橡胶硫化的基本知识
橡胶硫化原理

橡胶硫化原理橡胶硫化是指将橡胶原料加入一定量的硫化剂,在一定的温度和时间下,使其产生化学反应,从而使橡胶原料发生交联,形成橡胶制品的过程。
橡胶硫化的目的是提高橡胶原料的物理力学性能、抗老化性能和耐热性能,从而保证橡胶制品的使用寿命和安全性。
硫化剂的种类及作用常见的硫化剂包括硫、硫代硫酸酯、硫化氢、过硫酸盐、亚硝基化合物等。
其中硫化氢为典型的亲核试剂,为硫化反应提供活化的硫端;过硫酸盐为一种自由基引发剂,可以加速硫化反应的进行。
不同的硫化剂具有不同的反应机理和反应速度,且选用的硫化剂与橡胶种类和用途有关。
一般情况下,硫化速度越快、交联密度越高,橡胶制品的物理力学性能越优良。
硫化工艺的参数橡胶硫化的工艺参数包括硫化温度、硫化时间、硫化剂用量、交联密度、交联结构等。
这些参数之间相互影响,必须合理协调,才能得到优良的橡胶制品。
硫化温度是指橡胶制品在硫化过程中所经历的温度。
温度过高会导致硫化过程过快,造成橡胶制品内部交联密度不均、外部硫化层脆化;温度过低则会导致硫化速度缓慢、硫化程度不足、物理力学性能不好。
一般情况下,橡胶硫化的温度范围为120℃-180℃,不同的硫化剂对应不同的合理温度范围。
硫化剂用量是指在一定的温度、时间下,为了达到预定的交联密度所需的硫化剂量。
硫化剂的用量和硫化剂种类、硫化温度、硫化时间、交联密度等参数有关。
硫化剂用量过多会导致硫化密度过高、物理力学性能不足、成本增加;硫化剂用量过少则会导致硫化程度低、交联密度不足、物理力学性能不好。
一般情况下,硫化剂用量为1%-10%左右。
交联密度是指在橡胶硫化过程中,橡胶分子链之间所形成的交联点的数量和密度。
交联密度直接影响橡胶制品的物理力学性能、热化学性能和耐磨性能等。
交联密度越高,橡胶制品的物理力学性能越好,但过高的交联密度可能导致橡胶制品在低温下脆化;交联密度越低,橡胶制品的导电性和热传导性等性能越好,但是物理力学性能不好,容易脱层、开裂等。
橡胶的硫化过程
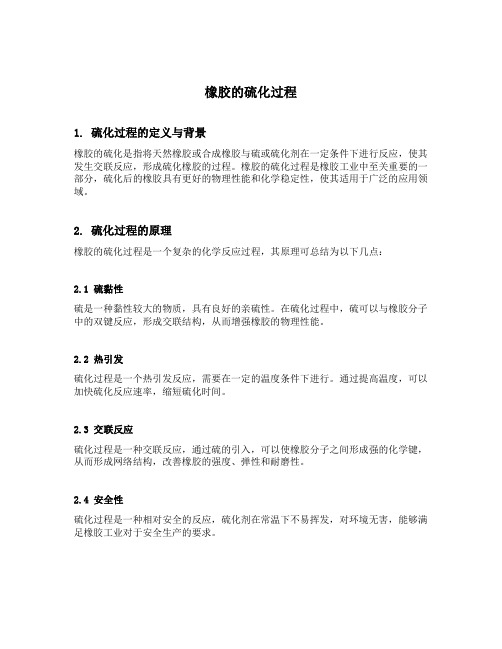
橡胶的硫化过程1. 硫化过程的定义与背景橡胶的硫化是指将天然橡胶或合成橡胶与硫或硫化剂在一定条件下进行反应,使其发生交联反应,形成硫化橡胶的过程。
橡胶的硫化过程是橡胶工业中至关重要的一部分,硫化后的橡胶具有更好的物理性能和化学稳定性,使其适用于广泛的应用领域。
2. 硫化过程的原理橡胶的硫化过程是一个复杂的化学反应过程,其原理可总结为以下几点:2.1 硫黏性硫是一种黏性较大的物质,具有良好的亲硫性。
在硫化过程中,硫可以与橡胶分子中的双键反应,形成交联结构,从而增强橡胶的物理性能。
2.2 热引发硫化过程是一个热引发反应,需要在一定的温度条件下进行。
通过提高温度,可以加快硫化反应速率,缩短硫化时间。
2.3 交联反应硫化过程是一种交联反应,通过硫的引入,可以使橡胶分子之间形成强的化学键,从而形成网络结构,改善橡胶的强度、弹性和耐磨性。
2.4 安全性硫化过程是一种相对安全的反应,硫化剂在常温下不易挥发,对环境无害,能够满足橡胶工业对于安全生产的要求。
3. 硫化过程的条件与方法橡胶的硫化过程需要一定的条件和方法,以确保硫化反应能够顺利进行。
3.1 温度温度是控制硫化反应速率和硫化时间的重要因素。
通常,硫化反应需要在高温条件下进行,一般为100-200摄氏度。
通过调节温度,可以控制硫化反应的速率和前进程度。
3.2 硫化剂硫化剂是触发硫化反应的重要因素,一般采用有机硫化剂或无机硫化剂。
常用的有机硫化剂有硫醇、硫胺等;无机硫化剂主要是硫。
不同的硫化剂对橡胶的硫化反应速率和效果有所差异,需要根据具体应用需求选择合适的硫化剂。
3.3 添加剂为了改善橡胶硫化过程的性能和效果,通常会添加一些辅助剂,如加速剂、活性剂、抗老化剂等。
这些添加剂可以提高硫化反应速率、改善硫化网络结构、延缓橡胶老化等,从而提高橡胶的物理性能和耐久性。
3.4 硫化方法橡胶的硫化方法主要有热硫化和冷硫化两种。
热硫化是在高温条件下进行的,常用于天然橡胶和低饱和度合成橡胶;冷硫化是在常温条件下进行的,常用于高饱和度合成橡胶。
很经典的橡胶硫化理论知识
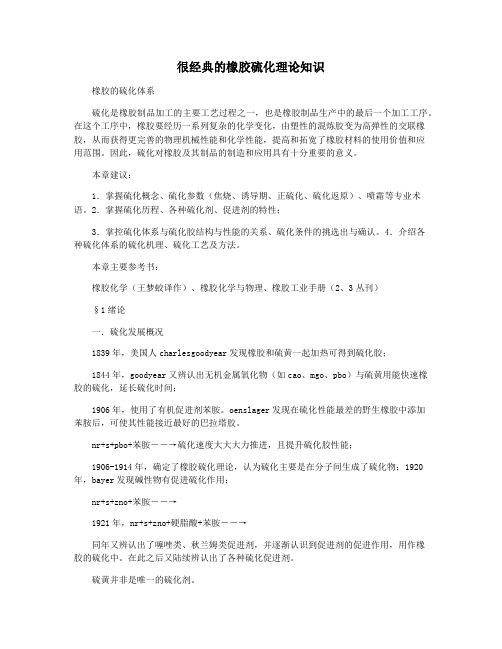
很经典的橡胶硫化理论知识橡胶的硫化体系硫化是橡胶制品加工的主要工艺过程之一,也是橡胶制品生产中的最后一个加工工序。
在这个工序中,橡胶要经历一系列复杂的化学变化,由塑性的混炼胶变为高弹性的交联橡胶,从而获得更完善的物理机械性能和化学性能,提高和拓宽了橡胶材料的使用价值和应用范围。
因此,硫化对橡胶及其制品的制造和应用具有十分重要的意义。
本章建议:1.掌握硫化概念、硫化参数(焦烧、诱导期、正硫化、硫化返原)、喷霜等专业术语。
2.掌握硫化历程、各种硫化剂、促进剂的特性;3.掌控硫化体系与硫化胶结构与性能的关系、硫化条件的挑选出与确认。
4.介绍各种硫化体系的硫化机理、硫化工艺及方法。
本章主要参考书:橡胶化学(王梦蛟译作)、橡胶化学与物理、橡胶工业手册(2、3丛刊)§1绪论一.硫化发展概况1839年,美国人charlesgoodyear发现橡胶和硫黄一起加热可得到硫化胶;1844年,goodyear又辨认出无机金属氧化物(如cao、mgo、pbo)与硫黄用能快速橡胶的硫化,延长硫化时间;1906年,使用了有机促进剂苯胺。
oenslager发现在硫化性能最差的野生橡胶中添加苯胺后,可使其性能接近最好的巴拉塔胶。
