零件制造工艺过程常识
机械加工基本常识
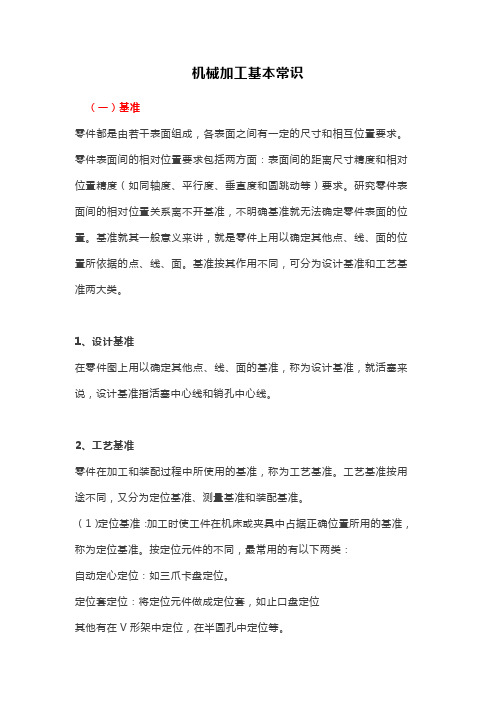
机械加工基本常识(一)基准零件都是由若干表面组成,各表面之间有一定的尺寸和相互位置要求。
零件表面间的相对位置要求包括两方面:表面间的距离尺寸精度和相对位置精度(如同轴度、平行度、垂直度和圆跳动等)要求。
研究零件表面间的相对位置关系离不开基准,不明确基准就无法确定零件表面的位置。
基准就其一般意义来讲,就是零件上用以确定其他点、线、面的位置所依据的点、线、面。
基准按其作用不同,可分为设计基准和工艺基准两大类。
1、设计基准在零件图上用以确定其他点、线、面的基准,称为设计基准,就活塞来说,设计基准指活塞中心线和销孔中心线。
2、工艺基准零件在加工和装配过程中所使用的基准,称为工艺基准。
工艺基准按用途不同,又分为定位基准、测量基准和装配基准。
(1)定位基准:加工时使工件在机床或夹具中占据正确位置所用的基准,称为定位基准。
按定位元件的不同,最常用的有以下两类:自动定心定位:如三爪卡盘定位。
定位套定位:将定位元件做成定位套,如止口盘定位其他有在V形架中定位,在半圆孔中定位等。
(2)测量基准:零件检验时,用以测量已加工表面尺寸及位置的基准,称为测量基准。
(3)装配基准:装配时用以确定零件在部件或产品中位置的基准,称为装配基准。
(二)工件的安装方式为了在工件的某一部位上加工出符合规定技术要求的表面,在机械加工前,必须使工件在机床上相对于工具占据某一正确的位置。
通常把这个过程称为工件的“定位”。
工件定位后,由于在加工中受到切削力、重力等的作用,还应采用一定的机构将工件“夹紧”,使其确定的位置保持不变。
使工件在机床上占有正确的位置并将工件夹紧的过程称为“安装”。
工件安装的好坏是机械加工中的重要问题,它不仅直接影响加工精度、工件安装的快慢、稳定性,还影响生产率的高低。
为了保证加工表面与其设计基准间的相对位置精度,工件安装时应使加工表面的设计基准相对机床占据一正确的位置。
如精车环槽工序,为了保证环槽底径与裙部轴线的圆跳动的要求,工件安装时必须使其设计基准与机床主轴的轴心线重合。
机械制造工艺学知识点总结(含名词解释)
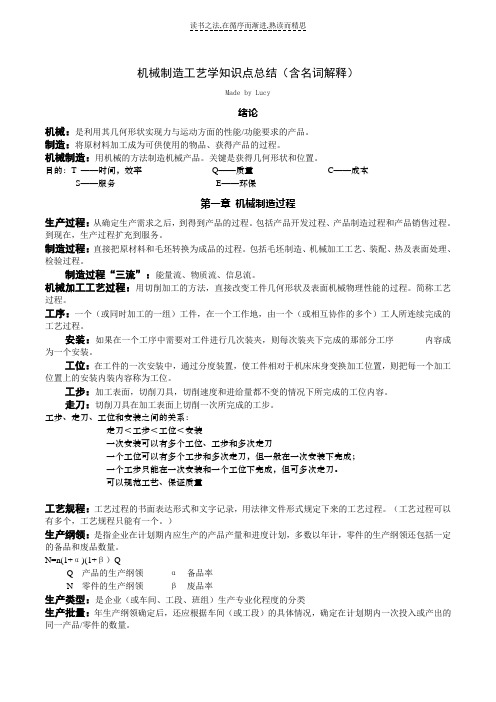
机械制造工艺学知识点总结(含名词解释)Made by Lucy绪论机械:是利用其几何形状实现力与运动方面的性能/功能要求的产品。
制造:将原材料加工成为可供使用的物品、获得产品的过程。
机械制造:用机械的方法制造机械产品。
关键是获得几何形状和位置。
目的:T ——时间,效率Q——质量C——成本S——服务E——环保第一章机械制造过程生产过程:从确定生产需求之后,到得到产品的过程。
包括产品开发过程、产品制造过程和产品销售过程。
到现在,生产过程扩充到服务。
制造过程:直接把原材料和毛坯转换为成品的过程。
包括毛坯制造、机械加工工艺、装配、热及表面处理、检验过程。
制造过程“三流”:能量流、物质流、信息流。
机械加工工艺过程:用切削加工的方法,直接改变工件几何形状及表面机械物理性能的过程。
简称工艺过程。
工序:一个(或同时加工的一组)工件,在一个工作地,由一个(或相互协作的多个)工人所连续完成的工艺过程。
安装:如果在一个工序中需要对工件进行几次装夹,则每次装夹下完成的那部分工序内容成为一个安装。
工位:在工件的一次安装中,通过分度装置,使工件相对于机床床身变换加工位置,则把每一个加工位置上的安装内装内容称为工位。
工步:加工表面,切削刀具,切削速度和进给量都不变的情况下所完成的工位内容。
走刀:切削刀具在加工表面上切削一次所完成的工步。
工步、走刀、工位和安装之间的关系:走刀<工步<工位<安装一次安装可以有多个工位、工步和多次走刀一个工位可以有多个工步和多次走刀,但一般在一次安装下完成;一个工步只能在一次安装和一个工位下完成,但可多次走刀。
可以规范工艺、保证质量工艺规程:工艺过程的书面表达形式和文字记录,用法律文件形式规定下来的工艺过程。
(工艺过程可以有多个,工艺规程只能有一个。
)生产纲领:是指企业在计划期内应生产的产品产量和进度计划,多数以年计,零件的生产纲领还包括一定的备品和废品数量。
N=n(1+α)(1+β)QQ---产品的生产纲领α---备品率N---零件的生产纲领β---废品率生产类型:是企业(或车间、工段、班组)生产专业化程度的分类生产批量:年生产纲领确定后,还应根据车间(或工段)的具体情况,确定在计划期内一次投入或产出的同一产品/零件的数量。
