轧辊磨工艺
高铬钢轧辊热处理工艺流程

高铬钢轧辊热处理工艺流程随着工业技术的不断发展,高铬钢轧辊在冶金行业中的应用也越来越广泛。
高铬钢轧辊是一种重要的轧钢设备零部件,对于材料的性能和寿命有着重要的影响。
热处理是提高高铬钢轧辊的性能和寿命的关键工艺之一。
热处理工艺流程的合理性和严谨性,直接影响轧辊的质量和寿命。
因此,对高铬钢轧辊的热处理工艺流程进行深入的研究和分析,对于提高轧辊的性能和寿命有着重要的意义。
一、热处理工艺流程概述高铬钢轧辊的主要工艺流程包括热处理前的准备工作、热处理工艺、热处理后的处理工艺等几个方面。
下面对这几个方面分别进行详细介绍。
1. 准备工作高铬钢轧辊在进行热处理之前,需要进行一些准备工作。
首先是对轧辊进行表面清洗和除油处理,以保证热处理时的表面质量。
其次是对轧辊的尺寸进行严格的检查和测量,确保尺寸符合要求。
最后还需要对轧辊的化学成分进行检测和分析,以确定材料的质量和性能。
2. 热处理工艺热处理工艺是高铬钢轧辊热处理的关键环节。
热处理工艺包括加热、保温、冷却等几个主要过程。
首先是将轧辊放入加热炉中进行加热,以达到所需的温度。
在加热过程中,需要控制加热速度和温度均匀性,以避免产生过热和温度不均匀的现象。
加热到一定温度后,将轧辊保温一段时间,使得材料的组织发生相应的变化。
最后是对轧辊进行冷却处理,使得材料的组织和性能得到稳定。
3. 热处理后的处理工艺热处理后的处理工艺主要包括表面清洗、除氧化皮、打磨和检测等几个环节。
首先是对轧辊进行表面清洗,除去热处理时产生的氧化皮和其他杂质。
然后再对轧辊进行打磨处理,以使得轧辊的表面粗糙度和尺寸精度达到要求。
最后是对轧辊进行质量检测,以保证其性能和质量。
以上就是高铬钢轧辊热处理工艺流程的概述。
下面将对每一个环节进行详细的介绍和分析。
二、准备工作高铬钢轧辊在进行热处理之前,需要进行一些准备工作,以保证热处理的顺利进行和质量的保证。
以下将对准备工作进行详细介绍。
1. 表面清洗和除油处理在进行热处理之前,需要对轧辊进行表面清洗和除油处理,以保证热处理时的表面质量。
磨辊 磨盘、轧辊、轴齿等硬面堆焊修复技术及施工方案
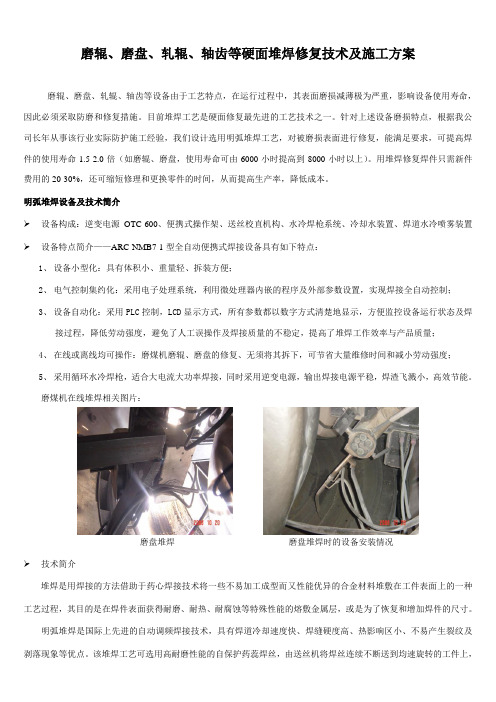
磨辊、磨盘、轧辊、轴齿等硬面堆焊修复技术及施工方案磨辊、磨盘、轧辊、轴齿等设备由于工艺特点,在运行过程中,其表面磨损减薄极为严重,影响设备使用寿命,因此必须采取防磨和修复措施。
目前堆焊工艺是硬面修复最先进的工艺技术之一。
针对上述设备磨损特点,根据我公司长年从事该行业实际防护施工经验,我们设计选用明弧堆焊工艺,对被磨损表面进行修复,能满足要求,可提高焊件的使用寿命1.5-2.0倍(如磨辊、磨盘,使用寿命可由6000小时提高到8000小时以上)。
用堆焊修复焊件只需新件费用的20-30%,还可缩短修理和更换零件的时间,从而提高生产率,降低成本。
明弧堆焊设备及技术简介➢设备构成:逆变电源OTC-600、便携式操作架、送丝校直机构、水冷焊枪系统、冷却水装置、焊道水冷喷雾装置➢设备特点简介——ARC-NMB7-1型全自动便携式焊接设备具有如下特点:1、设备小型化:具有体积小、重量轻、拆装方便;2、电气控制集约化:采用电子处理系统,利用微处理器内嵌的程序及外部参数设置,实现焊接全自动控制;3、设备自动化:采用PLC控制,LCD显示方式,所有参数都以数字方式清楚地显示,方便监控设备运行状态及焊接过程,降低劳动强度,避免了人工误操作及焊接质量的不稳定,提高了堆焊工作效率与产品质量;4、在线或离线均可操作:磨煤机磨辊、磨盘的修复、无须将其拆下,可节省大量维修时间和减小劳动强度;5、采用循环水冷焊枪,适合大电流大功率焊接,同时采用逆变电源,输出焊接电源平稳,焊渣飞溅小,高效节能。
磨煤机在线堆焊相关图片:磨盘堆焊磨盘堆焊时的设备安装情况➢技术简介堆焊是用焊接的方法借助于药心焊接技术将一些不易加工成型而又性能优异的合金材料堆敷在工件表面上的一种工艺过程,其目的是在焊件表面获得耐磨、耐热、耐腐蚀等特殊性能的熔敷金属层,或是为了恢复和增加焊件的尺寸。
明弧堆焊是国际上先进的自动调频焊接技术,具有焊道冷却速度快、焊缝硬度高、热影响区小、不易产生裂纹及剥落现象等优点。
高速铝箔轧机轧辊的磨削

k W
7 7
1 8
2 0
18 I 3 .8 4 3
.