nr+s+pbo+苯胺――→硫化速度大大大力推进,且提升硫化胶性能;1906-1914年,确定了橡胶硫化理论,认为硫化主要是在分子间生成了硫化物;1920年,bayer发现碱性物有促进硫化作用;nr+s+zno+苯胺――→1921年,nr+s+zno+硬脂酸+苯胺――→同年又辨认出了噻唑类、秋兰姆类促进剂,并逐渐认识到促进剂的促进作用,用作橡胶的硫化中。
在此之后又陆续辨认出了各种硫化促进剂。
硫黄并非是唯一的硫化剂。
1846年,parkes辨认出scl的溶液或蒸汽在室温下也能够硫化橡胶,称作“热硫化法”;1915年,辨认出了过氧化物硫化;1918年,发现了硒、碲等元素的硫化;1930年,发现了低硫硫化方法;1940年,相继辨认出了树脂硫化和醌肟硫化;1943年,辨认出了硫黄给与体硫化;二战以后又出现了新型硫化体系,如50年代发现辐射硫化;70年代脲烷硫化体系;80年代提1出了平衡硫化体系。
橡胶硫化知识

橡胶硫化橡胶硫化原理橡胶受热变软,遇冷变硬、发脆,不易成型,容易磨损,易溶于汽油等有机溶剂,分子内具有双键,易起加成反应,容易老化。
为改善橡胶制品的性能,生产上要对生橡胶进行一系列加工过程,在一定条件下,使胶料中的生胶与硫化剂发生化学反应,使其由线型结构的大分子交联成为立体网状结构的大分子,使从而使胶料具备高强度、高弹性、高耐磨、抗腐蚀等等优良性能。
这个过程称为橡胶硫化。
一般将硫化过程分为四个阶段,诱导-预硫-正硫化-过硫。
为实现这一反应,必须外加能量使之达到一定的硫化温度,然后让橡胶保温在该硫化温度范围内完成全部硫化反应。
橡胶硫化的来历硫化是胶料通过生胶分子间交联,形成三维网络结构,制备硫化胶的基本过程。
不同的硫化体系适用于不同的生胶。
以橡胶(生胶)为主体,加以多种辅助材料而成的合成体、(辅助材料有几大体系、填充补强、硫化、防护、增塑、特殊物质加入剂、)而硫化是包覆绝缘层或护套层以后的一种处理方法、其目的就是让辅助体系里的硫化体系发生作用,使橡胶永久交联、增加弹性、减少塑性。
硫化的名词是因最早时间是用硫磺使橡胶交联的故称硫化,沿用至今.橡胶硫化体系不饱和橡胶通常使用如下几类硫化体系。
以硫黄,有机二硫化物及多硫化物、噻唑类、二苯胍类,氧化锌及硬脂酸为主的硫化剂。
这是最通用的硫化体系。
但所制得的硫化胶的耐热氧老化性能不高。
烷基酚醛树脂。
多卤化物(如用于聚丁二烯橡胶、丁苯橡胶及丁腈橡胶的六氯乙烷)、六氯-对二甲苯。
双官能试剂[如醌类、二胺类、偶氮及苯基偶氮衍生物(用于丁基橡胶及乙丙橡胶)等]。
双马来酰亚胺,双丙烯酸酯。
两价金属的丙烯酸酯(甲基丙烯酸酯)、预聚醚丙烯酸酯。
用于硫化饱和橡胶的有机过氧化物。
饱和橡胶硫化不同种类的饱和橡胶时,可使用不同的硫化体系。
硫化三元乙丙橡胶时,使用有机过氧化物与不饱和交联试剂,如三烯丙基异氰脲酸酯(硫化剂TAIC)。
硫化硅橡胶时也可使用有机过氧化物。
乙烯基硅橡胶硫化时可在催化剂(Pt)参与条件下进行。
橡胶硫化知识一

橡胶硫化知识一1.硫化的定义硫化是胶料在一定条件下,橡胶大分子由线型结构转变为网状结构的胶联过程。
2.硫化历程2.1硫化反应过程硫化过程可以分三个阶段。
第一阶段为诱导阶段:先是硫磺分子和促进剂体系之间反应生成一种活性更大的中间化合物,然后进一步引发橡胶分子链,产生可交联的自由基或者离子。
第二阶段为交联反应阶段:可交联的自由基或者离子与橡胶分子链之间产生连锁反应,生成交联键。
第三阶段为网构形成阶段:此阶段的前期交联反应已趋于完成,产生的交联键发生重排和裂解反应,在此阶段的后期交联反应已基本停止,随之而发生的主要是交联键重排和热裂解的反应,最后得到网格稳定的硫化胶。
2.2硫化历程图A:焦烧时间(TS2)B:热硫化(TS2+B Time =TC90)C:平坦硫化D:过硫化橡胶硫化历程可以分为四个阶段:2.2.1、图中A段是热硫化开始前的延迟作用时间,相当于硫化反应的诱导期,称作焦烧时间。
长短取决于胶料配方和加工条件,主要受促进剂影响。
包括操作焦烧时间和剩余焦烧时间;操作焦烧时间指加工过程中热积累效应所消耗的焦烧时间,取决于加工条件(混炼、挤出等)。
剩余焦烧时间是指胶料在模腔加热时保持流动性的时间。
2.2.2热硫化阶段图中B 段是硫化反应中的交联阶段。
逐渐产生网构,促使橡胶弹性和拉伸强度急剧上升。
热硫化时间的长短取决于胶料配方。
这个阶段是衡量硫化反应速度的标志。
2.2.3平坦硫化阶段图中C 段相当于硫化反应中网状形成的前期。
这时,交联反应已趋完成,继而发生交联键的重排、裂解等反应,因而胶料的强度曲线出现平坦区,这段时间称为平坦硫化时间。
2.2.4过硫化阶段图中D 段以后的部分,相当于硫化反应中网构形成期的后期。
这阶段中,主要是交联键的重排作用,以及交联键和链段热裂解的反应,因此胶料的机械性能显著下降。
2.3硫化曲线的解说• ML ——最低转矩,N·m (kgf·cm )• MH ——到达规定时间之后仍然不出现平坦曲线或最高转矩的硫化曲线,所达到的最高转矩N·m (kgf·cm )•TS1——从实验开始到曲线由最低转矩上升0.1 N·m(kgf·cm)时所对应的时间,MIN•TS2——从实验开始到曲线由最低转矩上升0.2 N·m(kgf·cm)时所对应的时间,MIN•TC(x)——试样达到某一硫化程度所需要的时间,即试样转矩达到ML+X (MH-ML)时所对应的时间,MIN如X取值0.5,即TC50;X取0.9,即TC90)•硫检参数的意义:•ML:表示胶料的蠕变性,ML越低,蠕变性越好,反之,越差。