第九章 零件生产过程基础知识
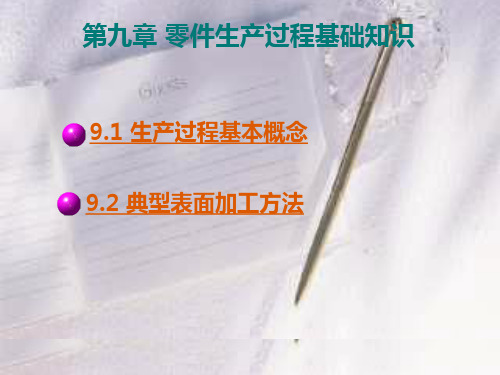
小常识:关于CAPP
制订零件工艺过程
复杂、繁琐、依靠经验、重点在管理
CAPP(Computer Aided Process Planning)
最低目标:工艺过程管理信息系统 标:代替经验丰富的工艺人员 智能生成零件的工艺过程
创成式、检索式
核心理论:成组技术+企业基础信息的统筹管理
二、套筒类零件加工工艺
1、套筒类零件的功用及结构特点 套筒类零件是指在回转体零件中的空心薄壁 件,是机械加工中常见的一种零件,在各类机器 中应用很广,主要起支承或导向作用。由于功用 不同,其形状结构和尺寸有很大的差异,常见的 有支承回转轴的各种形式的轴承圈、轴套;夹具 上的钻套和导向套;内燃机上的气缸套和液压系 统中的液压缸、电液伺服阀的阀套等都属于套类 零件。其大致的结构形式如图9-3所示。
画出并分析一专用铣削夹具,指出定位元件、夹紧元 件和夹具体并指出它们的作用。
答:左边固定钳口是定位元件,起到定位作用, 右边的活动钳口是夹紧元件起到夹紧,作用是装夹小而规则的零件。
安装举例 机械制造工艺学中,安装指齿轮毛坯经一次定位夹紧后,在工 件没有取下来,所进行的切削加工(铣齿)内容。
3. 工位
生产类型划分
二、机械加工工艺过程
机械制造过程是机械产品从原材料开始到成品之间各相互关联的劳动过 程的总和。它包括毛坯制造、零件机械加工、热处理、机器的装配、检验、 测试和油漆包装等主要生产过程,也包括专用夹具和专用量具制造、加工设 备维修、动力供应(电力供应、压缩空气、液压动力以及蒸汽压力的供给 等)。 工艺过程是指在生产过程中,通过改变生产对象的形状、相互位置和性 质等,使其成为成品或半成品的过程。 机械产品生产工艺过程又可分为铸造、锻造、冲压、焊接、机械加工、 热处理、装配、涂装等。其中与原材料变为成品直接有关的过程,称为直接 生产过程,是生产过程的主要部分。 而与原材料变为产品间接有关的过程,如生产准备、运输、保管、机床 与工艺装备的维修等,称为辅助生产过程。
冲压车间常识和管理

冲压车间常识和管理一、冲压车间概述冲压车间是制造业中的一种常见车间,主要用于生产冲压件。
冲压件是指通过冲压工艺将金属材料加工成所需形状的零件。
冲压工艺具有高效、精确和重复性好等特点,广泛应用于汽车、家电、机械等行业。
二、冲压工艺流程冲压车间的工艺流程通常包括以下几个步骤:1.材料准备:选择合适的金属材料,并使用剪板机或切割机将材料切割成所需尺寸。
2.冲压模具设计:根据零件的形状和要求,设计冲压模具,包括上模、下模和冲头等。
3.模具制造:根据设计图纸制造冲压模具,在加工过程中需要考虑模具的加工精度和表面质量。
4.冲压加工:将材料放置在冲床上,通过上下模具的运动使材料受力变形,得到所需的零件形状。
5.零件整形:对冲压件进行去毛刺、修边、矫正等处理,保证零件的质量和外观要求。
6.马达兰流程:对冲压件进行清洗和表面处理,提高零件的耐腐蚀性和美观性。
三、冲压车间的设备和工具冲压车间主要使用以下设备和工具:1.冲床:用于进行冲压加工的主要设备,根据生产需求可以选择单点冲床、连续冲床或多工位冲床。
2.切割设备:包括剪板机、切割机等,用于将金属材料切割成所需尺寸。
3.模具加工设备:包括数控铣床、数控车床等,用于制造冲压模具。
4.辅助设备:如切角机、拉床等,用于零件的整形和加工。
5.测量工具:如卡尺、量具等,用于测量零件尺寸和表面质量。
6.油压设备:用于冲床的驱动和辅助装置,如液压系统、润滑系统等。
四、冲压车间常见问题及解决方法在冲压车间的生产过程中,常会遇到一些问题,如下所示:1.材料浪费问题:冲压过程中,由于模具调试不精确或操作不当,可能导致材料浪费。
解决方法包括优化模具设计、提高操作技能和加强质量检查等。
2.模具磨损问题:冲压模具在长时间使用后容易出现磨损,影响零件质量和生产效率。
解决方法包括定期维护保养、提高硬度和涂覆保护层等。
3.零件变形问题:冲压过程中,由于材料性质或操作不当,零件可能出现变形。
解决方法包括调整工艺参数、优化模具结构和提高操作技能等。
机加工常识内容
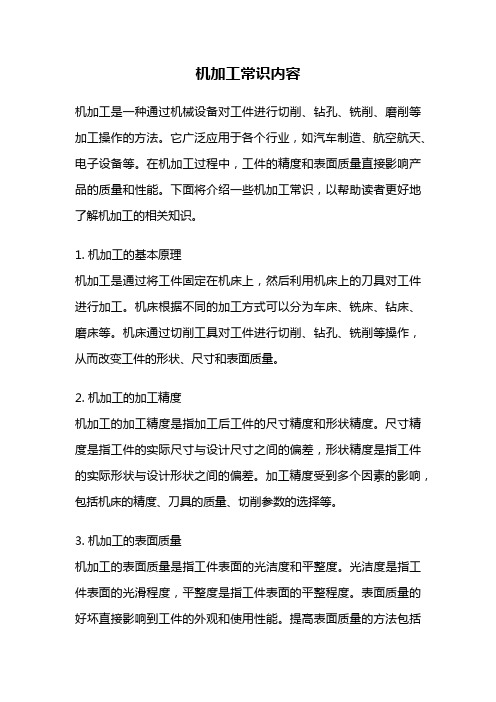
