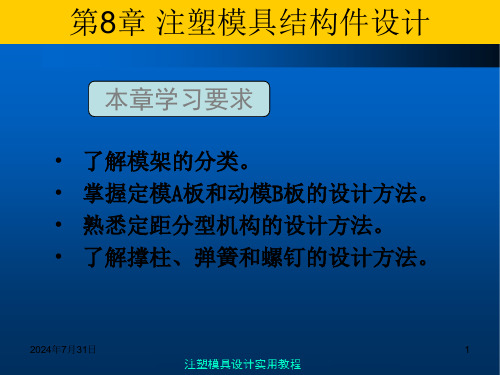
定模A板和动模B板的尺寸取决于内模镶件的外形尺寸,而内模 镶件的外形尺寸又取决于塑件的尺寸、结构特点和数量,内模镶 件设计详见第7章《注塑模具成型零件设计》。
从经济学的角度来看,在满足刚度和强度要求的前提下,模具 的结构尺寸越小越好。
确定定模A板和动模B板的尺寸常用计算法和经验法二种,在实 际工作过程中常用经验法。
2024年7月31日
20
第8章 注塑模具结构件设计
1.计算方法(相关公式见书) 2.经验确定法
模架长宽尺寸E和取决于内模镶件的长宽尺寸A和B,即A、B 板的开框尺寸。
2024年7月31日
21
第8章 注塑模具结构件设计
(1)A、B板的宽度尺寸确定。 一般来说在没有侧向抽芯
的模具中,模板开框尺寸A应大致等于模架推件固定板宽度尺寸C, 在标准模架中,尺寸C和E是一一对应的,所以知道尺寸A就可以 在标准模架手册中找到模架宽度尺寸E。
2024年7月31日
2
第8章 注塑模具结构件设计
8.1 概述
8.1.1 本章主要内容
• ① 模架的规格型号; • ② 动模板和定模板的设计; • ④ 方铁什么情况下要加高; • ⑤ 定距分型结构的设计; • ⑥ 撑柱的设计; • ⑦ 复位弹簧设计; • ⑧ 定位圈的设计; • ⑨ 紧固螺钉的设计。
2024年7月31日
29
第8章 注塑模具结构件设计
注意:① 表中的“A×B”和“框深a”均指动模板开框的长、 宽和深; ② 动模B板高度B等于开框深度a加钢厚Ha,向上取标准值 (公制一般为10的倍数); ③ 如果动模有侧抽芯,有滑块槽,或因推杆太多而无法加撑 柱时,须在表中数据的基础上再加5~10mm; ④动模板高度尽量取大些,以增加模具的强度和刚度。 动、定模板的长、宽和高度尺寸都已标准化,设计时尽量取 标准值,避免采用非标模架。
注塑模具设计教程

注塑模具设计教程
注塑模具设计是一门复杂而重要的技术,它是注塑加工过程中最关键的环节。
下面我将为大家简单介绍一下注塑模具设计的基本步骤和注意事项。
注塑模具设计的基本步骤主要包括产品设计、模具结构设计和模具零件设计。
首先,产品设计是整个模具设计的起点,要根据产品的功能和外观要求确定产品的形状、尺寸等参数,这对后续的模具设计非常重要。
其次,模具结构设计是指模具的整体结构,包括模具的开合方式、冷却系统、排气系统等,要根据产品的形状和工艺要求来确定模具结构,以保证产品的质量和生产效率。
最后,模具零件设计是指模具的各个零部件,如模具芯、模具腔、导向机构等,这些零部件要满足产品的形状和工艺要求,并能在生产过程中正常运行。
在注塑模具设计过程中,还需要注意以下几点。
首先,要考虑产品的特点和所用材料的性质,如产品的壁厚、缩水率、线收缩率等,以及材料的熔点、流动性等,这些因素会影响到模具的结构设计和零件设计。
其次,要合理选择模具材料,一般情况下,模具材料应具有高硬度、高强度和耐磨损等特点,以提高模具的寿命和使用效果。
再次,要注意模具的冷却系统设计,合理设置冷却水道,以提高产品的质量和生产效率。
最后,要考虑模具的制造工艺,合理划分工序和加工方法,以确保模具的加工精度和质量。
总之,注塑模具设计是一门复杂而重要的技术,它直接关系到产品的质量和生产效率。
通过合理的产品设计、模具结构设计
和模具零件设计,可以提高产品的质量和生产效率,降低成本,为企业带来更大的利益。
同时,在注塑模具设计过程中还要考虑产品特点、材料性质、模具材料选择、冷却系统设计和制造工艺。
希望以上内容可以对注塑模具设计有所帮助。
注塑模具设计和制造设备操作流程

注塑模具设计和制造设备操作流程注塑模具在塑料制品生产中扮演着至关重要的角色。
为了确保模具设计和制造的质量和效率,操作流程的规范化是必不可少的。
本文将介绍注塑模具设计和制造设备的操作流程,并对每个步骤进行详细的说明。
一、模具设计模具设计是注塑模具制造的第一步,它直接影响着后续的制造和使用效果。
一个好的设计可以提高模具的寿命、提高生产效率和产品质量。
以下是模具设计的操作流程:1. 确定产品要求:在进行模具设计之前,首先需要明确所需产品的要求,包括尺寸、形状、材料等。
2. 绘制产品图纸:根据产品要求,使用计算机辅助设计(CAD)软件或手工绘图,绘制产品的详细图纸,并标注尺寸和标准。