橡胶硫化工艺
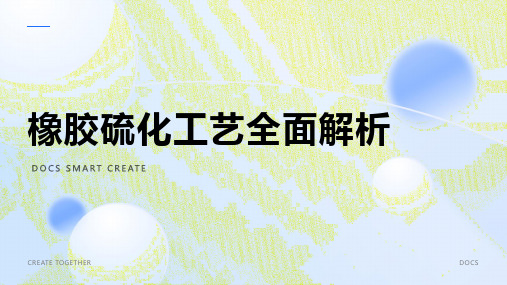
橡胶硫化工艺的未来发展趋势
智能化硫化工艺
• 利用物联网和大数据技术进行硫化工艺的监控和优化 • 提高硫化工艺的生产效率和产品质量
绿色硫化工艺
• 降低硫化工艺的能耗和污染排放 • 提高橡胶制品的环保性能
橡06胶硫化工艺在典型橡胶制品中的应用
实例
橡胶轮胎的硫化工艺与应用实例
橡胶轮胎的硫化工艺
• 热硫化工艺 • 压力硫化工艺
橡胶轮胎的应用实例
• 汽车轮胎 • 摩托车轮胎 • 飞机轮胎
橡胶密封件的硫化工艺与应用实例
橡胶密封件的硫化工艺
• 冷硫化工艺 • 压力硫化工艺
橡胶密封件的应用实例
• 汽车密封件 • 建筑密封件 • 航空航天密封件
橡胶输送带的硫化工艺与应用实例
• 热硫化工艺:加热橡胶材料进行硫化 • 冷硫化工艺:不加热橡胶材料进行硫化 • 压力硫化工艺:在压力条件下进行硫化
橡胶硫化工艺的特点
• 热硫化工艺:硫化效果好,生产效率较高 • 冷硫化工艺:适用于特殊场合,生产效率较低 • 压力硫化工艺:适用于大型橡胶制品,能提高制品的致密性
02
橡胶硫化工艺的主要方法及其原理
热硫化工艺及其原理
热硫化工艺
• 将橡胶材料加热至一定温度,加入硫化剂进行硫化 • 适用于大多数橡胶制品的硫化
热硫化工艺的原理
• 橡胶材料在加热过程中,分子链运动加剧,有利于硫化 剂的渗透 • 硫化剂与橡胶分子发生化学反应,形成交联结构,提高 橡胶制品的性能
冷硫化工艺及其原理
冷硫化工艺
• 在室温条件下,使用催化剂和硫化剂对橡胶材料进行硫 化 • 适用于特殊场合,如低温、高温或无法加热的场合
橡胶的硫化阶段

橡胶的硫化阶段
橡胶硫化是一种化学反应,通过该反应可以将未经处理的天然橡胶转化为可用于各种用途的强硬橡胶。
硫化过程中,橡胶分子中的双键得到交联,从而有效地增加了其力学强度和耐久性,使橡胶抵抗氧化、紫外线和化学腐蚀的能力增加。
橡胶的硫化反应是一系列化学变化,其中包括几个关键阶段:
1. 生成自由基:硫化反应通常在高温下进行,因此需要一些初始能量来开始反应。
这可以通过热处理或加入化学引发剂来实现。
在这阶段中,硫和橡胶生成自由基,为后续反应提供动力。
2. 交联反应:接下来,自由基开始反应,将橡胶分子中的双键连接在一起,形成长链聚合物。
这种链聚合体之间是通过以硫为主的交联原子连接在一起的。
这样的交联会使橡胶变得更加耐用且难以变形。
3. 硫化反应:交联反应持续进行时,硫通过一种称为“硫原子移动”的过程,将交联结构通过另一个分子连接在一起。
硫原子移动是此阶段的关键因素,因为它使橡胶分子之间的连通性增加。
硫原子可以在温度较高和高压下移动,并与其他橡胶分子连接起来形成更强的交联网络。
这些交联结构形成了一种三维网状结构,称为硫化橡胶。
4. 孤立化:在硫化反应的末期,未反应的硫将被孤立在橡胶材料中。
孤立的硫可通过抽出等方法去除,以提高橡胶的品质。
总之,橡胶硫化是一种重要的制造过程,可提高橡胶的强度和耐久性,并使其抵御多种自然和化学因素。
此外,硫化橡胶在许多领域具有重要的应用,如轮胎、密封件、管道和电线绝缘材料等。
橡胶硫化工艺流程
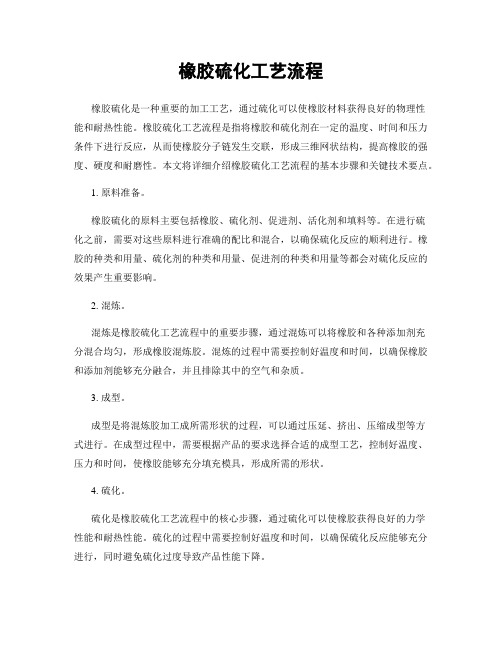
橡胶硫化工艺流程橡胶硫化是一种重要的加工工艺,通过硫化可以使橡胶材料获得良好的物理性能和耐热性能。
橡胶硫化工艺流程是指将橡胶和硫化剂在一定的温度、时间和压力条件下进行反应,从而使橡胶分子链发生交联,形成三维网状结构,提高橡胶的强度、硬度和耐磨性。
本文将详细介绍橡胶硫化工艺流程的基本步骤和关键技术要点。
1. 原料准备。
橡胶硫化的原料主要包括橡胶、硫化剂、促进剂、活化剂和填料等。
在进行硫化之前,需要对这些原料进行准确的配比和混合,以确保硫化反应的顺利进行。
橡胶的种类和用量、硫化剂的种类和用量、促进剂的种类和用量等都会对硫化反应的效果产生重要影响。
2. 混炼。
混炼是橡胶硫化工艺流程中的重要步骤,通过混炼可以将橡胶和各种添加剂充分混合均匀,形成橡胶混炼胶。
混炼的过程中需要控制好温度和时间,以确保橡胶和添加剂能够充分融合,并且排除其中的空气和杂质。
3. 成型。
成型是将混炼胶加工成所需形状的过程,可以通过压延、挤出、压缩成型等方式进行。
在成型过程中,需要根据产品的要求选择合适的成型工艺,控制好温度、压力和时间,使橡胶能够充分填充模具,形成所需的形状。
4. 硫化。
硫化是橡胶硫化工艺流程中的核心步骤,通过硫化可以使橡胶获得良好的力学性能和耐热性能。
硫化的过程中需要控制好温度和时间,以确保硫化反应能够充分进行,同时避免硫化过度导致产品性能下降。
5. 后处理。
硫化完成后,还需要进行后处理工艺,如冷却、清洗、修整等,以确保产品的质量和外观。
同时还需要进行产品的检验和包装,最终将产品送往市场。
总之,橡胶硫化工艺流程是一个复杂而精细的加工过程,需要严格控制各个环节,以确保产品的质量和性能。
只有在每个步骤中严格执行工艺要求,才能生产出符合要求的橡胶制品。
希望本文对橡胶硫化工艺流程有所帮助,谢谢阅读。
橡胶硫化压力、温度、(厚制品)时间计算(公式全,收藏)
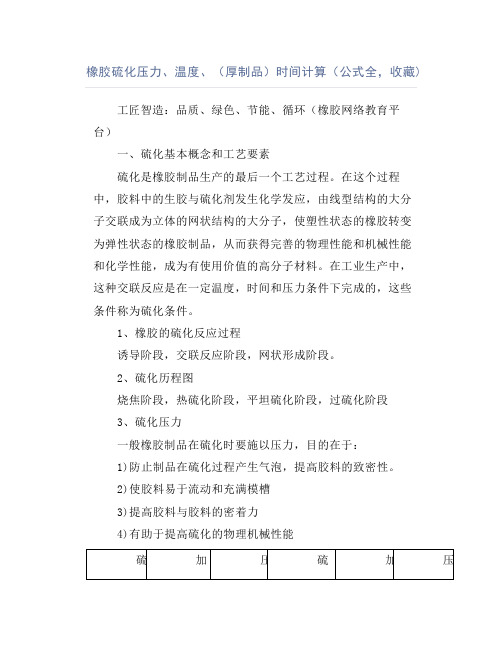
橡胶硫化压力、温度、(厚制品)时间计算(公式全,收藏)工匠智造:品质、绿色、节能、循环(橡胶网络教育平台)一、硫化基本概念和工艺要素硫化是橡胶制品生产的最后一个工艺过程。