理论 推 导 分 析 是 正 确 的, 为 优化 工 艺 过 程 和
模 具设 计 提 供 了 科 学 依 据 。
20 .9
4 8 .2
5 2 .3
—7 8 .
2 2
23 I53 i 54 .0 .0 .3
—24 . 参 考 文 献
将 平衡 主 轴 放在 平衡 架上 , 与 平衡 架导
就不 进刀 ( 向进给),速度 放 慢 进 行光 横 磨 。 最 后 按 粗 糙度 要 求 精 修 砂 轮 , 完 成 磨 削
工序 。
轨成9 。 j O角
使 砂轮 在平 衡 架 上 自 由滚 动 , 当砂 轮 停 止 时 用 粉笔 在最 上面 一 点 ( 轻 点 )作 一 记 最
~ 澜粮 酬 一辊 简 盯/ 一一 ,一 和 = 舨 蛐 揣 誓
一一兢 贼 粕靴 一 ~
板 形 变坏 。调 整 轧 制 油 可 勉 强 维 持 轧 制 。如 果 锥度 特别 大 时 ( 端 差 达 O 0 5 米 以 两 .1毫
上 ) , 轧 制 基 本无 法 进 行 。
前 ,应 事 先 按 轧 制 工 艺 要 求 的 凸 度 值 , 将 辊 形 成形 机 构 的 比例 杆 调 好 , 使 轧辊 弧 形符 合 轧 制 要 求 的辊 形 。 再 将 轧辊 表面 原 有 的缺 陷 如 辊 眼 、 各 种 擦 伤 印痕 、椭 圆 度 、 疲 劳层 及
砂轮组织 的橙紧直 接影 响磨 削生产率 和
硬,在适合轧 辊磨 削、能保证轧 辊精度和光 洁度 良好、砂轮不 易脱落的基础上,应适 当
维普资讯
冷轧辊磨削工艺

字体大小:大- 中- 小jincomai发表于08-08-07 15:58 阅读(1111) 评论(0)分类:铝板带冷轧辊的磨削是一项难度较大,对磨床性能和磨工操作水平要求都很高的工作。
目前,国内市场上委托磨削一对冷轧辊费用在5000元左右,一般的磨削成功率不会高于70%。
一对合格的冷轧辊除了要满足粗糙度、圆度、圆柱度、直径公差、凸度等技术要求外,还必须无明显表面缺陷。
对于前几项技术要求的控制相对较容易,而表面缺陷的控制难度很大[1-2]。
1 我公司M84100B磨床的基本参数和目前的性能1.1 M84100B磨床的基本参数最大磨削直径,1000 mm;最小磨削直径(新砂轮)120 mm,(旧砂轮)350 mm;工件最大旋径,1250 mm;中心高,630 mm;顶尖距,5000 mm;最大磨削长度,5000 mm;工件最大质量,20t;工件转速范围,5 r/min—50r/min;砂轮转速范围,600 r/min—1200r/min;中凸量及中凹量范围(在半径上),0.01 mm—1 mm;砂轮最大规格(新砂轮),750 mmX75 mmX305 mm;砂轮最小规格(旧砂轮),500 mmX75 mmX305 mm;砂轮横向进给量:①自动进给-调整手把每格刻度值,0.005 mm;②手动粗进给手轮每转,0.5 mm;③手动粗进给手轮每格刻度值,0.01 mm;④手动微进给手轮每转,0.002 mm—0.012 mm。
1.2 我公司M84100B磨床的性能我们在近50对冷轧辊的磨削试验过程中逐渐发现了磨床的一些缺陷,并及时在砂轮磨削、对刀、拖板浮起量调整、工艺选择等方面采取措施,来弥补各种缺陷所带来的影响。
(1) 砂轮轴及静压轴承。
这台磨床在使用中,发生过两次轧辊与砂轮碰撞的事故,还有三次因为进刀量过大,发生砂轮崩碎的事故。
经检查和分析研究发现这台磨床的砂轮轴是弯曲的;静压轴承回油管无油液回流,静压轴承的工作状态不太正常。
轧辊磨床技术操作规程

轧辊磨床技术操作规程万能轧辊磨床设备操作规程(沙钢集团沙景宽厚板厂热轧工段)一、设备简介沙钢集团沙景宽厚板厂万能轧辊磨床是由德国HERKULES制造,功能较强,技术领先于世界前列.万能轧辊磨床2006年6月安装在沙景宽厚板厂热轧工段磨辊间,专用于修磨工作辊、支撑辊,于2006年10月开始投入使用。
编辑此技术操作规程目的是加强设备维护保证工作,提高设备使用寿命,提高作业率和设备精度。
操作工、维修工负责轧辊磨床的维护、保养工作。
