工艺质量控制程序
工艺质量控制程序
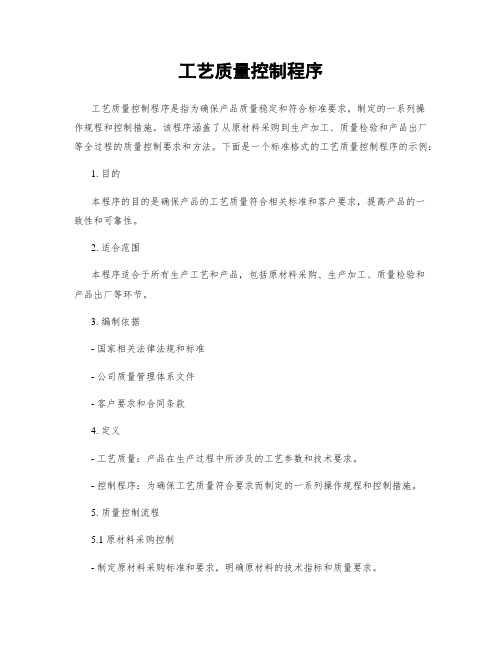
工艺质量控制程序工艺质量控制程序是指为确保产品质量稳定和符合标准要求,制定的一系列操作规程和控制措施。
该程序涵盖了从原材料采购到生产加工、质量检验和产品出厂等全过程的质量控制要求和方法。
下面是一个标准格式的工艺质量控制程序的示例:1. 目的本程序的目的是确保产品的工艺质量符合相关标准和客户要求,提高产品的一致性和可靠性。
2. 适合范围本程序适合于所有生产工艺和产品,包括原材料采购、生产加工、质量检验和产品出厂等环节。
3. 编制依据- 国家相关法律法规和标准- 公司质量管理体系文件- 客户要求和合同条款4. 定义- 工艺质量:产品在生产过程中所涉及的工艺参数和技术要求。
- 控制程序:为确保工艺质量符合要求而制定的一系列操作规程和控制措施。
5. 质量控制流程5.1 原材料采购控制- 制定原材料采购标准和要求,明确原材料的技术指标和质量要求。
- 与供应商建立合作关系,确保供应商具备合格的质量管理体系和能力。
- 对采购的原材料进行抽样检验和测试,确保原材料符合质量要求。
5.2 生产工艺控制- 制定生产工艺标准和要求,包括生产工艺流程、操作规程和设备参数等。
- 对生产设备进行定期维护和保养,确保设备正常运行和工艺参数的稳定性。
- 对生产过程中的关键环节进行监控和调整,及时发现并纠正工艺偏差。
5.3 质量检验控制- 制定质量检验标准和要求,明确产品的检验项目、方法和标准。
- 对生产过程中的关键环节进行抽样检验和测试,确保产品符合质量要求。
- 对不合格产品进行处理,包括返工、报废和整改等措施。
5.4 产品出厂控制- 制定产品出厂标准和要求,明确产品的包装、标识和出厂检验等要求。
- 对产品进行最终检验和测试,确保产品符合质量标准和客户要求。
- 对合格产品进行包装和标识,确保产品的完整性和可追溯性。
6. 质量控制记录6.1 原材料采购记录:包括原材料的采购合同、检验报告和供应商评估等记录。
6.2 生产工艺控制记录:包括生产工艺参数、设备维护记录和工艺调整记录等。
产品的生产工艺和质量控制流程

产品的生产工艺和质量控制流程在制造业中,产品的生产工艺和质量控制流程是确保产品质量和客户满意度的关键。
本文将介绍一种常见的产品生产工艺和质量控制流程,以确保产品的高质量。
1.产品设计和研发阶段在产品的设计和研发阶段,制造商首先确定产品的设计目标和规格要求。
同时,进行市场调研,以了解客户需求和竞争对手的产品。
在设计过程中,制造商要协同各个部门,例如设计、工程师和市场,以确保产品的功能、性能和外观都达到预期。
2.原材料采购和质量检测原材料的采购是产品生产的重要环节。
制造商需要寻找可靠的供应商,确保原材料的可靠性和质量。
一旦原材料到达生产现场,将对其进行质量检测。
这包括检查材料的规格、外观和性能,以确保它们符合产品要求和行业标准。
3.生产工艺和流程控制在产品的生产过程中,制造商必须制定和执行严格的生产工艺和流程控制。
这包括确保生产设备的正常运行和维护,遵循标准的操作规程。
制造商还应实施质量管理体系,例如ISO标准,以确保生产过程的可追溯性和一致性。
4.中间产品质量检验在生产过程中,制造商需要进行中间产品的质量检验。
这可以包括外观检查、尺寸测量、功能测试等。
通过及时发现和纠正生产过程中的问题,可以防止缺陷产品流入下一个流程或最终交付给客户。
5.最终产品质量检验和测试在产品生产完成后,制造商会进行最终产品的质量检验和测试。
这包括全面的外观检查、性能测试、可靠性测试等。
只有通过了严格的检验和测试,产品才能符合质量标准,并交付给客户。
6.售后服务和客户反馈一旦产品交付给客户,制造商应提供及时的售后服务。
这包括解决客户的问题、回答客户的咨询,以及处理客户的投诉。
此外,制造商还应积极收集客户的反馈和建议,以不断改进产品和生产工艺。
通过上述的产品生产工艺和质量控制流程,制造商可以确保产品的高质量和客户满意度。
这个流程应该是系统化、标准化和持续改进的,以适应市场和技术变化。
只有在有效的生产工艺和质量控制流程下,制造商才能在竞争激烈的市场中立于不败之地,赢得客户的信任和信赖。
工艺质量控制程序
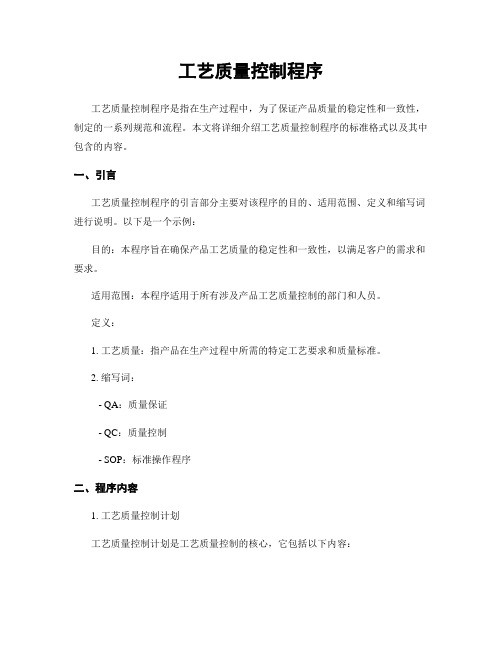
工艺质量控制程序工艺质量控制程序是指在生产过程中,为了保证产品质量的稳定性和一致性,制定的一系列规范和流程。
本文将详细介绍工艺质量控制程序的标准格式以及其中包含的内容。
一、引言工艺质量控制程序的引言部分主要对该程序的目的、适用范围、定义和缩写词进行说明。
以下是一个示例:目的:本程序旨在确保产品工艺质量的稳定性和一致性,以满足客户的需求和要求。
适用范围:本程序适用于所有涉及产品工艺质量控制的部门和人员。
定义:1. 工艺质量:指产品在生产过程中所需的特定工艺要求和质量标准。
2. 缩写词:- QA:质量保证- QC:质量控制- SOP:标准操作程序二、程序内容1. 工艺质量控制计划工艺质量控制计划是工艺质量控制的核心,它包括以下内容:- 产品工艺要求:详细描述产品的工艺要求,包括工艺流程、工艺参数、工艺标准等。
- 质量标准:明确产品的质量标准,包括外观、尺寸、性能等指标。
- 检验方法:定义产品的检验方法,包括检验设备、检验步骤、检验标准等。
- 抽样计划:确定产品的抽样方案,包括抽样数量、抽样频率等。
- 检验记录:规定对产品进行检验的记录方式和要求。