在这个过程中,胶料中的生胶与硫化剂发生化学发应,由线型结构的大分子交联成为立体的网状结构的大分子,使塑性状态的橡胶转变为弹性状态的橡胶制品,从而获得完善的物理性能和机械性能和化学性能,成为有使用价值的高分子材料。
在工业生产中,这种交联反应是在一定温度,时间和压力条件下完成的,这些条件称为硫化条件。
1、橡胶的硫化反应过程诱导阶段,交联反应阶段,网状形成阶段。
2、硫化历程图烧焦阶段,热硫化阶段,平坦硫化阶段,过硫化阶段3、硫化压力一般橡胶制品在硫化时要施以压力,目的在于:1)防止制品在硫化过程产生气泡,提高胶料的致密性。
2)使胶料易于流动和充满模槽3)提高胶料与胶料的密着力4)有助于提高硫化的物理机械性能硫化机把压力传递给模型,再由模型传递给胶料;二是硫化介质直接加压(如蒸汽加压);三是以压缩空气加压;四是由注压机注压等。
4、硫化温度和硫化时间硫化温度是橡胶发生硫化反应的基本条件,它直接影响硫化速度和产品质量。
硫化温度高,硫化速度快,生产效率高。
反之,硫化速度慢,生产效率低。
硫化温度高低应取决于胶料配方,其中最重要的是取决于橡胶种类和硫化体系。
但应注意的是,高温橡胶分子链裂解,至发生硫化返原现象,结果导致强伸性能下降,困此硫化温度不宜太高。
温度是硫化三大要素之一,与所有化学反应一样,硫化反应随温度升高而加快,并且大体适用范特霍夫定律,即温度每上升8~10。
C(约相当于一个表压的蒸汽压力),其反应速度约增加一倍;或者说,反应时间约减少一半。
随着室温硫化胶料的增加和高温硫化出现,硫化温度趋向两个极端。
从提高硫化效率来说,应当认为硫化温度越高越好,但实际上不能无限提高硫化温度。
首先受到橡胶导热性极小阻碍,对于厚制品来说,采用高温硫化很难使内外层胶料同时达到平坦范围;其次,各种橡胶的耐高温性能不一,有的橡胶经受不了高温的作用,如高温硫化天然橡胶时,溶于橡胶中的氧随温度提高而活性加大,引起强烈的氧化作用,破坏了橡胶的组织,降低了硫化胶的物理机械性能,第三,高温对橡胶制品中的纺织物有害为棉纤维布料超过期作废140℃时,强力下降,在240℃下加热四小时则完全破坏。
橡胶硫化三要素范文
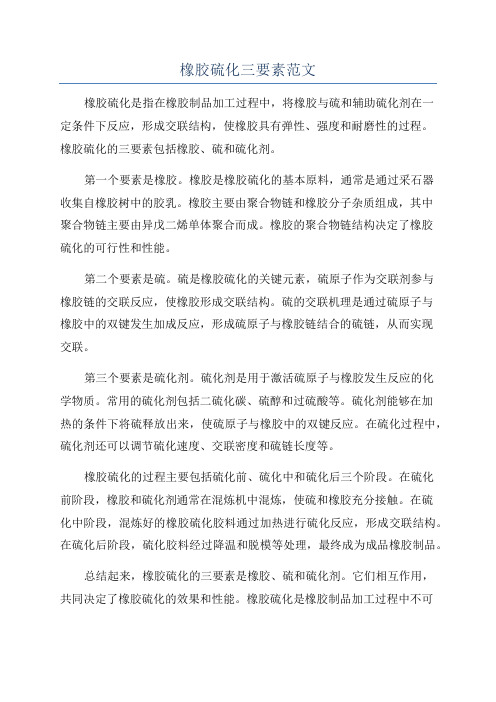
橡胶硫化三要素范文橡胶硫化是指在橡胶制品加工过程中,将橡胶与硫和辅助硫化剂在一定条件下反应,形成交联结构,使橡胶具有弹性、强度和耐磨性的过程。
橡胶硫化的三要素包括橡胶、硫和硫化剂。
第一个要素是橡胶。
橡胶是橡胶硫化的基本原料,通常是通过采石器收集自橡胶树中的胶乳。
橡胶主要由聚合物链和橡胶分子杂质组成,其中聚合物链主要由异戊二烯单体聚合而成。
橡胶的聚合物链结构决定了橡胶硫化的可行性和性能。
第二个要素是硫。
硫是橡胶硫化的关键元素,硫原子作为交联剂参与橡胶链的交联反应,使橡胶形成交联结构。
硫的交联机理是通过硫原子与橡胶中的双键发生加成反应,形成硫原子与橡胶链结合的硫链,从而实现交联。
第三个要素是硫化剂。
硫化剂是用于激活硫原子与橡胶发生反应的化学物质。
常用的硫化剂包括二硫化碳、硫醇和过硫酸等。
硫化剂能够在加热的条件下将硫释放出来,使硫原子与橡胶中的双键反应。
在硫化过程中,硫化剂还可以调节硫化速度、交联密度和硫链长度等。
橡胶硫化的过程主要包括硫化前、硫化中和硫化后三个阶段。
在硫化前阶段,橡胶和硫化剂通常在混炼机中混炼,使硫和橡胶充分接触。
在硫化中阶段,混炼好的橡胶硫化胶料通过加热进行硫化反应,形成交联结构。
在硫化后阶段,硫化胶料经过降温和脱模等处理,最终成为成品橡胶制品。
总结起来,橡胶硫化的三要素是橡胶、硫和硫化剂。
它们相互作用,共同决定了橡胶硫化的效果和性能。
橡胶硫化是橡胶制品加工过程中不可或缺的环节,通过橡胶硫化可以使橡胶具有优异的物理性能,广泛应用于各个领域。
橡胶硫化原理

橡胶硫化原理橡胶硫化是指橡胶在加入硫化剂的条件下,经过一定时间和温度的处理,使其分子内部发生交联反应,从而改善橡胶的物理性能和化学性能的过程。
橡胶硫化是橡胶加工的重要工艺之一,也是橡胶制品得以广泛应用的基础。
下面将从硫化的原理、影响硫化的因素以及硫化后橡胶的性能等方面对橡胶硫化进行详细介绍。
橡胶硫化的原理是指在硫化剂的作用下,橡胶分子链中的双键发生断裂,形成自由基,然后自由基与硫原子结合,形成硫键,最终实现橡胶分子的交联。
这种交联作用可以使橡胶分子链之间产生空间网状结构,从而使橡胶变得更加坚固和耐磨。
同时,硫化还可以改善橡胶的耐老化性能,提高橡胶的强度、硬度和弹性,增加橡胶的耐磨性和耐油性,改善橡胶的加工性能和热稳定性。
影响橡胶硫化的因素有很多,主要包括硫化剂的种类和用量、硫化温度和硫化时间等。
硫化剂的种类和用量直接影响着橡胶硫化的速度和程度,不同种类的硫化剂对橡胶的硫化速度和效果都有所差异。
硫化温度和硫化时间则是影响硫化反应进行的重要因素,温度过高会导致硫化剂过早挥发,温度过低则会延缓硫化反应的进行,硫化时间过长则会造成硫化过度,影响橡胶的性能。
硫化后的橡胶具有很多优良的性能,如耐热性、耐寒性、耐老化性、耐磨性、耐油性等。
这些性能使硫化后的橡胶被广泛应用于轮胎、橡胶管、橡胶板、橡胶密封件、橡胶软管等领域。
同时,硫化后的橡胶还可以通过改变硫化条件和硫化体系,实现不同硬度、不同强度和不同弹性的橡胶制品。
总之,橡胶硫化是一种重要的加工工艺,通过硫化过程可以改善橡胶的物理性能和化学性能,使其得以广泛应用于各个领域。