二、技术参数机床型号: MK84200x100型数控轧辊磨床工作范围:最大磨削直径(砂轮外径Φ900mm) 2000mm(砂轮外径Φ600mm) 2100mm最小磨削直径(砂轮外径Φ900mm) 260mm最大顶尖距 10000mm工件最大重量 130000Kg工件最大重量(用外装式活动顶尖) 10000Kg工件转速(无级变速) 3-40r,min砂轮规格(外径×宽度×孔径) Φ900x100×Φ305mm拖板纵向移动速度(z轴) 5—4000mm,min砂轮架横向(X轴)最大行程 900mm砂轮架横向(X轴)快速移动速度 625mm,min磨削中凸(中凹)量(半径) ?1.3mm连续横进给速度 0(002,0(12mm,行程1电子手轮微量进给 0(001mm,P尾架顶尖套筒行程 250mm数控测量装置的测量范围Φ260,Φ2100mm中心架支承辊颈的范围Φ250,Φ950mm中心架托瓦测量装置的测量范围Φ250,Φ950mm主要电机的参数工件(头架)电动机功率 2KW转速(无级) 750,1900r,min额定电压 40v砂轮电机功率 99KW转速(无级) l000,2000r,min额定电压 440v 拖板纵进给电机额定扭矩 42Nm转速 1500r/min 磨架横进给电机额定扭矩 16。
9Nm 转速 2000r/min 数控中高电机额定扭矩 5。
(完整版)冷轧辊的磨削工艺
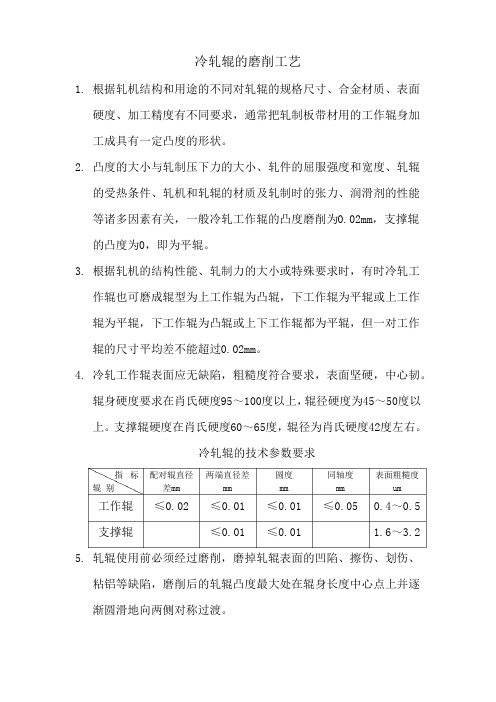
冷轧辊的磨削工艺1.根据轧机结构和用途的不同对轧辊的规格尺寸、合金材质、表面硬度、加工精度有不同要求,通常把轧制板带材用的工作辊身加工成具有一定凸度的形状。
2.凸度的大小与轧制压下力的大小、轧件的屈服强度和宽度、轧辊的受热条件、轧机和轧辊的材质及轧制时的张力、润滑剂的性能等诸多因素有关,一般冷轧工作辊的凸度磨削为0.02mm,支撑辊的凸度为0,即为平辊。
3.根据轧机的结构性能、轧制力的大小或特殊要求时,有时冷轧工作辊也可磨成辊型为上工作辊为凸辊,下工作辊为平辊或上工作辊为平辊,下工作辊为凸辊或上下工作辊都为平辊,但一对工作辊的尺寸平均差不能超过0.02mm。
4.冷轧工作辊表面应无缺陷,粗糙度符合要求,表面坚硬,中心韧。
辊身硬度要求在肖氏硬度95~100度以上,辊径硬度为45~50度以上。
支撑辊硬度在肖氏硬度60~65度,辊径为肖氏硬度42度左右。
冷轧辊的技术参数要求指标配对辊直径辊别差mm 两端直径差mm圆度mm同轴度mm表面粗糙度um工作辊支撑辊≤0.02≤0.01≤0.01≤0.01≤0.01≤0.050.4~0.51.6~3.25.轧辊使用前必须经过磨削,磨掉轧辊表面的凹陷、擦伤、划伤、粘铝等缺陷,磨削后的轧辊凸度最大处在辊身长度中心点上并逐渐圆滑地向两侧对称过渡。
6.根据实际生产的需要确保磨削质量和产品质量,砂轮的型号要进行合理的选择,考虑的主要因素有:粒度、硬度、结合剂、组织、线速度等。
轧辊磨削砂轮选择参考轧辊材质钢质轧辊磨削要求表面粗糙度Ra/um精磨(1.0以上)精磨(0.8~0.4)精磨(0.3~0.1)抛光(0.05~0.02)超精磨(0.01)磨料A.WAWA.SA粒度36~6060~80砂轮的选择硬度H.J结合剂VVVBB.R组织8、97、876、76、7WA.SA150WA.SA W63~W40WA.C W28~W14砂轮转速r/min拖板速度mm/min1000800500300J.KKFH.J磨床磨削工艺参数磨削步骤粗磨精磨抛光精抛轧辊转速r/min48504845进刀速度(横向进给量)mm0.0050.003进刀电流A1.41.21.00.84504504004500.0020.0017.磨削后轧辊表面不允许有可见横纹(水波纹)、刀花、印痕、砂眼等表面缺陷。
轧辊磨工安全技术操作规程
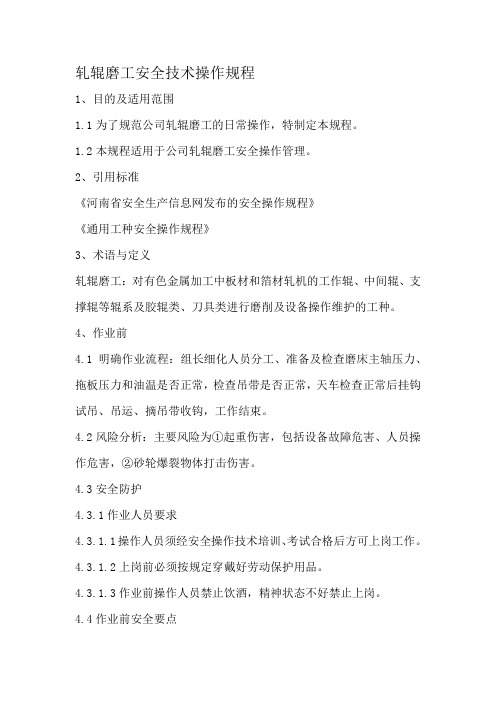
轧辊磨工安全技术操作规程1、目的及适用范围1.1为了规范公司轧辊磨工的日常操作,特制定本规程。
1.2本规程适用于公司轧辊磨工安全操作管理。
2、引用标准《河南省安全生产信息网发布的安全操作规程》《通用工种安全操作规程》3、术语与定义轧辊磨工:对有色金属加工中板材和箔材轧机的工作辊、中间辊、支撑辊等辊系及胶辊类、刀具类进行磨削及设备操作维护的工种。
4、作业前4.1明确作业流程:组长细化人员分工、准备及检查磨床主轴压力、拖板压力和油温是否正常,检查吊带是否正常,天车检查正常后挂钩试吊、吊运、摘吊带收钩,工作结束。
4.2风险分析:主要风险为①起重伤害,包括设备故障危害、人员操作危害,②砂轮爆裂物体打击伤害。
4.3安全防护4.3.1作业人员要求4.3.1.1操作人员须经安全操作技术培训、考试合格后方可上岗工作。