3. 设计模具结构:根据产品图纸,设计模具的整体结构,包括模具底板、模具腔、模具芯等。
考虑到产品的成型工艺和操作要求,合理设计模具的开合方式和冷却系统。
4. 模具零件设计:根据模具结构设计,细化模具的各个零件,如模具底板、模具腔、模具芯、滑块、顶针等。
确定零件的尺寸和标准。
5. 检查和修正设计:完成模具设计后,进行设计的检查和修正,确保设计的准确性和完整性。
二、模具制造模具制造是根据设计图纸和要求,使用各种设备和工艺加工制造模具的过程。
以下是模具制造的操作流程:1. 材料准备:根据模具设计要求,选择适合的模具材料。
常见的模具材料包括工具钢、合金钢等。
对于特殊要求的模具,可能需要进行材料的热处理等。
2. 加工粗加工:根据模具设计要求,进行模具的粗加工。
粗加工主要包括锯切、铣削、钻孔等工序,将原始材料加工成近似形状的模具零件。
3. 细加工:对已经进行粗加工的模具零件进行细加工。
细加工包括铣削、镗孔、磨削等工序,对模具零件进行精确的加工,以满足设计要求。
4. 组装和调试:将所有的模具零件进行组装,并进行调试。
调试包括模具的开合性能测试、冷却系统的检查等。
5. 表面处理:根据需要,对模具进行表面处理。
常见的表面处理方式包括镀铬、热处理等,以提高模具的硬度和耐磨性。
注塑模具设计与制造教程

03
注塑模具结构设计
分型面设计技巧及注意事项
分型面选择原则
确保产品顺利脱模,减少溢料和 飞边,简化模具结构。
分型面设计要点
分型面应位于产品断面轮廓最大 的地方,便于脱模;避免在分型 面上设计小孔或凹槽,防止溢料 和飞边;分型面的设计应便于模
具的加工和装配。
注意事项
分型面的选择应避免影响产品的 外观和性能;对于复杂的产品, 可能需要采用多个分型面进行脱
性能要求
模具材料应具有良好的切削加工性、热处理稳定 性、耐磨性、耐腐蚀性和抗疲劳性等性能。
精度与表面质量要求
精度要求
根据产品精度要求,确定模具的制造 精度和装配精度,保证产品的尺寸精 度和形位公差。
表面质量要求
模具表面应平整、光滑,无裂纹、毛 刺等缺陷;分型面、型腔等重要表面 应达到一定的粗糙度要求,以保证产 品的外观质量和脱模顺畅。
分类
根据模具的结构和使用特点,注塑模具可分为单分型面 注塑模、双分型面注塑模、带有侧向分型与抽芯机构的 注塑模以及热流道注塑模等。
注塑模具结构组成
导向部件
浇注系统
由主流道、分流道、浇口和冷料 穴等组成,用于将熔融的塑料从 注塑机喷嘴引入模具型腔。
包括导柱、导套等,用于保证动 模和定模在合模时的相对位置精 度。
压力调整技巧及常见问题解决方案
压力调整技巧
注射压力、保压压力和背压是注塑成型过程中的关键压力参数。 根据产品的结构、壁厚和塑料的流动性,合理调整这些压力参 数,以确保塑料充分填充模具并补偿收缩。
常见问题解决方案
针对飞边、短射、缩水等常见问题,通过调整注射速度、保压 时间和压力分布等参数,可以有效改善产品质量。
加工工艺流程梳理与规范操作指南
注塑模具设计流程
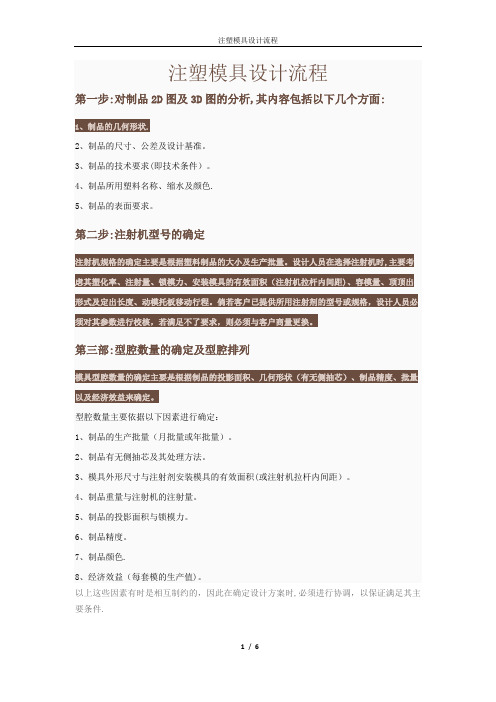
注塑模具设计流程第一步:对制品2D图及3D图的分析,其内容包括以下几个方面:1、制品的几何形状.2、制品的尺寸、公差及设计基准。
3、制品的技术要求(即技术条件)。
4、制品所用塑料名称、缩水及颜色.5、制品的表面要求。
第二步:注射机型号的确定注射机规格的确定主要是根据塑料制品的大小及生产批量。
设计人员在选择注射机时,主要考虑其塑化率、注射量、锁模力、安装模具的有效面积(注射机拉杆内间距)、容模量、顶顶出形式及定出长度、动模托板移动行程。
倘若客户已提供所用注射剂的型号或规格,设计人员必须对其参数进行校核,若满足不了要求,则必须与客户商量更换。
第三部:型腔数量的确定及型腔排列模具型腔数量的确定主要是根据制品的投影面积、几何形状(有无侧抽芯)、制品精度、批量以及经济效益来确定。
型腔数量主要依据以下因素进行确定:1、制品的生产批量(月批量或年批量)。
2、制品有无侧抽芯及其处理方法。
3、模具外形尺寸与注射剂安装模具的有效面积(或注射机拉杆内间距)。
4、制品重量与注射机的注射量。
5、制品的投影面积与锁模力。
6、制品精度。
7、制品颜色.8、经济效益(每套模的生产值)。