因此,对橡胶硫化原理的深入了解和掌握,对于提高橡胶制品的质量和性能具有重要意义。
橡胶硫化的原理
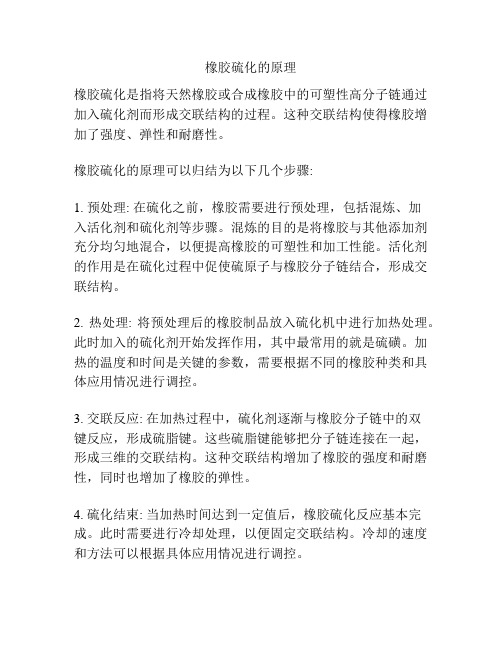
橡胶硫化的原理
橡胶硫化是指将天然橡胶或合成橡胶中的可塑性高分子链通过加入硫化剂而形成交联结构的过程。
这种交联结构使得橡胶增加了强度、弹性和耐磨性。
橡胶硫化的原理可以归结为以下几个步骤:
1. 预处理: 在硫化之前,橡胶需要进行预处理,包括混炼、加
入活化剂和硫化剂等步骤。
混炼的目的是将橡胶与其他添加剂充分均匀地混合,以便提高橡胶的可塑性和加工性能。
活化剂的作用是在硫化过程中促使硫原子与橡胶分子链结合,形成交联结构。
2. 热处理: 将预处理后的橡胶制品放入硫化机中进行加热处理。
此时加入的硫化剂开始发挥作用,其中最常用的就是硫磺。
加热的温度和时间是关键的参数,需要根据不同的橡胶种类和具体应用情况进行调控。
3. 交联反应: 在加热过程中,硫化剂逐渐与橡胶分子链中的双
键反应,形成硫脂键。
这些硫脂键能够把分子链连接在一起,形成三维的交联结构。
这种交联结构增加了橡胶的强度和耐磨性,同时也增加了橡胶的弹性。
4. 硫化结束: 当加热时间达到一定值后,橡胶硫化反应基本完成。
此时需要进行冷却处理,以便固定交联结构。
冷却的速度和方法可以根据具体应用情况进行调控。
总的来说,橡胶硫化的原理是通过加入硫化剂,在一定温度下使橡胶分子链之间形成交联结构,从而提高橡胶的强度、弹性和耐磨性。
这种硫化反应过程需要进行适当的预处理、热处理和冷却处理。
橡胶硫化温度时间和压力
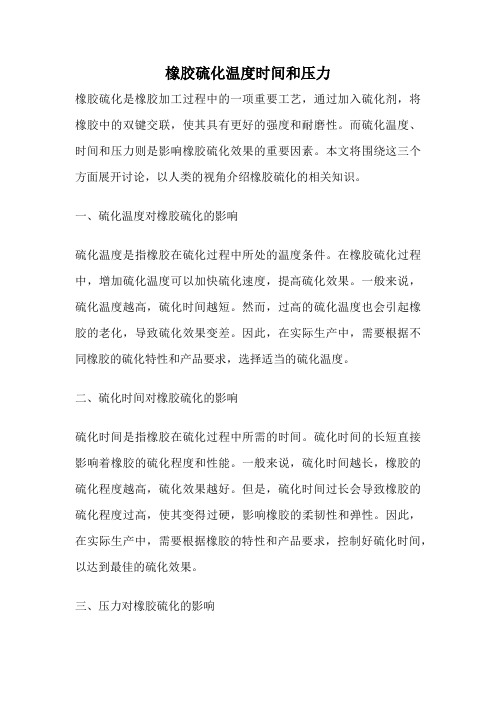
橡胶硫化温度时间和压力橡胶硫化是橡胶加工过程中的一项重要工艺,通过加入硫化剂,将橡胶中的双键交联,使其具有更好的强度和耐磨性。
而硫化温度、时间和压力则是影响橡胶硫化效果的重要因素。
本文将围绕这三个方面展开讨论,以人类的视角介绍橡胶硫化的相关知识。
一、硫化温度对橡胶硫化的影响硫化温度是指橡胶在硫化过程中所处的温度条件。
在橡胶硫化过程中,增加硫化温度可以加快硫化速度,提高硫化效果。
一般来说,硫化温度越高,硫化时间越短。
然而,过高的硫化温度也会引起橡胶的老化,导致硫化效果变差。
因此,在实际生产中,需要根据不同橡胶的硫化特性和产品要求,选择适当的硫化温度。
二、硫化时间对橡胶硫化的影响硫化时间是指橡胶在硫化过程中所需的时间。
硫化时间的长短直接影响着橡胶的硫化程度和性能。
一般来说,硫化时间越长,橡胶的硫化程度越高,硫化效果越好。
但是,硫化时间过长会导致橡胶的硫化程度过高,使其变得过硬,影响橡胶的柔韧性和弹性。
因此,在实际生产中,需要根据橡胶的特性和产品要求,控制好硫化时间,以达到最佳的硫化效果。
三、压力对橡胶硫化的影响压力是指橡胶在硫化过程中所受到的压力条件。
压力对橡胶硫化的影响主要体现在两个方面:一是加快硫化速度,二是改善硫化效果。
通过施加一定的压力,可以促使硫化剂更好地与橡胶发生反应,提高硫化效率。
同时,压力还可以使橡胶材料更加均匀地受热,减少硫化过程中的温度差异,进一步改善硫化效果。
因此,在橡胶硫化过程中,适当的压力是非常重要的。
橡胶硫化温度、时间和压力是相互影响的三个重要参数。
在实际生产中,需要根据不同橡胶材料的特性和产品要求,合理选择硫化温度、时间和压力,以达到最佳的硫化效果。
同时,还需要注意硫化过程中的安全性和环保性,合理控制硫化温度和时间,避免产生有害气体和废水。
只有在科学规范的硫化条件下,才能得到优质的橡胶制品,满足人们对橡胶制品的各种需求。
橡胶硫化工初级理论知识试题(简答题)
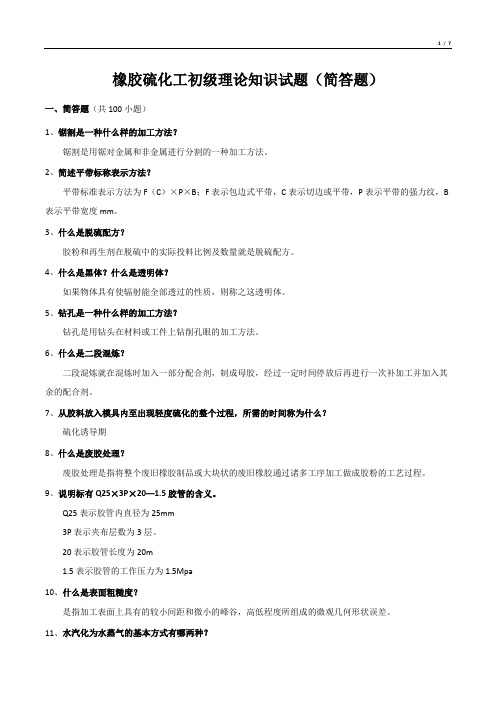
橡胶硫化工初级理论知识试题(简答题)一、简答题(共100小题)1、锯割是一种什么样的加工方法?锯割是用锯对金属和非金属进行分割的一种加工方法。
2、简述平带标称表示方法?平带标准表示方法为F(C)×P×B;F表示包边式平带,C表示切边或平带,P表示平带的强力纹,B 表示平带宽度mm。
3、什么是脱硫配方?胶粉和再生剂在脱硫中的实际投料比例及数量就是脱硫配方。
4、什么是黑体?什么是透明体?如果物体具有使辐射能全部透过的性质,则称之这透明体。
5、钻孔是一种什么样的加工方法?钻孔是用钻头在材料或工件上钻削孔眼的加工方法。
6、什么是二段混炼?二段混炼就在混炼时加入一部分配合剂,制成母胶,经过一定时间停放后再进行一次补加工并加入其余的配合剂。
7、从胶料放入模具内至出现轻度硫化的整个过程,所需的时间称为什么?硫化诱导期8、什么是废胶处理?废胶处理是指将整个废旧橡胶制品或大块状的废旧橡胶通过诸多工序加工做成胶粉的工艺过程。
9、说明标有Q25×3P×20—1.5胶管的含义。
Q25表示胶管内直径为25mm3P表示夹布层数为3层。
20表示胶管长度为20m1.5表示胶管的工作压力为1.5Mpa10、什么是表面粗糙度?是指加工表面上具有的较小间距和微小的峰谷,高低程度所组成的微观几何形状误差。
11、水汽化为水蒸气的基本方式有哪两种?蒸发和沸腾。
12、什么是元素符号?在化学上各种元素都用不同的符号来表示,这种符号叫元素符号。
在国际上元素符号是统一采用了该元素什么文之名称的第一个字母(大写)来表示。
拉丁文13、什么是绝对压力?绝对压力就是指在液体,气体或蒸汽表面上的实际压力。
