焊接机器人文献综述
自动焊接机器人论文参考文献范例
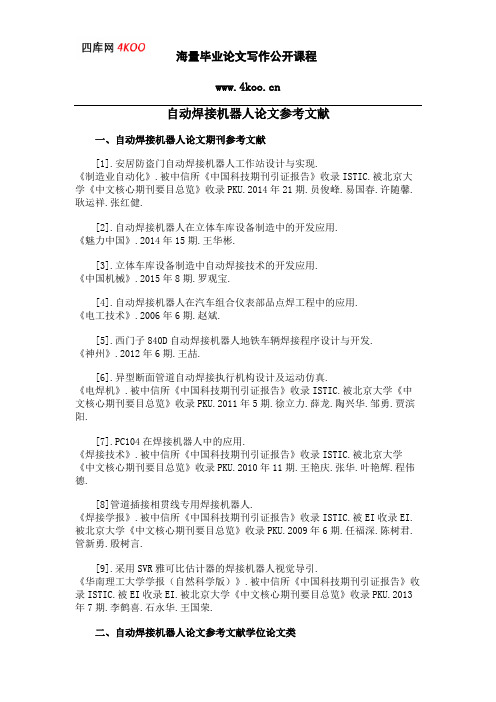
自动焊接机器人论文参考文献一、自动焊接机器人论文期刊参考文献[1].安居防盗门自动焊接机器人工作站设计与实现.《制造业自动化》.被中信所《中国科技期刊引证报告》收录ISTIC.被北京大学《中文核心期刊要目总览》收录PKU.2014年21期.员俊峰.易国春.许随馨.耿运祥.张红健.[2].自动焊接机器人在立体车库设备制造中的开发应用.《魅力中国》.2014年15期.王华彬.[3].立体车库设备制造中自动焊接技术的开发应用.《中国机械》.2015年8期.罗观宝.[4].自动焊接机器人在汽车组合仪表部品点焊工程中的应用.《电工技术》.2006年6期.赵斌.[5].西门子840D自动焊接机器人地铁车辆焊接程序设计与开发.《神州》.2012年6期.王喆.[6].异型断面管道自动焊接执行机构设计及运动仿真.《电焊机》.被中信所《中国科技期刊引证报告》收录ISTIC.被北京大学《中文核心期刊要目总览》收录PKU.2011年5期.徐立力.薛龙.陶兴华.邹勇.贾滨阳.[7].PC104在焊接机器人中的应用.《焊接技术》.被中信所《中国科技期刊引证报告》收录ISTIC.被北京大学《中文核心期刊要目总览》收录PKU.2010年11期.王艳庆.张华.叶艳辉.程伟德.[8]管道插接相贯线专用焊接机器人.《焊接学报》.被中信所《中国科技期刊引证报告》收录ISTIC.被EI收录EI.被北京大学《中文核心期刊要目总览》收录PKU.2009年6期.任福深.陈树君.管新勇.殷树言.[9].采用SVR雅可比估计器的焊接机器人视觉导引.《华南理工大学学报(自然科学版)》.被中信所《中国科技期刊引证报告》收录ISTIC.被EI收录EI.被北京大学《中文核心期刊要目总览》收录PKU.2013年7期.李鹤喜.石永华.王国荣.二、自动焊接机器人论文参考文献学位论文类[1].基于DSP和CPLD的焊缝视觉跟踪系统设计.被引次数:1作者:高志远.检测技术与自动化装置哈尔滨工程大学2013(学位年度)[2].拉丝漏板自动焊接机器人系统开发.被引次数:3作者:周伟.机械电子工程南京航空航天大学2008(学位年度)[3].拉丝漏板自动焊接机器人显微视觉伺服系统的研究与开发.被引次数:1作者:刘诚.机械电子工程南京航空航天大学2008(学位年度)[4].空间复杂焊缝焊接机器人设计及其控制系统研究.被引次数:3作者:郑祥格.机械电子工程浙江大学2012(学位年度)[5].机器人弧焊离线编程系统及其自动编程技术的研究.被引次数:49作者:何广忠.材料加工工程哈尔滨工业大学2006(学位年度)[6].中部槽自动焊接焊枪运动方法的研究与实现.作者:杨佳.机械工程浙江工业大学2014(学位年度)[7].机器视觉在焊接自动化系统中的应用研究.被引次数:3作者:程世东.检测技术与自动化装置西安石油大学2008(学位年度)[8].基于图像技术的焊接机器人视觉算法研究.被引次数:1作者:张海刚.控制理论与控制工程西安工业大学2009(学位年度)[9].焊接机器人示教系统开发及基于图像的示教新方法研究.被引次数:10 作者:朱志强.机械电子工程浙江大学机能学院浙江大学2008(学位年度)[10].全位置弧焊机器人机构及控制系统设计与实现.作者:胥潇.精密仪器及机械电子科技大学2014(学位年度)三、自动焊接机器人论文专著参考文献[1]自动激光焊接机器人系统在FPC焊接上的应用.李泽民,20102010中国高端SMT学术会议[6]奥运"鸟巢"工程机器人自动焊探索.戴为志.蒋力培.李宪政.沈李强.薛龙.李海斌.邹勇.张卫义,20062006中国机械工程学会焊接分会钢结构焊接国际论坛[7]基于多信息传感的FANUC焊接机器人系统研究.叶震.余焕伟.陈华斌.方古.陈善本.李杰,20122012年中国机器人焊接学术与技术交流会[8]港珠澳大桥焊接机器人系统应用.高峰.郭强.季富强.邹纪祥,2014中国交通建设股份有限公司2014年现场技术交流会[9]新型无导轨全位置焊接机器人研究及应用.邹勇.梁亚军.薛龙.蒋力培.黄军芬.张卫义,2008第五届全国计算机在焊接中的应用学术与技术交流会[10]球罐全位置智能焊接机器人研究.蒋力培.焦向东.薛龙.陈强.孙振国.王军波,2000“面向新世纪中国机器人产业化发展论坛”大会。
焊接机器人的发展历史及趋势
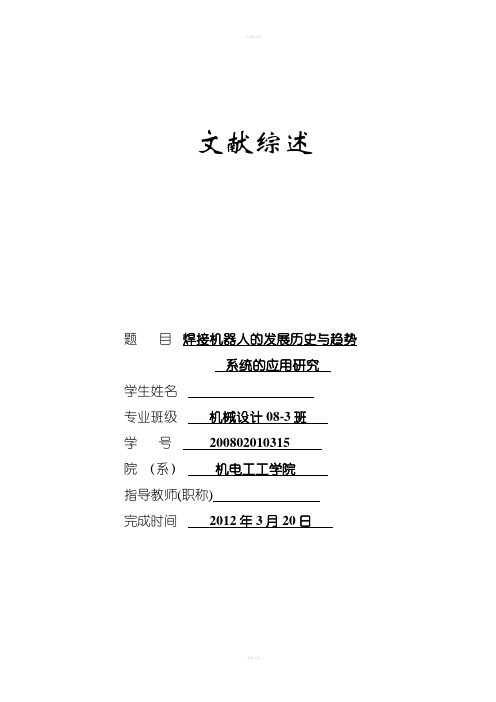
文献综述题目焊接机器人的发展历史与趋势系统的应用研究学生姓名专业班级机械设计08-3班学号200802010315院(系)机电工工学院指导教师(职称)完成时间2012年3月20日焊接机器人的发展历史与趋势摘要本文简单地介绍了焊接机器人技术发展的历程及我国焊接机器人技术研究的现状,论述了焊接机器人技术发展的趋势及研究的热点问题,即随着智能机器人技术和人工智能理论的进一步发展,多智能体焊接系统、焊接机器人中基于PC的控制器和模糊逻辑与神经网络的融合技术将成为研究的热点问题。
关键词:焊接机器人/焊缝跟踪/多智能体The history of development and trends of the welding robotAbstractThis paper briefly introduces the development course of welding robot technology and Chinese welding robot technology research present situation and discusses the trend of the development of the welding robot technology and research hot spot problems. That is as intelligent robotics and artificial intelligence theory further development. The multi-agent welding systems, welding robot based on PC controller and fuzzy logic and neural network of fusion technology will become the focus of research problems.Keywords:Welding robot,Seam tracking,Multi-agent1.焊接机器人的基本概念焊接机器人,英文名称:welding robot 定义:具有三个或三个以上可自由编程的轴,并能将焊接工具按要求送到预定空间位置,按要求轨迹及速度移动焊接工具的机器。
焊接机器人介绍范文
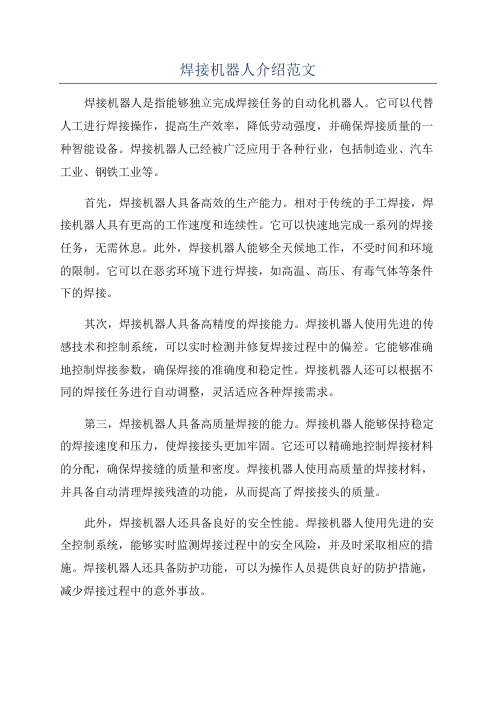
焊接机器人介绍范文焊接机器人是指能够独立完成焊接任务的自动化机器人。
它可以代替人工进行焊接操作,提高生产效率,降低劳动强度,并确保焊接质量的一种智能设备。
焊接机器人已经被广泛应用于各种行业,包括制造业、汽车工业、钢铁工业等。
首先,焊接机器人具备高效的生产能力。
相对于传统的手工焊接,焊接机器人具有更高的工作速度和连续性。
它可以快速地完成一系列的焊接任务,无需休息。
此外,焊接机器人能够全天候地工作,不受时间和环境的限制。
它可以在恶劣环境下进行焊接,如高温、高压、有毒气体等条件下的焊接。
其次,焊接机器人具备高精度的焊接能力。
焊接机器人使用先进的传感技术和控制系统,可以实时检测并修复焊接过程中的偏差。
它能够准确地控制焊接参数,确保焊接的准确度和稳定性。
焊接机器人还可以根据不同的焊接任务进行自动调整,灵活适应各种焊接需求。
第三,焊接机器人具备高质量焊接的能力。
焊接机器人能够保持稳定的焊接速度和压力,使焊接接头更加牢固。
它还可以精确地控制焊接材料的分配,确保焊接缝的质量和密度。
焊接机器人使用高质量的焊接材料,并具备自动清理焊接残渣的功能,从而提高了焊接接头的质量。
此外,焊接机器人还具备良好的安全性能。
焊接机器人使用先进的安全控制系统,能够实时监测焊接过程中的安全风险,并及时采取相应的措施。
焊接机器人还具备防护功能,可以为操作人员提供良好的防护措施,减少焊接过程中的意外事故。
总之,焊接机器人是一种高效、精确、高质量的自动化焊接设备。
它已经广泛应用于各种行业,如汽车制造、航空航天、化工等。
随着技术的不断进步,焊接机器人还将进一步提高焊接效率和质量,为工业生产带来更大的便利和发展。
焊接机器人文献综述

焊接机器人文献综述关节机器人对基于视觉反馈控制的激光焊接的焊缝追踪摘要:激光焊接对于机器人轨迹精度有相当高的要求。
为了提高机器人激光焊接时的动态轨迹精度,人们基于立体视觉反馈控制的原理提出一种新的三维焊缝追踪的方法。
这种方法建立了一种可视反馈控制系统,在该系统中有两个集中于一点的相机被安装在工业机器人的后面。
人们建造了一种具有坐标系统的工具以便把机器人最终环节的位置转移到该工具上。
人们提出了一种GPI 转移方法,这种方法是利用双目望远镜可视技术和一种逐行选配的修改法则来计算激光焦点和焊缝的位置,它使得激光焦点和焊缝之间的动态轨迹错误可以计算出来。
人们最终控制机器人的移动,并且在机器人运动学的基础上尽可能减少运动轨迹的错误。
实验结果表明,这种方法能有效改善用于激光焊接的工业机器人的运动轨迹的精度。
关键词:工业机器人,视觉反馈,焊缝跟踪,轨迹精度。
1 引言目前,卖给客户的关节机器人仅仅能够保证位置精度而不能保证运动轨迹。
然而,随着制造加工业的发展,一些高速和高精度的工作,例如激光焊接和切割,对轨迹精度有十分高的要求。
此外,在严格地结构化环境下目前的工业仅能够在预定的命令下移动,这限制了他们的应用范围。
人们提出了许多研究计划来改善机器人在人们所认识的环境下的能力。
作为一个重要的测量方法,视觉对改善工业机器人在人们所认识的不同的环境下的能力起着重要作用。
参照文献[1],人们以位置为基础建造了一种具有可视伺服系统的工业机器人,并且提出了一种运算法则,当事先知道物体一些特征点的距离时,利用这种法则就可以用一台照相机估计出物体的位置和外形。
参照文献[2],基于eye-in-hand的可视伺服结构,物体的平面移动轨迹实现了一种eye-on-object的方法。
参照文献[3],有这样一个问题:机器人最终环节的真实位置与人们用空间路径规划和图像基础控制的方法所预期的位置相差很远。
参照文献[4],人们开发了一种工业火焰跟踪系统来切割视觉上的平面图形。
机器人焊接技术论文(2)
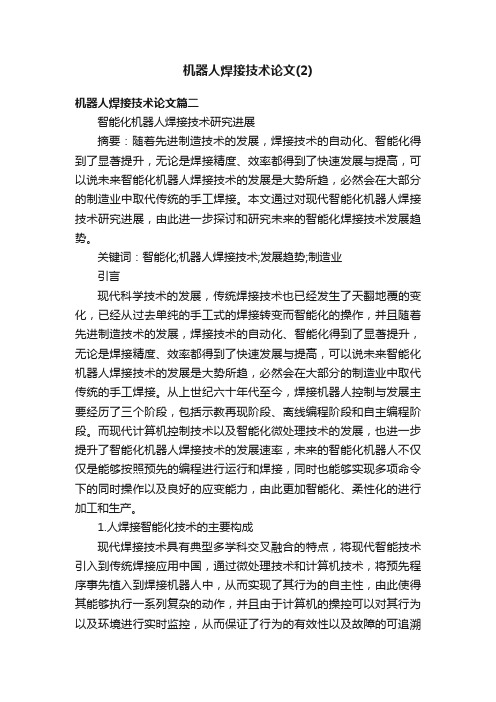
机器人焊接技术论文(2)机器人焊接技术论文篇二智能化机器人焊接技术研究进展摘要:随着先进制造技术的发展,焊接技术的自动化、智能化得到了显著提升,无论是焊接精度、效率都得到了快速发展与提高,可以说未来智能化机器人焊接技术的发展是大势所趋,必然会在大部分的制造业中取代传统的手工焊接。
本文通过对现代智能化机器人焊接技术研究进展,由此进一步探讨和研究未来的智能化焊接技术发展趋势。
关键词:智能化;机器人焊接技术;发展趋势;制造业引言现代科学技术的发展,传统焊接技术也已经发生了天翻地覆的变化,已经从过去单纯的手工式的焊接转变而智能化的操作,并且随着先进制造技术的发展,焊接技术的自动化、智能化得到了显著提升,无论是焊接精度、效率都得到了快速发展与提高,可以说未来智能化机器人焊接技术的发展是大势所趋,必然会在大部分的制造业中取代传统的手工焊接。
从上世纪六十年代至今,焊接机器人控制与发展主要经历了三个阶段,包括示教再现阶段、离线编程阶段和自主编程阶段。
而现代计算机控制技术以及智能化微处理技术的发展,也进一步提升了智能化机器人焊接技术的发展速率,未来的智能化机器人不仅仅是能够按照预先的编程进行运行和焊接,同时也能够实现多项命令下的同时操作以及良好的应变能力,由此更加智能化、柔性化的进行加工和生产。
1.人焊接智能化技术的主要构成现代焊接技术具有典型多学科交叉融合的特点,将现代智能技术引入到传统焊接应用中国,通过微处理技术和计算机技术,将预先程序事先植入到焊接机器人中,从而实现了其行为的自主性,由此使得其能够执行一系列复杂的动作,并且由于计算机的操控可以对其行为以及环境进行实时监控,从而保证了行为的有效性以及故障的可追溯性。