4.3.1.2上岗前必须按规定穿戴好劳动保护用品。
4.3.1.3作业前操作人员禁止饮酒,精神状态不好禁止上岗。
4.4作业前安全要点4.4.1检查设备各部位及安全装置是否良好,安全可靠。
检查砂轮是否有裂纹和缺口,紧固螺帽是否松动,发现问题及时处理,待一切正常后方可开车。
4.4.2砂轮质量必须符合技术要求,中心不得偏歪,否则禁止使用。
4.4.3工作前先空转1-3分钟,检查确认设备正常,方可开始工作。
4.5作业中安全要点4.5.1 磨床尾架增加胶垫时,应使用专用工具,一手操作尾架,一手加胶垫,夹紧合适避免力量过大使胶垫挤裂。
4.5.2 小磨床使用自制吊链换砂轮时,先检查吊链及安全卡是否正常,人与吊物应保持安全距离,然后进行操作;4.5.3 小磨床使用自制的旋转臂吊电机时,旋转臂下严禁站人。
4.5.4修磨砂轮时侧身对好刀,及时开启冷却液、然后撤身,为避免砂轮颗粒溅入眼睛,应戴好护目镜。
4.5.5轧辊磨削结束后,清洁表面磨削液,头架转速调至40-50r/min。
4.5.6验辊时(查看辊面质量),头架转速调至8-10r/min,操作者应站在轧辊的前方或侧面。
在线轧辊研磨技术(ORG)

鞍山钢铁集团公司 史乃安
1 概述
n
在线轧辊研磨装置(On-line Roll Grinder,简称ORG)是由 日本三菱重工开发的,主要作用:
q q q
提高精轧工作辊表面质量。 改善工作辊的不均匀磨损,控制辊型。 增加带钢的同宽轧制量,延长轧制计划,并可以实现自 由程序轧制。
n
在国外,ORG使用最多的是日本和韩国,共有20多套。 我国有三套,分别是宝钢1580热轧厂,鞍钢1780热轧生 产线和唐钢热轧厂。
工作辊表面
未使用ORG的辊型 (阴影部分为全面+段差研磨时,将被磨掉的部分)
使用全面+段差研磨后的理想辊型
全面与段差混合研磨效果示意图
n
研磨时刻:
q
板内研磨 (in bar): 在带钢轧制过程中对工作辊实施研磨
q
板间研磨(bar to bar) : 在前一带钢抛钢后与下一块带钢咬入精轧机 前的间隙时间内,对工作辊实施研磨
Ø
VG VS
VG VS VR VR
被动式
主动式 返回
q
压紧
Ø
砂轮以一定角度与工作辊接触,压紧力为恒定值(压力控制)
OH
a
返回
q
摆动
Ø
研磨时,砂轮沿工作辊表面往复运 动 每个砂轮可单独伸缩 每个砂轮都有其特定的研磨区域 上下ORG向相反方向摆动
WS DS WS DS
Ø Ø Ø
上下ORG摆动方向
2 1
q
辊面无环形沟槽,避免带钢横断面产生局部高点。这 一点,对冷轧用原料非常有利。
Ø
同宽轧制量可以达到70km以上。
未使用ORG的辊型 (轧制量45km)
使用ORG的辊型
磨轧辊磨削工艺及技术原理

2.6 轧辊配对要求(见下表)
轧辊类型
辊径允许差异范围 硬度允许差异范围
(mm)
(HS)
冷连轧机工作辊(1-4)
0.05
2
冷连轧机中间辊(1-4)
0.10
2
冷连轧机支撑辊(1-4)
1.00
2
平整机工作辊
2
平整机支撑辊
2
光整机工作辊
2
光整机支撑辊
2
注:1、配对轧辊的辊径差需符合表内的规定。 2、配对轧辊的硬度差要负荷表内的规定。
4 1 支撑辊装箱/拆箱装置
支撑辊装箱/拆箱装置
作业台上有两台抽出装 置;轧辊带箱最大重量 45t
作业台上有两台抽出装
5 1 工作辊装箱/拆箱装置
工作辊装箱/拆箱装置 置; 轧辊带箱最大重量为
7t
翻转 90 度;
支撑辊轴承座最大重量 10t
支撑辊轴承座翻转装置和工作
6 1 辊轴承座翻转装置
轴承座翻转
磨削不带箱的工作辊
电火花打毛机 3 1 ET620/8X5500-46
打毛工作辊表面
主要技术参数
轧辊不带箱最大重量 35t; 磨削直径范围 200-1400mm;
轧 辊 不 带 箱 最 大 重 量 6t; 磨削直径范围 200-900mm;
轧辊不带箱最大重量 8t; 打毛范围 Ra µm 0.8-10
最大工件长度(mm) 带有移动花盘 正常中心高度 正常设计(动压支撑托架) 最大工件重量(吨) 带有测量臂和测量横梁 标准支撑类型 轧辊磨床
2)万能磨床 WS III CP 35 201 x 5 000
最大工件长度(mm) 带有移动花盘 正常中心高度 加强设计(带静压支撑托架) 最大工件重量(吨) 带有测量臂和测量横梁 标准支撑类型 轧辊磨床
辊磨削工艺与常见磨削缺陷控制方法