14、夹布橡胶制品的结构形式有哪些?夹布橡胶制品的结构形式较多,它由橡胶与棉布、橡胶与锦纶、涤纶、尼龙布、绳(线)、聚四氟乙烯等组合成镶嵌而成。
15、什么是温度?温度是表示物体冷热程度的物理量。
16、胶料的剩余焦烧时间是指什么?剩余焦烧时间是指胶料在模具中受热时保持流动的时间。
橡胶硫化原理

橡胶硫化原理
橡胶硫化是指将天然橡胶或合成橡胶中的双键或多键通过硫化
剂的作用而发生交联反应,从而使其具有弹性和耐磨性的过程。
橡
胶硫化原理是橡胶工业中的重要基础知识,对于理解橡胶制品的性
能和生产工艺具有重要意义。
橡胶硫化的原理是在橡胶分子链中引入交联键,使得橡胶分子
链之间形成三维网状结构,从而增加了橡胶的弹性和耐磨性。
硫化
剂在橡胶硫化过程中起着至关重要的作用,它能够与橡胶分子中的
双键或多键发生化学反应,形成交联结构。
常用的硫化剂有硫磺、
硫化二苯胺、过氧化物等。
橡胶硫化的过程包括预硫化和后硫化两个阶段。
预硫化是指在
橡胶中加入硫化剂和促进剂,使其在加热条件下发生部分硫化反应,形成硫化胶块。
后硫化是指将预硫化的橡胶胶块在适当的温度、时
间和压力条件下进行加热处理,使其完成硫化反应,形成最终的橡
胶制品。
橡胶硫化的原理不仅仅是一种化学反应,更是一种复杂的物理
和化学过程。
在硫化过程中,橡胶分子链之间的交联结构会影响橡
胶的物理性能,如弹性、硬度、耐磨性等。
因此,控制硫化过程中的温度、时间、压力和硫化剂的种类和用量对于橡胶制品的性能具有重要影响。
除了硫化剂外,促进剂也是影响橡胶硫化过程的重要因素。
促进剂能够加速硫化反应的进行,提高硫化速度和硫化程度,从而影响橡胶制品的硫化性能和物理性能。
总的来说,橡胶硫化原理是一项复杂而重要的工艺技术,它直接影响着橡胶制品的质量和性能。
通过深入理解橡胶硫化的原理和过程,可以更好地指导橡胶制品的生产和应用,提高橡胶制品的质量和使用寿命,促进橡胶工业的发展。
硫化基础培训资料PPT课件

03 硫化工艺条件
温度
总结词
温度是硫化过程中最重要的参数之一,它决定了橡胶的交联程度和硫化速度。
详细描述
在硫化过程中,橡胶分子在高温下发生化学反应,形成三维网络结构。温度过高 可能导致橡胶过度硫化,降低物理性能;温度过低则会导致硫化速度减慢,甚至 无法完成硫化。因此,选择适当的温度是保证硫化质量的关键。
硫化环保要求与处理方法
废气处理
硫化过程中产生的废气可 能含有有害物质,应通过 专用废气处理装置进行处 理,确保排放达标。
废水处理
硫化过程中产生的废水可 能含有有害物质,应通过 废水处理设施进行处理, 确保排放达标。
固体废弃物处理
硫化过程中产生的固体废 弃物应按照相关规定进行 分类处理,避免对环境造 成污染。
。
硫化设备介绍
硫化罐
微波硫化机
辐射硫化机
用于高温高压下进行橡 胶硫化的设备,具有加 热、加压、计时等功能。
利用微波能量加热橡胶 材料的设备,具有高效、
节能、环保等特点。
利用高能射线照射橡胶 材料的设备,具有快速、
均匀加热等特点。
化学交联机
用于加入化学交联剂进 行橡胶交联的设备,具 有混合、加热、搅拌等
压缩永久变形检测
测试硫化橡胶在长时间受压后的变形程度, 反映其耐久性。
拉伸强度检测
在拉伸试验机上对硫化橡胶进行拉伸,测量 其拉伸强度,反映其力学性能。
耐化学腐蚀性能检测
通过浸泡或涂覆不同化学物质,观察硫化橡 胶的腐蚀情况。
硫化橡胶质量控制
01
02
03
04
控制原材料质量
确保所采购的原材料质量符合 标准,从源头上保证硫化橡胶
功能。
硫化设备操作与维护
橡胶硫化基础知识点
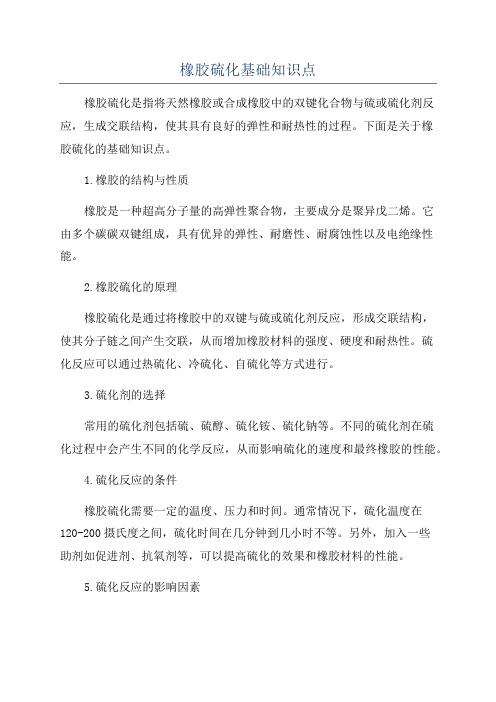
橡胶硫化基础知识点橡胶硫化是指将天然橡胶或合成橡胶中的双键化合物与硫或硫化剂反应,生成交联结构,使其具有良好的弹性和耐热性的过程。
下面是关于橡胶硫化的基础知识点。
1.橡胶的结构与性质橡胶是一种超高分子量的高弹性聚合物,主要成分是聚异戊二烯。
它由多个碳碳双键组成,具有优异的弹性、耐磨性、耐腐蚀性以及电绝缘性能。
2.橡胶硫化的原理橡胶硫化是通过将橡胶中的双键与硫或硫化剂反应,形成交联结构,使其分子链之间产生交联,从而增加橡胶材料的强度、硬度和耐热性。
硫化反应可以通过热硫化、冷硫化、自硫化等方式进行。
3.硫化剂的选择常用的硫化剂包括硫、硫醇、硫化铵、硫化钠等。
不同的硫化剂在硫化过程中会产生不同的化学反应,从而影响硫化的速度和最终橡胶的性能。
4.硫化反应的条件橡胶硫化需要一定的温度、压力和时间。
通常情况下,硫化温度在120-200摄氏度之间,硫化时间在几分钟到几小时不等。
另外,加入一些助剂如促进剂、抗氧剂等,可以提高硫化的效果和橡胶材料的性能。
5.硫化反应的影响因素硫化反应的速度和效果受到多种因素的影响,包括硫化剂的种类和浓度、温度、压力、橡胶的活性程度等。
其中,温度是影响硫化速率的最重要因素,温度越高,硫化速率越快。
6.硫化对橡胶性能的影响橡胶硫化后,可以显著提高橡胶材料的强度、硬度、抗拉强度、耐磨性和耐热性等性能。
交联结构可以限制分子链的运动,使橡胶材料具有良好的弹性和抗变形能力。
7.不同硫化方式的特点热硫化是指将橡胶和硫或硫化剂混合后,在高温下进行硫化反应。
冷硫化是指在室温下进行硫化反应,常用于对薄壁橡胶制品的硫化。
自硫化则是指在橡胶中含有一定比例的硫醇,通过热加工过程中的反应生成交联结构。
总结起来,橡胶硫化是将橡胶材料中的双键与硫或硫化剂反应,形成交联结构的过程。
硫化可以改善橡胶的弹性、硬度、抗拉强度、耐磨性和耐热性等性能,提高橡胶材料的使用寿命和适用范围。