可以说智能化机器人焊接技术是多种技术的集成,实现了远程监控管理、统一调度规划等多项功能,让现代焊接效率更高,流程更清晰,分工更明确,同时也更加便于管理与协调,仅仅需要通过改变一定的程序就能够实现整体的焊接模式和机器人行为,无疑与传统单一的机器人焊接而言有了长足的进步。
焊接机器人-外文文献
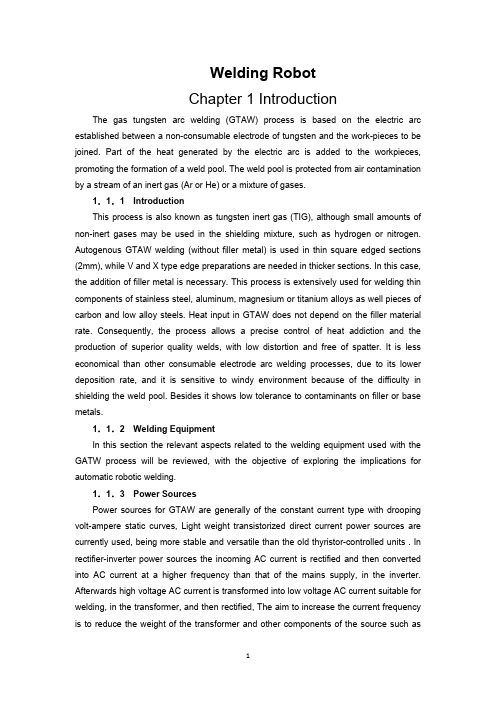
Welding RobotChapter 1 IntroductionThe gas tungsten arc welding (GTAW) process is based on the electric arc established between a non-consumable electrode of tungsten and the work-pieces to be joined. Part of the heat generated by the electric arc is added to the workpieces, promoting the formation of a weld pool. The weld pool is protected from air contamination by a stream of an inert gas (Ar or He) or a mixture of gases.1.1.1 IntroductionThis process is also known as tungsten inert gas (TIG), although small amounts of non-inert gases may be used in the shielding mixture, such as hydrogen or nitrogen. Autogenous GTAW welding (without filler metal) is used in thin square edged sections (2mm), while V and X type edge preparations are needed in thicker sections. In this case, the addition of filler metal is necessary. This process is extensively used for welding thin components of stainless steel, aluminum, magnesium or titanium alloys as well pieces of carbon and low alloy steels. Heat input in GTAW does not depend on the filler material rate. Consequently, the process allows a precise control of heat addiction and the production of superior quality welds, with low distortion and free of spatter. It is less economical than other consumable electrode arc welding processes, due to its lower deposition rate, and it is sensitive to windy environment because of the difficulty in shielding the weld pool. Besides it shows low tolerance to contaminants on filler or base metals.1.1.2 Welding EquipmentIn this section the relevant aspects related to the welding equipment used with the GATW process will be reviewed, with the objective of exploring the implications for automatic robotic welding.1.1.3 Power SourcesPower sources for GTAW are generally of the constant current type with drooping volt-ampere static curves, Light weight transistorized direct current power sources are currently used, being more stable and versatile than the old thyristor-controlled units . In rectifier-inverter power sources the incoming AC current is rectified and then converted into AC current at a higher frequency than that of the mains supply, in the inverter. Afterwards high voltage AC current is transformed into low voltage AC current suitable for welding, in the transformer, and then rectified, The aim to increase the current frequency is to reduce the weight of the transformer and other components of the source such asinductors and capacitors.1.1.4 Welding TorchThe welding torch holds the non-consumable electrode, assures the transfer of current to the electrode and the flow of shielding gas to the weld pool. Torches with welding regimes up to 200 A are generally gas-cooled and those with continuous operation between 200 and 500 A are water-cooled.1.1.5 Non-consumable ElectrodesNon-consumable electrodes are composed of pure tungsten or of tungsten alloys. Pure tungsten electrodes can be used with DC but are more sensitive to contamination, have lower service life-cycle and exhibit higher tip deterioration than alloyed electrodes. These electrodes can be used in welding of aluminum and magnesium alloys on AC. Thoriated tungsten (2% ThO2) electrodes are widely used in industrial applications due to its excellent resistance to contamination, easy arc starting and stable electric arc. Concerns about safety, because thorium oxide is radioactive, led to the development of other electrodes containing small proportions (around 2%) of simple earth rare elements such as lanthanum, yttrium and cerium or even mixtures of several elements . These electrodes have better operational characteristics than thoriated electrodes and can be used in welding carbon and stainless steels,nickel and titanium alloys. Zirconiated tungsten electrodes are excellent for AC due to its good arc starting, high resistance to contamination and small tip shape deterioration.1.1.6 Arc Striking TechniquesArc initiation by touch striking was used formerly in manual GTAW, but this technique is very sensitive to tungsten contamination, adversely affecting the service life of the electrode. High-frequency-high-voltage (e.g. 3 kV at 5 MHz) supplies are currently used in arc striking and AC arc stabilization in manual GTAW systems. This arc starting technique usually produces interference in electronic equipment in the vicinity of the power source. Programmed touch striking is an alternative technique developed for automatic systems. In this technique current and voltage are limited when electrode touches in the work-piece, in order to prevent electrode contamination. A pilot arc starting can also be used to initiate the main electric arc, though a more complex torch is needed.1.1.7 Shielding Gas RegulatorThe regulator is a device that reduces source gas pressure to a constant working pressure, independently of source pressure variations. Pressure reduction can be made in one or two stages. Regulators in two stages give in general more stable output flow. 1.2 Process ParametersIn this section the relevant