机加工常识内容机加工是一种通过机械设备对工件进行切削、钻孔、铣削、磨削等加工操作的方法。
它广泛应用于各个行业,如汽车制造、航空航天、电子设备等。
在机加工过程中,工件的精度和表面质量直接影响产品的质量和性能。
下面将介绍一些机加工常识,以帮助读者更好地了解机加工的相关知识。
1. 机加工的基本原理机加工是通过将工件固定在机床上,然后利用机床上的刀具对工件进行加工。
机床根据不同的加工方式可以分为车床、铣床、钻床、磨床等。
机床通过切削工具对工件进行切削、钻孔、铣削等操作,从而改变工件的形状、尺寸和表面质量。
2. 机加工的加工精度机加工的加工精度是指加工后工件的尺寸精度和形状精度。
尺寸精度是指工件的实际尺寸与设计尺寸之间的偏差,形状精度是指工件的实际形状与设计形状之间的偏差。
加工精度受到多个因素的影响,包括机床的精度、刀具的质量、切削参数的选择等。
3. 机加工的表面质量机加工的表面质量是指工件表面的光洁度和平整度。
光洁度是指工件表面的光滑程度,平整度是指工件表面的平整程度。
表面质量的好坏直接影响到工件的外观和使用性能。
提高表面质量的方法包括选择合适的刀具、控制切削参数、加工后的抛光等。
4. 机加工的工艺流程机加工的工艺流程包括工件的装夹、刀具的选择、切削参数的确定等。
在机加工过程中,工艺流程的合理性和操作的规范性对于保证加工质量至关重要。
在进行机加工之前,需要进行工艺设计和工艺规程的制定,以确保机加工过程的顺利进行。
5. 机加工的刀具选择刀具是机加工过程中最重要的工具,刀具的选择直接影响到加工效率和加工质量。
刀具的选择需要考虑工件材料、加工方式、加工精度等因素。
常用的刀具包括车刀、铣刀、钻头、磨头等。
选择合适的刀具可以提高加工效率和加工质量。
6. 机加工的切削参数切削参数是指切削过程中刀具和工件之间的相对运动参数,包括切削速度、进给量、切削深度等。
切削参数的选择需要综合考虑工件材料、刀具材料、切削方式等因素。
机械加工安全常识

机械加工安全常识一、机械加工的基本概念和分类1. 机械加工的定义机械加工是指利用机械设备对工件进行切削、磨削、冲压、焊接等加工过程,以改变工件的形状、尺寸、表面质量和性能的一种制造工艺。
2. 机械加工的分类机械加工可以根据加工方式和加工对象的不同进行分类,常见的机械加工包括铣削、车削、钻削、磨削、冲压等。
二、机械加工安全的重要性1. 机械加工事故的危害机械加工事故可能导致工人受伤甚至死亡,造成设备损坏和生产中断,对企业的生产经营和员工的身心健康都造成严重影响。
2. 机械加工安全的意义机械加工安全是保障员工生命安全和企业正常运营的重要环节,合理的安全措施和操作规范可以降低事故发生的概率,提高工作效率和生产质量。
三、机械加工安全常识1. 机械加工前的准备工作•确认机床和刀具的安全性能,检查设备是否正常运转。
•穿戴必要的劳动防护用品,如安全鞋、手套、护目镜等。
•清理工作区域,保持工作环境整洁。
2. 机械加工操作的注意事项•严禁戴手套操作,以免被卷入机器中。
•在操作过程中,保持专注,不要分心或急躁。
•使用合适的切削液,保持工件和刀具的冷却和润滑。
•对于大型工件,应采取适当的固定和支撑措施,防止工件移动或倾斜。
3. 机械加工后的安全处理•关闭机床电源,清理加工区域,确保设备和工作环境整洁。
•对于刀具和机床的维护保养,应按照操作手册的规定进行。
•及时清理切屑和废料,防止积累引发安全隐患。
四、常见机械加工事故及预防措施1. 切削工具事故•事故原因:切削工具磨损、断裂或安装不当。
•预防措施:定期检查切削工具的状况,确保切削工具的质量和安装正确。
2. 机床操作事故•事故原因:操作人员疏忽大意或操作不当。
•预防措施:提供操作培训,强调操作规范,严禁非专业人员操作机床。
3. 电气事故•事故原因:电气设备老化、维护不当或操作不当。
•预防措施:定期检查电气设备,确保设备正常运行,操作人员要接受电气安全培训。
4. 机械设备事故•事故原因:机械设备故障、缺乏维护保养或负载过大。
机械制造工艺学总结
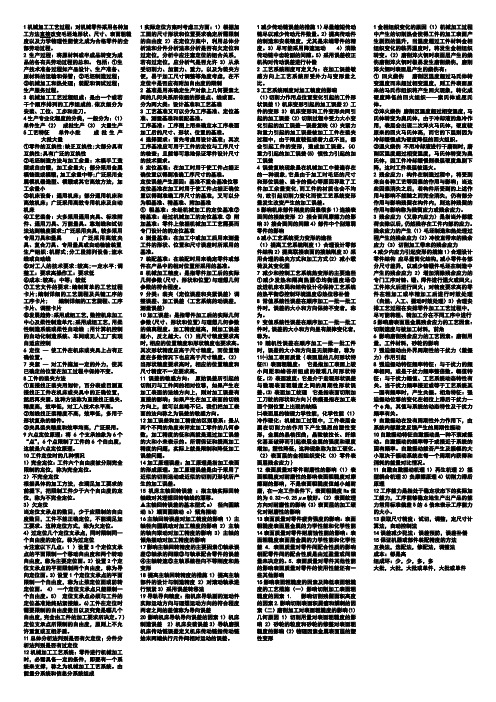
1机械加工工艺过程:对机械零件采用各种加工方法直接改变毛坯地形状、尺寸、表面粗糙部劳动过程。
2生产过程:将原材料或半成品转变为成品的各有关劳动过程的总和。
包括:①生产技术准备过程如产品设计、生产准备、原材料的运输和保管;②毛坯制造过程;③机械加工和热处理;装配和调试过程;生产服务过程。