2. 工艺质量控制流程工艺质量控制流程是指在生产过程中,对产品的各个环节进行控制和监督的流程。
以下是一个示例:- 原材料检验:对进货的原材料进行外观检查、尺寸测量、化学成分分析等,确保原材料的质量符合要求。
- 工艺参数设定:根据产品工艺要求,设定生产过程中的各项参数,如温度、压力、速度等。
- 生产过程控制:对生产过程中的各项参数进行监控和调整,确保产品的质量稳定。
- 在线检测:在生产过程中对产品进行在线检测,及时发现并纠正问题。
- 产品成品检验:对生产完成的产品进行外观检查、尺寸测量、性能测试等,确保产品符合质量标准。
- 不合格品处理:对不合格的产品进行分类和处理,包括返工、报废等。
3. 质量记录与报告质量记录与报告是工艺质量控制的重要环节,它包括以下内容:- 检验记录:对产品的检验结果进行记录,包括检验日期、检验人员、检验结果等。
工艺质量控制程序

工艺质量控制程序工艺质量控制程序是制造业中非常重要的一环,它涉及到产品质量的稳定性和可靠性。
一个完善的工艺质量控制程序可以帮助企业提高产品质量,降低生产成本,增强市场竞争力。
本文将从四个方面详细介绍工艺质量控制程序的重要性和实施方法。
一、质量控制程序的制定1.1 确定质量标准:首先,企业需要明确产品的质量标准,包括外观、尺寸、性能等方面。
通过与客户的沟通和市场需求的分析,确定产品的质量标准,为制定质量控制程序奠定基础。
1.2 制定工艺流程:根据产品的特点和质量标准,制定详细的工艺流程。
工艺流程应包括原材料采购、生产加工、装配和检验等环节,确保每个环节都符合质量标准。
1.3 制定检验标准:根据产品的特点和质量标准,制定详细的检验标准。
检验标准应包括外观、尺寸、性能等方面的要求,以确保产品在生产过程中能够达到质量标准。
二、质量控制程序的实施2.1 培训员工:质量控制程序的实施需要员工的共同努力和配合。
企业应对员工进行相关的培训,使其了解质量控制程序的重要性和具体要求,提高员工的质量意识和技能水平。
2.2 设立质量控制岗位:企业可以设立专门的质量控制岗位,负责监督和执行质量控制程序。
质量控制岗位应具备相关的专业知识和经验,能够有效地进行质量控制和问题解决。
2.3 引入质量管理工具:企业可以引入一些质量管理工具,如统计过程控制(SPC)、六西格玛(Six Sigma)等,用于监控和改进生产过程中的质量问题。
这些工具可以帮助企业及时发现和解决质量问题,提高产品的质量稳定性。
三、质量控制程序的监督和评估3.1 定期检查和评估:企业应定期对质量控制程序进行检查和评估,以确保其有效性和符合性。
通过检查和评估,发现问题并及时进行改进,提高质量控制程序的可靠性和稳定性。
3.2 数据分析和统计:企业可以通过对生产过程中的数据进行分析和统计,评估质量控制程序的效果。
通过分析数据,发现问题并找出原因,进一步改进生产过程,提高产品的质量。
工艺质量控制程序

工艺质量控制程序一、引言工艺质量控制是制造业的核心环节,它涉及到从产品设计到成品交付的每一个环节。
为了确保产品质量,满足客户要求,必须有一套严谨、高效的质量控制程序。
本文将详细阐述工艺质量控制程序的七个关键部分,以期为企业在生产实践中提供有益的参考。
二、工艺策划与设计明确产品要求:在工艺策划阶段,首先要明确产品的性能、功能和可靠性要求。
制定工艺流程:根据产品要求,设计合理的工艺流程,确保产品制造的效率与质量。
确定关键工艺参数:识别关键工艺参数,并设定合理的公差范围。
制定检验计划:确定在工艺流程中需要进行的检验点,以及相应的检验方法。
设计防错措施:为防止生产过程中出现错误,应采取有效的防错措施。
三、原材料质量控制供应商评估:对供应商进行全面评估,确保其能提供符合要求的原材料。
原材料检验:进货时对原材料进行严格检验,确保原材料质量。
原材料存储:合理规划原材料的存储环境,防止因存储不当导致的质量损失。
原材料追溯:建立原材料追溯体系,确保问题原材料的可追溯性。
原材料维护:定期对原材料进行复验,确保其质量稳定性。
四、工艺过程控制作业指导书:为操作人员提供详细、准确的作业指导书。
过程监控:通过适当的监控手段,确保工艺过程符合预设参数和要求。
过程记录:对工艺过程的重要参数进行记录,以便后续分析。
过程调整:根据实际情况,对工艺参数进行调整,以提高产品质量和效率。
操作人员培训:定期对操作人员进行培训,提高其技能水平,确保工艺过程的稳定。
五、检验与测量控制检验计划:制定详细的检验计划,明确检验项目、方法、频次和验收标准。
测量设备校准:确保测量设备的准确性和可靠性,定期进行校准和维护。
(完整版)生产工艺和质量控制方案
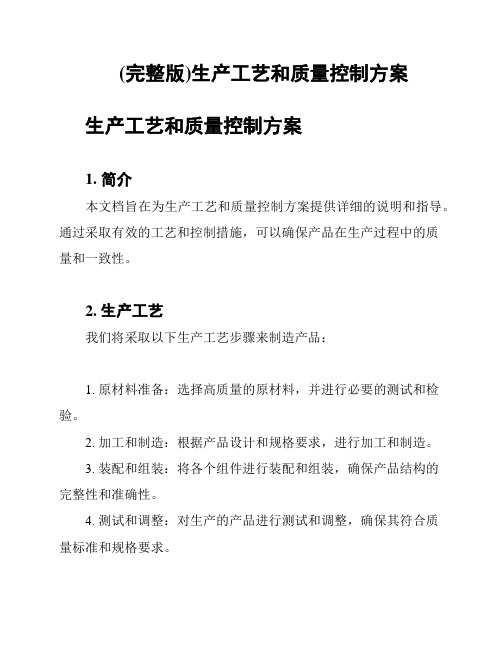
(完整版)生产工艺和质量控制方案生产工艺和质量控制方案1. 简介本文档旨在为生产工艺和质量控制方案提供详细的说明和指导。
通过采取有效的工艺和控制措施,可以确保产品在生产过程中的质量和一致性。
2. 生产工艺我们将采取以下生产工艺步骤来制造产品:1. 原材料准备:选择高质量的原材料,并进行必要的测试和检验。
2. 加工和制造:根据产品设计和规格要求,进行加工和制造。
3. 装配和组装:将各个组件进行装配和组装,确保产品结构的完整性和准确性。
4. 测试和调整:对生产的产品进行测试和调整,确保其符合质量标准和规格要求。
5. 检验和包装:对产品进行最终检验和包装,确保产品的完整性和外观质量。