parameters for the GTAW process will be reviewed with the double objective of presenting them and showing that they can certainly be used for automatic robotic welding.1.2.1 CurrentCurrent has direct influence on weld bead shape, on welding speed and quality of the weld. Most GTAW welds employ direct current on electrode negative (DCEN) (straight polarity) because it produces higher weld penetration depth and higher travel speed than on electrode positive (DCEP) (reverse polarity). Besides, reverse polarity produces rapid heating and degradation of the electrode tip, because anode is more heated than cathode in gas tungsten electric arc. Reverse polarity may be of interest in welding aluminum alloys because of the catholic cleaning action of negative pole in the work-piece, that is the removal of the refractory aluminum oxide layer. However alternating current is better adapted to welding of aluminum and magnesium alloys, because it allows balancing electrode heating and work-piece cleaning effects. Weld penetration depth obtained with AC is between depth obtained with DCEN and DCEP.1.2.2 Welding SpeedThe effect of increasing the welding speed for the same current and voltage is to reduce the heat input. The welding speed does not influence the electromagnetic force and the arc pressure because they are dependent on the current. The weld speed increase produces a decrease in the weld cross section area, and consequently penetration depth (D) and weld width (W) also decrease, but the D/W ratio has a weak dependence on travel speed. These results suggest that the travel speed does not influence the mechanisms involved in the weld pool formation, it only influences the volume of melted material. Normal welding speeds are from 100 to 500 mm/min depending on current, material type and plate thickness.1.2.3 Arc LengthThe arc length is the distance between the electrode tip and the work-piece. The arc length in GTAW is usually from 2 to 5 mm. If the arc length increases, the voltage to maintain the arc stability must increase, but the heat input to work-piece decreases due to radiation losses from the column of the arc. Consequently, weld penetration and cross section area of melted material decrease with increasing arc length.1.2.4 Shielding GasesShielding gases are used in GTAW in order to prevent atmospheric contamination of the weld metal. This contamination can produce porosity, weld cracking, scaling and evenchange in the chemical composition of melted material. Besides shielding gas also has a large influence on the stability of the electric arc. Gases with low ionization potential facilitate the ignition of the electric arc and those with low thermal conductivity tend to increase the arc stability. Argon is the most used GTAW shielding gas. It has low ionization potential and is heavier than air, providing an excellent shielding of the molten weld pool. Furthermore it is less expensive than helium, the other inert shielding gas used in the process. Argon is used in welding of carbon and stainless steels and low thickness aluminum alloys components. For welding thick aluminum work-pieces and other high-conductive materials, such as copper alloys, helium is recommended because it has higher ionization potential than argon, needing higher voltage for arc initiation and maintenance, but producing higher heat-input. Helium or helium/argon (30-80% He) mixtures allow increased welding speed and improved process tolerance. Mixtures of argon with up to 5% of hydrogen are frequently used in welding of austenitic stainless steels. Hydrogen increases arc-voltage and consequently heat input, increasing weld penetration and weld travel speed, as well improving weld appearance. Argon/hydrogen mixtures are also used in welding of copper nickel alloys. Argon is also used as back side shielding gas, mainly in welding of stainless steels, aluminum alloys and reactive metals.Flow rates of shielding gases depend on weld thickness, being 4-10 l/min for argon and 10-15 l/min for helium, because it is lighter than argon, and consequently less effective in shielding. Gases with a purity of 99.995% are used in welding most of the metals, though reactive materials such as titanium need contaminant level less than 50 ppm.1.2.5 Filler MetalsFiller metals are generally used for plate thickness above 2 mm, having chemical composition similar to that of the parent material. Filler metal diameter is between 1.6 and 3.2 mm and in automatic systems is normally added cold from a roll or a coil.1.2.6 Electrode Vertex AngleThe non-consumable electrode angle influences the weld penetration depth and the weld shape. Electrode angles between 30o and 120o are used. Small angles increase arc pressure and penetration depth but have high tip shape deterioration. Electrode angles from 60o to 120o maintain tip shape for longer periods and give welds with adequate penetration depth-to-width ratio.1.2.7 Cast-to-cast VariationCast-to-cast variation refers to variation observed in penetration of welds produced in the same welding conditions in several batches of austenitic stainless steel with nominallyidentical composition. These changes in the weld bead shape are attributed to variation in proportion of