3机械加工工艺过程组成:是由一个或若干个顺序排列的工序组成的.依次细分为安装、工位、工步和走刀。
4生产专业化程度的分类,一般分为:(1)单件生产(2)成批生产(3)大量生产5工艺特征单件小批成批生产大批大量①零件的互换性:缺乏互换性;大部分具有互换性;具有广泛的互换性②毛坯制造方法与加工余量:木模手工造型或自由锻,加工余量大;部分采用金属模铸造或模锻,加工余量中等;广泛采用金属模机器造型、模锻或其它高效方法,加工余量小③机床设备:通用机床;部分通用机床和高效机床;广泛采用高效专用机床及自动机床④工艺装备:大多采用通用夹具、标准附件、通用刀具、万能量具。
靠划线和试切法达到精度要求;广泛采用夹具,较多采用专用刀具和量具;广泛采用高效夹具、复合刀具、专用量具或自动检验装置生产组织:机群式;分工段排列设备;流水线或自动线⑤对工人的技术要求:较高;一定水平;调整工:要求高操作工:要求低⑥成本:较高;中等;较低⑦工艺文件的要求:编制简单的工艺过程卡片;编制详细的工艺规程及关键工序的工序卡片; 编制详细的工艺规程、工序卡片、调整卡片⑧发展趋势:采用成组工艺,数控机床加工中心及柔性制造单元;采用成组工艺,用柔性制造系统或柔性自动线 ;用计算机控制的自动化制造系统、车间或无人工厂实现自适应控制6定位—使工件在机床或夹具上占有正确位置。
7夹紧—对工件施加一定的外力,使其已确定的位置在加工过程中保持不变。
8工件的装夹方法①直接找正装夹用划针,百分表或目测直接找正工件在机床或夹具中的正确位置,然后再夹紧。
这种方法称为直接找正装夹。
精度高,效率低,对工人技术水平高。
机械加工的基本常识

机械加工的基本常识机械加工的一些基本常识和知识,如常用器械、加工工序、生产类型以及注意事项有哪些?以下是店铺收集整理的关于机械加工的基本常识,希望对你有帮助。
机械加工的基本常识介绍1 .机械加工的常用器械:包括数显铣床、数显成型磨床、数显车床、电火花机、万能磨床、外圆磨床、内圆磨床、精密车床等设备,这些设备可以进行精密零件的车、铣、刨、磨等加工,其加工精度可达2um。
2.机械加工的加工工序:机械加工的生产过程包括原材料的运输保存、生产准备、毛胚制造、零件的加工和热处理、产品的装配调试等内容。
通过机械加工,能改变原材料的形状、尺寸以及性能,使之成为符合要求的成品。
这一过程也叫工艺过程,是由一个或若干个顺序排列的工序组成的。
3.机械加工的加工类型:单件加工:就是单独生产某个零件,很少出现重复生产。
成批加工:就是成批的生产制造相同的零件。
大量加工:当产品的制造量很大时,则需要经常重复进行一种零件的生产。
零件的工艺过程在拟定时,由于零件的生产类型不同,所以所采用的加工方法、设备、工具、毛坯以及技术要求等这些方面,都是不同的。
4.机械加工的注意事项:(1)要便于加工操作,尽量减少不必要的弯腰、踮脚动作。
(2)定位应准确可靠,以防产生振动,造成误差。
(3)设备操作件的运动方向与被操作件的运动方向要符合规定要求,并要简易标明。
(4)设置必要的互锁机构,以防操作中出现不协调动作,引发危险。
(5)手柄、手轮、按钮的结构以及排列位置要符合要求。
一般启动按钮应安装在机壳内,并装设防止意外触动的护环,轴杆上应装有自动脱出装置,以防手轮、手柄伤人。
机械加工的发展现状随着现代机械加工的快速发展,机械加工技术快速发展,慢慢的涌现出了许多先进的机械加工技术方法,比如微型机械加工技术、快速成形技术、精密超精密加工技术等。
微型机械加工技术随着微/纳米科学与技术(Micro/Nano Science and Technology)的发展,以本身形状尺寸微小或操作尺度极小为特征的微机械已成为人们认识和改造微观世界的一种高新科技。
弹簧零件的加工和制作基本常识
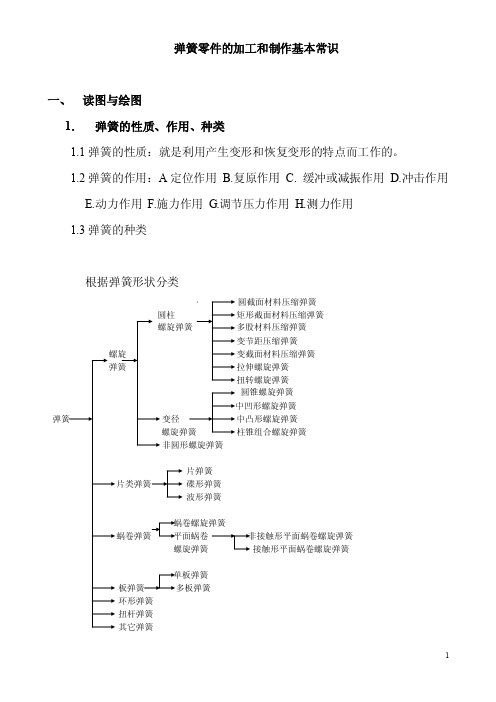
弹簧零件的加工和制作基本常识一、读图与绘图1.弹簧的性质、作用、种类1.1弹簧的性质:就是利用产生变形和恢复变形的特点而工作的。
1.2弹簧的作用:A定位作用B.复原作用C. 缓冲或减振作用D.冲击作用E.动力作用F.施力作用G.调节压力作用H.测力作用1.3弹簧的种类根据弹簧形状分类圆截面材料压缩弹簧圆锥螺旋弹簧变径非圆形螺旋弹簧片弹簧碟形弹簧波形弹簧螺旋弹簧接触形平面蜗卷螺旋弹簧环形弹簧扭杆弹簧其它弹簧2.各类弹簧的工作图及其审核弹簧的工作图:它包括几何参数、物理参数、和技术条件。