3. 质量控制为了确保产品的质量和一致性,我们将采取以下质量控制措施:1. 原材料质量控制:对原材料进行严格的选择和验收,确保其符合质量要求。
2. 生产过程监控:通过实时监控和检测,对生产过程中的关键参数进行控制和调整。
3. 工艺流程控制:建立标准的工艺流程,并进行必要的培训和指导,确保操作的一致性和准确性。
4. 检验和测试:对生产的产品进行严格的检验和测试,包括外观、尺寸、性能等方面,确保其符合质量标准。
5. 不良品处理:建立合适的不良品处理机制,包括分类、记录、分析和改进措施的制定。
6. 反馈和改进:建立良好的反馈机制,收集客户反馈和市场信息,对产品和生产过程进行持续改进。
4. 质量管理体系为确保生产工艺和质量控制方案的有效实施,我们将建立质量管理体系,包括以下方面:1. 质量目标设定:设定具体的质量目标,如产品合格率、客户满意度等,并进行定期评估和监控。
2. 质量责任分工:明确各个岗位和部门在质量管理中的职责和义务。
3. 培训和教育:对员工进行必要的培训和教育,提高其质量意识和操作能力。
4. 内部审核和评估:定期进行内部审核和评估,发现问题并采取预防和改进措施。
5. 外部认证和审核:通过外部认证和审核,确保质量管理体系的符合性和有效性。
工艺质量控制程序
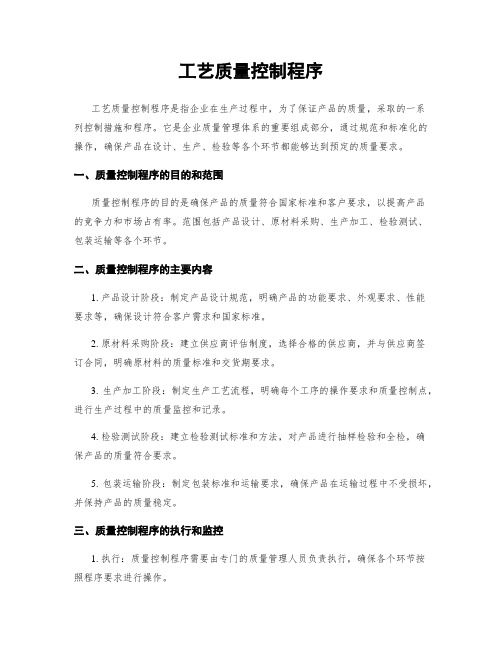
工艺质量控制程序工艺质量控制程序是指企业在生产过程中,为了保证产品的质量,采取的一系列控制措施和程序。
它是企业质量管理体系的重要组成部分,通过规范和标准化的操作,确保产品在设计、生产、检验等各个环节都能够达到预定的质量要求。
一、质量控制程序的目的和范围质量控制程序的目的是确保产品的质量符合国家标准和客户要求,以提高产品的竞争力和市场占有率。
范围包括产品设计、原材料采购、生产加工、检验测试、包装运输等各个环节。
二、质量控制程序的主要内容1. 产品设计阶段:制定产品设计规范,明确产品的功能要求、外观要求、性能要求等,确保设计符合客户需求和国家标准。
2. 原材料采购阶段:建立供应商评估制度,选择合格的供应商,并与供应商签订合同,明确原材料的质量标准和交货期要求。
3. 生产加工阶段:制定生产工艺流程,明确每个工序的操作要求和质量控制点,进行生产过程中的质量监控和记录。
4. 检验测试阶段:建立检验测试标准和方法,对产品进行抽样检验和全检,确保产品的质量符合要求。
5. 包装运输阶段:制定包装标准和运输要求,确保产品在运输过程中不受损坏,并保持产品的质量稳定。
三、质量控制程序的执行和监控1. 执行:质量控制程序需要由专门的质量管理人员负责执行,确保各个环节按照程序要求进行操作。
2. 监控:建立质量控制监控系统,对各个环节进行监督和检查,及时发现和纠正质量问题,确保程序的有效执行。
四、质量控制程序的改进质量控制程序需要不断改进和优化,以适应市场需求和技术进步。
企业应定期评估和审查质量控制程序的有效性,并根据评估结果进行改进和调整。
五、质量控制程序的效益质量控制程序的实施可以提高产品的一致性和稳定性,减少产品的次品率和售后问题,提高产品的可靠性和用户满意度。
同时,也可以提高企业的竞争力和市场声誉,为企业带来经济效益和社会效益。
六、质量控制程序的案例分析以某家制造业企业为例,该企业实施了严格的质量控制程序,通过对原材料的检验和筛选,确保原材料的质量符合要求;通过对生产过程的监控和控制,确保产品的加工精度和外观质量;通过对成品的全检和抽样检验,确保产品的质量稳定和可靠性。
生产工艺和质量控制方案

生产工艺和质量控制方案一、生产工艺方案1. 原料采购选择符合国家相关标准的原料供应商进行长期合作。
原料采购时需严格把关,确保原料的质量和安全。
2. 原料检测所有进厂原料均需通过严格的质量和安全检测,未通过检测的原料一律不得使用。
3. 生产过程- 预处理阶段:根据产品的特性,将原料进行必要的清洗、筛选、切割等预处理工作。
预处理阶段:根据产品的特性,将原料进行必要的清洗、筛选、切割等预处理工作。
- 加工阶段:将预处理后的原料按照生产工艺进行加工,如烹饪、烘烤、发酵等。
加工阶段:将预处理后的原料按照生产工艺进行加工,如烹饪、烘烤、发酵等。
- 包装阶段:加工后的产品进行包装,包装材料和包装过程需符合相关的食品安全标准。
包装阶段:加工后的产品进行包装,包装材料和包装过程需符合相关的食品安全标准。
4. 产品检测完成生产的产品需进行全面的质量和安全检测,检测合格后方可出厂销售。
二、质量控制方案1. 质量管理体系建立全面的质量管理体系,包含原料采购、生产过程、产品检测等各环节,确保产品的质量和安全。
2. 员工培训定期对员工进行质量管理和食品安全知识的培训,提高员工的质量意识和操作技能。
3. 质量检测- 进厂原料检测:对所有进厂的原料进行全面的质量和安全检测。
进厂原料检测:对所有进厂的原料进行全面的质量和安全检测。
- 生产过程检测:在生产过程中,定期对产品进行抽检,及时发现并解决可能存在的质量问题。
生产过程检测:在生产过程中,定期对产品进行抽检,及时发现并解决可能存在的质量问题。
- 出厂产品检测:完成生产的产品需通过全面的质量和安全检测,合格后方可出厂。
出厂产品检测:完成生产的产品需通过全面的质量和安全检测,合格后方可出厂。
4. 追溯系统建立产品质量追溯系统,一旦发现产品质量问题,可以迅速追溯到生产的具体环节,及时采取改正措施。
5. 持续改进根据质量检测结果和客户反馈,持续优化生产工艺和质量控制措施,进一步提高产品的质量和客户满意度。
工艺质量控制程序