以上这些因素有时是相互制约的,因此在确定设计方案时,必须进行协调,以保证满足其主要条件.型腔数量确定之后,便进行型腔的排列,以及型腔位置的布局。
型腔的排列涉及模具尺寸、浇注系统的设计、浇注系统的平衡、抽芯(滑块)机构的设计、镶件型芯的设计以及热流道系统的设计。
以上这些问题由于分型面及浇口位置的选择有关,所以在具体设计过程中,要进行必要的调整,以达到最完美的设计。
第四步:分型面的确定分型面,在一些国外的制品图中已作具体规定,但在很多的模具设计中要由模具人员来确定,一般来讲,在平面上的分型面比较容易处理,有时碰到立体形式的分型面就应当特别注意.其分型面的选择应遵照以下原则:1、不影响制品的外观,尤其是对外观有明确要求的制品,更应注意分型面对外观的影响.2、利于保证制品的精度。
ug注塑模具设计教程

ug注塑模具设计教程UG注塑模具设计是一种CAD软件,广泛应用于注塑模具的设计和制造过程中。
它具有强大的功能和灵活性,可以帮助工程师快速、高效地进行模具设计。
下面是一个简单的UG注塑模具设计教程,帮助初学者了解基本操作和流程。
首先,需要打开UG软件,然后选择创建新文件。
接下来,在顶部菜单栏中选择“文件”->“新建”->“零件”。
然后,选择适当的单位制和零件模板,点击“确认”。
接着,我们需要绘制模具的零部件轮廓。
在左侧的工具栏中选择适当的绘图工具,如线段、圆等,根据设计要求绘制模具的外形。
可以使用各种绘图和编辑工具对零件进行修整和调整。
完成零部件的绘制后,可以选择进行参数化建模。
这就是给零件添加尺寸和约束,并通过修改尺寸值来实现模具的形状调整。
参数化建模是UG的一个重要特性,它可以帮助设计师在设计过程中灵活地进行修改和优化。
接下来,我们可以对零件进行三维建模。
选择适当的工具,如拉伸、旋转、挤压等,根据需要将零件的二维轮廓转化为三维实体。
可以使用各种操作如修整、倒角等对模具进行进一步的完善和优化。
完成零部件的三维建模后,可以创建装配体。
选择菜单栏中的“装配体”选项,将各个零部件放置在正确的位置上,并设置适当的装配关系和约束。
这样可以模拟模具在实际使用过程中的动作和关系,方便进行后续的设计和分析。
最后,可以进行模具的细节设计和分析。
可以使用菜单栏中的各种工具和功能,如切削、填充、检查等,对模具进行进一步的细化和检验。
可以生成模具的图纸,并导出相关文件以供制造和生产使用。
UG注塑模具设计教程中还涉及很多其他的工具和功能,这里只是简单介绍了基本操作流程。
初学者可以通过学习和实践,逐渐掌握UG软件的使用技巧和方法。
在实际的模具设计中,还需要结合具体的需求和制造工艺进行综合考虑和优化。
希望这个简单的UG注塑模具设计教程能够对初学者有所帮助。
完整版注塑模具设计步骤
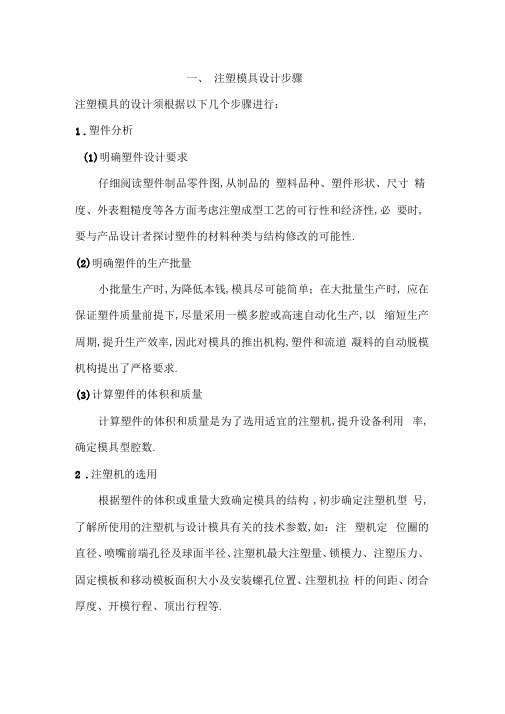
一、注塑模具设计步骤注塑模具的设计须根据以下几个步骤进行:1.塑件分析(1)明确塑件设计要求仔细阅读塑件制品零件图,从制品的塑料品种、塑件形状、尺寸精度、外表粗糙度等各方面考虑注塑成型工艺的可行性和经济性,必要时,要与产品设计者探讨塑件的材料种类与结构修改的可能性.(2)明确塑件的生产批量小批量生产时,为降低本钱,模具尽可能简单;在大批量生产时, 应在保证塑件质量前提下,尽量采用一模多腔或高速自动化生产,以缩短生产周期,提升生产效率,因此对模具的推出机构,塑件和流道凝料的自动脱模机构提出了严格要求.(3)计算塑件的体积和质量计算塑件的体积和质量是为了选用适宜的注塑机,提升设备利用率,确定模具型腔数.2.注塑机的选用根据塑件的体积或重量大致确定模具的结构 ,初步确定注塑机型号,了解所使用的注塑机与设计模具有关的技术参数,如:注塑机定位圈的直径、喷嘴前端孔径及球面半径、注塑机最大注塑量、锁模力、注塑压力、固定模板和移动模板面积大小及安装螺孔位置、注塑机拉杆的间距、闭合厚度、开模行程、顶出行程等.(1)凹、凸模零件工作尺寸的计算;(2)型腔壁厚、底板厚度的计算;(3)模具加热、冷却系统有关参数的计算.4.模具结构设计(1)塑件在模具中摆放位置及分型面选择;(2)模具型腔数确实定,型腔的排列方式等;(3)模具浇注系统的设计,包括流道布置以及浇口类型、大小及位置确实定;(4)模具成型零件的结构设计,主要是成型零件的结构形式;(5)制件推出机构设计;(6)侧分型与抽芯机构的设计(如需要的话);(7)排气方式设计;⑹模具总体尺寸确实定,选购模架.