trace elements in the material, such as sculpture, calcium and oxygen. Variations in trace elements seem to affect surface tension and metal flow into the pool . Weld pool shape is also affected by electromagnetic forces, arc pressure and thermo capillarity forces. To minimize this problem several strategies have been adopted such as the use of higher currents or of pulsed current, the application of adequate shielding gases or the application on plate surface of flux coatings containing active ingredients.1.3 Process VariantsGTAW is regarded as a high quality process for welding thin metals using low travel speed and low electrode deposition rate, requiring highly skilled personnel in manual welding. Variants developed seek to improve productivity, mainly deposition rate, penetration depth and welding speed. These variants are implemented in automatic or robotic systems. Hot-wire GTAW is a variant where a heated filler wire is fed to the rear of the melted weld pool at a constant rate.Filler wire is resistance heated close to melting point using mainly AC power sources, in order to minimize magnetic disturbance of the electric arc. Deposition rates up to 14 kg/h can be attained with this process. It has been used in heavy wall fabrication, maintaining high joint integrity .The use of a dual-shielding GTAW technique, where an additional concentric gas shield gives an increase in constriction and stiffness of the electric arc, may be used to increase welding speed and penetration depth .Constriction of the arc is produced by the external cold gas flow which decreases temperature of the outer part of the arc, decreasing the arc cross section where current flow occurs, consequently increasing current density and temperature. Electrode gas and annular gas may be of the same or of different compositions, such as Argon plus 5% hydrogen for internal gas and argon for external gas when welding austenitic stainless steels. This technique also tends to increase the risk of undercut. Very high currents (I > 300 A) may also be used in a conventional automated GTAW process to increase the penetration depth, but defects may form and the process becomes unstable above 500 A. The key hole mode gas tungsten arc welding process, which was developed a few years ago, seems to be suitable for ferrous and non-ferrous materials in the range from 3 to 12 mm. However, this key whole technique is extremely sensitive to arc voltage, and loss of material may occur through the keyhole vent.。
文献综述-便携式关节型弧焊机器人设计
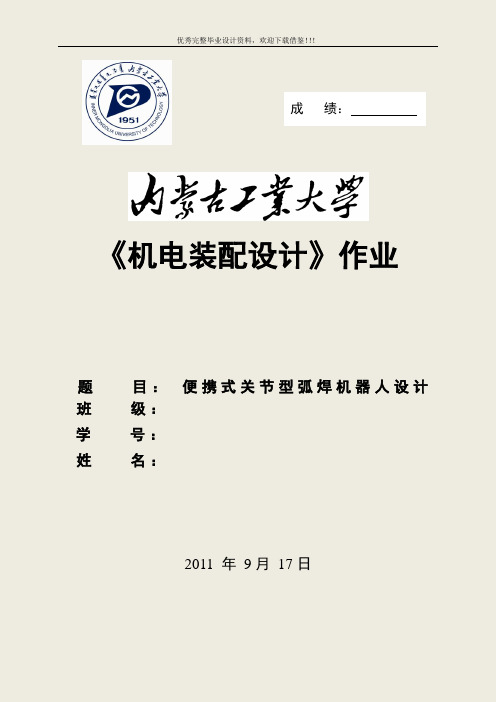
《机电装配设计》作业题 目: 便携式关节型弧焊机器人设计 班 级:学 号:姓 名:2011 年 9月 17日成 绩:一. 前期调研1 工业机器人的概念工业机器人是面向工业领域的多关节机械手或多自由度的机器人。
工业机器人是自动执行工作的机器装置,是靠自身动力和控制能力来实现各种功能的一种机器。
它可以接受人类指挥,也可以按照预先编排的程序运行,现代的工业机器人还可以根据人工智能技术制定的原则纲领行动。
2 工业机器人发展现状与前景展望在发达国家中,工业机器人自动化生产线成套设备已成为自动化装备的主流机器人发展前景及未来的发展方向。
国外汽车行业、电子电器行业、工程机械等行业已经大量使用工业机器人自动化生产线,以保证产品质量,提高生产效率,同时避免了大量的工伤事故。
全球诸多国家近半个世纪的工业机器人的使用实践表明,工业机器人的普及是实现自动化生产,提高社会生产效率,推动企业和社会生产力发展的有效手段.机器人技术是具有前瞻性、战略性的高技术领域。
国际电气电子工程师协会IEEE的科学家在对未来科技发展方向进行预测中提出了4个重点发展方向,机器人技术就是其中之一。
1990年10月,国际机器人工业人士在丹麦首都哥本哈根召开了一次工业机器人国际标准大会,并在这次大会上通过了一个文件,把工业机器人分为四类:⑴顺序型。
这类机器人拥有规定的程序动作控制系统;⑵沿轨迹作业型。
这类机器人执行某种移动作业,如焊接。
喷漆等;⑶远距作业型。
比如在月球上自动工作的机器人;⑷智能型。
这类机器人具有感知、适应及思维和人机通信机能。
日本工业机器人产业早在上世纪90年代就已经普及了第一和第二类工业机器人,并达到了其工业机器人发展史的鼎盛时期。
而今已在第发展三、四类工业机器人的路上取得了举世瞩目的成就。
日本下一代机器人发展重点有:低成本技术、高速化技术、小型和轻量化技术、提高可靠性技术、计算机控制技术、网络化技术、高精度化技术、视觉和触觉等传感器技术等。
移动焊接机器人焊接手臂设计(文献综述)【优秀】
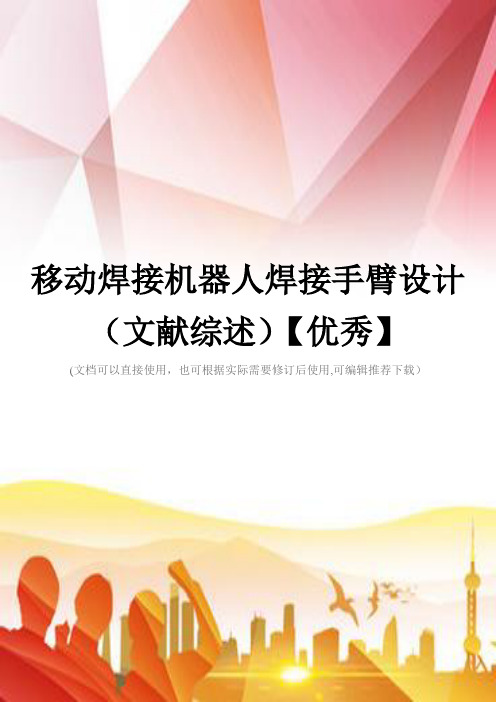
移动焊接机器人焊接手臂设计(文献综述)【优秀】(文档可以直接使用,也可根据实际需要修订后使用,可编辑推荐下载)移动焊接机器人焊接手臂设计(文献综述)研究目的和意义近年来随着工业自动化的发展机械手逐渐成为一门新兴的学科,并得到了较快的发展。
机械手广泛地应用于锻压、冲压、铸造、焊接、装配、机加、喷漆、热处理等各个行业。
特别是在笨重、高温、有毒、危险、放射性、多粉尘等恶劣的劳动环境中,机械手由于其显著的优点而受到特别重视。
总之,机械手是提高劳动生产率,改善劳动条件,减轻工人劳动强度和实现工业生产自动化的一个重要手段,国内外都很重视它的应用和发展。
焊接是机械制造工业的基本生产手段之一,提高焊接质量的稳定性和可靠性是至关重要的。
采用自动焊接技术是达到上述目的的唯一途径。
随着机械、电子计算机、自动控制技术的发展,工业机器人这一融合多学科技术的高科技产品得到了很大的发展,许多工业生产领域都应用了工业机器人,弧焊机器人就是其中的一种。
通用型弧焊机器人由机械系统、控制系统、驱动系统组成。
其中,机械系统包括机身、关节型手臂、焊接工具。
控制系统一般分为两部分:一部分是主控微型计算机和从微型计算机或单片微型计算机,微型计算机一般由主机、键盘、显示器、输入设备、输入/输出接口组成;另一部分为控制柜,由输入/输出接口、功率驱动放大电路组成。
驱动系统一般为液压驱动或电动驱动,常以动力站的形式单独放置,控制程序编程多采用示教编程。
这种结构形式的通用型弧焊机器人在国内流水生产作业线上得到了比较广泛的使用。
在石油化工、水利电力等企业许多焊接生产作业需要在室外或野外进行,有些还需要在狭小的生产作业空间内完成,外界环境恶劣,焊接生产作业条件十分苛刻,目前完成这些焊接生产一般都还采用手工操作。
能完成这样的焊接生产作业任务的自动焊接设备,弧焊机器人是首选的,但如沿用通用型弧焊机器人又受到机器人本体结构、体积、重量、抗干扰能力以及机器人价格的限制。
机器人文献综述

机器人文献综述机器人文献综述摘要:机器人是一种由主体结构、控制器、指挥系统和监测传感器组成的,能够模拟人的某些行为、能够自行控制、能够重复编程、能在二维空间内完成一定工作的机电一体化的生产设备。
机器人技术是综合了计算机、控制论、机构学、信息传感技术、人工智能、仿生学等多学科而形成的高新技术。
是当代研究十分活跃、应用日益广泛的领域。
也是一个国家工业自动化水平的重要标志。
关键词:机器人历史机器人分类移动机器人技术一、引言[1]机器人是当代自动化技术和人工智能技术发展的典型体现,也代表着制造技术发展的新水平,是一种由主体结构、控制器、指挥系统和监测传感器组成的,能够模拟人的某些行为、能够自行控制、能够重复编程、能在二维空间内完成一定工作的机电一体化的生产设备。
机器人尤其是工业机器人的广泛应用,极大提高了生产力。
目前世界上使用的机器人已有百万之多,并且次数目仍在快速增长。
其应用领域也从传统的制造业、军事应用逐步扩展到服务业、空间探索等。
二、机器人历史的发展[2]2015年,国内版工业4.0规划——《中国制造2025》行动纲领出台,其中提到,我国要大力推动优势和战略产业快速发展机器人,包括医疗健康、家庭服务、教育娱乐等服务机器人应用需求。
那么机器人发展阶段又如何呢?20世纪20年代前后,捷克和美国的一些科幻作家创作了一批关于未来机器人与人类共处中可能发生的故事之类的文学作品,使得机器人在人们的思想中成为一种无所不能的“超人”。
1954年,美国的戴沃尔制造了世界第一台机器人实验装置,发表了《适用于重复作业的通用性工业机器人》一文,并获得美国专利。
1960年,美国Unimation公司根据戴沃尔德技术专利研制出第一台机器人样机,并定型生产Unimate(意为“万能自动”)机器人。
同时,美国“机床与铸造公司”(AMF)设计制造了另一种圆柱坐标形式的可编程机器人Versatran(意为“多才多艺用途搬运机器人”)。
文献综述

1、文献名:弧焊机器人起始焊接位置图像识别与定位
作者:陈希章,,陈善本2
出处:0253一360X (2009 )04一0017一04
文献内容:(1)工件焊缝形式可以分为三类,起始焊接位
置的定义可以适用于各种形式的焊缝类型.