轧辊磨削工艺与常见磨削缺陷控制摘要:本文通过对磨床磨削的基本原理及加工特点,轧辊磨床的基本结构与运动方式,磨床的冷却与润滑及轧辊磨削工艺等方面的阐述,分析了轧辊磨削中常见缺陷的原因并提出预防措施。
关键词:轧辊磨削工艺缺陷控制1 .磨床磨削的基本原理及加工特点1.1磨削的基本原理磨削是金属切削加工方法之一,它是以砂轮切入工件,从而得到一定的儿何形状、尺寸精度和表面光洁度较高的零件。
磨削的基本原理:以极高速度旋转的砂轮作为刀具,切入以一定速度旋转或移动的工件中,砂轮的磨粒在工件表面强烈而高速的旋转(每一磨粒完成一次切削时间只有万分之几秒),强行擦过工件,挤压表面,磨削力使工件材料发生弹性变形和塑性变形,材料组织发生内部相对移动,此间产生极高的切削温度,锋利的磨粒迫使材料脱离工件,形成切屑。
1.2磨削加工的特点磨削加工得到极广泛的应用,它有以下的特点:1)磨削加工可以获得很高的精度和表面光洁度。
一般磨床可以达到1~2级精度,表面光洁度可达到▽7~▽10,高精度的磨削光洁度可达到▽12,精度可达到0.002毫米。
2)可以加工材料范围宽。
可加工软材料,如铸铁、有色金属等,还可以加工淬火钢,如CrMn钢、T12钢、20钢经渗炭淬火等,而且可以加工硬质合金。
3)磨削加工用于精加工过程中。
磨削加工的切削深度较小,在一次行程中所能切去金属层较薄,因此只能用精加工过程中。
2. 轧辊磨床的基本结构与磨床磨削运动2.1 轧辊磨床的基本结构用于对轧辊进行成形磨削的磨床即是轧辊磨床。
轧辊磨床是外圆磨床的一个分支,是一种专用磨床。
轧辊磨床一般为轧辊移动式,其基本结构由床身、头架、尾座、砂轮架、主轴、冷却液系统和电控设备等组成。
1)床身床身是保证磨削精度的基础。
轧辊磨床,其床身用来支承轧辊,砂轮架是固定的。
2)头架用来驱动轧辊,为保证驱动的平稳性和减震,一般采用多级皮带传动。
3)尾座尾座由上下两部分组成,下部延床身移动,上部可横向移动,以使两顶尖联机与砂轮轴线平行。
磨削工艺参数对轧辊表面粗糙度的影响

随着电子信息高新技术的发展,IC 框架材料已经得到 了广泛的应用,精轧机是框架材料生产的关键设备,轧辊是 轧机的重要部件,是实现轧制过程中金属变形的直接工具, 实际使用中对轧辊质量要求非常严格,主要的质量要求有强 度、硬度、耐用性、表面粗糙度等。强度、硬度、耐用性由轧 辊自身的性质决定,而表面粗糙度由磨削加工工艺确定。轧 辊磨削精度和表面粗糙度除了依靠精良的轧辊磨床之外,对 特定的加工辊选用与之相匹配的砂轮、和磨削工艺参数也是 至关重要的。
22
0.104 0.113 0.127 0.139 0.161 0.187
28
0.111 0.119 0.135 0.147 0.172 0.193
表 4 方法二 φ85 测量结果
工件转速(m/min) 砂轮转速(m/s)
45 40 35 30
25 20
14
0.098 0.108 0.119 0.134 0.168 0.179
磨 3μm、超精磨 2μm、无火花磨削 2 次的模式磨削时,粗
糙 度 值 最 低 为 0.099μm,表 面 较 光 洁。砂 轮 速 度 为 20m/
s,辊子转速 28m/min 采用粗磨 6μm、精磨 6μm、超精磨
6μm、无火花磨削 1 次的磨
表 5 方法一第二中间辊测量结果
工件转速(m/min) 砂轮转速(m/s)
1、图 2)。
表 1 方法一工作辊粗糙度测量结果
工件转速(m/min) 砂轮转速(m/s)
45 40 35 30 25 20
14
0.048 0.058 0.065 0.069 0.084 0.085
22
0.061 0.062 0.075 0.079 0.083 0.088
(精编)轧辊磨床技术操作规程

MQ8450B型和 MQ1350B型轧辊磨床技术一.轧辊磨床的型号及主要技术参数(一)大磨床:1.型号: MQ8450B X 2700型2 .主要技术参数:最大磨削直径:Ф560mm最小磨削直径:Ф80mm最大工件长度: 2700mm最大工件重量: 1500kg砂轮直径:最大: 750mm最小: 550mm砂轮工作线速度:最大: 35m/s最小: 28m/s砂轮工作进给手轮一转移动量:粗: 4mm细: 0.5mm 砂轮进给手轮刻度值:粗:每格 0.02mm细:每格 0.0025mm最大可磨凸或凹量: 1/1000(二)小磨床:1.型号: MQ1350B X 2000型2 .