模架已逐渐标准化,根据生产厂家提供的模架图册,选定模架,在以上模具零部件设计根底上初步绘出模具的完整结构图.5.注塑机参数的校核(1)最大注塑量的校核;(2)注塑压力的校核;(3)锁模力的校核;(4)模具与注塑机安装局部相关尺寸校核,包括闭合高度、开模行程、模座安装尺寸等几个方面的相关尺寸校核.模具总图绘制必须符合机械制图国家标准,其画法与一般机械图画法原那么上没有区别,只是为了更清楚地表达模具中成型制品的形状、浇口位置的设置,在模具总图的俯视图上,可将定模拿掉,而只画动模局部的俯视图.模具总装图应包括必要尺寸,如模具闭合尺寸、外形尺寸、特征尺寸〔与注塑机配合的定位环尺寸〕,装配尺寸、极限尺寸〔活动零件移动起止点〕及技术条件,编写零件明细表等.通常主要工作零件加工周期较长,加工精度较高,因此应首先认真绘制,而其余零部件应尽量采用标准件.实际上,以上设计步骤并不是独立的,而是互相牵制的,在设计中应随时根据出现的不合理结构及时调整.7.全面审核投产制造模具设计员一般应参与加工、组装、试模、投产的全过程.8.模具安装及试模步骤〔1〕模具安装1〕清理模板平面定位孔及模具安装面上的污物、毛刺.2〕如果模具外形尺寸不大,可采用整体安装法.先在机器下面两根导轨上垫好板,模具从侧面进入机架间,定模入定位孔,并放正, 慢速闭合模板,压紧模具,然后用压板或螺钉压紧定模,并初步固定动模,然后慢速开闭模具,找正动模,应保证开闭模具时平稳、灵活, 无卡住现象,然后固定动模.3〕调节锁模机构,保证有足够开模距及锁模力,使模具闭适宜当4〕慢速开启模板直至模板停止后退为止,调节顶出装置,保证顶出距离.开闭模具观察顶出机构运动情况,动作是否平衡、灵活、协调.5〕模具装好后,待料筒及喷嘴温度上升到距离预定温度20〜30C,即可校正喷嘴浇口套的相对位置及弧面接触情况,可用一纸片放在喷嘴与浇口套之间,观察两者接触印痕,检查吻合情况 ,须使松紧适宜,校正后拧紧注射座定位螺钉,紧固定位.6〕开空车运转,观察模具各局部运行是否正常,然后才可注射试模.〔2〕试模试模时,塑件上常可能会出现各种弊病,为此必须进行原因分析、排除故障.造成次、废品的原因很多,有时是单一的,但经常是多方面综合的原因.需按成型条件、成型设备、模具结构及制造精度、塑件结构及形状等因素逐个分析找出其中主要矛盾,然后再采取调节成型工艺参数、修整模具等方法加以解决.。
注塑模具设计和制造操作流程

注塑模具设计和制造操作流程注塑模具是在工业生产中广泛应用的一种工具,它用于制造各种形状的塑料零件。
在注塑模具设计和制造的操作流程中,需要经历多个步骤和环节,以确保最终的产品符合要求。
本文将详细介绍注塑模具设计和制造的操作流程。
1. 需求分析在开始注塑模具设计和制造之前,首先需要进行需求分析。
这包括与客户的沟通和了解客户对产品的要求。
在需求分析阶段,需要明确产品的尺寸、材料、颜色等方面的要求,以及产品将用途和预期使用寿命。
这些要求将为后续的模具设计和制造提供指导。
2. 设计草图在需求分析完成后,设计师将根据客户的要求和产品的特点绘制设计草图。
设计草图应准确反映产品的形状、结构和尺寸,并考虑到注塑成型的特点和要求。
在设计草图中,设计师通常会标注模具的尺寸、孔洞位置和活动部件的设计等重要信息。
3. 三维建模基于设计草图,设计师使用计算机辅助设计(CAD)软件进行三维建模。
三维建模可以更加直观地显示产品的形状和结构,同时可以进行尺寸调整和碰撞检测等操作。
设计师需要熟练掌握CAD软件的使用,以实现精确的模具设计。
4. 模具加工在完成三维建模后,进入模具加工环节。
模具加工通常包括数控加工、车铣加工、电火花加工等多个工艺。
根据设计要求,将选用合适的材料,并进行精密加工,以确保模具的尺寸和质量符合要求。
模具加工需要经验丰富的技术人员和高精度的加工设备的支持。
5. 组件装配模具加工完成后,需要进行各个零部件的组装。
这包括模具的固定板、活动板、导柱、导套、顶针等部件的安装和调试。
组装过程需要严格按照设计要求进行,以确保模具的运行和操作的顺畅性。
6. 试模和调试模具组装完成后,进行试模和调试。
在试模过程中,将注入塑料材料,并观察成型情况,如产品的尺寸、表面质量等。