(2)工件的起始焊接位置通过求取交点和角点
两种方法来求取.
(3)提出的由粗到细的两步方法充分利用了图
焊位的自主导引;结果表明,相机在距离工件120mm到210mm拍摄时,在x,Y和z方向上的导引精度分别为士O.S mm、士0.4mm和士1.Omm;设计了不同的截止频率的数字二阶巴特沃斯低通滤波器,对焊接电流信号进行
滤波,通过比较和分析,确定了最佳的滤波器截止频率;确定提取焊接电流特征值的算法,建立了焊接电流信号与焊枪高度之间的对应关系;设计了电弧高度跟踪算法,并将程序写入到DSP中;确定了焊接工艺参数,进行了电弧高度跟踪实验,结果表明,电弧跟踪的精度为士l.lmm;编写了软件系统,包括计算机主程序、机器人程序和DSP程序,实现了图像采集、图像处理、三维重建、焊接电流信号的数字处理,以及计算机与机器人、
搭建了具有视觉传感和电弧传感的焊接机器人系统;基于模块化的设计思想,分别开发了机器人焊接模块、视觉传感模块和电弧跟踪模块,其中视觉传感模块和电弧跟踪模块相互独立,只需要采用正确的通讯协议,就可以方便快速地移植到其他型号的焊接机器人上,便于相关产品的开发和推广;采用独特的圆形点阵标定靶,通过改进的MATLAB标定程序,同时完成相机标定和手眼标定,获得相机的内部参数和手眼转换关系矩阵,相对于传统的棋盘格式标定方法,速度更快、精度更高、抗相机畸变能力更强;针对焊缝区域的图像特点,提出了图像平滑、边缘提取、小面积滤波、Hough变换的图像处理流程,可以准确获取焊缝起始点或终点在图像上的像素坐标,通过调整相关参数,也适用于折线型焊缝中折点的提取;提出了适用于焊接机器人的立体视觉测量方法,采用“一目双位”的方式对目标点进行三维重建,计算目标点在机器人世界坐标系下的三维坐标,实现初始
焊接机器人的发展现状和机器人焊接质量控制
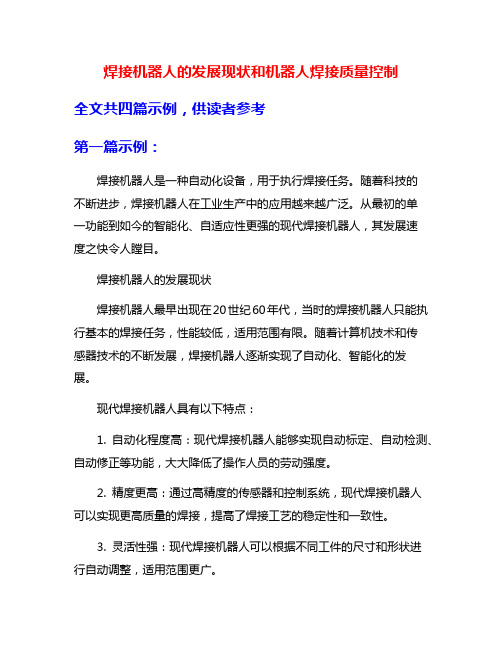
焊接机器人的发展现状和机器人焊接质量控制全文共四篇示例,供读者参考第一篇示例:焊接机器人是一种自动化设备,用于执行焊接任务。
随着科技的不断进步,焊接机器人在工业生产中的应用越来越广泛。
从最初的单一功能到如今的智能化、自适应性更强的现代焊接机器人,其发展速度之快令人瞠目。
焊接机器人的发展现状焊接机器人最早出现在20世纪60年代,当时的焊接机器人只能执行基本的焊接任务,性能较低,适用范围有限。
随着计算机技术和传感器技术的不断发展,焊接机器人逐渐实现了自动化、智能化的发展。
现代焊接机器人具有以下特点:1. 自动化程度高:现代焊接机器人能够实现自动标定、自动检测、自动修正等功能,大大降低了操作人员的劳动强度。
2. 精度更高:通过高精度的传感器和控制系统,现代焊接机器人可以实现更高质量的焊接,提高了焊接工艺的稳定性和一致性。
3. 灵活性强:现代焊接机器人可以根据不同工件的尺寸和形状进行自动调整,适用范围更广。
4. 安全性高:通过安全监控系统和防护装置,现代焊接机器人可以确保操作人员的安全。
5. 数据化管理:现代焊接机器人可以实现数据采集、分析和管理,帮助企业进行生产效率和质量的管理。
机器人焊接质量控制机器人焊接的质量控制是确保焊接工艺稳定性和焊接质量的重要环节。
以下是一些常用的机器人焊接质量控制方法:1. 视觉检测:通过高分辨率的摄像头和图像处理系统,实时监测焊接过程中的焊缝质量和焊接温度,及时发现问题并进行调整。
2. 激光测量技术:激光测量技术可以实现对焊缝尺寸、焊丝直径等参数的实时监测,确保焊接质量的一致性。
3. 热成像技术:通过热成像技术可以实时监测焊接过程中的温度分布,帮助调整焊接参数,提高焊接质量。
4. 智能控制系统:智能控制系统可以根据焊接过程中的实际情况进行实时调整,保证焊接质量的稳定性。
5. 数据分析:通过数据分析,可以对焊接过程中的参数进行统计分析,找出问题的根源并进行改进。
总结随着科技的不断进步,焊接机器人的发展速度之快令人瞠目。
我国焊接机器人应用现状及关键技术概述

我国焊接机器人应用现状及关键技术概述摘要:焊接机器人是智能化焊接制造的关键装备,在制造业转型升级向智能制造发展的当下,其重要性不言而喻。
结合我国焊接机器人应用情况,分析了焊接机器人技术发展现状、市场发展现状、行业应用现状及我国焊接机器人行业发展的痛点问题,并对焊接机器人的本体技术、焊接电源技术、传感技术、协调运动控制技术、离线编程与仿真技术以及系统集成技术等关键技术做了简要概述。
有助于全面展现我国焊接机器人应用现状,为我国焊接机器人技术与产业发展提供参考。
关键词:焊接机器人;智能制造;制造业转型升级;焊接关键技术1 焊接机器人技术发展现状在近现代全球市场中,制造行业面临区域或国际竞争日趋激烈,以提高生产效率、生产质量及市场反应速度,降低生产成本为目标的制造业转型升级越来越受重视。
在此背景下,使用灵活、可精准重复执行生产动作,能够代替对人员操作熟练程度要求较高的焊接自动化设备成为越来越多的科研机构研究焦点。
1952年全球首台数控机床诞生,应用于数控机床的多轴控制技术、伺服技术、精密减速机技术得到了长足发展,在数控技术的基础上,GeorgeCharlesDevol于1954年申请了全球第一个工业机器人专利。
此后工业机器人不断进化,在20世纪60年代,受控制技术、电机技术、传感器技术、微电子与计算机技术和精密机械制造等技术发展推动,以及大规模生产需求、柔性化生产需求的影响,工程师们逐渐将研究焦点转移到工业机器人上。
从20世纪60年代焊接机器人诞生到现在,焊接机器人的研究经历了示教再现型、低智能型、智能型三个阶段。
其中示教再现型机器人执行示教程序进行呆板的重复性工作,该类型机器人对焊接工件的一致性要求较高,对多变的外部环境适应性较差,对于结构不稳定易变形工件一般要求在组对工装上进行焊接。
低智能型焊接机器人在示教再现型机器人的基础上集成各种传感技术,如电弧传感、激光传感、视觉传感等,可获得一定的环境感知能力,在示教程序的基础上,可根据工件焊缝位置偏差及焊接尺寸偏差做出焊接路径及焊接工艺参数的实时调整,从而保证焊接质量。
视觉机器人焊接技术的研究综述与展望
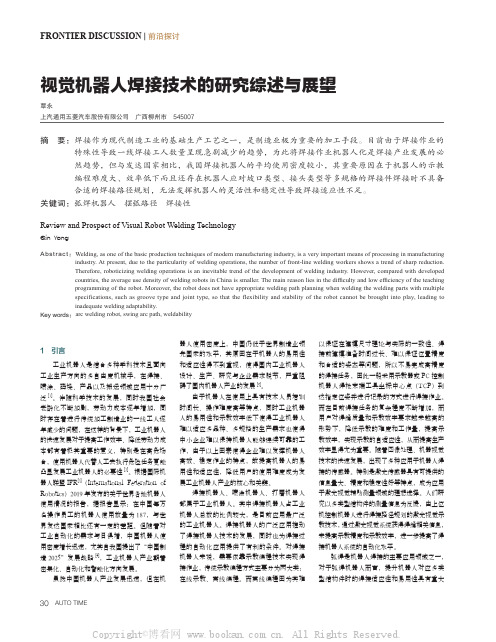
FRONTIER DISCUSSION | 前沿探讨视觉机器人焊接技术的研究综述与展望覃永上汽通用五菱汽车股份有限公司 广西柳州市 545007摘 要: 焊接作为现代制造工业的基础生产工艺之一,是制造业极为重要的加工手段。
目前由于焊接作业的特殊性导致一线焊接工人数量呈现急剧减少的趋势,为此将焊接作业机器人化是焊接产业发展的必然趋势,但与发达国家相比,我国焊接机器人的平均使用密度较小,其重要原因在于机器人的示教编程难度大、效率低下而且还存在机器人应对坡口类型、接头类型等多规格的焊接件焊接时不具备合适的焊接路径规划,无法发挥机器人的灵活性和稳定性导致焊接适应性不足。
关键词:弧焊机器人 摆弧路径 焊接性1 引言工业机器人是结合多种学科技术且面向工业生产方向的多自由度机械手,在焊接、喷涂、码垛、产品以及搬运领域应用十分广泛[1]。
伴随科学技术的发展,同时我国社会老龄化不断加剧,劳动力成本逐年增加,同时存在着进行传统加工制造业的一线工人逐年减少的问题,在这样的背景下,工业机器人的快速发展对于提高工作效率、降低劳动力成本都有着极其重要的意义,特别是在高危场合,使用机器人代替人工去执行危险任务更能凸显发展工业机器人的必要性[2]。