主要技术参数:最大磨削直径:Ф500mm最小磨削直径:Ф25mm最大工件长度: 2000mm最大工件重量: 1000kg砂轮直径:最大: 750mm最小: 550mm砂轮线速度:最大: 35m/s最小: 28m/S砂轮进给手轮一转移动量:粗: 4mm细:0.5mm砂轮进给手轮刻度值:粗:每格 0.02mm细:每格 0.0025mm旋钮上补偿量:粗:每格 0.02mm细:每格 0.0025mm最大可磨凸或凹量: 1/1000二.操作规程:(一)开机前的准备与检查工作:1.磨床操作者必须事先认真学习机床“使用说明书”,熟悉本机床的性能、规格,主要技术参数,熟悉各操作手柄、手轮、开关、按钮的位置、作用及使用方法,弄懂机床各部件的动作原理及相互间的关系。
2 .开机前应认真检查各电器开关、旋钮、各手柄、手轮是否停在正确位置;砂轮及各传动皮带防护罩是否完好和紧固好;检查砂轮是否有裂纹和是否紧固好,检查各处润滑油(或润滑脂)是否需要添加。
3 .开动机床前砂轮快速进给手柄应在后退位置,砂轮离工作台的距离应不少于快速进给的行程量。
4 .用手动各部件,检查其动作是否正常。
5 .开动各电机从低速至高速转动,看是否有异常现象。
6 .启动油泵,调整油路压力、工作台润滑压力及油量,排除工作台压筒内残留的空气。
轧辊磨床磨削工艺 用途
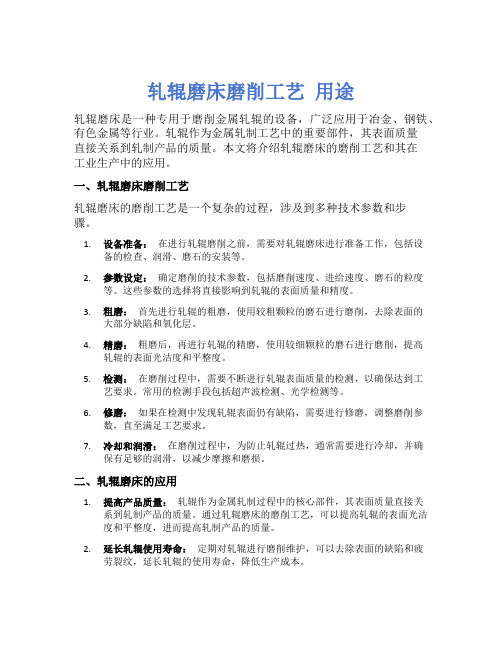
轧辊磨床磨削工艺用途轧辊磨床是一种专用于磨削金属轧辊的设备,广泛应用于冶金、钢铁、有色金属等行业。
轧辊作为金属轧制工艺中的重要部件,其表面质量直接关系到轧制产品的质量。
本文将介绍轧辊磨床的磨削工艺和其在工业生产中的应用。
一、轧辊磨床磨削工艺轧辊磨床的磨削工艺是一个复杂的过程,涉及到多种技术参数和步骤。
1.设备准备:在进行轧辊磨削之前,需要对轧辊磨床进行准备工作,包括设备的检查、润滑、磨石的安装等。
2.参数设定:确定磨削的技术参数,包括磨削速度、进给速度、磨石的粒度等。
这些参数的选择将直接影响到轧辊的表面质量和精度。
3.粗磨:首先进行轧辊的粗磨,使用较粗颗粒的磨石进行磨削,去除表面的大部分缺陷和氧化层。
4.精磨:粗磨后,再进行轧辊的精磨,使用较细颗粒的磨石进行磨削,提高轧辊的表面光洁度和平整度。
5.检测:在磨削过程中,需要不断进行轧辊表面质量的检测,以确保达到工艺要求。
常用的检测手段包括超声波检测、光学检测等。
6.修磨:如果在检测中发现轧辊表面仍有缺陷,需要进行修磨,调整磨削参数,直至满足工艺要求。
7.冷却和润滑:在磨削过程中,为防止轧辊过热,通常需要进行冷却,并确保有足够的润滑,以减少摩擦和磨损。
二、轧辊磨床的应用1.提高产品质量:轧辊作为金属轧制过程中的核心部件,其表面质量直接关系到轧制产品的质量。
通过轧辊磨床的磨削工艺,可以提高轧辊的表面光洁度和平整度,进而提高轧制产品的质量。
2.延长轧辊使用寿命:定期对轧辊进行磨削维护,可以去除表面的缺陷和疲劳裂纹,延长轧辊的使用寿命,降低生产成本。
3.提高生产效率:轧辊磨床可以实现对轧辊的自动磨削,提高了生产效率。
自动化的磨削系统可以在减少人工干预的同时,更好地控制磨削质量。
4.适用于不同金属:轧辊磨床适用于不同种类的金属轧辊,包括钢铁、铝、铜等,具有广泛的应用领域。
三、发展趋势和挑战1.智能化技术的应用:随着智能化技术的发展,轧辊磨床将更多地采用自动化、智能化的控制系统,提高生产效率和产品质量。
轧辊磨削工艺2
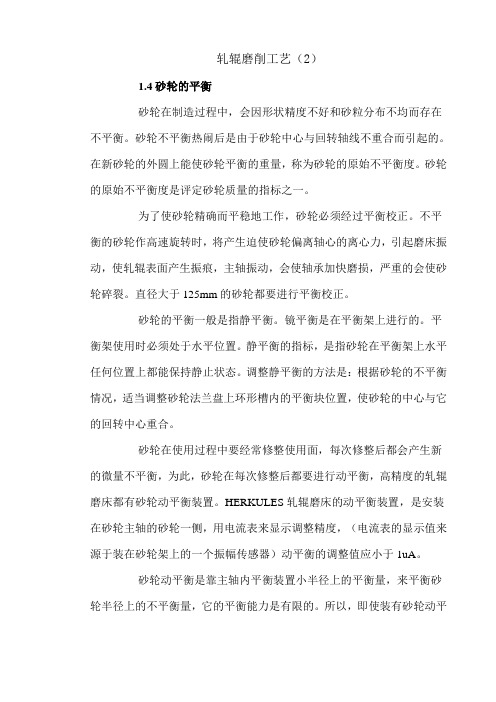
轧辊磨削工艺(2)1.4砂轮的平衡砂轮在制造过程中,会因形状精度不好和砂粒分布不均而存在不平衡。
砂轮不平衡热闹后是由于砂轮中心与回转轴线不重合而引起的。
在新砂轮的外圆上能使砂轮平衡的重量,称为砂轮的原始不平衡度。
砂轮的原始不平衡度是评定砂轮质量的指标之一。
为了使砂轮精确而平稳地工作,砂轮必须经过平衡校正。
不平衡的砂轮作高速旋转时,将产生迫使砂轮偏离轴心的离心力,引起磨床振动,使轧辊表面产生振痕,主轴振动,会使轴承加快磨损,严重的会使砂轮碎裂。
直径大于125mm的砂轮都要进行平衡校正。
砂轮的平衡一般是指静平衡。
镜平衡是在平衡架上进行的。
平衡架使用时必须处于水平位置。
静平衡的指标,是指砂轮在平衡架上水平任何位置上都能保持静止状态。
调整静平衡的方法是:根据砂轮的不平衡情况,适当调整砂轮法兰盘上环形槽内的平衡块位置,使砂轮的中心与它的回转中心重合。