工艺质量控制程序标题:工艺质量控制程序引言概述:工艺质量控制程序是企业生产过程中非常重要的一环,通过建立科学的质量控制程序,可以有效地保证产品质量,提高生产效率,降低生产成本。
本文将详细介绍工艺质量控制程序的内容和重要性。
一、制定质量控制标准1.1 确定产品质量标准:根据产品的特性和客户的需求,确定产品的各项质量指标,如尺寸、外观、性能等。
1.2 制定工艺流程:根据产品的生产工艺,确定每个生产环节的具体要求和控制标准。
1.3 制定检验标准:确定产品的检验方法和检验标准,确保产品符合质量要求。
二、建立质量控制体系2.1 培训员工:对生产人员进行质量控制知识和技能培训,提高其质量意识和操作技能。
2.2 设立质量控制岗位:建立专门的质量控制部门或岗位,负责监督和执行质量控制程序。
2.3 定期审核和改进:定期对质量控制程序进行审核,发现问题及时改进和完善。
三、监控生产过程3.1 设立监控点:在生产过程中设立关键控制点,对关键环节进行监控和记录。
3.2 实施过程控制:通过采集数据和实时监测,及时发现生产过程中的异常情况,保证产品质量稳定。
3.3 进行过程分析:对生产过程中的数据进行分析,找出问题根源并采取措施解决。
四、产品检验和验证4.1 抽样检验:对生产出来的产品进行抽样检验,确保产品符合质量标准。
4.2 实验室验证:对产品进行实验室测试验证,确保产品性能和质量符合要求。
4.3 不良品处理:对不合格产品进行处理,包括返工、报废等,防止不良品流入市场。
五、持续改进5.1 收集反馈信息:定期收集客户反馈信息和内部反馈意见,发现问题并及时改进。
5.2 设立改进计划:根据反馈信息和内部审核结果,制定改进计划,不断提升产品质量和生产效率。
5.3 持续学习和提升:加强员工培训和技能提升,保持质量控制程序的有效性和持续改进。
结语:通过建立科学的工艺质量控制程序,企业可以提高产品质量,降低生产成本,增强市场竞争力。
质量控制程序不仅是企业的生产管理工具,更是企业长期发展的重要保障。
(完整版)生产工艺和质量控制方案
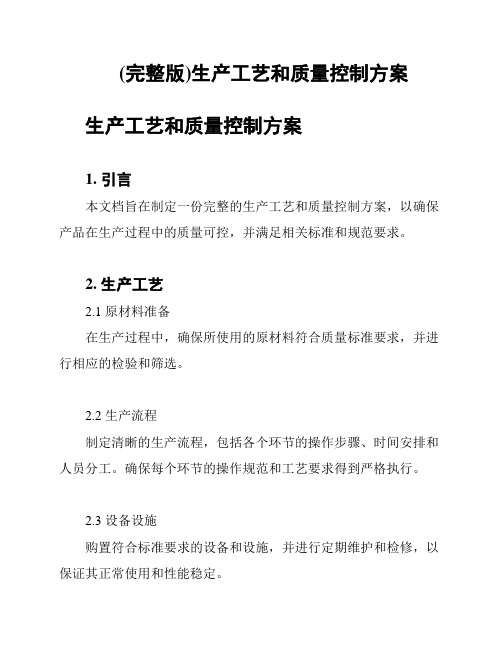
(完整版)生产工艺和质量控制方案生产工艺和质量控制方案1. 引言本文档旨在制定一份完整的生产工艺和质量控制方案,以确保产品在生产过程中的质量可控,并满足相关标准和规范要求。
2. 生产工艺2.1 原材料准备在生产过程中,确保所使用的原材料符合质量标准要求,并进行相应的检验和筛选。
2.2 生产流程制定清晰的生产流程,包括各个环节的操作步骤、时间安排和人员分工。
确保每个环节的操作规范和工艺要求得到严格执行。
2.3 设备设施购置符合标准要求的设备和设施,并进行定期维护和检修,以保证其正常使用和性能稳定。
2.4 人员培训对相关生产操作人员进行培训,包括工艺操作规范、安全操作要求和质量控制知识的传授。
确保员工具备相关技能和知识,能够正确操作生产设备和进行质量检验。
3. 质量控制3.1 原材料检验对所使用的原材料进行全面的检验,包括外观、物理性能和化学性质等方面的检测,确保原材料符合标准和质量要求。
3.2 生产过程监控在生产过程中,设置合适的监控点和监测手段,对每个环节的关键参数进行实时监测和记录。
发现异常情况及时采取措施进行调整和修正。
3.3 成品检验对生产出的成品进行全面的检验,包括外观、性能指标和功能测试等方面的评估。
确保产品符合标准和规范要求。
3.4 不良品处理对发现的不良品进行分类、记录和处理,同时分析不良品的原因,采取措施进行改进和预防,以提高产品质量。
4. 文件记录建立完善的文件记录系统,包括生产工艺文件、质量检验报告、不良品记录等。
确保记录准确、可追溯和可审查。
5. 改进措施定期开展质量管理评审,总结经验教训,找出存在的问题和不足,提出改进措施,并落实到生产实践中。
6. 结论本文档提供了一份完整的生产工艺和质量控制方案,通过严格执行该方案,可确保产品在生产过程中的质量可控并符合相关标准和规范要求。
工艺质量控制程序
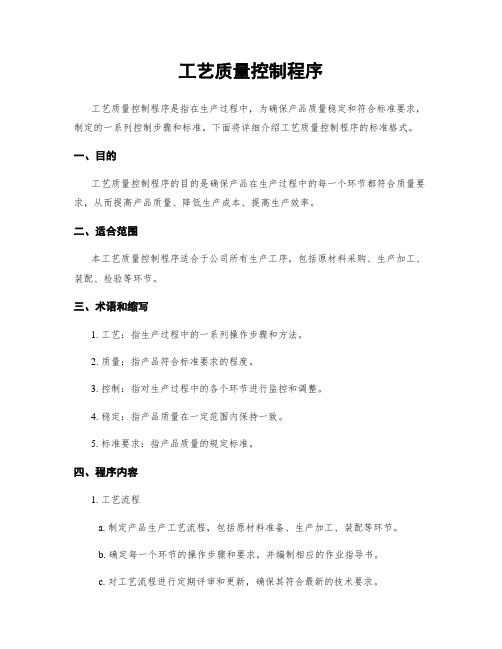
工艺质量控制程序工艺质量控制程序是指在生产过程中,为确保产品质量稳定和符合标准要求,制定的一系列控制步骤和标准。
下面将详细介绍工艺质量控制程序的标准格式。
一、目的工艺质量控制程序的目的是确保产品在生产过程中的每一个环节都符合质量要求,从而提高产品质量、降低生产成本、提高生产效率。
二、适合范围本工艺质量控制程序适合于公司所有生产工序,包括原材料采购、生产加工、装配、检验等环节。
三、术语和缩写1. 工艺:指生产过程中的一系列操作步骤和方法。
2. 质量:指产品符合标准要求的程度。
3. 控制:指对生产过程中的各个环节进行监控和调整。
4. 稳定:指产品质量在一定范围内保持一致。
5. 标准要求:指产品质量的规定标准。
四、程序内容1. 工艺流程a. 制定产品生产工艺流程,包括原材料准备、生产加工、装配等环节。
b. 确定每一个环节的操作步骤和要求,并编制相应的作业指导书。
c. 对工艺流程进行定期评审和更新,确保其符合最新的技术要求。
2. 质量标准a. 确定产品质量标准要求,包括外观、尺寸、材料、性能等方面。
b. 制定相应的检验方法和标准,确保产品在每一个环节都能进行有效的检验。
c. 对质量标准进行定期评审和更新,确保其与市场需求和技术发展保持一致。
3. 质量控制a. 在每一个环节设立质量控制点,对关键工序进行监控和检验。
b. 制定相应的质量控制计划和控制图表,记录和分析生产过程中的质量数据。