几何参数:包括弹簧的形状和尺寸。
物理参数:主要是指变形与载荷的关系及相应变形下的载荷大小。
技术条件:为使弹簧符合使用要求,需要达到的性能指标(如热处理硬度)及需要采取的工艺措施(如强压处理、喷丸处理、氧化处理或镀锌)2.1压缩螺旋弹簧的工作图及其审核2.1.1 圆柱压缩螺旋弹簧工作图圆柱压缩螺旋弹簧工作图的意义:2.1.1.1弹簧的自由状态时,压力P=0,变形F=0,此时弹簧的高度H0(或长度L0)称为自由高度2.1.1.2弹簧受最小工作载荷P1时,相应的变形和工作高度分别为F1和H1 2.1.1.3 P2是弹簧的最大工作载荷,相应的变形和工作高度为F2和H2,弹簧一般是在载荷P1和P2范围内工作2.1.1.4工作极限载荷:是在该载荷下,弹簧的工作极限应力τj已达到了材料所允许的扭转极限应力,工作极限载荷用Pj 表示,相应的变形和工作高度是Fj 和Hj2.1.2 对圆柱压缩螺旋弹簧工作图的审核 2.1.2.1几何参数的审核要对材料直径、弹簧直径、有效圈数、总圈数和自由高度进行审核D 1=D 2-d, D=D 2+d ,L=n1×π×D 2 ,t=nHbH 0+db=2D H , (压缩弹簧的自由高度与弹簧中径之比称为细长比)端头并紧磨平时:H b =[n1—(0.3~0.5)]×d, 两端头拼紧不磨平时:Hb=n1×dd -材料直径,D -弹簧外径,D2-弹簧中径,D1-弹簧内径, H 0-弹簧的自由高度,L -弹簧展开长度,b -弹簧细长比, t -弹簧节距,n1-弹簧总圈数,n -弹簧有效圈数, H b -弹簧压并高度审核几何参数:第一要审核这些参数的理论值有无错误 第二要审核这些参数是否合适两端固定的弹簧:b <5.3,一端固定另一端回转:b <3.7, 两端回转:b <2.6 2.1.2.2 物理参数的审核P ′=3248nD Gd P=3248nD FGd P ′-弹簧刚度,G -弹簧材料的剪切弹性模量(78500N/mm 2), P -弹簧载荷,F -弹簧变形,d -材料直径, n -有效圈数,D 2-弹簧中径刚度:弹簧产生单位变形量的工作负荷;它是用来度量弹簧承载能力的物理量。
机械设计常识知识点

机械设计常识知识点机械设计是一门综合性的学科,它涉及到多个领域和专业知识。
在机械设计过程中,掌握一些基本的常识知识点是非常重要的。
本文将介绍一些机械设计中常见的知识点。
1. 材料选择在机械设计中,材料的选择至关重要。
不同的材料具有不同的特性,例如强度、刚性、耐磨性等。
设计师需要根据设计要求和目标选择合适的材料。
常见的材料包括金属、塑料、复合材料等。
2. 受力分析在机械设计过程中,受力分析是必不可少的一步。
通过受力分析,可以确定零件的受力情况,避免设计中出现过载或者应力集中等问题。
常见的受力分析方法包括静力学分析、有限元分析等。
3. 结构设计结构设计是机械设计中的关键环节。
通过合理设计零件的结构,可以提高产品的性能和可靠性。
在结构设计中需要考虑到多个方面,例如刚度、稳定性、振动等。
4. 连接方式连接方式是机械设计中的一个重要问题。
不同的连接方式适用于不同的应用场景。
常见的连接方式包括焊接、螺栓连接、键连接等。
合理选择连接方式可以提高产品的拆卸和维修能力。
5. 传动方式传动方式是机械设计中的一个核心问题。
合理选择传动方式可以实现不同零件之间的运动转换。
常见的传动方式包括齿轮传动、链传动、皮带传动等。
6. 尺寸配合尺寸配合是机械设计中的一个重要方面。
合理的尺寸配合可以保证零件之间的运动平稳,防止出现偏差和卡死等问题。
常见的尺寸配合包括间隙配合、过盈配合等。
7. 热处理热处理是一种常用的工艺,在机械设计中应用广泛。
通过热处理可以改变材料的性能,例如提高硬度、强度等。
常见的热处理方式包括淬火、回火、正火等。
8. 表面处理表面处理是机械设计中的一个重要环节。
通过表面处理可以提高零件的耐磨性、防腐蚀性等。
常见的表面处理方式包括镀金属、喷涂、电镀等。
9. 制造工艺制造工艺是机械设计中需要考虑的一个方面。
在设计过程中需要考虑到制造的可行性和成本。
合理选择制造工艺可以提高产品的生产效率和质量。
总结:机械设计常识知识点包括了材料选择、受力分析、结构设计、连接方式、传动方式、尺寸配合、热处理、表面处理以及制造工艺等。
汽车零部件加工常识

汽车零部件加工常识