在橡胶工业中,橡胶硫化广泛应用于制造轮胎、橡胶密封件、橡胶管道等各种产业领域。
- 1、下载文档前请自行甄别文档内容的完整性,平台不提供额外的编辑、内容补充、找答案等附加服务。
- 2、"仅部分预览"的文档,不可在线预览部分如存在完整性等问题,可反馈申请退款(可完整预览的文档不适用该条件!)。
- 3、如文档侵犯您的权益,请联系客服反馈,我们会尽快为您处理(人工客服工作时间:9:00-18:30)。
硫化对结构与性能的影响在橡胶制品生产过程中,硫化是最后一道加工工序。
在这道工序中,橡胶经过一系列复杂的化学反应,由线型结构变成体型结构,失去了混炼胶的可塑性具有了交联橡胶的高弹性,进而获得优良的物理机械性能、耐热性、耐溶剂性及耐腐蚀性能提高橡胶制品的使用价值和应用范围硫化前:线性结构,分子间以范德华力相互作用性能:可塑性大,伸长率高,具有可溶性硫化时:分子被引发,发生化学交连反应硫化后:网状结构,分子间以已化学键结合结构:(1)化学键。
(2)交联键的位置;(3)交联程度(4)交联性能: 1)力学性能(定伸强度.硬度.拉伸强度. 伸长率.弹性)2)物理性能3)化学稳定性硫化后橡胶的性能变化:以天然橡胶为例,随硫化程度的提高1) 力学性能的变化(弹性. 扯断强度. 定伸强度. 撕裂强度. 硬度)提高(伸长率. 压缩永久变形. 疲劳生热)降低2)物理性能的变化透气率、透水率降低不能溶解,只能溶胀耐热性提高2) 化学稳定性的变化化学稳定性提高原因 a. 交联反应使化学活性很高的基团或原子不复存在,使老化反应难以进行b . 网状结构阻碍了低分子的扩散,导致橡胶自由基难以扩散7.2 硫化历程在硫化过程中,各种性能均会随硫化的进程而发生变化,这种变化曲线能够反映胶料的硫化历程,故称为硫化历程图。
下图为用硫化仪测出的硫化历程曲线。
该曲线反映胶料在一定硫化温度下,转子的转矩随硫化时间的变化。
A焦烧阶段;B.热硫化阶段;C.平坦硫化阶段;D.过硫化阶段A1.操作焦烧时间;A2.剩余焦烧时间1. 焦烧阶段(焦烧期-硫化起步阶段,硫化诱导期)1) 图中的ab段称为胶料的焦烧阶段,此时交联尚未开始,胶料在模腔内具有良好的流动性,也称为硫化诱导阶段。
胶料焦烧时间的长短决定胶料的焦烧性能和操作安全性。
胶料焦烧时间受胶料中硫化促进剂和胶料本身的热历史的影响较大2) 焦烧时间既包括橡胶在加工过程中由于热积累消耗掉的焦烧时间A1,称为操作焦烧时间;也包括胶料在模腔中保持流动性的时间A2,称为剩余焦烧时间硫化起步——硫化时,胶料开始变硬而后不能进行热塑性流动的那一点时间(焦烧)。
焦烧期的长短:决定了胶料的焦烧性及操作安全性。
取决于方,特别是促进剂。
可用迟效性促进剂:CZ焦烧时间的起点:实际上是从混炼时加入硫磺的那一时刻开始焦烧阶段的终点胶料开始发硬并丧失流动性操作焦烧时间——混炼,停放,成型残余焦烧时间——进入模具后加热开始到开始硫化这段时间若:操作焦烧时间> 焦烧时间,就发生焦烧防止焦烧:A 具有较长的焦烧时间:配方B 混炼、停放要低温,成型时要迅速,即减少操作焦烧时间2. 热硫化阶段(欠硫期-预硫阶段)1)热硫化阶段即图中的bc段,在该阶段橡胶的交联以一定的速度开始进行。
诱导期后,开始交联,至正硫化。
2)热硫化的速度和时间取决与胶料的配方和硫化的温度。
3)在此阶段,交联度低,即使在此阶段的后期,性能(主要是拉伸强度、弹性等)尚未达到预期的要求4)但其抗撕性、耐磨性,则优于正硫化胶料,若要求这些性能时制品可以轻微欠硫。
3. 硫化平坦阶段(正硫期-正硫化阶段)硫化平坦阶段即图中的cd段,此时交联反应已趋于完成,反应速度已较为缓和。
硫化胶的综合物理机械性能已达到或接近最佳值。
正硫化:在平坦硫化阶段,橡胶制品的综合物理机械性能达到最佳值,这种硫化状态称为正硫化,也称最宜硫化。
正硫化前期成为欠硫;正硫化后期则成为过硫,欠硫或过硫,橡胶的物理机械性能均较差。
正硫化时间:正硫化时间是指达到正硫化状态所需的最短时间,也称为“正硫化点”。
工艺正硫化时间:在实际操作中,往往是从制品的某些主要性能指标进行选择,从而确定正硫化时间,与理论上的综合物理性能有所区别,具有工艺上的概念。
因此,将通过这种确定的正硫化时间称为工艺正硫化时间。
一般橡胶制品的“工艺正硫化时间’ 应取其胶料的应力、应变最高值稍前一点制品达到适当的交联度的阶段,此时各项力学性能均达到或接近最佳值,其综合性能最好。
正硫化是一个阶段——各项性能基本上保持恒定或变化很少,也称硫化平坦期。
硫化平坦期的宽窄取决于:配方、温度等。
正硫化时间的选取:拉伸强度达到最高值略前的时间.主要是考虑“后硫化”。
4. 过硫阶段(过硫期)d 以后的部分为过硫化阶段。
在这一阶段中,不同的橡胶表现的情况不同:天然橡胶由于氧化断链反应程度较强,其各项物理机械性能下降;而大部分的合成橡胶,如SBR、NBR由于热交联和热氧化断链两种作用程度接近,因此,物理机械性能变化甚小或基本保持恒定。
1)正硫化后,继续硫化进入过硫化。
进入过硫化后:性能下降:硫化返原(断链多于交联,NR、IIR)性能恒定甚至上升:非返原(交联占优、环化)2)交联和氧化断链两种反应贯穿于橡胶硫化过程的始终。
只是在硫化过程的不同阶段两种反应优势不同。
3)进入过硫的早晚,即硫化平坦期的宽窄,主要取决于两个方面:1)配方(如TMTD);2)温度7.3 正硫化及其测定方法(一)正硫化及正硫化时间1.正硫化:橡胶制品性能达到最佳值时的硫化状态。