c. 对不符合质量要求的产品进行追溯和处理,并采取纠正措施,防止类似问题再次发生。
4. 培训和培训记录a. 对生产人员进行质量控制方面的培训,提高其质量意识和技能水平。
b. 记录培训内容、培训人员和培训时间,并保留相关培训证明材料。
5. 审核和评估a. 对工艺质量控制程序进行定期审核,确保其有效性和符合要求。
b. 对生产过程中的质量数据进行分析和评估,发现问题并及时采取措施进行改进。
六、责任和权限1. 生产部门负责制定和执行工艺质量控制程序。
工艺质量控制程序
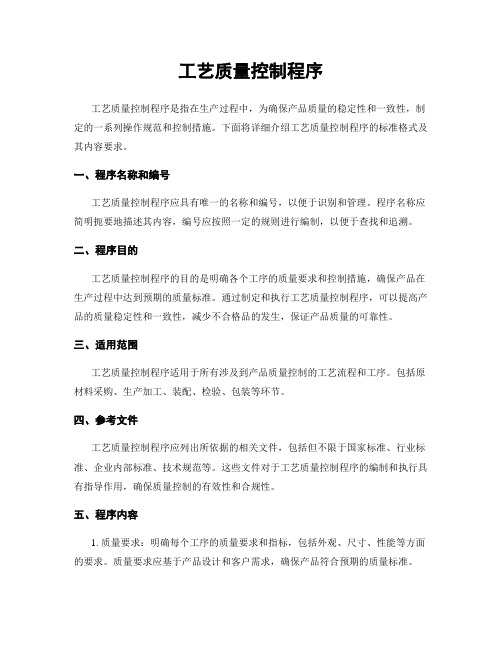
工艺质量控制程序工艺质量控制程序是指在生产过程中,为确保产品质量的稳定性和一致性,制定的一系列操作规范和控制措施。
下面将详细介绍工艺质量控制程序的标准格式及其内容要求。
一、程序名称和编号工艺质量控制程序应具有唯一的名称和编号,以便于识别和管理。
程序名称应简明扼要地描述其内容,编号应按照一定的规则进行编制,以便于查找和追溯。
二、程序目的工艺质量控制程序的目的是明确各个工序的质量要求和控制措施,确保产品在生产过程中达到预期的质量标准。
通过制定和执行工艺质量控制程序,可以提高产品的质量稳定性和一致性,减少不合格品的发生,保证产品质量的可靠性。
三、适用范围工艺质量控制程序适用于所有涉及到产品质量控制的工艺流程和工序。
包括原材料采购、生产加工、装配、检验、包装等环节。
四、参考文件工艺质量控制程序应列出所依据的相关文件,包括但不限于国家标准、行业标准、企业内部标准、技术规范等。
这些文件对于工艺质量控制程序的编制和执行具有指导作用,确保质量控制的有效性和合规性。
五、程序内容1. 质量要求:明确每个工序的质量要求和指标,包括外观、尺寸、性能等方面的要求。
质量要求应基于产品设计和客户需求,确保产品符合预期的质量标准。
2. 工艺控制措施:制定和描述每个工序的工艺控制措施,包括但不限于工艺参数设定、操作规程、设备校验和维护、环境条件等。
工艺控制措施应能够确保产品在生产过程中符合质量要求。
3. 检验方法:明确每个工序的检验方法和检验标准,包括取样方法、检测设备、检测程序等。
检验方法应能够准确判断产品是否符合质量要求。
4. 不合格品处理:规定不合格品的处理程序和责任人,包括不合格品的隔离、评审、返工或报废等。
不合格品处理程序应能够及时发现和处理不合格品,防止不合格品流入市场。
5. 记录和报告:要求每个工序进行记录和报告,包括但不限于工艺参数记录、检验记录、不合格品记录等。
记录和报告的目的是追溯和分析产品质量问题,及时采取纠正措施,提高产品质量。
工艺质量控制程序

工艺质量控制程序工艺质量控制程序是指为了确保产品质量的稳定性和一致性,制定和执行的一系列规范和步骤。
下面将详细介绍工艺质量控制程序的标准格式。
一、目的工艺质量控制程序的目的是确保产品在生产过程中符合质量标准和要求,以提高产品质量和客户满意度。
二、范围本工艺质量控制程序适合于所有涉及到产品生产过程的部门和人员。
三、定义1. 工艺:指产品的生产过程,包括原材料准备、加工、装配等环节。
2. 质量标准:指产品质量的要求和规范。
3. 控制点:指在工艺过程中需要进行检验和监控的关键环节。
四、程序1. 工艺设计阶段1.1 确定产品的质量标准和要求。
1.2 制定工艺流程,包括原材料选择、加工方法、装配顺序等。
1.3 设计并制定相应的检验和测试方法。
1.4 制定工艺文件,明确每一个工艺步骤的要求和控制点。
2. 原材料准备阶段2.1 确保原材料符合质量标准和要求。
2.2 对原材料进行检验和测试,包括外观、尺寸、化学成份等。
2.3 对不合格的原材料进行处理,如退货或者返工。
3. 加工阶段3.1 按照工艺流程进行加工操作。
3.2 对关键工艺步骤进行检验和测试,确保产品符合质量标准。
3.3 对不合格品进行处理,如修复、返工或者报废。
4. 装配阶段4.1 按照工艺流程进行装配操作。
4.2 对关键装配步骤进行检验和测试,确保产品符合质量标准。
4.3 对不合格品进行处理,如修复、返工或者报废。
5. 检验阶段5.1 对成品进行全面检验和测试,包括外观、尺寸、功能等。
5.2 检查产品是否符合质量标准和要求。
5.3 对不合格品进行处理,如修复、返工或者报废。
6. 记录和报告6.1 在每一个工艺步骤和检验环节记录相关数据和结果。
6.2 编制质量报告,包括产品合格率、不合格品处理情况等。
6.3 对质量问题进行分析和改进措施的制定。
五、责任1. 工艺部门负责制定和更新工艺流程和文件。
2. 生产部门负责按照工艺流程进行生产操作。
3. 质量部门负责检验和测试工作,并对不合格品进行处理。
工艺质量控制程序

工艺质量控制程序工艺质量控制程序是企业生产过程中的重要环节,它涉及到产品质量的稳定性和可靠性。
本文将详细介绍工艺质量控制程序的标准格式,包括程序的目的、范围、责任、流程、记录和评审等内容。
一、程序目的工艺质量控制程序的目的是确保产品在生产过程中能够符合相关质量标准和要求,保证产品质量的稳定性和可靠性。
二、程序范围工艺质量控制程序适用于企业生产过程中涉及到的所有工艺环节,包括原材料采购、生产加工、产品检验等。
三、程序责任1. 生产部门负责制定和执行工艺质量控制程序,确保生产过程中的质量控制措施得以有效实施。
2. 质量部门负责监督和检查工艺质量控制程序的执行情况,并提出改进建议。