如果发现问题,需要进行相应的调整和修正,以使产品达到客户的要求。
试模和调试过程可能需要多次重复,直到达到符合要求的效果为止。
7. 批量生产完成试模和调试后,模具可以投入批量生产。
注塑成型模具设计操作流程
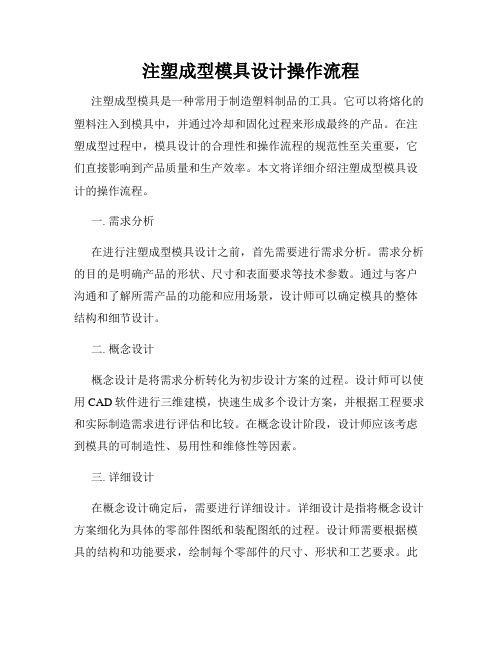
注塑成型模具设计操作流程注塑成型模具是一种常用于制造塑料制品的工具。
它可以将熔化的塑料注入到模具中,并通过冷却和固化过程来形成最终的产品。
在注塑成型过程中,模具设计的合理性和操作流程的规范性至关重要,它们直接影响到产品质量和生产效率。
本文将详细介绍注塑成型模具设计的操作流程。
一. 需求分析在进行注塑成型模具设计之前,首先需要进行需求分析。
需求分析的目的是明确产品的形状、尺寸和表面要求等技术参数。
通过与客户沟通和了解所需产品的功能和应用场景,设计师可以确定模具的整体结构和细节设计。
二. 概念设计概念设计是将需求分析转化为初步设计方案的过程。
设计师可以使用CAD软件进行三维建模,快速生成多个设计方案,并根据工程要求和实际制造需求进行评估和比较。
在概念设计阶段,设计师应该考虑到模具的可制造性、易用性和维修性等因素。
三. 详细设计在概念设计确定后,需要进行详细设计。
详细设计是指将概念设计方案细化为具体的零部件图纸和装配图纸的过程。
设计师需要根据模具的结构和功能要求,绘制每个零部件的尺寸、形状和工艺要求。
此外,在详细设计中还需要考虑模具的引导装置、冷却系统和排气系统等细节。
四. 材料选择材料选择是注塑成型模具设计中的重要环节。
设计师需要根据产品的特性、生产批量和经济性等因素选择合适的模具材料。
常用的模具材料有工具钢、不锈钢和铝合金等。
不同材料具有不同的强度、硬度和耐磨性,设计师需要根据具体情况进行选择。
五. 制造加工制造加工是将设计好的模具图纸转化为实际模具的过程。
通常情况下,制造加工包括数控加工、切割和铣削等工艺。
在制造过程中,需要严格按照图纸要求进行操作,并采取适当的质量控制措施,以确保模具的制造精度和表面质量。
六. 装配调试在模具制造完成后,需要进行装配调试。
装配调试的目的是验证模具的正确性和可靠性。
设计师和制造人员需要对模具进行全面检查,确保每个零部件的安装位置正确,加工尺寸符合要求,并进行必要的调整和修正。
ug注塑模具设计实例教程
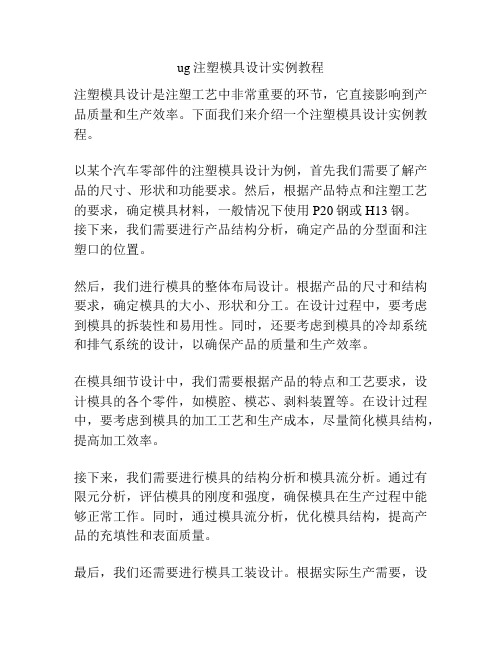
ug注塑模具设计实例教程
注塑模具设计是注塑工艺中非常重要的环节,它直接影响到产品质量和生产效率。
下面我们来介绍一个注塑模具设计实例教程。
以某个汽车零部件的注塑模具设计为例,首先我们需要了解产品的尺寸、形状和功能要求。
然后,根据产品特点和注塑工艺的要求,确定模具材料,一般情况下使用P20钢或H13钢。
接下来,我们需要进行产品结构分析,确定产品的分型面和注塑口的位置。
然后,我们进行模具的整体布局设计。
根据产品的尺寸和结构要求,确定模具的大小、形状和分工。
在设计过程中,要考虑到模具的拆装性和易用性。
同时,还要考虑到模具的冷却系统和排气系统的设计,以确保产品的质量和生产效率。
在模具细节设计中,我们需要根据产品的特点和工艺要求,设计模具的各个零件,如模腔、模芯、剥料装置等。
在设计过程中,要考虑到模具的加工工艺和生产成本,尽量简化模具结构,提高加工效率。
接下来,我们需要进行模具的结构分析和模具流分析。
通过有限元分析,评估模具的刚度和强度,确保模具在生产过程中能够正常工作。
同时,通过模具流分析,优化模具结构,提高产品的充填性和表面质量。
最后,我们还需要进行模具工装设计。
根据实际生产需要,设
计各种模具工装,如模修边装置、自动脱模装置等,以提高生产效率和产品质量。
总之,注塑模具设计是一个复杂而细致的过程,需要综合考虑产品的特点、工艺要求和生产成本。
通过合理的设计,可以提高产品的质量和生产效率,降低生产成本,为企业创造更大的利润空间。
希望以上的注塑模具设计实例教程对您有所帮助。
塑料注射模具设计PPT课件

(a)
图 4-26 主流道
(b)
2008年3月6日
第三节 浇注系统的设计
四、主流道设计与制造
定位环与浇口套的关系
图 4-27 定位环与浇口套
2008年3月6日
(4)浇口套常采用标准件,材料取45钢,装配后的加工。
2008年3月6日