根据国际机器人联盟IFR[3](International Federation of Robotics)2019年发布的关于世界各地机器人使用情况的报告,据报告显示:在中国每万名操作员工的机器人使用数量为187,与世界发达国家相比还有一定的差距。
但随着对工业自动化的需求与日俱增,中国机器人使用密度增长迅速,尤其自我国提出了“中国制造2025”发展战略[4],工业机器人产业朝着密集化、自动化和智能化方向发展。
虽然中国机器人产业发展迅速,但在机器人使用密度上,中国仍低于世界制造业领先国家的水平,其原因在于机器人的易用性和适应性得不到重视,使得国内工业机器人设计、生产、研究与企业需求脱节,严重阻碍了国内机器人产业的发展[5]。
(完整版)工业机器人文献综述

(完整版)工业机器人文献综述工业机器人文献综述生产力在不断进步,推动养科技的进步与革新,以建立更加合理的生产关系。
自工业革命以来,人力劳动己经逐渐被机械所取代,而这种变革为人类社会创造出巨大的财富,极大地推动了人类社会的进步时至今天,机电一体化,机械智能化等技术应运而生并己经成为时代的主旋律。
1.工业机器人的发展:1.1 机器人概念的诞生机器人技术一词虽然出现的较晚,但这一概念在人类的想象中却早已出现。
自古以来,有不少科学家和杰出工匠都曾制造出具有人类特点或具有动物特征的机器人雏形。
我国西周时期的能工巧匠就研制出了能歌善舞的伶人,这是我国最早的涉及机器人概念的文章记录,此外春秋后期鲁班制造过一只木鸟,能在空中飞行,体现了我国劳动人民的智慧。
机器人一词由捷克作家--卡雷尔.恰佩克在他的讽刺剧《罗莎姆的万能机器人》中首次提出,剧中描述了一机器奴仆Robot。
此次Robot被沿用下来,中文译成机器人。
1942年美国科幻作家埃萨克.阿西莫夫在他的科幻小说《我.机器人》中提出了“机器人三大定律”,这三大定律后来成为学术界默认的研发原则。
现代机器人出现于20世纪中期,当计算机技术出现,电子技术的进步,数控机床的出现及与机器人相关的控制技术和零件加工技术的成熟,为现代机器人的发展打下了基础。
1.2 国内机器人的发展史在我国目前采用工业机器人的行业主要有汽车行业、摩托车、电器、工程机械、石油化工等行业。
我国作为亚洲第三大的工业机器人需求国,对于工业机器人的需求量在逐年增加,从而吸引了大批工业机器人的制造商,加快了我国工业机器人技术的发展第一阶段是20世纪80年代,我国为t跟踪国际机器人技术的道路,当时以原机械工业部为主,航天工业部等部门联合组织国内的相关研究单位开展了工业机器人的研究,先后推出了弧焊、点焊、喷漆等多种工业机器人。
直到90年代,通过国家863计划等的K77,我国具备t独!)设计不}}生产工业机器人的能力,培养了一批高水平的研究生产队伍进入21世纪,中国的工业机器人发展进入t一个崭新的阶段,其中最大的特点是以企业为主体,以市场为导向、赢利为目标的机器人产业开发群体止在形成。
焊接机器人设计毕业论文

焊接机器人设计毕业论文摘要[0001]本发明涉及一种用来电阻焊工作的焊接机器人,它包括一个焊钳(21),一个焊接电流发生器(1),发生器连接在焊钳上的焊接电极(24,25),在电阻焊工作中为焊接电极提供电能,一个工业机器人。
工业机器人包括机器人手臂(2)和用于控制手臂移动的机械手控制装置(9)。
焊钳被连接到机器人手臂上,机械手控制装置被连接到焊接电流发生器和一个焊钳的钳驱动器上。
描述:本发明涉及一种焊接机器人。
[0002]DE 31 15 840 A1中介绍了焊接所用电阻,其特征在于,在焊接过程中,两焊接电极之间的电阻以参考电阻曲线为基准,随着电焊条接触力的变化而自动调整,此外,焊接电极所用的电压亦被调整至参考电位曲线上。
[0003]EP 1 508 396 B1 中介绍了焊接所用机器人,包括工业机器人和连接在机器人手臂上的焊钳。
焊钳,跟随机器人手臂移动,包含有两个电极臂,一个用来驱动电极臂的电动机,还有用于测量电机臂施加的接触力大小的力传感器。
该焊接装置还包括一个校正装置,根据实际接触力与理论接触力的偏差值,确定一个合适的变量来校正电动马达的位置。
[0004]本发明的目的是提供一种改善的焊接机器人。
[0005]本发明旨在创造一种用于电阻焊的新型焊接机器人,它包含以下几个方面:[0006]焊钳,由钳驱动器和两焊接电极构成,由钳驱动器驱动,在焊接机器人工作中,对至少两个要进行电阻焊接的材料加压。
[0007]焊接电流发生器,连接到焊机电极上,电阻焊工作中为焊接电极提供电能。
[0008]工业机器人,由机械手臂、机械手控制装置构成,控制装置用于控制机械手臂的移动,其中机器人手臂配置有为数众多的相互连接的肢,驱动连接到控制装置,焊钳连接到焊接电流发生器和钳驱动器上,在控制平台运行的电脑程序控制机械手臂的移动驱动器,钳驱动器也被设定好的模式控制着,使得在进行电阻焊作业时,预期的电位可以应用于焊接电极上,同时,也可以使得焊接电流发生器为焊接电极提供预期的电能。
焊接机器人的发展现状和机器人焊接质量控制
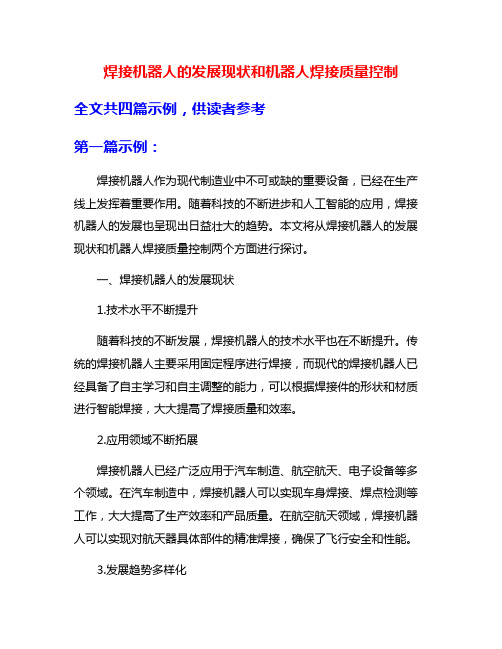
焊接机器人的发展现状和机器人焊接质量控制全文共四篇示例,供读者参考第一篇示例:焊接机器人作为现代制造业中不可或缺的重要设备,已经在生产线上发挥着重要作用。
随着科技的不断进步和人工智能的应用,焊接机器人的发展也呈现出日益壮大的趋势。
本文将从焊接机器人的发展现状和机器人焊接质量控制两个方面进行探讨。
一、焊接机器人的发展现状1.技术水平不断提升随着科技的不断发展,焊接机器人的技术水平也在不断提升。
传统的焊接机器人主要采用固定程序进行焊接,而现代的焊接机器人已经具备了自主学习和自主调整的能力,可以根据焊接件的形状和材质进行智能焊接,大大提高了焊接质量和效率。
2.应用领域不断拓展焊接机器人已经广泛应用于汽车制造、航空航天、电子设备等多个领域。
在汽车制造中,焊接机器人可以实现车身焊接、焊点检测等工作,大大提高了生产效率和产品质量。
在航空航天领域,焊接机器人可以实现对航天器具体部件的精准焊接,确保了飞行安全和性能。
3.发展趋势多样化随着市场需求的不断增加,焊接机器人的发展趋势也愈加多样化。
除了传统的气体保护焊、电弧焊等技术外,激光焊、等离子焊等新兴技术也正在逐渐应用于焊接机器人中,为焊接行业带来了更多的选择和可能性。
二、机器人焊接质量控制1.焊接参数实时监控在机器人焊接过程中,焊接参数的控制对焊接质量至关重要。
实时监控焊接电流、电压、速度等参数,可以及时发现焊接过程中的异常情况,并进行调整,保证焊接质量。
2.焊接质量检测机器人焊接完成后,需要对焊缝进行质量检测。
传统的方法是通过X射线检测、焊缝断面检测等方式对焊缝进行检测,但这些方法往往需要耗费大量的人力和时间。
现代技术可以利用机器视觉和人工智能技术,实现对焊缝的自动检测和分析,大大提高了检测效率和准确性。
3.质量控制标准化为了提高机器人焊接质量的稳定性和一致性,需要建立完善的质量控制体系。
制定标准化的焊接工艺和操作规程,对焊接机器人进行定期维护和检修,培训操作人员,建立焊接质量档案等措施都是保证焊接质量的重要手段。
我国焊接机器人应用现状及关键技术概述