3. 相关部门和人员要积极配合执行工艺质量控制程序,确保程序的有效实施。
四、程序流程1. 原材料采购控制:a. 生产部门根据产品特性和质量要求,制定原材料采购标准和规范。
b. 采购部门按照标准和规范选择合格的供应商,并建立供应商评估制度。
c. 采购部门对进货的原材料进行检验,确保原材料符合要求。
2. 生产过程控制:a. 生产部门制定生产工艺流程和操作规范,确保生产过程的稳定性和可控性。
b. 生产人员按照工艺流程和操作规范进行生产,确保产品质量的稳定性。
c. 过程中进行必要的检验和测试,及时发现和纠正生产过程中的问题。
3. 产品检验控制:a. 生产部门制定产品检验标准和方法,对成品进行全面的检验。
b. 质量部门负责进行产品检验,确保产品质量符合标准和要求。
c. 对不合格产品进行处理,包括返工、报废或退货等。
五、程序记录1. 原材料采购记录:a. 采购部门应建立原材料采购记录,包括供应商信息、采购数量、检验结果等。
b. 采购记录应保存至少一年,以备查证。
2. 生产过程记录:a. 生产部门应建立生产过程记录,包括生产工艺参数、操作记录、检验结果等。
b. 生产过程记录应保存至少一年,以备查证。
3. 产品检验记录:a. 质量部门应建立产品检验记录,包括检验方法、检验结果、不合格品处理等。
工艺质量控制程序
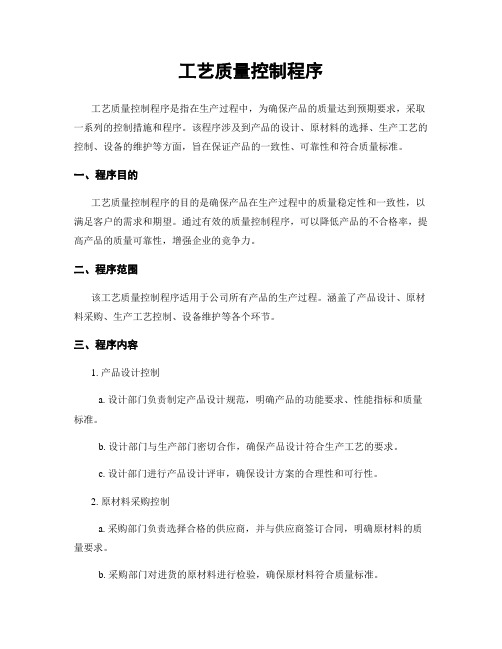
工艺质量控制程序工艺质量控制程序是指在生产过程中,为确保产品的质量达到预期要求,采取一系列的控制措施和程序。
该程序涉及到产品的设计、原材料的选择、生产工艺的控制、设备的维护等方面,旨在保证产品的一致性、可靠性和符合质量标准。
一、程序目的工艺质量控制程序的目的是确保产品在生产过程中的质量稳定性和一致性,以满足客户的需求和期望。
通过有效的质量控制程序,可以降低产品的不合格率,提高产品的质量可靠性,增强企业的竞争力。
二、程序范围该工艺质量控制程序适用于公司所有产品的生产过程。
涵盖了产品设计、原材料采购、生产工艺控制、设备维护等各个环节。
三、程序内容1. 产品设计控制a. 设计部门负责制定产品设计规范,明确产品的功能要求、性能指标和质量标准。
b. 设计部门与生产部门密切合作,确保产品设计符合生产工艺的要求。
c. 设计部门进行产品设计评审,确保设计方案的合理性和可行性。
2. 原材料采购控制a. 采购部门负责选择合格的供应商,并与供应商签订合同,明确原材料的质量要求。
b. 采购部门对进货的原材料进行检验,确保原材料符合质量标准。
c. 采购部门建立供应商评估制度,定期对供应商进行评估和考核。
3. 生产工艺控制a. 生产部门制定详细的生产工艺流程,包括原材料的配比、加工工艺、操作规程等。
b. 生产部门对生产过程进行监控,确保每个环节符合质量要求。
c. 生产部门建立不良品处理制度,对不合格品进行追溯和处理。
4. 设备维护控制a. 设备管理部门负责设备的维护和保养工作,确保设备处于良好的工作状态。
b. 设备管理部门建立设备巡检制度,定期对设备进行巡检和维护。
c. 设备管理部门对设备进行校准和验证,确保设备的准确性和稳定性。
5. 质量数据分析和改进a. 质量部门负责收集和分析质量数据,包括产品的质量指标、不良品率等。
b. 质量部门定期组织质量会议,对质量问题进行分析和改进。
c. 质量部门与相关部门合作,制定改进措施,并跟踪改进效果。
工艺质量控制程序
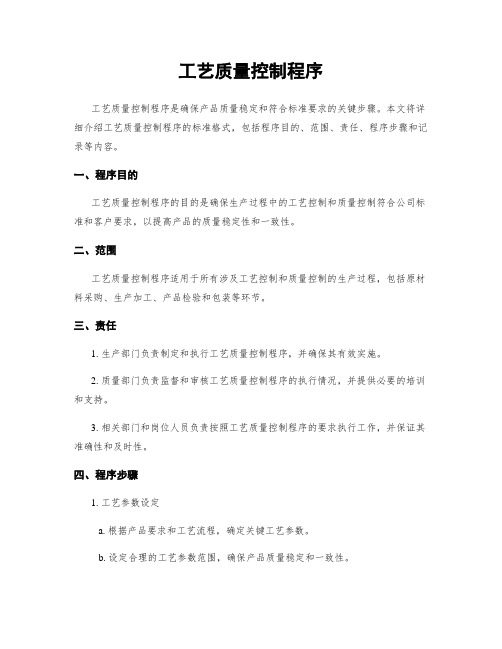
工艺质量控制程序工艺质量控制程序是确保产品质量稳定和符合标准要求的关键步骤。
本文将详细介绍工艺质量控制程序的标准格式,包括程序目的、范围、责任、程序步骤和记录等内容。
一、程序目的工艺质量控制程序的目的是确保生产过程中的工艺控制和质量控制符合公司标准和客户要求,以提高产品的质量稳定性和一致性。
二、范围工艺质量控制程序适用于所有涉及工艺控制和质量控制的生产过程,包括原材料采购、生产加工、产品检验和包装等环节。
三、责任1. 生产部门负责制定和执行工艺质量控制程序,并确保其有效实施。
2. 质量部门负责监督和审核工艺质量控制程序的执行情况,并提供必要的培训和支持。
3. 相关部门和岗位人员负责按照工艺质量控制程序的要求执行工作,并保证其准确性和及时性。
四、程序步骤1. 工艺参数设定a. 根据产品要求和工艺流程,确定关键工艺参数。
b. 设定合理的工艺参数范围,确保产品质量稳定和一致性。
c. 制定工艺参数设定记录,记录设定的参数数值和日期等信息。
2. 工艺控制a. 根据工艺参数设定,执行生产工艺控制。
b. 监测关键工艺参数,及时调整和纠正异常情况。
c. 制定工艺控制记录,记录关键工艺参数的监测结果和调整情况。
3. 质量检验a. 根据产品要求和质量标准,制定质量检验方案。
b. 对生产过程中的关键节点进行抽样检验,确保产品质量符合要求。
c. 制定质量检验记录,记录检验结果和日期等信息。
4. 不合格品处理a. 对于不合格品,及时停止生产并进行隔离处理。
b. 进行不合格品的分析和原因追溯,采取纠正措施防止再次发生。
c. 制定不合格品处理记录,记录处理措施和结果等信息。
五、记录为了确保工艺质量控制程序的有效实施和追溯,需要建立以下记录:1. 工艺参数设定记录:记录设定的工艺参数数值和日期等信息。
2. 工艺控制记录:记录关键工艺参数的监测结果和调整情况。
3. 质量检验记录:记录质量检验的结果和日期等信息。
4. 不合格品处理记录:记录不合格品的处理措施和结果等信息。