四 分流道设计
作用:使塑料熔体的流向得到平稳的转换并尽快 地充满型腔。
26.04.2021
第二节 塑件在模具中的位置设计
三、分型面的选择原则
有利于保证塑件质量
图 4-6 分型面的选择
尽量减少塑件在分型面上的投影面积
26.04.2021
第二节 塑件在模具中的位置设计
三、分型面的选择原则
有利于保证塑件质量
图 4-7 分型面的选择
要满足塑件的精度要求,比如同心度、同轴度、平行度等等
品外观、尺寸精度、物理性能和成型效率。
浇口过小:易造成充填不足(短射)、收缩凹陷、熔接痕等
外观上的缺陷,且成型收缩会增大。
浇口过大:浇口周围产生过剩的残余应力,导致产品变形
或破裂,且浇口的去除加工困难等。
2008年3月6日
2.浇口的类型及特点: 1)直接浇口(主流道型浇口):
直接浇口广泛应用于单型腔模具
1.主流道:把塑料熔体引入模具。 2.分流道:平稳地转向和分流 3.浇口:流道中最狭小的部分 作用:①调节、控制料流速度 ②调节、控制补缩时间 ③防倒流 4.冷料穴:储存冷料,防止冷料进入型腔。 ①堵塞浇口 ②影响塑件质量 浇注系统的设计是否适当,直接影响成型品的外观、物性、 尺寸精度和成型周期。
三、分型面的选择原则
分型面的选择要有利于简化模具结构
圆柱齿轮的注塑模设计
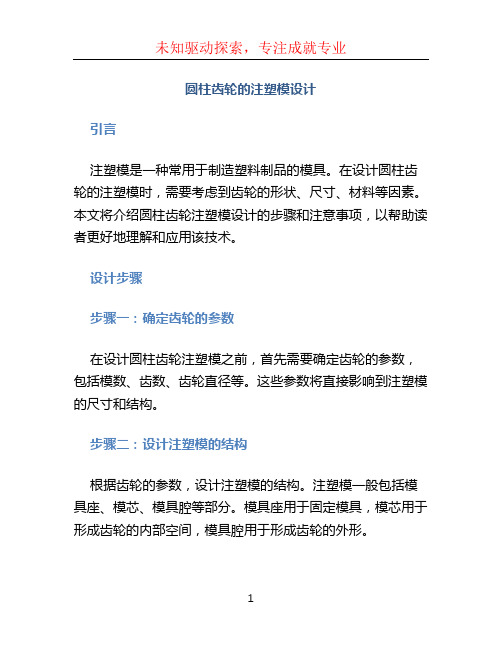
圆柱齿轮的注塑模设计引言注塑模是一种常用于制造塑料制品的模具。
在设计圆柱齿轮的注塑模时,需要考虑到齿轮的形状、尺寸、材料等因素。
本文将介绍圆柱齿轮注塑模设计的步骤和注意事项,以帮助读者更好地理解和应用该技术。
设计步骤步骤一:确定齿轮的参数在设计圆柱齿轮注塑模之前,首先需要确定齿轮的参数,包括模数、齿数、齿轮直径等。
这些参数将直接影响到注塑模的尺寸和结构。
步骤二:设计注塑模的结构根据齿轮的参数,设计注塑模的结构。
注塑模一般包括模具座、模芯、模具腔等部分。
模具座用于固定模具,模芯用于形成齿轮的内部空间,模具腔用于形成齿轮的外形。
步骤三:考虑齿轮的顶隙和侧隙在注塑模设计过程中,需要考虑齿轮的顶隙和侧隙。
顶隙用于确保齿轮齿宽方向有足够的空间,侧隙用于确保齿轮齿高方向有足够的空间。
合理的顶隙和侧隙设计可以提高齿轮的精度和耐磨性。
步骤四:确定注塑模的开模方式根据齿轮的形状和尺寸,设计合适的注塑模开模方式。
常用的开模方式包括斜顶开模、平顶开模等。
合适的开模方式可以提高注塑成型的效果和产品质量。
步骤五:设计注塑模的冷却系统注塑模的冷却系统是确保注塑成型过程中齿轮能够快速冷却和固化的关键部分。
合理设计冷却系统可以提高齿轮的表面质量和尺寸精度。
步骤六:设计注塑模的排气系统在注塑成型过程中,需要排除模腔和模芯之间的空气,以避免产生气泡和缺陷。
设计合理的排气系统可以确保齿轮成型过程中没有气泡和缺陷。
步骤七:设计注塑模的射出系统注塑模的射出系统是将熔融塑料注入模具腔和模芯的关键部分。
射出系统的设计需要考虑到射出压力、注塑速度等因素,以保证齿轮成型的效果和质量。
步骤八:进行模具结构优化完成注塑模的初步设计后,需要对其进行结构优化。
通过优化模具的结构,可以提高齿轮的精度、品质和生产效率。
注意事项在进行圆柱齿轮注塑模设计时,还需要注意以下几点:1.根据齿轮的功能和使用条件,选择合适的材料。
常用的注塑模材料包括钢材、铝材等。
2.设计注塑模时要考虑到齿轮的装配和拆卸方便性。
- 1、下载文档前请自行甄别文档内容的完整性,平台不提供额外的编辑、内容补充、找答案等附加服务。
- 2、"仅部分预览"的文档,不可在线预览部分如存在完整性等问题,可反馈申请退款(可完整预览的文档不适用该条件!)。
- 3、如文档侵犯您的权益,请联系客服反馈,我们会尽快为您处理(人工客服工作时间:9:00-18:30)。
注塑模设计教程·补充教程:注塑模具设计03标准模架MoldWizard有电子表格驱动的标准件库,这些库可被客户化,还可以依据用户的需要来扩展这些库以满足特殊的需求。
MW模块的标准件库中包含有模架库和标准件。
如何合理的选用模架及标准件,这是每个设计者必须面对的问题,因此需要先了解模架及标准件的相关知识。
标准模架分为两大类:大型模架和中小型模架。
两种模架的主要区别在于适用范围。