砂轮在使用过程中要经常修整使用面,每次修整后都会产生新的微量不平衡,为此,砂轮在每次修整后都要进行动平衡,高精度的轧辊磨床都有砂轮动平衡装置。
HERKULES轧辊磨床的动平衡装置,是安装在砂轮主轴的砂轮一侧,用电流表来显示调整精度,(电流表的显示值来源于装在砂轮架上的一个振幅传感器)动平衡的调整值应小于1uA。
砂轮动平衡是靠主轴内平衡装置小半径上的平衡量,来平衡砂轮半径上的不平衡量,它的平衡能力是有限的。
所以,即使装有砂轮动平衡的轧辊磨床,新砂轮在使用前都必须要进行静平衡才能使用。
1.5砂轮的修整砂轮的修整直接关系到轧辊的表面质量和生产效率。
因此,砂轮修整十分重要。
用砂轮修整工具将砂轮工作面已磨钝的表面修去,以恢复工作面的切削性能和正确几何形状的方法,叫做砂轮修整。
在磨削带有凸度的轧辊时,为了消除砂轮磨削痕迹,砂轮修整时必须对砂轮两个硬角进行处理,砂轮的表面也可以修整成圆弧形。
砂轮修整用的金刚笔上的金刚石,它的大小和形状对砂轮休整的结果有一定的影响。
对于砂轮直径400mm以上的砂轮,金刚石应不小于1.5克拉,使用变钝了的金刚石要注意调换角度。
浅谈轧辊磨床磨削轧辊
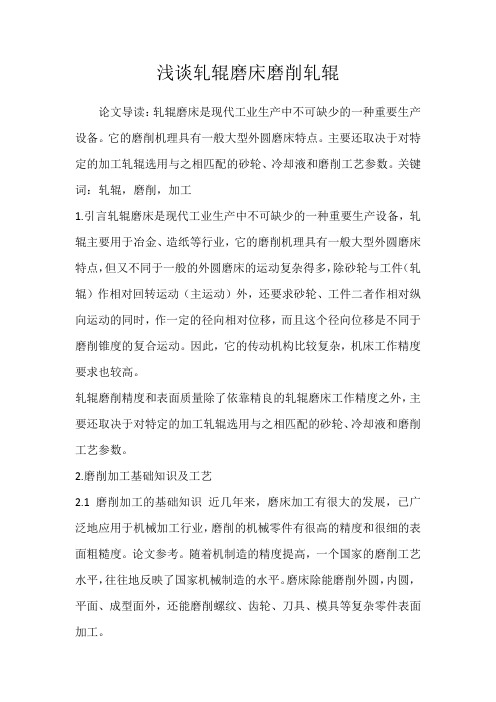
浅谈轧辊磨床磨削轧辊论文导读:轧辊磨床是现代工业生产中不可缺少的一种重要生产设备。
它的磨削机理具有一般大型外圆磨床特点。
主要还取决于对特定的加工轧辊选用与之相匹配的砂轮、冷却液和磨削工艺参数。
关键词:轧辊,磨削,加工1.引言轧辊磨床是现代工业生产中不可缺少的一种重要生产设备,轧辊主要用于冶金、造纸等行业,它的磨削机理具有一般大型外圆磨床特点,但又不同于一般的外圆磨床的运动复杂得多,除砂轮与工件(轧辊)作相对回转运动(主运动)外,还要求砂轮、工件二者作相对纵向运动的同时,作一定的径向相对位移,而且这个径向位移是不同于磨削锥度的复合运动。
因此,它的传动机构比较复杂,机床工作精度要求也较高。
轧辊磨削精度和表面质量除了依靠精良的轧辊磨床工作精度之外,主要还取决于对特定的加工轧辊选用与之相匹配的砂轮、冷却液和磨削工艺参数。
2.磨削加工基础知识及工艺2.1 磨削加工的基础知识近几年来,磨床加工有很大的发展,已广泛地应用于机械加工行业,磨削的机械零件有很高的精度和很细的表面粗糙度。
论文参考。
随着机制造的精度提高,一个国家的磨削工艺水平,往往地反映了国家机械制造的水平。
磨床除能磨削外圆,内圆,平面、成型面外,还能磨削螺纹、齿轮、刀具、模具等复杂零件表面加工。
磨床—磨床在磨削工件时,按加工要求不同,工作台纵向运动的速度必须可以调整,能实现无极变速,并在换向时有一定的精度要求,磨床要具备这些条件,磨床的纵向往复运动采用了液压传动,液压传动在磨床的工作台驱动及横向快速进退等方面已广泛应用。
液压传动工作原理—在机床上为改善液压传动的性能,以满足生产加工中的各种要求,磨床工作的液压传动系统是由以下四部分组成:执行部分—液压机(液压缸、液压马达)在压力油的推动下,作直线运动或回转运动,即将液体的压力能转换为机械能。
控制部分—压力控制阀,流量控制阀,方向控制阀等,用以控制液压传动系统所需要的力速度方向和工作性能的要求。
辅助部分—油箱滤油器,油管和油管接头等。
- 1、下载文档前请自行甄别文档内容的完整性,平台不提供额外的编辑、内容补充、找答案等附加服务。
- 2、"仅部分预览"的文档,不可在线预览部分如存在完整性等问题,可反馈申请退款(可完整预览的文档不适用该条件!)。
- 3、如文档侵犯您的权益,请联系客服反馈,我们会尽快为您处理(人工客服工作时间:9:00-18:30)。
轧辊磨工艺
本文就影响轧辊磨床磨削质量的主要因素:砂轮、磨削冷却液和几个相对运动速度的匹配等工艺问题进行阐述并根据工作经验提出最优对策。
轧辊磨床是现代工业生产中不可缺少的一种重要生产设备,主要用于冶金、造纸等行业,它的磨削机理具有一般大型外圆磨床特点,但又不同于一般的外圆磨床的运动复杂得多,除砂轮与工件(轧辊)作相对回转运动(主运动)外,还要求砂轮、工件二者作相对纵向运动的同时,作一定的径向相对位移,而且这个径向位移是不同于磨削锥度的复合运动。
因此,它的传动机构比较复杂,机床工作精度要求也较高。
轧辊磨削精度和表面质量除了依靠精良的轧辊磨床工作精度之外,主要还取决于对特定的加工轧辊选用与之相匹配的砂轮、冷却液和磨削工艺参数。