汽车零部件加工常识包括以下几个方面:
1.材料:汽车零部件加工的材料主要包括钢铁、有色金属、非金属材料等。
其中,钢铁材料应用最广泛,而有色金属则主要用于制造一些要求较高精度和轻量化的零部件。
非金属材料则主要用于一些承受压力较小或对重量要求较高的部件。
2.加工工艺:汽车零部件加工工艺主要包括铸造、锻造、焊接、机械加工、表面处理等。
不同的工艺适用于不同的材料和零件要求,需要根据实际情况进行选择。
3.加工精度:汽车零部件的加工精度直接影响着车辆的质量和性能。
因此,加工过程中需要保证高精度的要求,同时采取有效的检测手段和控制方法来确保加工精度。
4.质量控制:汽车零部件的质量控制是保证零部件质量和可靠性的重要环节。
需要对零部件进行一系列的质量检测和控制,包括进货检验、过程检验和最终检验等。
5.安全生产:汽车零部件加工过程中需要注意安全生产的规范和要求,采取相应的安全措施,防止生产事故的发生。
总之,汽车零部件加工需要遵循高精度、高质量、高效率的原则,加强工艺技术研发和生产过程控制,确保零部件的质量和可靠性,以满足汽车工业的需求。
汽车典型零件制造工艺之连杆制造工艺 ppt课件

这些平面常采用铣削或拉削加工,接合面的精加工一般采用高效磨削。
图为采用立式外拉床拉削分体式毛坯的连杆大头侧面、半圆孔及接合面,有 a,b 两 种 组 合形式, 每种形式 由两个工 步完成。 加工时以 小头孔、 端面及大 头外形表 面定位。
ppt课件
25
3. 连杆加工的新工艺——裂解
3.1 连杆裂解加工概述
连杆毛坯的制作方法:模锻、辊锻—模锻
ppt课件
7ቤተ መጻሕፍቲ ባይዱ
1. 连杆概述
连杆毛坯的分类:
体盖连成一体的整体式毛坯和体盖分开的分体式毛坯。 整体式毛坯在后续加工过程中需通过铣、锯或拉等形式将体盖切开。 为给切断工序保留加工余量,一般将整体式毛坯大头孔锻成椭圆形。
整体式连杆毛坯锻造工时少、模具少,是连杆毛坯制作的主要形式。
连杆裂解(连杆胀断)技术是20世纪90年代初发展起来的一种先 进的连杆加工新技术,其作用主要是使连杆体与连杆盖分离。经 过裂解加工的连杆接合面定位更加准确。
经过裂解加工的连杆
ppt课件
裂解加工过的连杆盖端面
26
3. 连杆加工的新工艺——裂解
连杆裂解技术的原理:
利用人为在连杆大头孔内加工出的V型槽或矩形槽(裂解槽);然后采 用一个楔形压头压入大头孔(连杆大头孔与压头之间还有一对半圆裂 解套,称胀块),当压头向下移动时,初始裂解槽由内孔不断向外扩 展,直至将大头孔沿裂痕断开,是连杆体与连杆盖分离。
小凸点
工艺凸台
辅助基准孔
ppt课件
11
2. 连杆的传统加工方法
1)加工两端面的定位
端面是后续加工其他表面的基准,因此连杆加工从端面加工开始。 加工连杆两端面时分别采用两种定位方式:Ⅰ工位为铣其中一个端面,用两 个V型块夹持连杆大端的两侧圆弧面,以保证两侧面加工余量均匀; Ⅱ工位 为铣另一端面,此时以已加工过的端面作为定位基准,即互为基准。
压铸常识知识点

压铸常识知识点什么是压铸?压铸是一种常见的金属成型工艺,也被称为压力铸造。
它是通过将熔化金属注入到特殊的铸模中,然后施加高压力冷却和固化金属来制造金属零件的过程。
压铸通常用于生产复杂形状的零件,如汽车发动机零件、电子设备外壳等。
压铸工艺步骤1.设计模具:首先需要根据产品的设计要求,制作合适的压铸模具。
模具的设计应考虑到产品的形状、尺寸和材料等因素。
2.加热金属:将所需的金属材料(通常是铝合金或锌合金)加热至熔点以上,使其变为液态。
3.充填模具:将熔化的金属注入到事先准备好的压铸模具中。
注入时需要控制注入速度和压力,以确保金属能够充分填充模具中的空腔。
4.施加压力:在金属充填完毕后,施加高压力以冷却和固化金属。
通过施加压力,可以确保金属紧密填充模具,并使其在冷却过程中保持形状稳定。
5.开模和取出:待金属充分冷却后,拆卸模具并取出铸件。
这一步通常需要使用专业的工具和设备,以确保铸件的完整性和质量。
6.后处理:根据实际需求,对铸件进行一些后续处理,如去除余料、打磨、抛光、热处理等,以获得最终的产品。
压铸的优势和应用压铸作为一种高效的金属成型工艺,具有以下优势:1.生产效率高:压铸可以实现自动化生产,大大提高了生产效率。
每个模具往往可以生产多个产品,而且生产周期相对较短。
2.零件质量好:压铸可以生产出形状复杂、尺寸精确的金属零件,具有较高的一致性和稳定性。