中小型模架的尺寸为B×L≤500mm×900mm,而大型模架的尺寸B×L为630mm×630mm~1250mm×20XXmm。
UG7【模架设计】对话框如图1所示。
图1在目录下拉菜单可以选择UG自带的标准模架供应厂商。
【目录】栏下拉列表显示被 Mold Wizard 选录的生产制造标准模架和标准件,包括四家世界著名公司的名称:美国DME 公司、德国 HASCO 公司、日本 FUTABA 公司、香港 LKM 公司。
选择其中一家公司牌号,【模架管理】对话框就显示该牌号系列标准模架。
【UNIVERSAL】选项是按实际需要自己配置模架模板尺寸。
日本FUTABA 公司的模架结构形式精炼,而且种类也多,标准模架如何选用就用 FUTABA 牌号模架进行介绍。
在【目录】栏下拉列表选择“FUTABA_S”,类型中选择“SB”, 如表1所示。
图2下面以FUTABA模架管理对话框为例:1)【目录】FUTABA模架分FUTABA_S、FUTABA_DE、FUTABA_FG、FUTABA_H四个分类,前三个分类又分为小型高强度模架和中小型模架,小型高强度模架用后缀区分。
2)【类型】显示指定供应商提供的标准模架类型号,每一个代号表示一种模架结构。
见表1所示为FUTABA的各系列。
3)示图区:显示所选模架的结构示意图、导柱放置位置和推杆与推板固定形式示意图。
4)模板尺寸显示窗:显示所选模架的系列标准模板在X-Y平面投影的有效尺寸,该窗口用来选择模板大小,系统根据模具的布局确定最适合的尺寸作为默认选择。
5)布局信息窗:显示成型零件尺寸。
6)模架组件选择窗:显示组成模架零件的尺寸表达式,用来选择模架零件。
模架组件部分名称见表2所示。
表1表27)模架组件尺寸表达式栏:用来设置和修改模架零件形状尺寸。
在模架组件选择窗选择的零件能在模架组件尺寸表达式栏显示,表达式栏设置非标尺寸数值,按 Enter 键,模架组件选择窗相应组件尺寸作相应改变。
8)模板尺寸设置区:用来设置模架主要模板厚度尺寸等其他结构参数。
模板尺寸设置区数据含义举例如下: AP_h表示定模A 板高度; BP_h 表示动模 B 板高度; CP_h表示垫块 C 板高度。
TW 栏选择 175:X 表示导柱安装在动模侧,选择175 : Z 表示导柱安装在定模侧, 450 表示定、动模座板窄的宽度;550 表示定、动模座板宽的宽度;U_h栏30: V、 40 : W表示支承板两种可供选择的高度,具体数值表示支承板的高度。
图39)xx图标:图标区有模架xx数据库图标、旋转成型零件图标等。
模架安装定位时模架宽度方向与模具坐标系 x 轴方向一致,在设置模具坐标系 x 轴方向时如果忘记调整成型零件宽度方向与 X 轴方向一致,可使用旋转图标旋转成型零件,使成型零件宽度方向和模架宽度方向与 X 轴方向一致。
一、FUTABA大水口标准模架图4 基本结构分类代号中的字母含义:A表示“有承板无推板”;B 表示“有承板有推板”;C表示“无承板无推板”;D表示“无承板有推板”。
图5 有承板无推板图6 有承板有推板图7 无承板无推板图8 无承板有推板细水口标准模架图9 细水口标准模架分有:D型和E型。
其中D型小水口有脱料板的,又分为DA、DB、DC、DD。
E型小水口无脱料板的,又分为EA、EB、EC、ED。
简化细水口标准模架有FA、FC和GA、GC图10F是有脱料板;G是无脱料板。
二、龙记大水口标准模架图11代号字母含义:A表示有托板;B表示有托板与推板;C表示无托板与推;D表示有推板。
I为工字模;H为直身模;T为直身模加面板。
细水口标准模架图12代号字母含义:D为有水口推板;A~D含义同上; E为无水口推板。
I 和H含义。
三、国标标准模架中、小型标准模架代号分A1~A4图13中、小型标准模架代号分P1~A9图14大型标准模架代号分A、B图15大型标准模架代号分P1~P4图16选用标准模架的过程选用标准模架的过程包括以下几个方面:根据制品图样及技术要求,分析、计算、确定制品类型、尺寸范围、壁厚、孔形及孔位、尺寸精度及表面性能要求、材料性能等,以便制订制品成形工艺、确定浇口位置、制品重量以及模具的型腔数目,并选定注射机的型号及规格。
选定的注射机应满足制品注射量和注射压力的要求。
确定模具分型面、浇口结构形式、脱模和抽芯方式与结构,根据模具结构类型和尺寸组合系列来选定所需的标准模架。