我国焊接机器人应用现状及关键技术概述摘要:焊接机器人是目前装备制造业和其他大型行业应用较为广泛的一种焊接方式,焊接机器人具有高度的智能化和自主性,通过传感器、视觉系统等设备实现对焊接过程的实时监测和控制,可以对焊接质量进行自动检测和调整,大大提高了生产效率和产品质量;焊接机器人可以与其他智能设备实现无缝协作,例如,与机床、自动送料机、物流系统等设备相结合,可以实现焊接、成形、运输、检测等多个工序的自动化和智能化控制,提高生产线的整体效率和自动化程度;焊接机器人还可以通过云计算、大数据等技术实现远程控制和智能化管理,通过实时监测和分析生产数据,可以及时发现问题并采取措施,优化生产过程和提高生产效率。
关键词:焊接机器人;应用现状;关键技术;概述引言国际标准化组织(ISO)将焊接机器人定义如下:焊接机器人是从事焊接(包括切割与热喷涂)的工业机器人,为了适应不同的用途,工业机器人最后一个轴的机械接口,通常是一个连接法兰,可安装不同工具(末端执行器),装接焊钳或焊(割)枪,使之能进行焊接、切割或热喷涂。
工业机器人是一种面向工业领域的多用途、可重复编程、靠自身动力和控制能力执行工作的机器装置。
伴随先进制造技术的发展,焊接机器人应用技术也日趋成熟,在应对高效率、高质量、柔性化及恶劣工作环境需求方面其优越性不断凸显。
1焊接机器人的基本原理和特点1.1基本原理焊接机器人是一种集机械、电子、计算机等多种技术于一体的自动化设备,其工作原理复杂且多样,需要通过计算机控制系统实现各种操作。
其基本原理可以简单概括为,机械结构、传动系统、控制系统、焊接装置等多个组成部分协同工作,完成焊接操作。
焊接机器人的工作流程一般可以分为以下几个步骤:1)计算机控制系统根据预设的焊接路径和焊接参数,控制机械臂移动到焊接位置;2)焊接装置启动,将电流、气体和焊丝等送到焊接区域;3)机械臂开始运动,将焊枪移动到预设的焊接位置,开始焊接,在焊接过程中,传感器监测焊接过程的各项参数,并反馈给计算机控制系统;4)焊接结束后,计算机控制系统停止机械臂的运动,焊接装置也停止工作,完成整个焊接过程。
焊接机器人技术的发展与运用综述
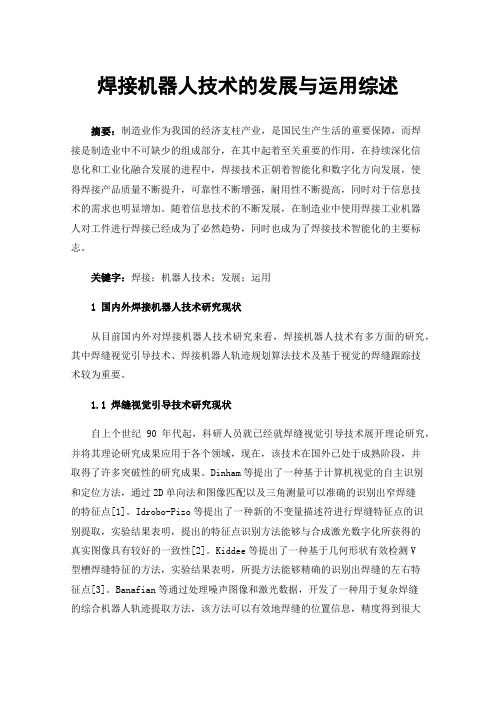
焊接机器人技术的发展与运用综述摘要:制造业作为我国的经济支柱产业,是国民生产生活的重要保障,而焊接是制造业中不可缺少的组成部分,在其中起着至关重要的作用,在持续深化信息化和工业化融合发展的进程中,焊接技术正朝着智能化和数字化方向发展,使得焊接产品质量不断提升,可靠性不断增强,耐用性不断提高,同时对于信息技术的需求也明显增加。
随着信息技术的不断发展,在制造业中使用焊接工业机器人对工件进行焊接已经成为了必然趋势,同时也成为了焊接技术智能化的主要标志。
关键字:焊接;机器人技术;发展;运用1国内外焊接机器人技术研究现状从目前国内外对焊接机器人技术研究来看,焊接机器人技术有多方面的研究,其中焊缝视觉引导技术、焊接机器人轨迹规划算法技术及基于视觉的焊缝跟踪技术较为重要。
1.1焊缝视觉引导技术研究现状自上个世纪90年代起,科研人员就已经就焊缝视觉引导技术展开理论研究,并将其理论研究成果应用于各个领域,现在,该技术在国外已处于成熟阶段,并取得了许多突破性的研究成果。
Dinham等提出了一种基于计算机视觉的自主识别和定位方法,通过2D单向法和图像匹配以及三角测量可以准确的识别出窄焊缝的特征点[1]。
Idrobo-Pizo等提出了一种新的不变量描述符进行焊缝特征点的识别提取,实验结果表明,提出的特征点识别方法能够与合成激光数字化所获得的真实图像具有较好的一致性[2]。
Kiddee等提出了一种基于几何形状有效检测V型槽焊缝特征的方法,实验结果表明,所提方法能够精确的识别出焊缝的左右特征点[3]。
Banafian等通过处理噪声图像和激光数据,开发了一种用于复杂焊缝的综合机器人轨迹提取方法,该方法可以有效地焊缝的位置信息,精度得到很大的改善[4]。
Aviles等提出了基于人工神经网络架构的工业焊接机器人自动焊接系统,实验结果表明,该系统可以准确的识别出焊缝的尺寸、外形等特征[5]。
相对于国外,国内科研人员对焊缝识别方法的研究较晚。
- 1、下载文档前请自行甄别文档内容的完整性,平台不提供额外的编辑、内容补充、找答案等附加服务。
- 2、"仅部分预览"的文档,不可在线预览部分如存在完整性等问题,可反馈申请退款(可完整预览的文档不适用该条件!)。
- 3、如文档侵犯您的权益,请联系客服反馈,我们会尽快为您处理(人工客服工作时间:9:00-18:30)。
焊接机器人文献综述关节机器人对基于视觉反馈控制的激光焊接的焊缝追踪摘要:激光焊接对于机器人轨迹精度有相当高的要求。
为了提高机器人激光焊接时的动态轨迹精度,人们基于立体视觉反馈控制的原理提出一种新的三维焊缝追踪的方法。
这种方法建立了一种可视反馈控制系统,在该系统中有两个集中于一点的相机被安装在工业机器人的后面。
人们建造了一种具有坐标系统的工具以便把机器人最终环节的位置转移到该工具上。
人们提出了一种GPI 转移方法,这种方法是利用双目望远镜可视技术和一种逐行选配的修改法则来计算激光焦点和焊缝的位置,它使得激光焦点和焊缝之间的动态轨迹错误可以计算出来。
人们最终控制机器人的移动,并且在机器人运动学的基础上尽可能减少运动轨迹的错误。
实验结果表明,这种方法能有效改善用于激光焊接的工业机器人的运动轨迹的精度。
关键词:工业机器人,视觉反馈,焊缝跟踪,轨迹精度。
1 引言目前,卖给客户的关节机器人仅仅能够保证位置精度而不能保证运动轨迹。
然而,随着制造加工业的发展,一些高速和高精度的工作,例如激光焊接和切割,对轨迹精度有十分高的要求。
此外,在严格地结构化环境下目前的工业仅能够在预定的命令下移动,这限制了他们的应用范围。
人们提出了许多研究计划来改善机器人在人们所认识的环境下的能力。
作为一个重要的测量方法,视觉对改善工业机器人在人们所认识的不同的环境下的能力起着重要作用。
参照文献[1],人们以位置为基础建造了一种具有可视伺服系统的工业机器人,并且提出了一种运算法则,当事先知道物体一些特征点的距离时,利用这种法则就可以用一台照相机估计出物体的位置和外形。
参照文献[2],基于eye-in-hand的可视伺服结构,物体的平面移动轨迹实现了一种eye-on-object的方法。
参照文献[3],有这样一个问题:机器人最终环节的真实位置与人们用空间路径规划和图像基础控制的方法所预期的位置相差很远。
参照文献[4],人们开发了一种工业火焰跟踪系统来切割视觉上的平面图形。
T.-J.小湖等人(艾德):机械手。
焊接处。
,Intellige。
&自动化、LNCIS 362, pp. 281–287,2007. Springer-Verlag Berlin Heidelberg 2007在本文中,为了改善激光焊接机器人移动轨迹的准确度,在轨迹追踪的过程中利用了用于焊缝识别[5]的GPI转移方方法,并且人们提出了一种改善过的运算法则以便更加精确地重建轨迹线和激光焦点。
与此同时,人们巧妙的建立了一种工具坐标系使得工具转移位置的计算容易而又快捷。
人们在机器人运动学的基础上计算机器人的改变位置,并最终控制机器人的移动以及尽可能的减少轨迹的错误。
2 激光焦点和轨迹线的三维重建所建立的机器人视觉伺服系统的硬件如如1所示。
一个激光加工工具和两个其中,(CLXi,CLYi,CLZi)--{CL}中线段上一点的坐标系,mm(CLl ,CLm ,CLn )--在{CL}中被检测线段的方向矢量,mm控制系统的提出是为了通过移动工业机器人来控制轨迹线上的激光焦点。
为了控制机器人的运动,轨迹线上的起始激光焦点应预先计算出来。