同时,压铸可以提供优良的表面光洁度和一致的机械性能。
3.节约材料:压铸过程中可以循环利用金属材料,减少了材料的浪费。
并且,由于压铸零件具有较高的强度和刚度,可以减少零件的数量,达到节约材料的目的。
压铸广泛应用于各个领域,包括汽车工业、电子设备、家电、通信设备等。
它可以制造出各种复杂形状的零件,如汽车发动机零件、手机外壳、航空航天部件等。
压铸还可以与其他加工工艺结合使用,如机加工、表面处理等,满足不同的产品需求。
压铸的未来发展随着科技的不断进步,压铸工艺也在不断发展和改进。
铸造工艺常识知识点总结

铸造工艺常识知识点总结铸造工艺常识包括了铸造的基本原理、工艺流程、材料选择、设备技术和质量控制等内容。
以下是一些铸造工艺的基本知识点总结:1. 铸造的基本原理- 铸造是将金属或合金加热至液态状态,倒入模具,然后冷却凝固成型的制造方法。
这种工艺可以制造出各种大小和形状的零件,具有很高的生产效率和经济性。
2. 铸造工艺流程- 铸造工艺流程包括模具设计、熔炼、浇铸、清理和后处理等关键步骤。
模具设计决定了最终产品的形状和尺寸,熔炼是将原料金属或合金加热至液态状态的过程,浇铸是将熔化的金属倒入模具的步骤,清理和后处理是对铸件进行去除毛刺、砂眼和表面处理的步骤。
3. 铸造材料选择- 铸造材料的选择包括金属及合金的选择,辅助材料的选择。
金属及合金的选择应考虑零件的用途、工作条件、强度要求、耐磨性、耐腐蚀性等因素,辅助材料选择应考虑模具材料,脱模剂,浇口和浇注系统等。
4. 铸造设备技术- 铸造设备包括熔炼设备、浇注设备、模具设备等。
熔炼设备主要有电弧炉、感应炉等,浇注设备主要有手工浇注、重力铸造、压力铸造等。
模具设备包括砂型、金属型、脱壳模、永久模等。
5. 铸造质量控制- 铸造质量控制包括原材料的质量控制、生产过程的质量控制和铸件的质量控制。
原材料的质量控制包括原料化学成分、物理性能、外观质量等。
生产过程的质量控制包括熔炼温度、浇注温度、冷却速度、浇注方式等。
铸件的质量控制包括尺寸精度、表面质量、内部缺陷等。
综上所述,铸造工艺是一种重要的金属加工技术,广泛应用于各个领域。
掌握铸造工艺的基本知识对于提高产品质量、降低生产成本具有重要意义。
希望本文对铸造工艺感兴趣的读者有所帮助。
- 1、下载文档前请自行甄别文档内容的完整性,平台不提供额外的编辑、内容补充、找答案等附加服务。
- 2、"仅部分预览"的文档,不可在线预览部分如存在完整性等问题,可反馈申请退款(可完整预览的文档不适用该条件!)。
- 3、如文档侵犯您的权益,请联系客服反馈,我们会尽快为您处理(人工客服工作时间:9:00-18:30)。
– 第一道切削加工工序所使用的基准 – 不是(粗加工时使用的基准)
• 精基准
– 第一道工序以后使用的基准
(1)粗基准
• 第一道切削加工工序所使用的基准
– 不是(粗加工时使用的基准)
• 第一道工序只能使用未加工表面作基准 • 选择粗基准的基础
– 保证各个加工表面都有足够加工余量 – 保证不加工表面的位置精度
– V型铁、挡块 – 平面用:支承钉、支承板 – 孔用:心轴、定位销
• 每种元件限制的自由度数量不同
– 形状决定的
• 钉(1),板(2),销(4、2、1) • V型铁(4、2),心轴(4、2)
支承钉
• 限制1个自由度
支承板
• 较长时,限制2个自由度
定位销
• 圆柱销:(长销:4,短销或圆锥销:2 ) • 菱形销(削边销):1 • 一面两销:用于箱体的完全定位
• 外圆、内圆
– 长(4)、短(2)
• 锥面
– 长(5)、短(3)
• 一般判断原则
– 观察小1、长2
定位基准:圆柱(内外圆)
• 长4、短2
定位基准:锥面
• 长5、短3
6、定位基准的选择原则
• 定位基准选择的出发点
– 保证加工精度、提高加工效率 – 从加工精度要求高的表面中选择
V型铁
• 长V型铁(4) • 短V型铁(2)
• 长心轴(4) • 短心轴(2)
心轴
5、基准:工件上定位的几何元素
• 基准
– 零件的设计制造中,用于确定零件上点线面 等几何要素的依据(也是一些点线面)
• 基准的种类
– 设计基准
• 设计时使用的基准
– 工艺基准
• 制造零件或者装配机器时使用 • 定位基准、度量基准、装配基准
设计基准
• 面2、3、孔4的设计 基准是面1
• 孔5的基准是孔4 • 实际上全部都是面1
定位基准
• 观察图示零件