工艺质量控制程序

工艺质量控制程序工艺质量控制程序是指为确保产品质量符合标准要求而制定的一系列操作规程和流程。
该程序旨在确保生产过程中的每个环节都能够被严格控制和监督,以保证产品的质量稳定性和一致性。
下面是一个标准格式的工艺质量控制程序,详细描述了该程序的各个环节和要求。
1. 程序目的:本工艺质量控制程序的目的是确保生产过程中的每个环节都能够按照标准要求进行操作,以保证产品质量的稳定性和一致性。
2. 适用范围:本程序适用于所有生产工序,包括原材料采购、生产加工、质量检验等环节。
3. 质量控制流程:3.1 原材料采购:- 与供应商签订合同,明确原材料的质量要求和交货期限。
- 对原材料进行检验,包括外观、尺寸、化学成分等方面的检测。
- 对合格的原材料进行入库操作,并进行标识和分类存放。
3.2 生产加工:- 根据产品工艺流程,进行生产操作。
- 在每个生产环节进行自检,确保每个工序的合格率达到标准要求。
- 对关键工序进行首检和末检,确保产品质量的稳定性和一致性。
3.3 质量检验:- 在生产过程中,定期进行抽样检验,检测产品的质量指标是否符合标准要求。
- 对不合格品进行记录和处理,包括返工、报废等措施。
- 对合格品进行标识和分类存放,以便后续的出库和交付操作。
4. 质量控制记录:- 对每个环节的质量控制操作进行记录,包括原材料检验记录、生产自检记录、质量检验记录等。
- 所有记录必须真实、准确,并保存一定的时间,以备查证和追溯。
5. 质量控制的责任:- 生产人员负责自己环节的质量控制,包括自检和首末检。
- 质检人员负责对产品进行抽样检验和质量记录的维护。
- 质量管理人员负责对整个质量控制程序的监督和管理。
6. 不合格品处理:- 对于不合格品,必须立即停止生产,并进行记录和处理。
- 不合格品的处理方式包括返工、报废等,必须经过质量管理人员的批准和确认。
7. 不符合项的纠正和预防:- 对于质量控制过程中出现的不符合项,必须进行纠正和预防措施的制定和执行。
质量控制的工艺流程控制
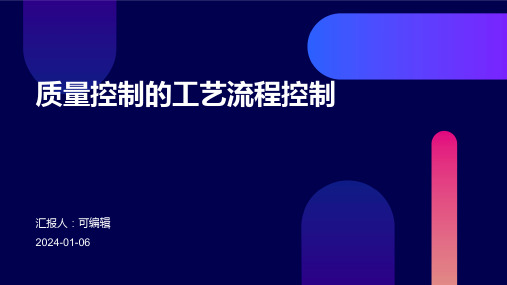
案例二:某电子制造企业的工艺流程改进
总结词:流程优化
详细描述:某电子制造企业针对现有工艺流程存在的问题,通过分析生产数据、优化工艺参数、改进 设备布局等方式,实现了工艺流程的优化。这一改进提高了生产效率、降低了不良品率,从而提升了 企业的竞争力。
案例三:某食品加工企业的质量安全控制
使用设备和工具,避免操作失误。
培训与指导
03
通过作业指导书对操作人员进行培训和指导,确保他们能够熟
练掌握操作技能和工艺要求。
在制品检验
检验标准制定
根据产品质量要求和工艺标准,制定在制品检验的标 准和规范。
检验过程控制
在制品检验过程中,应严格控制检验过程的质量,确 保检验结果的准确性和可靠性。
不合格品处理
质量控制的工艺流程控制
汇报人:可编辑 2024-01-06
目录
• 质量控制概述 • 工艺流程控制基础 • 质量控制工具与技术 • 工艺流程控制实践 • 质量控制与持续改进 • 案例分享
01
质量控制概述
质量控制定义
01
质量控制是指在生产过程中对产 品的质量进行检测、控制和监督 的一系列活动,以确保产品达到 预定的质量要求。
质量控制的发展历程
传统质量控制
依赖于检验员对产品进行抽检或全检,对不合格品进行处理。这种方法效率较低,不能 实时监控产品质量。
统计质量控制
利用统计学方法对生产过程进行监控和预测,通过收集和分析数据来控制产品质量。这 种方法能够实时监控产品质量,提高生产效率和产品质量稳定性。
全面质量管理
强调全员参与和全过程控制,通过建立完善的质量管理体系来提高产品质量和客户满意 度。这种方法注重预防措施和持续改进,能够提高企业的竞争力和品牌形象。
- 1、下载文档前请自行甄别文档内容的完整性,平台不提供额外的编辑、内容补充、找答案等附加服务。
- 2、"仅部分预览"的文档,不可在线预览部分如存在完整性等问题,可反馈申请退款(可完整预览的文档不适用该条件!)。
- 3、如文档侵犯您的权益,请联系客服反馈,我们会尽快为您处理(人工客服工作时间:9:00-18:30)。
工艺质量管理控制程序
1. 目的
为确保清洗工艺质量在施工的全过程均处于受控状态。
2. 范围
本程序适用于公司施工中的工艺质量控制。
(包括施工方案控制、工装模具管理、施工技术交底控制、施工环境控制)
3. 控制程序
3.1工艺文件控制
3..1.1工艺文件的审批
(1)工艺责任工程师负责项目工程全过程的工艺质量控制,参加设计交底和图纸会审,确定设计项目的使用功能和安全质量符合规范和满足业主的要求。
(2)通用或者专用工艺文件的编制由技术质量科负责,质量管理工程师审核,总工程师批准。
(3)施工组织设计∕施工方案由工艺责任工程师负责组织项目经理部编制,质量保管理工程师审核,总工程师批准,甲方相关人员确认会签,并按合同要求发放、登记、归档,保存期不少于5年。
(4)施工组织设计∕清洗施工方案编制原则
1)技术要求明确,符合设计和现行规范标准;
2)施工方法必须先进可靠和经济合理;
3)材料、施工设备机具和检测仪器配置合理,能满足施工质量要求,并处于完好可用状态;
4)施工作业人员配备合理,特种作业人员资质符合有关规范要求;
5)施工工序、关键和特殊过程质量控制明确,过程检验检测要求明确,方法措施完备,资料记录齐全;
6)必须根据项目特点建立项目部质量管理体系,设立相关责任人。