因为,焊接线的曲率通常很小,所以,焊接线被近似的看成是由许多直线组成的。
起始发现的问题变成计算直线中激光焦点M 的起始点N 。
构建一个覆盖点M 的平面并且与轨迹线垂直。
因此,平面与轨迹线的交点就是起始点。
其中,(CL X M ,CL Y M ,CL Z M )--在{CL}中激光焦点的坐标系,mm通过等式(3)就可以获得{CL}中起始位置(CL XN ,CL YN ,CL ZN )。
3 转置计算改变起始位置的坐标系,以及从{CL}到{T}的激光焦点,然后,通过{T}中的Jacobian矩阵在共同的空间中计算转化后的坐标系。
如下所示构建工具坐标系{T}(如图2所示)。
(1) 选择激光焦点OT 作为初始点,(2) 选择激光束作为ZT ,从纤维手电筒指向物体的焊接处,(3) XT 轴通过等式(4)来确定:(4) YT 轴通过等式(5)来确定:T E T E T E x z y += (5) 其中,E X CL —对{E}中X CL 的描述E X T ,E y T ,E Z T —对{E}中X T ,y T ,Z T 的描述{T}中TPMN 转换通过等式(6)来计算:()M N T T CL CL CL E E T MN -=p T (6) 在{T}中Jacobian 矩阵的计算与{E}中的相似,唯一的区别在于用n-1Bn =n-1An ETT 来代替n-1An 。
通过这种方法,工具末端的转置计算变成了机器人末端的转置计算。
这将更加容易和快捷。
(n-1An 是转置坐标系从n-1点的坐标系到最后一点的坐标系。
)当开始追踪时,保持机器人最终环节的方向不变。
用{T}中的Jacobian 矩阵在共同的空间内计算转换位置:[]()1661101⨯⨯-⨯⎥⎦⎤⎢⎣⎡=MN T n T n T p J qn qi q (7) 其中,qi ,(i=1,2,…,n )--机器人焊接点i 的转换点n —机器人焊接点的数目TJ —{T}中的Jacobian 矩阵4 实验与分析实验结果表明轨迹检测以及基于音响视觉的焊接机器人控制系统可以很好的用在轨迹识别,检测和自动追踪中。
即时追踪的错误少于0.5mm 。
例如,两块钢板紧紧地撞在一起而没有产生沟槽,机器人末端的追踪速度是20mm/s 。
焊缝(轨迹线)的位置和方向不能 预先知道。
图3a 是追踪前所拍摄的图像。
在图像中有两条短的白色平行线,它们是用来搜索的照相机的镜头下部的边界;长的白色直线是通过GPI 转移方式所探测到的轨迹线,白色的圆点是激光焦点,黑色的方形点是激光焦点和通过音响视觉运算法则在3维空间中所计算出来的轨迹线的起点。
图3b 所展示的是追踪结果的图像,其中激光焦点已经沿着焊接线移动到了其起点的位置。
(a )追踪前的图像 (b )追踪后的图像图4.左侧照相机追踪前后的图像 X,Y ,Z 轴上的错误和追踪到的空间距离上的错误如图4所示。
实验结果表明X,Y ,Z 轴上的错误的误差小于0.3mm ,空间距离上的错误的误差小于0.4mm 。
系统不仅能够自动的识别焊缝,并且在即时的轨迹追踪和控制中满足焊接的要求。
5 总结在这篇文章中,人们提出了让用于激光焊接的关节机器人进行3维焊缝追踪的方法,其基础是音响视觉反馈控制。
在例如激光焊接和切割的精密材料加工过程中,这种方法可以改善关节机器人动态轨迹的精确度。
通过人们所提出的这种运算法则,轨迹线和激光焦点可以以三维视觉的方式重建。
通过一个适当的工具坐标系,所需要的代替工具可以容易而又快捷的计算出来。
在机器人运动学的基础上,人们控制机器人的最终运动,并尽可能的减少轨迹的错误。
试验结果表明这种方法可以有效的提高激光焊接机器人的轨迹精度,并且应用这种方法的系统可以满足高精度轨迹追踪的要求。
鸣谢这项研究受到中国国家自然科学基金会(编号:50275083),以及用于高等教育博士计划的研究基金(编号:20020003053)的支持。
参考文献[1].Mana Saedan,Marcelo H.以3维视觉为基础的工业机器人的控制[A].Proc ofIASTED Intel on Robotics and Applications[C]. 福罗里达州,美国。
11月,2001;152-157[2].王建华,赵晓光,谭明.5-DOF可视伺服机器人追踪控制的研究[J].机器人.2005,27(3):215-219(中国)[3].Mezouar Y,Chaumette F.用于图像基础控制的计划[J].关于机器人学和自动化的IEEE Trans,2002,18(4):534549.[4].徐阚烈,费仁清,王晓刚等.关于2维线段追踪系统的研究[J].上海大学学报.1999,5(4):348-352(中国)[5].张文曾,陈强,杜洪等.Gray Projecting Integral Method for Line Dectection[J].清华大学学报(科技).2005,45(11);1446-1449(中国)管道焊接机器人的可视焊缝追踪系统袁立,德旭,严志国,和闵谭1.综合系统和智能科学重点实验室,自动化协会,中国科学院2.北京中国科学院研究生学院,100080P.R.中国(徐德,李园,谭)@/********************,ac,cn摘要:人们提出了一种以产生可视光线为基础的焊缝追踪系统,这种系统被应用于管道焊接机器人中。
首先,在对焊接表面激光反射和照相机的位置,激光所在的平面以及焊接后激光条纹图像的效果进行分析的基础上,设计出了视觉传感器。
为了防止在焊缝图像中出现严重的反射扰乱,人们开发了图像处理和特征抽取的运算法则。
为了对管道焊接进行焊缝追踪,人们采取了一种图像视觉控制系统。
人们通过控制管道焊接机器人的焊缝追踪实验来证实这个系统的性能。
1 引言在涉及机器人焊接的相关问题中,焊缝追踪是其中的一个重要的问题,它也是进行高质量的自动化焊接的基础。
工业上的焊接机器人大部分用于教学,并且机器人重复这个路径以满足焊接中光束的位置要求。
在焊接机器人的这种工作模式中存在一些问题,例如焊接位置的不精确性,由热量扩散而导致焊接处的变形与扭曲。
这些问题导致光束偏离其理论上的焊接路径,所以在焊接的过程中控制光束的焊缝轨迹是必要的[1]。
其次,管道焊接机器人不能预先对焊缝进行定义,因为当管道改变方向时,焊缝可能偏离管道内部的位置。
焊缝的轨迹可以随着轴线方向上管子的移动而改变。
在这种情况下,这种模式就不适合进行管道的焊接,并且焊接机器人需要修正光束和即时焊接时焊缝之间偏移。
为了避免在移动管道时出现焊缝的偏离,Prestion-Eastin Inc.提出了一种程序来控制轴线方向上管子的移动[2]。
Ref[3]参与讨论了当管道方向改变时管子在轴线方向上移动的原理。
解决问题的办法是用三自由度多机械手来升降管子,调整管子的位置,并摆正管子的方向。
这两种方法仅和管子的移动有关。
事实上,当管子改变方向时,焊缝将偏离其原来的位置。
然后,在进行高质量的焊接时就需要焊缝追踪系统。
T.-J. Tarn et al. (Eds.):机器人.焊接.,智能和自动化,LNCIS 362,pp.391-399,2007 Springer-Verlag Berlin Heidelberg 2007有一些种类的焊缝追踪系统通过不同种类的传感器开发出来。
这种以激光作为光线的可视传感器被广泛的应用,因为焊缝具有可靠性以及大量的信息,并且用于焊缝追踪系统的可视传感器被看做为自动焊接中前景很好的一种传感方法[4]。