– 加工外圆和端面时的 定位基准
• 孔的轴线
• 定位基准通常都以面 的形式体现
– 轴线->孔面 – 因此基准面要求有更
高的加工精度
常见定位基准表面确定的自由度
• 平面
– 大平面(3)、小平面(1)、狭长平面(2)
• 其它原则
– 表面光洁、平整、面积足够大、装夹稳固
• 重要常识
– 粗基准只能使用一次
(2)精基准
• 第一道工序后应该使用已加工表面作为 基准:精基准
• 选择的基础
– 保证精度
• 基准重合、基准同一、自为基准、互为基准
– 基准面的精度应该较高
• 选定基准面后,即使该表面设计精度不高,也 应该提高加工精度
二、安装与夹具
• 安装包括的概念
– 定位
• 进行机械加工前,必须将工件放在机床上,使 之在夹紧前占据正确的位置
– 夹紧
• 在加工过程中,为使工件能承受切削力,并使 之保持正确位置,必须将工件压紧夹牢
– 从定位到夹紧的整个过程:安装
1、工件安装的方法
• 工件的安装
– 一般均使用夹具
• 机床上自带的通用夹具、专门制作的专用夹具
检验
机床 车床 外圆磨床
生产类型
• 生产类型
– 零件大小+生产纲领(年产量) – 单件生产
• 通用机床、工夹量具、工序集中、需要熟练工
– 成批生产
• 专用机床、工夹量具、工序分散、工人技能要求一般
– 大量生产
• 广泛采用专用生产线、重复劳动、工人技能要求不高
• 无论那种批量,均可使用数控机床
– 尽量工序集中
零件制造工艺过程常识
机械制造基础
零件制造工艺过程常识
• 工艺过程的有关概念
– 工艺过程、工序、工步、生产类型
• 安装与夹具
– 基准、六点定位原理、基准选择原则、夹具
• 零件加工工艺制订的有关常识
– 内容、步骤、原则、工艺文件、CAPP
• 简单实例
一、工艺过程的有关概念
• 生产过程
– 机器制造时,由原材料到成品之间各个相互 关联的劳动过程的总和
工艺过程的组成
• 工序
– 三定一连续:
• 定机床、定工件、定工人 • 连续完成的加工内容
• 工序可以细分为工步
• 定刀具或装夹
工序 1
2 3
工序内容 车端面,钻中心孔,粗车各外圆,半精车各外圆,切槽、倒角、 车螺纹 (这里的工序很多-工序集中) 磨Ф30,Ф35,Ф45外圆至尺寸要求,靠磨Ф50台肩面
– 例如,可能包括
• 原材料运输和保管(库存) • 生产准备工作 • 毛坯制造、零件加工和热处理 • 产品装配、调试、检验、油漆、包装
工艺过程
• 工艺过程
– 生产过程的主要部分 – 机械加工工艺过程
• 用机械加工方法直接改变原材料或毛坯形状、 尺寸,使之变成成品
– 装配工艺过程
• 在装配车间将零件装配成机器的过程
• 直接安装
– 使用机床自带的通用夹具安装
• 有时需画线找正位置、费时、适用于单件小批
• 利用专用夹具安装
• 安装迅速可靠、精度高、成本高、批量生产
• 哲学问题?
• 单件小批生产、如果通用夹具不能保证精度或者非常费时, 怎么办?
2、关于专用夹具
导向元件 定位元件
夹紧机构
专用镗模通孔夹具
夹具体和其它部分
基准重合原则
• 考查3种定位基准下尺寸A的公差
– 以M定位 – 以H定位 – 以K定位
• 已知
– M-H的公差
• δc
– H-K的公差
• δB
以M定位
• 考虑基准不重合产生 的误差
• εA= δB + δc • 当然,还有这次加工
产生的加工误差
精基准选择的其它原则
• 基准同一原则
– 加工位置精度要求较高的一组表面,尽可能 选择同一个基准定位
– 有利于保证这些表面的相互位置精度
• 自为基准、互为基准 • 精度较高、装夹稳固可靠 • 夹具结构简单、工件安装加工方便
以H定位
粗基准选择原则
• 选择不加工表面
– 保证不加工表面的位 置精度
– 多个不加工表面
• 选择位置精度要求高 的
粗基准选择原则
• 选择要求加工余量均 匀的表面
– 该基准面的加工均匀 – 机床导轨表面要求
• 金相、性能一致 • 去处一层很薄的余量
粗基准选择原则
• 所有表面都要加工时,选择余量和公差 最小的表面,避免出现废品
3、六点定位原理:自由度
• 不受约束的物体
– 六个自由度:三个方向移动、三个方向转动
六点定位原理
• 六点定位原理
– 要完全确定工件位置, 必须有六个相应的支 承点来限制工件的六 个自由度
定位情况
• 完全定位 • 不完全定位 • 超(过)定位 • 欠定位:绝对不允许
4、夹具上的定位元件
• 夹具上用于限制工件自由度的元件