砂轮的选择
选择砂轮主要应满足如下要求:精磨时砂轮磨削时间要短,损耗要小;精磨时要求砂轮磨削发热小,微刃性好,磨削时不应有自励现象。
1.磨料的选择
、对于淬硬或非淬硬的钢质轧辊选用刚玉砂轮;而冷硬铸铁轧辊、橡胶辊、铜轧辊、花岗石辊子则使用碳化硅砂轮。
对不同材质的钢质轧辊还应选择与之相匹配的刚玉砂轮,才能获得较高的磨削精度和表面质量。
如合金钢轧辊选用铬刚玉(PA)砂轮,耐热合金钢轧辊使用锆刚玉(ZA)砂轮,对不锈钢轧辊要采用单晶刚玉(SA)。
2.粒度的选择
粗磨时选用粗粒度(24~60)砂轮;精磨时选用细粒度(60~100)砂轮;精密磨削时采用150粒度砂轮;超精磨削或镜面磨削时,一般使用微粉(W63~W14)砂轮。
3.硬度的选择
磨削辊面越硬,砂轮硬度应当选择越软。
(1)如果砂轮磨损太快,说明对于特定加工的轧辊所选用的砂轮太软,可采取以下改善措施:
A.提高砂轮的线速度;
B.提高拖板纵向进给速度,即工件每转拖板纵向进给量增加到砂轮宽度的2/3~3/4;
C.降低轧辊的速度。
如果采取上述措施后尚未取得明显的磨削效果,说明砂轮太软,不适用,应选择硬一点的砂轮。
(2)如果磨削辊子时,砂轮明显受阻(吃力)或很脏,钝化砂粒不易脱落,砂轮易粘着磨屑,磨削辊面出现烧伤、拉毛,则说明选用的砂轮太硬,可采取以下措施改善:
A. 降低砂轮线速度;
B. 提高辊子速度。
如果采取上述措施后尚未取得明显的磨削效果,说明砂轮太硬,应选择软一点的砂轮。
4.结合剂的选择
轧辊辊面除镜面磨削时选用树脂结合剂的砂轮外,其它磨削类型均以采用陶瓷砂轮为好。
二、磨削冷却液的选择
(1)磨削冷却液的作用
A.冷却作用
由于磨削区域无数磨削点的瞬时高温形成热聚集现象,在磨削和冷却过程中,被磨辊子
极薄一层表面与辊子内部造成很高的温度差,形成磨削热应力。
如果磨削热应力超过辊子材料的强度,辊子表面即会产生裂纹;如果磨削温度超过辊子材料的临界温度,则辊面发生磨削烧伤。
因此,在磨削过程中要求始终供给充足的冷却淮,将已产生的磨削热迅速从磨削区域带走。
B.清洗作用
细微的磨屑镶嵌在硝轮空隙中,破坏了砂轮的微刃性,降低了砂轮的磨削性能,并容易划伤辊子表面。
因此,要求磨削冷却液表面张力低、流动性好、渗透性强,在磨削区域起到良好的清洗作用,冲走磨屑和脱落的砂粒,保持砂轮的磨削性能。
C.防锈作用
磨削冷却液所含的防锈添加剂是一种极性很强的化合物,它在金属表面形成保护膜或与金属化合形成钝化膜,防止金属与腐蚀介质接触而起防锈作用。
(2)常用磨削冷却液
A.皂化液:润滑性较好,防锈性差,冷却性能一般,使用周期短。
B.化学磨削冷却液:防锈性、冷却性较好。
一般化学液中均含有亚硝酸钠,故有一定危害性。
C.新型磨削液:目前国内国外不断开发新型的环保的磨削液,无臭味,冷却、清洗性能优异,防锈防蚀效果好,但价格较高。
三、轧辊磨削工艺
(1)砂轮速度
粗、精磨钢质轧辊25~35m/s
粗、精磨冷硬铸铁轧辊20~25m/s
超精磨削、镜面磨削时15~20m/s
(2)工件(轧辊)速度
粗磨时30~50m/min
精磨时15~30m/min
精密抛光磨削时10~15m/min
当磨削细长辊子时应采用低速,尤其是磨削辊身尺寸小的光压延辊时,工件轧辊的速度小于10m/min。
(3)拖板纵向进给速度
粗磨时240~600m/min;或取工件每转拖板纵向进给量约为砂轮宽度的2/3~3/4。
精磨时80~200m/min;或取工件每转拖板纵向进给量约为砂轮宽度的1/4~1/2。
(4)拖板每往复行程横进给量
粗磨时横进给量应根据轧辊的硬度和磨削辊面的直径而定,一般取0.03~0.05mm/往复行程。
对于材料硬、辊颈大的轧辊,应减小横进给量。
精磨时0.005~0.01mm/往复行程。
精密抛光磨削时0.002~0.005mm/往复行程。
(5)操作工艺注意事项。
A.按特定的工件选择砂轮,并作砂轮平衡和修整。
B.精磨轧辊时,上班后机床应开车空运转30分钟,待机床热平衡稳定和液压油排净空气后,再时行磨削加工,便于稳定磨削精度。
C.在整个磨削过程中,特别是超精磨削和抛光镜面磨削时,保证供给充分的、清洁的冷却液,避免磨削烧伤、表面划痕等磨削缺陷的产生。
D.对于精度要求高的辊子,在无进给光磨时,可以采取一边磨削,一边使辊子慢速范围内不断变换转速,以减少或打乱机床各种频率的振动对磨削圆度和磨削波纹的影响,提高轧辊磨削质量。