2.正硫化时间:达到正硫化状态所需要的时间。
3.欠硫:处于正硫化前期,或者说硫化最佳状态之前的状态4.过硫:处于正硫化后期,或者说硫化最佳状态之后的状态(二)正硫化时间的测定方法1.物理—化学法(1)游离硫测定法(理论正硫化时间)(2)溶胀法(理论正硫化时间)2.物理机械性能测定法(1)300%定伸应力法(理论正硫化时间)(2)拉伸强度法(工艺正硫化时间)(3)压缩永久变形法(理论正硫化时间)(4)综合取值法3.专用仪器法用于测定橡胶硫化特性的测试仪器有各类硫化仪和门尼粘度计(1) 硫化仪法(2) 门尼粘度仪门尼焦烧时间t5:随硫化时间增加,胶料门尼值下降到最低点开始上升,一般由最低点上升至5个门尼值的时间称为门尼焦时间硫化特性曲线:初始粘度、最低粘度、焦烧时间、硫化速度.正硫化时间、活化能。
测定原理:胶料的剪切模量与交联密度成正比。
G =D · R · T 胶料剪切模量交联密度气体常数度门尼硫化时间t35:由最低点上升至35个门尼值所需硫化时间称为门尼硫化时间正硫化时间= t5+10(t35- t5)门尼硫化速度(Δt30):Δt30= t35-t5膨胀法是公认的测定正硫化时间的标准方法,所测得的正硫化时间为理论正硫化时间。
物理机械性能测定法和硫化仪法所测定的结果均为工艺正硫化时间1) 对硫化曲线常用平行线法进行解析,就是通过硫化曲线最小转矩和最大转矩值,分别引平行于时间轴的直线,该两条平行线与时间轴距离分别为ML和MH,即ML—最小转矩值,反映未硫化胶在一定温度下的流动性;2) MH—最大转矩值,反映硫化胶最大交联度;焦烧时间和正硫化时间分别以达到一定转矩所对应的时间表示:3) 焦烧时间ts1—从实验开始到曲线由最低转矩上升1kg·cm所对应的时间4) 起始硫化时间tc10:转矩达到ML+10%(MH—ML)时所对应的硫化时间5) 正硫化时间tc90—转矩达到ML+90%(MH—ML)时所对应的硫化时间6) 通常还以硫化速度指数VC=100/(tc90—tsx)。
7.4 硫化条件的选取及确定一、硫化压力1)橡胶制品硫化时都需要施加压力,其目的是:a.防止胶料产生气泡,提高胶料的致密性;b.使胶料流动,充满模具,以制得花纹清晰的制品c.提高制品中各层(胶层与布层或金属层、布层与布层)之间的粘着力,改善硫化胶的物理性能(如耐屈挠性能)。
2)一般来说,硫化压力的选取应根据产品类型、配方、可塑性等因素决定。
3)原则上应遵循以下规律:可塑性大,压力宜小些;产品厚、层数多、结构复杂压力宜大些;薄制品压宜小些,甚至可用常压硫化加压的方式有以下几种:(1) 液压泵通过平板硫化机把压力传递给模具,再由模具传递给胶料(2) 由硫化介质(如蒸汽)直接加压(3) 由压缩空气加压(4) 由注射机注射二、硫化温度和硫化时间硫化温度是硫化反应的最基本条件。
硫化温度的高低,可直接影响硫化速度、产品质量和企业的经济效益硫化温度高,硫化速度快,生产效率高;反之生产效率低提高硫化温度会导致以下问题;(1) 引起橡胶分子链裂解和硫化返原,导致胶料力学性能下降(2) 使橡胶制品中的纺织物强度降低(3) 导致胶料焦烧时间缩短,减少了充模时间,造成制品局部缺胶(4) 由于厚制品会增加制品的内外温差,导致硫化不均硫化温度的选取应综合考虑橡胶的种类、硫化体系及制品结构等因素各种橡胶的最宜硫化温度一般是:NR<143℃;SBR<180℃;IR、BR、CR<151℃;IIR<170℃;NBR<180℃1.等效硫化时间的计算1.通过范特霍夫方程计算等效硫化时间根据范特霍夫方程,硫化温度和硫化时间的系可用下式表示:τ1/τ2=k式中τ1—温度为t1的正硫化时间,minτ2—温度为t2的正硫化时间,minK—硫化温度系数例:已知某一胶料在140℃时的正硫化时间是20min,利用范特霍夫方程可计算出130℃和150℃时的等效硫化时间130℃的等效硫化时间为40min;150℃的等效硫化时间为10min2.硫化效应的计算(1)硫化效应的计算硫化效应等于硫化强度和硫化时间的乘积,即:E=I·t式中E—硫化效应;I—硫化强度;t—硫化时间硫化强度是胶料在一定温度下单位时间内所达到的硫化程度, 它与硫化温度系数和硫化温度有关I=K(T-100)/10式中K—硫化温度系数(由实验测定,或一般取K=2) T—硫化温度在实际计算中,由于每一种胶料硫化时,在硫化曲线上都有一段平坦范围,因此在改变硫化条件时,一般只要把改变后的硫化效应控制在原来的硫化条件的最小和最大硫化效应的范围内,制品的物理机械性能就可相近。
设原来的最大硫化效应为E大,最小硫化效应为E小,改变后的硫化效应为E,则要求:E小<E<E大例如;测得某一制品胶料的正硫化时间为130×20min,平坦硫化范围为20~120min,其最大和最小的硫化效应为:E小=2(130-100)/10·20=160 E大=2(130-100)/10·120=960因此,要求该制品在改变硫化条件后的硫化效应E必须满足下列条件:160<E<960(二)硫化热效应及热平衡1.硫化热效应硫化过程中,生胶与硫黄之间的化学反应是一个放热反应过程。
实验证明,生成热随结合硫黄的增加而增高。
在硫化开始阶段,因硫黄的熔融需要吸收热量,会出现温度降低的现象。
2.硫化热平衡硫化可看成是热交换过程,在供热方面有来自加热介质升温时的热量及胶料的反应生成热;在耗热方面,有胶料的吸热. 设备的散热及冷凝水的吸热等7.6 硫化方法橡胶制品多种多样,硫化方法也很多,可按使用设备的种类、加热介质的种类、硫化工艺方法等来分类。