施工部署、施工手段、质保措施、安保措施、环保和文明施工等措施明确完备。
7)施工方案内容:清洗项目名称、概况,应执行的施工验收技术规范、标准和质量管理程序文件,施工工序、方法、技术措施、关键质量控制点和质量验收指标,人员配备及相关资质要求,施工机具及检验仪器设备的配备要求施工进度计划、施工平面布置、质量技术措施,工作危险性分析及相应的安全技术措施,突
发事件应急预案等。
8)清洗技术方案变更由要求方提交变更申请书,经相关人员审核认可后由工艺责任工程师编制,按3.3条审核、批准、确认、会签、发放、登记、归档、保存。
3.1.2工艺文件的更改
工艺文件遇到下列情况应更改
1)设计资料、技术标准更改;
2)完善工艺文件;
3)采纳先进经验或革新成果;
4)与有关单位进行技术协调。
在清洗施工过程中涉及到工艺更改,应由技术员及时填写工艺更改单进行更改。
临时工艺资料更改由技术质量科批准,定型工艺资料更改应经质量工程师审核,技术质量科主管批准生效。
“更改单”应进行编号。
工艺更改应及时执行,一般要求于三天之内完成工艺文件的更改。
3.2工装模具的设计、制造、检验,建档、标识、保管、定期检验及报废的管理。
3.2.1 工装模具设计
3.2.1.1 工艺装备模具的设计由项目技术员根据安装结构、质量要求等提出,经项目工艺责任人审核后进行。
3.2.1.2 重要工装模具设计方案需经总工程师批准后方可进行设计绘图和工艺编制。
3.2.1.3 对简单、小型的工装模具,项目部技术人员可自行设计,但须由工程部统一编号,设计的图纸应统一发放和管理。
3.2.1.4 工装模具设计应保证达到项目的技术标准的质量要求,做到结构先进、使用可靠,操作安全、经济合理。
3.2.1.5 工装设计完成后,应履行签字审批手续,工艺责任工程师审核,质量管理工工程师批准,然后交有关人员保存。
根据需要设计图纸存档。
3.2.2 工装模具制造
3.2.2.1 一般工装的制造由项目部安排实施,重要工装制造由生产科安排实施。
3.2.2.2 工装制造过程中,工装设计人员应到现场及时解决制造过程中的问题。
3.2.3 工装模具的检验/验证及使用
3.2.3.1 工装模具制造完成后后,应按图纸规定的部位用钢印打出工装模具编号及制造日期后,交付检验。
3.2.3.2 设计人员、技术人员、检验员共同对工装模具进行检验/验证,检验/验证合格后的工装方可投入生产使用。
3.2.3.3 经验证合格的工装交使用后,由生产科保管员进行入库登记,建账并保管,使用人员按要求借用。
3.2.3.4 由项目部资料员负责收集工装模具的所有检验和实验资料,经项目检验责任人审核后归档。
3.2.3.5 生产科要建立所有压力管道检维修用工装模具的台账,统一编号。
3.2.3.6 生产科应对工装模具定期进行检验,发现不合格时,由生产科和技术科进行评估,能进行修复的按职责进行修理,修理完成后重新进行检验,合格后做好相关记录并存档。
经评估不能修理或无修理价值的,作报废处理,转移至指定地点,并在相应台账做好记录。
3.3施工环境控制与基础设施配置
3.3.1施工环境控制措施所需设施由工艺工程师负责组织项目部编制配备计划,质量管理工程师审核,管理者代表审批,生产科购置、验收,项目部使用、维护和保管。
3.3.6.2施工环境因素有工程技术环境、工程管理环境和劳动环境等,涉及范围较大,在拟定控制措施时必须全面考虑综合分析,配备必要的设施达到有效控制的目的。
3.2.3施工过程中因环境的改变应根据工程特点和具体条件应对影响质量的环境因素,采取有效的措施严加控制。
3.3.4清洗施工项目所需的基础设施配置计划由工艺工程师组织项目部编制,质量管理工程师审核,管理者代表审批,生产科购置、验收、项目部使用、维护、保管。
3.4施工质量管理
项目经理部是实施工艺执行控制单位,必须严格按有关规范标准和清洗施工技术方案实施化学清洗和高压水射流过程操作。
3.4.1清洗项目施工前,必须由工艺工程师和HSE工程师进行安全技术交底,项目相关责任人员及施工人员参加。
技术交底内容包括:
(1)施工技术方案交底就施工内容、施工方法、步骤、质量控制标准、进度
要求等向作业人员进行交底。
(2)施工现场调查到施工现场核实设备位置、状况,施工机具的摆放、大型起重机械吊装站位,脚手架的搭设与安全警示标识、应急通道的设置等。
(3)施工工序的衔接现场每道工序各工种交叉作业的时间与人员安排,通知、联络方式,问题的反馈与协调程序等。
(4)HSE管理措施交底工作危险性分析、风险控制措施和应急预案,交底后项目技术员填写“安全技术交底记录”并由参加人员会签。
3.4.2施工中相关专业责任工程师负责指导、检查和监督,确保工艺文件得以严格执行。
1)每道工序施工质量都要经过自检、互检和专业检,并经有关专业责任工程师认可签字。
2)关键部位、重要工序的见证点或停止点,必须由三方(业主,监理和施工)共检,认可.签字。
3)坚持清洗程序施工,坚持上道工序未经检测合格不得进行下道工序的施工原则。
4)项目部必须真实、准确、详细地填写施工记录,明确责任,保证可追溯性。
5)施工过程技术文件和交工技术文件应满足SH/T3543、SH/T3503的规定。
6)施工记录以交工文件整理归档。
3.4.3施工过程发生的清洗方案修改,不合理产品的处理,半成品、成品的保护按相关控制程序和文件处理。
3.4.4施工结束后,项目工艺责任工程师应对清洗项目工程施工进行总结,全面评价清洗工艺的正确性、适用性和先进程度。
4.相关文件
4.1《记录控制程序》
5.记录
5.1质量控制点检查记录。