核算所选定的模架在注射机上的安装尺寸要素及型腔的力学性能,保证注射机和模具能相互协调。
模架规格的选择模架规格的确定往往取决于模仁大小。
模架模板厚度与模仁尺寸之间的关系,如图17所示。
图17MW模式下的模架加载在MoldWizard模式下,模架的加载变得很简便,初始化后的模型设置了模具坐标系,模架则以模具坐标系为参照基准来进行加载、装配。
同样以一个实例例来说明初始化项目的模架加载过程。
操作步骤如下:图18图19图27 下面试修改曲面补片。
如图28 a)~c)所示,删除认为不合格的补片。
如图29所示重新补片:先网格曲面补,再用现有曲面加载。
重新分割型腔和型芯,成功,结果如图30所示。
6)创建滑块①打开型腔文件;②拉伸体1;③拉伸体2与拉伸体1合并;④与型腔求交,保留目标;⑤将滑块转化为型腔子零件;⑥创建求差以生成型腔切口。
a)b)c)图28 删除不合格曲面补片a)b)图29型腔型芯图30图31 拉伸体1图32 拉伸钵2的草图a)b)图33 拉伸体2·补充教程:注塑模具设计03标准模架MoldWizard有电子表格驱动的标准件库,这些库可被客户化,还可以依据用户的需要来扩展这些库以满足特殊的需求。
MW模块的标准件库中包含有模架库和标准件。
如何合理的选用模架及标准件,这是每个设计者必须面对的问题,因此需要先了解模架及标准件的相关知识。
标准模架分为两大类:大型模架和中小型模架。
两种模架的主要区别在于适用范围。
中小型模架的尺寸为B×L≤500mm×900mm,而大型模架的尺寸B×L为630mm×630mm~1250mm×20XXmm。
UG7【模架设计】对话框如图1所示。
图1在目录下拉菜单可以选择UG自带的标准模架供应厂商。
【目录】栏下拉列表显示被 Mold Wizard 选录的生产制造标准模架和标准件,包括四家世界著名公司的名称:美国DME 公司、德国 HASCO 公司、日本 FUTABA 公司、香港 LKM 公司。
选择其中一家公司牌号,【模架管理】对话框就显示该牌号系列标准模架。
【UNIVERSAL】选项是按实际需要自己配置模架模板尺寸。
日本FUTABA 公司的模架结构形式精炼,而且种类也多,标准模架如何选用就用 FUTABA 牌号模架进行介绍。
在【目录】栏下拉列表选择“FUTABA_S”,类型中选择“SB”, 如表1所示。
图2下面以FUTABA模架管理对话框为例:1)【目录】FUTABA模架分FUTABA_S、FUTABA_DE、FUTABA_FG、FUTABA_H四个分类,前三个分类又分为小型高强度模架和中小型模架,小型高强度模架用后缀区分。
2)【类型】显示指定供应商提供的标准模架类型号,每一个代号表示一种模架结构。
见表1所示为FUTABA的各系列。
3)示图区:显示所选模架的结构示意图、导柱放置位置和推杆与推板固定形式示意图。
4)模板尺寸显示窗:显示所选模架的系列标准模板在X-Y平面投影的有效尺寸,该窗口用来选择模板大小,系统根据模具的布局确定最适合的尺寸作为默认选择。
5)布局信息窗:显示成型零件尺寸。
6)模架组件选择窗:显示组成模架零件的尺寸表达式,用来选择模架零件。
模架组件部分名称见表2所示。
表1表27)模架组件尺寸表达式栏:用来设置和修改模架零件形状尺寸。
在模架组件选择窗选择的零件能在模架组件尺寸表达式栏显示,表达式栏设置非标尺寸数值,按 Enter 键,模架组件选择窗相应组件尺寸作相应改变。
8)模板尺寸设置区:用来设置模架主要模板厚度尺寸等其他结构参数。
模板尺寸设置区数据含义举例如下: AP_h表示定模A 板高度; BP_h 表示动模 B 板高度; CP_h表示垫块 C 板高度。
TW 栏选择 175:X 表示导柱安装在动模侧,选择175 : Z 表示导柱安装在定模侧, 450 表示定、动模座板窄的宽度;550 表示定、动模座板宽的宽度;U_h栏30: V、 40 : W表示支承板两种可供选择的高度,具体数值表示支承板的高度。
图39)xx图标:图标区有模架xx数据库图标、旋转成型零件图标等。
模架安装定位时模架宽度方向与模具坐标系 x 轴方向一致,在设置模具坐标系 x 轴方向时如果忘记调整成型零件宽度方向与 X 轴方向一致,可使用旋转图标旋转成型零件,使成型零件宽度方向和模架宽度方向与 X 轴方向一致。
一、FUTABA大水口标准模架。